Gradient syncFURNACE mOD-200 User manual

syncFURNACE OD Instruction & Installation Manual –Rev 09 Pg. 1 of 81
Combination Gas-Fired Water Heater / Central Air Fan-coil Unit
Model >
IMPORTANT:
•Be sure to read these instructions and fully understand prior to
installing this product.
•The wetted surface of this product contacted by consumable water
contains less than one quarter of one percent (0.25%) of lead by
weight.
•After installation, keep instructions near product for future reference.
•This product must be installed and serviced by a properly trained &
licensed professional heating contractor –FAILURE TO COMPLY
WILL VOID ALL PRODUCT WARRANTY
•It is the responsibility of the installation contractor (upon completion
of the installation) to explain to the Owner or Operator of the heating
system how to correctly use as per these instructions and local code
requirements. Be sure that they are familiar with all heating system
equipment as well as safety devices, shut-down procedure(s) and
the need for professional service annually before the heating season
begins.
CAUTION:
•After installation is complete it is the responsibility of the Owner or
Operator to ensure vent terminal(s) is cleared from snow, ice and/or
other debris.
Installation & Operation
Manual
www.gradientthermal.com
mOD-200
ANSI Z21.10.3 | CSA 4.3
UL 1995 | CSA C22.2 No. 236
Gas Water Heaters, Volume III Storage Water
Heaters, with Input Ratings Above 75,000 BTU per
Hour, Circulating and Instantaneous
Heating and Cooling Equipment
FURNACE + WATER HEATER

syncFURNACE OD Instruction & Installation Manual –Rev 09 Pg. 2 of 81

syncFURNACE OD Instruction & Installation Manual –Rev 09 Pg. 3 of 81

syncFURNACE OD Instruction & Installation Manual –Rev 09 Pg. 4 of 81
Index
1. Guideline to Symbols > .......................................................................................................... 5
2. General and Safety Instructions > ......................................................................................... 6
3. Included in Packaging >......................................................................................................... 6
4. Regulatory & General Installation Requirements > ................................................................ 7
6. Product Information & Specifications > ................................................................................. 8
Specifications: ..........................................................................................................................10
Model Number Identification: ...................................................................................................... 11
Components: ............................................................................................................................ 11
7. Dimensions and Connection Descriptions >.......................................................................... 12
8. Installation > ....................................................................................................................... 16
Minimum Clearances:................................................................................................................. 16
Mechanical Room & Combustion Air Supply Requirements: .............................................................16
General Venting: ....................................................................................................................... 17
Acceptable Vent Configurations: ..................................................................................................18
Acceptable Vent Materials Equivalent Lengths: ..............................................................................18
Room Dependent Combustion Air Supply: .................................................................................... 21
Connecting Vent Pipe to syncFURNACE OD: ..................................................................................22
Venting Termination Options: .....................................................................................................23
Venting Termination Clearances: ................................................................................................. 26
Mandatory Venting Pre-Fire Procedure: ........................................................................................ 27
Condensation Trap: ................................................................................................................... 28
Gas Line Connection: ................................................................................................................. 30
Plumbing syncFURNACE OD: ....................................................................................................... 31
Water Supply Quality Requirements: ........................................................................................... 36
Purging Air From syncFURNACE OD: ............................................................................................ 37
Connecting Control (Low-voltage) Wiring: .................................................................................... 38
Connecting Main Power (115Vac) Wiring: ..................................................................................... 40
Fan-Coil Installation: .................................................................................................................42
Control Setup: .......................................................................................................................... 45
9. Commissioning > ................................................................................................................. 52
Testing Water Pressure: .............................................................................................................52
Testing No Gas Safety: ..............................................................................................................52
Testing Gas Inlet Pressure:.........................................................................................................53
Testing Combustion: ..................................................................................................................57
10. Maintenance & Service >.................................................................................................... 59
Burner Cleaning [At Minimum, Perform Annually]:......................................................................... 59

syncFURNACE OD Instruction & Installation Manual –Rev 09 Pg. 5 of 81
Clean Combustion Chamber [At Minimum, Perform Annually]: ........................................................60
Check and Clean Condensation Line and Trap [At Minimum, Perform Semi-Annually]:........................ 60
Flue Gas Vent & Air Intake Sealing [At Minimum, Perform Annually]: ...............................................61
Igniter & Flame Sensor Electrodes [At Minimum, Perform Annually]: ...............................................61
Burner Flame [At Minimum, Perform Annually]: ............................................................................ 61
Additional Service and Maintenance Inspections:...........................................................................61
11. Troubleshooting >.............................................................................................................. 62
Appendix A: Internal Wiring Diagram > ................................................................................... 65
Appendix B: Sequence of Events > ........................................................................................... 66
Appendix C: Replacement Parts List >...................................................................................... 67
Appendix D: Handling Instructions for Refractory Cement Fibers (RFC) > ............................... 69
Appendix E: Annual Inspection & Maintenance Record > ......................................................... 70
Appendix F: Internal Pump Specifications > ........................................................................... 72
Appendix G: Heat Exchanger Specification >........................................................................... 73
Appendix H: Fan-Coil PERFORMANCE > .................................................................................... 74
5L MODEL: ............................................................................................................................... 74
10L MODEL: .............................................................................................................................75
14L MODEL: .............................................................................................................................76
18L MODEL: .............................................................................................................................77
22L MODEL: .............................................................................................................................78
Appendix I: Temporary Construction Heat > ............................................................................ 79
Appendix I: Example Humidifier Wiring Diagram > .................................................................. 80
1. GUIDELINE TO SYMBOLS >
!WARNING
!DANGER
!CAUTION
!NOTE
Indicates damage to
property may occur
Indicates possible minor to
medium personal injury may
occur
Indicates possible severe
personal injury may occur
Indicates possibility that
loss of life may occur

