Steamist HC-9 User manual

®
Owners Manual
Heavy Commercial Steambath Generator Models: HC-9 thru HC-24 with DCCP Control
05/13 Pub. No. 601-C
- 1 -
®

Table of Contents Models: HC-9 thru HC-24 with DCCP Control
05/13 Pub. No. 601-C
- 2 -
Table of Contents
I. Important Steam Bath Safety Guidelines.......................................................................
II. Warning Sign Installation................................................................................................
III. Pre-Installation................................................................................................................
IV. Rough-In.........................................................................................................................
V. Installation......................................................................................................................
VI. Digital Command Center Installation..............................................................................
VII. Digital Commercial Control Package Operation.............................................................
VIII. Limited Warranty.............................................................................................................
List of Illustrations
Warning Sign.............................................................................................................................
Figure 1 - Access Requirements (HC-9 thru HC-24).................................................................
Figure 2 - Dimensional Drawing for HC Steam Generator........................................................
Figure 3 - Typical Steam Generator Installation........................................................................
Figure 4 - Overview of Generator............................................................................................
Figure 5 - Sensor Installation.....................................................................................................
Figure 6 - Cables.......................................................................................................................
Figure 7 - Circuit Board Connections.........................................................................................
Figure 8 - Manager and User Controls......................................................................................
Programming Examples............................................................................................................
Specifications Chart..................................................................................................................
Figure 9 - Wiring Diagram.........................................................................................................
Figure 10 - Steam head Repositioning......................................................................................
Figure 11 - Steam head Installation...........................................................................................
Figure 12 - Optional Steam Deflector........................................................................................
Page
3
3
5
6
7
8
9
16
Page
3
4
4
5
6
8
9
9
10
11
13
14
15
15
15

Owners Manual
05/13 Pub. No. 601-C
Important Steam Bath Safety Guidelines
- 3 -
Models: HC-9 thru HC-24 with DCCP Control
I. Important Steam Bath Safety Guidelines:
A) Do not permit children to use the steam bath unless they
are closely supervised at all times.
B) Wet surfaces of the steam enclosures may be slippery.
The floor should be skid resistant. Bathers should use
care when entering and leaving.
C) The steam head is hot. Bathers should not touch the
steam head and avoid contact with steam near the steam
head.
D) Prolonged use of the steam bath can excessively raise
the internal human body temperature and impair the
body’s ability to regulate its internal temperature
(hyperthermia). Limit the use of steam to 10 – 15 minutes
until you are certain of your body’s reaction.
E) Excessive temperatures have a high potential for causing
fetal damage during the early months of pregnancy.
Pregnant or possibly pregnant women should consult a
physician regarding correct exposure. Obese persons and
persons with a history of heart disease, low or high blood
pressure, circulatory system problems, or diabetes should
consult a physician before using the steam bath.
F) Persons using medication should consult a physician
before using a steam bath since some medication may
induce drowsiness while other medications may affect
heart rate, blood pressure and circulation.
G) The Facility manager should fully understand the causes,
symptoms, and effects of hyperthermia which may be
described as follows: Hyperthermia occurs when the
internal temperature of the body reaches a level several
degrees above the normal body temperature of 98.6° F.
The symptoms of hyperthermia include an increase in the
internal temperature of the body, dizziness, lethargy,
drowsiness, and fainting. The effects of hyperthermia
include:
1) Failure to perceive heat.
2) Failure to recognize the need to exit the steam bath.
3) Physical inability to exit the steam bath.
4) Unawareness of impending risk.
5) Fetal damage in pregnant women.
6) Unconsciousness.
WARNING: The use of alcohol, drugs, or medication
can greatly increase the risk of hyperthermia.
II. Warning Sign Installation:
The warning sign shown below and provided with the genera-
tor MUST be permanently installed on the steam room door or
the wall immediately adjacent to the steam room.
!
WARNING
1. EXIT IMMEDIATELY IF UNCOMFORTABLE, DIZZY, OR SLEEPY. STAYING TOO LONG IN A
HEATED AREA IS CAPABLE OF CAUSING OVERHEATING.
2. SUPERVISE CHILDREN AT ALL TIMES.
3. CHECK WITH DOCTOR BEFORE USE IF PREGNANT, DIABETIC, IN POOR HEALTH, OR
UNDER MEDICAL CARE.
4. BREATHING HEATED AIR IN CONJUNCTION WITH CONSUMPTION OF ALCOHOL, DRUGS,
OR MEDICATION IS CAPABLE OF CAUSING UNCONSIOUSNESS.
5. DO NOT CONTACT STEAM HEAD OR STEAM AT THE STEAM HEAD.
REDUCE THE RISK OF OVERHEATING AND SCALDING
REDUCE THE RISK OF SLIPPING AND FALL INJURY
1. USE CARE WHEN ENTERING OR EXITING THE STEAM ROOM, FLOOR MAY BE SLIPPERY.
NOTE: FOR ADDITIONAL SAFETY CONSIDERATIONS SEE OWNERS MANUAL.
!

30"
40"
36"
RD
Command Module
AROMA 1
AROMA 2
WATER
STEAM 1
STEAM 2
HEATER
DRAIN
CR2032
1
12VAC GND
USER 2 USER 1MGR CTL
SENSOR 1 SENSOR 2
XLOW HIGH
AROMA 1 AROMA2
80 100
120
140
60
40
20
0
psi
Water Solenoid,
Valve ¼"
Water Inlet,
Strainer
½" NPT
Auxiliary
Manual Reset
Pressure Cutoff
Drain Outlet
Operating
Pressure
Control
Pressure
Gage
F
U
S
E
F
U
S
E
Steam Outlet #1
¾" NPT
15psi
Safety Valve
¾" NPT Outlet
Sight
Glass
Assembly
17"
5½"
21" 12½"
CONTROL POWER
STEAM 2
STEAM 1
24KW
208V
ASME
Data Plate
19"
6⅜"
2⅜"
Steam Valves may be
rotated by loosening
this union
Power Switch
Steam Solenoid
Switches (Shown
with optional 2nd
control package)
Heater
Access
ASME Plate
Located Inside
1" Manual Drain
Valve
1" Optional Auto
Blowdown Valve
Control Access
Access
Shown with optional
2nd control package
Steam Outlet #2
¾" NPT
05/13 Pub. No. 601-C
- 4 -
Figure 2 - Dimensional Drawing for Heavy Commercial Steam Generator (HC-9 thru HC-24)
Figure 1 - Access Requirements Models: HC-9 thru HC-24 with DCCP Control
Owners Manual

