ISOMET RFA1170-4+iMS4-L User manual

Dec 15
RF Power Amplifier &
Programmable Synthesizer
Including: Basic Deflector Alignment
Instruction Manual
RFA1170-4 + iMS4-L
Models -
RFA1170-4+iMS4-L : 50-90MHz, > 240W total RF output
DO NOT OPERATE
the RFA1170-4 types
or
LS700 type AO DEVICES
WITHOUT LIQUID COOLING
* (Always refer to the AO test data sheet)
ISOMET CORP, 5263 Port Royal Rd, Springfield, VA 22151, USA.
Tel: (703) 321 8301, Fax: (703) 321 8546, e-mail: isomet@isomet.com
www.ISOMET.com
ISOMET (UK) Ltd, 18 Llantarnam Park, Cwmbran, Torfaen, NP44 3AX, UK.
ISOMET

2
ISOMET
1. GENERAL
The Model RFA1170-4 is a class AB amplifier designed to drive the LS700- series of Isomet high
power Germanium acousto-optic deflectors with up to 300Watts across a 40MHz bandwidth. When
fitted with the iMS4-L synthesizer and controller cards, the RFA1170-4 power amplifier exhibits
programmable phase shift and amplitude compensation capability across the four RF output
channels.
This model is optimized for very fast rise and fall times and may be operated CW.
(Always refer to the AO device data sheet).
The RFA1170-4 + iMS4-L combo includes a number of features to aid monitoring and control:
Temperature monitoring and thermal Interlock for the Amplifier and associated AO deflector
“-Enable”control signal to enable RF amplifier (Closed contact = Active)
External “Trigger”input, 3v3 LV-TTL compatible
External “Clock”input, 3v3 LV-TTL compatible
Additional features are available under software control.
Please refer to the Isomet Software Development Kit available on-line.
A summary of the driver specification is shown in the following table:
Model Use Output Phase Shifted Output Power
with Frequency Outputs per Channel
RFA1170-4 LS700-1011 50 - 90MHz Yes > 80.0 Watt
+ iMS4-L

3
ISOMET
Figure 2 shows a block diagram of the Driver.
The iMS4-L comprises two PCB’s
Lower PCB features a four channel DDS and high speed FPGA with memory function.
Upper PCB is the main I/O interface and includes the USB II connection to the host
The -Enable signal is common to all four outputs. A closed contact between signal and ground will
enable the RF power amplifier. No external pull-up is required and if a voltage is applied to this pin it
must not exceed 3v3
The design includes thermal interlock protection which is also common to all four outputs
Each channel features a class A/B power stage to generate the final output level of up to 90W per
output.
Water cooling is required. The heatsink temperature must not exceed 70
C.
SERIOUS DAMAGE TO THE AMPLIFIER MAY RESULT IF THE TEMPERATURE
EXCEEDS 70
C.
SERIOUS DAMAGE TO THE AMPLIFIER MAY ALSO RESULT IF THE RF OUTPUT
CONNECTOR IS OPERATED OPEN-CIRCUITED OR SHORT-CIRCUITED.
SERIOUS DAMAGE TO THE AMPLIFIER WILL RESULT IF THE (FLOATING) INTERLOCK
INPUT SIGNALS ARE CONNECTED TO CHASSIS GROUND OR 0V
A low impedance d-c power supply is required. The operating voltage is +24V at a current drain of
approximately 32A. The external power supply should capable of > 40A, with
2% regulation and
<200mV ripple voltage for best results.
Figure 1 shows the connections.

4
ISOMET
3. INSTALLATION AND ADJUSTMENT
3.1 For continuous or duty cycled operation above >2%, always connect cooling water.
Flow rate greater than 2 litres / minute. Temperature < 20 deg.C
(Factory fitted water connections suit 8mm OD plastic tubing).
3.2 Connect +24V DC to the screw terminals of the filtered DC connector. DO NOT APPLY
POWER. The DC supply should be capable of 40A
3.2 Connect the (4) RF output TNC jacks to the (4) RF inputs of the acousto-optic deflector (or a
50
RF high power load). The connection order depends on the AO Bragg orientation (see
Figure 4) and will be either 11, 22, 33, 44 or 14, 23, 32, 41. The deflector
will not be damaged if the order is incorrect but the efficiency will be non-uniform. The
amplifier outputs must be terminated.
The cable lengths from the amplifier to the RF connections of the deflector must be equal.
3.4 Connect the Interlock of the acousto-optic deflector (7-way circular connector) to the 7-way
connector J9 of the RFA1170/4. A suitable cable is supplied.
The interlock signal triggers a fault conditionif the temperature of the modulator or internal
driver temperature exceeds 30ºC. This will disable the RF outputs.
There are two LED indicators
1: The bulkhead LED (above RF output J2) is bi-colour.
RED indicates 24Vdc is ON but the thermal interlocks and/or -ENABLE signal are
inactive.
Yellow indicates interlocks are OK and the -ENABLE signal is active.
RF will be output as soon as the iMS4-L is programmed and initiated.
2: LED stack on the iMS4-Linterface PCB
A GREEN (or RED) LED will beat at 1Hz indicating that the interface control circuitry has
initialized correctly
DO NOT connect any of the interlock signal wires to chassis ground or 0V.

