Akron DECKMASTER 3440 Assembly instructions

127006
STYLE 3440 DECKMASTER™ ELECTRIC MONITOR FOR
STANDARD CONFIGURATION WITH POTENTIOMETERS & U2 LOGIC BOX
INSTALLATION, OPERATING, AND MAINTENANCE INSTRUCTIONS
The following is intended to provide the basic instructions for installation, operation and maintenance.
Read and understand these operation instructions before use.

Page 2
Product Ratings
Electrical Specifications
MOTOR
12-VOLT SYSTEM (11-14 Volts DC) 24-VOLT SYSTEM (22-28 Volts DC)
Maximum
Operating Current
Normal*
Operating Current
Maximum
Operating Current
Normal*
Operating Current
Rotation 14 Amps 3-10 Amps 7.5 Amps 2-5 Amps
Elevation 14 Amps 3-10 Amps 7.5 Amps 2-5 Amps
Swing Arm 14 Amps 3-10 Amps 7.5 Amps 2-5 Amps
Pattern** 3-10 Amps 0.7-5.0 Amps 1.5-5.0 Amps 0.4-2.5 Amps
* Normal operating currents depend on operating conditions such as pressure, ow, etc.
** Pattern currents depend on the type of nozzle being used.
Mechanical Specifications
Parameter U.S. Measure Metric
Measure
Maximum Flow Rate 1250 GPM 4800 LPM
Maximum Pressure 200 PSI 14 Bar
Mass 55 Lbs. 25 kg
Tools Required
• Wrench for ange mounting bolts
• 1/2” hex head wrench in case there is a need to change the hard stop locations
Safety Symbols
Indicates a hazardous situation which, if not avoided, WILL result in death or serious injury
Indicates a hazardous situation which, if not avoided, COULD result in death or serious injury
Indicates a potentially hazardous situation which, if not avoided, may result in minor or moderate injury
Addresses practice not related to personal injury
Product Warnings, Cautions and Notices
Use only for reghting by trained operators.
Charge the unit slowly. Rapid charging may cause a pressure surge that has the potential to cause
an injury, or damage the monitor.
Do not stow or deploy the monitor while owing. Pressing the Stow or Deploy button causes the
nozzle to move automatically and the water stream may cause damage to equipment or injury
to personnel.
Aim the unit in a safe direction before pumping water through it, e.g., away from power lines.
Do not use the electric controls when the manual override cranks are being used or are in
position for use.
Do not exceed the maximum pressure or ow ratings of the monitor. Exceeding these ratings may
lead to an injury or may cause damage to the monitor.

Page 3
Do not install shutoffs on the outlet of the monitor. Shutoffs increase the potential for pressure surges
due to water hammer, which have the potential to cause an injury or damage the monitor.
Disconnect power and disable ow before maintenance.
Keep all personnel out of the Danger Zone, in front of the outlet of the monitor when the water source
is attached. Dangerous ow velocities can cause serious injury.
Ensure the thread on the nozzle swivel matches the thread on the monitor outlet. Do not
over-tighten the nozzle onto the unit.
Insufcient structural support at the inlet ange can lead to failure, which has potential to cause
an injury.
Not designed for explosive environments
The monitor contains moving parts. Keep hands, ngers and objects away from pinch points.
Operating the monitor without the permanent travel limit stops in place could cause damage to the
monitor and could potentially injure the operator.
Ensure that the monitor is returned to the Stow position after use.
If not equipped with an automatic drain valve, drain the monitor after use to prevent freeze damage.
The monitor, nozzle, logic box, control box, tether controller and eld adjustable stops are made for
optimal performance. Do not alter in any manner.
The monitor was designed for use with the 5177Akromatic, 1577 SaberMaster or 2499 Stack Tip
nozzles. Use of any other nozzle could affect the speed or operation of the unit and should be tested
before being put into service.
Replace the identication tags if they should become worn or damaged.
Not recommended for use in salt water applications
Not recommended to mount onto a raised ange. This may cause damage to the monitor’s ange
when tightening bolts.
Use a nozzle of the same material as the monitor to eliminate the effects of galvanic corrosion.
Mechanical Installation Instructions
The monitor is to be mounted on a waterway which is capable of withstanding the pressure applied to the monitor as
well as the reaction force and resulting bending moment of the nozzle (934 lbs. at 200 PSI and 1250 GPM).
Use the operating windows of gures 1a or 1b to determine the mounting area required.

Page 4
FIGURE: 1A - Operating Window
14-3/32
38-17/32
14-5/16
14-11/32
24-7/32
7-1/2
11-9/32
5-5/16
16-5/8
14-11/32 4-7/16
18-25/32
19-5/32
17-1/32
27-23/32
4-7/16
5-5/16
11-9/32
16-5/8
18-25/32
23-9/32
DECKMASTER WITH 5177 AKROMATIC NOZZLE
-45~ +225 ~
DEPLOYED
(LEFT SIDE VIEW)
DEPLOYED
(TOP VIEW)
+170 ~
-170~
STOWED
(TOP VIEW - NOZZLE AT +90~)
STOWED
(LEFT SIDE VIEW - NOZZLE AT +90~)
STOWED
(TOP VIEW - NOZZLE AT 0~)

