Trelawny VL LRS55 User manual

VL LRS55 Scabbler & VL Compactor
Operation and Maintenance Manual
www.trelawnyspt.co.uk

OPERATION
Foreword
Thank you for purchasing the
Vibro-Lo LRS55 Scabbler or VL
Compactor.
This manual contains the necessary
maintenance information for you to
ensure proper operation and care for
your machine.
It is essential for you to read
through these manuals
thoroughly.
In the unlikely event that you
experience problems with your
Vibro-Lo Compactor or Scabbler,
please do not hesitate to contact
your local dealer or agent.
We always welcome feedback and
comments from our valued
customers.
General Information
Before operating the VL LRS55
Scabbler/VL Compactor, this manual
must be read and understood by the
operator, if in any doubt ask your
supervisor before using this
equipment.
Failure to follow these instructions
could result in damage to the
Compactor/Scabbler and/or personal
injury.
Trelawny SPT Ltd disclaims all
responsibility for damage to persons
or objects arising as a consequence
of incorrect handling of the tool,
failure to inspect the tool prior to
starting work for damage, or other
faults that may influence the
operation or safe working of the tool,
or failure to follow the safety
regulations listed or applicable to the
job site.
The compactor version is primarily
designed for the compacting of
M.O.T. type 1 granular fill, it has
been certified and is fully compliant
with the New Road and Street works
act (Appendix 8), and has been
designed for use in small
reinstatements and restricted
excavations.
This tool must not be used in a
fixture
It can also be used for the
compaction of cold lay tarmac
(PCSMs), hot laid tarmac,
aggregates and soil.
IMPORTANT
Before operating this equipment,
the operator should read this
manual. Whenever possible, he/
she should be trained how to
operate the machine by an
experienced person.
Trial and error is not the safe way
to become familiar with this piece
of equipment.
Air Supply
The compressed air supply must
be free from water and dirt. The
installation of a filter/regulator/
lubricator air preparation set (with
moisture trap) adjacent to the tool
is strongly recommended.
Always clear the air hose before
connection to the tool. Ensure that
no moisture (condensation) is
present in the air hose.
Ensure that a minimum 19mm
(3/4”) bore air hose is used and
that all couplings are secure; leak
free and in good condition. Limit
the length of air hose to 15M (50ft).
Where extra length is necessary,
for each additional 15M (50ft) of air
hose used, the pressure drop is
approximately 0.16bar (3psi).
The correct air pressure for this
machine is to 6.2bar (90psi).
Do not let the operating pressure
fall below 5.5bar (80p.s.i.) or rise
above 6.9bar (100 psi) absolute
maximum.
Preferably, the compressor should
be able to supply a minimum of
18.9 L/s (40cfm) free air.
In particularly cold weather it is
recommended that a proprietary
anti-freeze lubricating oil be used.
Recommended Lubricants
Oil the tool daily before use. Put a
liberal quantity of one of the
following zinc free air tool
lubricants through the air inlet. It is
recommended that an inline
lubricator be installed in the air
hose adjacent to the tool.
SHELL Naturelle HF
CASTROL Carelube HTG 22
Cleaning
At intervals of no more than 100
hours use, or if operation becomes
unproductive, or if the piston
shows signs of sticking, dismantle
and clean with highly refined
paraffin. Replace any worn
components as necessary.
Immediately after cleaning,
thoroughly oil the tool with one of
the recommended lubricants.
Do wear Personal Protective
Equipment including safety goggles,
footwear, ear defenders and gloves.
In some environments it will be
necessary to wear facemasks or
breathing apparatus.
Do be aware that this tool is not
electrically insulated.
Do ensure that this tool is lubricated
daily.
Do be aware that this tool can create
dust and flying debris.
Do be aware of others working
around you.
Do keep hands and clothing away
from moving parts.
Do store this tool in a secure and dry
environment.
Always observe safe working
practices and local safety
regulations at all times.
Do not allow the tool to run
unattended.
Do not allow the tool to run
continuously whilst not in contact
with the surface being prepared.
Do not modify this tool in any way,
as this will invalidate the warranty
and could lead to serious injury.
Do not use this tool in potentially
explosive environments.
Do not drag this tool by the air hose.
Do not use petrol (gasoline),
thinners or any other high flash point
solvent to clean the tool.
The VL Compactor is also available
as a vibration reduced Scabbler or
can subsequently be fitted with a
Scabbler head for concrete floor
reduction or for the removal of
laitance from concrete floors.
All versions can be used both
indoors and out.
Safety
Alwa ys, read through these
instructions first before use.