5
ISOMET
3.5 Connect the USB to the host PC
3.6 Connect a voltage free contact to the -Enable SMA input.
3.7 Ensure the cooling water is on.
3.8 Apply + 24V DC to the amplifier
(The external trigger and clock inputs are not required for basic operation, depending on the
desired operating mode).
3.9 Adjustment of the RF output power is best done with amplifier connected to the acousto-optic
modulator.
The optimum RF power level required for the modulator to produce maximum first order
intensity will be different at various laser wavelengths. Applying RF power in excess of this
optimum level will cause a decrease in first order intensity (a false indication of insufficient RF
power) and makes accurate Bragg alignment difficult. It is therefore recommended that initial
alignment be performed at a low RF power level.
3.10 RF power is adjusted under software control
Please refer to the iMS SDK available at http://www.isomet.com/software.html
.
3.11 Set the power to a mid-level e.g.
Class Method description Setting
UpdateDDSPowerLevel 80%
UpdateRFAmplitude Wiper 40%
3.12 Program the DDS for a constant signal; Freq=70MHz, Ampl=100%, Phase=0 degree.
This will operate the AO device at its mid-scan position
3.13 Align the deflector head to insure that the incident light beam is centred in the active aperture
of the deflector.

6
ISOMET
Observe the diffracted first-order output from the acousto-optic modulator and the undeflected
zeroth order beam. Adjust the Bragg angle (rotate the deflector) to maximise first order beam
intensity.
3.14 After Bragg angle has been optimized, slowly increase the RF power until maximum first
order intensity is obtained. Record this intensity value (ISAT).
Typical values:
Class Method description Setting
UpdateDDSPowerLevel 80%
UpdateRFAmplitude Wiper 60%
3.15 To equalise deflection efficiency across the extremes of the scan, alternate between the
minimum and maximum desired frequencies (e.g. 50MHz and 90MHz input resp’) and adjust
the PHASE and AMPL values to give the same efficiency at both positions. Fine tuning of the
incident Bragg angle and RF power may be necessary for optimum results.
3.15 The amplifier is now ready for use.
Please contact Isomet for further guidance and example programs

7
ISOMET
-Enable (LVTTL)
T_DLY
RF Output
-Enable Response
The -ENABLE (active LOW) should be applied 2msec prior to the required active RF output.
The -Enable may remain LOW continuously. The RF amplifiers are design to be biased at 100% duty
factor.
T_DLY = 1.8msec
Pulsed Response
All versions of the RA1170-4 are designed for fast pulse operation up to CW operation
Typical output RF waveform is shown below
45W / 70MHz pulsed output
10%-90% rise / fall time = < 10nsec

8
ISOMET
4. MAINTENANCE
4.1 AO Device - Cleaning
It is of utmost importance that the optical apertures of the deflector optical head be kept clean
and free of contamination. When the device is not in use, the apertures may be protected by
a covering of masking tape. When in use, frequently clean the apertures with a pressurized
jet of filtered, dry air.
It will probably be necessary in time to wipe the coated window surfaces of atmospherically
deposited films. Although the coatings are hard and durable, care must be taken to avoid
gouging of the surface and residue of the cleaning solution. It is suggested that the coatings
be wiped with a soft ball of brushed (short fibres removed) cotton, slightly moistened with
clean alcohol. Before the alcohol has had time to dry on the surface, wipe again with dry
cotton in a smooth, continuous stroke. Examine the surface for residue and, if necessary,
repeat the cleaning.
4.2 Troubleshooting
No troubleshooting procedures are proposed other than a check of alignment and operating
procedure. If difficulties arise, take note of the symptoms and contact the manufacturer.
4.3 Repairs
In the event of deflector malfunction, discontinue operation and immediately contact the
manufacturer or his representative. Due to the high sensitive of tuning procedures and the
possible damage which may result, no user repairs are allowed. Evidence that an attempt
has been made to open the optical head will void the manufacturer's warranty.

