EVSE Viridian EV EPC20 Series User manual

Issue 1.2 May 2020 EVSE Protocol Controller 2.0 (EPC 2.0) | Viridian EV 1
EVSE Protocol Controller 2.0 (EPC 2.0)
hp://viridianev.co.uk
info@viridianev.co.uk

Issue 1.2 May 2020 EVSE Protocol Controller 2.0 (EPC 2.0) | Viridian EV 2
1.
Introducon
1.1 ABOUT THIS DOCUMENTATION
PURPOSE OF THIS DOCUMENTATION
This Manual contains all the informaon you need for commissioning and using the Viridian EV EPC 2.0. They are intended for
use by electrically skilled persons who commission the device.
SCOPE OF VALIDITY OF THIS DOCUMENTATION
This documentaon is valid for all components of the Viridian EV EPC 2.0 specied in this Manual and describes the delivery
state as of Feb 2020.
THIS PRODUCT IS BASED ON THE IEC 61851 AND SAE J1772 INTERNATIONAL STANDARDS

Issue 1.2 May 2020 EVSE Protocol Controller 2.0 (EPC 2.0) | Viridian EV 3
2 .
SAFETY INSTRUCTIONS
2.1 CAUTIONS & DANGERS
CAUTION: PLEASE OBSERVE THE SAFETY INSTRUCTIONS AND LEGAL NOTES
Installaon requirements for electrical equipment and EVSE vary by country and jurisdicon. It is the responsibility of the
installer/user of this product to ensure that legal installaon requirements are met. In the UK, this product must be
installed and used by a competent and qualied person who will ensure the equipment adheres to the IEE wiring
regulaons BS7671 (18th Edion or later) and current Building regulaons. This device has safety features that enable
and help with meeng these regulaons.
DANGER: VOLTAGE HAZARDS
Contact with live components can result in serious injuries. Disconnect the system and all devices from the power supply
before starng work.
2.2 FUSES
WARNING: UNDESIRABLE HEAT GENERATION OR FIRE DUE TO INADEQUATE FUSING.
The internal fuses are designed only to protect the device itself. The system installer and plant operator are responsible
for the necessary line protecon.
The relay outputs are not fused within the device. Without appropriate protecon of the relay outputs, overloading can
cause undesirable heat generaon or even re. The relay outputs are to be fused externally by the plant constructor.
2.3 REPAIRS
Repairs are not permied. Defecve devices must be disposed of in compliance with environmental requirements.
WARNING: DANGERS ASSOCIATED WITH UNAUTHORIZED OPENING OF THE DEVICE
Unauthorized opening of the device might place the user in danger or result in substanal damage to property.
CAUTION: INVALIDATION OF THE MANUFACTURER’S WARRANTY DUE TO
UNAUTHORIZED ALTERATIONS TO THE DEVICE
Alteraons to the devices are not permied. Failure to observe this requirement shall constute a revocaon of the
manufacturer’s warranty.

Issue 1.2 May 2020 EVSE Protocol Controller 2.0 (EPC 2.0) | Viridian EV 4
3.
DESCRIPTION
3.1 OVERVIEW OF THE EPC 2.0
The EPC 2.0 is a DIN rail mounted control module for IEC 61851 compable EV charge points. Key features include RCM support and
PEN Loss detecon, helping charge point manufacturers and installers meet regulaons in a cost-eecve way and protect against
electric shock in the unlikely event of an earth and neutral fault problem.

Issue 1.2 May 2020 EVSE Protocol Controller 2.0 (EPC 2.0) | Viridian EV 5
DEVICE VERSIONS • The Viridian EV EPC 2.0 has part numbers in this format:
EPC20(1)(2)(3). i.e. EPC20 P10-R
• (1) indicates the model B = Basic P = Plus
• (2) indicates the revision number
• (3) Presence of an R indicates supplied with RCM
SUPPLIED PARTS EPC 2.0 module, Current Transformer (CT), RCM (when selected; oponal part)
AREAS OF
APPLICATION & USE
• Controlling the charging procedure of electric vehicles in accordance with IEC61851
mode 3
• For communicaon with the electric vehicle according to IEC62196-2 or SAE J1172
MOUNTING Mounng onto standard rail according to DIN EN 60715
CONNECTION ELEMENTS • Mains input (207—257V @ 50Hz AC)
• 2 Relay contacts (230V AC ) for switching the load and Aux contactor
• Solenoid or motor interlock drive for socket (Conguraon dependant)
• Current Transformer (PEN Loss detecon on single phase systems)
• Vehicle interface / Signalling contacts
• Operang current input (IC) - voltage or resistance
• External LED support
INTEGRATED LED Displays the operang state of EVSE
Operang Temp -25 to 50 C
Congurable opons • Ability to restrict charging current ( IC ) up to system maximum.
• Tethered or Socket outlets
• 16A or 32A maximum operang currents depending on ed system contactor
• Solenoid or motor locking systems
• Interlock Feedback for status of motorised locks
• RCM support enable / disable
• Pen Loss enable / disable
• Lock engaged polarity
3.2 EPC 2.0 FEATURES

