Spraying Systems AA290AG Series User manual

AA290AG-- Series
AIR MOTOR-DRIVEN
TANK WASHER
Owner’s Manual
MI-290AG
Rev 4
North Ave. at Schmale Rd., P.O. Box 7900
Wheaton, Illinois 60189-7900 USA
Phone (630) 665-5000 * Fax (630) 260-0842* www.spray.com
Sprayin.g Systems
Co.®

MI-290AG Rev. 4
2
TABLE OF CONTENTS
FORWARD / INTRODUCTION ...................................................................................... 3
PRODUCT SPECIFICATIONS
AA290AG-- Air Motor-Driven Tank Washer...................................................... 4
Performance & Dimensional Data..................................................................4-5
MAINTENANCE INFORMATION
Removal / Replacement of Spray Nozzles........................................................ 6
Removal / Replacement of Air Motor Drive ..................................................... 6
Removal / Replacement of Motor Drive Coupling............................................ 7
Replacement of O-rings in Upper Bushing Retainer....................................... 7
Replacement of O-ring in Adjustable Flange................................................... 7
Replacement of Nozzle Hub Bushings ............................................................. 8
Replacement of Rotary Housing Bushings and O-ring .................................. 8
Air Motor Lubrication......................................................................................... 9
TECHNICAL INFORMATION
AA290AG-- Parts List....................................................................................... 10
Air Motor Drive Assembly................................................................................ 11
Lubrication Assembly ........................................................................... 12
Air Motor Drive Parts List...................................................................... 13
Gast
®
Motor Drive Operation & Maintenance Manual....................14-20
IMPORTANT: READ ALL INSTRUCTIONS BEFORE OPERATING UNIT

MI-290AG Rev. 4
3
PROPRIETARY NOTICE
The information contained in this document is the exclusive property of Spraying
Systems Co.
®
Reproduction in whole or part is prohibited without prior consent of
Spraying Systems Co.
®
FORWARD
The equipment and/or parts described in this document were manufactured and
assembled with the quality and high reliability, which have become synonymous with
the name of Spraying Systems Co.
®
Note:
The description and specifications contained herein were effective at the date of
printing. Spraying Systems Co.
®
reserves the right to alter or modify any unit
specification on and Spraying Systems Co.
®
product without notice or any obligation.
INTRODUCTION
The AA290AG Tank Washer is designed for high pressure (250 psi/17 bar MAX)
washing of tanks up to a recommended maximum diameter of eighty (80) feet (24.4 m)
with heated (200°F/93°C MAX) or unheated solutions at flow rates up to two hundred
(200) gallons per minute (752 l/min) with only up to a 22 psi/1.5 bar pressure drop
through the unit itself.
Tanks over eighty (80) feet (24.4 m) in diameter may be cleaned adequately
depending on the maximum tank dimension, cleaning solutions being used,
temperatures, spray pressures, flow rates and the material being cleaned from the tank.
The AA290AG Tank Washer may be used with plain water or with a variety of
chemicals (compatible with stainless steel, ethylene propylene rubber, and carbon
graphite filled Teflon®). However, if chemicals are used, the unit should be flushed with
clean water at the end of the day before the unit is stored away. A liquid line strainer
before the unit is recommended to remove large particles, which may damage unit.
IMPORTANT: High impact sprays may cause severe injury. The liquid pressure
to the tank washer should never be turned on while the unit is outside the tank.

MI-290AG Rev. 4
4
/
(
15
1/2"
{396
mm)
APPROX.
----
EXTENSION
I n.lGTM
1
v•·
{197
mm)
l
ROTATING
HOUS
ING
_/
®--0..
" /
THE
AA290AG--
AIR
MOTOR-DRIVEN
ROTARY
TANK
WASHER
PROJECTS
CLEANING
SOLUTION
IN
CONCENTRATED
HI
GH
IMPACT,
SOLID
STREAM
SPRAYS
•••
WITH
ROTATING
MOTION
T
HA
T
COVERS
ALL
INTERNAL
SURFACES
or
TANKS.
SLOW,
CONTROLLED
ROTATIONAL
SPEEDS
OF
ROTATING
HOUSING
AND
NOZZLE
TURRET
PROV
I
DE
A
THOROUGH
CLEANING
ACTION
ON
THE
TANK
SURFACE.
NOTE:
LUBRICATOR
.I.SSEMBLY
(SUPPLIED
WITH
UNIT)
IS
REQUIRED
FOR
AIR
SUPPLY
LIN£.
LIQUID
IN
LE
T
CONN.
2"
NPT
{f)
OR
2"
BSPT
(F)
-
,4--
I
NLE
T
BODY
IIIOUNTING
FLANGE
(SEE
DATA
SHEET
290AG
-1)
'\
I
ROTA
Tl
NG
NOZZLE
TU
RR
ET
WI
TH
SOILD
STREAM
VEEJET
ca
NOZZLES
- 2
REQUIRED
(4
NOZZLE
TURRET
OPTIONAL)
TYPE
31
6
ST
Al
NLESS
STEEL
3/4"NPT
(f)
~
e
CAN
BE
USED
AS
A
PERMANENTLY
INSTAliED
UNIT
OR
REMOVABLE
U
NIT.
e
mENSION
INTO
T
ANK
IS
FUL!Y
ADJUSTABLE.
e
NOZZLE
TURRET
WITH
2
OR
4
SOLID
STREAM
NOZZLES
IS
GEAR
DRIVEN
TO
GIVE
f"Ul!
COVERAGE
or
IN
TERNAL
TANK
SURFACES.
•
MOTORIZ
ED
DRIVE
UNIT
IS
MOUNTED
OUTSIDE
or
THE
TANK.
•
ROTATIONAL
SPEED
OF
THE
NOZZLE
TURRET
IS
INDEPENDENT
or
THE
CLEANING
LIQUID
PRESSURE
ANO
FLOW.
e
FOR
TANK
DIAMETERS
UP
TO
APPROXl~TEL
Y 80
FT.
(24.4
m),
SEE
DATA
SHEET
7204
1.
e
FOR
SPECIFICATIONS
AND
ADDITIONAL
INFORMATION,
SEE
DATA
SHEETS:
290AG-t,
PL290AG,
AND
CURRENT
TANK
WASH
CA
TALOG.
e
MAX
PRESSURE:
250
PSI
(17 bar):
FLOW:
200
GPM
(752
I/min);
TEMP:
200' F
(93'
C)
.
e
FILTER,
REGULATOR/LUBRICATOR
SUPPLIED
WITH
UNIT.
e
WITTED
PARTS
ARE
TEFLON•,
TYPE
316
STA
IN
LESS
STEEL,
AND
E
PR
.
HOW
TO
ORDER
EXAMPLE:
AAB29
OAGB
F- 6-
2+
5543D-H3/ 4U-316SSD0350
-fll L
SPECIFY
NOZZLE
SIZE
,!c
MATERIAL
(SEE
D.S.
290AG-1)
SPECIFY
NUMBER
Of
NOZZLES
2
OR
4,
•
THIS
WILIL
DETERMINE
FLANGE
SIZE.
SPECIFY
EXTENSION
LENGTH
IN
FEET.
F
LANGE
s1zr
*
ADD
"B"
TO
THE
PART
NO
.
FOR
BS
PT
CONNECTIONS
DEBCRPTION:
110.
AA2IIOAQ.-
AJA
MOT0IU)IIIV!'.N
TANK
WA811Et f8sea~~£0:
_!>,_O
.
Bo•
7900
-
--
L I01811-
__
Nn..2.
--

