Mepu K-SERIES User manual

MEPU Oy
Mynämäentie 59, 21900 Yläne, Finland
www.mepu.com
K-SERIES MOBILE DRYER
OPERATING MANUAL
M180k, M205k, M240k, M275k, M300k, M365k and M420k
ID: D00125-2019_EN Rev.A

D00125-2019_EN 1
TABLE OF CONTENTS
1FOREWORD...............................................................................................................................3
1.1 WARRANTY AND WARRANTY TERMS ......................................................................3
2Important information for mobile dryer operators.......................................................................4
3Basics of grain drying..................................................................................................................5
4Technical specification of the mobile dryer.................................................................................6
4.1 Hopper and feeding auger conveyor....................................................................................7
4.2 Elevator................................................................................................................................7
4.3 Pre-cleaner and spreader......................................................................................................7
4.4 Grain bin ..............................................................................................................................7
4.5 Drying cells..........................................................................................................................8
4.6 Exhaust air cases and exhaust air aspirators ........................................................................8
4.7 Feeding apparatus ................................................................................................................8
4.8 Bottom trough, and bottom aspirator, sampling unit.........................................................10
4.9 Dryer furnace .....................................................................................................................10
4.10 Electrical equipment ..........................................................................................................10
4.11 Frame .................................................................................................................................10
5Deploying and positioning of a mobile dryer. ...........................................................................11
5.1 Mobile dryer deployed indoors..........................................................................................11
5.2 Power supply......................................................................................................................12
5.3 Electrical switchboard........................................................................................................13
5.4 Oil.......................................................................................................................................16
5.5 Smokestack ........................................................................................................................16
5.6 Dryer furnace .....................................................................................................................17
6Operating the dryer ....................................................................................................................19
6.1 Filling the dryer..................................................................................................................19
6.2 Drying ................................................................................................................................20
6.3 Emptying the dryer.............................................................................................................21
6.4 Dryer settings.....................................................................................................................22
6.4.1 Setting the filling delay..................................................................................................22
6.4.2 Cooling timer................................................................................................................23
6.4.3 Work/ pause time relay................................................................................................24
6.4.4 Setting the burner thermostat.....................................................................................25
6.4.5 Setting of the drying thermostat.................................................................................26
6.4.6 Setting of the feeding apparatus.................................................................................27
6.4.7 Setting of the pre-cleaner aspirator............................................................................27
6.4.8 Setting the spreader disc..............................................................................................28
6.4.9 Setting the air flow rate...............................................................................................29
6.4.10 Drying of partial batches.............................................................................................30
6.4.11 Cleaning the central channel after drying a partial batch.......................................32
6.5 Drying of different grain varieties .....................................................................................32
6.6 Aspects to be noted in respect of hot air dryers.................................................................32
7Maintenance...............................................................................................................................33
8Malfunctions ..............................................................................................................................35

D00125-2019_EN 2
9Concise operating instructions...................................................................................................37
9.1 In the beginning of the drying season make the following checks....................................37
9.2 Filling.................................................................................................................................37
9.3 Drying ................................................................................................................................37
9.4 Emptying............................................................................................................................38
9.5 After the drying season ......................................................................................................38
10 Technical data ............................................................................................................................39
11 User settings...............................................................................................................................42
12 Declaration of conformity..........................................................................................................44

3 D00125-2019_EN
1FOREWORD
This Manual contains instructions for operating a K-series mobile dryer.
Before starting to use the dryer please read the Manual carefully, and familiarise yourself with the
operations and precautions, in order to ensure that you use the unit efficiently and safely.
Keep this Manual at hand, and review it always with any new employees. If you need additional
information or help, please call your machine dealer or the Mepu Oy service number.
1.1 WARRANTY AND WARRANTY TERMS
This product is intended for professional use. Installation, operating and maintenance of the
equipment presumes general skills and understanding of machinery and equipment, which a
professional farmer is expected to have.
The warranty period is one (1) year in agricultural use. The warranty period starts from the
delivery of the product. The warranty period for the furnace and the heat exchanger is seven
(7) years.
The warranty does not cover any damages caused by misuse or any other damages resulting
from the same.
The warranty covers faults caused by poor workmanship and materials. Damaged parts are
repaired or replaced with serviceable parts. If however it is established that the damage is
not covered by the warranty, we shall charge for any expenses connected with the same.
Warranty repairs do not extend the warranty period.
The warranty does not cover consequential damages, resulting losses, lost profit, shipping
costs, travel expenses, down time, modification of the original structure of the equipment or
any other economic losses.
The warranty shall apply in the event that the equipment has been installed, operated and
maintained observing the instructions of the manufacturer and any effective regulations.
The warranty does not cover premature wear or damage of parts resulting from negligent
maintenance.
Any matters related to warranty and possible expenses have to be pre-agreed with Mepu Oy before
performing any repairs.