18"
Water Line, ½" NPT - Run from a
cold water pipe. Provide a local
shut-off valve.
Motorized Drain Valve (Optional)
- Use a 1" pipe routed to an
indirect waste line to be used for
the drain or blowdown tank.
Safety Relief Valve, ¾" NPT -
Connect to indirect waste or as
required by local codes
Commercial HC Stand
(Optional)
Inside Steam Room
Temperature Sensor - Single tier seating 6
feet above floor or Double tier seating 7
feet from the floor
Digital Command Center -
Cable supplied is 50’ in length.
100’ cable is available by special
order. Maximum functional cable
length is 100 feet. User Bypass Control -
Cable supplied is 50’ in
length. 100’ cable is
available by special order.
Maximum functional cable
length is 100 feet.
Steam Outlet,
¾" NPT
Utility Room Steam Room
Steam Line,
¾" Copper
Outside Steam Room
Inside Steam Room
05/13 Pub. No. 601-C
- 5 -
Figure 3 - Typical Steam Generator Installation
CONTROL POWER
STEAM 2
STEAM 1
24KW
208V
ASME
Data Plate
Owners Manual
Pre-Installation Models: HC-9 thru HC-24 with DCCP Control
The Heavy Commercial steam generator (HC-9 thru HC-24)
comes from the factory assembled, carefully wired, and tested.
Please read all instructions before installing or servicing.
IMPORTANT:
1. All Plumbing and Electrical work must conform to
local and national codes.
2. All power must be OFF to the steam generator when
installing or servicing the unit.
3. Do not use or install unauthorized components,
accessories or products on the generator or its'
piping.
III. Pre-Installation:
The following general information should be used in conjunc-
tion with your architect, designer and contractor in providing a
suitable and safe steam room environment for the steam
bathers.
IMPORTANT: Refer to the specification plate affixed to
the cabinet of the steam bath generator.
A) Insure that the model steam generator unit purchased is
sized adequately for your steam room.
B) Be sure to have the proper electrical supply. Determine
proper size of wire, voltage, amperage, and phase for the
steam generator based on the specification plate attached
to the generator and the chart in the back of this manual.
C) Provide an inline fuse/circuit breaker as required sized in
accordance with specification chart. Do not install a GFI
Ground Fault Interrupter to this equipment.
D) Select a location to install the generator to allow sufficient
room (See Access Area Requirements) for access to the
unit in the event service is required. Select a clean dry
indoor location protected from freezing. Do not store
flammable materials such as gasoline, thinners, paints,
etc. in the same area as the steam generator. Do not
store corrosive materials such as chlorine near the steam
generator.
E) Location of the steam generator should be placed where
the ambient temperature range is: 40ºF to 104ºF.
E) For safe low temperature draining (blow down) of the
steam generator it may be necessary to drain into an
ASME blow down tank. If required additional space for the
tank will be necessary. Consult with your architect or
licensed plumber. The blow down process can potentially
dump boiling water down the drain and damage the
drainage system.
F) The steam generator should be located as close as
possible to the steam room. If the steam generator is
more than ten feet from the steam head, insulate the
steam pipe with appropriate pipe insulation rated for a
minimum of 250ºF.
G) The serial number plate should be visible when installed.
H) The steam room must be completely sealed on all sides,
top and bottom. Floor, walls, and ceiling should be
completely covered with waterproof material such as tile.
Floor and bench materials must be slip resistant (see
Safety Guidelines).
I) Provide a floor drain inside the steam room for condensate
run-off and steam room cleaning.
J) Only water tight lighting fixtures approved for the applica-
tion should be used.
!
!

L1 L2 L3
Optional Steam
Solenoid #2
Steam
Solenoid #1
Water
Level
Probes
Reset
Button
Limit
Control
Power
(See Specification Chart)
Aroma
Power Light
Aroma
Fuse
Heater
Contactor(s)
1 AMP
Control Fuses
Pressure
Control
Loosen union to rotate
solenoids to the optimal
installation position
Safety Relief
Valve
Aroma Power
connection 15
AMP 120V
H N G GND
High
XLow
05/13 Pub. No. 601-C
- 6 -
Figure 4 - Top of Generator
Owners Manual
Rough-In
IV. Rough-In:
A) Plumbing Rough-In:
The heavy Commercial “HC” Steam Generator requires
the following connections: 1/2" NPT piping for the water
inlet, 3/4" copper tubing for each steam outlet, and 3/4"
NPT safety valve should be piped to an indirect waste
line. A 1” drain line for an optional auto blow down
assembly must be piped to an indirect waste.
IMPORTANT: The Optional Auto Blow Down feature
can dump a few gallons of boiling water down the drain
and potentially damage the plumbing. It may be
necessary to drain into an ASME Blowdown Tank
(Available as an option from Steamist) depending on
the requirements of plumbing system and local codes.
1) Rough-in a ½" water line from a cold water supply.
Provide a local shut-off valve.
2) Rough-in the steam line using 3/4" copper tubing. Do
NOT use iron or galvanized pipe, it will rust and
discolor wall of steam room. For a steam line that is
longer than 10 feet use an appropriate pipe insula-
tion rated for a minimum of 250ºF. The steam head
should be located approximately 18" above the floor
and as far from the bather as possible. Do NOT
install shut-off valves in this line. Do NOT create
traps or valleys in this line which would trap conden-
sation and block the flow of steam.
3) Rough-in a 1” drain line for a manual drain or an
optional auto blow down assembly and provide for
an indirect waste, to be used for draining steam
generator.The indirect drain must be in accordance
with local plumbing codes.
4) Rough-in a drain line using ¾" pipe routed to an
indirect waste from the Safety Relief valve. The
discharge end of this pipe must NOT be restricted in
any way. It must be piped in a way that would safely
discharge steam and/or boiling water in the event of
a failure. Always follow local plumbing codes.
B) Electrical Rough-in:
1) Route power supply cable to the location where the
steam generator will be installed.
2) Route control cables as described in the Digital
Command Center.
Models: HC-9 thru HC-24 with DCCP Control
!