Issue 1.2 May 2020 EVSE Protocol Controller 2.0 (EPC 2.0) | Viridian EV 6
3.3 EPC 2.0 PEN LOSS DETECTION SYSTEM
In the event of a fault in the PEN conductor supplying the property the Protecve Earth terminal may become live and as such
carry potenally dangerous current.
For single phase charge points only* the EPC 2.0 can protect the user in the event of an open PEN conductor in the power
distribuon network. In the event of a fault in the PEN conductor the EPC 2.0 will disconnect all conductors including the pro-
tecve earth conductor.
The device measures earth current (using supplied current transformer (CT)) and voltage (between Live and Neutral); either
measurement outside of the factory set limits will cause a fault condion which will cause the EPC 2.0 to open the EV and Aux
contactors, isolang the EV and disconnecng all conductors including the PE conductor, meeng minimum requirements in
BS 7671: 2018 amendment 1, 722.411.4.1 (iv) and (v).
A single pole isolaon contactor with a 240V coil rated for the nominal EVSE load is required to disconnect and isolate PE for
this funconality to work.
Details regarding the connecons of the EPC 2.0 and the CT can be found in the Terminal Assignment table (6.2) and the Wir-
ing example (6.3)
Important note: Single phase & 3 phase installaons
Full PEN Loss detecon funconality in the EPC 2.0 has been designed in accordance with UK specicaons (BS 7671: 2018
amendment 1, 722.411.4.1 (iv) and (v)) for single phase charge points only*.
The EPC 2.0 complies with paragraph BS 7671:2018 amendment 1, secon 722.411.4.1 paragraph (iv) for single phase installa-
ons by monitoring the supply voltage. If this is outside of limits (207 - 254 V) the device will open both relay contacts thereby
isolang the charge point socket from the mains network, including the earth path.
Addionally, the device complies with paragraph (v) of the above secon as the PEN Loss CT is designed to sense this fault
current in the earth conductor and open both relay contacts thereby also isolang the charge points socket from the mains
network, including the earth path.
It is up to the user creang the EVSE using an EPC 2.0 to understand if it is a single phase or three phase installaon and apply
the requirements of BS 7671: 2018 amendment 1 accordingly.
It is up to the user creang the EVSE using an EPC 2.0 to know and understand their local regulaons outside the UK and
whether this device suitably protects against an open PEN conductor situaon in the distribuon network.
*If the PEN Loss CT is sll connected and PEN Loss is enabled, the device will sll open the contactors and isolate the charge
point socket for the 3 phase charge points (meeng paragraph (v) of the above specicaon), however full PEN Loss detecon
has been designed to meet both paragraphs (iv) and (v) of the above specicaon and not all live conductors are being meas-
ured in a 3 phase charge point by the EPC 2.0.

Issue 1.2 May 2020 EVSE Protocol Controller 2.0 (EPC 2.0) | Viridian EV 7
3.4 RCM OPERATION
The EPC 2.0 has a residual current monitor funcon to monitor currents in the system which protects the system in the event
of fault current being detected. The unit is Factory set to trigger at 6mA DC or greater . If this condion arises the EPC 2.0 will
disable charging and indicate a fault condion ( see table below ) .
In order to reset the fault state, the EV and the EVSE need to be disconnected and reconnected.
If the fault current is sll present then the device will return to a fault state and disable charging. If this persists then consult
troubleshoong guide.
Important note: RCM not installed
If no RCM device is being used in the EVSE then this funconality needs to be disabled as per the conguraon table in this
document, reference secon ( 4.1. )
3.5 SELECTABLE CHARGING CURRENT ( IC )
Selecng charging current on installaon
The EPC 2.0 can be congured to restrict the maximum current available to charge the EV on installaon of the device . This
is achieved by a ng a resistor greater than 100 Ω ( See 4.2 for more informaon ) . If the IC resistor is not ed the EPC 2.0
will default to the maximum current available either 16A or 32A as selected via the DIP switch ,reference secon 4.1

