Crossbow Technology AHRS500GA Series User manual

AHRS500GA Series Operator’s Manual
Document 7430-0060-02
Revision A, December 2002
Crossbow Technology, Inc., 41 Daggett Dr., San Jose, CA 95134
Tel: 408-965-3300, Fax: 408-324-4840
SUNSTAR传感与控制 http://www.sensor-ic.com/ TEL:0755-83376549 FAX:0755-83376182 E-MAIL:[email protected]m
SUNSTAR自动化 http://www.sensor-ic.com/ TEL: 0755-83376489 FAX:0755-83376182 E-MAIL:[email protected]

Revision History
Revision
Date Author Comments
-01_A 9/16/02 JR Initial Release
-02_A 12/02 DJ Added limitation section, changed
startup time to 90 seconds
©2001-2002 Crossbow Technology, Inc. All rights reserved. Information
in this document is subject to change without notice.
Crossbow and SoftSensor are registered trademarks and AHRS500GA is a
trademark of Crossbow Technology, Inc. Other product and trade names
are trademarks or registered trademarks of their respective holders.
SUNSTAR传感与控制 http://www.sensor-ic.com/ TEL:0755-83376549 FAX:0755-83376182 E-MAIL:[email protected]m
SUNSTAR自动化 http://www.sensor-ic.com/ TEL: 0755-83376489 FAX:0755-83376182 E-MAIL:[email protected]

AHRS500GA Series Operator’s Manual
Doc# 7430-0060-02 Rev. A Page i
Table of Contents
1Introduction......................................................................................................1
1.1 The AHRS500GA Series Motion and Attitude Sensing Units.......1
2Package Contents............................................................................................2
3AHRS500GA Description.............................................................................3
3.1 AHRS500GA Coordinate System.......................................................3
3.2 Connections.............................................................................................4
3.2.1 I/O Cable.........................................................................................5
3.2.2 Power Input and Power Input Ground.......................................5
3.2.3 Case Ground...................................................................................5
3.2.4 SerialData Interface.....................................................................5
3.2.5 BIT Status Output Pin ..................................................................6
3.2.6 Magnetometer calibration Input Pin ..........................................6
3.2.7 No Connection...............................................................................6
3.2.8 Quick Digital interface connection............................................6
3.3 Measurements.........................................................................................7
3.3.1 Attitude and Heading....................................................................7
3.3.2 Sensor Measurements...................................................................8
3.3.3 BIT Processing..............................................................................8
3.4 Commands.............................................................................................10
3.5 Data Packet Format..............................................................................10
3.6 Timing....................................................................................................11
3.7 Magnetic Heading................................................................................11
4AHRS500GA Operation..............................................................................12
4.1 Normal Operation.................................................................................12
4.2 Calibration Operation..........................................................................12
4.3 Viewing AHRS500GA Data with GyroView.................................12
4.3.1 GyroView Computer Requirements.........................................12
4.3.2 Install GyroView.........................................................................12
4.3.3 Connections..................................................................................12
4.3.4 Setup GyroView..........................................................................13
4.3.5 Take Measurements....................................................................13
5Limitations.....................................................................................................15
5.1 Installation.............................................................................................15
SUNSTAR传感与控制 http://www.sensor-ic.com/ TEL:0755-83376549 FAX:0755-83376182 E-MAIL:[email protected]m
SUNSTAR自动化 http://www.sensor-ic.com/ TEL: 0755-83376489 FAX:0755-83376182 E-MAIL:[email protected]

AHRS500GA Series Operator’s Manual
Page ii Doc# 7430-0060-02 Rev. A
5.2 Calibration.............................................................................................15
5.3 Operation...............................................................................................15
5.4 Range Limitations................................................................................15
6AHRS500GA Installation............................................................................16
7Appendix A. Mechanical Specifications...................................................17
8Appendix B. AHRS500GA Output Quick Reference............................18
9Appendix C. Hard and Soft Iron Calibration...........................................19
9.1 Hard/Soft Iron Calibration Requirements........................................19
9.2 Hard/Soft Iron Calibration Introduction...........................................19
9.3 AHRS500GA Hard and Soft Iron Calibration Procedure .............19
9.3.1 Equipment Needed......................................................................20
9.3.2 Installation and Calibration Cable Connections.....................20
9.4 Calibration Process..............................................................................21
9.4.1 Starting the Calibration..............................................................21
9.4.2 Switch to Mag Cal Mode...........................................................23
9.4.3 Collecting Calibration Data.......................................................23
9.4.4 Evaluating Calibration Data......................................................25
9.4.5 Completing the Calibration.......................................................27
9.4.6 Testing the Calibration...............................................................27
10 Appendix D. Warranty and Support Information...............................28
10.1 Customer Service .................................................................................28
10.2 Contact Directory.................................................................................28
10.3 Return Procedure..................................................................................28
10.3.1 Authorization...............................................................................28
10.3.2 Identification and Protection.....................................................29
10.3.3 Sealing the Container.................................................................29
10.3.4 Marking.........................................................................................29
10.3.5 Return Shipping Address...........................................................29
10.4 Warranty................................................................................................29
SUNSTAR传感与控制 http://www.sensor-ic.com/ TEL:0755-83376549 FAX:0755-83376182 E-MAIL:[email protected]m
SUNSTAR自动化 http://www.sensor-ic.com/ TEL: 0755-83376489 FAX:0755-83376182 E-MAIL:[email protected]

AHRS500GA Series Operator’s Manual
Doc# 7430-0060-02 Rev. A Page iii
About this Manual
The following annotations have been used to provide additional
information.
XNOTE
Note provides additional information about the topic.
þEXAMPLE
Examples are given throughout the manual to help the reader understand the
terminology.
PIMPORTANT
This symbol defines items that have significant meaning to the user
MWARNING
The user should pay particular attention to this symbol. It means there is a
chance that physical harm could happen to either the person or the
equipment.
The following paragraph heading formatting is used in this manual:
1 Heading 1
1.1 Heading 2
1.1.1 Heading 3
Normal
SUNSTAR传感与控制 http://www.sensor-ic.com/ TEL:0755-83376549 FAX:0755-83376182 E-MAIL:[email protected]m
SUNSTAR自动化 http://www.sensor-ic.com/ TEL: 0755-83376489 FAX:0755-83376182 E-MAIL:[email protected]

