CSP Pacific BarrierGuard 800 User manual

Product & Installation Manual : BarrierGuard 800
Ph 0800 655 200 or visit www.csppacific.co.nz July 2013 / Page 1
BarrierGuard800
Temporary Steel Safety Barrier
NCHRP 350 TL-3 & TL-4
Product and Installation Manual

Product & Installation Manual : BarrierGuard 800
Ph 0800 655 200 or visit www.csppacific.co.nz July 2013 / Page 2
Table of Contents
Application Guide . . . . . . . . . 3
Limitations and Warnings . . . . . . . . 4
System Design Considerations . . . . . . . 5
Major Components List . . . . . . . . 7
Installation Details . . . . . . . . . 8
Ground Conditions & Anchor Specifications . . . . . 10
Crash Cushions . . . . . . . . . 13
Delineators . . . . . . . . . . 13
Installation Tools List . . . . . . . . 14
Installation Procedure . . . . . . . . 16
Full Height Terminal Installation. . . . . . . 17
Ramped End Terminal Installation . . . . . 18
Standard Section Installations . . . . . . 19
Intermediate Anchoring . . . . . . . 20
Laying BarrierGuard 800 . . . . . . . 21
Joining BarrierGuard 800 Sections . . . . . 21
Drilling for Anchors . . . . . . . . 22
Maintenance & Repair . . . . . . . 23
Removal . . . . . . . . . 25
Special Operations . . . . . . . . 26
Diagrams of Offset . . . . . . . 27
Expansion Joints . . . . . . . . 28
External Anchor Shoe Connection . . . . . 29
Inner Anchor Shoe Connection . . . . . . 30
Lifting BarrierGuard 800 . . . . . . . . 31
Truck Mounted Cranes . . . . . . . 31
Using Chains. . . . . . . . . 32
Using Tag Ropes . . . . . . . . 34
Turning Barrier Over . . . . . . . 34
Safety Zones for Loading . . . . . . . 35
Loading and Unloading from Trucks . . . . . . 36
Noise Pollution . . . . . . . . 37
Risk Assessments . . . . . . . . . 38
Unloading and Loading Units . . . . . . 38
Connection of Units . . . . . . . . 39
Coring/Drilling for Installation of Anchor System. . . . 40
Righting Inverted Units/Inverting Units . . . . . 40
Frequently Asked Questions . . . . . . . 41
Installation Check List . . . . . . . . 42
Appendix A - Technical Drawings . . . . . . 44
Appendix B - Letter of Acceptance . . . . . . 47

Product & Installation Manual : BarrierGuard 800
Ph 0800 655 200 or visit www.csppacific.co.nz July 2013 / Page 3
Preface
The CSP Pacific BarrierGuard 800 is a temporary barrier system, in conjunction with an
approved crash cushion, that is a rapidly deployable safety barrier for use where a vehicle
restraint system conforming to NCHRP350 TL-3 or TL-4 is required.
As with any roadside safety device, the BarrierGuard 800 must be installed properly to ensure
proper performance. Thoroughly review and fully understand the instructions and product
limitations before starting the installation. Do not start the installation without the proper plans
and tools required.
If you require additional information or have questions about the BarrierGuard 800
system please call CSP Pacific on 0800 655200 or email
Introduction
BarrierGuard 800 has been extensively tested in accordance with NCHRP 350 and has
successfully demonstrated its capability to achieve the containment and performance Levels of
Test Level 3 and 4. NCHRP350 TL-3 crash test criteria is an impact with a 2.2 Tonne vehicle
at speed of 100kph at an impact angle of 25degrees. NCHRP350 TL-4 crash test criteria is an
impact with a 8.0 Tonne vehicle at speed of 80kph at an impact angle of 15degrees and has
the same containment energy as a TL-3 impact.
BarrierGuard 800 is a deformable vehicle restraint system acting as a continuous beam,
anchored to the ground at the end of each run through specially designed terminal sections. It
consists of single elements of prefabricated 6.0m long or 3.0m long steel barrier. Two
elements are bolted together at the factory providing 12.0m long or 6.0m long sections with
male and female QuickLink connectors to facilitate speedy erection on site. Connection is
achieved by lining up the barrier and locking the QuickLink connectors together. The
permissible length of the system is unlimited as the barrier, which is only anchored at the end
of each run, attains its performance characteristics by a combination of torsional rigidity and
self-weight.
System Application Guide
BarrierGuard 800 is a versatile longitudinal steel barrier that has many uses and is quick and
easy to install. BarrierGuard 800 is normally made up of two 6m barrier sections that are pre
assembled by being bolted together to form a 12m length with the QuickLink linking system at
either end. To make the BarrierGuard 800 as versatile as possible there are also sections
made up from 2 No. 3m sections to create 6m lengths and a selection of short radius sections
to enable installations around tight radii.

