Bluerprint Lab REACH BRAVO Use and care manual

REACH BRAVO
INTEGRATION MANUAL
www.blueprintlab.com
tel: +61 (2) 9519 7651
|
email: info@blueprintlab.com

Page 1of 37
Blueprint Lab Confidential Proprietary Information not to be reproduced or made available to third parties without prior consent from
Blueprint Lab and not to be used in any unauthorised way. © Blueprint Lab Pty Ltd 2021
Contents
1SAFETY INFORMATION.............................................................................................................................3
1.1 CRUSH POINTS AND COLLISION HAZARDS ..............................................................................................3
1.2 SHOCK HAZARD.......................................................................................................................................3
1.3 BACKDRIVABILITY WARNING ..................................................................................................................4
1.4 LEAK DETECTION.....................................................................................................................................5
1.5 SERVICING SCHEDULE .............................................................................................................................5
1.5.1 Bravo Servicing Overview................................................................................................................5
1.6 OBSTACLE SETUP.....................................................................................................................................6
1.7 EMERGANCY STOP ..................................................................................................................................6
1.8 ELECTRICAL INSTALLATION .....................................................................................................................6
1.9 PHYSICAL INSTALLATION.........................................................................................................................6
1.10 OPERATING ENVIRONMENT ...................................................................................................................6
1.10.1 Operating and Storage Temperature..............................................................................................6
1.10.2 Pressure ..........................................................................................................................................6
1.10.3 Explosive Environments ..................................................................................................................6
2PRODUCT OVERVIEW...............................................................................................................................7
MAIN PRODUCT FEATURES.................................................................................................................................7
2.1 AVAILABLE CONFIGURATIONS ................................................................................................................7
2.2 END-EFFECTOR OPTIONS ........................................................................................................................8
2.3 RELATED PRODUCTS AND ACCESSORIES.................................................................................................9
3SPECIFICATIONS .....................................................................................................................................10
3.1 MECHANICAL ........................................................................................................................................10
3.2 DIMENSIONS, MODULES AND RANGE OF MOTION .................................................................................10
3.2.1 Bravo 7.......................................................................................................................................... 10
3.2.2 Bravo 5.......................................................................................................................................... 12
3.2.3 Bravo 3.......................................................................................................................................... 13
3.2.4 Bravo 2.......................................................................................................................................... 15
3.3 ENVIRONMENTAL .................................................................................................................................16
3.4 ELECTRICAL AND COMMUNICATION ....................................................................................................16
3.4.1 Power Interface............................................................................................................................. 16
3.4.2 Communication Interface .............................................................................................................16
3.5 KINEMATIC, DYNAMIC, DH PARAMETERS, AND OTHER PROPERTIES....................................................16
4INTERFACING AND INTEGRATION ..........................................................................................................17
4.1 BRAVO 5/BRAVO 7...............................................................................................................................17
4.1.1 Mechanical....................................................................................................................................17
4.1.2 Electrical........................................................................................................................................19
4.1.3 Communication Protocol ..............................................................................................................20
4.2 BRAVO 2/BRAVO 3...............................................................................................................................20
4.2.1 Mechanical....................................................................................................................................20
4.2.2 Electrical........................................................................................................................................22
4.3 INTEGRATION ELECTRICAL DIAGRAM ...................................................................................................23
5CONTROL OPTIONS ................................................................................................................................24
5.1 REACH CONTROL...................................................................................................................................24
5.2 EXTERNAL INPUTS.................................................................................................................................24
5.2.1 Gamepad ......................................................................................................................................24

