Trust TA333 User manual

Trust Automation, Inc. TA333 High Power Linear Drive
6-Feb-09 Operating Manual Page 1 of 38
TA333
High Power Linear Servo Amplifier
PRELIMINARY Operating Manual
Revision 0.13

Trust Automation, Inc. TA333 High Power Linear Servo Amplifier
10-Apr-09 Page 2 of 38
This Page Left Blank

Trust Automation, Inc. TA333 High Power Linear Servo Amplifier
10-Apr-09 Page 3 of 38
Copyright Information
© 2009 Trust Automation, Inc. All rights reserved.
This document is provided for Trust Automation, Inc. customers, solely for the purpose of assisting our
customers in the use and installation of our products. Other uses are unauthorized without the written
permission of Trust Automation, Inc. The text and graphics included are for purpose of illustration only
and information is subject to change without notice. Trust Automation, Inc. and the Trust Automation,
Inc. logo are trademarks of Trust Automation, Inc. – a California corporation.
For information regarding re-use of this material or to report errors, omissions, inconsistencies, etc,
please contact Technical Support at:
Trust Automation, Inc.
143 Suburban Road, Bldg. 100
San Luis Obispo, CA 93401
Web: www.trustautomation.com
Phone: (805) 544-0761
FAX: (805) 544-4621
Handling and Safety Information
Trust Automation products contain static sensitive parts that may be damaged if handled improperly.
We strongly encourage you to follow proper ESD procedures when handling electronic components.
Removing component covers, except where expressly permitted, may expose products to static
damage and increase the risk of premature failure.
High voltages are present in some Trust Automation products. Maintenance or repair should only be
performed by qualified personnel and only under power down conditions. Maintenance and repair shall
be limited to those items described in this operating manual as user approved. All other repair and
maintenance shall be performed by Trust Automation, Inc.

Trust Automation, Inc. TA333 High Power Linear Servo Amplifier
10-Apr-09 Page 4 of 38
This Page Left Blank

Trust Automation, Inc. TA333 High Power Linear Servo Amplifier
10-Apr-09 Page 5 of 38
Table of Contents
1.0 Features and Setup ........................................................................................................... 7
1.1 Introduction...................................................................................................................................7
1.2 Setup..............................................................................................................................................8
1.3 Drive Modes...................................................................................................................................8
1.4 Command Input.............................................................................................................................9
1.5 Upgrading from a TA320 or TA330..............................................................................................9
1.6 Transconductance Ratio..............................................................................................................9
1.7 Thermal Limits ............................................................................................................................10
1.8 Dynamic Transconductance Selection.....................................................................................10
1.9 Enable Input ................................................................................................................................11
1.10 Fault Output...............................................................................................................................11
1.11 Ground Connections................................................................................................................12
1.12 Drive Power Supply..................................................................................................................12
1.13 Optional External 24VDC Supply.............................................................................................13
1.14 Power Dissipation Calculations ..............................................................................................13
1.15 Motor Connections...................................................................................................................14
1.16 Serial Monitoring.......................................................................................................................15
2.0 General Specifications.................................................................................................... 18
2.1 Electrical Specifications.............................................................................................................18
2.2 Mechanical Specifications.........................................................................................................18
2.3 Environmental Specifications....................................................................................................18
2.4 TA333 Safe Operating Area Curve (SOA) .................................................................................19
2.5 TA333 Output Frequency Response.........................................................................................22
3.0 Mechanical Information................................................................................................... 23
3.1 Dimensions..................................................................................................................................23
4.0 Connector and Switch Information................................................................................ 24
4.1 Front Panel Connector and Switch Layout ..............................................................................24
4.2 Connector Types.........................................................................................................................24
4.3 J1 – External 24VDC Supply......................................................................................................24
4.4 J2 – Serial Monitoring Port ........................................................................................................24
4.5 J3 – Command Signals...............................................................................................................25
4.6 J4 – Hall Sensor Input ................................................................................................................25
4.7 J5 – Motor Signals......................................................................................................................25
4.8 J6 – Motor Power........................................................................................................................25
4.8 SW1 – Switch Settings ...............................................................................................................26
4.9 SW1 – Switch 3 and 4, Fixed Gain and DTS Settings..............................................................26
4.10 SW1 – Switch 5-8 Motor type...................................................................................................27
4.11 Isolation Diagram......................................................................................................................28
5.0 Application Examples ..................................................................................................... 30
5.1 Brushless Motor, Sinusoidal (Differential Command Input)...................................................30
5.2 Brushless Motor, Sinusoidal (Single Ended Command Input)...............................................31
5.3 Brushless Motor, Trapezoidal, Hall Commutation...................................................................32
5.4 Brush Motor, Bridge Mode.........................................................................................................33
5.5 Brush Motor, Dual Motor Mode .................................................................................................34
5.6 Stepper Motor, Sinusoidal Commutation .................................................................................35
6.0 Warranty........................................................................................................................... 36
7.0 TA333 Hardware Revision History ................................................................................. 37
8.0 TA333 Manual Revision History ..................................................................................... 38