AHRS500GA Series Operator’s Manual
Page iv Doc# 7430-0060-02 Rev. A
SUNSTAR传感与控制 http://www.sensor-ic.com/ TEL:0755-83376549 FAX:0755-83376182 E-MAIL:[email protected]m
SUNSTAR自动化 http://www.sensor-ic.com/ TEL: 0755-83376489 FAX:0755-83376182 E-MAIL:[email protected]

AHRS500GA Series Operator’s Manual
Doc# 7430-0060-02 Rev. A Page 1
1Introduction
1.1 The AHRS500GA Series Motion and Attitude Sensing
Units
This manual explains the use of the AHRS500GA Series of products, nine-
axis measurement system designed to measure stabilized pitch, roll and yaw
angles in a dynamic environment.
The AHRS500GA is a nine-axis measurement system that combines linear
accelerometers, rotational rate sensors, and magnetometers. The
AHRS500GA uses the 3-axis accelerometer and 3-axis rate sensor to make
a complete measurement of the dynamics of your system. The addition of a
3-axis magnetometer also allows the AHRS500GA to make a true
measurement of magnetic heading.
The AHRS500GA is the solid-state equivalent of a vertical gyro/artificial
horizon display combined with a directional gyro.
The AHRS500GA series units are low power, fast turn on, reliable and
accurate solutions for a wide variety of stabilization and measurement
applications.
All AHRS500GA products have an RS-232 serial link. Data is streamed
continuously.
Crossbow Technology AHRS500GA units employ onboard digital
processing to compensate for deterministic error sources within the unit and
to compute attitude information. The AHRS500GA units accomplish these
tasks with an analog to digital converter and high performance Digital
Signal Processors.
The AHRS500GA uses angular rate sensors and linear acceleration sensors
that are micro-machined devices. The three angular rate sensors consist of
vibrating ceramic plates that utilize the Coriolis force to output angular rate
independently of acceleration. The three MEMS accelerometers are surface
micro-machined silicon devices that use differential capacitance to sense
acceleration. Solid-state MEMS sensors make the AHRS500GA both
responsive and reliable. The magnetic sensors are state-of-the-art miniature
fluxgate sensors. Fluxgate sensors make the AHRS500GA sensitive and
responsive, with better temperature performance than other technologies
such as magneto-resistive sensors.
The AHRS500GA Series of products utilize a sophisticated Kalman filter
algorithm to allow the unit to track orientation accurately through dynamic
maneuvers. The Kalman filter will automatically adjust for changing
dynamic conditions without any external user input. No user intervention
or configuration is required at power-up.
SUNSTAR传感与控制 http://www.sensor-ic.com/ TEL:0755-83376549 FAX:0755-83376182 E-MAIL:[email protected]m
SUNSTAR自动化 http://www.sensor-ic.com/ TEL: 0755-83376489 FAX:0755-83376182 E-MAIL:[email protected]

AHRS500GA Series Operator’s Manual
Page 2Doc# 7430-0060-02 Rev. A
2Package Contents
In addition to your AHRS500GA sensor product you should have:
•1 CD with GyroView Software
GyroView will allow you to immediately view the outputs of the
AHRS500GA on a PC running Microsoft® Windows™. You can
also download this software from Crossbow’s web site at
http://www.xbow.com.
•1 Digital Signal Calibration/Maintenance Cable.
This links the AHRS500GA directly to a serial port. Only the
transmit, receive, power, and ground channels are used. The
magnetometer calibration switch will be visible on the connector.
•1 AHRS500GA Installation Manual
This contains the installation and calibration information for the
AHRS500GA model type ordered.
SUNSTAR传感与控制 http://www.sensor-ic.com/ TEL:0755-83376549 FAX:0755-83376182 E-MAIL:[email protected]m
SUNSTAR自动化 http://www.sensor-ic.com/ TEL: 0755-83376489 FAX:0755-83376182 E-MAIL:[email protected]

AHRS500GA Series Operator’s Manual
Doc# 7430-0060-02 Rev. A Page 3
3AHRS500GA Description
3.1 AHRS500GA Coordinate System
The AHRS500GA will have a label on one face illustrating the
AHRS500GA coordinate system. With the connector facing you, and the
mounting plate down, the axes are defined as:
X-axis –from face with connector through the AHRS500GA
Y-axis –along the face with connector from left to right
Z-axis –along the face with the connector from top to bottom
This is the default configuration for the generic AHRS500GA model. Other
coordinate frame orientations are supported given the model type
purchased, and these will be reflected in the label as well as through the
model configuration number. The axes form an orthogonal right-handed
coordinate system. An acceleration is positive when it is oriented towards
the negative side of the coordinate axis. For example, with the
AHRS500GA sitting on a level table, it will measure zero g along the x-and
y-axes and +1 g along the z-axis. Gravitational acceleration is directed
downward, and thus will be defined as positive for the AHRS500GA z-axis.
The angular rate sensors are aligned with these same axes. The rate sensors
measure angular rotation rate around a given axis. The rate measurements
are labeled by the appropriate axis. The direction of a positive rotation is
defined by the right-hand rule. With the thumb of your right hand pointing
along the axis in a positive direction, your fingers curl around in the
positive rotation direction. For example, if the AHRS500GA is sitting on a
level surface and you rotate it clockwise on that surface, this will be a
positive rotation around the z-axis. The x-and y-axis rate sensors would
measure zero angular rates, and the z-axis sensor would measure a positive
angular rate.
The magnetic sensors are aligned with the same axes definitions and sign as
the linear accelerometers.
Pitch is defined positive for a positive rotation around the y-axis (pitch up).
Roll is defined as positive for a positive rotation around the x-axis (roll
right). Yaw is defined as positive for a positive rotation around the z-axis
(turn right).
The angles are defined as standard Euler angles using a 3-2-1 system. To
rotate from the body frame to an earth-level frame, roll first, then pitch, and
then yaw.
SUNSTAR传感与控制 http://www.sensor-ic.com/ TEL:0755-83376549 FAX:0755-83376182 E-MAIL:[email protected]m
SUNSTAR自动化 http://www.sensor-ic.com/ TEL: 0755-83376489 FAX:0755-83376182 E-MAIL:[email protected]

