CowTech Ciclop 3D User manual

CowTech Ciclop 3D
Scanning Guide
[Document subtitle]
CowTech Engineering, LLC
Big Timber, MT

CowTech Ciclop 3D Scanning Guide
1
Introduction................................................................................................................. 2
Things to Have Before Starting.................................................................................... 3
Assembling the Hardware.........................................................................................................................3
Assembling the Electronics ....................................................................................................................... 3
Installing the Software .............................................................................................................................. 6
How the 3D Scanner Works ........................................................................................ 7
Selecting an Object...................................................................................................... 8
Calibration.................................................................................................................... 9
Connecting the Camera ..........................................................................................................................10
Using the Control Workbench ................................................................................................................ 10
Using the Adjustment Workbench.......................................................................................................... 12
Using the Calibration Workbench...........................................................................................................19
Using the Scanning Workbench .............................................................................................................. 22
Post-Processing Tips .................................................................................................. 24
Inverting Normals Before Generating A Mesh........................................................................................ 24
Exporting A Mesh With Texture in .OBJ Format .....................................................................................27
Supplemental Troubleshooting Guides..................................................................... 34
Precisely Calibrating the Stepper Motor Driver......................................................................................34
Tips for Troubleshooting Camera Connectivity Problems ......................................................................36

CowTech Ciclop 3D Scanning Guide
2
Introduction
This guide was written for use with the CowTech Ciclop 3D Scanner, which began as a Kickstarter project
in February 2016. The aim of this guide is to show you how to get the highest quality scans possible, and is
based off our own experience with using the scanner. It covers the physical act of scanning an object
utilizing your Ciclop and a free accompanying program called Horus, and assumes that you already have a
scanner built and ready to go. For help with assembling your CowTech Ciclop 3D Scanner, please see our
assembly guides on the CowTech website: http://www.cowtechengineering.com/downloads
This guide is not comprehensive. Usually there is a significant amount of post-processing work to be done
after a scan. Although we do offer some related tips, please refer to the links below for help with any kind
of post-processing work (if for example you want to turn your raw scans into meshes usable with a 3D
printer or other 3D software packages).
We also highly recommend taking a look at the following resources if you need troubleshooting help not
covered in this document.
Post-processing and Scanning Guides:
CowTech website’s downloads section - http://www.cowtechengineering.com/downloads
BQ’s Ciclop and Horus Documentation Page - http://diwo.bq.com/en/documentation-ciclop-and-
horus-2/
Horus Github - https://github.com/bqlabs/horus
Troubleshooting Hardware and Electronics Related Issues:
CowTech Ciclop Facebook Group - https://www.facebook.com/groups/564912093672675/
CowTech Ciclop 3D Scanner Google Group –
https://groups.google.com/a/cowtechengineering.com/forum/?hl=en#!forum/cowtech-ciclop-
3d-scanner
Troubleshooting Software Related Issues
BQ Ciclop 3D Scanner Google Group - https://groups.google.com/forum/#!forum/ciclop-3d-
scanner
Horus Github - https://github.com/bqlabs/horus

