CO-TRUST E10 Series User manual

User Manual of E10 Series AC Servo Driver
2
Contents
1 SAFETY ANNOUNCEMENT ........................................................................................4
2 SPECIFICATIONS ........................................................................................................7
3 INSTALLING...............................................................................................................11
3.1 Driver Installing Environment ....................................................................11
3.2 Driver Environmental Condition.................................................................11
3.3 How to Install Driver..................................................................................11
3.4 Installation Direction and Intervals ............................................................12
3.5 Motor Installation Environment..................................................................13
3.6 How to Install Motor ..................................................................................13
4 WRING........................................................................................................................16
4.1 The Main Power Input Terminal................................................................17
4.2 Control Power Input Terminal....................................................................17
4.3 Braking Resistance and Bus Output Terminals.........................................17
4.4 Motor power cable interface......................................................................19
4.5 Permanent magnet safe brake of Motor....................................................19
4.6 Encoder Input Interface Terminal..............................................................20
4.7 Control Interface Terminal.........................................................................21
4.8 Communication Interface Terminal、Terminal Resistance and Restore Factory Default..24
5 DETAILS OF CONTROL AND GIVEN SIGNAL .........................................................28
5.1 Given Command Source...........................................................................28
5.2 Control Signal Definition and Multiplexing Choice.....................................29
5.2.1 Selection of Digital input multiplexing functions ..............................30
5.2.2 Selection of External input logic level..............................................33
5.2.3 Selection of Digital output multiplexing functions ............................34
5.2.4 Pin function configuration & simu IO...............................................35
5.3 Details of Control Signal............................................................................38
5.4 Selection of Internal Speed Switching Under External Speed Control Mode....................46
5.5 Communication command selection under communication control mode (P4=4).............47
5.6 Selection of Torque Limitation Output(TLC) and Zero-speed Detection Output(ZSP) Signal48
6 PARAMETER LIST.....................................................................................................49
6.1 Parameter Checklist..................................................................................49

User Manual of E10 Series AC Servo Driver
3
6.2 Details of Parameters................................................................................52
6.3 Electronic gear ratio Setup........................................................................80
7 COMMUNICATION FUNCTIONS ...............................................................................81
7.1 Introduction of CANopen protocol.............................................................81
7.2 Introduction of ModBus RTU Protocol.......................................................84
8 APPLICATIONS OF BASIC CONTROL MODES.......................................................90
8.1 Test Run....................................................................................................91
8.2 External Control Mode ..............................................................................93
8.2.1 Application Example of External position control mode...................93
8.2.2 Application Example of External speed control mode.....................96
8.2.3 Application Example of External torque control mode.....................97
8.3 Communication control mode....................................................................98
8.3.1 Application Example of Communication position control mode.......98
8.3.2 Application Example of Communication speed control mode .......104
8.3.3 Application Example of Communication torque control mode.......108
9 INTRODUCTION AND EXAMPLE OF APPLICATION FUNCTIONS .......................110
9.1 Homing Function.....................................................................................110
9.2 Communication Multi-Position\Speed\Torque control .............................125
9.3 Adjustment function of Pulse...................................................................128
9.4 Special Speed-Position Control Mode.....................................................130
10 PROTECTIVE FUNCTION......................................................................................136
11 GAIN ADJUSTMENT..............................................................................................141
11.1 System Control Block Diagram of E10 Series Servo Driver..................141
11.2 Setup the Related Gain Parameters of Servo.......................................141
11.3 The Curve Graphic of Servo Upper Computer MagicWorks Tuner.......145
11.4 The Principles and Methods of Parameter Adjustment .........................147
11.5 Gain Switching......................................................................................148