4 D00125-2019_EN
2Important information for mobile dryer operators
Avoid falling down
After having installed the grain silo fasten the ladder and back rails as well as the roof
guardrails. Be particularly careful when working on the roof in rain, or if the roof is
covered with ice.
Disconnect the dryer power cable from the network when you:
-Remove protective covers to carry out maintenance or adjustment work.
-Clean the bottom part of the elevator or the auger conveyor channel.
-Adjust the tension of the elevator chain or the conveyor V-belts.
-Go into the grain silo to adjust the spreader disc.
-Open the burner for maintenance.
Fire hazard; make sure that the dryer and its surroundings are clean
-The discharge pipes of the pre-cleaner and the bottom aspirator must be led
sufficiently far from the dryer, and preferably take them via the cyclone to the
debris bin. The air sucked into the furnace must be absolutely clean.
-Damp and partially dusty air from the side air channels must be led sufficiently
far away from the dryer, so that it is not mixed into the furnace intake air.
-Mixing exhaust air with furnace intake air significantly reduces drying efficiency.
-It is advisable to check the cleanliness of the internal bottom of the furnace and
the exhaust air channels every 100 hours. Moreover, at the end stage of every
grain batch being dried, open the discharge lever, which is situated between the
feeding apparatus and the elevator at the back of the dryer.
Avoid oil spills
Having adjusted the burner pressure make absolutely sure that you have closed the
pressure gauge tap. If the tap is left open the pressure gauge can be damaged and fuel
oil could spill into the environment. Protect the oil hoses between the oil tank and the
burner such that they cannot be damaged by moving objects or people around the
dryer.
Additional lighting
The drying season is at the end of summer, when evenings and nights are already dark.
Therefore make sure that there is sufficient additional lighting around the dryer to
ensure work safety.
Filling and emptying of the dryer
When you fill or empty the dryer make sure that no bystanders are threatened by the
risk of being run over by the moving units or get crushed between the trainer and the
hopper.
Extinguishing equipment
During the working season there must be a 12 kg ABE-3 type fire extinguisher on the
dryer.
Operating instructions
Remember to read the operating instructions before installation of or operating the
unit.

5 D00125-2019_EN
3Basics of grain drying
The keeping quality of harvested grain depends on its moisture content and the grain temperature
achieved by the method of storage. Under the conditions in Scandinavia and the northern
hemisphere, the moisture content of grain after harvesting varies typically between 15–45%, which
requires taking measures to improve the keeping quality of grain. The climatic conditions in the
northern hemisphere prevent from achieving sufficiently low moisture content figures if just natural
drying processes are used. During the harvesting season the relative air humidity can reach as high
as 80–90%. Thus drying methods where no auxiliary equipment is used cannot produce low
moisture contents. Therefore grain has to be handled applying various methods in order to improve
its keeping quality. The established handling methods include various drying techniques and –in a
smaller scale –freezing of grain.
The functioning of dryers is based on strong air flows circulating through the grain batch being
dried, and subsequently discharging the air into the atmosphere. Dissipation of moisture can be
facilitated by increasing the temperature of the grain being processed. The homogeneity of drying
quality can be increased by circulating and cooling the grain during the drying process.
However, there are certain basic rules involved in the drying process, which should be observed to
prevent drop of grain properties, such as germinative capacity or baking properties. The most
important aspects that need to be monitored are grain temperature, circulation rate and air flow.
These values vary by individual grain types and the case-by-case temperature settings must be
determined through experience. The values are also affected by some dryer-specific aspects.
Approximate drying air temperatures:
Seed grain 50 … 60o C
Bread grain 60 … 70o C
Fodder grain … 80o C
Recommended grain temperature:
Below 45o C … germinative capacity drops
If drying is carried out in hot weather, make sure that the grain is circulated and dried property in
order to avoid overheating.

6 D00125-2019_EN
4Technical specification of the mobile dryer

7 D00125-2019_EN
4.1 Hopper and feeding auger conveyor
Grain is loaded into the filling hopper equipped with a bottom conveyor, which feeds
grain to the elevator. In rubber flap elevator models, the feeding auger conveyor
features a manual disconnect switch, which allows disconnecting the auger conveyor
from the rest of the removal equipment for the time of drying. The standard filling
hopper is a 1.3m3 longitudinal hopper, which allows to dump the grain from the side,
either from right or left. In bucket elevator models, the feeding auger operates with its
own motor.
4.2 Elevator
Mobile dryers equipped with a rubber flap elevator:
Grain is lifted to the top of the dryer with a chain elevator. There is a 2-way divider at
the top of the elevator, which allows feeding the grain either into the pre-cleaner and
from there into the dryer, or into the discharge pipe. The bottom conveyor of the dryer
is also powered by the elevator motor.
In a smaller model (180), the top of the elevator can be turned town to reduce the
transport height.
Mobile dryers equipped with a bucket elevator:
The elevator is the Skandia bucket elevator featuring steel buckets. In this case the
bottom conveyor is always equipped with its own motor.
The bottom trough under the bottom cone is equipped with a rotation sensor. The
rotation sensor stops the unit when the dryer gets clogged.
4.3 Pre-cleaner and spreader
From the elevator, grain flows directly along the trough into the pre-cleaner, from
where the grain will move directly to the
spreader. The task of the motor-driven spreader
disc is to spread the grain evenly throughout the
grain bin. The vertically adjustable spreader disc
is connected to the top conveyor via a bevel gear.
4.4 Grain bin
Moist grain swells when its temperature rises.
When the drying process progresses the volume
of grain is reduced significantly. The grain bin of
the mobile dryer is optimised to function under
any conditions. The purpose of a large grain bin is
to act as a buffer when the grain level varies,
which happens due to pre-cleaning and drying of
the grain.
Guardrails and the access platform included in the standard delivery are attached to the
top of the grain bin. There is an inspection hatch at the rear of the bin, which is used to
monitor the dryer filling process. The standard delivery set also includes a rotating
level guard, which stops the filling process when the dryer is full. The manhole on the
roof gives access into the bin for adjusting the spreader disc or cleaning the insides of
the grain bin.

