GREER Company MicroGuard 400 Manual

Greer CompanyCrane Systems
GREER COMPANY 1918 E. Glenwood Place, Santa Ana, CA 92705 Tel: (714) 259-9702 Fax: (714) 259-7626
MG®400 Computer Training Manual PN W424900 - 11/07/02
1 of 18
MicroGuard400 Service Training
Troubleshooting & Maintenance
TEST
100%
VIEW SET
INFORMATION
W
DOWNCLEAR UP SELECT
DEDUCT
ERECTED STOWED
OPERATOR ALARMS CONTRAST
WORKING
AREA
W
MAX
MicroGuard 424
5.82
3.46 ATB ALARM
60%
57.2 8F49.1
OUTRIGGERS 360o
MAIN BOOM
NO FLY OR JIB
CRANE
SET UP STOWED
DEDUCT
RCI 414/424 Display
RCI 434 Display
MG®400 Computer Assembly
RCI 500 Display

Greer CompanyCrane Systems
GREER COMPANY 1918 E. Glenwood Place, Santa Ana, CA 92705 Tel: (714) 259-9702 Fax: (714) 259-7626
MG®400 Computer Training Manual PN W424900 - 11/07/02
2 of 18
MicroGuard®400 Service Training Manual
Table of Contents
General Description .........................................................................................................3
Fault Codes .....................................................................................................................4
Voltage Supplies and Checkpoints ..................................................................................5
Internal Power Supplies..............................................................................................5
Terminal Block Markings ............................................................................................6
Testing Pressure Transducers Through Drive Voltage ....................................................7
Pressure Transducer Resistance Measurement ........................................................8
Analog Input Terminals (AIN)...........................................................................................8
Extension “Pot” Operation................................................................................................9
Boom Extension Sensor (AIN2) .....................................................................................10
Boom Angle Sensor (AIN3)............................................................................................11
Extension Reel Assembly (reeling drum) .......................................................................12
Anti Two-Block System Components.............................................................................13
Where Do Relays Come From?...............................................................................14
Swing Potentiometer (Swing Pot) ..................................................................................15
Checking the Swing Potentiometer ..........................................................................16

Greer CompanyCrane Systems
GREER COMPANY 1918 E. Glenwood Place, Santa Ana, CA 92705 Tel: (714) 259-9702 Fax: (714) 259-7626
MG®400 Computer Training Manual PN W424900 - 11/07/02
3 of 18
MicroGuard400 Computer
Troubleshooting & Maintenance
Overview
The MG® 400 Computer can be used with several different Greer RCI displays, most commonly
the RCI 500. Prior to 1999, several OEM’s used the MG® 400 as a “production line” computer.
In 1999, Greer introduced the MG® 500 Computer and the “Fast Cal” methods that equipment
manufacturers now employ.
General Description
The MG® 400 Computer is larger than the MG® 500 Computer. It contains two separate boards
called the processor board and the interface board.
The processor board on top contains all of the computer programming, stores the memory, does
the calculating, and supplies the visual outputs for the RCI display. The interface board below
contains two voltage power supplies that provide the voltages necessary for operation of the
computer and the display, including the analog and digital functions. The interface board routes
these voltages to the appropriate locations.
The larger power supply source with the light is responsible for 5 volt power; the smaller power
supply produces the 15 volts used in conjunction with several different power applications.
There are numerous “voltage check points” on both the processor and the interface boards,
as well as electrical checks involving the interface board terminal blocks, e.g., drive voltage for
the analog sensor functions.
Improper handling of the computer unit may cause damage to the upper board as the cover and
boards are not hinged. For handling instructions, refer to the Greer maintenance manual.
Fault Codes
When a fault is detected by the system, a number will appear under one or more of the four fault
group headings (A - D) shown on the next page. The information screen will illuminate the word
“FAULT,” the RED LED will light up, and the audible alarm will sound.
To diagnose Faults in the system at any time during operation, PRESS and HOLD the “TEST”
button, which will initiate the self-test function followed by an on-screen display of identied faults
in groups A through D.

Greer CompanyCrane Systems
GREER COMPANY 1918 E. Glenwood Place, Santa Ana, CA 92705 Tel: (714) 259-9702 Fax: (714) 259-7626
MG®400 Computer Training Manual PN W424900 - 11/07/02
4 of 18
Fault Codes continued
Group “A”
Sensor Faults
Group “B”
I/O Faults
Group “C”
Memory Faults
Group “D”
General Faults
001 Piston Pressure 00 No Fault 00 No Fault 00 No Fault
002 Rod Pressure 01 Digital input/output 01 Executive Rom 01 No Duty Found
004 Boom Extension 02 Analog input/output 02 Duty Rom 02 Current Duty Bad
008 Boom Angle 04 Display 03 Not Used 04 Configuration
Uncalibrated
016 Not Used 04 Scratchpad Rom
032 Swing “A” 08 Personality Rom
064 Swing “B”
Faults in the external sensors are detected without the need of the self-test .
The above faults do not include the entire list of possible Faults and Fault Codes. Please see the
maintenance manual for a complete listing.
Interpreting Multiple Faults that Add Up to More than the Numbers Listed.
Example: If the fault is 012, pick the largest fault(s) from the list that will subtract from 12 and
then add to get the equivalent. In this instance, the answer would be 008 and 004.
In this example, the faults indicate that both the extension and angle sensor have failed. Fault
indications of this type are unlikely, however, there should be an investigation of electrical
readings and cable routings. Outputs from analog sensors can be measured with an accurate
voltmeter.