User Manual of E10 Series AC Servo Driver
4
1 Safety Announcement
Please be sure to observe
To avoid personal injury and possession damage, the matters which need attention will
be explored in more detail below.
Please read the following instructions or precautions carefully before using the servo
driver, and must be complied with the installation and debugging preventive measures
and operating procedures.
Disclaimer: Because the user not strictly in accordance with the operating requirements,
causing serious consequences, and CO-TRUST is not responsible for.
The following DANGER and CAUTION symbols are used according to the level of
dangers possibly occurring if you fail to observe the instructions or precautions indicated.
DANGER
Danger indicates an imminently hazardous situation which, if not
Operate according to the requirement, will result in personal injury"
CAUTION
Caution indicates a potentially hazardous situation which, if not
operate according to the requirement, may result in mild or moderate
injury and equipment damage.
DANGER
Only professional electrical engineer should be allowed to
handle wiring.
May cause an electric shock and fire
danger.
Please confirm the input main power is on shut-off status
before wiring.
May cause an electric shock and fire
danger.
Please tightly connect power terminal with motor connectors.
May cause an electric shock and fire
danger.
Please do not touch the output terminals directly; The Output
line of Servo driver must avoid shorting with shell, and never
short the output line.
May cause an electric shock and fire
danger.
Please set up safety device such as breaker etc, so as to cut off
power supply in time while external circuit short circuit and
equipment failure occur.
May cause an electric shock and fire
danger.

User Manual of E10 Series AC Servo Driver
5
DANGER
Please do not dismantle after servo driver power-ON.
May cause an electric shock.
For a while after power off, the internal circuits of driver is kept
at higher voltage, please perform the transportation and wiring
at least 15 minutes after the power off.
May cause an electric shock.
Do not use it in vibration 、fierce shock place.
May cause an electric shock, personal
injury and fire danger.
Don’t submerge the cable to oil and water.
May cause an electric shock,
equipment malfunction or damage.
Do not use wet hands for wiring and operation.
May cause an electric shock and
personal injury.
Do not insert your hands into the driver.
May cause an electric shock and
burns.
Avoid the place where the driver is subjected to dust, corrosive
gases, conductive objects (such as copper cuttings), liquids
and inflammables.
May cause an electric shock and fire
danger.
Avoid to place flammable objects near motors, drivers and
regenerative resistors.
May cause an electric shock and fire
danger.
Don't touch the motor, driver radiator or its regenerative
resistor, since they become hot.
May cause an electric shock and
burns、equipment malfunction or
damage.
Make sure to ground the earth terminal of the driver and motor.
If not connect to ground, may cause
an electric shock.
CAUTION
Don’t seize the cable、encoder line or motor shaft while
transporting.
May cause personal injury and
equipment malfunction or damage.
Avoid to use the servo driver in cases of damage, short of
materials.
May cause personal injury.
Avoid to use it under direct sun beams.
May cause fire danger.

User Manual of E10 Series AC Servo Driver
6
CAUTION
Avoid to block the ventilation holes of driver, and do not let
foreign matter fall into the servo driver.
May cause fire danger.
Please comply with the requirements of installation method
and direction.
May cause personal injury and
equipment malfunction or damage.
Don’t connect the input power wire to the output terminal U, V,
and W.
May cause equipment malfunction or
damage.
When two or more servo drivers place in the same cabinet ,
please ensure servo interval and effective heat transfer.
May cause personal injury and
equipment malfunction or damage.
If an error occurs, remove the causes for the error and secure
the safety before rebooting the operation.
If do not eliminate alarm error, may
cause personal injury.
When driver failure occurs , please cut off the power supply of
the driver.
If large current continued to flow
through, may cause fire danger.
If necessary to use external braking resistor, please further
preparation, and don't touch braking resistor while working.
May cause an electric shock and
personal injury.
Please input specified voltage, do not connect 220V AC power
to the 24V DC control power of the servo driver.
May cause equipment malfunction or
damage.
Please process trial operation phase of servo motor while
servo motor and mechanical transmission axis is under
unconnected status.
May cause personal injury.
The nominal torque of servo motor should be greater than the
actual load torque.
The long-term use may cause
equipment malfunction or damage.
Non-professionals are not allowed to perform repair and
maintenance for servo driver.
May cause personal injury and
equipment malfunction or damage.
Please cut off the power supply in case of long time no use.
May cause personal injury.

