Donatas Design Arrow V.5 User manual

Assembly manual
Thank you for buying aeromusical plane Arrow V.5 from Donatas Design!
Arrow V.5 evolved from famous 4D trainer with variable pitch propeller placed inside the fuselage.
This plane is the best choice for those who want to learn 3D or 4D flying.
This plane kit is milled in order to save some plane’s weight (about 9 grams). This is very important
factor while competing in F3P competitions.
I recommend to use 18,5g AXI2203/RACE motor and 2s light lypo battery for Arrow V.5 if you plan
to fly indoor. For outdoor flights AXI 2204/54 with 3s light lypo are recommended.
NOTE! Additional reinforcement to the airframe will be needed if you decide to use more
powerfull motor.
This kit includes all items necessary to finish the kit: depron parts, carbon rods, flat carbon, hi
quality fiberglass hardware set, motor mount, Z ends for servo attachment, velcro tape for battery
fixation and pull-pull line.
Equipment selection
Motor: AXI2203/Race (for indoor flying, weight - 18,5g)
AXI2203/40 (for indoor VPP flying, when model is extremely light)
AXI 2204/54 (for outdoor flying in light wind, weight - 25,9g)
AXI 2204/54 EVP (VPP flying, motor weight - 25,9g)
ESC: Competition option Castle Creation Phoenix 10a, budget version CC Thunderbird 9.
Battery: Desire Power V8, 35C 300mah, 2S/7,4V, weight 16g. (Light indoor)
Desire Power V8, 35C 380mah, 2S/7,4V, weight 22g. (Powerful indoor)
Desire Power V8, 35C 380mah, 3S/11.1V, weight 30g. (Powerful outdoor or VPP)
Servos: Dig. JR 290G single servo for elevator and rudder, 2 servos can be used on ailerons.
Dig. JR 188 single servo for elevator or rudder, 2 servos can be used on ailerons.
Hitec 65hb single servo on ailerons and rudder.
Radio: At least 4 channel programmable radio with minimum programming of exponential. I would
recommend more advanced radio like JR 9 or JR11 that have travel adjustment, dual rates, trim
steps, digital trimmers, mixes, and other useful functions. These will help you to setup your plane
faster and to seek for the best results.
Receiver : As light as possible! For e.g., I use and have no complaints about:
Spektrum 2,4ghz Ar6300 2g.
Duplex 2.4ghz R6Gindoor 3.6g
1

2
Here you can see fiberglass hardware set. It was done in order to achieve the best control of
plane’s moving surfaces. Now you can use long servo arms and servo horns. Moreover, you will
be able to have less pressure on control rod, use full potential of your servos and not to lose
resolution. In addition to this, few small pieces will reinforce certain areas that face many
different forces (hard landings, hi-G manoeuvres, etc.).

You will need just a few basic tools and materials to
finish your Arrow V.5:
Sharp hobby knife, file, 1.5mm drill, piece of
sanding paper, scissors, screwdriver, solder,
and Donatas Design bevelling tool.Mercury
Adhesives foam friendly CA glues (M100F),
Mercury Adhesives Accelerator MH 16 “3M
Blenderm medical tape” (further - Blenderm
tape) for control surface attachment, kevlar
thread. Building:
Split fuselage by using sharp knife. Do not throw out depron "trash" (servo holes’ cuts). For
example, if you decide to use two aileron servos you can glue back these small pieces inside the
fuselage and avoid ‘’ugly’’ holes in this way.
3
Required tools and adhesives:
Make sure you remove all steps
that were connecting fuselage.
Repeat this procedure for all parts.
If you want to build lighter plane, here is one
suggestion: ‘’shave“ ends of 0,5mm flat carbon. You will
save some weight and will have very useful thin carbon.
Next step - reinforcement of some critical
parts. Here you can see how aileron
compensator is being reinforced with thin
carbon.
Cut aileron edge with Donatas Design
bevelling tool. This will guarantee easy
deflection down (when it is attached to the
wing), and great clean look .

4
Glue 0.5 mm carbon on the back and leading edges of the wings. Carbon length required for back
edge - 70 cm, for front - 83 cm. The very end of carbon is fixed with small piece of Blenderm tape.
Optional reinforcement: Glue thin carbon (you might use the one that remained after ‘’shaving“ the
main carbon parts) like it is shown in the pictures. This gives very good strength for elevator and
prevents stabilizer part from cracking.
When flat carbon is glued to the wing and aileron edges are bevelled, it is time to attach these two
parts. I highly recommend using Blenderml tape for this step. It sticks extremely well to depron
surface. Moreover, the tape is not shiny so it does not stand out or change colour scheme of the
plane.
Black circles in the picture on the right mark certain places where small pieces of Blenderm tape
should be placed. This reinforcement prevents ailerons from moving away from the wings after
many hours of flying.