MI-290AG Rev. 4
5
MOTOR
£ND
Vl[W
OF
INLET
BODY
MOUNTING
FLANGE
>-----'0,D.
Fl.ANGE
(SEE
TAB
.
,1-----~
SPRAY
HEAD
TANK
D1At.lET£R
OPENING
REQUIREMENTS
FOUR
NOZZLES:
.8.25'
[•209
.5
mm]
MIN
.
lWO
NOZZLES:
••A'
BOLT
HOII
EQUALLY
SPACED
FOR
QTY.
(SEE
TAB.)
DIA.
BOLT
CIRCLE
(SEE
TAB.)
,1.25•
[•184.1
mm]
MIN.
*
DIRECTION
OF
ROTATION
IS
VERY
IMPORTATNT.
NOZZLE
HUB
MUST
ROTATE
IS
INDICATED.
@Ip""'"'
--
Co.
FLANGE
O.
D.
DIA.
DIA.
OF
NO.
OF
• A
BOLT
HOII
Fl.ANG
E
BOLT
PART
NO.
OF
HANG[
CIRCLE
HOLES HOLES
58265-BF-31
&L
.,3.5 ,11.75 8 .
88
58265-10H16L
.,s.o
•14.25
12
1.00
AIR
MOTOR
DATA
AIR
APPROX.
SPEED
AIR
TIME
FOR
PRESSURE
ONE
COMPLETE
REVOLUT
I
ONS
AT
MOTOR
(RPM)
CONSUMPTION
CYCLE
(M
I
NUTES)
REOUIRED
FOR
1
[OP~,\
i~o
l;j
at~\
iso
P;j
COMPIITE
CYCLE
PSI
bar
3A5
bar
7.24
ba
SCFM
I/NC,
7.24.,.
12
0.83
6 2
4.7
2.2
11
32
14
0.97
8 4
5.4
2.5
7
17
61
16
1.10
10
8
6.3
3.0
6 8
18
1.24
--
9
7.1
3.4
--
7
K~M
AN
~
~"TCLl
I
Ml
VAKT
1
IIH
LII/UIU
, •.,.,UKl,
FLOW
RATE
DATA
AVG.
TOTAL
FLOW
or
2
NOZZLES
(EQUAL
CAPACITY)
GALLONS
PER
WINUTE
(LITERS
PER
MINUTE)
INLET
PRESSUR
E,
PSI
(bor)
NOZZL£
50
3.
5
100
/7
150
/,a
200
,,
5\
250
/17
55430-H3
4U-316SS00100
22
85
32
121
39
1«
45
1771
50
188
55430-H3
4U-31
•••00200
45
171
63
241
77
,
..
89
,~,,
100
j/1
55,UO-H3
4U-316SS00250
56
71
79
~1
97
'""
1112
441
125
471
55430-H3
4U-316SS00350
78
298
111
422
136
505
157
618
175
658
55430
H3
4U
316SS00400
RQ
'rn
MOTOR-DRIVEN
EXTENSION
TANK
WASHER
No.
LENGTH
M290AG8F-3-2
3'
(0
.9
m)
M290AG8F-4-2
4'
(1.2
m)
M290AG8F-6-2
6'
(1.8
m)
M290AG10F-3-4
3'
(0,9
m)
M290AG10F
- 4- 4
.4'
(1.2
m)
M290AG10F-6-4
6'
(1.8
m)
DESCR
I
PTION:
IPD:IFICA'IIONI
FOi
No.
M
ZIOAII
F-_-_
AIR
MCnOll-..vEN
TAI«
WASHEii
1?A
..
,
\
...
~77
1JQ
JnA
ionn
·1~,
WEIGHT
56
LBS.
(25
.5
kg)
60
UIS.
(27.3
kg)
69
UIS.
(31.4
kg)
63
UIS.
(28.
7
kg)
67
UIS.
(30
.5
kg)
76
LBS.
(34.6
kg)
·s~~ga
RH.
No.
3
Roi.
Dot
•
-~••I
No,
noAG-1
SHEET OF

MI-290AG Rev. 4
6
MAINTENANCE
Removal and replacement of spray nozzles (see parts list drawing PL 290AG: p10)
Unscrew spray nozzles (20) from nozzle hub (19) and inspect for wear and plug gage. If
the nozzles need replacement, obtain new nozzles.
If a nozzle is plugged or partially plugged, clean out the orifice and inlet area with a
wooden toothpick or other relatively soft probe. Screwdrivers, wire or other hard metal items
may scratch and severely damage the orifice and should not be used.
Replace spray nozzles (20) in nozzle hub (19) by tightly screwing them in.
Removal of #46340 air motor drive (see parts list drawing PL 46340: p13)
First make sure unit is completely disconnected from air source. Using a 3/16” Allen
wrench, unscrew and remove both 1/4-20 socket head cap screws (5) and respective spring
washers (4). You should now be able to lift the air motor drive completely off the inlet body
casting, leaving the aluminum adapter (3) still attached to the 46340 air motor drive. The two
M5 socket head cap screws (1) and respective spring washers (2) can then be unscrewed and
removed using a 4 mm hex Allen wrench.
Replacement of #46340 air motor drive (see parts list drawing PL 46340: p13)
First make sure the unit is completely disconnected from air source. Next, insert the 1/4-
20 socket head cap screws (5) and spring washers (4) in the aluminum adapter (3). Align the
M5 through holes on the aluminum adapter (3) with the female threaded M5 holes on the gear
reducer (10) and secure with the 4mm Allen wrench. Attach, if not already attached, the coupler
(8) to the gear reducer (10) drive shaft and insert the coupler end of the air motor drive
assembly through the hole in the top of the 290 inlet casting. Use the 3/16” hex Allen wrench to
tighten the 1/4-20 socket head cap screws and washers in the aluminum adapter to the casting
inlet.
Note: Air motor assemblies on older AA290A assemblies can be removed by disconnecting the
unit from the air source, then removing and unscrewing the cap screw bolts and lock washers
holding the air motor flange to the 290 inlet casting.

MI-290AG Rev. 4
7
Replacement/Removal of air motor drive coupling (8) (see parts list PL 46340: p13)
First, follow procedure above for “Removal of #46340 Air Motor Drive”. With a rubber
mallet tap the coupling (8) to dislodge it from the gear reducer (10).
Align the key way on the coupling (8) with the key (9) on the gear reducer (10) shaft and
lightly tap the coupling (8) till the coupling (8) bottoms on the gear reducer (10) shaft. By
reversing the above steps you will be able to remove the coupling (8) from the gear reducer (10)
shaft.
Note: The coupling (8) on the gear reducer (10) shaft has a press fit so the coupling (8) does
not come apart during assembly or disassembly.
Replacement of o-rings (3) in upper bushing retainer (2) (see parts list PL 290AG: p10)
If it has not already been done, remove the air motor sub-assembly per the previous
instructions. Now carefully press out the groove pin (8). Loosen the upper bushing retainer (2)
and remove it from the shaft (9). Remove o-rings (3), gasket (22) and retainer (2) and replace
with new parts.
Note: If the o-ring (5) in the adjustable flange assembly (5-7) is going to be replaced it should
be done now. See replacement of o-ring in adjustable flange section below.
Reinstall the upper bushing retainer (2) with the gasket (22) by carefully sliding both
parts over the shaft (9). Replace groove pin (8). Thread retainer (2) into the inlet body (4) and
tighten. Attach the air motor assembly (1) per the previous instructions.
Replacement of o-ring (5) in adjustable flange (7) (see parts list PL 290AG: p10)
With the air motor (1), groove pin (8), and upper bushing retainer (2) removed, remove
the drive link retainer screw (18), and drive link (21). Note the position of the drive link tabs.
Remove lower bushing retainer (15) that also includes the shaft bushing (16), and o-ring (3).
Now slide the shaft (9) out of the unit. Next remove either the inlet body (4) or bevel gear sub-
assembly (11) including the rotary housing (13) and nozzle hub (19) from the extension tube
(10). Loosen the three set screws (6) and slide the flange assembly (7) off the extension tube
(10). Replace the o-ring (5) and reassemble flange onto the extension tube (10). Reassemble
all parts onto the unit. Make sure all parts are tightened before start up of the unit making sure
that the drive link (17) is installed with tabs in the same position noted earlier.

MI-290AG Rev. 4
8
Replacement of nozzle hub bushings (14)) (see parts list PL 290AG: p10)
Unscrew (clockwise-left hand thread) rotary housing plug (21), and slide bushings (14),
and nozzle hub (19) off the rotary housing (13). Remove any foreign material from nozzle hub
gear teeth. To replace parts, slide one bushing (14) onto rotary housing tube (13), push up to
the shoulder. Next slide nozzle hub (19) followed by second bushing (14) onto rotary housing
tube (13). Finally screw on (counterclockwise) rotary housing plug (21) and tighten with wrench
until tight.
Replacement of rotary housing bushing (14), split bushing (12), shaft bushing (16) and o-
ring (3) (see parts list PL 290AG: p10)
Note position of drive link (17) tabs relative to rotary housing (13). Remove drive link
retaining screw (18), and drive link (17) from unit. Next remove the lower bushing retainer (15).
Now slide the rotary housing (13) assembly with its bushing (14) and split bushing (12) off the
bevel gear sub-assembly (11). Remove any foreign material from the bevel gear teeth.
Remove worn bushing (14) and split bushing (12) from the rotary housing (13). Remove
worn shaft bushing (16) and o-ring (3) from the lower bushing retainer (15) and replace with new
parts. Inspect shaft (9) for wear and replace shaft if worn.
Now you are ready to reassemble the unit by first installing the split bushing (12) nearest
the gear (11). Holding split bushing (12) in place on bevel gear sub-assembly (11), slide rotary
housing (13) over split bushing. Install bushing (14) over bevel gear sub-assembly (11) into
rotary housing (13).
Now carefully screw the lower bushing retainer (15) over the shaft (9) and into bevel
gear sub-assembly (11). Tighten retainer (15). Reinstall the drive link (17) with tabs in the
same position noted earlier and tighten retainer screw (18).

