assemblage SET-300B User manual

A S S E M B L A G E
SET-300B POWER AMPLIFIER
Construction and Operation Manual

3
Dear Assembler,
Congratulations on purchasing the Assemblage SET-300B power amplifier. We are very proud of the Assemblage SET-300B, both
technically and perhaps more importantly, sonically. Utilizing modern, high quality parts, the SET-300B has been designed to provide
many years of trouble-free operation, using readily available tube types (these are tube types, which are still in production - and will
continue to be so).
Assemblage SET-300B Assembly Manual
Page Contents
4Parts List
5 Tools required
6SET-300B Functions
8Before You Start
9 Stripping/soldering instructions
10 Assembled PC Boards
11 Main PC Board Parts Placement Guide
12 Assembly Instructions
• Initial preparation-parts count schematic/numbering conventions
• First stage - board stuffing
• Second stage - bottom cover feet, transformer removal, installation of RCA jacks, mute switch, binding posts,
300B sockets, IEC module & input signal cable.
•Third stage - wiring of power transformer, output transformers, choke, IEC socket, and correct
configuration of power transformer primary windings (e.g. 100/120/200/220/240 V).
•Fourth stage - installation of PC boards
• Fifth stage - faceplate & power switch shaft mounting.
• Sixth stage - final check
• Seventh stage - last step
14 Schematics
19 Mono Block Operation Setup
25 Troubleshooting
25 Assemblage SET-300B Signature Upgrade and Preview
26 Specifications
27 Future Upgrades
27 Guarantees and Warranty
Warning and Disclaimer of Liability
When constructing this kit, take care that the assembly steps are followed precisely. Be aware that there will be dangerous high
voltages present in the amplifier. Under no circumstances does The Parts Connection or Sonic Frontiers International assume
liability or responsibility for injury or damages sustained in the operation or assembly of this equipment, or for damages to any
equipment connected to it. If you have any questions regarding the assembly or set up of the SET-300B, please do not hesitate to
contact us.
2790 Brighton Road, Oakville, Ontario,Canada L6H 5T4
Toll Free: 1-800-769-0747 (U.S. and Canada)
Telephone: (905) 829-5858
Facsimile: (905) 829-5388
Web Site: http://www.sonicfrontiers.com/TPC
E-mail: [email protected]

3
4
Parts List
Item/Value Qty/Unit Reference Designators
Printed Circuit Boards
qMain Board 1 Large main PCB
qPower Supply PCB’s 3 Filter Banks Main, Left and Right
qAC Switch PCB 1 Side mounted switch PCB
Semiconductors
qTL400G Bridge - 4A 200PIV 2 BR100; LBR100
qRB151 Bridge - 1A 1000PIV 1 BR400
qSF4007 - 1A 1000PIV 4 D1, 2; LD1, 2
qLED - Coool Blue 1 LED1
Capacitors
q0.1uF 50VDC 3 CC1, CC2, CC3
q0.47uF 400VDC (Sig) 2 C3; LC3
q470uF 16VDC (Sig) 2 C1; LC1
q100uF 100VDC (Sig) 2 C4; LC4
q220uF 160VDC 2 C2; LC2
q10uF 450VDC 5 C5, C6, C300; LC5, LC6
q100uF 400VDC 2 C200A, C200B
q220uF 400VDC 4 C202A, C202B; LC202A, LC202B
q470uF 400VDC 2 C201A, C201B
q4700uF 16VDC (Sig) 5 C100, C101, C400; LC100, LC101
q0.1uF 275VAC 1AC1
Resistors 1/2W
q1K Metal Film (Sig) 2 R2; LR2
q1K2 Carbon 1 RF1
q100R H4 HOLCO (Sig) 4 R5, R8; LR5, LR8
q100R Metal Film 8 R11, R12, R301, R302, R400,
R401; LR11, LR12
q475R Metal Film (Sig) 2 R3; LR3
q100K H8 HOLCO 2 R1; LR1
q249K Metal Film (Sig) 2 R10; LR10
Resistors 1-2W
q220K 2W 8 R205A, R205B, R206A, R206B,
R208A, R208B; LR208A, LR208B
q33K 2W (Sig) 2 R4; LR4
q68K 2W 4 R209A, R209B; LR209A, LR209B
q100K 2W 1 R300
q150K 2W 2 R210, LR210
Resistors 5W
q5R6 3W 4 R200, R201, R202, R203
q10k 3W (Sig) 2 R6; LR6
q0.56R 5W 4 R100, R101; LR100, LR101
q1K 5W 2 R207; LR207
q3K 5W 4 R13B, R13C; LR13B, LR13C
q3K9 5W 4 R13, R13A,; LR13, LR13A
q10K 5W 2 R7; LR7
q15K 5W 4 R9A, R9B; LR9A, LR9B
q6R8 5W 1 (+HV See text)
Trimpot
q200R 1/2W 2 VR1, LVR1
PC Board Hardware
q8 Pin PCB Mount Octal 5 V1, V2, V3, V6, V7
q#4-40 1/2” Stand-off 10 Under V1, V2, V3, V6, V7
q#4-40 1/4” SS Philips PH 20 V1, V2, V3, V6, V7 Stand-off’s
q#4 Lock Washer 10 V1, V2, V3, V6, V7 Stand-off’s
q#6-32 1/4” SS Philips PH 22 Holds PCB’s to Chassis Stand-off’s
q#6 Lock Washer 4 AC SW PCB & Under Ground
Screws
Item/Value Qty/Unit Reference Designators
Chassis Components
qMain Chassis 1
qMain Chassis Bottom Cover 1
qFront Panel - Aluminum 1
qSwitch Button 1
Transformers/Choke
qO/P Transformers 2
qPower Transformer 1
q4H 250ma Choke 1
Vacuum Tubes
q6SN7GT / 6H8C 1 V2
q6BX7GT 2 V1, V3
qGZ37 2 V6, V7
Chassis Mounted Hardware
qRCA Jack - RED (Sig) 1 RCA Audio I/P Right
qRCA Jack - WHITE (Sig) 1 RCA Audio I/P Left
qToggle Switch 1 Mute Switch
qDPST AC power switch 1 AC power switch
q4 Pin Ceramic Socket 2 300B sockets
qDual Binding Posts (1pr) (Sig) 2 Speaker Posts
qIEC Socket 1 AC Input
qBlack Rubber Chassis Feet (Sig) 4 Chassis bottom cover
qSolder lug #6 3/4” 2 Solder Lug
qFuse 2.5A or 1.25A Slo-Blo 1 F1
Mounting Hardware
qM3 10mm (3/8”) Blk CS screw 2 IEC socket
q#6-32 x 1/4” Zinc Philips 2 Solder lug attachment,
I/P Com. to Chassis
q#6-32 x 1/4” Blk Philips 12 Holds bottom cover
q#6-32 x 3/4” SS Philips 4 Feet
q#8-32 3/8” Blk Philips 2 Holds Choke
q#10-32 3/8” Blk Philips 12 Transformers
q#10 Blk Split Washer 12 Transformers
qNylon Washers 4 300B tube sockets
q#6-32 kepnut 4 Holds 300B Sockets
q#8-32 kepnut 2 Holds Choke
q#10-32 kepnut 2 Holds Faceplate
Hookup Wires & Associated
qShielded 4 conductor (Sig) 24” Shielded input cable
qHook-up Black 18awg 48” IEC socket, Spkrposts, Filter Banks
qHook-up Green 18awg 24” Ground wiring
qHook-up Red 18awg (Sig) 12” power supplies B+, B+1
qHook-up Brown 18awg 12” power supplies B+2, LB+2
qHook-up Blue 18awg 12” power supply B+3, LB+3
qHeat-shrink tubing Black 1/8” 6” IEC Terminals & LED
qHeat-shrink Tubing Black 3/16” 6” I/P and AC primary wiring
q#30 Twist Connectors 4 O/P Transformer Secondary
Configurations
qKimber Kable TCSS (Sig) 4” To 300B Grids
Miscellaneous
q3” Cable Ties 8 Transformer wires
qCable Tie Mounts 1 Power transformer wires
qExtension Shaft 2 AC Switch to Front panel button
qShaft Coupler 2 AC Switch to Front panel button
qNylon Blk Hole Plug 1 Hole plug for Level Control
knockout
qWondersolder 10ft
qSolderwick 1ft
q18/3 CSA Power Cord 6 Foot 1
qConstruction and Operation Manual (If you cannot locate this, we are in big trouble!)
qWarranty Card
Please note, if you are planning to install the Signature Parts Upgrade kit at this same time, take note of the parts labeled “Sig.” in this manual. Refer to the Parts
Upgrade Instructions for these replacement parts.

5
In addition to the parts supplied in the kit, you will need the following tools to complete construction of
the SET-300B kit.
1Pencil tip soldering iron of good quality (700°F tip temperature)
1 #0 Philips screwdriver
112mm wrench or ratchet (1/2” will also work)
110mm combination wrench (not shown) (3/8” will also work)
1 5/16” nut driver
1 Pair of needle nosed electronics pliers
1 Wire stripper or hobby knife (If you trust yourself with your fingers!)
1 Ruler/Scale (not shown)
1 Voltmeter (optional)
Tools Required

56
SET-300B Functions
B
C D E D
A
GEF

7
Control Functions
A LED
When the coool blue LEDis lit, the SET-300B is “ON”,
receiving power from the power supply.
B ON-OFF button
When in the ON position (button depressed), high
voltage power is received by the SET-300B circuitry
from the power source. Due to the warm up
characteristics of tubes, it will take 30 seconds for the
tubes to pass full signal. It is suggested that the
SET-300B remain muted or the volume control on the
preamp be turned down for this first minute. When in
the OFF position (not depressed), the SET-300B is not
receiving power and is not operational.
Connection Functions
C Detachable AC Power Cord Socket
Plug the Detachable Power Cord into this socket.
D Speaker Connection Posts
These 5-way binding posts accept a connection from
one pair of speakers. The negative connections are to
be made to the black connectors; left speaker to the
terminals marked left and right to the terminal marked
right.
E Preamplifier Input
This input accepts RCA input connections from an
external preamp or crossover; connect left channel to
left channel and right channel to right channel.
F Mute/Operate Switch
The input of the 300B may be muted via this switch.
This is handy when changing interconnect cables or
even isolating system components for trouble
shooting purposes.
G Optional Set - Control
This level control may a switched attenuator or
potentiometer from TPC or one of your own favorites.
This will allow a source device to be directly
connected to the amplifier input jacks thereby
bypassing an outboard preamp.
WARNING - DISCONNECTTHE AC DETACHABLE
POWERCORDFROMTHESET-300B ANDWAIT 5
MINUTES BEFORE REMOVING BOTTOM COVER,
TUBES OR FUSE.