Before operating the tool ensure that
the tool is not near your chin or face.
Safe use of this tool requires a solid
stance and secure foothold; the
operator must adopt a firm and
stable position at all times.
On start up, the vibration reduction
component within the tool will cause
the machine to rise three to four
inches (100mm), to operate the tool
pull the lever towards the handle
grip.
Compactor Version
Let the tool do the work; allow a
period of time to become
accustomed to the vibration
dampened compaction action. The
tool does not require any down force
to operate; excessive pressure will
prevent the tool from working
effectively and may reduce the
compaction rate.
The optimum speed for a
compaction pass is approximately
ten seconds per linear meter; it will
achieve optimum compaction after
four passes, using an average depth
of 150mm (6”) of un-compacted
MOT Type 1 granular fill.
Scabbler Version
Let the tool do the work; allow a
period of time to become
accustomed to the vibration-
dampened action. The tool does not
require any down force to operate;
excessive pressure will prevent the
tool from working effectively.
Bush Hammer style headed pistons
are best suited to concrete reduction
and for laitance removal; these may
reduce the likelihood of damage to
the aggregate, ensuring that a
stronger bond is created with the
next layer.
Cruciform headed pistons are suited
to the reduction of concrete or where
a smoother finish is required; these
will reduce the aggregate as well as
the concrete surface.
To switch off, simply release the
throttle lever.
OPERATION / MAINTENANCE
Risk of Hand-Arm
Vibration Injury
These tools may cause Hand-arm
Vibration Syndrome injury if their use
is not adequately managed. We
advise you to carry out a risk
assessment and to implement
measures such as; limiting exposure
time [i.e. actual trigger time, not total
time at work], job rotation, ensuring
the tools are used correctly, ensuring
the tools are maintained according to
our recommendations, and ensuring
that the operators wear personal
protective equipment [PPE]
particularly gloves and clothing to
keep them warm and dry. Employers
should consider setting up a
programme of health surveillance to
establish a benchmark for each
operator and to detect any early
symptoms of vibration injury.
We are not aware of any PPE that
provides protection against vibration
injury by attenuating vibration
emissions.
See „Specifications‟ section for
vibration emission data.
Further advice is available from our
Technical Department.
Starting Work
Before use, screw the vibration
reducing side handle to the bracket
fitted on the main tube handle and
tighten by hand.
The side handle height can be
positioned for operator comfort; the
lower the side handle is positioned
down the tube the easier it will be to
manoeuvre the tool.
Prior to operating the tool check: -
That all fittings are secure, free from
air leaks and that air hoses are in
good condition.
That all parts of the tool are fully
screwed together and secure, if you
are in any doubt ask your supervisor
before using this equipment.
That the air pressure is correct for
this tool 6.2 bar (90 p.s.i.).
That a liberal amount of lubricant
has been put into the air inlet of the
tool. (See recommended lubricants)
Maintenance
Only a competent person, in a
suitably equipped workshop, must
carry out maintenance.
Disconnect the tool from the air
supply before carrying out any of
the following operations.
Dismantling
Clean all debris from the exterior of
the tool.
Loosen the 8mm caphead screw on
the side handle and slide the side
handle (10) up towards the handle
valve body (4). Hold the body
assembly (18) in a vice, using the
flats provided.
Check to see if the body and cowls
original mating identification dimples
are still visible, if not make a mark
opposite one another on the body
and the cowl to aid assembly.
With a 9mm punch, drive out the 2
securing pins on either side of the
cowl (9). Slide the cowl (8) and the
secondary spring (12) towards the
side handle (10). Unscrew the
locknut (16) by holding the handle
tube (11) in a vice, approximately six
inches (150mm) away from the lock
nut.
Using a cold chisel bend back the
tab washer (16A) from the flats of
the locknut (16).
Using a suitable spanner on the flats
of the locknut (16) unscrew from
handle tube (11). This may need a
sharp blow to break the bond.
Supporting the weight of the body,
unscrew the locknut and remove the
body assembly from the handle tube
(11).
Remove the tube from the vice. Next
hold the body in the vice using the
flats provided. Insert a 4mm steel
rod/bar into the hole on centre shaft,
located near the top of the spring.
Rotate the spring (15) on the shaft
so that it “screws” down the 4mm
rod/bar; rotate until a gap appears
between the spring (15) and thrust
ring (13).
Remove circlip and thrust ring. To
relieve the spring tension wind the
spring in the opposite direction until
the spring is at its free 'unloaded'
length. Withdraw the 4mm pin and
remove the spring (15), locknut (16)
and O' Ring cushion (17).

