Lennox G43UF SERIES Guide




















Other manuals for G43UF SERIES
6
Other Lennox Furnace manuals

Lennox
Lennox Elite series User manual
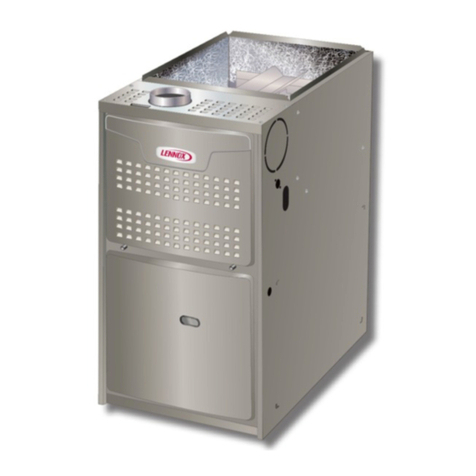
Lennox
Lennox Allied Air A95UH1D User manual
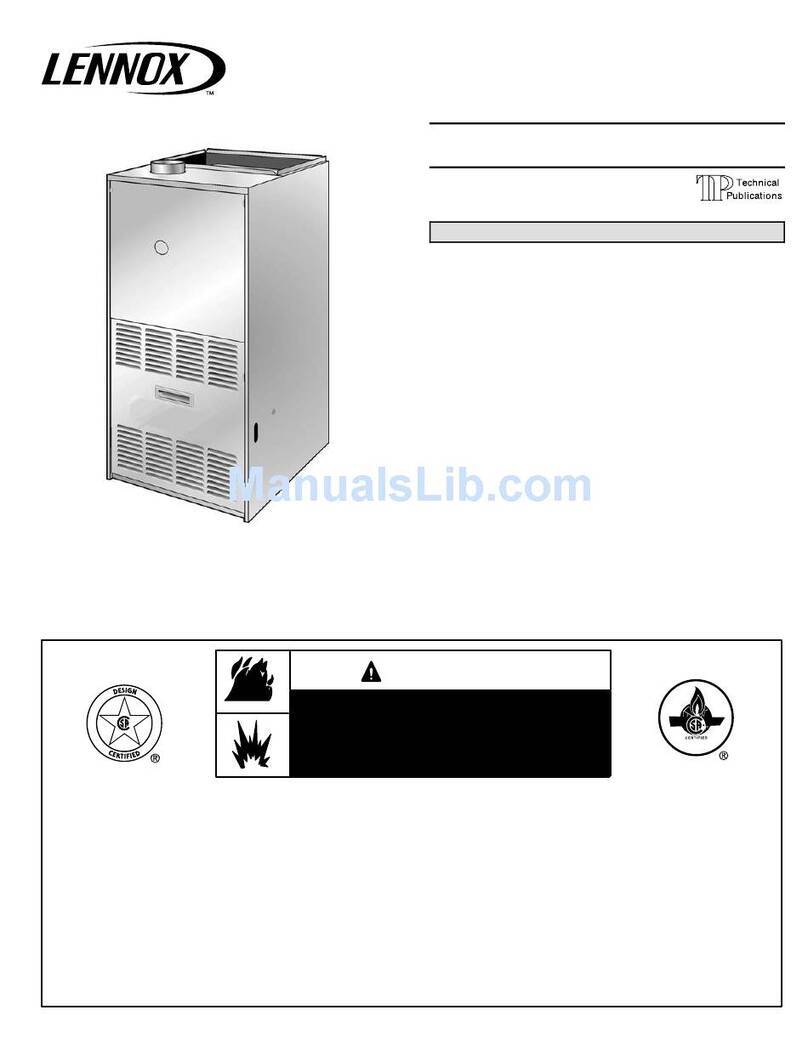
Lennox
Lennox G60DF(X) Series User manual
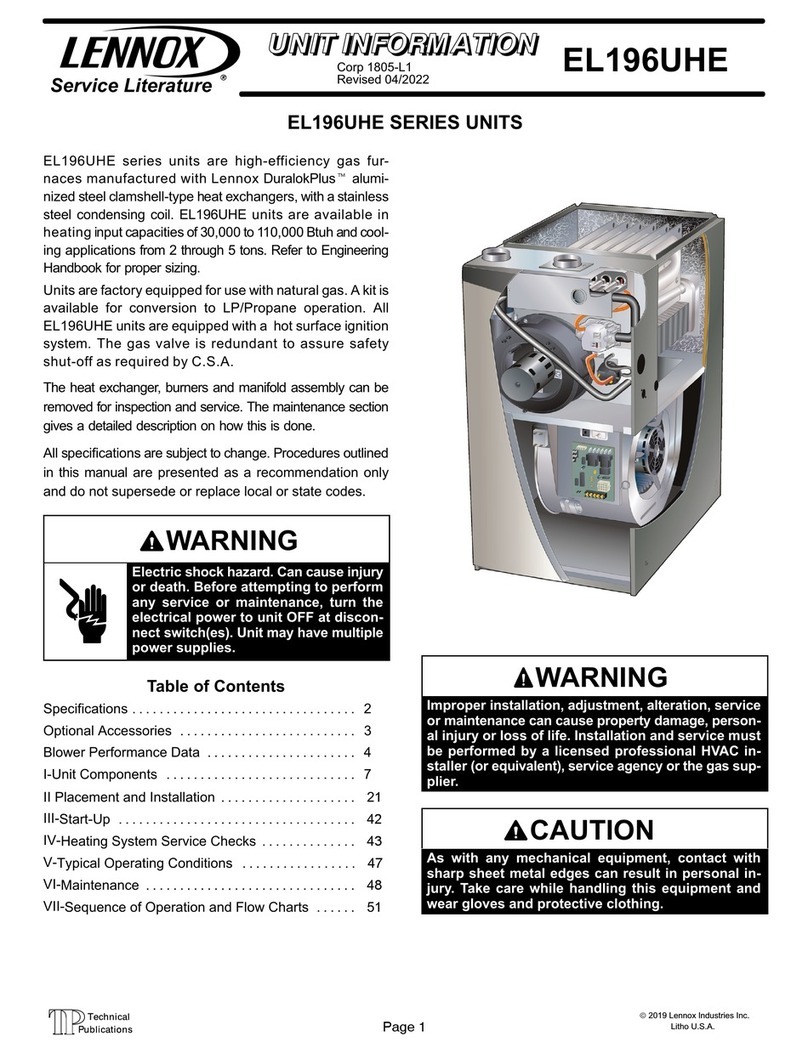
Lennox
Lennox EL196UH030XE24B Owner's manual
