Datsun 510 series Instruction manual




















Other manuals for 510 series
2
This manual suits for next models
2
Other Datsun Automobile manuals

Datsun
Datsun 411 Series User manual
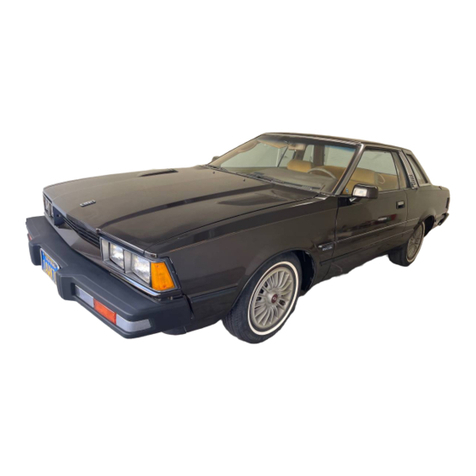
Datsun
Datsun 1981 200SX User manual
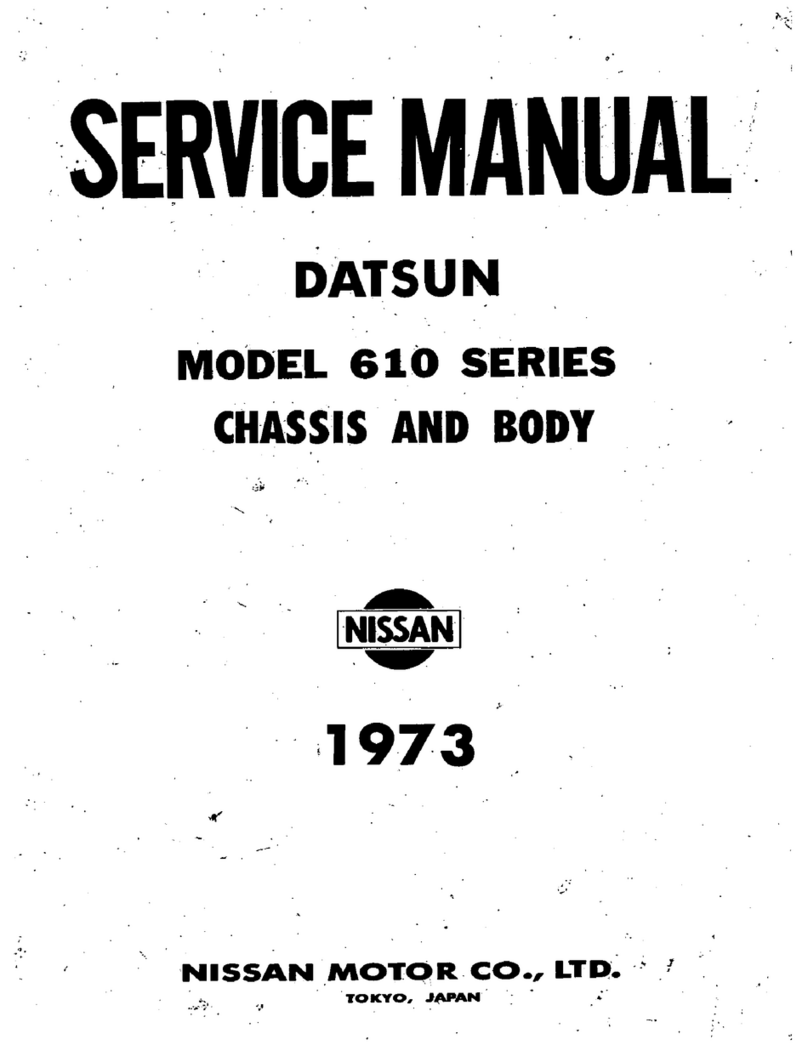
Datsun
Datsun 610 Series 1973 User manual
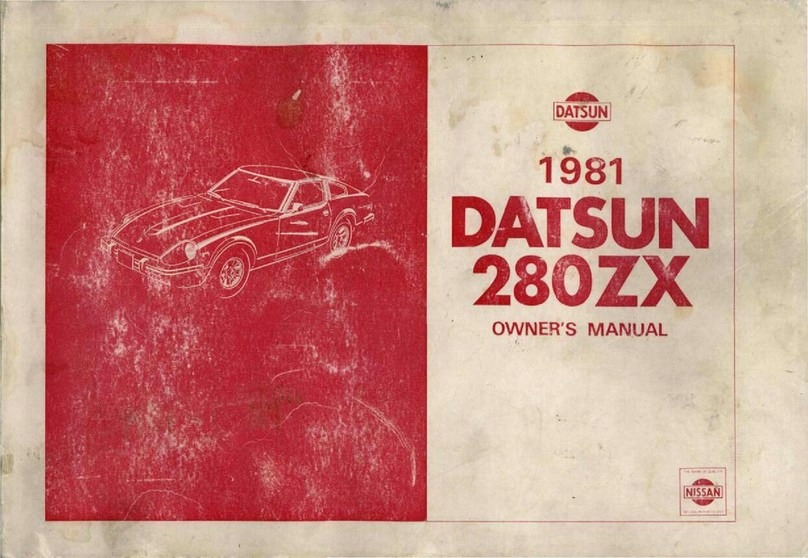