8 D00125-2019_EN
4.5 Drying cells
The drying cells have many air ducts. The drying process is uniform, because air is
blown into the central channel between the drying cells, from where moist air is
discharged through the drying cells towards the sides into the exhaust air cases. In the
rear part of the central channel there is a cleaning/ inspection hatch. There are shutters
preventing air flow installed between the cells for drying of partial batches.
4.6 Exhaust air cases and exhaust air aspirators
The task of the exhaust air cases is to collect the humid air from the drying cells, which
is then lead through the exhaust channels towards the sides of the dryer. One of the
exhaust channels features a thermostat that measures the exhaust air temperature. The
digital display of the thermostat is located in the electrical switchboard.
The exhaust air aspirators for the exhaust air cases are available as optional equipment.
The aspirators serve to reduce condensation of moisture in the exhaust air cases. The
aspirators also improve ventilation inside the dryer.
4.7 Feeding apparatus
During the drying process grain flows from the rotating feed rollers evenly down into
the conical base. There are six speed rollers in the dryer. At both ends of the feeding
apparatus there are movable hatches for cleaning the feed rollers.
The volume of the feeding apparatus is 0.81 cubic metres. The shafts feature with ball
bearings at each ends, and a nylon sliding contact bearing at the centre. There is a
hatch underneath each feed roller, which is opened when the dryer is unloaded.
The five blade feed roller functions smoothly, even when the grain humidity is high,
and the feed rate stays uniform in terms of volume throughout the entire drying
process, regardless of the moisture content of grain. However, it is important to note
that the flow increases in terms of weight towards the end of the drying process as the
grain size is reduced.
The steep-angled feed troughs ensure even drying process and reliable circulation
under any circumstances. The structure of the feeding apparatus is very tight, allowing
to dry even small seeds (such as turnip rape).
The feeding apparatus features a bottom hatch shut-off mechanism to open and close
the bottom hatches. The opening mechanism is operated either with a cam.

9 D00125-2019_EN
The feeding apparatus with a cam operated bottom hatch opening mechanism features
a separate cam for opening and closing every bottom hatch. In such a feeding
apparatus the second and the fifth cam (see Figure) has an intermediate position, which
can be used to control the flow of grain into the bottom trough when the hatches are
opened with the cam.
CLOSED INTERMEDIATE POSITION OPEN

10 D00125-2019_EN
All bottom hatches must be closed during the drying process or
filling the dryer!
The bottom hatches must not be closed, if there is grain in the
bottom trough (risk of damage).
The driving engine of the feeding apparatus is an inverter-controlled
gear motor, from which the rotating movement is transmitted
through the chain drive to the feeding shafts. At the production
facility the grain circulation rate is adjusted to approximately 182 hl/ hour. The feeding
amount can be freely adjusted by rotating the control
knob on the electrical switchboard.
4.8 Bottom trough, and bottom aspirator, sampling unit
The steep-sided bottom trough is made of durable hot
galvanized steel plates. The bottom aspirator removes
dust and steam from the bottom trough, keeping the
elevator clean throughout the entire drying process.
From feed rollers the slanting sides of the trough direct
grain to the bottom conveyor on the bottom of the
trough, which removes the grain to the elevator. The sampling unit is located in the
rear of the bottom trough. The sampling unit facilitates monitoring of the drying
process. Remove the cover and tilt the sampling tube downward and let grain fall into
the sampling bin.
4.9 Dryer furnace
All dryer models feature an efficient and durable furnace. Power range of the furnaces:
250–500 kW. The blower capacities /air rates are: 4.0–11 kW / 14000–24500 m3/h.
The burner flame burns in the middle of the cylindrical firebox, and heat is transmitted
into the vertical plate heat exchangers. The combustion chamber is made of fire-
resistant steel. The vertical heat exchangers release heat evenly and efficiently. This
ensures excellent efficiency and durability of the furnace.
4.10 Electrical equipment
The electrical equipment and automatic systems of the dryer are installed at the
factory. The dryer is ready for use as soon as the dryer's equipment is connected to the
respective outlets, the unit is connected to the power network, and
the oil burner hoses are placed into the oil tank.
Before starting any maintenance work remember to always turn
the main switch into the OFF position, or disconnect the power
cables from the network.
4.11 Frame
The sturdy steel beam frame and large air filled rubber tyres make it possible to
transport the dryer at the maximum speed of 50 km/h. During the drying process, the
frame must be supported at five support points. On M240k and larger dryers the wheel
shaft is supported with shaft supports. The drawbar can be detached to save space.
Towing of a mobile dryer filled with grain is categorically prohibited.

