Alamarin Jet Jet-160 Operating instructions


Repair Manual 1 2
Version 1.00
Version 1.00
alamarin-jet
water jet propulsion unit
REPAIR MANUAL
Alamarin-Jet Oy has published this manual in order to guide the owners and users as
well as companies carrying out repairs to
alamarin-jet
water jet propulsion unit .
Alamarin-Jet Oy has published other manuals separately for technical designers, users
and mechanics.
From here on in this manual the
alamarin-jet
water jet propulsion unit will be refer-
red to as ”jet”. This term refers exclusively to a propulsion unit manufactured byAla-
marin-Jet Oy.
The instruction covers the following jet propulsion models:
Jet-160 Jet-180 Jet-185
If the given information is type specic, this will be expressed in the text.
Clarifying gures will be used in this manual.
NOTE - the text includes a warning of a slight danger or a possibility of minor damage to equip-
ment
HINT - the text includes useful additional information or a hint which facilitates the work perfor-
mance or procedure
STOP!
SERIOUS DANGER - the text includes a warning of danger to life
WARNING - the text includes a warning of a danger that can lead to personal injury, breaking
down of equipment or serious malfunction of equipment
WARRANTY
GUARANTEE MATTER - the text includes a guarantee clause
Symbols used in the Repair Manual:
ARROW DESCRIBING MOTION
INDICATOR ARROW
XPART MARKING

Version 1.00
3 Repair Manual 1
Version 1.00 Version 1.00
Index 3
List of Appendixes ...............................................................................................4
1. Drive Shafts and Coupling Flanges.................................................................5
1.1. Joint Types...............................................................................................5
...1.1.1. Constant Velocity Shaft.....................................................................5
...1.1.2. Rubber Joint......................................................................................6
...1.1.3. Cardan Shaft.....................................................................................6
1.2. Tightening the Fastening Screws.............................................................6
1.3. Balance....................................................................................................6
1.4. Coupling Flanges.....................................................................................7
2. Bearing and Main Shaft...................................................................................8
2.1. Front Bearing ...........................................................................................8
...2.1.1. Disassembly......................................................................................8
... 2.1.1.1. Jet-160.......................................................................................8
... 2.1.1.2. Jet-180/185..............................................................................11
...2.1.2. Assembly and Installation ...............................................................13
... 2.1.2.1. Jet-160.....................................................................................13
... 2.1.2.2. Jet-180/185..............................................................................14
2.2. Rear End Bearing Disassembly and Assembly......................................15
3. Impeller..........................................................................................................17
3.1. Detachment............................................................................................17
3.2. Repair.....................................................................................................17
3.3. Installation..............................................................................................18
3.4. Type........................................................................................................20
4. Reversing Deector and Control Shafts ........................................................22
4.1 Reversing Deector.................................................................................22
...4.1.1. Detachment.....................................................................................22
...4.1.2. Repair .............................................................................................23
...4.1.3. Installation.......................................................................................23
5.Steering Nozzle and Shafts............................................................................24
5.1. Steering Nozzle......................................................................................24
...5.1.1. Detachment.....................................................................................24
...5.1.2. Repair .............................................................................................24
...5.1.3. Installation.......................................................................................25
5.2. Control Shafts ........................................................................................25
6. Stator.............................................................................................................25
6.1. Detachment............................................................................................25
...6.1.1. Detachment One Part at a Time .....................................................26
...6.1.2. Detachment as Whole.....................................................................26

Repair Manual 1 4
Version 1.00
Version 1.00
6.2. Repair......................................................................................................... 27
6.3. Installation.................................................................................................. 27
7. Electronic Reversing Deector Control.............................................................. 27
7.1. Installation Instructions............................................................................... 28
7.2. Adjustment Instructions.............................................................................. 29
APPENDIXES
Appendix 1. Recommended Greases and Tightening Torgues............................. 30
Appendix 2. Impeller Dimensions.......................................................................... 31
Appendix 3. Ordering a Spare Part Impeller.......................................................... 32
Appendix 4. SE-01................................................................................................. 33
Appendix 5. SE-02................................................................................................. 34
Appendix 6. Exploded Views................................................................................. 35

Version 1.00
5 Repair Manual 1
Version 1.00 Version 1.00
1. Drive Shafts and Coupling Flanges
Between the jet and the engine there is always an intermediate shaft which transmits the
power from the engine to the jet propulsion unit’s main shaft. There are various types of
shafts. Normally, the shaft has been chosen and installed by the boat’s manufacturer.
1.1. Joint Types
A constant velocity shaft is a cardan shaft between the engine and the jet, which allows
angle deviations. The joints are based on balls rolling on a spherical surface. This shaft
type enables vibration-free running even if the joint angles at different ends of the shaft
deviate from each other.
1.1.1. Constant Velocity Shaft
Detachment, Repair and Installation
At the engine side the constant velocity shaft is attached to the ywheel, to a coupling
ange installed by the engine manufacturer or to the gearbox. There can be an adapter
ange between the joint and the engine, with which the engine and shaft hole spacings
are tted with each other.
There can also be an adapter ange between the jet’s coupling ange and the joint.
Open the joint fastening screws
at the jet side and leave the pos-
sible adapter attached to the
coupling ange. The bolts can
be hex or socket screws (gure
1.1.1-1).
Open the joint fastening screws at the engine side and leave the possible adapter at-
tached to the ywheel.
The rubber covers and the whole end of the joint are removable parts of the constant
velocity shaft.
If the rubber cover of the joint is broken, lubricating grease comes out and the danger is
that the whole joint may break down. A broken rubber must be replaced immediately.
Follow the manufacturer’s instructions in repair and installation.
Figure 1.1.1-1

