ENDEVCO 4418 User manual

DOCUMENT EDVIM4418 REVISION B Page 1 of 14
Instruction Manual
4418 Bridge Signal Conditioner

DOCUMENT EDVIM4418 REVISION B Page 2 of 14
SAFETY CONSIDERATIONS
This equipment has been designed and tested in accordance with the following standards:
EN61326-1:2013 Electrical equipment for measurement, control and laboratory use – Group1, Class
B (Emissions)
EN61326-1:2013 Electrical equipment for measurement, control and laboratory use – Industrial
Environment (Immunity)
CFR 47, Class A Code of Federal Regulations: Pt 15, Subpart B
The 4418 has been tested as an Unintentional radiator (sub part B) and as a Class A product.
RADIO AND TELEVISION INTERFERENCE
NOTE: This equipment has been tested and found to comply with the limits for a Class A digital device, pursuant to
Part 15 of the FCC rules. These limits are designed to provide reasonable protection against harmful interference
when the equipment is operated in a commercial environment. This equipment generates radio frequency energy and,
if not installed and used in accordance with the instruction manual, may cause harmful interference to radio
communications.
Operation of this equipment in a residential area is likely to cause harmful interference in which case the user will be
required to correct the interference at his own expense.
In order to maintain compliance with FCC regulations, shielded cables must be used with this equipment.
Operation with non-approved equipment or unshielded cables is likely to result in interference to radio & television
reception.
This equipment is not designed to be used in potentially explosive environments. It should not be used in the presence
of flammable liquids or gases.
This manual contains information and warnings that must be followed to ensure safety of personnel and the safe
operation of the equipment.
Warnings:
Switch off all power to equipment before making or breaking a connection. Failure to do so may cause damage to the
equipment.
Any adjustment, maintenance or repair, other than detailed within this manual, must be carried out by trained service
personnel.
If it is suspected that the correct operation of the equipment is threatened, impaired or otherwise, it must be made safe
and free from further operation until the threat has been removed.
Rohs Compliant 2015/863/EU
Waste Electronic and Electronic Equipment Directive: 2012/19/EU
This product complies with the WEEE Directive (2012/19/EU) marking requirement. The affixed product label (below)
indicates that you must not dispose this electrical/electronic product in domestic household waste.
To return unwanted product for disposal, please contact your local MSS Representative.
Li-ion

DOCUMENT EDVIM4418 REVISION B Page 3 of 14
Table of Contents
Page
1. Product Description 4
2. Detailed Description 4
2.1 Input
2.1.1 Connection 4
2.1.2 Status 4
2.2 Output
2.2.1 Connection 4
2.2.2 Gain 5
2.2.3 Filter 5
2.3 Power
2.3.1 Turn On 5
2.3.2 Low Battery Indicator 5
2.3.3 Battery Charge Indicator 5
3. Operation
3.1 Transducer Connection 6
3.2 Output Connection 6
3.3 Gain Setting 6
3.4 Filter Selection 6
3.5 ZMO Adjustment 7
3.6 Battery Charging 7
4. Maintenance, Calibration and Repair
4.1
4.1.1 Equipment Required 8
4.1.2 Preliminary Instructions 8
4.1.3 Check Procedure 9
4.2 Repair 9
4.3 Battery Replacement 9
5 Frequency Response Curves
Gain = 1 11
Gain = 10 12
Gain = 100 13
LP Filter Response Curves 14
6 Performance Specification 15

DOCUMENT EDVIM4418 REVISION B Page 4 of 14
1. Product Description
The Model 4418 Bridge Signal Conditioner is a portable/desk top low-noise Signal Conditioner for use with
Bridge and Variable Capacitance type transducers. The unit provides the excitation supply to the
transducer, signal amplification and filtering. Signal amplification (gain) is selectable as x1, x10 or x100
and the fixed frequency cut-off filter is selectable as IN or OUT. The unit is powered from an internal
Lithium Ion (Li-ion) battery that can be recharged using the supplied charger. LED indicators are used to
show the status of the battery, gain range selected, filter in, input status and battery charge.
Fig 1. Back Panel
2. Detailed Description
2.1 Input
2.1.1 Connection
The 4418 supports Piezo-Resistive (PR) transducers having a full bridge architecture and variable
capacitance (VC) types having a differential output. Input is via a Binder 5 pin miniature circular
connector located on the front panel. Power to the transducer is available at the input socket in the
form of a 10 VDC Excitation voltage. Bridge balance or Zero Measure and Output (ZMO)
adjustment is provided by means of a control (Offset) mounted on the rear panel. Note: No internal
provision is made for bridge completion resistors. If a half-bridge transducer is to be used,
bridge completion resistors must be added externally.
2.1.2 Status
An indicator on the front panel shows the status of the input – if a transducer is connected
and functioning correctly the indicator will be lit “green”. If a fault condition exists, the indicator
will be lit “Red”. A fault condition exists when either the input is open circuit, i.e. no
transducer connected, or if the input is short circuit, i.e. a cable fault. Note: During turn on, both
green and red conditions are cycled before the steady state is reached.
2.2 Output
2.2.1 Connection
The output connector is a standard BNC located on the front panel with one side connected to
signal ground. The case of the unit is also connected to signal ground. If a connection to
earth is required it should be made through the output connector and associated
instrumentation.
2.2.2 Gain
Three levels of amplification (gain) are provided and selectable on the front panel.
The selected gain level is shown by the associated indicator.