5
There are few ways of how you can attach elevator to stabilizer. The easy one is to cut control
surface in 45 degree angle with Donatas Design bevelling tool and to use Blenderm tape to attach
elevator to stabilizer (in the same way as ailerons are attached to the wings). Such method is good
for those who use solid pull-push system. On the other hand, if you use pull-pull cables, the below
method is superior because it will keep the tension of the pull-pull cables from displacing the
hinge line.
Some of us use TVC (Trust Vector Control) system. It puts a lot of forces on motor mount and front
part of the plane. Here is one small trick how you can deal with these problems: cut off about 3 cm
of plane’s nose and glue in thin carbon piece. This will help you to make plane’s nose much
stronger and to reduce noise caused by high G manoeuvres.
So I use so called ”8 method. As you see in the picture,
- ing
-
” elevator is connected with stabilizer in old
fashioned way. This one was used when people did not have high quality hinges. To use the “8”
hinge, firstly use a sanding bar to round the leading edge of the elevator and the trailing edge of the
stabilizer. Secondly, prepare about 12 pieces of Blenderm tape as follows: take 2 pieces (about 1 x
1.5 cm) and tape the sticky sides (across the 1 cm length) together to form an overlap of
approximately 0.5 cm. The result of this should be: 0,5 cm of „neutral“ tape from both sides and 2
cm of sticky tape. Take prepared tape and glue one of the sticky sides on the top of stabilizer. The
other sticky side of the tape should be glued on the bottom of elevator. Repeat the same steps with
the rest of tape’s pieces. Every second piece should be glued upside-down. This way of
connection is the best for pull pull cables. It allows deflect surface up to 180 degree with no
effort. Moreover, „8" method will help to withstand pull pull cable tension forces and will
guarantee elevator’s stay in place for a long long time.

6
The time for the most important step of Arrow V.5 building has come. You should place tail section
to the main wing precisely as shown in the picture. Use some heavy objects to press separate
parts on the flat table. Measure distance from each wing tip to stabilizer very carefully. It has to be
the same on the both sides. You should also make sure that nose’s, wings’, and tails’ tab line is
straight.
The next step in this stage of building - attachment of the front of the plane. Glue it as it is shown in
picture on the left. Make sure cut out for fuselage tabs are aligned with the cut outs in the wing and
tail.
You can see one more additional reinforcement for top part of fuselage in the picture on the right.
Using sharp knife make a careful cut as it is shown in the picture. The Best way is to stick to the
outline of the cockpit, this way carbon reinforcement will not stand out.
Every shockflyer has its’ weak points, one of these - the place where wings are attached to the
fuselage. My advice is to reinforce this area with fiberglass cloth. Cut a small piece of fiberglass
cloth, put few drops of foam friendly CA glue, and stick it as it is shown in the picture. Make sure
that glue spread evenly, and all material is wet. If it happens so that you put some extra amount of
CA, clean it with paper towel. Remember that any extra weight is unwanted. And too much of CA
glue is one of the areas where you can collect weight very quickly. You may check this by weighting
your CA bottle before and after plane building (the difference you get will be the weight you put on
your plane in the form of glues).

7
Glue a flat thin carbon piece to reinforce the
top of the fuselage; this reduce the likelihood
of the depron bending if an inverted landing
occur.
Cut slots for the “V” shape carbon reinforcement. This is
necessary step to ensure that both sides of the elevator
will deflect exactly the same for precise control.
Glue the bottom part of fuselage inverted on
the flat table. Put some heavy objects on tail
and wings.This will help to keep them straight.
It is very important for precise flying plane.
Now lets add 1 mm carbon rods to reinforce
the fuselage structure. Sand the tips of each
carbon rod before gluing to increase
adhesion. To aid accurate construction, use
a pair of square items like CD covers or
credit/phone cards that have 90 degree angle.
Place these objects (plastic cards are my
favorite) from both sides to keep the depron
bottom perpendicular to the horizontal fuse.
The last picture shows all carbon rod
reinforcements for the tail and back of the
fuselage. This type of reinforcement is both
50% lighter than old fashion depron box and
more torsionally rigid, keeping the wing and
stab aligned during rolls.
Use pieces of scrap depron as shown (red arrow) to strengthen the joint of the trailing
edge of the wing with the fuselage and the carbon rod bracing.

8
Now we need to prepare the main wing support. Here you can see reinforcement piece made
from 0.5 mm fiberglass. You will find a similar part in your Arrow V.5 kit. Glue it at the centre of
the wing chord on the bottom of the fuselage.
Mark 23 cm distance (measuring from fuselage towards wingtip) on the leading and trailing
edges of the wing (both sides). These are attachment points for the 1.5 mm carbon wing
support rods (26 cm long each). Use plastic cards to make sure the fuselage remains at a 90
degree angle to the wing. DO NOT GLUE 4 carbon rods in the centre yet.
Glue four carbon rods to the main wing. Using needle and Kevlar thread make a couple
loops to tie together the carbon rod and flat carbon (you will have to remove the plane from
the table for this step). Couple drops of CA glues on top will guarantee an amazing strenght.
Wings will remain in the same position no matter how hard you will fly your plane.