Repair Manual 1 6
Version 1.00
Version 1.00
The rubber joint is an elastic rubber element on the intermediate shaft between the en-
gine and the jet. The rubber element dampens the vibrations and sudden torsional loads
that are transmitted from the engine to the boat’s hull, and allows some angle deviation.
An intermediate shaft equipped with rubber joints is installed similarly to a constant
velocity shaft. Because the shaft, engine and jet propulsion unit anges are not always
compatible, it is usually necessary to use adapter anges.
There are various types of intermediate shafts equipped with a rubber joint. The
manufacturer’s instructions must be followed in repair and installation.
1.1.2. Rubber Joint
1.1.3. Cardan Shaft
The cardan shaft has been pivoted with spider bearings. The joint angles at different
ends must be of equal size to attain vibrationless and durable running.
The cardan shaft has been installed similarly to the constant velocity shaft. Adapter an-
ges are used sometimes because the shaft, engine and jet propulsion unit anges are not
always compatible.
1.2. Tightening the Fastening Screws
The following information will serve as general instructions:
Always tighten the fastening screws of the coupling anges ngertight rst and after
that in a crosswise sequence gradually until they are at the correct torque. This ensures
that the joint is attached evenly to the coupling ange.
However, check with the manufacturer that possible instructions given separately by the
manufacturer are followed in tightening.
Use thread locking compound to tighten the bolts. Observe the manufacturer’s instruc-
tions on using a thread locking compound.
1.3. Balance
The balance and correct installation of the intermediate shaft on the joints at different
ends is imperative to a functioning whole. Unbalance of the intermediate shaft, anges
that have been tightened or attached incorrectly cause the equipment to break down very
quickly.

Version 1.00
7 Repair Manual 1
Version 1.00 Version 1.00
Figure 1.4-3
IF AN INTERMEDIATE SHAFT THAT HAS BEEN INSTALLED
OR BALANCED INCORRECTLY CAUSES DAMAGE, THE GUA-
RANTEE IS NOT VALID!
WARRANTY
1.4. Coupling Flanges
Different kind of coupling anges are installed to the jet’s main shaft depending on the
type of the intermediate shaft and engine power. Commonest of these are SAE 1310,
VNA 10.
If necessary, there is an adapter between the coupling ange and the transmission shaft,
which enables fastening.
Removing:
The coupling ange is tightened on the conical shaft end with an M16 nut. Unscrew the
nut (gure 1.4.-1) and pull the ange off the cone with a puller (gure 1.4-2). There is
a spacer under the fastening nut, which presses the shaft on the coupling ange. Never
install the coupling ange without the spacer. Remove the wedge from the groove (-
gure 1.4-3).
Figure 1.4-1
Figure 1.4-2

Repair Manual 1 8
Version 1.00
Version 1.00
The shaft can be stopped from rotating with a bolt that is pushed
through the fastening screw hole against the surface of the bearing
housing. See gure 1.4-1.
Different models have different types of bearing housing structure. This does not affect
the fastening of the coupling ange.
2. Bearing and Main Shaft
2.1.1. Disassembly
2.1. Front Bearing
2.1.1.1 Jet-160
The bearing housing is xed in the casting. Only the support bearing housing is remova-
ble.
Before the shaft can be disassembled, the reversing deector, the steering nozzle, the
stator (see sections 4-6), and the impeller (see section 3) must be removed from the rear
of the jet. The boat must be out of the water.
Remove the coupling ange as described in section 1.4.
Open the fastening screws of the support bearing housing (6 pcs) as in gure 2.1.1.1-1
and remove the support bearing housing (gure 2.1.1.1-2).
Figure 2.1.1.1-1
Figure 2.1.1.1-2

Version 1.00
9 Repair Manual 1
Version 1.00 Version 1.00
The shaft protrudes into the en-
gine room with the bearings. The
t may be tight, but when pushed
from the outside, enough force is
produced to remove the shaft (gu-
re 2.1.1.1-3).
There are still two shaft seals in
the bearing housing. They can be
removed with for example a sc-
rewdriver.
Figure 2.1.1.1-3
The bearing (gure 2.1.1.1-4) consists of a thrust bearing that receives the pure axial
force (A) and an angular ball bearing that carries radial loads (C). The plate (B) between
the bearings transmits thrust from the thrust bearing to the outer race of the angular ball
bearing.
The safety ring (D) prevents the bearings from sliding off the shaft. The actual forces
are received with the shoulder in the support bearing housing, which presses on the ou-
ter race of the bearing.
A
B
C
D
Figure 2.1.1.1-4

Repair Manual 1 10
Version 1.00
Version 1.00
To remove the bearings, rst
remove the safety ring (A) and
then push the bearings off the
shaft (B) (gure 2.1.1.1-5).
A
B
Figure 2.1.1.1-5
Figure 2.1.1.1-6
There is a needle bearing in the
support bearing housing, which
carries radial forces. There is a
shaft seal behind the bearing,
and a safety ring in front of it,
which stops the bearing from
sliding out from the bearing hou-
sing.
To remove the bearing, rst re-
move the safety ring (gure
2.1.1.1-6) and then push the seal
and the bearing from the seal
side at the same time.

