Motrec E-300 Installation instructions
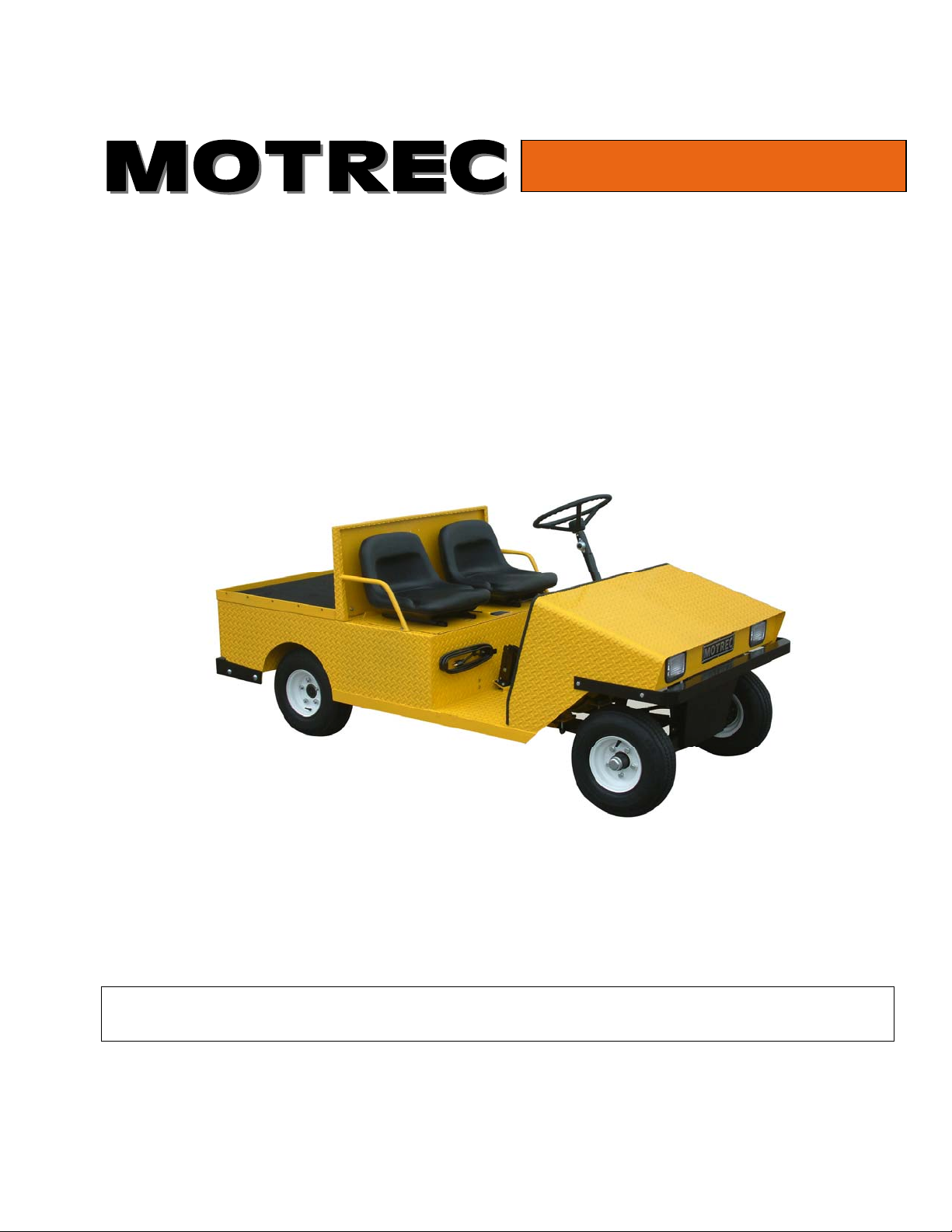
E-300
OPERATOR AND MAINTENANCE MANUAL
SPARE PARTS LISTS INCLUDED
SERIAL NUMBER : 1034258 & UP
Printed in Canada
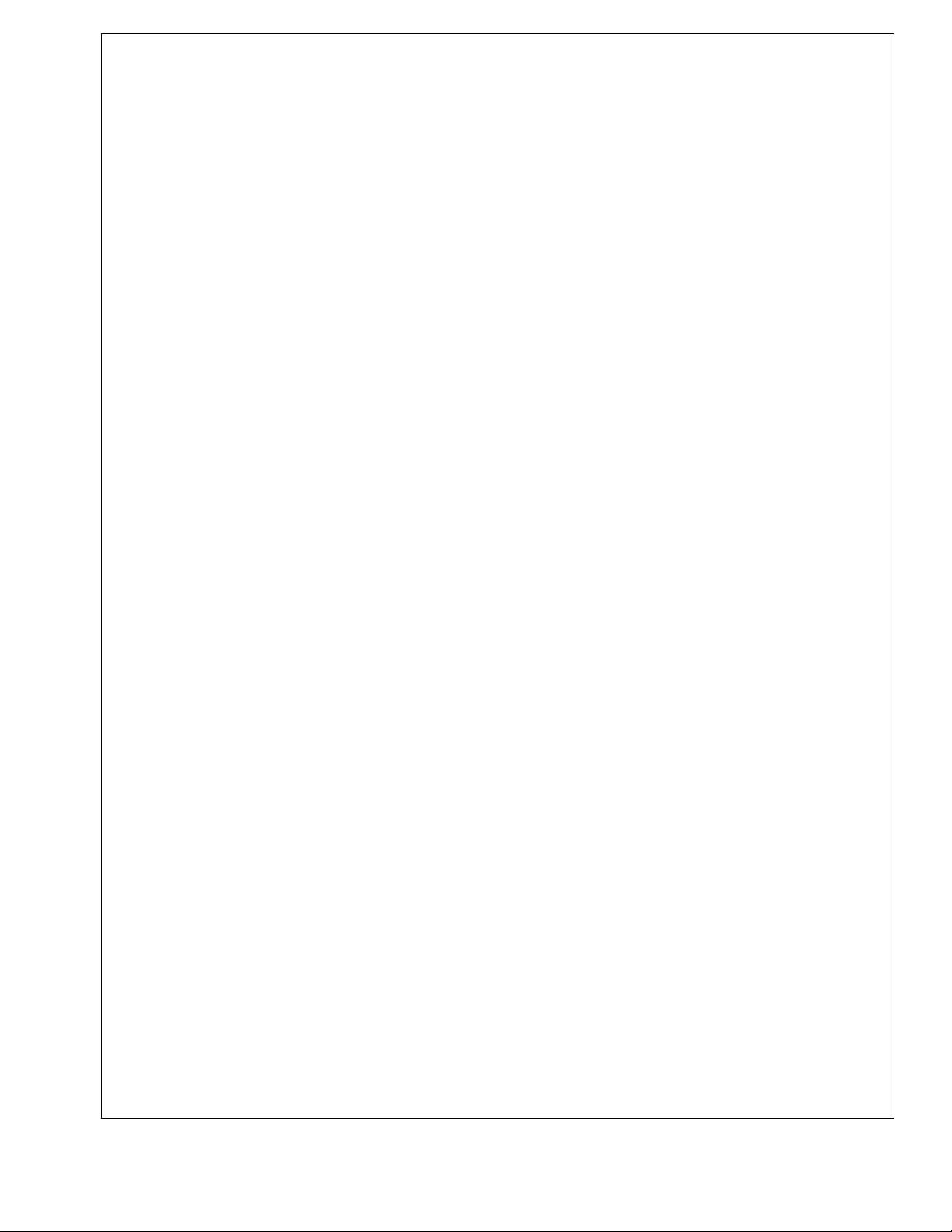
27/04/2005
One Year Limited Warranty
Effective April 25, 2005, MOTREC, Inc. (MOTREC) hereby warrants to the Original Retail Purchaser (Owner) that
any of its vehicles shall be free from any defect in materials for a period of 90 DAYS while in the possession of
such Original Retail Purchaser. This warranty IS NOT TRANSFERABLE to any subsequent Buyer.
The warranty period is extended to one year or one thousand (1,000) hours, which ever first occurs, on the electric
motor, differential (parts that bathe in oil) and the electronic speed controller. For battery chargers, MOTREC initial
90 days warranty coverage applies. Charger fuses and diodes are not included in this warranty. MOTREC makes
no warranty or representation with respect to the internal combustion engine, tires and batteries, since their
respective manufacturers cover such parts. Accessories (light, gage, horn, etc), electrical contacts (switch,
solenoid, contactor, relay), diodes & fuses, belts & pulleys, filters & spark plugs, lubricants, brake linings & shoes,
brake drums & discs, seals, seats, trim and other items subject to wear are not included in this warranty; nor is any
item that in MOTREC sole opinion, shows evidence of neglect, misuse, abuse, collision or alteration.
This warranty shall not apply to normal maintenance requirements as described in the User Manual, and to
damages during shipment. The latter is the carrier's responsibility. No compensation will be allowed for delays.
To initiate warranty coverage on any MOTREC vehicle, the Dealer must complete and return the
“Sales/Installation Report” to MOTREC within 30 days after delivery to the Original Retail Purchaser; or within 90
days after the delivery date to the Dealer, which ever occurs first. Failure to follow these procedures will result in
considering the warranty coverage effective as of the shipment date from the factory.
The defective vehicle must be returned, at the Owner's expense, to an authorised MOTREC Dealer within 30 days
after failure. The Owner will not be charged for parts and labour required for warranty repairs, which must be
performed by an authorised MOTREC Dealer only. The vehicle will be returned at the owner’s expense. The
Warranty Claim Forms must be completed and returned with the defective part(s) to MOTREC within 30 days after
repair was done. No compensation will be allowed for damages caused by vehicle downtime.
It is the responsibility of the owner of the vehicle to make sure that the driver is properly trained and instructed in
the safety features and operation of the vehicle, including vehicle stability, as required by OSHA and ANSI-B56.
Operators shall read, understand and follow the safety and operating instructions in MOTREC Manual before
driving the vehicle. Operators shall not be permitted to drive the vehicle unless a complete and adequate training
has been provided. Driving a vehicle constitutes a hazard. The driver is responsible for the control of the vehicle
while driving and must always evaluate and care for all peculiar situations that he or she may meet while driving.
The driver assumes the inherent hazards related to this activity. The vehicle is designed for off-road use only.
MOTREC disclaims any liability for incidental or consequential damages, to include, but not be limited to, personal
injury or property damage arising from vehicle misuse, lack of maintenance or any defect in the vehicle.
It is the responsibility of the Owner of the vehicle to make sure that the service technicians are properly trained as
required by OSHA and ANSI-B56. Service technicians shall read, understand and follow instructions in the
MOTREC manual before servicing the vehicle. Only qualified and authorized personnel shall be permitted to
maintain, repair, adjust and inspect the vehicle.
MOTREC prohibits, and disclaims responsibility for, any vehicle modification altering the weight distribution and
stability, increasing the speed or affecting the safety of the vehicle. Such modifications can cause serious
personal injury or property damage for which MOTREC disclaims any responsibility.
For Owners that are located outside North America, the warranty period starts the date of shipment from the
factory, and the defective parts must be returned at the Owner's expense to MOTREC prior to warranty repair.
