Gasmaster R Series User manual

high
efficiency wall boiler
Installation Manual
2021
For Model numbers:
Installation
Service and maintenance
Start up
Parts
WARNING: If the information in this manual is
not followed exactly, a fire or explosion may
result causing property damage, personal injury
or loss of life.
WHAT TO DO IF YOU SMELL GAS:
Switch off the appliance.
Shut off the gas supply.
Open the windows.
Do not try to light any appliance.
Do not touch any electric switch.
Do not use any phone in your building.
Leave the house.
Immediately call your gas supplier from a
neighbour’s phone. Follow the gas
supplier's instructions.
If you cannot reach your gas supplier,
call the fire department.
WHAT TO DO IF YOU SMELL FLUE
GASSES:
Switch off the appliance.
Open the windows.
Shut off the gas supply.
Leave the house.
Contact a registered installer or
a registered service center.
Gasmaster
100, C140, C200
H100, H140, H200
R 100C, R 140C, R 200C
R 100H, R 140H, R 200H

Table of contents
Part 1 –Introduction
4
Hazard definitions
4
User responsibilities
7
Boiler operation
7
Manufacturer conditions
7
Installer responsibilities
7
When servicing boiler
7
When pressure testing boiler
7
Main parts
8
Functionality of main parts
11
Part 2 –Specifications / Technical data
12
Part 3 - Appliance location
14
Location checks
14
Appliance Area Ventilation Air Openings
14
Closet Installations
15
Alcove Installations
15
Residential Garage Installations
15
Prior to wall mounting
16
Cold weather handling
16
Wall mounting
16
Part 4 - General venting
17
Combustion Air-Intake Contamination
17
Near Appliance Vent/Air-Intake Piping
18
Venting options
18
Installation instruction Muelink & Grol vent and air system
19
Concentric installation
19
Cut-able installation
20
Installation of a vent system configuration with wall terminal
22
Additional instructions for termination through a wall with a wall terminal.
23
Mounting instructions for wall terminal Installation
23
Installation of a vent system configuration with roof terminal
25
Additional instructions for termination through a roof with a roof terminal
26
Mounting instructions for roof terminal Installation
26
Mandatory Pre-commissioning Procedure for Plastic Venting
28
Vent/Air-Intake Pipe Length Determination
28
Venting Rules and Guidelines
28
Part 5 - Vent /air - intake termination clearances
30
Removing an Existing Boiler from Common Venting System 31
Part 5.1 –Further Venting Options (PP)
32
Part 6 - Condensate Drain
37
Cleaning
38
Part 7 - Central heating (CH) and Domestic Hot Water (DHW) circuit
39
Automatic Air Relief valve
39
Frost protection
39
Vent corrosion
39
Vent
39
Pressure relief valve
39
Control module
40
Backflow preventer
40
Connect the supply and return piping of the CH circuit
41
Connect the tap water (DHW) circuit (Cxxx types)
41
Connect the tank (Hxxx types)
41
Connect an external expansion tank
42
Use of pumps and maximum remaining head at boiler CH supply connection
42
Installation examples
43
H model piping diagrams
44
C model piping diagrams
47
Part 8 - Installing gas piping
51
Installation
51
Connecting the gas line
51
Propane usage
51
Part 9 - Electrical connections
52
Opening the front cover
52

Table of contents (continued)
Part 10 - Lighting the appliance / First start-up
54
Fill and refill of the CH section
56
Step 1:Turn power on and De-air cycle
57
Step 2: Perform calibration of the boiler
57
Step 3: Adjust settings
60
Table 10.1 Settings menu
61
Weather dependent control / Outdoor sensor set up
62
Set the hot water comfort: eco or comfort
63
Diagnosis menu
64
Part 11 - Installation check list
66
Installation
66
Start-up
66
Operational Checklist
66
Before Leaving
66
Instructions to Installing Contractor
66
Part 12
- Annual maintenance and inspection
67
Annual Inspection Checklist
67
Crystalline Silica
68
Refractory Ceramic Fibers (RFC)
70
Part 13
- Parts list
71
Part 14
–Troubleshooting
73
Servicing the Appliance
73
Displaying faults
73
Fault history
73
Fault codes
74
Reset fault
74
Fault code list
74
Trouble shooting list
75
Possible causes and solutions
76
Part 15 –Start Up Checklist
77
Part 16 –Maintenance Checklist
78
3

Part 1 –Introduction
Hazard definitions
The following defined terms are used throughout this manual to bring attention to the
presence of hazards of various risk levels or to important information concerning the life of the
product.
Indicates presence of hazards that can cause severe
personal Warning injury, death or substantial property damage.
Indicates presence of hazards that will or can cause minor
or Caution moderate personal injury or property damage.
Indicates special instructions on installation, operation or
Notice maintenance that are important but not related to personal injury
or property damage.
Throughout this manual units of measure are often expressed in both imperial and metric units of
measure. Note that for absolute temperature indications degrees Fahrenheit (°F) and degrees Celsius
(°C) have been used. To convert a certain temperature from °C to °F the following formula has been
used: °F = °C × 1.8 + 32.
Temperature differences (delta) in this manual have been expressed in degrees Kelvin (K).
For your convenience conversion tables for temperature, pressure and volume are listed below.
Pressure
Bar Psi
0.7 10.1
1.0 14.5
1.5 21.8
2.0 29.0
2.8 40.6
3.0 43.5
Temperature
°C
F
-15
5
-10
14
0
32
20
68
50
122
60
140
70
158
80
176
Volume
Litre
Gallon
1
0.26
5
1.32
10
2.64
20
5.28
100
26.4
200
52.8
300
79.3
4

Part 1 –Introduction
FOR YOUR SAFETY, READ BEFORE OPERATING
WARNING: If you do not follow these instructions exactly, a fire or explosion may
result causing property damage, personal injury or loss of life.
A. This appliance does not have a pilot. It is
equipped with an ignition device which
automatically lights the burner. Do not try to
light the burner by hand.
B. BEFORE OPERATING smell all around the
appliance area for gas. Be sure to smell next to
the floor because some gas is heavier than air and
will settle on the floor.
WHAT TO DO IF YOU SMELL GAS
Switch off the appliance.
Shut off the gas supply.
Open the windows.
Do not try to light any appliance.
If you cannot reach your gas supplier, call
the fire department.
WHAT TO DO IF YOU SMELL FLUE GASSES
Switch off the appliance
Open the windows
Shut off the gas supply
Leave the house
Contact a registered installer or a
registered service center.
C. Use only your hand to turn the gas switch. Never
use tools. If the switch will not turn by hand, don’t try to
repair it, call a qualified service technician. Force or
attempted repair may result in a fire or explosion.
Do not touch any electric switch.
Do not use any phone in your building. D. Do not use this appliance if any part has been
Leave the house.
Immediately call your gas supplier from
a neighbour’s phone. Follow the gas
supplier's instructions.
under water. Immediately call a qualified service
technician to inspect the appliance and to replace
any part of the control system and any gas
control which has been under water.
OPERATING INSTRUCTIONS
1. STOP! Read the safety information above very
carefully.
2. Turn off all electric power to the appliance.
3. Set the thermostat to lowest setting.
4. Do not try to light the burner by hand.
5. Make sure the CH system is filled with water and
de-aired. Make sure the gas line is de-aired. Wait
five (5) minutes to clear out any gas. Then smell for
gas, including near the floor. If you smell gas,
STOP! Follow “B” in the safety information above. If
you don't smell gas, go to the next step.
6. Make sure that heat can be transferred into
the CH system.
7. The main gas switch is situated directly
underneath the boiler in the gas supply line and
below the gas pressure regulator. Turn the main
gas switch clockwise to close the gas supply.
8. Wait five (5) minutes to clear out any gas. Then
smell for gas including near the floor. If you smell
gas, STOP! Follow “B” in the safety information
above on this page. If you don’t smell gas, go to the
next step.
9. Turn the main gas switch counter clockwise
to open.
10.Turn on all electric power to the appliance and
start the calibration procedure of the boiler (at first
start-up).
11. Set thermostat to desired setting.
12. If the appliance will not operate turn off gas to
appliance and call your service technician or gas
supplier.
Turn clockwise
to close valve
TO TURN OF GAS TO THE APPLIANCE
1. Turn off all electric power to the appliance if
service is to be performed.
2. Set the thermostat to lowest setting.
3. The main gas switch is situated directly
underneath the boiler in the gas supply line and
below the gas pressure regulator.
4. Turn the valve clockwise to close the gas
supply
5