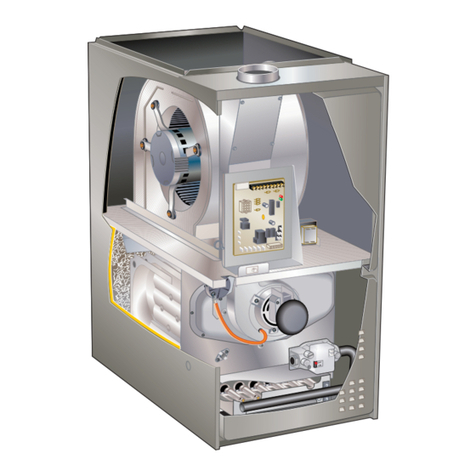
Lennox
Lennox ML180DFE SERIES Installation and operation manual

Lennox
Lennox Elite series User manual
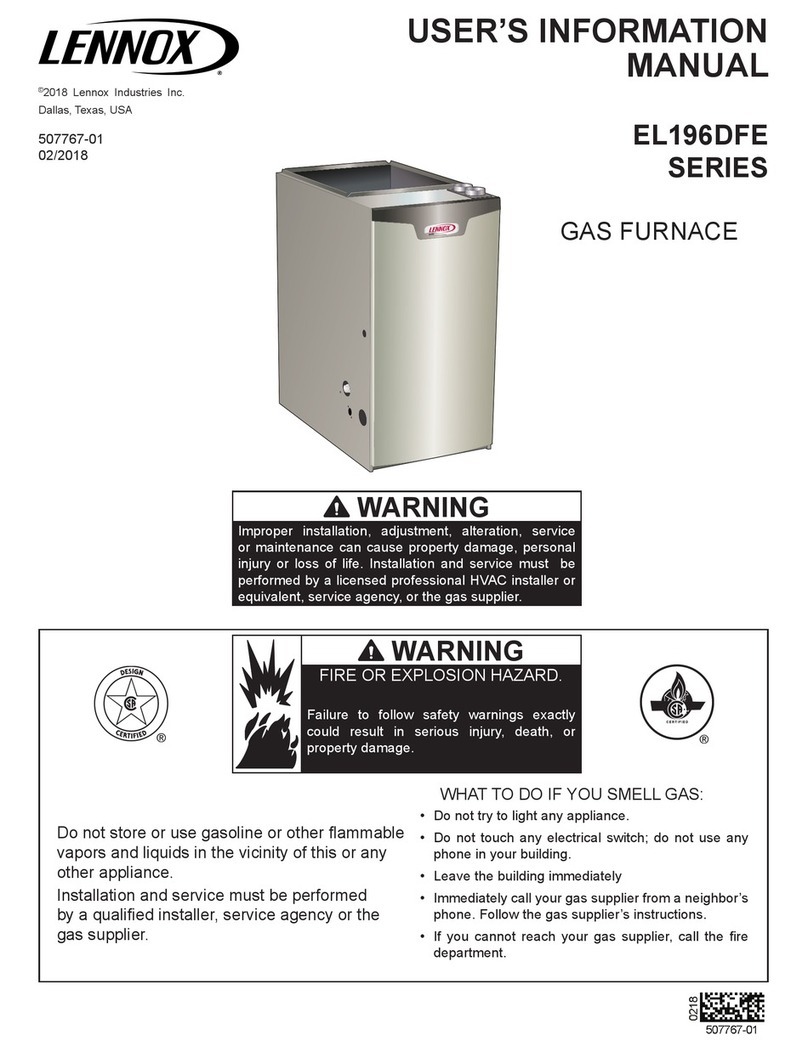
Lennox
Lennox EL196DFE Series Guide

Lennox
Lennox MERIT ML180DFE User manual
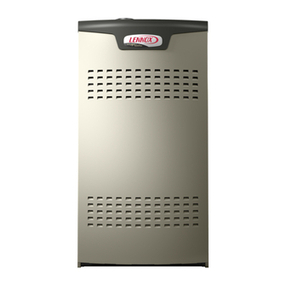
Lennox
Lennox EL280UHE Service manual

Lennox
Lennox SIGNATURE SLO185BV Series User manual
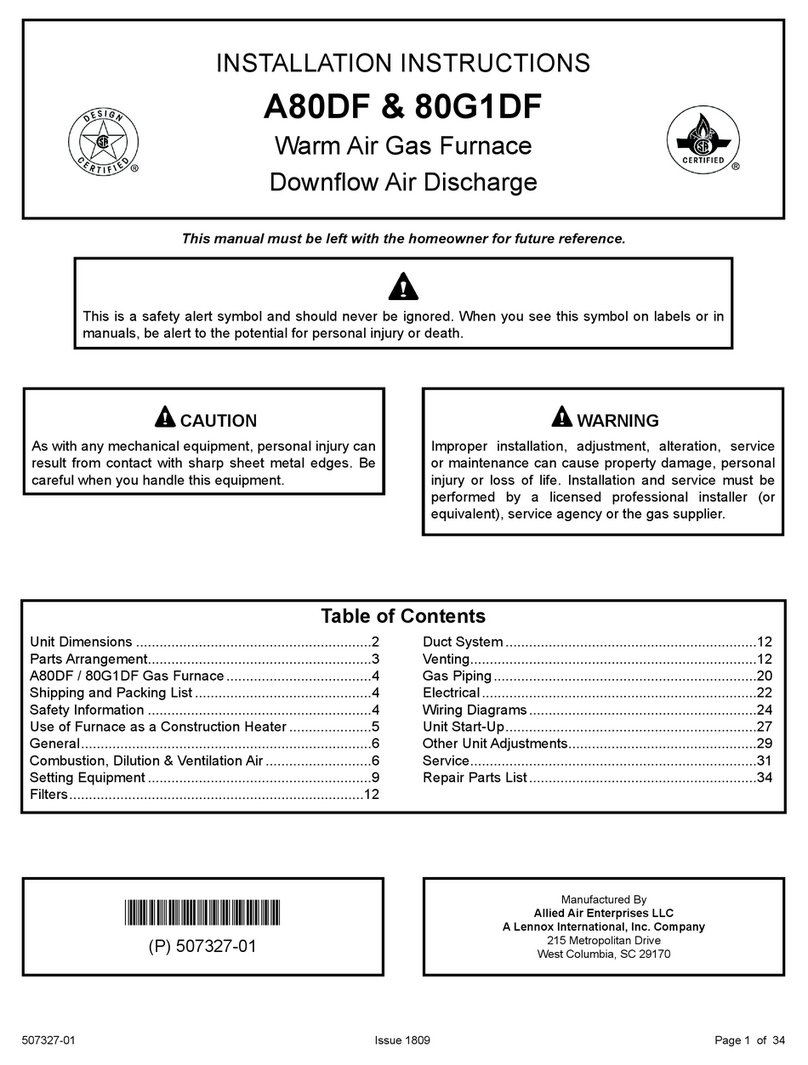
