Danfoss EEA-PAM-591-A-10 User manual

Revision history Table of revisions
Date Changed Rev
August 2023 First edition 0101
Installation Guide
Servo Amplifier
2 | ©Danfoss | August 2023 BC459665217198en-000101

This commission guide is laid out in the sequence you should follow to install your servovalve amplifier.
Read this guide first and take special note of the cautions. Then, prior to installation, visually inspect your
new servovalve amplifier for defects or damage from shipping. If you notice any problems or need
assistance, contact the factory at (313) 695-7000.
Follow this general procedure when installing the EEA-PAM-591-A Servovalve Amplifier:
1. Become familiar with the general operation of the amplifier car by referring to the "Servo Amplifier
Discussed" and "Operating Data" sections.
2. Familiarize yourself with the amplifier card switch settings and front panel adjustments by referring
to the "Amplifier Settings" section.
3. Set up the amplifier card current limits and null adjustments by referring to the "Amplifier Set-Up"
section.
4. Decide on your application needs (position control, velocity control, force control, etc.) and the
characteristic of your command feedback input signals (voltage or current). Then set the switches on
the amplifier card, install the card in the holder, and make the appropriate connections according to
the information in the "Application Notes" and "Control Input Options" sections.
5. Adjust the proportional, integral and Derivative Gains (depending on which is appropriate for your
application) according to the procedure outlined in the "PID Set-Up Procedure" section.
Installation Guide
Servo Amplifier
General Installation Procedure
4 | ©Danfoss | August 2023 BC459665217198en-000101

This amplifier is designed to drive Vickers by Danfoss SM4 and SP4 servovalves and most other industry
standard servovalves such as Moog, Atchley, Pegasus, Rexroth, etc. in open and closed loop servo
systems. The package offers flexible circuitry in a standard rack mount format requiring a single +24 vdc
supply.
Control Input Stage
The amplifier can accept control signals of either voltage or current. The command signal input at pin B6
and the feedback signal input at pin B8 are voltage type up to ± 10. Control inputs at these pins can
utilize the amplifier's "Ratio" potentiometer which provides for amplitude ratio balancing. The signals
may be inverting or non-inverting via on board switch S1-2 (see switch descriptions). For current loop
inputs, pin Z6 is used to accept the current and pin Z8 is used as a current return. Signal inputs on pin Z6
can be inverting or non-inverting via on board switch S1-1 (see switch descriptions). Input at pin Z6 can
be either a command or a feedback signal of voltage type however, the Ratio potentiometer will have no
influence. All above mentioned control signal inputs can be monitored at front panel test point TP1.
By adjusting the on board potentiometer "Input Bias" a ± 10v signal can be added (summed) to the
control signals, providing input offset when required. The signal present at TP1 is also monitored by the
Tracking Error circuitry. The circuitry performs a comparison of the signal at TP1 to that of a user set
reference point, set by on board potentiometer "Tracking Err." This comparison feature allows the user to
establish a tracking error set point. If the signal at TP1 exceeds the "Tracking Err" set point the front panel
yellow LED will illuminate and the on board "Alarm Output" will energize (opto-coupled transistor turns
on).
P.I.D. Compensation Stage
Signals at test point TP1 are applied to the P.I.D. compensation section of the amplifier. The Proportional,
Integral, and Derivative stages of this amplifier are independently adjustable and switch selectable. On
board switch S1-3 is used to activate the Proportional Gain stage, switches S2-1, S2-2, and S2-3 are used
to activate the Integral Gain stage and switches S2-4, S2-5 and S2-6 are used to activate the Derivative
Gain stage (see switch descriptions for details).
The Proportional Gain can be used to influence system stiffness and possibly accuracy. This stiffness is
typically described as system response.
The Derivative Gain provides a means for system damping. This damping is effective in reducing control
signal overshoot. Damping may be required in systems that require high stiffness or accuracy. Integral
Gain can be used to reduce static error. Static errors are typically those errors that exist but do not
generate enough error signal for load correction. In positioning systems, the Integral Gain is typically not
applied until the actuator approaches position. To facilitate this function an "Integrator Reset Input" is
provided at pin Z24. This pin allows fr external control of the Integral stage.
The summed result of the Proportional, Derivative and Integral stages are present at output pin B18.
(maximum output is ± 10v at 5 ma).
Power Pre-amplifier and Current Limiter Stage
The output of the P.I.D. compensation network (present at pin B18) is also applied to the Power Pre-
amplifier stage. This Pre-amplifier provides yet more adjustable Proportional Gain if desired. This Pre-
amplifier directly feeds the voltage to current driver and its output is ± 6v at 2 ma).
In parallel with this Pre-amplifier are two current limiting circuits. These circuits are used to establish the
maximum positive and negative output currents. This feature allows the user to customize the amplifier
for a particular valve in use, thus protect the valve from currents that exceed its rating. By adjusting on
board potentiometers "+ Current Limit" and "- Current Limit" the amplifier output current can be limited
from 0 to 100% of full scale output.
Current Output Stage
The output of the power pre-amplifier and current limiters is applied to the current output stage. This
stage converts the voltage signal into an appropriate current output. Current is applied to the valve
through pin B26. A current return path from the valve is supplied at pin B28 providing closed loop
temperature compensation.
Installation Guide
Servo Amplifier
Servo Amplifier Discussed
©Danfoss | August 2023 BC459665217198en-000101 | 5