78
Before you start assembling your SET-300B, please take a few
minutes to read this preface on the construction manual and the kit.
Zen and the Art of Electronics Assembly:
Assembling a high quality electronic device requires a certain frame
of mind. The object is not to rush through and get the kit assembled
as quickly as possible, but to methodically and correctly put together
the pieces of this audio jigsaw puzzle. The kit could take as long as 6-
8 hours to complete, so plan your attack accordingly and take breaks
often, you will find the natural places to do so as you go through the
assembly steps. The final kit appearance will benefit from your rested
mind.
If the instructions are followed to the letter, the amplifier will work
correctly right from the start. If you try to assemble the kit purely from
the pictures/illustrations without reading the body of the text, your unit
will most likely not work.
Please note that this kit is not intended for the complete novice. A
certain level of competency is assumed in electronics assembly - i.e.
the ability to solder, and to be able to use a voltmeter/multimeter.
General Instructions:
Where necessary a simple overview of the upcoming step is
presented to you before you actually do that procedure. This little
preamble will help to clarify the next assembly step and give you a
broader understanding of the construction methods to use, and
hopefully aid you in getting it right the first time. Following this is a list
of the parts or components that will be needed or constructed in this
immediate section, then a detailed description of the assembly
procedures for that section.
The top of the printed circuit boards is the one side that has the white
silk-screening on it. Therefore you know that the backside has no
screening on it and no parts, except it is the backside that the tube
sockets will be mounted to.
Parts Count:
While every precaution has been taken to ensure that you have
received a complete kit, your kit has been picked and packed by
humans. Therefore, please use the Parts List on page 4, to ensure
that you have all parts present and accounted for. Before you
convince yourself that something is missing, check again! Large
cardboard boxes are notorious for hiding small parts, as are the
packing materials.
Stuffing the PC Boards:
If you inspect the main board (this is the largest of the boards with
which your are supplied with), you will notice that all parts locations
have been labeled with the appropriate part reference designator.
Each different set of components has been placed in its own
individual bag, which has its own label which lists the part type. (You
will find the reference designators listed on the Parts List.) Therefore,
when you are asked to install the resistor R1, you simply procure the
labeled bag with that part in it. Once the part is installed and soldered
in place, you can check that component off the supplied checklist in
this manual. There are also several photos and diagrams detailing
parts placement to reduce any possible confusion that may arise
regarding parts placement. Please note too, that there may be some
subtle differences between some of the parts shown in the
photographs and those supplied with your kit. On occasion, our
technical staff may substitute parts with ones of equal or higher
quality.
NOTE: Talking about part substitutions, there are Signature parts
upgrade kits available for the SET-300B. These upgrade kits replace
components in the signal path, input wiring, power supply filter caps,
coupling caps, the addition of film bypass caps, and
vibration/isolation components. (see page 25 for details)
The parts for your Assemblage kit have been packaged into several
groups: capacitors, resistors, semi-conductors, and hardware. Each
component type is individually packaged to allow for ease of
identification.
The process of stuffing the main board with parts is in fact a relatively
simple procedure - Generally the sequence will be to simply obtain
the bag containing the appropriate part, carefully bend the leads,
place the part into the holes in the PC board, then solder and trim the
leads. (Please review our soldering instructions on the next page).
Soldering:
Let it be said once, to get it out of the way - all soldering must be done
with rosin core solder! There is no warranty on equipment in which
acid core solder has been used. Please use the silver solder
provided in the kit.
Wire Stripping:
Unless otherwise instructed elsewhere in this manual, the normal
procedure to ‘prepare’ a cut wire is as follows;
qTrim or cut the wire to the desired length.
qStrip back the wire jacket 3/16”(~5mm), to expose the wire inside.
Use your favorite tool, the knife or wire strippers. If you are using the
knife, please be careful and read the instructions on the following
page.
qTwist the wire strands to gather them together and then solder them.
This is called the ‘tinning process’.
Mechanical Assembly:
The SET-300B has been designed with ease of assembly in mind. To
this extent, the chassis has been designed with built-in standoffs, to
which the PC boards are attached. This allows the PC boards to be
easily installed and removed.
There is a minimum of wiring involved in putting this kit together -
generally the power transformer must be wired to the PC boards, the
output transformers connect to the speaker binding posts and the
300B sockets directly, and the IEC socket connects the power
transformer and AC switch board. The Mute switch and the input (I/P),
RCA jacks are wired to the Main PC board.
We will leave most wiring until the last few steps, as we will first
concern ourselves with correctly placing and soldering all the
components to the PC boards.
Please be sure to follow the installation instructions closely, because
some important mounting details etc. may be included in any step.
Before You Start - Kit Overview

9
Wire Stripping with a Knife
If you own a wire stripper, we’re assuming you know how to use
it. If not, and you are new to the world of audio construction, you
can use a hobby knife to do the same job. Simply cut around the
insulation leaving an appropriate length for the lead, be very
careful to cut only the insulator and not the wire itself. Pull the
excess insulation away and you have your lead. If the wire is
made of strands, twist the lead between your fingertips to keep
it from fraying.
• If a lead bender is not being used, hold the component (resistor,
capacitor, LED,...) with a pair of needle nose pliers and bend the
leads to the appropriate width so it can fit through the donut
pads in its position on the circuit board.
• DO NOT bend the leads by applying pressure to the component,
bend by pushing directly on the lead. Bend only as in the picture,
this will make it easier to remove the parts from the PCB in the
event that you may want to upgrade the part later, without
removing the PCB from the chassis.
•Position the component on the circuit board and hold it in
position as you bend the leads out.
• To help conduct the heat from the soldering iron, “tin” the tip of
iron by applying a touch of solder to the already heated iron tip.
Soldering
• Push the soldering iron tip against the lead and the foil
donut pad on the circuit board and hold for 2 seconds.
• Then apply the solder to the other side of lead, also
touching the donut pad. Let the heated lead and pad melt
the solder, not the iron tip. The solder should flow around
the lead.
• Remove the iron and solder and let the connection cool.
Trim off the excess lead.
• NOTE: When done CORRECTLY, by heating the lead and
foil donut pad simultaneously, the solder should flow
outward, gradually blending from the lead to the foil.
• When done INCORRECTLY, by just heating the foil pad
and not the lead, a hard rosin bead will surround the lead,
insulating it from the connection.
• An INCORRECT solder joint is also done by just heating
the lead and not the foil pad. Here a hard rosin bead forms
on the pad, insulating it from the lead.
• To correct these unacceptable solder joints reheat and if
necessary apply a little more solder.
•HINT:It is handy to keep a damp sponge nearby to clean
the iron’s tip after each joint is completed.
Solder Bridges - solder bridges usually happen when too much
solder is used, or the solder is dragged from one connection to
another when heat is applied. If a bridge develops, turn the
circuit board upside down and reheat the connection, allowing
the solder to flow onto the iron tip. Then resolder the connections
as before, being careful that just enough solder is used to make a
connection.