Lennox
Lennox Allied Air A80DF User manual
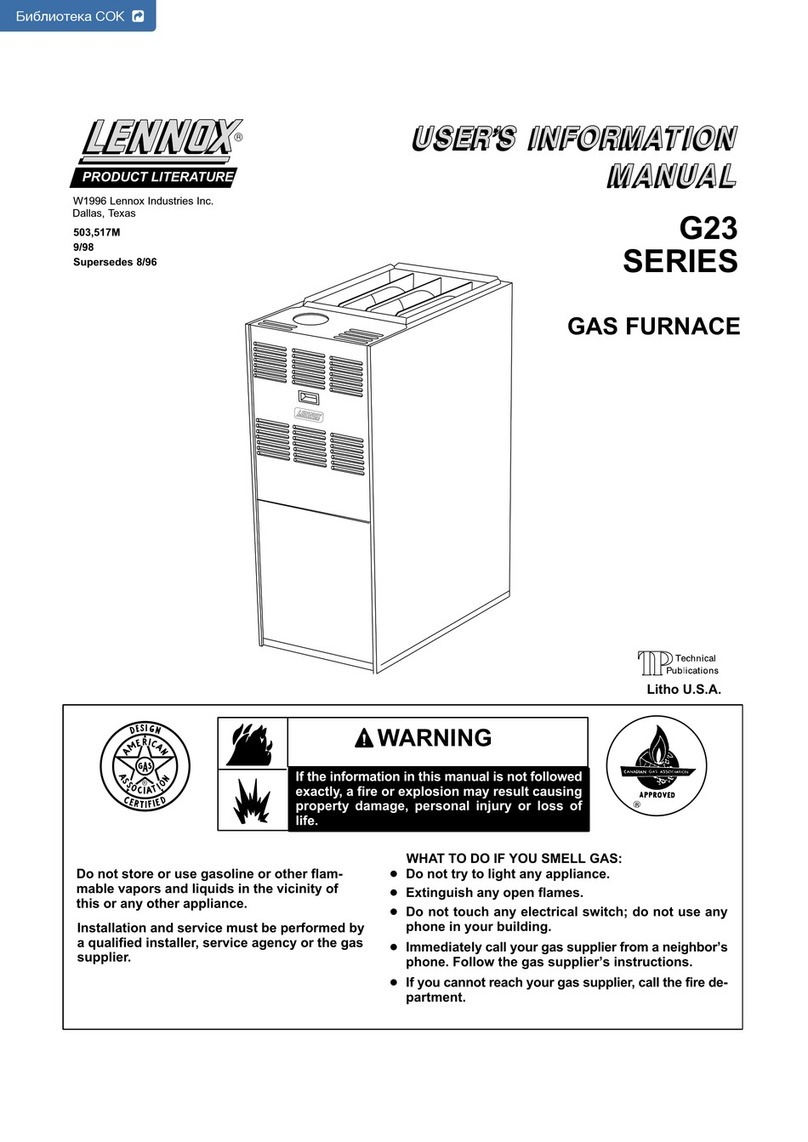
Lennox
Lennox G23 Series Guide

Lennox
Lennox GSR14 User manual
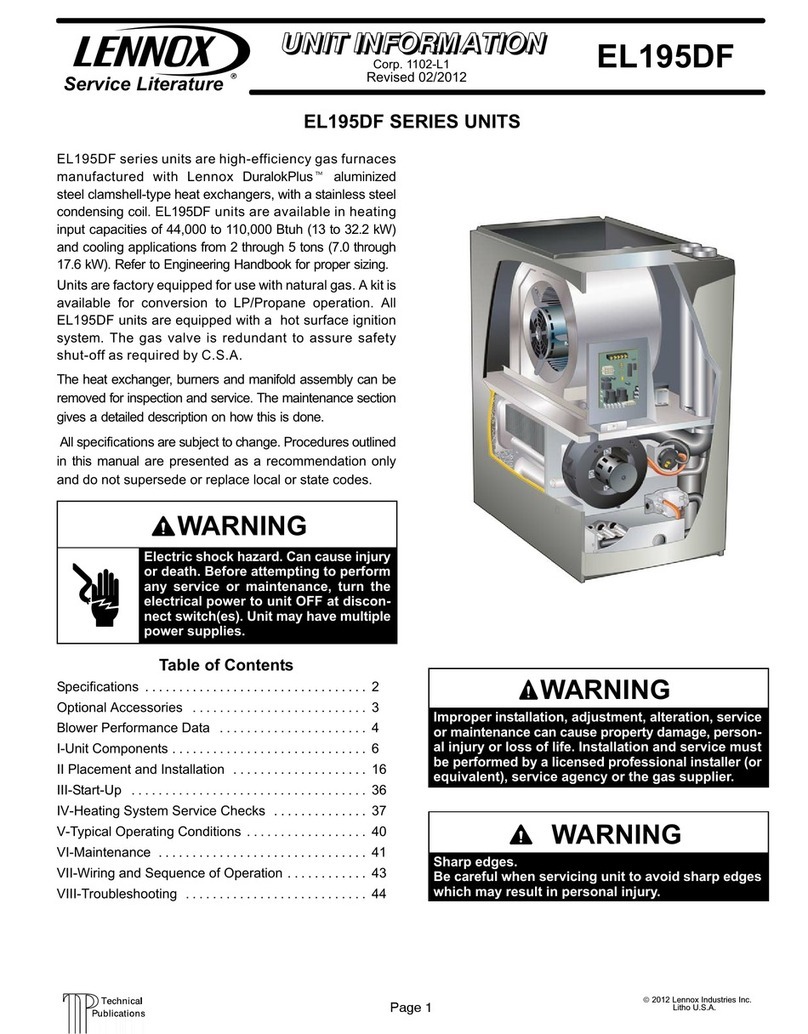
Lennox
Lennox EL195DF SERIES User manual

Lennox
Lennox Signature G60UHV36A-070 User manual
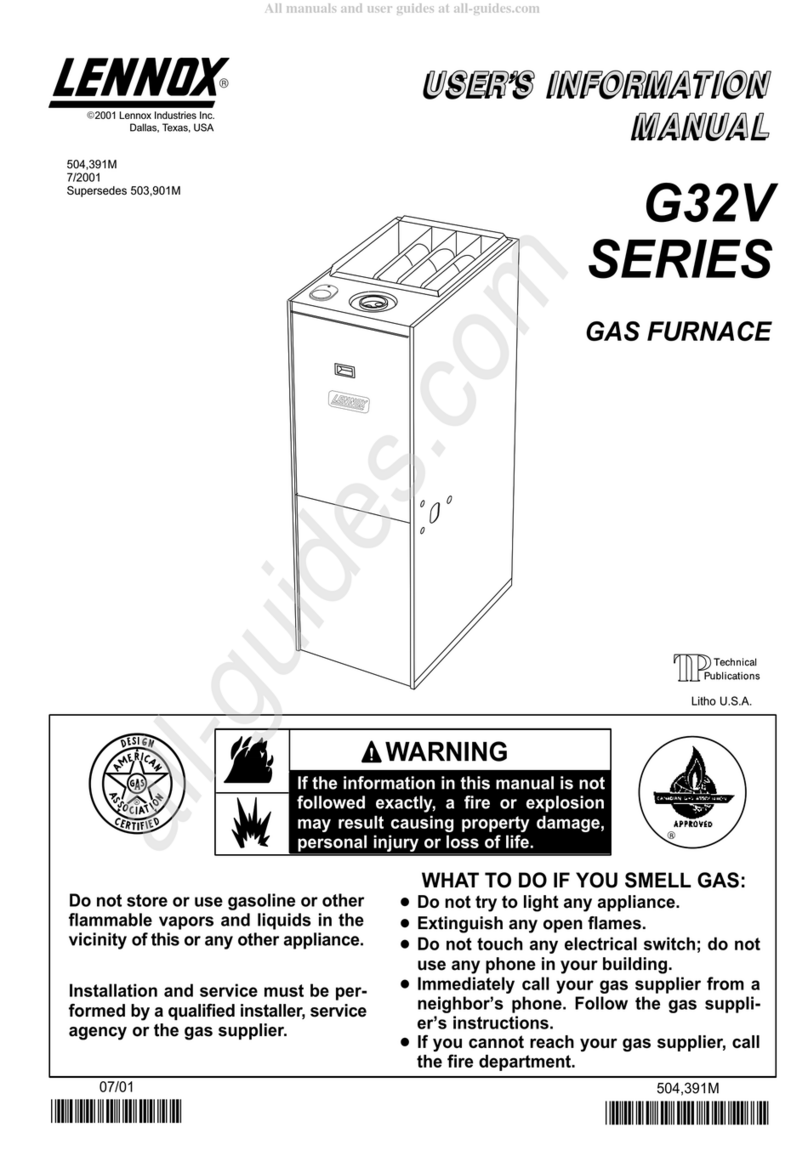
Lennox
Lennox G32V SERIES Guide
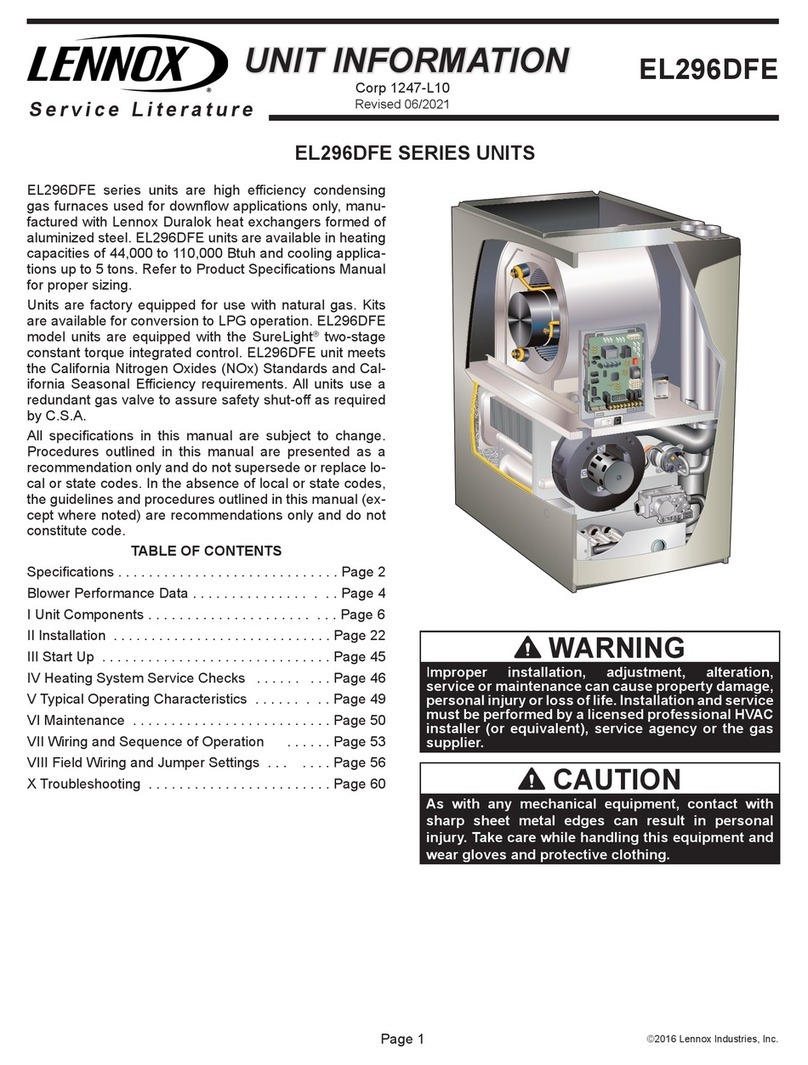