Datsun
Datsun 280ZX 1981 User manual
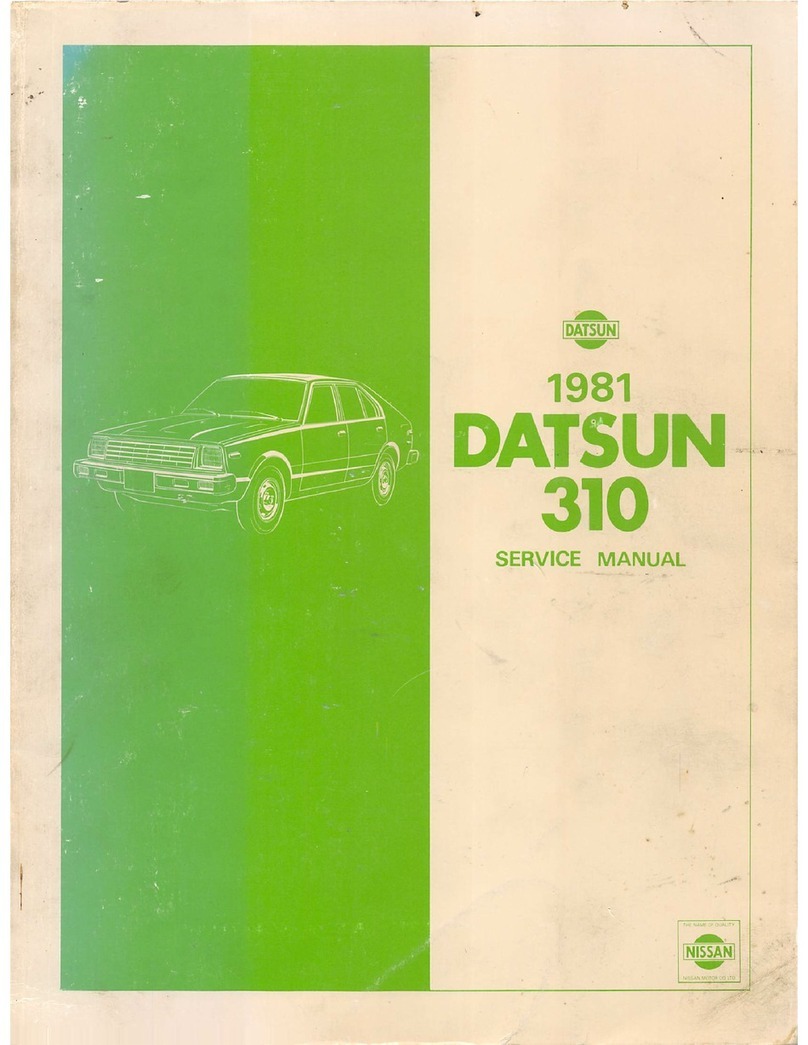
Datsun
Datsun 1981 310 User manual
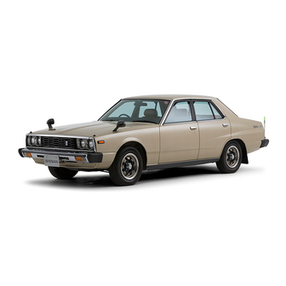
Datsun
Datsun C210 series User manual
