B&B ARMR 400 Series User manual

B&B ARMR
A Division of B&B Roadway and Security Solutions 04X0 Rev G
MODEL 400 SERIES
SLIDING GATE
VEHICLE BARRIER
INSTALLATION MANUAL
B&B ARMR
Headquarters/Tech Support:
5900 S Lake Forest Dr Suite 230
McKinney, TX 75070
Phone: (800) 367-0387
Fax: (972) 385-9887
E-mail: [email protected]
www.bb-armr.com
MADE IN THE USA

Installation and Operations Manual —Model 400 Series TABLE OF CONTENTS iv
B&B ARMR
A Division of B&B Roadway and Security Solutions 04X0 Rev G
INTRODUCTION
Welcome!
Congratulations on your purchase of a B&B ARMR vehicle barrier. In addition to
providing detailed operating instructions, this manual describes how to install, maintain,
and troubleshoot your vehicle barrier. If you require additional assistance with any
aspect of your vehicle barrier's installation or operation, please contact us.
With years of experience in all aspects of perimeter security and related disciplines, our
products are used throughout the world to control access and to protect people,
equipment, and facilities. We offer a broad range of vehicle barrier and related security
services:
Turnkey installations
Routine barrier preventative maintenance or emergency repairs (including
work on non-B&B ARMR products)
Spare or replacement parts
Custom designs or special installations
Equipment upgrades (modernize your old equipment with state-of-the-art
hydraulics and control systems)
Ancillary security equipment such as security guard enclosures, card readers,
security lighting, and many other security related products.
Technical support via telephone and possible on site support with advanced
scheduling.
Safety
Your safety is important to us. If you have any questions or are in doubt about any aspect of
the equipment, please contact us. While B&B ARMR does not assume responsibility for
injury to persons or property during installation, operation, or maintenance, we can provide
verbal guidance, additional written instructions, or the services of a factory engineer. We're
here to help you operate your vehicle barrier safely and effectively.
As the user, you are responsible for correct and safe installation, operation, and maintenance
of this equipment. Users must follow the specific instructions and safety precautions located
in this manual. In addition they must:
Your safety is extremely important to us. If you have any
questions or are in doubt about any aspect of the equipment,
please contact us.

Installation and Operations Manual —Model 400 Series TABLE OF CONTENTS v
B&B ARMR
A Division of B&B Roadway and Security Solutions 04X0 Rev G
Be aware of and follow the safety standards of the Occupational Safety and
Health Administration (OSHA), as well as other applicable federal, state, and
local safety regulations and industry standards and procedures. For installation
outside the United States, users must also follow applicable international,
regional, and local safety standards.
Engage only trained and experienced staff to install, operate, and maintain the
equipment.
Ensure that all repairs are performed correctly, using properly trained staff and
the right tools and equipment.
How to Contact Us
If you have any questions or experience any problems with your vehicle barrier—or if we
can help you with any other facility security issues—please contact us directly at:
Corporate/Tech Support:
B&B ARMR
5900 S Lake Forest Dr Suite 230
McKinney, TX 75070
Phone: (800) 367-0387
Fax: (972) 385-9887
E-mail: [email protected]
System Installation Record
To assist in documenting the products installed in your system, please take a minute to
record the following reference information. This information can be located on the blue
B&B ARMR model number plate located on the product in the cylinder access area.
Additional columns are added for your convenience in documenting other components in
the system.
Site:
Job #:
Date:
Serial Number:
Model Number:
Voltage:
Phase:

Installation and Operations Manual —Model 400 Series TABLE OF CONTENTS vi
B&B ARMR
A Division of B&B Roadway and Security Solutions 04X0 Rev G
Table of Contents
INTRODUCTION......................................................................................................................................... iv
Welcome! .................................................................................................................................................iv
Safety........................................................................................................................................................iv
How to Contact Us...................................................................................................................................v
System Installation Record.....................................................................................................................v
1. ORIENTATION....................................................................................................................................... 7
1.1 Overview .......................................................................................................................................... 7
1.2 Options............................................................................................................................................12
1.3 Specifications ..................................................................................................................................12
2. INSTALLATION.....................................................................................................................................13
2.1 Introduction.....................................................................................................................................13
2.2 Preliminary Considerations............................................................................................................13
2.3 Typical Installation of the Motor and Receiver Stanchions ............................................................14
2.4 Installing the Gate and Motor Components....................................................................................16
2.5 Hydraulic Unit Installation.............................................................................................................18
2.6 Control System Installation.............................................................................................................19
5. TROUBLESHOOTING ...........................................................................................................................21
6. ENGINEERING DRAWINGS.................................................................................................................23
7. WARRANTY............................................................................................................................................30