Lennox
Lennox EL296DFE Series User manual
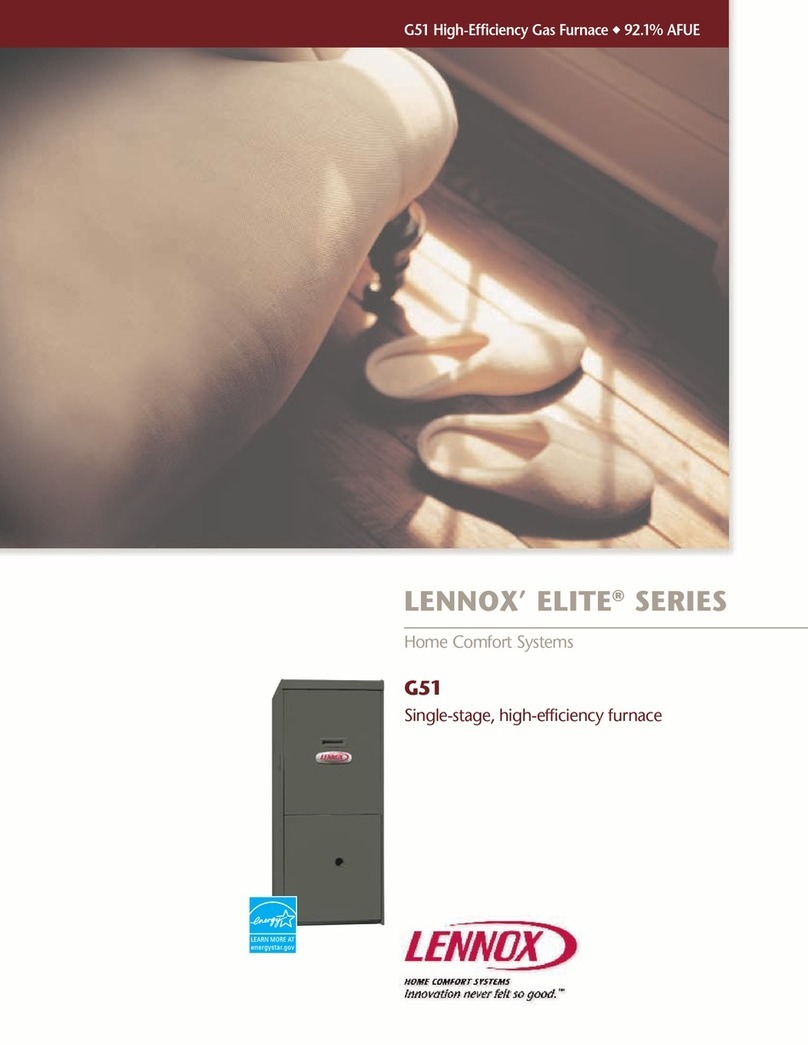
Lennox
Lennox G51 User manual
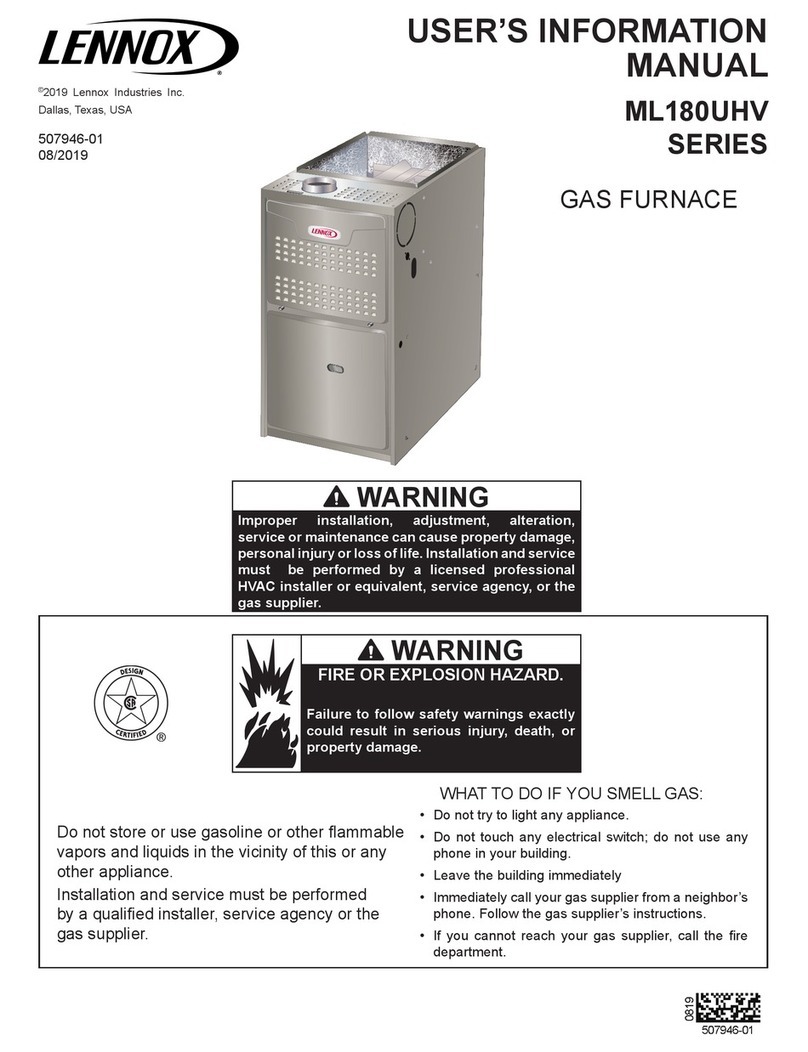
Lennox
Lennox ML180UHV Guide

Lennox
Lennox HART-1445-26 Assembly instructions
Popular Furnace manuals by other brands
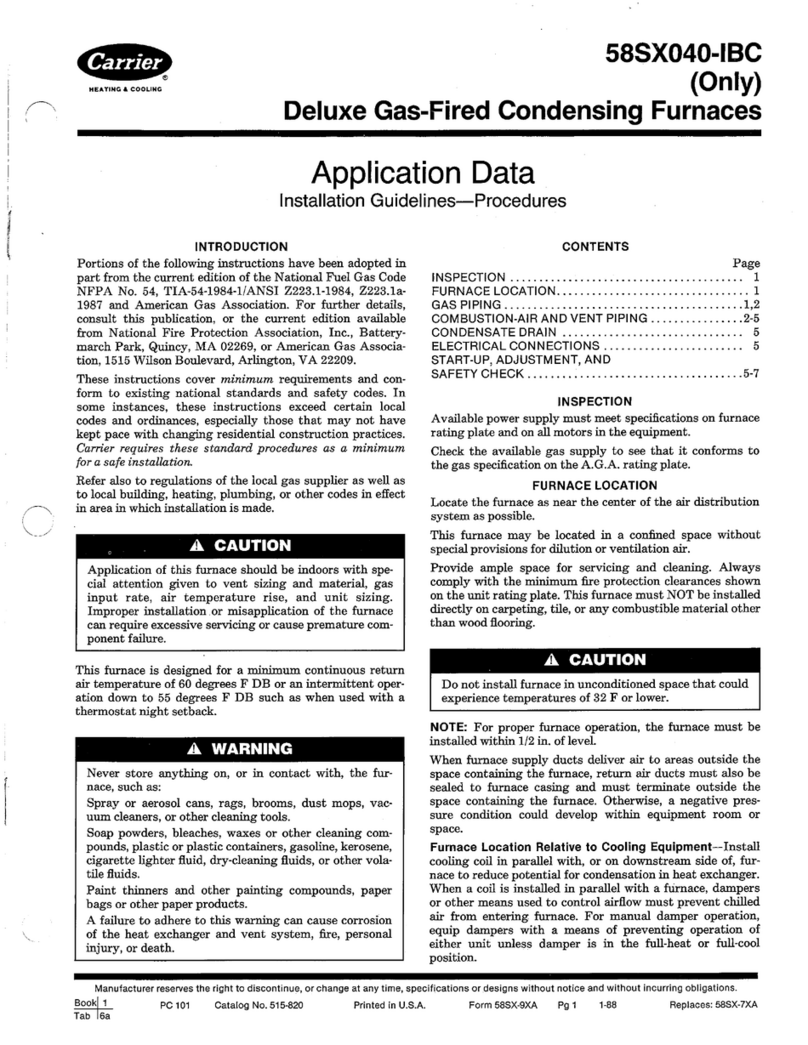
Carrier
Carrier 58SX040-IBC Application data
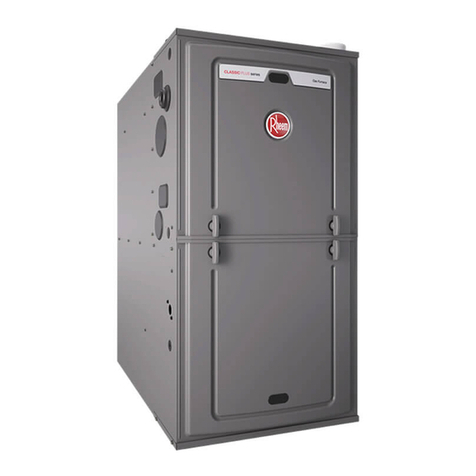
Rheem