Part 1 –Introduction
Warning
Crystalline Silica - Certain components confined in the combustion chamber may contain this
potential carcinogen. Improper installation, adjustment, alteration, service or maintenance can
cause property damage, serious injury (exposure to hazardous materials) or death. Refer to section
12 for information on handling instructions and recommended personal protective equipment.
Installation and service must be performed by a qualified installer, service agency or the gas
supplier (who must read and follow the supplied instructions before installing, servicing, or removing
this appliance. This appliance contains materials that have been identified as carcinogenic, or
possibly carcinogenic, to humans).
Warning
Void Warranty - This appliance must have water flowing through it whenever the burner is on or it
will damage the unit and void the warranty. Failure to follow these instructions may result in serious
injury or death.
Warning
Compliance of this boiler with CSA B51 has not been verified due to an exemption provided in a
provincial pressure vessel code. The installation of the gas appliance must conform to the
requirements of this manual, your local authority and the CAN/CGA B149 Installation Codes. Where
required by the Authority, the installation must conform to the standard for Controls and
Safety Devices for Automatically Fired Boilers ANSI/ASME CSD-1.
Caution
Not taking into account the specified maximum calcium and chloride levels for the DHW and
CH circuits will void the warranty.
Commissioning new systems should include flushing the complete system with water.
Before filling the heating system the water hardness must be checked. If above 5 gpg (grains per
gallon) adequate measures must be taken by adding a tested and approved limescale protector,
compatible with all metals and plastics. For continued protection we recommend regular control of
concentration level at least once a year.
For application of frost protection only tested and approved antifreeze, compatible with all metals
and plastics, can be used. For continued protection we recommend regular control of concentration
level and pH, at least once a year.
6
Gasmaster

Part 1 –Introduction
User responsibilities
This manual is for use only by a qualified heating installer / service technician. Only a registered installer /
service technician is allowed to perform the installation of the appliance and the first start-up of the system. Ask
the installer to explain the system to you. Refer to user’s Information manual for user reference. Have this boiler
and its vent system serviced / inspected by a qualified service technician, at least every 12 months.
Warning
Failure to keep the Vent and Combustion Air Intake clear of ice, snow, and other debris may result in
property damage, serious injury, or death.
Warning
Boiler operation
Should overheating occur or gas supply fail to shut off, do not turn off or disconnect electrical supply to
circulator. Instead, shut off the gas supply at a location external to the appliance.
Do not use this boiler if any part has been under water. Immediately call a qualified service technician to
inspect the boiler and to replace any part of the control system and any gas control that has been under water.
Manufacturer conditions
The manufacturer does not accept any liability for damage caused by non-observance of the installation
instructions. Service activities must exclusively be carried out by qualified installers using original parts.
Failure to comply with the above could result in severe personal injury, death or substantial property damage.
Installer responsibilities
A qualified installer is a licensed person who has appropriate training and a working knowledge of the
applicable codes, regulations, tools, equipment and methods necessary to install a boiler or water heater. The
Installer assumes all responsibility for a safe installation and that it meets the requirements of the
instruction manual, as well as National and local codes. It is also the installer’s responsibility to inform the User /
Owner of their obligation with respect to the description under “User Responsibilities”. Failure to follow this
warning could result in fire, serious injury, or death.
This manual contains information of the
boiler, before installing. Perform steps in the order given. Store the manual in the transparent envelope adjacent
to the boiler.
The installer is liable for the installation and the first start-up of the appliance. The installer must observe
the following instructions:
Read the instructions of the appliance in the manuals delivered and observe these.
Install the appliance in compliance with the applicable law and standards: compliance of this boiler with CSA
B51 has not been verified due to an exemption provided in a provincial pressure vessel code.
The installation of the gas appliance must conform to the requirements of this manual, your
local authority, and the CAN/CGA B149 Installation Codes. Where required by the Authority, the
installation must conform to the standard for Controls and Safety Devices for Automatically Fired Boilers
ANSI/ASME CSD-1.
Perform the first start-up and all checks that are required. See section 10 for manual /
automatic calibration.
Explain system functioning to the user.
Warn the user about the obligation to have the appliance serviced and inspected at least every
12 months.
Hand over all manuals to the user and inform the user about the storage location.
The is a “Direct Vent”, Class IV appliance requiring a “Special Venting System”. Vent and Combustion
Air Intake piping must be piped to the outdoors. Failure to follow instructions will result in serious injury or death.
When servicing boiler
To avoid electric shock, disconnect electrical supply before performing maintenance.
When pressure testing boiler
The boiler and its individual gas pressure valve must be disconnected from the gas supply piping system during
any pressure testing of that system at test pressures in excess of 6.5 kPa (0.95 psi). The boiler must be isolated
from the gas supply piping system by closing its individual manual shutoff valve during any pressure testing of
the gas supply piping system at test pressures equal to or less than 6.5 kPa (0.95 psi).
7
Gasmaster
Heating Only R 100H, R 140H, R 200H and Combi R 100 C, R 140C, R 200C
Read all instructions, including this manual and all other information shipped with the
R Series
R Series

Part 1 –Introduction
The is a high efficiency gas wall boiler and is designed for heating a central heating (CH) system
and producing domestic hot water (DHW).
The main functions of the boiler are:
1.) Heating the house: Central Heating (CH)
2.) Producing Domestic Hot Water (DHW)
The total system for CH and DHW-production consists of:
•The boiler;
•Central heating and vent piping;
•Radiators; baseboard; in floor heating and/or hydronic
air handlers
•Hot water taps.
Main parts
The boiler consists of the following main parts:
Figure 1.1
CH Heat exchanger
The heat exchanger located in the middle of the boiler makes sure that the heat that becomes available during
the gas burning process is transferred to the CH circuit.
DHW heat exchanger (only Cxxx types)
The heat exchanger located in the back of the boiler makes sure that the heat that becomes available during
the gas burning process is transferred to the DHW circuit.
Fan
The air necessary for gas burning is propelled by a fan. To save electrical energy the boiler has
been equipped with a high efficiency fan.
Burner
The fan brings forward the gas / air blend necessary for the burning process. The ignition electrode ignites
the blend to drive the burning process.
Gas valve
The gas valve makes sure the exact amount of gas necessary for burning is supplied.
3-way valve and circulation pump
The heat generated by the burning process is used within the CH or DHW circuit. The 3-way valve makes sure
the correct circuit is driven depending on the demand. The pump makes sure the correct amount of water is
delivered through the cold water intake.
Burner control
The burner control drives the general steering and safety system of the boiler
8
R Series
R Series
R Series
R Series