Product & Installation Manual : BarrierGuard 800
Ph 0800 655 200 or visit www.csppacific.co.nz July 2013 / Page 4
BarrierGuard 800 has successfully been tested with a selection of anchoring methods and in
various ground conditions making it a versatile system that can be used on many differing
surfaces.
The barrier system is used as a temporary barrier for road construction sites where it can be
used for nearside or offside applications to protect construction sites and construction
workforce as a positive form of protection. It can also be used as a positive separation for
opposing traffic flows in a contra-flow situation.
With the versatile shorter barrier sections and radius sections most vertical and horizontal
curve alignments can be accommodated so BarrierGuard 800 is just as useful for the local
roads as well as on the State Highway network.
Limitations and Warnings
The BarrierGuard 800 systems have been designed and tested in accordance to the criteria
detailed in the National Cooperative Highway Research Program Report No. 350 (NCHRP
350) for longitudinal barriers, and have been accepted for use by the US Federal Highway
Administration (FHWA).
For BarrierGuard 800 to perform as tested it must be correctly installed and anchored in
accordance with the details contained in this manual. If the installation of the BarrierGuard 800
is not able to be flared as per this manual then there must be an approved NCHRP 350 TL-3
crash cushion connected to the barrier with a clear zone area of 6 x 22.5m adjacent to the
crash cushion and behind the barrier that is flat and without hazards. In addition workers,
equipment and materials should be a minimum of 6m behind the barrier. Please refer to the
drawings in the appendix of this manual.
When properly installed and maintained the BarrierGuard 800 allows an impacting vehicle to
be stopped in a safe and predictable manner under the NCHRP 350 impact conditions. Vehicle
impacts that vary from NCHRP 350 impact conditions described for longitudinal barriers may
result in significantly different results than those experienced in testing. Vehicle impact
characteristics different than, or in excess of, those encountered in NCHRP 350 testing
(weight, speed and angle) may result in a system performance that does not meet the NCHRP
350 evaluation criteria.
The adjacent road operating speed must be limited to 100kph for TL-3 performance. The
installation should endeavour to minimise the impact angles to 25 degrees (1 lateral:2.14
forward). If the BarrierGuard 800 installation is for TL-4 performance then the operating speed
must be limited to 80kph and impact angles minimised to 15 degrees (1 lateral: 3.73 forward).
The system should be delineated in accordance with road controlling authority requirements.
The BarrierGuard 800 needs to be installed on a firm surface that prevents the system from
becoming embedded in the surface over long periods of time. Debris and foreign objects
should not be in the clear zone.

Product & Installation Manual : BarrierGuard 800
Ph 0800 655 200 or visit www.csppacific.co.nz July 2013 / Page 5
Safety Statements
General Safety
•All required traffic safety precautions should be complied with. All workers should wear
required safety clothing (high visibility vests, steel capped footwear, gloves etc.)
•Only authorised trained personnel should operate any machinery. Where overhead
machinery is used, care must be taken to avoid overhead hazards.
•Gloves should be worn at all times.
System Design Considerations
Slopes
For the system to perform correctly it should be installed to ground that has a cross slope of no
more than 8% or 1:8. On slopes greater than this, approval is required from the road
controlling authority.
Curbs
BarrierGuard 800 can be installed to a surface which is raised by a curb of no more than
100mm high. If the barrier is installed next to the curb you must ensure that the curb is out of
the clear zone and does not prevent the barrier deflecting as intended. If there is no option
but to install in front, behind or on a curb, approval is required from the road controlling
authority.
Undulating Ground Conditions
Site specific grading may be necessary to ensure that there are no “humps” or “hollows” that
may significantly alter the impacting vehicles stability or substantially alter the height of the
BarrierGuard 800 in relation to the ground.

Product & Installation Manual : BarrierGuard 800
Ph 0800 655 200 or visit www.csppacific.co.nz July 2013 / Page 6
Soil Conditions
BarrierGuard 800 is installed above ground so soil conditions on site are not applicable.
However it is recommended that the system is installed on a compacted surface.
Underground services
Before drilling for the installation of anchors it is important to check the area for any under
ground services.
Median and Roadside applications
BarrierGuard 800 can be used in both roadside and median/bi-directional traffic applications.
Anchoring conditions
BarrierGuard 800 has been designed and tested to be used utilising several different types of
anchoring conditions these include concrete, asphalt and soil, for further details please see
page 10 of this manual.
Clear Zone
When anchored at both ends BarrierGuard 800 requires a clear zone of 1.5m behind to allow
the system to perform correctly. When anchored every 12m the deflection is reduced 0.92m.