Page 5
FIGURE: 1B - Operating Window
15-21/3
2
15-21/32
13-5/32
39-7/8
7-1/2
24-7/32
5-5/16
16-5/8
4-7/16
18-27/32
18-11/32
19-1/4
11-9/32
14-3/8
4-7/16
29-1/32
24-9/16
18-25/32
5-5/16
16-5/8
11-9/32
DECKMASTER WITH 1578 SABERMASTER NOZZLE
-45~ +225 ~
DEPLOYED
(LEFT SIDE VIEW)
DEPLOYED
(TOP VIEW)
+170 ~
-170~
STOWED
(TOP VIEW - NOZZLE AT +90 ~)
STOWED
(LEFT SIDE VIEW - NOZZLE AT +90~)
STOWED
(TOP VIEW - NOZZLE AT 0~ )

Page 6
Bolt Spec and Tightening Procedure
Use four 5/8” bolts and nuts of grade ve minimum and suitable washers. There must be a minimum of six threads of
engagement. Use a ring gasket conforming to ASME 16.21. The notch that is cut into the side of the inlet ange is the
front of the monitor (see Figure 2).
Start the bolt tightening procedure by lubricating the nuts and bolts. Hand tighten the nuts until they are snug against
the ange. The nal torque of the bolts should be a maximum of 100 lb-ft. Following the correct sequential order as
shown in gure 2, tighten the bolts to 30% of the nal torque. Repeat the tightening sequence to 60% of the nal
torque. Repeat a third time to 100% of the nal torque. Finally, repeat the sequence at the nal torque.
Rotational Hard Stops
The stainless steel rotational hard stops set the boundaries for the area that the monitor is allowed to travel left
(counterclockwise) and right (clockwise). The stop in the lower row controls the left (CWW) travel, and the stop in the upper
row controls the right (CW) travel. Refer to gure 3 for the locations of the upper row and the lower row, as well as points 1-5.
The monitor is shipped with a stop in the lower row at point 1, which stops the monitor at -170° CCW, and a stop in the
upper row at point 5, which stops the monitor at +170° CW. To set a different boundary area, swap the positions of the
steel hard stop and a plastic plug. Refer to gure 4 to select a desired boundary area. Both the stops and the plugs
have a 1/2” hex head.
FIGURE: 2 - Bolt Torque Order
FIGURE: 3 - Hard Stop and Plug Locations
HARNESS
JUNCTION BOX
#2
#3
NOTCH AT
FRONT OF
MONITOR
#4
#5
UPPER ROW
LOWER ROW
HARNESS
JUNCTION BOX
#1
#2
#3
#4

Page 7
FIGURE: 4 - Boundary Areas Set by Rotational Hard Stops

Page 8
Nozzle Installation
The nozzle should be threaded onto the outlet of the monitor. Place the pattern actuator in a position that does not
stretch the power cord, and then tighten the swivel. Verify that the actuator orientation does not interfere with
the monitor.
Controller Box Installation
This monitor is used with a 6032 Universal II Controller. It normally mounts on or below the deck and must be mounted
close enough to the monitor so that the 10 foot cable of the monitor wiring harness has sufcient slack to allow the
monitor to travel through its full rotational range. Refer to the “6032 Universal II Controller Installation, Operation &
Maintenance Manual” (part number 122552) as a guide.
Do not extend the monitor wiring harness.
Electrical Installation Instructions
Make the I/O and power connections to the 6032 controller and then plug the monitor harness into the controller. Refer
to the “6032 Universal II Controller Installation, Operation & Maintenance Manual” (part number 122552) as a guide
Harness 721582 for Power & Signal Connector J1 on Controller
Contact Position Function Comments Wire Color & Size
1 Power In – Vehicle Battery (+12/24 VDC) Red – 12 AWG
2Power In – Vehicle Battery (−) Black – 12 AWG
3 Power In – Auxiliary Battery (+12/24 VDC) (Optional) Green – 12 AWG
4Power In – Auxiliary Battery (−) (Optional) Black – 12 AWG
5 Output – H-Bridge #5A Red – 16 AWG
6 Output – H-Bridge #5B Black – 16 AWG
7 Output – Logic #1 Panel LED Brown – 16 AWG
8 Output – Logic #2 Discharge Red – 16 AWG
9 Output – Logic #3 Orange – 16 AWG
10 Output – Bi-stable Relay Common Yellow – 16 AWG
11 Output – Bi-stable Relay N.O. Green – 16 AWG
12 Output – Bi-stable Relay N.C. Blue – 16 AWG
13 Input – Switch #1 (System Enable) Brown – 18 AWG
14 Input – Switch #2 + Right / Left - Red – 18 AWG
15 Input – Switch #3 + Up / Down - Orange – 18 AWG
16 Input – Switch #4 + Stream / Fog - Yellow – 18 AWG
17 Input – Switch #5 + Valve Open / Close - Green – 18 AWG
18 Input – Switch #6 + Gallonage High / Gallonage Low - Blue – 18 AWG
19 Input – Switch #7 + Oscillate Set / Pause - Violet – 18 AWG
20 Input – Switch #8 + Deploy / Stow - Gray – 18 AWG
21 Input – Switch #9 + Aux Agent 2 / Aux Agent 1 - White – 18 AWG
22 Power Out – Peripheral (+12/24 VDC) Powers the System Enable (#13) Brown – 18 AWG
23 Data – J1939 CAN High (+) Yellow – 18 AWG
24 Data – J1939 CAN Low (−) Green – 18 AWG
25 Power Out – Peripheral (−) Drain – 18 AWG
26 Data – Proprietary CAN High (+) (Unused) Sealing Plug
27 Data – Proprietary CAN Low (−) (Unused) Sealing Plug
28 Data – V-Mux Com A (+) (Unused) Sealing Plug
29 Data – V-Mux Com B (−) (Unused) Sealing Plug
Table 1 – Power & Signal Harness Connections