Part 1 –Introduction
Boiler dimensions
All dimensions mentioned in the figures below are in inches.
9

Part 1 –Introduction
Main parts
E
F
G
H
I
J
A: Fan
B:
ignition / ionisation electrode
C C: Flue gas temperature limiter (NTC)
D: Maximum temperature fuse (TF)
E: Manual vent (must open to bleed
air before first igntion. Attach hose
and open until smooth water flows)
F:
Burner and heat exchanger
G: Pump vent
H: CH Supply sensor
I: Magnetite filter
B
J: Hydroblock
K: Connections
L: Internal expansion tank
A
L
Figure 1.2
Hydroblock
B
C
B: 3-way valve
C: Heat exchanger tap water
D: Adjustable by-pass
E: Flow sensor and hot water temperature
sensor
F: Pump
G: Water pressure sensor and return
Sensor (located behind gas valve)
H: Gas valve
I: Filter
J: Drain valve
EDFG H I J
Figure 1.3
10
I
D
K

Part 1 –Introduction
Functionality of main parts
Control
The boiler can be controlled by an on/off thermostat or an OpenTherm® thermostat. The heat
delivery is continuously variable between approx. 14% and 100% of the power of the appliance to obtain
a constant temperature in the house.
Variable speed fan
To save energy, a high efficiency fan (A, figure 1.2) has beenapplied. The fan has a variable speed
and energy absorption. If less heath is needed, the fan rotates slower and uses less energy.
Pump
The has an integrated pump (F, Figure 1.3) that is controlled by the burner control and has a
variable pump speed. The speed of the pump may vary between 60 and 100%. The burner control
determines the speed of the pump by means of the temperature difference between the supply sensor
(H, figure 1.2) and the return sensor (G, figure 1.3).
Domestic hot water production (Cxxx types)
This appliance has a built-in plate heat exchanger (C, figure 1.3) with limited tap water storage. All
connections are internal. While a flow limiter takes care of the maximum hot water quantity, the tap water is
heated up to about 61 °C (142 °F). The boiler starts preparing tap water at a flow of 2.5 l / min
(0.66 gal. / min.) and stops when the flow drops below 1.8 l / min (0.48 gal. / min).
Automatic flue gas temperature limiter
The appliance has been equipped with a built-in protection against too high flue gas temperatures. This
protection closes the gas supply as soon as the flue gas temperature becomes too high, after which the
unit is locked, displaying a fault code.
(Separate) supply and discharge pipes
The optimum connectionfor air supply and flue gas discharge pipe is obtained by using the flue gas
systems as described in this manual. The boiler does not have certification for other flue gas systems.
CH and DHW circuit
Warning
If no diffusion-tight plastic pipes for supply and return are applied for radiators or floor heating, place a
partition betweenthe CH water of the boiler and the water in the system. For example, use a plate heat
exchanger. This prevents contamination of the heat exchanger by, among others, magnetite. When such
a partition is not placed, the guarantee for all parts in the supply and return of the unit will be null and void.
Drain valve
The appliance has a drain valve (J figure 1.3), allowing simple draining of the water.
Pressure relief valve
The supplied PRV appliance needs to be placed directly on the return pipe of the boiler.
Pump vent
The pump vent (G, figure 1.2) has been connected to the vent drain (E, figure 1.4), making visible
any leakage from the vent on the outside of the appliance.
Adjustable by-pass
The appliance also has an internal, permanently adjustable by-pass (D, figure 1.3). The single purpose of
this internal by-pass is to achieve circulation. In case the layout of the installation is such that a situation
could occur in which there is no CH flow, it is mandatory to install an external by-pass at least 6 meters (20
ft) from the boiler.
Option for solar boiler combination
If the boiler is used in combination with a solar tank, the boiler must remain switched on in summer in order
to prevent Legionella bacteria infection. Make sure that the maximum DHW temperature does not exceed 65
°C (149 °F). This may cause a risk of burning for the user. Install an automatic mixer in the hot water pipe
between the boiler and the tap points to avoid this problem.
Frost protection
The appliance has a built-in frost protection that starts the boiler when the CH water temperature drops
below 6 °C (43 °F).
11
R Series
R Series
R Series

Part 2 –Specifications / Technical data
JK
A
B C D
D
E F
G
H
I
Figure 1.4
Table 1.1 Tech Specifications
Character
Description
Connection size (SI, Metric)
Connection size (Imperial)
A
Connection for condensate trap
25
mm
0.98 inch
B
Filling valve
-
-
C
CH supply
22.22 mm
3/4“ CPS (7/8“ outer diameter)
D
-DHW outlet (C models)
22.22 mm
3/4“ CPS, (7/8“ outer diameter)
-Mains water supply for filling loop
(H models)
E
Vent drain for pump air vent
-
-
F
Connection for gas line
-
1/2“ NPT outer pipe thread
G
Flow limiter (C models only)
C models only
Located inside the boiler at outlet H
H
-Cold tap water (C models)
22.22 mm
3/4“ CPS, (7/8“ inch outer
-Tank supply hot (H models)
diameter)
I
-CH return (C model boilers)
22.22 mm
3/4“ CPS, (7/8“ inch outer
-CH return and Tank Return (H
diameter)
Model boilers)
J
Concentric vent connection OR
Concentric 80/125mm
Concentric 3”/ 5”
2 pipe exhaust connections
80
mm
3” (need adapter if using (C)PVC
K
Air intake (when using a 2 pipe syst)
80mm
3” (need adapter if using (C)PVC
General
Metric /
Eco-King C140, H140
Eco-King C200, H200
Imperial
Dimensions (h x
mm / inch
695x480x410 /
695x480x410 /
695x480x410 /
w x d)
27.4x18.9x16.1
27.4x18.9x16.1
27.4x18.9x16.1
Weight (empty)
kg / lb
31 / 68
34 / 75
37 / 82
Maximum absorbed electric
W / Btu/h
155 / 529
155 / 529
200/ 628
power
DHW operation
Nominal load
Btu/h
16-99,000 16-105.000
19.800-135.000
26.900-185.000
Tap quantity at
2.0 2.1
2.6
4
60°C (dT=50K)
gal/min
Tap quantity at
3.6 3.7
4.4
6.1
40°C (dT=30K)
gal/min
Hot tap water
°C / ° F
61
–142 61-142
61 - 142
61
–142
DHW / TAP operation*
(connected to an external hot
water tank)
Input (0-2000ft) Gross calorific
value
BTU/h
16.000-105.000
19.800-135.000
26.900-185.000
CH operation
Nominal input (0-2000 ft) Gross
calorific value
Btu/h
16.000-89.000 / 16.000-90.800
19.800-113.600
26.900-159.000
Max Output (0-2000 ft) at 50/30
°C**
Btu/h
85.000
106.500
150.000
* MAX DHW Input levels listed occur in both C (combi) & H model boilers when producing hot water. H-model connected to an external hot water tank.
** Output in condensing mode 12
R 100
R 140
R 200
R 100C
R 140C
R 200C
R 100H
R 140H
R 200H
R 100
R 140
R 200