syncFURNACE OD Instruction & Installation Manual –Rev 09 Pg. 6 of 81
2. GENERAL AND SAFETY INSTRUCTIONS >
1. After receiving the product, inspect the unit for any possible physical damage that may have
occurred during transportation.
2. These instructions must be kept at installation site. Additional copies are available - on request -
from Gradient Thermal Inc.
3. Installation, Start-up & Service must be performed with due care and attention and must only be
performed by competent, qualified, licensed and trained heating contractor(s).
4. Always be safety conscious. Never risk your health or your life. Your safety and the safety of the
dwelling occupants must always take highest priority.
5. Failure to read and comply with all instructions and applicable National and local codes may result
in hazardous conditions that could result in property damage and injury to dwelling occupants
which in extreme cases may result in death.
6. Improper installation, service and/or maintenance can cause flue products to flow into living space.
Flue products contain poisonous carbon monoxide. Properly install product to minimize carbon
monoxide output and to ensure safe operation to prevent flue products from entering living space
by following the venting installation instructions in this manual and installation
instructions provided by venting material manufacturer.
7. Never operate this product without a venting system. An improper venting system can cause
carbon monoxide poisoning.
8. Information contained inside this and other related product documentation must be read and
followed. Failure to do so may result in loss of warranty coverage. Warranty will be rendered null
and void.
3. INCLUDED IN PACKAGING >
syncFURNACE OD qty –1
Document Package qty –1 replacement part no. 110184
Outdoor Sensor qty –1 replacement part no. 110182
!DANGER
!WARNING
Should overheating occur or the gas supply fail to shut-off, DO NOT turn off or
disconnect the electrical supply to the pump. Instead, shut-off the gas supply at a
location external to the appliance.
DO NOT use this product if any part has been under water. Immediately call a qualified
service contractor to inspect and if necessary replace any affected electrical or gas control
component(s)
!WARNING
REFRACTORY CEMENT FIBER (RFC) > Certain components confined in the combustion
chamber may contain this potential carcinogen. Improper installation, adjustment,
alteration, service or maintenance can cause property damage, serious injury (exposure to
hazardous materials) or death. Refer to APPENDIX D for information on handling
instructions and recommended personal protective equipment.

syncFURNACE OD Instruction & Installation Manual –Rev 09 Pg. 7 of 81
4. REGULATORY & GENERAL INSTALLATION REQUIREMENTS >
1. syncFURNACE OD must be installed in accordance with the instructions and details outlined in this
manual. Failure to comply will result in product warranty to be null and void.
2. READ AND FOLLOW ALL SAFETY WARNINGS
3. Failure to remove or maintain the area where the product will operate free of combustible
materials, gasoline and other flammable liquids or vapors can result in severe personal injury,
death, or substantial property damage.
4. All applicable local, state, national and provincial codes, ordinances, regulations, and laws must be
observed.
5. For Massachusetts installations, code requires the product be installed by a licensed plumber or
gas-fitter.
6. The installation of this product must conform to the requirements of the local authority having
jurisdiction or, in the absence of such requirements, to the National Fuel Gas Code, ANSI
Z223.1/NFPA 54, and/or Natural Gas and Propane Installation Code, CAN/CSA B149.1.
7. All electrical wiring and grounding must conform to the requirements of the local authority having
jurisdiction and/or, in accordance to the latest edition of CSA 22.1 Part 1 of the Canadian Electric
Code for Canadian installations or the National Electric Code ANSI/NFPA No. 70 for U.S.
installations.
8. Water temperatures over 120°F can cause severe burns instantly or death from scalding.
9. This product is equipped with a direct spark ignition device.
10. This product is supplied with a factory installed (inside the cabinet) pressure relief valve rated to
150psig (10 bar).
11. Install CO detectors as per the requirements of your local authority having jurisdiction.
12. The controller has a built-in sensor that will automatically detect the installations altitude and make
the appropriate adjustments to operate the water heater up to 4,500 feet (1372m) above sea level
without de-ration.
13. This product is heavy –requires minimum two people to lift & move in place. Failure to comply
may result in personal injury.
14. Product is for indoor installations only. Install near a floor drain. All components must be
protected from potential water damage. Prevent external dripping and/or spraying water from
coming in contact with components inside this product –during both installation, service and
maintenance. Failure to comply may result in serious injury and/or loss of warranty coverage.
Warrant may be rendered null and void.
15. The product should be installed in a location where leakage within the unit or at its piping
connections will not result in damage to the area adjacent to the appliance or to lower floors of the
structure. When such locations cannot be avoided, it is recommended that a suitable drain pan,
adequately drained, be installed under the product. GRADIENT THERMAL INC. IS NOT LIABLE
FOR ANY WATER DAMAGE. IT IS INSTALLER AND HOME OWNERS RESPOSONSIBILITY
TO ENSURE ADEQUATE DRAINING IS AVAILABLE IN THE AREA ADJECENT TO THE
PRODUCT.
16. When syncFURNACE OD is used with an air conditioner, syncFURNACE OD MUST be installed so
that the indoor A/C coil is DOWNSTREAM from the syncFURNACE OD supply duct to avoid freeze-
up of the water coil inside syncFURNACE. If duct is installed in a parallel flow arrangement, a
damper (or other means to control the flow of air) must adequately prevent chilled air from
entering syncFURNACE OD. If the damper is manually operated, it must be equipped to prevent
operation of the cooling unit, unless it is in the full cooling mode.
17. Ensure that condensate fluid from A/C coil CANNOT leak back into and cause damage inside
syncFURNACE OD.

syncFURNACE OD Instruction & Installation Manual –Rev 09 Pg. 8 of 81
18. The maximum allowable ambient temperature of the room where this product will be installed is
104°F (40°C).
19. Suggested list of codes and standards for the United States and Canada -
a. General Installation:
i. - Installation of Air Conditioning and Ventilation Systems NFPA 91 (latest edition).
b. Duct Systems:
i. Sheet Metal and Air Conditioning Contractors National Association (SMACNA)
ii. American Society of Heating, Refrigeration, and Air Conditioning Engineers (ASHRAE)
iii. 2001 Fundamentals Handbook Chapter 34 or 2000 HVAC Systems and Equipment
Handbook Chapters 9 and 16
iv. US and Canada: Air Conditioning Contractors Association (ACCA) Manual D
c. Acoustical Lining and Fibrous Glass Duct:
i. US and Canada: current edition of SMACNA; NFPA 90B as tested by UL Standard 181
for Class 1 Rigid Air Ducts
d. Plumbing Systems:
i. US and Canada: ICC International Plumbing Code (IPC); Uniform Mechanical Code
(UMC); Uniform Plumbing Code (UPC)
6. PRODUCT INFORMATION & SPECIFICATIONS >
syncFURNACE OD is a combined, modulating gas-fired tankless condensing water heater and hydronic fan-
coil unit, designed to provide space heating via warm-air fan-coil and potable water heating on-demand.
Available with an internal add-on to provide whole home DHW re-circulation. It is 100% factory tested
and calibrated.
An advanced internal controller operates both the modulating gas-fired tankless condensing water heater
and hydronic fan-coil unit. The controller monitors and adjusts the combined system to minimize energy
usage during operation.
syncFURNACE OD incorporates a stainless steel, modulating gas-fired tankless condensing water heater
that is factory set for use with Natural Gas (optional factory set propane model is available).
The hydronic fan-coil unit has an internal pump circulates hot water through a water coil heat exchanger.
The hot water coil is built using copper tube and aluminum fins to provide excellent heat exchange. A
blower inside the fan-coil is used to move building air across the coil and distribute heated air back out to
the building. In addition to space warm-air heating, the fan-coil unit can also perform continuous air-
circulation (fan-only) and air-conditioning (air-conditioning coil & condenser sold separately) functions for
the building. The fan-coil unit is available in either low-velocity (low static pressure) or high-velocity (high
static pressure) configuration.