Greer CompanyCrane Systems
GREER COMPANY 1918 E. Glenwood Place, Santa Ana, CA 92705 Tel: (714) 259-9702 Fax: (714) 259-7626
MG®400 Computer Training Manual PN W424900 - 11/07/02
5 of 18
Checkpoint Requirement Tolerance
B+ +9-36V .5
+VP +12V -.5
+5 +5 +/- .1
+15 +15 +/- .1
-15 -15 +/- .1
Voltage Supplies and Check Points
Look at the terminal board and begin supplying power to it.
The main power coming into the terminal board is usually a
9-36 VDC supply coming directly from the crane. If the
voltages at the B + and B - terminals on TB -1 are not
present, check the voltage on the vehicle.
Internal Power Supplies: The computer generates its
own internal power from the incoming battery voltage. This
power can be monitored at the test points inside the
computer adjacent to the fuses and Battery Input
Terminals. The tolerances for these voltages are listed in
the table below as well as in a graphic illustrating the
voltage check points.
To monitor the internal power supplies, use a digital voltmeter set to the appropriate VDC setting
and attach to the appropriate voltage check points on the terminal board. Note the two power
supplies sitting side-by-side on the board. The larger (left) power supply provides 5 V power.
The smaller (right) power supply provides 15 V. There are two fuses on the face of the board
immediately above the voltage checkpoints. These 1A fuses, labeled “FS1” and “FS2,” protect
the functions of display power and power supply. Replace these fuses ONLY with an identical
replacement, or damage may occur to the main board or tracings.
5 V
15V
FS1
FS2
B+
GND
+VP
+5V
Res
+15V
-15V

Greer CompanyCrane Systems
GREER COMPANY 1918 E. Glenwood Place, Santa Ana, CA 92705 Tel: (714) 259-9702 Fax: (714) 259-7626
MG®400 Computer Training Manual PN W424900 - 11/07/02
6 of 18
Terminal Block Markings
Terminal blocks are marked as shown in the graphic to
the right. Note that there are multiple Drive Voltage
terminals (DR+ and DR-) in different locations. Note that
these terminals are all common on the computer board
assembly. The same is true of any OV or +VP terminals.
For example, checking the drive voltage on TB2 should
provide exactly the same readout as at any drive voltage
terminal on TB3.
AIN2 and AIN3 are typical voltages checkpoints for
analog input signals from the boom angle and length
pots. These signals will vary depending on how the unit
is operated at the time the reading is taken. Refer to the
maintenance manual for further definition of terminal
blocks.
Because the drive voltages are all common, any analog
sensor can be suspect. If, for example, drive voltage is
low, and +15 V is within tolerance, each of the analog
sensors must be removed, one at a time, until the sensor
that is causing the voltage to sag is located and replaced. If the voltage continues to sag, the
processor board should be replaced as the drive voltage power supply is integrated into the
processor board.
This is a simple process of elimination, which will help pinpoint a failing sensor, an abrasion, or a
pinch in a wire or loom. All wiring could become suspect at this time and should be carefully
checked. Output tests can also be run at the sensors by attaching the voltage meter at the
sensor output and watching as the sensor is extended or raised. Voltage skips or gaps can be
detected using this technique.
+DR
0V
-DR
+DR
0V
+DR
-DR
-DR
0V
AIN1
AIN0
-DR
AIN5
AIN6
AIN2
+VP
0V
+DR
+DR
TX0-
TX0+ AIN4
TX1+
TX1-
-DR
0V
AIN3
+VP
+VP
OV
OV
OV
OV
OV
TB2
TB3
TB4
Voltage Checks

Greer CompanyCrane Systems
GREER COMPANY 1918 E. Glenwood Place, Santa Ana, CA 92705 Tel: (714) 259-9702 Fax: (714) 259-7626
MG®400 Computer Training Manual PN W424900 - 11/07/02
7 of 18
Testing Pressure Transducers Through Drive Voltage
The pressure transducer used with the MG® 400 Computer is a remote pressure transducer. It
is usually mounted directly onto the boom lift cylinder and cabled into the computer through
connectors that are attached to the proper drive and output channels. The transducer starts out
as a balanced bridge with Drive Voltage input, and “0” output. As soon as the boom is raised,
which applies moment to the cylinder, the internal pressure will change in the transducer and the
resistance across the bridge will change, causing output to the TX0, TX1 side of the bridge.
This output indicates to the computer that the weight or center of gravity of the boom is
changing. The reading is then converted to load.
To check the input and outputs on this circuit, go to the terminal blocks marked DR+ and DR-,
and TX0+ and TX0-. The terminal located immediately below the base-side transducer is the
rod-side transducer. In the maintenance manual, there is a procedure for the changeout and
setup of a new transducer. Refer to the Greer Calibration manual for the procedures for zeroing
the transducer and performing load tests.
Refer to the procedure on the following page for testing the resistance of a normal transducer.
Remember that the readings must balance. If not, the transducer is unbalanced and may give
faulty load readings.
DR+
DR-
TX0+
TX0-
DR+
DR-
TX0-TX1