Rheem 96V Series installation instructions

United States Stove
United States Stove HOTBLAST 1200G owner's manual
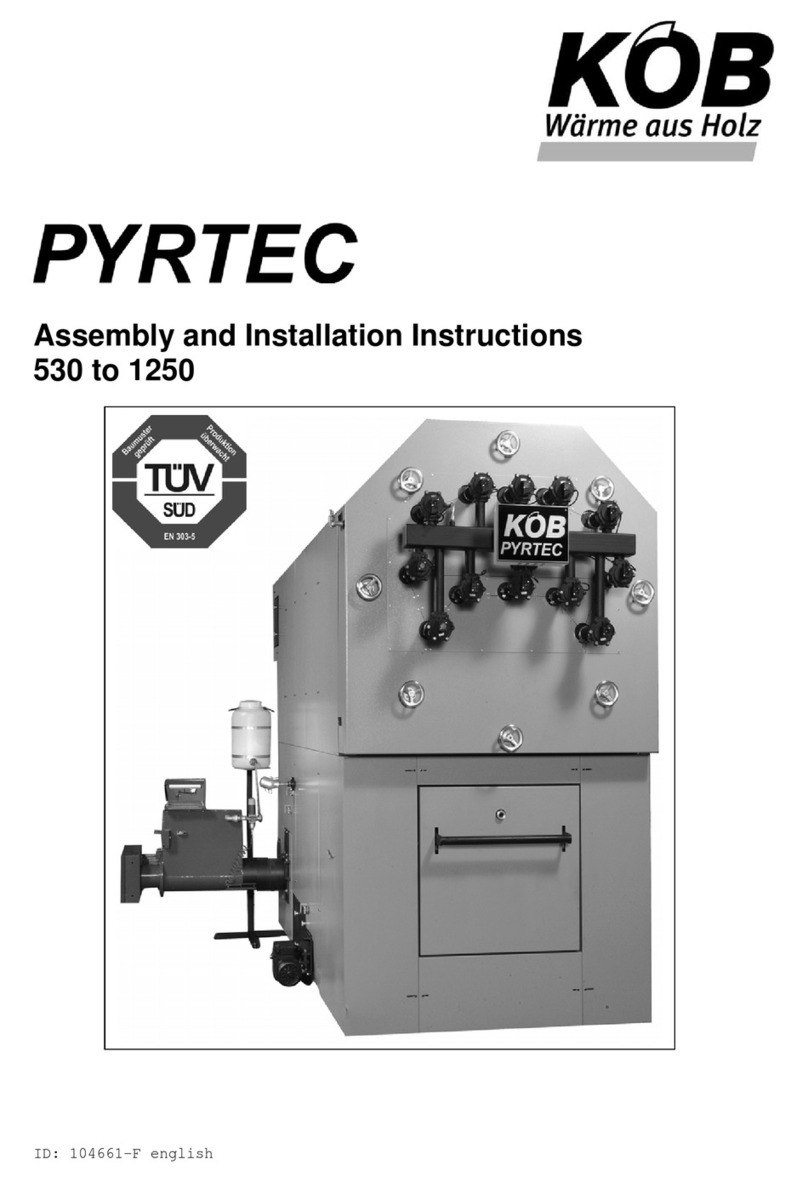
KOB
KOB KOB PYRTEC SERIES Assembly and installation instructions
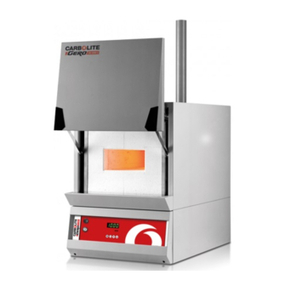
VERDER
VERDER CARBOLITE GERO AAF 11/3 Installation, operation and maintenance instructions
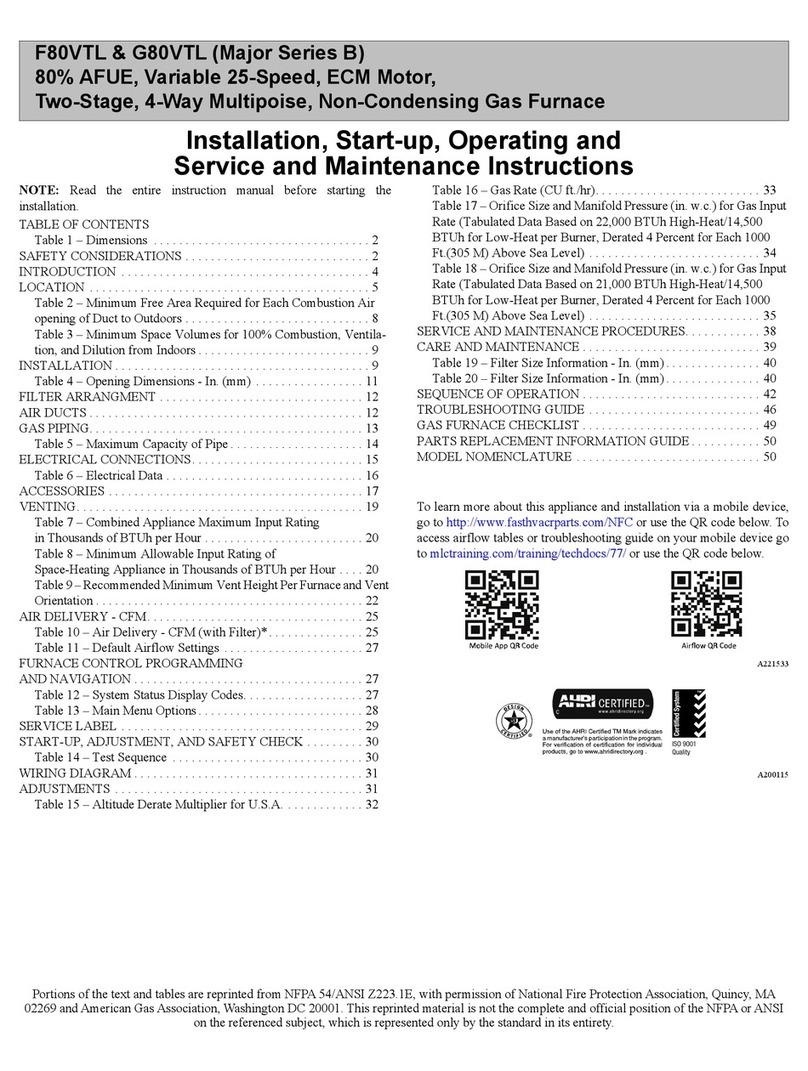
Carrier