Now, when carbon rods are glued to the wing and Kevlar thread is in place, return the plane to
the flat table. Use some weights to press it down to table. Now double check vertical fuselage
position and glue the four carbon rods to the fuselage.
Now you can glue two support SFG's from depron to the wing support carbon rods.
This is optional aileron reinforcement using 1 mm carbon rod. This upgrade reduces
aileron flex and makes roll control more precise and is highly recommended for Arrow V.5.9

Carbon structure from different angle.
When all updates are installed, make sure elevator is flat and deflect easy to both sides.
It is now a good time to glue flat carbon pieces into the “V shape slots we cut earlier. After gluing
the flat carbon inside the epron slots, glue fiberglass square plates on the top and bottom of the
elevator as shown in picture. Similar to the optional aileron reinforcement, 0.7mm carbon rod
(not included in kit) can be used to stiffen the elevators on Arrow .
“
d
the
V.5
When all updates are installed, make sure aileron is flat and deflect easy to both sides. 10

11
Landing gear should be installed before starting works
with the top of the fuselage. Start by reinforcing the
bottom of the fuselage with a 6 cm piece of thin carbon
and fiberglass cloth. Landing gear legs are made of 1.5
mm carbon rod and are 24 cm long. Mount the gear legs
as shown in the picture angled slightly forward towards
the motor. This will provide stable standing on the
ground. I also highly recommend tying the gear legs to
the wing leading edge flat carbon, using kevlar thread
and needle, as it was done for the wing support rods.
Now it is time to decide what aileron servo configuration will be used. Arrow V.5 has very
big and powerful ailerons, so strong servos are required. Single servo option is a Hitec
65HB connected to 6 volts (if connected to 2S lipo, it will burn out after ~50 flights). Two
servo option is either JR290Gs or JR188s. JR290s are heavier, but have a very precise
geartrain that will stay tight for hundreds of flights. If smaller weight is your priority - JR
JR188s is the better option. All of these high quality servos are a bit heavy, but can be
lightened, as shown for this Hitec 65HB: screws and bottom case should be removed, and
servo should be reinforced with Blenderm tape. Please keep in mind that such
modifications will likely void manufacturer's warranty.

If you decide to use single servo, install it in
the cut out of the wing, and glue the top of
the fuselage as it is shown.
Cut slots in the ailerons for the aileron horns. Try to keep them as symmetrical as possible. Next
step - neutralize (zero) the trim and sub trim on the aileron channel of your radio, and put an
original servo arm on the aileron servo, as close to the center position as possible. Then glue
provided fiberglass offset servo to the original servo arm making sure it is centered exactly. After
this 100% of servo throw is available for control deflection, giving the best possible resolution and
maximum equal deflection to both sides. Reinforce the joint between the fiberglass arm and the
original arm with a couple wraps of kevlar thread, and then saturate the thread with CA (complete
this step with the arm off of the servo). Glue Z-bends on each carbon rod’s side. Such carbon rod
will connect servo arm with control horns. Z-bend linkages are included in the kit for regular use.
A competition upgrade to improve precision is the use of tiny ball links. I learn this trick from top
USA pilot and builder Devin McGrath. Ball links are not included in the kit. The ones I use are T-
Rex 250 from Horizon Hobby.
Here you can see push rod connected to servo arm. It is ready for final adjustment and attachment
to aileron control horn. This is difficult part because there is no good way to adjust length of push
rod, so you have to measure few times to be sure it will be right size.
I use top hole on servo horn and second (from side) on servo arm. Whether using ball links or Z-
bends, attaching them to the 1.5 mm carbon push rod is done the same way. On one end of the
push rod, overlap the carbon rod and Z-bend (or plastic housing of ball link) and glue together.
Reinforce this joint with several wraps of kevlar thread, and saturate the thread with glue. Now,
using some scrap of depron, make a pair of “clamps” to hold the ailerons centered. Attach the
completed end of the push rod to the servo, and attach another Z-bend (or ball link assembled) to
the control horn. Cut the carbon push rod to length that slightly overlap the Z-bend (or ball link)
attached to the control horn. When satisfied with the length, glue the push rod and Z-bend (or ball
link) together. Remove the push rod, and wrap the remaining joint with kevlar thread.
12
I use top hole on servo horn and second
(from side) on servo arm.

