DOMAILLE ENGINEERING APM-HDC-5320 Series User manual

APM-HDC-5320
Series
User’s Guide

Table of Contents
APM-HDC
5320 Series
Fiber Optic Polishing Machine
User’s Guide
Welcome ................................................................................2
Overview.................................................................................2
Getting Started.......................................................................3
Unpacking & Setup ...................................................................3
Precautions..............................................................................5
Parts and Functions ...............................................................6
Machine Diagram...................................................................6&8
Machine Setup ......................................................................10
Initial Setup...........................................................................10
System Conguration ..............................................................11
Polisher Load Cell Calibration ...............................................12
Process Variables: Setting & Copy/Backup Procedures..............14
User Rights & Settings.........................................................17
Maintenance Schedule.........................................................20
Motor Speed Calibration.......................................................24
Process Setup ........................................................................24
Inter-Machine Process Transfer.................................................28
Machine Operation ...............................................................30
Polishing Fixture Installation ....................................................30
Polishing Pad and Film Placement .............................................31
Power Up...............................................................................32
Polishing Process Selection and Polishing Procedure.....................33
Predened Rework Start Step...................................................34
Step Pause Button...............................................................34
Step Reset Button................................................................34
Select Step.........................................................................35
Cancel Polishing Process.......................................................35
Machine Shut Down ............................................................35
Machine Maintenance .........................................................35
Daily .....................................................................................35
Monthly.................................................................................36
Machine Alarms....................................................................38
Service & Support ...............................................................40
Technical Specications ...........................................................40
CE Notice...............................................................................41
Company Information .........................................................42
Limited Warranty..................................................................43

1
Printing History
Edition 4, January 2021
© Copyright 2021 by Domaille Engineering, LLC

Welcome
Overview
Congratulations on selecting the APM-HDC-5320, the premier ber
optic connector polishing machine.
This User’s Guide will assist you in the setup, operation, and
maintenance of the APM-HDC-5320 machine to maximize the
use and life of this equipment.
The APM-HDC-5320 is designed to address the need to efciently
polish a large volume of connectors while maintaining a consistent
high level of quality.
The APM-HDC-5320 allows you to create processes through an
easy-to-use touch-screen panel. The panel displays programmed
settings for speed, time, pressure, polishing lm used, lubricant
type and pad durometer. Additional setting options include:
language selection, ramp-up speed, ramp-up pressure, delay pres-
sure apply, speed ramp down, pressure ramp down, polishing
xture weight, maintenance intervals and polishing lm counters.
Operators need minimal training to follow the touch-screen prompts
of your programmed processes.
The number of processes that can be dened and stored within the
APM-HDC-5320 machine is only limited by the amount of internal
memory. Therefore hundreds of processes can be stored on a single
machine. Additionally, the APM-HDC-5320 provides you with total
exibility in the number of steps you dene within each of your pol-
ishing processes.
The APM-HDC-5320 provides the capability to store your processes
in machine memory as well as on a USB storage device. A USB
storage device can be used to back up your dened processes and
to copy processes from one machine to another. This not only saves
process setup time for each machine, but also ensures consistent
process settings.
2

Getting Started
Unpacking & Setup
NOTE: Due to the weight of the APM-HDC-5320, it is recommended
that two people lift it from the shipping case.
1. Remove all loose components from the machine area in the ship-
ping case.
2. Remove the plastic bag from around the Overarm to provide
access to the Overarm.
3. Use the Overarm as a lifting handle by grabbing as close to the
Overarm pivot point as possible.
a. Lift the machine straight up while rmly holding the case
down on the outside edges. If the machine is lifted at an
angle, it will cause binding in the case.
b. Gently place the machine on a suitable, stable
work surface.
4. Remove remaining plastic wrapping from machine and
touchscreen panel.
5. Inspect the machine for any damage that may have occurred
in shipping.
6. Remove the BLUE Koby Air Filter from the shipping case.
Remove plastic cap from air supply tting on the back of the
machine. Connect plastic airline provided by pushing line rmly
into tting. Connect other end of airline to BLACK capped end of
Koby Air Filter.
7. Using the proper air supply ttings, connect the RED capped end
of Koby Air Filter into your compressed air system. The inlet of
the Koby Air Filter is ¼” NPT pipe thread. The compressed air
requirements are: 90-120 pounds per square inch (6.2- 8.5 bar),
clean, dry, oil-free air.
8. Connect Drain Hose provided to Drain Hose Fitting on back of
machine. Route Drain Hose to a collection container below
the bench.
9. In order to raise and lower the Overarm, you must release
the Overarm locking mechanism. Press the Black Overarm
Quick-Release button located at the front of the Overarm and
lift up.
3