Carrier F80VTL Installation, start-up, operating and service and maintenance instructions

Haier
Haier GE NF80DS installation instructions
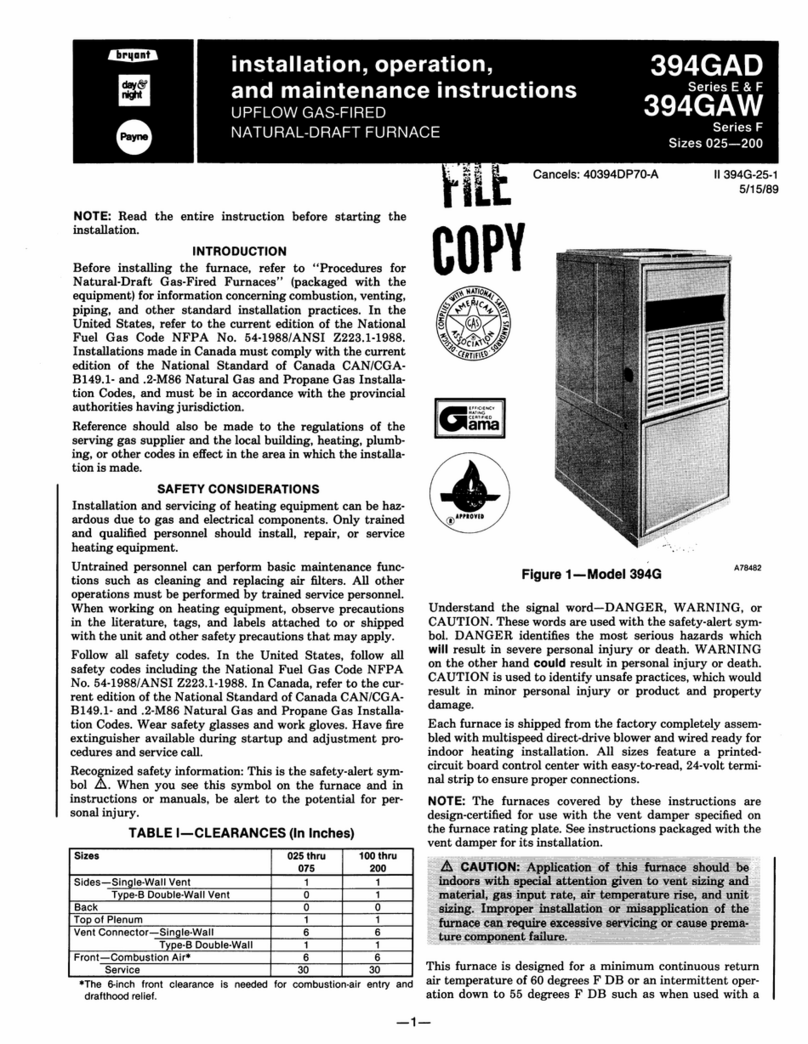
Carrier
Carrier 394GAD installation instructions
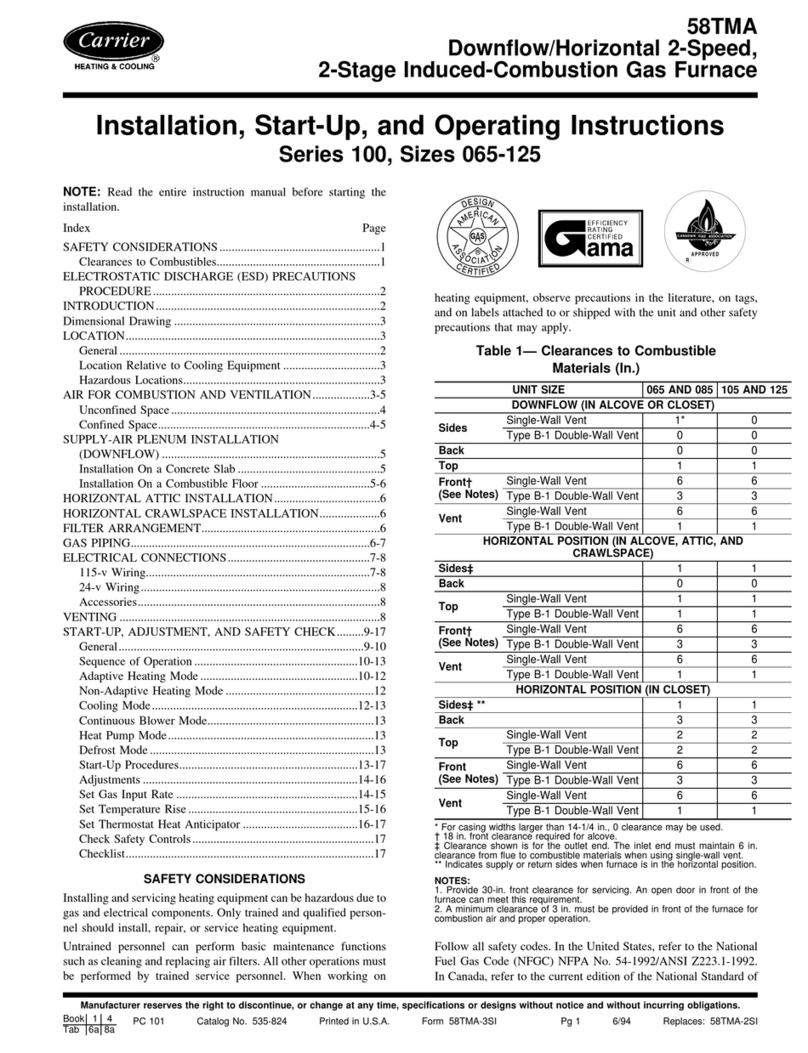
Carrier
Carrier 58TMA Installation, start-up, and operating instructions

Hotblast
Hotblast 1400E Owner's installation and operation manual