Issue 1.2 May 2020 EVSE Protocol Controller 2.0 (EPC 2.0) | Viridian EV 8
3.6 FUNCTION APPLICATION EXAMPLE
The following shows a schemac applicaon example of an electric vehicle charge point / EVSE assembled with a EPC 2.0. For
example, applicaon opon A shows a Type A RCD, an MCB and the 16A / 32A contactor. Applicaon example B shows a
RCBO (Type A, C curve) and a 16A / 32A contactor.
In all applicaons / installaons the local wiring regulaons must be adhered too.
STATES OF THE CHARGING VEHICLE
STATE A: Vehicle is not connected
STATE B: Vehicle connected but not ready to receive energy.
STATE C: Vehicle is connected/ready to receive energy/no venlaon of the charging area is required in buildings
STATE D: Vehicle is connected/ready to receive energy but venlaon of the charging area is required in buildings
(funcon not supported by EPC 2.0)
STATE E: Short-circuit/power supply disconnected from electric vehicle/electricity is not available/other power supply
problem
STATE F: EVSE is not available/other power supply problem
Opon A
Opon B

Issue 1.2 May 2020 EVSE Protocol Controller 2.0 (EPC 2.0) | Viridian EV 9
3.7 SEQUENCE OF CHARGING PROCESS
1. INITIALIZATION
Aer the operang voltage is applied, the module carries out inializaons and funcon tests indicated by two LED pulsing
sequences and then waits for vehicle connecon (indicated by pulsing blue LED).
2. CHARGING PROCESS
The module waits for a charging cable or vehicle to be connected (state A) indicated by the blue LED connually pulsing . If an
approved
connecng cable has been connected (see Proximity) and state B is indicated by the vehicle, the module changes the LED to
be steady-blue and acvates the interlock. A connuing ashing White LED will indicate that the lock is obstructed if the
system has been congured for an interlock.
Aer interlocking, the charge-enable relays are acvated if the vehicle is signalling state C. The charging process is acvated,
and the LED is changed to steady-green (LED indicaon : A colour combinaon is used to indicate the rmware version . The
maximum congured charging current is indicated by a series of white pulses ) If state D is indicated (venlaon required)
then charging and interlock are deacvated as the EPC does not provide a fan-enable mechanism, and the LED is changed to
steady-red.
In a fault condion the charge-enable relay and the interlock are deacvated and the LED is changed to connually pulse red.
A slowly pulsing RED LED will require no manual intervenon to restart charging from a fault condion, once the fault has
been idened and cleared . A rapidly pulsing RED LED will require manual intervenon.
VENTILATION REQUIREMENT
WARNING: SUFFOCATION HAZARD WHEN CHARGING INDOORS
Without venlaon, a danger of suocaon can arise due to gas build-up with some baery types when charging indoors. If
the charging process takes place indoors, forced-air venlaon should be installed. The Viridian EV EPC 2.0 does not monitor
the funconality of the forced-air venlaon systems and so are not compable.
CONTROL PILOT
The pilot circuit is used for the bi-direconal exchange of informaon between the charging staon and the vehicle. Via this
signal, the charging staon indicates to the vehicle the maximum permied charging current which the vehicle can call up. The
operaonal readiness of the charging staon is also indicated. Via this signal, the vehicle indicates to the charging staon its
current state of charging readiness.
WARNING
Via the pilot signal, the EPC 2.0 module species the maximum charging current that can be drawn by the vehicle. This
specied current must be consistent with the line protecon congured for the charging device and the rest of the plant
conguraon. Failure to observe this noce can result in injury to persons or property damage.
PROXIMITY
With free cable installaons the charging device detects the maximum current carrying capacity of the connected charging
cable via the proximity signal. The acvated charging output coded in the pilot signal is no greater than the current carrying
capacity of the charging cable.
The EPC 2.0 is designed to operate with available charging current signals of 16A and 32 A ,depending on the current carrying
capacity of the cable that is detected. Note : The adversed current from the EVSE maybe downgraded depending on the
current carrying capacity of the cable detected. . The charging circuit that is acvated must be designed with a suitable line
protecon for 16A for the installed system .For charging cables that have a current carrying capacity of 32A according to IEC
61851 the system must be designed with a suitable line protecon .

Issue 1.2 May 2020 EVSE Protocol Controller 2.0 (EPC 2.0) | Viridian EV 10
DESCRIPTION OF THE 10 WAY DIP SWITCH
POSI-
TION
OFF ( POSTION UP ) ↑
Supplied Default Setting
ON ( DOWN POSTION)↓
116A Maximum Current 32A Maximum Current
2Free Socket Outlet Tethered Cable Outlet
3Motorised Locking Mecha-
nism
Solenoid Locking Mechanism
4Lock feedback signal Ena-
bled
Lock feedback signal Disabled
5Hella Actuator Phoenix Actuator
6Residual current monitoring
Enabled
Residual current monitoring
disabled
7PEN Loss for single phase sys-
tems enabled
PEN Loss for single phase sys-
tems disabled *
8Not Used Not Used
9Not Used Not Used
10 Not Used Not Used
4.
Conguraon
4.1 DIP SWITCH
Congurable features are selected on a 10-way DIP switch located on the top of the EPC 2.0 .The device will be provided
with the default conguraon of the DIP switch ( see table ) . The Unit will be supplied with the push t lid to t aer
the correct selecon for 16A or 32A installaon.
This lid can carefully be removed in future by using a small at blade screwdriver , placing this at the base of the slot and
pushing into the device to press in each clips unl it releases upward .
* If disabled it will disable charge point if voltage on monitored phase is outside of correct range but will
self-recover. If this persists then contact electricity supplier.