Releasing the Quick-Release button will allow the Overarm to lock
in one of the three (3) xed positions.
10. Remove the Drip Tray, Drip Tray Bracket and Splash Guard. The
Drip Tray can be attached on either the right or left side of the
machine. This diagram illustrates how the Drip Tray Bracket
slides onto the back right or left corner of the machine (when
facing machine). Place the bracket snug against the back corner
and rmly tighten the bracket screw. Slide the Drip Tray rod into
the bracket hole. Attach Splash Guard at desired position for the
xture with the Overarm in the up position.
4

Precautions
For safe, effective operation of the APM-HDC-5320 Polishing
Machine, please observe the following:
• Keep hands, jewelry, hair and loose clothing away from the
rotating Platen while the machine is in operation.
• Keep all surfaces of the machine clean at all times. Conne water
and slurry to Platen area.
• Do not attempt to repair or service any components inside the
APM-HDC-5320 machine. Contact Domaille Engineering,
LLC if service is required.
• Use only the stylus provided or ngers when touching screen
panel. Do not use hard objects.
WARNING: Do not use an air hoses on or around the
Platen. This forces water and contaminants into the wear
surfaces and mechanical drive unit, potentially causing
machine failure.
Damage caused by air hose use is not covered under
warranty.
5

Parts and Functions
Machine Diagram
Overarm Sensor
Pivoting Overarm
Standard 5” Platen
with 8” Option
7” PC-Based, Full-Color
Capacitive Touchscreen
USB Slot
Operator Step-by-Step
Prompts
Force, Speed
and Time Displays
Automatic Pressure
Adjustment by
Connector Quantity
Pneumatically Controlled
Polishing Pressure
6
9
8
1
2
3
4
5
7
6

Overarm Sensor
Operator Step-by-Step
Prompts
7” PC-Based, Full-Color
Capacitive Touchscreen
Force, Speed and
Time Displays
Pneumatically Controlled
Polishing Pressure
Pivoting Overarm
Automatic Pressure
Adjustment by
Connector Quality
Standard 5” Platen
with 8” Option
USB Slot
allows cycle start when arm is in the correct position
provides easy cleaning of xtures between steps and
quick change of xtures
accounts for a varying number of connectors inserted
in the polishing xture
provides exibility in xture capacity and polishing
lm size
for lm, pad type, lubricant, and operator instructions
programmable interface for dening and storing
unlimited processes and for easy-to-use, error-free
operation
for feedback of process step-specic settings
provides consistent polishing force
used for machine-to-machine process replication
process back up, videos, and bar code scanning
1
2
3
4
5
6
7
8
9
7

Air Supply Fitting
Parts and Functions
Machine Diagram
Power Switch
Power Cable
1
3
5
2
Fan Filter
Drain Hose Fitting
8
4

Power Switch
Drain Hose Fitting
Power Cable
Fan Filter
Air Supply Fitting
machine on or off
main source of power to machine
collects large particulates such as dust from production.
Please see “Machine Maintenance” for monthly cleaning
requirement
provides path for excess liquid
provides connection between polishing machine and
facility air supply
1
2
3
4
5
9

Machine Setup
Initial Setup
Before operating the APM-HDC-5320, you must congure the system
and dene your processes.
Plug the power cord into the back of the machine and into a
properly grounded outlet- 100-240 VAC, 50/60Hz. If your power
cord is equipped with a GFCI, you MUST push the reset button on
the plug to supply power to the machine.
1. Turn on power switch located at the back of the machine.
2. Lift screen cover (Note: screen cover should be down when
machine is operating).
3. The touchscreen will default to the “Home” tab screen. If the RED
emergency screen is displayed, reset by turning “Emergency
Stop” button CLOCKWISE.
4. Press the language button to select desired language.
5. Press “Machine Start” button.
6. After pressing “Machine Start” button, the user can select a
process as showin in Fig. 1.
10