Trust Automation, Inc. TA333 High Power Linear Servo Amplifier
10-Apr-09 Page 6 of 38
Figures
Figure 1 – Enable Circuit ......................................................................................................... 11
Figure 2 – Fault Circuit ............................................................................................................ 11
Figure 3 – Drive Power Connection......................................................................................... 12
Figure 4 – Com Port Settings for Serial Communication ......................................................... 15
Figure 5 – Data Transmission Format, HyperTerminal............................................................ 16
Figure 6 – Sample Fault Printout ............................................................................................. 17
Figure 7 – TA333 SOA Curve.................................................................................................. 19
Figure 8 – Output Current vs. Time Graph for Time to Fault @ ~30°C.................................... 20
Figure 9 – Dissipation Wattage vs. Time for Time to Fault @ ~30°C ...................................... 20
Figure 10 – Temperature De-rating, Time to Fault for Dissipation Wattages vs. Heatsink
Temperature ............................................................................................................................ 21
Figure 11 – TA333 Frequency Response ................................................................................ 22
Figure 12 – TA333 Mechanical Dimensions ............................................................................ 23
Figure 13 – TA333 Front Panel ............................................................................................... 24
Figure 14 – Fixed Gain and DTS Settings ............................................................................... 26
Figure 15 – SW1 Motor Type settings ..................................................................................... 27
Figure 16 – TA333 Isolation Diagram ...................................................................................... 28
Figure 17 – Application Example 1 .......................................................................................... 30
Figure 18 – Application Example 2 .......................................................................................... 31
Figure 19 – Application Example 3 .......................................................................................... 32
Figure 20 – Application Example 4 .......................................................................................... 33
Figure 21 – Application Example 5 .......................................................................................... 34
Figure 22 – Application Example 6 .......................................................................................... 35
Tables
Table 1 – Data Transmission Format ...................................................................................... 16
Table 2 – Fault Codes ............................................................................................................. 16
Table 3 – Electrical Specifications ........................................................................................... 18
Table 4 – Mechanical Specifications ....................................................................................... 18
Table 5 – Environmental Specifications................................................................................... 18
Table 6 – Connector Types ..................................................................................................... 24
Table 7 – External 24VDC Supply Connector.......................................................................... 24
Table 8 – Serial Monitoring Connector .................................................................................... 24
Table 9 – Motor Command Signals Connector........................................................................ 25
Table 10 – Hall Sensor Input Connector.................................................................................. 25
Table 11 – Motor Signals Connector ....................................................................................... 25
Table 12 – Motor Power Connector......................................................................................... 25
Table 13 – SW1 Settings .........................................................................................................26
Table 14 – Fixed Gain and DTS Switch Settings..................................................................... 26
Table 15 – SW1 Motor Type Selection .................................................................................... 27

Trust Automation, Inc. TA333 High Power Linear Servo Amplifier
10-Apr-09 Page 7 of 38
1.0 Features and Setup
1.1 Introduction
The TA333 is a 4th generation Trust Automation Linear Drive featuring a true Class-AB linear amplifier
with pure analog throughput at virtually infinite resolution and is free from digital conversion losses. This
versatile linear drive is an excellent choice for a variety of different servo motors and applications that
require high resolution positioning and/or ultra low noise applications with sensitive measuring
equipment, (e.g., transducers, sensors).
The TA333 is a highly configurable device with four common configuration modes:
•Drive one brushless motor using external sinusoidal commutation.
•Use Hall Effect sensor feedback for smooth internally commutated trapezoidal operation.
•Supports one or two brush or voice coil type motors.
•Drive a two coil stepper motor under sinusoidal control.
The TA333 features digital on-the-fly gain control (Dynamic Transconductance or DTS). This allows an
application to modify the drive transconductance on-the-fly, permitting both high acceleration control
and high resolution control. Normally one of these parameters is sacrificed in favor of the other due to
DAC limitations at the driving motion controller.
Why use a Trust Automation linear amplifier?
The majority of motion control applications use PWM (Pulse Width Modulated) drives. PWM drives are
very efficient, but are electrically noisy as they operate by pulsing the motor at full supply voltage at
typical frequencies of 4 kHz to 30 kHz. This pulsing tends to saturate everything electrically in the
surroundings, often including the intended operation. A second side effect of using PWM drives shows
up in ultra-high precision systems requiring nanometer precision. Due to the pulsing nature of the PWM
drive, the motor will tend to dither causing position error that cannot be tuned out.
The TA333 features a true Class-AB linear power stage with a fast current feedback loop to put it in
torque mode. This means that the output is a pure current signal with virtually no distortion around zero,
eliminating all of the side effects of a PWM drive. Some Class-C linear designs, which have a dead
band at zero volts out, attempt to mask this with a fast current loop. This works for some applications,
but performance will suffer in ultra-high precision applications.
Two important considerations where linear servo amplifiers are utilized are cooling and power supply
selection. A linear servo amplifier acts similarly to a large electronic variable resistor. Any power supply
voltage not delivered to the load is dumped as heat into the heatsink. Power supply voltages should be
matched closely to the required load voltage with a small margin for overhead. Excessive supply
voltage will result in amplifier overheating. Cooling linear servo amplifiers is often overlooked or not well
understood. Many products are available with similar current output specifications, but require the user
to supply heatsinks or fans. The TA333 incorporates a large heatsink with integral cooling fans to
accommodate most demanding applications provided there is adequate air space around the chassis
and the ambient temperature does not exceed specification. The TA333 intelligently monitors
temperature and compensates its internal dissipation to protect the drive from damage due to high
temperatures. The TA333 has a serial diagnostics port to monitor application performance and power
levels to aid in assuring optimal performance and a long life.
All Trust Automation drive products are built for safety, installation ease and long life. The TA333 offers
a fully isolated user interface for safe operation in high voltage applications. In addition the TA333