Version 1.00
11 Repair Manual 1
Version 1.00 Version 1.00
2.1.1.1 Jet-180/185
In removing the shaft, the Jet-180/185 requires the same procedures as the Jet-160.
Open the fastening screws of the support bearing housing (4 pcs) and remove the sup-
port bearing housing (gures 2.1.1.2-1 and 2.1.1.2-2).
The actual bearing housing is attached to the body with sealing and
adhesive compound. It is not necessary to remove it, unless it is dama-
ged.
Figure 2.1.1.2-1 Figure 2.1.1.2-2
The shaft protrudes into the engine
room with the bearings. The t may be
tight, but when pushed from the outsi-
de, enough force is produced to remo-
ve the shaft (gure 2.1.1.2-3).
Figure 2.1.1.2-3
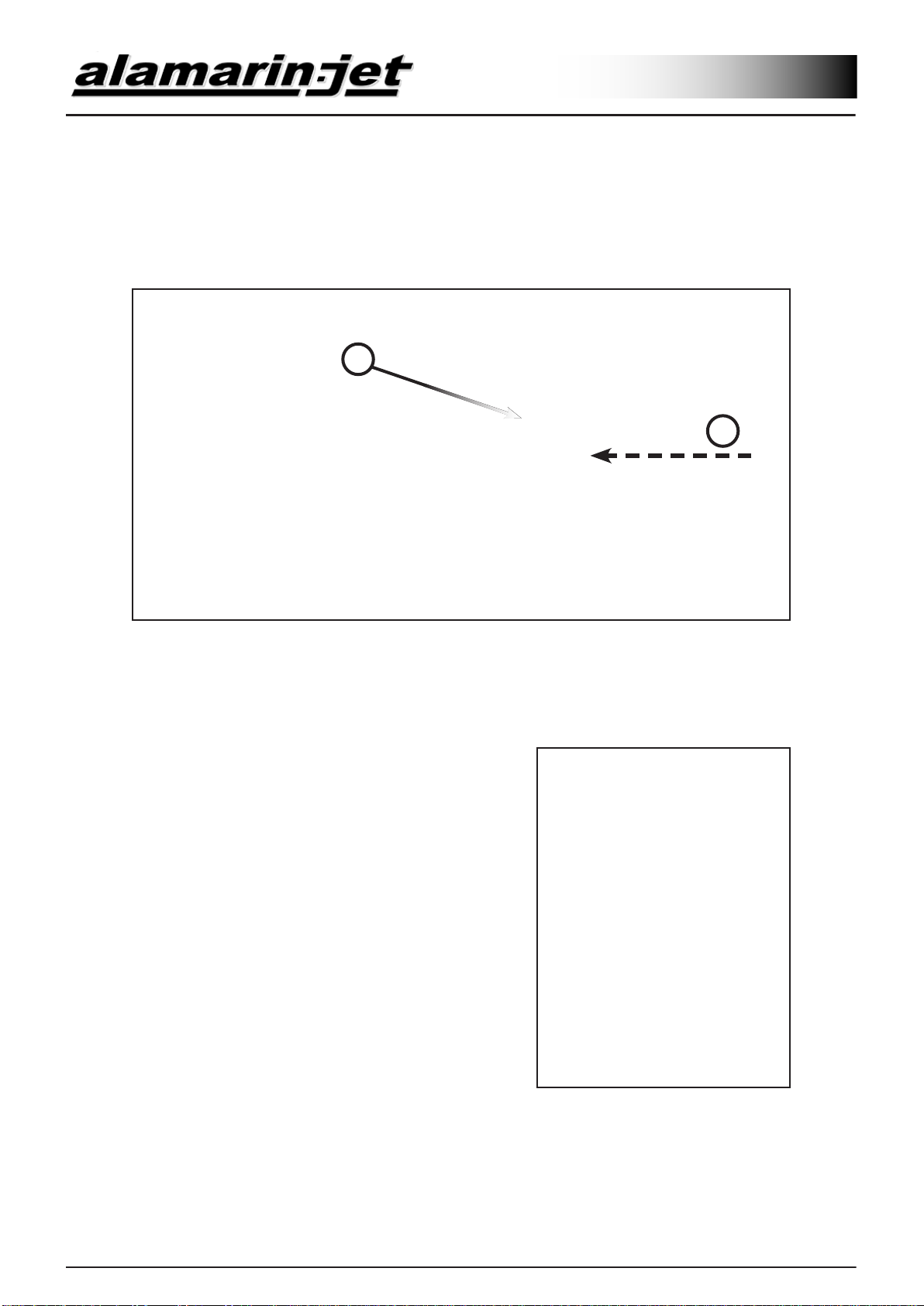
Repair Manual 1 12
Version 1.00
Version 1.00
One four-point bearing is tted to the shaft, which receives the thrust and carries some
radial loads. The safety ring (A) stops the bearing from sliding off the shaft. The actual
forces are received with the shoulder in the support bearing housing, which presses on
the outer race of the bearing. See gure 2.1.1.2-5.
A
Figure 2.1.1.2-5
B
To remove the bearing, remove the safety ring and push the bearing to the direction of
the safety ring groove (B). See gure 2.1.1.2-5.
Figure 2.1.1.2-6
Behind the safety ring in the support
bearing housing is the actual groove
ball bearing that carries radial forces.
Behind the bearing there is a shaft seal.
To remove the bearing, rst remove
the safety ring and then push the seal
and the bearing from the seal side at
the same time (gure 2.1.1.2-6).

