ivact IVS A User manual

IAI5001-01 Page 1 of 9 07/18
iVS Range Installation and Operating Manual
This document provides necessary information for the installation and commissioning of the iVS A to D Range
Failsafe quarter-turn electric actuator. Each unit is shipped from the factory with initial calibration of cams and
switches completed for 0° –90° operation. However, these are general settings and serve as a starting point for
proper calibration of the actuator in its real-world application.
Only competent and trained personnel should install, maintain and operate iVS actuators. Any work related to
an actuator must be carried out in accordance with this manual, accompanied manuals, and related codes and
regulations. Local workplace health and safety rules should always be followed.
NOTE: Throughout the documentation we reference CLOCKWISE (CW)rotation (spring retracted) as moving in
the CLOSE direction and COUNTER-CLOCKWISE (CCW) rotation (spring compressed) as moving in the OPEN
direction.
Receiving / Inspection
•Carefully inspect for shipping damage. Damage to the shipping carton is usually a good indication that it has
received rough handing. Report all damage immediately to the freight carrier and your seller.
•After unpacking the product and information packet, please take care to save the shipping carton and any
packing material, in case of product return or replacement. Verify that the item on the packing list or bill of
lading is the same as your own documentation. If there is any discrepancy, please contact the seller.
Storage
•If the actuator cannot be installed immediately, store it in a clean, dry environment. The actuator must be
protected from excess moisture and dust, until you are ready to connect the electrical cables. The actuator
should not be installed outside, unless it is powered up and has the proper conduit connections.
•If the actuator must be installed, but cannot be wired, do not remove the plastic cable entry plugs. When
the actuator is wired, it is recommended to replace the plastic cable entry plugs with water-proof conduit
fittings.
•Storage temperature should be within the standard operating temperature range of the actuator.

IAI5001-01 Page 2 of 9 07/18
Before installing the actuator onto the valve or damper, check the following:
1. Check the actuator nameplate for the output torque
of the actuator. The output torque should be a
minimum of 30% greater than the actual maximum
requirement of the valve or damper. See Photo 1.
2. Check to ensure that the enclosure rating is suitable
for the area of installation.
3. Check the wiring diagram, as per the wiring diagram
code on the nameplate, and confirm that it meets
the electrical requirements.
4. Check the actuator nameplate for correct voltage,
prior to wiring. See Photo 1.
Actuator Installation
1. The actuators have been factory calibrated to
operate between 0° and 90°. Most failsafe quarter-
turn products will not require recalibration of these
settings. If any travel adjustment is necessary,
please refer to the “Limit Switch Setting” section
below.
2. The actuators are shipped in the full CLOSE (CW)
position (spring retracted). The 2-color mechanical
position indicator shows “CLOSE” (see Photo 2) and
on the actuator base, the female drive is aligned as
shown (see Photo 3). If the actuator is not in the full
CLOSE (CW) position, use the manual override (if
supplied) to reposition the actuator. See “Manual
Override” section below for instructions.
3. Fully CLOSE the valve or damper to which the
actuator is to be mounted. Note that the actuators
rotate CW (as viewed from above the unit) when
moving in the CLOSE direction.
4. Assemble necessary adaption components and
attach the actuator to the valve or damper.
Photo 2
Photo 3
Photo 1