Page 9
The DeckMaster comes tted with a harness and connector ready for direct plug-in to the Universal II controller. While
this is congured for “plug and play” installation, removal of the connector to run through a bulkhead may be necessary
from time to time. In that event, or in the event of troubleshooting, the following table is provided for reference.
Deutsch Plug for J2 Connector on Controller (Part No. HDP26-18-14SN-L017)
Contact Position Wire Color Function
A Black Power Out – Switch and Position Sensor (−)
B White Input – Rotation Switch (Voltage)
C (Sealing Plug) Input – Multifunction #2 (Unused)
D Red Input – Swing Arm Position Sensor (Voltage)
E Green Power Out – Position Sensor (+5 VDC)
F (Sealing Plug) Data – Lin Bus (Unused)
G Orange Output – Rotation Motor (Right)
H Blue Output – Rotation Motor (Left)
J White/Black Output – Elevation Motor (Up)
K Red/Black Output – Elevation Motor (Down)
L Green/Black Output – Pattern Motor (Stream)
M Orange/Black Output – Pattern Motor (Fog)
N Blue/Black Output – Swing Arm Motor (Deploy)
P Black/White Output – Swing Arm Motor (Stow)
Table 2 – Monitor Harness Connections
3440 DeckMaster with UII control Initial setup
The following functions can be congured in the setup mode:
• Monitor Orientation (sideways or inverted mounting)
• Restore Factory Defaults
• Obstacle Avoidance
• Electric Riser Disable/Enable
• Stow and Deploy Positions
To enter the setup mode, follow these steps:
1. Turn power off to the Universal II Controller.
2. Press and HOLD the Stream switch (can be done on the Joystick or the Toggle Switch Box).
3. Turn power on to the Universal II Controller while continuing to hold the Stream switch.
4. Wait 3-4 seconds and release the Stream switch.
The Universal II Controller should now be in setup mode. When in setup mode, the LED on the operator station will
be slowly blinking (a short blink followed by a long pause). If it is not slowly blinking, repeat steps 1-4 above.
FIGURE: 5
FRONT VIEW
F
G
HJ
K
A
B
C
D
E
L
M
N
P
SIDE VIEW REAR VIEW
M
L
KJ
H
C
B
A
D
N
G
F
E
P
DEUTSCH
HDP 26-18-14SN-L017
DEUTSCH
0411 -310-1605
CONTACT
REMOVAL TOOL
DEUTSCH
0462 -201-16141
SOCKET
CONTACT

Page 10
All setup functions except the Stow and Deploy Positions can be scrolled through by pressing the Stream switch. Each
time the Stream switch is pressed, another function is active for conguration. If a function is congured and saved
using the Fog switch, the next function will be automatically selected. Activating the Stream command will abort this
function without storing the position and the next function will be selected. Entering the Stow and Deploy Positions
programming modes can only be accomplished by activating the Stow or Deploy switch while at the start of the setup
menu (LED Code 1 Slow blink). (See the sections for Stow Position and Deploy Position for more detail).
To aid in determining which setup menu the monitor is in, the LED on the operator station has been programmed to blink
a different code for each function. Table 3-1 below lists the LED codes for each function. The codes have two parts.
The LED code will start with either one, two, three or four short blinks, a short pause (LED off), another series of short
blinks, then a long pause (LED off). The rst number in the LED code is the one, two, three or four blinks and the second
number is the second series of blinks before the long pause. If an OEM is using their own operator station that has no
LED, the codes will also be available on pin #7 of the 29 pin interface connector on the UII logic box.
Setup Parameter Blink Code 34405XXX Position Feedback Units
Beginning of setup 0-1 (One slow blink) Programming Order (See Notes)
Right Soft Limit 1-1 NOTE 2
Left Soft Limit 1-2 NOTE 2
Up Soft Limit 1-3 NOTE 2
Down Soft Limit 1-4 NOTE 2
Stow 1-5 NOTE 4
Deploy 1-6 NOTE 4
Monitor Orientation 1-7
Zero Position Sensors 1-8 NOTE 1
Restore Factory defaults 1-9
Obstacle avoidance Disable 2-1
Obstacle Avoidance Manual Operation 2-2 NOTE 3
Obstacle Avoidance Auto Operation 2-3 NOTE 3
Obstacle Avoidance Learn 2-4 NOTE 3
Stow rotation position 2-7 NOTE 4
Electric Riser disable 3-1
Electric Riser enable 3-2
CAN Valve Disable 4-1
CAN Valve Enable 4-2
CAN Valve Pair 4-3
CAN Valve Calibrate 4-4
NOTES:
1. This step only needs to be done in two cases. If there is a position indicator in the system and/or the monitor is
mounted such that the physical rotational zero position is not in line with the physical center of the apparatus.
If needed, this step must be done rst before setting ANY other positions. This setting will erase any previously set
positions including obstacle avoidance and stow/deploy.
2. These steps must be performed. The soft limits must be programmed so that the monitor stops before hitting a
hard limit. Hitting a hard limit will cause a sensor error code. If there is an active sensor error code, all soft limits and
automatic functions (stow/deploy, oscillation and obstacle avoidance) are ignored and the monitor will move
throughout its entire physical range with no restrictions which could cause collisions with the truck or truck
mounted obstacles.
3. These steps are optional and depend on the application needs.
4. Stow/Deploy position programming should be done after soft limits and obstacle avoidance (if used)