syncFURNACE OD Instruction & Installation Manual –Rev 09 Pg. 9 of 81
IN THE STATE OF MASSACHUSETTS ONLY
(a) For all side-wall vented gas fueled equipment installed in every dwelling, building or structure used in whole or in
part for residential purposes, including those owned or operated by the Commonwealth and where the side-wall
exhaust vent termination is less than seven (7) feet (2.14m) above finished grade in the area of the venting, including
but not limited to decks and porches, the following requirements shall be satisfied:
1. INSTALLATION OF CARBON MONOXIDE DETECTORS. At the time of installation of the side wall horizontal
vented gas fueled equipment, the installing plumber or gas-fitter shall observe that a hard wired carbon monoxide
detector with an alarm and battery back-up is installed on the floor level where the gas equipment is to be installed
and on each additional level of the dwelling, building or structure served by the equipment. It shall be the
responsibility of the property owner to secure the services of qualified licensed professionals for the installation of
hard wired carbon monoxide detectors.
a. In the event that the side-wall horizontally vented gas fueled equipment is installed in a crawl space or an
attic, the hard wired carbon monoxide detector with alarm and battery back-up may be installed on the next
adjacent floor level.
b. In the event that the requirements of this subdivision can not be met at the time of completion of installation,
the owner shall have a period of 30 days to comply with the above requirements; provided, however, that
during said 30 day period a battery operated carbon monoxide detector with an alarm shall be installed.
2. APPROVED CARBON MONOXIDE DETECTORS. Each carbon monoxide detector as required in accordance with
the above provisions shall comply with NFPA 720 and be ANSI/UL 2034 listed and IAS certified.
3. SIGNAGE. A metal or plastic identification plate shall be permanently mounted to the exterior of the building at a
minimum height of eight (8) feet (2.44m) above grade directly in line with the exhaust vent terminal for the
horizontally vented gas fueled water heater or equipment. The sign shall read, in print size no less than one-half
(1/2) inch in size, “GAS VENT DIRECTLY BELOW. KEEP CLEAR OF ALL OBSTRUCTIONS”.
4. INSPECTION. The state or local gas inspector of the side-wall horizontally vented gas fueled equipment shall not
approve the installation unless, upon inspection, the inspector observes carbon monoxide detectors and signage
installed in accordance with the provisions of 248 CMR 5.08(2)(a) 1 through 4.
(b) EXEMPTIONS: The following equipment is exempt from 248 CMR 5.08(2)(a) 1 through 4:
1. The equipment listed in Chapter 10 entitled “Equipment Not Required To Be Vented” in the most current
edition of the NFPA 54 as adopted by the Board; and
2. Product Approved side-wall horizontally vented gas fuelled equipment installed in a room or structure separate
from the dwelling, building or structure used in whole or in part for residential purposes.
(c) MANUFACTURER REQUIREMENTS –GAS EQUIPMENT VENTING SYSTEM PROVIDED. When the manufacturer of
Product Approved side-wall horizontally vented gas fueled equipment does not provide the parts for venting the flue
gases, but identifies “special venting systems”, the following requirements shall be satisfied by the manufacturer:
1. The referenced “special venting system” instructions shall be included with the appliance or equipment
installation instructions; and
2. The “special venting system” shall be Product Approved by the Board, and the instructions for that system
shall include a parts list and detailed installation instructions.
(e) A copy of all installation instructions for all Product Approved side-wall horizontally vented gas fueled equipment,
all venting instructions, all parts list for venting instructions, and/or all venting design instructions shall remain with
the appliance or equipment at the completion of installation.

syncFURNACE OD Instruction & Installation Manual –Rev 09 Pg. 10 of 81
SPECIFICATIONS:
Low Velocity / Normal Static Duct
High Velocity / High Static Duct
Physical
5L
10L
14L
18L
22L
06H
10H
15H
Weight
lbs
215
225
235
245
260
225
235
245
Dimensions [H x L x W]
in
40.5 x
30
x 17.5
40.5 x
30
x 17.5
40.5 x
37
x 17.5
44.5 x
37
x 21
44.5 x
37
x 24
40.5 x 30
x 17.5
40.5 x 37
x 17.5
40.5 x 30
x 17.5
Ambient Temperature - Operation
°F
50 to 90
Ambient Temperature - Storage
°F
35 to 105
Electrical
Rated Voltage
Vac
115 (Single Phase)
Rated Frequency
Hz
60
Minimum Circuit Ampacity
MCA
7.8
14.7
14.7
14.7
18.7
14.7
14.7
14.7
Max Fuse or CKT BKR Size
A
15
20
20
20
25
20
20
20
Internal Transformer
40VA; Primary 115Vac / Secondary 24Vac
Fan-coil
Blower Motor Type
Direct Drive Motor [ECM or Variable-speed Motor Type]
Blower Motor HP
3/4
3/4
3/4
1
3/4
3/4
3/4
Blower Motor Full Load Amps
FLA
2.3
9.6
9.6
9.6
12.8
9.6
9.6
9.6
Blower Wheel Type, Size
Bkwrd
Crv
FC
10x6
FC
10x6
FC
10x6
FC
11x10
FC 10x6
FC 10x6
FC 10x6
Max External Static Pressure
inch
w.c.
0.6
1.5
Air-Flow Range - Nominal [Adjustable]
CFM
200 -
500
300 -
1000
400 -
1400
600 -
1800
800 -
2200
200 -
600
300 -
1000
500 -
1500
Total Face Area
ft²
1.42
1.42
2.24
2.64
3.03
1.42
2.64
2.64
Fins Per Inch
FPI
10
10
10
10
10
10
10
10
Heating Output Range [@ 140F Supply]
MBH
19 - 30
19 - 50
19 - 65
19 - 80
19 - 99
19 - 35
19 - 50
19 - 65
Thermal - Natural Gas Model
Burner Input [Low Fire - High Fire]
MBH
19 - 192
Burner Output [Low Fire - High Fire]
MBH
18.7 - 186
Nat Gas Supply Pressure [Min - Max]
inch
w.c.
3.5 - 10
Gas Valve Manifold Pressure [Min - Max]
inch
w.c.
-0.03 - -0.6
Energy Factor [EF]
%
.95
Thermal - Propane Model
Burner Input [Low Fire - High Fire]
MBH
19 - 192
Burner Output [Low Fire - High Fire]
MBH
18.7 - 186
Propane Supply Pressure [Min - Max]
inch
w.c.
8 - 13
Gas Valve Manifold Pressure [Min - Max]
inch
w.c.
-0.03 - -0.6
Domestic Hot Water
Hot Water Setpoint [Min - Max]
°F
102 - 145
Incoming Water Temperature [Min - Max]
°F
35 - 105
Water Pressure [Min - Max]
psig
30 - 150
DHW Flow @ Δ35°F
usgpm
10.5
DHW Flow @ Δ 45°F
usgpm
8.2
DHW Flow @ Δ 72°F
usgpm
5.1
DHW Flow @ Δ 77°F
usgpm
4.8
Minimum Activation Flow Rate
usgpm
0.5 (Standard Mode) | 0.1 (Re-circ Mode)
Re-circulation Pump
Grundfos 15-78
Flue Venting
Approved Vent Size
inch
2", 3"
Approved Vent Material
PVC, CPVC, polypropylene / special vent type BH (Class II, A/B/C)
Max Vent Lengths
ft
2" dia = 30ft per vent run | 3" dia = 100ft per vent run
Vent Clearance
0" to Combustables