System Conguration
System Conguration allows you to set the following (Fig. 2):
1. Loadcell Calibration
2. Process Variable Settings
3. User Rights and Settings
4. Maintenance Schedule
5. Motor Speed Calibration
11
Fig. 1
Fig. 2

Two (2) interface methods are available for entering system
conguration data, (1) the touchscreen keypad, or (2) a Windows
Microsoft Compatible USB keyboard. If using a keyboard, plug the
USB connection into the port on the left side of the machine AFTER
the machine has powered up. Use the drop down menu under
“Conguration” to select the desired conguration screen.
Polisher Load Cell Calibration
The APM-HDC-5320 Polisher has been calibrated at Domaille
Fiber Optic Equipment prior to shipment. Recalibration is not typically
necessary; however machine calibration should be checked on a bi-
weekly schedule. Recalibration and loadcell verication of the ma-
chine can be preformed two ways:
1. Using the automatic Domaille EZ-CAL USB Load Cell - PN
MK15300 (recommended).
2. Using an external loadcell of the user’s choice.
When using the automatic EZ-CAL USB Load Cell, follow these steps:
1. Remove the polishing xture from the Overarm and the rubber
pad from the top of the Platen.
2. Clean top of Platen to remove any water, grit or dirt to ensure that
the EZ-CAL USB Load Cell will be set
on a clean, dry surface.
3. Place the EZ-CAL USB Load Cell on
the Platen and center it under the
Overarm plunger.
4. Plug the USB connector of the
EZ-CAL Load Cell into
the side USB port of the
polishing machine.
5. Allow EZ-CAL Load Cell 15 minutes of warm up before starting
calibration.
6. On the touchscreen, select the “System Cong.” tab, then select
“Load Cell Calibration” in the conguration dropdown box using
the DOWN arrow as necessary (Fig. 3).
7. Select the “Auto Cal” button to begin the automatic calibration
process or if the user is only verifying the calibration press the
“Verify LC” button.
12

8. If calibrating the machine with the “Auto Cal”, the machine will
automatically run thru a number of steps and calibrate the
machine on its own. This calibration can take anywhere from
30-60 seconds and when it is nished it will ask for the user to
select “Accept” or “Cancel”. Select the “Accept” button to nish
the calibration process or “Cancel” to abort and run it again.
When using an external master load cell follow these steps to
calibrate the machine.
1. Remove the polishing xture from the Overarm and the rubber
pad from the top of the Platen.
2. Clean the top of the Platen to remove any water, grit, or dirt from
the surface to ensure that the external master load cell will be set
on a clean, dry surface.
3. Place the external master load cell on
the Platen and center it under the
Overarm plunger.
4. Allow external master load cell 15
minute of warm up before starting calibration.
5. On the touchscreen, select the “System Cong.” tab, then select
“Load Cell Calibration” in the conguration drop down box using
the DOWN arrow as necessary (Fig. 3).
6. Select the “Manual Cal” button to begin the calibration process.
7. Once step one of the manual calibration process starts, raise the
Overarm just enough for the plunger to clear the master load cell
and select the “Tare” button on the touchscreen checking to see if
the master loadccell reads 0 lbs. while doing this.
8. Once step two activates, lower the
Overarm back down onto the
master load cell and lock it into
place by releasing the black arm
button. When ready select the
“Apply Pressure” button on the touchscreen until the master load
cell reading matches the 20 lbs. of polishing machine load cell.
9. At this point, calibration is complete. Select the “Span” button on
the touchscreen to SAVE the calibration to the machine.
NOTE 1: If you wish to cancel during the middle of calibration a
“Cancel” button is displayed so you can exit the process
without changing any settings.
13

NOTE 2: A “Default Calibration” button is available so the user can
restore the machine calibration settings back to the factory
calibration settings at anytime.
NOTE 3: When unplugging the EZ-CAL USB load cell from the
polishing machine, rst transition to the HOME tab so the load
cell is not taking readings. When the machine is on the HOME
tab the load cell readings are halted making it safe to unplug
the device.
Process Variables: Setting & Copying/Backup Procedures
The APM-HDC-5320 allows you to dene valid variables that can be
used in the denition of your polishing processes. These variables in-
clude (1) a list of polishing lms, (2) a list of types of polishing pads,
(3) a list of lubricants that can be dened for polishing processes,
and (4) a maximum quantity of connectors that can be polished at
one time.
The maximum quantity of connectors (Max. Quantity) setting is
displayed, but not modiable at this time.
To MODIFY process variables, rst select the “System Cong.” tab,
then select “Process Variable Settings” in the “Conguration” box,
using the DOWN arrow as necessary.
Maximum Quantity Setting:
This variable has been preset to 72 and is not modiable at this
time.
14
Fig. 3