MI-290AG Rev. 4
9
AIR MOTOR LUBRICATION
Use detergent SAE #10 automotive engine oil. Consult with you local supplier of
lubricants or contact your local Spraying Systems CO
.
®sales office.
NOTE: The air source must be water free, and be properly lubricated to prevent rust and
excessive friction from wearing out the motor prematurely. If the air motor is properly
taken care of, it should last for many cleaning cycles before repair or replacement.
Manual Lubrication: Add 10-20 drops of oil, every 8 hours of operation, to air motor
through inlet port while air source is shut down.
Automatic Lubrication: Inline air lubricator (page 8) should be adjusted to feed 1 drop per
minute for high speed or continuous duty use. Do not over feed oil as contamination of exhaust
air may result.

MI-290AG Rev. 4
10
*
*
*
*
*
*
*
*
ITEit
?
ART
H
O.
DESCR
IPllON
1 46340-290 Iii•
Motor
o,;,. Assemb
ly
2 CP2JG51-1-!-1
GSS
Upper
8ush
in6
· ~el~i
r.
er. T
ypet
~1-G
Stol
n
le~~
$IHI
3 CP7717-10-EPR 0-Riig, El\ylene
Propy
:ene
Ruober,
(~
Re,
(:'
.)
A
CP23642
-
SS
In
,t
Body,
Slain
css
Stee
l (2"
N.P.T.
Cono
.)
CPB23642
-
SS
In.et
Body,
Slain
ess
Stee
l (2"
8.
S.P.T.
Conn.)
5
CP7717
- 2-
JJ2
-ffR 0- Ri,g,
El
,1
ylene
Propy
:ene Rubber
6 CP2J668-SS Set S:rew, Stci1less
Sleel
(3 Req'd)
7
CP58260
-
8f
- J
16
L fl
ange
I,
Hub
Welding
S
ub-Assembly
, i
ype
316L
Stoinle,s
S
tee
l,
fo·
AA__290AG8f-
_- 1
CP58260
-
IOF
-
316L
f
onge
I<
Hub
Weldin~
Sub
-
Assembly
, i
ype
316L
Stainless
Steel,
fo•
AA...2
90AG8
F- _- 4
CP58265
-
8f
-
5S
AcjJsloble
F
lo
,
,e
Sub
-
Ass,rrbly,
S1ci
n.
511.
(lnclJdes
llems
5,
6 &
7)
For
A...290AG!f
-- 2
CP58265
-
1Cf
-
SS
A
dju
skb
le
Flan
go
Sub
- ~
.sse
m
bly,
Sta
n.
SI
i. (lnclud,s lterrs
S,
6 iI
7)
for
AA_19JAG8F
- _- 4
8
CP2J65
5-
SS
Gri:o'-'e
P
in
, S
toi
n
less
Sleel
g CP23660- -316SS Shafi,
Type
316
Stain
less Stoel
10
CP2366
1-
__
- 31
6SS
E:i
de
rsio
n
Tu':le,
Type
3.
lS
Stainless
S·8eil
11 CP23667-316SS
Bevel
Goor
Sub-Assml>ly, l
ype
J I6
Stfrloss
Sleel
12
CP23679-1-cc·
mr
Split
Bu,hing, Corban
Grop
hi
t,
f i
ll
ed T
EFL
ON"'
(1
Req'
d)
13
CP23644-SS
Rota1
Housirg,
Sl
:
in
l
ess
Steel
14
CP23679-CCRTEf
Bush'n3,
Ccrba
n
Grcphile
Fil
led
TffLON
111
(3
,eq
'd)
IS
CP23663-1-316SS
Low
er
Bush'ng
R:eta'ne
,,
Typ
e 316
S~inless
Steel
15
CP23658
-
CCRTEr
Shoff
Bushirg,
Carta,
Gra
ph
ite
Filled
TEr
L
CN®
17
CP23649-3
16S
S
Drive
Li
rk
,
Type
316
Sbin
less Steel
18
CP
191
07-
316SS
Screw,
T
y;,e
316
Sto
irless
Slee!
19
CP23647
- 2-
SS
Nozz
e
Hub,
Stainless
Slee
\
For
Al._29C-AG8F
- _- 2 w
T!h
2
Nozzles
CP2364
7- L-
SS
Nozz
le
Hub,
St
oia
loss
Sl,el,
For
Al._290AG
1
0f
- _- 4
with
4 Nozzles
20 55430-
H5/
4U-
Spray
t-.o
z:z:
le,
Solid
S
fr
eam VooJ
el
~ou
le
W"tt,
Stabilizor 'lar-e,
316SSOO
___
T
·1ae
3i 6 Stcirle,s St,,I
(2
or
'-
Req'd)
21
CP23664
-
316SS
Rotary
Housi
ng PI
J,
·,
Type
315
Ski
nless Sle,I
22
CP58355
- NY
Gos
~,1.
Nylo
n
li'
o.
AA2
·
30AG8
"- _
-2
Af
r
Mv
to
r-Oilven
Te
n~
Wosher
w
ith
2
riozz
r
es
N
o.
AA290AG10F
- _- 4
A"
r Mcbr-Drive,
Taak
Wcsher
wi
li
4
Nozzles
N
o.
M8290Ac.l
f- _- 2
A'r
Mel
or
-
Drive,
Ta
nk
We
-she·
wit
n 2
Nozz
les
(BSP
T Vmion)
~'
o.
AAB290AG"
1
0F"-
_- 4
Air
~o
r
or
-
Dr
r~·•n
Ta
nk
Washu
,,
,
(t
h 4
rfo
zz
ln
(
8SPT
Version}
He
,
<o.
21
050
LUBHATCR
ASSEMB
LY
(SEE
PL 210lC)
IS
l UP
PLI,O
WITH
EACH
M...290A.C
J -_- _
lt
•
~o
.
A.
629CAG
- <
IT
Sp<:f
•
:?
:irt~
Ki
l (
nc::
h.
c'
l
!t
o I i•
en:!i
!'t'arbd wih
•)
©
s,ra,·1g
Srr..m
Co.
, - - - 7
: ~
I,?.
:--
,
-7
2l"-f'l't
! "--._8 I
20
14
~
: l o -"
~
.
~
- 9 :
~
i
I
2
-L
tt
3~ -
??
_L
:
I
I
I
I
I
I
~
:
L I
______
J
DESCRIPTION:
- 10
r
L
____
_
Ho.
M290AGJ-
_- _
at
No.
AAB29OAG_r-_-_
AIR
MOTOR
-
DRIVEN
TANK
WASflER
{wl
TH
2
OR
4 NDZZLES}
12
20
@/Q
\ ~
fl
"-
19
'
14
'-
13
9_
,4
-
--
3
~-15
Q -
16
g,-
17
.a.
-
18
~
se~~~s~~!
~~!.~
o:
P .n
Amr
7Ann
•
Wh
111
•t
nn,
II
RC11.R.Q.7QOO
Rav
. N
o.
8
Re
f.
Parts List No.
PL
290AG
SHEET
OF

MI-290AG Rev. 4
11
AIR
MUFFLER
---------
AIR
INLET
CONN.
1/4"
NPT
(M)
GEAR
REDUCER
--
--
PERMANENTLY
LUBRICATED
290 TA
NK
WASH
ER
AD
A
PTER
290
INLET
AIR
APPROX.
SPEED
PRESSURE
AT
t.l0TOR
(RP
M)
PS
I
bar
50
PSI
(3.-45
bar)
250
PSI
(17.24
b(]r)
12
0.83
6 2
14
0.97
8 4
16
1.10
10
8
18
1.
24
-- 9
~3
15/16"
r
[100.1
mm]
APPROX
AIR
CONSU
M
PTION
SCF
M
I/sec.
4.7
2.2
5.4
2.5
6.3
3.0
7.1
3
.4
~ - -
--
AIR
MOTOR
REQU
I
RES
SAE
#10
AUTOMOTIVE
E
NGINE
OIL
FOR
LUBRICATION
10"
[254
mm]
APPROX.
Tit.I
E
FOR
ONE
COt.l
P
LETE
CYCLE
(MINUTES)
50
PSI
(3.45
bar)
250
PSI
(17.24
bar)
11
32
7
17
6 8
--
7
PARTS
LI
ST
PL4634O
APPROX.
WEIGHT
6
.2
5 lbs
[2
.8 k
g]
REVOLUTIO
NS
REQUIRED
FOR
1
COMPLETE
CYCLE
61
RP
M
AND
CYCLE
Ti
t.I
E
VARY
WITH
LIQU
ID
PRESSURE.
SEE
DATASHE
ET 4
6340
FOR
PERFORMA
NCE
DATA
OF
THIS
MOT
OR
ON A
090
& 1
90
TANKWASHER,
DESCRIPTION:
No.
48340-
_ _ _ AIR DRIVEN
MOTOR ASSEMBLY
FOR
290
AIR
MOTOR-
DRIVEN
TANK
WASH
E
RS
c Spraying Systom•
Co.
~
se~~e.
~?:5~!!!~~£0:
P.O. Box
7900
-Wheaton, II.
60189-7900
Rev
.
No
.
Ref.
Data Sheet No.
48340-290
SHEET
OF