syncFURNACE OD Instruction & Installation Manual –Rev 09 Pg. 11 of 81
MODEL NUMBER IDENTIFICATION:
mOD-200-N-14LEN1
Model Name
Burner Max Input Capacity
mOD = Integrated, Modulating Gas-Fired Instantaneous
Water Heater & Hydronic Fan Coil Unit
120 = 120,000 BTU/hr
Hydronic Configuration
2 = 1 supply & return, w_ re-circ & fc bypass
3 = 1 supply & return, w_o re-circ
1 = 1 supply & return, w_ re-circ
Fan-coil Nominal CFM
10L = 1,000 CFM, Low static
14L = 1,400 CFM, Low static
18L = 1,800 CFM, Low static
22L = 2,200 CFM, Low static
200 = 192,000 BTU/hr
06H = 600 CFM, High static
10H = 1,000 CFM, High static
15H = 1,500 CFM, High static
18H = 1,80 0 CFM, High static
Controller
N = No Duct Zoning
Z = Duct Zoning
Fan-coil Blower Motor
P = PSC, Forward Curve
R = Entry Variable-speed, Forward Curve
E = HE Variable speed, Forward Curve
D = Decstar Variable-speed, Forward Curve
B = Variabl e-speed, Backward Curve
Factory Setup - Burner Fuel
N = Natural-Gas
P = Propane
05L = 500 CFM, Low stat ic
03H = 300 CFM, High static
COMPONENTS:

syncFURNACE OD Instruction & Installation Manual –Rev 09 Pg. 12 of 81
7. DIMENSIONS AND CONNECTION DESCRIPTIONS >
mOD-200-05L/ 10L
mOD-200-06H
Inch mm Inch mm
Z140.50 1029 Z11 23.13 588
Z217.50 445 Z12 0.88 22
Z31.50 38 Z13 15.63 397
Z41.50 38 Z14 10.45 265
Z514.00 356 Z15 3.17 81
Z623.00 584 Z16 12.81 325
Z730.00 762 Z17 0.50 13
Z841.26 1048 Z18 16.44 418
Z943.40 1102 Z19 0.50 13
Z10 0.88 22 Z20 6.60 168
Z21 16.40 417
Z22 11.50 292
Dimension #
Length
Dimension #
Length
Inch mm Inch mm
A- INTERNAL PRV TO DRAIN 3/4" NPT FEM ALE 1.93 49 6.63 168
B- CONDENSATE TO DRAIN 7/8" CORR HOSE 2.63 67 5.13 130
C- COLD WATER [IN] 3/4" NPT FEMALE 3.50 89 1.04 26
D- HOT WATER [OUT] 3/4" NPT FEM ALE 8.21 209 3.00 76
E- RE-CIRC LINE [IN] 3/4" NPT FEM ALE 5.18 132 3.00 76
F- GAS 1/2" NPT FEM ALE 2.18 55 20.20 513
Pipe Connection
Thread
Specification
Location
Xref ↔
Location
Yref ↕

syncFURNACE OD Instruction & Installation Manual –Rev 09 Pg. 13 of 81
mOD-200-14L
mOD-200-10H
Inch mm Inch mm
A- INTERNAL PRV TO DRAIN 3/4" NPT FEM ALE 6.44 163 4.41 112
B- CONDENSATE TO DRAIN 7/8" CORR HOSE 9.63 244 5.13 130
C- COLD WATER [IN] 3/4" NPT FEMALE 3.50 89 1.04 26
D- HOT WATER [OUT] 3/4" NPT FEM ALE 8.21 209 3.00 76
E- RE-CIRC LINE [IN] 3/4" NPT FEM ALE 5.18 132 3.00 76
F- GAS 1/2" NPT FEM ALE 2.18 55 20.20 513
Pipe Connection
Thread
Specification
Location
Xref ↔
Location
Yref ↕
Inch mm Inch mm
Z140.50 1029 Z11 23.13 588
Z217.50 445 Z12 0.88 22
Z31.50 38 Z13 15.63 397
Z41.50 38 Z14 10.45 265
Z514.00 356 Z15 3.17 81
Z623.00 584 Z16 19.66 499
Z737.00 940 Z17 0.50 13
Z841.26 1048 Z18 16.44 418
Z943.40 1102 Z19 0.50 13
Z10 0.88 22 Z20 6.60 168
Z21 16.40 417
Z22 11.50 292
Dimension #
Length
Dimension #
Length

syncFURNACE OD Instruction & Installation Manual –Rev 09 Pg. 14 of 81
mOD-200-18L
mOD-200-15H
Inch mm Inch mm
A- INTERNAL PRV TO DRAIN 3/4" NPT FEMALE 6.44 163 4.41 112
B- CONDENSATE TO DRAIN 7/8" CORR HOSE 9.63 244 5.13 130
C- COLD WATER [IN] 3/4" NPT FEMALE 3.50 89 1.04 26
D- HOT WATER [OUT] 3/4" NPT FEMALE 8.21 209 3.00 76
E- RE-CIRC LINE [IN] 3/4" NPT FEMALE 5.18 132 3.00 76
F- GAS 1/2" NPT FEMALE 2.18 55 24.20 615
Pipe Connection
Thread
Specification
Location
Xref ↔
Location
Yref ↕
Inch mm Inch mm
Z144.50 1130 Z11 23.13 588
Z221.00 533 Z12 0.88 22
Z31.50 38 Z13 19.13 486
Z41.50 38 Z14 13.92 354
Z518.00 457 Z15 6.45 164
Z623.00 584 Z16 19.66 499
Z737.00 940 Z17 0.50 13
Z845.18 1148 Z18 19.93 506
Z947.39 1204 Z19 0.50 13
Z10 0.88 22 Z20 6.60 168
Z21 20.40 518
Z22 11.50 292
Dimension #
Length
Dimension #
Length

