Sub driver MOEBIUS SKIPJACK User manual

THE MOEBIUS SKIPJACK SUBMARINE
CONVERTION TO RADIO CONTROL
Instruction Manual
Download and read the Adhesives & Fillers 101 pdf file
The Fittings Kit!2
Marking Off, Test Fitting, and Punching holes!3
Assembling the Aft Dive Planes & Rudder!3
Cutting the Hull for the Z Type Configuration!5
Drilling and opening Upper Hull Holes!5
Preparing And Assembling The Sail!8
Installing the Sub-driver Foundations!11
Welding the Lower Hull Together!12
Assembling the Upper Hull!14
Installing The Sail!15
Installing the Torpedo System!17
Sub-driver and Mission Check Tasks!20
The Moebius Skipjack R/C Conversion Instructions
Page 1

The Fittings Kit
The Moebius Skipjack R/C Conversion Instructions
Page 2
A stern planes and yoke
B rudders and yoke
C after Sub-driver foundations
D Sub-driver shock absorber
E forward Sub-driver foundation
F nest transverse bulkhead
G nest keel piece
H torpedo tube nest foundations
I torpedo muzzle bulkhead
J propeller shaft foundation
K propeller
L propeller shaft, bearings and coupler
M hull rudder hole blanking discs
N sail plane operating shaft bushings
O hull stand hole blanking pieces
P Sub-driver restraining strap foundation
Q sail planes and bell-crank
R sail-to-hull mounting foundations
S sail plane bell-crank shaft retainers
T sail plane bell-crank
U mechanical fasteners
V after radial flange
W forward radial flange
X upper hull securing screw and foundations

Marking Off, Test Fitting, and Punching holes
Out of the box, the hull is broken down
into four large hull sections or quarters,
two upper hull quarters and two lower hull
quarters.
Take the two stern hull quarters, identify
the 3/16" diameter resin blanking pieces
(M)-hull rudder hole blanking discs &
(O)-hull stand hole blanking pieces)
and insert and CA each disc into a rudder
operating shaft hole, leave a bit of the
blanking disc standing proud of the hull.
Sand it to contour to the tight radius at that
point of the stern.
On the inside of the two stern quarters,
grind flush the raised flanges of the former
rudder operating shaft bores.
Do not permanently glue anything else together yet,
though some of the below shots show assembled
hull quarters.
From the center of the blanking discs, measure 1/4"
aft and drill a new 1/8" diameter rudder operating
shaft hole, top and bottom hulls.
Glue in the two oblong resin (O) Hull Stand
Blanking Pieces into the two oblong holes, one in
each of the bottom hull quarters.
Assembling the Aft Dive Planes & Rudder
Check the fit, within the hulls stern, of the
stern planes and rudders, as well as (J) Prop
Shaft Foundation.
Using 1/16" diameter brass rod, (not supplied)
make two Pushrods, 7" in length, each with a
Z-bend at one end.
One Pushrod makes up to the rudder bell-
crank, the other Pushrod makes up to the stern
plane bell-crank.
Install Klik-on Magnets to the ends of the
The Moebius Skipjack R/C Conversion Instructions
Page 3

Pushrods. (see right) using CA adhesive.
Make up the Pushrods to the yokes to check
them for operation.
Take the two Propeller shaft foundations
and, after grinding away the radial and
longitudinal raised braces at the stern of the
two stern hull quarters, test them for a tight fit. Keep
the lower after hull quarter Propeller Shaft
Foundations in place for the next step, the dry-fit of
the running gear and control surfaces.
Install the two Rudders and two stern planes as
seen here.
Check for non-interference of control surfaces and yokes through the full travel (not to exceed 35-degrees
left/right and rise/dive). Note how the intermediate drive shaft runs through the center of the rudder yoke
and over the swing-arm of the stern plane yoke.
Make the Intermediate Drive Shaft.
Use an 8 1/4" length of .014" wall thick,
7/32" outside diam. either brass or
aluminum tubing with half a Dumas
nylon dog bone inserted into each
end.
Each dog-bone pinned to the shaft
with a transverse length of 1/16" brass
rod peened at each end.
Work out how much dog-bone half
projects past the tube as you integrate
the running gear with the SD.
The Moebius Skipjack R/C Conversion Instructions
Page 4