05/13 Pub. No. 601-C
- 7 -
Owners Manual
Rough-In / Installation Models: HC-9 thru HC-24 with DCCP Control
C) Digital Commercial Control Package rough- in:
The DCCP is factory wired for either one or two steam
rooms. The following installation instructions are typical
for both room installations. IMPORTANT: The command
center cable, USER BYPASS CONTROL cable and
sensor cable are not the same and must not be confused.
1) Digital Command Center rough-in: Route the command
center cable from the generator to the selected dry mounting
location convenient to the facility operator.
IMPORTANT: the cable is 50’ long. 100’ cable is
available by special order. Maximum functional cable
length is 100 feet.
2) USER BYPASS CONTROL: Route the USER
BYPASS CONTROL cable from the generator to the
selected area outside of the steam room.
3) Room Temperature Sensor: Route the temperature
sensor cable from the generator to the selected
location inside the steam room. For sensor installa-
tion and location, see Figure 3. Make sure the
generator end is located near the generator mount-
ing location and the sensor end is located near the
sensor mounting location. Important: the cable is 50’
long. 100’ cables are available by special order.
Maximum functional cable length is 100 feet.
V. INSTALLATION
A) Plumbing Installation: Care must be taken when installing
the steam generator. Leave proper access for servicing
(See Installation Area Requirements). (Refer to Figure 3
for typical steam generator installation.) CAUTION: The
steam generator is designed to be used ONLY in an
upright and level position; to do otherwise would damage
the unit and void the warranty. For convenient access
mount the steam generator on the optional Steamist
stand designed specifically for the steam generator.
1) Water supply: Purge the water supply line before
connecting to the steam generator. In areas where
high water pressure may be a problem a water
hammer arrestor should be installed.
2) Steam line: Connect the steam line from the previ-
ously roughed-in location to the steam solenoid
valve on the generator marked “steam outlet.” If the
generator is equipped to provide steam to two rooms
care must be taken to make sure the proper steam
solenoid is piped to the proper room.
3) Safety Line: Connect the 3/4" NPT safety valve into
the previously installed indirect waste line.
4) Optional automatic blow down: Pipe into the 1"
indirect waste line.
5) For steam head installation (see Page 15).
6) The steam, safety, and drain pipes become hot
during operation and should be insulated with
appropriate rated pipe insulation to protect against
accidental contact.
B) Electrical Installation: WARNING ALL POWER TO THE
STEAM GENERATOR MUST BE TURNED OFF.
1) Remove the top access cover to the electrical power
compartment . (See Figure 4.)
2) Locate appropriate knockout and mount a proper
strain relief into knockout hole.
3) Strip back the power cable’s outer insulation jacket
and insert into the box. Strip back insulation 3/4"
from the incoming wires: single phase (two power
and one ground). 3 phase (three power and one
ground).
4) Insert ground wire into grounding lug.
CAUTION: Make sure ground wire does not come in
contact with live electrical connections.
5) Locate power block and insert power wires into
proper power lug terminals on top of the block and
secure.
C) Aroma Pump Option: The aroma pump requires a
separate 15 amp 120 volt branch circuit to be connected
(see Figure 4). This is only necessary to run the aroma
pump and is not needed if the pump is not used. To
connect the power, remove the top cover of the generator.
Select the knock out to route the 15 amp 120 volt line into
the box. Connect the neutral, hot, and ground to the
terminal block. Replace the cover. Plug in the pump into
the appropriate receptacle depending on which room the
pump is connected to.
NOTE: The pump will only pump when the appropriate
room control is in the MAX mode, the ambient room
temperature of that room is above the IDLE setting and
the steam valve for that room is on. This feature
reduces oil consumption by limiting the pumping to the
max mode only. Maximum economy of oil consumption
can be realized by programming the DCCP to remain in
idle mode throughout the day. If programmed this way
the oil will only be dispensed when a steam bather
presses the button on the user control outside the
steam room switching the steam bath to MAX mode for
a preset time defined by the manager (recommended
setting is 10 minutes). Programmed this way the oil is
only pumped on the demand from the user and is a
substantial cost savings (See Operating Instructions
page 9).
!
!
!