Issue 1.2 May 2020 EVSE Protocol Controller 2.0 (EPC 2.0) | Viridian EV 11
4.2 INPUT CURRENT TO VEHICLE
INPUT CURRENT RESISTANCE SELECTION INFORMATION
An Input Current (IC) resistance (or equivalent voltage) restricts the current maximum adversed by the EPC 2.0
and therefore the operang current while charging . The resistor (or voltage) is applied across the IC and 0V
terminals. It is recommended to use a resistor of 0.1% tolerance & power rang of 63mW or greater.
The IC values are as described below for either the 16A and 32A systems respecvely
16A Installaon
32A Installaon
Max Current IC Resistance (Ohms) IC Equivalent Voltage (V)
32A 732 2.1132
31A 698 2.0554
30A 665 1.9970
29A 634 1.9400
28A 619 1.9117
27A 590 1.8553
26A 562 1.7990
25A 536 1.7448
24A 511 1.6909
23A 491 1.6465
22A 475 1.6102
Max Current IC Resistance (Ohms) IC Equivalent Voltage (V)
16A 348 1.2908
15A 332 1.2462
14A 316 1.2006
13A 301 1.1568
12A 280 1.0938
11A 267 1.0537
10A 249 0.9968
9A 237 0.9580
8A 221 0.9050
7A 205 0.8506
6A 191 0.8018

Issue 1.2 May 2020 EVSE Protocol Controller 2.0 (EPC 2.0) | Viridian EV 12
Max Current IC Resistance (Ohms) IC Equivalent Voltage (V)
21A 453 1.5588
20A 432 1.5084
19A 412 1.4589
18A 392 1.4080
17A 374 1.3610
16A 348 1.2908
15A 332 1.2462
14A 316 1.2006
13A 301 1.1568
12A 280 1.0938
11A 267 1.0537
10A 249 0.9968
9A 237 0.9580
8A 221 0.9050
7A 205 0.8506
6A 191 0.8018
If an IC resistor is not ed the EPC 2.0 will default to the maximum current proclaimed as available determined by the
DIP switch of either 16A or 32A
If an IC resistor or less than 100-Ω, MIN, is ed then the EPC 2.0 will reduce the adversed current capacity
to 7A for ve seconds aer which the EV P1 Contactor and the interlock will be disabled and the EPC 2.0 will
enter into a forced Status A unl the input current resistance is increased

Issue 1.2 May 2020 EVSE Protocol Controller 2.0 (EPC 2.0) | Viridian EV 13
4.3 LED DISPLAY & TROUBLESHOOTING
LED DISPLAY
The EPC 2.0 has a 3-color LED for displaying operang states and fault condions. The LED can be lit in blue,
green, red, white or purple The meaning of the individual displays is shown in the following tables:
GENERAL TROUBLESHOOTING
To test if the EVSE built with the EPC is funconing as intended it is suggested to iniate a charging session and check the
operaon of the unit by following the sequence below:
• With nothing connected check that EPC LED is ashing blue
• Connect the connector to the vehicle - Check that EPC LED turns to solid blue
• Start a charging session on the vehicle - Check that EPC LED turns green and chosen contactor is energised
• Stop a charging session from within vehicle (Type 2) or by pressing the switch to remove the connector from the vehicle
(Type 1) - Check that EPC LED turns to solid blue and contactor is de-energized
• Remove connector from vehicle - Check that EPC LED is now ashing blue
TROUBLESHOOTING FOR QUALIFIED PERSONNEL ONLY
• Is the EPC and socket/tethered cable correctly earthed? The 0V terminal on the EPC should be connected to Protecve
Earth in order for the system to operate correctly.
• Ensure all connecons in the EVSE are ghtened to the correct Torque seng. For M3 terminals on the EPC: 0.6-1.2Nm .
Consult relevant manufacturer documentaon for other parts used
• Check for correct operaon of RCBO & Contactor
• Check for a short between the CP and 0V terminal on EPC
LED DESCRIPTION OF OPERATING STATE
COLOUR STATUS
NOT LIT NOT LIT The EPC 2.0 is not acve, switched o
• No power supply
• Device defecve
BLUE PULSING The EPC 2.0 is waing for the electric vehicle to be connected
to the EVSE (State A)
BLUE STEADY Electric vehicle connected, electric vehicle is not ready for
charging (State B)
GREEN STEADY Charging process acve (State C)
WHITE PULSING The interlock is acvang . If this connues to ash then the
lock may be obstructed
RED STEADY Electric vehicle requires venlaon, charging deacvated
(State D) - EPC 2.0 does not support this funconality so
charging disconnued
RED PULSING EVSE Fault detected. Charging deacvated (Status F) See
Troubleshoong guide.