Assembled PC Boards

11
Main PC Board Parts Placement Guide

1112
Assembly Instructions
PC Board Preparations:
I know that you are more than ready to go, so lets start off by preparing
the printed circuit boards, (PCB’s).
Locate the “panelized” PCB and break them apart by twisting the board
or cutting at the bridging tabs, producing 5 separate printed circuit
boards.
The 5 boards are as follows;
qMain PCB (the largest one),
qLeft CH Filter Bank,
qMain Filter Bank,
qAC SW PCB,
qRight CH Filter Bank.
Using your file - debur the edges of all the boards where the bridging
tabs have left a jagged broken edge.
Then get ready to really start the assembly of your new SET-300B
amplifier. This is where you create those plumes of solder resin smoke,
which seems to lull you into your own private world. You know that
entrancing state that your mind invariably takes you to when you dwell so
deeply into the concentration of building something with your own
hands... Let these thoughts flow through your mind now, turn on your
soldering iron, and here we go!
PC Board Stuffing:
Please note that with the exception of the tube sockets and their
standoffs, all components mount on the silk-screened side of any of the
PC boards. Outlines for components are silk-screened on the PC board
to aid in the part identification and to facilitate the correct placement of
the components. Remember that the reference designators are also
included in the Parts List on page 4.
Following the stuffing sequence guide below, you simply obtain the bag
containing the appropriate part, carefully bend the leads, place them into
the holes in the PC board, and solder into place. Trim the leads from the
rear side and that is it! Repeat this process several times, and the
boards will be stuffed. Assembly proceeds in this order.
Rectifier Diodes & Bridges:
Very important: the band on the diodes must correspond to the band
on the diode outline on the PC board.
qD1,2 LD1,2 SF4007
Installing these Bridge Rectifiers correctly add an extra challenge, are
you up to it? CUE: Look for the “+” sign on the part to align with the PCB
markings.
qBR100, LBR100 TL400G
(Keep these cut leads they will be used later.)
qBR400 RB151
Resistors:
Important: Resistors identified with an asterisk “*” should be raised off the
PC board surface by approximately 3/16” (or 4mm), in order to aid heat
dissipation of that part.
Resistors: (Keep some of these small resistor leads for later use.)
qR1, LR1 100K Holco (Black w/white lettering)
qR2, LR2 1K (Sig)
qR3, LR3 475R (Sig)
qR5,8, LR5,8 100R Holco (Black w/white lettering) (Sig)
qR10, LR10 249K (Sig)
qR11,12, LR11,12 100R Metal Film (coloured stripes)
qR301,302, R400,401 100R Metal Film (coloured stripes)
qRF1 1K2
qVR1, LVR1 200R Trimpot - (Turn the trimmer pots to
their center position if they are not there already.)
Next these are all - raised above PCB 3/16” (4mm)!
qR4, LR4 33K 2W* (Sig)
qR209A, B, LR209A, B 68K 2W* On Left & Right CH Filter Banks
qR300 100K 2W*
qR210, LR210 150K 2W* On Left & Right CH Filter Banks
qR205A,B, R206A,B 220K 2W* On Main Filter Bank
qR208A,B, LR208A,B 220K 2W* On Left & Right CH Filter Banks
qR6, LR6 10K 3W* (Sig)
qR200, R201, R202, R203 5R6 3W*
qR13, R13A, LR13, LR13A 3K9 5W*
qR13, B, C, LR13,B, C 3K 5W*
qR7, LR7 10K 5W*
qR207, LR207 1K 5W* On Left & Right CH Filter Banks
qR402, 9B, LR9A, B 15K 5W*
qR100,101 LR100,101 .56R 5W*
8-Pin Tube Socket Installation on the Main PCB:
As noted above, all of the tube sockets will be mounted on the rear side
of the Main PCB. (The side with no white silk-screening on it). Notice the
labeling on the PCB -”REAR SIDE SOCKET”.
You will need to gather these parts:
q8 Pin PCB Mount Octal Sockets x5
q4-40 x 1/4” Philips screw, Pan head x20
q #4 Internal tooth lock washer x10
q 4-40 1/2” Hex. Aluminum Stand-off x10
qAs a sub-assembly, loosely screw the standoff’s to each of the octal
sockets using the 4-40 screws, (no washers used here). The 2 standoff’s
point in the same direction as the socket pins.
Note that there is only ONE electrically correct orientation for these
8-pin sockets when placed into the PC board. Each socket has a central
hole with a notch groove. This is the indexing keyway, which must line up
with the silk-screen outline on the topside of the PC board.
qNow place the socket assemblies in their appropriate locations - do not
solder yet!
qFrom the component side, secure the socket sub-assembly to the PCB
with the 4-40 screws and #4 lock washers.
qTighten up the screws to hold the tube sockets securely to the stand-
offs. You may need to hold the standoff’s secure as you tighten the
screws.
qCheck again that the tube sockets are aligned properly. Now is the
time to solder the socket pins to the PCB.
qOnce the sockets have been soldered to the PC board, the ends of the
pins can be trimmed.
Capacitors - Electrolytic:
Did you know that electrolytic caps are polarity sensitive? Yes they are,
and do you know what happens to them if you put them in backwards?
Nothing, not until you apply power to them that is, then they BLOW UP in
a big puff of smoke!!! No kidding, so please take note of the picture that
shows the cap polarity. Look at the caps, the NEGATIVE leads or
terminals are all marked with a large wide band with a negative sign in it.
This then means that the opposite lead or terminal will be the POSITIVE
one. Align the Positive with the “+” sign on the PCB. Get this wrong and
your neighbours may end up knowing about it when they see the smoke
signals emanating from your work shop window.
+
–

13
qC1, LC1 470uF 16V (Sig)
qC2, LC2 220uF 160V
qC4, LC4 100uF 100V (Sig)
qC5,6, LC5,6, 10uF 450V
qC300 10uF 450V
qC100,101, LC100,101, 4700uF 16V (Sig)
qC400 4700uF 16V
qC200A,B 100uF 400V On Main Filter Bank
qC201A,B 470uF 400V On Main Filter Bank
qC202A,B, LC202A,B 220uF 400V On Left & Right CH Filter Banks
Capacitors - Film, etc.:
qCC1,2,3 .1uF 50V
qC3, LC3 .22uF 600V *** Keep these cut leads for
later use *** (Sig)
qAC1 .1uF 275VAC On AC SW PCB
Switch:
qSW1 DPST Push-On Push-Off switch for AC SW PCB
Miscellaneous Parts:
Wiring:
From the backside of the PC board, filament power needs to be
jumpered over to V1 from V3. Note the pair of enclosed pads that are
just above the two tube sockets. Look for the markings labeled “A >”,
and “< A”. These pairs of pads need to be connected together with
the green wires, and you need not worry about the polarity because
this is an AC filament voltage.
qGreen 18awg 7.75” (200mm) x 2
qCut 2 pieces of 18awg Green wire 7.75” (200mm) long and ‘prepare’
both ends for soldering.
qFrom the back of the PC board, insert and solder the pair of wires
into the empty pair of pads at V1.
qTwist these wires tightly together to take up the slack and then insert
the free ends into the pair of pads closest to V3.
Note: Do not thread this wire between the tube socket standoff and
its pins. The tube input grid pin 1 is too close for comfort here.
qAs you solder these into place check that you put them into the
grouped pads labeled “<A”.
qFrom the top of the PCB, trim the excess wires at both V1 and V3.
LED Indicator Light:
Because the distance from the PC board to the mounting hole in the
front of the main chassis/faceplate is greater than the length of the
LED leads, wire extensions must be soldered to the LED leads. Use
two resistor leads left over from the installation of the resistors. Two
1”(25mm) lengths are sufficient. Heat shrink tubing is then used to
cover and isolate the leads from any chance of a short circuit. This is
very important because the LED is supplied by the V1 & V3 filament
supply, which is biased up to a high DC voltage potential, which saves
the tube cathode from self-destruction. Then the LED leads are bent
to enable it to be mounted into the front panel hole.
qLED1 Coool Blue LED power indicator x 1
qcut leads x 2
q1/8” heatshrink tubing 1 5/8”(42mm) x 2
qAttach the two extension leads to the LED leads by first holding the
LED leads with a pair of needle nose pliers. See the photo please.
This is very important to do because the heat being applied while
soldering on the extensions can easily destroy the LED! We need to
keep this ‘coool blue’ LED cool!
The total lead length needs to be at least 1 7/8” (47mm) long.
qCut 2 pieces of 1/8” heatshrink tubing 1 5/8”(42mm) long.
qSlide the heatshrink tubing over the LED leads up to the LED body
and shrink it into place by heating the tubing with the soldering iron or
a hot air gun.
qNext we will bend the LED at a right angle according to the picture.
Pay close attention to the flat side of the LED body. LED’s are polarity
demanding. Align the LED flat side with the PCB screening. If your
LED does not have a flat side, then be sure that the long lead, or the
ANODE, connects to the round pad on the PCB, or the pad labeled
“A”.
qPut the LED aside for now because it will be easier to mount it later
after the PCB is installed.
This now completes the soldering of the PC boards. Just before you
take a break and admire your handy work... Go back and double-
check all your work. You know, look for the presence of solder bridges,
cold solder joints or missed solder joints, stray pieces of wire, leads
not trimmed, and check that all components are inserted correctly
with regards to polarity.
This is a good time to sample your favorite refreshments or get some
fresh air.
Bottom Cover & Main Chassis Assembly:
Welcome back. Next we will work on mounting of the feet, IEC socket,
RCA jacks, speaker binding posts, mute switch, and whatever other
parts or components that I can’t think of now that needs to assemble
to the chassis itself at this time.
Anxious to get going I know, but lets protect your investment a bit first.
Clean your work area from any foreign objects that may scratch the
chassis or transformers while they are on their back. You may want to
place a soft cloth or towel on your working surface to provide a safe
padded working environment.
Bottom Cover
Feet:
This simple step will get us off to a running start you might say. The
four rubber feet can now be fitted to the cover for the bottom of the
chassis.
qRubber Feet x 4 (Sig)
q6-32 x 3/4” Philips screws x 4
Using the 6-32 3/4” screws, bolt the feet in place in each corner of the
bottom cover. CUE: The feet will lie flat or will be flush to the surface
of the cover when mounted correctly.
qPut this cover aside for now we will need it later.
Main Chassis:
Place the chassis right-side-up in front of you on your clean scratch-
proofed surface.
17/16”
5/16”