DOCUMENT EDVIM4418 REVISION B Page 5 of 14
2.2.3 Filter
A low pass filter is provided in the form of a second order Butterworth. The typical response
curves of the filter are shown on page 14. With the filter indicator lit, the filter is selected IN.
2.3 Power
Power for the Conditioner comes from an internal Li-ion cell pack, and a supplied external universal
power adapter. The power adapter functions as a charger for the internal battery, but also will power
the Conditioner. Battery charge and discharge are managed by internal circuitry to provide a safe
and effective environment for the battery to operate. It is recommended that the charger be
disconnected once charging has stopped to maximize battery life. Warning! Only use the power
adapter supplied with the 4418 for charging otherwise internal damage may occur!
Fig 2. Front Panel
2.3.1 Turn On.
The conditioner is turned on and off by a switch on the rear panel. To turn on, press “1”.To turn off,
press “0”. When turned on, the Conditioner will cycle through the front panel indicators lighting the
gain indicators in turn and the filter indicator.
2.3.2 Low Battery Indicator
The battery Low indicator is on the front panel and will be lit “Red” when the battery reaches a
pre-determined discharge level. At this point it is recommended that the charger be connected.
If the charger is not connected at this point the unit will continue to function until a second
predetermined battery discharge level is reached. At this point all power is turned off and no
further operation is possible until the battery is recharged.
2.3.3 Battery Charge Indicator
The battery charge indicator is mounted above the charger socket on the rear panel. Whilst
charging is in progress the indicator will be lit “green”. When charging is complete the
indicator is extinguished.
3. Operation
It is recommended that the 4418 be placed on charge before using for the first time.
Note: Ensure the Conditioner is turned off before making any connecting to the 4418.
Once connections have been made, the unit can be turned on with the switch located on the rear
panel. The unit will then cycle the front panel gain and filter indicators to verify that they are working.
It is recommended that the unit be turned on at least 5 minutes before taking measurements to
allow for the internal circuits to stabilize.

DOCUMENT EDVIM4418 REVISION B Page 6 of 14
3.1 Transducer Connection
The transducer is connected to the 5 pin input socket. A high accuracy voltage reference source
provides power to the transducer. When powered, the transducer will set a voltage at the inputs of
the 4418 of approximately 5VDC (dependent on the transducer and the offset). The 4418 monitors
this voltage to be within a pre-set range. If the voltage is within the range the status indicator is
turned Green and the system is ready to use. If the voltage is out of range, the status indicator is
turned Red – a fault condition exists. Note: Some transducers can take 1 – 2 minutes before
the voltage settles into range.
Fig 3.
Pin Connections - as viewed from the front of the 4418 or the rear (wire side) of the mating input plug.
3.2 Output Connection
Measuring Instrumentation, e.g. data acquisition, data logger etc. should be connected to the output
socket using coaxial cables. Load impedance should be no lower than 100kΩto meet all
specifications. Ideally, the 4418 should be placed near the measuring instrumentation to minimize
the effect of cable capacitance loading.
3.3 Gain Setting
Depressing the “Gain” switch cycles through the gain ranges of x1, x10 and x100. The gain range
selected is shown by the indicator above the range being lit. The gain together with the transducer
sensitivity determines the acceleration range available from the system and the output sensitivity,
e.g. for an accelerometer having a sensitivity of 10mV/g pk, and the maximum output of the 4418
being 10V pk:
Gain = 1 Range = 1000g Output sensitivity = 10mV/g
Gain = 10 Range = 100g Output sensitivity = 100mV/g
Gain = 100 Range = 10g Output sensitivity = 1000mV/g
3.4 Filter Selection
A second order low pass filter is selected by depressing the filter switch. This toggles the filter in
and out. With the indicator lit, the filter is selected IN. The Standard filter provides attenuation of
-3dB at 10 kHz. The filter maybe used to reduce the effects of HF noise and aliasing in data
acquisition systems.
3.5 The Bridge Balance (Offset)
The control, located on the rear panel, provides a means of adjusting the unbalanced output of the
transducer for a zero measured output of the signal conditioner. To adjust the Bridge Balance, first
place the transducer in an axis which is not the primary sensitive axis, i.e. at 90 degrees. Monitor
the output of the signal conditioner with a dc voltmeter. With the power turned ON and after the
recommended stabilization time, adjust the control for as close to zero volts as possible at the
output.
The 4418 utilizes low drift components in the design. However, small changes may be required after
the initial setting. When using the x100 gain, the adjustment of the control is very sensitive. It is,
Pin 1 – Excitation -ve (Black)
Pin 2 – Signal -ve (White)
Pin 3 – Cable Shield*
Pin 4 – Signal +ve (Green)
Pin 5 – Excitation +ve (Red)
*Pin 3 is connected to output signal ground.