Issue 1.2 May 2020 EVSE Protocol Controller 2.0 (EPC 2.0) | Viridian EV 14
5.
TROUBLESHOOTING
5.1 GENERAL TROUBLESHOOTING
TROUBLESHOOTING FOR QUALIFIED PERSONNEL ONLY
Follow commissioning guide to determine the nature of the fault.
• PEN Loss . Contact DNO or the ulity company responsible for the supply
• Single Phase monitoring
• Is the EPC and socket/tethered cable correctly earthed? The 0V terminal on the EPC 2.0 should be
connected to Protecve Earth in order for the system to operate correctly.
• Ensure all connecons in the EVSE are ghtened to the correct Torque seng. For M3 terminals on
the EPC: 0.6-1.2Nm - (factory seng of 1nm). Consult relevant manufacturer documentaon for oth-
er parts used
• Check for correct operaon of RCBO & Contactor
• Check for a short between the CP and 0V terminal on EPC
• Interlock does not acon : Check LK FB , LK+ and LK- connecons
LED DESCRIPTION OF OPERATING STATE
COLOUR STATUS
White Flashing lock is obstructed.
Purple Steady PEN Loss detected . The EPC 2.0 has disconnected the EVSE .
Contact DNO or the ulity company responsible for the sup-
ply .
Red Slow Pulsing State E
• Communicaon or Power fault to EV
• EVSE Fault—Maintenance or repair required QUALI-
FIED PERSONNEL
Red Fast Pulsing
• RCM Fault: 6mA DC current detected
• Diode Check Fail

Issue 1.2 May 2020 EVSE Protocol Controller 2.0 (EPC 2.0) | Viridian EV 15
6.
CONNECTION
WARNING: UNDESIRABLE HEAT GENERATION OR FIRE DUE TO INADEQUATE FUSING
The internal fuses are designed to oer dual protecon only for the device itself. The system installer and plant opera-
tor are responsible for the necessary line protecon. The relay output control signal is not fused within the device. .
The 16A/32A relay contactor outputs are to be fused externally by the plant constructor. Without appropriate pro-
tecon of the relay outputs, overloading can cause undesirable heat generaon or even re.
WARNING: VIA THE PILOT SIGNAL, THE VIRIDIAN EV EPC 2.0 CHARGING CONTROLLER SPECIFIES THE MAXI-
MUM CHARGING CURRENT THAT CAN BE CALLED UP BY THE VEHICLE.
This specied current must be consistent with the line protecon congured for the charging device and the rest of
the plant conguraon. Failure to observe this noce can result in injury to persons or property damage
WARNING: THE CONDUCTOR CROSS-SECTIONS MUST BE DESIGNED CORRESPONDING TO A
STANDARD-COMPLIANT SYSTEM CONFIGURATION.
The cables that are to be connected must be designed according to the respecve type of circuit. Failure to observe this noce
can result in injury to persons or property damage.
Depending on the device version the Viridian EV EPC charging controller is connected to the EVSE in the following
methods:
6.1 CONNECTING TERMINALS & TERMINAL ASSIGNMENT
TETHERED CABLE
“Tethered” means that the charging cable is permanently connected to the EVSE.. The RCBO should be rated at the maxi-
mum current ( 16A/ 32A ) set via the DIP switch ( See Conguraon )
FREE CABLE / SOCKET VERSION
“Free” means that the charging cable is not permanently connected and that the user is expected to provide their own.
The EPC 2.0 will energize the 16A or 32A Relay Contactor as selected during installaon
NOTICE
The temperature stability of the cable used must be designed for at least for 75°C. Failure to observe this can result in
injury to persons or property damage
STRIPPED LENGTH SUITABLE CONDUCTOR
CROSS SECTION / AWG
Torque
0,5 ... 2.5 mm2 / 20-14 AWG 0.5 Nm
• Without core ends prepared: 0.5 ...
2.5 mm2
We advise using 0.25mm2 bootlace
ferrules on smaller gauge wire.
0.5 Nm