It is good practice to renew all
O'Rings and especially the locknut
wiper seal O‟Ring that is located
inside the lock nut (17).
Replace any parts showing signs of
wear; paying particular attention to
the small bore of the cylinder.
Prior to assembly, inspect the centre
shaft of the body, if there is any sign
of corrosion lightly polish out any
markings with fine emery cloth.
Fit one of the O'Rings (17) over the
centre shaft to act as a cushion.
Fit a new O‟Ring seal (17) into the
locknut (16) and lubricate the seal
(17) using general-purpose bearing
grease.
Slide the locknut onto the centre
shaft, followed by the tab washer
(16A) with the tab towards the
spring. Liberally grease the centre
shaft prior to fitting the spring (15).
Then insert a 4mm rod/bar through
hole in the centre shaft.
Rotate the spring (15) until there is
sufficient clearance to fit the thrust
ring (13).
Fit a new circlip (14). Relieve the
tension in the spring by rotating
approximately two turns in the
opposite direction. Check that the
new circlip (14) is seated correctly
and is secure before removing the
4mm pin.
Piston and Cylinder Assembly.
(Threaded Piston)
Fit a new wiper seal (24) and
O'Rings (21) and (22) to the
appropriate small and large grooves
on the cylinder (23).
Fit a new O'Ring (20) to the piston
(19) and insert into the cylinder (23).
Screw on the compactor foot (25) or
Scabbler head until it butts up
against shoulder of piston (19).
Hold in vice vertically, gripping on
compactor foot (25) or Scabbler
head on the spanner flats.
Fully secure using a suitable wrench
on the piston‟s (19) spanner flats to
a torque of 500lbs/ft (678Nm).
OPERATION / MAINTENANCE
Hold body assembly (18) on the flats
provided and unscrew the cylinder
(23).
(Threaded Piston)
Hold the Compactor foot (25) or
Scabbler head (27) securely in a
vice, then using a 1¼” (32mm)
spanner on the piston flats, unscrew
the compactor foot and remove the
piston (19) from the cylinder (23).
Remove the piston O' Ring (20) and
remove cylinder wiper seal (24) and
O' Rings (21) and (22).
(Pin fit Piston)
Hold the compactor foot or Scabbler
head (25) securely in a vice, then
using a 12mm punch drive out the
spiral retaining pin (30) and remove
the compactor foot or Scabbler
head, remove the piston (19) from
the cylinder (23). Remove cylinder
wiper seal (24) and O' Rings (21)
and (22).
Valve Body Servicing
Hold handle tube (11) in vice,
approximately six inches (150mm)
away from the valve assembly and
with the locking rivet uppermost,
knock out the rivet using a sharp
chisel. Looking as from the top of
the handle, using a soft-faced
hammer, strike the air inlet boss
downward in an anti clockwise
direction and unscrew from handle
tube (11).
This may need a sharp blow initially
to break the bond. Remove the
handle tube (11) from the vice.
Secure the valve body assembly in
the vice, holding on the main body.
Using a suitable spanner unscrew
the adapter (1) from the valve body,
remove the spring (2) and retrieve
the valve stem (6) with its O‟Rings
(3) and (26). Using a 8mm punch,
drive out the throttle lever pivot pin
and withdraw the throttle lever (5).
ASSEMBLY
Before any assembly takes place,
ensure all parts are clean and have
a film of air tool oil lubrication unless
otherwise stated.
Avoid lubricating oil or grease
contaminating the threads of the
cylinder (23), tube handle lock nut
(17), and handle valve body (4).
These will require securing with a
thread-locking adhesive.
Ensure that the threads of the
cylinder and body are clean and free
of oil; apply a bead of Loctite 243 or
similar to the first few threads of the
cylinder (19).
Hold the body assembly in a vice on
the flats provided and screw cylinder
(23) in by hand, using a suitable
wrench on the spanner flats tighten
to a recommended torque of 135Nm
(100 lbs/ft).
Piston and Cylinder Assembly.
(Pin fit Piston)
Fit a new wiper seal (24) and both
O' rings (21) and (22) to the
appropriate small and large grooves
on the cylinder (23).
Insert the piston (19) into the
cylinder .
Fit the compactor foot (25) or
Scabbler head until it butts up
against the piston.
Align the holes in the piston and
compactor foot or Scabbler head.
A
7/16
” Allen Key is a good fit for this
purpose or use a suitable piece of
wooden dowelling.
Hold the spiral pin (30) with a pair of
pliers to avoid hitting the fingers, and
then using a hammer, drive in the
spiral pin (30) fully to secure the
compactor foot or Scabbler head.
Ensure that the threads of the
cylinder and body (18) are clean and
free of oil; apply a bead of Loctite
243 or similar to the first few threads
of the cylinder.
Hold the body in a vice on the flats
provided and screw cylinder in by
hand, using a suitable wrench on the
spanner flats on the cylinder (12)
tighten to a recommended torque of
15Nm (100 lbs/ft).
Handle/Valve Body Assembly
Apply general-purpose grease to the
valve stem, insert valve stem (6) with
its O'Ring (3) into valve guide
followed by the spring (2).
Screw in adaptor (1) by hand and
using a 27mm (1
1/16
”) spanner fully
tighten.