MI-290AG Rev. 4
12
I
I.
~"""
I I
©
__
...
ITEM
PART
NO.
DESCRIPTION
1 CP22023 Coupler, Bross
2 CP22024-I CouDler Nlccle, Stael
3 CP22025 FIiter /
Reg
uIator
4 26383-
1/4-100
Gouge
s
CP7998-7/8
Close
Nlpcle, Bross
6 CP22027 Lubricator
No,
21
030
Lu
brlcator
Ass
•mblv
Dl!8CRIPT
ION
:
No.
21050
WmllCA'JOlt
ASSDIB.Y
..
SprayingSystems
CO:
'lIJ' sgray Nozzle•
and
Acceaaorlea
P.
. •
ox
7900
•
Wlwlllon.
I.
801111-7'1100
Rn.
No. Pone
U.t
No.
PL
21030
R.t
. IHl!l!T OF

MI-290AG Rev. 4
13
•
•
•
•
•
4 5
J \ \ 6 7 8
\ \ \
1B
•
//
/
~it~
I
___
n n
~
·~
~
't--t!}_j I 4 5
I I I /
1.
1 2 9
ITEM
PART
NO
.
DESCRIPTlOH
1
CP46766-20-316SS
IIETRIC
SOCKET
HEAD
CAP
sen,
MS
1
0.8
x
20
mm
LG.
TYPE
316
STAINLESS
STEEL
(2
REQ'D)
2
CP46352-5-316SS
METRIC
SPRING
WASHER,
5
mm,
STAINLESS
STEEL
lYPE
316
(2
REQ'D)
3
CP46J.45-190-AL
090/190
ADAPTER,
IJ.J.JMINUM
{FOR
MODEL
IMD90AG--
OR
M190AG--)
CP463-45-290-AL
290
AllAPTDI,
AUJMINUM
[FOR
MODEL
IM290AG--}
'
CP46553-SS
SPRI~
WASHER
,
1/4"
,
STAINLESS
STEEL
TYPE
18-8
(2
REQ'O)
5
CP26197-1/2-SS
SOCKET
HEAD
CAP
SCREW,
1/4-20 x
1/2
LG
.
TYPE
18-8
STAINLESS
STEEL
(2
REC'D)
6 CP7717-2-214-VI
0-RIHG,
VITON
7 CP7717-2-124-VI
0-RIHG,
VITON
CP46343
-
316SS
COUPLING,
316
STAINLESS
STEEL
(FOR
MODEL
fM090AG
--
OR
M190AG
--
)
8
CP46343
-
290
-
316SS
COUPLING,
316
STAINLESS
STEEL
(FOR
MODEL
fM290AG
--
)
9
CP46J49-4-IBO
METRIC
KET,
5
mm
THICK,
STEEL
10
CP46J42
GEAR
REDUa:R
11
CP463«-8-IBO
IIETRIC
SET
SCREW,
CUP
POINT,
118
1
1.25
x 8
mm
LG.
ALLOY
STEEL,
Bl.ACK
O~OE
COATING
(2
REQ'D)
12
CP46J47-I
MOTOR
PINI
ON,
STEEL
13
CP46346-4-IBO
METRIC
SET
SCREW,
CUP
POINT,
M4
1
0.7
x 4
mm
LG
.
ALLOY
STEEL,
BLACK
O~DE
COATING
14
46350
AIR
MOTOR
,
GAST
1UP-NRV-10
,t
AIR
MOTOR
MUrF'l.ER
,
GAST
AF350
15
CP38674--7
90'
STREET
ELBOW
,
1/8
NPT
(I,(]
•
1/8
NPT
(F'),
BRASS
16
CP26396-1
HEX
PI
PE
NI
PPLE
,
1/4
NPT
(M)
1
1/8
NPT
{II).
BRASS
©•--c..
1\
11
\
I
11
NO.
463,40-190
I.IR
MOTOR
ASSEMBLY
{FOR
MODEL
fMD90AG--
OR
M190AG--)
NO.
46340-290
AIR
MOTOR
ASSEMBLY
(FOR
MODEL
fAA290AG--)
NO.
4-6351
GEAR
BOX
SUB-ASSEMBLY
INCLU
OED
ALL
ITEhlS
MAR
KID
WITH
• • •.
INCW
QED
TOOLS·
3/15"
HEX
ALLEN
WRENCH
FOR
ITEM
5 (1/4-20
SOCKET
HEAD
CN'
SCREW)
2
mm
HEX
AllEN
WRENCH
FOR
ITEM
13
{M4
SET
SCREW)
\
4
mm
HEX
ALLEN
WRENCH
FOR
ITEM
1
(M5
SOCKET
HEAD
CAP
SCREW)
I:
ITEM
11
(MB
SET
SCREW)
.
14
DESCRIPTION:
No.
<CG40-1to
or
4U40-2IO
All
IIICIT1III
a\11111
ASSDa.T
!f9s~~o.
I ---L- I
._...
...._
Rav. No. 2
Raf.

MI-290AG Rev. 4
14
PART
NO.
45-200
D170PL
(Rev.
D)
AM SERIES LUBRICATED AIR MOTORS
OPERATION & MAINTENANCE MANUAL
Model 2AM Shown Model 4AM Shown Model
6AM
Shown Model 16AM Shown
Thank you for purchasing
thi
s Gast product.
It
is
manufactured to the highest standards
using quality materials. Please follow all recommended maintenance, operational
and safety instructions
and
you will receive years of
tr
ouble free service.
IMPORTANT: PLEASE READ THIS
MANUAL
AND SAVE FOR FUTURE REFERENCE.
General information
• Clearances: Model
1
AM/
1 UP
2AM
2AM *
4AM
4AM *
6AM
8AM
1
6A
M
Total End Clearance (in/mm)
0.00020/0.0508
0.00025/0.0635
0.00025/0.0635
0.00035/0.0889
0.00035/0.0889
0 00035/0.0889
0.00048/0.1219
0.00060/0.1
524
Top
Clearance (in/mm)
0.0015/0.0381
0.0015/0.0381
0.0025/0.0635
0.001
5/0
.0381
0.0025/0.0635
0.0015/0.0381
0.0015/0.0381
0.0015/0.0381
• Models with the l
as
t three digits greater than
500
(ie
2A
M XXX-501)
• Vane Lile:
• Operating Pressure: Depends upon speed,
ope
rating pressure and motor maintenance.
1
00
psi
or
below (7 bar)
Product Use Criteria:
• Operate
at
temperature
up
to
250°F
(121°C).
• Protect unit from dirt and moisture.
• Use ONLY
co
mpressed air
to
drive motor.
• Air lin
es
co
nnected to motor should be the same size or
the next size larger than the intake port for e
ffi
cient
ou
tput and speed
co
ntro
l.
• Protect a
ll
s
ur
rounding
it
ems from
ex
haust a
ir.
• Bearingsare grease packed.
• Use
Gas
t
#AD220or
a detergent SAE#10 aut
omo
tive
engine oil tor lubricating.
C·OGAST
ISO
9001
&
14001
CERTIFIED www.gastmfg.com
A
Unit
of
IKXCorporation
®Registered Trademark/™Trademark
of
Gast Manufacturing Inc
.,
Copyright
©2
001
Gast Manufacturing
In
c All Rights Reserved.