Issue 1.2 May 2020 EVSE Protocol Controller 2.0 (EPC 2.0) | Viridian EV 16
6.2 EPC TERMINAL ASSIGNMENT
ALL VERSIONS
COMMISSIONING
To test if the EVSE built with the EPC is funconing as intended it is suggested to iniate a charging session and
check the operaon of the unit by following the sequence below:
• With nothing connected check that EPC LED is ashing blue
• Connect the connector to the vehicle - Check that EPC LED turns to solid blue
• Start a charging session on the vehicle - Check that EPC LED turns green and chosen contactor is energised
• Stop a charging session from within vehicle (Type 2) or by pressing the switch to remove the connector from
the vehicle (Type 1) - Check that EPC LED turns to solid blue and contactor is de-energized
• Remove connector from vehicle - Check that EPC LED is now ashing blue

Issue 1.2 May 2020 EVSE Protocol Controller 2.0 (EPC 2.0) | Viridian EV 17
EPC 2.0 TERMINAL ASSIGNMENT
TERMINAL DESCRIPTION
L (LINE) This is where the AC ‘live’ or ‘line’ connecon is made (207-257V @ 50Hz AC)*
N (NEUTRAL) This is where the AC ‘neutral’ connecon is made (207-257V @ 50Hz AC)*
0V (PE) This is where the Protecve Earth ( ground ) and 0v connecons for the RCM and
IC resistor circuits are made*
LK+
Conguraon is dependent .
• Provides a drive current to connuously energise the solenoid interlock
• Provides a drive current to change the motorised interlock state to locked
( The signal is acvated for 500ms and changes to pulsed 500ms intervals
unl the lock is engaged. ( See LK FB )
Rang 12V 300mA
LK-
Conguraon is dependent .
• Provides a return path for the solenoid interlock drive current LK+.
• Provides a drive current to change the motorised interlock state to unlocked
( The signal is acvated for 500ms and changes to pulsed 500ms intervals
unl the lock is disengaged. ( See LK FB )
Rang 12V 300mA
LK FB If lock feedback has been selected via DIP switch 4
COM Relay 1 & 2 (common) Live from integrated electrical protecon or mains terminals
P1 Relay 1 to coil on the EVSE ( 16A / 32A ) Contactor
P2 Relay 2 to coil on the Auxiliary Contactor
PP ( Proximity Pilot ) Connecon for the IEC61851 / J1772 EVSE Connector ( see Proximity )
CP ( Control Pilot ) Connecon for the IEC61851 / J1772 EVSE Connector ( see Pilot Circuit )
IC ( Input Current ) The liming Input Current to the EV , Resistor connecon ( The other connecon
of the Resistor is the 0v (PE) terminal.
12V 12V Supply to provide power to the RCM
FLT Connects to RCM ‘ Fault out’. The EPC 2.0 reads if fault condion reported by the
RCM
TST Connects to RCM ‘ Test’ . The EPC 2.0 uses this to check the operaon of the
RCM before each charging session commences.
CT1 ( PEN) Connecon for current transformer 1; measures earth current for PEN Loss detec-
on (or base load for load sharing in EPC 2.0 + models )
CT2 Connecon for the other side of current transformer 1
NC Not Connected . Not used .
CT3 Connecon for current transformer 2; measures EVSE current draw in EPC 2.0 +
models (not used in the basic EPC 2.0 models)
CT4 Connecon for the other side of current transfer 2
RSA RS485 connecon available in EPC 2.0 + models
RSB RS485 connecon available in EPC 2.0 + models
RSG RS485 ground connecon available in EPC 2.0 + models
• * On tethered and free cable installaons the electrical protecon and contactor should be rated according to
the maximum current capacity selected via the DIP switch on the EPC 2.0 of either 16A or 32 A

Issue 1.2 May 2020 EVSE Protocol Controller 2.0 (EPC 2.0) | Viridian EV 18
6.3 230 V AC POWER SUPPLY
WIRING EXAMPLE: Socket Outlet
WARNING: THE EXTERNAL CONTACT BLOCKS USED MUST BE FLOATING
AND SAFELY SEPARATED FROM UNSAFE CIRCUITS.
Failure to observe this can result in injury to persons or property damage
* Optional fitting : Refer to section 4.2