IAI5001-01 Page 3 of 9 07/18
5. Tighten mounting bolts, making sure actuator is centered on the valve/damper drive shaft.
6. Before applying power to the unit, utilize the handwheel (if supplied) to check for unobstructed manual
operation from fully CW to fully CCW positions. (See “Manual Override” section below.)
7. Remove the cover and make the electrical connections as per the wiring diagram. Typical connections have
AC Neutral or DC (-) to terminal 1 and AC Live or DC (+) to terminal 3 or 4. Connection to terminal 3 to OPEN
(CCW). Connection to terminal 4 to CLOSE (CW).
8. For models where auxiliary switches are provided, terminals A - F are for 2 x SPDT adjustable auxiliary
switches. They are dry type Form C, rated 5A @ 250V AC max. Terminals A, B & C are for the OPEN position
auxiliary switch (adjustable). Terminals D, E & F are for the CLOSE position auxiliary switch (adjustable).
9. Connect the ground wire to PE inside the electric actuator.
10. Replace cover and secure cover screws.
11. Do NOT apply power at this time. See “Commissioning” section below.
12. Check below explanation of Duty Cycle. The intended service should not go above the maximum duty cycle
as noted on the actuator nameplate.
Installation Notes
•These actuators are designed to be used between a horizontal and upright position. Do NOT mount the
assembly with the actuator top below a horizontal position.
•When installing conduit, use proper techniques for entry into the actuator. It is preferred that the conduit
entries face downward. Use drip loops to prevent conduit condensate from entering the actuator. Use proper
fittings to maintain the NEMA 4X integrity of the housing. Seal (pot) the conduit entries.
•Use proper wire size to prevent actuator failure. All terminals accept 12 -18AWG solid/stranded wire.
•Do NOT touch any components on the PCB with metal tools or bare hands.
•The internal heater is to be used in all applications. Do NOT install the actuator outdoors or in humid
environments, unless it is powered up and the heater is functioning.
•Do NOT parallel wire multiple actuators together without utilizing isolation relays. If this is your intention,
please contact Innovative Actuation Incorporated for a multiple actuator parallel wiring diagram.

IAI5001-01 Page 4 of 9 07/18
Duty Cycle
Duty cycle is the percent of time that an actuator spends running, as a fraction of the total time. Duty cycle is
directly related to heat; excessively repositioning an actuator typically results in motor overheating, which can
cause permanent damage and/or reduced service life.
Duty performance can be calculated as follows:
(example iVS-D Range actuator: open cycle-17 seconds, close cycle-12 seconds, total runtime-29 seconds ON
and 40 seconds OFF)
Motor Runtime = 17s, Total time = 17s + 40s = 57s, therefore this duty cycle would be 30% (17/57). Standard
duty with iVS Range actuators is 50% so it is within the allowed limit. 34 seconds is the minimum off time in this
example.
Manual Override (if supplied)
A manual override gearbox (if supplied) compresses the
spring as the valve is opened. See Photo 4. The unit is
shipped without the handwheel assembled, as shown in
Photo 5. Using the hardware provided, thread the
socket-head cap screw onto the end of the input shaft
and tighten bolt securely.
The handwheel does not require a clutch mechanism.
Clockwise rotation closes the valve or damper.
Counter-clockwise rotation opens the valve or damper.
The handwheel does not rotate when the actuator
motor is running.
The handwheel MUST be brought back to the fully
clockwise CLOSE position before automated operation.
If not, this will limit valve’s travel and will not allow the
valve to fully close. If the handwheel is rotated when the
actuator is under electrical power, the actuator will
return to its last position, after the handwheel is
released. Do NOT utilize any mechanical advantage
devices to rotate the handwheel (pipes, wrenches,
extension bars, etc.).
Photo 4
Photo 5

IAI5001-01 Page 5 of 9 07/18
Spring Canister
The spring canister provides failsafe positioning and is seen in Photo 6. The end caps should not be removed, as
they house loaded springs that could possibly cause harm. A warning label is attached to each unit, see Photo
7, to warn against such action.
Mechanical End Stop
The mechanical end stop is used to adjust the fully clockwise CLOSE position. Adjusting this end stop will increase
or decrease the valve end travel. It is not to be used as an electrical travel limiting device. The mechanical end
stop MUST always be set, before the limit switch settings.
•Ensure that the power is OFF. Locate the housing cap (see Photo 8) and remove the cap screws using a 5mm
Allen Key. Use a 17mm wrench to loosen the hex nut and adjust the end stop. (See Photo 9).
•For iVS-A models, one full turn of the end stop = 2.3 degrees. For iVS-B, C, and D models, one full turn of the
end stop = 1.4 degrees. Once adjusted, tighten the hex nut, replace the cover and tighten screws.
•If any adjustment has been made, the closed limit switch TC2 must be reset. Refer to “Limit Switch Setting”
section below for instructions.
Photo 8
Photo 7
Photo 6
Photo 9
End Stop Housing
Hex Nut
End Stop