Product & Installation Manual : BarrierGuard 800
Ph 0800 655 200 or visit www.csppacific.co.nz July 2013 / Page 7
Major Components List
BG800 12m section, male/female QuickLink
BG800 6m section, male/female QuickLink
BG800 with full height anchor
BG800 with a crash cushion end treatment
BG800 12m ramped end, male/female QuickLink
BG800 6m ramped end, male/female QuickLink or bolted
BG800 12m fixed gate post section

Product & Installation Manual : BarrierGuard 800
Ph 0800 655 200 or visit www.csppacific.co.nz July 2013 / Page 8
BG800 3m mobile hinge section
BG800 6m wheeled gate section
BG800 6m gate section
All M16 Bolts used for connecting sections of Barrier Guard 800 together to be at least
Grade 8.8

Product & Installation Manual : BarrierGuard 800
Ph 0800 655 200 or visit www.csppacific.co.nz July 2013 / Page 9
Installation Details
It is important that before any installation is carried out the correct planning and preparation
takes place which includes a site visit. This is necessary to keep to a minimum the time spent
on site and that the installation goes quickly and without issue. Things that need to be
considered and checked are, any lifting restrictions i.e. low bridges, any underground services
in the vicinity of drilling operations, layout and alignment of the barrier including any radii that
the barrier may have to go round. It is important to also ensure the correct loading of the
BarrierGuard 800, i.e. it is put on to the delivery truck the right way around and the terminal
sections are in the correct place on the load.
The ground conditions that the barrier is to be installed on and anchored to need to be
established to ensure the correct anchoring choice is made and the appropriate anchor shoe is
connected to the barrier. Full details of common ground conditions and the available types of
anchors and anchor shoes can be found on pages 10 to 12. For use of BarrierGuard 800 on
any ground conditions or anchors that are not shown in this drawing please contact CSP
Pacific for advice.
Standard NCHRP 350 tested BarrierGuard 800 only requires anchoring to the ground at each
end of a run, there are integral anchor points beneath an easily removed cover at the extreme
end of the specially designed anchor sections. There is a second anchor point at the first
bolted joint up stream of the end of the section; these anchors can either be external or
internal anchor shoes depending upon site restrictions or preference. Both the anchor shoes
and the integral anchor points require 4 x anchor pins/bolts each (8 in total per end anchor
section).
The Length of Need of BarrierGuard 800 is the total installed length between the two Inner
Anchor Shoes.
The Beginning of the Length of Need is measured 6m from the approach (upstream) end of
the BarrierGuard 800 terminal (at the Inner Anchor Shoe). If an approved, gating (non-
redirective) end termination such as an ABSORB 350® crash cushion is connected to the
BarrierGuard 800 terminal, then the Beginning of the Length of Need is 6m from the approach
(upstream) end of the BarrierGuard 800 terminal (Inner Anchor point). If an approved, non-
gating (redirective) end termination such as a TAU II® crash cushion is connected to the
BarrierGuard 800 terminal, then the approach (upstream) end of such system becomes the
beginning of the Length of Need.
When deciding Length of Need of a system consideration must be given to the proximity of any
anchor points to any excavations, if the BarrierGuard 800 is to be used to protect errant
vehicles from excavations we recommend that the anchoring takes place beyond any
excavation and if any extra anchoring is required it should be single sided away from the
excavated face.
The minimum recommended installed length of BarrierGuard 800 is 18m between Inner
Anchor Shoes i.e. for an installation with no approved crash cushion connected to the end
terminal; the minimum total system length including terminals and anchors is 60m. Please
refer to the relevant drawings located in Appendix A.

Product & Installation Manual : BarrierGuard 800
Ph 0800 655 200 or visit www.csppacific.co.nz July 2013 / Page 10
Anchor Foundation Specifications
The BarrierGuard 800 system has been designed to attach to concrete or asphalt foundations,
or anchored into soil using driven piles. Use the anchorage specified on page 11, depending
on the foundation at the specific job sit.
1. Concrete Pad
Foundation:
Min 150mm reinforced PCC pad or 200mm
non reinforced PCC pad
2. Asphalt over Subbase
Foundation:
Min 150mm AC over 150mm compacted
DGA subbase
3. Asphalt only
Foundation:
Min 200mm AC
4. Asphalt over P.C. concrete
Foundation:
AC over PCC
5. Compacted Subbase (DGA) – Soil
Foundation:
Min 200mm compacted PGA subbase or
equivalent soil properties
150mm reinforced
or 200 non
reinforced
150mm
150mm
200mm
AC
PCC

Product & Installation Manual : BarrierGuard 800
Ph 0800 655 200 or visit www.csppacific.co.nz July 2013 / Page 11
Material Specifications
Portland Cement Concrete (PCC)
Stone aggregate concrete mix, 28 MPa
minimum compressive strength (Sampling per
ASTM C31-84 or ASTM C42-84A, testing per
ASTM C39-84)
Asphaltic Concrete (AC)
AR-4000 A.C. (Per ASTM D3381 '83) 19mm
maximum, medium (type A or B) aggregate
Sieve Size % Passing
25mm 100
19mm 95-100
9.5mm 65-80
No. 4 49-54
No. 8 36-40
No. 30 18-21
No. 200 3-8
Compacted Subbase (DGA)
150mm minimum depth, 95% compaction,
class 2 aggregate
Sieve Size % Passing
75mm 100
64mm 90-100
No. 4 40-90
No. 200 0-25