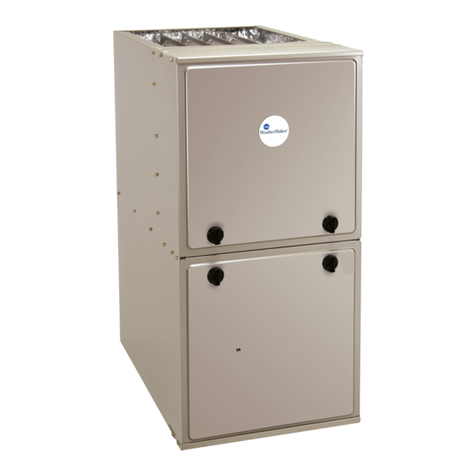
Carrier
Carrier PG96VTA Installation, start-up, operating and service and maintenance instructions
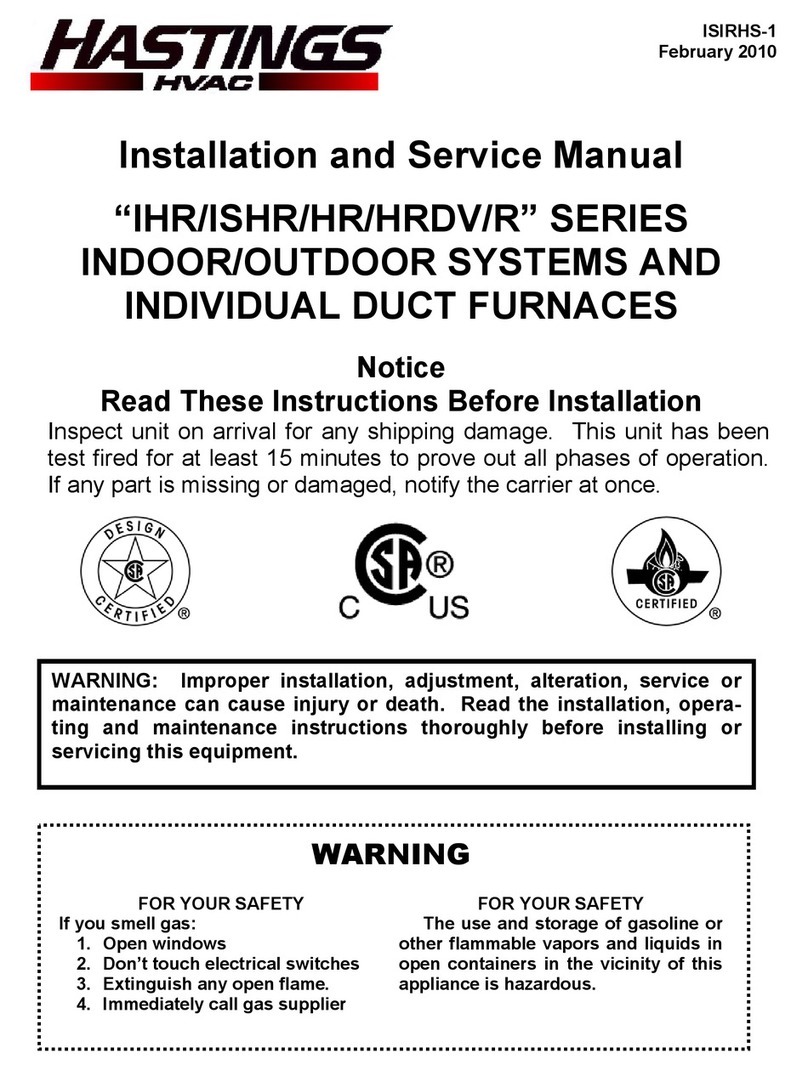
Hastings
Hastings IHR SERIES Installation and service manual
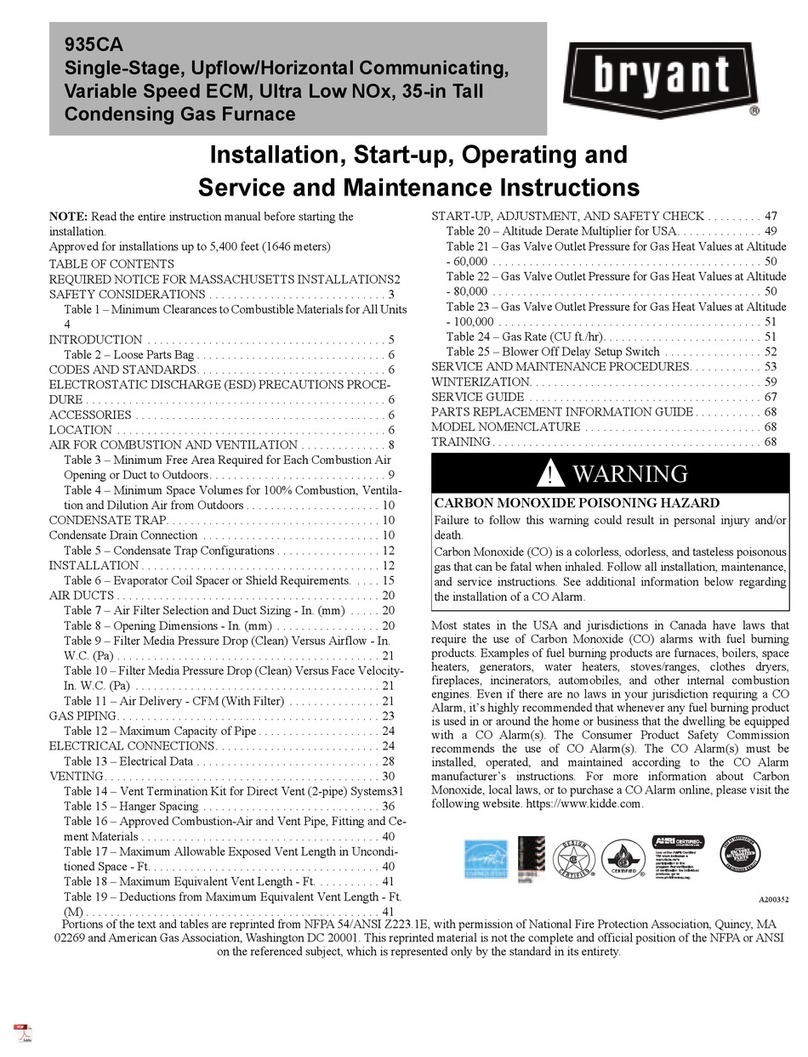
Bryant
Bryant 935CA Installation, start-up, operating and service and maintenance instructions

Bryant
Bryant 820SB Installation, operating, & maintenance instructions