AHRS500GA Series Operator’s Manual
Page 4Doc# 7430-0060-02 Rev. A
3.2 Connections
The AHRS500GA500 has a male DB-15 connector. The signals are as
shown in Table 1.
Table 1Connector Pin Assignments
Pin Signal Electrical Specifications
1RS-232 Transmit +/-4.5 VDC min wrt power ground.
2RS-232 Receive +/-25 VDC max wrt power ground.
3VDC Power Input 10-40 VDC normal, 9VDC emergency
4Power Input Ground
5No connection Do not connect
6No connection Do not connect
7RS-422 Transmit + A
8RS-422 Transmit –A 2.0 VDC differential output (min) into
100 ohms. Common mode output voltage,
3VDC max.
9Signal Ground Capacitive coupling to internal system
ground. Should be connected to user’s
system ground to reduce RS232 and
RS422 signal noise.
10 Factory mode pin Factory reserved; do not connect
11 Factory mode pin Factory reserved; do not connect
12 Magnetometer
calibration input (hard
and soft iron cal)
Active: Short to power ground.
Inactive: Open circuit. (Internally pulled
to +3.3VDC through 10Kohm resistor)
13 Hardware BIT Status Open collector, requires user pull-up
resistor. Max pull-up voltage: +15VDC
Max current sink: 10ma.
14 RS-422 Receive + A
15 RS-422 Receive –A Common mode input voltage range:
3VDC wrt power ground.
N/A Case Ground Electrically connected to I/O connector
shell
SUNSTAR传感与控制 http://www.sensor-ic.com/ TEL:0755-83376549 FAX:0755-83376182 E-MAIL:[email protected]m
SUNSTAR自动化 http://www.sensor-ic.com/ TEL: 0755-83376489 FAX:0755-83376182 E-MAIL:[email protected]

AHRS500GA Series Operator’s Manual
Doc# 7430-0060-02 Rev. A Page 5
3.2.1 I/O Cable
The user must provide a shielded cable with the shield connectedto the I/O
connector shell in order to provide the required EMI protection. The cable
sent with the unit is intended to provide the user with the ability to perform
a magnetometer calibration, and provide routine magnetometer calibration
maintenance of the system, and will not provide adequate shielding.
3.2.2 Power Input and Power Input Ground
The AHRS500GA power requirements are described in the table below. It
is designed to operate with either a nominal 14VDC or 28VDC aircraft
power system.
Table 2Electrical Power Input Requirements
Item Requirement AHRS500GA specification
1.
Input Supply
voltage 10-40 VDC
2.
Input Supply
Current 1 Amp (max)
3.2.3 Case Ground
The case is electrically connected to the I/O connector shell. The shell
should be electrically connected to the user’s cable shield. The case is
isolated from the Power Input Ground, and should be bolted to a good
conducting surface that is grounded.
3.2.4 Serial Data Interface
The interface specification is a factory configurable RS-422 or RS-232, also
with factory configurable baud rates (see table below) depending on the
model configuration chosen. Data output is continuous at a fixed frequency
dependant on the baud rate (see table below).
Table 3Supported BAUD Rates and Output Rates
BAUD Rate Output Rate
9600 25
19200 50
38400 100
57600 200
The unit has both an RS-232 and RS422 serial interface. During factory
configuration, one port is configured as the user data port while the other is
SUNSTAR传感与控制 http://www.sensor-ic.com/ TEL:0755-83376549 FAX:0755-83376182 E-MAIL:[email protected]m
SUNSTAR自动化 http://www.sensor-ic.com/ TEL: 0755-83376489 FAX:0755-83376182 E-MAIL:[email protected]

AHRS500GA Series Operator’s Manual
Page 6Doc# 7430-0060-02 Rev. A
a factory diagnostic port to monitor BIT data. The unit can be configured to
allow either port to be the user data port, defaulting the other for BIT
diagnostics. The port definition is specified by the model configuration
chosen and will be detailed in the model configuration sheet shipped with
the unit.
3.2.5 BIT Status Output Pin
The BIT status output pin will become active high if the system is
experiencing a failure. The BIT is an open collector signal and requires a
pull-up resistor for proper operation.
3.2.6 Magnetometer calibration Input Pin
The AHRS500GA has an input pin to control the magnetometer hard-iron
calibration function. When this pin is active (low) the unit will collect the
data necessary for magnetometer calibration. When it becomes inactive, the
calibration data shall be used to compute the hard and soft iron
compensation values. During normal operation, no connection should be
made to this pin; this pin shall be tied high internally with a pull-up resistor.
This feature has been added as a means to performa Hardiron/Softiron
calibration without sending the calibration commands to the unit. Please
see Appendix C, for a complete explanation of the Hardiron/Softiron
calibration process, and how this pin can be used as a means of
implementing the calibration.
3.2.7 No Connection
During normal operation of the AHRS500GA, no connection is made to the
factory test pin. This pin has an internal pull-up mechanism and must have
no connection for the AHRS500GA to operate properly.
3.2.8 Quick Digital interface connection
On a standard DB-9 COM port connector, make the connections as
described in Table 2.
Table 4DB-9 COM Port Connections
COM Port Connector AHRS500GA Connector
Pin # Signal Pin # Signal
2RxD 1TxD
3TxD 2RxD
5GND* 4GND*
*Note: Pin 4 on the AHRS500GA is data ground as well as power ground.
SUNSTAR传感与控制 http://www.sensor-ic.com/ TEL:0755-83376549 FAX:0755-83376182 E-MAIL:[email protected]m
SUNSTAR自动化 http://www.sensor-ic.com/ TEL: 0755-83376489 FAX:0755-83376182 E-MAIL:[email protected]