Page 2of 37
Blueprint Lab Confidential Proprietary Information not to be reproduced or made available to third parties without prior consent from
Blueprint Lab and not to be used in any unauthorised way. © Blueprint Lab Pty Ltd 2021
5.2.2 Master Arm................................................................................................................................... 25
5.3 LOW-LEVEL CONTROL IMPLEMENTATION ............................................................................................25
6BENCH SETUP AND ACCEPTANCE TEST...................................................................................................26
6.1 BENCH SETUP........................................................................................................................................26
6.1.1 Physical interfacing....................................................................................................................... 26
6.1.2 Communication Setup................................................................................................................... 28
6.1.3 Reach Control................................................................................................................................ 29
6.2 ACCEPTANCE TEST ................................................................................................................................31
6.2.1 Range of Motion TEST...................................................................................................................31
6.2.2 Master Arm test (if applicable) .....................................................................................................33
7RECOMMENDED SERVICING SCHEDULE..................................................................................................36
8BLUEPRINT LAB SUPPORT PROGRAM.....................................................................................................36
9REVISION HISTORY.................................................................................................................................37
Note: Jump to Section 6: Bench Setup and Acceptance Test for instructions on how to setup your manipulator.

Page 3of 37
Blueprint Lab Confidential Proprietary Information not to be reproduced or made available to third parties without prior consent from
Blueprint Lab and not to be used in any unauthorised way. © Blueprint Lab Pty Ltd 2021
1 SAFETY INFORMATION
This section describes the necessary safety information and precautions relevant to the setup and operation of
the Reach Bravo manipulator system. To ensure correct and safe use of Blueprint Lab manipulators, carefully
read this section and make yourself well acquainted with the contents. Follow any warnings and cautions
included. In conjunction with this manual, it is important that the users have knowledge of safety
considerations and make correct judgments on safety procedures during operation.
Reach Bravo manipulators are highly dexterous, electromechanical devices that can move with a high degree
of freedom. Failure to take necessary safety measures or mishandling due to not following the instructions in
this technical supplement may result in damage to the robot or injury to personnel.
1.1 CRUSH POINTS AND COLLISION HAZARDS
Crush hazards exist on the Reach Bravo in locations where two limbs can compress
together as well as in the jaws of the grabber stage of the manipulator. It is important
that the operator ensures the working area of the manipulator is clear prior to
operation.
1.2 SHOCK HAZARD
There should be no attempt made to remove the external housing of the manipulator to
expose the internal circuitry. Doing so could cause injury or fatality by electrical shock.

Page 4of 37
Blueprint Lab Confidential Proprietary Information not to be reproduced or made available to third parties without prior consent from Blueprint Lab and not to be used in any unauthorised way. © Blueprint Lab Pty
Ltd 2021
1.3 BACKDRIVABILITY WARNING
Axes G and D (see diagram below) use a software limits to ensure they do not rotate beyond their described Range of Motion. When power is off, this software limit is
inactive allowing the joint to be rotated past its limit.
When the arm is powered on, it does not know it has been rotated past its limit and will continue as normal. This can cause damage to the joint.

Page 5of 37
Blueprint Lab Confidential Proprietary Information not to be reproduced or made available to third parties without prior consent from
Blueprint Lab and not to be used in any unauthorised way. © Blueprint Lab Pty Ltd 2021
1.4 LEAK DETECTION
All Reach Bravo products have an internal vacuum pulled inside the modules of the manipulator. This vacuum
is monitoring by an internal Leak Detection System. If there is a breach in the vacuum, this message will appear
in the help menu of Reach Control.
It is important that users do not remove any of the internal screws of the port, at the risk of releasing the
modules vacuum.
1.5 SERVICING SCHEDULE
Blueprint Lab have a recommended servicing schedule for manipulator products of 1 year or 200 operational
hours, whichever occurs first. Adhering to this servicing schedule ensures Blueprint Lab manipulators maintain
their performance within the operational specification and reduced the risk of failure in the field.
1.5.1 BRAVO SERVICING OVERVIEW
System Item Procedure Description
System
Item
Procedure Description
Subassembly
Mechanical
O-rings
Replace
Gears
Clean and re-lubricate
Keyway systems
Check backlash and tune
Crimps, connectors and wire harness
Visually Inspect
Internal Fasteners
Replace and apply Loctite
Motors
Check output torque
Subassembly
Electrical
Electrical Board
Check indicators and functionality
Encoders
Visually Inspect and recalibrate if
required.
Encoder boards
Check indicators and functionality
Subassembly
Software
Software Revision
Upgrade to latest software
Configuration Settings
Check and update if required
Kinematics
Check and update if required
Whole
Anodising
Visually Inspect
External fasteners
Replace
Quality Control
Perform Outgoing quality control and
provide