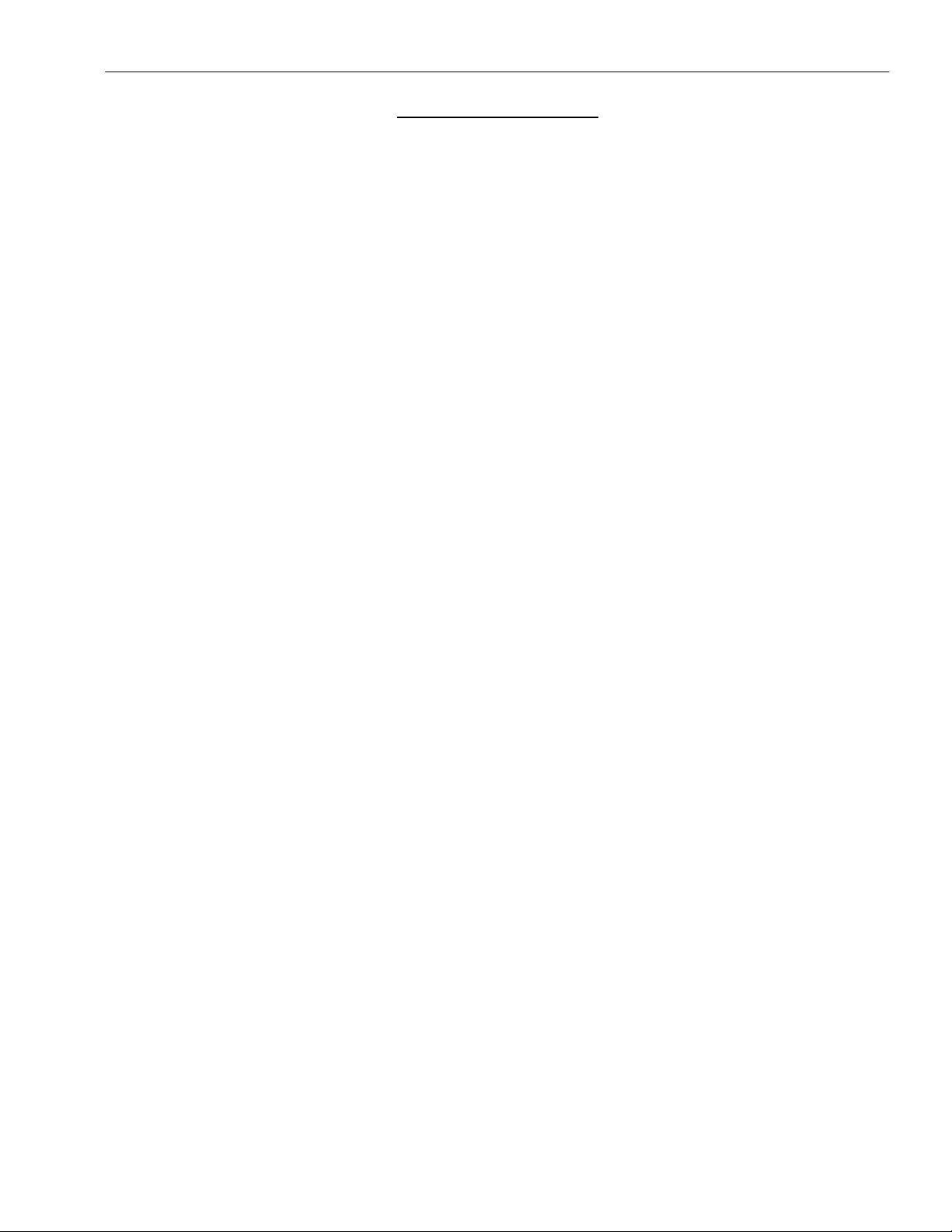
Table of contents
- 3 -
TABLE OF CONTENTS
INSTRUCTIONS 4
SAFETY WARNINGS FOR OPERATORS 5
OPERATING INSTRUCTIONS 6
MAINTENANCE 7
SAFETY WARNINGS FOR SERVICE TECHNICIANS 8
DECALS AND LABELS 10
PERIODIC MAINTENANCE CHECKLIST 11
ACCELERATOR 12
BELT INSTALLATION AND TENSIONING 13
HYDRAULIC BRAKES 14
MECHANICAL BRAKES 15
FRONT AXLE AND STEERING 16
BATTERY MAINTENANCE 17
BATTERY CHARGER 19
ELECTRICAL TROUBLESHOOTING 20
CURTIS SPEED CONTROLLER 23
WIRING :STANDARD CONFIGURATION 25
DIAGNOSTICS AND TROUBLESHOOTING 26
TROUBLESHOOTING CHART 27
LED DIAGNOSTICS 29
PROGRAMMING PARAMETERS –E-300, E-302, E-322 &E-330 30
CURTIS PMC MOTOR CONTROLLER 31
WIRING :STANDARD CONFIGURATION 33
MAINTENANCE AND ADJUSTMENT 35
PMC 1204/1205 TYPICAL ELECTRICAL WIRING 37
SPARE PARTS 38
BODY 39
DIFFERENTIAL AND MECHANICAL DRUM BRAKES 40
HYDRAULIC DRUM BRAKES 42
MECHANICAL DRUM BRAKES 43
BRAKE CONTROLS –DRUM BRAKE 44
HYDRAULIC BRAKE CONTROLS 45
FRONT ASSEMBLY 46
MOTOR AND DRIVE 48
ELECTRICAL DIAGRAM –SEPEX MAIN CIRCUIT 49
ELECTRICAL DIAGRAM –SERIES MAIN CIRCUIT 50
ACCESSORIES –NO DC/DC CONVERTER 51
ACCESSORIES –DC-DC CONVERTER 52
OPTIONS 53
BATTERIES CONFIGURATIONS -36V 55
BUILT-IN CHARGER MODEL 6430-00 56
PORTABLE CHARGER MODEL 07710-02 57
BUILT-IN/PORTABLE 40A CHARGER 58
BUILT-IN/PORTABLE CHARGER MODEL 16360-40 59
MOTREC ILLUSTRATED ACCESSORIES 60
BATTERY DISCHARGE INDICATOR (HOBBS) 62
CURTIS FOOT PEDAL 63
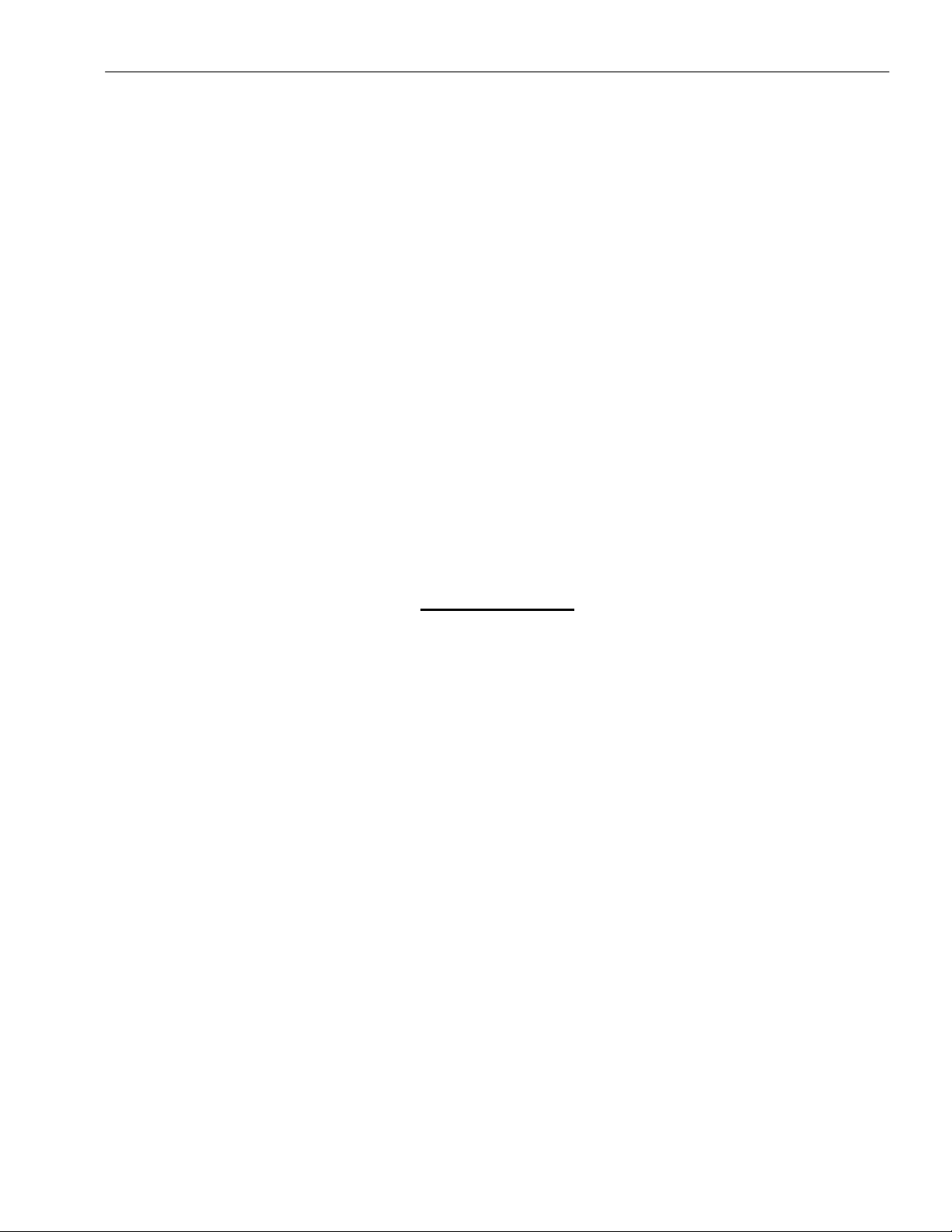
Instructions
- 4 -
INSTRUCTIONS
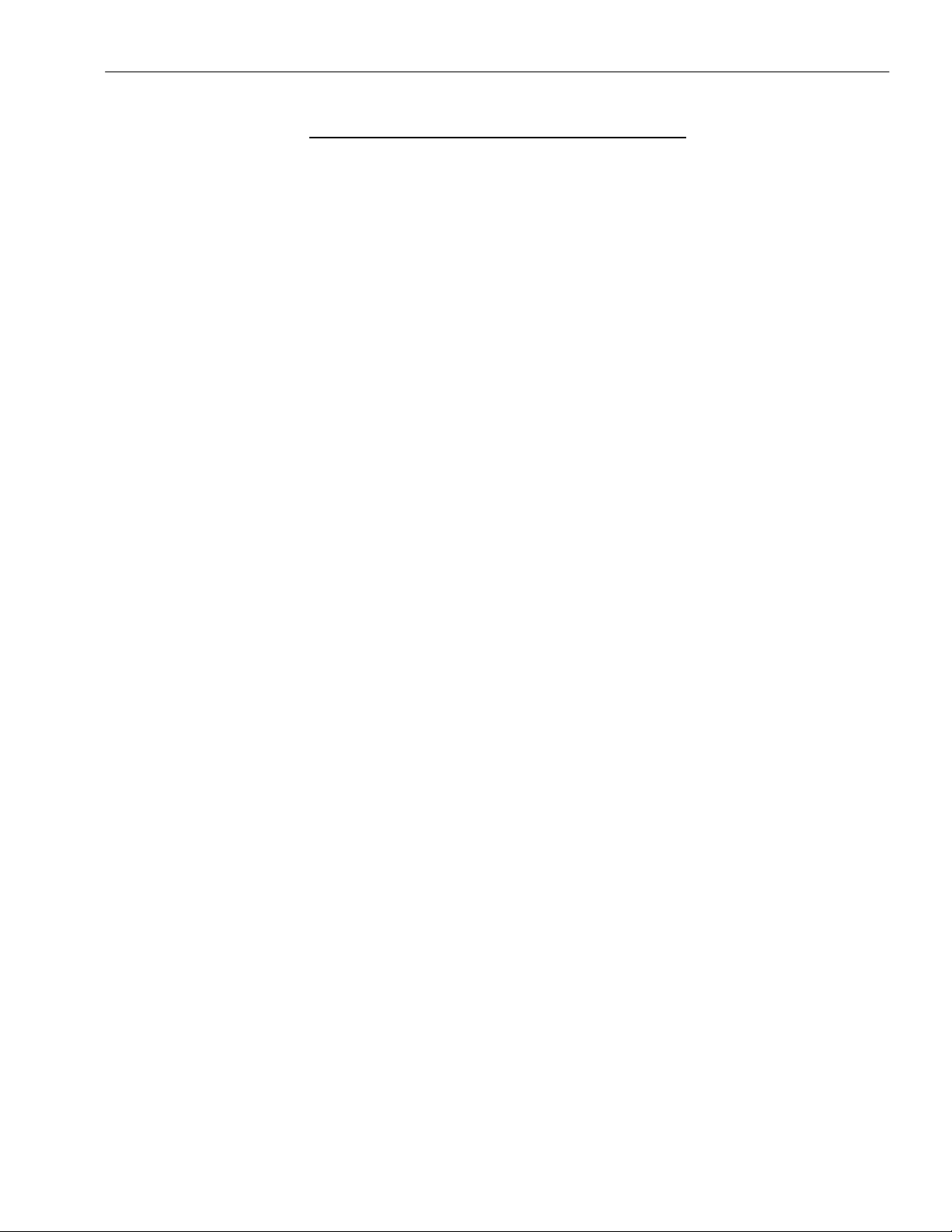
Instructions
- 5 -
SAFETY WARNINGS FOR OPERATORS
•FAILURE TO OBEY THE FOLLOWING SAFETY RULES MAIN RESULT IN SEVERE INJURY.
•It is the responsibility of the owner of this vehicle to train operators to ensure that they understand the operating
characteristics of this vehicle, including training in vehicle stability, and obey the following safety rules and
guidelines. Owner shall comply with OSHA and ASME/ANSI B56.8 & B56.9 regulations for vehicle use,
safety rules, operator training and certification. Do not drive this vehicle unless you are a qualified operator.
•Do not drive this vehicle under the influence of drugs or alcohol.
•Do not drive this vehicle on public roads and highways. This vehicle is designed to be driven in buildings.
•The electrical system of this vehicle will make sparks which can ignite inflammable materials. Never use the
vehicle in hazardous areas where there are inflammable materials, explosive dust or fumes in the air.
•Have your vehicle inspected regularly by trained personnel, and cease operation if a malfunction occurs.
•Do not open battery compartment to prevent battery explosion, acid splashing, severe damage to eyes or skin.
•Do not open motor compartment. Keep clear from moving, rotating(wheels, sheaves, etc) or lifting parts.
•Never carry more passengers than number allowed for this vehicle. Wait until all occupants are seated and
holding on before moving. Always keep all body parts inside vehicle. Keep both hands on steering wheel.
•Do not exceed the vehicle cargo load capacity and gross trailing weight capacity, rated for flat hard even surface.
Different operating conditions such as loose terrain or ramps reduce vehicle capacity.
•Avoid loose, unbalanced or top-heavy loads to keep a good stability and prevent overturn. Do not load cargo that
can fall off the vehicle. Do not carry cargo that is longer, wider or higher than this vehicle.
•Always depress slowly the accelerator for smooth acceleration. Avoid stunt driving or horseplay.
•Avoid sharp turns, always slow down before turning, to prevent vehicle overturn or trailer jack knife. Vehicle is
more sensitive to overturn and jack knife when traveling on inclines or when carrying a heavy load.
•Always drive straight up and down the face of an incline, never across the face, to prevent overturn and trailer
jack knife. Drive slower and start applying brakes sooner on inclines to adjust for longer stopping distance.
•Use extra care and drive slowly in reverse, in congested areas or on wet or slippery ground.
•Keep to the right under normal conditions. Maintain a safe distance from all objects.
•Slow down and sound the horn when approaching a corner or other blind intersections.
