FIAMA SERVO.M-E Guide

Positioning unit SERVO.M_E-P
Data: 01/12/20 file: Servo.M_EP_CS_1.7_ing.doc pg 1/7
USER’S MANUAL AND MAINTENANCE
POSITIONING UNIT “SERVO.M-E” “SERVO.M-P”

Positioning unit SERVO.M_E-P
Data: 01/12/20 file: Servo.M_EP_CS_1.7_ing.doc pg 2/7
Manual purpose
This manual has been designed by the manufacturer to provide the necessary information regarding the unit
SERVO to those who are authorized to carry out safely its installation, maintenance, dismantling and
disposal. All the necessary information for the buyers and planners can be found in the Sales catalogue.
Other than adopting good technical construction methods, the information should be read carefully and
strictly applied. Inobservance of this information could cause risks for the health and safety of people and
economical damage. This information, provided by the manufacturer in the original language (Italian) is also
available in other languages to satisfy legislative and/or commercial needs. A responsible person in an ideal
place must keep this manual in good conditions so that it is always available for consultation. In case this
manual is lost or deteriorates, a replacement should be requested directly from the manufacturer quoting the
manual’s code. This manual reflects the state of skill of the instrument at the time of input on the market:
however the manufacturer reserves the right to make changes, add or improve the manual without giving any
reason to hold the present manual inadequate.
Identification of the equipment
The identification plate represented is applied on the instrument.
To find out the identification code of the instrument, consult the sales catalogue.
Environmental conditions
Temperature setting: min. 0°C, max. + 50°C.
It is forbidden to use the instrument other than its specific use and in potentially explosive conditions or where
anti- explosive elements are used.
Storage
Here below are some references to be followed for the storage of the device.
Avoid environments with excessive humidity and those exposed to bad weather (avoid open areas). Avoid
putting the instrument directly on the ground. Store the instrument in its original packing.
Conformity declaration and EC marking
The instrument answers to the following Communitarian Directives:
2014/30/EU Electromagnetic compatibility, 2011/65/EU RoHS
Maintenance
The instrument does not need a particular maintenance except cleaning to do only with a soft cloth dampen
with ethylic alcohol or water. Do not use hydrocarbon solvents (petrol, diluents, etc.): the using of these
products could affect the proper functioning of the instrument.
Reparations should be done only and exclusively at the FIAMA technical assistance centre.
Assistance request procedure
For any kind of technical assistance request, contact the sales department of the Manufacturer directly
indicating the information given on the identification plate, the number of hours used and the type of defect.
Manufacturer’s responsibility
The manufacturer declines any responsibility in case of:
• Using the instrument contrary to the national safety and accident-prevention laws.
• Wrong installation, inobservance or wrong procedures of the instructions provided in the present manual.
• Defective electrical power supply.
• Modifications or tampering.
• Operations carried out by untrained or unqualified staff.
The safety of the instrument also depends on the strict observance of the procedures indicated in the
manual: always operate the instrument in its functioning capacity and carry out a careful routine maintenance.
• All phases of inspection and maintenance should be done by qualified staff.
• The configurations provided in the manual are the only ones permitted.
• Do not try to use it anyway contrary to the indications provided.
• The instructions in this manual do not substitute but accomplish the obligations of the current legislation
regarding the safety laws.