13
If you decide to use two aileron servos, glue foam into the single aileron servo mounting location.
To prepare locations for two servos, cut servo size holes in both SFG's as shown. Having two aileron
servos will require a little more setup work, but in my opinion is worth the time for the advantages
gained. First it will be much easier to place battery where ever you want without interference from
the aileron servo or linkage. The goal is to place all equipment such that the proper center of gravity
is achieved without the battery. In this way, different size/weight batteries can be used at the same
location without affecting the CG. Another advantage of two aileron servos is the ability to use
flaperons. Flaps/elevator mixing can give some unique and crazy manoeuvres. And last but not
least, when two aileron servos are use, the control horns are located in the middle of the aileron,
reducing span wise flex of the ailerons.
Fiberglass cloth is used to reinforce the control horn
mount. Try to use a short carbon rod with precise
attachment of servo to aileron with no play. Picture
shows ball link connected to first version of hardware.
As with the single servo, there are two options for
connections of the carbon pushrod. Z-bends are
supplied in the kit, and can be upgraded to T-Rex 250 ball
links.
NOTE! Hardware in the picture is slightly different from
the one you receive in kit.
Now it's time to prepare elevator servo. Here are some ways you can save weight on JR290G.
Remove the servos screws and bottom of the case, and hold the servo together with Blenderm tape.
You can cut down weight to 7.4g, which is a very good weight for a high performance digital servo.
The 290G has a very precise set of gears that will remain slop free for many flights. I use and
recommend this servo for both elevator and rudder control.
Servo arm prepared for elevator’s pull-pull. A
piece of 50 mm x 1.5 mm carbon rod is glued to
a JR290G servo arm and reinforced with
several wraps of kevlar thread. As with the
aileron servo(s), center the servo arm and
carbon rod with the sub trim and trim to 0 to
ensure equal servo travel to both sides.

14
Here you can see 40 mm x 1.5 mm carbon rod
installed to elevator. It must be exactly same
length on both sides. The provided cable
material will work fine. On the other hand, if you
decide to use ball links instead of Z-bends, I
recommend using ”upgraded” material (I use it
for my competition models). Firstly, 5KG fishing
line is wound around the elevator carbon rod
(and glued), and then with a very small amount of
tension, it is wound and glued to the carbon rod
on the elevator servo. After this is done for both
sides, the fishing line is spiral wound with kevlar
thread (and saturated with CA). This combination
of materials provides extremely good control
without “spring effect” and the tension is
constant regardless weather conditions.
The last surface to complete is the rudder. As with the elevator, I recommend using pull-pull control
system with the same “8" hinging method. Also very important upgrade for rudder strength and its
long life is a piece of thin flat carbon going from counterbalance to middle of rudder.
Using foam friendly CA glues attach fiberglass triangle pieces to rudder as shown in the picture,
keeping them close to the hinge line. Make sure the triangle pieces are glued to the thin flat
reinforcement carbon. Carefully glue a 45 mm x 1.5 mm carbon rod into the triangle pieces, keeping
the length on each side equal.

15
For extra strength, the bottom hinges can be completed using fiberglass tape. I also put soft Velcro
on tail skid area to prevent noise during takeoffs and landings.
The standard motor mounting method uses either the wooden or fiberglass mounts in the kit. Using
your motor as a template, mark hole locations on the mount, and attach the motor with screws.
Check the angle of the nose of the plane before gluing the motor mount. There should be 1-2
degrees of right thrust and no up/down thrust. If you need to change angle after few test flights, I
recommend using shims of thin wood between the motor and motor mount.
After gluing the motor mount to the plane, each “leg” of the motor mount can be additionally
secured with a piece of Blenderm tape.

16
Optional: For more advanced pilots, I recommend trying TVC (Trust Vector Control) system to allow
some crazy manoeuvres. Motor moves side to side with TVC, controlled by the rudder servo. Here
you can see construction of such system. I use ball links connected to motor for smooth and noise
free system. Please keep in mind that the motor wires may break from repeated bending as the
motor moves. For this reason, support the motor wires as shown in the picture so that the much
more flexible wires of the Castle Creations Phoenix 10A ESC will be bending. This method has been
100% reliable for me.
Depron cut out for motor with TVR system. AXI2203/Race motor (view from the front).
Here you can see the
c o m p l e t e d m o t o r
installation. Fiberglass cloth
adds strength to the motor
mounting area to handle the
added stresses from TVC.
The Castle Creation ESC will
be mounted on the right side
of the plane about 5cm from
motor mount. With the motor
deflected fully to the left,
attach the ESC, allowing just
a small amount of slack in the
wires between the ESC and
motor.