CowTech Ciclop 3D Scanning Guide
3
Things to Have Before Starting
There are a number of items you will want to have on hand before you begin scanning.
Assembling the Hardware
You will need a fully assembled Ciclop. If you haven’t done so yet, please refer to the “downloads” section
of the CowTech website for assembly instructions:
http://www.cowtechengineering.com/downloads
It is important to build the scanner in the order prescribed by the assembly instructions. Some parts in the
assembly are press fit and cannot be taken apart again without risking damage. It pays to get it right the
first time.
Assembling the Electronics
The following sections will walk you through the process of putting the electronic components of the
scanner together. This section is here so that you do not break any of your scanner’s parts. Please follow it
carefully.
Calibrating the Stepper Motor Driver (the Easy Way)
At right is a picture of the Stepper Motor Driver. This component
of the scanner should be handled with care. It can be shorted out
and ruined with improper handling. Please carefully follow the
instructions in this document to ensure that it works properly.
The screw shown in the picture at right controls how much
electrical current is given to the Ciclop’s stepper motor. This motor
spins the scanning table, which allows the scanner to get a 360°
view of an object. You want to ensure that this screw is adjusted
to the right position. Too much electrical current, and the
motor may eventually fail or the Stepper Motor Driver may
overheat. Too little electrical current, and the motor will not
turn properly and results in inaccurate scans.
Orient the Stepper Motor Driver such that the screw is on the
bottom and the black square is above it. See the section below
titled “Plugging in the Boards and Components” for a picture of
this orientation. The screw has a flat side. The flat side of the
screw is normally pointing straight down. Using a Phillip’s head
screwdriver, turn the screw 45° counterclockwise. This
corresponds to the hour hand’s position on a clock at 4:30. See
the diagram at right.
If your Stepper Motor Driver is having issues, we highly
recommend consulting the more detailed calibration guide presented at the end of this document.
SCREW
HEAT SINK

CowTech Ciclop 3D Scanning Guide
4
Stacking the Boards
WARNING: It is easy to short out and ruin the Stepper Motor Driver on your scanner. Please ensure that
none of the boards are plugged in while you connect them to one another. If any of the boards are
powered while doing so, you run the risk of ruining the Stepper Motor Driver.
The three circuit boards included with the Ciclop are shown below.
Uno Clone
CT Board
Stepper Motor Driver
The boards all stack on top of one another. The Uno Clone sits at the bottom of the stack, the CT board is
in the middle, and the Stepper Motor Driver is on top. It is essential to properly orient the boards.
The CowTech logo on the CT Board should be oriented opposite from the USB and power plugs
on the Uno Clone.
The small screw on the Stepper Motor Driver should be oriented closer to the power plug on the
CT Board. On the CT Board, there is also a silkscreen just under the pins for the Stepper Motor
Driver that indicates the proper orientation.
A picture of all three boards correctly assembled can be found on the next page.

CowTech Ciclop 3D Scanning Guide
5
Plugging in the Boards and Components
Make sure to plug in the boards and components as shown in the picture below. It is possible to damage
the Stepper Motor Driver if the boards are plugged in incorrectly. The blue connections on the right side
of the board will require a flathead screwdriver to secure in place.
USB Plug to
Computer
DO NOT USE THIS
PLUG
Barrel Plug to
Wall Outlet
LED Strip.
Darker Wire on Top
Lighter Wire on Bottom
Darker Wire
Lighter Wire
Lasers.
Black Wires in the Middle
Red Wires connect as
labeled on the silkscreen.
Stepper Motor.
Make sure the blue wire is
to the left.
The wire on the right may
or may not be black. It’s
fine if the wire is not black
as labeled.
Heat Sink.
The heat sink has an adhesive backing. Peel
off its cover and stick it to the black square
on the middle of the Stepper Motor Driver.

CowTech Ciclop 3D Scanning Guide
6
Installing the Software
Horus
Horus is a software program on your computer that connects to the Ciclop scanner. This guide was
written for use with Horus version 0.2rc1. You can download Windows, Mac, or Ubuntu versions of Horus
for free at the link below. Run the installer and follow the onscreen instructions. The installer may give
you the option to install “FTDI Drivers” or “Arduino Drivers.” Neither are necessary to run the CowTech
Ciclop 3D Scanner.
https://github.com/bqlabs/horus
After installation, it is recommended that you restart your computer before continuing.
Uno Clone Drivers
Horus interfaces with the components of the scanner via
the Uno Clone. In order to enable your computer to
recognize the Uno Clone when it’s plugged in, you may
have to download and install Uno Clone drivers. These
drivers can be found on the CowTech website. Please see
the link below. Unzip the file, run “SETUP.EXE,” and then
click “INSTALL.”
http://www.cowtechengineering.com/downloads
Logitech C270 Webcam Drivers
The Ciclop uses a Logitech C270 Webcam to make scans.
Although your computer may recognize the webcam if
plugged in straight out of the box, Horus will not be able
to. Horus requires a special set of webcam drivers, all of
which can be obtained from the Logitech website below.
Make sure that you download drivers that match your
operating system. The installer will give you the option to
install:
“Logitech Webcam Drivers”
“Logitech Webcam Software”
“Logitech Motion Detection”
The last two options are not necessary to run the CowTech Ciclop 3D Scanner.
http://support.logitech.com/en_us/product/hd-webcam-c270
If you ever have trouble getting Horus to recognize the webcam, uninstall and then reinstall Horus. In some
cases, Horus needs to be able to see the Logitech C270 drivers during installation in order to recognize