Version 1.00
13 Repair Manual 1
Version 1.00 Version 1.00
Figure 2.1.1.2-7
There is one shaft seal in the bearing
housing. There are two additional seals
between the bearing housing and the
body, so the bearing housing must be
removed to replace them. This is done
by pushing the bearing housing to the
direction of the engine room through
the intake duct. The easiest way to re-
move the shaft seals is e.g. with a sc-
rewdriver, but the bearing housing sur-
faces must not be scratched. See gure
2.1.1.2-7.
2.1.2. Assembly and Installation
2.1.2.1 Jet-160
Make sure that the bearing housing and
the support bearing housing are absolu-
tely clean.
Push the thrust bearing on the shaft.
The thrust bearing consists of three
parts. It is important that the parts are
placed on the shaft in the correct order.
The thrust washer (A), whose shaft
hole diameter is smaller, is placed rst.
The rolling element (B) is placed af-
ter this, and the thrust plate (C), whose
shaft hole diameter is larger, is placed
last. The spacer ring (D) that goes bet-
ween the bearings has to be installed
so that the relief goes on the four-point
bearing side. The four-point bearing (E)
and the safety ring are installed last.
A
B
C
D
E
Figure 2.1.2.1-1

Repair Manual 1 14
Version 1.00
Version 1.00
2.1.2.2 Jet-180/185
Make sure that the bearing housing and the support bearing housing are absolutely
clean.
If you also wanted to change the seals behind the bearing housing, the bearing housing
must be pushed off the housing. New seals are installed sequentially and the same way
up. Pay attention to the direction of the lips! As the seal is being pushed into place, the
lips must point away from the installer.
Push the shaft through the bearing hou-
sing so that the bearing denitely goes
to the bottom of the bearing housing.
Install a shaft seal in the bearing hou-
sing. The orientation of this seal is also
important, as a seal that is installed cor-
rectly stops grease from going into the
engine room. The lip must point at the
installer. See gure 2.1.2.1-2 (B).
Push the needle bearing in the support
bearing housing and place the safety
ring in the groove.
Place the shaft seals in the bearing housing. Pay attention to the direction of the lips! As
the seal is being pushed into place, the lips must point away from the installer.
WARNING! If the shaft seal is installed backwards, water gets into
the bearing housing! Also, make sure that the ring that supports the lip
is made of rubber. A steel spring will rust! See gure 2.1.2.1-2 (A).
The third, securing shaft seal is placed in the bearing housing. Continue to pay attention
to the direction of the lips!
Push the new bearing on the shaft and use bearing retaining compound to ensure the
xity of the inner race.
Place the safety ring into its the groove.
Push the shaft through the bearing housing so that the bearing denitely goes to the bot-
tom of the bearing housing.
Install a shaft seal in the bearing housing. The orientation of this seal is also important,
as a seal that is installed correctly stops grease from going into the engine room. The lip
must point at the installer.
Push the groove ball bearing in the support bearing housing and place the safety ring in
the groove.
WARNING! If the shaft seal is installed backwards, water gets into
the bearing housing! Also, make sure that the ring that supports the lip is
made of rubber. A steel spring will rust! See gure 2.1.2.1-2 (A).
A
B
Figure 2.1.2.1-2

Version 1.00
15 Repair Manual 1
Version 1.00 Version 1.00
2.2. Rear End Bearing Disassembly and Assembly
The rear end bearing is similar in Jet-160 and Jet180/185 models. Most commonly the
rear bearing is grease lubricated. The alternative is a water lubricated bearing. Remo-
ving and installing is done the same way in both cases.
Before the rear end bearing can be disassembled, the reversing deec-
tor, the steering nozzle and the stator (see sections 4-6) must be remo-
ved from the rear end of the jet. The boat must be out of the water.
The rear end bearing housing is glued
to the stator. It is possible to remove
the housing. When changing the rear
end bearings, it is recommended that
the whole housing is replaced. When
only changing the seals, they should
be replaced without removing the bea-
ring housing.
Shaft seals can be removed e.g. with a
screwdriver. When placing new ones,
the correct orientation of the lips must
be paid attention to! The lips must
point at the installer.
WARNING! If the shaft seal is installed backwards, water gets into
the bearing housing!Also, make sure that the ring that supports the lip is
made of rubber. A steel spring will rust!
After the stator has been re-
moved, the bearing housing is
pushed from the back until it
comes loose.
Figure 2.2-1
Figure 2.2-2