Using a 8mm punch align the hole in
the throttle lever (5) with the holes in
the handle (4). Using a small hammer
fit the throttle lever pin (7).
Tube to Handle Assembly. Hold
handle tube (11) in vice, about six
inches (150mm) away from the valve
assembly.
Ensure that the threads of the Handle
and Tube are of Loctite 243 or a
similar product and free of oil; apply a
bead to the first few threads of the
Handle and screw in the handle (4)
until hand tight.
Looking from the top of the handle,
using a soft-faced hammer, strike the
air inlet boss downward in a clockwise
direction until tight.
Body to Handle Tube Assembly
Ensure that the thread of the lock nut
(16) is clean and free of oil; apply a
bead of Loctite 243 or a similar
product to the first few threads of the
lock nut (16).
Hold the handle tube (11) firmly in a
vice, take extra care while inserting
the spring (15) into the tube not to
contaminate the tube threads with
grease, otherwise the thread lock
adhesive will not cure, screw in the
locknut (16) until hand tight.
Using a suitable wrench, tighten the
locknut to a torque of 100lbs/ft
(135.5Nm).
Knock over the tab washer onto
one of the locknut flats.
Lubricate the mating faces of the
cowl and body with a general
purpose bearing grease.
Slide cowl (8) and spring (12)
down onto body assembly and
align the dimple on the body with
the dimple on the cowl, align the
holes using a 9mm bar.
Drive one of the spiral securing
pins (9) through the free hole.
Remove 9mm bar and fit the
second spiral pin (9).
It is important that the pins are
fitted centrally in the cowl.
Remove tool from vice and re-
position side handle (10) and
tighten the M8 caphead screw.
Machine Storage
Storage: over 3 months.
Clean the outside of the machine
and inspect the piston and
cutterhead for wear, replace any
worn parts as required.
Put a liberal amount of lubricant
into the air inlet of the tool and run
the tool for a few seconds to
disperse the oil around the tools
internal components.
Lubricate the exposed part of the
piston and cylinder.
(See recommended lubricants)
Cover the machine to protect it:
Store the machine in a dry place.
When next used, continue as per
“Starting work section”.
Disposal
When the tool and its accessories
are taken out of service for disposal,
it is recommended that: -
Dismantle into component form,
segregated according to material
composition and disposed of using
waste recycling processes specified
by local regulations.
Machinery Directive
Information
This tool has been designed and
produced in accordance with the
following directive:
2006/42/EC Machinery Directive
and applicable harmonised standard:
EN ISO 1 1148-4:2010
If your company has any problem
with our products or would like to
discuss the possibility of an
improvement being made to them,
then please do not hesitate to contact
us. Your comments are both
important and appreciated.
OPERATION / MAINTENANCE
TECHNICAL SPECIFICATIONS COMPACTOR SCABBLER
Length 1270mm (50)”
Weight 21.5kg (47.3lbs)
Blows per minute 1300
Air Pressure 6.2 bar (90psi)
Air Consumption 11.61 lps (25cfm)
Sound pressure level 98.0db(A)
Vibration Level (H1)* 3.5m/s2(K= -0% +40%) 4.2m/s2(K= -0% +40%)
Vibration Level (H2)* 2.9m/s2(K= -0% +40%) 3.9m/s2(K= -0% +40%)
*H1, Indicates test taken from the primary handgrip location at the trigger.
*H2, Indicates test taken from the secondary handgrip location.
Users should be aware that for other applications, the vibration readings may be higher than specified.
The 4.2 m/s² value is only applicable to compaction of MOT (DOT) type 1. sub-base material