14

15

1516
Transformer Removal:
Before proceeding any further, remove the transformers from the
chassis. This may make life a whole lot easier and avoid the chance
of damaging or scratching the transformers.
Why remove them you say, aren’t we trying to assemble this thing? Yes
we are but for one, they may be in backwards, and they will get in our
way for now. So out they come.
qUnscrew the screws holding the transformers in place - remove the
output transformers first! Then the power transformer can be
removed. Set all the transformers aside where they won’t get in the
way, we will, actually you will reinstall them later.
Now we may place the chassis up-side-down in front of you, again on
your clean scratch-proofed surface.
Choke Inductor:
Still in the mood for disassembly? Guess what gets removed now? If
you guessed the power supply filter choke, you where right. Do so
and put it aside for later. Put the nuts and screws in a safe place as
well.
Speaker Binding Posts:
Install the speaker binding posts, (yes I did say install), such that the
red post lines up with the “+” screening on the rear of the chassis, or
towards the top of the chassis, and the black post lines up with the
“-” screening on the rear of the chassis. Use the supplied washers
and nuts, and ensure that the posts are attached tightly to the chassis.
(5/16” nutdriver)
NOTE: Be aware that the individual post itself sits into a key-way in its
mounting housing.
qDual 5-way Binding Posts x 2 (Sig)
Be prepared, we are now entering into some of the more delicate
assembly procedures involved with this SET-300B construction kit.
300B Tube Sockets:
Here is an easy warm-up to what is to come. The 300B tube sockets
are to be correctly oriented, mounted to the chassis openings. The
nylon shoulder washer will cushion the ceramic socket from the
abrasive and crushing kepnut.
qCeramic wafer socket x 2
q#6 nylon washer x 4
q#6 Kepnut x 4
qView the top of the socket and notice that all the pin access holes are
NOT all the same size. There is a pair of large and small holes.
qSlide the socket over the two mounting studs flanking the two largest
chassis cutouts.
Be sure that the largest pair of socket holes are to the rear of the
chassis! Please be sure to get this correct, because there are no other
pin identifications on this ceramic wafer socket.
qInstall the nylon washers over the studs, and then the #6-32 kepnuts.
qSnug up the nuts, there is little chance that the socket will be
damaged, because of the compliant nature of the nylon washers.
qTo prepare the socket pins for the installation of the Main PC board,
we will now bend the solder lugs of these terminals inward toward the
center of the socket. See the photo for the finished look. CUE: Place
the MAIN PCB over the socket to see if the socket pins clear the
edges of the circuit board cutout.
qRepeat this procedure for the other 300B socket.
BeforeAfter
RCAInput Jacks:
Install the RCA jacks, making sure that the insulating washers are
correctly saddled within the chassis holes. The solder lugs will need
to be positioned properly for future connections and likewise for the
jack.
Right I/P
qRCA female jack with RED band x 1 (Sig)
qRed is for the Right channel I/P. Note the screening label “R” on the
chassis rear panel, indicating the Right channel I/P.
qFrom the inside working outwards, place the solder lug on the jack,
then the nylon shoulder washer.
qPlace these into the chassis hole from the rear.
qApply the flat nylon washer and then the nut from the outside.
(12mm nutdriver or wrench)
qNotice that the RCA jack signal terminal is notched. Align this notch
to face upwards towards you and while tightening the nut hold the
solder lug so that it points straight over to the opposite RCA jack.
qOne more finer detail, bend the solder lug out to 45 degrees from
the chassis. Check out the photo to ensure you get a clear picture of
this setup. You will be soldering to this lug later and we need good
access to it and this will also help to ensure that the wire lead
mounting into this hole will not come in contact with the rear chassis.
Left I/P
qRCA female jack with WHITE band x 1 (Sig)
qWhite is for the Left channel, I am sure you know where this one
goes, go for it.
qThis time the solder lug again points towards the opposite RCA jack
Mute Switch:
Having a mute switch is one of the nice features of this kit. The vertical
travel of the long bat handle makes it easy to access from the front
and unmistakable as to what position the control is in (Up for Mute,
and Down for Operate).
qDPDT toggle switch x 1
qThe switch mounts from the inside of the chassis along with the
indexing or anti-spin washer. Note that this washer also has a keying
position tab that must fit into the hole provided in the chassis.
RED WHITE
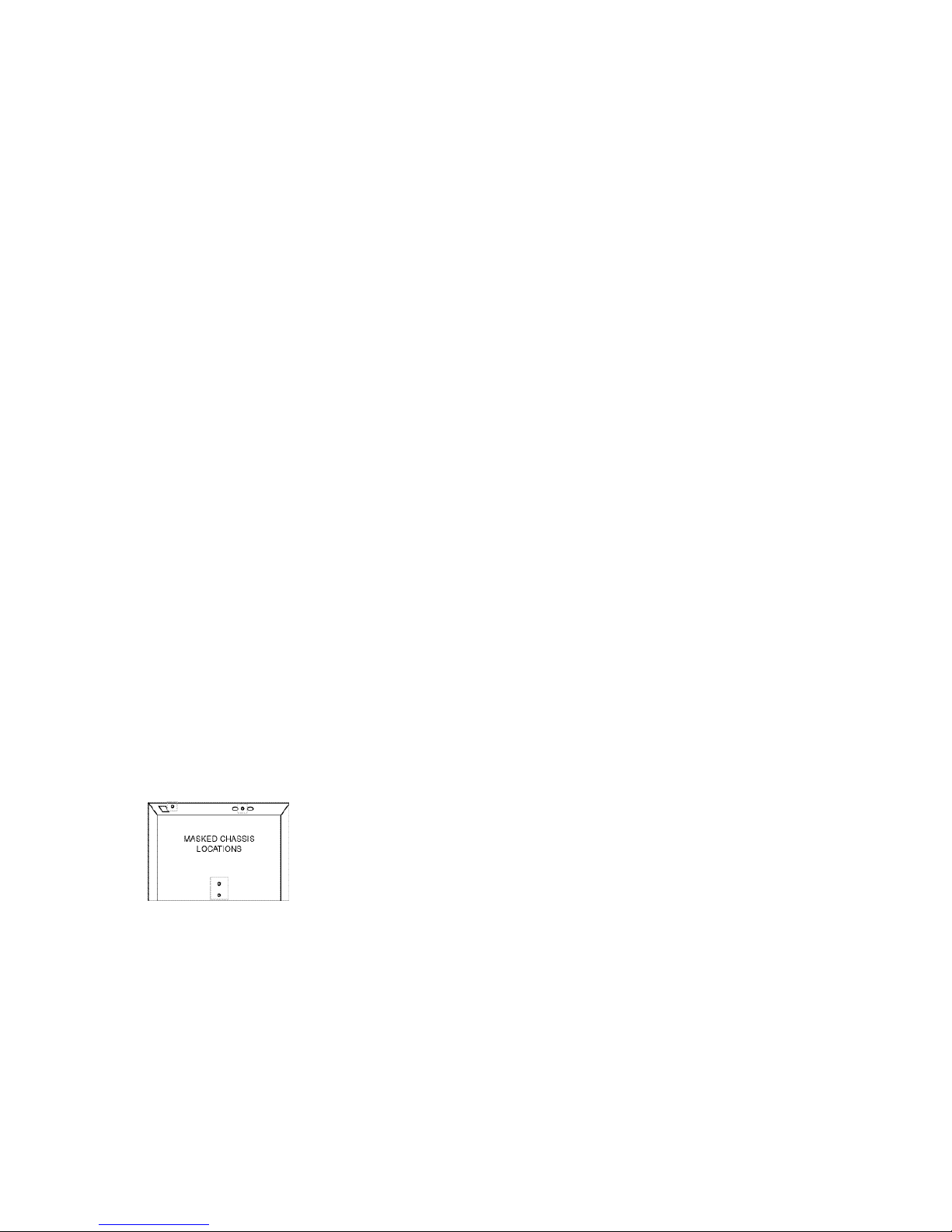
17
qFrom the rear side of the chassis screw on the switch nut using a
5/16” nut-driver, lightly tighten it. Installation of the lock washer is
optional. These switches can be delicate, be careful not to over
tighten the nut. Also note that the switch can be knocked and
damaged if you are not careful while handling the chassis.
RCAJack to Mute Switch Wiring:
Here is where your nimble little fingers will give you an edge over the
next guy. If you are a practicing brain surgeon or the S.W.A.T. team
bomb specialist, or simply an accomplished needle nose master, you
may find these next few steps entertaining. For the rest of you, just
take your time, what’s the hurry, I have not been timing you.
qTake a good look at the photo of these wired components and start
by taking one of the cut resistor leads and connecting it to one of the
eyelets of the RCA jack solder lugs.
qCrimp the lead into position through the hole on the RCA solder
lug.
qDo not solder it into position yet. The signal common wire needs to
be inserted into this hole later.
qDo the same on the opposite RCA solder lug.
qBring these two leads together onto the center terminals of the Mute
switch, bridging the left and right center switch terminals together as
well. Trim the length of the leads as necessary.
qCarefully solder these center terminals of the Mute switch to the two
ground leads.
qFind two more cut leads long enough to fit between the RCA center
signal pin and the top lug on the Mute switch. See the photo as
necessary.
qOne end of these leads wraps around the Mute switch top terminal
lug closest to its adjacent RCA I/P jack, and the other end is then
inserted into that RCA jack center pin hole.
qRepeat this for the opposite channel.
qAt this time solder the leads at the Mute switch only.
Chassis Solder Lug:
The single point chassis ground for this amplifier is located directly
between the RCA jacks and above the Mute switch, on the inside of
the chassis. If there is paint on the standoff top, it must be removed.
This is a good time to ensure that all chassis ground connection point
standoffs are free of paint. Note the 4 different standoff locations to
check for unwanted paint.
qsolder lug
q#6-32 1/4” zinc screw
qIf this standoff has no paint on its top surface, mount the solder lug
using a #6-32 1/4” zinc screw and bend the lug out to be like the
photo.
qNext, using one more cut resistor lead, wrap one end to the solder
lug on the chassis standoff. The other end connects to the center of
the ground connections made on the Mute Switch (center pins).
qSolder the connection at the Mute Switch only at this time.
Input wiring:
More fun to come doc’. We are now going to prepare both ends of the
Signal I/P cable and attach one end to the RCA jacks.
qShielded 4 Conductor Input x 24” (710mm) (Sig)
Signal cable
q3/16” Heatshrink tubing 1/2” (13mm) x 1
qCheck that this cable is no longer than 28” (710mm)
qOn one end of the cable, to be dubbed ‘the long end’, remove 1.5”
(38mm) of the outer insulating jacket. This is the signal input end of
the wire.
qOn the other end of the cable, to be dubbed ‘the short end’, remove
1.25” (32mm) of the outer insulating jacket.
qWith a sharp fine tip equipped utensil like a safety pin, carefully
unbraid the outer braided shield of this cable. Use the tip to
methodically comb back one braid bundle at a time. Settle back in a
comfortable chair because will take 5-10 minutes each end to do.
qDo the same on the opposite end.
qOnce you have unbraided the shields back to the jacket, on the
‘long end’ straighten and twist the shield wire into a nice single
conductor and cut it to 1” (25mm) in length. Tin this end.
qOn ‘the short end’ we do not need the shield at all. Please trim it right
back to the outer jacket.
qAt both ends, trim off the cotton filler material with your side cutters.
qNotice the colour coding of the 4 conductors. 1 pair has solid
colours and the other is not, it has a stripe. Twist into like pairs and
prepare and tin the ends by stripping off the standard 1/8” (32mm) of
the wires’ jackets.
Note: These conductors are not tin plated copper wire so you must
be sure to tin the ends thoroughly. The conductor jacket is
polyethylene so it can take the heat.
qBasically we now have a blue and a white wire in each twisted pair.
For clarification, we will use the SOLID Blue and White wires as the
Left channel, and the Blue wire will be the signal common for this pair.
qThe first connection to make with ‘the long end’, will be the Solid
Blue wire to the Left channel RCA jack solder lug (this is the jack to
your right). Simply slide this Solid Blue wire into the open solder lug
hole and solder both conductors into place.
qDo the same on the Right channel connecting the Blue w/white
stripe wire to the Right RCA solder lug hole.
qTo connect the remaining White wires, try to maintain the twisted pair
and position the wires into the holes of their respective RCA signal
input pins.
qSolder these connections to the RCA jacks.
qAlmost there, one more connection to make. That would be... to
connect the shield wire. Not sleeping I hope.
qLocate the chassis solder lug and notice that nice large
accommodating hole just waiting to be used. Solder the shield into
this position.
qFinally we will dress this cable by sliding a 1/2” (13mm) piece of
3/16” shrink tubing onto the cable from the free end. Slide it over the
exposed shield and wires as far as you can neatly do, then shrink into
position.
qTemporarily, you may want to tape this cable to the inside of the
chassis along its walls to the right side and then the front. This will
keep it out of harms way, not to mention testing your patience.
Well, was the operation a success? I hope so, because we are not
going back in.
IEC - AC Power Socket:
The IEC socket is the next component to be installed. I am sure that
you know that this is where the AC power cord is connected, but this
is also where the main power fuse is housed. Notice the small sliding
drawer below the receptacle opening, on the front side. You may even
notice that the fuse drawer will not open if the power cord is installed!
We will need to prepare and attach a few wires to this IEC socket
before we install it into the chassis, so here we go.
qBlack 18awg 4”(100mm) x 1 wire ‘A’
qBlack 18awg 2”(50mm) x 1 wire ‘C’
qGreen 18awg 2.5”(64mm) x 1 wire ‘B’
qHeat-shrink tubing 1/8” .5” (13mm) x 3
qIEC Socket x 1
qM3 10mm (3/8”) Blk CS screws x 2