Trust Automation, Inc. TA333 High Power Linear Servo Amplifier
10-Apr-09 Page 8 of 38
housing reduces the risk of operator injury and protects the drive, ensuring longer useful life. All
connections utilize pluggable terminal connectors making them easy to install and remove while
reducing the risk of connection errors.
1.2 Setup
The TA333 is configurable for several drive motor type options and configurations. All configurations
require the use of bipolar supplies that can be in the range of 24 to 100V. Current outputs are
adjustable from 10 to 25A.
Some of these options are shown in the application example section.
1.3 Drive Modes
Sinusoidal
Sinusoidal commutation of three-phase brushless servo motors plus a linear drive power stage
eliminates the familiar cogging and torque ripple problems that plague most trapezoidal digital drives.
Control is consistent and smooth at any velocity.
In sinusoidal mode, the TA333 is designed to accept two command signals (A and B @ ±10V) from a
motion controller that is performing the commutation based upon encoder feedback. The TA333 derives
the third phase internally (C = - (A+B)). (See application example 5.1 and 5.2)
Trapezoidal
Trapezoidal operation is the simplest configuration used to drive a DC brushless motor. The TA333
reduces the audible tick often associated with Hall commutation by smoothing the transitions without
sacrificing performance. As a practical limitation, Hall commutation is limited to ~ 3 kHz throughput. In
this mode, the motors Hall Sensors are connected to J4. If the motor has differential Hall outputs, only
connect the “+” Hall outputs to J4 and leave the “–” Hall signals unconnected. (Do not tie to ground, the
motor will be damaged.)
The motion command signal (±10V) is connected to the “A” command input. (See application example
5.3)
Brushed-Bridge
Brushed-bridge mode supports operating a traditional brushed or voice coil-type motor, bridged across
the A & C output phases. The command signal (±10V) is connected to the “A” command input. (See
application example 5.4)
Brushed-Dual
This mode supports driving two independent brushed or voice coil-type motors. This mode could also
be used to drive a stepper motor in sinusoidal mode. The first motor (winding) would be connected to
the “A” phase output and the common ground of the bipolar power supply. The second motor (winding)
would connect to the “B” phase output and the common ground. The command inputs (±10V) are
connected to the “A” and “B” command inputs. (See application examples 5.5 and 5.6)

Trust Automation, Inc. TA333 High Power Linear Servo Amplifier
10-Apr-09 Page 9 of 38
1.4 Command Input
Motion command connections to the TA333 are made at J3. Inputs are provided for two of the three
phases (A and B) and the TA333 can derive the third phase (C = - (A+B)) in sinusoidal applications.
The inputs are common mode terminated at 10K and there is no need to ground an input if it is unused.
The input range is set to ±10V commands.
Differential Inputs
Using differential input helps reduce or eliminate potential noise susceptibility from other sources.
Connect the motion controller ± command outputs to the TA333 ± inputs at J3. For best immunity use a
twisted pair cable. Terminate the motion controller signal ground to the TA333 ISO ground connection
at J3. (See application examples 5.1)
Single-Ended Inputs
Many motion controllers only offer single-ended command signals with a common ground. Single-
ended configurations are accommodated by referencing the A+ and B+ signals to the command output
and referencing the A- and B- signals to the motion controller signal ground. It is good practice to use a
twisted pair cable for the “+” command, terminating the “-” command at the controller signal ground.
Terminate the motion controller signal ground to the TA333 ISO ground connection at J3.
(See application example 5.2)
1.5 Upgrading from a TA320 or TA330
When changing a preexisting application from a TA320 or TA330, the command signal polarity must be
reversed to maintain the applications direction of motion.
The original TA320 and TA330 linear amplifiers operated with inverted outputs, meaning a positive
command induces a negative current. The TA333 is a non-inverting amplifier (positive command =
positive current).
Examples:
•Differential inputs would place the motion controller’s “+” signal on the TA333 “–” command
input and the controller’s “–” signal on the TA333 “+” command input.
•Single-ended configurations place the motion controller’s command output on the TA333 “–”
command inputs and terminate the TA333’s “+” command inputs to the motion controller’s
signal ground and the TA333 ISO ground connection.
1.6 Transconductance Ratio
The TA333 operates in current mode (commonly referred to as Torque mode). For a given input
voltage, the TA333 will output a proportional current by raising the output voltage until the commanded
current is drawn. As current flow in a motor is directly proportional to torque, it is common to refer to this
as “Torque mode”. The ratio between the command voltage and the output current is referred to as the
“Transconductance Ratio,” which is measured in amps per volt and is expressed by the following
equation:
gm = Io/ Vc