User Manual of E10 Series AC Servo Driver
7
2 Specifications
Technical Specifications for Driver
Type Specification
E10 Servo driver
Order No.
200W (Low inertia)
CTSD E10-B2012-M000
400W (Low inertia)
CTSD E10-B4012-M000
750W (Low inertia)
CTSD E10-B7512-M000
1KW (Low inertia)
CTSD E10-B1022-M000
1KW (Middle inertia)
CTSD E10-B1022-M001
200W (Low inertia +
CANopen)
CTSD E10-B2012-M100
400W (Low inertia +
CANopen)
CTSD E10-B4012-M100
750W (Low inertia +
CANopen)
CTSD E10-B7512-M100
1KW (Low inertia +
CANopen)
CTSD E10-B1022-M100
1KW (Middle+CANopen)
CTSD E10-B1022-M101
Basic Specifications
Input
Power
Main Power
Single phase, 220VAC±15%, 50/60Hz
Control Power
24VDC±15%
Encoder Feedback
Incremental Encoder, 2500 p/r (Resolution: 10000)
Cooling Method
Natural cooling (200W、400W), Fan-cooling (750W、1KW)
Control Method
Use FOC(Magnetic positioning control)and SVPWM(Space
Vector Modulation)
Communication Functions
Modbus protocol, Based on RS-485, support radio
CANopen protocol
Braking Resistance
Internal / External braking resistance(Mainly applied to
emergency start-stop situation)
Protective Function
Over-voltage、
under-voltage、
over-current、
over-load、
over-heat、
over-speed、excess position deviation、encoder feedback error、
over-braking ratio、overtravel inhibit、EEPROM error etc.
Display and Operation
5 LED Digital lights, can connect external servo debugger
Parameter Setup
MagicWorks Tuner software or connect external servo debugger

User Manual of E10 Series AC Servo Driver
8
Properties
Speed rate
of change
Load rate of
change
0~100%: 0.1% or less(Under rated revolution)
Voltage rate of
change
Rated voltage:±15%: 0%(Under rated revolution)
Temperaturer
ate of change
25±25℃: ±0.1% or lower(Under rated revolution)
Frequency Response
100Hz(when JL=JM)
Integrated PLC Control
Function
NO
Input And Output Signal
Position
Output
Output Type
Open-collector output
Digital Input (7DI)
Servo-ON、Alarm clear、CW/CCW overtravel inhibit、Internal
speed selection、
torque limitation selection、
Gear ratio switching、
Control Mode switching、Gain switching、pulse input inhibit、
zero-Speed clamp、positional deviation clear, IO multiplexing
function registers selection.
Digital Output (4DO)
Servo-Ready、Alarm output、Torque limit output、Positioning
complete、SpeedArrival、Zero -Speed detection output、Brake
clear output, IO multiplexing function registers selection.
Analog Input
12bit A/D: 1 input
Position Control Mode
Max. Input Pulse Frequency
Differential method: 500KHz, open-collector method: 200KHz
Pulse Command Mode
Pulse+Direction, A+B, CW+CCW
Command Control Mode
External pulse control /16 communication register command
Feedforward Compensation
0~1000‰(Setup resolution 1‰)
Positioning Complete
0~32767 command unit(Resolution set to 1 command unit)
Electronic Gear Ratio
Electronic Gear Ratio :N/M times, N:1~10000,
M:1~10000(1/200<N/M<200)

User Manual of E10 Series AC Servo Driver
9
Speed Control Mode
Analog
Input
Voltage
Range
-10V~+10V(Resolution:12 bit )
Input
Resistance
19K
Sampling
Frequency
1KHz
Command Control Method
External analog Command/8 internal speed command/32
communication register command
Command Smoothing Mode
Lowpass filtering, Smoothing time constant: 0~2500(x10us)
Torque Limitation
Internal parameters/External analog
Torque Control Mode
Analog
Input
Voltage
Range
-10V~+10V(Resolution:12 bit )分辨率1
Input
Resistance
19K
Sampling
Frequency
1KHz
Command Control Mode
External analog Command /32 communication register command
Command Smoothing Mode
Lowpass filtering, Smoothing time constant :0~2500(x10us)
Speed Limitation
Internal parameters/External analog
Application Environment
Operating Temperature
0℃~55℃
Storage Temperature
-20℃~70℃
Humidity
Lower than 90% RH (No condensation)
IP Level
IP20
Installation Place
No corrosive gas, inflammable gas, oil mist or dust etc.
Installation Method
Install in vertical position
Altitude
Lower than 1000m
Atmospheric Pressure
86Kpa~106Kpa
Cable Type
Motor cable
Order No.
200W, 400W, 750W, 1KW
(Low inertia)
CTSD MOL-M3110
1KW (Middle inertia)
CTSD MOL-M3120
Encoder cable
Order No.
200W, 400W, 750W, 1KW
(Low inertia)
CTSD ENL-M3110
1KW (Middle inertia)
CTSD ENL-M3120