Page 11
(Setup Continued)
1. If further programming is needed, turn system power off, press and hold the “Stream” switch and turn system
power back on. Within a few seconds, the LED on the control panel will begin to blink once approximately
every three seconds.
2. To program a new deploy position, momentarily press the “Deploy” switch. The monitor will proceed to the
default deploy position and stop. The LED on the control panel will be blinking a code of 1-6 meaning you are
in deploy setup mode. After the monitor stops, use right/left/raise/lower controls to position the monitor nozzle
to the desired deploy position.
3. When the nozzle is in the desired position, you can save it by pressing either the “Stream” or “Fog” switches.
If you use the “Stream switch” the nozzle will go to the stream position during deploy. If you use the “Fog”
switch, the nozzle will go to the fog position during deploy.
4. Once the position has been saved, the LED on the control panel will go back to blinking once every three
seconds. From this point, you can reset the UII logic box by momentarily pressing the fog switch and it will
reboot into normal operation mode or continue to step 5 to program the stow position.
5. To program a new stow position, momentarily press the “Stow” switch. The monitor will proceed to the default
stow position and stop. The LED on the control panel will be blinking a code of 1-5 meaning you are in stow
setup mode. Only the nozzle elevation can be set for the stow function. Use the “Raise” or “Lower” controls to
move the nozzle to the desired position.
6. When the nozzle is in the desired position, you can save it by pressing either the “Stream” or “Fog” switches.
If you use the “Stream switch” the nozzle will go to the stream position during stow. If you use the “Fog”
switch, the nozzle will go to the fog position during stow.
7. Once the position has been saved, the LED on the control panel will go back to blinking once every three
seconds. From this point, you can reset the UII logic box by momentarily pressing the fog switch and it will
reboot into normal operation mode or continue to step 2 below to program the Home position.
POSITION SENSORS
The DeckMaster monitor has been provided with two potentiometers and a Swing Arm Sensor. The two potentiometers
measure the position of the elevation and rotation. The “Home” position is set at the factory for the middle of the
rotation range and coincides with the monitor facing the forward physical position (in line with the vertical groove on
the outside diameter of the mounting ange). The home position can be adjusted to allow the monitor to stow at any
rotational position between the rotational stops. The Swing Arm Sensor determines which position the Swing Arm
(center elbows) are in, Stowed, Deployed or somewhere in between. It puts out a different signal for each of the three
positions that the logic box uses for proper sequencing and error reporting. These signals are also visible as different
colored LED’s on the face of the sensor. See gure below.
To Adjust the Home Position:
1. Enter the setup mode. See instructions above for entering the setup mode.
2. Using the “Stream switch, advance to setup code 2-7.
3. Operate unit left or right to desired Home position.
4. Press the “Fog” switch to store the Home position.
5. Cycle power on to the Universal II Controller. The monitor will now stow at the new Home position.
RAISED
LOWERED
(Red)
(Yellow)
(Green)
Swing Arm
Senser

Page 12
OPERATING INSTRUCTIONS
A. PANEL CONTROLLER OPERATION
The panel controller is used to control the monitor and nozzle.
1. To deploy the monitor for use:
2. Locate the STOW/DEPLOY switch and push the toggle switch up for three seconds and release.
3. To stow the monitor after use:
4. Locate the STOW/DEPLOY switch and push the toggle switch down for three seconds and release.
5. To change the horizontal monitor position toward the right or left:
6. Press the proper toggle switch toward “RIGHT” or “LEFT” respectively, as labeled on the controller, until the
desired position is reached.
7. To change the vertical monitor nozzle position upward or downward:
8. Press the proper toggle switch toward “RAISE” or “LOWER” respectively, as labeled on the controller, until the
desired position is reached.
9. To change the nozzle pattern toward the straight stream or fog position:
10. Press the proper toggle switch toward “STRAIGHT” or “FOG” respectively, as labeled on the controller, until the
desired nozzle position is reached.
B. MANUAL OVERRIDE CONTROLS
The manual override control is to be used only when the power to the monitor is off. A single override crank with a 1/4”
hex drive is provided and attached to the monitor for use on both the horizontal and vertical override controls and the
stow/deploy control. To use the manual override, insert the hex drive end of the override crank into the hexagon shaped
hole on the shaft end opposite the motor. Rotate the override crank in the desired direction to aim the monitor.
When the override crank is no longer in use, put it back in the storage position. Do not use the
electric controls when the override crank is being used or is in position for use.