EXPLODED VIEW

PARTS LIST
ITEM PART NUMBER DESCRIPTION
1 627.5002 Adapter
2 712.5001 Valve Spring
3 809.5599 O‟Ring (Valve seat)
4 424.5025 Handle Assembly (includes 1,2,4,5,6,7,& 26.)
5 649.5001 Throttle Lever
6 448.5022 Valve Stem (Includes O‟Rings)
7 813.0840 Throttle Lever Pivot Pin
8/18 411.5052 Cowl & Body Assembly
9 813.1040 Locking Pin
10 422.5220 Side Handle
11 624.5002 Handle Tube
624.5006 Handle Tube Long Version (400mm longer)
12 712.5003 Secondary Spring
13 628.5002 Thrust Ring
14 815.5509 Circlip
15 712.5002 Spring
16 625.5002 Locknut
16A 720.5003 Tab washer
17 809.6289 O‟Ring (Centre Bar Seal & Cushion)
18 see item 8 Body Assembly
19 612.5001 Piston (Screw fit)
612.5005 Piston (Pin fit)
20 809.6499 Piston O‟Ring (Screw fit)
23 613.5001 Cylinder
24 829.5001 Wiper seal
25 450.5007 127mm Diameter Compactor Foot (Screw Fit)
450.5017 127mm Diameter Compactor Foot (Pin Fit)
450.5001 100 x 100mm Compactor Foot (Screw Fit)
450.5011 100 x 100mm Compactor Foot (Pin Fit)
450.5003 127 x 152mm Compactor Foot (Screw Fit)
450.5013 127 x 152mm Compactor Foot (Pin Fit)
450.5006 100 x 200mm Compactor Foot (Screw Fit)
450.5016 100 x 200mm Compactor Foot (Pin Fit)
26 809.0069 O‟Ring (Valve Stem Seal)
27 426.5051 Scabbler Head - Five Point TCT (Screw Fit)
441.5359 Scabbler Head - Five Point TCT (Pin Fit) includes pin
426.5052 Scabbler Head - Cruciform TCT (Screw Fit)
441.5360 Scabbler Head - Cruciform TCT (Pin Fit) includes pin
441.5369 Scabbler Head - Nine point TCT (Pin Fit) included pin
28 813.1050 Roll Pin (Pin Fit Type)
29 Not Assigned
30 806.2080 Trigger Guard Screw
31 665.5500 Trigger Guard
809.6599 Cylinder O‟Ring (Small) (No longer fitted 8/2012)
809.6619 Cylinder O‟Ring (Large) (No longer fitted 8/2012)

Vibration Statement
(K) Equals the factor of uncertainty, which allows for variations in measurement and production.
Vibration data figures are tri-axial, which gives total vibration emission.
Risk of Hand Arm Injury
Because of various factors, the range of vibration emission during intended use of these tools is expected to be between
3.5m/s² –5.88m/s².
The vibration is dependent on the tool model, task, the operators grip, and feed force employed etc.
Noise level measured in accordance with: EN ISO 15744: 2008
Vibration measured in accordance with: EN ISO 28927:2012 and EN ISO 20643:2005
Trelawny tools are thoroughly tested under specified conditions in accordance with applicable internationally recognised
standards. When a tool is used on site the conditions may not be the same as those used in our tests.
Trelawny Surface Preparation Technology operates a policy of continuous product development and refinement and
therefore reserves the right to change technical specifications and product designs without giving prior notice.
© Copyright 2009, Trelawny SPT Limited, CV31 1XT. UK All rights reserved. Any unauthorised use or copying of the
contents or part thereof is prohibited. This applies to trademarks, model denominations, part numbers and drawings.
Use only genuine Trelawny spares.
The use of non-Trelawny spare parts invalidates the warranty.
TECHNICAL DATA