Page 6of 37
Blueprint Lab Confidential Proprietary Information not to be reproduced or made available to third parties without prior consent from
Blueprint Lab and not to be used in any unauthorised way. © Blueprint Lab Pty Ltd 2021
Any additional rectification work required will be assessed and quoted during the servicing process.
1.6 OBSTACLE SETUP
Ensure that the manipulator is setup correctly using the bench test and platform integration procedures shown
elsewhere in this manual. In particular, care should be taken to ensure that permanent obstacles in the
workspace are correctly defined to avoid collision between the manipulator and other equipment. The
manipulator arrives with a ‘floor’ obstacle installed to avoid collision with the bench/test platform.
1.7 EMERGANCY STOP
It is strongly recommended that an ESTOP button is included in the power circuit when bench level testing the
manipulator. Additionally, a digital ESTOP is included in the Reach Control software.
1.8 ELECTRICAL INSTALLATION
For bench level testing, it is strongly recommended to use a controlled power supply with a current limiting
circuit and/or a Residual Current Device (RCD) mechanism.
1.9 PHYSICAL INSTALLATION
Prior to operation, ensure that the manipulator is firmly secured using the supplied mounting kit, or an
alternative solution with the appropriate specifications.
1.10OPERATING ENVIRONMENT
1.10.1 OPERATING AND STORAGE TEMPERATURE
The manipulator system is specified for use from -10°C to 40°C (operating) and up to 80°C storage.
1.10.2 PRESSURE
The Reach Bravo is Depth Rated to operate at the equivalent of 300MSW.
1.10.3 EXPLOSIVE ENVIRONMENTS
Reach Bravo manipulators are not designed to meet explosion-proof specifications. Do not use the robot and
controller in environments containing inflammable gas, gasoline or solvent. Explosions or fire may otherwise
result.

Page 7of 37
Blueprint Lab Confidential Proprietary Information not to be reproduced or made available to third parties without prior consent from
Blueprint Lab and not to be used in any unauthorised way. © Blueprint Lab Pty Ltd 2021
2 PRODUCT OVERVIEW
The Reach Bravo is an advanced electric manipulator system that opens a new set of compact inspection and
intervention opportunities for militaries, service providers, researchers, and other operators.
Designed originally for the harsh subsea environment, and with an operating depth of 300m, the Reach Bravo is
also suitable for austere out-of-water applications.
With a highly modular design, the Reach Bravo is available in configurations ranging from a single-function
grabber (linear) or rotate actuator up to the seven-function Bravo 7. The Reach Bravo range is a one-stop-shop
for multiplying the manipulation capability of your inspection class vehicle or other platform.
MAIN PRODUCT FEATURES
•Master Arm Enabled
•300m Depth Rated
•All-Electric, Zero Oil
•Accessory Port for Camera, Lights, and other Sensors/Tools
•Embedded NVIDIA TX2 (5/7F Only) for Real-Time Perception and Control
•Adjustable Grab Force
•On-board Kinematics
•Workspace Obstacles
•Collision Protection
•One-click deploy/stow position
2.1 AVAILABLE CONFIGURATIONS
Bravo 7 –Seven-Function Manipulator
RB-7001
Bravo 5 –Five-Function Manipulator
RB-5001

Page 8of 37
Blueprint Lab Confidential Proprietary Information not to be reproduced or made available to third parties without prior consent from
Blueprint Lab and not to be used in any unauthorised way. © Blueprint Lab Pty Ltd 2021
Bravo 3 –Three-Function Manipulator
RB-3001
Bravo 2 –Two-Function Manipulator
RB-2001
2.2 END-EFFECTOR OPTIONS
Wide Quad Jaws
RB-1025
Interlocking Quad Jaws (Stainless Steel option)
RB-1041 (RB-1055)
Parallel Jaws
RB-1034
Cutter
RB-1031
Image Not Available

