Blue Seal Evolution Series User manual

Service Manual
Gas/Electric Convection Oven Ranges
GE54 / GE56 / GE58
Blue Seal Evolution Series Gas / Electric Convection Ranges © Copyright Moffat Ltd. 21 June 2016
Amendment 10
Service Manual
Gas / Electric Convection Oven Ranges
GE54 / GE56 / GE58

Blue Seal Evolution Series Gas / Electric Convection Ranges © Copyright Moffat Ltd. 21 June 2016
Amendment 10
ALL INSTALLATION AND SERVICE REPAIR WORK MUST BE CARRIED OUT BY QUALIFIED PERSONS
ONLY.
WARNING:
MAKING ALTERATIONS MAY VOID WARRANTIES AND APPROVALS.
IMPORTANT:

Contents
Blue Seal Evolution Series Gas / Electric Convection Ranges © Copyright Moffat Ltd. 21 June 2016
Amendment 10
This manual is designed to take a more in depth look at the Blue Seal Gas / Electric Ranges for the purpose of making the units more
understandable to service people.
There are settings explained in this manual that should never require to be adjusted, but for completeness and those special cases
where these settings are required to change, this manual gives a full explanation as to how, and what effects will result.
Section Page No.
1. Specifications ........................................................................................................................... 2
2. Installation ............................................................................................................................... 8
3. Operation ................................................................................................................................ 12
3.1 Description of Controls
3.2 Explanation of Control System
4. Maintenance ........................................................................................................................... 14
4.1 Routine Maintenance
5. Fault Finding ........................................................................................................................... 15
5.1 Fault Finding Charts
5.2 Fault Diagnosis
6. Service Procedures ................................................................................................................. 22
6.1 Access
6.2 Replacement - Open Burners (up to Ser No. 718549)
6.3 Replacement - Open Burners (from Ser No. 718550)
6.4 Replacement - Griddle Burner
6.5 Replacement - Oven
6.6 Adjustment / Calibration
7. Accessories ............................................................................................................................. 46
Gas Conversion Kits
Joining Caps
8. Exploded Parts Diagrams ....................................................................................................... 49
8.1 Convection Range Gas Cooktop
8.2 GE54 Oven Assembly
8.3 GE56 / GE58 Oven Assembly
9. Circuit Schematics .................................................................................................................. 66
9.1 Convection Ovens (GE54 / GE56 / GE58)
10. Wiring Diagram ...................................................................................................................... 67
10.1 Convection Ovens (GE54 / GE56 / GE58)
11. Service Contacts ..................................................................................................................... 69
Appendix A. Gas Type Conversion .................................................................................................. 70
Appendix B. Hob Type Conversion.................................................................................................. 77
Appendix C Removing Hob From Range......................................................................................... 80

2
1
Specifications
Blue Seal Evolution Series Gas / Electric Convection Ranges © Copyright Moffat Ltd. 21 June 2016
Amendment 10
Dimensions - GE54
Refer to Page 3 for Cook Top Options
Dimensions - GE56

3
1
Specifications
Blue Seal Evolution Series Gas / Electric Convection Ranges © Copyright Moffat Ltd. 21 June 2016
Amendment 10
Dimensions - GE58
Refer to Page 3 for Cook Top Options

4
1
Specifications
Blue Seal Evolution Series Gas / Electric Convection Ranges © Copyright Moffat Ltd. 21 June 2016
Amendment 10
Cook Top Options GE56-D Cook Top Options GE56-C
Cook Top Options GE56-B Cook Top Options GE56-A
Cook Top Options GE58-D Cook Top Options GE58-C
Cook Top Options GE58-B Cook Top Options GE58-A
Cook Top Options
Cook Top Options GE54-D Cook Top Options GE54-C

5
1
Specifications
Blue Seal Evolution Series Gas / Electric Convection Ranges © Copyright Moffat Ltd. 21 June 2016
Amendment 10
Model Numbers Covered in this Specification
GE54D[1] 4 Open Burners + Electric Convection Oven.
GE54C[1] 2 Open Burners + 300mm Griddle + Electric Convection Oven.
GE56D[1] 6 Open Burners + Electric Convection Oven.
GE56C[1] 4 Open Burners + 300mm Griddle + Electric Convection Oven.
GE56B[1] 2 Open Burners + 600mm Griddle + Electric Convection Oven.
GE56A[1] 900 mm Griddle + Electric Convection Oven.
GE58D[1] 8 Open Burners + Electric Convection Oven.
GE58C[1] 6 Open Burners + 300mm Griddle + Electric Convection Oven.
GE58B[1] 4 Open Burners + 600mm Griddle + Electric Convection Oven.
GE58A[1] 2 Open Burners + 900mm Griddle + Electric Convection Oven.
[1] - Open Burner Options;
F- with Flame Failure Protection.
PF- with Pilot and Flame Failure Protection.
Gas Supply Requirements
- Australia
- New Zealand
* Measure burner operating pressure at the manifold test point with two burners operating at full setting.
Operating pressure is ex-factory set, through the appliance regulator and is not to be adjusted, apart from when
carrying out gas conversion, if required. (Refer to ‘Gas Conversion’ section for details).
Natural Gas LP Gas (Propane)
Input Rate (N.H.G.C.)
- each Open Burner
28 MJ/hr
28 MJ/hr
- each 300mm Griddle Section 21 MJ/hr 21 MJ/hr
Supply Pressure 1.13 - 3.4 kPa 2.75 - 4.50 kPa
Burner Operating Pressure (*) 0.95 kPa (*) 2.6 kPa (*)
Gas Connection 3/4” B.S.P. Male
Natural Gas LP Gas
Input Rate (N.H.G.C.)
- each Open Burner
28 MJ/hr
28 MJ/hr
- each 300mm Griddle Section 21 MJ/hr 21 MJ/hr
Supply Pressure 1.13 - 3.4 kPa 2.75 - 4.50 kPa
Burner Operating Pressure (*) 0.95 kPa (*) 2.6 kPa (*)
Gas Connection 3/4” B.S.P. Male