NOTES

Trelawny SPT Ltd
13 Highdown Road, Sydenham Industrial Estate, Leamington Spa,
Warwickshire, CV31 1XT, United Kingdom
Telephone: +44 (0)1926 883781 - Fax: +44 (0)1926 450352
Email: sales@trelawny.co.uk
© TSPT UK 2009 Part No: 735.4000 issue 4.11.16
www.trelawnyspt.co.uk
Table of contents
Popular Garbage Disposal manuals by other brands
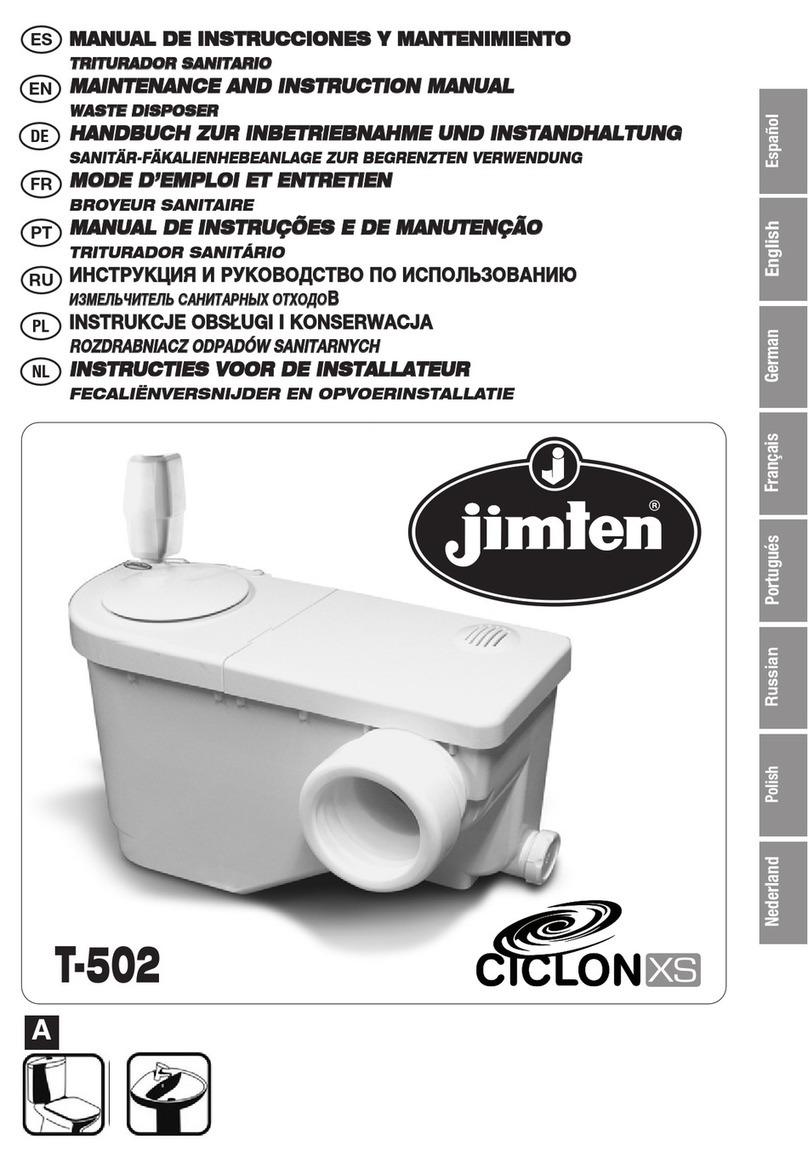
JIMTEN
JIMTEN Ciclon XS T-502 Maintenance and Instruction Manual