Positioning unit SERVO.M_E-P
Data: 01/12/20 file: Servo.M_EP_CS_1.7_ing.doc pg 3/7
Description
The positioning unit SERVO.M is made of a geared motor in direct current with microprocessor control of the
driving gear and of an incremental position transducer (encoder) or absolute (precision potentiometer)
assembled on the output shaft with interface for field bus and display with 5 digits. It realises in a single and
compact device a complete system for the control of axis being able to receive by bus a dimension to reach
and start with the positioning by a control type PID. The version SERVO.M-E has a position transducer with
an incremental optic encoder, while the version SERVO.M.P has a precision potentiometer.
The SERVO.M unit has a hollow shaft output to enable a simple assembling and a versatile use, even with
pre-existent manual motion machines that have to be automated. Therefore it is suitable for a large number
of applications in machinery within industries such as printing, packaging, woodworking,
marble, plastic, etc. A simple linking and lay out are guaranteed by a supervisor (PC, PLC), the system
interfaces with a bus-field to control the positioning and enable the modifications of the control parameters
(present quota, speed, state).
The communication record can be MODBUS RTU, CANopen, PROFIBUS DP.
For the electric connection there are separate ways for the power-supply and communications cables: the
SERVO.2M has 2 press-cables PG9 for the input and output of the connections, the SERVO.3M has 3 press-
cables for the input and output (2 PG9, 1 PG7).
Installation
Before installing the instrument, read the following warnings:
a) Connect the instrument strictly following the instructions of the manual.
b) Carry out the connections using the correct wires within the limits of the tension and power supply as
indicated in the technical data.
c) The instrument does not have an ON/OFF switch, hence it comes on when connected to the power supply.
For safety reasons, the equipment connected permanently to the power supply requires a bi-phase selector
switch which should be within easy reach of the operator.
d) If the instrument is connected to any apparatus not isolated electrically, carry out an earth connection to
avoid it being connected directly through the structure of the machine.
e) It is the responsibility of the user to check, before using , the correct settings of the parameters of the
instrument to avoid damage to persons or things.
f) The instrument cannot function in a dangerous environment (inflammable or explosive). It can be
connected to elements that operate in the same atmosphere only through appropriate interfaces, according
to the current safety
regulations.
g) Avoid dust, humidity, corrosive gases, heat sources.

Positioning unit SERVO.M_E-P
Data: 01/12/20 file: Servo.M_EP_CS_1.7_ing.doc pg 4/7
Power supply
a) Before connecting the unit, check that the power supply tension is within the permitted limits and that it
corresponds to the one indicated on the tag.
b) Carry out the electrical connections with the instrument disconnected.
c) For the power line to instruments and sensors, a power supply line separate from that of the power is
required : it is necessary to use an isolating transformer.
d) The power line should provide a device that separates the set fuses of the instruments and should not be
used to regulate relays, contactors, etc.
e) If the network tension is very disordered (ex. from the change-over of the power units, motors, inverters,
welders, etc.), use the appropriate filters of the network.
f) If an earth connection is needed, ensure that the plant has a good earth system: tension between neutral
and earth <1V and the resistance <6 Ohm.
Gear motor assembly:
To assemble the unit correctly adhere to the following instructions:
Two M4 screws can be used moreover, that can be screwed in the two brass inserts M4x12 : this is in case
the servo motor has to make many manoeuvres or is used continuously.
The unit is therefore inserted through the hollow shaft of diameter Ø20 millimetre (50mm deep) on the
driving shaft of the machine.
Ensure that the hollow shaft is perpendicular to the support base.
Block the hollow shaft on the machine shaft using the bolt screw M4 on the clamping metal ring.
N.B. = The gear motor does not have parts that need maintenance or oiling.
If necessary, protect the unit from: dust, water, collisions, extreme temperatures.
Manually turn the shaft of the reducer using the clamping ring (tightened on the hollow shaft)
only if necessary.
Do not exceed permitted torque.
Do not dismantle or open the unit, particularly the part of the reducer.
Do not pierce/modify the container or the hollow shaft.
POTENTIOMETRIC VERSION Before assembling the SERVO, it is fundamental to place the shaft of the
machine and the shaft of the SERVO in the correct position, for example half way or towards the end, in a
way that there is correlation between the position of the SERVO and that of the machine. To do that, the
motion of the hollow shaft of the SERVO should be serially commanded by the control unit (PLC, PC, etc):
do not rotate the shaft by hand.
The calculation of the number of turns that the hollow shaft has to finish to develop the total motion of the
machine is determined by multiplying the reduction ratio of the reducer of the potentiometer by the number
of turns of the potentiometer itself (total reduction ratio = R).
In case that the maximum number of allowed rotations by the shaft is exceeded, a mechanical friction
intervenes to safeguard the potentiometer transducer.
NB: the SERVO is provided with the hollow shaft and the potentiometer positioned half way.
ELECTRICAL CONNECTION
Disconnect from power supply before connecting/disconnecting the equipment/machinery.
The connecting cables must be kept separate from the power lines or from electromagnetic
interference sources.
Pay careful attention to the electrical connections: any failure caused by a faulty connection
will render the guarantee null and void.
The power supply must be in the permitted range, a higher range could damage the
equipment.
Remove the 3 closing screws of the cover to access the terminal box.
Slide the cables in the cables press and carry out the connections according to the following figure:

Positioning unit SERVO.M_E-P
Data: 01/12/20 file: Servo.M_EP_CS_1.7_ing.doc pg 5/7
1
1
PROFIBUS - MODBUS
+ - Power Supply 24VDC
B1÷B2 = PROFIBUS B line, +RS485
A1÷A2 = PROFIBUS A line, - RS485
+ - Power Supply 24VDC
B1÷B2 = CAN-L, +RS485
A1÷A2 = CAN-H, - RS485
COM = CAN_GND
Before setting SERVO it is necessary to set the address and baud rate of device using dip-switch S1 and S2
as showed in the following table according to the model of SERVO used.
If the SERVO is the last node of net, set at ON the dip-switch S3 (both switches 1 and 2 at ON).
IMPORTANT: during this phase it is advisable to pay very attention to not damage the dip-switch and the
electronic components on card-board. It is strictly forbidden to take off the card of its case.
Assemble the wiring clip jumper to assure the continuity of shield mostly for the profibus cables.
Setting of device address and serial communication speed – MODBUS protocol
The setting of baud rate is made by the dip-switch S1 (set in factory at 19200) and that of the address with
dip-switch S2 (se in factory at 1). Valid addresses are from 1 to 247.
By changing of address or baud rate is necessary to switch off and turn on the Servo.
S2
12345678
ADDRESS
ON OFF OFF OFF OFF OFF OFF OFF 1
OFF ON OFF OFF OFF OFF OFF OFF 2
ON ON OFF OFF OFF OFF OFF OFF 3
OFF OFF ON OFF OFF OFF OFF OFF 4
etc…… etc……
S1
12
BAUD RATE
OFF OFF 2400
ON OFF 4800
OFF ON 9600
ON ON 19200
CANOPEN - MODBUS

Positioning unit SERVO.M_E-P
Data: 01/12/20 file: Servo.M_EP_CS_1.7_ing.doc pg 6/7
Setting of device address – PROFIBUS protocol
The setting of address is made by dip-switch S2 (set at factory at 1). Valid addresses from 1 to 127. The
speed is measured automatically.
Setting of device address and serial communication speed – CANopen protocol
Transmission speed of serial communication (baud rate: 10, 20, 50, 100, 125, 250, 500, 1000kbaud).
The setting of baud rate is made by 2 dip-switch of S1 and with dip 8 of S2; the address is set with dip 1-7 of
S2 (set in factory at 1). Valid addresses 1-127.
By changing of address and baud rate is necessary to switch off and turn on the Servo
Power Supply connector
M12-T male as viewed externally with exit shaft directed downwards
M12T PIN
CONNECTOR
WIRE
COLOR CONNECTION
1 BROWN +24V POWER SUPPLY
2 WHITE NOT CONNECTED
3 BLUE GND POWER SUPPLY
4 BLACK NOT CONNECTED
S2
12345678
ADDRESS
ON OFF OFF OFF OFF OFF OFF OFF 1
OFF ON OFF OFF OFF OFF OFF OFF 2
ON ON OFF OFF OFF OFF OFF OFF 3
OFF OFF ON OFF OFF OFF OFF OFF 4
etc…… etc……
S2 S1
812
Baud
Rate
(Kbaud)
OFF OFF OFF 10
OFF ON OFF 20
OFF OFF ON 50
OFF ON ON 100
ON OFF OFF 125
ON ON OFF 250
ON OFF ON 500
ON ON ON 1000
S2
1234567
ADDRESS
ON OFF OFF OFF OFF OFF OFF 1
OFF ON OFF OFF OFF OFF OFF 2
ON ON OFF OFF OFF OFF OFF 3
OFF OFF ON OFF OFF OFF OFF 4
etc…… etc……
2
3
1
4