Product & Installation Manual : BarrierGuard 800
Ph 0800 655 200 or visit www.csppacific.co.nz July 2013 / Page 12
Types of Anchor Anchor connecting to BarrierGuard 800
Flat top pin: 30mm
Embedment depth: 400mm
Hole size: 32mm x 450mm deep
Can be used on foundation
conditions types 1, 2, 3, 4
External Anchor Shoe Assembly
Can be used with:
1" X 200mm Threaded bar
1" X 460mm Threaded bar
M24 Mech anchor
Flat top pins
Flag top pins (non traffic face)
Flag top pin 30mm
Embedment depth 400mm
Hole size: 32mm x 450mm DEEP
Can be used on foundation
conditions types 1, 2, 3, 4
NOT TO BE USED EXTERNALLY
OF TRAFFIC FACE
Single Intermediate Anchor
Can be used with:
1" X 200mm Threaded bar
1" X 460mmThreaded bar
M24 Mech anchor
Flat top pins
Flag top pins (non traffic face)
210mm galvanised threaded bar
assembled with a M24 galv washer
and M24 nut – use with suitable
chemical resin anchor. 150mm
embedment.
Can be used on foundation
conditions type 1 only
Double Intermediate Anchor
Can be used with:
1" X 200mm Threaded bar
1" X 460mm Threaded bar
M24 Mech anchor
Flat top pins
Flag top pins (non traffic face)
M24 x 460mm galvanised threaded
bar assembled with a
M24 galv washer and M24 nut – use
with suitable chemical resin anchor.
400mm embedment.
Can be used on foundation
conditions type 1, 2, 3, 4
Special
External Anchor Shoe Assembly
Can be used with:
1" X 200mm Threaded bar
1" X 460mm Threaded bar
M24 Mech anchor
Flat top pins
Flag top pins (non traffic face)
Subbase anchor pile
M24 Mechanical anchor with
effective embedment depth of
150mm.
Can be used on foundation
conditions type 1 only
Special
Intermediate Subbase Anchor
Can be used with Subbase
anchor pile
Special
Subbase anchor pile 140mm
Embedment depth of 800mm
Can be used on foundation
conditions type 5
MUST BE DRIVEN

Product & Installation Manual : BarrierGuard 800
Ph 0800 655 200 or visit www.csppacific.co.nz July 2013 / Page 13
Crash Cushions
When choosing a suitable crash cushion for use with BarrierGuard 800 special consideration
must be given to opting for a Gating (non re-directive) Crash Cushion or a Non-Gating (re-
directive) Crash Cushion. A Non-Gating Crash Cushion is one that has been tested to
withstand a side impact from an errant vehicle and a Gating system is one that has not been
tested for this impact angle. If opting for a Gating Crash Cushion then consideration must be
given to allow for a safe run out area behind the system.
If it is not possible to locate the terminal ends outside the Clear Zone, then an approved end
termination (such as a crash cushion) can be fitted to the BarrierGuard 800. Any crash cushion
will have its own anchoring specifications and assembly instructions. Any connection between
BarrierGuard 800 and the approved end termination will be designed and supplied by either
CSP Pacific or the approved end termination supplier.
Approved end terminations that are currently available with designed connections are:
i ABSORB 350® - refer to the CSP Pacific ABSORB 350® Product & Installation manual
for number of units required.
ii TAU II® - refer to the CSP Pacific TAU II® Product & Installation manual for further
information.
Please note that i is Gating (non re-directive)and ii is Non-Gating (re-directive).
The performance of the selected crash cushion and the BarrierGuard 800 could be greatly
affected if the barrier is positioned next to a curb or other fixed object, The barrier should be
positioned so that all fixed objects are outside of the barriers Clear Zone for the speed and
containment level.
Delineators
Depending on location, delineation may be required as per the Road Controlling
Authority Guidelines.
For further details consult MoTSaM, Part 2: Section 5 or contact CSP Pacific on 0800 655200

Product & Installation Manual : BarrierGuard 800
Ph 0800 655 200 or visit www.csppacific.co.nz July 2013 / Page 14
Installation Tools List
Lifting Device: Must have suitable lifting capacity and reach to lift, manoeuvre and
install BarrierGuard 800 (e.g. Truck mounted crane such as a HIAB). It
is also recommended that these cranes are remote control for ease of
use
Lifting Chains: A two leg assembly with a 2500kg lifting capacity, each chain is 2m
long c/w a hook and locking clasp, and shortening clutch. This is
suitable for lifting 12m sections of barrier and 6m sections made
up from 2 x 3m sections only
A two leg set with a 2500kg lifting capacity, each chain needs to be 3m
long c/w hook and locking clasp, and shortening clutch. These chains
are for lifting 6m lengths of barrier that are half of the 12m
sections
Tag rope: Rope with spring loaded karabiner clip. The Rope length needs to be
1.5 times the lifting height of the barrier
Drilling Equipment: Either an electric hammer drill c/w 32mm drill bit or an Air driven Rock
Drill c/w 33mm rock drill tool. To speed up installation consideration
should be given to having 2 drilling machines available
Also a Diamond Core drill suitable for cutting a 32mm hole up to
300mm deep in case of reinforcement bar when drilling in concrete
Generator: For use with the hammer drills, and or Diamond Core drill. Should be
capable of a high enough output to drive two hammer drills at the
same time as a minimum
Extension Leads: For generator above
10m Tape Measure
Road Marking Paint and Chalk
2 x 1.8m Crow Bar/Wrecking Bar
8mm Allen Key
10mm Allen Key
Magnetic BarrierGuard 800 “T” Bar socket and suitable handle
Wooden Packers: Approx 520mm x 300mm x 19mm, wooden ply wood packers. These
are used to support barrier over uneven surfaces
Timbers: Two blocks approx 200mm x 200mm x 300mm.
Approx 75mm x 75mm timber bearers