Cutting the Hull for the Z Type Configuration
A Z Type type break between the two hull
halves provides for quick access (only one
screw at the stern holds the hull halves
together), is strong, and is less susceptible
to flexing than a simpler horizontal
break that runs completely around the bow
and maybe even the stern.
Take the Forward lower hull and
Upper stern Hull in hand and put the
other hull sections aside.
Forward lower hull: Identify the second
radial stiffening frame from the bow. Set
the compass at 3" inches. Place the point
into the right-angle union between hull and
frame, mark a radial line into the inside of
the hull quarter denoting the bow cut line.
Do the same for the Stern upper hull.
That datum frame is the one at the leading
edge of the horizontal stabilizers. Set the compass at 2 1/4"
It's much easier to follow the cut line if it's on the surface of the hull quarter, so now you have to transfer
the inner cut line to an outer cut line. Plug in a 100 Watt light bulb, and us it to back-light the interior of the
hull quarter so you can see the internal radial inked in line through the translucent plastic. Pencil in cheat
marks to the surface of the hull over the line you see through the hull. After enough points are put down to
get an accurate indication as to the lines true form, lay down some masking tape, it's edge at the cheat-
marks, and ink in a proper cut line to the outside of the hull using the edge of the tape to guide the
Sharpie pen point.
Remember, cut off the stern of the Stern upper hull, and cut off the bow of the Forward lower hull.
Don't screw up! And don't cut these pieces off till later, we're just marking things off at this point. Use a
Japanese saw to make these cuts.
Check twice and cut once!
!Drilling and opening Upper Hull Holes
Mark then drill or grind out the openings on top of the two hull
quarters. Here are two upper hulls, the top one has its holes opened
up. The bottom unit has just been marked off as to hole shape,
location, and size.
Use new drill bits spun at low speed. Styrene takes to the bit well,
keep the pressure light as you punch through. The indented round
depressions on the sides (upper and lower) of the hulls indicate drill
size to use. For holes larger than 3/32, start the hole with a 1/16"
bit, this serving as a pilot-hole that better directs the cut of the larger
bit that follows. When using high-speed cutting bits, work in short,
low pressure jabs.
The Moebius Skipjack R/C Conversion Instructions
Page 5

Punch out 7/16" diameter holes in the centers of the six ballast tank vents on the forward deck flat. Do the
same for the four ballast tank vents on
the after deck flat. Don't touch the four
big Main Sea Water holes on the after
lower hull quarter after quarter hull
section, those will later be covered by
Photo Etched gratings.
The following hole locations are now
marked off along centerline on the
forward upper hull quarter.
Measurements are taken from the
projecting nib, marked 'datum' on the
above photograph, just aft of the
forward deck flat:
1. A square hole who's forward
transverse line is 3/16" from datum,
and after transverse line is 5/8" from
datum. The longitudinal edges of this
inked in hole are 1/16" inboard of the
troughs that accept the indexing lips at
the bottom of the sail assembly. Later
the lower sail plane bell-crank gear will project through this hole.
2. 2 1/4" aft from datum is a 3/16" hole that will pass the snorkel head-valve tube down into the hull. If you
use the 3.5 Sub-driver unit, the SAS snorkel foundation piece will be used as a marking stencil to indicate
where you'll drill 1/16" holes that accept the self-tapping machine screws securing that foundation atop
the hull, under the sail. See picture.
3. 6" aft from datum is the first of three 1/4" holes that vent air in and out of the hull, under the sail and
exhaust fairing.
4. 8" aft from datum is the second 1/4" vent hole
5. 10" aft from datum is the third 1/4" vent hole
The Moebius Skipjack R/C Conversion Instructions
Page 6

The many square holes you have to
punch open in the bottom of the two
lower hull quarters is done with drill,
square files, and sanding sticks. The
work goes pretty well if you take your
time and outline the inset gratings
molded into the plastic with a Sharpie
pen. You'll lose all that beautiful
detail, but to be a practical r/c model
submarine that works as a wet-hull
type, it has to be done.
I suggest you punch out all the
holes before sticking the hull quarters
together, the parts are easier to
handle when they are smaller
assemblies. Note, the lower hull has
also taken advantage of the engraved
lines of the torpedo tube shutter doors to open those up -- that model will later be outfitted with six
practical launchers.
The Moebius Skipjack R/C Conversion Instructions
Page 7

Preparing And Assembling The Sail
Once you have marked out the holes that go under the sail, snip the two nubs (indexing pins) off the hull
and at their former location, drill 7/64" holes. These will pass the 4-40 machine screws that hold the sail
assembly down onto the upper hull. There is a third nub, back near the after portion of exhaust fairing, on
the after upper hull quarter. Snip it off too, but drill no hole there yet.
Flip the forward upper hull piece and work on the inside. Open a 1” x 1/4” extension of the square hole.
(see above) This will eventually pass the pushrod magnet that makes up to the magnet at the base of the
sail plane bell-crank assembly. Note the orientation, and the side where you put in the new cut, and it's
measurements. Grind away excess. The outboard long side of that the hole butts up against the raised
portions of hull under the sail -- those raised portions accommodate the longitudinal indexing troughs atop
the hull. The photo shows how the linkage eventually goes in there.
With masking tape, put the sail halves together, ready to open up the bottom of the sail to pass the bow
plane linkage (mounted within the sail) and snorkel head-valve assembly (mounted atop the hull, but
fitting within the installed sail). Two complete sails are shown here.
The top sail has already been opened up,
the bottom sail has been marked off.
Tack-glue the forward and after resin
foundation pieces within one half of the
sail, then tape the other half of the sail
onto it. With a Sharpie pen mark off the
spot where you will drill a 3/32" hole and
tap it for a 4-40 machine screw. Take
everything apart and punch those holes
and cut the threads into the sail
foundation pieces.
Most apparent in this photo, at the base
of the sail, at its perimeter, the plastic
extends down into long-running lips that
engage the deep troughs set within the
top of the hull. The two 4-40 machine
The Moebius Skipjack R/C Conversion Instructions
Page 8