17
Here is the alternative way to make motor mount for TVC. The same M2 size ball links are used.
Wrap bolts with thread and CA (gluing to the motor will be easier). I recommend to use good
quality strong CA. My personal choice is Mercury Adhesives M1100G, this is extremely strong CA
Glue 1.5 mm x 60 mm carbon rod as is shown in
the picture. This carbon rod will be used for
connection with rudder servo. Reinforce the
glue joint with kevlar thread as CA alone will not
handle the high forces of TVC.
Picture on the right: 4 pieces of 0.5 mm thick
flat carbon measuring 3 x 70 mm. With a sharp
knife, trim the plastic ball links to 3 mm thick,
making flat spots to which the carbon pieces
are glued (and wrapped with thread). This is the
easiest way to have TVC system on your Arrow
V.5.

18
TVC systems that use one servo to control both the motor and rudder need to have the pull-pull
cables crossed for the rudder to have the motor and rudder moving in the correct directions. You
can see exact measurements for connecting TVC system . In the picture below
Example of motor mount for AXI 2203/40 (for VPP flying).
Square area under motor is made for pitch servo. I
recommend Hitec 5035 for pitch control.
In pictures below you can see two options how to make
landing gear. The first option is the easiest. Use pre-
assembled gear legs and wheels that come in the kit. I prefer
to use depron wheel pants reinforced with fiberglass plates
because they are lighter and look better in the air. If you use
depron wheel pants, don't forget to glue piece (3 mm x 20
mm) of soft Velcro on bottom of wheel pant. This will reduce
noise and make landings a bit softer.

19
Assembly of model is almost done, now its time to place all equipment. This last step is very
important in order to set the correct center of gravity. My competition Arrow V.5 CG is
from the wing leading edge. I place all equipment as close as
possible to the C.G. In the picture above you can see the Jeti Duplex R6G indoor receiver
mounted on the fuselage next to the aileron servo.
23.8 cm
from the motor mount, and 11 cm
Here you can see the right side of fuselage with ESC mounted. NOTE! Wires can flex without
tension, this is very important! It is a small homemade voltage regulator to supply 6 volts to all
servos next to the ESC.
A small depron box is built to tightly fit the battery, which is mounted very closely to the
aileron servo. The battery is held in place with a small piece of Velcro on the right side.
Battery weight is 22.3g; such weight is very good for 35C 380 capacity.