DOCUMENT EDVIM4418 REVISION B Page 7 of 14
therefore, recommended that the zero measured offset be adjusted first on the x1 and/or x10 to set
the control in the right region.
3.6 Battery Charging
Ensure that both the Charger and Conditioner are turned OFF before connecting. Plug the Charger
connector into the socket on the rear panel of the Conditioner. Turn on the charger. Charging is
accomplished in two stages:
Stage 1 – Fast Charge Mode.
“Fast Charge Mode”, covers both constant current and constant voltage modes and charges the
battery to approximately 85% of its capacity in approximately 2 hours. Once 85% capacity has
been achieved, the charging will automatically switch into “Stage 2”.
Stage 2 – Top Off Mode.
“Top Off Mode” will deliver sufficient charge to top up the battery to 100% of its capacity in
approximately 45 minutes.
Once 100% capacity has been achieved the charge indicator will extinguish. In the event of a fault
with the battery charging circuit, or the battery pack itself, the charge indicator will be lit “Red”. In
this event, please contact your local representative to arrange for the repair of the Conditioner.
The charging times are approximate and will vary depending on initial battery charge state and
temperature. If the Conditioner is turned on whilst being charged, the power from the charger will
be shared between operation and charging with the priority given to operation.
Note: To conserve battery life, it is recommended that once the battery is fully charged, the
charger is disconnected.

DOCUMENT EDVIM4418 REVISION B Page 8 of 14
Fig 4. Simplified Block Diagram
4. Maintenance, Calibration and Repair
4.1 If the unit is suspected of not working or malfunctioning it can be checked by use of the following
circuit. This circuit should also be used when performing a calibration of the unit. Note: To verify
the LF response of the signal conditioner it will be necessary to increase the value of the capacitor.
Fig 5. Test Circuit
4.1.1 Equipment Required:
Signal Generator (AC +DC)
DMM
Oscilloscope
5
2
3
4
1

DOCUMENT EDVIM4418 REVISION B Page 9 of 14
4.1.2 Preliminary Instructions
Ensure the battery is fully charged.
Connect the circuit above to the input of the 4418.
Set the signal generator (AC) for 70.7 mVpk (50 mV rms) at a frequency of 100Hz.
Turn on the 4418 and select a gain of x1. Allow 5 minutes to stabilize.
4.1.3 Check Procedure
Connect the DMM and Oscilloscope to the output of the 4418.
Measure with the DMM a voltage of 50 mV rms and undistorted as shown on the oscilloscope.
Select a gain of x10.
Measure with the DMM a voltage of 500 mV rms and undistorted as shown on the oscilloscope.
Select a gain of x100.
Measure with the DMM a voltage of 5000 mV rms and undistorted as shown on the oscilloscope.
To verify the output noise, replace the signal generator with a short circuit.
With the short circuit applied, set the DMM to DC volts and with a gain of x1 adjust the bridge
balance control. Verify the output of the 4418 varies between > -30mV to > +30mV.
To verify the DC performance, set the signal generator to DC volts and apply the same 50 mV dc
level
Note: With the generator set to 0V, adjust the bridge balance control for 0V at the output before
applying the DC signal.
There are no user adjustments internally. If any of the above conditions are not met, the unit
Should be considered faulty and in need of repair.
4.2 Repair
If in the event that the Conditioner requires repair, please contact your local Sales Representative
or distributor who will advise on the return’s procedure.
4.3 Battery Replacement
Battery life is > 300 cycles, which under typical operating conditions should exceed 3 years. Should
the battery need to be replaced please contact your local Sales Representative or distributor who
will advise on the return’s procedure.

DOCUMENT EDVIM4418 REVISION B Page 10 of 14
This page is Left intentionally blank

DOCUMENT EDVIM4418 REVISION B Page 11 of 14
TYPICAL FREQUENCY RESPONSE CURVES:

DOCUMENT EDVIM4418 REVISION B Page 12 of 14

DOCUMENT EDVIM4418 REVISION B Page 13 of 14

DOCUMENT EDVIM4418 REVISION B Page 14 of 14
Table of contents
Popular Network Hardware manuals by other brands
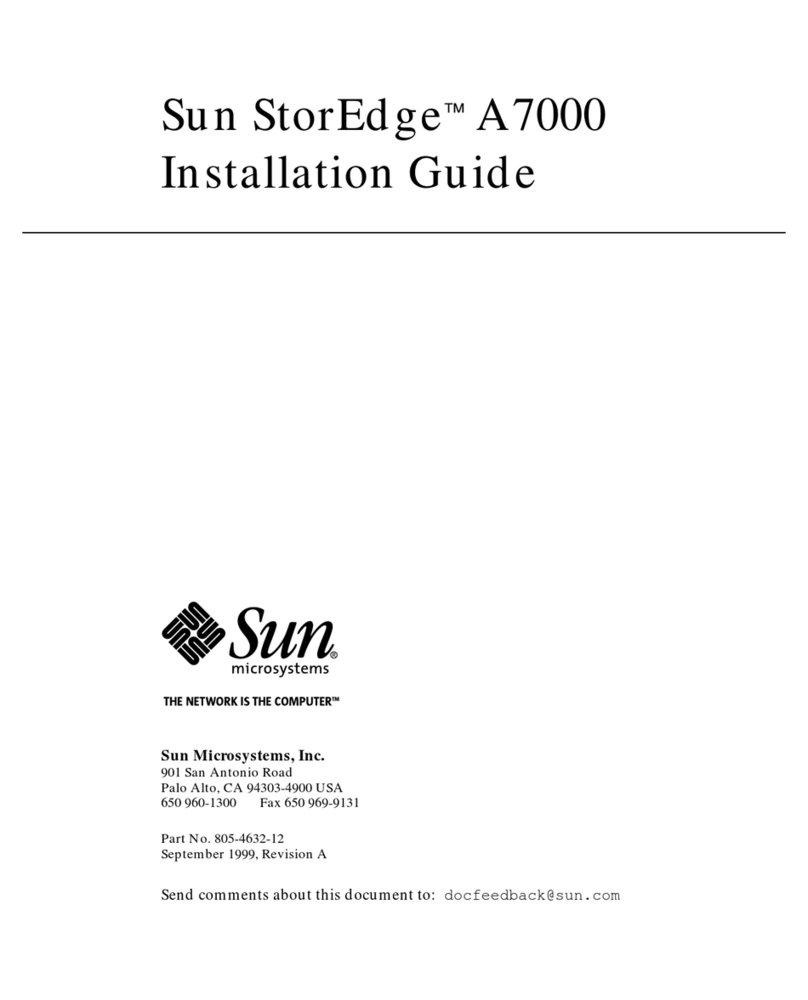
Sun Microsystems
Sun Microsystems Storedge A7000 installation guide