AHRS500GA Series Operator’s Manual
Doc# 7430-0060-02 Rev. A Page 7
Power is applied to the AHRS500GA on pins 3 and 4. Pin 4 is ground; Pin
3 should have 10-40 VDC unregulated at 275 mA.
The default serial interface is standard RS-232, model configured baud rate,
8 data bits, 1 start bit, 1 stop bit, no parity, and no flow control, and will
output at a model configured output rate.
Crossbow will supply AHRS500GA communication software examples
written in LabView. Source code for the AHRS500GA serial interface can
be obtained via the web at http://www.xbow.com. The source code has a .vi
file format and requires a National Instruments LabView 5.0 or newer
license to use.
3.3 Measurements
The AHRS500GA Series is designed to operate as a complete attitude and
heading reference system. See the “Data Packet Format” section for the
actual structure of the data packet.
3.3.1 Attitude and Heading
In angle mode, the AHRS500GA acts as a complete attitude and heading
reference system and outputs the stabilized pitch, roll, and yaw angles along
with the angular rate, acceleration, and magnetic field information. The
angular rate, acceleration, and magnetic field values are calculated as
described in the sensor section.
The Kalman filter operates in angle mode to track the rate sensor bias and
calculate the stabilized roll, pitch, and yaw angles.
The AHRS500GA uses the angular rate sensors to integrate over your
rotational motion and find the actual pitch, roll, and yaw angles. The
AHRS500GA uses the accelerometers to correct for rate sensor drift in the
vertical angles (pitch and roll); the AHRS500GA uses the magnetometers to
correct for rate sensor drift in the yaw angle. This is the modern equivalent
of an analog vertical gyro that used a plumb bob in a feedback loop to keep
the gyro axis stabilized to vertical. The AHRS500GA takes advantage of
the rate gyros’ sensitivity to quick motions to maintain an accurate
orientation when accelerations would otherwise throw off the
accelerometers measurement of the AHRS500GA orientation relative to
gravity; the AHRS500GA then uses the accelerometers to provide long term
stability to keep the rate gyro drift in check.
The AHRS500GA uses a sophisticated Kalman filter algorithm to track the
bias in the rate sensors. This allows the AHRS500GA to use a very low
effective weighting on the accelerometers when the AHRS500GA is
moved. This makes the AHRS500GA very accurate in dynamic maneuvers.
SUNSTAR传感与控制 http://www.sensor-ic.com/ TEL:0755-83376549 FAX:0755-83376182 E-MAIL:[email protected]m
SUNSTAR自动化 http://www.sensor-ic.com/ TEL: 0755-83376489 FAX:0755-83376182 E-MAIL:[email protected]

AHRS500GA Series Operator’s Manual
Page 8Doc# 7430-0060-02 Rev. A
The AHRS500GA outputs the stabilized pitch, roll and yaw angles in the
digital data packet in angle mode. To convert the digital data to angle, use
the following relation:
angle = data*(SCALE)/215
where angle is the actual angle in degrees (pitch, roll or yaw), data is the
signed integer data output in the data packet, andSCALEis a constant.
SCALE= 180°for roll, pitch and yaw.
3.3.2 Sensor Measurements
The analog accelerometer and gyro sensors are sampled, converted to
digital data, temperature compensated, corrected for misalignment, and
scaled to engineering units. The digital data represents the actualvalue of
the quantities measured. A calibration table for each sensor is stored in the
AHRS500GA non-volatile memory. The data is sent as signed 16-bit 2’s
complement integers. To convert the acceleration data into G’s, use the
following conversion:
accel = data*(10 * 1.5)/215
where accel is the actual measured acceleration in G’s, data is the digital
data sent by the AHRS500GA, and10 is the G Range for your
AHRS500GA. (The data is scaled so that 1 G = 9.80 m s-2.) This maximum
G range is a default value.
To convert the angular rate data into degrees per second, use the following
conversion:
rate = data*(800*1.5)/215
where rate is the actual measured angular rate in °/sec, data is the digital
data sent by the AHRS500GA, and800 is the Angular rate Range of the
AHRS500GA. This maximum angular rate is a default value.
3.3.3 BIT Processing
The BIT message in each packet provides comprehensive information into
system health. The following information is supplied in the BIT byte fields
of the data packet. The table contains the actual bit definition present in the
two-byte output BIT field in the angle mode data packet (see section 3.6
below). The description defines the bit’s active (1) position.
SUNSTAR传感与控制 http://www.sensor-ic.com/ TEL:0755-83376549 FAX:0755-83376182 E-MAIL:[email protected]m
SUNSTAR自动化 http://www.sensor-ic.com/ TEL: 0755-83376489 FAX:0755-83376182 E-MAIL:[email protected]

AHRS500GA Series Operator’s Manual
Doc# 7430-0060-02 Rev. A Page 9
Table 5Bit Message Definition
BIT Data Description Bit
Location
Hard Failure An unrecoverable failure has
occurred Bit 0
Soft Failure A soft failure has been detected. A
soft failure can be generated by any
BIT condition designated “soft”. If
the soft failure persists for more than
2100 data packets the Hard Failure
bit is turned on and the Soft Failure
bit is permanently on.
Bit 1
Not Ready The system is not ready to use Bit 2
Power Fail A power failure has been detected.
The system is on hold-up power and
is about to lose power.
Bit 3
Comm A serial port (user) communications
error (ex over-run, parity) has been
detected.
Bit 4
Reboot Detect A processor reset was detected
possibly due to a watchdog timeout
or low-power setting.
Bit 5
Calibration
Table A bad calibration table in flash
memory has been detected. Bit 6
Turn Indicator A turn has been detected Bit 8
Not ready, waiting for power-up or
post sensor saturation Bits 10,9: 11
Valid data but in initialization mode Bits 10,9: 10
Valid data but using only gyro
integration to provide attitude output Bits 10,9: 01
Algorithm Status
Full accuracy data Bits 10,9: 00
Magnetometer
Cal Status A Hardiron/Softiron calibration is
being performed. Bit 11
Magnetometer
Cal Validity Bad stored Hardiron/Softiron
calibration data has been detected Bit 12
Magnetometer
Cal Performance The Hardiron/Softiron calibration is
unsatisfactory Bit 13
SUNSTAR传感与控制 http://www.sensor-ic.com/ TEL:0755-83376549 FAX:0755-83376182 E-MAIL:[email protected]m
SUNSTAR自动化 http://www.sensor-ic.com/ TEL: 0755-83376489 FAX:0755-83376182 E-MAIL:[email protected]