Page 13
MAINTENANCE INSTRUCTIONS
Your DeckMaster monitor and nozzle should be inspected prior to and after each use to ensure it is in good operating
condition. Periodically, an unanticipated incident occurs where the unit is misused in a manner that is inconsistent with
standard operating practices. A partial list of potential misuses includes:
• Operating above the maximum rated pressure or ow.
• Prolonged exposure to temperatures above 130°F, or below -25°F.
• Operating in a corrosive environment.
• Having the DeckMaster nozzle hit a xed object during operation or transportation.
• Any other misuse that might be unique to your specic environment.
Also, there are many “tell tale” signs that indicate repair is in order, such as:
• Controls that are either inoperable or difcult to operate.
• Excessive wear
• Poor discharge performance
• Water leaks.
If any of the above situations are encountered, the DeckMaster monitor should be taken out of service, repaired, and
tested by a qualied technician before placing back in service.
Greasing of the elevation and rotation joints is not required under normal operating conditions. Check the motor
operating current periodically to conrm the current is within the Normal Operating Current ranges listed under Product
Ratings. If the current has risen above the normal range, it may be necessary to add additional grease to the joint or to
overhaul the joint to clean and replace the grease. See Table 1 and Table 2 below for grease volumes.
Periodically inspect the condition of the grease in the elevation and rotation joints. See the tables below for
recommendations regarding the condition of the grease.
Do not apply grease more frequently than 1 time per month.
Standard recommended grease is Lubriplate Low Temp. This is an anhydrous calcium, NLGI 1.5 grade lubricant. The
color is white.
For extreme or harsh environments or for continuous duty usage applications, Mobilith SHC460 grease is recommended.
This is a synthetic hydrocarbon grease + lithium complex soap thickener, NLGI 1.5 grade lubricant. DIN 51825: KPHC1-
2N-40. The color is red.
Use of any grease with an NLGI rating higher than 1.5 is not recommended. This may result in excessive operating
currents/stalled motors.
Grease Condition Evaluation (Standard Lubriplate Low Temp grease):
Color: Action:
White None
Gray Add grease to the joint according to Table 1 be-low
Black Component needs overhaul. Clean and remove old
grease. Reapply grease to ball races and gears prior
to re-assembly according to Table 2 below.
Grease Condition Evaluation (Optional Grease: Mobilith SHC460):
Color (Standard Lubriplate Low Temp grease): Action:
Red None
Reddish Brown Add grease to the joint according to Table 1 be-low
Black Component needs overhaul. Clean and remove old
grease. Reapply grease to ball races and gears prior
to re-assembly according to Table 2 below.
Table 1: Adding Grease to an Assembled Monitor
Joint: Grease volume:
Rotation 1.0 oz. (29mL)
Elevation 0.25 oz. (7.4mL)

PHONE: 330.264.5678 or 800.228.1161 I FAX: 330.264.2944 or 800.531.7335 I akronbrass.com
WARRANTY AND DISCLAIMER: We warrant Akron Brass products for a period of five (5) years after purchase against defects in materials or workmanship. Akron Brass will repair or replace product
which fails to satisfy this warranty. Repair or replacement shall be at the discretion of Akron Brass. Products must be promptly returned to Akron Brass for warranty service.
We will not be responsible for: wear and tear; any improper installation, use, maintenance or storage; negligence of the owner or user; repair or modification after delivery; damage; failure to follow
our instructions or recommendations; or anything else beyond our control. WE MAKE NO WARRANTIES, EXPRESS OR IMPLIED, OTHER THAN THOSE INCLUDED IN THIS WARRANTY STATEMENT,
AND WE DISCLAIM ANY IMPLIED WARRANTY OF MERCHANTABILITY OR FITNESS FOR ANY PARTICULAR PURPOSE. Further, we will not be responsible for any consequential, incidental or
indirect damages (including, but not limited to, any loss of profits) from any cause whatsoever. No person has authority to change this warranty.
© Akron Brass Company. 2018 All rights reserved. No portion of this can be reproduced without the express written consent of Akron Brass Company.
revised: 05/18
ISO 9001 REGISTERED COMPANY
ERROR CODES
Error Codes consist of a two part blink code. The rst digit can be 1, 2 or 3 short blinks followed by another set of short
blinks (1-9). On the last blink of the second digit the LED remains on so it appears to be a long blink, then the code
repeats itself. For example, error code 1-1 appears visually as a short blink, short pause with LED off, then a long blink,
then another short pause with the LED off, then repeats.
1-1 Rotation sensor Rotation mag switch was not detected during a stow or deploy sequence.
1-2 Elevation sensor Elevation mag switch was not detected during a stow or deploy sequence.
1-3 Swing Arm sensor (3440 Only) Monitor is in stowed or deployed mode and the swing arm sensor signal is lost or sending an
invalid value (regardless of mode)
1-6 Obstacle Avoidance prole missing The obstacle avoidance feature is turned on but the avoidance prole has not been learned
1-7 Rotation hard stop N/A
1-8 Elevation hard stop N/A
1-9 Swing Arm hard stop An unexpected hard stop encountered while stowing or deploying after leaving a valid stowed or
deployed position
2-1 Electric Riser The electric riser function has been turned on but the riser is not available on the network
2-2 CAN Valve Not Calibrated Valve function turned on and paired but not yet calibrated.
2-3 CAN Valve Not Located Pairing process failed during setup or valve lost power and/or CAN communications while
operating
Table of contents
Other Akron Monitor manuals