Lupus
Lupus LUPUSNET LE900 user manual
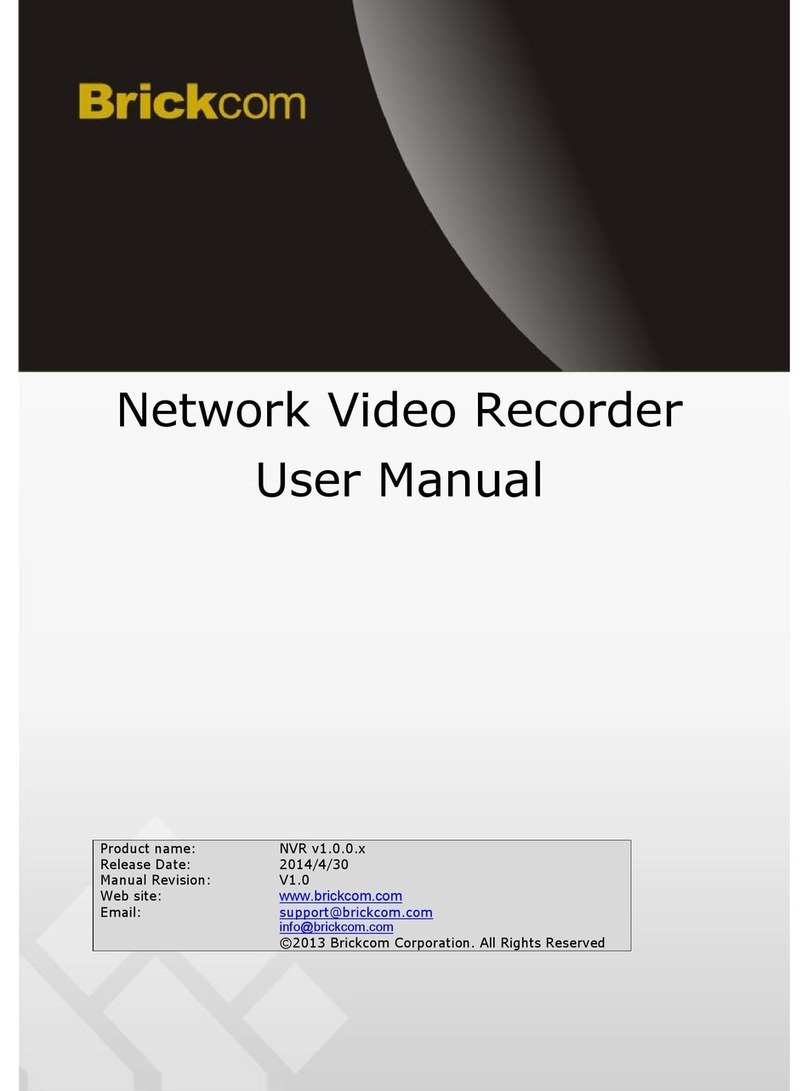
Brickcom
Brickcom NR-2104 user manual
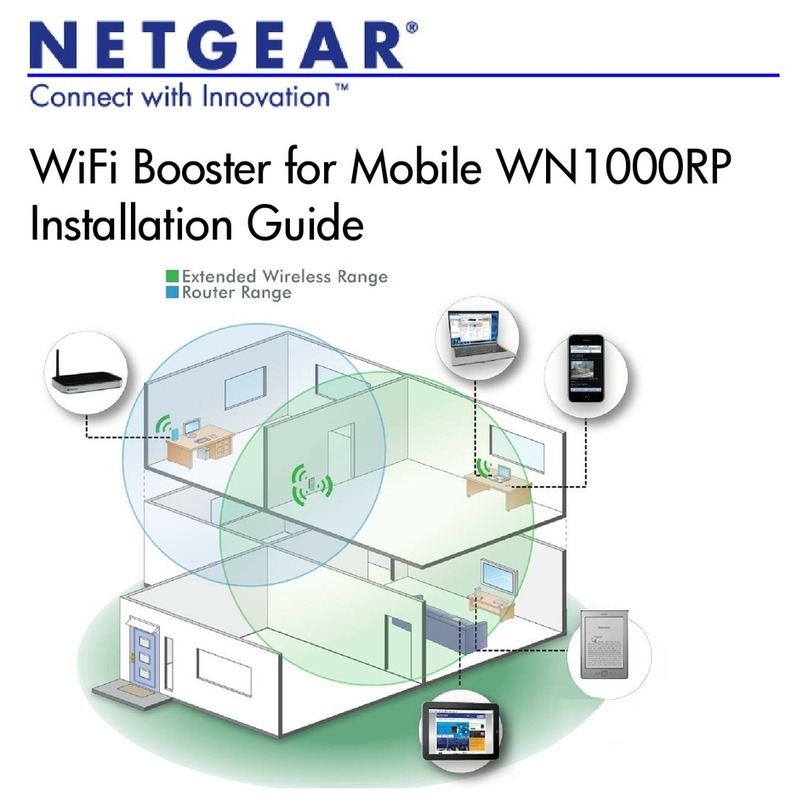
NETGEAR
NETGEAR WN1000RP installation guide