Greer CompanyCrane Systems
GREER COMPANY 1918 E. Glenwood Place, Santa Ana, CA 92705 Tel: (714) 259-9702 Fax: (714) 259-7626
MG®400 Computer Training Manual PN W424900 - 11/07/02
8 of 18
Pressure Transducer Resistance Measurement
• With the power to the computer off, disconnect the piston pressure transducer from the
terminal blocks +DR, -DR, TX0+ and TX0- within the computer.
• With the DVM set to the Ohms range, measure the resistance between red and blue wires.
The resistance should be 350 Ω+/- 10 Ω.
• With the DVM set to the Ohms range, measure the resistance between yellow and green
wires. The resistance should be 350 Ω+/- 10 Ω.
• With the DVM set to the Ohms range, measure the resistance between pins. Each of the
open wires red, blue, green, yellow and the case of the transducer. There should be no
connection between the case and any of the pins.
Analog Input Terminals (AIN)
Some terminals on terminal strip TB3 will be marked “AIN” followed by a numeral
(0, 1, 2, etc.) “AIN” stands for Analog Input. This means that at this terminal there is an
incoming signal to the computer from an analog sensor, such as extension, or boom
angle. It is important to be able to identify which terminal goes to which function, as a
voltage reading may be necessary to determine if a problem with one of the analog
sensors exists. Therefore, each of the “AIN” channels must be identified as well as what
information each one feeds into the computer. The first Analog sensor identified here
will be the extension sensor.
Red
Blue
Green
Yellow
Typical Transducer W/ Wiring

Greer CompanyCrane Systems
GREER COMPANY 1918 E. Glenwood Place, Santa Ana, CA 92705 Tel: (714) 259-9702 Fax: (714) 259-7626
MG®400 Computer Training Manual PN W424900 - 11/07/02
9 of 18
Approx. .25 Volts
Retracted
Approx. 2.5 Volts Extended
+-
OUTPUT
+-
OUTPUT
Extension Pot Operation
As discussed in earlier lessons, the extension
pot is a precision 10-turn pot. Drive voltage is
introduced into the + side, and - to the other
end of the coil.
The output side or “wiper,” as it is sometimes
called, will have a set starting point
(normally .25 V) and as the pot is rotated, the
voltage will linearly increase until at some point,
it will reach the drive voltage, which is 5.25 V
(+- .25 V).
This voltage rise must be steady and consistent
without voltage spikes or skips where the
voltage drops off. Using a voltmeter, measure
the reading at “AIN2” on the computer
termination board. The schematic below illustrates checkpoints, followed by an explanation of
the checkout procedure on the next page.
1
2
3
4
5
6
7
8
9
10
11
12
13
14
15
16
+DR
AIN0
AIN1
-DR
OV
+DR
AIN2
AIN3
AIN4
-DR
0V
+DR
AIN5
AIN6
-DR
0V
TB3
Approximate Voltages
For Training Purposes
Only
0 Volts
5 Volts
Retracted
Extended
0 Volts
Retracted
Extended
Output
Extension Pot Schematic

Greer CompanyCrane Systems
GREER COMPANY 1918 E. Glenwood Place, Santa Ana, CA 92705 Tel: (714) 259-9702 Fax: (714) 259-7626
MG®400 Computer Training Manual PN W424900 - 11/07/02
10 of 18
Boom Extension Sensor Ain2
To check the Boom Extension Sensor Voltage, follow the procedure below. To access the
voltage checkpoints, carefully remove the computer cover. Move the processor board out of the
way and secure it to prevent damage. Remove the extension reel cover for access to the
terminal strip in the computer reel.
1. Fully retract the boom. Access the computer and termination boards. Using a digital
voltmeter set to read DC voltage, measure the analog sensor drive voltage. Place the
negative lead on any 0 (Zero) volt or DR- terminal of the Analog Input Group.
2. Place the positive lead of the meter on the AIN2 terminal of the Analog Input Group. The
voltage should be greater than 0.25 volts.
3. Extend the boom as far as is safe to do so. The boom need not be horizontal for this test.
The voltage should be less than 5 volts. (Usually around 2.5 volts depending on the boom
length). During extension, the voltage should increase linearly; during retraction the
voltage should decrease linearly.
4. If the voltage is out of the range listed above, remove the four screws that secure the cover
on the extension reel, which is located on the left side of the main boom section; remove the
cover.
5. Under the cover on the right side of the extension reel is a terminal strip. This terminal strip
has six wires connected to the bottom screws. With a digital voltmeter set to read DC
voltage, place the negative lead on the terminal with the attached blue wire (- Drive) and the
positive lead on the terminal with the attached red wire (+Drive).
6. The voltage should be 5.25+/-0.1 volts. If this voltage is out of range, and if the Analog Drive
Voltage measured in the computer was OK, it is possible that the cable is open or grounded
between the computer and the extension reel. Check all connections and plugs that may be
between these two components. Repair or replace as required. Refer to the proper wiring
schematic for the unit being worked on. For wiring details, refer to the Installation Manual for
the model of the crane being tested or OEM wiring schematics.
7. With the negative lead of the voltmeter connected to the blue drive (negative) and the
positive lead of the voltmeter connected to white (extension signal), the voltage should be
the same as the voltage measured at AIN2 of the analog input group in the computer. If this
voltage is not the same, it is possible that the cable between the reel and the computer is
faulty.