•Before leaving the vehicle, park on a level ground flat surface, turn off all switches, set the forward/reverse
switch to neutral, set the parking brake, remove the key. Do not park the vehicle on an incline.
•Before battery charging, park the vehicle in a well ventilated area set for. Do not operate it when charging. To
interrupt a charging cycle, disconnect the AC plug; disconnecting the DC plug or a battery terminal, or operating
the vehicle, could damage the charger and produce a spark, battery explosion and acid splashing.
•Use another driver to steer this vehicle while it is towed. Be sure the driver uses brakes when you slow or stop
the towing vehicle. Do not exceed 5 MPH or carry any passenger while towing this vehicle.
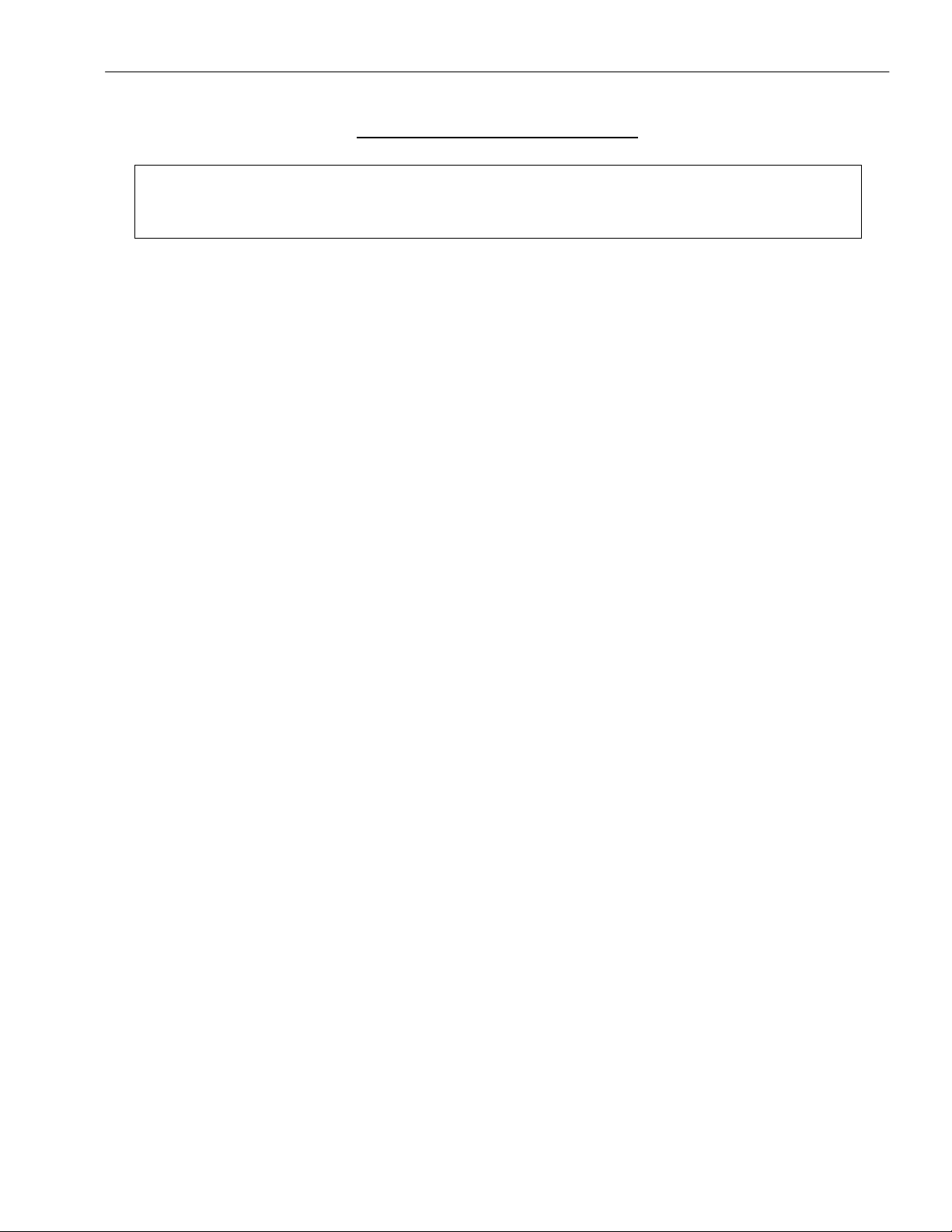
Instructions
- 6 -
OPERATING INSTRUCTIONS
It is the responsibility of the owner of this vehicle to ensure that the operator understands the
operating characteristics of this vehicle, and obeys the safety instructions (ANSI B56).
Do not drive this vehicle unless you are a qualified operator.
BEFORE USING VEHICLE.
Before turning on key switch: set to neutral, check for any visible damage, check brake pedal.
BATTERIES
Never open the battery compartment unless you have received proper training for battery maintenance.
Batteries emit explosive hydrogen gas that can be ignited by a spark or loose terminal. Battery acid
causes severe damage to eyes or skin. Flush the contaminated area immediately with water.
BATTERY CHARGER:
Park the vehicle in a well ventilated area for battery charging. Most battery chargers come with an
electronic control that starts when the charger is plugged and stop when the battery is fully charged. To
interrupt the charging cycle, disconnect the AC-plug, do not disconnect the DC plug.
BATTERY DISCHARGE INDICATOR:
The green light moves from right to left as batteries are being discharged. When the green light is at the
last position on the left the batteries must be recharged. A flashing light warns the operator that further
discharge will damage batteries. See HOBBS indicator instructions
KEYSWITCH:
Depress brake pedal and turn the key switch clockwise for on position. Always turn off all switches,
set the F/R selector to neutral, set the parking brake, remove the key before leaving the vehicle.
HORN:
Depress the horn button on the steering column or handle bar.
F/R SWITCH:
Three positions with neutral at center. Depress the front part of the rocker switch for forward direction.
Depress the rear part of the rocker switch for reverse direction. Always set switch to neutral, turn off
all switches, set the parking brake, remove the key before leaving the vehicle.
ACCELERATOR PEDAL:
It is designed for right foot operation only, and controls the speed of the vehicle.
FOOT BRAKE PEDAL:
It is designed for right foot operation only. The brake force is proportional to the pressure on the pedal.
PARKING BRAKE:
Pull handbrake lever to apply. Never park the vehicle on an incline. Always turn off all switches, set
the F/R selector to neutral, set the parking brake, remove the key before leaving the vehicle.
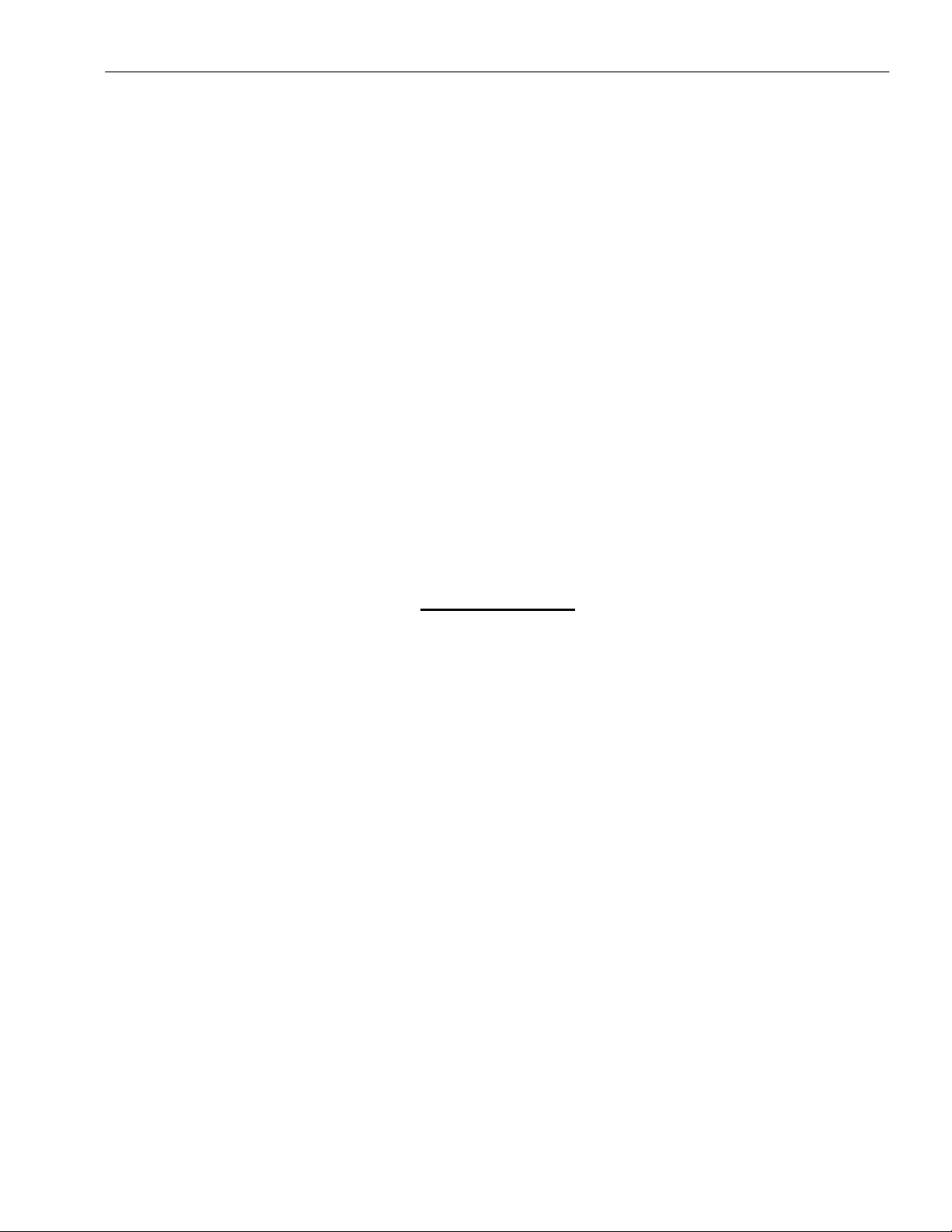
Maintenance
- 7 -
MAINTENANCE
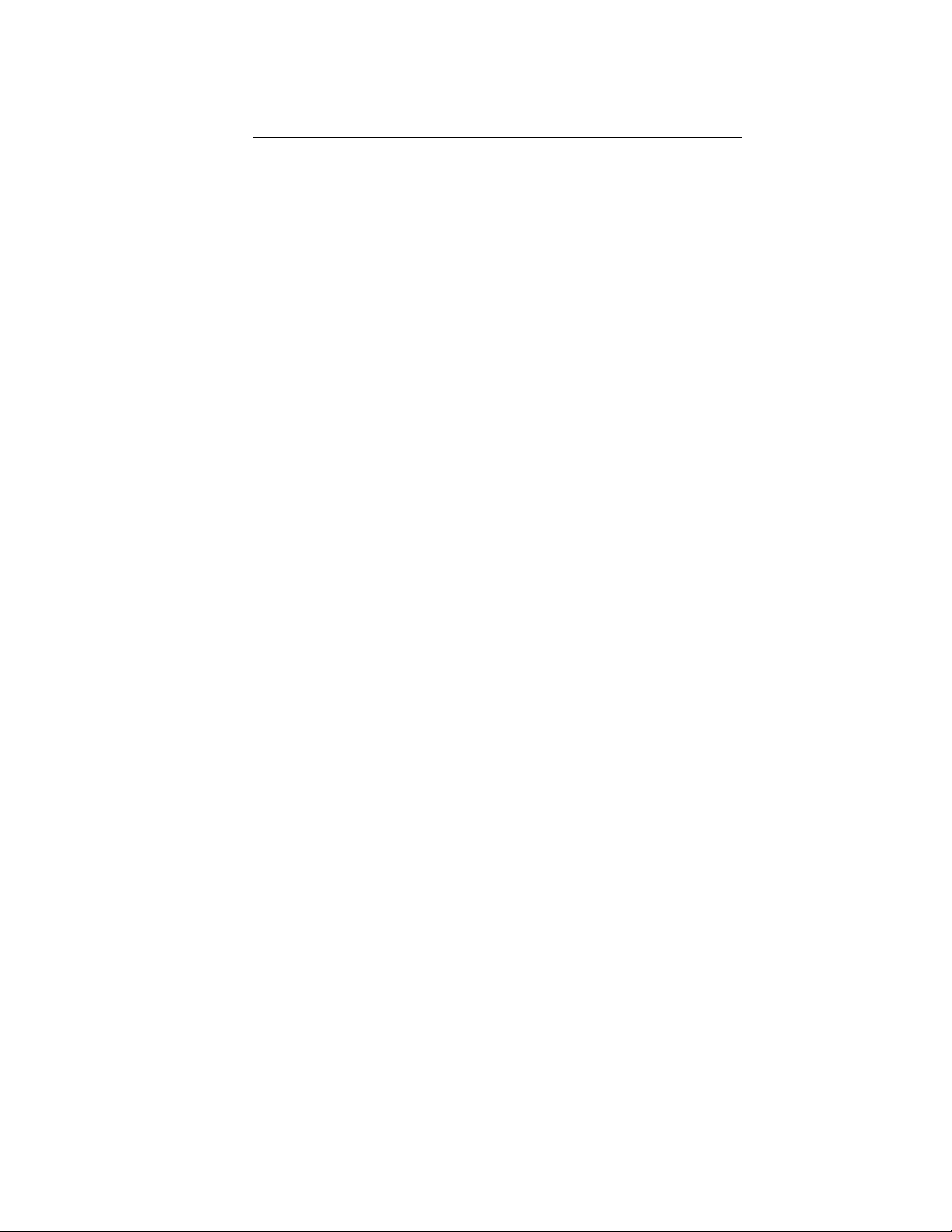
Maintenance
- 8 -
SAFETY WARNINGS FOR SERVICE TECHNICIANS
FAILURE TO OBEY THE FOLLOWING SAFETY RULES MAIN RESULT IN SEVERE INJURY.