9
ISOMET
Schematic of Acousto-optic scanner and drive electronics.
RF
1st Order Scan
0th Order
Input Laser Beam
Intensity Modulation
Tuning Voltage
SEP
SCAN
BRAGG
AO Deflector
Deflector Driver
The input Bragg angle, relative to a normal to the optical surface and in the plane of deflection is:
Bragg = fc
2.v
The separation angle between the zeroth order and mid scan point of the first order is:
sep = fc
v
The first order scan angle is:
scan = f
v
Modulation rate (Gaussian profile) is:
Tr = 0.65 d/v
Scanning Resolution is:
N = f .d/v
where : = wavelength
f = scan frequency bandwidth
fc = centre frequency
v = acoustic velocity of interaction material
(5.5mm/us for Ge)
d = beam waist along acoustic axis

10
ISOMET
G1/8 Coolant Fittings
to suit 6mm O/D pipe
( 2places)
Mounting Holes
6mm diameter
(4 places)
J1 J2 J3 J4
INT'L
0V +24V dc
Ch2
Ch1 Ch3 Ch4
+
-
Model:
S/N : ISOMET
170
200
280
265
3
122
-Enable CTRL CLK TRG
USB II
Outline
Connector Summary
J1: TNC, RF Output Ch1
J2: TNC, RF Output Ch2
J3: TNC, RF Output Ch3
J4: TNC, RF Output Ch4
INT: 7-way Circular Panel Plug, Binder 712 (AOD Temp and isolated Interlock Input)
USB II: Host PC USB connection
CTRL: Reserved for future use
CLK:External data clock input
TRG: External trigger input
-Enable: Connect signal to return to enable
Figure 1: Driver Installation

11
ISOMET
+24Vdc
.
.
.
o
+
o
o
+
+
+
micro-DB25
13
25
2
14
1
o
HiDB37
1
16
33
44
15
30
PAStage
TNC
J1
Output
Pre-Amp
GainSet
FPGA
Gate
TNC
J2
Output
TNC
J3
Output
TNC
J4
Output
DDS
MCX MCX
iMS4-L
or
iMS4-P
Figure 2: Driver Block Diagram

12
ISOMET
Signal
Connector
Spec
-Enable
SMA
Internal pull up to 3v3
Voltage free contact recommended
Open = Off, Closed =ON
CTRL
9-way D-type
Reserved for future designs
CLK
SMA
LVTTL, 3v3 max
TRG
SMA
LVTTL, 3v3 max
USB
B-type
II
INT
7-way Binder
I2C (cable supplied)
Vdc
Screw terminal
24Vdc , 40A
LED indicators, 2 off:
1: The bulkhead dual colour LED fitted above RF output J2
RED indicates:
24Vdc is ON, but one or more of the following conditions exist:
Interlock failure (over temp)
-ENABLE signal inactive (open circuit)
RF_GATE not enabled in S/W
YELLOW indicates amplifier enabled and RF outputs live
2: LED stack on the iMS4-L interface PCB
GREEN (or RED) LED will beat at 1Hz indicating that the interface control circuitry has
initialized correctly
Figure 3: Signal listing