Installation and Operations Manual —Model 400 Series TROUBLESHOOTING 7
B&B ARMR
A Division of B&B Roadway and Security Solutions 04X0 Rev G
1. ORIENTATION
1.1 Overview
This manual addresses B&B ARMR Model 400 Series sliding cantilever gate vehicle
barriers. The 400 Series barriers have high stopping power, and are designed to stop and
disable a vehicle that tries to breach them. They are one in a series of anti-terrorism vehicle
barrier designs manufactured by B&B ARMR.
There are currently several models in the 400 Series: Model 400, Model 400A, Model 450,
and Model 450A . The general descriptions of these basic models are as follows:
Model 400—a sliding cantilevered crash gate rated to stop a 15,000-pound
vehicle traveling at 30 miles per hour.
Model 400A—a sliding cantilevered crash beam rated to stop a 15,000-pound
vehicle traveling at 30 miles per hour.
Model 450—a sliding cantilevered crash gate similar to the Model 400 but with
a higher stopping power, the barrier is rated to stop a 15,000-pound vehicle
traveling at 50 miles per hour.
Model 450A—a sliding cantilevered crash beam rated to stop a 15,000-pound
vehicle traveling at 50 miles per hour.
Figure 1-1 will orient you to the three basic components of a 400 series vehicle barrier.
1. Gate Leaf (consisting of the pickets, the skirt, and the beam)
2. Motor Stanchion
3. Receiver Stanchion
The sub-sections below briefly describe each of the components, and additional details
are provided in other sections of this manual.

Installation and Operations Manual —Model 400 Series TROUBLESHOOTING 8
B&B ARMR
A Division of B&B Roadway and Security Solutions 04X0 Rev G
1.1.1 Gate Leaf
The gate leaf (often just called the gate) consists of three parts: the pickets, the skirt, and the
beam. The pickets are typically 1" square steel tubes spaced on 2.5" centers. The skirt is steel
plate unless configured differently by customer. The pickets and skirt are usually assembled
so that they are anti-climb, meaning there are no protrusions to serve as toeholds on the
vehicle-approach side of the gate leaf. The standard gate height is 108 inches (9 feet or 2.75
meters) above grade. The standard opening when the gate leaf is fully retracted is 144 inches
(12 feet or 3.66 meters). This is the space through which a vehicle will pass, and corresponds
to the standard width of a traffic lane.
Figure 1-1: Basic Components of a 400 Series Gate*
* This figure is for illustration only. It shows the back (non-impact) side of an unpainted 400
series vehicle barrier undergoing testing. An as-shipped unit would be fully painted and
would have other finish features not shown here.
The beam part of the gate leaf is a massive steel I-beam. It provides the heavy-duty structure
that stops the impacting vehicle. The stopping power is not from the beam alone, but from
the manner in which the stanchions' heavy steel tubes transfer the vehicle's energy from the
beam to the foundation.
Motor
Stanchion
Receiver
Stanchion
Gate Leaf
- Pickets
- Beam
- Skirt

Installation and Operations Manual —Model 400 Series TROUBLESHOOTING 9
B&B ARMR
A Division of B&B Roadway and Security Solutions 04X0 Rev G
While the pickets and skirt do not serve as principal structural elements, they do provide an
important protective function. The height of the gate and its strength are designed to intercept
and stop the attacking vehicle's load if the force of the impact launches it forward.
1.1.2 Motor Stanchion (and Associated Hydraulic and Control Unit)
The motor stanchion—which is embedded in a concrete foundation—supports the gate
during opening and closing. It houses the hydraulically driven motor that opens and closes
the gate (gate leaf) and also the roller wheels upon which the gate rolls as it moves. During
vehicle impact, its heavy steel tubes transfer the impact loads to the foundation.
The Model 400 Series vehicle barrier operates from a complete, self-contained hydraulic and
control unit housed in a sealed enclosure with locking doors mounted nearby. For
information on the specific hydraulic unit mated with this gate, please refer to the associated
Operation and Maintenance manual provided separately. The hydraulic unit is designed to
operate for long periods with very little maintenance. It contains the hydraulic reservoir
(which is not pressurized), hydraulic pump, and all of the required valves, manifolds, and
flow control devices. An electric motor operates the gear-type hydraulic pump, which
operates by a system pressure switch independent from the gate signal command. The
hydraulic oil from the pump is drawn through a filter and into a manifold that distributes to
an accumulator, then directional flow control valve. The directional control valves are
energized from the PLC and control circuits to allow hydraulic oil to flow through flow
control valves and out to the charlynn motor. The flow control valve monitors the gate
speed. The operating logic controls the valves to ensure the correct gate position based on
input controls from any set of dry contacts, such as limit switches and safety devices.
These components are sized so that the gate will open or close at about one foot per second
(one meter per 3 seconds). The opening/closing speed can be varied—within limits—by
adjusting hydraulic flow control valves, as described later in this manual.
The hydraulic pumping unit also houses the electric pump drive motor and control circuitry.
The motor is typically a three horsepower, 208 / 240-480 volt, three-phase motor (refer to the
associated manual for variances). An overload circuit protects the motor in the event of
power fluctuations. During a power failure the gate can be operated from a hand pump, and it
can also be opened and closed manually. The hydraulic and control unit is typically mounted