Greer CompanyCrane Systems
GREER COMPANY 1918 E. Glenwood Place, Santa Ana, CA 92705 Tel: (714) 259-9702 Fax: (714) 259-7626
MG®400 Computer Training Manual PN W424900 - 11/07/02
11 of 18
Boom Angle Sensor Ain3
To check the Boom Angle Sensor Voltage, follow the procedure below. To access the voltage
check points, carefully remove the computer cover and move the processor board out of the way
and secure it to prevent damage. You may also want to remove the angle reel cover to access
the terminal strip in the computer reel.
1. Place the main boom at a 0 ° (zero) angle. Verify that it is at a 0 ° (zero) angle with an
inclinometer.
2. Access the Termination Board. Check the Analog Drive Voltage. With a digital voltmeter set
for DC volts, connect the negative lead of the meter to any 0 (zero) volt terminal of the
Analog Input Group.
3. Connect the positive lead to the AIN 3 terminal of the Analog Input Group.
4. With the boom horizontal, the voltage should be 0.4 +/- 0.1 volts.
5. Raise the main boom to a 60 ° angle. Verify that the main boom is at a 60 ° angle with an
inclinometer.
6. With the boom at a 60 ° angle, the voltage should be 3.02 +/-0.1 volts. If this is out of range,
remove the cover from the extension reel located on the left side of the main boom.
7. Under the cover on the right side of the extension reel is a terminal strip. This terminal strip
has six wires connected to the bottom screws.
8. With a digital voltmeter set to read DC voltage, place the negative lead on the terminal with
the blue wire (-Drive) and the positive lead on the terminal with the red wire (+Drive).
9. The voltage should be 5.25+/-0.1 volts. If this voltage is out of range and the Analog Drive
Voltage has been checked as in step 2 and is OK, it is possible that the extension reel cable
is open or grounded between the computer and the extension reel. Check all connections
and plugs between these two components. Repair or replace, as required. Refer to the
installation manual for the particular unit you’re working on, or the OEM manual of the crane
being tested for wiring details.
On the following page, see an illustration of the Extension Reeling Assembly for reference and
identification of components discussed in the last two procedures. Also listed are procedures for
setting up the extension reel sensors after reel or potentiometer replacement.

Greer CompanyCrane Systems
GREER COMPANY 1918 E. Glenwood Place, Santa Ana, CA 92705 Tel: (714) 259-9702 Fax: (714) 259-7626
MG®400 Computer Training Manual PN W424900 - 11/07/02
12 of 18
Extension Reel Assembly (reeling drum)
The Greer Extension Reel Assembly has several important functions. These functions
are as follows:
• To store the ATB cable on the extension reel. The cable must be layered neatly so that the
cable is maintained and the lay will be as neat as possible.
• To house the angle sensor enclosure. The angle sensor is enclosed inside the housing
shown above and has its own cover. The pendulum is made of brass and attaches to the
shaft of the angle pot and it is dampened with magnets to assure the movement is precise.
• Provides a terminal strip for termination of all wiring for the length, angle, and ATB sensors.
• Houses a separate bracket to house the length potentiometer length pot clutch assembly.
The reel is normally mounted on the left side of the boom, and in most cases has at least 1
cable guide per boom section.
ATB Cable
To Boomtip
Boom Angle
Sensor
Reeling Drum
Assembly
Computer Cable
Assembly
Terminal
Block
Extension
Pot

Greer CompanyCrane Systems
GREER COMPANY 1918 E. Glenwood Place, Santa Ana, CA 92705 Tel: (714) 259-9702 Fax: (714) 259-7626
MG®400 Computer Training Manual PN W424900 - 11/07/02
13 of 18
Anti 2-Block System Components
The signal from the Anti Two-Block (ATB) switches at the boom and fly tips is a switched
ground. The ground signal is powered in the computer at the 0 ° volt terminal of the digital input
group.
When there is no ATB alarm, the switches at the boom head are closed allowing the
ground to be returned to the computer at the ATBIN terminal.
When there is a two-block condition, the appropriate ATB switch will go to the open position,
thereby removing the ground from ATBIN and causing ATB Alarm and Function Disconnect.
The ATB board in the computer controls the ATB alarm and Function Disconnects separately.
The ATB board, located in the computer box:
• Operates the function disconnects by controlling the coil of RL2, ATB relay,
at DOUT 1.
• Operates the audible alarm and on-screen message by controlling the logic level at DIN13.
RELAY
1
RELAY
2
TB4
TB5 TB6 TB7
ATB
BOARD
1
2
3
4
5
6
7
8
9
10
11
12
13
14
15
16
1
2
3
4
5
6
7
8
9
10
11
12
13
14
15
16
1
2
3
4
5
6
7
8
9
10
11
12
13
14
15
16
1
2
3
4
5
6
7
8
9
10
11
-CL
+CL
TB3
1
2
3
4
5
6
7
8
9
10
11 0V
0V
0V
0V
+VP
+VP
+VP
+VP
DOUT/DIN/
NC
C
NO
NC
C
NO
NC
C
NO
ATBIN
+12V
B+
+5V -5V
Note: = White