13
ISOMET
AOD
1st
0th
Input
1st 0th
Input
0th 1st
1st 0th
Input
Input
Amplifier
Increasing Phase
Delay
AOD
AOD
AOD
Correct orientation as viewed from top of AOD
(Connector identification may differ)
Connection options for Beam Steered AO Deflectors
Amplifier
Amplifier
Amplifier
RF1
RF4
J1
J3
J2
J4
J1
J3
J2
J4
Increasing Phase
Delay
Increasing Phase
Delay
J1
J3
J2
J4
Increasing Phase
Delay
RF1
RF4
RF1
RF4
RF1
RF4
RF1
RF4
RF1
RF4
RF1
RF4
RF1
RF4
RF1
RF4
RF1
RF4
J1
J3
J2
J4
Increasing Phase
Delay
Figure 4: Connection Orientation. (Assumes the iMS4-L is programmed accordingly)
Table of contents
Other ISOMET Amplifier manuals
Popular Amplifier manuals by other brands
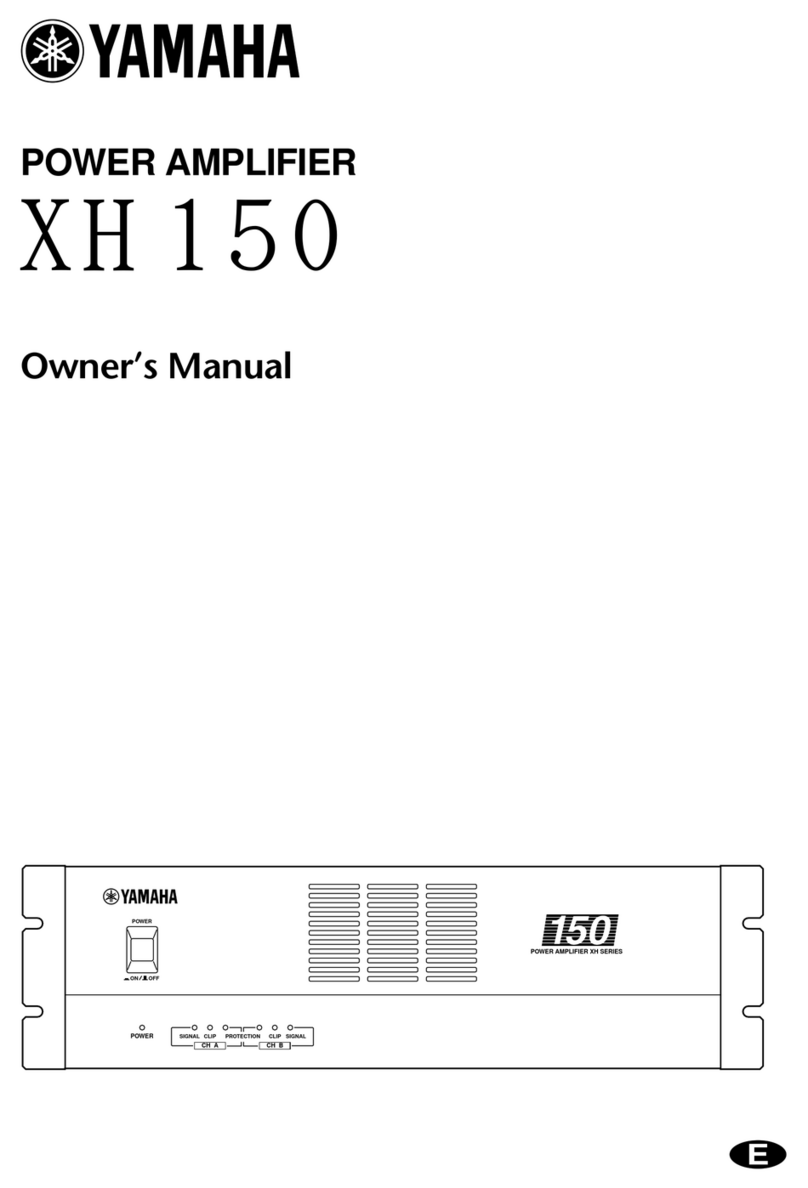
Yamaha
Yamaha 150 owner's manual
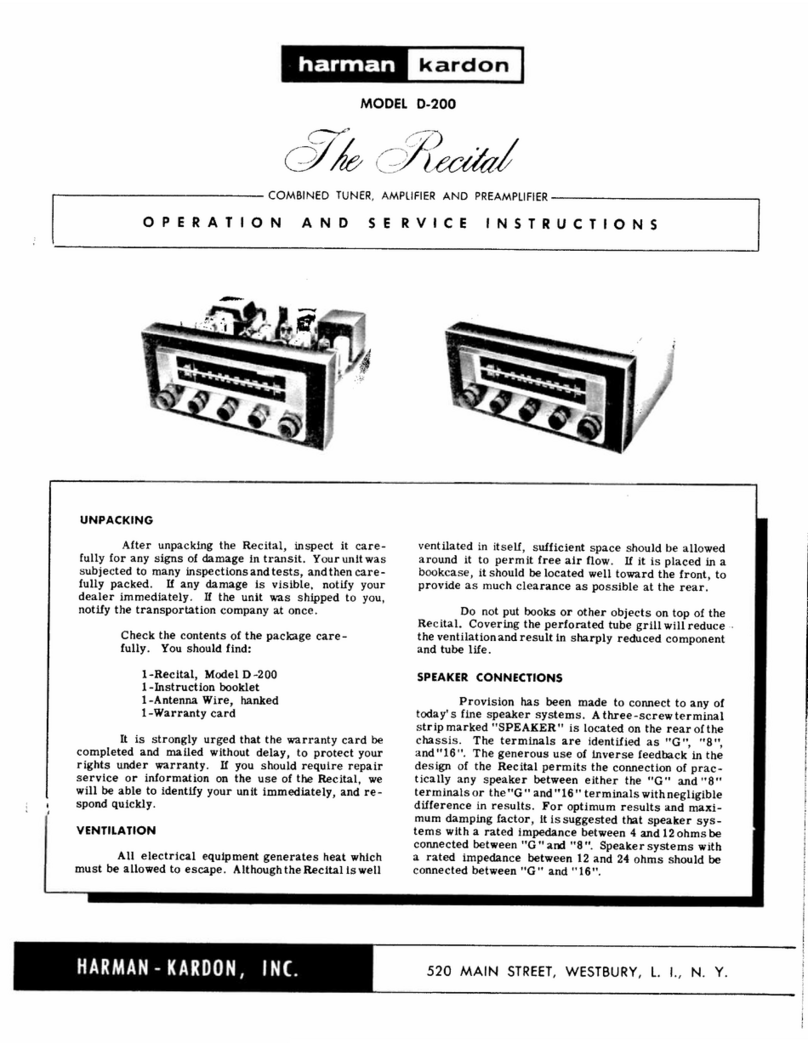
Harman Kardon
Harman Kardon The Recital D-200 Operating and service instructions
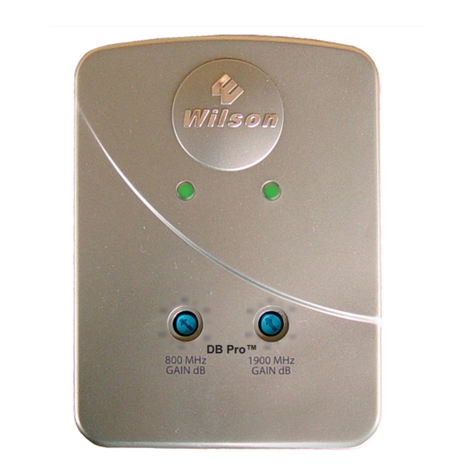
Wilson Electronics
Wilson Electronics 271265 Installation guides
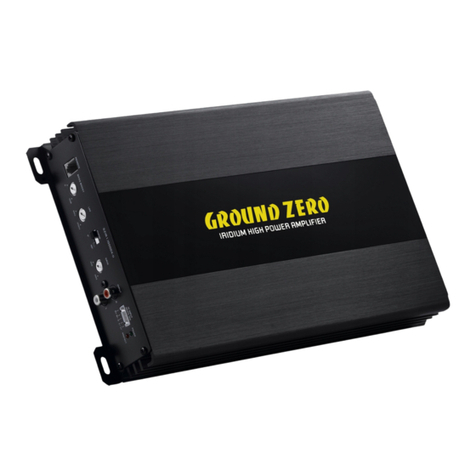
Ground Zero
Ground Zero Iridium GZIA 1.1000DX-II owner's manual
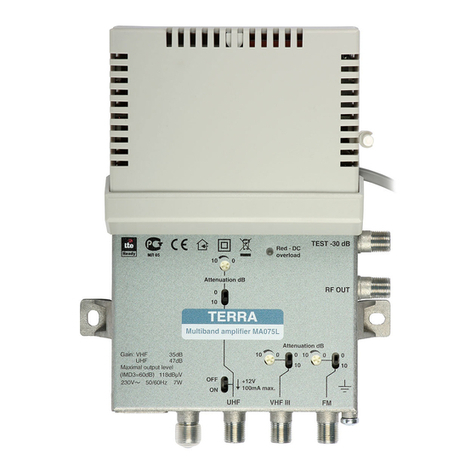
Terra
Terra MA074L quick start guide
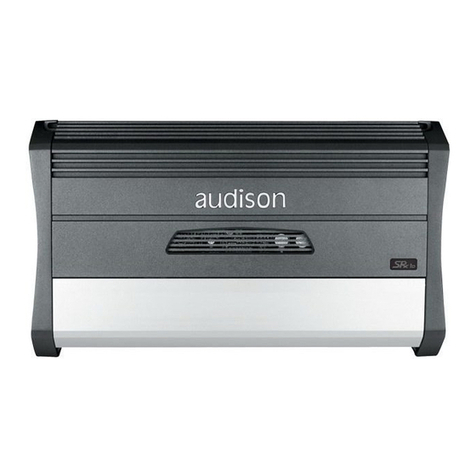
Audison
Audison SRx 1D Advanced manual