1718
qM3 10mm (3/8”) Blk CS screws x 2
qSolder lug x 1
q 6-32 1/4” Zinc Philips screw x 1
<Insert IEC wired photo>
qPrepare the list of wires and heatshrink tubing to the lengths above.
Prepare the wire this time by stripping 1/4” (6.5mm) of the jacket off
the ends.
qFollowing the photo captions, attach the Black wires ‘A’ and the
Green wire ‘B’ to the terminals labeled ‘L’ and the center bottom
terminal, the ground, respectively.
qTry to insert the wires into the holes in the IEC terminals and crimp
or wrap the wire around the terminal before soldering.
qSlide the heatshrink tubing onto the black wire only and shrink it over
the terminal.
qThe 2” black wire is used to link the fuse terminal to the “L” terminal
on the back of the IEC module. Slide two pieces of heat shrink tubing
on the link, 1 for each end. The “L” terminal now becomes the bottom
left terminal in this Photo.
qFrom the outside, install the IEC module into the chassis with the
fuse drawer towards the bottom of the chassis.
qSimply bolt in place using the supplied M3 screws.
qNext screw the solder lug to the chassis standoff next to the IEC
module.
qThe green wire from the IEC module will be soldered to this lug now.
No heatshrink tubing is to be used on this connection. Loop the wire
through the solder lug hole, crimp and solder.
Main Chassis Assembly
Now we can start mounting and connecting the remaining hardware
like the choke, transformers and the PC boards, and finish off the
required wiring. Lets transform this basic black pizza box into an
amplifier!
Choke Mounting:
In the main power supply of this 300B amplifier we use a choke or
inductor plus capacitors in a pi filter arrangement. This AC ripple filter
works very efficiently in purifying the high voltage. This Choke is
mounted inside of the chassis. We will also prepare the leads for easy
installation to the Main Filter Bank PC board.
q#8-32 1/2” Philips screws x 2
q#8-32 kepnuts x 2
q4H Choke Inductor x 1
qBefore you jump the gun and install this piece of iron, we will dress
the leads. Tightly twist the black and white wires and trim them to 4.5”
(115mm) long and tin the ends.
qRelocate the choke mounting hardware that you put aside (#8 nuts
and screws), and relocate the two mounting holes in the center rear of
the chassis.
qOK now the choke is installed such that the wires exiting its end bell
are facing towards the left side or the IEC module.
qInsert the screws from the outside of the chassis, and tighten down
the kepnuts for the inductor into position with an 11/32” nut-driver
while holding the head of the screw with a Philips screwdriver.
Power Transformer Mounting:
The custom power transformer is the single transformer with the most
wires coming out of it. It is mounted from the top of the chassis and it
needs to be properly oriented. Once installed all the primary and
secondary wires will be cut and groomed to be neat as possible.
qPower Transformer x 1
q#10-32 3/8” Blk Philips x 4
q#10 Split lock washers x 4
qNow that you have such a nice clean soft working surface, lets test
it out. Check for any foreign materials that may cause scratches to the
chassis top surface.
qFor greater ease of this next assembly sequence, flip the chassis
over onto its right-side-up position. No kidding you say.
qWe need to arrange this transformer position so that the primary
winding wires coloured, brown, orange, white, and black, etc., all face
towards the RIGHT Channel or the IEC module.
qWith this relationship in mind, gently place the transformer on its
side on top of the chassis, on top of where the tube sockets will be.
qFeed the Primary and Secondary wires down through the large
access holes into the chassis cavity. Lift the transformer up and onto
its mounting location when you have fed enough of the wires through
to allow this to happen. CUE: Watch out for pinched wires!
qUsing the #10-32 screws and lock washers, secure the power
transformer to the top of the chassis.
Output Transformer Mounting:
The custom output transformer pair is also mounted from the top of the
chassis and they need to be properly oriented as well.
q#10-32 3/8” Blk Philips x 8
q#10 Split lock washers x 8
qOutput Transformers x 2
qWe need to arrange these transformers’ position so that the primary
winding wires coloured red and blue are entering the access holes
closest to the front of the chassis.
qWhile holding the O/P transformer above its mounting position, feed
the wires down into the appropriate access holes and then place the
transformer down onto the chassis.
qUsing the #10-32 screws and lock washers, secure both of the O/P
transformers to the top of the chassis.
This is now the end of the grunting section. Chassis assembly is
always involving the heavy work. Lets put aside our macho bronze
and re-apply our brains.
A quick check of what we have just installed would be in order now. It
is easy to correct anything at this stage; no E.C.N.’s needed here.
Check the following:
qAre the SPEAKER BINDING POSTS arranged with the RED terminal
towards the TOP of the chassis, or away from you? A little “+” sign will
also be adjacent to this RED post.
qIs the IEC AC input module positioned such that the green wire is
away from you closer to the TOP of the chassis, which ‘looks like’ the
bottom from here?
qThe POWER TRANSFORMER RED wires need to be to the RIGHT
side of center.
qThe OUTPUT TRANSFORMER secondary end with the bundle of six
(6) wires must be to the REAR of the chassis.
qAre the wires from the CHOKE on the LEFT side?
Good work, lets move on. That is of course that you are ready for the,
‘not difficult’, but demanding task of correctly wiring this amplifier.
Live
wire A
BlackNeutral
Link
wire C
Black
Ground
wire B
Green