Greer CompanyCrane Systems
GREER COMPANY 1918 E. Glenwood Place, Santa Ana, CA 92705 Tel: (714) 259-9702 Fax: (714) 259-7626
MG®400 Computer Training Manual PN W424900 - 11/07/02
14 of 18
Where Do Relay Signals Come From?
There are two relays on the termination board (lower) that are marked Relay 1and Relay 2.
These relays are mounted in such a way, that they can work parallel with each other as well as
separately. (When ATB function is tripped, the overload signal may still be closed (the opposite
also applies) There are two signals that may interrupt the flow of power to the relay coils:
• The brown wire, which is the ground signal that is returning from the reel to the ATBIN
port on the termination board
• The green signal that is directed by the processor on the upper board. If either
connection to the relay coils is interrupted, it will cause function lockout.
This circuit is built into the circuit board, making it impossible to visually see the color-codes
inside the computer. The purpose of this system is to be able to separate the two conditions
when they occur, visually as well as with warnings on the display console.
5V Supply
TB7
6
7
8
9
10
11
NC
C
NO
NC
C
NO
c
NO
NC
+ Coil
- Coil
RELAY
2
c
NO
NC
+ Coil
- Coil
+12V or
Crane Power
To FKO
ATB IN
Overload Signal
from Processor
1
RELAY
Typical Relay Wiring Diagram FKO

Greer CompanyCrane Systems
GREER COMPANY 1918 E. Glenwood Place, Santa Ana, CA 92705 Tel: (714) 259-9702 Fax: (714) 259-7626
MG®400 Computer Training Manual PN W424900 - 11/07/02
15 of 18
Swing Potentiometer (Swing Pot)
The position of the upper structure in relation to the carrier must be determined. This is
accomplished by means of a swing potentiometer generally mounted in the collector ring under
the hydraulic swivel. If the system does not have input from the swing potentiometer, it will not
be able to find a duty. The swing pot is a multi-directional pot that has overlapping ends to
assure that as the upper structure of the crane rotates around in a circle “the end” is never
reached. The potentiometer is furnished by the manufacturer of the crane and is nearly always
mounted inside the collector ring on the bottom of the hydraulic swivel. The swing pot is reliable
and usually does not cause a problem.
First explore the wiring diagram of the swing pot to see the source of the drive and analog
voltages that run this circuit. Note the schematic below:
TB3
TB4
TB5
TB6/ TB7
RELAY
1
RELAY
2
ATB BOARD
1
2
3
4
5
6
7
8
9
10
11
12
13
14
15
16
1
2
3
4
5
6
7
8
9
10
11
12
13
14
15
16
1
2
3
4
5
6
7
8
9
10
11
12
13
14
15
16
1
2
3
4
5
6
7
8
9
10
11
1
2
3
4
5
6
7
8
9
10
11
AIN1
+DR
AIN0
-DR
OV
+DR
AIN2
AIN3
AIN4
-DR
0V
+DR
AIN5
AIN6
-DR
0V 0V
0V
0V
0V
+VP
+VP
+VP
+VP
DOUT
DIN/
NC
C
NO
NC
C
NO
NC
C
NO
-CL
+CL
180
0
W1
W2
SWINGPOT
Typical Swing Pot Schematic
These colors may or may not match
the Manufacturers or Installers Color
Codes.

Greer CompanyCrane Systems
GREER COMPANY 1918 E. Glenwood Place, Santa Ana, CA 92705 Tel: (714) 259-9702 Fax: (714) 259-7626
MG®400 Computer Training Manual PN W424900 - 11/07/02
16 of 18
To check the Swing Potentiometer, follow the procedure below:
1. Access the computer and Termination Board.
2. Check the Analog Drive voltage.
3. With a digital voltmeter set for DC volts, check the voltage at the connections to the
potentiometer located on the ATB board. Connection 1 has an attached red wire and
connection 3 has an attached black wire.
4. Connect the black lead of the DVM to connection 3 (black wire) and the red lead of the DVM
to connection 1 (red wire). The voltage should be 4.125 +/- 0.1 volts. If this voltage is out of
range, the Termination Board may need to be replaced.
5. With the black lead on any 0 volt terminal, check the voltage at the AIN 5 and AIN 6
terminals. The voltage should be 4.50 +/- 0.1 maximum and 0.365 +/-0.1 minimum.
Both of these voltages should rise and fall linearly within this range, as the upper is rotated
left or right. If the Drive Voltage and the voltage at the connection to the potentiometer were
correct and the voltages on AIN 5 and AIN 6 are out of range, the swing potentiometer must
be replaced.
Contact your distributor or your Factory Service Department for procedures on replacing
the swing potentiometer.