Additional signals such as "Output Bias" and "Dither" are also applied to the input of the current output
stage. The output bias is typically understood as an electronic null adjust and is capable of biasing the
output from ± 12% of full scale output. Dither is an optional adjustment that can be used to reduce the
effects of sitting or stiction. This signal is basically a low amplitude fixed frequency AC signal that is
superimposed onto the output signal. This allows the valve spool to remain active while at null. Front
panel adjustment "Dither" will affect the amplitude of this signal while potentiometer P12 will adjust the
frequency (factory set at 200 hz).
The amplifier is factory set for ± 200 ma output, however, if desired the maximum output capability can
be reduced via on board jumper "JP1." The amplifier provides three jumper positions labeled (A), (B), and
(C). When jumper JP1 is in the (C) position, the amplifier can output ± 200 ma, ± 100 ma when in the (B)
position, or ± 50 ma when in the (A) position. This feature may be beneficial where greater control of the
input span is desired. Output current can be monitored at front panel test point TP2. The output is in
volts where 1 mv equals 1 ma of output current.
Installation Guide
Servo Amplifier
Servo Amplifier Discussed
6 | ©Danfoss | August 2023 BC459665217198en-000101

Power requirements Nominal +24vdc < 500 ma: (at 200 ma load) Range +20 to
+32 vdc.
Maximum ripple ± 5% pk:
Reverse polarity protected.
Amplifier shuts down below +20 vdc.
Output voltages
At pins B2 and Z2 ± 15vdc < 50 ma: Ripple <50 mv pk/pk
(- 15vdc not short circuit protected)
Command signal inputs
Voltage input
Current input
At Pins B6, B8 or Z6: Range ± 10 vdc.
Impedance: 100k ohms.
At pins Z6 and Z8: Range 0 to 20 ma.
Impedance: 249 ohms.
Output current drive
Jumper selectable (jumper "JP1") (A) position ± 50 ma
(B) position ± 100 ma
(C) position ± 200 ma
Front panel test points
Tracking error monitor (TP1)
Output current monitor
± 10v full scale: short circuit protected.
1 mv/ma: short circuit protected.
Edge connector monitor points
P.I.D. output monitor
Pre-amp output monitor
At pin B18: ± 10 v at 5 ma
At pin Z26: ± 6 v at 2 ma
Input bias 0 to ± 10 vdc
Output bias 0 to ± 12% of full scale output.
Current limiters 0 to ± full scale output current.
Dither
Amplitude
Frequency
0 to 20% of full scale output current.
50 to 400 hz.
Proportional Gain .1 v/v to 20 v/v
Integral Gain
Low range
High range
0 to 40 v/v-sec
2 to 300 v/v-sec
Derivative Gain
Low range
High range
.05 to .2 v-sec/v
.3 to 2 v-sec/v
Pre-amp Gain 1 to 15 v/v
Drift over operating temperature range < ± .03% of full scale output at maximum gain
Operating temperature range 0 to 50°C
Storage temperature range -25 to 85°C
Installation Guide
Servo Amplifier
Operating Data
©Danfoss | August 2023 BC459665217198en-000101 | 7