Repair Manual 1 16
Version 1.00
Version 1.00
When installing a new housing or water lubricated bearing, clean the old adhesive resi-
dues off the stator.
Figure 2.2-3
After removing the adhesive
residues, spread adhesive on
the outer surface of the bearing
housing (gure 2.2-3) and push
the bearing housing in place.
Wipe excess adhesive off the
area of the bearing housing and
stator seam.
Let the adhesive dry for 48 h
before installing the stator (NB.
the adhesive manufacturer’s
recommendations).
There is a replaceable wear
sleeve (gure 2.2-4 A) at the
rear end of the shaft. It is re-
moved by rst opening the bolt
(gure 2.2-4 B) and removing
the locking plate (gure 2.2-4
C) at the end of the shaft. Sea-
ling compound has been put
between the wear surface and
the shaft to prevent water ow,
which is why force must be
used to withdraw the sleeve.
Figure 2.2-4
After you have installed the rear bearing to the stator, and the stator has been installed
in place, remember to grease the rear bearing. Instructions for installing the stator have
been given in section 6.1.3.
Grease recommendation: See Appendix 1.
A
B
C

Version 1.00
17 Repair Manual 1
Version 1.00 Version 1.00
3. Impeller
3.1. Detachment
The boat must be lifted out of the water to remove the impeller. Before you can get to
the impeller, the reversing deector, the steering nozzle and the stator must be removed.
See sections 4-6.
Before the rear end bearing can be disassembled, the reversing deec-
tor, the steering nozzle and the stator (see sections 4-6) must be remo-
ved from the rear end of the jet. The boat must be out of the water.
Loosen the fastening screws of
the impeller and remove one of
the screws (gure 3.1-1).
Screw the screw into the threa-
ded hole (A) in the cone and
tighten carefully until the cone
loosens.
Take the bolt out of the threa-
ded hole and spin it loosely into
the free hole (B), i.e. back in its
original place.
Pull the impeller off the shaft. Figure 3.1-1
A
B
The plastic cone may still sit tightly
on the shaft, but it can be loosened
by pushing a screwdriver into the
opening in the cone and forcing the
cone open. See gure 3.1-2.
3.2. Repair
Faults with the impeller that require repair are slight bending and cracking of the blades.
If a blade has been bent, carefully tap it back to its former position. Compare the posi-
tion of the blade to the other blades.
After straightening, make sure that there are no cracks at the bending point. If there are
cracks, the blade must be repaired by welding.
If a piece has broken off the blade, it can be repaired by welding ller metal in the
crack. However, we strongly recommend to exchange the whole impeller.
Figure 3.1-2

Repair Manual 1 18
Version 1.00
Version 1.00
Welding can create heat stress, which may cause the impeller to bre-
ak when used. This is why the manufacturer is not responsible for the
breaking down of a repaired impeller.
Impeller material: GTp10
Filler metal: EL-CuSn7 (ESAB OK 94.24).
If the impeller has been repaired with ller metal, it is to be machined
if necessary and it is imperative that it be balanced!
3.3. Installation
Screw the adjuster sleeve (A)
and the possible additional ring
on the shaft. The sleeve has a
left hand thread, but the additio-
nal ring is unthreaded.
Place the wedge (B) in its groo-
ve (gure 3.3-1).
Figure 3.3-1
A
B
The place for the wedge groo-
ve (A) on the mounting cone
is marked on the impeller with
a line. Set the cone so that the
wedge groove is aligned with
the line (B) as in gure 3.3-2.
Figure 3.3-2
BA

Version 1.00
19 Repair Manual 1
Version 1.00 Version 1.00
Push the impeller with the cone
on the shaft (gure 3.3-3).
Tighten the screws ngertight
and push the impeller as far in
the intake duct as it goes.
Figure 3.3-3
When installing the impeller, be careful not to leave your ngers bet-
ween the impeller blade and the cone wall! Use the working position
shown in gure 3.3-3!
Tighten the screws to a torque
of 20 Nm. During tightening the
impeller recedes slightly out-
wards in the cone hole, which
causes the gap to adjust to the
correct size automatically. After
this, tighten the impeller adjus-
ter sleeve as tight as manually
possible. See gure 3.3-4 (A).
There can be a gap of 0.2 mm
between the impeller blade and
the cone (B). During installati-
on, the lower edge is touching
the cone and in the upper part
of the impeller there may be a
slightly bigger gap due to the
weight of the shaft and the im-
peller. This gap disappears when
the shaft is centered on the sta-
tor nally.
Too wide a gap between the cone and the impeller blade causes
loss of power.
Figure 3.3-4
AB