6
1
Specifications
Blue Seal Evolution Series Gas / Electric Convection Ranges © Copyright Moffat Ltd. 21 June 2016
Amendment 10
- United Kingdom
Appliance Classification
Category: II2H3P.
Flue Type: A1
Natural Gas (G20) Propane (G31)
Open Burner
(each)
Griddle
(each 300mm section)
Open Burner
(each)
Griddle
(each 300mm section)
Heat Input (nett) Nominal 6.5 kW 5.5 kW 6.5 kW 5.5 kW
Reduced 1.75 kW 1.85 kW 1.75 kW 1.95 kW
Gas Rate (nett) Nominal 0.69 m3/hr 0.58 m3/hr 0.51 kg/hr 0.43 kg/hr
Reduced 0.19 m3/hr 0.20 m3/hr 0.14 kg/hr 0.15 kg/hr
Supply Pressure 20 mbar 37 mbar
Burner Operating Pressure (*) 9.5 mbar (*) 26 mbar (*)
* Measure burner operating pressure at the manifold test point with two burners operating at full setting.
Operating pressure is ex-factory set, through the appliance regulator and is not to be adjusted, apart from
when carrying out gas conversion, if required. (Refer to ‘Gas Conversion’ section for details).
- All Other Markets
(*)
Measure Burner operating pressure at manifold test point with two burners operating at 'High Flame'
setting.
(*) NAT, LPG & Butane Only - Operating pressure is ex-factory set and is not to be adjusted, unless when
converting between gasses, if required.
(**) TOWN GAS Only - Adjust burner operating pressure using adjustable gas regulator supplied.
Refer to ‘Gas Conversion and Specifications’ section of this manual for further details.
Gas Connection
Gas supply connection point is located at the rear of the appliance, approximately 130mm from the right hand side, 35mm
(GE54), 32mm (GE56), 35mm (GE58) from the rear, 655mm from the floor and is reached from beneath the appliance.
(Refer to the ‘Dimensions’ section).
Connection is ¾" BSP male thread.
Natural Gas Town Gas
(**)
Input Rate (N.H.G.C.)
- each Open Burner
28MJ/hr
28MJ/hr
- each 300mm Griddle Section 21MJ/hr 21MJ/hr
Supply Pressure 1.13 - 3.4kPa 0.75 - 1.50kPa
Burner Operating Pressure (*) 0.95kPa (*) 0.63kPa (*)
Gas Connection 3/4” B.S.P. Male
LP Gas
(Propane)
28MJ/hr
21MJ/hr
2.75 - 4.50kPa
2.6kPa (*)
LP Gas / Butane
28MJ/hr
21MJ/hr
2.75 - 4.50kPa
2.6kPa (*)

7
1
Specifications
Blue Seal Evolution Series Gas / Electric Convection Ranges © Copyright Moffat Ltd. 21 June 2016
Amendment 10
MODEL
1-Phase Connection
1P+N+E
230-240V
3-Phase Connection
3P+N+E
400-415V
GE54 5.8 kW,
23.9 Amps @ 235V 5.8 kW
L1 - 8.5 Amps
L2 - 7.7 Amps
L3 - 7.7 Amps
GE56 6.8 kW,
27.9 Amps @ 235V 6.8 kW
L1 - 9.5 Amps
L2 - 9.2 Amps
L3 - 9.2 Amps
GE58 6.8 kW,
27.9 Amps @ 235V 6.8 kW
L1 - 9.5 Amps
L2 - 9.2 Amps
L3 - 9.2 Amps
Electrical Supply Requirements
Electrical Connection
GE54 - GE56 Models Only.
Electrical supply connection point is located at the rear of the appliance, approximately 74mm from the right hand side,
501mm from the rear and 150mm from the floor.
GE58 Models Only.
Electrical supply connection point is located at the rear of the appliance, approximately 374mm from the right hand side,
501mm from the rear and 150mm from the floor.
When connecting a this electric appliance to the mains supply, ensure that the following is carried out:-
An isolating switch is fitted within 2m of the appliance, but not on the appliance and in such a position that the user
does not have to reach across the cooking surface.
Supply cord shall be oil-resistant, sheathed flexible cable and not lighter than ordinary polychloroprene or other
equivalent synthetic elastomer sheathed cord (as per AS/NZS 3191 part 2.10.11. or IEC 60245-IEC-57) e.g. HO5 RN-F
Type.
The branch supply line shall be individually overload protected to the correct current rating and the supply chord shall
be protected against any mechanical or thermal damage.
A grommet is fitted around the wiring entry hole into the appliance.
All wiring connections must be tight.
Refer to the appropriate wiring standards for the size of cable that is to be supplied to an appliance for the current drawn on
that line.
THIS APPLIANCE MUST BE EARTHED. IFTHE SUPPLY CORD IS DAMAGED, IT MUST BE REPLACED BY ASUITABLY QUALIFIED PERSON IN
ORDER TO AVOID AHAZARD.
Warning