19
Chassis Wiring (Part 1):
In this section we will connect the output transformers and set the O/P
load impedance to 4,8, or 16 Ohms, configure the power transformer’s
primary windings for your AC line voltage, then connect and install the
AC SW PCB.
qBlack 18awg hookup wire 10.5” (267mm) long x 1
(For Stereo configuration)
qBlack 18awg hookup wire 11.5” (292mm) long x 1
(For Mono Block configuration)
qBlack 18awg hookup wire 1 2” (305mm) long x 1
q3” Cable Ties x 2
qTwist style Connector x 4
Output Transformer Wiring/Configuration:
First the 300B plate connection to the output transformers will be dealt
with.
qThe RED wire from the transformers need to be trimmed to a length
of 5.75”(146mm) measured from the chassis opening.
qStrip this silver-plated copper, teflon jacketed leads to 1/4” (6.5mm).
qLooking from the top of the 300B tube socket, attach this RED lead
to the bottom right pin. CUE: Look for the right hand small hole in the
socket which is the closest to you as you are working from the front of
the chassis. Wrap and crimp the wire into place and then solder. Do
both channel sockets the same way. Please check the photo for
proper pin ID if in doubt, this socket does not have pin numbers on it
to aid you here.
The following blue wires are the high voltage connections for the
output transformer and therefore the 300B’s. These will be connected
to the Main Filter Bank at a later time, but we will get them ready now.
Note that each wire is a different length, if you wish it to be.
qPrepare the BLUE wire of the LEFT CHANNEL O/P, which is the
Right side as you are looking at it from the top, to a length of 7 1/4”
(185mm).
qNow prepare the other BLUE wire for the RIGHT CHANNEL, which
is the Left side as you are looking at it from the top, to a length of 5”
(127mm). For all of you really fussy D.I.Y.er’s, make this wire the same
length as the left channel, (7 1/4”). I have tried to keep perfect
symmetry wherever possible in this design.
Mono Block operation or Stereo operation?
Two B or not two B, that is the question. The option is yours, do you
want two SET-300B’s per channel driving your speaker cabinet, or do
you want one SET-300B per channel to drive your speaker cabinet? To
put it another way, do you want a Mono Block setup with 16 watts of
power for your one speaker cabinet, where you will need two amp
chassis’s for stereo, or are you going to run a single Stereo amplifier
chassis with 8 watts O/P per channel, to drive your pair of speaker
cabinets?
Hence, if you are running the standard Stereo chassis skip down to
the heading - ‘Stereo Operation’.
Mono Block Operation:
Now here is a feature that will make some of you very happy! For those
of you who would prefer to run your SET-300B as a mono block, this
next setup is for you. (Remember of course, that for a stereo or multi-
channel setup you do need a SET-300B mono block for each audio
channel running.) The power increases from 8 watts to 16 watts in this
mode as well.
The format here is that we will connect the two audio channels
together at the input and apply your input signal to either I/P RCA jack.
The doubling of power will be developed by configuring the output
transformer windings in series with each other. The speaker will then
be connected from the ‘-’ of the Right channel speaker post, to the ‘+’
of the Left channel speaker post. One last point to consider - if you
want your output speaker impedance set to 8 ohms, the two individual
transformer windings need to be set for 4 ohms operation. Eight ohm
transformer setup is therefore needed if your speakers are 16 ohm
impedance.
A permanent signal common return wire must be connected to the
“-” speaker binding post of the Right channel and another that
interconnects the “+” post of the Right channel to the “-” post of the
Left channel before the transformer secondary wires are attached.
When reconfiguring for different speaker loads, you will not be
changing these connections.
qCut and prepare one 12”(305mm) length of Black 18awg hookup
wire. One end treated as per the usual and the other gets stripped to
3/4” (19mm), tin them both.
qCut and prepare one 11.5” (292mm) length of Black 18awg hookup
wire. Both ends gets stripped to 3/4” (19mm), tin them both.
qI hope that your soldering iron is good and hot because it will need
to be to connect these wires to the terminals of the speaker posts.
qREAD CAREFULLY: In the groove at the end of the “-” speaker post
of the Right channel, the ‘long end’ of this wire is snugly wrapped,
then, snugly again back around itself to form an “eyelet” shape. Twist
this eyelet so that it is tight. We don’t want this connection to be
disturbed in the future when you may want to reconfigure the O/P for
a different speaker load.
CUE: If you approach the post from the center of the chassis, the wire
will line up better for its connection to the center of the Main PC board.
Connection of the free end will be left until the Main circuit board is
installed into the chassis.
qConnect the 11.5” wire to the “+” post in the same fashion.
qThe other end of this wire is then similarly connected to the “-”
terminal of the Left channel speaker post.
qLightly tin the “+” speaker post to get it ready for the wire
connections to come.
The next step is to configure the Output transformer secondary
windings for the proper speaker load. Remembering what I said
above, look below in the ‘Stereo Operation’ section for the wiring
configurations for your application, and also follow the ‘General
Instructions’ below to make your connections to the binding posts
themselves.
Once this is done please advance down to ‘Chassis Wiring (Part 2)’.
Stereo Operation:
The following construction steps are to be followed if you are using
your SET-300B amplifier in a - standard two channel in one chassis or
stereo chassis operation.
A permanent signal common return wire must be connected to the “-
” speaker binding posts before the transformer secondary wires are
attached. When reconfiguring for different speaker loads, you will not
be changing this connection.
qCut and prepare one 12”(305mm) and one 10.5” (267mm) lengths
of Black 18awg hookup wire. One end as per the usual and the other
gets stripped to 3/4” (19mm), tin them all.
qI hope that your soldering iron is good and hot because it will need
to be to connect these wires to the “-” terminals of the speaker posts.
qThe 12” wire will connect to the Left channel “-” binding post, and
the 10.5” wire will connect to the Right channel “-” binding post.
qREAD CAREFULLY: In the groove at the end of the “-” speaker post,
the ‘long end’ of this wire is snugly wrapped, then, snugly again back
around itself to form an “eyelet” shape. Twist this eyelet so that it is
tight. We don’t want this connection to be disturbed in the future when
you may want to reconfigure the O/P for a different speaker load.
CUE: If you approach the post from the center of the chassis, the wire
will line up better for its connection to the center of the Main PC board.
Connection of the free end will be left until the Main circuit board is
installed into the chassis.
qLightly tin the “+” speaker posts to get it ready for the wire
connections to come.
red wire
from output
transformer
small holes
large holes

1920
qNow to configure the secondary windings for the desired speaker
load, please first refer to the following chart.
4 Ohm Speaker Impedance
Wire Colours Connections To
White & Brown Spkr + (RED)
Black & Green Spkr - (BLK)
Blue & Yellow each other with special
twist connector
8 Ohm Speaker Impedance
Wire Colours Connections To
White & Yellow Spkr + (RED)
Black Spkr - (BLK)
Blue, Green & Brown each other with special
twist connector
16 Ohm Speaker Impedance
Wire Colours Connections To
White Spkr + (RED)
Black Spkr - (BLK)
Blue & Yellow each other with special
twist connector
Green & Brown each other with special
twist connector
General Instructions:
qNeatly group the wires as they enter the chassis through the access
hole and twist them together into a spiral. If you are a ‘hot shot’ with
the drill, go for it. Otherwise use your fingers.
qTrim these leads to a length no longer than 4.5” (113mm), strip the
teflon jacket 3/8” (9.5mm) from all the ends and only tin the wires that
will be terminated to one of the speaker binding posts. (See the chart
above).
qUse a 3” Cable Tie about 1.5” (38mm) from the end of the wires to
hold the group.
qAccording to the chart above, twist the conductors together and
solder them to the appropriate speaker post. Or if the lead gets
connected to another lead and not a binding post terminal, twist them
together, and then use one of the special twist connectors to firmly
hold the wires together. CUE: If you are connecting 3 wires, (i.e. 8
Ohm setup), then use the larger twist connector. You may solder this
connection first if you feel uneasy about using this reliable, high-force
connection device.
Chassis Wiring (Part 2):
Power Transformer:
Input AC Voltage Configuration:
This kit allows you to configure the amplifier to be used with an AC
source ranging from 100VAC to 240VAC. You will choose from one of
five different nominal voltage settings.
In a nutshell, there are two primary windings in the power transformer.
In a basic parallel connection the transformer will be set for 120VAC
nominal line voltage or a slight variation to the theme will allow for a
nominal voltage of 100VAC. Expanding on this, if we set the primaries
in series, certain combinations will allow operation with 200VAC,
220VAC or 240VAC as a nominal input AC voltage.
In this same sequence of instructions you will be connecting and
installing the AC SW PCB.
Oh good, I just remembered that I enjoy preparing these transformer
windings. This is where I use my power drill to spin and twist the wires
together to make very uniform snuggly twisted pairs. It adds that
‘professional’ look.
Connection of Power Transformer Primary Wires:
qYou may go directly to jail... no no, go straight to the section that
describes the setup for your particular AC line voltage. (We’ll see if you
did something wrong later and decide your consequences then!)
q3/16” Heatshrink tubing 1/2” (13mm) x 2
q1/8” Heatshrink tubing 1” (25mm) x 2
qAC SW PCB x 1
q#6-32 1/4” Philips screws x 2
q#6 lock washers x 2
100V operation:
qSnuggly twist the BLACK and BROWN wires together.
qSnuggly twist the WHITE and ORANGE wires together.
qSnuggly twist the BLACK/WHT and BROWN/ORG wires together.
qPrepare and trim the BLK/WHT & BRN/ORG pair of wires to 9”
(230mm).
qLocate the AC SW PCB, and on it you will see the label “OUT” and
two solder pads.
qInsert the BLK/WHT & BRN/ORG wires into these pads from the top
and solder them from the rear, trim any excess leads.
qTrim the WHITE & ORANGE pair of wires to 9” (230mm). Strip 3/8”
(9.5mm), twist together, and lightly tin these wires.
qSlide a piece of heatshrink tubing onto this pair of wires.
qThis pair of WHT & ORG wires are then soldered to the IEC AC
module, to the pin labeled ‘N’ (middle terminal). I know that you will
not be able to see this very will so observe the photo.
qOnce soldered on, slide the heatshrink tubing over this connection
and shrink it into place.
qTwo down and one to go. The last remaining pair do not connect to
anything, not even each other. The truth of it is though, these wires will
be live and must be treated with care to prevent an electrocution.
qOn the BLACK & BROWN wires are trimmed to 9” (230mm), more
than cutting off any of the exposed wire lead ends.
qSlide a piece of 1” (25mm) long small heatshrink tubing (1/8”), onto
each wire end, but only half way. Shrink the tubing in place and fold
the loose end back against the wire. Take another piece of 1” (25mm)
long 3/16” tubing and slide it over BOTH of these wires to couple the
ends together.
qYou have rolled the dice, please advance down to ‘STICKY Pad
Placement’.
120V operation:
qSnuggly twist the WHITE and ORANGE wires together.
qSnuggly twist the BLK/WHT and BRN/ORG wires together.
qSnuggly twist the BLACK and BROWN wires together.
qPrepare and trim the BLACK & BROWN pair of wires to 9” (230mm).
qLocate the AC SW PCB, and on it you will see the label “OUT” and
two solder pads.
qInsert the BLACK & BROWN wires into these pads from the top and
solder them from the rear, trim any excess leads.
qTrim the WHITE & ORANGE pair of wires to 9” (230mm). Strip 3/8”
(9.5mm) and twist them together and lightly tin these wires.
qSlide a piece of 1/2” long 3/16” heatshrink tubing onto these wires.
But don’t let it slide down into the transformer below.
qThis pair of WHT & ORG are then soldered to the IEC AC module,
to the pin labeled ‘N’, which is the middle terminal. I know that you will
not be able to see this very will so observe the photo at the bottom of
this section.
qOnce soldered on, slide the heatshrink tubing over this connection
and shrink it into place.
qTwo down and one to go. The last remaining pair of BLK/WHT and
BRN/ORG wires do not connect to anything not even each other. The
truth of it is though, these wires will be live and must be treated with
care to prevent an electrocution.
qThe BLK/WHT and BRN/ORG wires are trimmed to 9” (230mm),
more than cutting off any of the exposed wire lead ends.
qSlide a piece of 1” (25mm) long small heatshrink tubing (1/8”), onto
each wire end, but only half way. Shrink the tubing in place and fold
the loose end back against the wire. Take another piece of 1” (25mm)
long 3/16” tubing and slide it over BOTH of these wires to couple the
ends together.
qYou have rolled the dice, please advance down to ‘STICKY Pad
Placement’.