Page 9of 37
Blueprint Lab Confidential Proprietary Information not to be reproduced or made available to third parties without prior consent from
Blueprint Lab and not to be used in any unauthorised way. © Blueprint Lab Pty Ltd 2021
2.3 RELATED PRODUCTS AND ACCESSORIES
See respective manuals of related products for details.
Master Arms
RM-5201 and RM-7201
Reach Control Pro
RC-2000

Page 10 of 37
Blueprint Lab Confidential Proprietary Information not to be reproduced or made available to third parties without prior consent from
Blueprint Lab and not to be used in any unauthorised way. © Blueprint Lab Pty Ltd 2021
SPECIFICATIONS
3
3.1 MECHANICAL
Bravo 7
Bravo 5
Bravo 3
Bravo 2
Functions
7
5
3
2
Degrees-of-Freedom
6
4
2
1
Full-Extension Reach
900mm
750mm
410mm
320mm (static)
Dynamic Full-
Extension Lift
10kg
12kg
15kg
N/A
Base Joint Torque
110Nm
50Nm
N/A
Max Dynamic Lift
15kg
20kg
N/A
Max Axial Load
100kg
200kg
Wrist Torque
20Nm
Linear/Grabber Force
1000N
Weight (in Air)
9kg
7.5kg
3.8Kg
2.7Kg
Weight (in Water)
4.5kg
4kg
2.6kg
1.6kg
Joint Speed (24-48V)
45 - 80 deg/s
End-effector
Repeatability
<1cm
N/A
3.2 DIMENSIONS, MODULES AND RANGE OF MOTION
3.2.1 BRAVO 7
Note: Base joint is software limited to 359° (not continuous).
Bravo 7 –Dimensions and rotational capacity.

Page 11 of 37
Blueprint Lab Confidential Proprietary Information not to be reproduced or made available to third parties without prior consent from
Blueprint Lab and not to be used in any unauthorised way. © Blueprint Lab Pty Ltd 2021
Bravo 7 –Module breakdown.
Bravo 7 –Range of Motion top view (left) and side view (right).

Page 12 of 37
Blueprint Lab Confidential Proprietary Information not to be reproduced or made available to third parties without prior consent from
Blueprint Lab and not to be used in any unauthorised way. © Blueprint Lab Pty Ltd 2021
3.2.2 BRAVO 5
Note: Base joint is software limited to 359° (not continuous).
Bravo 5 –Dimensions and rotational capacity.
Figure 1 Bravo 5 module breakdown.
Bravo 5 module breakdown.

Page 13 of 37
Blueprint Lab Confidential Proprietary Information not to be reproduced or made available to third parties without prior consent from
Blueprint Lab and not to be used in any unauthorised way. © Blueprint Lab Pty Ltd 2021
Bravo 5 –Range of motion top view (left) and side view (right).
3.2.3 BRAVO 3
Bravo 3 –Dimensions and rotational capacity

Page 14 of 37
Blueprint Lab Confidential Proprietary Information not to be reproduced or made available to third parties without prior consent from
Blueprint Lab and not to be used in any unauthorised way. © Blueprint Lab Pty Ltd 2021
Bravo 3 –Range of motion of the Bravo 3 (top view)
Bravo 3 –Module breakdown

Page 15 of 37
Blueprint Lab Confidential Proprietary Information not to be reproduced or made available to third parties without prior consent from
Blueprint Lab and not to be used in any unauthorised way. © Blueprint Lab Pty Ltd 2021
3.2.4 BRAVO 2
Note; Bravo 2 Range of Motion is limited to the continuous rotate joint only.
Bravo 2 –Dimensions and rotational capabilities.
Bravo 2 –Module breakdown