CowTech Ciclop 3D Scanning Guide
7
them properly. If your problem persists, see our troubleshooting guide at the end of this document for
more help.
How the 3D Scanner Works
The CowTech Ciclop can generate scans with or without a texture. A scan with texture will be colored like
the object is, while a scan without texture will be the object’s geometry only. The Ciclop utilizes a camera,
two lasers, and a spinning table to make scans.
When an object is placed on the spinning table, the lasers flash on and “paint” the object with vertical red
lines. The camera takes an image and records the areas that show up as red on the object. If the scan is
recording textures, the camera also records the colors visible at these areas. This happens just after the
lasers flash off. The table then rotates at a very small angle (usually a fraction of a degree) and the
process repeats until the table makes a full revolution.
The output of the scan is known as a “point cloud” and is saved as a .ply file. A point cloud is simply a
collection of coordinates that represent points in 3D space. Calibrating the scanner ensures that Horus
knows how much the table spins and the locations of the camera / lasers with respect to the object. It
uses this information to coherently assemble these points in 3D space so that they resemble the scanned
object. Smaller angles of rotation will take longer but result in higher resolution scans.
The quality of your scans will vary widely based on three important factors:
Object –colors, finish, and features of the scanned object
Lighting –ambient lighting in the room
Calibration –brightness, contrast, saturation, and exposure of the camera
The remainder of this guide will walk you through our process for generating scans step by step.

CowTech Ciclop 3D Scanning Guide
8
Selecting an Object
Select an object suitable for scanning. The Ciclop uses red lasers to highlight sections of an object for the
camera to record in 3D space. When selecting an object to 3D scan, it’s important that the object makes
it easy for the camera to see the red lasers. It’s ultimately up to you to experiment with what works and
what doesn’t, but the following are good guidelines to follow for your first scan.
Shiny or reflective objects are difficult to scan. They reflect the lasers off their surface, making the object
more difficult for the camera to detect. Additionally, a reflective surface will reflect different areas of its
surroundings while it rotates around, meaning that the camera will not be able to capture its textures
well.
Red, black, or darkly colored objects are difficult to scan. Red surfaces are difficult to tell apart from the
red light from the lasers. Black surfaces tend to absorb of the laser’s light, making it difficult for the
camera to detect the object. Other colors like dark brown and dark purple
are likewise hard to detect. If the object you would like to scan is red,
black, or darkly colored in certain areas, it is likely that it will show up as
blank spaces in the scan and require significant post-processing work to
fix.
Concave or interior features are difficult to scan. Concave features are
areas of an object that form pockets or overhangs. The lasers generally
can’t reach the inside of the pockets, and they’ll show up as large holes in
the model. Models with rounded, convex features generally result in
better scans.
Significant detail on the top of bottom of an object may require multiple scans and post-processing work to
properly capture. The lasers generally don’t see the top or base of an object. If you’d like to capture these
areas of an object, please see our supplementary post-processing tips at the end of this document.
CONCAVE
CONVEX