AHRS500GA Series Operator’s Manual
Page 10 Doc# 7430-0060-02 Rev. A
3.4 Commands
The AHRS500GA does not have a command structure.
3.5 Data Packet Format
In general, the digital data representing each measurement is sent as a 16-bit
number (two bytes). The data is sent MSB first then LSB.
Table 6AHRS500GA Series Data Packet Format
Byte Data
0Header (0xAA)
1Header (0x55)
2Roll Angle (MSB)
3Roll Angle (LSB)
4Pitch Angle (MSB)
5Pitch Angle (LSB)
6Heading Angle (MSB)
7Heading Angle (LSB)
8Roll Angular Rate (MSB)
9Roll Angular Rate (LSB)
10 Pitch Angular Rate (MSB)
11 Pitch Angular Rate (LSB)
12 Yaw Angular Rate (MSB)
13 Yaw Angular Rate (LSB)
14 X-Axis Acceleration (MSB)
15 X-Axis Acceleration (LSB)
16 Y-Axis Acceleration (MSB)
17 Y-Axis Acceleration (LSB)
18 Z-Axis Acceleration (MSB)
19 Z-Axis Acceleration (LSB)
20 Model Number (MSB)
21 Model Number (LSB)
22 BIT (MSB)
23 BIT (LSB)
24 Checksum (MSB)
These numbers are sent as a 16-bit signed integer in 2's complement format.
The data is sent as two bytes, MSB first then LSB.
SUNSTAR传感与控制 http://www.sensor-ic.com/ TEL:0755-83376549 FAX:0755-83376182 E-MAIL:[email protected]m
SUNSTAR自动化 http://www.sensor-ic.com/ TEL: 0755-83376489 FAX:0755-83376182 E-MAIL:[email protected]

AHRS500GA Series Operator’s Manual
Doc# 7430-0060-02 Rev. A Page 11
Each data packet will begin with a two-byte header (hex AA 55) and end
with a two-byte checksum. The checksum is calculated in the following
manner:
1. Sum all packet contentsexcept header and checksum.
2. Divide the sum by hex FFFF.
3. The remainder should equal the checksum.
The packet also contains the model type configuration number, and the BIT
word output. Please refer to section 3.3.3 for details about the BIT word
processing.
3.6 Timing
The default AHRS500GA data output rate is 100 samples per second.
Depending on the model configuration chosen, the system output sample
rate can be set to a different constant value.
In some applications, using the AHRS500GA’s digital output requires a
precise understanding of the internal timing of the device. The processor
internal to the AHRS500GA runs in a loop-collecting data from the
sensors, processing the data, and then collecting more data. The data is
reported to the user through a parallel process.
The unit goes through three processes in one data cycle. First, the sensors
are sampled. Second, the unit processes the data for output. After
processing the data, the AHRS500GA will make another measurement
while presenting the current measurement for output. Third, the unit
actually transfers the data out over the RS-232 port.
3.7 Magnetic Heading
Magnetic north is the direction toward the magnetic north pole; true north is
the direction towards the true North Pole.
The AHRS500GA yaw angle output is referenced to magnetic north. The
direction of true north will vary from magnetic north depending on your
position on the earth. The difference between true and magnetic north is
called declination or magnetic variance. You will need to know your
declination to translate the AHRS500GA magnetic heading into a heading
referenced to true north.
SUNSTAR传感与控制 http://www.sensor-ic.com/ TEL:0755-83376549 FAX:0755-83376182 E-MAIL:[email protected]m
SUNSTAR自动化 http://www.sensor-ic.com/ TEL: 0755-83376489 FAX:0755-83376182 E-MAIL:[email protected]

AHRS500GA Series Operator’s Manual
Page 12 Doc# 7430-0060-02 Rev. A
4AHRS500GA Operation
4.1 Normal Operation
The AHRS500GA is configured to output data continuously when power is
applied. The AHRS500GA does not recognize any input serial commands.
4.2 Calibration Operation
The AHRS500GA can be commanded to perform a hard/soft iron
calibration for the magnetometers using the procedure in Appendix C. Data
supplied during normal operation will not be available and the data output
should not be used for flight purposes.
4.3 Viewing AHRS500GA Data with GyroView
Crossbow includes GyroView software to allow you to directly view the
AHRS500GA data. Install the GyroView software, connect the
AHRS500GA to your serial port, apply power to your unit and start taking
measurements.
4.3.1 GyroView Computer Requirements
The following are minimum capabilities that your computer should have to
run GyroView successfully:
•CPU: Pentium-class
•RAM Memory: 32MB minimum, 64MB recommended
•Hard Drive Free Memory: 15MB
•Operating System: Windows 95, 98, NT4, 2000
4.3.2 Install GyroView
To install GyroView in your computer:
1. Insert the CD “Support Tools” in the CD-ROM drive.
2. Find the GyroView folder. Double click on the setup file.
3. Follow the setupwizard instructions. You will install GyroView
and a LabView Runtime Engine. You will need both these
applications.
If you have any problems or questions, you may contact Crossbow directly.
4.3.3 Connections
The AHRS500GA is shipped with a calibration/maintenance cable to
connect the AHRS500GA to a PC communications port.
SUNSTAR传感与控制 http://www.sensor-ic.com/ TEL:0755-83376549 FAX:0755-83376182 E-MAIL:[email protected]m
SUNSTAR自动化 http://www.sensor-ic.com/ TEL: 0755-83376489 FAX:0755-83376182 E-MAIL:[email protected]

AHRS500GA Series Operator’s Manual
Doc# 7430-0060-02 Rev. A Page 13
1. Connect the 15-pin end of the digital signal
calibration/maintenance cable to the port on the AHRS500GA.
2. Connect the 9-pin end of the calibration/maintenance cable to the
serial port of your computer.
3. Connect the 15-pin end of the digital signal
calibration/maintenance cable to the aircraft mating cable.
4. Bolt the base of the unit to a grounded surface. A good ground is
required for EMI and lightning over-voltage protection.
MWARNING
Do not reverse the power leads! Applying the wrong power to the
AHRS500GA can damage the unit; although there is reverse power
protection, Crossbow Technology is not responsible for resulting damage to
the unit should the reverse voltage protection electronics fail.
4.3.4 Setup GyroView
With the AHRS500GA connected to your PC serial port and powered, open
the GyroView software (Rev 2.3 or later).
1. GyroView should automatically detect the AHRS500GA and
display the serial number and firmware version if it is connected.
2. If GyroView does not connect, check that you have the correct
COM port selected. You find this under the “DMU” menu.
3. Select the type of display you want under the menu item
“Windows”. Graph displays a real time graph of all the
AHRS500GA data; FFT displays a Fast-Fourier transform of the
data; Navigation shows an artificial horizon display.
4. You can log data to a file by entering a data file name. You can
select the rate at which data is saved to disk.
5. If the status indicator says, “Connected”, you’re readyto go. If
the status indicator doesn’t say connected, check the connections
between the AHRS500GA and the computer; check the power;
check the serial COM port assignment on your computer.
4.3.5 Take Measurements
Once you have configured GyroView to work with your AHRS500GA, pick
what kind of measurement you wish to see. “Graph” will show you the
output you choose as a strip-chart type graph of value vs. time. “FFT” will
show you a real-time Fast-Fourier transform of the output you choose.
“Navigation” will show an artificial horizon and the stabilized pitch and roll
output of the AHRS500GA.
SUNSTAR传感与控制 http://www.sensor-ic.com/ TEL:0755-83376549 FAX:0755-83376182 E-MAIL:[email protected]m
SUNSTAR自动化 http://www.sensor-ic.com/ TEL: 0755-83376489 FAX:0755-83376182 E-MAIL:[email protected]