Switches
S1-1: Control Input Invert– Affects control input on Pins Z6 and Z8. Set to the (A) position, the input signal
will be inverted at test point (TP1). Set to the (B) position, the input signal will not be inverted at test
point (TP1).
S1-2: Control Input Invert– Affects control input on Pins B6 and B8. Set to the (A) position, the input signal
will be inverted at test point (TP1). Set to the (B) position, the input signal will not be inverted at test
point (TP1).
S1-3: P Gain Enable– Used to control the Proportional Gain stage of the PID amplifier. Set to the (A)
position, the proportional stage input will be enabled. Set to the (B) position, the proportional stage
input will be disabled.
S2-1: I Gain High Range– Used to select the high range of Integral Gain. Set closed, the gain range is 2 to
300 volts/sec-volt. Switch S2-3 should never be closed at the same time as this switch.
S2-2: I Gain Low Range– Used to select the low range of Integral Gain. Set closed, the gain range is 2 to 40
volts/sec-volt. Switch S2-3 should never be closed at the same time as this switch.
S2-3: I Gain Enable– Used to control the Integral Gain stage input. Set closed, the integrator is disabled.
Set open, in conjunction with S2-1 or S2-2 closed, the integrator is enabled. Switch S2-1 and switch S2-2
should never be closed at the same time as this switch. Note: If the Integral Gain is not used, close S2-3
and ground the integrator reset pin (Z24). This will prevent the integrator output from drifting and
influencing other control signals.
S2-4: D Gain High Range– Used to select the high range of Derivative Gain. Set closed, the gain range is .3
to 2 volt-sec/volt. Switch S2-6 should never be closed at the same time as this switch.
S2-5: D Gain Low Range– Used to select the low range of Derivative Gain. Set closed, the gain range is .05
to .2 volt- sec/volt. Switch S2-6 should never be closed at the same time as this switch.
S2-6: D Gain Enable– Used to control the Derivative Gain stage input. Set closed, the stage is disabled.
Switch S2-4 and switch S2-5 should never be closed at the same time as the switch.
Installation Guide
Servo Amplifier
Amplifier Settings
8 | ©Danfoss | August 2023 BC459665217198en-000101

Front Panel Adjustment
Tracking Err Used to set a tracking error set point. The set point will be
continuously compared to the signal at TP1. If the signal
at TP1 xceeds the set point, the tracking error alarm
output will energize and the "err" LED will illuminate.
Gain When adjusted fully CCW, the pre-amp gain is 15 volts/
volt. This adjustment affects overall amplifier gain.
Factory set fully CCW.
Current + Limit Used to set the maximum allowable positive output
current. Adjusted fully CCW, no positive current is
available. Adjusted fully CW, maximum positive current is
available. Factory set fully CCW.
Current – Limit Used to set the maximum allowable negative output
current. Adjusted fully CCW, no negative current is
available. Adjusted fully CW, maximum negative current
is available. Factory set fully CCW.
P Gain Affects the amount of Proportional Gain applied to the
control signal (providing P Gain stage is enabled – see
switch descriptions). Adjusted fully CCW, the
Proportional Gain is .1 volts/volt. Adjusted fully CW, the
Proportional Gain is 20 volts/volt. Too much P Gain may
cause instability. Factory set fully CCW.
I Gain Affects the amount of Integral Gain applied to the control
signal (providing I Gain stage is enabled – see switch
descriptions). Adjusted fully CCW, the Integral Gain is 2
volts/sec-volt. Adjusted fully CW, the Integral Gain is 40
volt/sec-volt in the low range and 300 volts/sec-volt in
the high range. (See switch description for range
settings). Too much Integral Gain may cause oscillations.
Factory set fully CCW.
D Gain Affects the amount of Derivative Gain that is applied to
the control signal. (Providing D Gain stage is enabled –
see switch descriptions). Ajusted fully CCW, the
Derivative Gain is .05 volt-sec/volt in the low range and .3
volt-sec/volt in the high range. Adjusted fully CW, the
Derivative Gain is .2 volt-sec/volt in the high range. Too
much D Gain may reduce system response. Factory set
fully CCW.
Ratio Used to balance unequal amplitude command and
feedback signals connected at inputs (B6) and (B8).
Adjusted CW will increase the signal ratio of (B6) to (B8).
Adjusted CCW will decrease the signal ratio of (B6) to
(B8). Factory set centered.
Dither Used to control the dither amplitude. Adjusted fully CCW,
no dither is applied. Adjusted fully CW, 20% of the full
scale output is applied. Too much dither will cause
actuator trembling. Factory set fully CCW.
Input Bias Used to control the amount of input bias applied to the
input stage. Adjusted fully CCW, the input is biased –10
volts. Factory set for zero volt bias.
Output bias 1 Used to control the amount of output bias applied to the
output driver. Adjusted fully CW, the output driver will be
biased, 12% of full scale in the positive direction.
Adjusted fully CW ,the output driver will be biased, 12%
of full scale in the positive direction. Adjusted fully CCW,
the output driver will be biased 12% of full scale in the
negative direction. Factory set for zero bias.
Installation Guide
Servo Amplifier
Amplifier Settings
©Danfoss | August 2023 BC459665217198en-000101 | 9