2
Installation
8
Blue Seal Evolution Series Gas / Electric Convection Ranges © Copyright Moffat Ltd. 21 June 2016
Amendment 10
Installation Requirements
NOTE:
It is most important that this appliance is installed correctly and that operation is correct before use.
Installation shall comply with local gas and health and safety requirements.
This appliance shall be installed with sufficient ventilation to prevent the occurrence of unacceptable
concentrations of health harmful substances in the room, the appliance is installed in.
Blue Seal Gas / Electric Range Convection Ovens are designed to provide years of satisfactory service, and correct installation is
essential to achieve the best performance, efficiency and trouble-free operation.
This appliance must be installed in accordance with National installation codes and in addition, in accordance with relevant National /
Local codes covering gas and fire safety.
AUSTRALIA / NEW ZEALAND: - AS/NZS 5601 - Gas Installations.
- AS/NZS3000 - Wiring Rules.
UNITED KINGDOM: - Gas Safety (Installation & Use) Regulations 1998.
- BS 6173 - Installation of Catering Appliances.
- BS 5440 1 & 2 - Installation Flueing & Ventilation.
- BS7671 - Requirements for Electrical Installation.
IRELAND: - IS 820 - Non - Domestic Gas Installations.
Installations must be carried out by authorised persons only. Failure to install equipment to the relevant codes and
manufacturer’s specifications shown in this section will void the warranty.
Components having adjustments protected (e.g. paint sealed) by the manufacturer are only to be adjusted by an
authorised service agent. They are not to be adjusted by the installation person.
Unpacking
Remove all packaging and transit protection from the appliance including all protective plastic coating from the exterior
stainless steel panels.
Check equipment and parts for damage. Report any damage immediately to the carrier and distributor.
Report any deficiencies to the distributor who supplied the appliance.
Check that the available gas and electrical supply is correct to that shown on the rating plate located on the front right hand
corner of the bottom sill.
Location
1. Installation must allow for a sufficient flow of fresh air for the combustion air supply.
2. Installation must include adequate ventilation means, to prevent dangerous build up of combustion products.
3. Never directly connect a ventilation system to the appliance flue outlet.
4. Position the appliance in its approximate working position.
5. All air for burner combustion is supplied from beneath the appliance. Legs must always be fitted and no obstructions placed
beneath or around the base of the appliance, as obstructions will cause
incorrect operation and / or failure of the appliance.
NOTE: Do not obstruct or block the appliances flue. Never directly connect a ventilation system to the appliance flue
outlet.
Clearances
NOTE: Only non-combustible materials can be used in close proximity to this appliance.
* Side clearances can be 50mm when the adjacent surface is at least 100mm below cooking surface.
Combustion Air Requirements:
GE505 / GE54 GE506 / GE56 GE508 / GE58
Natural Gas (G20) 24m3/hr 36m3/hr 48m3/hr
LPG / Butane (G31) 25m3/hr 38m3/hr 50m3/hr
Town Gas 24m3/hr 36m3/hr 48m3/hr
Combustible Surface Non Combustible Surface
Left/Right hand side 250mm (*) 0mm
Rear 100mm 0mm