syncFURNACE OD Instruction & Installation Manual –Rev 09 Pg. 15 of 81
mOD-200-22L
mOD-200-18H
Inch mm Inch mm
A- INTERNAL PRV TO DRAIN 3/4" NPT FEMALE 6.44 163 4.41 112
B- CONDENSATE TO DRAIN 7/8" CORR HOSE 9.63 244 5.13 130
C- COLD WATER [IN] 3/4" NPT FEMALE 3.50 89 1.04 26
D- HOT WATER [OUT] 3/4" NPT FEMALE 8.21 209 3.00 76
E- RE-CIRC LINE [IN] 3/4" NPT FEMALE 5.18 132 3.00 76
F- GAS 1/2" NPT FEMALE 2.18 55 24.20 615
Pipe Connection
Thread
Specification
Location
Xref ↔
Location
Yref ↕
Inch mm Inch mm
Z144.50 1130 Z11 23.13 588
Z224.00 610 Z12 0.88 22
Z31.50 38 Z13 22.13 562
Z41.50 38 Z14 16.92 430
Z518.00 457 Z15 9.45 240
Z623.00 584 Z16 19.66 499
Z737.00 940 Z17 0.50 13
Z845.18 1148 Z18 22.93 582
Z947.39 1204 Z19 0.50 13
Z10 0.88 22 Z20 6.60 168
Z21 20.40 518
Z22 11.50 292
Dimension #
Length
Dimension #
Length

syncFURNACE OD Instruction & Installation Manual –Rev 09 Pg. 16 of 81
8. INSTALLATION >
MINIMUM CLEARANCES:
Inch mm Inch mm Inch mm Inch mm Inch mm Inch mm
Minimum 000000000000
Recommended for Service 28 711 4102 24 610 12 305 0 0 1 25.4
Vent Pipe
Clearance Requiements
Front
Back
Sides
Top
Bottom
Note:
1. It is highly suggested that Recommended for Service minimum clearance requirements are
maintained to ensure straight forward access for future product service / maintenance.
2. This product can NOT be installed on carpeting.
3. See venting installation instructions in this manual for required vent pipe clearances.
MECHANICAL ROOM & COMBUSTION AIR SUPPLY REQUIREMENTS:
1. Keep room free from and never store any flammable materials near product.
2. Room air and combustion air supply must be free of halogenated hydrocarbons at all times.
a. eg. Contained in paint solvents, spray cans, paints and detergents.
b. Avoid excessive dust.
3. Combustion air supply must be located so to avoid any contents of chlorine, ammonia, or alkali
agents. Installation near a swimming pool, washing machine, or laundry room will expose
combustion air to these contents and will cause premature failure of the heat exchanger and will
void product warranty.
4. Avoid installation in rooms that have continuously high levels of humidity
a. eg. Laundry rooms, indoor pool/hot tub rooms, farms and facilities with livestock manure
5. Avoid combustion air sources that can be contaminated with the following (but not limited to);
a. Fabric softeners, bleaches, detergents, cleaners, chemical fertilizers, herbicides, pesticides,
dust, methane gas, sawdust, chloride, fluoride, calcium chloride, fiber based insulation.
If these requirements are not followed exactly, a fire or explosion may
result causing property damage, personal injury or loss of life.
DO NOT store or use gasoline or other flammable vapors and liquids in
the vicinity of this or any other appliance
!WARNING

syncFURNACE OD Instruction & Installation Manual –Rev 09 Pg. 17 of 81
GENERAL VENTING:
syncFURNACE OD utilizes a modulating gas power burner and incorporates a sealed combustion venting
design. This product requires a “Special Venting System” designed for pressurized venting.
syncFURNACE OD is suitable for use for sidewall (horizontal) and vertical venting using field supplied
venting materials. This product is approved for both direct vent (sealed combustion) and direct exhaust
(sealed exhaust, room dependent combustion air supply) in both horizontal and vertical installation
configurations.
This product must be installed so that all air for combustion is taken from the outside atmosphere and all
combustion flue gas is discharged safely to the outside atmosphere.
Pay careful attention to the following:
1. DO NOT common vent syncFURNACE OD with any other new and/or existing gas fired product.
2. It is highly recommended that syncFURNACE OD be located so that venting lengths can be as short
and direct as possible. Pay special attention to manage the impact of the steam plume of the
exhaust gas to minimize the impact to surrounding structures.
3. Inspect all finished exhaust vent/air intake piping to ensure:
a. All piping and fittings used are marked and made of approved material(s).
b. Meets the acceptable size, length and number of elbow requirements listed in this manual.
c. Installation is in accordance with prevailing provisions of local codes.
d. Installation meets the requirements of this instruction as well as the instructions of the field
supplied venting material(s) and/or product(s).
4. Venting, condensate drainage and combustion air must be installed in compliance with local codes
and must follow the instructions provided with components and/or systems. All venting must be
installed in accordance with the requirements of the jurisdiction having authority:
a. In Canada, Part 8, Venting Systems of the CAN/CGA B149.1 or B149.2 Code and any other
local building codes are to be followed.
b. In the U.S., Part 7, Venting of Equipment of the National Fuel Gas Code, ANSI 223.1, latest
edition, prevails.
c. Where there is a discrepancy between the installation instructions below, and the code
requirements, the more stringent shall apply.
5. DO NOT install vent pipe such that flue gases flow downwards. MUST be vented vertically
upwards or horizontal with upward slope –see below requirements for acceptable slopes.
6. Inspect finished vent system thoroughly to ensure all joints are airtight and comply with these
instructions and the instructions provided by the field supplied venting materials.
7. It is highly recommended that annually the entire vent system be inspected for leaks.
8. Keep exhaust gas plumes well away from all building air intakes, including those located on
neighboring structures. It is the installer’s responsibility to ensure proper installation that prevents
damage from exhaust gas plumes to exterior walls and neighboring structures.
9. Side-wall vent terminations should be located on a wall that is least likely to receive high-speed,
prevailing winds. High-speed, prevailing winds may affect water heater operation and could cause
flue gas plumes damage to occur to nearby exterior walls. It is the installer’s responsibility to
review the side-wall terminations and take all precautions necessary to shield and protect the vent
terminations and exterior walls from damage.
10. It is the responsibility of the installer to contact local building or fire officials concerning any
installation restrictions and/or inspection requirements that may apply. Permits may be required
before initiating installation.
11. Installation in manufactured (mobile) homes shall conform to the Manufactured Home Construction
and Safety Standard, Title 24 CFR, Part 3280 and/or CAN/CSA Z240 MH Series, Mobile Home.