Akron
Akron OMEGA XP 3528 User guide
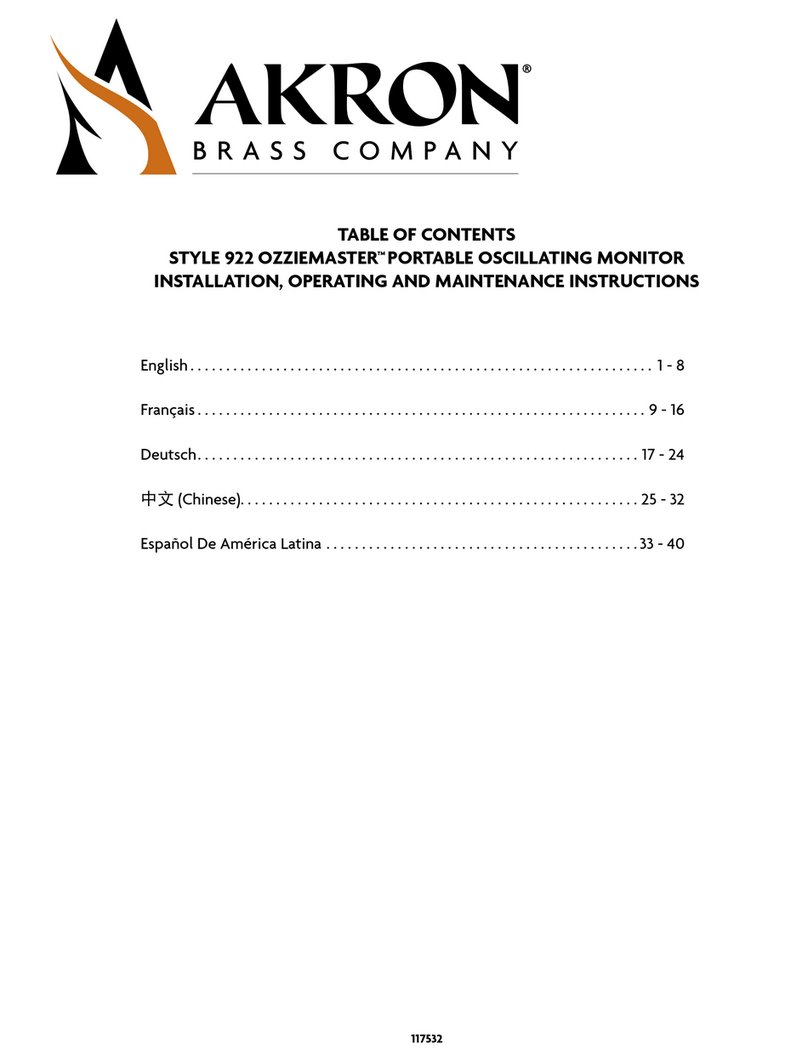
Akron
Akron OZZIEMASTER 922 Assembly instructions