EN
OC
I
L
I
S
R
A
E
L
C
.
Z
O
.
L
F
2
/
1
t
e
N
0
2
5
1
3
.
o
N
m
e
t
I
.
A
.
S
.
U
N
I
E
D
A
M
NOTE: Location of the sensor is as follows:
a) Single tier seating - 6 feet above floor.
b) Double tier seating - 7 feet above floor.
No. 8 Plastic
anchors
5/8” Hole
Cable to
Steam Generator
Temperature
Sensor and Housing
(Shipped Assembled)
No. 8 Screws
1” Long
2
3
4
5
STEPS TO INSTALL SENSOR:
1) Take new sensor assembly and connect to 50’
sensor cable. Please observe polarity of the 50’ cable.
Make sure the male end of the cable is routed toward
the sensor in the steam room.
2) Peel off adhesive backing from sensor.
3) Carefully apply silicone sealant around rear edge.
4) Feed wires back into wall and press sensor firmly to
wall (be careful to align plate holes with anchor holes).
5) Install screws, and snap chrome cover back into
place.
6) Temperature sensor assembly must form a 100%
water tight seal to the wall using silicone supplied.
1
50 Foot Sensor Cable
Male end
50’ sensor cable
Male end
05/13 Pub. No. 601-C
- 8 -
Figure 5 - Sensor Installation - Inside Steamroom
Owners Manual
Digital Command Center Installation Models: HC-9 thru HC-24 with DCCP Control
VI. Digital Command Center Installation:
WARNING: All the electrical power to the steam
generator MUST be turned OFF before proceeding with
installation.
A) The DCCP comes factory wired for either one or two
steam rooms. The following installation instructions are
typical for both room installations. The configuration for
one or two room is set at the factory. When the generator
is configured for two rooms (SRP-Second Room Package
must be ordered) it will have 2 room temperature sensors
(one per room), two electric steam valves, two USER
BYPASS CONTROLs, and two steam heads. The electric
steam valves will be labeled 1 and 2. The connections for
the sensors, USER BYPASS CONTROL(s), and aroma
pumps, will all be labeled for room 1 and room 2. It is very
important to pay attention not get the connection to room
1 and room 2 crossed. If the generator is configured for
one room there will not be any special markings.
B) USER BYPASS CONTROL(s): The USER BYPASS
CONTROL should be located outside the steam room
door convenient to the bather. This control gives the
bather limited control of the steam room. The system will
operate without this control but this function is lost. See
the operating instructions for further information on this
function. Route the USER BYPASS CONTROL wire from
the selected mounting area to the control board in the
steam generator (see Figue 6 and 7). The USER
BYPASS CONTROL mounts to 2-1/8” or 55 mm round
hole in the wall.
C) DIGITAL COMMAND CENTER is intended to be used
solely by the manager. It should be located at a conve-
nient height for programming. It may be mounted on the
wall of the utility room near the steam generator, in the
manager’s office, or the front desk. The factory supplied
wire is 50 feet long, therefore the generator must be
located within its reach.
IMPORTANT: The digital command center is unique
and not to be confused with the USER BYPASS
CONTROL wires or the sensor wires. The Digital
Command Center uses a 4 wire connector, the USER
BYPASS CONTROL uses a 6 wire connector and the
room sensor uses a 2 wire connector. Route the Digital
Commander Center wire from the selected mounting
location to the control board located in the steam
generator (see Figure 6 and 7). The Digital Command
Center mounts to a hole in the wall 2-1/2”w x 7-7/8”h.
D) Room Temperature Sensor(s): The room temperature
sensor is required for operation. The sensor must be
located in the steam room approximately six feet above
the floor and never closer than one foot to the ceiling or
the corner of the room. Route the cable from this location
to the control module on the steam generator. The sensor
mounts to a 5/8” hole in the wall (see Figure 5 for more
detail).
!
!

User Bypass Control
(User 1 & User 2)
Steam Room Sensor
(Room 1 & Room 2)
DCCP Control
05/13 Pub. No. 601-C
- 9 -
RD
Command Module
AROMA 1
AROMA 2
WATER
STEAM 1
STEAM 2
HEATER
DRAIN
CR2032
1
12VAC GND
USER 2 USER 1MGR CTL
SENSOR 1 SENSOR 2
XLOW HIGH
Figure 7 - Circuit Board Connections
User Bypass Control Cable
(6-pin Connector)
Digital Command Center Cable
(4-pin Connector)
Figure 6 - Cables
Owners Manual
Digital Commercial Control Package Operation Models: HC-9 thru HC-24 with DCCP Control
VII. Digital Commercial Control Package Operation:
This control is designed to maximize energy savings by
allowing the facility manager set a lower operation temperature
called IDLE TEMP and also satisfy the steam bather with the
ability to by-pass this feature on demand by pressing the
USER BYPASS CONTROL button. Unlike a typical 24 /7 timer
which has only an ON or OFF mode, the Digital Command
Center has three modes MAX, IDLE and OFF. MAX is the
normal ON mode reserved for peak hours of use when the
steam room is held at the optimum steam bath temperature.
IDLE mode is the energy saving mode. IDLE is set below the
MAX temperature and provides a significant energy savings.
As needed, the steam bather can easily switch to the MAX
setting by pressing the button on the USER BYPASS CON-
TROL.
A) USER BYPASS CONTROL: The USER BYPASS CON-
TROL button is only functional during the IDLE mode. In
the IDLE mode the USER BYPASS CONTROL, typically
mounted at the entrance to the steam room, is waiting for
the user to press the button and select the MAX mode.
IDLE mode is indicated on the USER BYPASS CON-
TROL by one lit bar. Pressing the USER BYPASS
CONTROL button starts the MAX CYCLE TIMER and
immediately begins to heat the room to the MAX setting.
This temporary MAX CYCLE TIMER is programmable up
to 60 minutes by the facility manager. MAX TEMP mode
is indicated by all bars lit. When the Digital Command
Center is set to MAX TEMP the USER BYPASS CON-
TROL icon displays max (all bars lit). In the MAX TEMP
mode the USER BYPASS CONTROL buttons do not
function. When the DIGITAL COMMAND CENTER is in
the OFF mode the USER BYPASS CONTROL icon will be
off (no bars lit) and the user buttons do not function.
B) Programming the DIGITAL COMMAND CENTER can be
broken down into 3 separate sections, SET EVENT, SET
VALUE, and SET CLOCK. The buttons on the control are
grouped accordingly. SET EVENT is used to set the time
and day that a particular mode (MAX, IDLE, or OFF) is to
begin. SET VALUE is intended to set the MAX and IDLE
temperature as well as the MAX CYCLE TIMER. The SET
CLOCK section is only for adjustment of the current time
and day. The DIGITAL COMMAND CENTER display light
comes on when any button is pressed. The light will
remain on for 5 minutes after the last button is pressed.
1) SET CLOCK: The SET CLOCK section of the Digital
Command Center is used exclusively for setting the
current time and day. It is a convenient place to
make changes for daylight savings time without
having to reprogram other settings. The clock has a
battery backup in the Control Module that will keep
time for up to one year with no power.
(a) DAY Setting: Press the lower DAY button to
toggle the current day of the week.
(b) HOUR Setting: Press the lower HOUR button to
select the current AM or PM hour and the
correct hour will be displayed.
(c) MINUTE setting: Press the Lower MINUTE
button until the correct minute is displayed.
2) SET VALUE: The SET VALUE section of the keypad
is used to program the following 4 parameters:
(a) MAX1 TEMP is used to set the maximum
desired operating temperature of the steam
bath. It is set by pressing the button until the
preferred maximum temperature is displayed.
Note: The MAX TEMP cannot be set lower than
the IDLE TEMP. Selection of the MAX TEMP
setting is at the discretion of the facility
manager.
(b) MAX2 TEMP (only available with SRP) is used
to set the desired operating temperature of a
second steam room. It is programmed the same
as MAX1 TEMP.
(c) IDLE TEMP is used to program a lower
temperature setting during periods of less
frequent usage. It is set by pressing the button
until the desired set-back temperature is
displayed. The feature can be disabled by
setting it to 00.The IDLE TEMP cannot be set
higher than the lowest MAX TEMP value.