Repair Manual 1 20
Version 1.00
Version 1.00
If the impeller does not rotate properly after installation, open the impeller screws, pull
it out a little and tighten the screws again.
Close the inspection hatch.
Install the reversing deector, the steering nozzle and the stator in place as one whole.
(Section 6.1.3.)
Attach the loop joint on the reversing deector to the lever at the end of the control
shaft. (Section 4.1.3)
Attach the loop joint on the steering nozzle to the lever at the end of the control shaft.
(Section 5.1.3)
Add grease in the end bearing.
See grease recommendations in appendix 1.
3.4. Type
Impeller type is determined by engine power and maximum revolutions.
You can check the type by looking at the markings on stamped on the impeller (gures
3.4-1 and 3.4-2).
Figure 3.4-1
Figure 3.4-2
This manual suits for next models
2
Table of contents
Popular Engine manuals by other brands
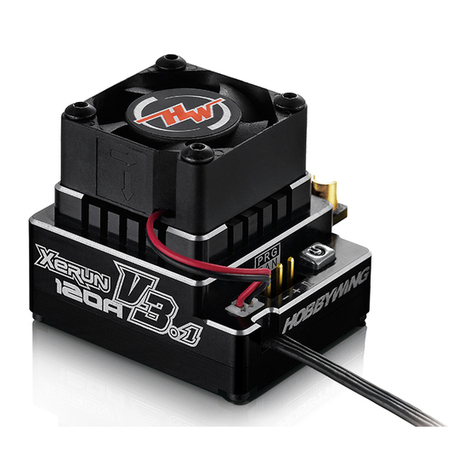
Hobbywing Technology
Hobbywing Technology XERUN-120A-V3.1 user manual
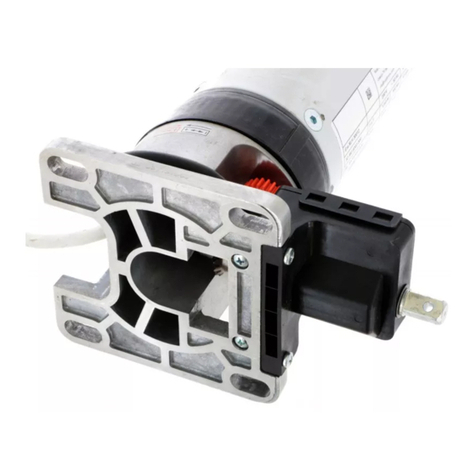
Nice
Nice ERA XL Instructions and warnings for installation and use
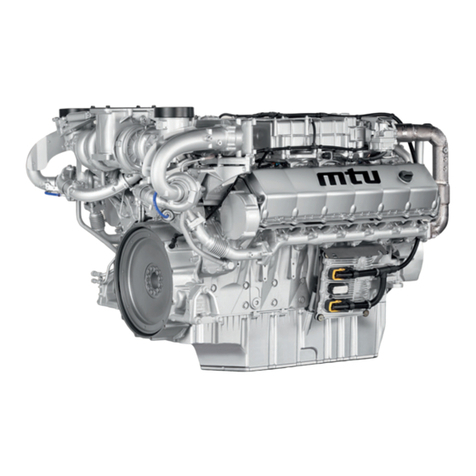
MTU
MTU 12 V 1600 R50 operating instructions

Wacker Neuson
Wacker Neuson M 1000 Operator's manual
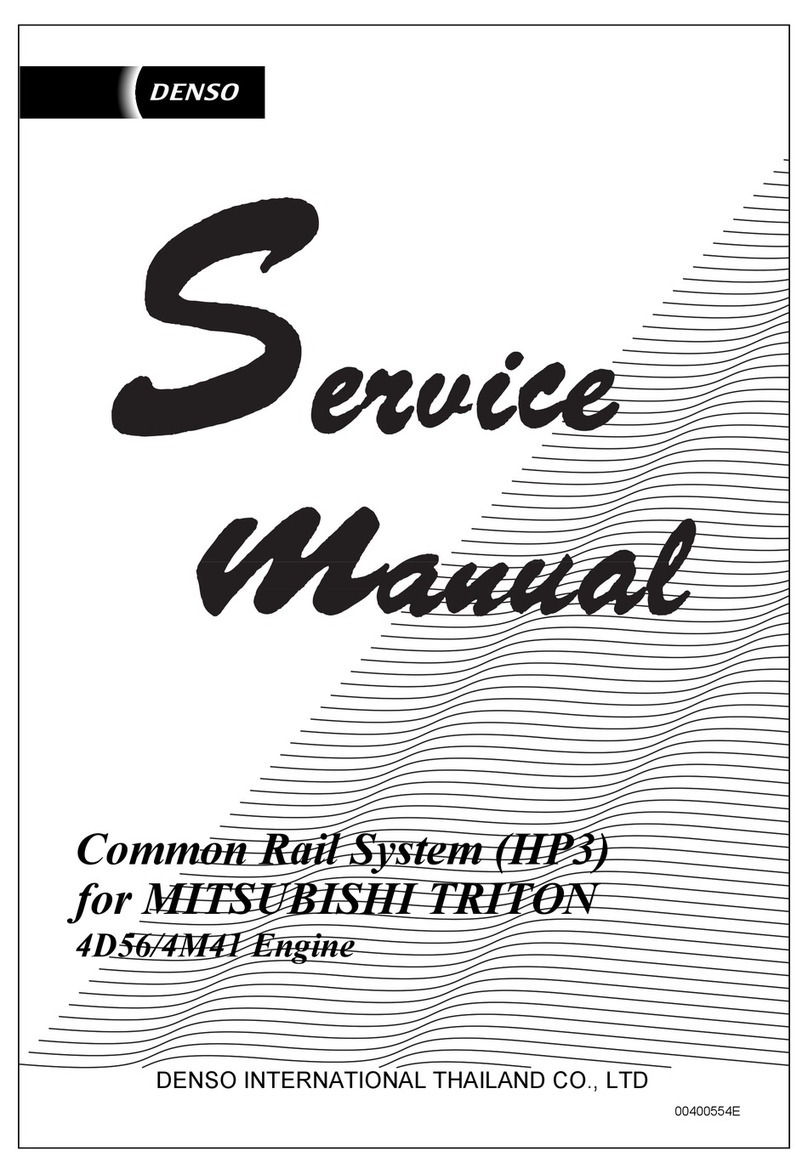
Denso
Denso 4D56 Service manual
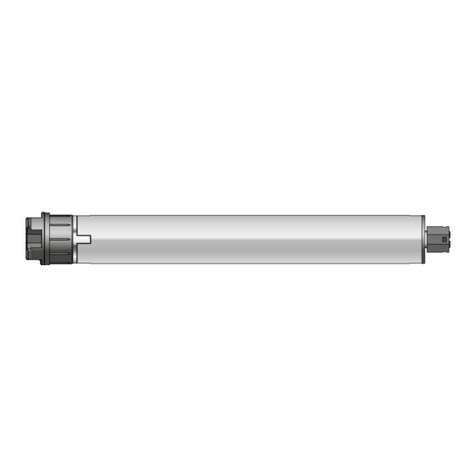
GEIGER
GEIGER GB45R Series Original assembly and operating instructions