AHRS500GA Series Operator’s Manual
Page 14 Doc# 7430-0060-02 Rev. A
Let the AHRS500GA warm up for 90 seconds when first turned on. This
allows the Kalman filter to estimate the rate sensor biases. Now you’re
ready to use the AHRS500GA!
SUNSTAR传感与控制 http://www.sensor-ic.com/ TEL:0755-83376549 FAX:0755-83376182 E-MAIL:[email protected]m
SUNSTAR自动化 http://www.sensor-ic.com/ TEL: 0755-83376489 FAX:0755-83376182 E-MAIL:[email protected]
Table of contents
Popular Industrial Electrical manuals by other brands

Arcteq
Arcteq AQ-E215 instruction manual
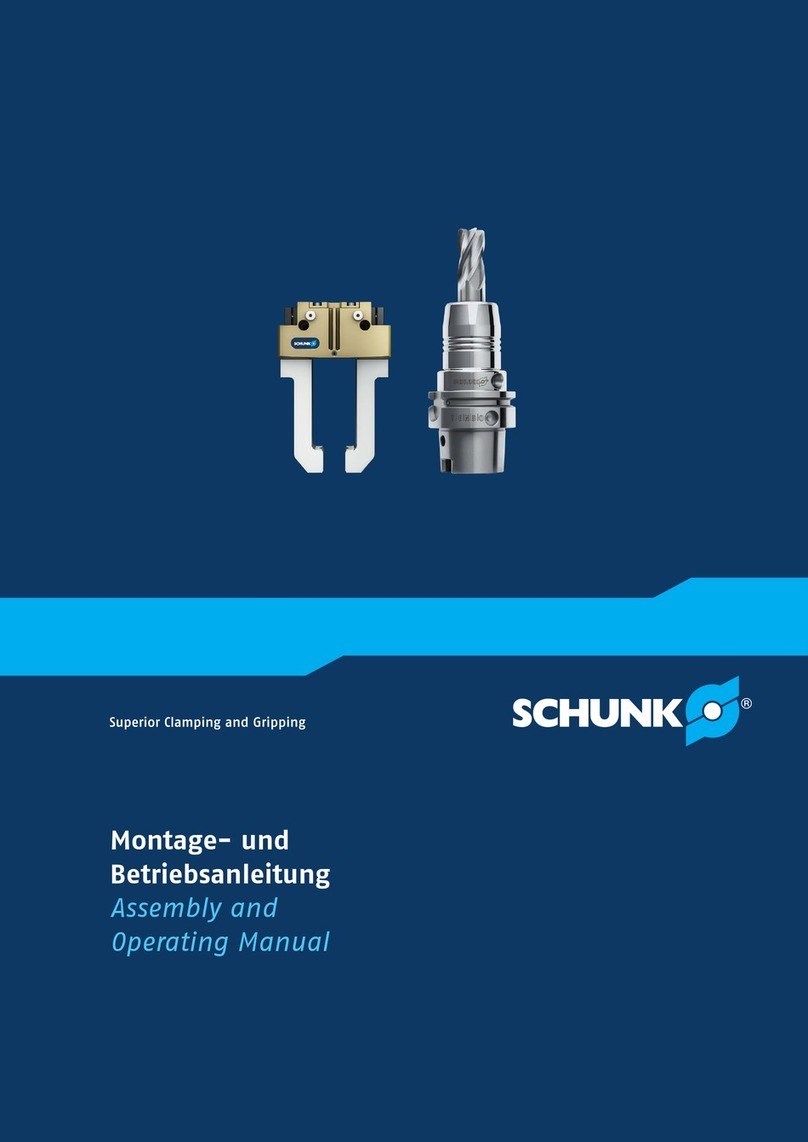
SCHUNK
SCHUNK ELB Series Assembly and operating manual
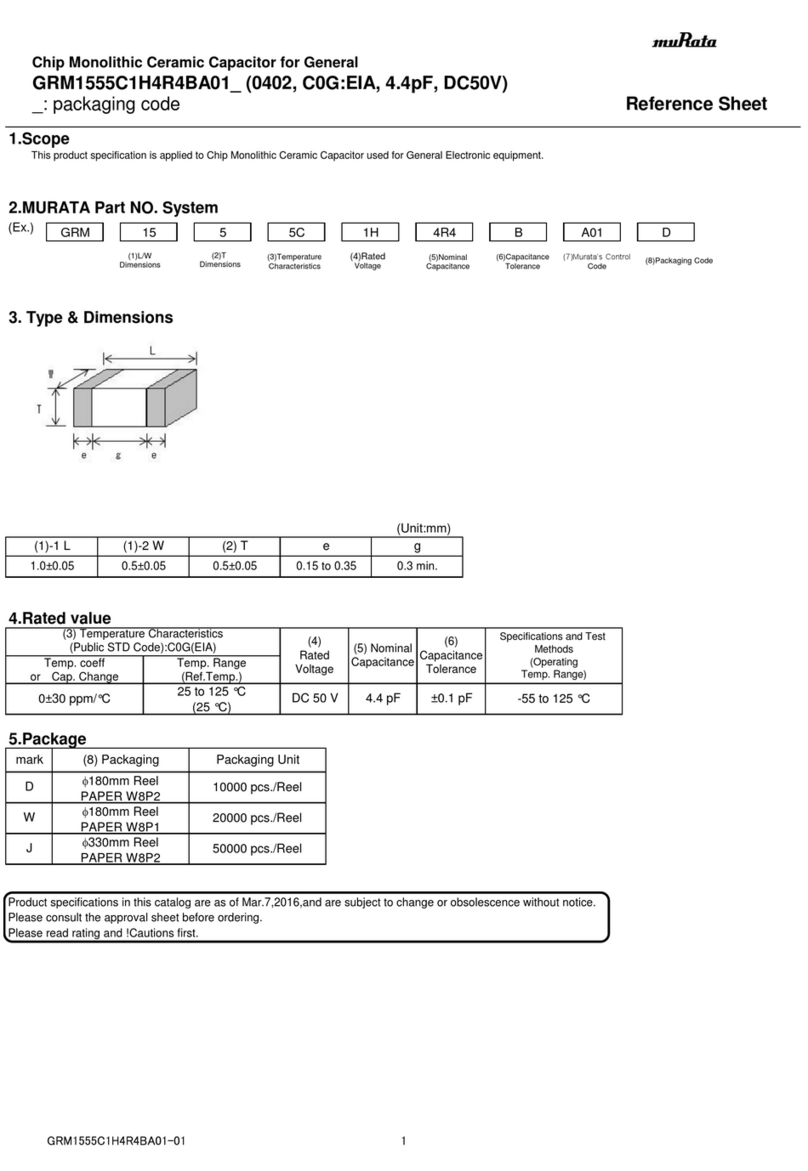
Murata
Murata GRM1555C1H4R4BA01 Series Reference sheet
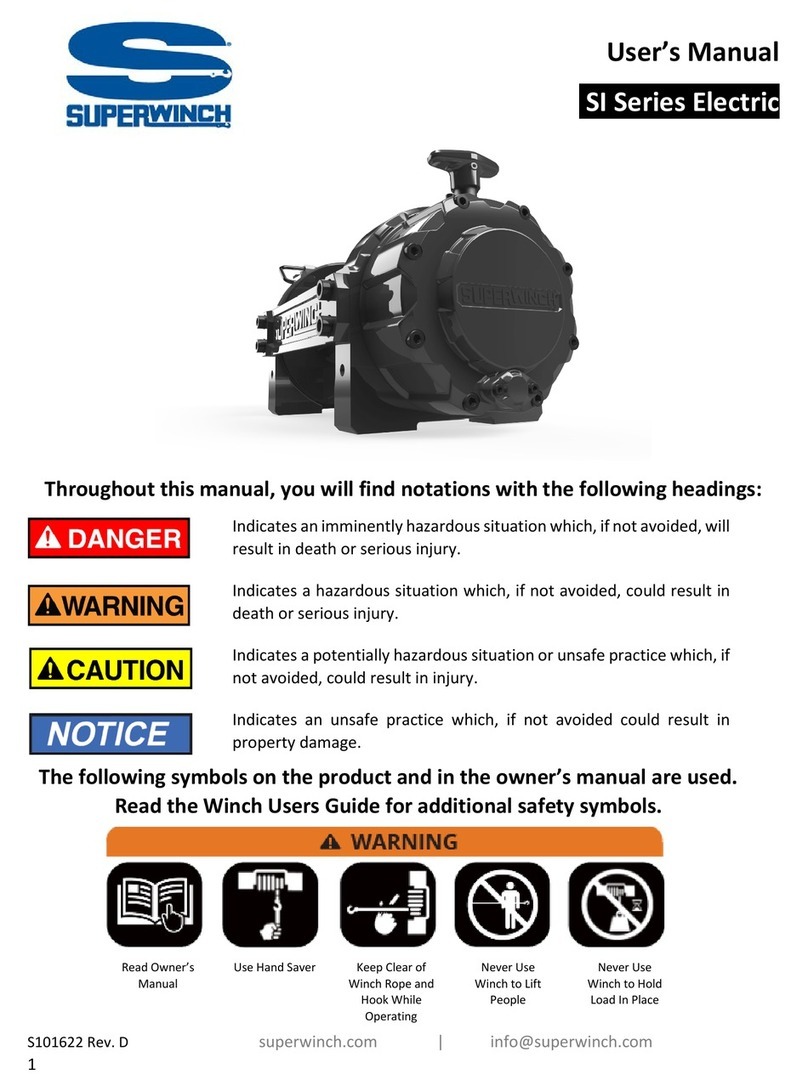
Superwinch
Superwinch SI Series Electric user manual