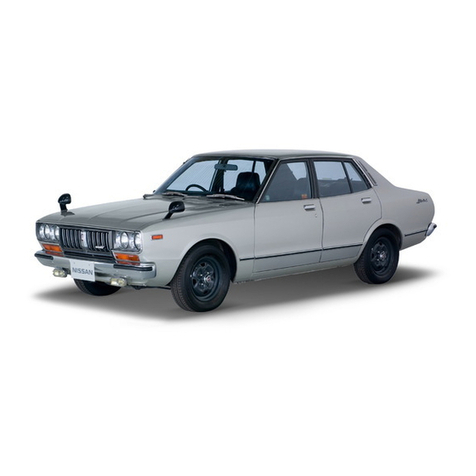
Datsun
Datsun Bluebird 180 B User manual

Datsun
Datsun 1980 200SX User manual
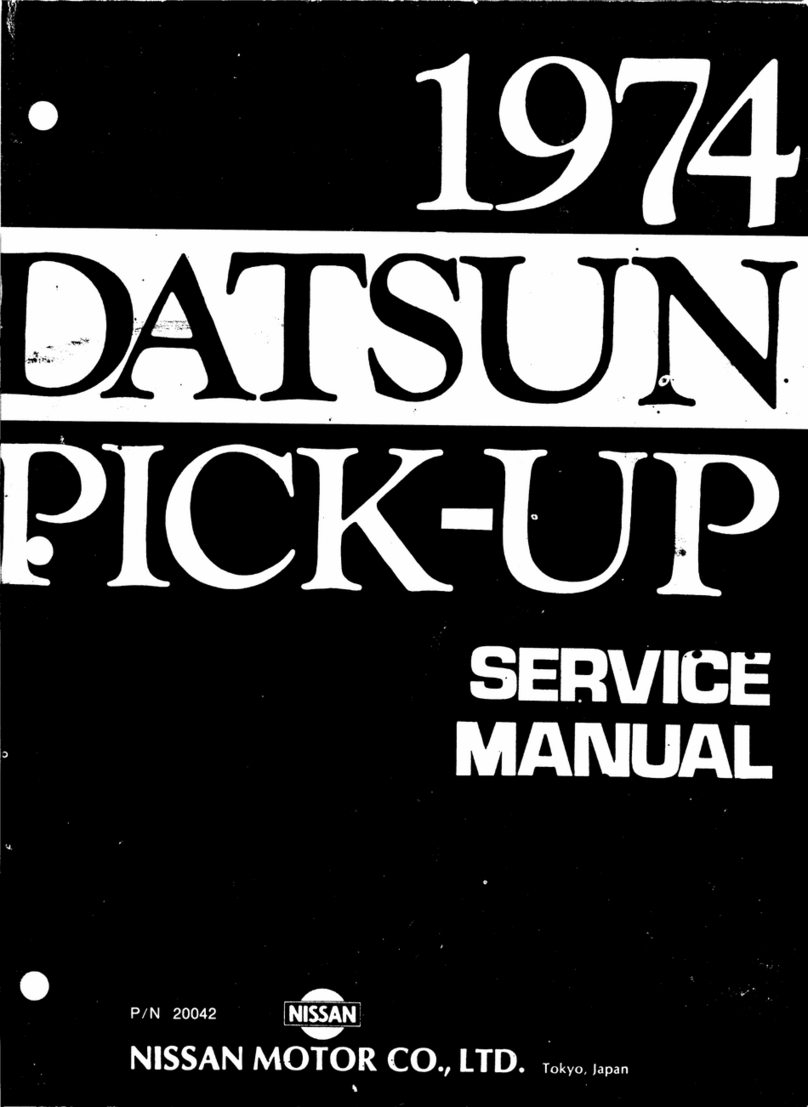
Datsun
Datsun Pick-Up 1974 User manual