11 D00125-2019_EN
5Deploying and positioning of a mobile dryer.
Mobile dryers need not be placed in a building. The design of a mobile dryer permits using it
outdoors without any special protective structures. Nevertheless, it is advisable to build a light
unheated shelter around the dryer, or an element silo to be used as grain storage, which also gives
the structure its walls. If a more permanent building is constructed, note the aspects related to
building permits.
Always contact the local construction and fire rescue authorities before you start the
installation.
5.1 Mobile dryer deployed indoors
Air flows of a dryer positioned indoors shall be arranged such that dust from the cleaners and outlet
ducts does not get mixed into the dryer intake air.
When selecting the deployment site make sure that the required electrical and oil connections are
available. Select such location for the oil tank or oil barrels that the oil lines do not cross any
passageways, in order to prevent them from getting damaged. The oil tank must be placed at least 3
m away from the dryer.
In other respects the dryer shall be located in the optimal place and such that there is enough space
for the trailer-tractor combination for driving and turning around. The place where the dryer is
installed has to be as level as possible in relation to the frame of the dryer, and have sufficient load-
bearing properties, e.g. a concrete slab. Moreover, it is necessary to consider any dust and noise
hazards.
Before commissioning the dryer it is advisable to set up
a block for the trailer, in order to avoid damaging the
hopper. If the dumping height of the trailer is low, it is
advisable to build a ramp for the hopper.
Air flows in an enclosed space
The intake air has to be taken from
outside the building using an
extension pipe (A). The debris/ dust
pile (B) of the pre-cleaner and the
bottom aspirator have to be led
through the cyclone out from the
building into a separate dust
collection bin. Exhaust air pipes (2
pcs) are taken outside the building
(C). The smokestack is led outside
the building (D). The grain line is
installed such that the loading is
flexible (E). Make sure that the
furnace gets dust-free air in any
conditions.

12 D00125-2019_EN
5.2 Power supply
The electrical equipment is installed and tested at the factory. The unit is equipped with a 10 m
electrical cable with either 32 A or 63 A plugs. If you need more cable, it has to be of the VSEN
5x6 mm2type. Any dryers sized 240K and larger: use cable 5 x 16 mm2. An undersized cable can
overheat, causing hazards and other malfunctions. If more than 50 m of cable is needed, check with
the local electrician to establish the proper cable size.
The elevator, pre-cleaner, the spreader and the feeding auger conveyor with its own motor,
are connected to the power circuit of the dryer via the sockets located on the electrical panel
on the rear wall of the dryer. The panel also features the I/0 switch operating the conveyor
equipment.
The bottom aspirator is connected to the socket (2) at the
front of the bottom trough.
The speed sensor of the bottom conveyor is connected to
the rectangular socket (3) located on the front side of the
bottom conveyor and the bottom trough.
The bottom conveyor featuring its own motor is connected
to the power socket (1) on the front wall of the bottom
trough. OPTION
Dryer power supply
The feeder cable is connected to the connector on the side of the electrical switchboard. If the cable
is connected to the power network, the main fuse capacity has to be at least 25A–63A, depending
on the equipment installed on the unit. If the unit is connected to the power network and the main
switch is turned to position I, the work lights of the unit (1 next to the electrical switchboard, 1 at
the rear of the unit) are turned on.
The cable and the fuse size of the unit vary depending on the equipment installed on
the unit.
When connecting the unit to the power network, make sure that the main switch is
in the OFF position.
Checking the rotation directions
The rotation directions of all motors are checked at the factory during the test run. However, when
you connect the dryer at the deployment site it is advisable to recheck the directions of rotation. The
best way to do it is to check the direction of rotation of the furnace fan. Keep the dryer mode switch in
the position 3 (drying) for about 3 seconds, and after that it is possible to check the rotation direction
of the furnace fan. The correct direction is indicated on the sticker located under the fan's intake.
If the dryer's power supply is moved to another socket, or if the dryer’s extension
cord has been replaced, check the rotation direction again.
Also note that the power supply has to be a five-wire system, i.e. L1, L2, L3, N and PE.

13 D00125-2019_EN
5.3 Electrical switchboard
A. Group fuses and earth leakage circuit breaker. The actuators are
protected by fuses and an earth leakage circuit breaker.
B. Main switch. Under the protective cover. The electrical equipment of the
dryer can be disconnected from the power network. The switch must
always be turned to OFF position, when any maintenance work is carried
out.
C. Drying process selector switch, see section: 6. Operating the dryer, on page
20
D. Emergency stop button. The emergency stop button is used to stop the
dryer in case of an accident or emergency (may be used only in case of an
emergency).
The electrical switchboard has been pre-installed, adjusted and tested at the
factory.
Data label of the switchboard.
Using the number and the year of the label
you can order new electrical switchboard
labels, if necessary.
Electrical switchboard cabinet,
Signal lights and control buttons
The operation mode switch must be on 0-postion when using manual controls
Actuator
Actuator use
Emergency stop reset
Resetting the emergency stop button. Before resetting, all
emergency stop buttons must be released. Emergency stop
buttons can be released by rotating or pulling them upwards.
After this, press the emergency reset button.
Cooling
Lights up when the cooling is switched on.
Drying
Lights up when the drying is switched on.
Dryer full
Lights up when the dryer is full.
Rotation detector malfunction/reset
Lights up if the rotation detector has malfunctioned, stops the
bottom auger and the elevator. Press button to reset.