WatchNet
WatchNet ENM-04 POE Quick connection guide
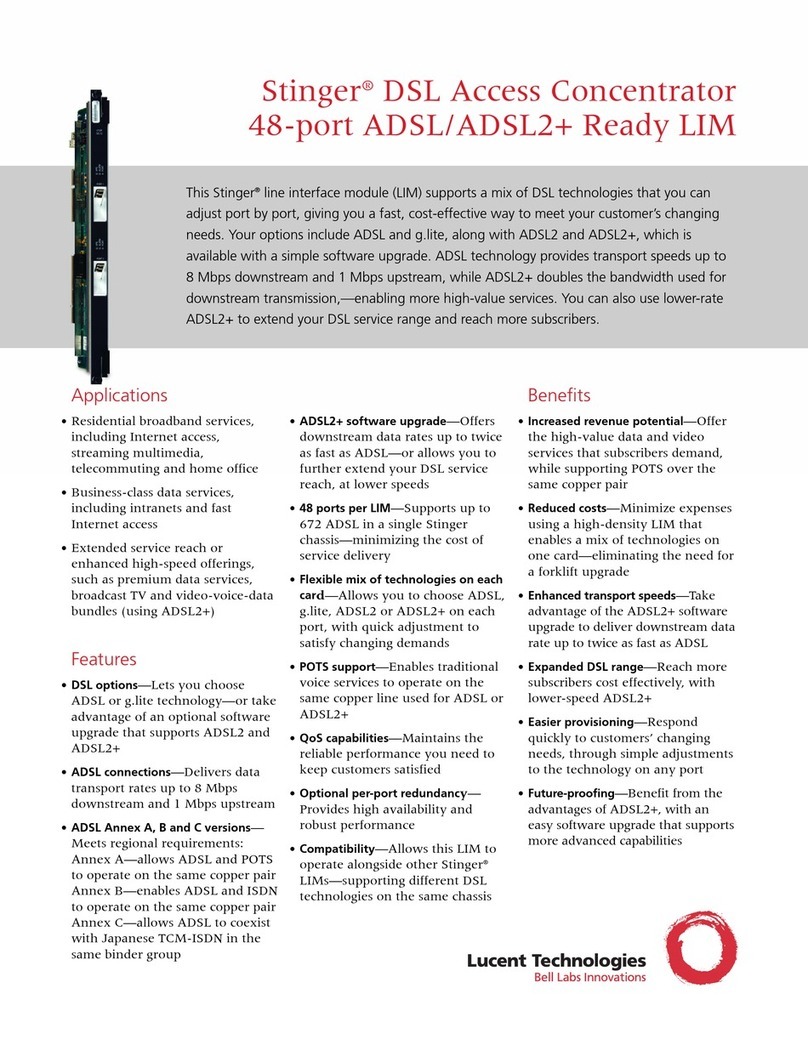
Lucent Technologies
Lucent Technologies Stinger STGR-LIM-AP-48 Specifications
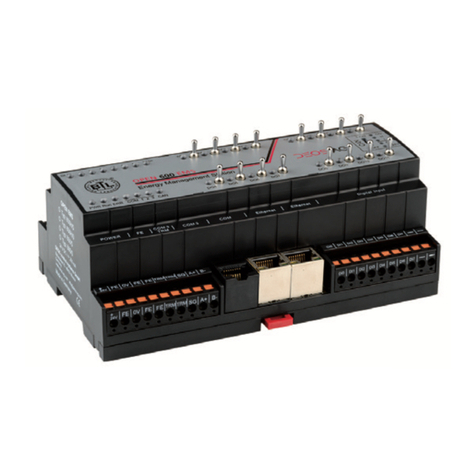
DEOS
DEOS OPEN 600 EMS datasheet