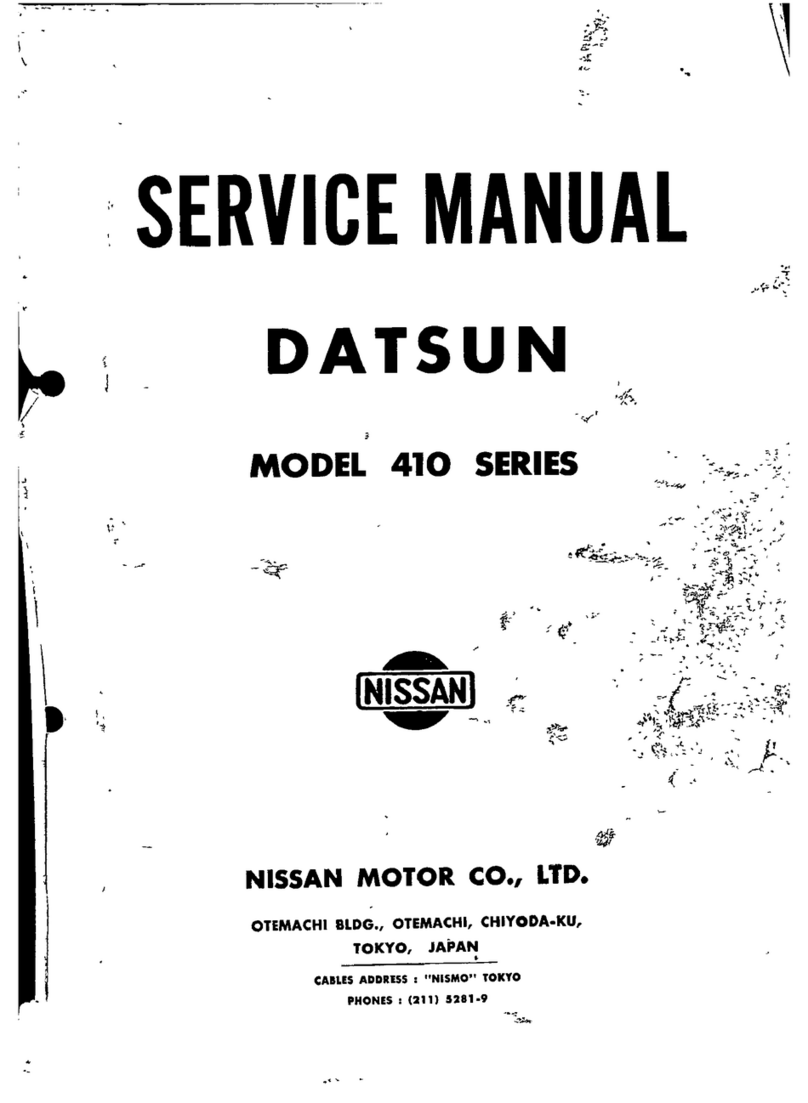
Datsun
Datsun BLUEBlRD L 410 Series User manual
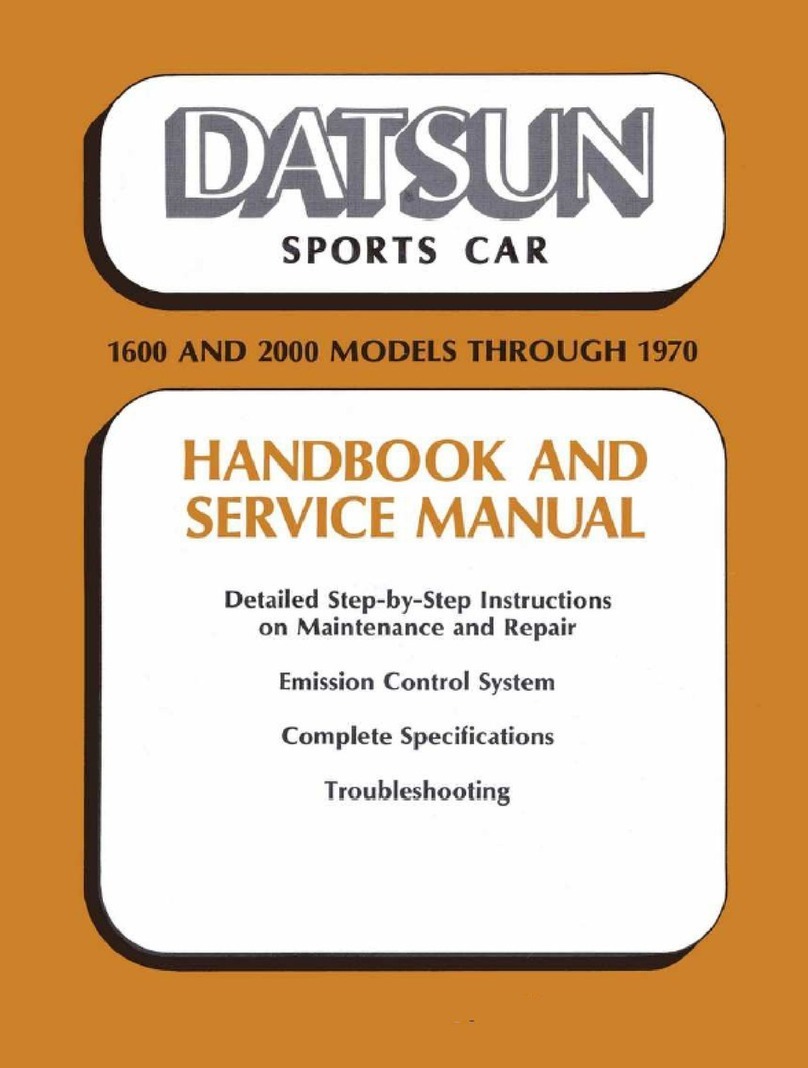
Datsun
Datsun SPL311-U User manual

Datsun