14 D00125-2019_EN
Overheat
Light when overheat limit is reached
Engine protection
Frequency converter malfunction
Channel fans
Channel aspirators can be switch off or put on during the
drying process.
Workpause time relay
Activate or deactivate work-pause time relay
Feeder speed
Adjusts how quickly the grain rotates inside the dryer
Channel fans
Manual control of the elevator (Operation mode switch 0-position)
Elevator
Manual control of the elevator (Operation mode switch 0-position)
Bottom conveyor
Manual control of the bottom auger (Operation mode switch 0-position)
Feeding conveyor
Manual control of the feeding conveyor (Operation mode switch 0-
position)
Precleaner
Manual control of the precleaner (Operation mode switch 0-position)
Feeder /Bottom fan
Manual control of the feeder/bottom fan (Operation mode switch 0-
position)
Main fan
Manual control of the main fan (Operation mode switch 0-position)
Under the protective cover
Cooling timer
Adjusting the length of the cooling time. Cf section: Cooling
timer Cooling timer, page 22
Work/pause time relay
Cf. section: Work/ pause time relay Work/ pause time relay,
page 25
Drying thermostat
Adjusting the temperature range of the drying; i.e. at what
temperature the drying will move on to cooling.
Burner 2-flame thermostat
Adjusts the blasting temperature from the furnace to the
dryer.
The blower and the overheating thermostats are read
from the position of 9 o'clock. Both thermostats are
pre-set at the factory. See section: Factory settings,
on page 18

15 D00125-2019_EN
Electrical switchboard upper cabinet
If the group fuses tend to trip often, contact an electrician to have the unit fixed so that it is safe to
use.

16 D00125-2019_EN
5.4 Oil
So that the warranty would remain valid for the Oilon oil burner, fixed pipes must
be installed to the burner, and the installation work may be carried out only by a
company specialised in oil burner installations and approved by Tukes (The Finnish
Safety and Chemical Agency).
Check with the authorities in your country to find such approved specialised workshop. Information
about the burner and its installation can be found in the burner manual, which is included in the set
of dryer documents. Register your burner online through the Olion Care service to ensure the
validity of your warranty.
5.5 Smokestack
The dryer delivery set includes smokestack sections, connecting collars, the ash / soot removal
elbow, as well as a rain cap. The outlet pipe starting at the side of the furnace is connected to the
ash/ soot removal elbow and 2 or 4 m (depending on the size of the unit) smokestack sections along
with the rain cap. The smokestack sections are intended for outdoor use. When installing these
indoors, additional insulation is required; it is recommended to consult with the local fire safety
authority before the installation.
Contact the local fire rescue or construction authorities to establish the appropriate
location and height of the smokestack.

17 D00125-2019_EN
5.6 Dryer furnace
Deployment
The furnace installed on the mobile dryer is ready for use, after the on-site electrical and oil circuit
connections have been made. Before starting the drying mode, check the following furnace parts:
Check that the oil hoses are connected correctly (the arrow on the filter and the pump
indicate the suction and return sides).
Check that the oil filter is upright.
Check that the explosion hatch and the soot hatch are closed.
Check that the smokestack is compliant with the requirements and is tightly fastened to the
dryer.
The economy of the drying process can be significantly affected by two furnace related aspects:
Therefore, before commissioning the dryer, read the furnace operating and maintenance manual
carefully. The furnace settings must always be checked with the furnace installer in order to ensure
clean burning and low oil consumption. The warranty is valid, provided that the burner is serviced
annually by a professional.
Burners and nozzles
The nozzle capacities shown in the table are intended for 10 bar oil pressure. The nozzle capacities
can be reduced below the values shown in the table, if necessary. The 1 and 2 stage ratios can also
be modified, but the total capacity of the nozzles must not be exceeded.
Furnace
type
Burner
Max
power
[kg/h]
Nozzle size I
stage
Nozzle size
II stage
Nozzle power
kg/h
Flame plate
setting
[mm]
210
Oilon KP 26
19
4 gal 80°
14.2
46
210
Oilon KP 26 H
19
3.5 gal 80°
1.5 gal 80°
12.9 + 5.84=18.8
42
250
Oilon KP 26 H
23
4 gal 80°
2 gal 80°
14.2 + 7.4=21.6
43
300
Oilon KP 26 H
29
5 gal 80°
2 gal 80°
18.5 + 7.4=25.9
50
400
Oilon KP 50 H
38
6 gal 80°
3 gal 80°
23.4 + 11.6=35
2.7
500
Oilon KP 50 H
48
8.5 gal 80°
4 gal 80°
33.1 +14.2=47.3
4.6
The nozzle spray angle must be 80 degrees. Exceeding these nozzle capacities cause the
warranty to become void.
Furnace temperature settings
If the drying air temperature rises above the set value of the burner thermostat, the burner shall stop
and will restart when the temperature has dropped by 2–4o C.
If the furnace is equipped with a 2 stage burner (KP 26 H or KP 50 H), the thermostat has two
settings, one for 1 stage and the other –for 2 stage. In this case note that the setting for the 1 stage
has to be higher than the setting for the 2 stage. The idea is that the burner should never switch off
during the drying process; instead the 2 stage should compensate the variations of the outdoor
temperature. If the outdoor temperature drops, the 2 flame shall burn for longer intervals, while rise
of the outdoor temperature reduces the need for the 2 flame.
The setting value of the overheat thermostat is a bit higher than that of the burner thermostat, and it
makes sure that the temperature of the furnace does not rise too high. If the dryer is stopped in the
middle of the drying process, the fan thermostat stops the furnace fan only after the furnace
temperature has dropped below the temperature value set for the fan thermostat.