CowTech Ciclop 3D Scanning Guide
9
Calibration
Calibration is the difference between a good scan and a bad scan. Follow all of the steps below to ensure
that you get a good one. If you come across any further tips and tricks, please do share them with us on
our FaceBook page! https://www.facebook.com/groups/564912093672675/
When you first start up Horus, you’ll be greeted by the window shown below. Close the window. The
window prompts you to launch the “wizard,” and in our experience the wizard generally does not make
for very good calibrations. You can get much more accurate scans by calibrating manually.
Horus’ functionality is divided into four separate windows called “Workbenches.”Each workbench is suited
to a different step in the calibration process. You can cycle through the workbenches by clicking on the
drop-down bar on the top right corner of the window. The default workbench is the Scanning
Workbench, which is what you see below.
SWITCHES BETWEEN
WORKBENCHES

CowTech Ciclop 3D Scanning Guide
10
Connecting the Camera
Plug in the camera and press the Connect Icon on the top left
corner of the screen. If all goes well, you will see live footage from
the camera in the middle segment of the Scanning Workbench. If
you’re having issues with this step, there are a number of possible
solutions. Please see the end of this document for troubleshooting
help.
Using the Control Workbench
The Control Workbench helps you test the different components of the scanner. You can use it to
troubleshoot any issues you may have with the motors, lasers, or camera. The button on the left side of
the workbench can control all of these components.
We’ll use the Control Workbench to make sure that our lasers and object are in a good position to scan.
Vertically Align the Lasers
1
Place the calibration pattern on the table.
The calibration pattern comes with your
scanner, and it’s fairly important. Don’t
lose it! Be sure that it is as perfectly
perpendicular with the table as possible.
If the calibration pattern is skewed, you
may get some skewed scans after
calibration.
2
Turn on the left and right lasers. Use the
buttons on the left side of the Scanning
Workbench. In the picture at right, you
can see that the left laser is much broader
(and therefore dimmer) than the right
laser. This needs to be fixed.
CONNECT ICON

CowTech Ciclop 3D Scanning Guide
11
3
Focus the lasers. The lasers have a small
plastic lens on the end that focuses the
beam into a line. Rotate it to make the
line as thin and bright as possible. A thin
laser makes it easier to capture fine
detail.
4
Rotate the lasers so that they’re vertical.
You can use the borders between the
checkers to help align the lasers. They
should be perfectly parallel.
Ensure Good Laser Coverage
1
Remove the calibration pattern and place
your object on the table. The calibration
process will require a lot of switching back
and forth between the two, so keep the
calibration pattern handy.
FOCUSING LENS

CowTech Ciclop 3D Scanning Guide
12
2
Rotate the table with your hands. You may
notice that the lasers don’t hit as much of
the object at certain angles.
3
Adjust the position of the lasers or object
to ensure good coverage. Good coverage
means that the lasers are visible along the
entire length of the object. Ensure that
this is true for all angles of the table. It
may take some guess and check work to
get it right. Some examples of good and
bad coverage are given at right.
GOOD
BAD
4
Mark object’s position on the table. You will want to be able to replicate the objects current
position later. A piece of tape works well to mark the boundaries of the base of the object. If you
adjusted the position of the laser holders, it may also be worth it to make sure the lasers are still
vertical and focused, as it’s easy to accidentally skew them during this step.
Using the Adjustment Workbench
The adjustment workbench is where you adjust the camera’s settings. The camera’s settings are crucial.
When using the lasers, the camera relies on distinguishing red from other colors to differentiate the
object’s space from empty space. When calibrating, the camera relies on distinguishing white from black