Owner shall comply with OSHA and ASME/ANSI B56.8 & B56.9 regulations for vehicle maintenance.
Only qualified and authorized personnel shall be permitted to maintain, repair, adjust and inspect
carriers, vehicles, tractors, and batteries.
Before any maintenance work, park the vehicle on flat level surface, turn off all switches, remove key,
lift wheels off the ground and secure with jack stands of adequate capacity. Don’t connect charger.
Keep clear from moving parts such as tires, sheaves and motor.
Follow the maintenance instructions applicable to the type of repair, maintenance, or service.
Always wear a face shield and gloves when working around batteries.
Before opening the battery compartment, disconnect the charger, turn off all switches and remove the
key. Batteries emit highly explosive gases which greatly increase when charging; do not disturb
connections or produce sparks around batteries to avoid a battery explosion and acid splashing. Battery
acid causes severe damage to eyes or skin. Flush contaminated area immediately with water.
Use insulated tools to avoid sparks that can cause battery explosion and acid splashing.
Use two counteracting tools, double-wrench technique, when disconnecting or tightening terminals on
the battery and the speed controller to avoid cracking the terminal or battery post welds.
Before cleaning or replacing a battery, charger, speed controller, contactor, relay, diode, or any other
component in the power circuit, always disconnect the charger, turn off all switches, remove the key,
wear a face shield and gloves, identify battery polarity and disconnect battery leads, discharge the
capacitor in the controller with a 10 ohms, 25 W resistor for a few seconds across B+ and B-.
After cleaning, the power must not be reapplied until terminal areas are thoroughly dry.
On EE rated vehicles, make sure that all the additional protectors are properly installed and that the
static strap makes a good contact with the ground.
Keep cables and wires clear from mechanical and rubbing action. Make sure cable insulation is free
from cutting or visible damage.
Before replacing a fuse or circuit breaker, identify the cause of failure and repair.
Programmable controllers must be programmed using the parameter settings in this service manual,
before connecting the motor, to avoid sudden vehicle movement and accident.
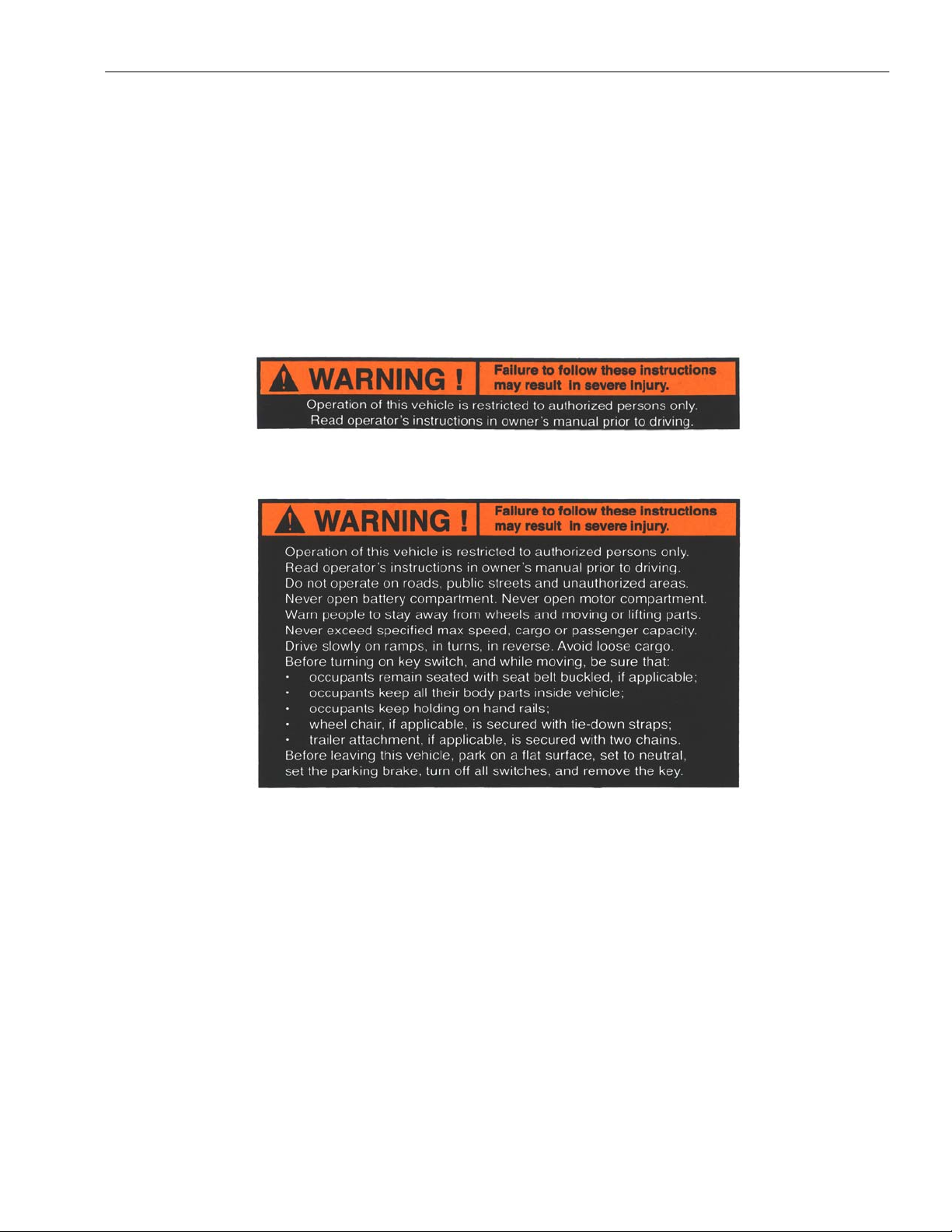
Maintenance
- 9 -
Do not try to increase motor speed by changing parameter settings in the speed controller; it can cause
accident and severe damage to the motor.
SEPEX speed controls are protected by a diode in the power circuit to filter inductive loads in the event
of a sudden power interrupt. Some speed controllers require a diode to filter inductive loads on the KSI
input. Removing the diodes will cause the speed control failure.
Before resuming maintenance operations, inspect safety warnings stickers and replace any if damage is
found and part of the text can’t be read.
The dashboard security warning is depicted by the following image:
The general security warning is depicted by the following image:
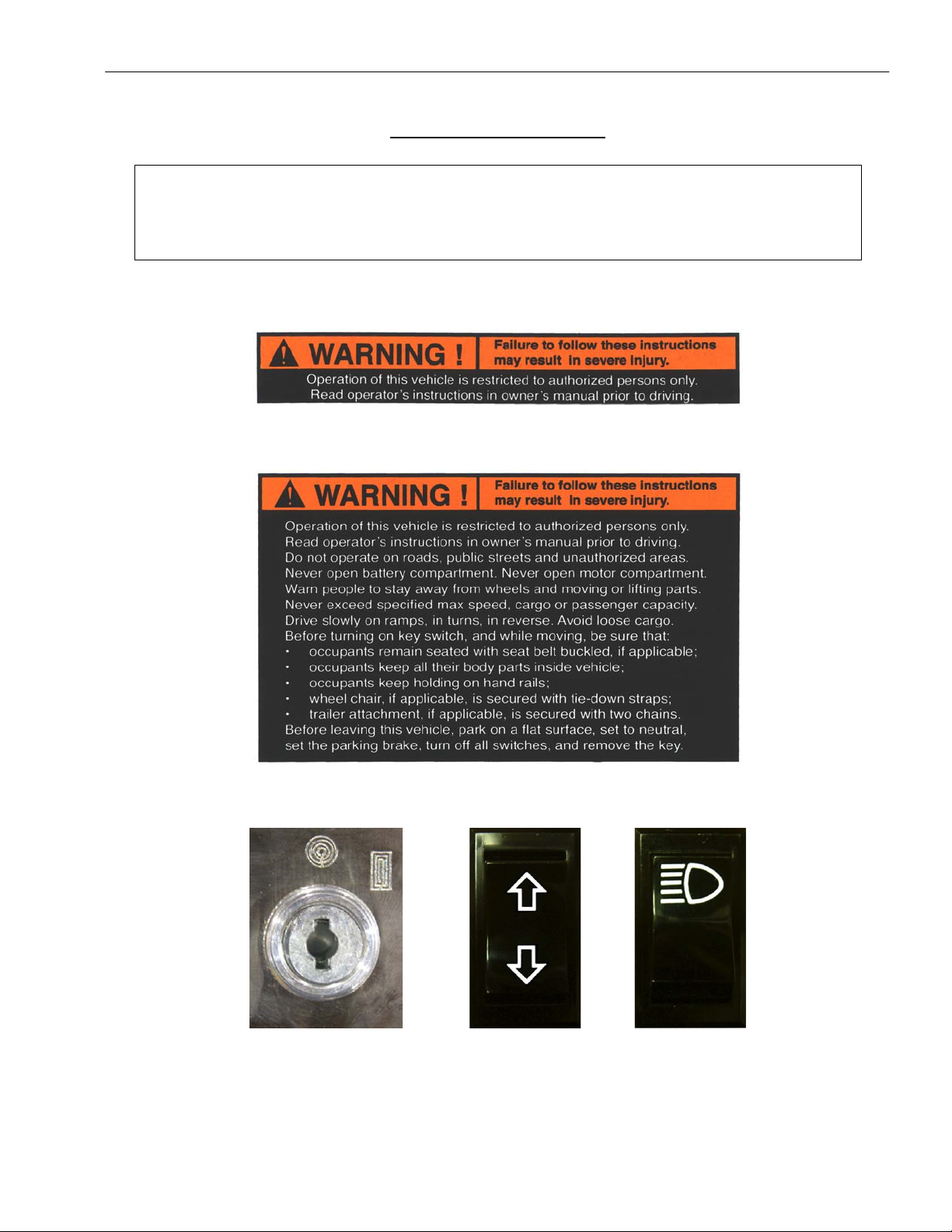
Maintenance
- 10 -
DECALS AND LABELS
! CAUTION !
The images included in this section depict the decals/markings installed on the vehicle. It is of
prior importance that theses decals/markings remain unaltered and readable. Else, the sticker
or the part bearing the marking has to be replaced.
Dashboard security warning label:
General security warning label:
Respectively, key switch markings, forward/reverse selector markings and light switch marking:
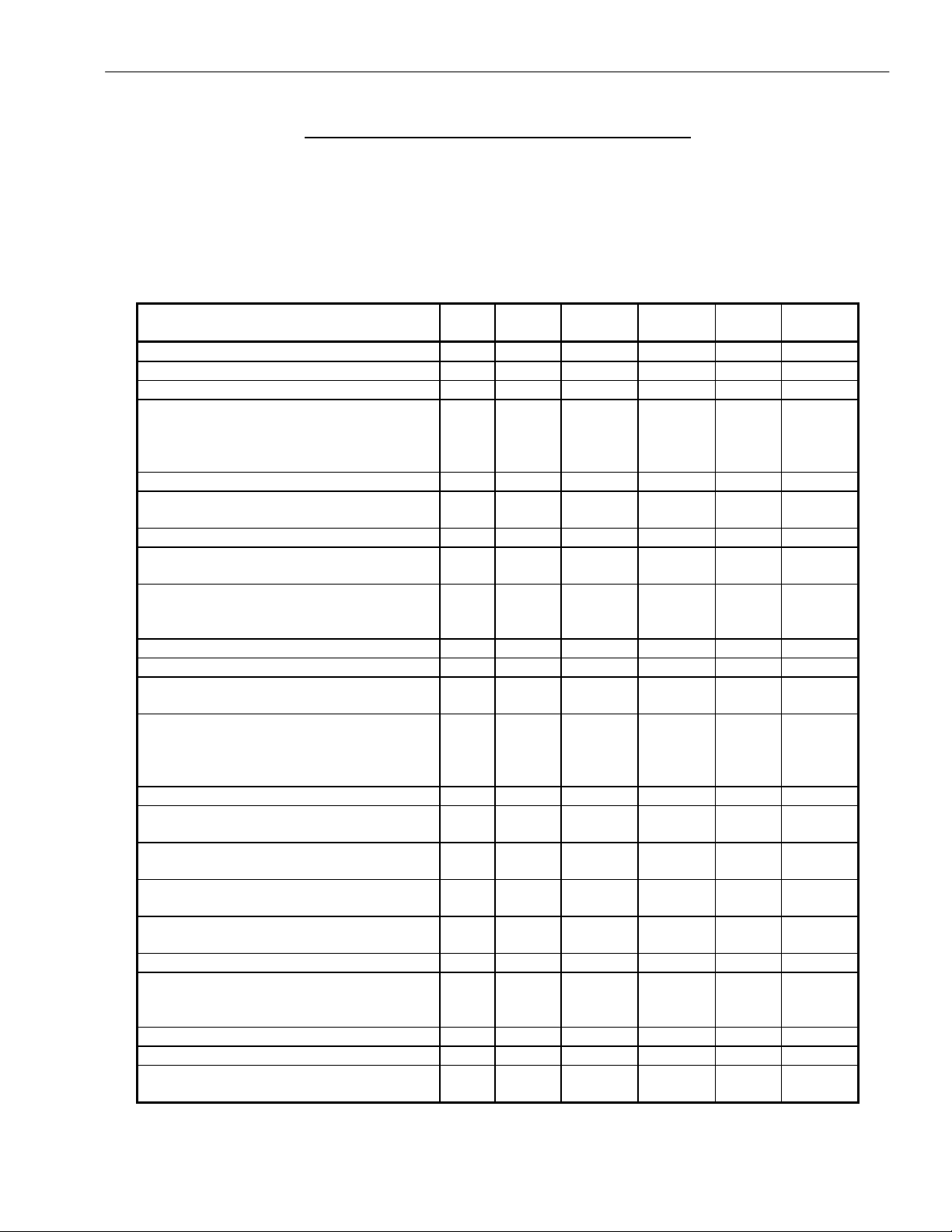
Maintenance
- 11 -
PERIODIC MAINTENANCE CHECKLIST
! WARNING !