Product & Installation Manual : BarrierGuard 800
Ph 0800 655 200 or visit www.csppacific.co.nz July 2013 / Page 15
Small Impact Gun: C/w suitable sockets. 24mm impact socket as a minimum
Compressor: For the Rock Drills and Impact Gun. Should be capable of driving two
rock drills at once
Extension Pipes: For compressor above
Spanners/Wrenches: Combination spanners to include as a minimum 2 No each of the
following 13mm, 24mm, 30mm, 32mm & 36mm
13mm and 19mm Drive Socket sets
Torque Wrench (S): Suitable for torques up to 150 Nm. C/W suitable 24mm socket
Torque Wrench (L): Suitable for torques up to 300 Nm. C/W suitable 32mm socket
Podger (Round Pry Bar)
Sledge Hammer
Measuring Wheel
Cranked Crow Bar: Useful for removing tight pins

Product & Installation Manual : BarrierGuard 800
Ph 0800 655 200 or visit www.csppacific.co.nz July 2013 / Page 16
Installation Procedure
When planning the job it is essential that the following points are established and agreed with
the client:
•The required performance level of the BarrierGuard 800 relevant to the operating speed
environment;
•The start, finish and alignment of the BarrierGuard 800;
•Any additional anchorages required (e.g. to reduce deflection at a specific hazard that
cannot be relocated away from the safety zone) and their locations;
•Any curvature of the BarrierGuard 800 in both the horizontal and vertical planes;
•The type of road surface and the method of anchorage;
•Any expansion joints are identified;
•In the case of concrete pavements, if reinforcement is encountered when drilling that this
can be drilled through;
•The method of reinstatement of drilled holes when the BarrierGuard 800 is removed;
•There are no underground services, waterproof membranes etc. which could be damaged
by drilling;
•There are no overhead cables that could be contacted by the lifting operation; and
•There is adequate working room and safety zone.
Prior to loading in preparation for the job, the orientation of the BarrierGuard 800 must be
determined and the truck loaded with all barriers facing the correct way and as the barriers are
loaded a visual check on there condition must be carried out, if in doubt of the suitability of a
damaged barrier do not use until checked by a competent person.
Installation is normally started from the end of the BarrierGuard 800 and laid in the direction of
traffic flow. Sometimes when a long length of BarrierGuard 800 is to be installed and site
conditions allow, the installation can commence at any point along the length of the run, using
a section of BarrierGuard 800 with two male ends as the first unit to be placed and subsequent
standard sections laid outwards in both directions from this section simultaneously, this double
male quick link section can easily be identified by applying a paint mark to the top external
face of the barrier.
BarrierGuard 800 is always secured at its end by a Ramped End terminal or transitioned to an
approved end termination (such as a Crash Cushion). Details of Crash Cushion transitions are
available from CSP Pacific.

Product & Installation Manual : BarrierGuard 800
Ph 0800 655 200 or visit www.csppacific.co.nz July 2013 / Page 17
Full Height Terminal Installation
For External Anchor Shoe Applications:
1. Lower the terminal into the correct position as agreed
with the client.
2. Drill through the External Anchor Shoe (DO NOT
ANCHOR AT THIS TIME) anchor to the ground after
completely connecting first standard section to the
terminal section (see Standard Sections Installation
section), use the appropriate method of anchoring as
agreed with the client prior to installation (see Drilling
for Anchors section).
3. Go directly to point 7 from the following (For Inner
Anchor Shoe Applications section).
For Inner Anchor Shoe Applications:
1. Mark out the location of the first Inner Anchor Shoe on the centre line of the barrier run 6m
in from the start of the terminal section.
2. Centralise the Inner Anchor Shoe over this mark.
3. Drill through the Inner Anchor Shoe and fasten using the appropriate method as agreed
with the client prior to installation (see Drilling for Anchors section).
4. Lower a male Full Height Terminal over the Inner Anchor
Shoe so that the horizontal bars of the frame at the 6m
joint are located inside the Inner Anchor Shoe frame. DO
NOT LOCK THE BARRIER TO THE INNER ANCHOR
SHOE AT THIS TIME. Completely connect the initial
standard section to the terminal section first (see
Standard Sections Installation section).
5. Reach through the access hatch and place shims between the horizontal bars of the frame
and the Inner Anchor Shoe to take up any clearance.