screws running up from within the hull into the
resin foundations fixed in the sail make fast the
sail to the hull, yet provide for quick and easy
separation of the two for transportation,
adjustment, or repair.
When the r/c SKIPJACK leaves the surface, an
unobstructed path for venting air, trapped in the
diesel exhaust fairing, has to be provided. Failure
to get all the air out of the fairing will upset the
boats trim and make it difficult to hold exact depth
when cruising along at slow speed. So, the
following operation has to be done before
securing the sail foundation pieces (sail-to-hull
mounting foundations-R) to one half of the sail
assembly: Grind a 1/8" deep by 1/8" wide vent
channel atop the after foundation piece. A
corresponding vent hole is drilled into the top,
forward bulkhead where the exhaust fairing meets the trailing edge of the sail proper.
You will need the ability to flex the bottom of the sail a bit to get the lower sail plane bell-crank (sail plane
bell-crank-T) on and off its bell-crank
shaft retainers (sail plane bell-crank
shaft retainers-S). To accomplish that
the sail foundations are glued to only
one side of the assembled sail.
This permits the unglued underside of
the sail to pull away from the other sail
half when flexed to install or remove the
lower sail plane bell-crank.
You see here how the sail plane
operating shafts fit within the rather
thick hub of the resin upper bell-crank
(sail planes and bell-crank-Q). The gear
portion of the upper bell-crank engages
the gear portion of the lower bell-crank
which works around its shaft to rotate
the upper bell-crank when subject to the
axial motion of the pushrod that runs
from the motor-bulkhead of the SD.
Here I'm grinding away the raised molded in place bores of the original operating shaft holes projecting
from inside the sail halves. The hole, as it is, is too big for the 1/8" diameter sail plane operating shaft.
You see between the trailing edge of the sail planes and the ground away bore of one sail half the as of
yet untouched bore. A small resin bushing (sail plane operating shaft bushings-N), installed into the
original hole reduces its diameter to the required 1/8" bore required by the sail plane operating shaft. The
two bushings are pushed in and CA'ed in place.
Note that a set screw, set within the hub of the upper bell-crank unit, secures the operating shaft of a sail
plane -- these set screws easily reached from the opening in the bottom of the sail assembly.
Tape the halve of the sail together. install the sail planes by running each operating shaft into the bore of
the upper bell-crank. With the two planes lined up with they're cords parallel to the top of the sail, and the
center of the gear section faced down and perpendicular to the cord, tighten the two set-screws to secure
the planes to the upper bell-crank part.
The Moebius Skipjack R/C Conversion Instructions
Page 9

The two resin lower bell-crank shaft retainers are placed on the ends of the brass pivot pin, and the
entire unit installed into the inverted sail and oriented so that its teeth meshed with those of the upper
bell-crank. Squeezing the hull halve together between thumb and forefinger, to hold the shaft from
moving, tack-glued the retainers to the sail halves -- use only enough CA to hold them in place. Check
that rotation of the lower bell-crank caused free unbinding rotation of the upper bell-crank. Break
and reposition the retainers as required until free, minimal back-lash operation of the linkage is achieved.
Position the clear piece that represents the
emergency stern-light within the sail, then
assemble the sail and hold it together with
masking tape.
Avoiding those areas where masking tape is
(you don't' want the thin glue to get sucked
i n t o t h e t a p e s e d g e s b y c a p i l l a r y
action) brush thin solvent cement along the
seam at the leading edge of the sail, along
the top of the sail where the sail top piece will
sit, along the trailing edge of the sail, and
over the seam atop the diesel exhaust fairing.
Also run cement onto these seams from the
inside. Leave the assembly to dry for a few
hours.
DO NOT apply cohesive glue to the bottom of
the sail. Remember, you want to flex the bottom portion to get the lower bell-crank shaft in and out of its
resin retainers.
The Moebius Skipjack R/C Conversion Instructions
Page 10