2
Installation
9
Blue Seal Evolution Series Gas / Electric Convection Ranges © Copyright Moffat Ltd. 21 June 2016
Amendment 10
Assembly
NOTE:
All Models are delivered completely assembled. No further assembly is required.
This appliance is fitted with adjustable feet to enable appliance to be positioned securely and level. This
should be carried out on completion of gas connection.Refer to ‘Gas Connection’ section.
Optional Accessories (Refer to Replacement Parts List)
Plinth Kit. For installation details, refer to the instructions supplied with each kit.
1. Check that all the feet (or castors) are securely fitted.
2. Adjust the four feet to make the Range steady and level.
Gas Connection
NOTE: ALL GAS FITTING MUST ONLY BE CARRIED OUT BY AN AUTHORISED PERSON.
1. It is essential that the gas supply is correct for appliance being installed and that adequate supply pressure and volume are
available. The following checks should be made before installation:-
a. Gas Type the appliance has been supplied for, is shown on coloured
stickers located above the gas connection point and rating plate. Check
that this is correct for the gas supply the appliance is being installed for.
The gas conversion procedure is detailed in this manual.
b. Supply Pressure required for this appliance is shown in the
‘Specifications’ section of this manual. Check the gas supply to ensure
adequate supply pressure exists.
c. Input Rate of this appliance is stated on the Rating Plate and in the
‘Specifications’ section of this manual. The input rate should be checked
against the available gas supply line capacity. Particular note should
be taken if the appliance is being added to an existing
installation.
NOTE: It is important that adequately sized piping runs directly to the connection joint on the appliance with as few tees
and elbows as possible to give maximum supply volume.
2. Fit the gas regulator supplied, into the gas supply line as close to the appliance as possible.
NOTE: The gas pressure regulator provided with this appliance is convertible between Natural Gas and LPG and is already
converted ex-factory to the gas type labelled beside the gas connection point. The regulator outlet pressure is
fixed ex-factory and it is NOT to be adjusted.
The regulator connections are 3/4" BSP female.
The connection to the appliance is 3/4" BSP male.
(Refer to the ‘Specifications’ section for the gas supply location dimensions).
NOTE: A Manual Isolation Valve must be fitted to the individual appliance supply line.
3. Correctly locate the appliance into its final operating position and using a spirit level, adjust the legs so that the unit is level and
at the correct height.
4. Connect the gas supply to the appliance. A suitable jointing compound which resists the breakdown action of LPG must be
used on every gas line connection, unless compression fittings are used.
5. Check all gas connections for leakages using soapy water or other gas detecting equipment.
NOTE: The burner operating pressure is to be measured at the manifold test point with 2 burners operating at ‘Full’
setting.
Fig 1
Rating Plate will be
located in this Area
DONOT USE ANAKED FLAME TO CHECK FOR GAS LEAKAGES.
Warning

2
Installation
10
Blue Seal Evolution Series Gas / Electric Convection Ranges © Copyright Moffat Ltd. 21 June 2016
Amendment 10
6. Check that the gas operating pressure is as shown in ‘Specifications’ section.
NOTE: Measure Burner Operating Pressure at manifold test point with 2
burners operating at ‘Full’ setting.
7. Verify the operating pressure remains correct.
Electrical Connection
NOTE: ALL ELECTRICAL CONNECTIONS MUST ONLY BE CARRIED OUT BY AN AUTHORISED PERSON.
Each appliance should be connected to an adequately protected power
supply and isolation switch mounted adjacent to, but not behind the
appliance. This switch must be clearly marked and readily accessible
in case of fire.
1. Check electricity supply is correct as shown on Rating Plate
attached to lower front hand side of front sill panel.
2. Supply terminal connections are located at rear of appliance.
Refer to ‘Electrical Connections’ in ‘Dimensions’ section of manual.
3. Open oven door and remove oven control panel, to allow
connection access for the electrical supply.
4. Connect mains supply to L1, L2 and L3 connection terminals.
Refer to 'Electrical Supply Requirements' section for connection
details.
NOTE: This appliance can be converted from 3 Phase to Single
Phase supply by connecting the single phase input to L1
and adding a bridge wire between the L1, L2 and L3
connections, (refer to Fig 3 opposite and the information
shown in the 'Electrical Supply Requirements Table' in the
'Specifications' Section).
5. Connect neutral and earth conductors to neutral stud and earth stud respectively.
6. For all connections, ensure that conductors are secure and appropriately terminated.
7. Tighten the cable gland to secure against tension on the cable.
8. Check polarity of each connection is correct to the mains connection terminals markings on the appliance.
NOTE:
This appliance must be earthed.
Fixed wiring installations must incorporate an all-pole disconnection switch.
9. Correctly locate the appliance into its final operating position and using a spirit level, adjust the legs so that the appliance is
level and at the correct height.
10. Connect power supply to the appliance.
11. Check electrical supply is within the input rating specification, refer to ‘Specifications’ section).
Fig 2
Manifold Test
Point
Add bridging
wires between
L1, L2 and L3.
Neutral supply
connection to N
Phase supply
connection to L1
P N
Fig 3
THIS APPLIANCE MUST BE EARTHED. IFTHE SUPPLY CORD IS DAMAGED, IT MUST BE REPLACED BY ASUITABLY QUALIFIED PERSON IN
ORDER TO AVOID AHAZARD.
Warning
Changing the supply from 3 phase to single phase will increase the electrical current
loading on the supply cable. Ensure that the supply cable used is of a sufficient size for
the current loading, refer to the 'Electrical Supply Requirements'.
Caution

2
Installation
11
Blue Seal Evolution Series Gas / Electric Convection Ranges © Copyright Moffat Ltd. 21 June 2016
Amendment 10
Commissioning
1. Before leaving the new installation;
a. Check the following functions in accordance with the operating instructions.
Light the Griddle.
Light the Open Burners. (F - Flame Failure Option).
Light the Open Burners. (PF - Pilot and Flame Failure Option).
Check the Low Fire Burner Operation.
Check the High Fire Burner Operation.
Check the Oven Heating.
Check the Oven Thermostat Operation.
Check the Oven Fan Operation.
b. Ensure that the operator has been instructed in correct lighting, operation, and shutdown procedure for the appliance.
NOTE: If for some reason it is not possible to get the appliance to operate correctly, shut ‘Off’ the gas supply and contact
the supplier of this appliance.