Part 2 –Specifications / Technical data
High Altitude Operation
The boiler is designed to operate at its maximum listed capacity in installations less than or equal to 610 m
(2000 ft) above Sea Level. Since the density of air decreases as elevation increases, maximum specified capacity
should be de-rated for elevations above 610 m (2000 ft) in accordance with the table underneath.
Elevations
610 m (2000 ft)
914 m (3000 ft)
1219 m (4000 ft)
1372 m (4500 ft)
De-rate by 3,6%
De-rate by 5,4%
De-rate by 7,2%
De-rate by 8,1%
De-rating is performed automatically by the appliance via the electronic gas-air ratio controller.
Warning
Combustion –At elevations above 610 m (2000 feet), the combustion of the appliance must be checked with
acalibrated (altitude corrected) combustion analyzer to ensure safe and reliable operation. It is the Installers
responsibility to check the combustion of the appliance. Failure to follow these instructions may result in
property damage, serious injury, or death.
Table 1.1 Technical specifications (continued)
13
Other technical
data
Allowed
Pa / Psi
200 / 0.029
200 / 0.029
200 / 0.029
resistance of flue
gas system
PH value of the
4 - 5.5
4 - 5.5
4 - 5.5
condensed water
Available CH
mH2O / kPa
2.1 / 21
1.9 / 19
1.5 /15
pump pressure at
dT20 ºC
Max resistance
kPa
50
70
100
DHW
Maximum supply
°C / ° F
85 / 185
85 / 185
85 / 185
temperature
Filling pressure
bar (kPa) / Psi
1.5 - 2.5 (150 - 250) /
1.5 - 2.5 (150 - 250) /
1.5 - 2.5 (150 - 250) /
CH part min./
21.8 –36.3
21.8 –36.3
21.8 –36.3
max.
Connection
bar (kPa) / Psi
0.2 - 10 (20 - 1000) / 2.9
0.2 - 10 (20 - 1000) 2.9
0.2 - 10 (20 - 1000) 2.9
pressure sanitary
- 145
- 145
- 145
water min./max.
Volume of tap
liter / gal
0.3 / 0.08
0.5 / 0.13
0.5 / 0.13
water heat
exchanger
Max. Calcium
Ppm / mg/l
50
50
50
level (CaCo3)
DHW at 60 °C*
Max. water
Gpg
2.9
2.9
2.9
hardness( CaCo3)
CH / DHW
Max. chloride
Ppm / mg/l
150
150
150
level DHW
Allowed pH value
pH
7 - 8.5
7 - 8.5
7 - 8.5
water
CO2 content of
%
9,0 +/- 0,3
9,0 +/- 0,3
9,0 +/- 0,3
flue gas
Temperature flue
°C / °F
85 / 185
85 / 185
85 / 185
gas at 176 / 140
°F (80/60 °C) (at
an ambient
temperature of
68°F (20 °C))
Item
NOxemission,
mg/kWh/
< 15 /
< 15 /
< 15 /
RAL UZ 61
ppm
< 30
< 30
< 30
CO emission,
mg/kWh/
< 20 /
< 20 /
< 20 /
RAL UZ 61
ppm
< 50
< 50
< 50
R 100
R 140
R 200
R 100
R 140
R 200
R Series
R Series

Part 3 - Appliance location
In all cases, the must be installed indoors in a dry location where the ambient temperature must be
maintained above freezing and below 38°C (100°F). Gas components must be protected from dripping, spraying
water, or rain during operation and servicing. Consider the proximity of system piping, gas and electrical supply,
condensate disposal drain, and proximity to vent termination when determining the best appliance location.
Warning
Water or flood damaged components must be replaced immediately with new factory approved components
as failure to do so may result in fire, serious injury, or death.
Location checks
The wall must be strong enough to carry the weight of the boiler. The boiler shall be installed such that
the gas ignition system components are protected from water (dripping, spraying, rain, etc.) during boiler
operation and service(circulator replacement, condensate trap, control replacement, etc.). Select a place where
possible noise production by the boiler is not inconvenient. Both the air supply and the flue gas discharge pipe
(concentric system) must be connected to the exterior wall or to the roof surface (use parts specified in section 4).
Furthermore, in case of Cxxx types, install the boiler as close as possible to the most regularly used tap points, to
make sure that the DHW pipes are not unnecessary long. This reduces the waiting time for hot water and
unnecessary waste of water.
Warning
The boiler must not be installed on / nearby carpeting.
Check the availability of the following provisions:
-Water supply;
-Venting connection;
-Gas supply;
-Electrical power (grounded);
-A connection for a condensate trap;
-A wall able to carry the appliance’s weight.
Remove any combustible materials, gasoline and other flammable liquids from the installation area.
If the boiler is to replace an existing boiler, check for and correct any existing system problems such
as system leaks.
Appliance Area Ventilation Air Openings
If appliance area clearances are less than the recommended clearances specified in Table 3-1, the appliance
area must be ventilated (Figure 3.1). Each ventilation air opening must meet the minimum requirements of 22 cm2
per kW (1 in2per 1000 Btu/hr) but not less then 645 cm2 (100 in2). The lower ventilation opening must be located
within 6” of the floor while the upper opening must be located 6” from the top of the space.
Notice
If the "Appliance Area" does not meet all of the recommended clearances listed in Table 3-1, it is considered
a Closet or Alcove. In Canada closet and alcove installations require approved vent pipe, fittings, cements,
and primers.
Table 3-1 Minimum clearances for installation and service
Model
Clearances
Dimensions –mm (inches)
no.
Bottom
Front
Top
Left Side
Right Side
Rear
Vent pipes
and hot
water pipes
Minimum mm /
280
457
(18")1
152
(6")
13 (0.5")
13 (0.5")
0 (0")
30 (1.2") 2
inch.
(11")
Recommended
457
457
(18")
1
152
(6")or
305 (12")
305 (12")
0 (0")
30 (1.2")
2
(18")
or more
more
or more
or more
or more
Minimum
280
457
(18")1
152
(6")
13 (0.5")
13 (0.5")
0 (0")
30 (1.2") 2
(11")
Recommended
457
457
(18")
1
152
(6")) or
305 (12")
305 (12")
0 (0")
30 (1.2")
2
(18")
or more
more
or more
or more
or more
Minimum
280
457
(18")1
152
(6")
13 (0.5")
13 (0.5")
0 (0")
30 (1.2") 2
(11")
Recommended
457
457
(18")
1
152
(6")) or
305 (12")
305 (12")
0 (0")
30 (1.2")
2
(18")
more
or more
or more
or more
1152 (6") if front surface is removable allowing 457mm (18") clearance (i.e. closet installation). See ventilation air opening dimensions in figure 3-1
2Surrounding. 14
R Series
R Series
R Series
R 100
R 140
R 200