18 D00125-2019_EN
Factory settings
Unit
Type
Factory
setting
Action
Fan thermostat
Capillary
50 °C
The fan starts when the temperature is
exceeded. Always make sure that the
dryer power is switched on.
Burner thermostat 1 stage
Digital
90 °C
Puts the 1 stage flame off at this
temperature. The nozzle has to be
dimensioned such that it does not put
the 1 stage flame off.
Burner thermostat 2 stage
Digital
80 °C
Puts the 2 stage flame off at this
temperature.
Overheat thermostat
Capillary
120 °C
If the temperature is exceeded,
switches to overheat -> alarm.
Drying process setting
thermostat
Digital
50 °C
(30-50) °C
Factory setting 50°C, normal
operating setting 30–50. If
the set value is exceeded,
switches over to cooling.
Cooling timer
Digital
1h:30min
When the cooling is activated, the
clocks starts counting down the
cooling time. After the time has
lapsed, the unit is switched off.
Minimum value 1 min.
Level guard delay
Digital
5s
The period during which the dryer is
being filled after the sensor has given
the signal.
Pre-cleaner setting
Manual
1/2
At the mid-point. If it is open too
much, grain can get mixed into the
debris.
Pre-cleaner weight
Manual
Right at the
bottom
Evens up the flow of grain into the
dryer.
Spreader disc
Manual
Holes 3 cm
open
Down, and the bottom holes open by
ca 3 cm.
Main fan setting
Manual
Fully open
Limits the air flow if necessary.
Partial batch shutters or
central channel hatches
Manual
Open
Normally open. For partial batches –
closed. Opens or shuts off the air flow
to the top drying cells.
Feeding apparatus
hatches
Manual
Closed
To be kept closed Opened, if required,
for emptying.
Feeding speed
Electrical
5
At the mid-point. Measure the time
when emptying with the feeding
apparatus, and adjust the feeding
apparatus speed, if necessary.