Preliminary Conditions
The following set-up procedure should be performed after hydraulic nulling of the servovalve has taken
place. These steps are designed to aid the user in adjusting the amplifier for the particular valve in use.
Refer to Figure 1 for calibration connections and monitor points.
These procedures assume that the appropriate output range jumper "JP1" has already been selected. If
this jumper is moved at a later date, these procedures should be repeated.
Before beginning, ensure the following conditions exist:
•The hydraulic power is off.
•The servovalve is connected per Figure 1.
•No control signals are connected to the amplifier.
•The +24 VDC supply and ground are connected to the proper input pins.
•The front panel adjustments "current + limit," "current – limit," "dither" and "gain" are adjusted fully
CCW.
•Pin BZ4 and pin Z24 are jumpered together. (This is done to ensure no integrator interaction during
calibration.)
•On board switches are set as follows: S1-1, S1-3 in (B) position, S1-2 in (A) position, S2-1, S2-2, S2-4,
S2-5 in open position and S2-3, S2-6 in closed position.
Adjusting Output Null
While monitoring the signal at front panel test point TP2, adjust "output bias" for 0.000v (1mv = 1 ma
output current).
Adjusting Current Limiters
The purpose for setting the current limiters is to establish a relationship between maximum control
signal amplitude and maximum valve current. This procedure will utilize the input bias as on board
command source to set the current limits.
1. While monitoring front panel test point TP1, adjust input bias for +10v. To utilize this signal it must be
allowed to pass through the Proportional Gain stage of the amplifier. To allow this set switch S1-3 to
the (A) position. To ensure the full signal is passing through this stage, monitor edge pin B18 and
adjust "P Gain" for unity or –10v reading (the signal at B18 is inverted with respect to TP1).
2. While monitoring front panel test point TP2, adjust "current – limit" for maximum rate valve current.
(Remember 1 mv = 1 ma output current. For example, a 200 ma valve would read at TP2 as 200 mv.)
3. While monitoring from panel test point TP1, adjust input bias for –10v.
4. While monitoring front panel test point TP2, adjust "current + limit" for maximum rated valve current.
Adjusting Input Null
While monitoring front panel test point TP1, adjust "input bias" for 0.00v reading.
Amplifier Calibration Diagram
Figure 1. Servovalve amplifier set-up connections
Installation Guide
Servo Amplifier
Amplifier Set-up
10 | ©Danfoss | August 2023 BC459665217198en-000101

Typical position control utilizing full P.I.D.
Typical velocity or pressure control.
Typical force control utilizing P and D.
Installation Guide
Servo Amplifier
Application Notes
©Danfoss | August 2023 BC459665217198en-000101 | 11

Option 1
In this configuration, command and feedback signals are voltages of opposite polarity and may require
ratio balancing.
If the two signals are of equal amplitude, adjust ratio pot to center position. (Approximately 9 turns from
full CW)
If the two signals are of unequal amplitude, adjust ratio pot from center position CW to increase feedback
ratio or CCW to increase command ratio.
Switch S1-2 can be set to either (A) or (B). Refer to switch description.
Option 2
In this configuration, command and feedback signals are voltages of the same polarity.
For this configuration the ratio pot should be adjusted fully CCW.
When using this configuration, care must be taken that switches S1-1 and S1-2 are not set to the same
position. In this example, the command is not inverted, so switch S1-2 is set to (B). The feedback signal is
inverted so switch S1-1 is set to (A).
Installation Guide
Servo Amplifier
Control Input Options
12 | ©Danfoss | August 2023 BC459665217198en-000101

Option 3
In this configuration, one of the control signals is a voltage and the other is a 4-20 ma current loop.
For this configuration the ratio pot should be adjusted fully CW.
Before the voltage control signal is connected, the current loop signal must be calibrated. If the 4-20 ma
signal is to be summed with a single ended control signal (Ex. 0 to 10v) apply 4 ma's and adjust the input
bias so test point TP1 reads 0.00v. If the signal is to be summed with a double ended control signal (Ex. ±
10v), apply 12 ma's and adjust the input bias for 0.00v at test point TP1.
Installation Guide
Servo Amplifier
Control Input Options
©Danfoss | August 2023 BC459665217198en-000101 | 13