Product & Installation Manual : BarrierGuard 800
Ph 0800 655 200 or visit www.csppacific.co.nz July 2013 / Page 18
6. Slide the Horizontal Locking Pin through the holes in the
Inner Anchor Shoe, secure with retaining clips and
replace the cover over the access hatch.
7. Remove the 8 No. bolts (3 along each side and 2 on the
end) from the end cap section of the barrier and lift off the
terminal cover (approx 30kgs).
8. Drill through the Anchor Plate and fasten using the appropriate method as agreed with
the client prior to installation (see Drilling for Anchors section). Replace and secure
cover.
The anchorage at the departure end of the run uses a
similar method to the approach end but with a female Full
Height Terminal. The Inner Anchor Shoe position can
either be determined by measuring 6 metres from the end
of the outer skin of the last section of barrier already
installed, or by temporarily placing the Full Height Terminal
section in position and marking the joint line. For External
Anchor Shoe applications, fixing is done with the terminal
in place as with the approach end.
Ramped End Terminal Installation
CAUTION: THE USE OF A RAMPED END TERMINAL AT ANY EXPOSED LOCATION MUST
ONLY BE USED IN SPEED LIMIT ZONES WITH A POSTED SPEED 50 KM/H OR LESS
This is an identical operation to the Full Height Terminal Installation except the anchored
end terminates in a ramp down to ground level as opposed to at full height. Follow the same
procedure as for the Full Height Terminal Installation up to and including point number 6, then:
1. Remove the cover at the terminal end of the Full Height Terminal, drill through the Anchor
Plate and fasten using the appropriate method as agreed with the client prior to installation
(see Drilling for Anchors section). Replace cover.
2. Drill through the Anchor Plate and fasten using the appropriate method as agreed with the
client prior to installation (see Drilling for Anchors section). Replace cover.
The anchorage at the departure end of the run uses a similar method to the approach end but
with a female ramped terminal end. The Inner Anchor Shoe position can either be determined
by measuring 6 metres from the end of the outer skin of the last section of barrier already
installed, or by temporarily placing the end terminal section in position and marking the joint
line. For External Anchor Shoe applications, fixing is done with the terminal in place as with the
approach end.

Product & Installation Manual : BarrierGuard 800
Ph 0800 655 200 or visit www.csppacific.co.nz July 2013 / Page 19
Standard Section Installation
All sections must be physically bolted together through the top
QuickLink plates using the double lock assembly shown in
these photographs. These assemblies are pre-installed on the
BarrierGuard 800 and the connected sections are simply
bolted together by attaching the nut into the magnetic socket of
the “T” Bar, lowering it through the hole located in the roof of
the BarrierGuard 800 and placing it over the bolt thread. The
“T” Bar can then be used to tighten the connection.
At the beginning and end of each run of barrier each terminal
section and the adjacent standard length of BarrierGuard 800
must also be bolted through the bottom QuickLink plate with an
additional lock assembly. This applies to both the approach and
departure end. This procedure is performed in the following
way.
If using the External Anchor Shoe. – After placing the terminal
section on the ground the next operation is to connect the next section of BarrierGuard
800 to it using the QuickLink and then secure the upper QuickLink plates as described
above.
These two sections are then lifted sufficiently so that wooden
blocks no less than 200mm x 200mm in section and spanning the
full width of the BarrierGuard 800 can be placed either side of the
joint, and the BarrierGuard 800 lowered onto the blocks.
The lower QuickLink plates are then secured by placing nut over
the preinstalled nyloc nut and bolt assembly and tightening it. The
BarrierGuard 800 can then be lifted, the wooden blocks removed
and the barrier then placed on to the ground.
Once this procedure has been carried out and the BarrierGuard 800 is placed in the correct
position on the ground, the drilling of the anchor holes can be carried out (see Full Height
Terminal Installation section)
If using the Inner Anchor Shoe – Carry out the procedures described above to secure both the
upper and lower QuickLink plates of the QuickLink joint between the terminal section and the
next standard section. After completing the above procedures lower the BarrierGuard 800
back onto the Inner anchor shoe and then anchor with the Horizontal Locking Pin (see Inner
Anchor Shoe Applications section). This procedure must be carried out before the end
of the terminal is fixed to the surface, before the External anchor is fixed or before the
terminal section is locked to the Inner Anchor Shoe.