Installation and Operations Manual —Model 400 Series TROUBLESHOOTING 10
B&B ARMR
A Division of B&B Roadway and Security Solutions 04X0 Rev G
on a concrete pad close to the motor stanchion. Conduits connecting the unit and motor
stanchion carry the hydraulic lines and electrical control cables.
The unit also houses the gate control circuitry, the main components of which are the PLC
(programmable logic controller) that is programmed with the gate's operating logic, the
motor starter, and the motor overload protector. The control circuit is 120-volt, single-phase
with 24-volt dc input. The outputs are 24-volt dc and 120-volt ac and some are customer
defined for dry contacts. The unit has a built-in 120-volt convenience outlet (the customer
supplies power and wiring to the box), and a master switch turns off all the power to the unit
for maintenance and repairs. A disconnect is required for the 208-volt coming into the unit,
and should be located close by.
The key components of the motor stanchion are shown in Figure 1-2.
Figure 1-2: Model 400 Series Motor Stanchion
Roller Wheel
Conduit
Limit Switch
Mount

Installation and Operations Manual —Model 400 Series TROUBLESHOOTING 11
B&B ARMR
A Division of B&B Roadway and Security Solutions 04X0 Rev G
1.1.3 Receiver Stanchion
The receiver stanchion—which is embedded in a concrete foundation—captures (and locks
in model 450) the end of the gate in place when the gate is fully closed. During vehicle
impact, its heavy steel tubes transfer the impact loads to the foundation. Because of its
relatively small size compared to the motor stanchion, it has additional reinforcements
(gussets, stabilizer beams, and braces). Figure 1-3 shows the key components of the receiver
stanchion.
The 450 gates have a pair of two inch thick, stainless steel pins that are hydraulically raised
and locked in place. A pair of proximity switches monitors the location of the pins that locks
the gate from moving until they are in the full-up position. Three conduits are needed for the
450 receiver stanchion from the HPU, one for the hydraulic lines and two for control wires.
The control wire is 120-volts for the IR beam and 24-volt dc for the proximity switches.
Figure 1-3: Model 400 Series Receiver Stanchion

Installation and Operations Manual —Model 400 Series TROUBLESHOOTING 12
B&B ARMR
A Division of B&B Roadway and Security Solutions 04X0 Rev G
1.2 Options
The Model 400 Series vehicle barriers are available with a broad array of options, as listed
below. Consult your purchase order or other ordering documentation to determine whether
your unit has the optional equipment.
A wooden traffic control gate arm to warn the vehicle operator. This arm is
positioned in front of the gate and does not rise until the gate is fully open, and
it closes before the gate starts to close.
Red/amber traffic lights. The light remains red if the gate is in any position
except fully open.
In-ground loop detector to detect the presence of a vehicle and prevent
accidental closing of the gate onto the vehicle.
Infrared safety beams to detect pedestrian traffic or as an additional vehicle
sensing device.
Keypads, card readers, or other vehicle access control devices.
Heater and/or cooling fan for the hydraulic pumping unit.
Heaters for the motor stanchion's hydraulic motor and for the roller wheels (for
extreme winter conditions).
1.3 Specifications
Key specifications for the Model 400 Series vehicle barriers are as follows.
Certified vehicle-stopping power as summarized in the table below.
Barrier
Model
Vehicle Weight
Vehicle Speed
U.S. Department of
State Rating*
400 & 400A
15,000 pounds
(~6,800 kg)
30 mph
(~48 kph)
K4
450 & 450A
15,000 pounds
(~6,800 kg)
50 mph
(~80 kph)
K12
* If you are unfamiliar with the rating system nomenclature, contact B&B ARMR
for additional information.
Design operating frequency is 45 open and close cycles per hour.
Design operating temperature range is 20°F –100°F (Y°C –Y°C).