MI-290AG Rev. 4
15
Your safety and the safety of others
is
extremely important
We have provided many important safety messages
in
this manual and on your product. Always read
and obey all safety messages.
r.,i
. .
[l]
This
1s
the safety alert symbol. This symbol
alerts you to hazards that can kill
or
hurt you and
others. The safety alert symbol and the words
"DANGER" and "WARNING" will precede all safety
messages. These words mean:
ADANGER
You
will be killed
or
seriously injured
if
you don't
follow instructions.
AwARNING
You
can be killed
or
seriously injured
if
you don't
follow instructions.
All safety messages will identify the hazard, tell you
how to reduce the chance of injury, and tell you
what can happen
if
the safety instructions are not
followed.
INSTALLATION
Correct installation is your responsibility. Make sure
yo
u have the proper
in
sta
ll
a
ti
on cond
iti
ons and that
th
e
sp
ec
ified insta
ll
ation clearances are ava
il
a
bl
e.
AWARNING
Injury Hazard
Install proper guards
as
needed.
Failure to follow this instruction can result in
burns
or
other serious injury.
Mounting
This product
ca
n be insta
ll
ed
in
any orienlation. Mount
the motor to a
so
li
d base plate that is mounted to a
stabl
e,
rigid operating surtace.
In
sta
ll
a pressu
re
regulator or simple shut-o
ff
val
ve
to
co
ntrol mot
or.
Connection
Check the direction of
th
e motor airtl
ow
. A single
rotation motor will operate prope
rl
y only
in
one direction.
In
sta
ll
a filter in
th
e air line before
th
e
co
nn
ec
ti
on to the
moto
r.
Co
nn
ect lines to motor
in
th
e proper direction.
A reversible motor w
ill
work
eq
ually we
ll
in
bo
th
directions. Connecting a 4-way valve with piping to
both air po
rt
s of
th
e motor will make reversing possibl
e.
Do not add any thrust to the end or side of the shaft
when making connections. Do
not
use a hammer
on the shaft
or
connections.
Accessories
A muffler is shipp
ed
with the air motor (exce
pt
16AM)
but is not insta
ll
ed. Consult
yo
ur Gast
re
prese
nt
ative
f
or
addilional filler recommendalions.
In
sta
ll
a moisture
trap a
nd
filter
in
th
e air line ahead of
th
e motor. For
th
e
most e
ffi
cie
nt
output and
co
ntrol of speed, use air lines
that are
th
e same si
ze
or the next pipe si
ze
la
rg
er
th
an
the motor intake po
rt
.
An a
ut
omatic air line lubricat
or
should be insla
ll
ed
1
8"
or
as
close as possible
in
th
e air line just ahead of
th
e
motor. Adjust
th
e lubricator to feed one drop of o
il
for
every 50-
75
CFM of air moving through
th
e motor. Air
co
nsumption at va
ri
ous speeds and pressures are
ava
il
a
bl
e from your
bcal
Gast represe
nt
ati
ve
or
th
e
factory.
OPERATION
AWARNING
Injury Hazard
Air stream from product may contain solid or liquid
material that can result in
eye
or skin damage.
Do Not use combustible gases to drive this motor.
Wear hearing protection. Sound level from motor
may exceed
85db(A)
.
Failure to follow these instructions can result
in
burns, eye injury
or
other serious injury.
It
is your responsibility to operate this product at
recommended speeds, loads and room ambient
temperatures. Do not run the motor at high speeds
with no load. This will result in excessive internal
heat that may cause motor damage.
The starting torque is less than the running torqu
e.
Th
e
starting torque will vary depending upon the position of
the vanes when stopped in relation to
th
e air intake
port.
Use a pressure regulator and/or simple shut-o
ff
valve to
r
eg
ul
ate
th
e motor's speed and torqu
e.
This will prov
id
e
the r
eq
uir
ed
powerand will conserve air.
MAINTENANCE
AWARNING
Injury Hazard
Disconnect air supply and vent all air lines.
Wear eye protection when flushing this product.
Air stream from product may contain solid or liquid
material that can result
in
eye
or
skin damage.
Flush this product in a well ventilated area.
Do Not use kerosene or other combustible solvents
to flush this product.
Failure to follow these instructions can result
in
burns, eye injury
or
other serious injury.
It
is your responsibility to regularly inspect and
make necessary repairs to this product
in
order to
maintain proper operation.

MI-290AG Rev. 4
16
Lubrication
Use Gast #AD220
or
a detergent SAE #10 automotive
engine oil for lubricating. Lubricating is necessary
to
prevent rust on all moving parts. Excessive moisture in
the air line
rray
cause rust
or
ice to form in the muffler
when air expands
as
if passes through the motor.
Install a moisture separator in the air line and an after
cooler between compressor and air receiver
to
help
prevent moisture problems.
Manual Lubrication
Shut the air motordown and oil after every 8 hours of
operation. Add 10-20 drops ot oil
to
the air motor intake
port.
Automatic Lubrication
Adjust inline oiler to feed 1 drop of oil per rrinute for
high speed
or
continuous duty usage.
Do
Not overteed
oil
or
exhaust air may become contarrinaled.
Check intake and exhaust filters afterfirst 500 hours of
operation. Clean filters and determine how frequently
filters should
be
checked during future operation. This
one procedure will help assure the product's
performance and service life.
Flushing
Flushing this product
to
remove excessive dirt, foreign
particles, moisture
or
oil that occurs in the operating
environment will help to maintain proper vane
performance. Flush the motor if it isoperating slowly
or
inefficiently.
Use only Gast #AH2558 Flushing Solvent. DO NOT
use kerosene
or
ANYother combustible solvents
to
flush this product.
1. Disconnect air line and mutfler.
2. Add flushing solvent directly into motor.
If
using
liquid solvent, pour several tablespoons directly
into the intake port.
If
using Gast #AH255B, spray
solvent for 5-10 seconds into intake port.
3. Rotate the shaft by hand in both directionsfor a
few rrinutes.
4.
You
must wear
eye
protection
lor
this step.
Cover exhaust with a cloth and reconnect the air
line. Slowlyapply pressure until there is no trace
of solvent in the exhaust air.
5. Listen for changes in the sound of the motor.
If
motorsoundssmooth, you are finished.
If
motor
does not sound like it is running smoothly,
installing a service kit will
be
required.
(See "Service Kit Installation").
Check that all external accessories such
as
rellel
valves
or
gauges are attached and are not damaged
before operating product.
Shutdown
It Is your responslbllHy
to
follow proper shutdown
procedures to prevent product damage.
1. Turn off air intake supply.
2. Disconnect plumbing.
3. Remove air motorfrom connected machinery.
4.
Wear eye protection. Keep away from air
stream.
Use clean,
dry
air to rerrove condensation.
5. Lubricate motor with a small amount of oil in
chamber. Rotate shall
by
hand several limes.
6. Plug
or
cap each port.
7. Coat output shaft with oil
or
grease.
8. Store motor in a
dry
environment.
SERVICE KIT INSTALLATION
Gast wlll NOT guarantee lleld-rebulH product
performance. For perlonnance guarantee, the
product must be returned to a Gast authorized
service
facility_
Service kit contents vary. Most contain vanes, end cap
gasket, body gasket, bearings and a muffler element
or
felt.
Majorand Minor Rebuilds
Tool kits which Include a more In-depth rebuild
manual areavailable through your Gast distributor.
These kits include the tools required
to
rerrove and
reassemble end plates, bearings and shalt seals, and
to
set the proper end clearance. The rebuild manual also
includes step
by
step instructions, including illustrations,
to
help achieve a successful rebuild. Gast
Manufacturing, Inc. highly recommends using the air
motor rebuid manual and tool kit when attempting a
rrinor
or
major rebuild toyour Gast air motor.
Minor Rebuild:
1. Remove the end cap.
2. Remove dead end plate bolts.
3. Remove dead end plate. (Use factory issued tool,
do not use screwdriver to remove the end plate.
4. Remove the dowel pins from the body and push
back into end plate until flush
or
just below the
machined surface of the end plate.
5. Remove vanes.
6. Clean parts. Check for scoring on the end plate
and rotor assembly.
If
scoring exists, send unit
to
a Gast authorized service facility.
7. Lubricated models only: Lightly oil and reinstall
vanes.
8. Place the proper end plate gasket on the end
plate.
If
the original isdamaged, replace with a
new one supplied in the Service Kit.
9. Place the dead end plate on the body.
10. Pressthe bearing onto the shaft using a factory
supplied bearing pusher.
11.
Tap
dowel pins into body and install end plate
bolts.
lighten
bolts
to
75-100 in-lbs.
12. Set end clearance
as
required by model:
1AM-4AM and NL22-NL52 models -use the
bearing taper from kit
to
lightlytap on inner race of
the dead end bearing
to
free up and center the
rotor in the body.
6AM-8AM models -lightly strike the drive end
shaft with a soft hammer
to
push the rotor away
from the drive end plate. The rotor must NOT rub
on either end plate.
13. Reattach end cap.
14. Hthe air motor is lubricated, applya few drops
of Gast #AD220 lubricant into ports. Rotate shalt
by
hand for a few rotations.
Major Rebuild:
1. Remove the end cap.
2. Remove dead end plate bolts.