3
Operation
12
Blue Seal Evolution Series Gas / Electric Convection Ranges © Copyright Moffat Ltd. 21 June 2016
Amendment 10
3.1 Description of Controls
Description of Controls
Heating Indicator
Lamps (Amber) for
Top & Bottom
Elements
Power Indicator
Lamp (White)
Griddle Option
Burner Control
๐OFF Position
PILOT Burner
HIGH Flame
LOW Flame
Gas Control Knobs
Piezo Igniter
(Located here when fitted
with Griddle Option)
Open Burner Option
OFF Position
HIGH Flame
LOW Flame
Rear Burner
Front Burner
(Indicators are located above
the Gas Control Knobs).
Oven Top Heat Control
๐OFF Position
LOW Position
1Position
2Position
3Position
4Position
HIGH Position
Fig 4
Oven Thermostat
Control
๐OFF Position
Temperature Graduations 50°
C to 320°C

3
Operation
13
Blue Seal Evolution Series Gas / Electric Convection Ranges © Copyright Moffat Ltd. 21 June 2016
Amendment 10
3.2 Explanation of Control System
Safety System
The purpose of the safety system is to shut off the flow of gas if
the pilot flame goes out. It is comprised of the flame itself, the
thermocouple, and the flame failure gas valve.
The pilot flame is lit by holding in the gas control knob, which in
turn temporarily pushes the plunger inside the safety valve
open and allows gas to flow through. Once the burner is lit, the
thermocouple will begin to generate millivolts (after about 10 to
30 seconds of being heated) and will energize the
electromagnet inside the gas valve. Once energized the
electromagnet holds the plunger inside the gas valve in the
open position. The plunger has to be pushed all the way in for
the electromagnet to be able to hold it in place.
If the burner flame goes out for some reason, the thermocouple
will cool after about 10 to 30 seconds and stop generating
millivolts. The electromagnet will then de-energize, and the
plunger will snap shut, cutting off gas flow.
Detail of each component in the safety system is explained
below.
Millivolts are provided to the electromagnet by the
thermocouple (not shown) which generates millivolts when
heated. The thermocouple screws into a fitting at the back of
the gas valve to make an electric connection. By pressing in the
gas control knob, the plunger can be temporarily held open
while lighting.
There's two reasons for this; gas has to flow through the safety
valve to make it possible to light the pilot burner, and secondly
the plunger has to be pushed all the way in for the
electromagnet to hold it in. i.e. the electromagnet is strong
enough to hold the plunger in once there, but is not strong
enough to pull it in by itself. Sometimes a problem with the
flame not staying lit after releasing the button can be attributed
to not pushing the plunger all the way in.
The Fault Finding Charts at Section 5 should be used to identify
any incorrect operation. On correct identification of the
operating fault the Fault Finding charts will make reference to
the corrective action required, or refer to the Fault Diagnosis
section and / or Service section to assist in correction of the
fault.
The tip of the thermocouple is located in the pilot burner flame
and the nut at the other end of the thermocouple screws into
the back of the gas valve. Inside the copper tubing is a wire
which is joined at the tip but insulated from the rest of the
tubing. These two parts (the copper tubing and wire) make up
the "wiring" for an electrical circuit. When these two dissimilar
metals, wire and tip, are heated an electrical voltage is
produced.
This type of thermocouple generates between 7 and 30
millivolts when heated in the pilot flame.
Electromagnetic Flame Failure Gas Valve
The purpose of the safety valve is to shut off the flow of gas if
the pilot flame goes out.
Inside the body of the gas valve is an electromagnet connected
to a spring loaded plunger. When the electromagnet is
energized, it holds the plunger in, allowing gas to flow through
the valve. When the electromagnet is de-energized, the
plunger snaps to the closed position, stopping the flow of gas.
Figure 3.2a
Insulator Nut Conductor Tip
Internal
Wire
Thermocouple
The thermocouple is a device that generates electricity when
heat is applied to the tip.
Figure 3.2b
Thermocouple
Gas flow
Electromagnet
Plunger
Shaft
Knob
Gas flow Plunger
Control Knob

4
Maintenance
14
Blue Seal Evolution Series Gas / Electric Convection Ranges © Copyright Moffat Ltd. 21 June 2016
Amendment 10
4.1 Routine Maintenance
BLUE SEAL GAS / ELECTRIC RANGES - MAINTENANCE SCHEDULE
Business Name and Address:
Date: Service Report No.:
Phone: Fax:
Serial No:
Clients Order No: Serviceman:
Model: Blue Seal Gas / Electric Range. Remarks:
1 Inspect exterior condition of unit.
2 Check working gas pressure correct to rating plate. Pressure _______ kPa
3 Regrease gas cocks (Cooktop / Griddle if fitted).
4 Inspect thermocouples (Cooktop / Griddle-if fitted).
5 Replace all thermocouples (every 12 months).
6 Inspect injectors are clean and free from blockages.
7 Check piezo ignition of pilots (griddle-if fitted).
8 Check pilot flames.
9 Check for gas leaks.
10 Inspect supply leads and connections.
11 Inspect elements / element connections.
12 Check current draw of each element.
13 Check for arcing or loose screws on connections and contactors.
14 Check operation of temperature controller (thermostat).
15 Check function of indicator lights.
16 Check door micro switch operates fan when door opened.
17 Check door operation.
Service Comments:
Additional work / repairs required:
Customer Approval:
Customers Name (print): Title:
Customers signature: Date:
It is recommended that this form is photocopied and kept on file for continued use.