Installation and Operations Manual —Model 400 Series TROUBLESHOOTING 13
B&B ARMR
A Division of B&B Roadway and Security Solutions 04X0 Rev G
2. INSTALLATION
2.1 Introduction
We designed the Model 400 Series vehicle barriers for quick and easy installation. However,
every site is different and each 400 series will vary due to the choice of options or special
design features. Accordingly, the instructions below may have to be varied slightly for your
particular installation. If you need help, or are unclear about any of these instructions, please
contact B&B ARMR for assistance.
Your safety is extremely important to us. Be sure to
follow the specific instructions presented below.
You are responsible for the correct and safe
installation, operation, and maintenance of this
equipment.
2.2 Preliminary Considerations
Before beginning site excavation and barrier installation, note the following important
considerations.
Inspect the site and verify there are no underground utilities or overhead wires or
obstructions in the excavation area.
If possible, locate the installation away from routine foot traffic to reduce the
chance for pedestrian injury from the barrier's moving gate.
Make sure that there is adequate free area adjacent to the motor stanchion's
installation location so that the vehicle barrier gate can be slid onto the stanchion
after the stanchion is cemented in place.
Locate the HPU within twenty feet of the wheel stanchion. If the pump needs to
be further away from the stanchion, please contact B&B ARMR.

Installation and Operations Manual —Model 400 Series TROUBLESHOOTING 14
B&B ARMR
A Division of B&B Roadway and Security Solutions 04X0 Rev G
2.3 Typical Installation of the Motor and Receiver Stanchions
Perform the following steps to install the motor and receiver stanchions.(Always refer to your
submittal for your specifications.)
2.3.1 Excavate the holes for the stanchions as shown in the Foundation Drawings
supplied in your submittal. (See generic drawings in the drawings section).
Place the stanchions in the excavation holes.
2.3.2 Install the axles for the roller wheels in the appropriate holes in the
stanchions and tighten the setscrews against the flats on the axles. Tighten
the setscrews securely, and use a locking compound on the setscrews threads
if available. Use care when installing the axles, as they serve as the critical
measuring point for final installation.
2.3.3 The tops of the axles must be 31-¾ inches above the roadbed height at the
roadbed's highest point (If wheels are factory installed make sure they are
35-¾ inches above the roadbed). Adjust the stanchion's position in the
excavation to bring the axles to the correct height. Use a transit to level all
four points (the top of the end of each axle) and make any final adjustments
in the positions of the stanchions so that the transit is reading within 1/32nd of
an inch at each of the four points. It is CRITICAL THAT THE SHAFTS
ARE PERFECTLY LEVEL for the gate to function properly. Verify also
that the stanchions are plumb and level.
2.3.4 Place a partial pour of concrete into the excavation holes to lock the
stanchions in place. Use the transit to verify the stanchions remain level and
plumb.
2.3.5 Rough in the conduits. All conduits, fittings, sweeps, and couplings must be
electrical grade (gray color); do not use plumbing type (white color). All
conduits are run to the hydraulic pump unit. Accordingly, run all the conduits
for your installation to the location where the hydraulic unit's concrete pad
will be located. Run the conduits together and be sure the conduits are long
enough to extend above the anticipated height of the hydraulic unit's pad.
(See section 2.5, Hydraulic Unit Installation, for additional information.)
2.3.6 Make the final concrete pour, again making sure the axle height does not
change and remain level and plumb. Remove any concrete that might have
splattered inside the exposed conduits.
2.3.7 After the concrete has set, install the roller wheels, collars and nuts onto the
axles. Place two collars (spacers) on each side of the shaft, then the wheel,
then another collar, and finally the nut. Adjust the wheels and axle nuts so
there is no side play in the wheels, but yet they can still be turned easily by
hand. Tighten set screw on the nut. Grease the wheel bearings using the

Installation and Operations Manual —Model 400 Series TROUBLESHOOTING 15
B&B ARMR
A Division of B&B Roadway and Security Solutions 04X0 Rev G
grease fittings. The wheels may be pre-greased. Be careful not to over-
grease the bearings; make sure the grease does not leak out of the sides of the
bearings.
2.3.8 Install the four guide wheels into the guide wheel receivers on the wheel
stanchion. Leave the bolts fully backed off to allow the guide wheels to
insert completely into the receivers.
Figure 2.3 –Interior View of Motor Stanchion

Installation and Operations Manual —Model 400 Series TROUBLESHOOTING 16
B&B ARMR
A Division of B&B Roadway and Security Solutions 04X0 Rev G
2.4 Installing the Gate and Motor Components
Perform the following steps to install the gate (gate leaf), motor, and limit switches on the
motor stanchion.
2.4.1 Lift the gate assembly using a crane or forklift. Guide the gate onto the first
set of roller wheels, with the wheels fitting between the I-beam and the
channel. Push the gate onto the second set of roller wheels.
2.4.2 Move the gate by hand to the halfway position. Install the stop plates onto
the ends of the gate.
2.4.3 Attempt to slide the gate through about ⅔ of its travel. If the gate binds,
adjust the roller wheels to eliminate the binding.
2.4.4 Mount the motor and gear assembly. Mount the motor on the wheel post
closest to the roadway opening, and on the side between the two single posts.
Leave the motor mount in the down position with the bolts slightly loose
until the motor rotation and limit switches have been tested.
2.4.5 Mount the limit switches. They are generally mounted on the wheel post
located on the barrier's run-out side (see figures 2.4.5-a, and 2.4.5-b).
2.4.6 Bolt the limit switch ramps (these are 2-foot/.66-meter long sections of
electrical rack mounting) so they engage the limit switches' lever arms. The
ramps must be located so they engage the switches before the gate reaches
the desired spot, to allow for drift. The weight of the gate will allow the gate
to coast even after the limit switches are activated. Plan for the gate to travel
between 4 to 6 inches after the limit switch is activated. The ramps are long
to ensure the gate will not coast so far when the gate comes to a stop, that the
switches' lever arms become disengaged.