Greer CompanyCrane Systems
GREER COMPANY 1918 E. Glenwood Place, Santa Ana, CA 92705 Tel: (714) 259-9702 Fax: (714) 259-7626
MG®400 Computer Training Manual PN W424900 - 11/07/02
17 of 18

Greer CompanyCrane Systems
GREER COMPANY 1918 E. Glenwood Place, Santa Ana, CA 92705 Tel: (714) 259-9702 Fax: (714) 259-7626
MG®400 Computer Training Manual PN W424900 - 11/07/02
18 of 18
Table of contents
Other GREER Company Desktop manuals
Popular Desktop manuals by other brands
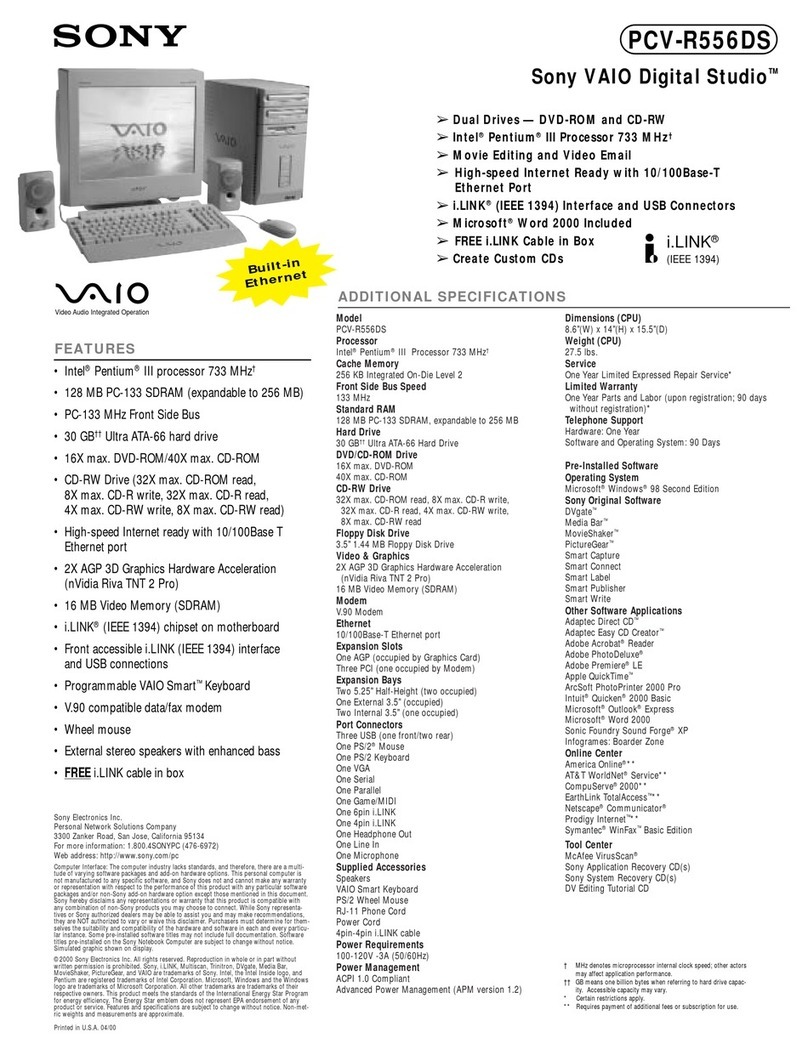
Sony
Sony PCV-R556DS - Vaio Digital Studio Desktop... Specifications