CowTech Ciclop 3D Scanning Guide
13
to detect the calibration pattern. The Adjustment Workbench lets you adjust the camera’s settings
separately for each task to maximize its ability to tell colors apart.
Success is dependent on the lighting of the room. Although we have some general tips about lighting, you
may need to experiment with different kinds of light to get good results.
Calibration Capture
Calibration Capture covers all the settings that govern how the camera looks at the checker pattern during
calibration. Horus tells you if the camera can detect the pattern by displaying a series of rainbow lines
running between the squares on the camera’s feed at the right side of the workbench.
The trick is to get Horus to display these rainbow lines for as wide a range of rotation as possible. Rotating
the table away from the position where it directly faces the camera makes the pattern slanted from the
camera’s perspective. The more slanted the pattern can be while still displaying the rainbow lines, the
better the calibration will be.
1
Place the calibration pattern on the table.
2
Adjust the light until you see the rainbow
lines. The picture at right gives you an
example of what the rainbow lines look
like. Horus can get quite picky about
recognizing the pattern, so be prepared to
adjust the settings of the camera and
experiment with a few different light
sources.
RAINBOW LINES

CowTech Ciclop 3D Scanning Guide
14
-
The more indirect the light is, the better.
Direct light can cause glare on the slightly
reflective surface of the sticker, which
makes the black squares in some areas
indistinguishable from the white ones. The
picture at right is an example of this. If
even one square is obscured by too much
glare, Horus will not recognize the pattern.
To get more indirect light, try shining a
lamp at a white surface near the scanner.
The white surface will bounce a fair
amount of indirect light onto the pattern
without glare.
3
Rotate table to the left or right with your
hand. Try to see how far you can rotate
the table before the rainbow lines go
away. They usually go away when one side
of the pattern is exposed to less light and
becomes darker. When the pattern’s
lighting becomes inconsistent like this,
Horus will fail to recognize the pattern.
The picture at right shows the angle at
which Horus just begins to stop
recognizing the pattern
4
Add light sources to either side of the table.
This increases the scanner’s range of
pattern detection. At right you can see
how this allows Horus to detect the
pattern at a steeper angle of rotation.
Again, this may take some time to get
right.
TOO BRIGHT (GLARE)
TOO DARK

CowTech Ciclop 3D Scanning Guide
15
4
Fiddle with settings to get Horus to detect
the pattern at as steep angle as possible.
The picture at right is the result of
modifying only the brightness, and gives a
decent angle of detection. Generally, you
want to be able to detect the pattern
when displaced at least 45° from its initial
position directly facing the camera. If you
can do more, do it!
-
Be patient and experiment. After adding
more light and adjusting all the settings,
we arrive at an angle that’s roughly 65°
from the initial table position. It may take a
little patience and guess and check work to
get it right.
6
Maximize the range for the other side as
well. The picture at right is the result of
adding some indirect light to the right side
of the table.
7
Check the pattern when facing the camera directly once again. Slowly rotate the table with your
hand all across the range where the pattern is detected. Sometimes adding more light on the sides
will make the pattern too bright in the center, giving detection on the sides but not in the middle.
Make sure that the rainbow lines are detected along the entire range of rotation from left to right.

CowTech Ciclop 3D Scanning Guide
16
Calibration Segmentation
Calibration segmentation covers all the settings that govern how Horus tells red laser light from other
colors. Horus will show you which areas register as laser light with white highlights, while leaving
everything else black. This is important during calibration, when Horus uses light from the lasers shining
on the calibration pattern to orient the lasers and table in relation to the camera.
The goal is to get Horus to detect only the laser light that shines on the white squares. Ideally, the areas
where the laser lines hit the black squares should not be detected. We also want to lines to be stable (not
constantly shifting) and to be relatively crisp.
1
Turn off the lights. For this step, less
ambient light will allow the red laser light
to shine brighter and make it easier to
detect. The lights will stay off when it’s
actually time to scan. We can do this
because we are not capturing a texture.
If we were capturing a texture, we would
want to keep the lights on during
scanning. Lights on means that you get an
accurate depiction of the object’s colors.
Just be warned that texture scans may
make calibration more difficult and
possibly compromise the level of detail of
the scan.
2
Make sure Horus does not detect the
background. In the picture on the
previous step, the top four lines are from
the wall rather than from the calibration
pattern. To remove them, hang a darkly
colored sheet behind the table or move
the table further away from the wall.
AREA ABOVE
PATTERN IS NOT
DETECTED