syncFURNACE OD Instruction & Installation Manual –Rev 09 Pg. 18 of 81
ACCEPTABLE VENT CONFIGURATIONS:
1. Direct Vent, Two-pipe systems consisting of the following termination types;
a. Horizontal air intake and exhaust vent pipes
b. Vertical air intake and exhaust vent pipes
c. Horizontal air intake and vertical exhaust pipes
Installer must follow the instructions of this manual and install in accordance with the National Fuel
Gas Code, ANSI Z223.1 (U.S.) or CSA B149.1 (Canada) and local codes.
2. Direct Exhaust, room dependent combustion air supply;
a. Horizontal exhaust termination
b. Vertical exhaust termination
Installer must follow the instructions of this manual and install in accordance with the National Fuel
Gas Code, ANSI Z223.1 (U.S.) or CSA B149.1 (Canada) and local codes.
ACCEPTABLE VENT MATERIALS EQUIVALENT LENGTHS:
Acceptable Material Canada United States
PVC ULC-S 636 ANSI/ASTM D1785
CPVC ULC-S 635 ANSI/ASTM F441
Stainless Steel, AL-29-4C (SS) ULC-S 636 UL-1738
Polypropylene (PP) ULC-S 636 -
PVC ULC-S 636 ANSI/ASTM D2564
CPVC ULC-S 636 ANSI/ASTM F493
Primer PVC / CPVC ULC-S 636 ANSI/ASTM F656
- If allowed by local codes, combustion-air / air-inlet venting does not require use of high-temperature materials -
ABS is acceptable. It is the responsibility of the installation contractor to check and confirm with local codes /
jurisdiction of authority.
- See Max Equivalent Lengths table (on following page) for allowable flue gas and combustion air material sizes
and lengths.
Required Venting System Standards
Approved Vent Materials
Flue Gas (Exhaust) /
Combustion Air (Intake)
Venting System
Pipe Cement
Notes:
!DANGER
Vent and Air-Inlet are to be piped separately. This product cannot share a common vent or air-
inlet with multiple water heaters. Failure to comply will result in serious injury or death.
If the above criteria is not properly observed and syncFURNACE OD damage results - any warranty coverage on
syncFURNACE OD and its related components will be null and void.
DO NOT locate product in
areas where high levels of
dust or humidity are present
!CAUTION
DO NOT install / operate
syncFURNACE OD during
construction - will cause heavy
suiting of burner and heat
exchanger fouling.
!CAUTION
DO NOT operate product in
an area that is under
construction or renovation.
!CAUTION

syncFURNACE OD Instruction & Installation Manual –Rev 09 Pg. 19 of 81
Model
Vent Size Fuel
Max Equivalent
Length
Maximum
Number of Elbows
2" [60mm] Natural Gas 30 feet [9.1m]
2" [60mm] Propane 30 feet [9.1m]
3" [80mm] Natural Gas 100 feet [30.4m]
3" [80mm] Propane 100 feet [30.4m]
Maximum Number of Elbows Does NOT Included Termination Elbows
Max Equivalent Lengths
mOD-200
Max Equivalent Length is Per Vent Run
6
[This area intentionally left blank]
The use of cellular core PVC (ASTM F891), cellular core CPVC, or Radel®
(polyphenolsulfone) in the exhaust venting system is prohibited. Failure to follow
these instructions may result in property damage, personal injury, or death.
!WARNING
Covering non-metalic vent pipe and fittings with thermal insulation is
prohibited. Failure to follow these instructions may result in property damage,
personal injury, or death.
!WARNING
All vent and air-inlet materials installed on gas fired appliances in Canada or the
United States must meet the standards listed in the above Acceptable Vent
Materials Table. Failure to comply could result in fire, serious injury or death.
!WARNING