Dell
Dell Precision 370 WHM Quick reference guide
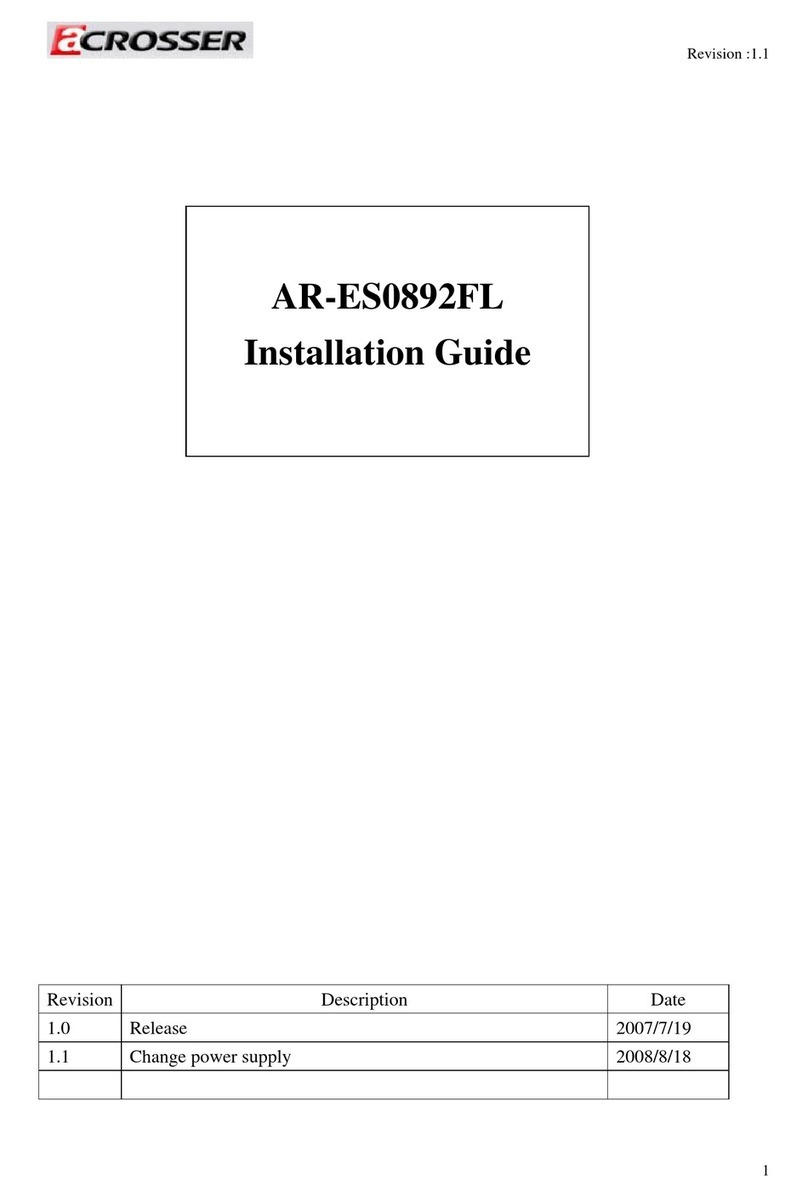
Acrosser Technology
Acrosser Technology AR-ES0892FL installation guide
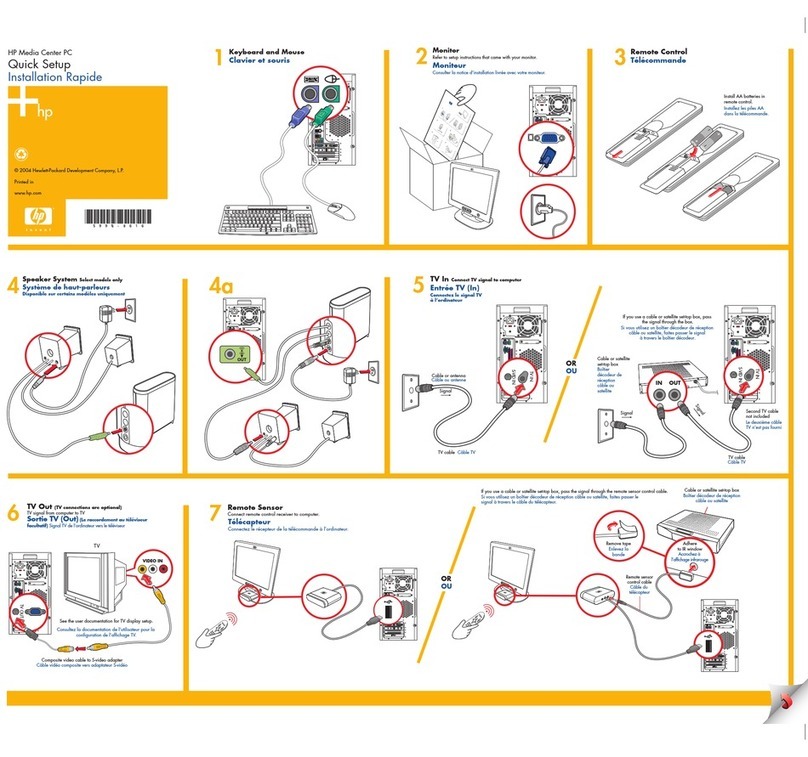
HP
HP Media Center m1000 - Desktop PC Quick setup