Page 16 of 37
Blueprint Lab Confidential Proprietary Information not to be reproduced or made available to third parties without prior consent from
Blueprint Lab and not to be used in any unauthorised way. © Blueprint Lab Pty Ltd 2021
3.3 ENVIRONMENTAL
Operating Temperature Range
-10°C to 35°C
Storage Temperature Range
-10°C to 70°C
Depth Rating
300MSW
Housing Material
Hard Anodized AL6061
3.4 ELECTRICAL AND COMMUNICATION
3.4.1 POWER INTERFACE
Bravo 7
Bravo 5
Bravo 3
Bravo 2
Input Voltage
20-48V
20-48V
24-48V
24-48V
Power Draw
(Nominal with
10kg)
200W
200W
60W
60W
Power Draw
(Max with 10kg)
300W
300W
150W
N/A
3.4.2 COMMUNICATION INTERFACE
Processor
NVIDIA TX2
Interface Low-level Protocol
Ethernet, RS485, and RS232 (for units shipped Dec 20
onwards)
Proprietary Communication Protocol
Blueprint Lab Reach System Communication Protocol
Document (BPL-RCPD)
3.5 KINEMATIC, DYNAMIC, DH PARAMETERS, AND OTHER
PROPERTIES
For more detailed information to assist with research and low-level control/autonomy applications, please
contact Blueprint Lab regarding our Reach System Research Data Pack.

Page 17 of 37
Blueprint Lab Confidential Proprietary Information not to be reproduced or made available to third parties without prior consent from
Blueprint Lab and not to be used in any unauthorised way. © Blueprint Lab Pty Ltd 2021
4 INTERFACING AND INTEGRATION
Note: 3D CAD files for our manipulators are available upon request to assist with integration.
4.1 BRAVO 5 / BRAVO 7
4.1.1 MECHANICAL
MANIPULATOR BASE INTEGRATION

Page 18 of 37
Blueprint Lab Confidential Proprietary Information not to be reproduced or made available to third parties without prior consent from
Blueprint Lab and not to be used in any unauthorised way. © Blueprint Lab Pty Ltd 2021
CONNECTOR CLEARANCE

Page 19 of 37
Blueprint Lab Confidential Proprietary Information not to be reproduced or made available to third parties without prior consent from
Blueprint Lab and not to be used in any unauthorised way. © Blueprint Lab Pty Ltd 2021
4.1.2 ELECTRICAL
POWER CONNECTOR - DWTEK MCBH4M
Bulkhead Connector Receptacle
Male Face View
Interface Cable (Supplied)
MCIL4F - MC Inline, 4C Female to unterminated ends (100cm)
COMMUNICATION CONNECTOR –DWTEK MCBH8ME
Bulkhead Connector Receptacle
Male Face View
Pins
Description
Colour
1
RS485 A
Brown
2
RS485 B
Light brown
3
RS232 TX (data to vehicle)
Blue
4
RS232 RX (data from vehicle)
Light blue
5
ETH RX-
Orange
6
ETH RX+
Light orange
7
ETH TX-
Green
8
ETH TX+
Light green
Interface Cable (Supplied)
MCIL8FE10 - MC Ethernet Inline, 8C Female to unterminated ends (100cm).
Pins
Description
Colour
1
GND
Black
2
POWER
White
3
POWER
Red
4
GND
Green
This manual suits for next models
9
Table of contents
Popular Robotics manuals by other brands