Installing the Sub-driver Foundations
Before installing the two sets of Sub-driver foundations, shock absorber, and SD Velcro strap
foundation, it's wise to mark out a centerline to
the inside of the lower hull quarters.
Examine the two sets of resin SD foundations
provided. The smaller set (C) goes aft and the
cut-outs within those clearly defines where they
butt up against a frame in the lower after hull
quarter.
The other, larger set of foundations (E) fits
against the forward face of the aftermost frame
in the forward lower hull quarter. Note that the
circular edge at the top of these foundations is
not concentric with the circular edge at the
base. On both sets of foundations the narrower
portions of the pieces of the foundation halves
meet at the bottom of the hull -- get that
straight before CA'ing them permanently in
place!
With the forward set of SD foundations (E) glued against the frame, butt the after end of the Sub-driver
shock-absorber (D) (where the pin projects up) up against the forward face of the Sub-driver
foundations. Center it, then using a line pencilled, mark onto the hull where the holes will be drilled to
pass the six securing 2-56 machine screws.
Remove the shock absorber and grind away a 1/2" wide, 3/8" deep channel down between the two halves
of the Sub-driver forward foundations. This channel permits disassembly of the shock-absorber
components, should that every be necessary.
The forward end of the Sub-driver strap foundation (P) butts up against the after face of the forward
most frame of the after lower hull quarter. (The tall end of this resin piece goes forward, the shorter end
goes aft). Lay the piece on its side within the hull and mark off where you will punch two 3/32" diameter
holes into the bottom of the hull, these will pass two 2-56 flat-head machine screws that secure the strap
foundation piece to the lower hull.
Before drilling a hole, push a pointed rat-tail file hard into the plastic, a sort of 'pilot-hole' that works to
guide the drill bit as it opens up the hole.
Drill out 3/32" holes to pass the flat-head 2-56 machine screws that secure the SD shock absorber to the
bottom of the forward lower hull quarter.
To the outboard side of the hull, bevel these holes with a counter-sink bit to accept the flat-head screws
that secure both the shock-absorber and strap foundation.
The Moebius Skipjack R/C Conversion Instructions
Page 11

Welding the Lower Hull Together
The forward and after lower hull quarters
are welded together using solvent type
cement. As you can see, the two hull
quarters are mounted on a flat board to
insure that their edges fall along the
same plane. Note that a rubber band is
used to push the after end of the forward
quarter down hard onto the radial flange
of the after quarter.
Just as in metal welding, which involves
pre-heating of the weld area, the contact
areas of the plastic to be bonded is
treated to make it receptive to deep
fusion once the state change is effected
to the parts being joined. Before assembly, the
radial flange of the lower after quarter and mating
surface of the forward lower quarter are soaked in
the very thin solvent cement to soften those
surfaces. Then, quickly, the gelled solvent cement
is beaded onto the flange and the two hull
quarters assembled on the flat board, the rubber
band made up, and the work left for twelve-hours
to harden.
Once the center, radial union between the two
lower hull quarters has hardened, the assembled
lower hull is taken off the board, inverted, and the two upper hull quarters are set upon it -- a test dry-fit.
any sprue left at the horizontal centerline between the lower hull and two upper hull quarters is identified,
cut and filed back until a tight fit between the three hull pieces is achieved.
Take things apart, insert two slivers of wax-paper onto the edge of the lower hull over the radial joint --
this to prevent any adhesive that runs down from the upper hull pieces from getting onto the lower hull
piece. Don't worry, if you keep the wax-paper slivers small enough they will conform to the tongue-in-
groove union enough to not distort the fit between the three hull pieces too much. Or, you can wax the
edges. Your call.
Lay the after upper hull quarter down, get it to register with the lower hull and hold the assembly together
with rubber bands. Soften the flange of that piece and corresponding inside surface of the forward upper
hull quarter with brushed on thin solvent cement, then smear on beads of gelled cement to the surface of
the flange and quickly position the forward upper hull quarter on top of the lower hull and make the
assembly fast with rubber bands. Leave the upper hull to dry twelve-hours.
As the r/c SKIPJACK features a hull that opens up at its centerline equatorially, it's vital that the upper and
lower hull index together as well as possible owing to the fact that the only clamping force applied when
they are assembled is at the extreme bow and extreme stern. Any misalignment between the two hull
halves during assembly of the quarters would suffer unsightly open seams between the halves.
Here, a length of sprue has been heat-stretched to a mean diameter of .025". This is used to fill the
inevitable seam between the two hull quarters of the upper and lower hull pieces. As with pre-heating
of metal parts to be joined is done to enhance fusion, wetting the groove between the
The Moebius Skipjack R/C Conversion Instructions
Page 12

hull quarters liberally with thin solvent cement works to soften the plastic and weld with the adjoining filler
rod and hull quarter.
If need be, to insure an open seam of uniform width and depth to better receive the filler rod -- use an
eighteen-tooth-per-inch hack-saw blade to achieve a uniform .025" wide by .025" deep groove for the filler
rod.
Lay in the filler rod, brushing on solvent as you go. Things get gummy as you work and soon the rod
dissolves into the adjoining material. The result is a near perfect fusion weld between the forward and
after hull quarters.
Carefully following the inked on radial lines, a razor saw was used to remove the tail-cone from the after
upper hull quarter, and bow from the
forward lower hull quarter. Using a
wide hard-block, sand the radial
faces of all parts with #240
sandpaper. If you were careful you
lost no more than 1/16" of kerf, that
will be made up later with CA-
baking soda filler.
The Moebius Skipjack R/C Conversion Instructions
Page 13