19 D00125-2019_EN
6Operating the dryer
The drying process consists of four different stages. Filling, drying, cooling and emptying.
6.1 Filling the dryer
Preparations
Before starting the operations determine the suitable trainer dumping height, and remember to set
up a block for the trailer, to avoid damaging the hopper.
Check the following before dumping:
1. That the shutters of the feeding apparatus are closed. Make sure that all the shutters are
tightly closed.
2. That the divider at the top end of the elevator is in position 3 “drying”, i.e. the grain is
flowing into the dryer unit.
3. That the switching cam of the feeding auger is in the “closed” position.
4. That the air intake shutter is adjusted correctly, so that kernels do not fly into the debris
pipe.
5. That all the inspection doors are closed.
Filling
After preparation you can start filling the dryer by turning the selector
switch on the electrical switchboard to position 2 “filling”. This activates
the elevator system and the pre-cleaner motor. After that you can start
pouring the grain into the hopper.
If necessary, e.g. when the empty trailer is changed for a full one, the filling
can be stopped either with the 1/0 switch at the rear of the dryer, or with the
selector switch. If the time for changing the trailers is short (less than 15
minutes), there is no need to stop the filling process. If no new grain is
delivered, the conveyors should be emptied of the grain, in order to
minimise the clogging risk when the next filling process starts.
The level guard stops the filling process with a short delay, after the grain level has reached the
level guard sensor and blocked its rotating action. The level guard delay time is set at the factory.