Positioning unit SERVO.M_E-P
Data: 01/12/20 file: Servo.M_EP_CS_1.7_ing.doc pg 7/7
Technical characteristics
Motor magnetic permanent dc power, 70W (150W max)
Power supply 24Vdc ±20%, 2,5A (6,5A max)
Hollow shaft Ø20mm H7, depth 50mm
50/1 max 115RPM (8Nm @ 70RPM non continuous)Gear motor reduction ratio
75/1 max 75RPM (12Nm @ 45RPM non continuous)
Encoder (SERVO E)incremental optical encoder on output shaft
Resolution 1000 pulse/turn
Potentiometer (SERVO P)Precision potentiometer transducer
Resolution 16000 points
Number of turns/ linearity 340°/1% - 3 turns /0,25% - 5 turns /0,25% - 10 turns /0,15%
Potentiometer reducer reductions 1/1; 3,3/1; 10/1; 24/1; 30/1; 90/1, others on request
Electrical connection 4 poles terminal board supply, 4 poles terminal board field-bus,
max 1,5mm2
Cable out SERVO.2M 2 cable glands PG9 (cable Ø 5 - 8mm)
Cable out SERVO.3M 1 cable gland PG7 for supply (cable Ø 3 - 6mm)
2 cable glands PG9 for field-bus (cable Ø 5 - 8mm)
Weight 1100g
Protection level IP54
Working temperature 0-60°C
Temperature 10-85%
Directive: 2014/30/EU Electromagnetic compatibility, 2011/65/EU RoHS
Manufacturer
All communications to the manufacturer should be addressed to:
FIAMA s.r.l., Via G. Di Vittorio, 5/A - 43016 San Pancrazio (Parma) - Italy
Tel. (+39) 0521.672.341 - Fax. (+39) 0521.672.537 – e-mail: info@fiama.it - www.fiama.it
FIAMA srl is not responsible for any damage to persons or things caused by tampering and wrong
use and in any case that are not consistent with the features of the instrument.
This manual suits for next models
1
Table of contents
Popular Engine manuals by other brands
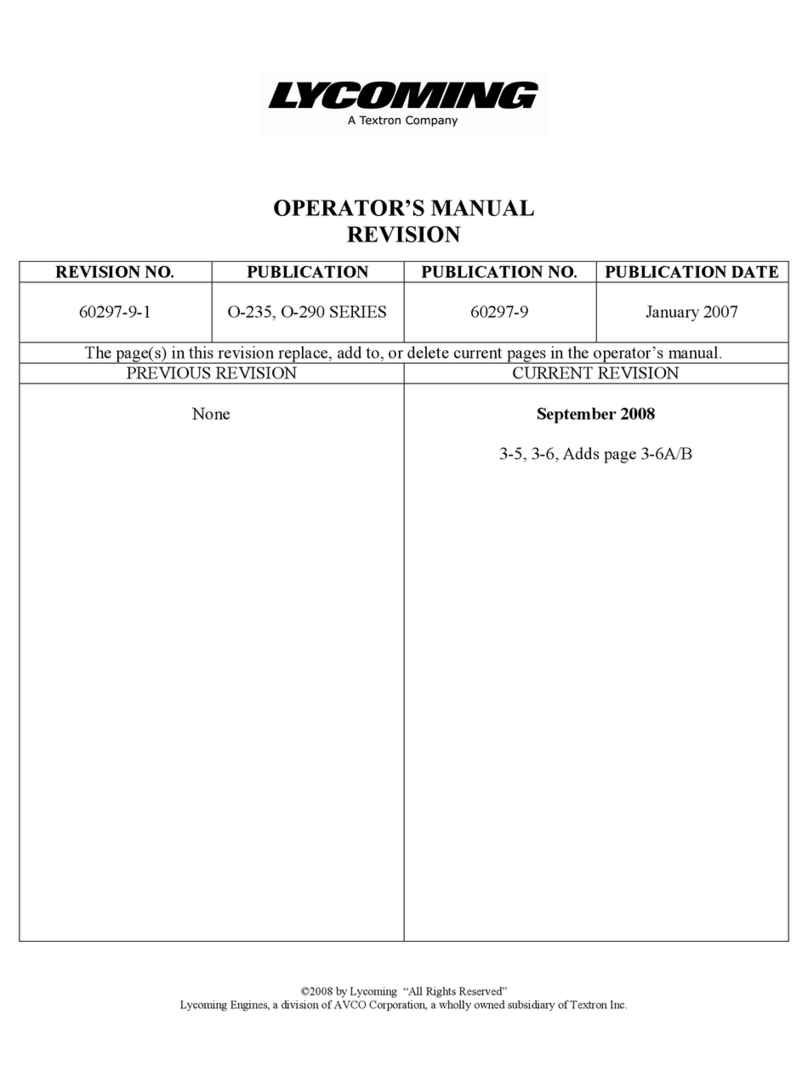
Textron
Textron Lycoming O-235-C Operator's manual