Assembling the Upper Hull
Carefully following the inked on radial lines, a razor
saw was used to remove the tail-cone from the after
upper hull quarter, and bow from the forward lower
hull quarter. Using a wide hard-block, sand the radial
faces of all parts with #240 sandpaper. If you were
careful you lost no more than 1/16" of kerf, that will
be made up later with CA-baking soda filler.
(Right photo) To the right are installed flanges.
Center and left are yet to be installed flanges and the
hull sections they go into. you want one-half of the
tail-cone flange (after radial flange-V) to project past
the
radial edge. However, you ant only 3/8" of the
forward flange (forward radial flange-W) to project
past the bow pieces radial edge.
As they arrive, the stiff, polystyrene flanges are flat.
Put a curl into them by running a flange piece over a
small dowel as you apply pressure between dowel
and finger as you pull the flange through. Keep at it
until the flange retains a curl close to the radius of the
part it will fit within.
Test fit the flanges to the tail-cone and bow piece.
Onto the bow piece flange mark with pen or pencil
where some of the flange overlaps two of the flood-
drain openings. Once you've affirmed a good fit of the
flanges, remove them, cut away those areas
of the forward flange so marked, coat the
flange and hull pieces with thin solvent
cement to soften they're surfaces, apply
gelled cement, then quickly assemble the
flanges to their respective hull pieces, clamp
and let sit for at least twelve-hours.
A single 4-40 flat-head machine screw
passes through a hole in the upper hull half,
pushing it all down upon the after radial
flange.
Up forward, the radial flange of the lower hull
captures the bow piece attached to the upper
hull, pulling the two hull halves together.
The Sharpe-kachur Z union at work!
The Moebius Skipjack R/C Conversion Instructions
Page 14

Installing The Sail
If I gave the impression in a previous installment
of this article that the lower bow piece could be
installed to the upper hull half before installation
of the torpedo tube nest assembly (the three
piece structure comprising nest transverse
bulkhead-F, nest keel piece-G, and torpedo
muzzle bulkhead-I), I was mistaken. The nest
assembly must first be assembled, CA'ed within
the forward hull piece, and only then can the
forward hull piece be glued to the upper hull half.
At this point most of the major assembly chores
have been done. All that is left is to screw the
three pieces of the torpedo nest assembly
together, glue it into the lower hull section (the
one sawed off from the lower hull); mount that
bow piece under the forward end of the upper
hull; make up the securing screws to the Sub-
driver shock-absorber and strap foundation; and
test fit the SAS snorkel assembly (if used).
Note here the two round-head 4-40 machine
screws that run up from inside the upper hull,
through the base of the sail, and into the thread of
the sail foundations. This is how the sail is pulled
down securely upon the hull.
The sail plane pushrod is made up to
demonstrate how its magnet engages the magnet
partially encapsulated within the resin arm of the
lower sail plane bell-crank.
The short length of tube extending into the hull
projects into and made tight by the elbow's O-ring.
The elbow unit in foreground shows off this
sealing O-ring.
The 90-degree elbow fitting that makes up to the
induction tube permits the rather stiff 'flexible'
induction hose to make up to the manifold atop
the Sub-driver without getting in the way of the
sail plane pushrod. The elbow accepts, through its
watertight O-ring, the projecting induction tube,
the body of the elbow rests up against the top of
the hull where it is slathered with RTV adhesive to
hold it in place, as you see in the elbow glued
within the top of the upper hull. This permits
removal of the entire snorkel assembly for
maintenance, yet assures watertight integrity of
the snorkel assembly when reinstalled.
The sail is removable is afford access to the hull
mounted SAS snorkel assembly, as well as to
adjust the sail planes if needed. The snorkel
assembly comes with the Sub-driver.
The reason I had you assemble the two sail
halves together, but not the top of the sail, was to
permit viewing through the open top of the sail as
you check the snorkel float free to run the 1/4" or
so vertically without rubbing up against the inside
walls of the sail. Once satisfied that all is well
within, the sail is taken off the hull, and the top
piece glued in place with thin formula solvent
cement.
The Moebius Skipjack R/C Conversion Instructions
Page 15

Before running through the screw fasteners
through the bottom of the hull, making up
the Sub-driver Shock-Absorber and Strap
Foundation, bevel the outside of the holes to
counter-sink the flat-head screws. Use a variable
speed drill and a sharp bit, and keep the speed
slow to insure the plastic does not melt.
The job of the Sub-driver shock-absorber is to
dissipate collision energy, acting as a damper. So
doing, the shock-absorber enhances the models
ability to avoid handling and running damage,
such as shearing of the Sub-driver indexing pin or
crushing of the models bow. The spring loaded
Shock-absorber acts as a damper A shock-
absorber is recommended for all models
employing 3.5 sized Sub-driver's and up.
2-56 nuts tightened on the screws, then treated
with Threadlocker or CA, keeps them from
vibrating loose. Apply CA around the base of the
shock-absorber where it meets the hull.
The Moebius Skipjack R/C Conversion Instructions
Page 16