Mitsubishi Electric
Mitsubishi Electric MELFA RH-6SQH Series instruction manual
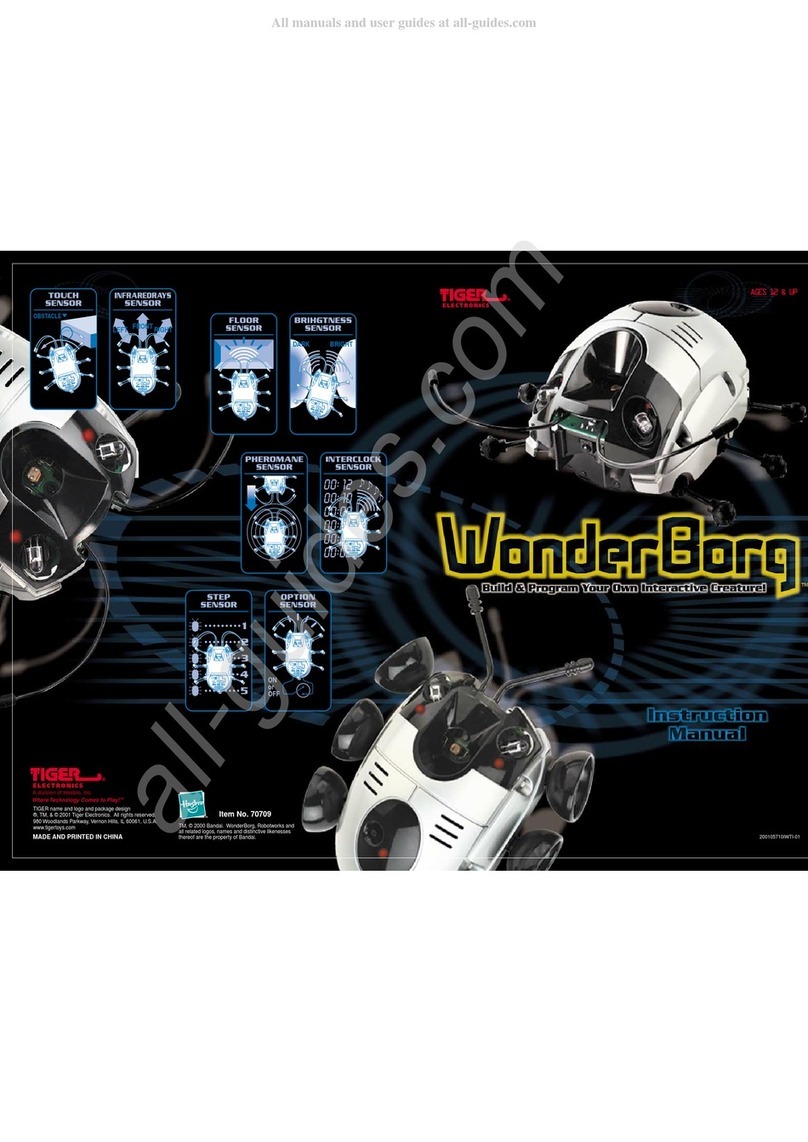
Tiger Electronics
Tiger Electronics WonderBorg instruction manual
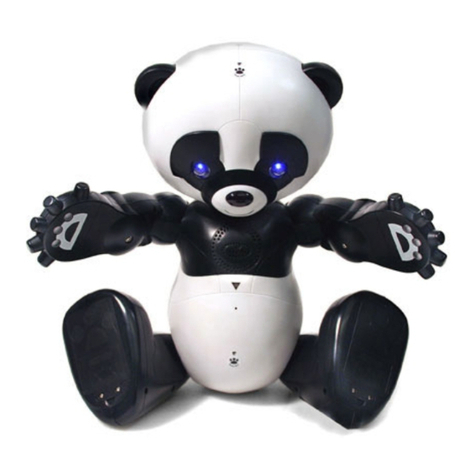
WowWee
WowWee ROBOPANDA 8068 user manual