Installation and Operations Manual —Model 400 Series TROUBLESHOOTING 17
B&B ARMR
A Division of B&B Roadway and Security Solutions 04X0 Rev G
Figure 1 Limit Switch Mounting
2.4.7 Bolt the limit switch plates so they engage the limit switches' lever arms. The
plate must be located so that both limit switches are hit in the correct
sequence. The first limit switch tells the controller to slow the gate down.
The second limit tells the controller to stop the gate.
2.4.8 Grease or cosmoline needs to be added to the rack, pinion and wheel areas to
prevent oxidation. This should be checked and touched up during the
monthly maintenance as needed.

Installation and Operations Manual —Model 400 Series TROUBLESHOOTING 18
B&B ARMR
A Division of B&B Roadway and Security Solutions 04X0 Rev G
2.5 Hydraulic Unit Installation
Refer to separate manual for information on the specific model provide.
2.5.1 Typically, the Model 400 series hydraulic unit is mounted on a concrete pad.
Generally, the hydraulic, electrical power, and control conduits will be run
together, and all will turn up out of the concrete pad to attach to the
hydraulic unit. Additional conduits may be required for traffic lights, loop
detectors, and other options. Contact B&B ARMR if you are unclear about
the conduit requirements for your installation.
2.5.2 Place the hydraulic unit on the pad over the exposed conduits and bolt the
unit in place. (The feet on the unit will accept standard concrete anchors.) If
you mount the unit to an intermediate steel structure, make sure that
structure is securely fastened to the pad.
2.5.3 Terminate the electrical power and control conduits in the electrical box and
the hydraulic hose conduit to the hydraulic side of the HPU. The hydraulic
conduit should be cut flush with the concrete pad. This will allow the
hydraulic hose to move slightly when pressure is applied without rubbing
against any sharp edges on the conduit.
2.5.4 Install the hose by pulling it into the conduit, making sure to protect the hose
from any sharp edges. When you cut the hose to length do not cut it too
short, as the hose will shrink in length when under pressure.
2.5.5 Connect the hoses to the fittings located on the manifold. The two fittings
on the left side of the manifold operate the gate, while the set on the right
operate the locking pin cylinder (model 450 & 450A only)
2.5.6 The hydraulic unit's oil tank holds 30 gallons. Approved hydraulic oil must
be added by removing the tank lid and pouring into the tank. The tank
should be filled until the oil is half way up the sight glass. (See the
Maintenance section for oil specifications and additional details.) You may
see small amounts of oil in the unit when it arrives. This is residue from
factory testing prior to shipment

Installation and Operations Manual —Model 400 Series TROUBLESHOOTING 19
B&B ARMR
A Division of B&B Roadway and Security Solutions 04X0 Rev G
2.5.5 Connect the hoses to the motor and also the locking pin cylinder (450 &
450A only) before the system is turned on.
2.6 Control System Installation
Refer to the associated hydraulic pumping unit (HPU) manual for further clarification of
the following information ad any references later to the (HPU).
Install three-phase power to the lower right corner of the electrical box using the
terminals marked L1, L2, L3, Neutral, and Ground.
All devices that require ac power (such as loop detector, traffic lights, and infrared
beams) can get 120-volt ac from the left side of the electrical box. Turning off the switch
next to the convenience outlet disconnects all of the control power.
Most other wiring is low-voltage (24-volt dc). Terminate all low-voltage inputs on the red
terminal blocks at the bottom of the electrical box. Wire all switching devices (gate open,
gate close, limit switches, and so on) so that each device gets 24-volt dc power from the
left side of the I terminal blocks. Attach each device's input termination point wire to the
appropriate I terminal block (I0, I1, I2, etc.) and the device's output termination point
wire to the appropriate Q terminal block (Q0, Q1, Q2, etc.). A summary of key control
wiring terminations is as follows.
Traffic Lights (120-volt ac) Common to 120-volt neutral
Red light to TLR (upper right)
Amber light to TLG (upper right)
Panel Indicator Lights (24-volt dc) Common to 24-volt dc negative
Red to PLR (upper right)
Green to PLG (upper right)
Open Button Button to open gate –Normally Open
Button common to I0
Button point to 24-volt dc+