Trust Automation, Inc. TA333 High Power Linear Servo Amplifier
10-Apr-09 Page 10 of 38
gm= current gain (Transconductance)
Io= output current
Vc= command voltage
Example:
If: I
odesired = 15A and Vc(max) = 10V
Then: g
m= 15 / 10 or 1.5A/V
For every 1 volt of command 1.5A of current will be driven.
Note: Current output is limited by Ohm’s Law (I = Vsupply / Rmotor)
TA333 is factory configured for 10A, 15A, 20A and 25A for a commanded input voltage of ±10V, set at
SW1, positions 3 and 4. (See table 4.9)
Note: 25A output duration is limited by the SOA graph and temperature. (See SOA section 2.4)
Custom Transconductance ratios can be preset by the factory. Please contact
1.7 Thermal Limits
The TA333 is internally thermally protected with integral variable speed cooling fans. The heatsink
temperature is monitored and the fan speed is automatically adjusted to maintain a safe operating
temperature. If the heatsink temperature rises to 70°C, a FAULT output is generated but the drive will
continue to operate. If FAULT is ignored and the heatsink temperature rises to 90°C, the drive will
shutdown. When the heatsink temperature drops below 40°C, the drive can be re-enabled by toggling
the enable line.
1.8 Dynamic Transconductance Selection
A feature pioneered by Trust Automation, Dynamic Transconductance, or DTS, enables on-the-fly
changes to the transconductance settings. This feature is advantageous in frictionless systems (i.e., air
bearing systems) where start, stop and turn around currents are high, but moving currents are very low.
Due to the digital nature of most motion controllers there is limited DAC resolution to cover both the
high and low currents with sufficient resolution. By switching the transconductance on the fly, the
motion controller’s DAC can be utilized at its full resolution for both high current moves and precision
motion.
The DTS inputs are logically “OR”ed with the DTS switch inputs. In this way a highest current setting
can be chosen by the switches and logic can “OR” with this data to set a lower setting.
The TA333 accomplishes this by allowing the motion controller to logically control the DTS bits D0 and
D1 through pins 5 and 6 of J3 (5V TTL). (See application example 5.4)

Trust Automation, Inc. TA333 High Power Linear Servo Amplifier
10-Apr-09 Page 11 of 38
1.9 Enable Input
The ENABLE input can be selected as active-high or active-low logic at SW1 position 1. (See table 4.8)
The input must be pulled to logic low (ISO GND) or logic high (ISO +5) for the TA333 to operate. The
ENABLE line is pulled up internally to ISO +5. The TA333 provides an isolated +5V source at connector
J3 and J4 with a maximum draw of 100mA. If the application requires more current, the user must
supply an external 5V that must be referenced to the ISO ground connection.
The TA333 must not be enabled during power up. If the drive is powered up when enabled, the drive
will not enable and will assert FAULT. The ENABLE input must then be cleared and re-asserted to
enable the drive.
Note: A minimum sinking capability (IOL) of 5mA is required.
Note: Logic low input minimum voltage (VIL) is 0.8V. Logic high input minimum voltage (VIH) is 2.0V with
a maximum on 5.2V.
See circuit in the following figure:
Figure 1 – Enable Circuit
1.10 FAULT Output
The TA333 FAULT output is selectable as active-high or active-low logic, set at SW1 position 2. (See
table 4.8) The TA333 will assert FAULT upon over-current or thermal overload based on the SOA
graph. (See section 2.4) Past FAULT information is stored in internal memory and may be accessed at
the serial monitoring port. (See section 1.16)
Note: Logic output high minimum voltage (VOH) is 2.5V. Logic output low maximum voltage (VOL) is
0.8V.
See circuit in the following figure:
Figure 2 – Fault Circuit

Trust Automation, Inc. TA333 High Power Linear Servo Amplifier
10-Apr-09 Page 12 of 38
1.11 Ground Connections
Command and Signal Logic
Connections to a motion controller must be referenced to ISO ground at J2. These signals include
Enable, FAULT, DTS and the analog command inputs. For single-ended command signals, reference
the TA333 command A- and B- inputs to ISO ground on connector J2.
ISO Ground and all user interface signals on J2, J3 and J4 are isolated from drive power GND and the
External 24V GND with a minimum 1500V hipot separation.
1.12 Drive Power Supply
A pair of matching power supplies (24V to 100V) must be used to power the TA333. A high quality
switching supply is suitable for most applications. These supplies tend to be small, affordable, and
highly available. Trust Automation recommends supplies with an output ripple less than 100mV. Some
high quality supplies available offer less than 50mV. In some cases, particularly where there is great
concern for noise interference, a linear power supply, regulated or unregulated, will be required. For
unregulated supplies, verify that the voltage supplied either at V+ or at V- does not exceed the absolute
maximum supply voltage of 100V. Also note that the supplies must be within 12V of each other or a
supply fault will be generated.
When using the TA333 or any linear servo amplifier, power supply voltage that is not delivered to the
motor will be lost as heat in the amplifier. (See section 1.14)
When selecting supplies for a given motor application it is recommended that the total voltage be
approximately 20V more than the required motor voltage. (The TA333 can drive to within ~ 8V of the
supply). Excessive supply voltages will result in higher peak wattage dissipation. Reference the SOA
graph for actual currents allowed. (See section 2.4)
Figure 3 – Drive Power Connection
Connect the positive supply positive “+” to V+ and the positive supply negative “-” to GND. Connect the
negative supply positive “+” to GND and the negative supply negative “-” to V-. This is shown in Figure
3 above.
Note: When designing a system E-stop, never cut the motor leads. Doing so will result in a runaway
condition and may damage the TA333. Always cut the incoming DC supply (crowbar with a low value
resistor) to the TA333 to produce a rapid stop.