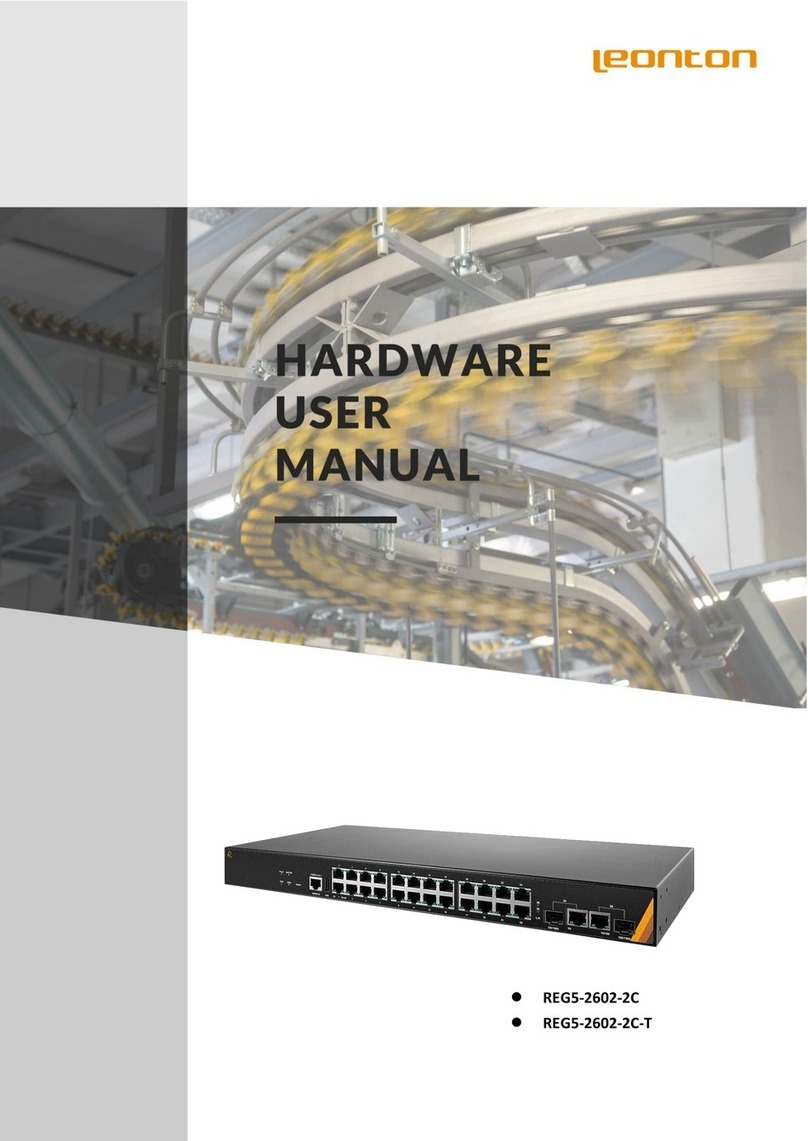
Leonton
Leonton REG5-2602-2C Series Hardware user manual
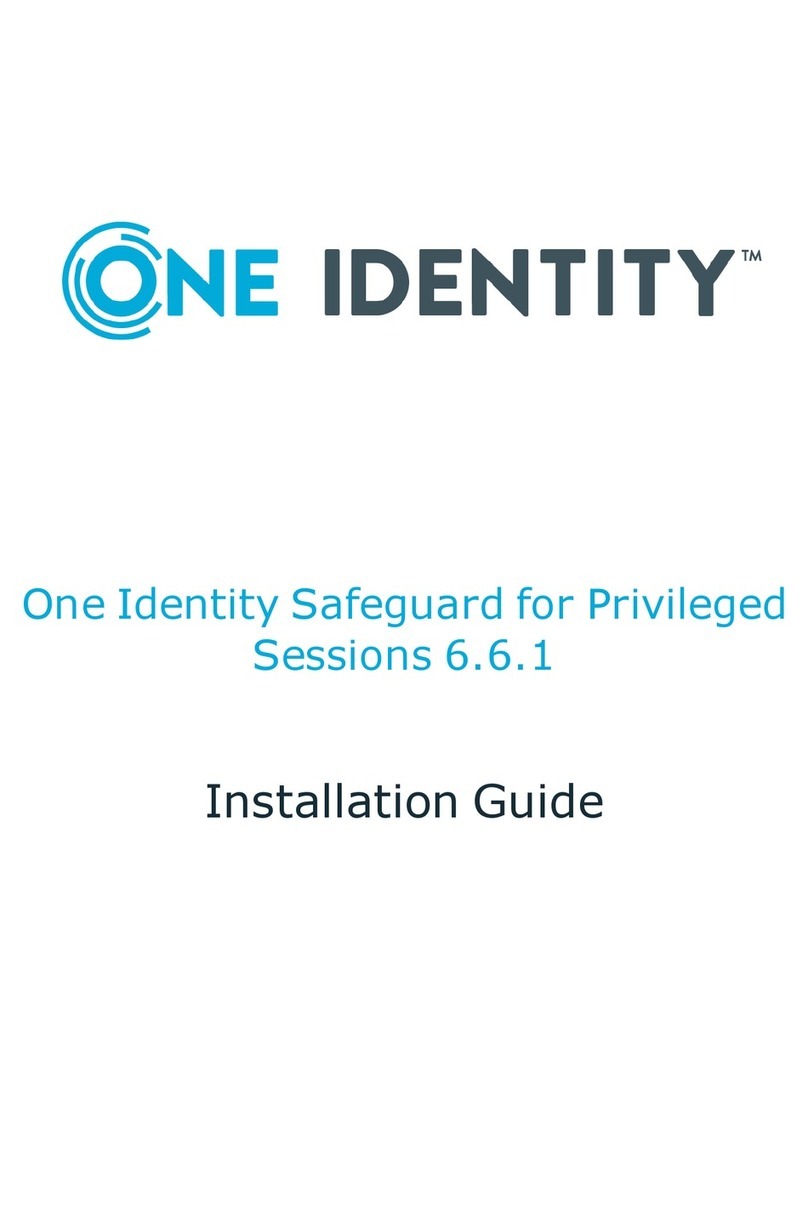
One Identity
One Identity Safeguard for Privileged Sessions T1 installation guide