20
After having done our best to build the plane straight and strong, now its time to use a feature of the
radio that will help the plane fly precisely. Many pilots do not pay so much attention to trimming of
the plane. Before each flight in competition I make a short flight to be sure the plane is flying
straight and perfect. Since Arrow V.5 surfaces are really big, it is very important to have very
precise trims with small trim steps. Original radio setup is for 4 steps on each trim click, and this is
too much for precise adjustments. Here you can see how I put trim step to the lowest number
possible. One click of trim is equal to just one step in the servo arm movement.
Final step in your plane assembly is the radio setup. Here you can see my personal settings on my
JR9X radio. Arrow V.5 is very easy and neutral flying airplane; therefore no mixes are necessary. I
just put throttle curve to 90% to limit amp draw, which is necessary since I use a slightly larger
propeller (GWS 8x4.3) than AXI recommends for the AXI2203/Race motor. Final step in your plane
assembly is radio setup. Here you can see my personal setting on my JR9X radio. Arrow V5 is very
easy and neutral flying airplane, therefore no mixes are necessary. I just put thr curve to 90
percents, to limit amp draw. I have to do this because i use slightly to big propeller (GWS 8x4,3)
than AXI recommends for AXI2203/Race motor.
56 degree up.
Aileron deflection. Hi rates, on
my competition Arrow V.5.52 degree down.
Elevator deflection. Hi rates, on
my competition Arrow V.5.
64 degree up. 67 degree down.
Table of contents
Popular Toy manuals by other brands
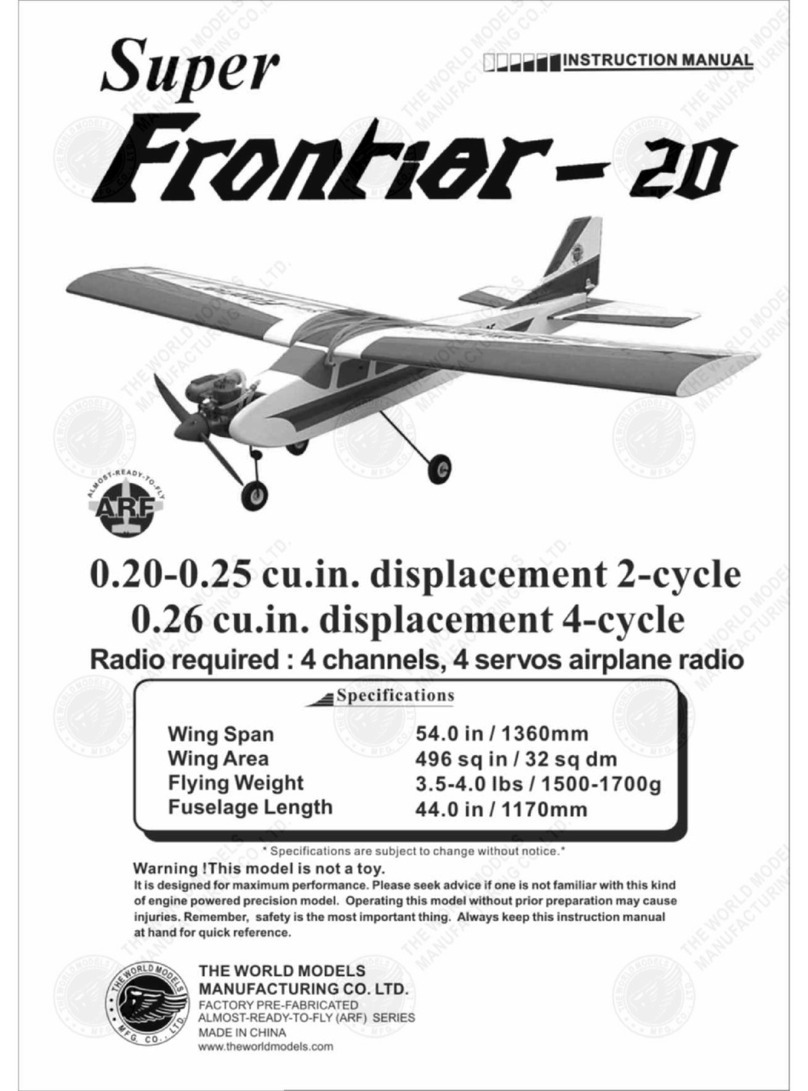
The World Models Manufacturing
The World Models Manufacturing Super Frontier-20 instruction manual
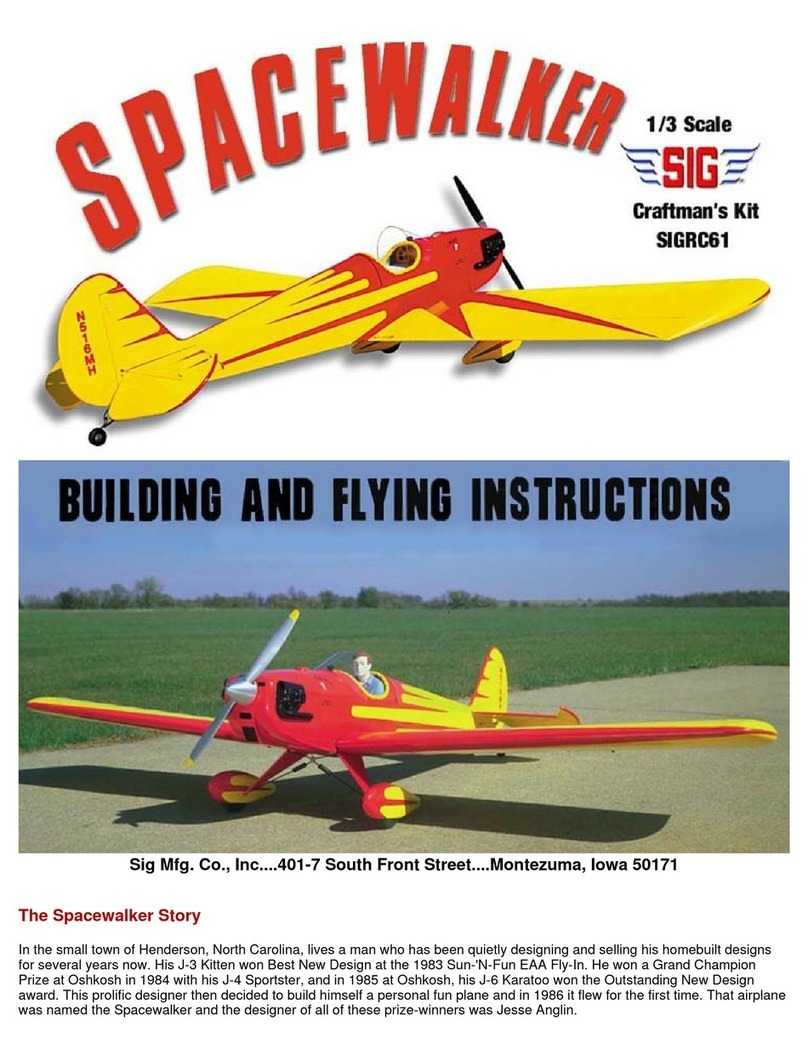
spacewalker
spacewalker SIGRC61 Building and flying instructions
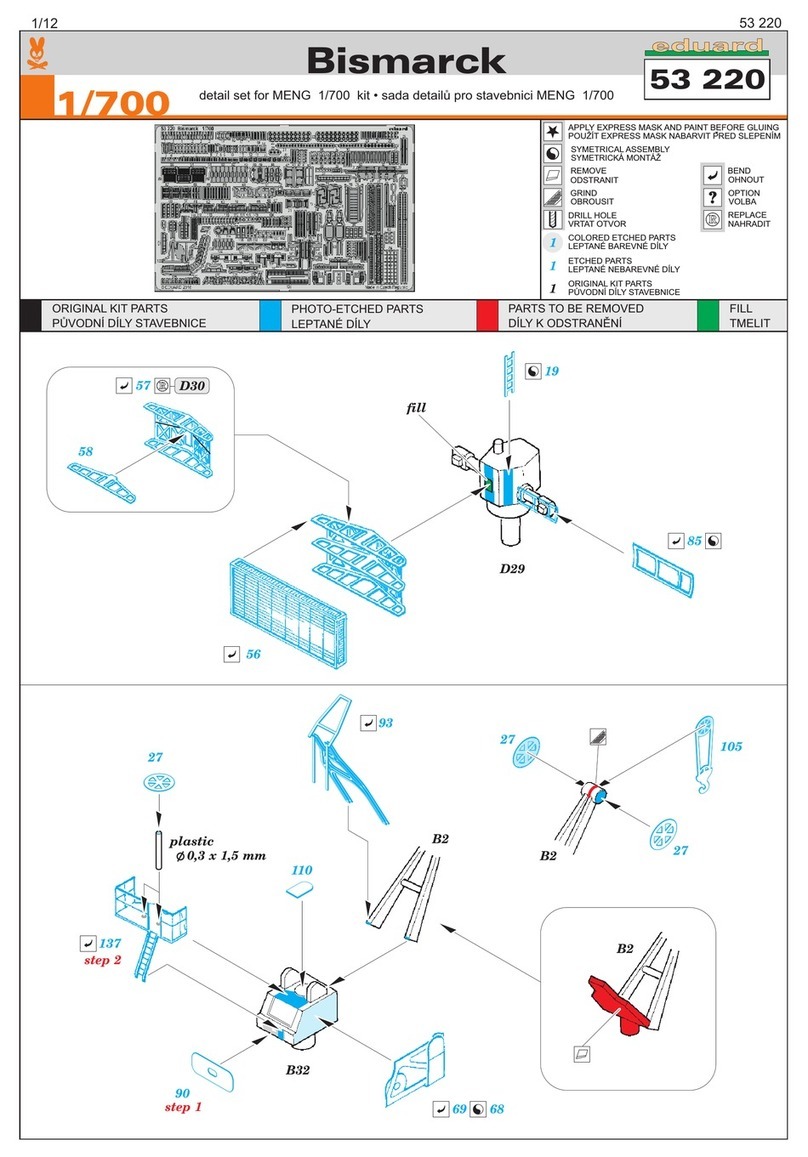
Eduard
Eduard Bismarck manual