MI-290AG Rev. 4
17
3.
Remove dead end plate. (Use factory issued tool,
do
not use screwdriver
to
remove the end plate.)
4.
Remove the dowel pins from the body and push
back into end plate until flush
or
just below the
machined surface of the dead end plate.
5.
Remove rotor using an arbor press.
6.
Remove vanes and ejection mechanism if
reversible. (Ejection mechanisms mayconsist of
vane springs, pins, caps
or
cam rings.)
7.
Remove shaft seal and bearings from drive end
plate and bearing from dead end plate. (Use
factory issued tool.)
8. Do Not remove drive end plate bolts
or
drive end
plate.
9.
Clean parts. Check for scoring on the end plates
and rotor assembly.
If
scoring exists, send unit to
a Gast authorized service facility.
1
O.
For reversible models only:
1AMand 1UP models -place a new cam ring
between the rotor and the drive end plate.
2AM and 4AM models -place springs
and
caps
in rotor.
6AM, 8AM and 16AM models -install push pins.
11.
Place the drive shall of the rotor assemblythrough
the drive end plate. Press the drive bearing onto
the drive shaft using a factory supplied bearing
pusher.
12. Using the bearing taper from the
Tool
Kn, lightly
tap on inner race of the drive end bearing to snug
up rotor
to
drive end plate.
13. Install newvanes
as
required
by
model:
All single rotation units -the angle cuts
on
the
vane face to center of the rotor.
Reversible unns2AM and 4AM -the notch on
vane faces
to
centerof the rotor.
6AM, 8AM and 16AM models -install the vane
spring lip into the notch at one end of the vane
and place in rotor vane slot with spring facing
pushpin.
14. Place the proper end plate gasket on the body of
dead end.
It
the original is damaged, replace
with a new one supplied in the service
kn.
If
your air m:itoruses O-lings, place the new
O-rings in the body groove. Some models
do
not
use end plate gaskets
or
O-rings.
15. Place the dead end plate
on
the body.
16. Install the dead end bearing and press into place
with bearing pusher tool from tool kit.
17. Install the dowel pins.
18. Fully tighten the remaining bolts
to
75-1
oo
in-lbs.
19. Set end clearance
as
required
by
model:
1AM-4AM and NL22-NL52 models -use the
bearing taper from the Tool Kit and lightly tap on
the inner race of the dead end bearing
to
free up
and center the rotor in the body.
6AM-8AM models -lightly strike the drive end
shaft with a soft hammer to push the rotor away
from the drive end plate. The rotor must NOTrub
on either end plate.
20. Apply a small amount ol grease
to
bearing seal
and install the drive end bearing seal
by
pressing
flush
wnh
bearing pushing tool from
Tool
Kit.
21. Reattach end cap.
22. If
the
air
motor is lubricated, applya few drops
of Gast ltAD220 lubricant into portsand rotate
shaft
by
hand for a few rotations.

MI-290AG Rev. 4
18
EXPLODED PRODUCT VIEW, PARTS & ORDERING INFORMATION
1AM
SERIES
REF#
DESCRIPTION
QlY
1AM-NCC-12
1AM
-NCW-14
1AM
-
NRV
-39A 1AM-NRV-56
1A
SEAL 1
AC
1
90A
AC
1
90A
AC190A
AC
190A
211
BEARING
2
AG5<11
AG5<11
AG549 AG5ill
3 DOWEL
PIN
4 D324A D324A 0324A 0324A
4
DRIVE
E
ND
PLATE 1 AG537 AG539 AC520 AC520D
5M
SHIMS 2 AC5278 AC5278 AC527B AC527B
6 BODY 1 AC521 AC521 AC 191 AC191
7 CAM RING 2 AC1
95
AC195
8
OOTOR
ASSEMBLY 1 AC524 AC536
AC
1
93
AC187
911
VANE
4 AC205A AC205A AC259A AC259A
8
10
DEAD
END
PLATE 1 AG538 AG540 AC192
AC
192
1
111
END
CAP
GAS
K
ET
1 AC229 AC229 AC229 AC229
12 DEAD END
CAP
1 AC228A AC228A AC228A AC228A
u•A
MUFFL
ER
1 AF350 AF350 AF350 AF350
...
FOAM
1 AG896 AG896 AG896 AG896
...
SERVICE KIT 1
K200 K200
1<201
1<201
1UPSERIES
REF#
DESCRIPTION
QlY
1U
P.
N
CC-
1A
1U
P.
NCW-2A 1UP.NRV
-3A
1UP.NRV-4
1A
SEAL 1 AC190A
AC
190A AC190A AC190A
2&
BEARING 2
AG5<11 AG5<11
AG549 AG5ill
3
OOWEL
PIN
4 0324A D324A 0324A 0024A
4
DRIVE
END
PLATE 1 AC616 AG520B AC520 AC520D
5M
SHI
MS 2 AG527B AG527B AC527B AC527B
6 BODY 1 AE899 AE899 AE898 AE898
7
CAM
RING
2
AC
195
AC
1
95
8
OOIDR
ASSE
MBLY 1 AE896 AE895 AE897 AF746
9 & VANE 4 AE893 AE893
AE894
AE894
8
10
DEAD
END
PLATE 1 AC617 AC192A
AC
192
AC192
1111
END
CAP GASKET 1 AC229 AC229 AC229 AC229
12
DEAD
END
CAP 1 AC228A AC228A AC228A AC228A
...
II
MUFFL
ER
1 AF350 AF350 AF350 AF350
...
FOAM
1 AG896 AG896 AGB96 AG896
...
SERVICE
KIT
1
K285 K285
1<286 1<286
•••
It
em not sh
ow
n.
11
Denotes parts
in
clud
ed
in
the Service Kit.
Exploded views are shown for
reference onl
y.
Units may vary
depending upon spec
ifi
c model.
1AM-NRV-60 1AM-NRV-63A
AC
1
90A
AC
1
90A
AG549 AG549
D324A D324A
AC520D AG520
AG527B AG527B
AC191 AC191
AC1
95
AC1
95
AC007 AC193B
AC259A AC259A
AC192 AC192
AC229 AC229
AC228A AC228A
AF'J50 AF'J50
AG896 AG896
1<278
K278
1UP.NRV-
10
1UP.NRV-
11
AC
1
90A
AC
1
90A
AG549 AG549
D324A D324A
AG520 AG520D
AG527B AG527B
AE898 AE898
AC195 AC195
AE3
19 AE333
AE894 AE894
AC192 AC192
AC229 AC229
AC228A AC228A
AF'J50 AP.350
AG896 AG896
K298 K298
M Parts used on models manufactur
ed
prior to 1998.
Parts
li
st
ed
are for stock models. For specific OEM models, please consult
th
e factory.
When corresponding abo
ut
or
ordering parts, please
gi
ve complete model and serial numbers.

MI-290AG Rev. 4
19
WARRANTY
Gast tinished products, when properly installed and operated under normal conditions ot use, are warranted
by
Gast
to
be free from defects in material and workmanship for a period of twelve (12) months from the date of purchase from
Gast
or
an authorized Gast Representalive
or
Distributor.
In
order
to
obtain pertormance underthis warranty, the buyer
must promptly (in no event later than thirty (30) daysalter discovery of the defect) give written notice of the defect
to
Gast Manufacturilg Incorporated, PO Box 97, Benton Harbor Michigan USA49023-0097
or
an authorized Service
Center (unless specificallyagreed upon in writing signed
by
both parties
or
specitied in writing
as
part of a Gast OEM
Quotation). Buyer is responsible for freight charges both
to
and tram Gast in all cases.
This warranty does not apply to electric motors, electrical controls, and gasoline engines not supplied
by
Gast. Gasl's
warranties also
do
not extend toany goods
or
parts which have been subjected
to
misuse, lack of maintenance,
neglect, damage by accident
or
transit damage.
THIS EXPRESS WARRANTY EXCLUDES ALL OTHER WARRANTIES OR REPRESENTATIONS EXPRESSED OR
IMPLIED BY ANY LITERATURE,
DATA,
OR PERSON. GAST'S MAXIMUM LIABILITY UNDER THIS EXCLUSIVE
REMEDY SHALL NEVER EXCEED THE COST OF THE SUBJECT PRODUCTAND GASTRESERVES THE RIGHT,
AT ITS SOLE DISCRETION, TO REFUND THE PURCHASE PRICE
IN
LIEU OF REPAIR OR REPLACEMENT.
GASTWILL NOT
BE
RESPONSIBLE
OR
LIABLE FOR INDIRECT OR CONSEQUENTIAL DAMAGES OF ANY KIND,
howeverarising, including but not limited
to
those for use of any products, lossof time, inconvenience, lost profit, labor
charges,
or
other incidental
or
consequential damages wnh respect to persons, business,
or
property, whether
as
a
result of breach ot warranty, negligence
or
otherwise. Notwithstanding any other provision of this warranty, BUYER'S
REMEDYAGAINST GAST FOR GOODS SUPPLIED OR FOR NON-DELIVERED GOODS
OR
FAILURE
TO
FURNISH
GOODS, WHETHER
OR
NOT BASED ON NEGLIGENCE, STRICT LIABILITY OR BREACH OF EXPRESS
OR
IMPLIED WARRANTY IS LIMITED SOLELY, AT GAST'S OPTION,
TO
REPLACEMENT OF
OR
CURE OF SUCH
NONCONFORMING OR NON-DELIVERED GOODS OR RETURN OF THE PURCHASE PRICE FOR SUCH GOODS
AND
IN
NO EVENT SHALL EXCEED THE PRICE OR CHARGE FOR SUCH GOODS. GAST EXPRESSLY
DISCLAIMS ANY WARRANTY OF MERCHANTABILITY OR FITNESS
FORA
PARTICULAR USE OR PURPOSE WITH
RESPECT
TO
THE GOODS SOLD. THERE ARE NO WARRANTIES WHICH EXTEND BEYOND THE DESCRIPTIONS
SET FORTH
IN
THIS WARRANTY, notwithstanding any knowledge of Gast regarding the use
or
uses intended to
be
made of goods, proposed changes
or
additions
to
goods,
or
any assistance
or
suggestions that mayhave been made
by
Gast personnel.
Unauthorized extensionsof warranties by the customer shall remain the customer's responsibility.
CUSTOMER
IS
RESPONSIBLE FOR DETERMINING THE SUITABILITY OF GASTPRODUCTS FOR CUSTOMER'S
USE OR RESALE, OR FOR INCORPORATING THEM INTO OBJECTS OR APPLICATIONS WHICH CUSTOMER
DESIGNS, ASSEMBLES, CONSTRUCTS OR MANUFACTURES.
This warranty can
be
modified
only
by authorized Gast personnel by signing a specific, written description
of
any
modifications.
MAINTENANCE
RECORD
DATE
PROCEDURE
PERFORMED