CNB
CNB XNET IJB2000 instruction manual
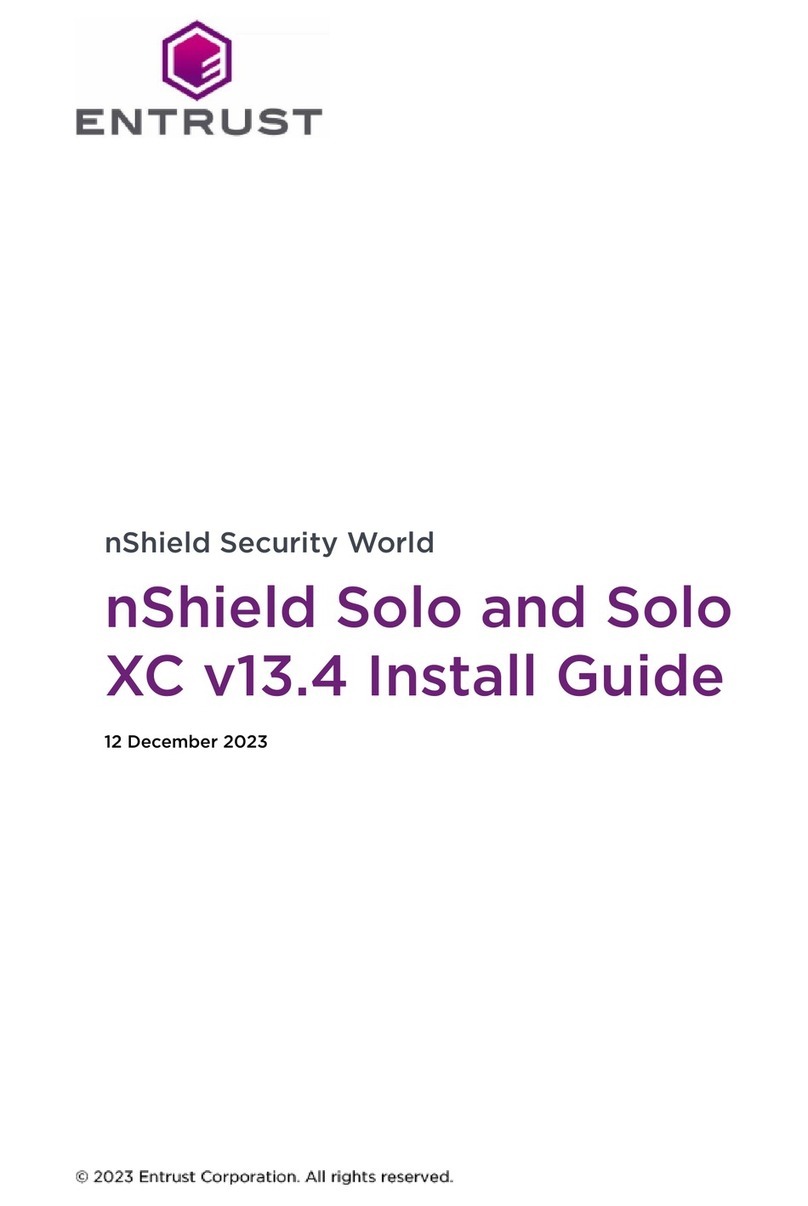
Entrust
Entrust nShield Solo install guide
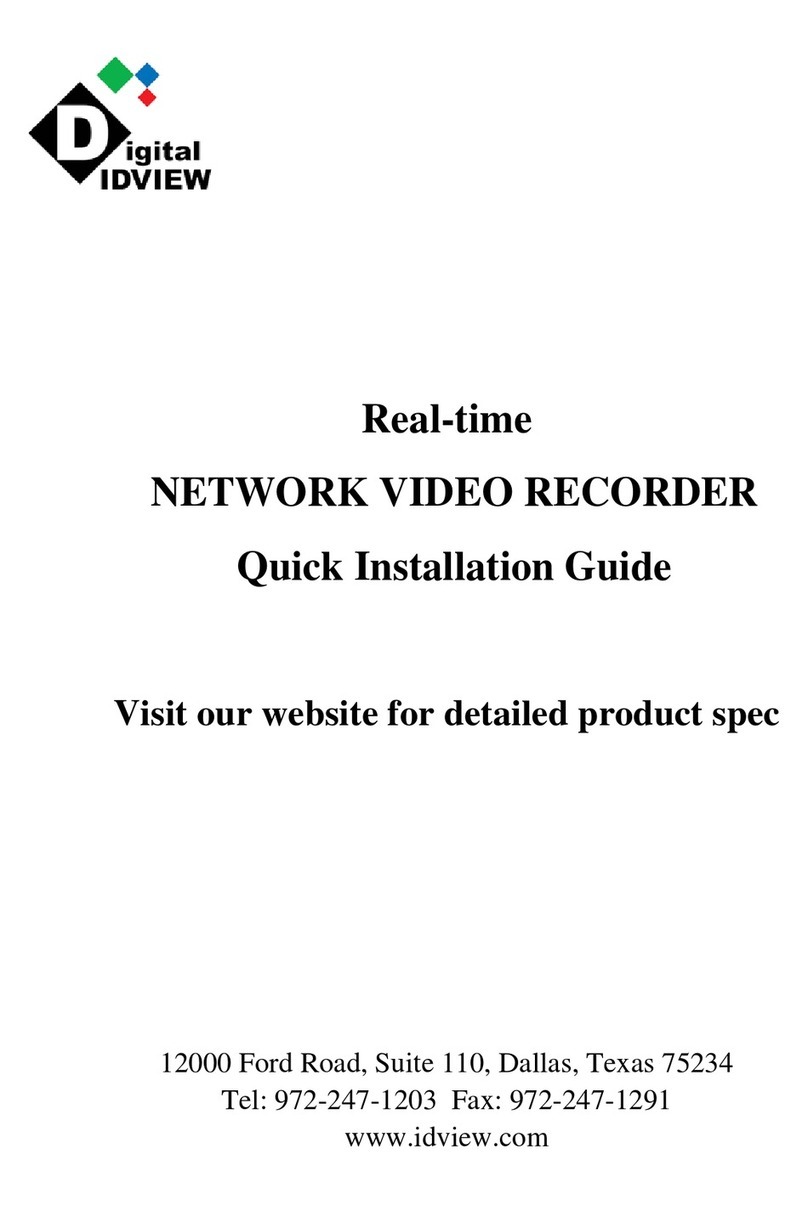
Idview Digital
Idview Digital 960H Quick installation guide