IAI5001-01 Page 6 of 9 07/18
Commissioning
This procedure will assume that the actuator is installed correctly, both mechanically and electrically, with
correct power, and has been manually cycled.
Electrically test Full OPEN (CCW) and CLOSE (CW) positions.
A. Apply power to terminals marked 1 & 3 (OPEN)
•The actuator will drive to the full OPEN (CCW) position (as viewed from ABOVE the
actuator).
•If this is NOT the correct stop position, refer to the “Limit Switch Setting” section below
to reset LS1.
B. Remove power from terminal marked 3 (CLOSE)
•The actuator failsafe springs will drive to the full CLOSE (CW) position (as viewed from
ABOVE the actuator).
•If this is NOT the correct stop position, refer to the “Limit Switch Setting” section below
to reset LS2.
Limit Switch Setting
The travel cams are set to control the open and closed position of the valve. The position is set to stop the travel
of the actuator when the travel cams activate the limit switch. Standard is two limit switches (LS1 & LS2), one
for open, one for closed. LS1 & LS2 limit the maximum range by disabling the electric motor. LS3 & LS4 are
optional. See Photo 10. They allow external equipment to confirm that the valve has reached the fully open and
fully closed positions. Care must be taken to ensure that LS3 & LS4 are set to trip prior to LS1 & LS2, so that
proper end of travel indication is provided. The travel cams can be adjusted with a 2.5mm Allen key.
NOTE: For units that are not equipped with a manual override, power will need to be supplied to the actuator
to set some of the limits. If the unit has a fail-position CW on power loss, you will require power to set
LS1 and LS3. If the unit has a fail-position CCW on power loss, then power will be needed to set LS2 and
LS4. Care must be taken when adjusting these limits with live power present.

IAI5001-01 Page 7 of 9 07/18
•To set LS1, the OPEN position (Full CCW Position):
oTurn power off and use manual override to turn valve to
the open position.
oRemove cover and loosen the set screw on the bottom
cam TC1.
oRotate cam clockwise to reset the switch contact.
oThen, slowly rotate cam counter-clockwise until a light
click is heard.
oSecurely tighten the cam and apply power to check the
end position.
•To set LS2, the CLOSE position (Full CW Position):
oTurn power off and use manual override to turn valve to
the closed position.
oLoosen the set screw on cam TC2.
oRotate cam counter-clockwise to reset the switch
contact.
oThen, slowly rotate cam clockwise until a light click is
heard.
oSecurely tighten the cam and apply power to check the
end position.
•To set LS3 - OPEN (Auxiliary Switch):
oEnsure that the actuator is in the fully CCW position.
oLoosen the set screw on cam TC3.
oRotate cam clockwise to reset the switch contact.
oThen, slowly rotate cam counter-clockwise until a light
click is heard.
oSlowly continue to rotate in the same direction for
approx. 3°.
oSecurely tighten the cam and apply power to ensure this
switch trips, before reaching the end position.
Photo 10
Switch Arrangement in Model ‘A’
Photo 11
Switch Arrangement in
Models ‘B, C, and D’
TC1
TC2
TC3
TC4
LS1
LS2
LS3
LS4

IAI5001-01 Page 8 of 9 07/18
•To set LS4 - CLOSE (Auxiliary Switch):
oEnsure that the actuator is in the fully CW position.
oLoosen the set screw on cam TC4.
oRotate cam counter-clockwise to reset the switch contact.
oThen, slowly rotate cam clockwise until a light click is heard.
oSlowly continue to rotate in the same direction for approx. 3°.
oSecurely tighten the cam and apply power to ensure this switch trips, before reaching the end
position.