Installation and Operations Manual —Model 400 Series TROUBLESHOOTING 20
B&B ARMR
A Division of B&B Roadway and Security Solutions 04X0 Rev G
Close Button Button to close gate –Normally Open
Button common to I1
Button point to 24-volt dc+
Locking Pin Open Limit Switch Jumper required for non 450 gates
Switch common to I2
Switch point to 24-volt dc+
Safety Stop Jumper Jumper installed makes gate stop instead of
open when a safety device is detected.
Jump 24-volt dc+ to I3
Gate Close Limit Switch Switch must be wired for the gate to work
Switch common to I4
Switch point to 24-volt dc+
Gate Open Limit Switch Switch must be wired for the gate to work
Switch common to I5
Switch point to 24-volt dc+
Safety Devices Switch common to I6
Switch point to 24-volt dc+
Stop Button Button to stop gate –Normally Closed
Button common to I7
Button point to 24-volt dc+
Locking Pin Close Limit Switch Jumper required for non 450 gates
Switch common to I10
Switch point to 24-volt dc+
Emergency Close Button Closes gate regardless of Safety Devices
Button common to I11
Button point to 24-volt dc+
Loop Detector –One loop detector and harness come pre-wired for use as a
safety. Two loops can be wired in series and connected to inputs #7 and #8 on the
loop detector harness. If you wish to use a loop as a free exit, contact B&B
ARMR for prices or wiring information.

Installation and Operations Manual —Model 400 Series TROUBLESHOOTING 21
B&B ARMR
A Division of B&B Roadway and Security Solutions 04X0 Rev G
5. TROUBLESHOOTING
The table below provides guidance on identifying and correcting issues with your Model 400
Series vehicle barrier. If you encounter problems that you cannot fix, contact B&B ARMR
and we will gladly work with you to correct them.
Model 400 Series Troubleshooting Guide
Symptom
Actions
Gate does not go open
1. Check power
2. Check overload protector
3. Check pressure gauge
4. Manually open the gate by depressing the
directional control valve to see if problem
is mechanical or electrical. If mechanical,
check for binding on the gate. If not:
5. Check PLC input
6. Check that safeties are clear
7. Check PLC output
8. Check push button operation
9. Check locking pin and proximity switch,
gate will not open unless the pins are up
and I3 is lit on the PLC
Gate does not go close
1. Check power
2. Check overload protector
3. Check pressure gauge
4. Manually close the gate by depressing the
directional control valve to see if problem
is mechanical or electrical. If mechanical,
check for binding on the gate. If not:
5. Check PLC input
6. Check that safeties are clear
7. Check PLC output
8. Check push button operation
9. Check locking pin and proximity switch,
gate will not open unless the pins are up
and I3 is lit on the PLC
HPU does not build up pressure, but is
running
1. Check power
2. Close pressure relief valve

Installation and Operations Manual —Model 400 Series TROUBLESHOOTING 22
B&B ARMR
A Division of B&B Roadway and Security Solutions 04X0 Rev G
Symptom
Actions
HPU pump will not turn on
1. Check power
2. Check motor overload, press start
3. Check motor starter
4. Check low level switch
5. Check pressure switch
Gate makes noise during operation
1. Check that roller wheel bearings are
greased
2. Check that gate is not moving too fast
3. Check that the guide wheels are properly
adjusted
4. Check that the spur gear is properly
adjusted to the gear rack
Hydraulic unit is excessively hot
1. Check that the pressure relief valve is
closed (fully clockwise)
2. Check that the pressure switch is adjusted
to shut the motor off before 1850psi
3. Check for correct voltages
Gate moves too slowly
1. Check for mechanical binds (guide wheels
out of adjustment, debris under the wheels
or on the inside of gate
2. Check flow control valve
Traffic indicator light does not change
1. Check proper limit switch operation
2. Check bulbs
3. Check PLC outputs
Locking pins are moving but not giving
signals up or down to I3
1. Check the proximity switches at the
locking pin mechanism
This manual suits for next models
4
Table of contents
Other B&B ARMR Other manuals
Popular Other manuals by other brands