Maintenance operations must be made by properly trained service technicians.
−Keep clear from moving parts such as tires, sheaves and motor.
−Check for all EE protections, when applicable, and keep cables and wires clear from mechanical and rubbing action
−Batteries contain sulphur acid that can cause severe burns on skin or eyes.
−When working around batteries, wear acid proof protective equipment: face shield and gloves.
−Use electrically insulated tools to avoid sparks that can cause battery explosion.
−Before any maintenance work, park the vehicle on a flat level surface, turn off all switches, remove the key, lift the wheels off the
ground and secure with jack stands of adequate capacity, identify and disconnect battery leads. Don’t connect the charger.
PERIOD
CHECK/PERFORM HOURS
DAY
WEEK
20 MONTH
50 QUART.
200 YEAR
1000 2 YEARS
2000
MECHANICAL DAMAGE, OIL LEAKS X
REVERSE ALARM, DEADMAN SWITCH X
TIRE PRESSURE, pressure rating on tire X
CHECK/FILL BATTERIES,
add distilled water to cover plates. Fill to the
recommended level after the batteries have
been fully charged.
X
MASTER CYLINDER FLUID (DOT 3) X
BRAKE PEDAL TRAVEL
2” (50 mm) maximum travel X
STEERING FOR PLAY X
PARKING BRAKE LEVER
requires 10 lbs. (5 kg) force to apply X
BELTS AND PULLEYS
-10 lbs (5kg). force for 1/8” (3mm) deflexion;
-pulleys alignment, see procedure.
X
CLEAN/TIGHTEN WIRE TERMINALS X
WASH BATTERY TOP WITH WATER X
MOTOR BRUSHES FOR WEAR
-brushes must exceed holders X
ACCELERATOR ADJUSTMENT
-1/8” (3 mm) travel to activate micro-switch;
-0 to 50 ohms when micro-switch activated;
-4500 to 5500 ohms with pedal down.
X
HYDR. BRAKE LINES FOR LEAK X
BRAKE MECHANICAL LINKAGES
for wear & play X
BRAKE LININGS FOR WEAR
1/16” (1.5 mm) minimum lining thickness. X
LUBRICATE brake pedal pivots, steering
column, ball joints and kingpins. X
OIL (SAE 30) LEVEL IN DIFFERENTIAL
Before adding oil, check oil seals for leaks. X
FRONT WHEEL BEARINGS PLAY X
TIGHTEN NUTS/BOLTS
electric terminals; drive; steering; brakes;
suspension; body.
X
REPLACE DIFFERENTIAL OIL(SAE 30) X
CLEAN AND RE-PACK FRONT HUBS X
SERVICE DIFFERENTIAL, replace the three
oil seals, wheel bearings, oil (SAE 30) X
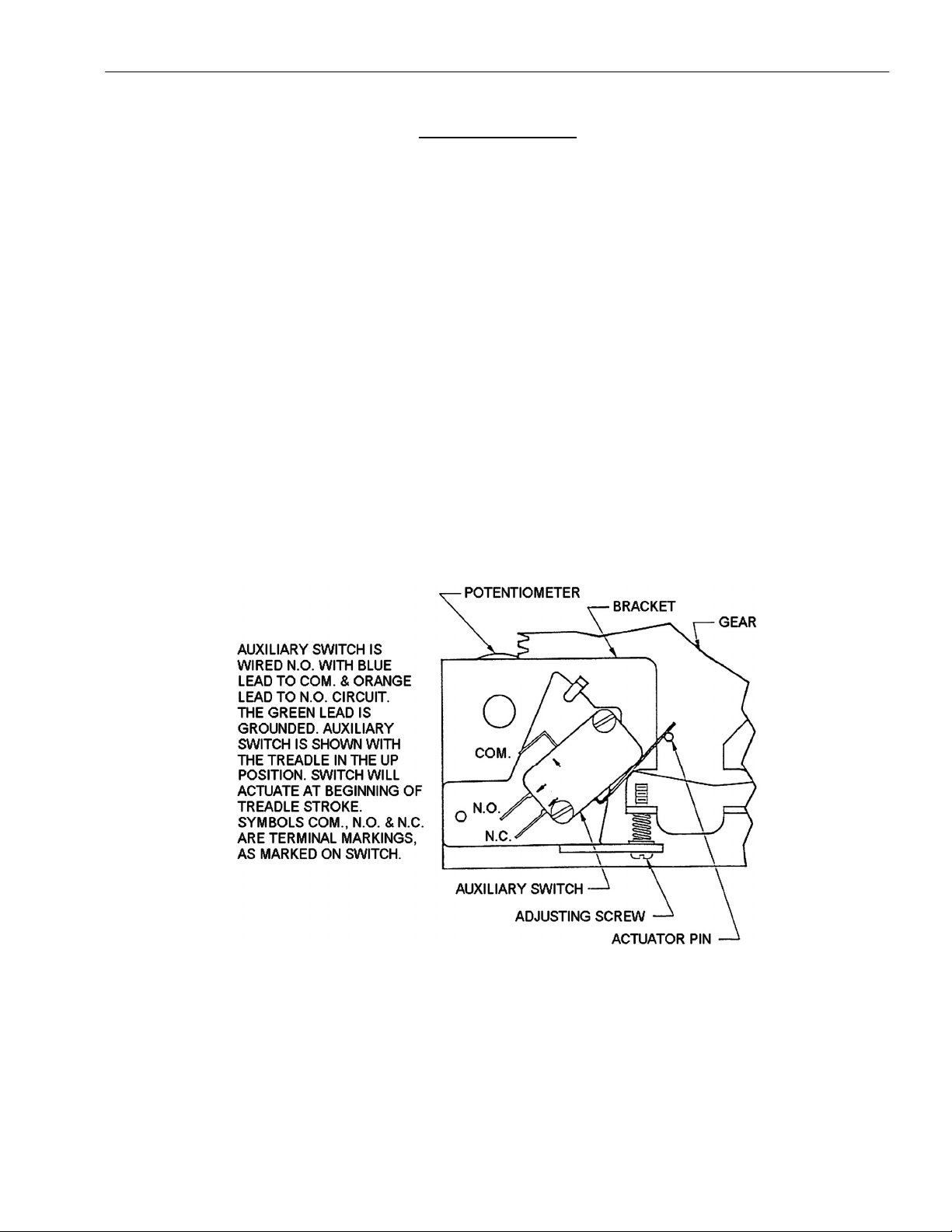
Maintenance
- 12 -
ACCELERATOR
GEAR
−Remove the cover.
−Backlash between gears must be reduced to a minimum by sliding holder; use locktite 262
to lock the three screws.
−When the plastic gear is fully depressed a small backlash must remain between the gears.
−When the plastic gear is released its rear portion must not exceed the pedal case.
MICRO-SWITCH
The micro-switch must deactivate the on/off solenoid when the accelerator is released; turn the
adjusting screw (shown on figure below) to adjust the micro-switch height.
POT
−Remove the terminals 2 and 3 on PMC to measure resistance signal.
−When the micro-switch is activated the signal must be less than 50 ohms. When the front
portion of the pedal is fully depressed the signal must be more than 4600 ohms.
−To modify the resistance, turn the adjusting screw to change the micro-switch height (see
figure below).
Proceed with the same verifications after the accelerator cover is on and then connect terminals 2 and 3.
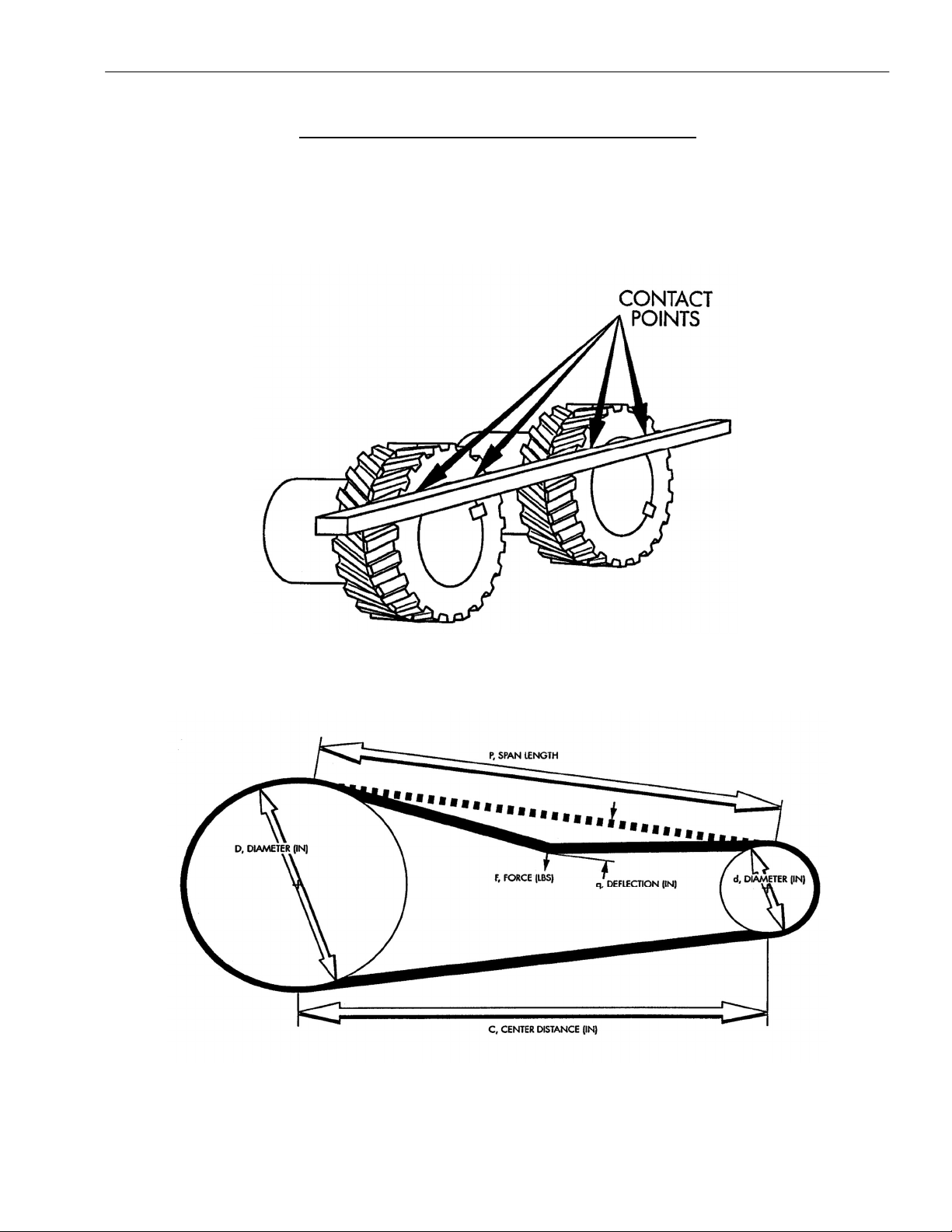
Maintenance
- 13 -
BELT INSTALLATION AND TENSIONING
INSTALLATION
Adjust the sprockets using a straight edge. Slide up the edge on the larger pulley until it contacts the
smaller pulley. Properly adjusted pulleys will provide three points of contact. Properly aligned pulleys
will provide four points of contact. Tighten setscrews and recheck alignment.
TENSIONING
Check the force F required to provide a deflection of 1/8 in. If the measured force is less than 15 lbs
then lengthen centre distance C.