Trust Automation, Inc. TA333 High Power Linear Servo Amplifier
10-Apr-09 Page 13 of 38
1.13 Optional External 24VDC Supply
The TA333 internal logic may optionally be powered by an external 24VDC (±5%) source for
convenience when using serial monitoring or in extremely noise sensitive applications. The external
power connection is at J1. The internal 24V source provides power by default automatically but is
disabled if an external source is connected.
When internally powered, some low level noise may be generated by this supply that may have an
effect on the drive performance. While the noise level is small, it may be a factor depending on the
application. When externally powered, the electrical noise level is further reduced, providing the
quietest operation possible. When externally powered, there will be 50-100mV of random electrical
noise on the motor outputs. When internally powered, there will be about 150mV at 160 kHz riding on
the background 50-100mV of random noise.
1.14 Power Dissipation Calculations
Since the TA333 Power stage is linear, voltage not applied to the motor is converted directly to heat.
Heat generated by the drive is directly proportional to the voltage drop (across the amplifier) multiplied
by the motor current. (Think of a linear amplifier as a large variable resistor, current out = current in.)
Heat dissipation is a critical factor when the motor is in a stalled motion condition. (low voltage at the
motor, but high current output). The heatsink is limited to a maximum of 600W continuous dissipation.
Peak dissipation is limited to 1350W for a very short time period (<1ms). A practical design should limit
peak dissipation to 1000W or less. Actual dissipation limits depend on specific conditions including
temperature, load dynamics and event time. For most accurate peak dissipation allowable, see SOA
chart. (See section 2.4)
The TA333 features a microprocessor that constantly monitors the wattage across the drive to protect
the Class-AB power stage from damage. At any given moment in time there is one power device (upper
or lower) that is handling the majority of the drive wattage regardless of whether the load is a floating
brushless motor or a ground-referenced brushed-type load. Calculations are based on the highest
current and voltage across any phase with respect to the power supply ground.
When predicting SOA wattage limits with a brushless motor (or single brushed-type motor in bridge
mode), use half of the expected voltage across any pair of phase leads against the voltage of one of
the two supplies.
For a brushed-type load that is directly referenced to the power supply ground, use the full predicted
voltage across the motor against one of the two supplies.
Brushless example:
Assume a have a pair of 72V supplies and a motor that is expected to require 15A peak load at a phase
to voltage requirement of 20V according to calculations. Because a brushless motor voltage is specified
as phase-to-phase, we will divide the predicted voltage in half to give a ground referenced motor
voltage of 10V.
PD= Imotor (Vsupply – Vmotor)
Imotor = 15A [calculated based on required torque]
Vmotor = 10V [calculated based on velocity]
Vsupply = 72V [one of two 72V supplies]

Trust Automation, Inc. TA333 High Power Linear Servo Amplifier
10-Apr-09 Page 14 of 38
PD= 15A (72V-10V)
= 930W *
* This is over the 600W continuous dissipation rating so there will be a short time limit applied based on
the SOA chart before FAULT is generated. See SOA chart. (See section 2.4)
Dual-brushed example:
Assume a pair of 48V supplies and a motor that is expected at any one time to require 10A peak load at
a phase voltage requirement of 12V according to calculations. Because the motor(s) are referenced to
the power supply ground, the calculations are based on the full motor voltage.
PD= Imotor (Vsupply – Vmotor)
Imotor = 10A [calculated based on required torque]
Vmotor = 12V [calculated based on velocity]
Vsupply = 48V [one of two 48V supplies]
PD= 10A (48V-12V)
= 360W *
* This is under the 600W continuous dissipation rating, but the current is over the 6A continuous, so
there will be a time limit applied based on the SOA chart before FAULT is generated (10A @ 30c =
~3.2sec before fault). (See SOA chart, section 2.4)
1.15 Motor Connections
The TA333 motor connections are made at connector J5. The available output voltage is limited to the
supply voltage, less approximately 8V off each rail. With ±48V supplies, there will be 80V available
across the motor before the output starts to clip. Pin 1 on J5 is earth ground and is electrically isolated
from all power connections. By physically connecting the TA333 chassis and the motor chassis to an
earth ground, immunity from external noise sources is increased.
Note: When designing a system E-stop, never cut the motor leads. This will result in a runaway
condition and may damage the TA333. Always cut the incoming DC supply (crowbar with a low value
resistor) to the TA333 to produce a rapid stop.
Brushless Motor
The phase outputs A, B and C correlate to most motor callouts as U, V and W or in some cases R, S
and T. (See application examples 5.1, 5.2, and 5.3)
Brushed Motor in Bridged Mode
To drive a single brushed motor in bridge mode, connect the motor “+” lead to the A phase output and
the motor “–” lead to the C phase output. This configuration allows the full bipolar supply voltage to be
driven across the motor in any direction of rotation. The motor can be a traditional brushed or voice coil
type. (See application example 5.4)