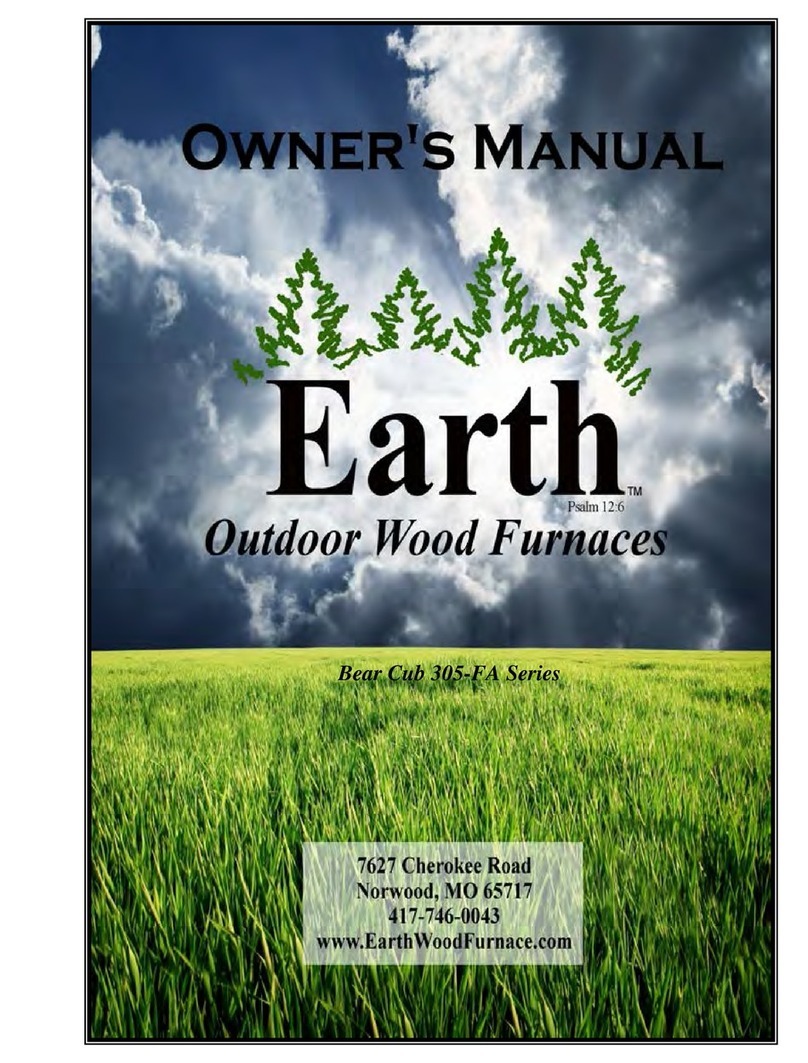
Earth
Earth Bear Cub 305-FA Series owner's manual
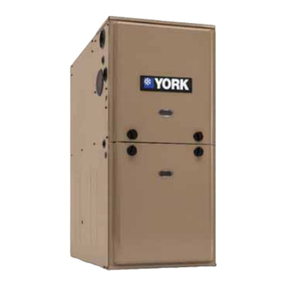
York
York TM9V*C installation manual
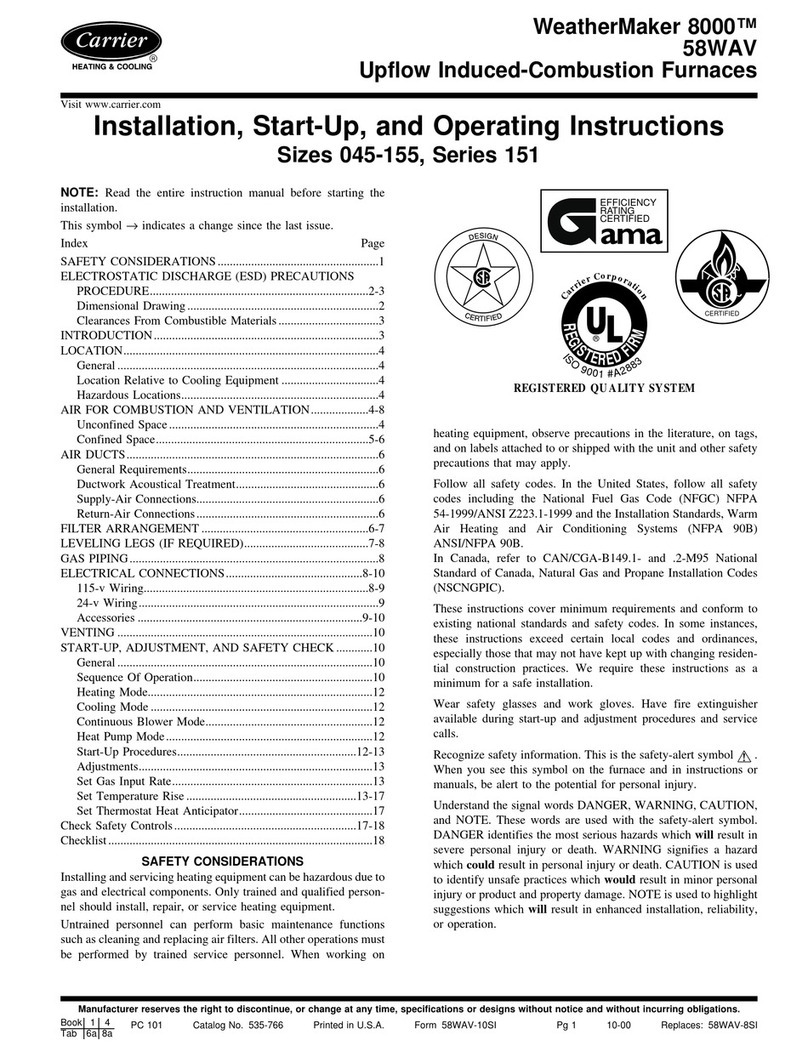
Carrier
Carrier WeatherMaker 8000 Installation, start-up, and operating instructions
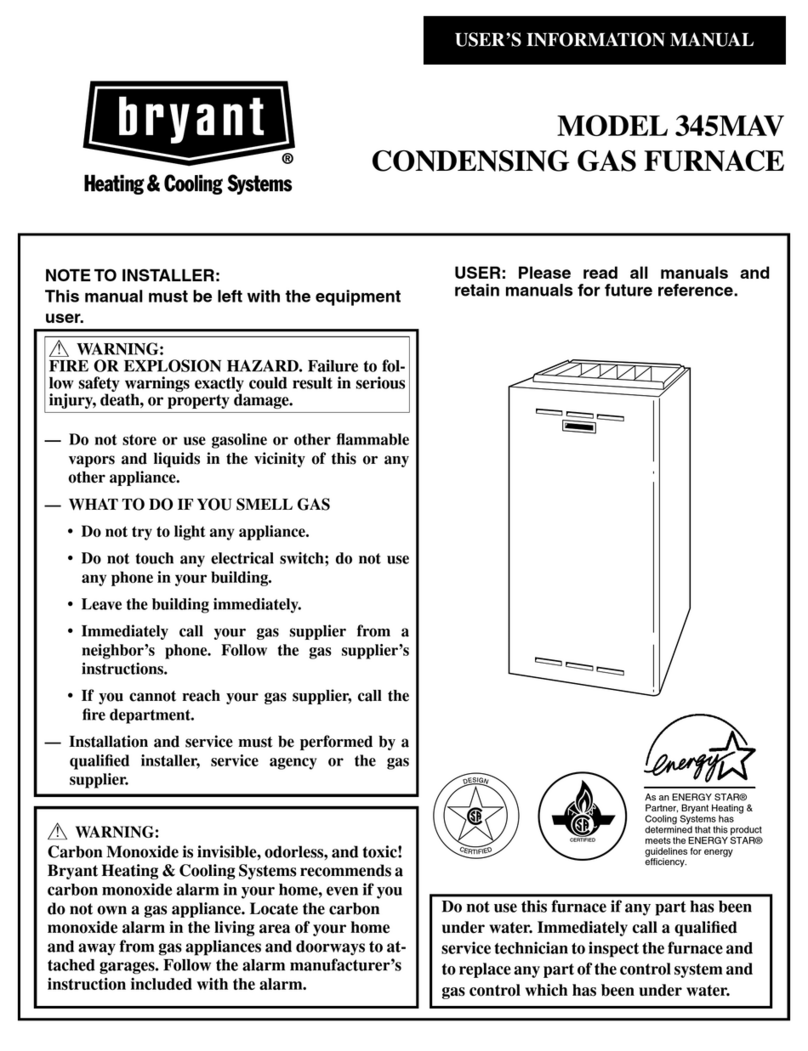
Bryant
Bryant 345MAV User's information manual