Datsun 1968-1973 510 Instruction manual

Datsun
Datsun 1000 Instruction manual
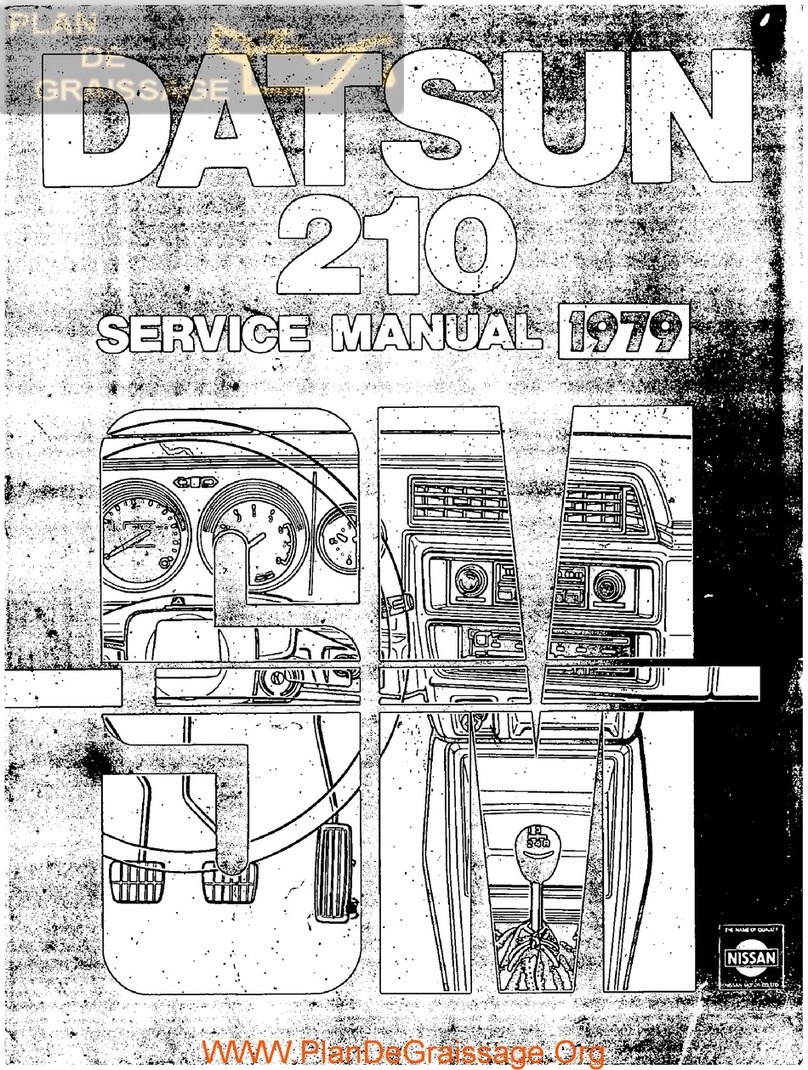
Datsun
Datsun 210 1979 User manual
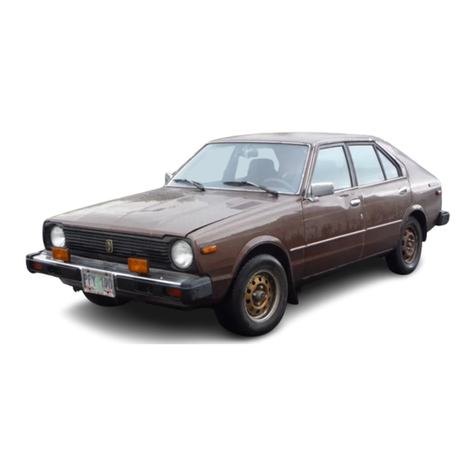
Datsun