Installing the Torpedo System
A torpedo firing SKIPJACK is an optional. The
nest foundation is provided with the fittings kit.
http://www.sub-driver.com/torpedo-systems/
torpedo-system-1-72nd-scale.html
and a technical paper on the system,
http://support.caswellplating.com/index.php?/
Knowledgebase/Article/View/359/47/torpedo-
launcher-instructions-172
The Torpedo Nest assembly's primary job is to
stiffen the bow of the SKIPJACK against handling
and collision damage. It is a vital part of this boat,
even if torpedoes aren't installed, and the
Torpedo Tube Nest foundation (H) is not
installed.
The SKIPJACK kit is principally made of 'high-
impact' polystyrene plastic that has nowhere the
strength and shock resistance of glass reinforced
plastic (GRP).
In the picture above a nest of six 1/72 torpedo
tubes, secured within the Torpedo Tube Nest
foundation (H), all sit secure and in
proper registration atop the keel piece. The
muzzle ends of the tubes project into and are held
in alignment by the torpedo muzzle bulkhead.
The three pieces that make up the nest assembly
attached together with the aid of four 2-56 round-
head machine screws and CA wicked into all
joints.. A quick and easy means to insure that the
torpedo muzzle bulkhead and nest transverse
bulkhead fit perpendicular to the nest keel piece is
to lay the assembly over some graph-paper and
eye-ball it. Block sand the forward and aft keel
edge to square up the unit.
Note how the bottom edge of the keel piece
indexes with the anchor well and frame that
projects up from the bottom of the forward hull
piece -- it insures that you get the nest assembly
to sit the correct distance from the front of the
boat.
The two engraved lines, one either side of muzzle
bulkhead, will help you
With the Nest Assembly’s radial orientation within
the hull.
The Moebius Skipjack R/C Conversion Instructions
Page 17

Test fit the Nest Assembly into the lower bow
piece and mark off the contact points between
within the hull with a pencil or pen. Remove the
next assembly and rough up the contact areas
with #240 sandpaper. Do the same for the upper
hull half, where the torpedo muzzle bulkhead
will make contact in that section.
If you are going to equip the SKIPJACK with a
practical weapon system, before installing the
nest assembly, grind and file open the torpedo
shutter doors.
Molded into the sides of the torpedo muzzle
bulkhead are engraved longitudinal lines to guide
you as you register the nest assembly to the
lower hull piece. When lining up the assembly
rotate it until the two engraved lines fall along the
edge within the bow piece, and proper radial
alignment is achieved. Pressing the assembly
down tight into the lower hull, tack-glue it to the
hull with staggered dabs of thin formula CA.
Release the pressure, then check again for
proper alignment. Apply thick formula CA along all
contact points and let it soak in and harden.
Leave the CA to cure naturally.
This picture shows to good advantage how the
lower edge of the Nest Keel Piece (G) indexes
the nest assembly lengthwise by engaging the
forward frame and raised anchor well. Note that in
this shot, the bow portion of the lower hull half has
not yet been razor sawed away.
If you wish to install the SKIPJACK torpedoes see
http://www.sub-driver.com/torpedo-systems.html
Each weapon system package contains one
launcher (which can be configured for either
mechanical or pneumatic actuation) and three gas
propelled torpedoes/weapons.
The Torpedo Tube Nest foundation (H) is
optional and is only used if you opt to include the
Torpedo Launchers. This can always be added at
a later date.
Glue the forward lower bow piece to the upper
hull half. Note the pencil mark near the inboard
and outboard edge of the upper hull -- marked off
to indicate where to stop brushing on the thin
solvent cement used to soften up both the upper
hull matting edge and lower bow section mating
The Moebius Skipjack R/C Conversion Instructions
Page 18

edge. Once you get the
mating edges softened with
solvent adhesive, the two
pieces are assembled, more
thin solvent cement was run
into the seam where
capillary action pulled it into
the gap and the two pieces
start to fuse together. To insure a tight
seal, rubber-bands are wrapped around the
assembly.
The flat heads of the screws holding the Sub-
driver shock-absorber (D) and Sub-driver
foundation (C&E) on the bottom of the hull need
to be secured permanently. A drop of thin CA
adhesive is dabbed onto each screw head and
left to soak in about a minute, followed by a
sprinkling of baking soda to wick up the adhesive
and cure it. Work the CA-baking soda filler with a
file to conform to the curvature of the hull.
The Moebius Skipjack R/C Conversion Instructions
Page 19