IAI5001-01 Page 9 of 9 07/18
Troubleshooting
Problem
Remedies
Motor does not operate and overheats.
There may be a valve issue. Inspect/replace the valve.
Check for any obstructions in the flowline.
Motor shaft or bearing may be broken. Replace parts.
Check to see if the closed limit switch is set properly.
Possibly a wiring issue. Check terminal numbers 3 & 4 to see if they
are wired correctly.
The actuator operates, but the motor is hot.
The actuator may be operating too frequently. Check if operation
is within duty rating of actuator.
Overload issue. Runtime may be longer than specified. New valve
may be required.
The voltage may be under-/over-rated. Check the supply voltage.
The actuator may be against one of the mechanical end stops.
Reset limit switches and adjust end stops again.
The valve does not move when given a signal or in manual
operation.
Check installation between the actuator and valve as it may not be
assembled properly.
Verify that the set screws of the travel cams are tightened.
The torque requirement of the valve may be larger than the
output torque of the actuator Check sizing to confirm correct
actuator selection for the valve.
When operating two or more actuators simultaneously, one
of the motors is hot or working abnormally.
There may be a parallel wiring connection issue. Check current
values and install a relay.
Table of contents
Popular Range manuals by other brands
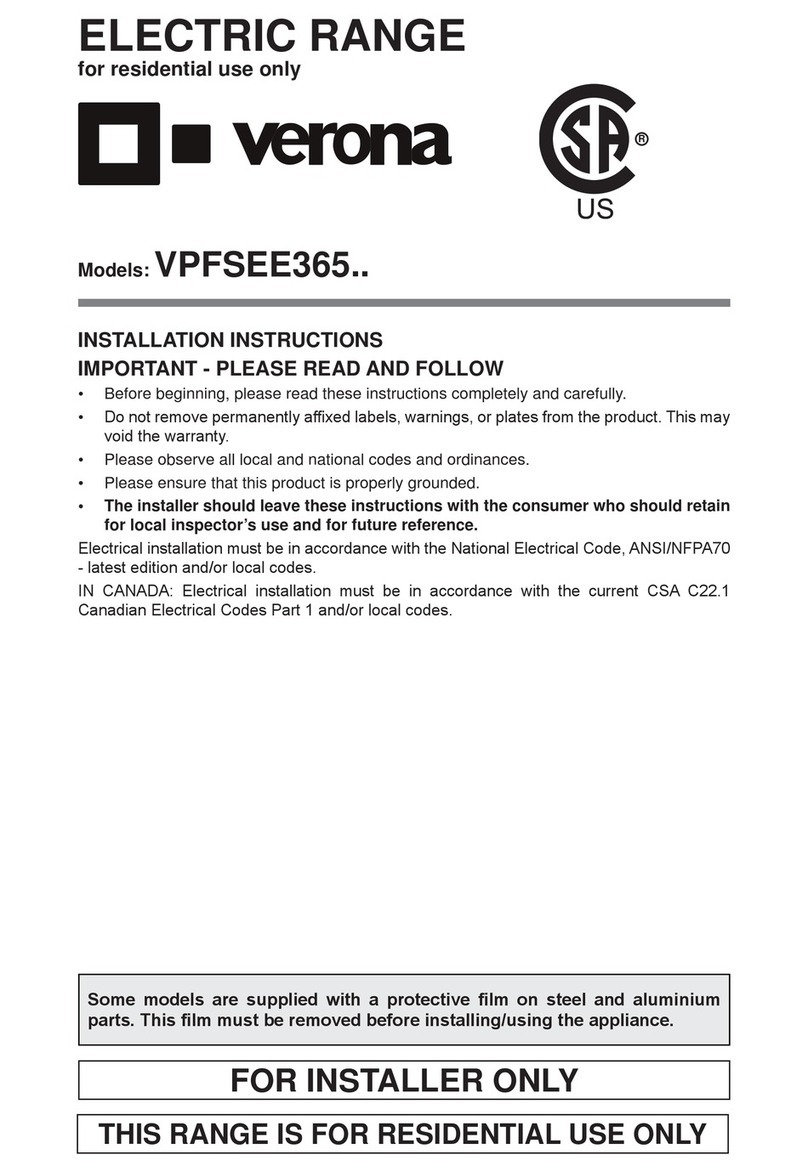
Verona
Verona Prestige VPFSEE365SS installation instructions