CowTech Ciclop 3D Scanning Guide
17
3
Fiddle with the settings until only white
squares are detected. It can be difficult to
make it so that all of them show up with
equal thickness. It’s fine if only two or
three of the white squares show up on
each laser. Experiment with the settings
to see what works best. A brief
description of each one is below.
Threshold –Changes the minimum intensity of light that counts as laser light. Any pixel that
falls below this value is discarded. This is like the “brightness” setting on the camera.
Blur –Draws a box around each pixel. That pixel’s intensity will count only as the average of all
pixels within the box. The value of Blur changes the size of the box drawn. This is similar to the
“saturation” or “contrast” setting on the camera.
Window –Discards pixels that fall outside a certain distance from the highest intensity pixels in
the image. This is similar to the “exposure” setting on the camera.

CowTech Ciclop 3D Scanning Guide
18
Scan Segmentation
1
Put your object on the table. This step is
just like Calibration Segmentation, except
you use the object rather than the
calibration pattern.
2
Fiddle with the settings. Depending on
the color of your object, they might be
slightly different from those from
Calibration Segmentation. Examples of
some bad settings are at right. Use the
picture above these three as an example
of good segmentation.
TOO CHOPPY
TOO THIN
TOO BLURRY
3
Rotate table to ensure good coverage. Double check that the lasers hit all the areas of your object
that you want to scan.