Daily Program Number
Keypad lock
Clock
Max Temperature/Current
Temperature for Room 1
Idle Temp
24/7 Event Programming
buttons
Timer/Temperature setting
buttons
Lock Button
Time of day setting
Max/Idle/Off mode indicator
Day of the week indicator
AM/PM indicator
Max Temperature/Current
Temperature for Room 2
0-60 Minute Max Cycle Timer
05/13 Pub. No. 601-C
- 10 -
Figure 8 - Manager & User Control
User Idle/Max Display
Idle/Max Button
Owners Manual
Digital Commercial Control Package Operation Models: HC-9 thru HC-24 with DCCP Control
(d) MAX CYCLE TIMER is used to set the duration
that the system will be in MAX TEMP mode
after the USER BYPASS CONTROL button is
pressed in. It is set by pressing the correspond-
ing button on the Digital Command Center.
Each time the button is pressed the minutes will
increase in one minute increments from “:00” to
“:60”. If the MAX CYCLE TIMER is programmed
to “:00”, this feature will be disabled and the
USER BYPASS CONTROL(S) will be disabled.
(e) Degree °C or °F change is made by placing a
jumper over the CN112 pins for °C or by
removing it for °F (Jumper not included). The
power must be OFF when making this change.
See Command Module on Wiring Diagram
page 14.
3) SET EVENT: Before programming the SET
EVENT, it is necessary to determine the hours
the steam bath will operate and in which mode.
Each day of the week can have up to six events
programmed. The chart on the following page
will help organize your plan for the SET EVENT
function. The top 2 sections of the chart are
filled in with 2 examples
NOTE: Program #1 is set to 12:00am by default.
This time cannot be altered. You can however set
12:00am to: OFF, IDLE, or MAX.
®
®
!

05/13 Pub. No. 601-C
- 11 -
Owners Manual
Digital Commercial Control Package Operation
EXAMPLE 1 shows the club opening at 8AM. Assuming it is
not busy the first few hours so the mode is selected as IDLE.
Then at 10AM it gets busy and the program switches to MAX.
At 3PM it slows down again and the control switches back to
IDLE. Then at 7PM it gets busy again and switches to back to
MAX. At 10PM the club closes.
EXAMPLE 2 shows the club opening a 8AM and set to IDLE
all day until 10PM when the club closes. This would yield
maximum energy savings and is the recommended program.
At any time the system is in IDLE mode the user can activate
the MAX TEMP mode by pressing the USER BYPASS
CONTROL button.
Photo copy the chart and use it as a work sheet to plan you
settings:
Models: HC-9 thru HC-24 with DCCP Control
PROG # 123456
EXAMPLE 1
MAX
IDLE
OFF X
X
X
X
X
X
TIME 12:00AM 8:00AM 10:00AM 3:00PM 7:00PM 10:00PM
PROG # 1 23456
EXAMPLE 2
MAX
IDLE
OFF XX
TIME 12:00AM 8:00AM 10:00AM 3:00PM 7:00PM 10:00PM
TU
MAX
IDLE
MAX
IDLE
FR
OFF
OFF
TIME
SU
MAX
IDLE
OFF
MAX
OFF
TH
IDLE
MO
WE
SA
MAX
IDLE
OFF
PROG # 1 23456
TIME
TIME
TIME
TIME
TIME
TIME
MAX
IDLE
OFF
MAX
IDLE
OFF
X
Note: If the steam room is open 24 hours a day you may set Program #1 to MAX or IDLE and do not need to
set an OFF value unless you are turning it off to drain the system.
!