syncFURNACE OD Instruction & Installation Manual –Rev 09 Pg. 20 of 81
Notes:
1. syncFURNACE OD is supplied with 3” Flue Gas and Combustion Air vent connections. If reducing to
2”, make transition as soon as possible.
2. Minimum acceptable equivalent vent length is 5 feet (1.53m) for 2” diameter materials and 8
feet (2.44m) for 3” diameter materials.
3. For elbows, both 2” & 3” diameter, use the following to calculate max equivalent length:
a. 90° elbow long radius –equivalent length = 5 feet (1.53m)
b. 90° elbow short radius –equivalent length = 8 feet (2.44m)
c. 45° elbow –equivalent length = 3 feet (.92m)
4. Equivalent length of elbows must be included when determining total equivalent vent length.
5. Max equivalent vent length is allowable length for each (flue gas or combustion air) vent run.
6. Both Flue Gas and Combustion Air vent piping must use same diameter material for entire system.
7. The equivalent length of the termination does not need to be included when calculating equivalent
length of the venting system. ie, if using two 90° elbows and a 45° elbow (one 90° elbow + one
45° elbow for Flue Gas, one 90° elbow for Combustion Air) as a termination, these elbows do not
need to be included in the equivalent length calculation nor for the max number of elbows
calculation.
8. If a low point is required in the venting system, proper condensation drain pipe(s) must be
installed according to the instructions of the vent material supplier.
9. Condensate inside flue gas venting must drain from the termination point back to the water heater.
Combustion Air vent piping must slope away from water heater towards termination point.
a. Horizontal venting runs, flue gas termination point must slope back towards water heater
and combustion air must slope away from water heater towards termination point at a slope
no less than:
i. For 2” Øpipe, horizontal runs < (less than) 4 feet (1.22m) = ¼” (6.4mm) per foot
ii. For 2” Øpipe, horizontal runs > (greater than) 4 feet (1.22m) = ½” (13mm) per foot
iii. For 3” Øpipe, ¼” (6.4mm) per foot
10. In Canada, the first three (3) feet (.92m) of vent piping must be readily accessible for inspection.
11. DO NOT use ABS or any cellular core pipe for Flue Gas vent piping.
12. Vent Adapters and Termination Kits are acceptable if they are marked and meet the requirements
of the above Required Venting System Standards for the country they are being installed in. Vent
Adapters and Termination Kits can only be used in the above diameters and if provided by the
following manufacturers:
a. IPEX –ULC-S 636 / ANSI/ASTM F441 approved
b. CENTROTHERM Eco Systems –Innoflue SW, Flex & Concentric - ULC-S 636 / UL-1738 app.
c. M&G Duravent
d. NOVAFLEX GROUP –Flexmaster –Z-Vent AL-29-4C approved, Z-Dens polypropylene
e. Ecco Polyproplyne Vent
13. When cutting venting pipe, ensure square cuts are made and remove all burrs from joints and
fittings. DO NOT allow burrs and debris to enter venting system.
14. If using PVC or CPVC gas venting material, all joints must be properly cleaned, primed and
cemented. Only use primers and cements listed in the above table and that are approved for use
with the venting material.
15. Only use approved pipe cement and primers. Consult manufacturer’s installations to ensure
correct use of products.
16. Do not use excessive amounts of primers and cements when joining PVC and/or CPVC gas venting
material. Using excessive amounts can lead to pooling inside venting system. Upon completion of
venting system assembly, allow venting system cement to properly cure for a minimum of 8 hours
before turning on the gas and operating the burner on the water heater. Consult the pre-
commission procedure for plastic venting in this manual for further information.
This manual suits for next models
8
Table of contents
Popular Water Heater manuals by other brands
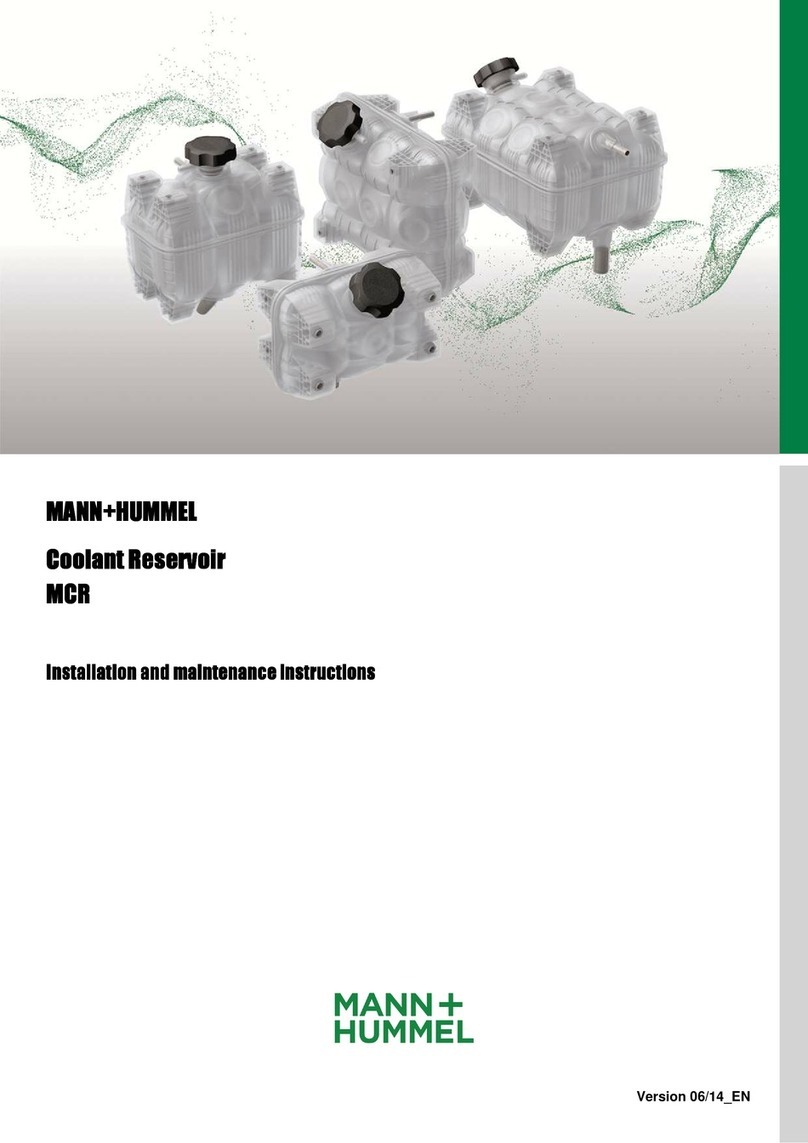
MANN+HUMMEL
MANN+HUMMEL MCR Series Installation and maintenance instructions

STIEBEL ELTRON
STIEBEL ELTRON PSH 30 EL Operation and installation

BaltGaz
BaltGaz NEVALUX-5611 user manual

Rheem
Rheem PVG Installation, operation and service manual
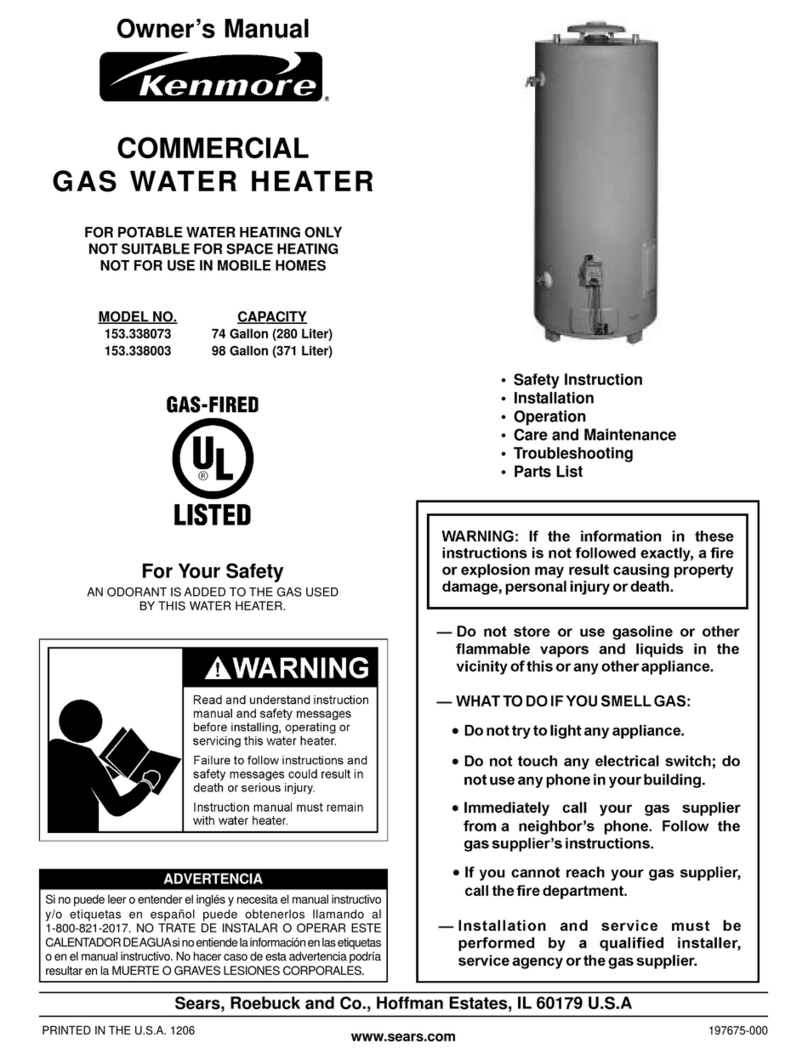
Kenmore
Kenmore 153.338003 owner's manual