CowTech Ciclop 3D Scanning Guide
19
Saving the Adjustment Profile
The settings you got from the previous steps can be saved and loaded for later. This is
extremely useful as long as you have consistent lighting, as it saves you the trouble of
fiddling with settings each time you’d like to scan. The files are saved with the .json file
extension.
Using the Calibration Workbench
The calibration workbench is how the scanner figures out where its components are in
3D space. This is crucial for making the model geometrically accurate. Once the camera
settings have been worked out in the Adjustment Workbench, the scanner accounts for
distortions caused by the camera’s lens and triangulates the positions of the lasers, and
table.
Pattern Settings
1
Make sure that rows and columns are set at
6 and 11, respectively. If you count them
on the calibration pattern, you might
notice that there are in actually 7 rows and
12 columns. Regardless, if you set these
values to 7 and 12, your scanner will not be
able to recognize the patterns. This may be
patched at some point.
Also set the square width to 12.7 mm.
You’re free to measure them yourself, but
this value works well.
This manual suits for next models
1
Table of contents
Popular Scanner manuals by other brands
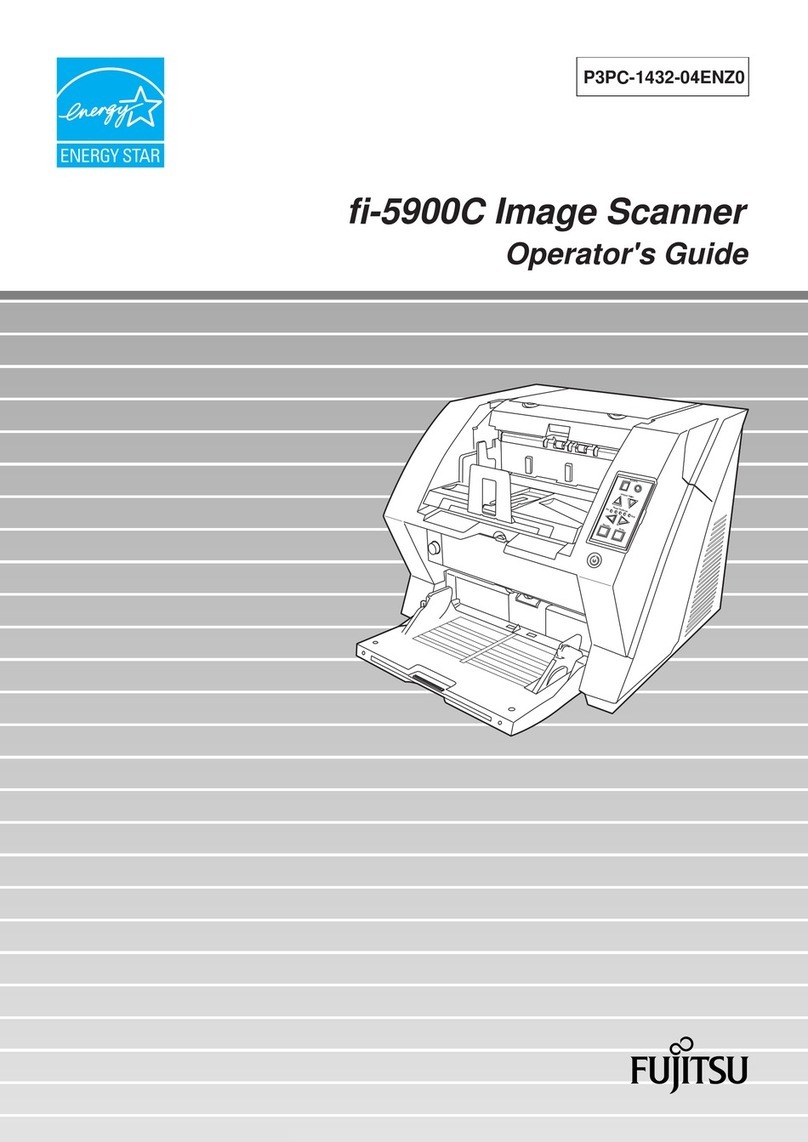
Fujitsu
Fujitsu FI-5900C Operator's guide
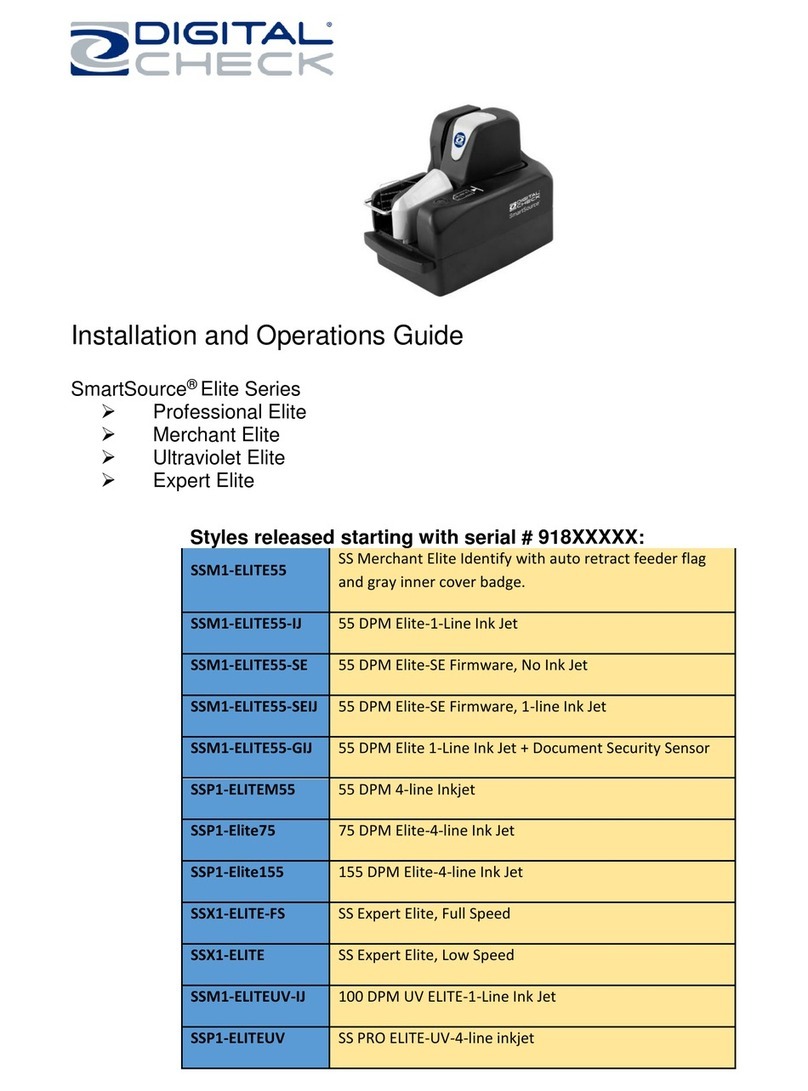
Digital Check
Digital Check SmartSource SSM1-ELITE55-IJ Installation and operation guide
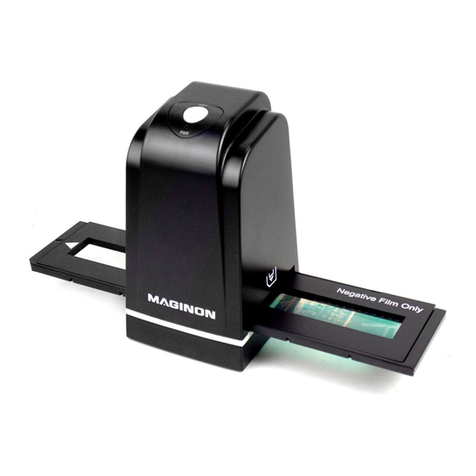
MAGINON
MAGINON FS 500 instruction manual