5
Fault Finding
15
Blue Seal Evolution Series Gas / Electric Convection Ranges © Copyright Moffat Ltd. 21 June 2016
Amendment 10
5.1 Fault Finding Charts
5.1.1 Cooktop
Open Burners
Fault Possible Cause Remedy
Pilot won’t light.
(PF fitted Burners only).
Gas control knob not held in.
No gas supply.
Gas pressure too low.
Blocked pilot injector.
Gas control valve faulty.
Hold in button while lighting pilot.
Ensure gas is connected and on (bottles
not empty).
Check gas supply pressure.
(Refer Specifications Section).
Clean or replace pilot injector.
(Refer Service Section 6.2.3 / 6.3.6).
Replace gas control valve.
(Refer Service Section 6.2.5 / 6.3.5).
Main burners will not light. Wrong size or blocked main injectors.
Obstruction in main burner.
Incorrect gas supply pressure.
Faulty gas control valve.
Replace / clean main injectors.
(Refer Service Section 6.2.2 / 6.3.3).
Clean main burner.
Check gas supply pressure.
Replace gas control valve.
(Refer Service Section 6.2.5 / 6.3.5).
Main burners go out when control knob
released.
Releasing knob before thermocouple
heated.
Pilot to small (PF burners only).
(Refer Fault Diagnosis 5.2.1).
Thermocouple incorrectly positioned.
Thermocouple faulty.
(Refer Fault Diagnosis 5.2.1).
Gas valve magnet faulty.
(Refer Fault Diagnosis 5.2.1).
Hold control knob in for longer (10 secs)
after lighting the burner.
Check gas supply pressure
(Refer Specifications section).
Clean or replace pilot injector
(Refer Service section 6.2.3 / 6.3.6).
Correctly re-position thermocouple.
Replace thermocouple.
(Refer Service Section 6.2.4 / 6.3.4).
Replace gas valve magnet.
(Refer Service Section 6.3.7).
Low fire rate too high. Incorrect gas supply pressure.
Low fire adjustment incorrect.
Check gas supply pressure.
Adjust low fire.
(Refer Service section 6.6.2).
Burner goes out when set to low position. Incorrect supply pressure.
Low fire rate set too low.
Check / adjust gas supply pressure.
Check / adjust low fire rate.
(Refer Service Section 6.6.2).
Main burner flame
incorrect colour (yellow / wavy).
Incorrect gas pressure.
Incorrect injector size.
Obstruction in burner.
Check supply pressure.
Check injector for correct size.
Inspect burner for obstruction.
ALL INSTALLATION AND SERVICE REPAIR WORK MUST BE CARRIED OUT BY SUITABLY QUALIFIED PERSONS ONLY.
Warning

5
Fault Finding
16
Blue Seal Evolution Series Gas / Electric Convection Ranges © Copyright Moffat Ltd. 21 June 2016
Amendment 10
Fault Possible Cause Remedy
Pilot flame small / lazy / yellow.
(PF fitted burners only).
Gas pressure too low.
Blocked / incorrect size pilot injector.
Check gas supply pressure.
(Refer Specifications section).
Clean or replace pilot injector.
(Refer Service section 6.2.3 / 6.3.6).
Pilot goes out when knob released.
(PF fitted burners only).
Releasing knob before the thermocouple is
heated.
Pilot flame too small.
(Refer Fault Diagnosis 5.2.1).
Thermocouple faulty.
(Refer Fault Diagnosis 5.2.1).
Gas magnet faulty.
(Refer Fault Diagnosis 5.2.1).
Hold control in for longer (10 sec), see if
pilot will stay lit.
Correct fault.
Replace thermocouple.
(Refer Service Section 6.2.4 / 6.3.4).
Replace gas magnet.
(Refer Service Section 6.3.7).
Open Burners (cont’d)