MI-290AG Rev. 4
20
PART
NO.
45-200
D170PL
(Rev.
D)
TROUBLESHOOTING
CHART
Problem
Low
Lo
w
Won
't
Run
Runs
Hot
T
or
qu
e
Spee
d
• • •
• • •
• • • •
• •
•
•
• • •
•
•
AUTHORIZED SERVICE FACILITIES
Gast Manufacturing Inc.
2550 Meadowbrook Road
Benton Harbor, MI 49022
TEL 616-926-
6171
FAX
: 616-927-0808
www.gastmfg.com
Wainbee Limited
215 Brunswick Blvd.
Poi
n
te
Claire, Quebec
Canada H9R 4R7
TEL 514-697-8810
FAX
51
+697
-3070
Gast Manufacturing Inc.
505 Washington Ave
Carlstadt, NJ 07072
TEL 201-933-8484
FAX
: 201-933-5545
Wa
inbee Limited
5789 Coopers Avenue
Mississauga, Onta
ri
o
Canada L4Z 3S6
TEL 905-568-1700
FAX
: 905-568-0083
Runs
Well
R
eas
on
&
Remedy
Then
S
lows
For
Problem.
Down
Dirt
or
foreign
mat
er
ial
present.
In
s
pe
ct
and
clean.
Int
e
rnal
rust.
In
sp
ec
t
and
cl
ea
n.
•
Va
ne
s
mi
sa
ligned
.
Realign
vanes
.
Low
air
pr
essu
re.
In
c
re
ase
pressure
.
Air
line
t
oo
s
mall
.
In
s
tall
larger
line
(s)
.
•
Re
s
tricted
exhaust.
Inspect
and
repair.
•
Motor
is
jammed.
Di
sasse
mble
and
repair
.
•
Air
so
ur
ce
inadequate
.
In
s
pe
ct a
nd
repa
ir.
•
Air
source
to
o
far
from
motor
.
Rec
on
fi
g
ure
se
tup
.
Brenner Fiedler & Assoc.
13824 Bentley Place
Cerrit
os,
CA
90701
Gast Manufacturing Co., Ltd