Frigidaire
Frigidaire PLEF489GCA Guide installation instructions

Frigidaire
Frigidaire ES510 Use & care manual

KitchenAid
KitchenAid KDRS505X Use & care guide
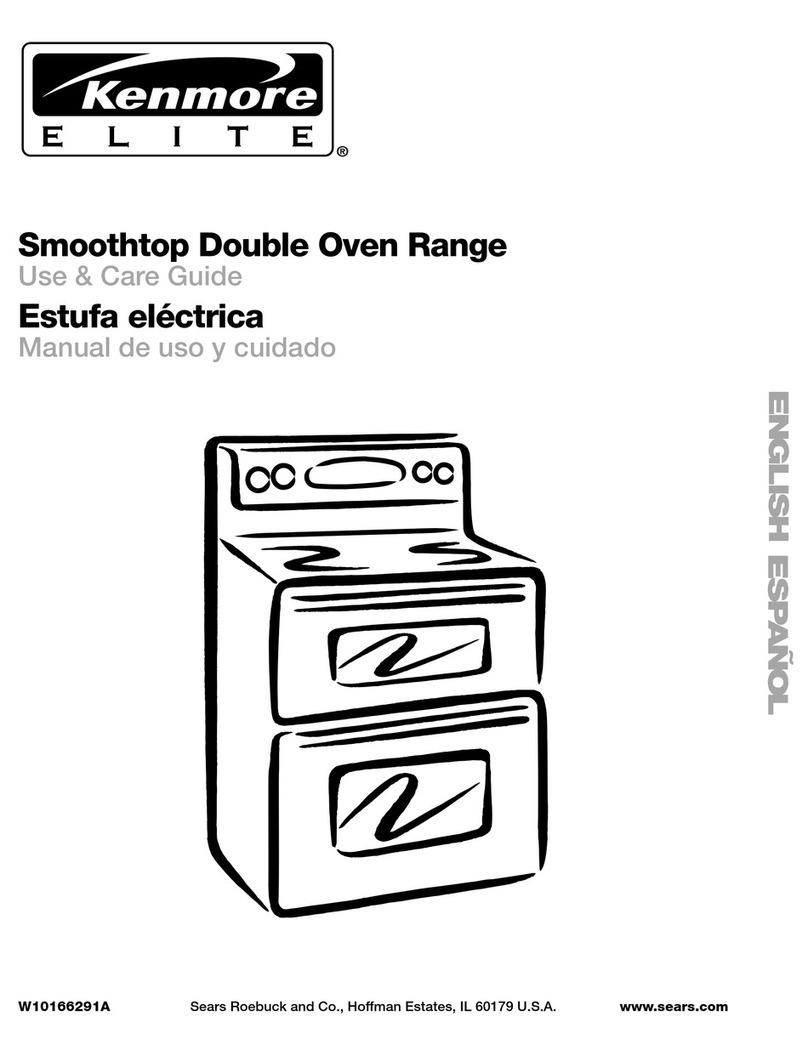
Kenmore
Kenmore W10166291A Use & care guide

Thermador
Thermador Professional Pro Grand PRD48JDSGU/09 Use and care guide