15
Film Settings:
1. Select “Film” in the “Selecting Setting” box, using the DOWN
arrow as necessary (Fig. 4).
2. Select the “New” button to access the keypad, and add a new lm
type.
3. Type in a lm name for your polishing process. The lm name
can be up to 16 characters in length.
4. Select “OK”.
5. Repeat the above for all lms used in all polishing processes.
To DELETE a lm name, highlight the name, then select the “Delete”
button.
Pad Settings:
1. Select “Pad” in the “Select Setting” box, using the DOWN arrow
as necessary.
2. Select the “New” button to access the keypad, and add a new pad
type.
3. Type in a pad name for use in your polishing process. The pad
name can be up to 16 characters in length.
4. Select “OK”.
5. Repeat the above for all pad types used in all polishing processes.
To DELETE a pad name, highlight the name, then select the “Delete”
button.
Lubricant Settings:
1. Select “Lubricant”, using the down arrow in the “Select Setting”
box as necessary.
2. Select the “New” button to access the keypad, and add a new
lubricant type.
3. Type in a lubricant name for use in your polishing process. The
lubricant name can be up to 16 characters in length.
4. Select “OK.”
5. Repeat the above for all lubricant types used in all polishing
processes.

Fig. 4
To DELETE a lubricant name, highlight the name, then select the
“Delete” button.
Transfering Process Variables
Once your variable settings have been established, they can be
copied to a USB memory stick. This allows “Process Variable Data”
to be transferred to other APM-HDC-5320 machines as well as
providing backup and retrieval capability.
A USB memory stick has been included with the shipment of your
APM-HDC-5320.
To SAVE process variable data to a USB:
1. Insert USB storage device into USB slot on the lower left side of
the machine.
2. Select “System Cong.” tab, then select “Process Variable
Settings”.
3. Copy settings by selecting “Machine Memory to Memory Stick”.
You will be prompted, if “Process Variable Data” already exists on
the USB memory stick.
NOTE: If the USB memory stick already contains variable data,
copying the “Machine Memory to Memory Stick” will overwrite
the variable settings on the stick.
To load “Process Variable Data” from an already existing le on a
USB storage device, use the following procedure:
1. Insert USB storage devicde into USB slot on lower left side of the
machine.
16

To MODIFY “User Rights & Settings”, touch the “System Cong.”
tab, then select “User Rights & Settings” in the “Conguration” box,
using the DOWN arrow as necessary (Fig. 5).
Password Setting
A one (1) to four (4) digit password can be used to password protect
the “Process Conguration”, “Process Transfer” and “System
Conguration” tabs. One password can be activated per machine.
2. Select “System Cong.” tab, then select “Process Variable
Settings”.
3. Transfer settings by selecting “Memory Stick to Machine Memory”
so that all your USB storage settings are contained in the machine
memory.
User Rights & Settings
The “User Rights & Settings” screen (Fig. 5) allows you to dene ten
(10) machine specic parameters, including:
(1) a password
(2) enablement of connector quantity adjustment by the operator
(3) enablement of process step selection by the operator
(4) enablement of Micro-G® polishing accessory
(5) enablement of video playback
(6) enablement of auto calibration
(7) enablement of DE DataLink® sysetm
(8) enable lm count
(9) display of pressure in pounds or kilograms
(10) zero speed
Fig. 5
17