User Manual of E10 Series AC Servo Driver
10
Model Description of Servo Driver
Model Description of Servo Motor
The cable Model Description of Motor and Encoder
C T S D M16-B4011-M000
C T S D MOL-M3110
Reserved
0
CO-TRUSTDriver products
CO-TRUSTDriver products
CTSD
CTSD
Rated power 40X10 W : ( )
1
401
Without Band-type brake
None
With Band-type brake
Power cable with Band-type brake wires
0
1
0
1
Motor
Motor power cable
Encoder cable
M
MOL
ENL
Low inertia
Middle inertia
High inertia
1
A
2
M
3
H
380VAC
220VAC
80VDC
A
B
C
60 60mm*
80 80mm*
110 110mm*
130 130mm*
180 180mm*
6
8
B
D
I
Optical axis with Flat、
Solid With Keys、
Directly outgoing line
Solid With Keys and Screw holes、
AirSockets outgoing line
Solid With Screw holes、
0
1
1
2
2
3
Aseries motor
Adaptive series E10 series:
M seriesmotor
H1A series
Hseriesmotor
H2A series
A
1
M
A
H
2
9pin General Encoder
Cable length 3m:
9pin Wiring-saving Encoder
5m
15pin None-sparing Encoder
7m
20pin None-sparing Encoder
0
3
1
5
2
7
3
Flange Dimensions :
Motor Specification :
Aseries motor
M seriesmotor
Hseriesmotor
Voltage Identification:
CTSD E10-B4012-M000
CO-TRUST Driver productsCTSD Supplement flag bit00
Economical servo driver
Standard Low-Voltage Servo Driver
Standard High-Voltage Servo Driver
E10
H1A
H2A
380VAC
220VAC
80VDC
Voltage Identification:
A
B
C
Rated Power 1
: ( )40X10 W
401
0
1
2
Support Modbus Protocol
Support Modbus and CAN Protocols
A
M
H
Adapt to A series motor
Adapt to M series motor
Adapt to H series motor
0
1
2
3
9pin General Encoder interface
9pinWiring-savingEncoderinterface
15pinNone-sparingEncoderinterface
20pinNone-sparingEncoder interface
SupportModbusand
Industry Ethernet Protocols

User Manual of E10 Series AC Servo Driver
11
3 Installing
Installing Driver and Motor
Please properly install the servo driver and servo motor to avoid malfunctions or
accidents.
3.1 Driver Installing Environment
The storage and installation of products must satisfy the environmental
requirements.
Servo driver must install according to the direction and the interval of the
specifications, and shall be in good heat dissipation condition.
Installation must use fireproofing material, and shall not be installed on top or near
the inflammables in order to prevent fire.
Electric cabinet that used to install servo driver should prevent dust, corrosive gas,
conductive objects (such as copper chips), liquid and inflammables etc.
Servo driver and servo motor should avoid shock and vibration.
3.2 Driver Environmental Condition
Item
Conditions
Operating temperature
0 °C to 55 °C
Storage temperature
-20 °C to +70 °C
Ambient Humidity
Lower than 90% RH (No condensation)
Altitude
Lower than 1000 meters
Vibration
10~57Hz 3.5mm, 57~150Hz 1g
Atmospheric Environment
No Corrosive gas, inflammable gas, oil mist or dust etc.
3.3 How to Install Driver
The servo driver use base plate installation method, install in vertical direction, the
schematic diagram of base plate installation see as figure 3.1:

User Manual of E10 Series AC Servo Driver
12
143.8
527.5 5 5
55
201
189 0
Ø5
175
43±0.3
Figure 3.1 Base plate installation method of Servo driver
3.4 Installation Direction and Intervals
In order to allow enough space surrounding for ventilation, please leave larger
interval when in actual installation.
So as to prevent the ambient temperature of the driver continuing to rise, best to
contain a radiator in electricity cabinet to blow reciprocal winds to the driver.
Figure 3.2 Installation intervals for one or more servo drivers