Datsun 1980 310 User manual
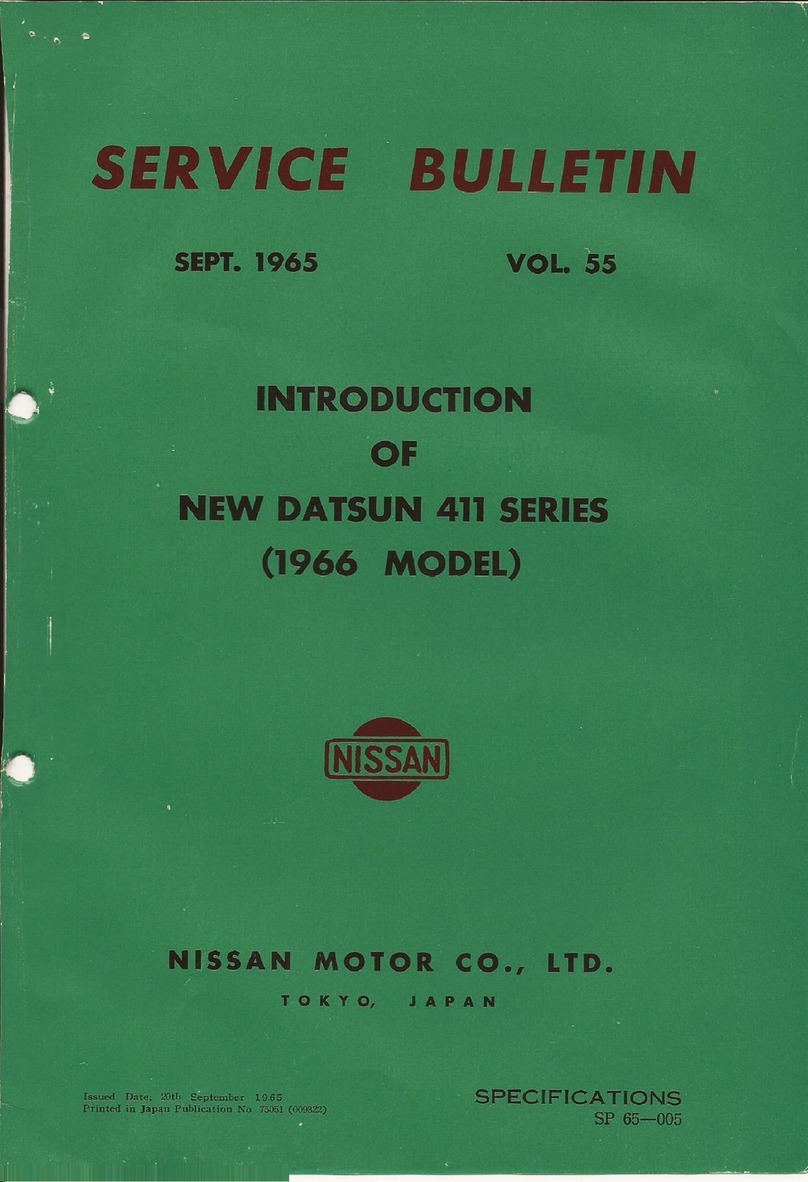
Datsun
Datsun 411 Series 1966 Reference manual
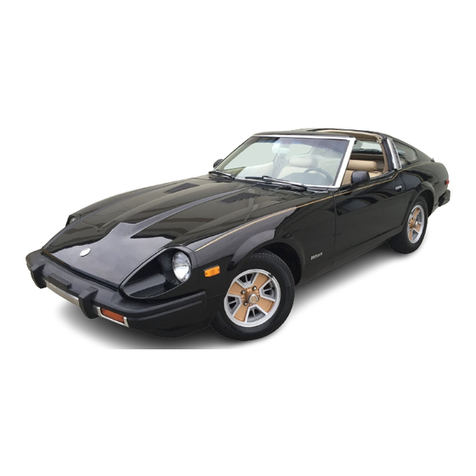
Datsun
Datsun 280ZX 1980 User manual

Datsun