Beech House, Knaves Beech
Business Centre, Loudwater
TEL 800-843-5558
TEL: 310-404-2721
FAX
: 310-404-7975
Japan Machinery
Co
, Ltd
Cent
ral
PO
Box 1451
Tokyo, 100-91 Japan
TEL 81-3-3573-5421
FAX
81
-3-3571-7865
or 81-3-3571 -7896
High Wycombe, Bucks
HP
10
9SD
England
T
EL
: 44 628 532600
FAX
: 44 628 532470
General Correspondence
should be sent
to
Gast Mfg. Inc.IA Unit of IDEX Corporation
PO
Box
97
Benton Harbor, Ml 49023-0097
ISO 9001 & 14001 CERTIFIED www.gastmfg.com
A Unit
of
IKXCorporat
ion
This manual suits for next models
6
Table of contents
Popular Engine manuals by other brands
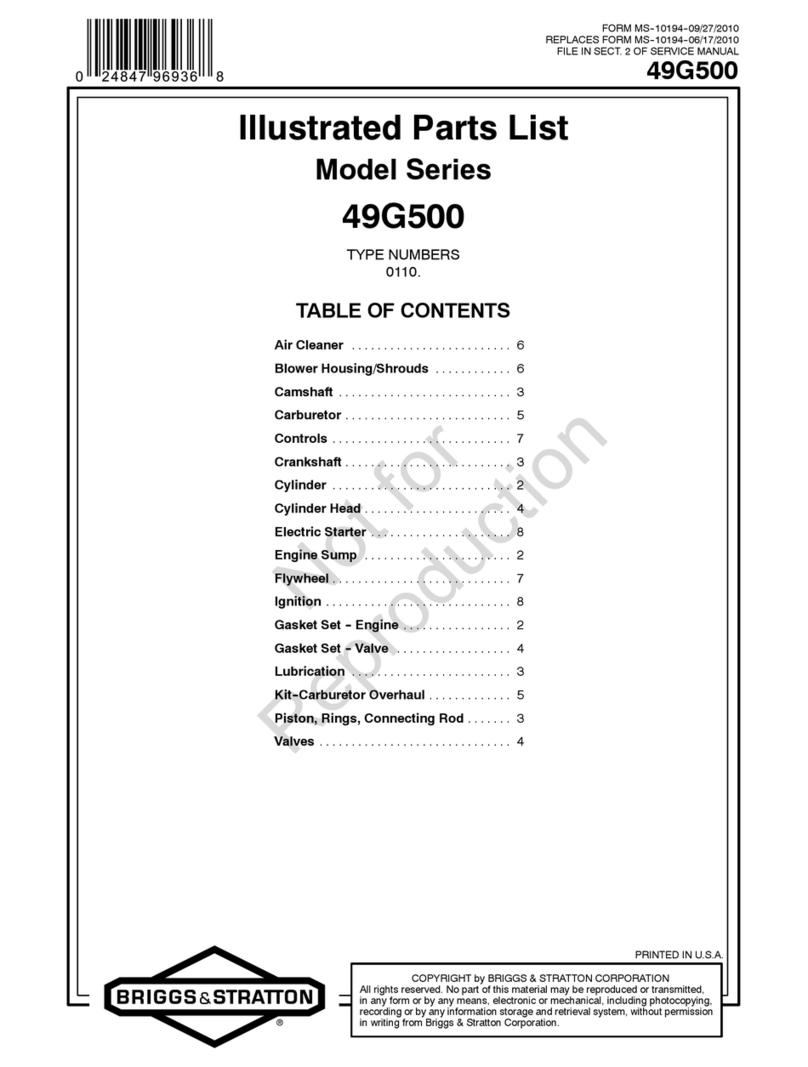
Briggs & Stratton
Briggs & Stratton 49G500 Series Illustrated parts list
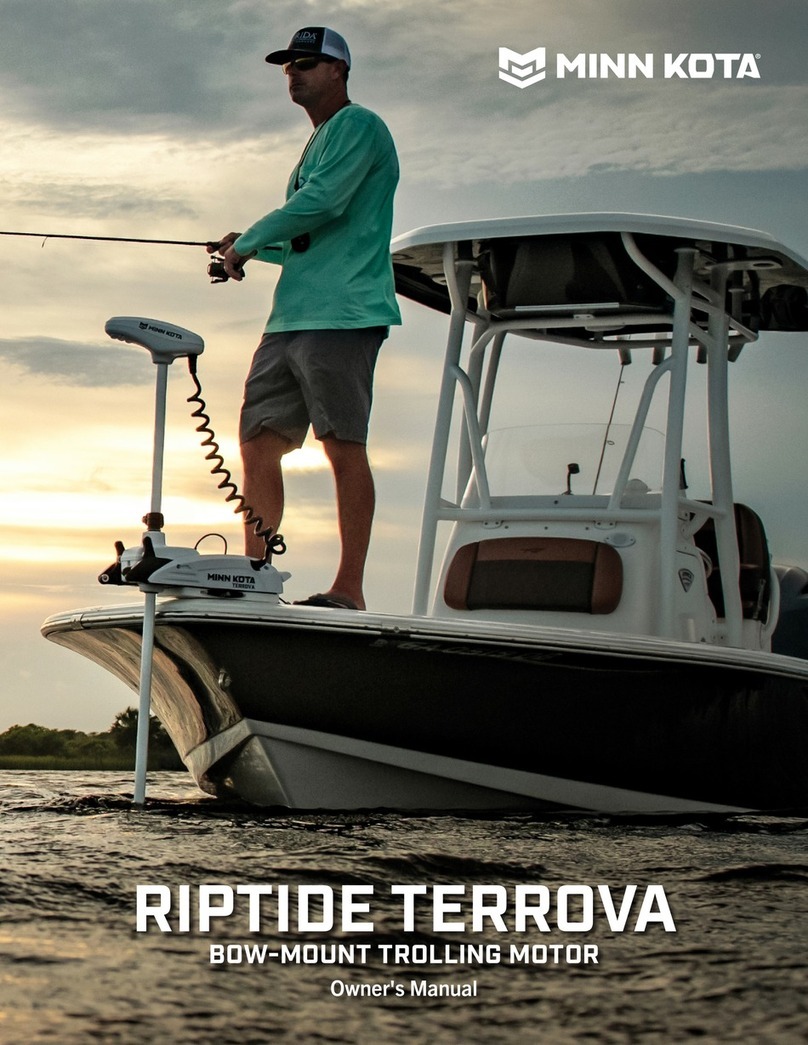
MINN KOTA
MINN KOTA RIPTIDE TERROVA owner's manual
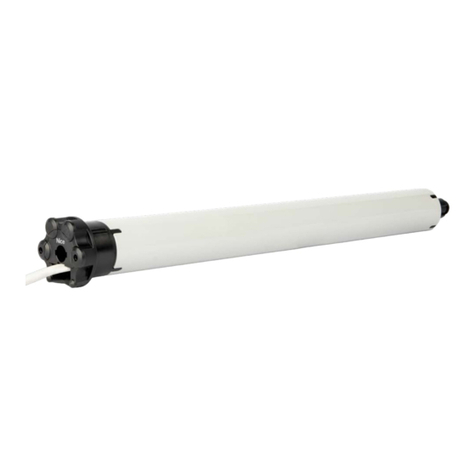
Nice
Nice NX FIT MZ 2017 SH BD Instructions and warnings for installation and use
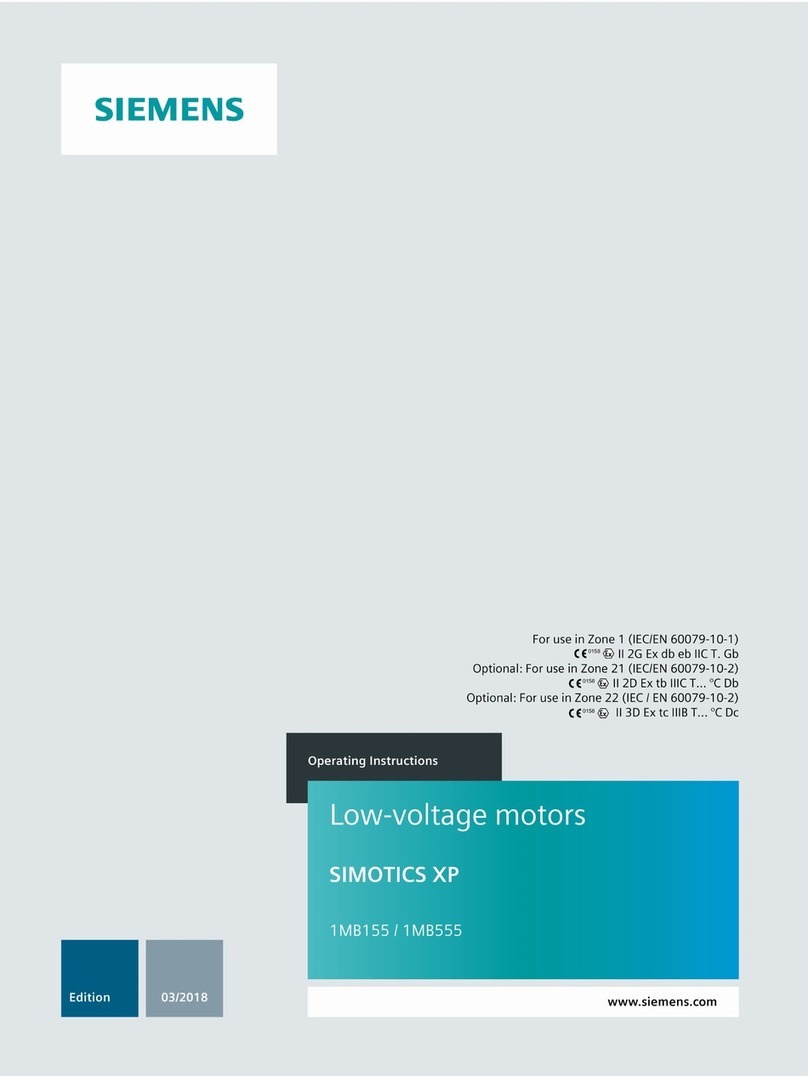
Siemens
Siemens SIMOTICS XP 1MB155 operating instructions
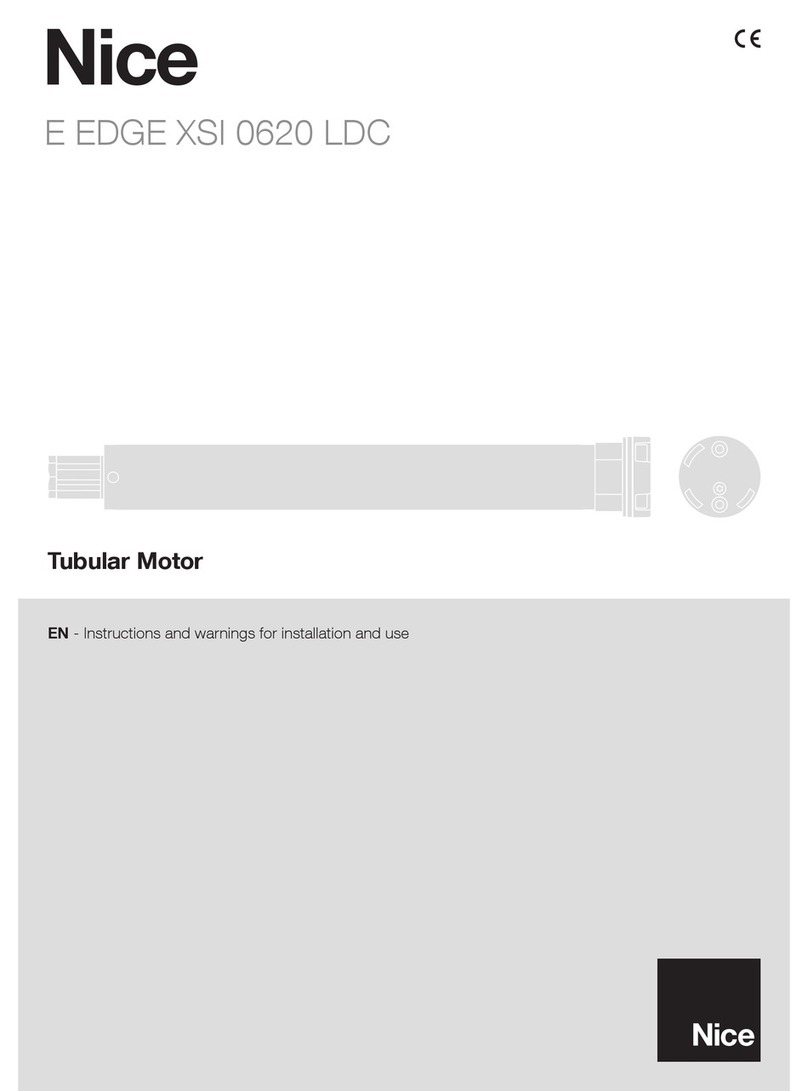
Nice
Nice E EDGE XSI 0620 LDC Instructions and warnings for installation and use
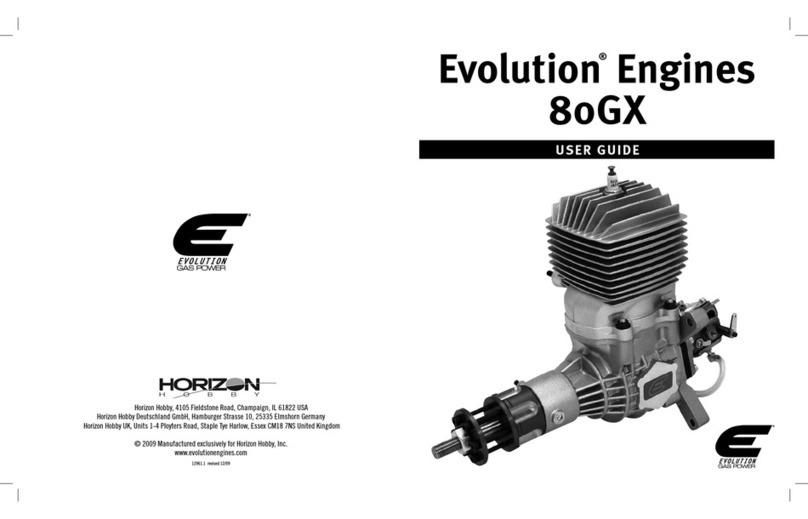
Evolution
Evolution 80GX user guide