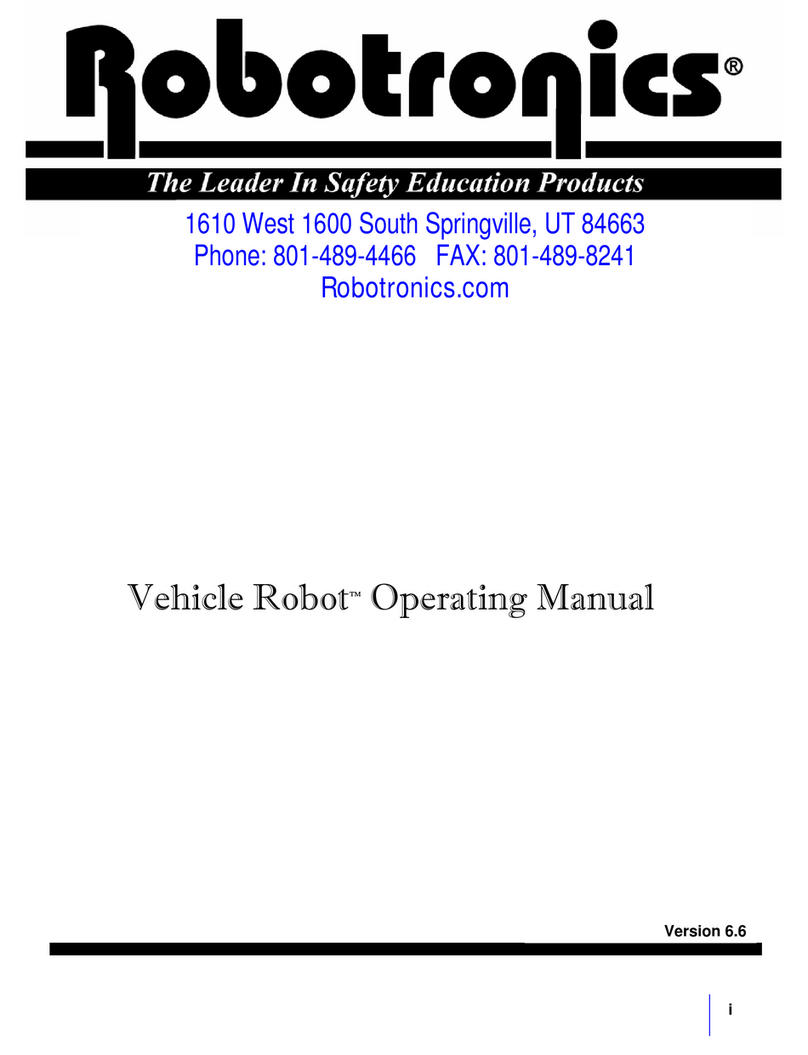
Robotronics
Robotronics Vehicle Robot operating manual
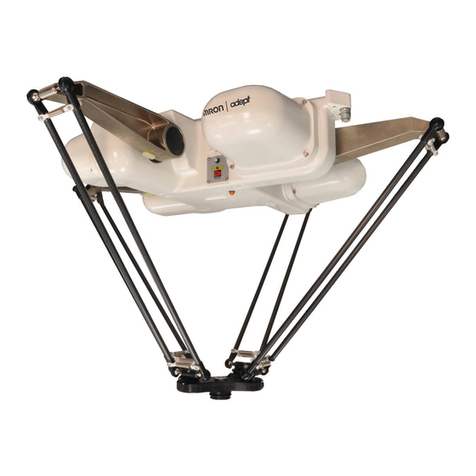
Omron
Omron Quattro 650H Quick setup guide
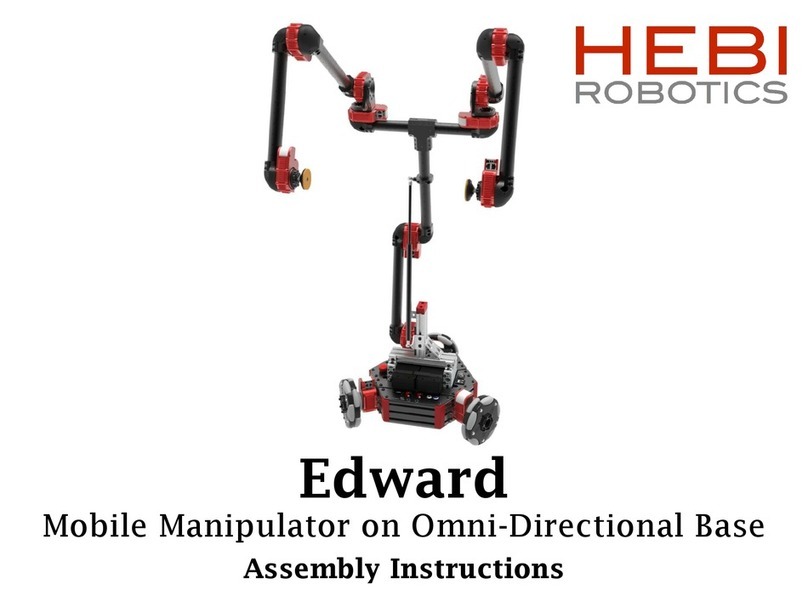
HEBI Robotics
HEBI Robotics Edward Assembly instructions