05/13 Pub. No. 601-C
- 12 -
Owners Manual
Digital Commercial Control Package Operation
4) Programming SET EVENT: To program the SET
EVENT section, first press the PROG# button on the
Digital Command Center. The display will flash the
current program number and show the start time of
that program. The program can only be changed
while flashing. To enter a new program, first press
the DAY button in the upper SET EVENT section to
choose the individual day or a block of days (i.e.
M-TU-W-TH-F, or SU-M-TU-W-TH-F-SA). With the
proper day(s) selected, press the MAX/IDLE/OFF
button to choose the mode for program 1.
Note: The time for program 1 is factory fixed to
12:00am, if the steam bath is to start at a later time,
Program 1 must be set to Off.
Program 1 is complete. Press PROG# button to get
to program 2. Enter the start time of program 2 and
select the mode. You are only programming the start
time of each program. The end time is automatically
the start time of the next program. The last program
entered is limited to 11:59PM. If the facility operates
beyond midnight, program 1 of the next day must be
set to 12:00 AM for continuous operation. Follow the
same process for all the programs and days of the
week. To exit the programming mode, press the
ENTER button or wait 30 seconds and it will stop
blinking and your changes will be saved.
Note: Programs 1 through 6 are sequential and
therefore it will not be possible to set a new program
before the end of the previous program.
(a) Programming Tip: To modify an existing
program press the PROG# button and the
upper DAY button to get to highlight the
program you want to change. Then modify the
setting with the appropriate button. Entries will
be saved automatically in 30 seconds or by
pressing the enter button.
(b) Programming Tip: If the facility operates on
nearly the same schedule every day, it may be
easier to program all seven days to the same
common program and then go back and
program Sunday to be off if the facility is closed
that day.
(c) Programming Tip: You can review your program
by pressing the PROG# button and toggling
through the programs and toggling through the
days of the weeks, and observing the time
settings. If you made no changes simply press
the enter button to return to normal or it will
return in 30 seconds.
(d) Programming Tip: When reviewing the program
and a block of days are selected, if all the
individual programs for those days do not
match, the clock will display --:--. This is normal
and any adjustments made at this time will
reprogram all days selected to match the new
entry.
5) Manager lock function: The Digital Command Center
has a locking feature that prevents any setting to be
changed when locked. To lock the control, press the
lock button, the lock icon will flash for up to 30
seconds. While the icon is flashing, press any three
consecutive buttons, and then press the lock button
again to confirm. The three consecutive buttons
pressed are the password. The system control will
be locked and the lock icon will be on steady. To
unlock, press the lock button and then press the
same three consecutive buttons as the previous
password, the system will be unlocked and the lock
icon will disappear. If the password is lost or forgot-
ten, it can be reset. This will require two people. Turn
off the main power (circuit breaker), have a second
person then press and hold the lock button on the
Digital Command Center while the first person turns
the power back on. The system will be unlocked.
Also see the reset section for an alternate method
(step 11).
6) Temporary Mode setting: By pressing
IDLE/MAX/OFF button on the Digital Command
Center you can temporarily change the current mode
(IDLE/MAX/OFF). This is only a temporary change
until the next programmed event.
7) Auto-Blow Down: The optional auto-blow down
becomes active in the OFF mode. When first
entering OFF mode, the steam valves will deactivate
and the generator will continue to maintain normal
pressure. After 5 minutes the generator will shut
down and the drain will open. Boiling water will exit
under pressure and the water valve will turn on to
help flush the generator. After 2 minutes the drain
will close and the generator will refill. After a total of
7 minutes the generator is ready to start a new cycle.
If the facility is operated 24 hours a day, a 7 minute
OFF mode should be programmed in to allow for a
proper drain cycle. In areas where the water is hard,
a second drain cycle can be programmed by adding
an extra 7 minute off mode program.
Models: HC-9 thru HC-24 with DCCP Control
!
!

05/13 Pub. No. 601-C
- 13 -
Owners Manual
Digital Commercial Control Package Operation Models: HC-9 thru HC-24 with DCCP Control
minute OFF mode during an “Off-Peak” daytime
period. IMPORTANT: Due to possible code violations
or damage to the building drainage system the hot
boiling water exiting in this process may require a
Blow-Down Tank. Consult with your licensed
contractor. Blow-Down tanks may be purchased
separately.
8) Steam Control: The steam valve(s) are controlled
according to the room temperature sensor(s) and the
programmed mode. When the room temperature is
lower than the set temperature by one degree the
steam valve will turn on. When it reaches the set
temperature it turns off. If for some reason the room
temperature exceeds the MAX TEMP setting (of
either room) by more than 10 degrees the Digital
Command Center will turn off the generator until that
room temperature drops to 1 degree below the set
temperature.
9) Aroma Control: There are two aroma control relays
(one for each room) located in the Command Module
on the generator. These relays can be used with
most aroma pumps available. The relays are
programmed to conserve aroma therapy oil. The
relays are only on when the following conditions are
met. The program for that room must be in the MAX
mode, the steam valve for that room must be on and
the temperature in that room must be above the IDLE
setting. When all these conditions are met, then the
aroma relays will energize.
10) Fahrenheit and Celsius: The Fahrenheit or Celsius
temperature can be selected by changing a jumper in
the Command Module (CN112). When it is not
connected (open circuit), it will be Fahrenheit. When it
is connected, it will be Celsius. The Jumper must be
switched with power off (See wiring diagram on page
11).
11) Reset Feature: If it is ever necessary to reset all the
programs and start over press and hold the PROG#
button and the lower MIN button for five seconds
simultaneously. This will reset every setting in the
Command Center. This process can also be used to
unlock the control if the password is lost or forgotten.
Model
No.
Product
No. KW
Volts/
Phase/
Amps
Shipping
Weight
HC-9
HC-12
HC-15
HC-18
Specications Chart
60900
60901
60902
60903
60904
61200
61201
61202
61203
61204
61500
61501
61502
61503
61504
61800
61801
61802
61803
61804
62400
62401
62402
62403
62404
9
12
15
18
24
Max.
Cu. Ft.
400
500
620
740
1000
240/1/38
208/1/43
240/3/22
208/3/25
480/3/11
240/1/50
208/1/58
240/3/29
208/3/33
480/3/15
240/1/63
208/1/72
240/3/36
208/3/42
480/3/18
240/1/75
208/1/87
240/3/43
208/3/50
480/3/22
240/1/100
208/1/115
240/3/58
208/3/67
480/3/29
Water
Inlet
Steam
Outlet
Dimensions
21”x19”x25”
21”x19”x25”
21”x19”x25”
21”x19”x25”
21”x19”x25”
140 lbs.
150 lbs.
150 lbs.
150 lbs.
150 lbs.
1/2” NPT
1/2” NPT
1/2” NPT
1/2” NPT
1/2” NPT
3/4” NPT
3/4” NPT
3/4” NPT
3/4” NPT
3/4” NPT
Line
Fuse
50
60
30
35
15
70
80
40
45
20
80
90
45
60
25
100
110
60
70
30
125
150
80
90
40
HC-24