Akron
Akron OMEGA XP 3528 Assembly instructions
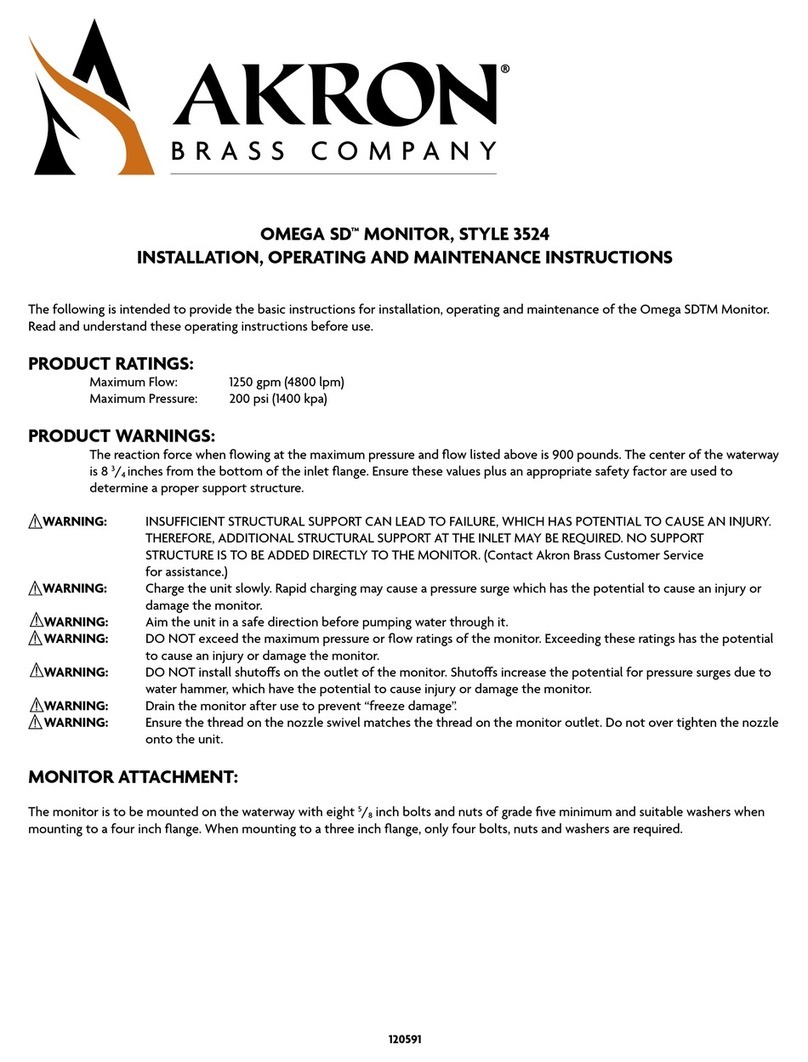
Akron
Akron OMEGA SD 3524 Assembly instructions
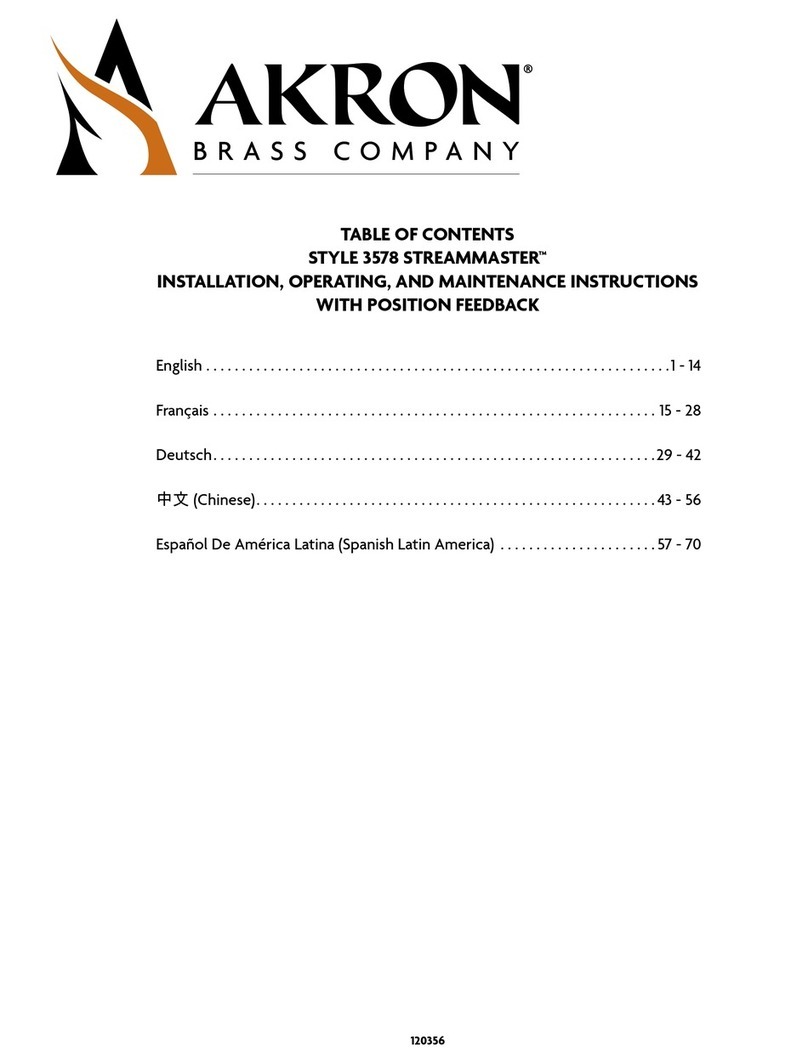
Akron
Akron 3578 STREAMMASTER Assembly instructions