Trust Automation, Inc. TA333 High Power Linear Servo Amplifier
10-Apr-09 Page 15 of 38
Dual Brushed Motor Mode
Two independent motors or one stepper type motor may be driven in this configuration. For two
brushed-type motors (or voice coils) connect the (+) lead of the first motor to the A phase output (drive
with the A command) and connect the (–) lead to the power supply common (Pin 2 on J6). Connect the
second motor (+) to the B phase output (drive with the B command) and the (–) lead to the power
supply common. (See application example 5.5)
Stepper Motor
Two coil sets on a stepper type motor may be driven in this configuration. This configuration is the
same as the dual brushed mode except that the two coil sets are in the same motor. The linear
command is driven on command A and B with a motion controller setup to drive a stepper motor
sinusoidally. (See application example 5.6)
1.16 Serial Monitoring
The TA333 has a high speed data port for monitoring drive performance and logging of fault conditions.
The five pin port at J2 provides access to a TTL serial data stream presented at 230,400 baud. Set up a
terminal program (such as HyperTerminal) with the baud rate set to 230,400 bits per second, 8-bit data,
no parity, 1 stop bit, and flow control to no handshaking.
An optional TTL to USB serial cable may be ordered as CBLZ-0910-01 to facilitate connection to a PC.
Reference the FTDI installation guide for installing the TTL to USB serial cable.
Figure 4 – Com Port Settings for Serial Communication
When the TA333 is powered up, the serial port will transmit the firmware version and the drive mode
set by SW1 position 5 through 8. (See section 4.10 for more information)
Figure 5 - Firmware Version and Drive Mode

Trust Automation, Inc. TA333 High Power Linear Servo Amplifier
10-Apr-09 Page 16 of 38
Once the TA333 is enabled, data will begin transmitting in the following format:
Figure 6 – Data Transmission Format, HyperTerminal
Figure 6 shows the drive set to brushless motor mode, no faults, heatsink at 22°C, positive supply at
24V and negative supply at 24V. There is less than 1A current flow and integer math has placed the
dissipation at 9W.
The data stream may be stopped by transmitting “s” followed by “Rtn.” The data stream will resume
upon sending the “s” + “Rtn” sequence again. Data layout is formatted as:
Data field Data Name Description
1 Fault Amp fault data (See fault chart)
2 Temp, Celsius Temperature of heat sink, SOA de-rated as temperature rises.
3 Phase Voltage The captured phase voltage
4 + Supply V Positive supply voltage
5 - Supply V Negative supply voltage
6 Phase Current The highest captured phase current
7 Wattage Amp dissipation wattage based on data gathered
Table 1 – Data Transmission Format
Faults are formatted as:
Table 2 – Fault Codes
Fault Name Description
0x0000 No Fault Operation Normal
0x0002 Temp Over temp fault at 70c, The TA333 will disable @ 90c
0x0001 Supply Under voltage @ 20V, Over voltage @ 105V
0x0004 Current Over current fault based on time limit and SOA
0x0008 Wattage Over continuous wattage limit based on time and SOA
0x0010 Peak Wattage Peak wattage limit based on time and SOA
0x0020 Enable Enable fault if drive is powered up in the enabled state

Trust Automation, Inc. TA333 High Power Linear Servo Amplifier
10-Apr-09 Page 17 of 38
The TA333 captures the last ten fault conditions that have occurred. This data can be accessed by
sending “p” followed by “Rtn” either before enabling or after sending the stop “s” command.
Figure 7 – Sample Fault Printout
If the TA333 is powered up with the optional 24V input and the enable signal is active, two faults will be
generated. The first reported fault will be 0x0020 enable fault followed by 0x0021, indicating there is a
supply fault in addition to an enable fault.

Trust Automation, Inc. TA333 High Power Linear Servo Amplifier
10-Apr-09 Page 18 of 38
2.0 General Specifications
2.1 Electrical Specifications
Feature Units
V
alue
Supply Voltage (Bipolar) V ± 24 – ± 100
Equivalent Motor Voltage V Vsup – 8V (~ 8V from either supply rail)
External 24V Supply VDC 24 ± 5% @ 1.0A
Maximum Output Current A 25 (See SOA Chart section 2.4)
Continuous Output Current A 6 RMS (8.6 Peak)
Quiescent Bias Current A ~0.5 (Class A/B biasing current)
Fault V 5 TTL Level 0 or 1
Enable V 5 TTL Level 0 or 1
Command Input V ±10 (±12 absolute max)
Command Input Impedance kΩ10
Torque Gain A/V 1.0 - 2.5
Bandwidth kHz 5.0 (0.820mh / 0.65 ΩLoad)
Harmonic Distortion THD % 0.036 (Voltage to Current)
Signal to Noise ratio SNR db -79.06 (1A @ 1kHz)
Trapezoidal Bandwidth kHz 3.0 (Consult factory for higher speeds)
Min Load Inductance mH 0.100
Min non-inductive load Ω2.0
Table 3 – Electrical Specifications
2.2 Mechanical Specifications
Feature Units
V
alue
Length in (cm) 14.90 (37.85)
Width in (cm) 7.69 (19.53)
Height in (cm) 4.70 (11.94)
Weight lb (kg) 13.5 (6.12)
Table 4 – Mechanical Specifications
2.3 Environmental Specifications
Feature Details
Maximum Altitude 6,560ft (2,000 meters)
Temperature (ambient)
Normal operation 5°C to +40°C
Temperature de-rating See SOA Chart – Section 2.4
Storage -40°C to +70°C
Heatsink +70° C Maximum
Heat Dissipation (@ 25°C)
Continuous 600W
Peak 1350W, See SOA Chart – Section 2.4
Airflow Internal fans, variable speed, thermally controlled
Humidity
Operating 10% to 70%, non-condensing
Storage 10% to 95%, non-condensing
Pollution Degree 2 Non-conductive, non-condensing
Table 5 – Environmental Specifications