Preliminary Considerations
Before energizing the control system, review your application carefully. What would happen if your
system overshoots – will damage result?
In an application where the load moves freely and cannot impact against anything or be crushed by the
actuator, overshoot can be tolerated during the adjustment of the loop.
However, in a clamping application, for example, overshoot could damage the actuator or the load being
clamped.
Stop and ask yourself – "Will my adjustments cause damage if not done properly?" If so, you may have
to modify the equipment for safety reasons so that it can tolerate over-positioning, overspeed, or higher-
than-planned forces during adjustments.
Caution: A bad setting of the PID parameters may cause the drive to oscillate.
An oscilloscope and a means of generating a square wave (signal generator or system controller) is
required in order to tune a closed loop controller. To adjust the controller parameters, the command
signal into the amplifier should continuously switch between 10-30% and 70-80%. Each signal level
should have a dwell time of several seconds (Figure 2).
Before installing the card, the potentiometers P, I, and D should be at the fully counter clockwise position
and the switches on the card should be set based on the application described in the "Application Notes"
section.
Finally, install the card and connect the command and feedback signals based on the appropriate option
described in the "Control Input Option" section.
Caution: If the feedback signal is not of the proper polarity, your load will promptly "run away" when the
command signal is applied. This is because the feedback is being added to, not subtracted from, the command
signal at the summing junction, producing a constantly increasing error signal.
Tuning Procedure
1. Connect a monitoring device, such as an oscilloscope or an XY recorder to the COMMAND INPUT, and
the FEEDBACK signals (see "Control Input Options").
Caution: Care should be taken when taking measurements using TP2. If this test point should become
grounded, the feedback command will change in turn causing unintended operation.
Do not attempt to visually "eyeball" the results of the adjustment. Visual observation of the actuator is
not accurate enough. If you do not know how to operate the monitoring device, seek the assistance
of someone who DOES know how to use it.
2. Energize the system and be sure the servo valve has been mechanically nulled.
3. Apply the step input repeatedly, and slowly increase the Proportional Gain of the amplifier a little at a
time while observing the system response (via the feedback signal).
A position control system, for example, will respond as shown in Figure 3.
As Proportional Gain is increased, the step input will give increasingly faster response. Eventually the
gain will reach a value where the input step will cause the actuator to just barely reach the desired
position.
Continue increasing the Proportional Gain until the system achieves the position that the step input
should produce, as shown in Figure 4.
4. When the Proportional Gain is set high enough so that the step input causes the desired position to
be achieved, measure the response time using the time base of monitoring instrument.
5. Now, continue to raise the Proportional Gain until a moderate overshoot occurs, as shown in Figure 5.
6. Begin increasing the DERIVATIVE Gain now, a little at a time, while observing the response carefully.
The overshoot should begin to reduce as Derivative Gain is increased.
Continue increasing the Derivative Gain, and applying the step input, until the overshoot is
eliminated (Figure 6).
Installation Guide
Servo Amplifier
PID Set-Up Procedure
14 | ©Danfoss | August 2023 BC459665217198en-000101

If you find that you have turned the Derivative Gain to maximum, and overshoot is still occurring,
then you have set the Proportional Gain too high. If this occurs, turn the Derivative Gain BACK TO
MINIMUM, then decrease the Proportional Gain a bit and try Step 6 again.
7. When overshoot has been eliminated, measure the response time once again. You should see a
marked improvement, as shown in Figure 7.
8. When the overshoot is corrected, try to increase the Proportional Gain some more, until a slight
overshoot occurs. The see if additional Derivative Gain will correct it. You should soon reach a point
where response time cannot be improved any further.
9. Cycle the system several times, using the step input, to see whether the adjustments are stable. If
occasional overshoot is noted, decrease the Proportional Gain SLIGHTLY, until this stops occurring.
10. When the Derivative Gain is set satisfactorily, you can then attempt to set the Integral Gain to
eliminate any steady state error.
Remember that you want the Integral Gain to be disabled (RESET) during the dynamic part of the
motion cycle.
If Integral Gain is improperly timed, the overshoots will return. This is usually caused by the
interaction between the Derivative and Integral terms, as they "fight" each other for control.
If Integral Gain is set too high, you may even lose control of the system as it oscillates out of control. If
this occurs, shut down the amplifier, turn the Integral Gain back to minimum, and start again.
When in doubt, set the Integral Gain on the LOW side, since it tends to LESSEN THE STABILITY of a
closed loop system.
11. Watch the system carefully through the first few days of operation, to ensure that you have not set
the gains too high. Some performance "drift" can be expected as the hydraulic fluid changes
temperature or as new mechanical components "wear-in," producing the need for some "fine tuning"
later on.
Figure 2. Set-up command signal
Figure 3. Increasing Proportional Gain.
Installation Guide
Servo Amplifier
PID Set-Up Procedure
©Danfoss | August 2023 BC459665217198en-000101 | 15

Figure 4. Reaching desired command level.
Figure 5. Moderate overshoot.
Figure 6. Eliminated overshoot by adding Derivative Gain.
Installation Guide
Servo Amplifier
PID Set-Up Procedure
16 | ©Danfoss | August 2023 BC459665217198en-000101

Figure 7. Better response using additional P and D Gain.
Installation Guide
Servo Amplifier
PID Set-Up Procedure
©Danfoss | August 2023 BC459665217198en-000101 | 17