Westerbeke
Westerbeke FOUR-60 Technical manual and parts list

Briggs & Stratton
Briggs & Stratton 110400 Operating & maintenance instructions
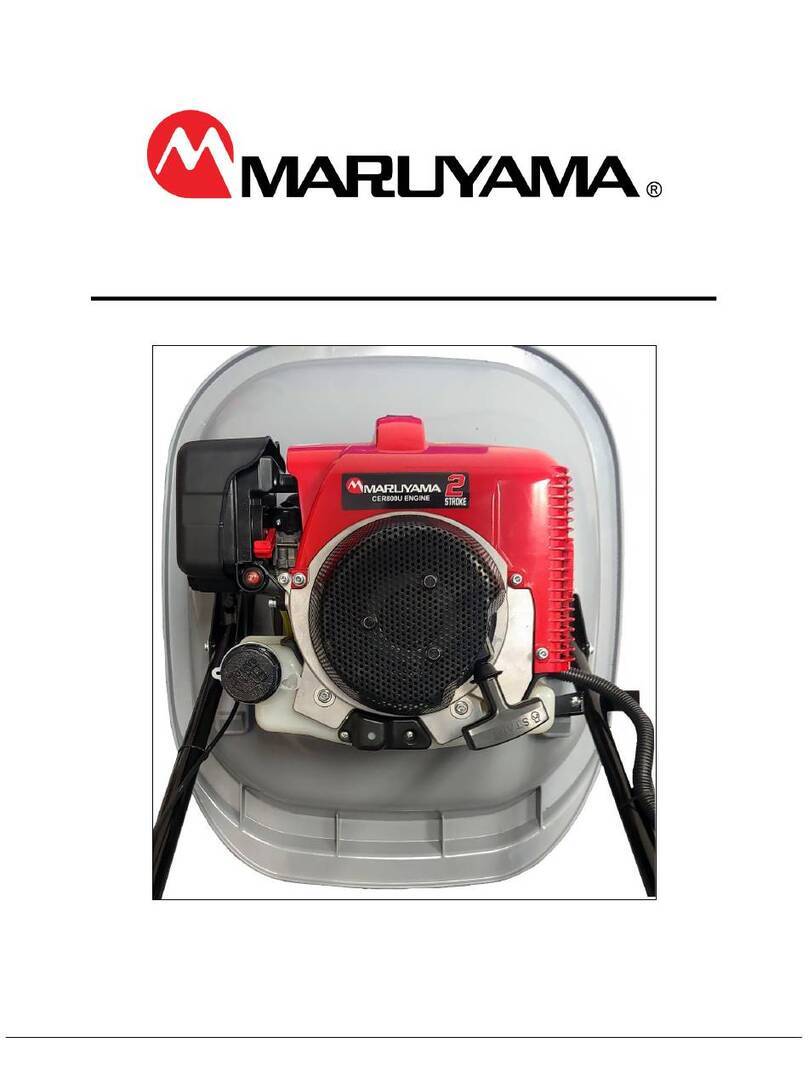
Maruyama
Maruyama CER800U Replacement
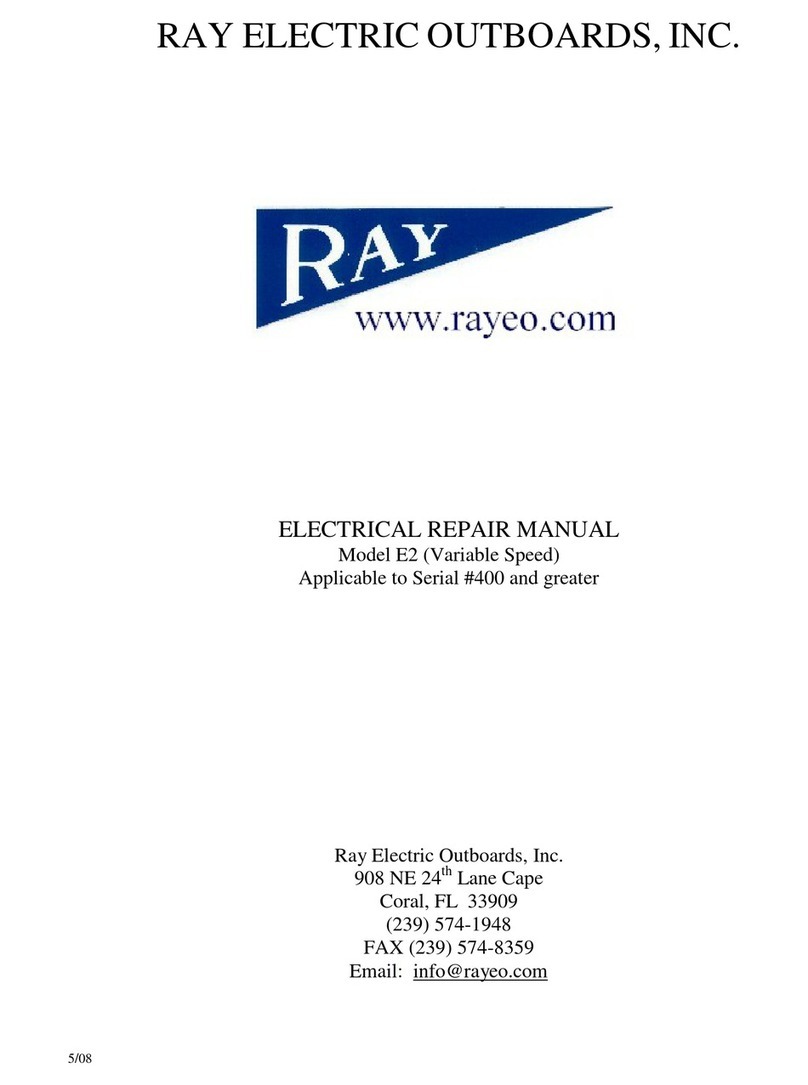