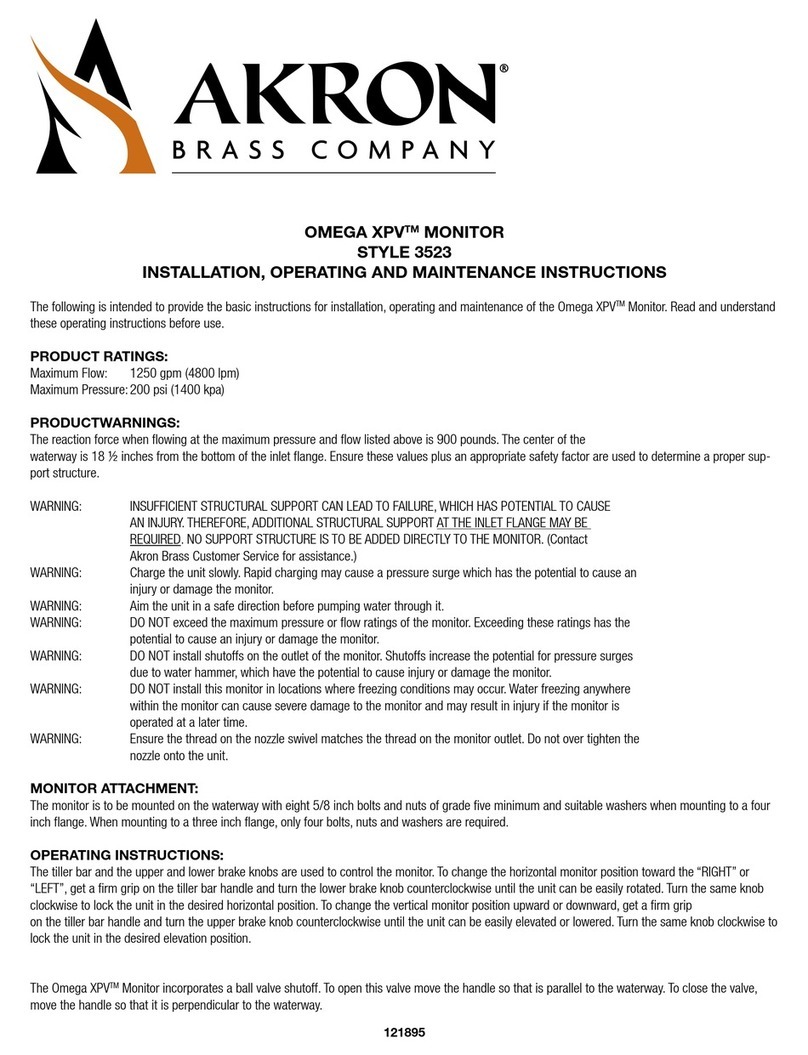
Akron
Akron OMEGA XPV 3523 Assembly instructions
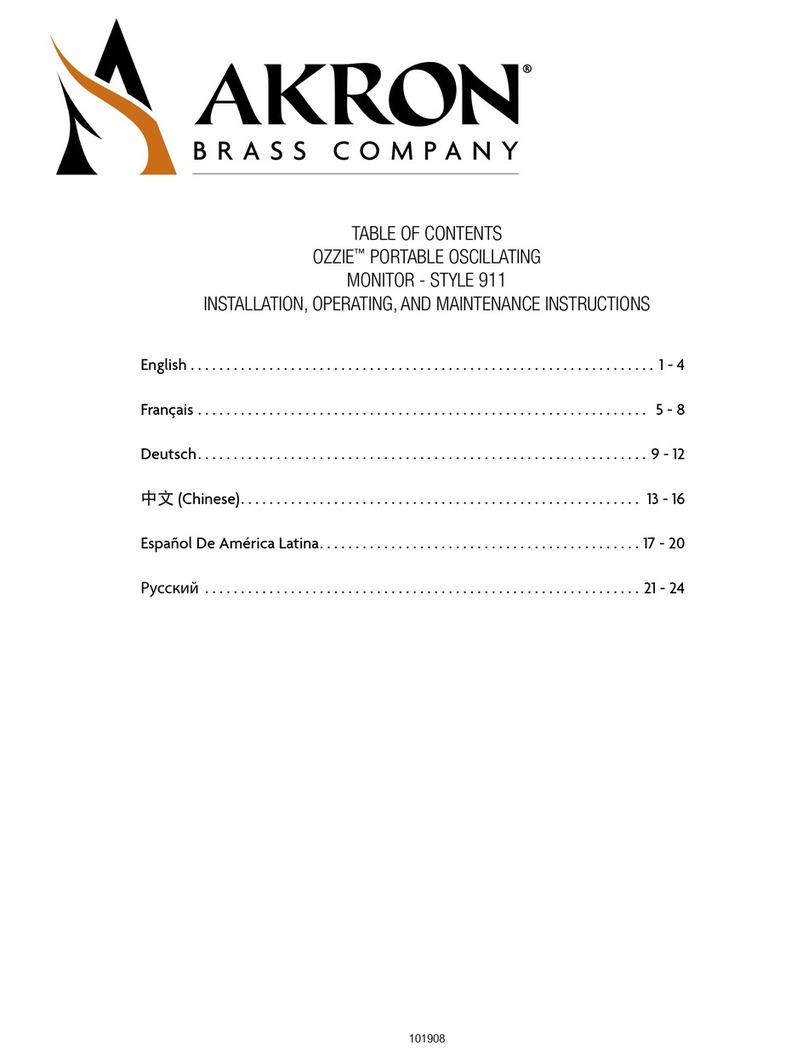
Akron
Akron OZZIE 911 Assembly instructions
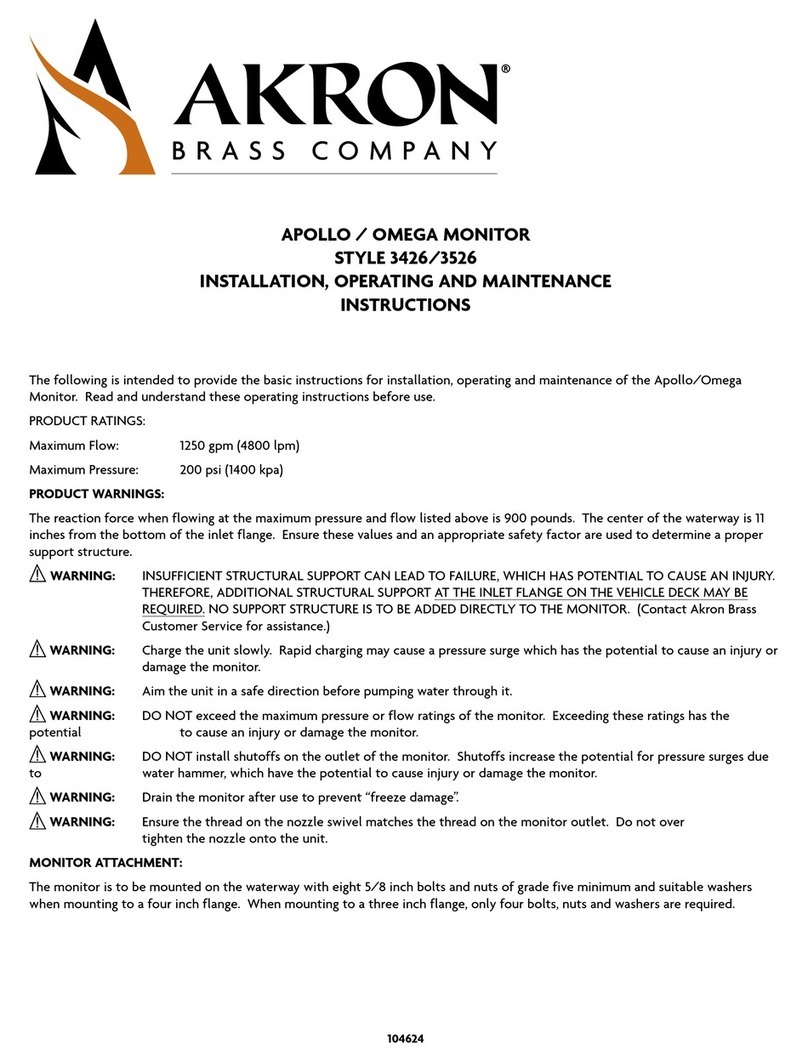
Akron
Akron APOLLO 3426 User manual