Power supplies
•EHA-PSU-704-A-10
Input power: 110/130/220/240 vac
Output: +24 vdc @ 4 amps
Dimensions:9.84 in x 4.53 in x 2.76 in
Style: Open frame, panel mount Assembly (order) number: 732166
•EHA-PSU-704-B-10
Input power: 110/130/220/240 vac
Output + 24 vdc @ 4 amps
± 15 vdc @ 250 ma
± 10 vdc @ 50 ma
Dimensions: 9.84 in x 4.53 in x 2.76 in
Style: Open frame, panel mount Assembly (order) number: 732167
Universal card holder
Style: Accepts Eurocard format of 3U height
Connector: DIN 41612 F48 female
Connections: Screw terminals
Dimensions: 5.1 in x 5.7 in x 2.2 in Assembly (order) number: 732683
Female edge connector for 19' rack
Style: Adaptable into rack housing
Connector: DIN 41612 F48 female
Connections: Solder terminals
Dimensions: 3.74 in x 1.15 in x .69 in
Assembly (order) number: 508178
Command and ramp generator
EEA-DSG-453-A-10
Supply voltage: + 24 vdc @ 4 w max.
Command selects: 5 (± 10 v range)
Ramp selects: 5 (.1 to 10 s range)
Style: Eurocard format, 3U height
Assembly (order) number: 02104128
Installation Guide
Servo Amplifier
Accessory Products
18 | ©Danfoss | August 2023 BC459665217198en-000101