KitchenAid
KitchenAid INTEGRATED COMPACTOR Use and care guide

Meiwa
Meiwa MX80 operation & maintenance
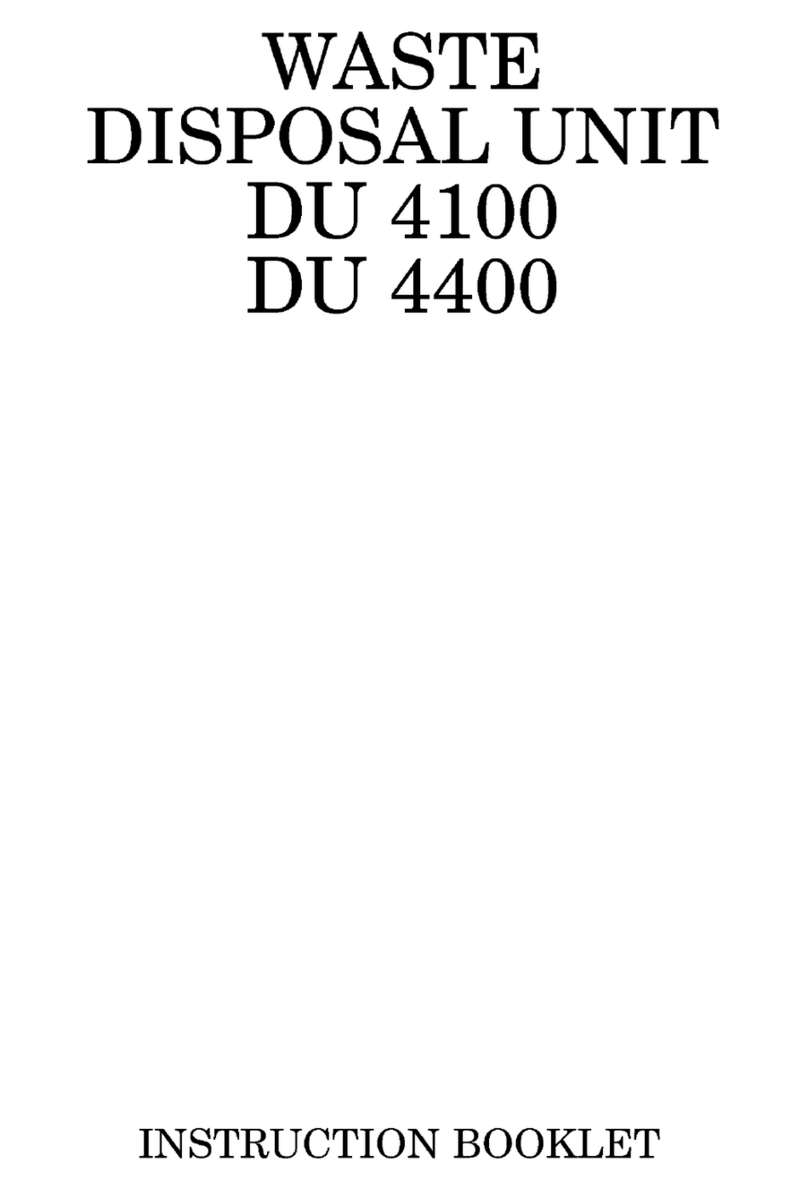
Zanussi
Zanussi DU 4400 Instruction booklet
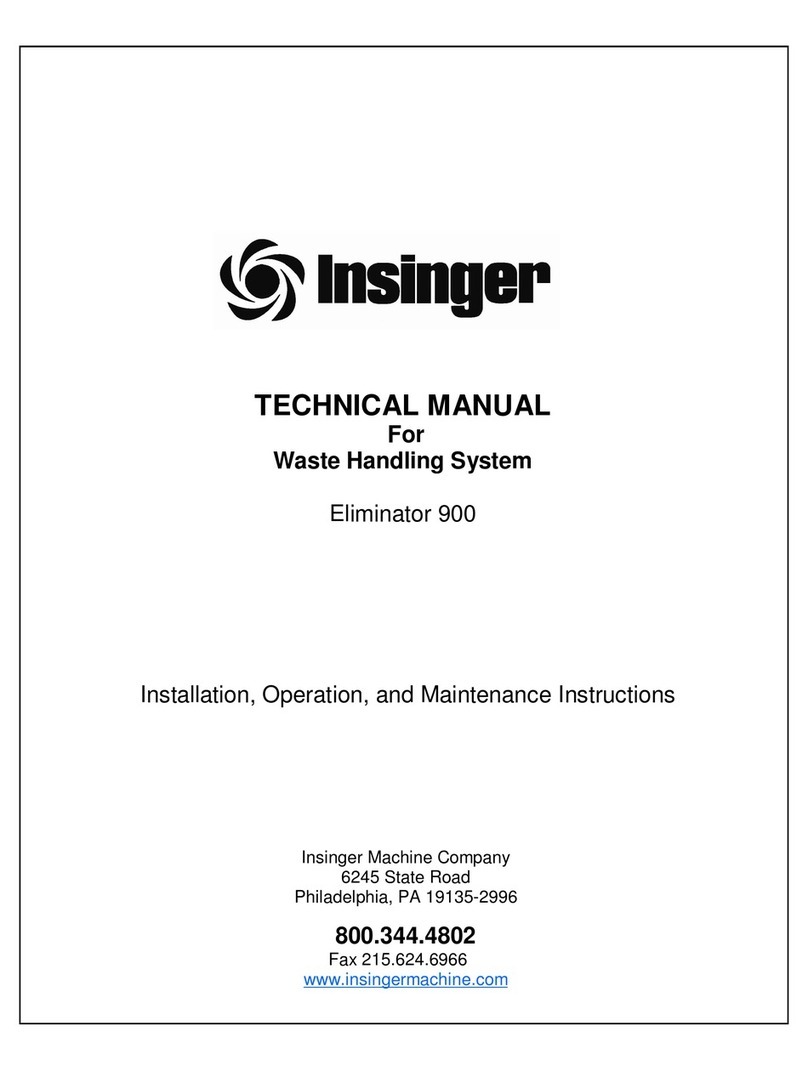
Insinger
Insinger Eliminator 900 Technical manual