User Manual of E10 Series AC Servo Driver
13
3.5 Motor Installation Environment
Avoid installing the motor in rain water and direct sunshine rooms.
Avoid the place where the motor is subjected to dust, corrosive gases, conductive
objects, liquids and flammable gases.
Keep motor in well-ventilated, no humidity, no oil and no water places.
Ambient temperature should be held in -20~50℃(No freezing), in case of motor
operates for a long-term under small space or near heating equipment, should
consider to use forced cooling.
Humidity should not higher than 90%RH(No condensation).
Servo motor should avoid vibration and impact.
3.6 How to Install Motor
1. Maters needing attention in installation
Encoders are high precision components, please remember to protect when
handling or installation, also should avoid to knock or collide.
Please do not use a hammer knocking directly on axial end when install or remove
the coupling in the motor shaft.
Try perfect alignment between shafts, otherwise may cause vibration, and damages
of the bearings.
Avoid dragging motor shaft, outgoing line or encoder when handling the motor.
This motor isn't subjected to water and/or oil drops, please put the cable outlet
downward when installing the motor.
Don't use the motor with the cables being immersed in oil or water.
Avoid long time in the overloading operations, otherwise the motor will be damaged.
Be sure to firmly install the motor, and should prepare some measures to against
loosening.
2. Installing method
The Servo motor can be installed either vertically or horizontally. Installation dimension
refer to following figures.

User Manual of E10 Series AC Servo Driver
14
C0.012
2 0
Ф14h6
Ф50h7
6 0 .5
3 0
2
3 7
L
Ф70
4 4 5-.Ф
11 0
-.01
50
-.0 03
A-A
1.5: 1
3 .2
200W L=102
400W L=122
Figure 3.3 200W/400W (Low inertia) type Motor installation dimension (Unit: mm)
4-Φ6
Φ90
80
80
8
25
.
3
35 L
Φ70 0
-0.030
Φ19 0
-0.018
A
60
-0.03
15.5 0
-0.1
A-A
750W L=150
1.0KW L=190
Figure 3.4 750W/1KW(Low inertia) type Motor installation dimension (Unit: mm)
4-Φ9
Φ145
130
14
40
Φ22h6
Φ110h7
.
5
57 166
2.5
6h9
24.5 0
-0.1
M6XL22 A
A-A
1.5:1
Figure 3.5 1KW(Middle inertia) type Motor installation dimension (Unit: mm)

User Manual of E10 Series AC Servo Driver
15
3. Technology parameter of Motor
Motor
Type
Rated
Power
Rated
Voltage
Rated
revolution
Rated
Torque
Rated
Current
Peak
Torque
Back-Emf
Constant (Ke)
Poles
Rotor
Inertia
Feedback
Encoder
CTSD
M16-B201
1-M000
200W
220VAC
3000rpm
0.637N·
m
1.5A
1.911N·
m
28V/Krpm
4
0.17
Kg·cm2
2500ppr
Incremental
Encoder
CTSD
M16-B401
1-M000
400W
220VAC
3000rpm
1.27N·m
2.8A
3.8 N·m
28V/Krpm
4
0.302
Kg·cm2
2500ppr
Incremental
Encoder
CTSD
M16-B751
1-M000
750W
220VAC
3000rpm
2.39N·m
3A
7.1N·m
48V/Krpm
4
1.82
Kg·cm2
2500ppr
Incremental
Encoder
CTSD
M16-B102
1-M000
1.0KW
220VAC
2500rpm
4N·m
4.4A
12N·m
56V/Krpm
4
2.97
Kg·cm2
2500ppr
Incremental
Encoder
CTSD
M2D-B102
2-M200
1.0KW
220VAC
2500rpm
4N·m
4.0A
8N·m
72V/Krpm
4
8.5
Kg·cm2
2500ppr
Incremental
Encoder

User Manual of E10 Series AC Servo Driver
16
4 Wring
General wiring diagram
Those who are authorized for wiring or inspection must qualify to the job.
To avoid electrical shock hazards, please perform the wiring and inspection at least
15 minutes after the power off.
Figure 4.1 External port schematic diagram