Danfoss Power Solutions is a global manufacturer and supplier of high-quality hydraulic and
electric components. We specialize in providing state-of-the-art technology and solutions
that excel in the harsh operating conditions of the mobile off-highway market as well as the
marine sector. Building on our extensive applications expertise, we work closely with you to
ensure exceptional performance for a broad range of applications. We help you and other
customers around the world speed up system development, reduce costs and bring vehicles
and vessels to market faster.
Danfoss Power Solutions – your strongest partner in mobile hydraulics and mobile
electrification.
Go to www.danfoss.com for further product information.
We offer you expert worldwide support for ensuring the best possible solutions for
outstanding performance. And with an extensive network of Global Service Partners, we also
provide you with comprehensive global service for all of our components.
Local address:
Danfoss
Power Solutions GmbH & Co. OHG
Krokamp 35
D-24539 Neumünster, Germany
Phone: +49 4321 871 0
Danfoss
Power Solutions ApS
Nordborgvej 81
DK-6430 Nordborg, Denmark
Phone: +45 7488 2222
Danfoss
Power Solutions (US) Company
2800 East 13th Street
Ames, IA 50010, USA
Phone: +1 515 239 6000
Danfoss
Power Solutions Trading
(Shanghai) Co., Ltd.
Building #22, No. 1000 Jin Hai Rd
Jin Qiao, Pudong New District
Shanghai, China 201206
Phone: +86 21 2080 6201
Danfoss can accept no responsibility for possible errors in catalogues, brochures and other printed material. Danfoss reserves the right to alter its products without notice. This also applies to products