lamart
lamart SENSOR Series PRODUCT INFORMATION AND INSTRUCTIONS

Teral
Teral DSP-125H-AWS manual
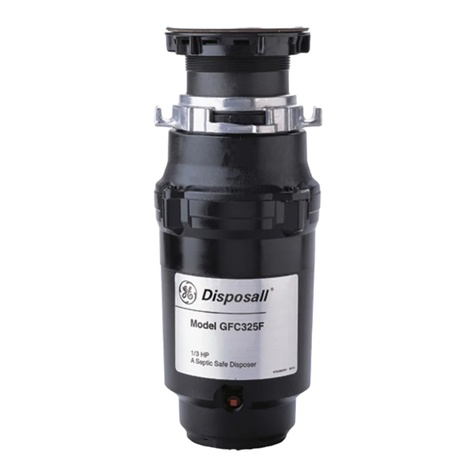
GE
GE Disposall GFB1000F Series Owner's Manual & Installation Instructions
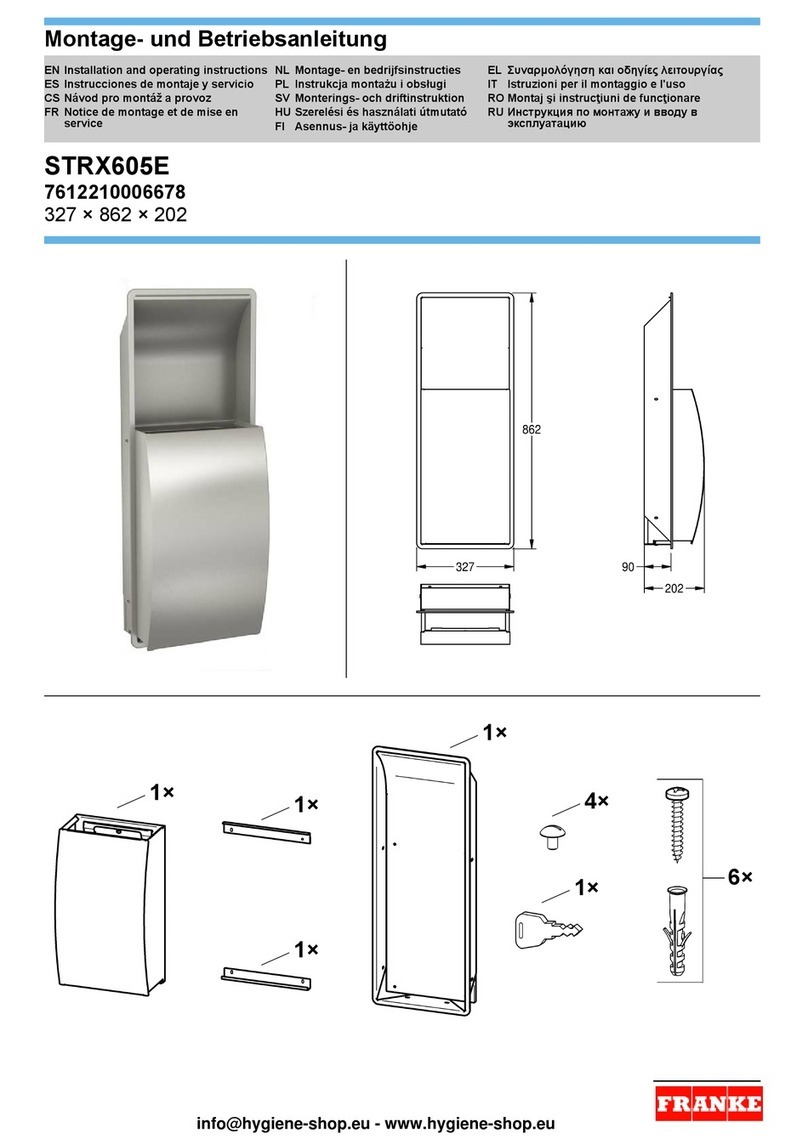
Franke
Franke STRATOS STRX605E Installation and operating instructions

EVE
EVE FWD560+ Instruction and installation manual
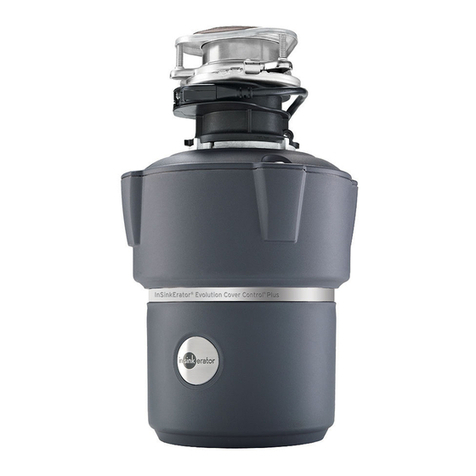
InSinkErator
InSinkErator Evolution CoverControl Plus manual

Elephants Foot
Elephants Foot eDiverter Photo step by step instruction booklet