Datsun 200SX User manual
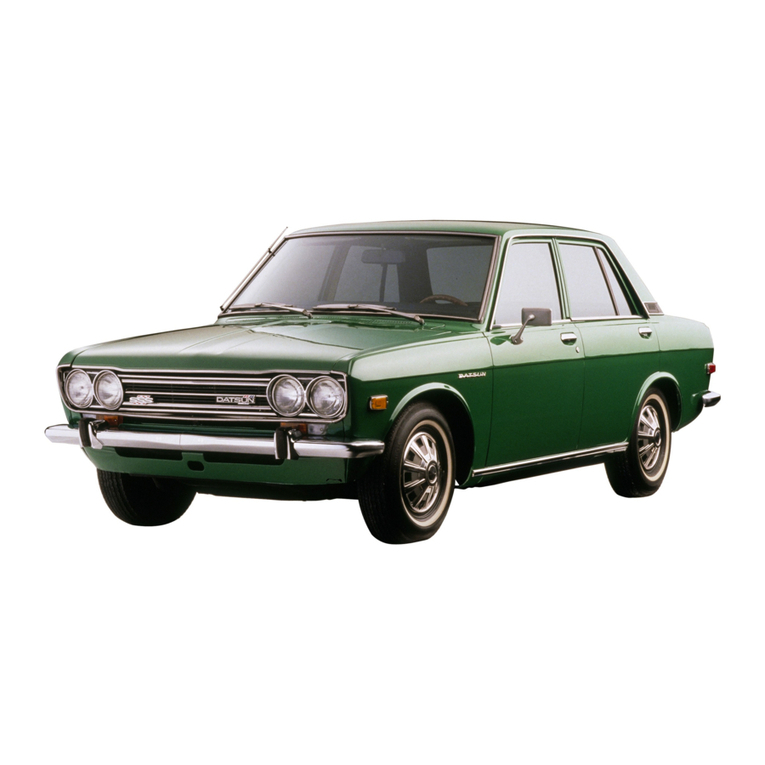
Datsun
Datsun 510 series Instruction manual
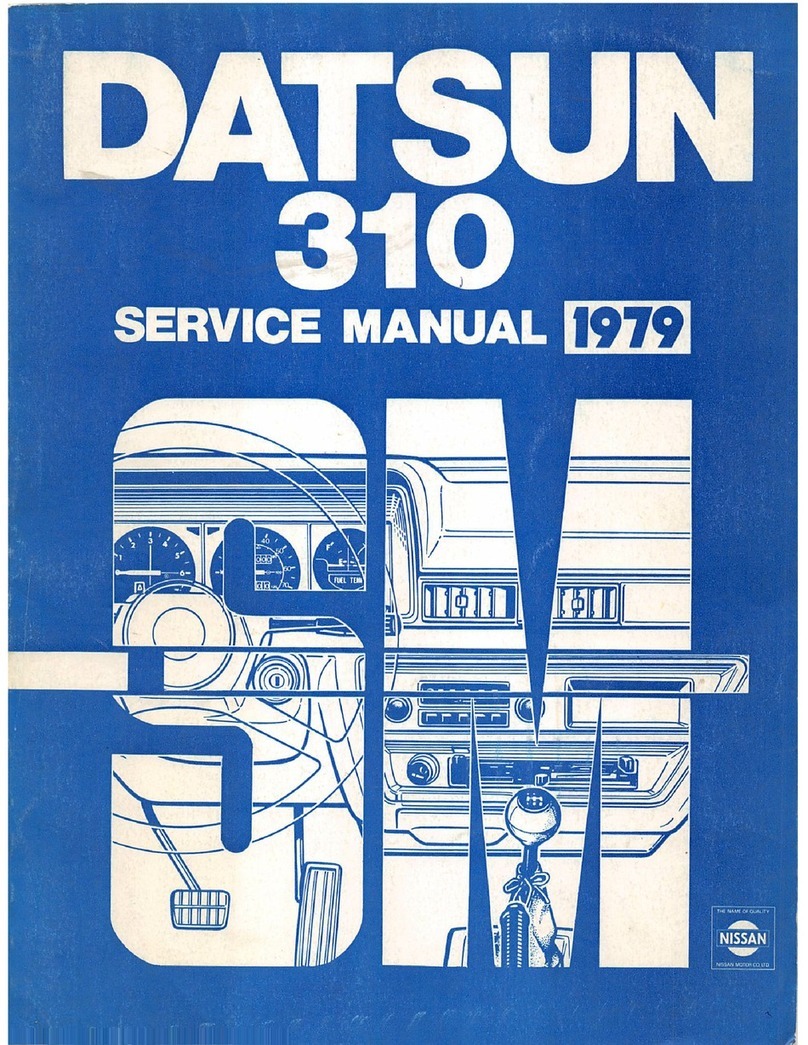
Datsun
Datsun 310 N10 Series 1979 User manual