5
Fault Finding
17
Blue Seal Evolution Series Gas / Electric Convection Ranges © Copyright Moffat Ltd. 21 June 2016
Amendment 10
Fault Possible Cause Remedy
Pilot won’t light. Gas control knob not being held in.
No gas supply.
Gas pressure too low.
Blocked pilot injector.
Gas control valve faulty.
Hold in button while lighting pilot.
Ensure gas is connected and turned
‘On’ (bottles not empty).
Check gas supply pressure.
(Refer Specifications Section).
Clean or replace pilot injector.
(Refer Service Section 6.4.6).
Replace gas control valve.
(Refer Service section 6.4.1).
Piezo ignitor not sparking. Short in high tension lead.
(Refer Fault Diagnosis 5.2.2).
Check ignition electrode is not cracked and
is correctly positioned.
Piezo Ignitor faulty.
(Refer Fault Diagnosis 5.2.2).
Replace HT lead.
(Refer Service Section 6.4.9).
Re-position or replace ignition electrode.
Replace piezo ignitor.
(Refer Service Section 6.4.10).
Pilot flame small / lazy / yellow. Gas pressure too low.
Blocked / incorrect size pilot injector.
Check gas supply pressure.
(Refer Specifications Section).
Clean or replace pilot injector.
(Refer Service Section 6.4.6).
Pilot goes out when knob released. Releasing knob before the thermocouple is
heated.
Pilot flame too small.
(Refer Fault Diagnosis 5.2.1).
Thermocouple faulty.
(Refer Fault Diagnosis 5.2.1).
Gas magnet faulty.
(Refer Fault Diagnosis 5.2.1).
Hold control in for longer (10s), see if pilot
will stay lit.
Correct fault.
Replace thermocouple.
(Refer Service Section 6.4.7).
Replace gas control magnet.
(Refer Service Section 6.4.2).
Main burner will not light. Wrong size or blocked main injector.
Obstruction in burner.
Incorrect supply pressure.
Faulty griddle gas control valve.
Replace / clean main injector.
(Refer Service Section 6.4.4).
Clean burner.
Check supply pressure.
Replace griddle gas control valve.
(Refer Service Section 6.4.1).
Main burner flame incorrect colour
(yellow / wavy).
Aeration setting incorrect.
Incorrect gas pressure.
Incorrect injector size.
Obstruction in burner.
Adjust griddle burner aeration.
(Refer Service Section 6.6.3).
Check supply pressure.
Check injector correct size.
Inspect burner for obstruction.
Pilot goes out when control knob released. Incorrect gas pressure.
Faulty gas control valve.
Check supply / adjust pressure.
(Refer Specifications Section).
Replace griddle burner gas control valve.
(Refer Service Section(6.4.1).
Griddle Burner