21
200V operation:
qSnuggly twist the BLACK and BROWN wires together.
qSnuggly twist the WHITE and BRN/ORG wires together.
qPrepare and trim the BLK/WHT wire to 9” (230mm).
qLocate the AC SW PCB, and on it you will see the label “OUT” and
two solder pads.
qInsert the BLK/WHT wire into either one of these pads from the top
and solder from the rear, trim any excess lead.
qTrim the ORANGE wire to 9” (230mm). Strip 3/8” (9.5mm) and lightly
tin this wire.
qSlide a piece of heatshrink tubing onto this wire.
qThis ORANGE wire is then soldered to the IEC AC module, to the pin
labeled ‘N’ (middle terminal). I know that you will not be able to see
this very will so observe the photo.
qOnce soldered on, slide the heatshrink tubing over this connection
and shrink it into place.
qThe last remaining WHITE & BRN/ORG pair connects to each other.
Trim these wires to 9” (230mm). Strip 3/8” (9.5mm) and lightly tin these
wires.
qWe will make an inline ‘pigtail’ wire termination. Holding the wires
side by side, twist the two leads together and solder.
qSlide a 1” (25mm) piece of Heatshrink tubing over this connection
half way. Shrink this and fold over the loose end onto itself and apply
a 1/2” (13mm) piece of heatshrink tubing over the first one and shrink
it again.
qThree down and one to go. The last remaining BLACK & BROWN
pair do not connect to anything, not even each other. The truth of it is
though, these wires will be live and must be treated with care to
prevent an electrocution.
qOn the BLACK & BROWN wires are trimmed to 9” (230mm), more
than cutting off any of the exposed wire lead ends.
qSlide a piece of 1” (25mm) long small heatshrink tubing (1/8”), onto
each wire end, but only half way. Shrink the tubing in place and fold
the loose end back against the wire. Take another piece of 1” (25mm)
long 3/16” tubing and slide it over BOTH of these wires to couple the
ends together.
qYou have rolled the dice, please advance down to ‘STICKY Pad
Placement’.
220V operation:
qSnuggly twist the BLK/WHT and BROWN wires together.
qSnuggly twist the WHITE and BRN/ORG wires together.
qPrepare and trim the BLACK wire to 9” (230mm).
qLocate the AC SW PCB, and on it you will see the label “OUT” and
two solder pads.
qInsert the BLACK wire into either one of these pads from the top and
solder from the rear, trim any excess lead.
qTrim the ORANGE wire to 9” (230mm). Strip 3/8” (9.5mm) and lightly
tin this wire.
qSlide a piece of heatshrink tubing onto this wire.
qThis ORANGE wire is then soldered to the IEC AC module, to the pin
labeled ‘N’ (middle terminal). I know that you will not be able to see
this very will so observe the photo.
qOnce soldered on, slide the heatshrink tubing over this
connection and shrink it into place.
qThe WHITE & BRN/ORG pair connects to each other. Trim these
wires to 9” (230mm). Strip 3/8” (9.5mm) and lightly tin these wires.
qWe will make an inline ‘pigtail’ wire termination. Holding the
wires side by side, twist the two leads together and solder.
qSlide a 1” (25mm) piece of Heatshrink tubing over this
connection half way. Shrink this and fold over the loose end onto
itself and apply a 1/2” (13mm) piece of heatshrink tubing over the
first one and shrink it again.
qThree down and one to go. The last remaining BLACK & BROWN
pair do not connect to anything, not even each other. The truth of it is
though, these wires will be live and must be treated with care to
prevent an electrocution.
qOn the BLACK & BROWN wires are trimmed to 9” (230mm), more
than cutting off any of the exposed wire lead ends.