Fisher-Price
Fisher-Price Pixter Multi-Media H4651 owner's manual
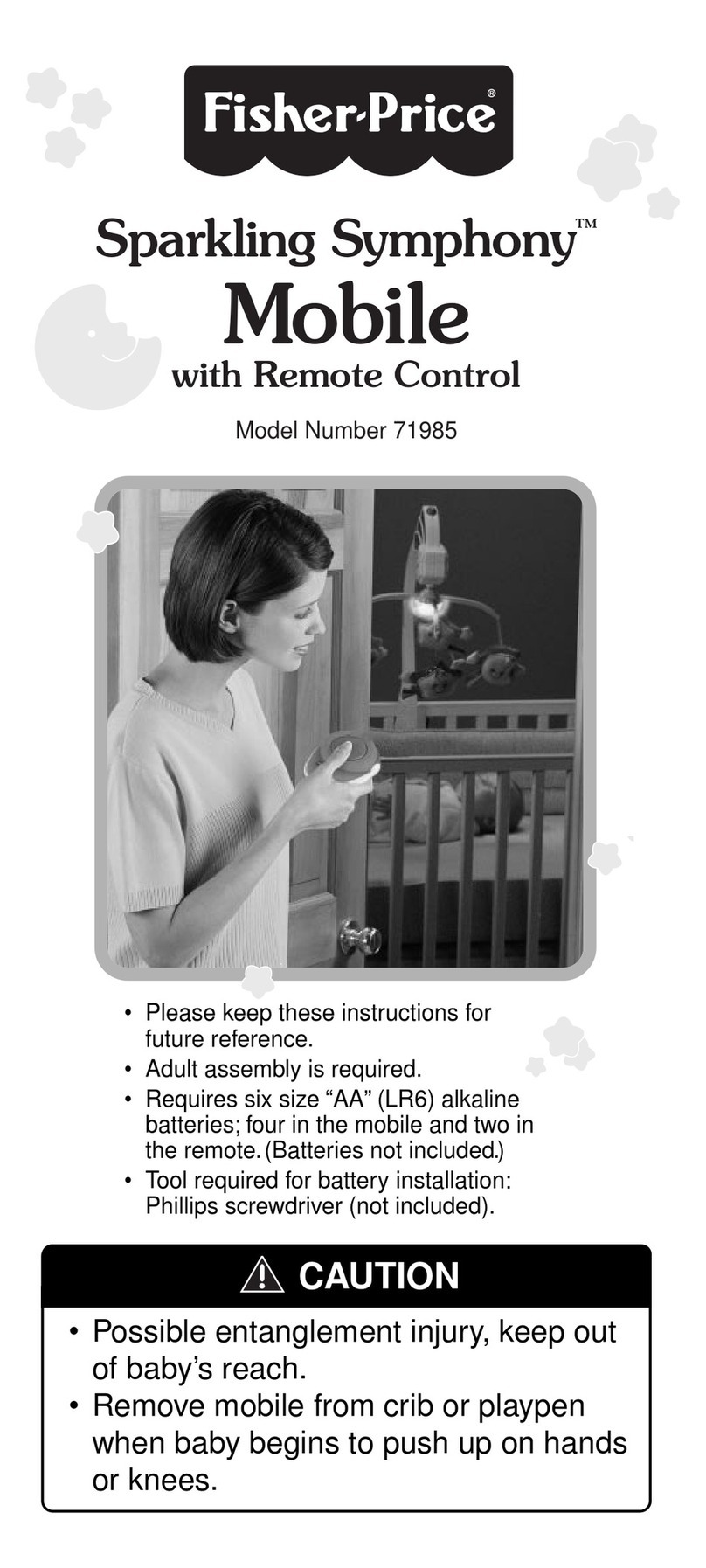
Fisher-Price
Fisher-Price Sparkling Symphony Mobile user manual
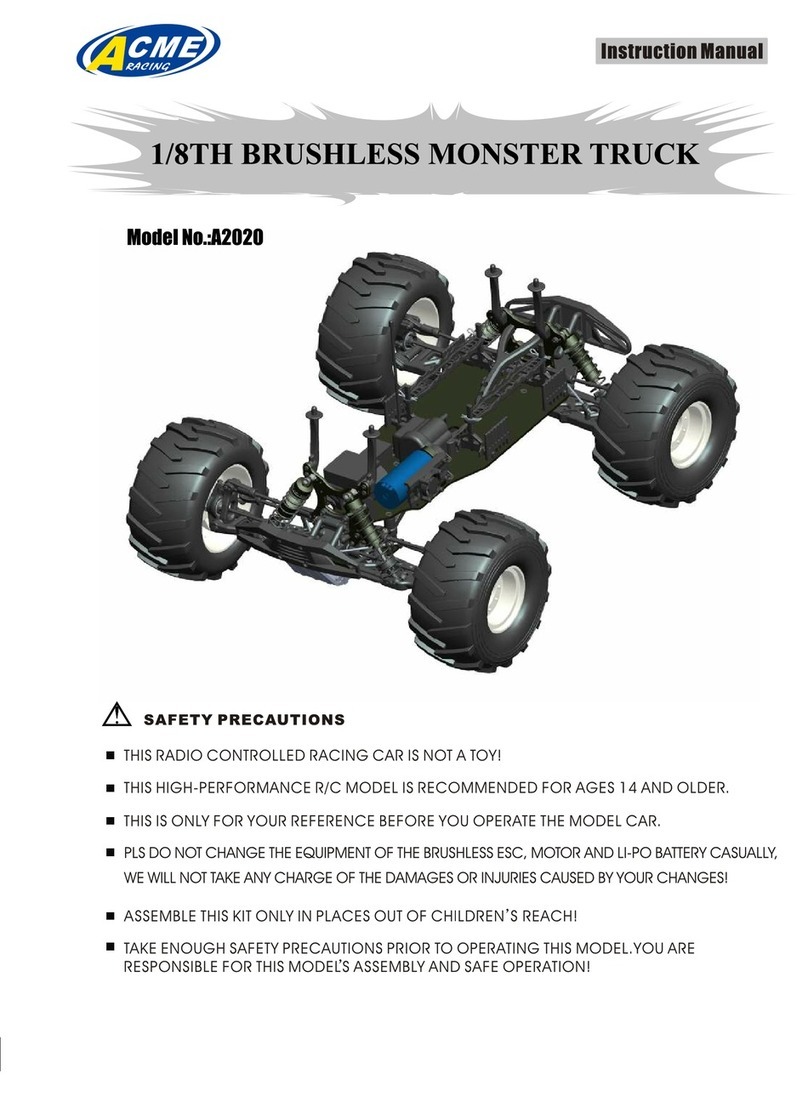
ACME Racing
ACME Racing A2020 instruction manual