Product & Installation Manual : BarrierGuard 800
Ph 0800 655 200 or visit www.csppacific.co.nz July 2013 / Page 20
For the departure end, the procedure is similar to that of the approach end. Install the
departure terminal in the usual fashion, but do not drill and fix the External Anchor, lock the
terminal to the Inner Anchor Shoe or fix the end of the terminal to the surface.
Once the system is connected and the top QuickLinks bolted together, lift the BarrierGuard
800 and place the two wooden blocks either side of the joint. Lower the BarrierGuard 800 onto
these blocks and connect the lower QuickLink plates as with the approach end. Once the
securing of the upper and lower plates of the QuickLink has been completed then either fix the
External Anchor to the ground or lock the terminal to the Inner Anchor Shoe and then fix the
end of the terminal as detailed in Ramped End Terminal Installation.
Intermediate Anchoring
Additional anchorage along the length of the installed BarrierGuard 800 may be specified. A
requirement of the NZTA BarrierGuard 800 acceptance is that the maximum spacing
between anchor points is 72m. This may be waived in special circumstances subject to an
application in writing to the National Manager Traffic & Safety.
It is recommended that continuous lengths of standard working width BarrierGuard 800 that
exceed 480m (i.e. 40 standard 12m sections) have an intermediate anchoring at intervals not
exceeding 480m.
There are 2 different types of intermediate anchors for use with
BarrierGuard 800 one that is connected at the QuickLink Joint and
the second which is attached to the barrier at the bolted joint.
To fit the Intermediate Anchor at the QuickLink joint, lower the
barrier to the ground with the male end supported on a block at least
300mm high. Bolt the anchor plate to the barrier using the two tubes
located inside the barrier on the lower QuickLink plate on the male
end.
Use M24 x 120 grade 8.8 bolts with nuts and a washer, the nuts and washers must be located
inside the barrier. The bolts should be tightened to a torque of approximately 90Nm, i.e.
normal spanner tight.
Table of contents
Popular Security Sensor manuals by other brands
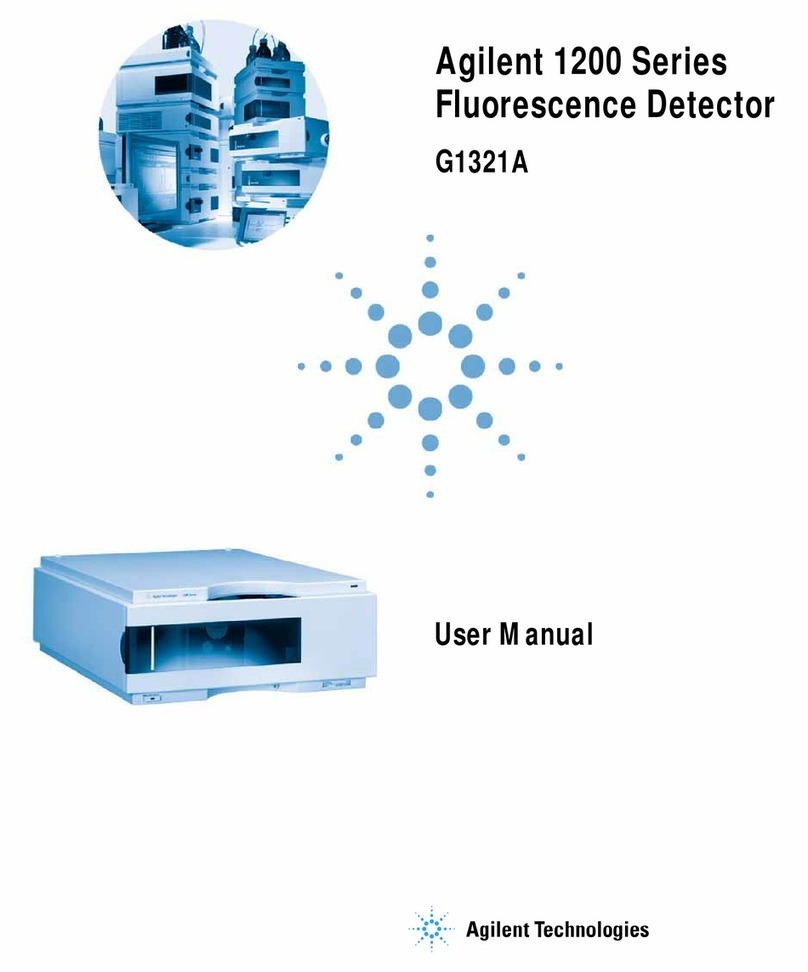
Agilent Technologies
Agilent Technologies 1200 series user manual
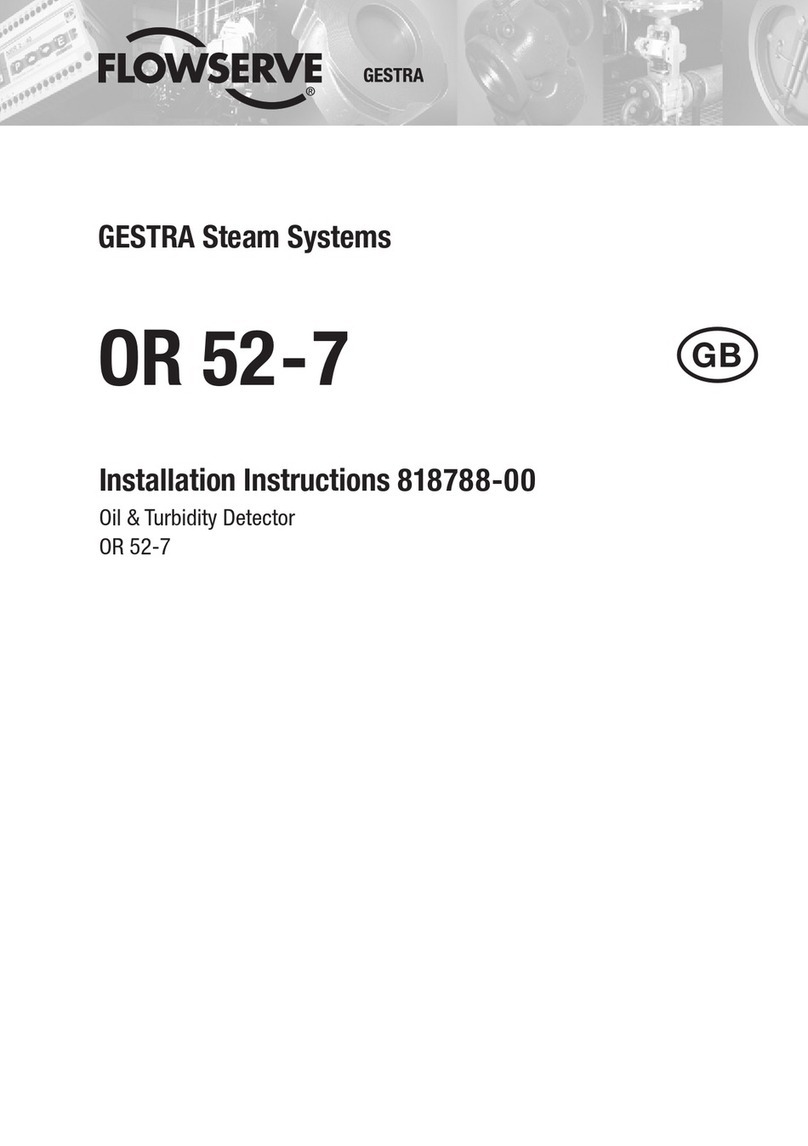
Flowserve
Flowserve GESTRA OR 52-7 installation instructions
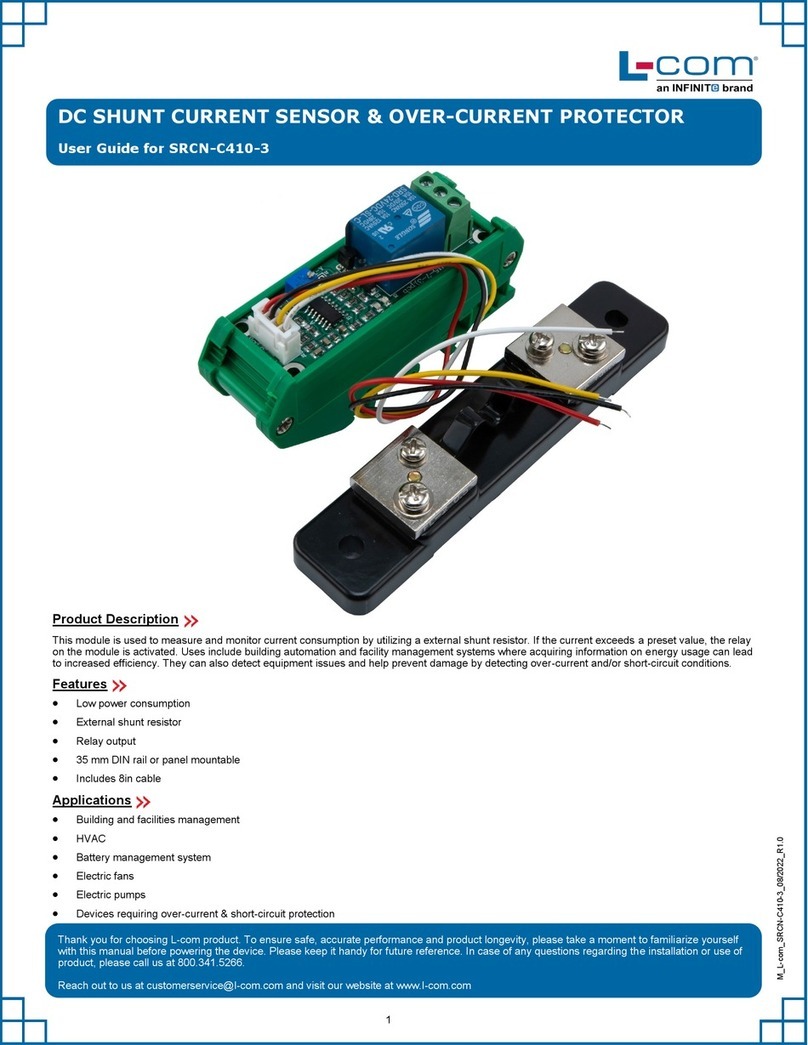
Infinite
Infinite L-com SRCN-C410-3 user guide

Gardigo
Gardigo 60035 operating instructions

Honeywell
Honeywell 14506873-001 installation instructions

iSysmart
iSysmart SGZB11C user manual