User Manual of E10 Series AC Servo Driver
17
4.1 The Main Power Input Terminal
Terminal
No.
Symbol
Name
Description
X5
L1
Main Power Input Terminal
Single phase input 220VAC±15%,
50/60Hz
N
PE
Caution
In order to improve anti-jamming ability, advise to provide the power supply through
noise filter.
Advise to install the none-fusing type of circuit breaker so as to cut off the external
power supply in time while driver failure occurs.
To avoid electric shocks, you can choose isolation transformer to provide electrical
power.
Be sure to connect the grounding terminal PE with the electricity cabinet to the
ground, multiple servos to avoid connecting with ground in series.
Proposal specification list of driver peripheral equipment:
Wire thickness of the main power: 750W/1.0KW 0.75mm2/AWG15
Rated current of breaker: 10A/Per one breaker
Noise filter: Single phase power filter(First-order common mode +First-order differential mode)
Rated voltage: AC 0-300V、40-440Hz Rated Current: 10A
4.2 Control Power Input Terminal
Terminal
No.
Symbol
Name
Description
750W/1.0KW
X4
0V
Control Power 24VDC
Input Terminal
Control Power Input Range:
24VDC±15%
24V
Caution
The control power of E10 series servo adopt to 24VDC for power supply,avoid to
switch-on 220V AC power supply.
The rated current consumption of control power for a single servo is 450mA; 24V
DC control power recommends 2A as the rated current.
4.3 Braking Resistance and Bus Output Terminals
Terminal
No.
Symbol
Name
Description
X7
DCN
The negative of direct current bus
The negative bus inside the driver.
RB1
Brake resistor terminal
The brake output terminal inside the
driver.
RB2
Internal Brake resistor terminal
The brake resistor inside the driver.

User Manual of E10 Series AC Servo Driver
18
DCP
The positive of direct current bus
The positive bus inside the driver.
Caution
Avoid to set P132 to 2 while using internal brake resistor.
Please install the external braking resistance on incombustible matters such as
metal etc, advise to set external protection like temperature insurance etc.
Usually shorted RB1 and RB2, if "Excessive brake ratio" alarm occurs, please
disconnect RB1 with RB2, and insert a proper external braking resistor between
DCP and RB1, the specification recommend to use 100Ω 200W~300W, and set
P132 as 1 or 2.
DCP and DCN are the DC bus terminals of driver, applied to DC common bus of
multiple servos system.
Please don't touch driver braking resistance and bus terminal within 15 minutes after
the power off.
Advised not to use common DC bus, if really have to use common DC bus, the
phase of the input power source must be the same. Such as if one servo connect R
to N, other servos cannot connect T to N,or S to N.The diagram of wiring see as
follows:

User Manual of E10 Series AC Servo Driver
19
4.4 Motor power cable interface
Terminal
No.
Symbol
Name
Description
X6
U
U phase of Motor
Corresponds to the motor
V
V phase of Motor
Corresponds to the motor
W
W phase of Motor
Corresponds to the motor
PE
Ground terminal
Corresponds to the motor
Caution
Match the colors of the motor lead wires to those of the corresponding motor output
terminal U、V、W.
Please make sure to connect the grounding terminals of the motor to avoid electric
shock.
Don't touch the motor terminals, as the U、V and W phases of the motor will remain
high pressure after power off.
The plug serial number of U、V、W、PE (200W、400W、750W、1000W Low inertia
motor) is: 3、2、1、4; The plug serial number of U、V、W、PE (1000W middle inertia
motor) is: 2、3、4、1;
4.5 Permanent magnet safe brake of Motor
The wiring diagram of motor permanent magnet safe brake see as follows:
200W/400W Permanent magnet safe brake of Motor
Voltage:24V
Wiring:1→24V、2→0V
Relay
1
3
5
7 8
6
2
4
Connectto 0V
Connectto 9' (COM- of
driver connectto 0V)
or connectto the output
points ofPLC
Connectto 2 4V+
Connectto 24V+
1
2
16
-+AMP
750W/1000WPermanent magnet safe brake of Motor
Voltage:24V
Wiring:1→24V、2→0V、3→Null
31
Relay
1
3
5
7 8
6
2
4
Connectto 0V
Connectto 9' (COM- of
driver connectto 0V)
or connectto the output
points ofPLC
Connectto 2 4V+
Connectto 24V+
2
<Note> Connect the control terminal of brake resistance via relay (Control terminal: DC24V, load
capacity is greater than or equal to 1A), and connect a Schottky diode in parallel at the control terminal of
relay (Diode type is recommended as 1N4148, Package: DO-35 glass package, instrumented).