Sub-driver and Mission Check Tasks
Successful operation of the r/c model submarine
equipped with a Semi-Aspirated (SAS) type Sub-
driver (SD) is contingent on the careful and
complete adherence to a series of maintenance
procedures before, during, and after use. Failure
to follow the bellow tasks will result in degradation
of the system, reduction in system performance,
or even complete loss of the system do to sinking.
Perform the mission checks religiously and don’t
proceed until an identified problem is addressed
and put right.
WARNING: While in the water never invert the
SD as the snorkel and safety float-valves will
unseat, flooding the interior of the SD.
CAUTION: Before placing the SD in the water,
insure that either the snorkel induction hose or a
blanked off hose is connected to the five-point
manifold, or the SD’s induction line will flood.
CAUTION: Never ‘hover’ the submarine
employing the SAS sub-system – once you
commence a blow from depth, continue the
evolution until the sail totally broaches the
surface. Failure to equalize the pressure within
the SD after a ‘blow’ (with the snorkel head-valve
immersed) will result in a pressure-differential
across the LPB that, at some point, will increase
where ballast water can no longer be pushed out
using SD air as the source.
PRE-MISSION
These are the tasks you perform in the shop to
integrate the SD with the model submarine, check
things out, get your field-box up to speed, and
pack up the car.
1. Preparing the SD: To the inboard side of the
motor-bulkhead, apply a drop of oil to each of the
pushrod seals. Insure that the motor-bulkhead
and forward bulkhead (cap) O-rings are clean and
well greased. Check the mission-switch ‘off’, then
insert the battery and make up it’s connector to
the power cable, Insert the motor-bulkhead and
forward bulkhead into the SD cylinder – check
that their O-rings have not been squeezed out of
the bulkhead grooves. Place a drop of oil on the
rubber element of the vent valve. Turn on the
transmitter. Is the Transmitter battery charged?
Turn on the SD mission-switch. Check for correct
operation of all functions. Check the Lipo-Guard
lights, do they indicate a fully charged battery?
Turn the SD system off, then turn the transmitter
off.
2. Check the SD system for leaks: Blank off the
snorkel induction flexible hose brass inlet nipple
of the five-point manifold (a short length of flexible
hose with a plug at one end makes a fine blank);
pull the end of the external flexible induction hose
form the motor-bulkhead nipple; put that end in
your mouth and take a suction – while holding the
suction, crimp the hose with a hemostat; put the
SD aside and wait at least three-minutes. Put the
open end of the flexible induction hose into an
ear, and listen for the inrush of air (a ‘whooshing’
sound) as you remove the hemostats jaws from
the hose. If you don’t hear the rush of air back
into the SD, then there is a leak somewhere and
you have to go through the SD leak-check
operations. If the SD is tight, proceed.
3. Reattach the flexible external induction hose to
the motor-bulkhead manifold and remove the
blanking hose from the five-point manifold.
4. Check the external induction plumbing for
leaks: Turn the transmitter and SD system; attach
the upper hulls snorkel induction flexible hose to
the five-point manifold, invert the sail (gravity
working on the snorkel float to ‘close’ the head
valve) and place the transmitters stick to the
‘blow’ position for ten-seconds. Leave the sail
inverted for thirty-seconds; then, with your ear to
the sail, quickly turn the upper hull right-side-up
and listen for a ‘whooshing’ sound as the snorkel
head-valve opens, permitting air to rush in to
break the partial vacuum within the SD created as
the LPB took a suction on SD internal air. If you
don’t hear the whooshing sound, there is a leak
somewhere in the external induction plumbing.
Find and fix the leak before proceeding.
MISSION
CAUTION: Never ‘hover’ the submarine
employing the SAS sub-system – once you
commence a blow from depth, continue the
evolution until the sail totally broaches the
surface. Failure to equalize the pressure within
the SD after a ‘blow’ (with the snorkel head-valve
immersed) will result in a pressure-differential
across the LPB that, at some point, will increase
where ballast water can no longer be pushed out
using SD air as the source.
While at the lake or pool it’s a wise practice to
maintain a written account of problems
encountered during operation of your model
The Moebius Skipjack R/C Conversion Instructions
Page 20
Popular Toy manuals by other brands