Kodak
Kodak PS810 Brochure & specs
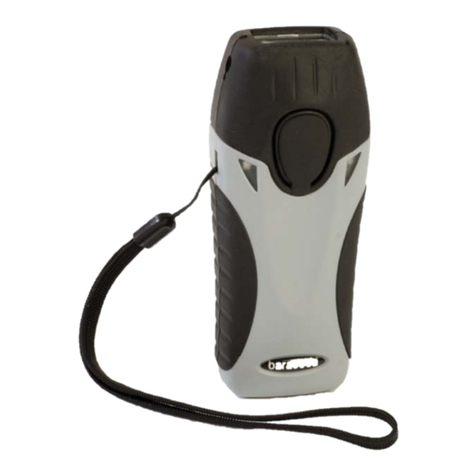
Baracoda
Baracoda RoadRunner BRR-FS Brochure & specs
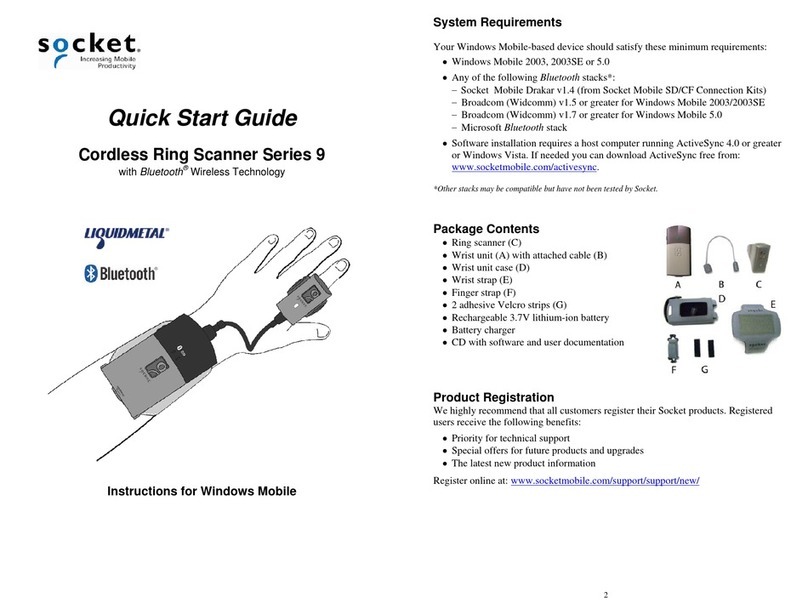
Socket
Socket Cordless Ring Scanner Series 9 quick start guide