Trust Automation, Inc. TA333 High Power Linear Servo Amplifier
10-Apr-09 Page 19 of 38
2.4 TA333 Safe Operating Area Curve (SOA)
The TA333 features a micro processor that constantly monitors the operating conditions on the
amplifier to prevent damage. This processor continuously calculates the dissipated wattage and sets a
fault threshold based on heatsink temperature, supply voltage, and motor current. The formulas for
calculated limits are current, wattage and temperature.
Current Limit
For currents that result in a dissipation wattage below 600W, the processor limits the time
logarithmically from infinite time at 6A down to 500ms at 25A. (See current vs. time graph).
Wattage Limit
If the resulting dissipation wattage exceeds 600W, the time to fault is much shorter as it is now
operating in the “knee” of the SOA curve. (See wattage vs. time graph).
Temperature Limit
The microprocessor takes into account the heatsink temperature when calculating the wattage time
limit. Time to fault is de-rated at about 15ms per 20°C rise. (See temp vs. time for an example at
876W). If the heatsink temperature exceeds 70°C FAULT is generated, and at 90°C the drive will
shutdown.
Figure 8 – TA333 SOA Curve

Trust Automation, Inc. TA333 High Power Linear Servo Amplifier
10-Apr-09 Page 20 of 38
Current vs. Time
5
7
9
11
13
15
17
19
21
23
25
500 1500 2500 3500 4500 5500 6500
Time (ms)
Current
Figure 9 – Output Current vs. Time Graph for Time to Fault @ ~30°C
Wattage vs. Time
600
700
800
900
1000
1100
1200
1300
1400
15 25 35 45 55 65 75 85
Time (ms)
Wattage
Figure 10 – Dissipation Wattage vs. Time for Time to Fault @ ~30°C
Table of contents
Popular Amplifier manuals by other brands
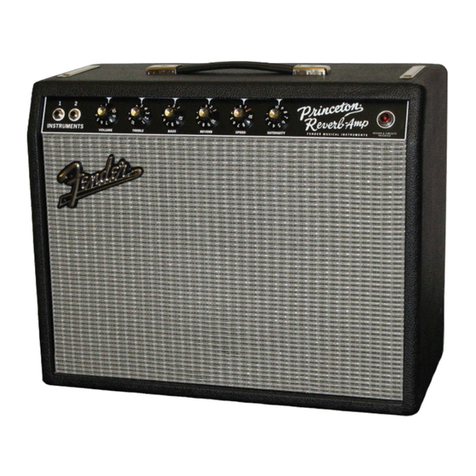
Fender
Fender 65 Princeton Reverb-Amp owner's manual
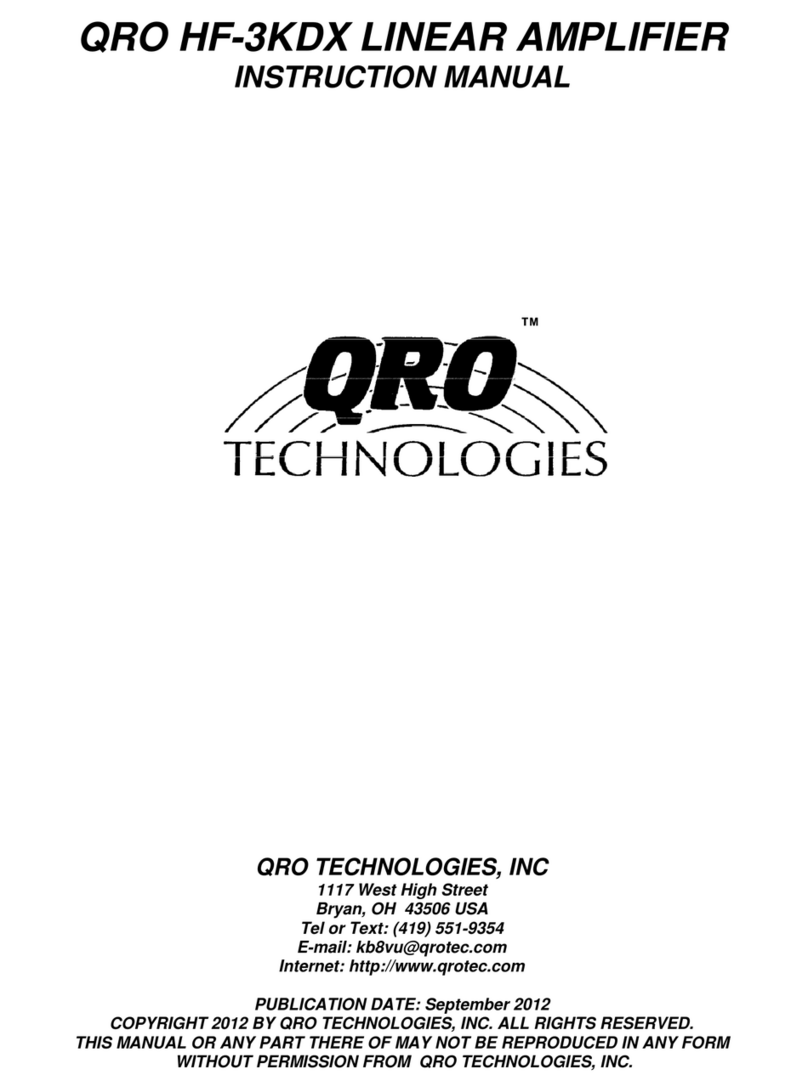
QRO Technologies
QRO Technologies HF-3KDX instruction manual
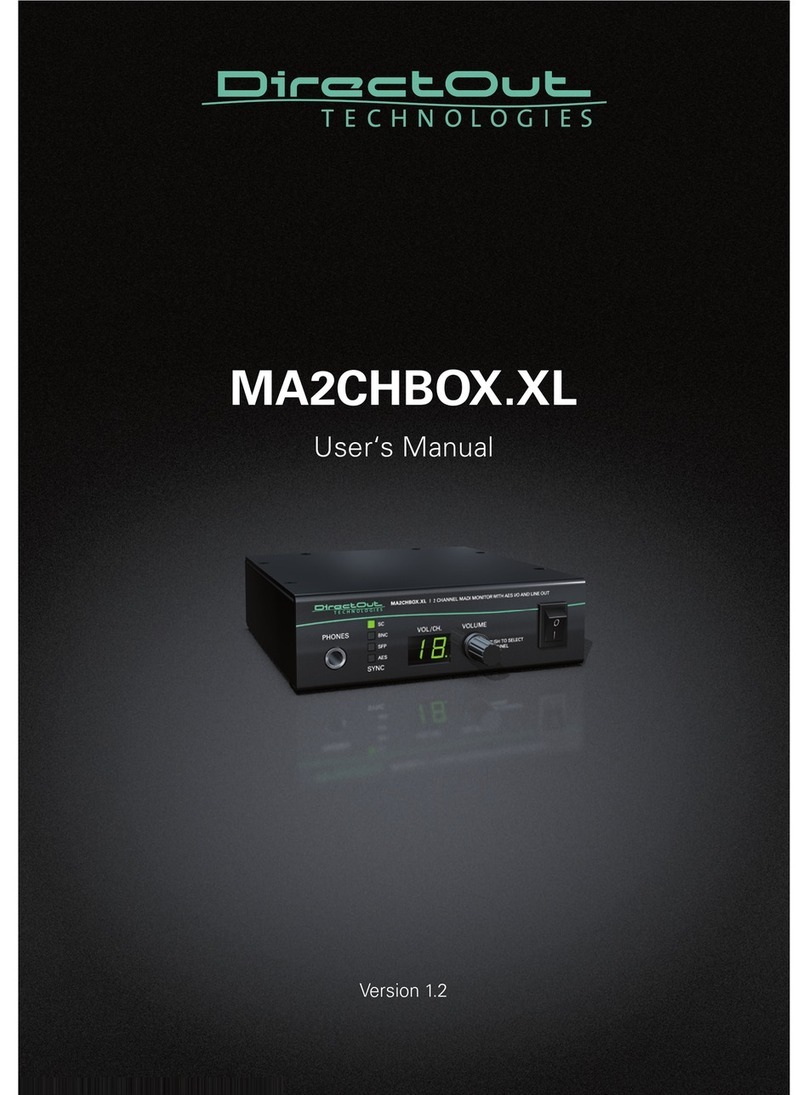
DirectOut Technologies
DirectOut Technologies MA2CHBOX.XL user manual

Teledyne
Teledyne PowerMAX Operation manual
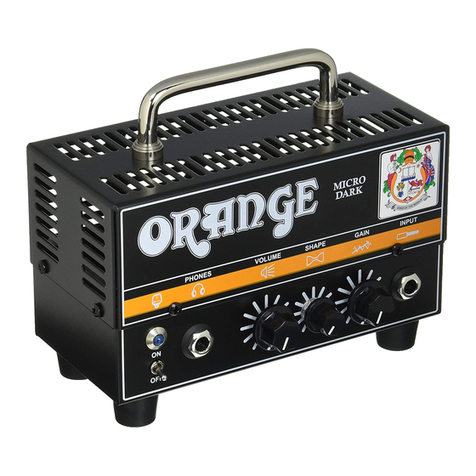
ORANGE
ORANGE MICRO TERROR quick start guide

Tone Bliss
Tone Bliss Sparkle user guide