Murata
Murata GRT155C81E224KE01 Series Reference sheet
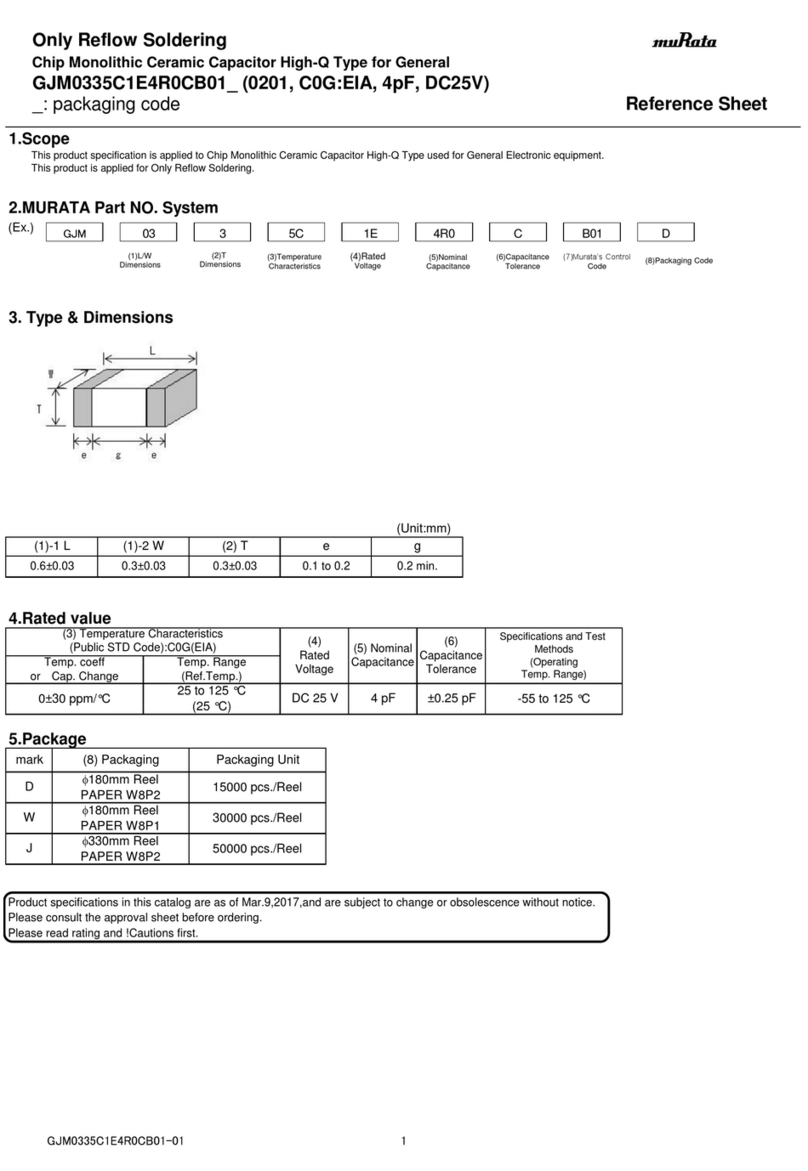
Murata
Murata GJM0335C1E4R0CB01 Series Reference sheet