qSlide a piece of 1” (25mm) long small heatshrink tubing (1/8”), onto
each wire end, but only half way. Shrink the tubing in place and fold
the loose end back against the wire. Take another piece of 1” (25mm)
long 3/16” tubing and slide it over BOTH of these wires to couple the
ends together.
qYou have rolled the dice, please advance down to ‘STICKY Pad
Placement’.
240V operation:
qSnuggly twist the WHITE and BROWN wires together.
qSnuggly twist the BLK/WHT and BRN/ORG wires together.
qPrepare and trim the BLACK wire to 9” (230mm).
qLocate the AC SW PCB, and on it you will see the label “OUT” and
two solder pads.
qInsert the BLACK wire into either one of these pads from the top and
solder from the rear, trim any excess lead.
qTrim the ORANGE wire to 9” (230mm). Strip 3/8” (9.5mm) and lightly
tin this wire.
qSlide a piece of heatshrink tubing onto this wire.
qThis ORANGE wire is then soldered to the IEC AC module, to the pin
labeled ‘N’ (middle terminal). I know that you will not be able to see
this very will so observe the photo.
qOnce soldered on, slide the heatshrink tubing over this connection
and shrink it into place.
qThe WHITE & BROWN pair connects to each other. Trim these wires
to 9” (230mm). Strip 3/8” (9.5mm) and lightly tin these wires.
qWe will make an inline ‘pigtail’ wire termination. Holding the wires
side by side, twist the two leads together and solder.
qSlide a 1” (25mm) piece of Heatshrink tubing over this connection
half way. Shrink this and fold over the loose end onto itself and apply
a 1/2” (13mm) piece of heatshrink tubing over the first one and shrink
it again.
qThree down and one to go. The last remaining BLK/WHT &
BRN/ORG pair do not connect to anything, not even to each other. The
truth of it is though, these wires will be live and must be treated with
care to prevent an electrocution.
qOn the BLK/WHT & BRN/ORG wires are trimmed to 9” (230mm),
more than cutting off any of the exposed wire lead ends.
qSlide a piece of heatshrink tubing onto each wire end, but only half
way. Shrink the tubing in place and fold the loose end back against
the wire. Take a third piece of tubing and slide it over BOTH of these
wires to couple the ends together.
You have rolled the dice, please advance down to ‘STICKY Pad
Placement’.
AC SW PCB Mounting:
Sorry for the switching around of instructions but we need to mount
this AC Switch PC board before going any further.
q#6-32 1/4” Philips screws x 2
q#6 lock washers x 2
qThe lonely Black wire from the IEC ‘L’ terminal (top one), is to be
connected to the solder pad labeled “BLK”. Solder this wire from the
back side of the AC SW board, and trim any excess wire.
qFirmly secure this PCB now to the side panel using the #6 screws
and #6 lock washers. CUE: Secure the top screw first. This will hold
the PCB in place while struggling to get the lower one installed.
qGood work, more on to ‘Welcome travelers...’.
Live
wire A
BlackNeutral
Link
wire C
Black
Ground
wire B
Green
Table of contents
Popular Amplifier manuals by other brands
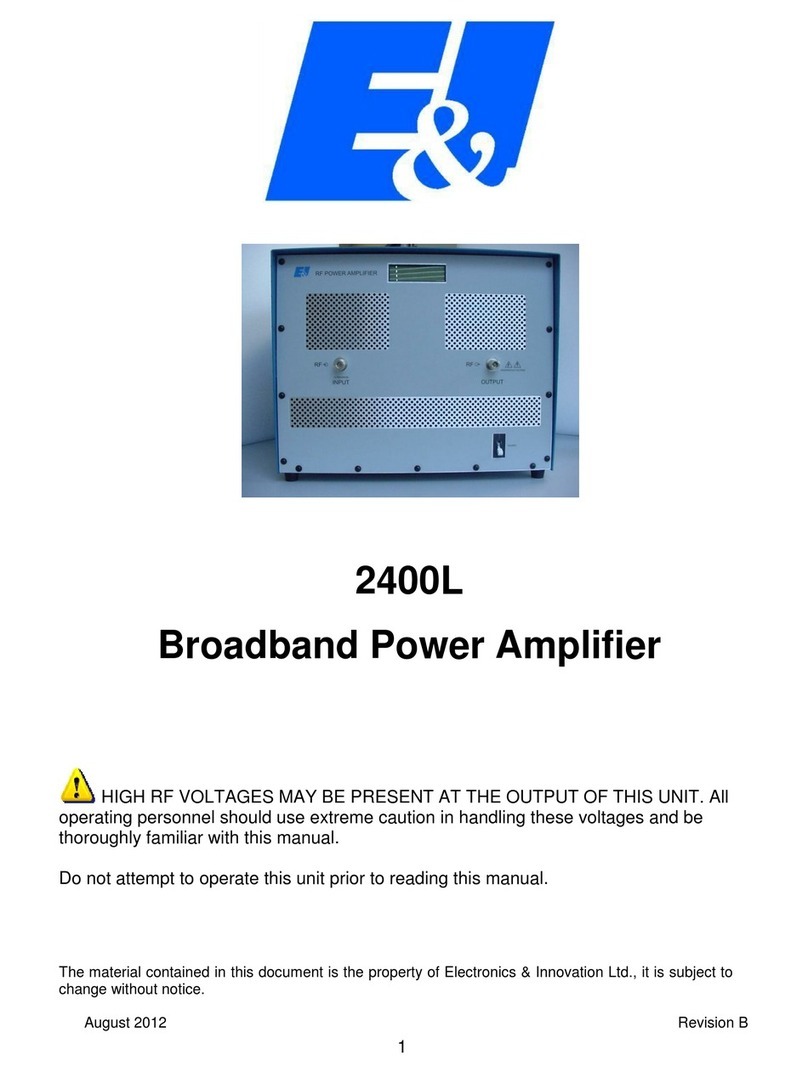
E&I
E&I 2400L manual
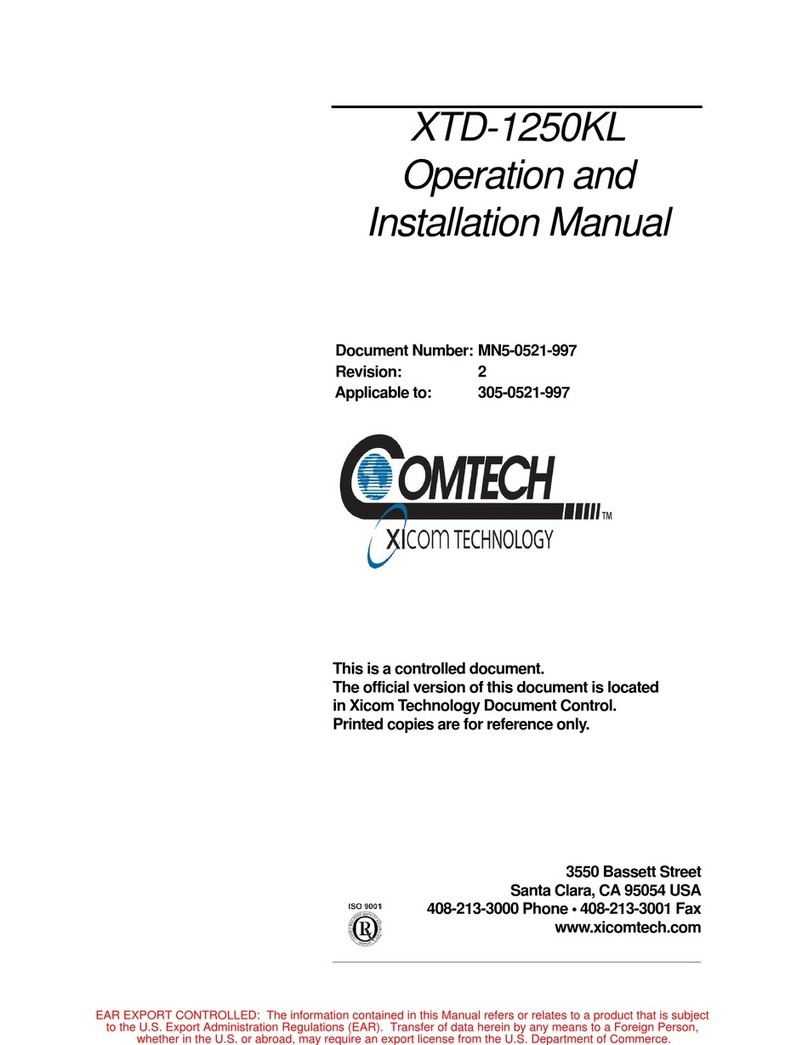
Comtech Xicom Technology
Comtech Xicom Technology XTD-1250KL Operation and installation manual
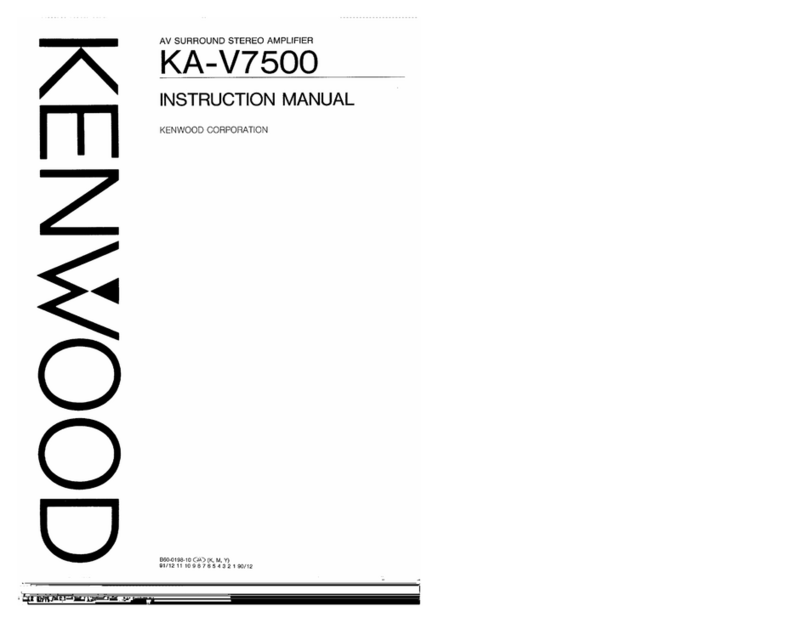
Kenwood
Kenwood KA-V7500 instruction manual
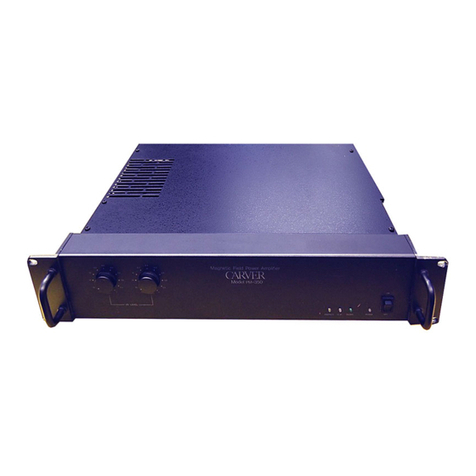
Carver
Carver PM-350 Operator's manual
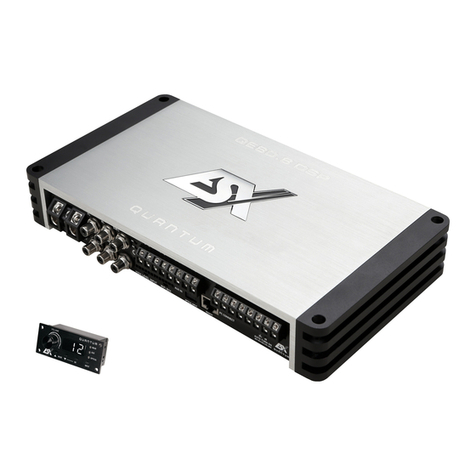
ESX
ESX Quantum QE80.8DSP owner's manual
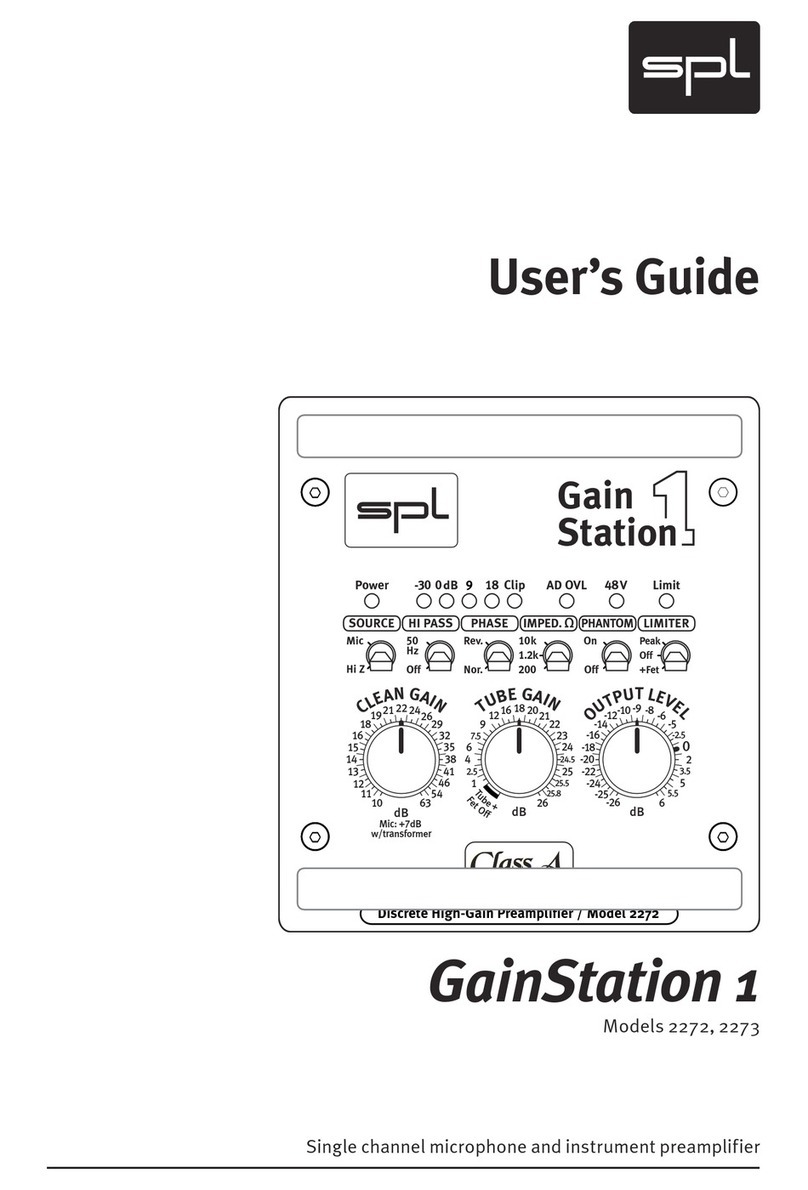
Sound Performance Lab
Sound Performance Lab Gain Station 2272 user guide