When the “Password” box is unchecked, no password protection is in
effect. To activate “Password Protection” and reset the password:
1. Touch “Password” box until large checkmark appears. Current
password will be in the box to the right.
2. Touch the box with current password in it to access the keypad.
3. Type in a one (1) to four (4) character password.
4. Select “OK”.
To DISABLE “Password Protection” touch “Password” box to uncheck
the box.
Enable Quantity Adjustment
Checking the “Enable Qty Adj” box allows the machine operator to
change the quantity value on the “Production” tab screen. When this
value changes, the APM-HDC-5320 adjusts the pressure in
proportion to the original process pressure value to account for the
change in the number of connectors being polished. The polishing
xture weight is also gured into the equation.
For example, if the original process pressure is set at 1.00 lbs. with
the default number of connectors for that process set at 12 with a
polishing xture weight of 0 lbs., and the operator only loads 8
connectors into the polishing xture and sets the quantity value on
the “Production” tab screen to 8, the pressure will automatically be
adjusted to 0.67lbs. (0 + 1/12 * 8 = 0.67 lbs.).
Once xture weight is added, the quantity adjust will compensate
but xture weight will remain as part of the overall compensation as
follows:
xtureweight+totalpressure
Pressureperconnector=
connector quantity
Thus, adjusting quantity of connectors will maintain the same
pressure per connector.
This pressure adjustment due to the change in the quantity value
is maintained for one complete run of the process and then returns
back to the original process denition setting. The change in quantity
and Pressure is noted by the YELLOW highlight of these values on
the “Production” tab screen.
18
Table of contents
Other DOMAILLE ENGINEERING Sander manuals
Popular Sander manuals by other brands
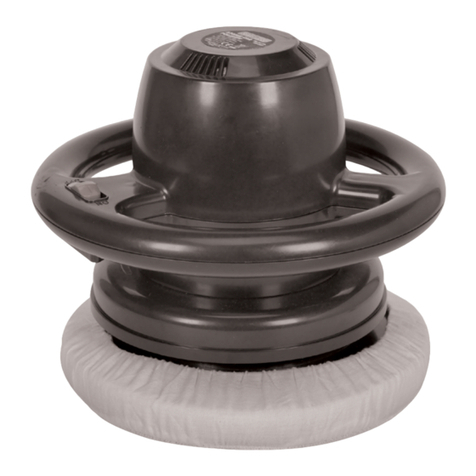
Sealey
Sealey ER230P.V2 instructions
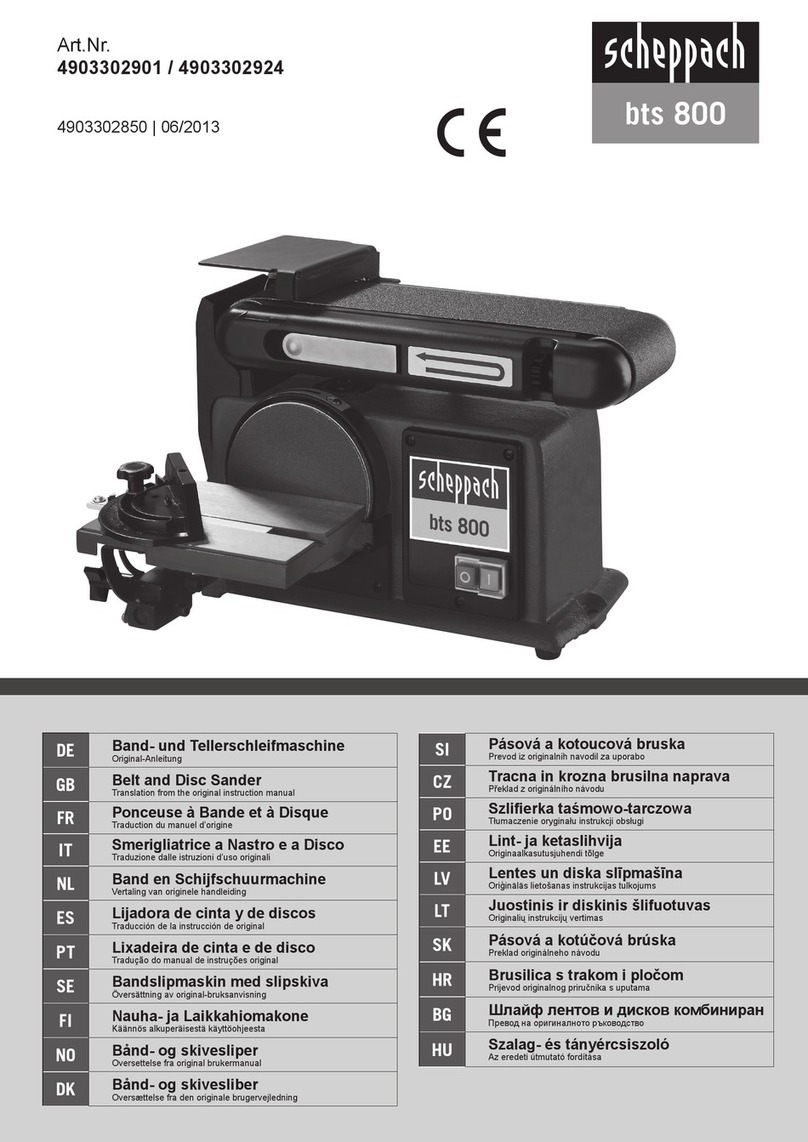
Scheppach
Scheppach 4903302924 Translation from the original instruction manual
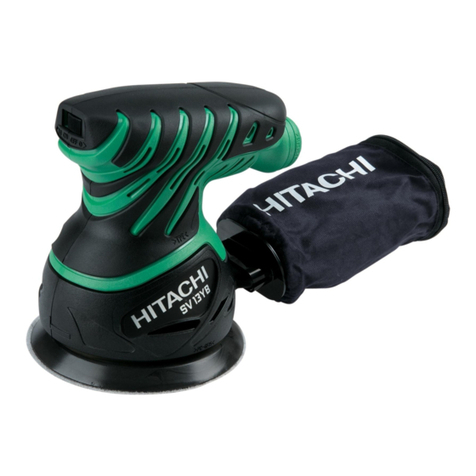
Hitachi
Hitachi SV13YA - 5" Random Orbit Finishing Sander Safety and instruction manual
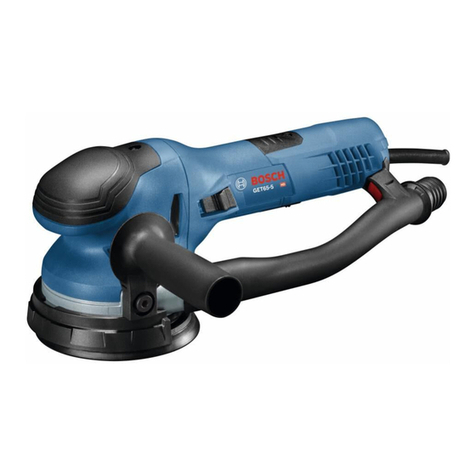
Bosch
Bosch GET65-5 Operating/safety instructions
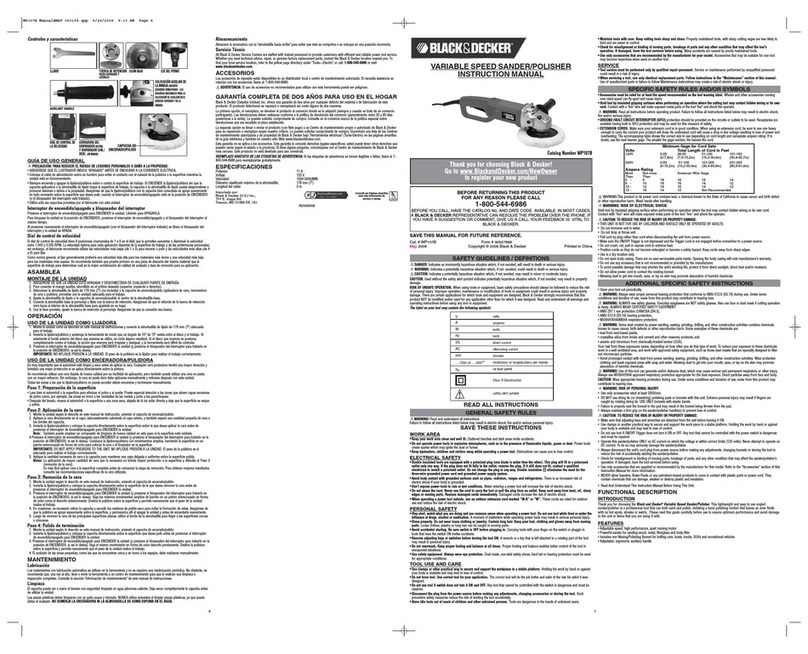
Black & Decker
Black & Decker WP107B instruction manual

Clarke
Clarke C2K 13 Operator's manual