Festo
Festo CPX-FB33 operating instructions

Murata
Murata GRM2165C1H332JA01 Series Reference sheet

Eaton
Eaton RMQ-Titan M22-FI Series Instruction leaflet
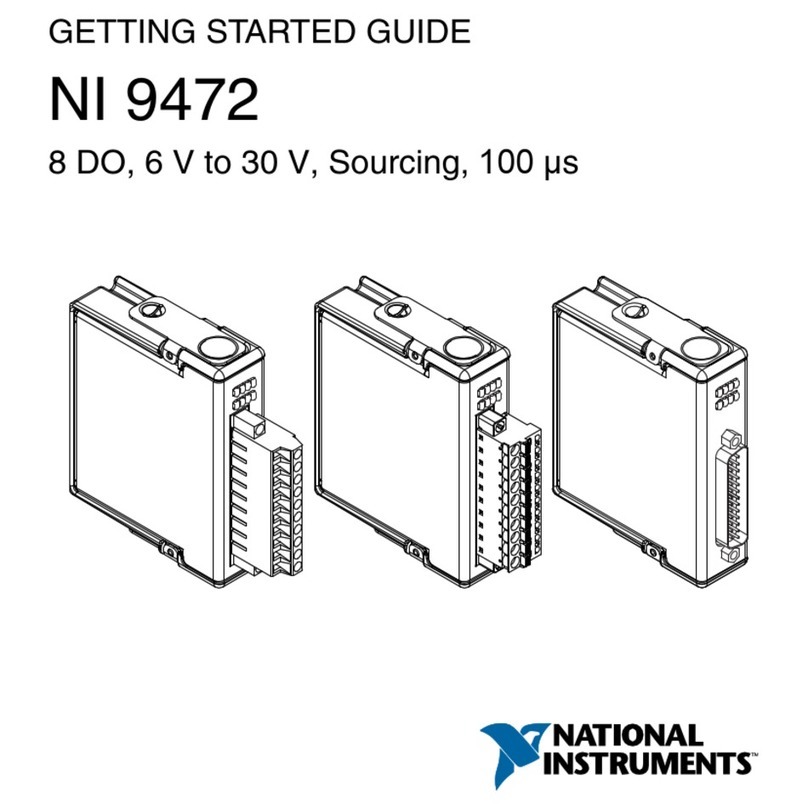
National Instruments
National Instruments NI 9472 Getting started guide
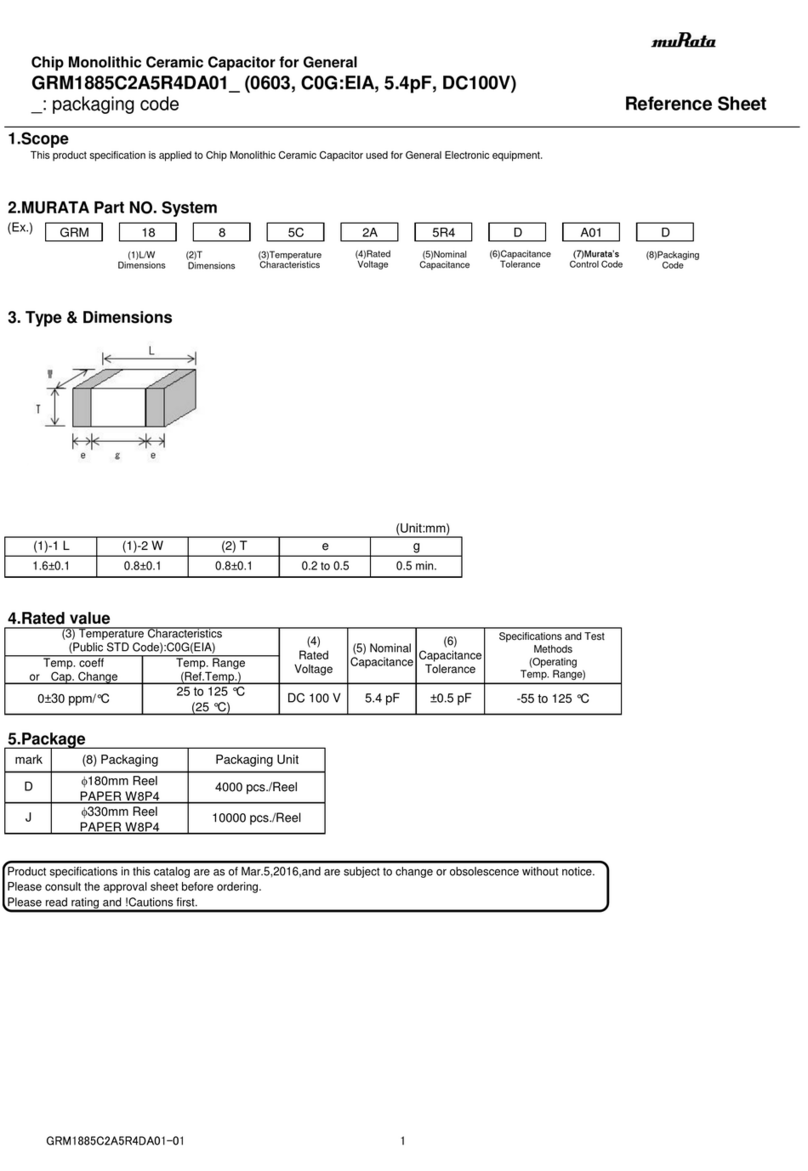
Murata
Murata GRM1885C2A5R4DA01 Series Reference sheet

Monacor
Monacor TM-25 instruction manual