Part 3 - Appliance location
Closet Installations
For closet installations, it is necessary to provide two ventilation air openings as shown in Figure 3-1 each
providing a minimum area equal to 22 cm2per kW (1 in2per 1000 Btu/hr), but not less then 645 cm2(100 in2)
and within 152 mm (6”) of the top and bottom of the closet door. See Table 3-1 for minimum recommended
clearances.
Alcove Installations
Alcove installations have the same minimum clearances as closet installations, except the front must be
completely open to the room at a distance no greater then 457 mm (18”) from the front of the appliance and the
room is at least three (3) times the size of the alcove. Provided these conditions are met, the appliance
requires no extra ventilation air openings to the space. See Table 3-1 for minimum recommended clearances.
Residential Garage Installations
When installed in a residential garage, mount the appliance a minimum of 457 mm (18”) above the floor. Locate or
protect the appliance so it cannot be damaged by a moving vehicle. Check with your local authorities for
Figure 3.1 Closet installation minimum clearances
Top view
30 mm (1.2”) surrounding
clearance for concentric
vent pipe
152 mm (6”) max.
above vent opening
Left and right Side 13 mm (0.5”)
Front 152 mm (6”)
Removable Surface or Closet Door
Top 152 mm (6”)
Ventilation Air Opening
22 cm2per kW (1 in2per 1000
Btu/hr), min. 645 cm2(100 in2)
Ventilation Air Openings
are not required if the
appliance area meets
the listed Recommended
Clearances in Table 3-1.
152 mm (6”) max.
below vent opening
Bottom view
30 mm (1.2”) surrounding
clearance for hot water pipes
Closet/alcove installations in Canada require approved concentric systems or
Warning vent and air-inlet pipe, fittings, cements and primers. Failure to comply may result
in damage or serious injury.
15

Part 3 - Appliance location
Prior to wall mounting
Care must be taken to place the boiler in a safe location prior to installation on the wall to prevent damage to
the mechanical connections.
The delivery contains:
The boiler; Installation manual for the installer; User manual for the homeowner;
A wall support bracket;
A condensate trap with swivel nut;
A pressure relief valve.
An (internal) expansion tank
Caution
Cold weather handling
If the boiler has been stored in a cold location below -18 °C (0°F) before installation, handle with extra care
until the plastic components come to room temperature.
Wall mounting
Determine and mark the location for the CH supply and discharge pipes. Secure the wall mounting bracket to
a solid wall using field supplied lag screws (anchors when mounting on a concrete wall), adequate to support
the weight of the appliance.
Ensure the bracket is mounted in level position. Refer to Table 1.1 for the appliance weight.
Mount the appliance to the bracket by aligning the slot in the back of the appliance with the hook protruding
from the wall bracket. The top of the slot must rest at the bottom of the groove in the lower hooked part of the
wall mounting bracket.
In unusually dirty or dusty conditions, care must be taken to keep heater cabinet door in place at all times.
Failure to do so VOIDS WARRANTY!
Figure 3.2 wall mounting
16

Part 4 - General venting
The boiler is a direct vent, category IV, appliance with sealed combustion requiring certain venting
systems. All combustion air is drawn directly from outdoors, with some specific exceptions. The housing closes the
appliance on the rear plate air-tightly. All products of combustion are vented directly outdoors. Both the Vent and
Air-Intake piping should be piped to the outdoors, using the vent material and rules outlined in this section. Under
no conditions may this appliance vent gases into a masonry chimney. Safety provisions with regard to (too) high
flue gas temperatures to protect synthetic intake / discharge piping have been provided within the boiler.
The safety system shuts down the gas supply in case the temperature of the flue gasses becomes too high, after
which the appliance will not run until re-started. Installations must comply with CSA B149.1 and local requirements.
Warning
The boiler cannot share a common vent or air-intake with multiple appliances. Failure to comply will result
in serious injury or death.
The appliance does not use air (Oxygen) from the installation room, except with specific exceptions as
noted later in this manual. The front cover closes the housing air-tight making sure air is only supplied by the vent air
intake. Therefore make sure the front cover always has been placed in its position during operation of the appliance.
Shown graph describes the relationship between system power (BTU/hr) and resistance (Psi) of the supply
and discharge. Till a pressure of 200 Pa (0.030 Psi), power will remain the same. Bigger resistance causes
power decrease.
90000
80000
70000
60000
50000
40000
30000
20000
10000
Power
0
1
0,015
0,0302
0,0453
0,058
4
0,073
5
Figure 4.1 Pressure resistance vs power Pressure
Have horizontal runs sloping backwards to the boiler not less than 5 cm / mtr (0.6 inch / feet) from the terminal to
the boiler l to prevent condensate moisture from running into the air intake piping.
Combustion Air-Intake Contamination
Be careful not to locate the Air-Intake termination in an area where contaminants can be drawn in and used for
combustion. Combustion air containing dust, debris or air-borne contaminants will drastically increase the required
maintenance and may cause a corrosive reaction in the Heat Exchanger which could result in premature failure,
fire, serious injury, or death. See Table 4-1 for a list of areas to avoid when terminating air-intake piping. These
same conditions should be avoided when drawing intake air from boiler room.
Table 4-1 - Corrosive Products and Contaminant Sources
Products to Avoid
Contaminated Sources to Avoid
Antistatic fabric softeners, bleaches, detergents,
Laundry facilities
cleaners
Perchloroethylene (PCE), hydrocarbon based
Dry cleaning facilities
cleaners
Chemical fertilizer, herbicides/pesticides, dust,
Farms or areas with livestock and manure
methane gas
Paint or varnish removers, cements or glues, sawdust
Wood working or furniture refinishing shops
Water chlorination chemicals (chloride, fluoride)
Swimming pools, hot tubs
Solvents, cutting oils, fibreglass, cleaning solvents
Auto body or metal working shops
Refrigerant charge with CFC or HCFC
Refrigerant repair shops
Permanent wave solutions
Beauty shops
Fixer, hydrochloric acid (muriatic acid), bromide,
Photo labs, chemical / plastics processing plants
iodine
Cement powder, crack fill dust, cellulose, fibre based
Concrete plant or construction site
insulation
17
R Series
R Series
R Series
R Series

Part 4 - General venting
Warning
Do not store or use gasoline or other flammable vapors and liquids in the
vicinity of this or any other appliance. Failure to follow instructions may
result in serious injury or death.
Warning
Only use vent and air systems as specified in this manual.
Notice
Venting Options - Due to potential moisture loading (build-up) along the exterior wall, sidewall venting may not be
the preferred venting option. Be aware of this possibility when choosing sidewall or roof termination
Installation instruction for concentric vent and air system - General
Examine all components for possible shipping damage prior to installation;
Proper joint assembly is essential for a safe installation. Read all instructions before beginning
the installation and follow these instructions exactly as written;
Check the integrity of joints upon completion of assembly;
This venting system must be free to expand and contract under normal operation;
This venting system must be supported in accordance with these instructions;
Assure unrestricted vent movement where required through walls, ceilings and roof penetrations; Do
not mix pipe, fittings or joining methods from different vent system manufacturers.
Do not use any type of glue material to join parts with this venting system.
Caution
Always use genuine roof or wall terminations for concentric installs. Terminating the vent pipe or air inlet with
elbow or tee for termination is prohibited when using concentric venting. Single pipe terminations permit elbow or
tee as termination as explained later in the manual. Always refer to the installationmanual(s) delivered with the
Parts. Instructions included with vent terminal materials contain more detailed instructions.
These systems are intended for residential and commercial installations. They may be used in combination with
ANSI category II and IV gas-burning appliances. The maximum positive pressure is 8 inches w.c. The maximum
flue gas temperature of the appliance is 110°C (230°F) (ULC-S636-Class IIC).
18