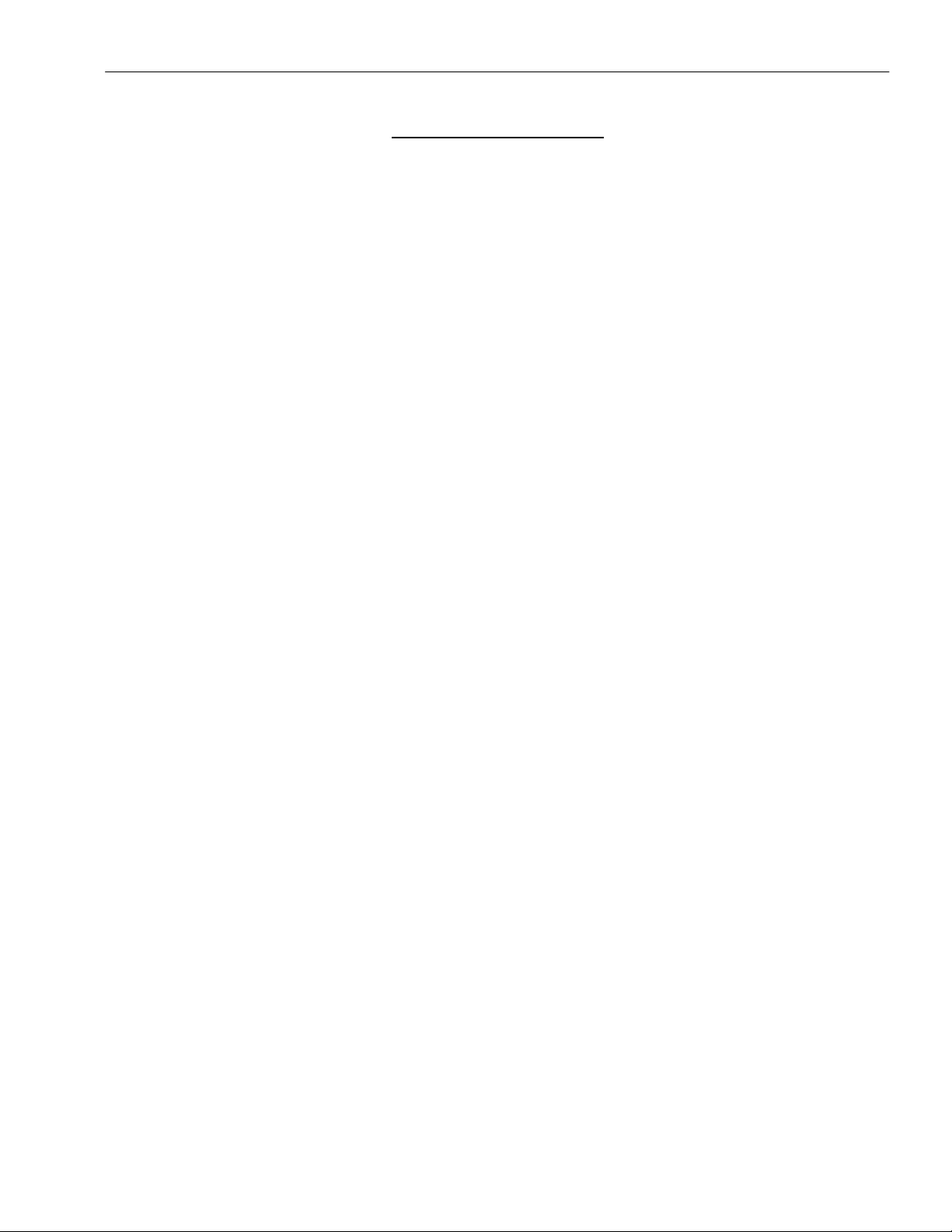
Maintenance
- 14 -
HYDRAULIC BRAKES
DRUM BRAKES
Remove brake drums and check linings wear; the linings should have a thickness exceeding 1/16" (1.5
mm). Turn the brake adjustment to reduce the clearance between lining and drum but avoid contact or
drag when the wheels are turned and the pedal is released.
DISC BRAKES
Check pad linings for excessive wear; the linings should have a thickness exceeding 1/16" (1.5 mm).
Disc brakes are self-adjusting.
BRAKE PEDAL
If the brake pedal becomes soft or spongy, air may have entered the hydraulic system and the brake
system has to be bled:
1. fill the master cylinder with brake fluid (DOT-3);
2. bleed front callipers one at a time by having someone applying a steady pressure on the brake
pedal, and close the bleeder before allowing the brake pedal to return to up position;
3. fill the master cylinder with brake fluid (DOT-3);
4. bleed rear wheel brakes one at a time, following the same procedure;
5. fill the master cylinder with brake fluid (DOT-3);
6. clean every fitting and line, remove traces of oil;
7. apply a continuous pressure on the brake pedal for about five minutes ;
8. Finally, inspect brake lines and fittings for leaks ;
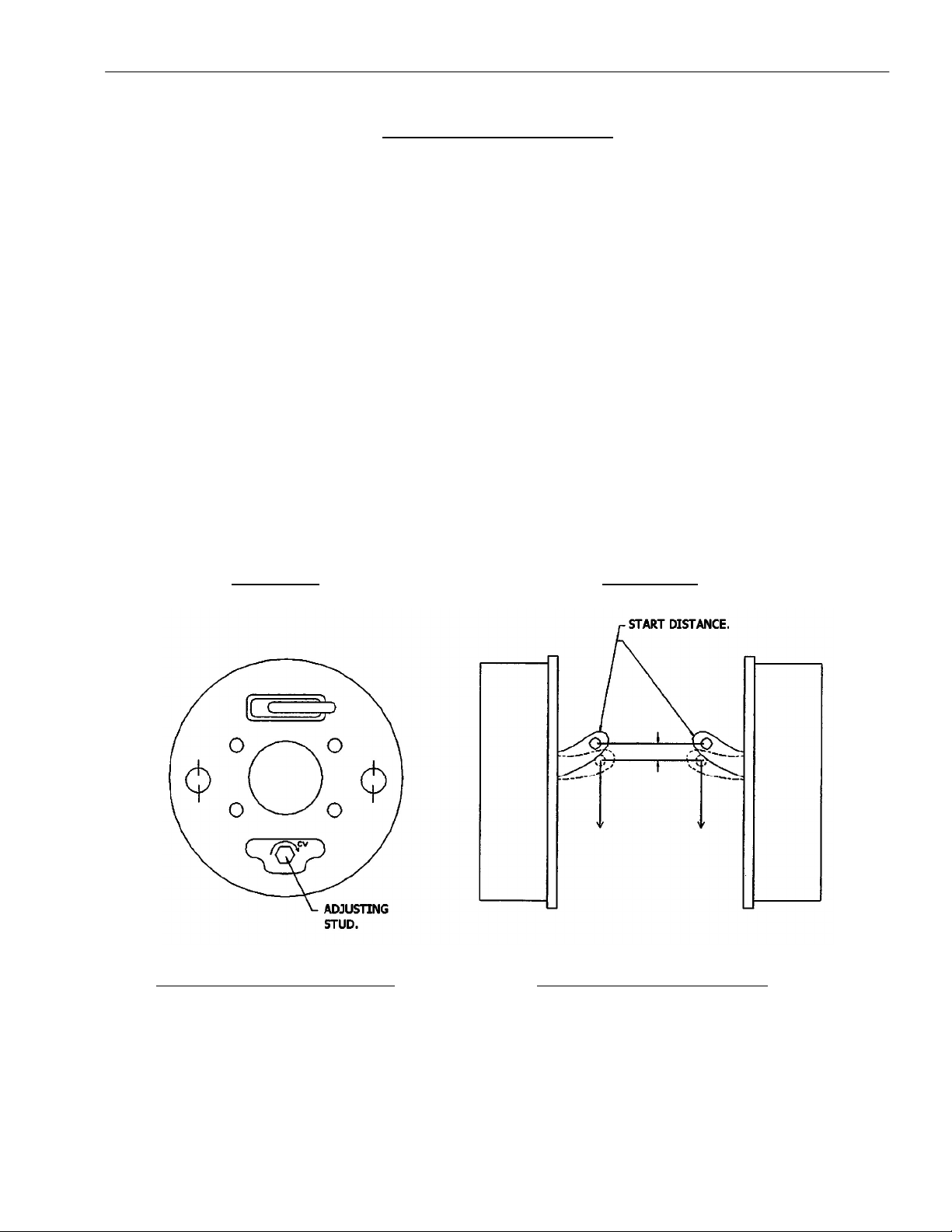
Maintenance
- 15 -
MECHANICAL BRAKES
REPLACING THE BRAKE SHOES
−raise the vehicle until the rear tires clear the floor and install two jack stands on rear;
−disassemble and clean the adjusting screw assembly;
−check brake lever for wear;
−replace all spring parts;
−apply Hi-Temp grease and install the adjusting screw assembly;
−pump the brake pedal to automatically adjust the brake shoes, before making a road test.
SELF ADJUSTING DRUM BRAKES
This type of brake does not require manual adjustment. Before installing pulling rods, make sure they
are adjusted to the same length.
MANUALLY ADJUSTED DRUM BRAKES, Old Design.
Before any brake adjustment, check the brake levers on the inboard side of the brake backing plates.
The brake levers must be equally pulled (see figure A). Adjust pulling rods if necessary. The brake
shoes are adjusted by turning the stud (17mm key) located on the inboard side of the brake backing
plate (see figure B). Turning the stud clockwise will reduce the drum to shoe clearance. Properly
adjusted shoes will equally brake the rear wheels.
Figure B Figure A.
Brake plate and adjusting screw Equal distance for brake levers
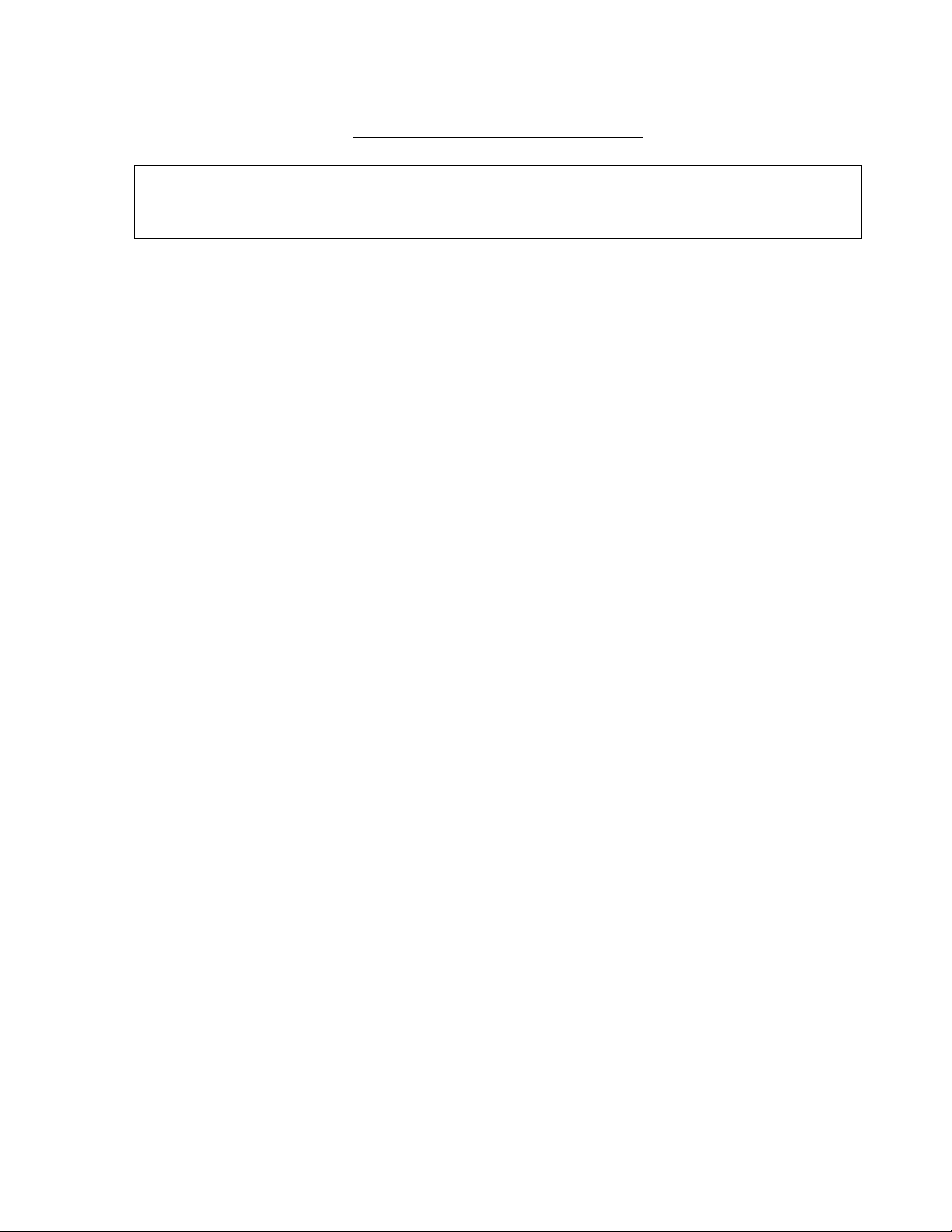
Maintenance
- 16 -
FRONT AXLE AND STEERING
! CAUTION !
Before maintenance, turn off all switches, set to neutral, set parking brake, remove the key,
and raise the front end of the vehicle supporting it with two jack stands of adequate capacity
STEERING INSPECTION
−Check tire inflation pressure, suspension components, tie rods straightness, tie rod ends play
(wear), play (wear) in wheel bearings, kingpins and bushings.
REPLACING & ADJUSTING THE STEERING GEAR
−Remove the pitman arm;
−The steering box makes 6.5 turns, center the steering gear (3.25 turns from either side);
−Align the front wheel straight. Install the pitman arm.
TOE-IN ADJUSTEMENT
−With the wheels in straight forward direction, measure the inside (left to right) distance between
the front tires, at the front and rear of the tires;
−Turn the rear tie rod until the distances are equal and tighten the two lock nuts on the tie rod.
REMOVING & GREASING OF FRONT HUBS, required once-a-year
−Remove dust cap and cutter pin, unscrew nut, remove hub;
−Inspect bearings and races for wear and replace worn bearings;
−Replace the seal;
−Pack the hub with wheel bearing grease and re-assemble.
ADJUSTING FRONT HUBS
−Tighten spindle nut to 30 ft-lb to seat the bearing and back off the nut to the next slot;
−Install a new cutter pin and the dust cap.