5
Fault Finding
18
Blue Seal Evolution Series Gas / Electric Convection Ranges © Copyright Moffat Ltd. 21 June 2016
Amendment 10
Fault Possible Cause Remedy
Low fire rate too high. Incorrect supply pressure.
Low fire adjustment incorrect.
Check supply / adjust pressure.
(Refer Specifications Section).
Adjust griddle low fire setting.
(Refer Service Section 6.6.4).
Griddle Main burner goes out when control
knob released.
Incorrect supply pressure.
Low fire adjustment incorrect.
Check supply / adjust pressure.
(Refer Specifications Section).
Adjust griddle low fire setting.
(Refer Service Section 6.6.4).
Griddle Burners (cont’d)
Other manuals for Evolution Series
10
This manual suits for next models
3
Table of contents
Popular Hob manuals by other brands
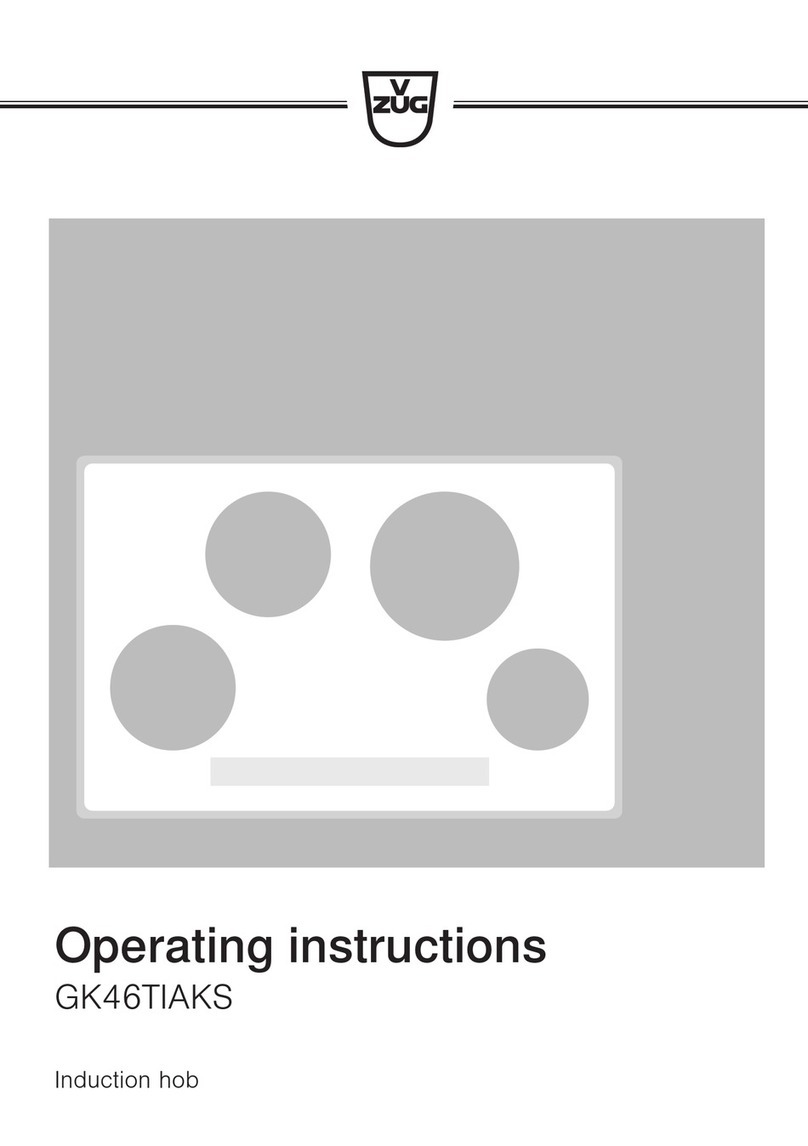
V-ZUG
V-ZUG GK46TIAKS operating instructions
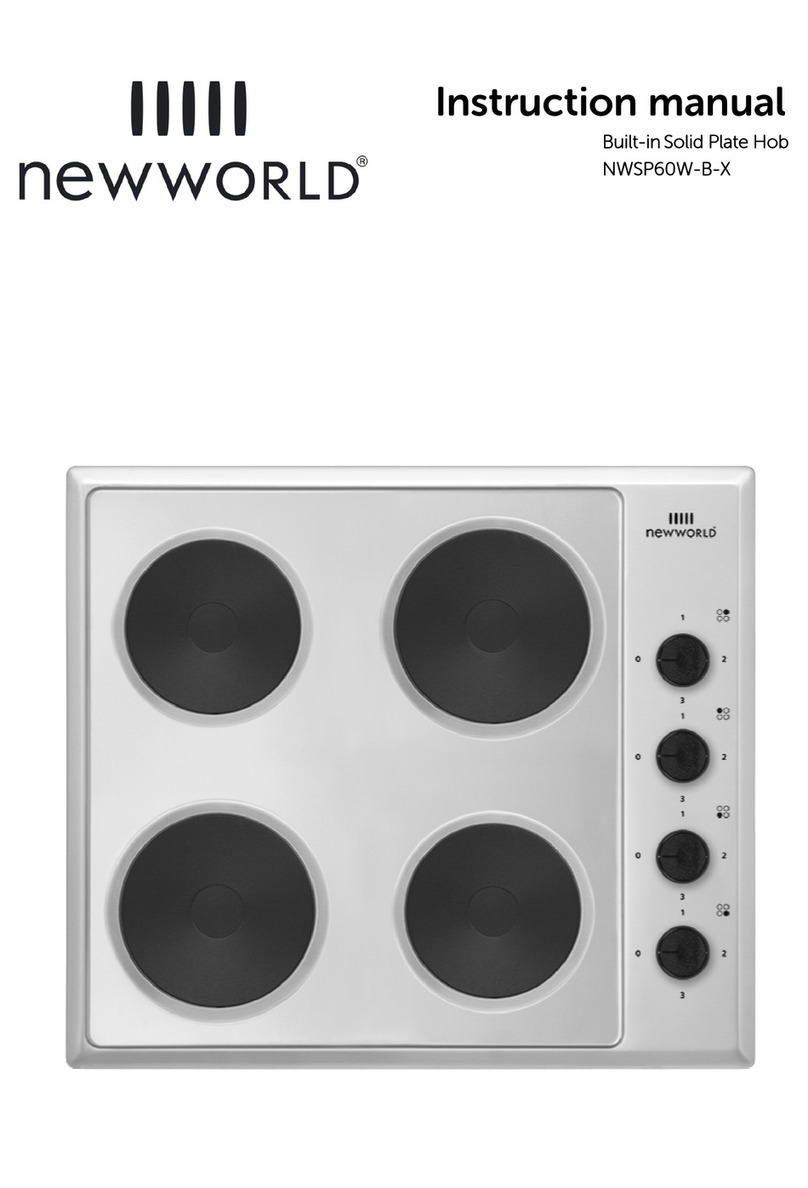
New World
New World NWSP60W-B-X instruction manual
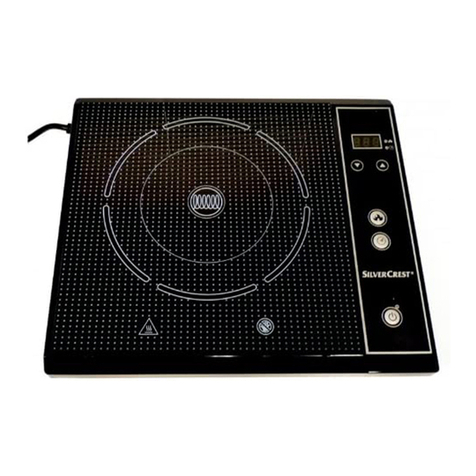
Silvercrest
Silvercrest SILVERCREST SIKP 2000 A1 operating instructions
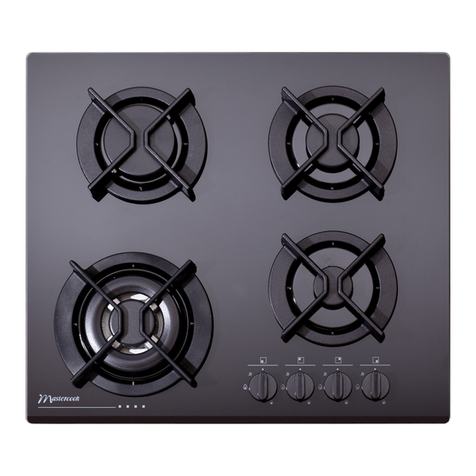
Master cook
Master cook 2CMI-4GLST Instructions for use and maintenance

Goldline
Goldline GL301N installation instructions

Range Master
Range Master RMB70HPNGFGL user guide