Issue 1.2 May 2020 EVSE Protocol Controller 2.0 (EPC 2.0) | Viridian EV 19
6.6 SHUTDOWN OF POWER BRANCH
According to IEC 61851, a shutdown of the power branch on compleon of the charging process within 3 s is
required. A shutdown of the power branch on transion from state C to state A is required within 100 ms. The
Viridian EPC 2.0 deacvates the relay output within this requirement aer detecng the shutdown criterion.
WARNING: THE SHUTDOWN OF THE POWER BRANCH, IN PARTICULAR THE POWER
CONTACTOR, IS TO BE DESIGNED IN SUCH A WAY THAT THE ENTIRE IMPACT CHAIN DOES
NOT EXCEED THE REQUIRED 100 MS.
Failure to observe this noce can result in death or serious physical injury.
6.5 FUNCTIONAL GROUNDING
VEHICLE INTERFACE ACCORDING TO IEC 61851
1. Connect the terminals “CP” and “PP” (on free cable versions only) directly to the EVSE socket
2. First connect the ground connecon of the vehicle interface to the 0V reference point and then route this
potenal from there
DANGER: NEVER USE THE TERMINALS OF THE VIRIDIAN EPC 2.0 CHARGING
CONTROLLER AS A 0V REFERENCE POINT.
Always route this externally from the device! The 0V reference point within the plant must be
6.4 EXTERNAL LED CONNECTOR
An external RGB LED can be driven by the EPC 2.0. It is 0V acve with common 12V. A wiring harness and connect-
or on one end will be an oponal extra with the EPC 2.0 that can be cut to length by user and connected to their
chosen LED.
External LED Connector

Issue 1.2 May 2020 EVSE Protocol Controller 2.0 (EPC 2.0) | Viridian EV 20
7.
MOUNTING
7.1 MOUNTING ONTO STANDARD RAIL
1. Clip the device (a) vercally onto the horizontal DIN rail (b).
Swing the device downward unl the unlocking slider on the DIN rail clicks into place.
Table of contents
Other EVSE Controllers manuals
Popular Controllers manuals by other brands

Müller
Müller MDR-057 Operating and assembly instructions
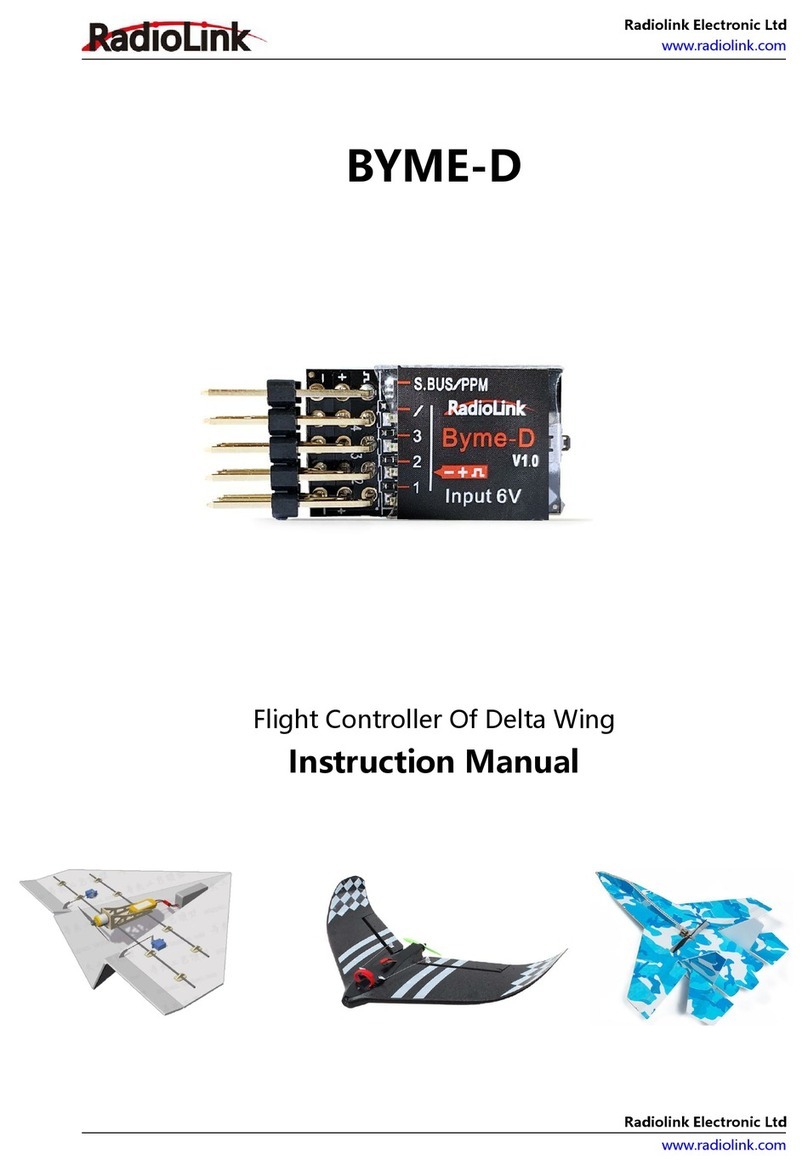
RadioLink
RadioLink BYME-D instruction manual
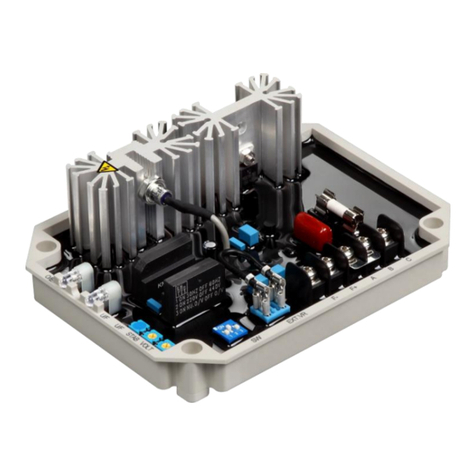
Kutai electronics
Kutai electronics ADVR-073 Operation manual