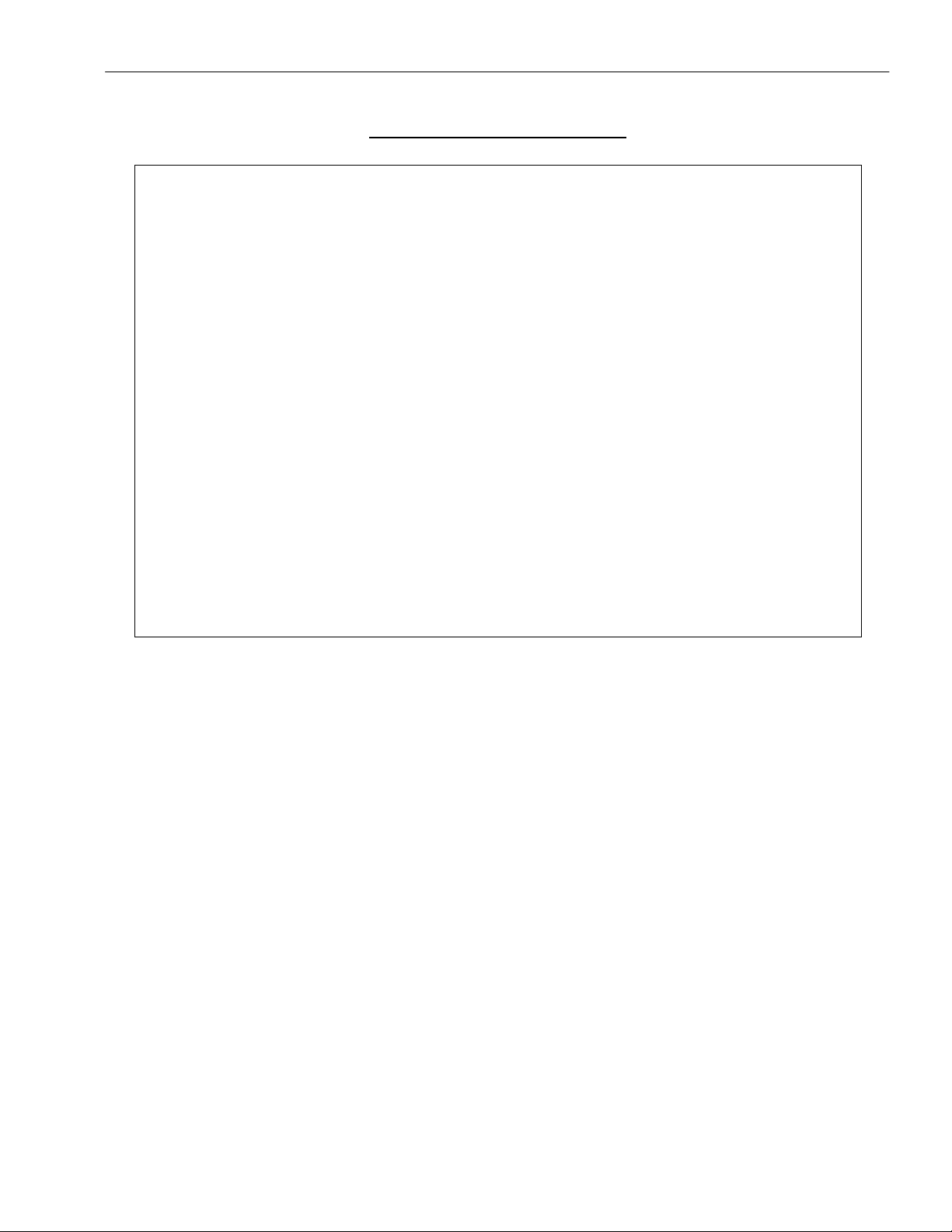
Maintenance
- 17 -
BATTERY MAINTENANCE
! WARNING !
−It is the responsibility of the owner of this vehicle to ensure that the service technicians are
properly trained, read and obey the safety rules and guidelines in this manual (ANSI B56).
−Maintenance operations must be made by properly trained service technicians only.
−Before any maintenance work, park the vehicle on a flat level surface, turn off all the
switches, set to neutral, remove the key, lift the wheels off the ground and secure with jack
stands of adequate capacity.
−Keep charger disconnected while doing any maintenance work.
−Always wear a face shield and gloves when working around batteries.
−Battery emits highly explosive gases; do not produce sparks to avoid battery explosion and
acid splashing. Battery acid causes severe damage to eyes or skin. Flush contaminated area
immediately with water.
−Use insulated tools to avoid sparks that can cause battery explosion and acid splashing.
−Use two counteracting tools, double-wrench technique, when disconnecting or tightening
battery posts.
−Before cleaning or replacing a battery, discharge the capacitor in the controller with a 10
ohms, 25 W resistor for a few seconds across B+ and B-, identify battery polarity and
disconnect battery leads.
−After cleaning, the power must not be reapplied until terminal areas are thoroughly dry.
Battery Leads and Connectors.
Check for loose connections, damaged cables, acid spill, loose terminal posts, quarterly.
Battery Post Corrosion.
If corrosion is present on battery posts, remove the cable connectors, use a wire brush to remove
particles, and then clean them with a cloth that has been moistened with ammonia.
Electrolyte Level,
Does not apply to sealed battery.
−Daily charged batteries normally require watering once a week. Under watering leads to a
shortened battery life. Over watering leads to battery corrosion. Be careful not to overfill any cell
to avoid electrolyte to be forced out while charging.
−Fill each cell to plate level with distillated or de-ionized water, before battery charging. Refill each
cell after full charge, and avoid overfill.
Battery Mounting.
A loose battery increases damaging effects of vibrations and is more prone to short out.
Battery Discharge Limit.
Discharging below a 20% state of charge cuts down the battery life and the number of cycles available.
At 20% state of charge, specific gravity of 6V battery should be 1180; and 1220 for industrial battery.
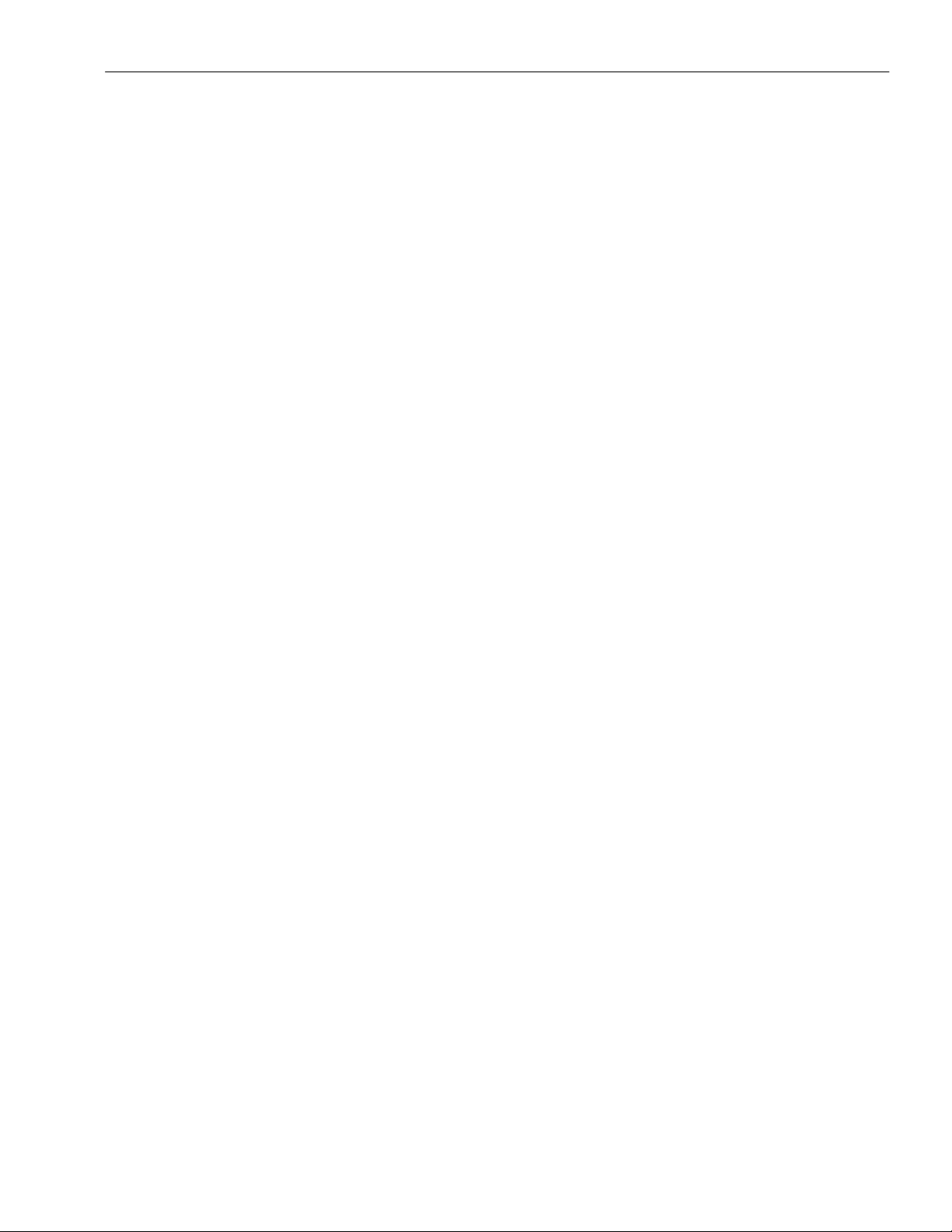
Maintenance
- 18 -
Frequency of charge.
−Always charge battery in a well ventilated area set for and approved for charging. When a battery is
discharged to its 20% state of charge, it is best to charge immediately.
−Batteries require a low current equalization charge (min 4 hours) at least every week, to equalize
battery cells, improve battery performance and life in number of cycles.
−Never leave a charger connected for more than 20 hours.
Storage.
−Keep the battery from getting cold, it would loose its capacity.
−Let the battery warm up before charging.
−Charge batteries in “stored” vehicles every month.
Defective Battery.
Check specific gravity of each cell; if a cell is shorted, voltage drop may occur only when there is
current.

Maintenance
- 19 -
BATTERY CHARGER
! CAUTION !
Always unplug the AC and DC electrical cords before attempting any repairs to the charger.
CHARGER DOES NOT TURN ON:
−Dc output cord of portable chargers must be disconnected from batteries after every charge to
restart;
−Check dc fuse links;
−Check battery voltage at the battery connector;
−Check ac outlet and cordset;
−Replace electronic control ;
RELAY CLOSES AND TRANSFORMER HUMS BUT AMMETER DOES NOT REGISTER:
−Check dc fuse links;
−Check the continuity of the dc output cord, ammeter, diodes and all connections in the dc
circuit;
−Check diodes;
−Check capacitor(rapidely increasing resistance);
SINGLE CHARGER FUSE BLOWS:
−Disconnect and check diodes;
BOTH FUSE LINKS BLOW:
−Check the battery pack and battery connector polarity;
−Disconnect and check diodes.
CHARGER OUTPUT IS LOW:
−Disconnect and check diodes;
−Can be caused by a transformer failure.
AMMETER READS 30 AMPS FOR MORE THAN 30 MINUTES:
−Check the battery pack;
CHARGER DOES NOT TURN OFF:
−Check specific gravity in each battery cell;
−As much as 16 hours may be required to properly charge heavely discharged new or cold
batteries;
−Replace electronic control.
AC LINE FUSE OR CIRCUIT BREAKER BLOWS:
−Check ac cordset;
−Check ac line fuse rating;
−Replace electronic control;
−Can be caused by a transformer failure.
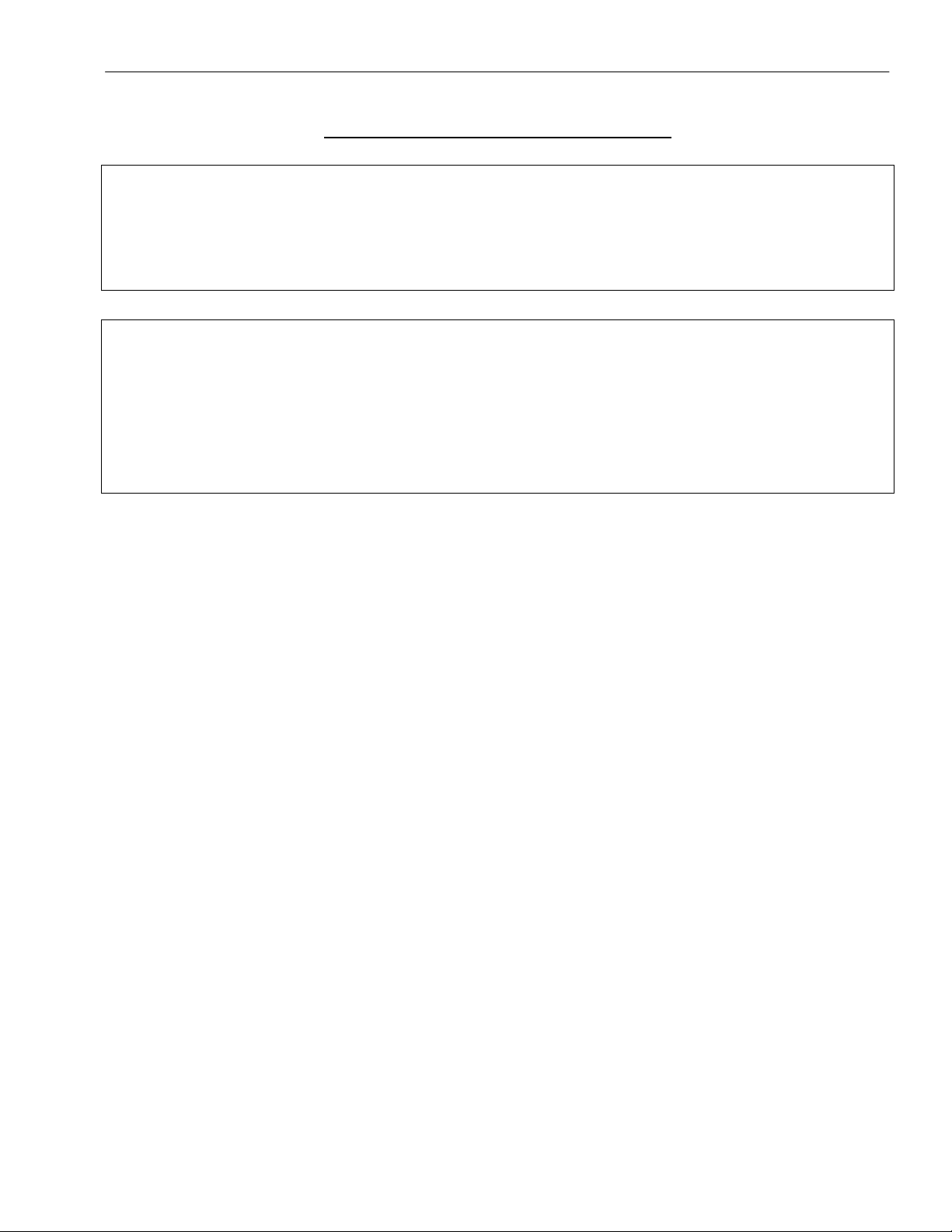
Maintenance
- 20 -
ELECTRICAL TROUBLESHOOTING
! WARNING !