dataTaker
dataTaker DT80 user manual
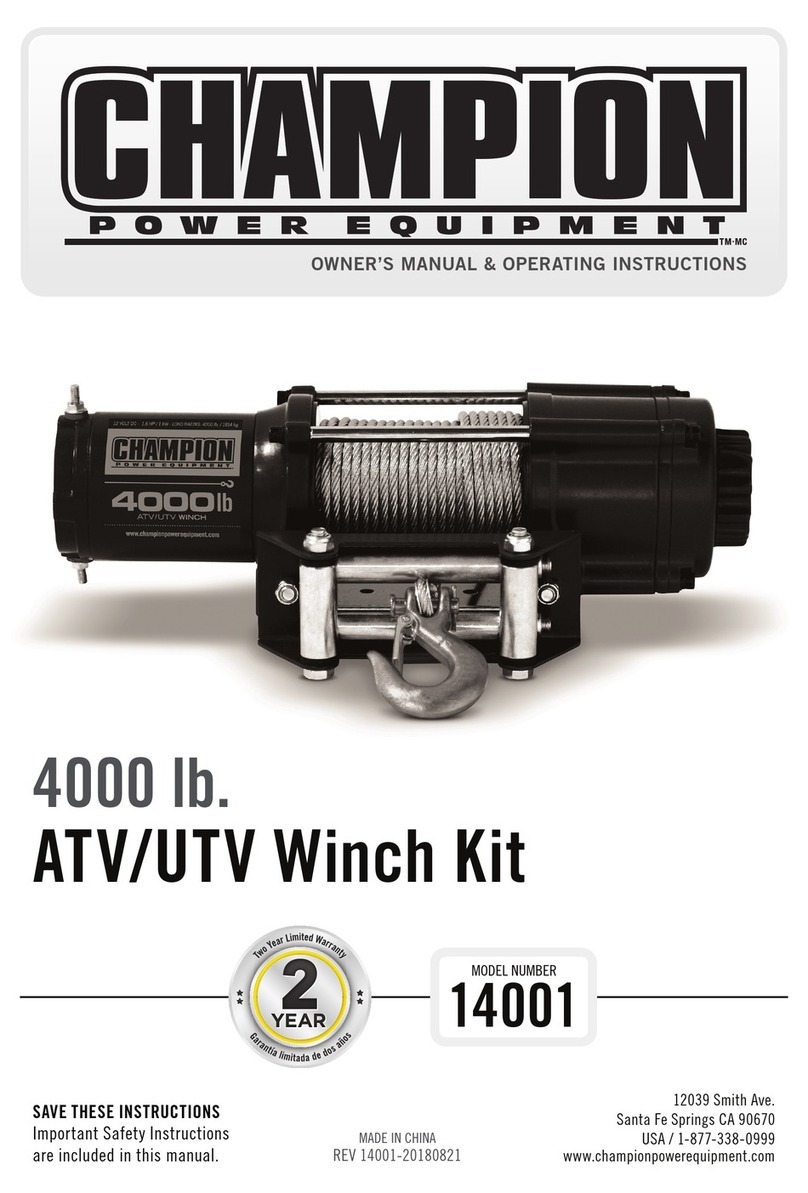
Champion Power Equipment
Champion Power Equipment 14001 Owner's manual & operating instructions
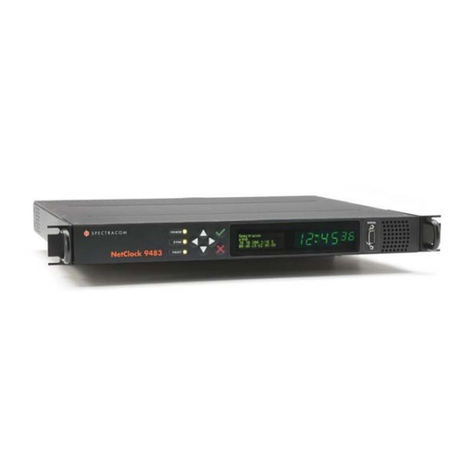
Spectracom
Spectracom NetClock 9400 Series User reference guide
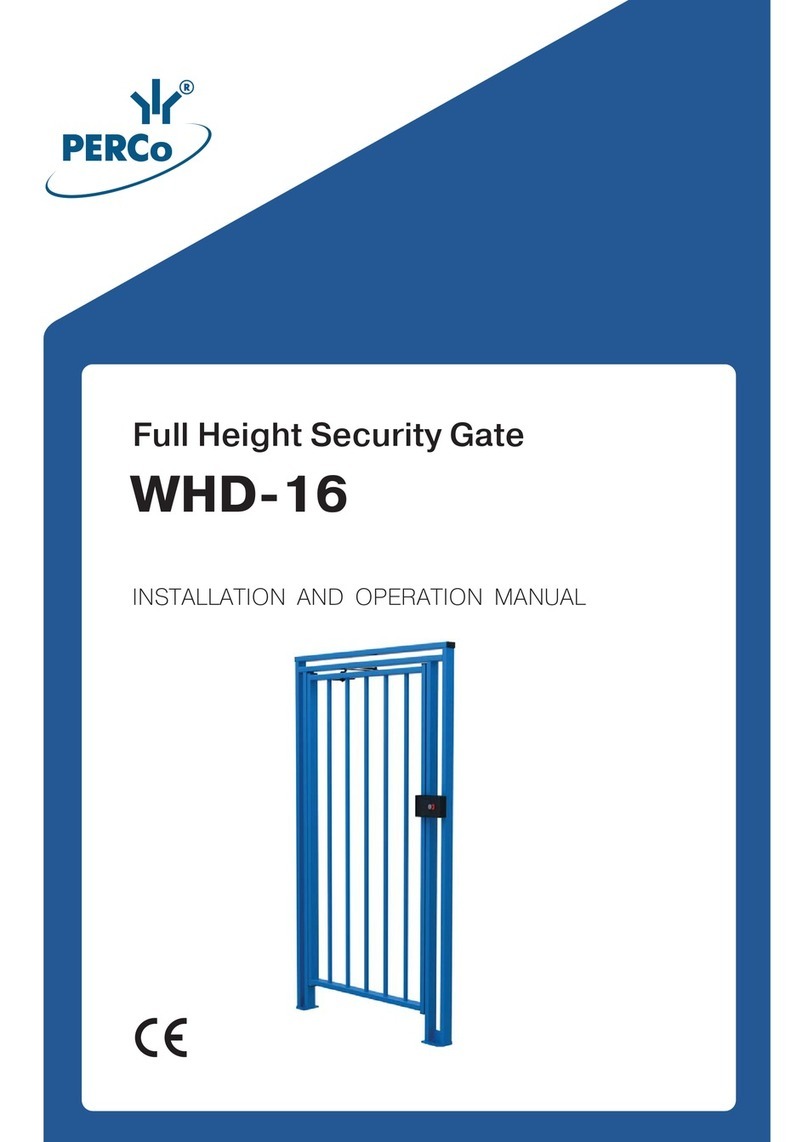
PERCo
PERCo WHD-16 Installation and operation manual