Part 4 - General venting
Concentric installation
These instructions must be followed together with the instructions in the manual that is supplied with the roof or
wall terminal. That manual gives special instructions for applications, pressure drops, maintenance and mounting of
the complete vent system. Before installing the Concentric Vent & Air System, read and follow the instructions of
the manual that is supplied with the terminal
Caution
Do not use grease or other lubricant on the vent seals. Only water may be used for this purpose.
Grease or other lubricant can make the seal brittle or it can result in tears in the surface of the seal, this will result
in flue gas leakage.
Installation:
1. Start at the appliance flue connector, install the system with the female ends (with the integral seal) pointing
away from the appliance. Fasten the flue gas system as soon as possible to the wall so that a tight connection of
the flue gas system to the boiler is guaranteed and that it will be impossible to get clearances between the flue gas
system and the boiler due to any unexpected cause.
2. Check that the seal is retained correctly in the groove section as described in 6b.
3. Take precautions with horizontal installation, the slope must be at least 5 cm/mtr (0.60 inch/feet) towards
the boiler.
4. Shortening this type of concentric is not allowed, use when necessary a telescopic or special Cut-able
Concentric Vent & air section, these sections are telescopic over a length of 330 till 400 mm (13 till 17.3 inch).
5. First, mount the brackets on a fixed part of the building. (i.e. wall).
6. Brackets must be fixed as follows, see figure 4.2:
6a. Straight vent sections that are installed vertical must be supported with brackets every 6 feet (2 m) or less,
see figure 4.2, dimension B.
6b. Straight vent sections installed with a slope must be supported with at least one bracket per section, this
brackets must be installed at a maximum distance of 15 cm (6 inch) from the female end, see figure 4.2,
dimension A.
6c. Bends and T pieces are sufficiently supported when a bracket is fixed at the female end of the
connected straight.
Figure 4.2 Bracket supporting
7. Mount the vent elements in the brackets.
8. It is recommended to rotate the joints slightly when assembling them. Only use water for easier assembling.
9. Take care that the load of the flue system is not supported on the appliance.
10. The outer vents must be secured with the 2 provided self-tapping screws. See figure 4.3. Use a low
torque setting to drill the screws into the vent system.
11. Fix the clamp around the flue.
19

Part 4 - General venting
Figure 4.3 Bracket securing
Warning
Use only the provided self tapping screws, these screws have the correct length. Using screws with a longer
length will damagethe actual PP vent.
Cut-able installation These instructions must be followed together with the instructions in the manual that is
supplied with the roof or wall terminal. That manual gives special instructions for applications, pressure drops,
maintenance and mounting of the complete vent system. This product is a cut-able concentric vent & air section
that must be installed as part of the concentric vent and air system. It’s not allowed to build a complete system
with cut-able sections only. Before installing the cut-able concentric vent section, read and follow the instructions
of the manuals that are supplied with the terminal and the (concentric) vent air system.
Installation
1. Measure the gap between the two parts between which the cut-able concentric vent section must be installed.
2. Cut the concentric vent section with regard to the instructions on the adhesive on the product see also figure
4.4.
Figure 4.4 Vent section cutting
20
This manual suits for next models
6
Table of contents
Other Gasmaster Boiler manuals
Popular Boiler manuals by other brands

ICI Caldaie
ICI Caldaie SIXEN 350 Instructions for installation, use and maintenance manual

DeDietrich
DeDietrich NeOvo EcoNox EFU 22 user guide
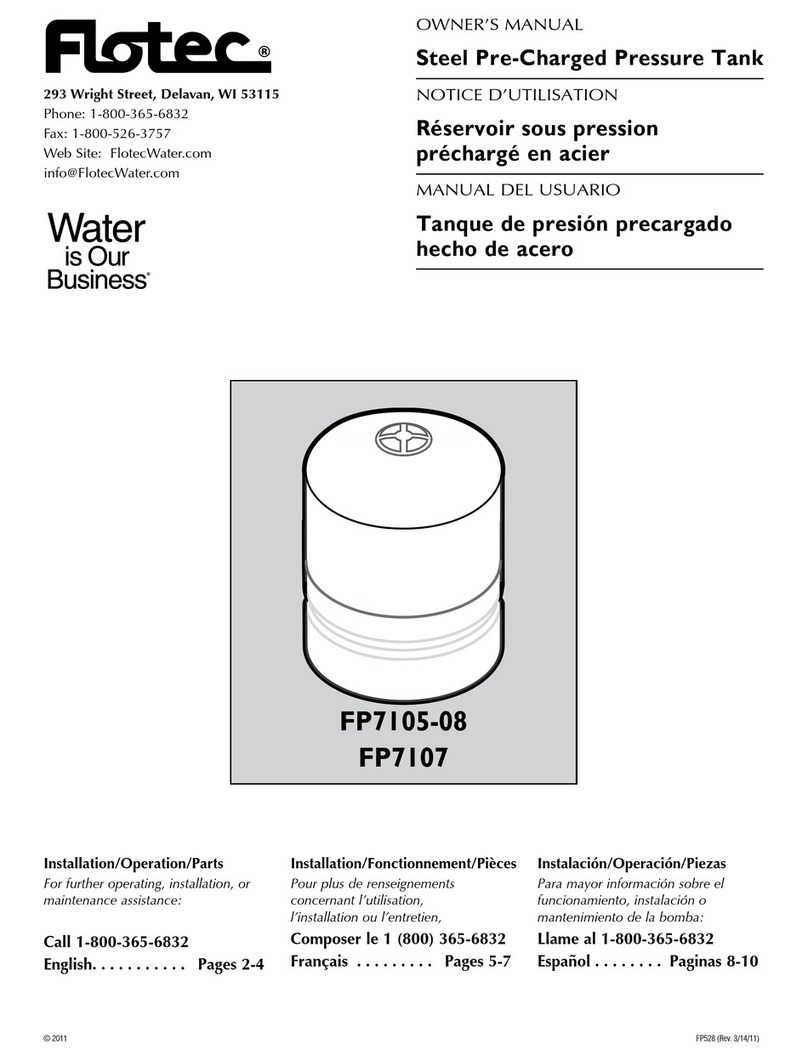
Flotec
Flotec FP7105-08 owner's manual