50’ Cable
50’ Cable
Digital
Command
Center
Optional User
Bypass
Control 2
User
Bypass
Control 1
Room
Sensor 1
Room
Sensor 2
Transformer
For 480V Units
12 VAC Class 2
Transformer
Control
Fuses
1
2
50’ Cable
50’ Cable
50’ Cable
COIL COIL
L1
L3
L2
T2
T1
T3
Incoming Power Supply
208-240-480V
BL
RD
BK
Contactor Contactor
L1
L3
L2
T2
T1
T3
L1 L2 L3 G
F2
F1
Pressure
Control
Pressure
Limit
Control
TANK
Power
Switch
Temp Probe
Optional
High
Limit
Steam
Solenoid
Valve 1
Optional
Steam
Solenoid
Valve 2
Water
Solenoid
Auto Drain
Steam
Switch 2
Steam
Switch 1
M
G 120VN
15AMP
Branch
Circuit
Aroma
Light
Note: All factory wires are 18AWG unless
otherwise noted. Power and heater wire
gauge are set by the factory.
*Note: CN112 Jumper open: Fº Jumper 2
to 3: Cº Turn off power to make this change
reset.
*CN112
F3
Light
Note: Select
BL for 240V
RD for 208V
BK
RD
BN
BL
VT
VT
PROBE
14WT
12GN
14YL
14BN
RD
GY
WT
12GN
OR
OR
YL
YL
RD
BKBK
BK
RD
OR
CLOCK
BATTERY
OR
RELAY LIGHTS
Steam1 & 2
Aroma 1 & 2
Heater
Drain & Water
Yellow
Green
Red
Blue
Command Module
AROMA 1
AROMA 2
WATER
STEAM 1
STEAM 2
HEATER
DRAIN
CR2032
1
14BK
12VAC GND
USER 2 USER 1MGR CTL
SENSOR 1 SENSOR 2
XLOW HIGH
YL
YL
OR
BK
Pub. No. 601-C
- 14 -
Owners Manual
Figure 9 - "HC" Wiring Diagram with Options
05/13

05/13 Pub. No. 601-C
- 15 -
¼" to ½"
¾" NPT (Brass Pipe)
Must use sealant tape.
Apply silicone around
the steam pipe to form
a watertight seal.
Head assembly
(Cover plate & hub)
Back
Plate
Apply Silicone to
the back edge of
the Back Plate
Wrap the threads
of the nipple with
pipe sealant tape.
Aroma
Well
120°
120°
Head assembly
(Cover plate & hub)
Center Hub
Aroma
Well
If repositioning is necessary remove
3 screws and rotate 120
If needed to improve bather comfort the included optional
steam deflector can be installed to block the flow of
steam from any of the shown sides of the steam head.
Head Assembly
Back View
Deflector Plate
7. Center and square the back plate over the nipple. While
holding it in place screw the head on to the nipple hand
tight.
8. Adjust the back plate and head to line up squarely.
Remove any excess silicone with rubbing alcohol.
NOTE: The steam head has been designed with a 360
degree dispersion of steam to improve circulation and
to minimize the hotspots created with the traditional
steam heads. For maximum comfort the steam head
should always be located as far from the seating area
as possible. Should the location of the steam head
necessitate blocking the steam from a particular
direction to improve bather comfort, the supplied
deflector plate can be added to any of the three sides
shown to help divert the steam away from the bather.
The deflector is attached to the back side of the head
before installation with 2 stainless steel screws
provided.
1. Make sure the 3/4” nipple protrudes beyond the tile ¼" to
½".
IMPORTANT: If the nipple protrudes beyond ½” the O-ring will
not make a proper seal and the nipple will have be adjusted.
2. Wrap the threads of the nipple with pipe sealant tape.
3. Make sure the head will line up in the upright position when
tightened. The head should only be firmly hand tight. Using a
wrench on the head may damage it. Screw the head on to the
nipple and see how it lines up. Once a proper alignment is
made remove the head.
NOTE: If necessary the head can be repositioned by disas-
sembling the hub from the cover and selecting one of the two
alternate positions as shown in figure 1.
4. Re-apply sealant tape if necessary.
5. Place a bead of silicone around the pipe, sealing the pipe to
the wall.
6. Place a bead of silicone around the back outer edge of the
back plate.
3199 Steamhead Installation Instructions Models: HC-9 thru HC-24 with DCCP Control
Figure 10
Figure 11 Figure 12 - Optional Deector
!