Bosch
Bosch GWH 425 PN Applications manual

Heatworks
Heatworks model 1 Installation & user manual
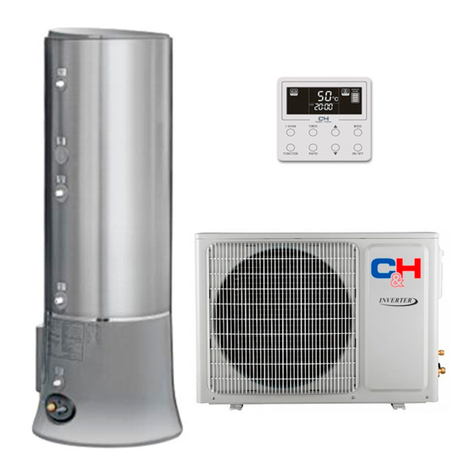
Cooper & Hunter
Cooper & Hunter CH-HP3.5SWNK owner's manual
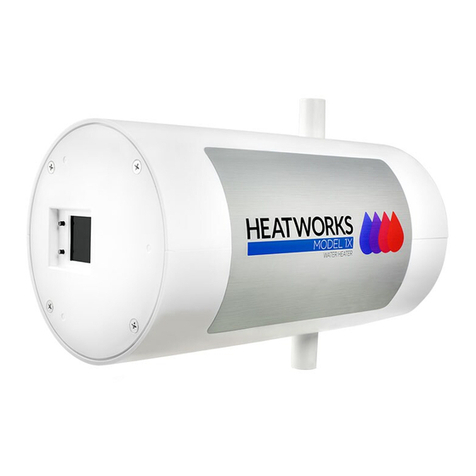
Heatworks
Heatworks MODEL 1X Installation & user manual
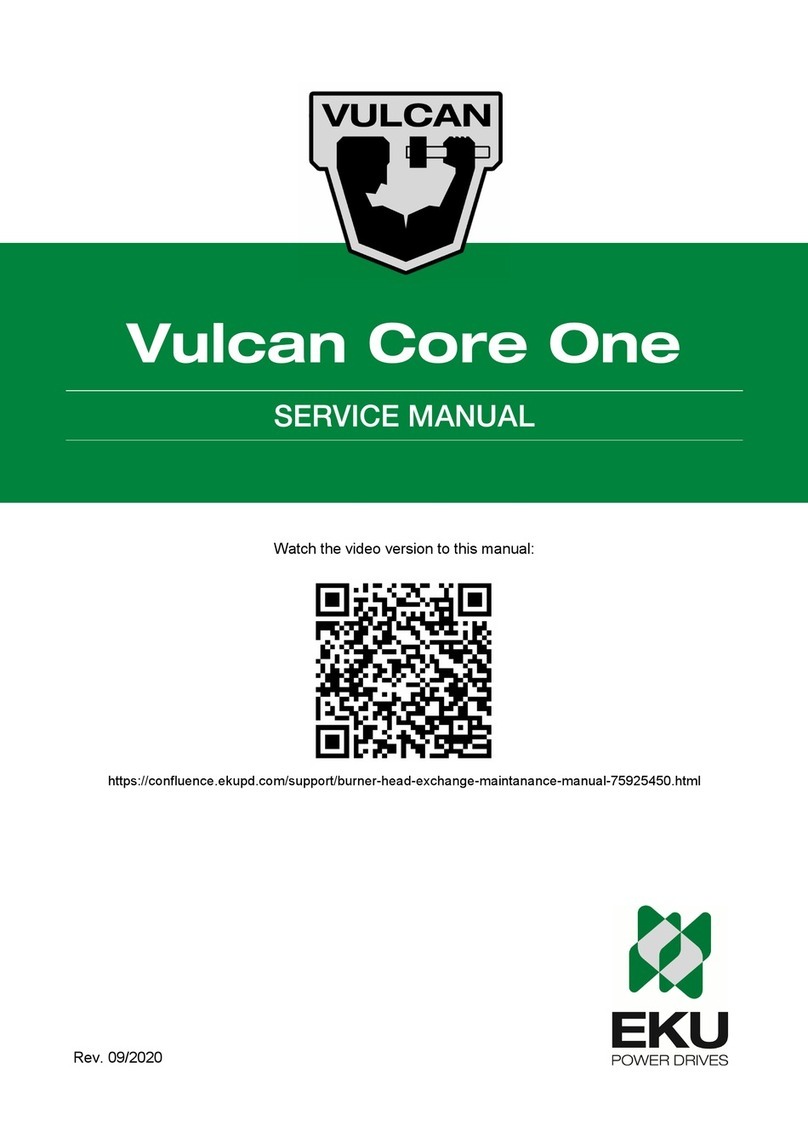
Vulcan-Hart
Vulcan-Hart Core One Service manual
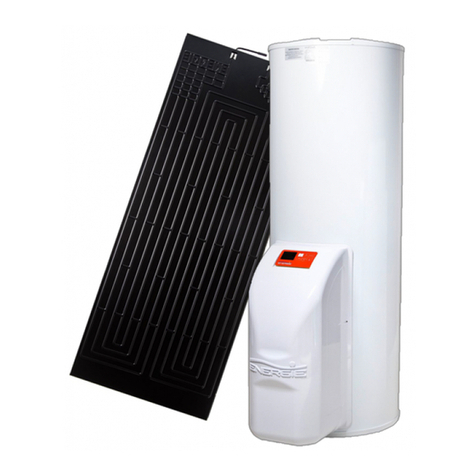
Energie
Energie ECO 200esm Installation Instructions and Use & Care Guide
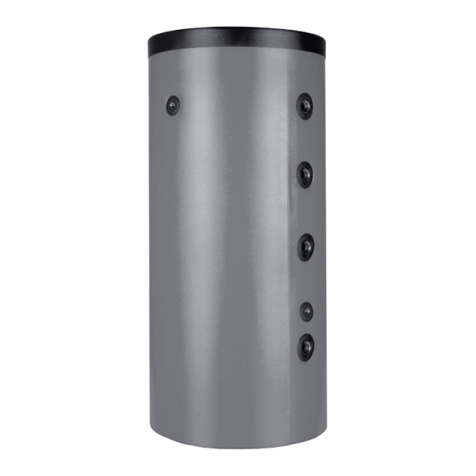
Argo
Argo Technibel TANK 200L Usage and maintenance manual