When the dryer is full, there should be about 30 cm of free space below the lower edge of the
spreader disk.
If the dryer is too fill the grain blocks the functioning of the spreader disk. If the spreader disc
cannot rotate, the thermal relay of spreader disk will trip. Reset the thermal relay after about 15
minutes, and remove excess grain from the dryer.
To empty the dryer turn the divider away from the dryer, move the trailer under the pipe, and move
the selector switch to position 1 (emptying). Check the grain level from the manhole. After
discharging a sufficient volume of grain stop the emptying process by turning the selector switch to
position 0.
Before starting the drying process disconnect the hopper bottom auger from the elevator, by pulling
the switch cam backward. After that, close the shutter between the bottom end of the elevator and
the hopper. If necessary, you may leave some grain in the hopper.
In hoppers equipped with their own engine the auger is automatically controlled. When the filling
process is activated, the hopper auger starts automatically, and stops respectively, when the unit is
full.
This manual suits for next models
7
Table of contents
Popular Dryer manuals by other brands
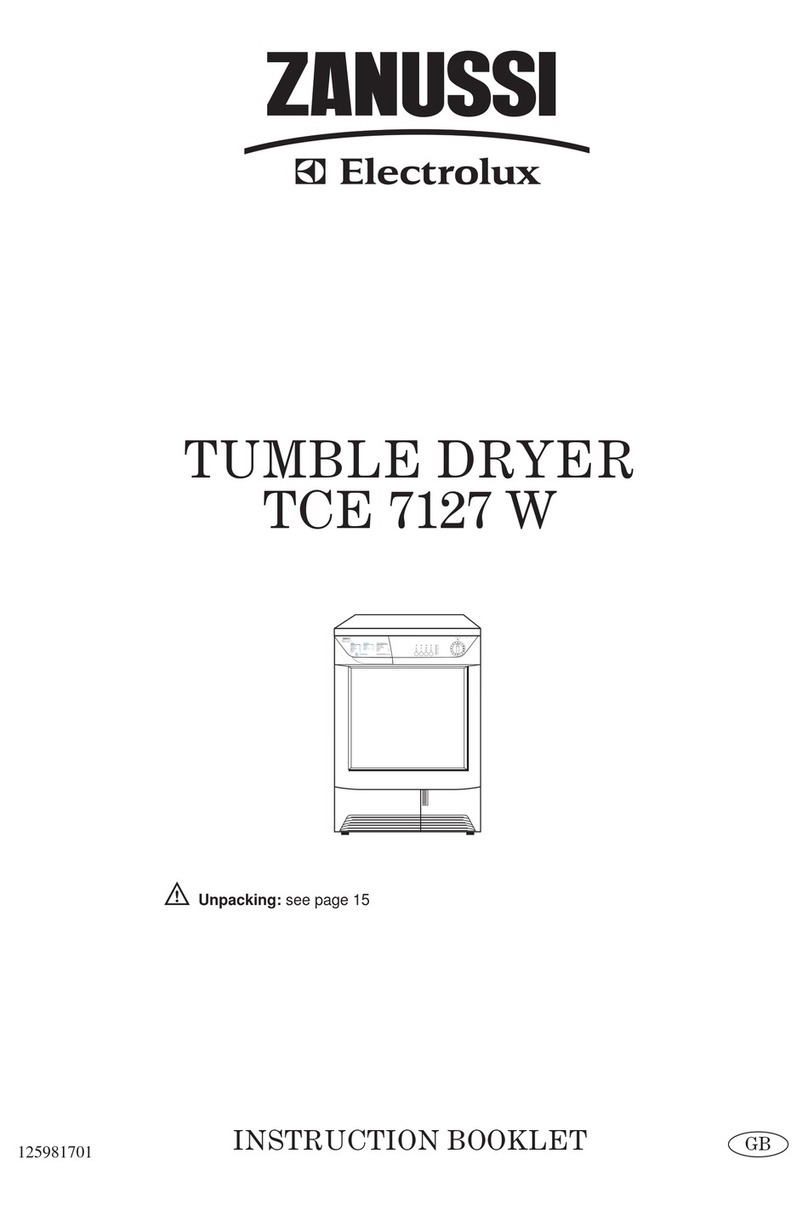
Electrolux
Electrolux Zanussi TCE 7127 W Instruction booklet
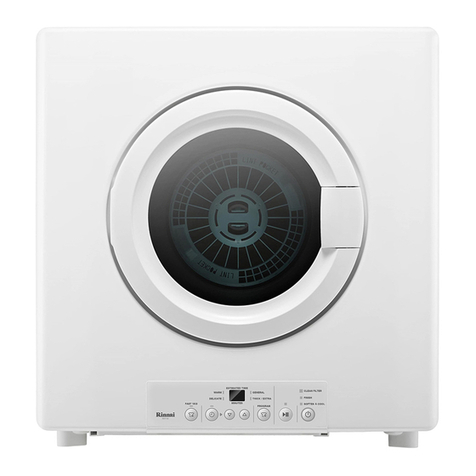
Rinnai
Rinnai RDT-62-RM-W operating instructions
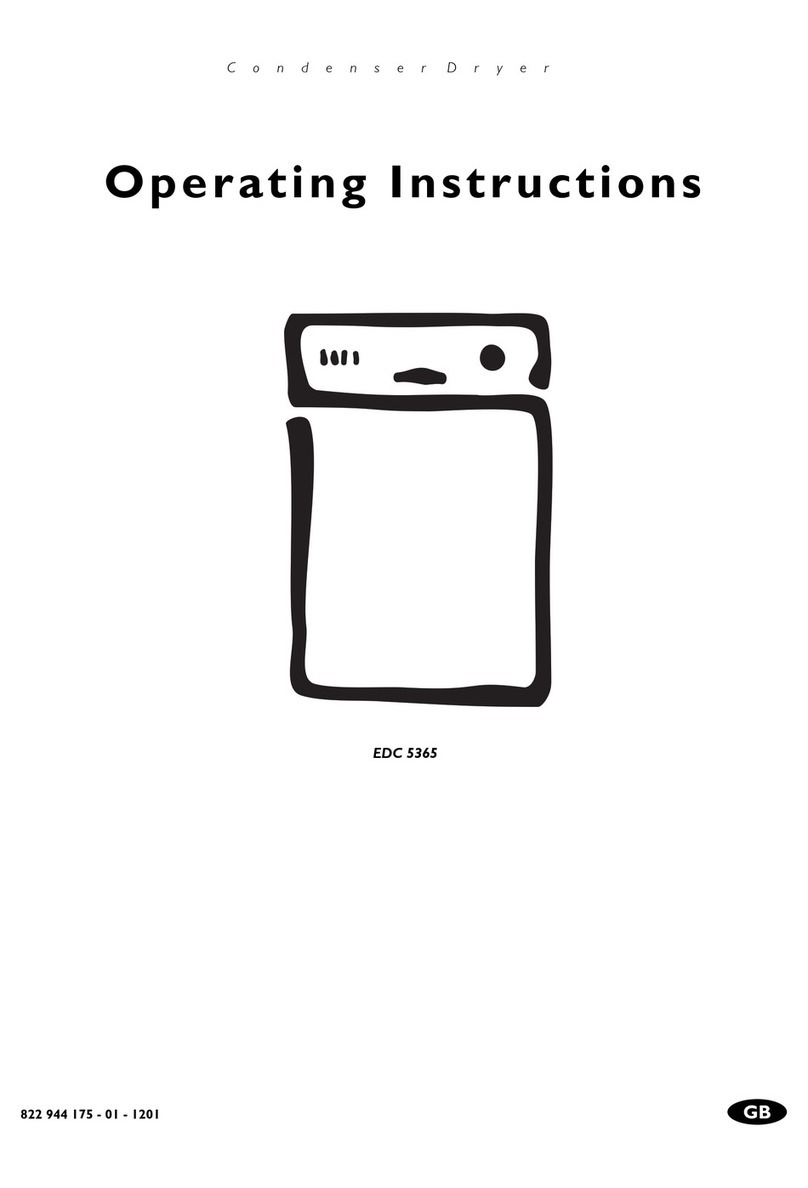
Electrolux
Electrolux EDC 5365 operating instructions
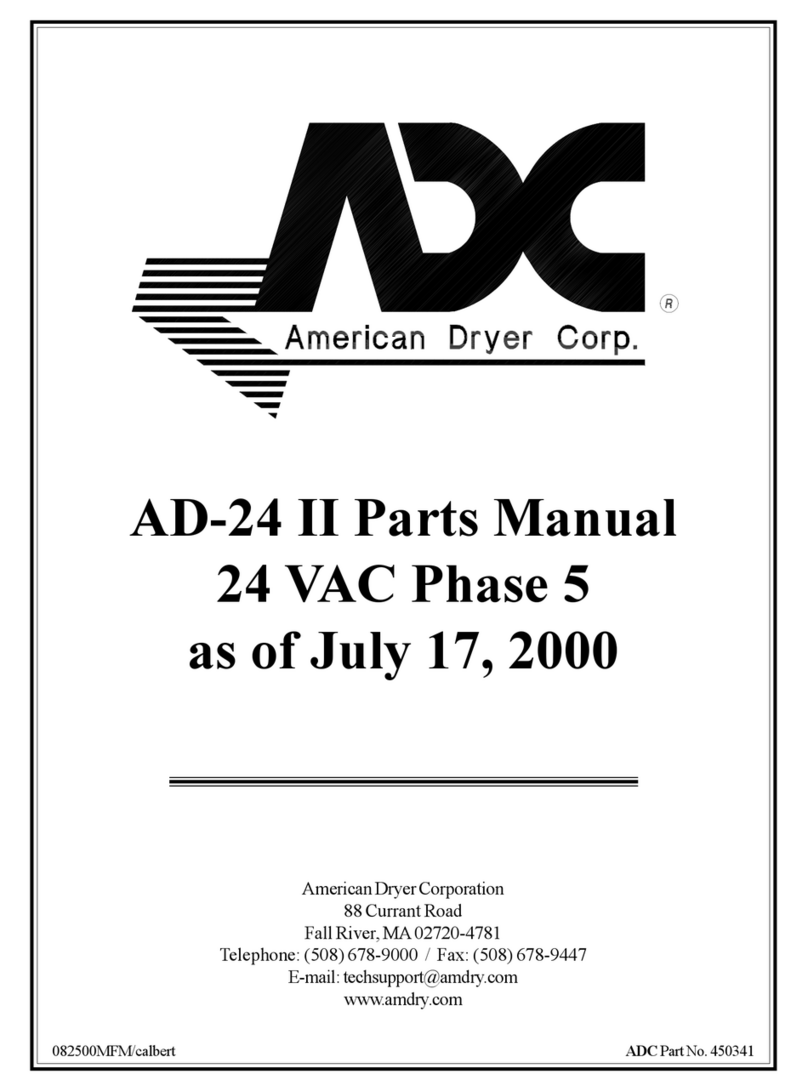
American Dryer Corp.
American Dryer Corp. AD-24 II parts manual
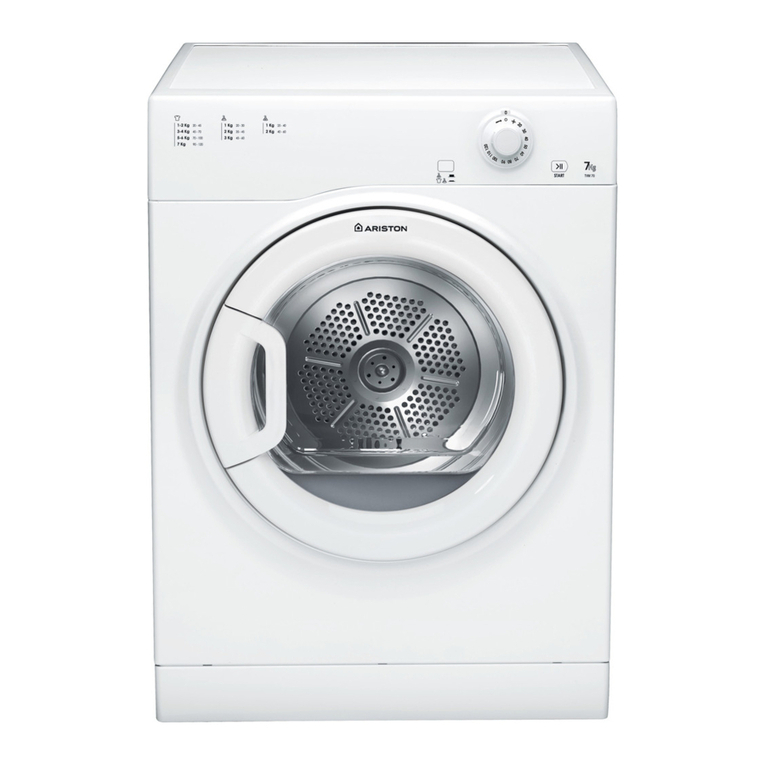
Ariston
Ariston TVM 70 Instruction booklet

Speed Queen
Speed Queen LES17 Specifications