Navien
Navien NCB300-28K Installation & operation manual
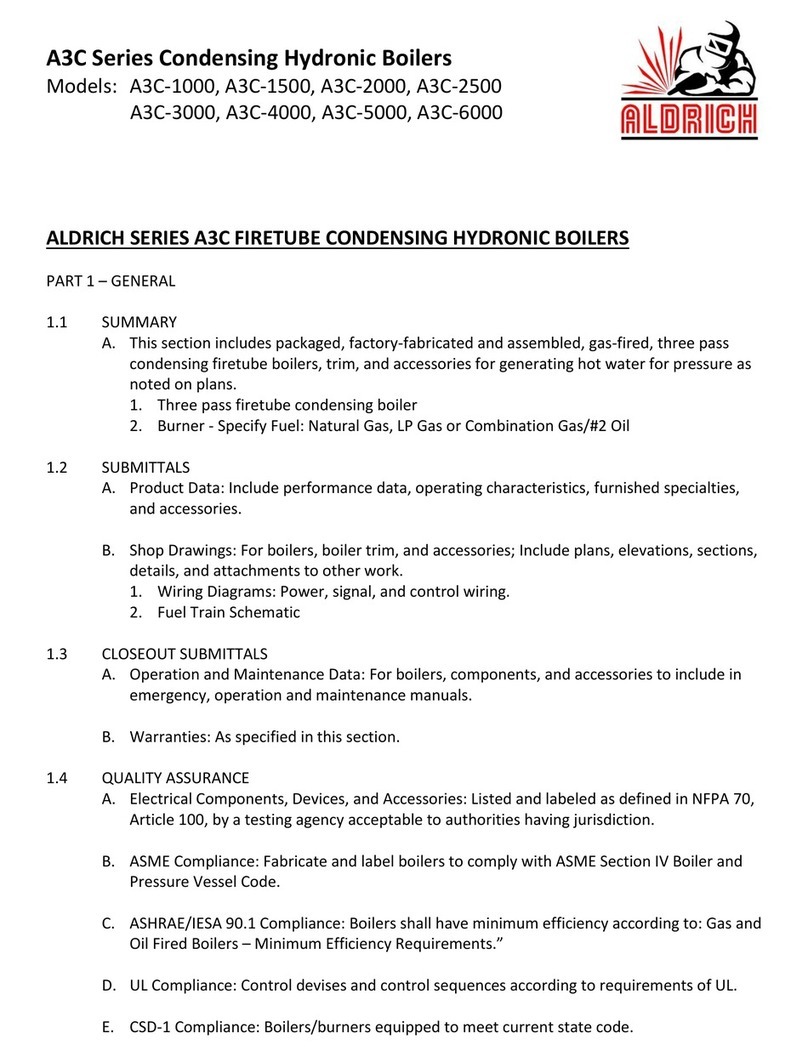
Aldrich
Aldrich A3C-1000 Product data
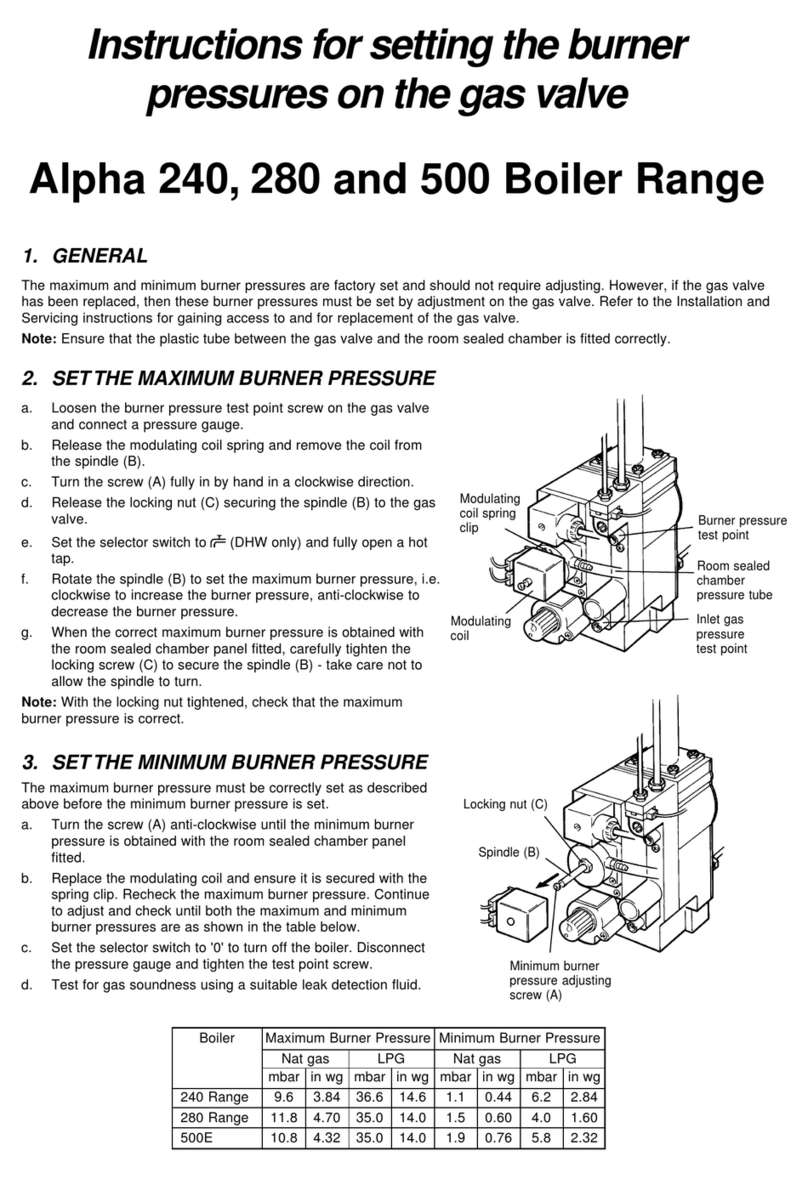
Alpha
Alpha Alpha 240 Boiler Range Function guide
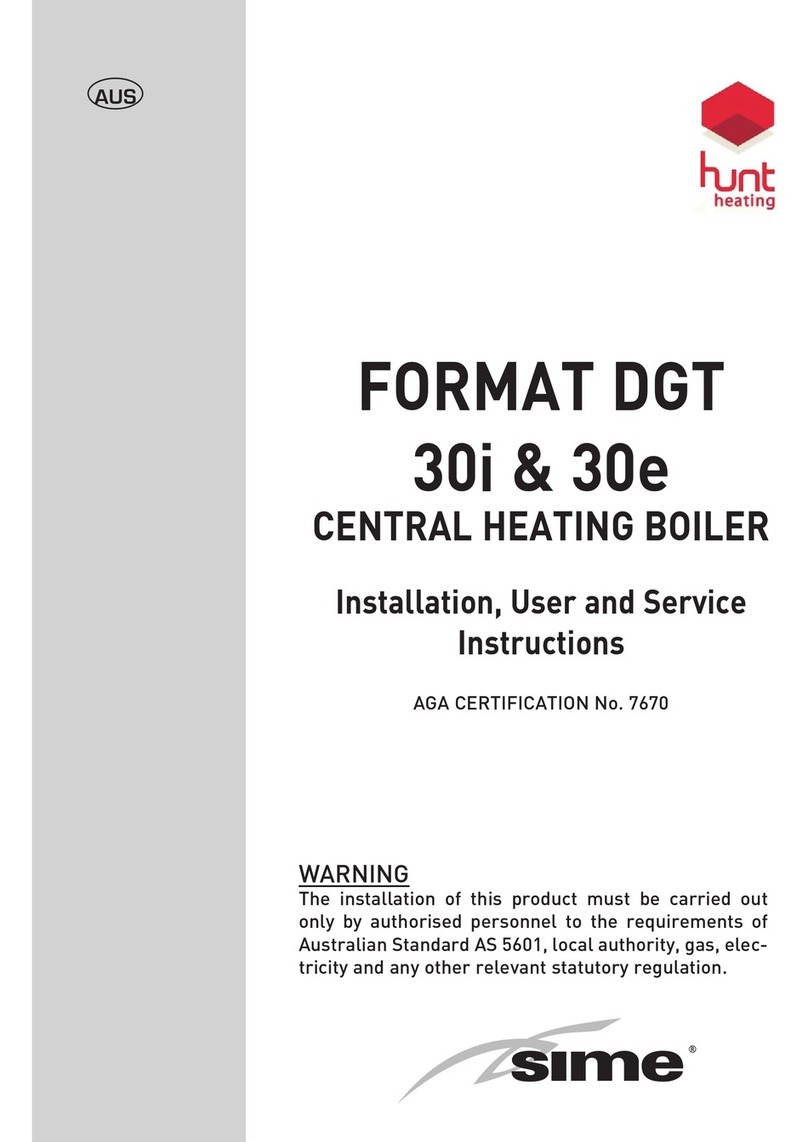
Sime
Sime FORMAT DGT 30i Installation, user and servicing instructions
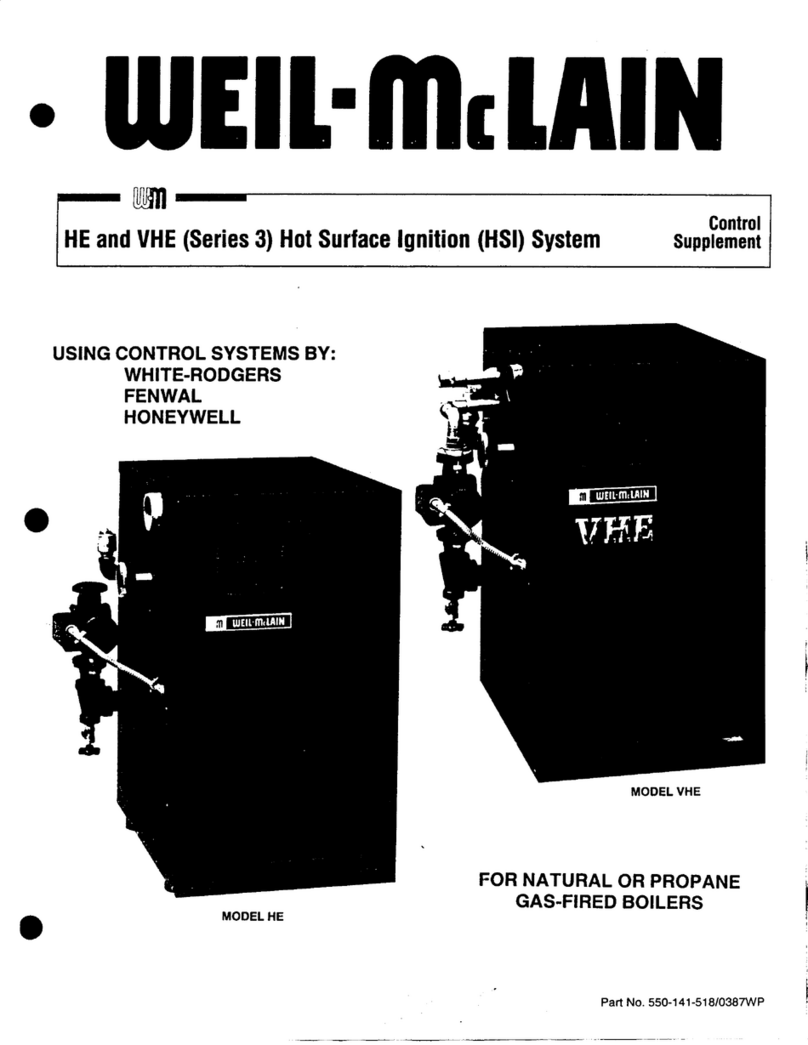
Weil-McLain
Weil-McLain VHE Series 3 Control supplement