Hasbro
Hasbro Spiderman 3 New Goblin Spider Slayer 69129 instruction manual
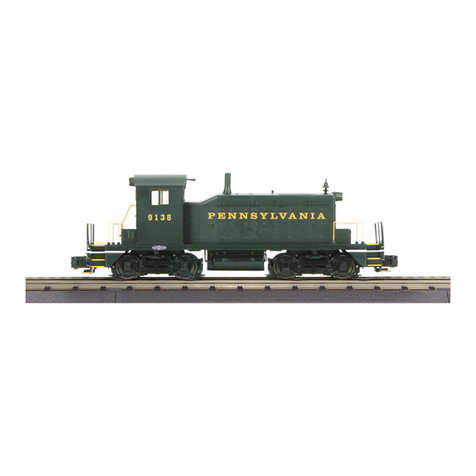
MTHTrains
MTHTrains Rail King SW-1 Diesel Engine Operator's manual
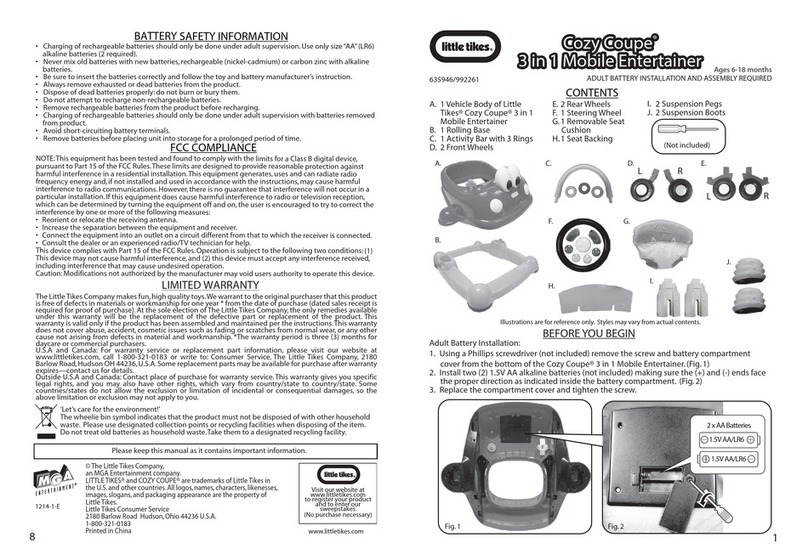
Little Tikes
Little Tikes Cozy Coupe 3 in 1 Mobile Entertainer manual
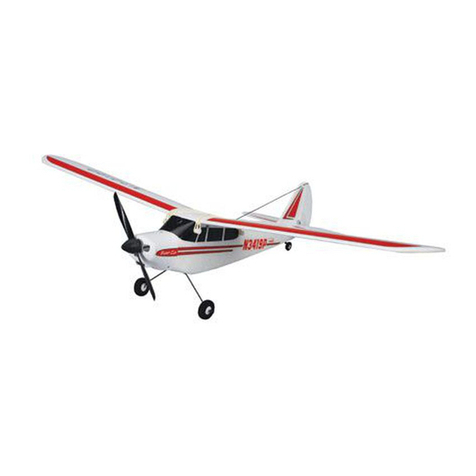
HobbyZone
HobbyZone HobbyZone instruction manual

Eduard
Eduard SS528 instruction sheet
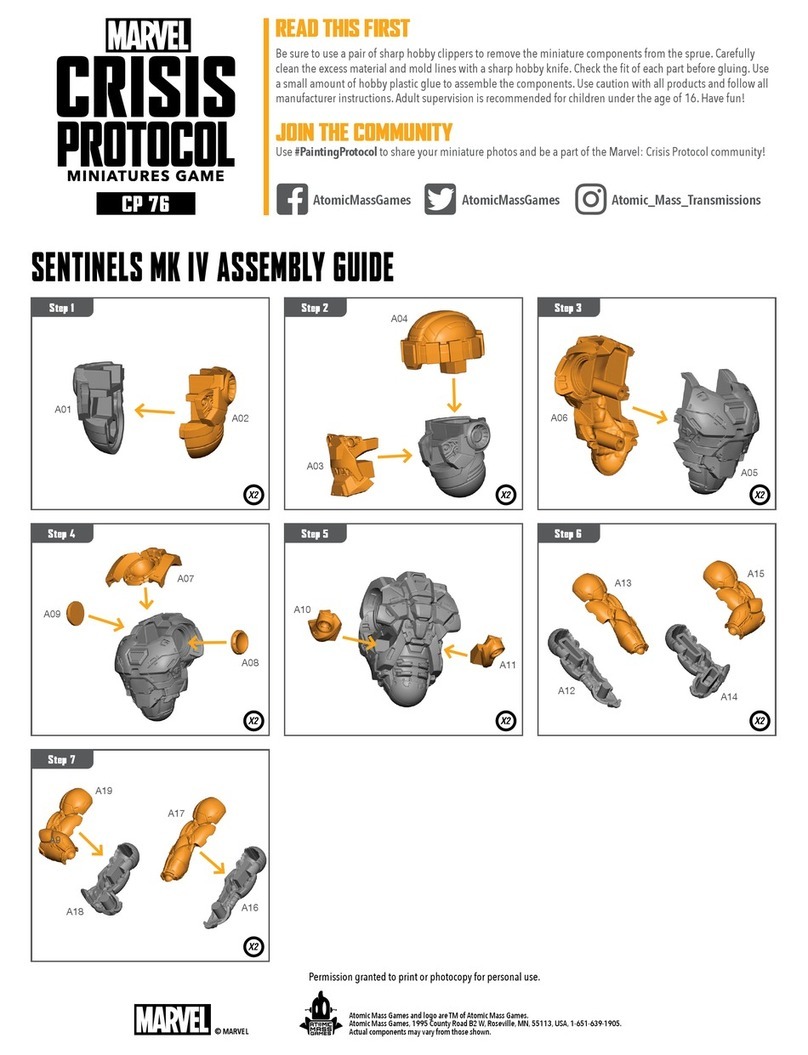
ATOMIC MASS GAMES
ATOMIC MASS GAMES MARVEL CRISIS PROTOCOL MINIATURES GAME SENTINEL MK... Assembly guide