Rinnai
Rinnai R1349 Installation guides
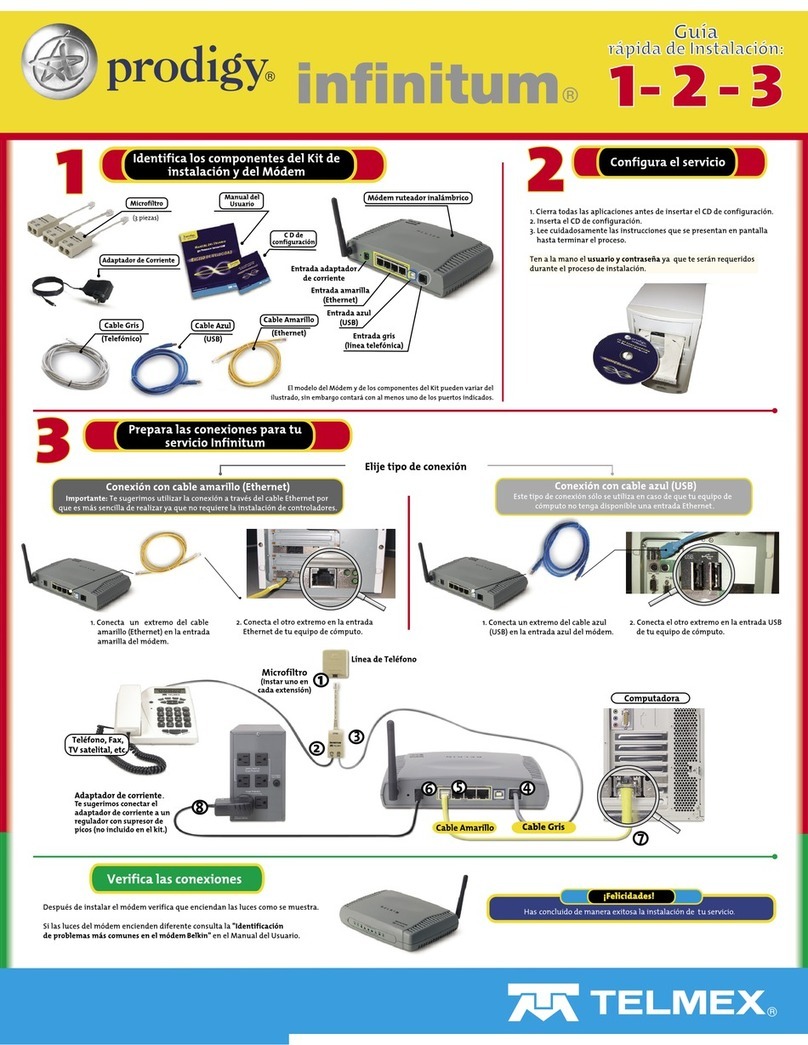
Belkin
Belkin F5D7631-4-TNOR Quick install guide