LIMITED WARRANTY
STEAMIST, INC. hereby warrants that its Steamist generators Models HC-9, HC-12, HC-15, HC-18, and HC-24 are free from all
defects in workmanship and materials for one (1) year from the date of purchase.
This warranty does not extend to damage caused by improper or negligent installation or use, or for any repairs attempted by
any person other than an authorized Steamist dealer and shall be limited to the repair or replacement of defective parts by
STEAMIST or its authorized dealers. After the unit has been disconnected and returned to STEAMIST's plant or to one of its
authorized dealers warehouses, said repairs shall be without charge if within ninety (90) days of the date of purchase. After the
expiration of ninety (90) days for the duration of the limited warranty period, there shall be a reasonable charge for labor incurred
in connection with the repair or replacement indicated above.
Freight: Within the first ninety (90) days and with prior company approval, Steamist will pay all freight charges on items covered
under our warranty. Thereafter and until the end of the warranty period, and with prior company approval, the customer is
required to ship freight prepaid to Steamist's factory and Steamist will then ship freight prepaid back to customer.
This is not a service contract and this warranty does no include regular maintenance, cleaning or periodic check-ups, which are
the sole and exclusive responsibility of the purchaser and are required as a condition of keeping this limited warranty in full force
and effect.
This warranty shall not become effective unless the attached registration of Warranty is completed and returned to STEAMIST
within fifteen (15) days of the date of installation.
This warranty is non-transferable and shall extend only to the original purchaser who shall have been named in the Registration
of Warranty.
This warranty is void if any of the following should occur:
1. If the serial number has been altered or removed.
2. If the product is modified in any manner which STEAMIST concludes after inspection affects the reliability of the
product.
3. If the product has been repaired or serviced by anyone not specifically designated and authorized by STEAMIST.
4. If the product is damaged because it is not operated or installed in accordance with supplied instructions.
The sole responsibility of STEAMIST under this warranty shall be limited to the repair of the product or replacement thereof,
including parts, in the sole discretion of STEAMIST INC. The consumer's sole remedy shall be such repair of replacement as is
expressly provided herein and under no circumstances shall STEAMIST be liable for any loss or damage be it direct or conse-
quential arising out of the use or inability to use this product.
THE FOREGOING IS IN LIEU OF ALL OTHER WARRANTIES AND SPECIFICALLY EXCLUDES AND DISCLAIMS
EXPRESS AND IMPLIED WARRANTIES OF MERCHANTABILITY OR OF FITNESS FOR PARTICULAR USE OF
PURPOSE. THERE ARE NO WARRANTIES WHICH EXTEND BEYOND THE DESCRIPTION ON THE FACE HEREOF
AND NEITHER STEAMIST NOR ITS DEALERS ASSUMES OR AUTHORIZES ANY PERSON TO ASSUME FOR ANY
OF THEM ANY OTHER OBLIGATION OR LIABILITY IN CONNECTION WITH SAID EQUIPMENT.
No warranty whether express or implied is given or made with respect to any accessory supplied by anyone other than
STEAMIST.
Purchaser acknowledges that no other representations were made to him or relied on by him with respect to the quality and
function of the generators.
Model No. ____________________ Serial No. ____________________ Date of Purchase ____________________
05/13 Pub. No. 601-C
- 16 -
Owners Manual
East Coast Office: 25 E. Union Ave., East Rutherford, NJ 07073 • Tel: 800-577-6478 • Fax: 201-933-0746
West Coast Office: Tel: 800-355-6478 • Fax: 661-940-1617
®
Other manuals for HC-9
2
This manual suits for next models
1
Table of contents
Other Steamist Portable Generator manuals
Popular Portable Generator manuals by other brands
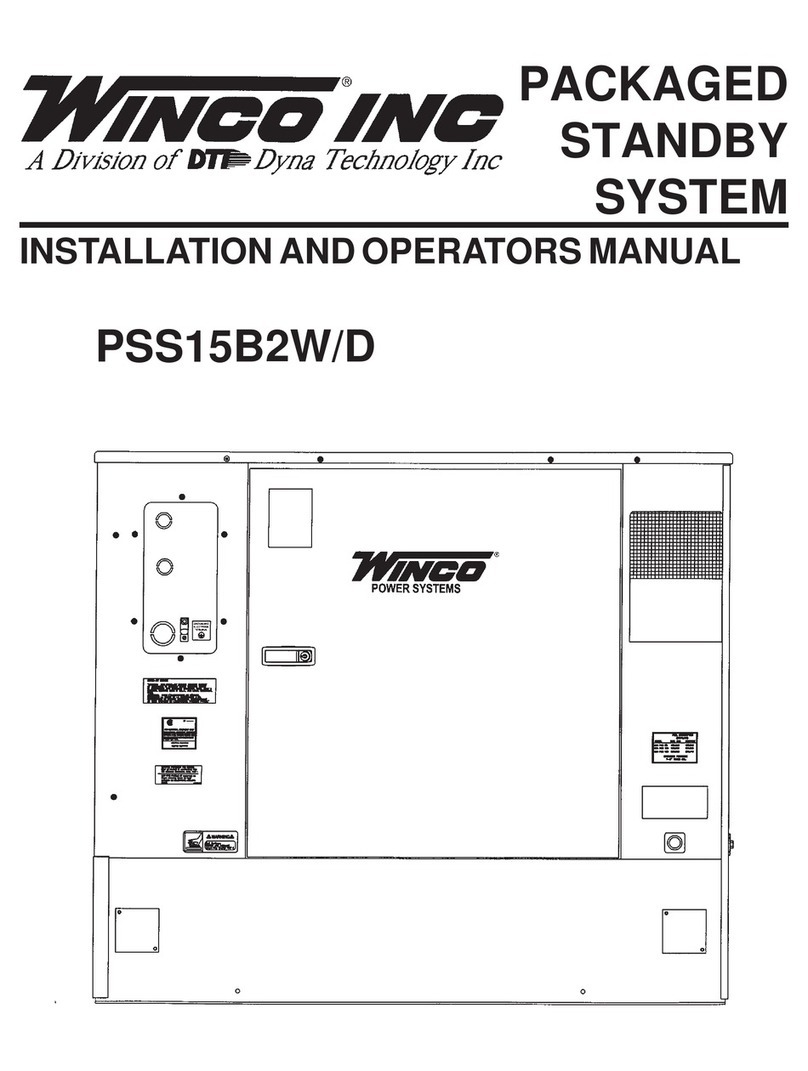
Winco
Winco PSS15B2W/D Installation and operator's manual
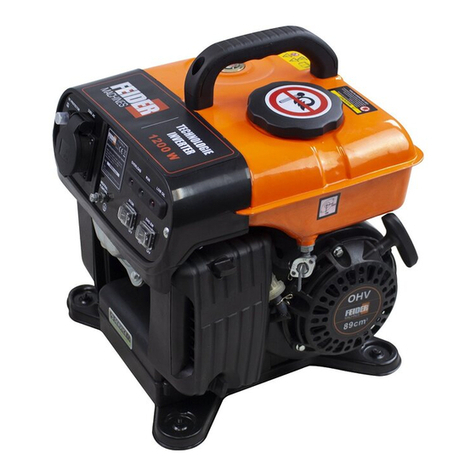
Feider Machines
Feider Machines FG1600i-A Original instruction manual

Teleco
Teleco Telair ENERGY 2510D Use and maintenance manual and instructions for installation
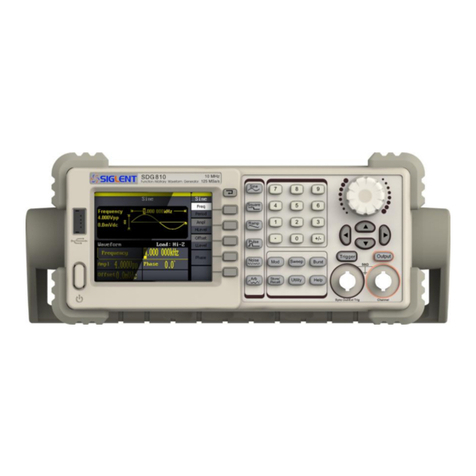
SIGLENT TECHNOLOGIES
SIGLENT TECHNOLOGIES SDG800 Series user manual

HBS
HBS ARC 1550 operating manual

iPower
iPower GXS5000D owner's manual