Norac
Norac UC4 Plus Rogator 64 Series installation manual
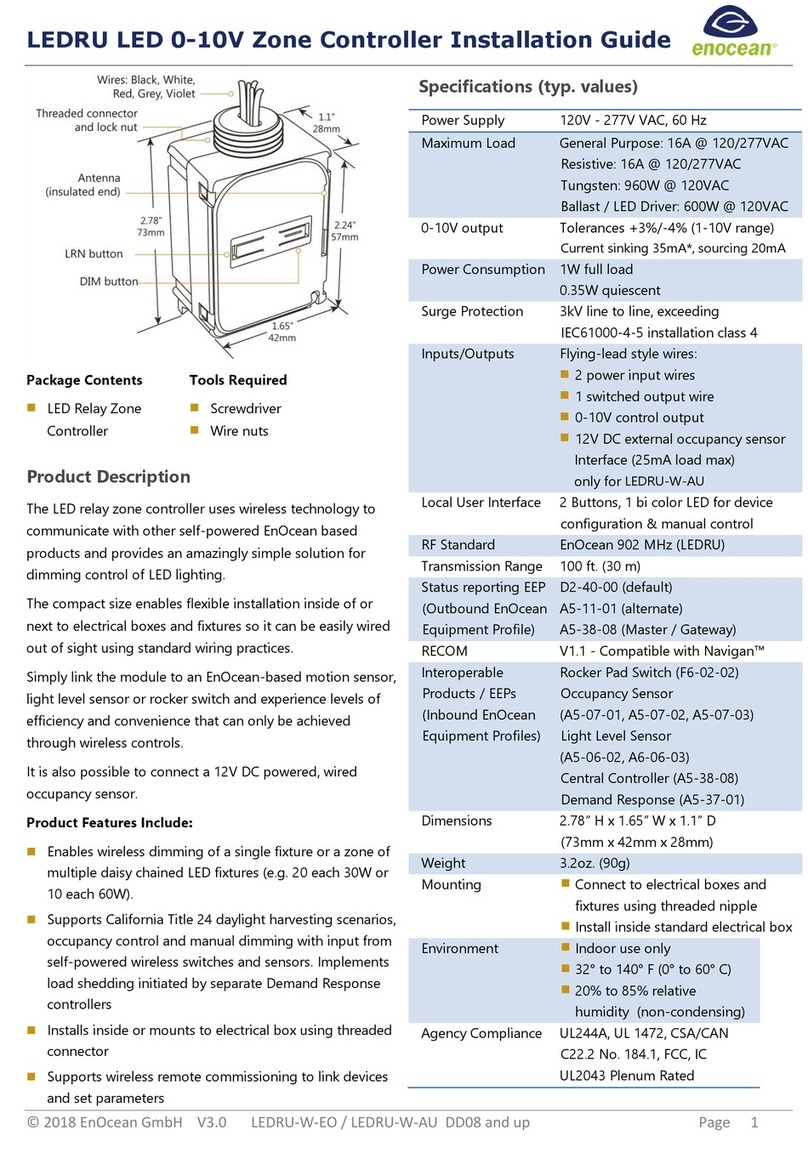
EnOcean
EnOcean LEDRU installation guide
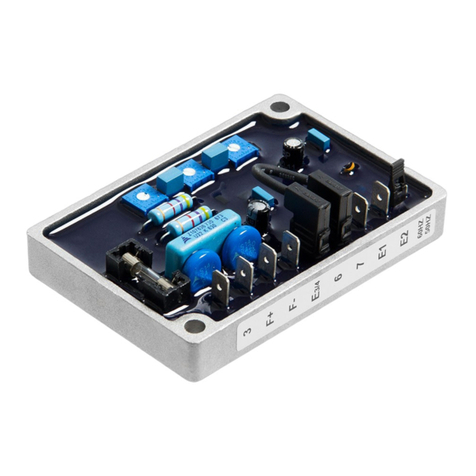
Optimus
Optimus AVR-A-OPT-02 Installation and operation manual