Maintenance work must be performed by trained service technicians only.
It is the responsibility of the owner of this vehicle to ensure that the services technicians are properly
trained, understand and obey the safety rules and guidelines (ANSI B56).
All service technicians must read and understand the maintenance warning section in this manual.
! WARNING !
Before any maintenance work, park the vehicle on a flat level surface, turn off all switches, remove the
key, lift the wheels off the ground, secure with jack stands of adequate capacity, disconnect charger.
Always wear safety glasses.
Batteries emit highly explosive gases that can be ignited by a spark. Before disconnecting a high
current terminal, turn off all switches, disconnect battery charger, disconnect batteries.
Keep clear from moving parts such as tires, sheaves and motor.
PMC SELF DIAGNOSTIC
If your PMC comes with a status led, use the flashing code to help troubleshooting.
BATTERY VOLTAGE
Make sure batteries are securely connected. Measure voltage between + and - terminals . We will call
this value B+ or full battery voltage.
ACCESSORIES NOT WORKING
−Check the fuses on the batteries and the DC/DC converter.
−Check voltage across + and – terminals on the battery gage; if not B+, check wiring.
−Turn the key switch ON, check voltage between output terminal on the key switch and the -
terminal on the battery gage; if not B+, replace the key switch.
−Check voltage across DC/DC converter output terminals; if not 12-Volt, replace the converter.
−Depress the accessory switch, check voltage across accessory terminals. If not 12-Volt, replace the
switch. If 12-Volt, replace the accessory.
FORWARD ONLY
On a SEPEX motor control, check the reverse signal input on the controller.
On a series wound motor control, a bad reverse contactor is the most probable cause of the problem.
Switch to reverse and check voltage on the reverse control wire. If not B+, replace the F/R switch. If
B+, turn off the key switch, disconnect batteries, disconnect power terminals on the F/R contactors,
check the resistance across N.C. power terminals of the reverse contactor. If not 0 ohm, change the
reverse contactor. If 0 ohms, switch to forward and check the resistance across the forward N.O. power
terminals. If not 0 ohms, change the forward contactor.
Table of contents
Other Motrec Golf Car manuals
Popular Golf Car manuals by other brands
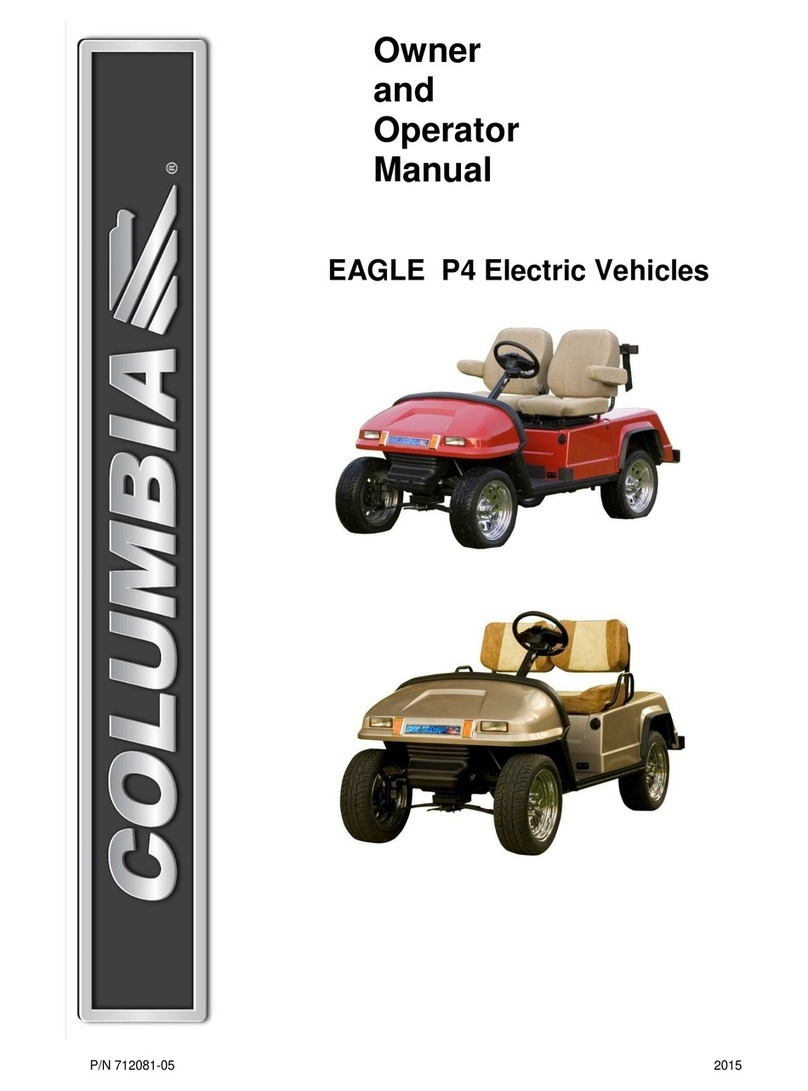
Columbia
Columbia EAGLE P4 Owner's and operator's manual
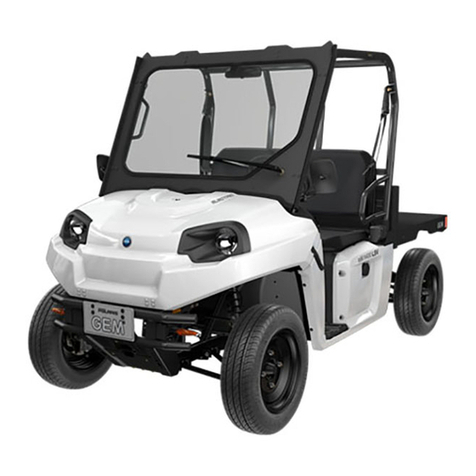
GEM
GEM eM1400 LSV 2018 owner's manual
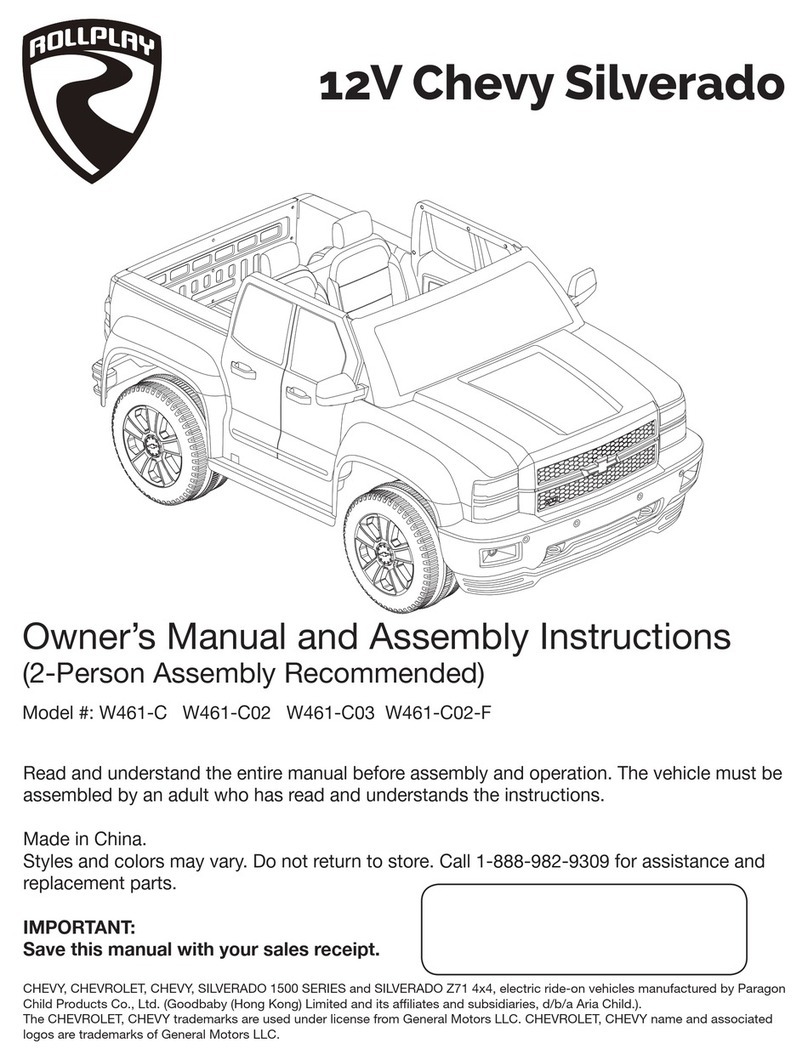
Rollplay
Rollplay 12V Chevy Silverado W461-C02 Owner's manual and assembly instructions
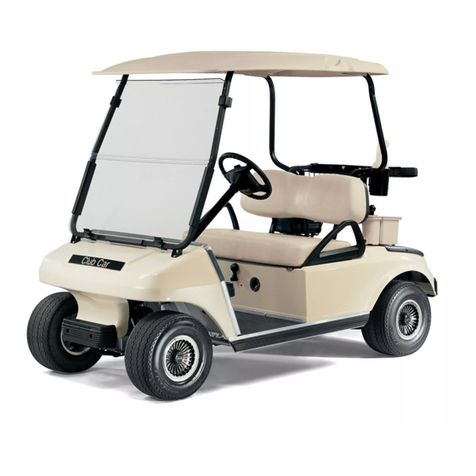
Club Car
Club Car DS Golf Cars 2004 owner's manual

Textron
Textron EZGO TXT ELiTE FREEDOM Service & parts manual
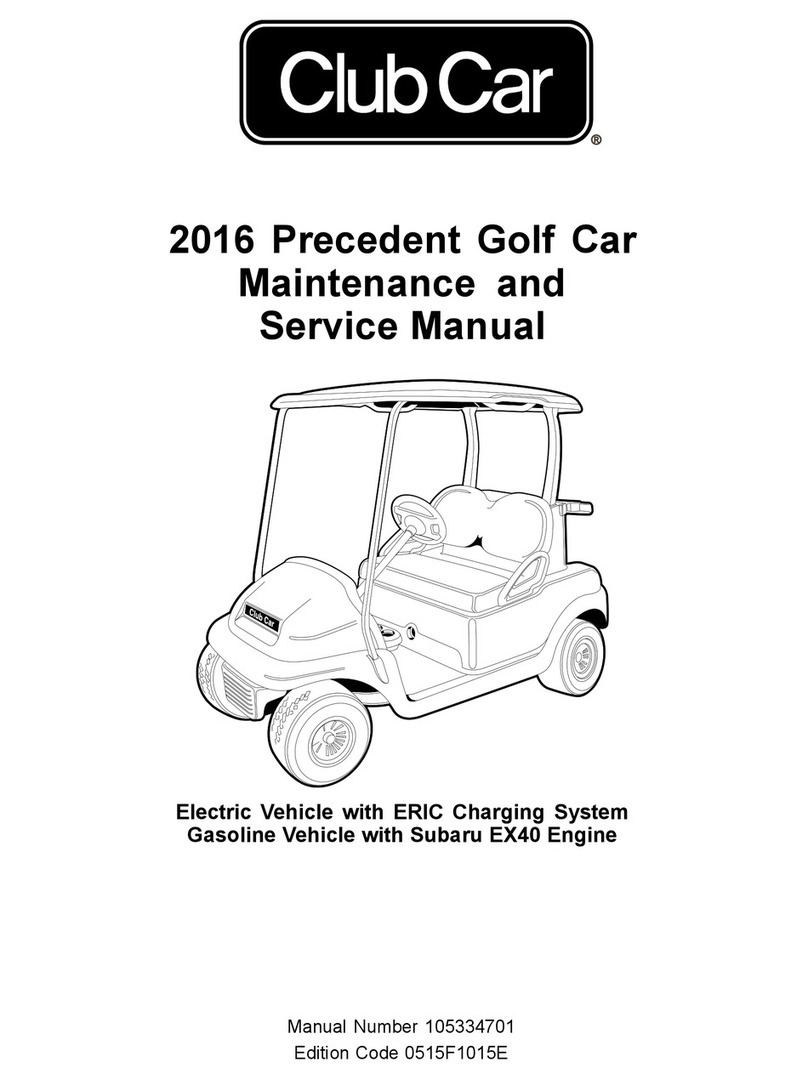
Club Car
Club Car Precedent 2016 Maintenance and service manual