already on order provided that such alterations can be made without subsequent changes being necessary in specifications already agreed.
All trademarks in this material are property of the respective companies. Danfoss and the Danfoss logotype are trademarks of Danfoss A/S. All rights reserved.
©Danfoss | August 2023 BC459665217198en-000101
Products we offer:
•Cartridge valves
•DCV directional control
valves
•Electric converters
•Electric machines
•Electric motors
•Gear motors
•Gear pumps
•Hydraulic integrated
circuits (HICs)
•Hydrostatic motors
•Hydrostatic pumps
•Orbital motors
•PLUS+1®controllers
•PLUS+1®displays
•PLUS+1®joysticks and
pedals
•PLUS+1®operator
interfaces
•PLUS+1®sensors
•PLUS+1®software
•PLUS+1®software services,
support and training
•Position controls and
sensors
•PVG proportional valves
•Steering components and
systems
•Telematics
Hydro-Gear
www.hydro-gear.com
Daikin-Sauer-Danfoss
www.daikin-sauer-danfoss.com
Table of contents
Other Danfoss Amplifier manuals
Popular Amplifier manuals by other brands
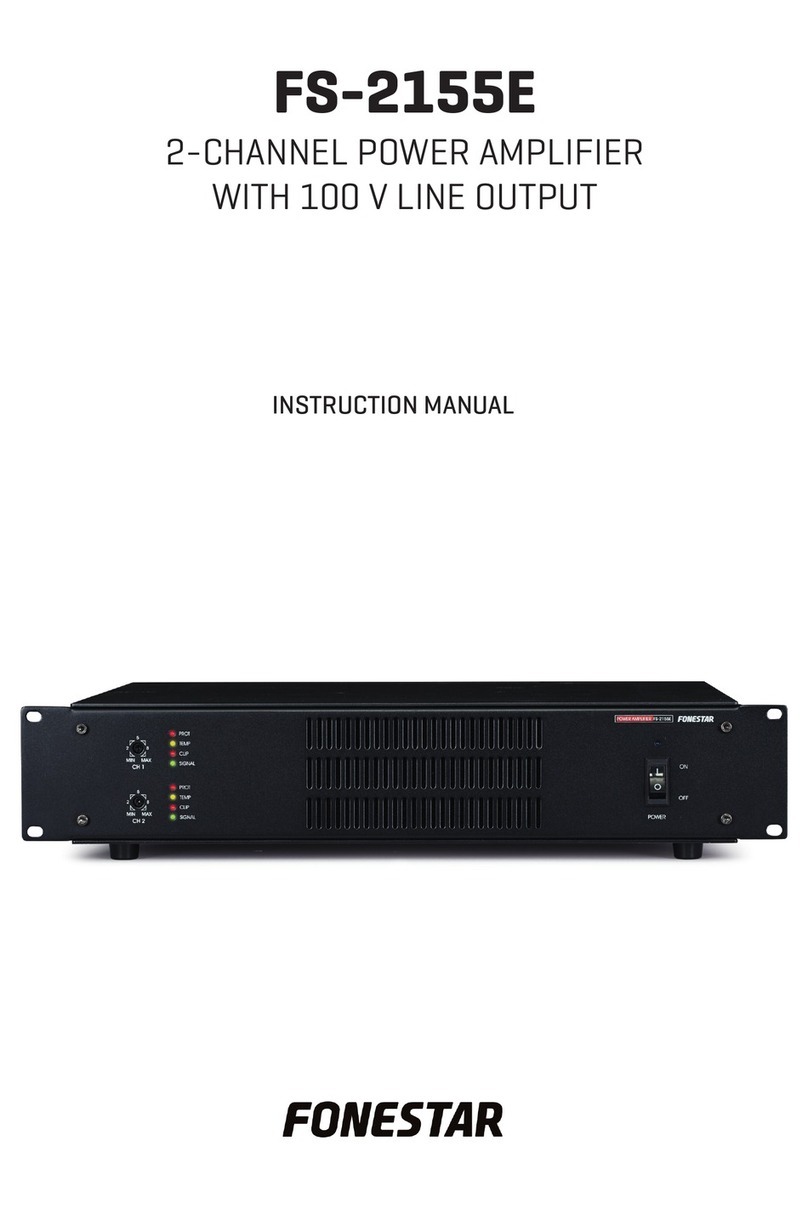
FONESTAR
FONESTAR FS-2155E instruction manual
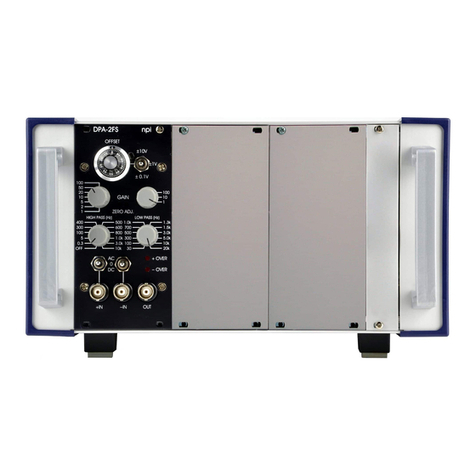
NPI
NPI DPA-2FS operating instructions
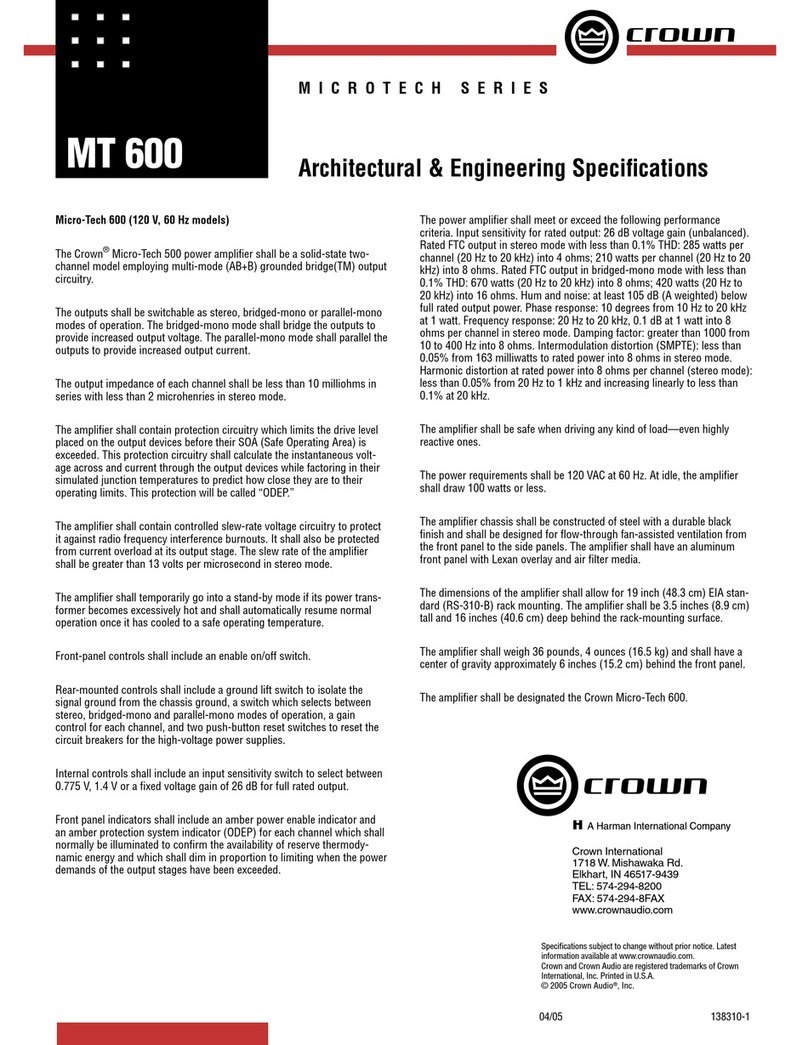
Crown
Crown Micro-Tech MT-600 Architectural & engineering specifications
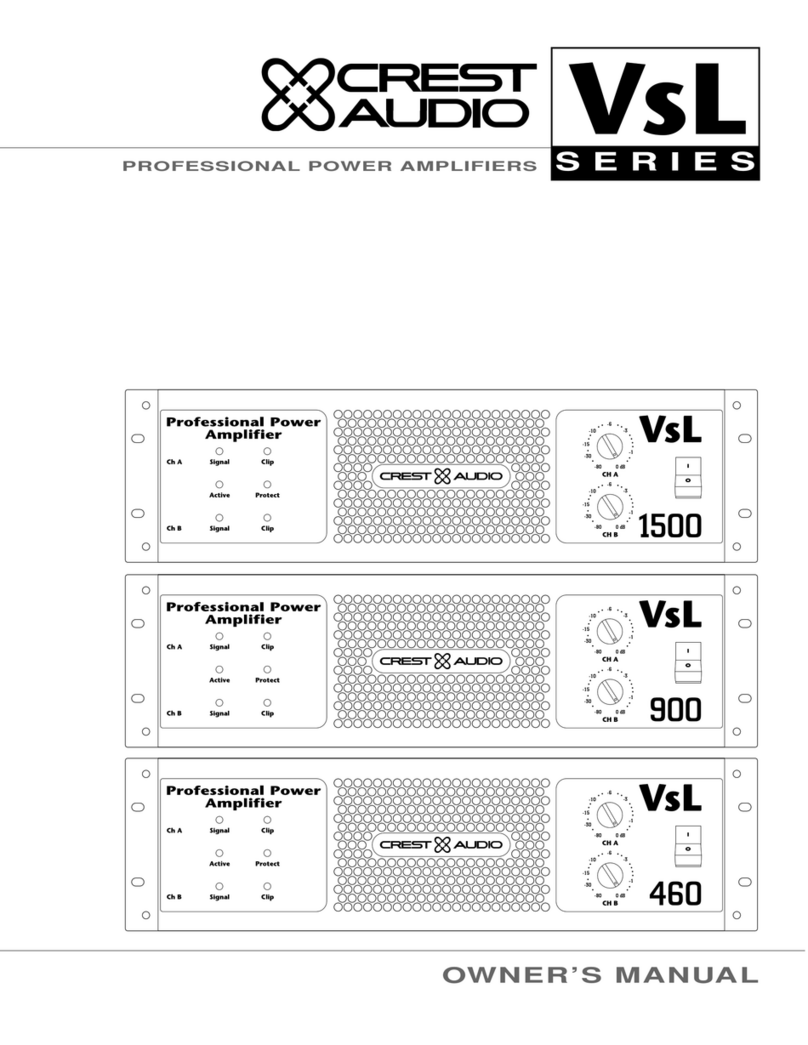
Crest Audio
Crest Audio VSL 1500 owner's manual

ELECTROCOMPANIET
ELECTROCOMPANIET AW-250 owner's manual
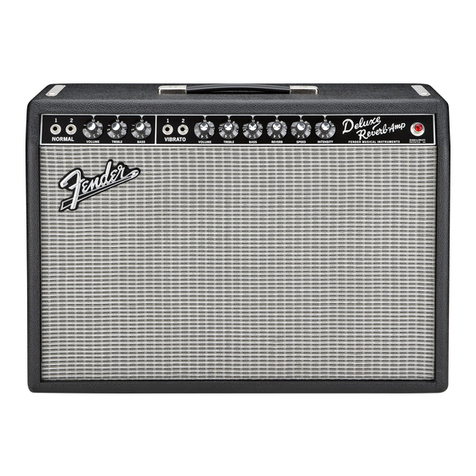
Fender
Fender 65 Deluxe Reverb operating instructions