Ray Electric Outboards
Ray Electric Outboards E2 Repair manual
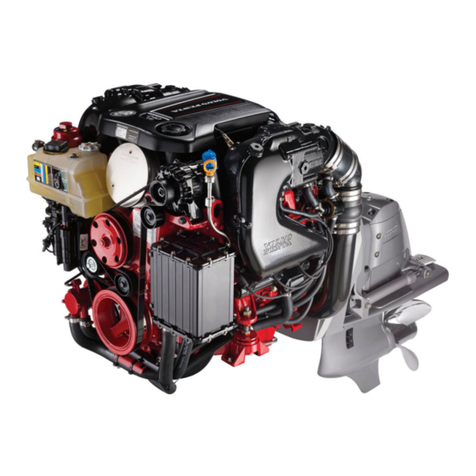
Volvo Penta
Volvo Penta V6-240 Operator's manual
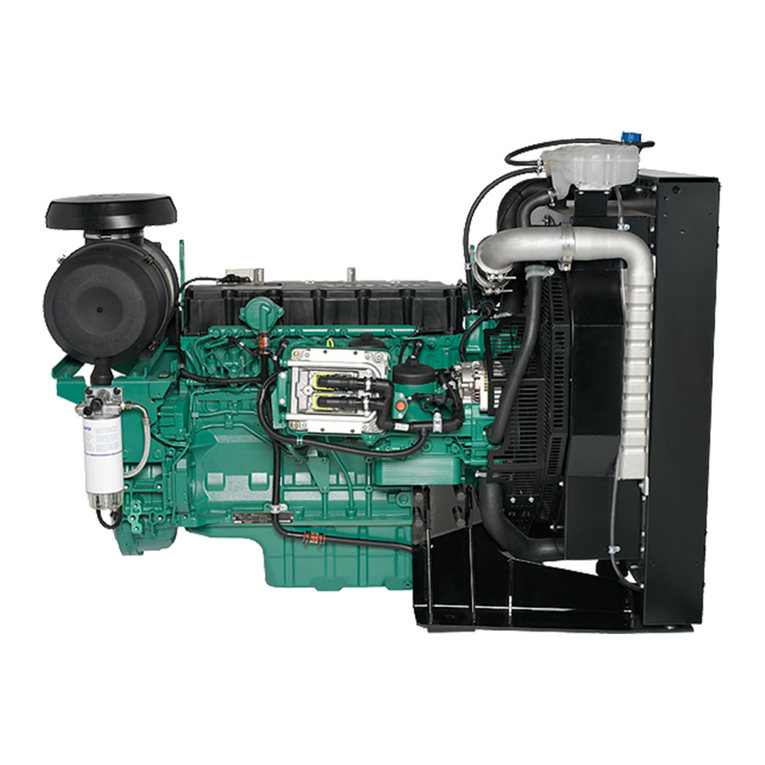
Volvo Penta
Volvo Penta TAD734GE manual