Sime
Sime Dewy Equipe P100 Box manual
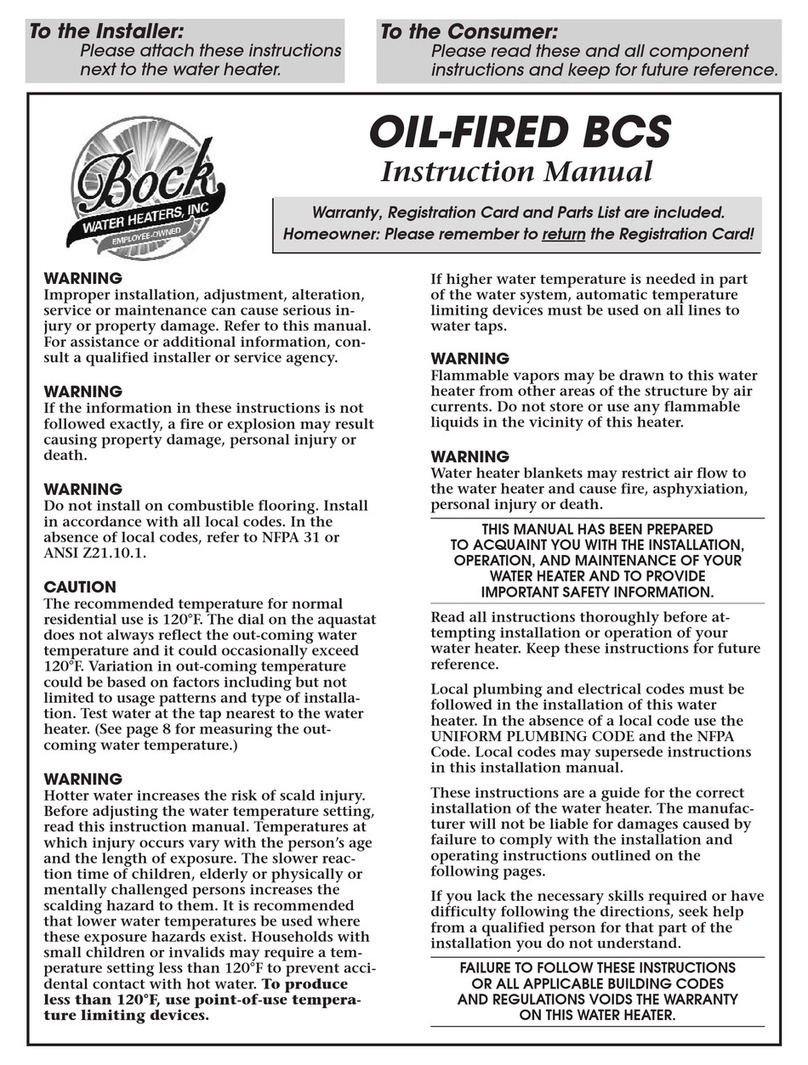
BCS
BCS Oil-Fired instruction manual
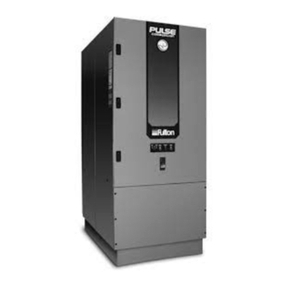
FULTON
FULTON PulseHW Series Installation, operation and maintenance manual
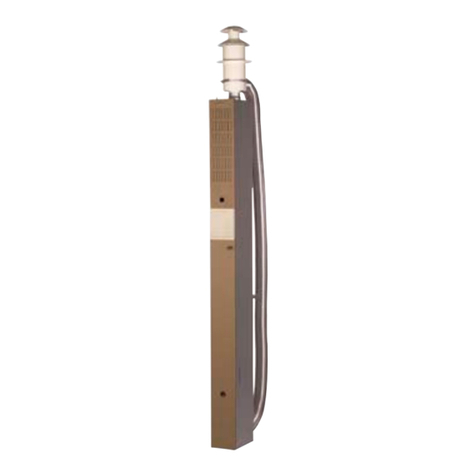
Alde
Alde Comfort 2923-2928 Service manual