Detroit Diesel
Detroit Diesel DDFP Series Operation and maintenance instruction manual
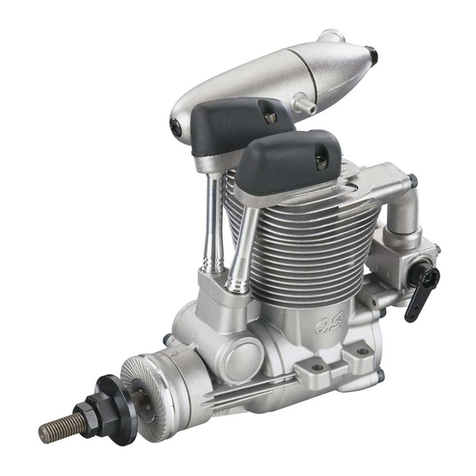
O.S. engine
O.S. engine FS-62V Owner's instruction manual
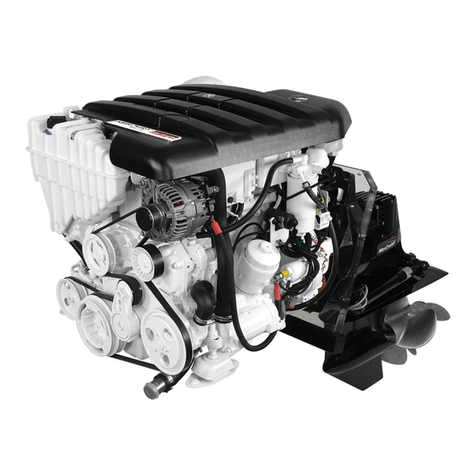
Mercury
Mercury 2.8 Diesel Operation & maintenance manual

ABB
ABB HT574427 Operation manual
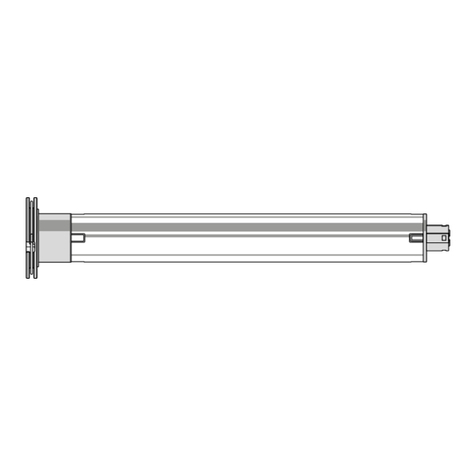
GEIGER
GEIGER SOLIDline Original assembly and operating instructions