User Manual of E10 Series AC Servo Driver
20
Please refer to Figure 4.4 or 4.5 for the wiring diagram.
4.6 Encoder Input Interface Terminal
E10 series servo motor adopt to connect incremental encoder signal, which including
encoder power, A、B、Z signal and shield layer(Contains Hall signal U、V、W), the specific
wiring see below table:
Terminal
No.
Connector
Pin of
servo
Pin of motor
(Low inertia)
Pin of motor
(Middle inertia)
Name
X2
1
10
11
Hall signal V+
2
6
12
Hall signal W+
3
7
6
Encoder signal Z+
4
4
4
Encoder signal A+
5
9
5
Encoder signal B+
6
12
14
Hall signal V-
7
8
15
Hall signal W-
8
5
9
Encoder signal Z-
9
14
7
Encoder signal A-
10
13
8
Encoder signal B-
11
11
10
Hall signal U+
12
15
13
Hall signal U-
13
2
2
Encoder signal +5V
power supply
14
3
3
Encoder grounding
15
1
1
PE grounding
Caution
Short-circuiting between Encoder PE grounding wire and Encoder signal lines might result
in damage of servo and motor.
1
5
610
15 11
V+
W+
Z+
A+
B+
V-
W-
Z-
A-
B-
U+
U-
+5V
GND
PE 15141211
1 2 4 5
+5V GND A+ Z-
W+Z+ W- B+V+
U+V- B- A- U-
PE
12
5 3 610
13 15 1411
Viewing from Servo Viewing from Motor(Low inertia) Viewing from Motor(1KW Middle inertia)
Figure 4.2 Encoder interface
Table of contents
Popular Servo Drive manuals by other brands
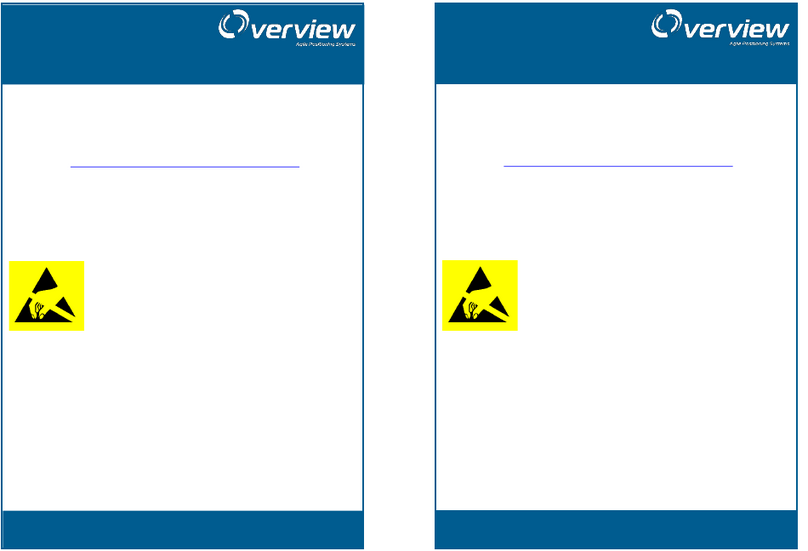
Overview
Overview Leto OVU00243 quick start guide
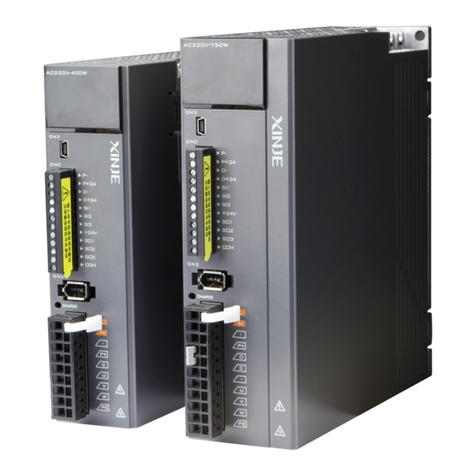
Xinje
Xinje DS5L1 Series user manual
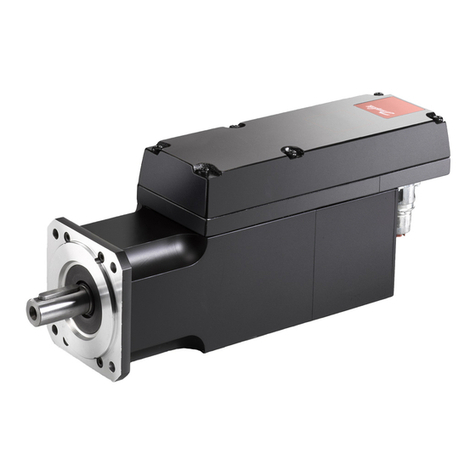
Danfoss
Danfoss VLT Integrated Servo Drive ISD 510 System Design guide
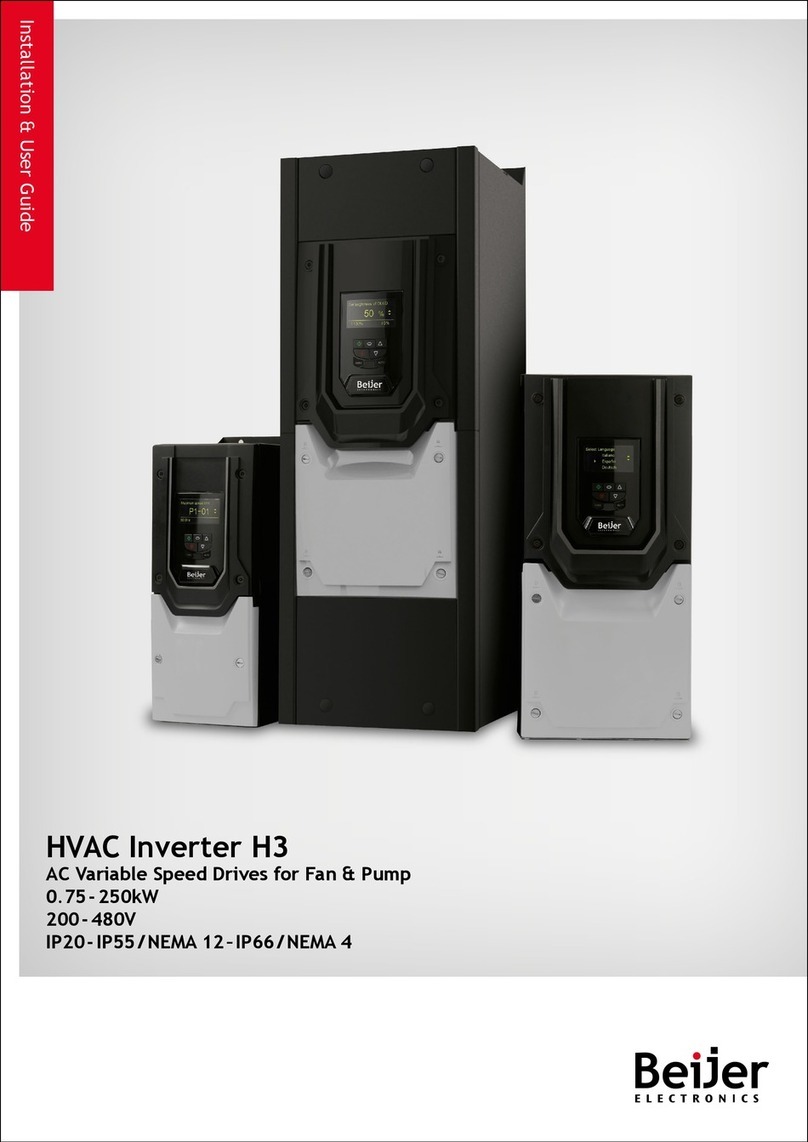
BeiJer
BeiJer BFI-H3-22-0043-1F12-MN Installation & user guide
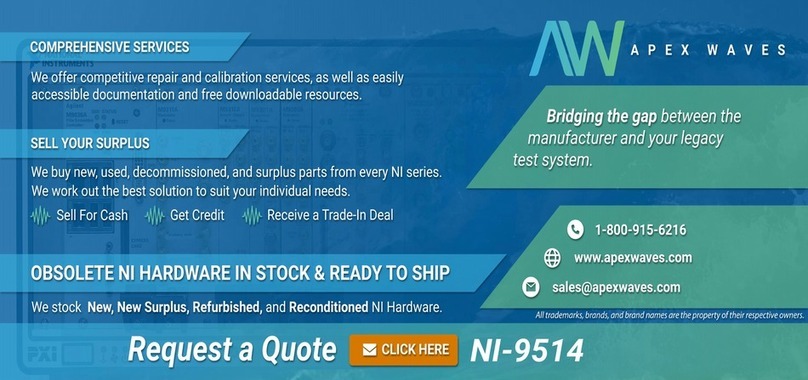
National Instruments
National Instruments NI 9516 Operating instructions and specifications

Mitsubishi
Mitsubishi MR-JE-10A instruction manual