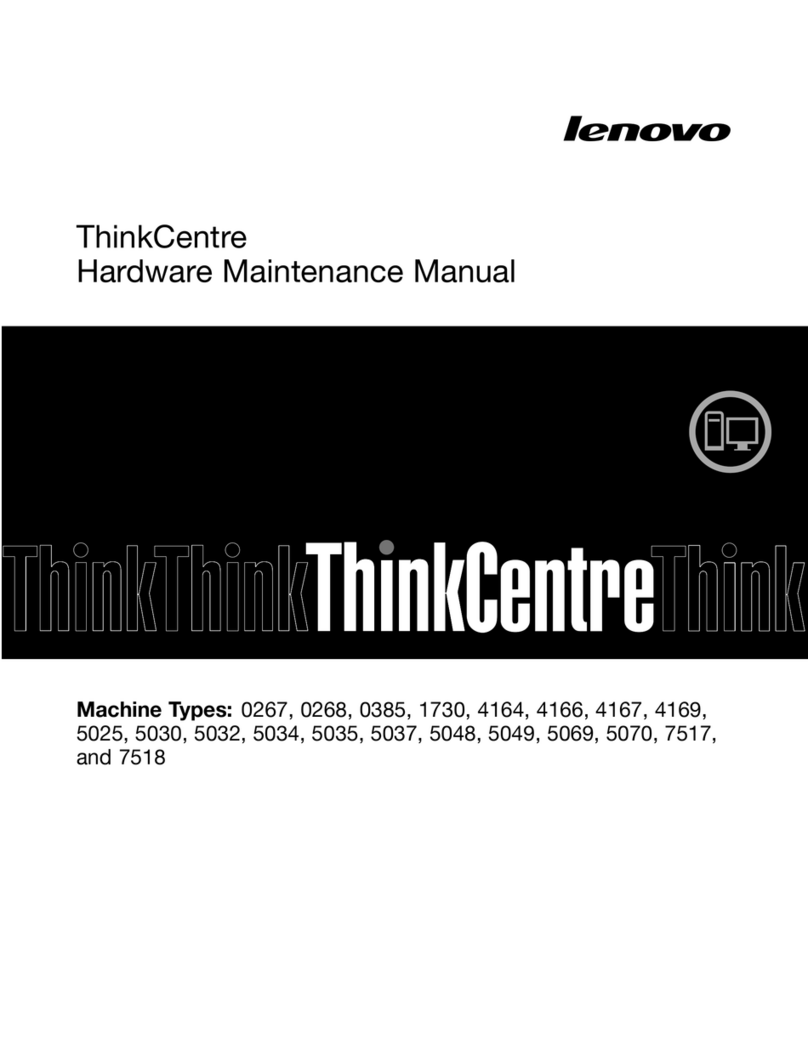
Lenovo
Lenovo 7517A3U Hardware Maintenance Manual
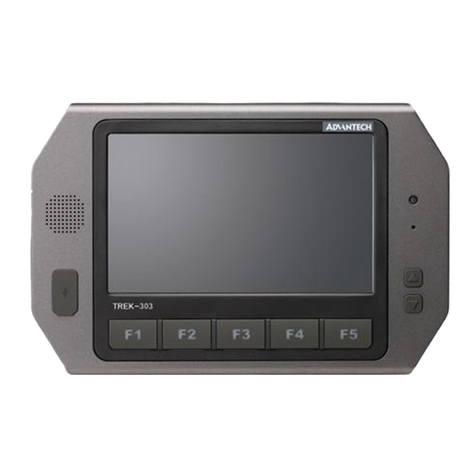
Advantech
Advantech TREK-550 user manual
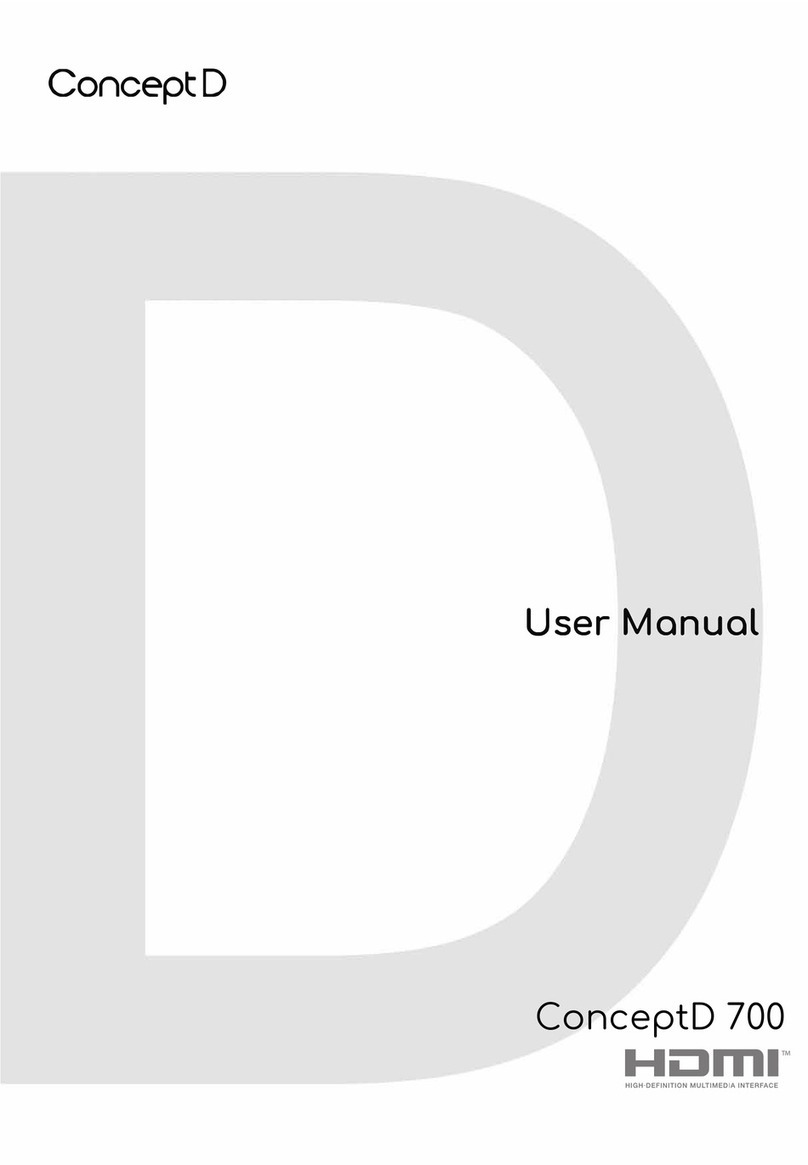
Acer
Acer ConceptD 700 user manual
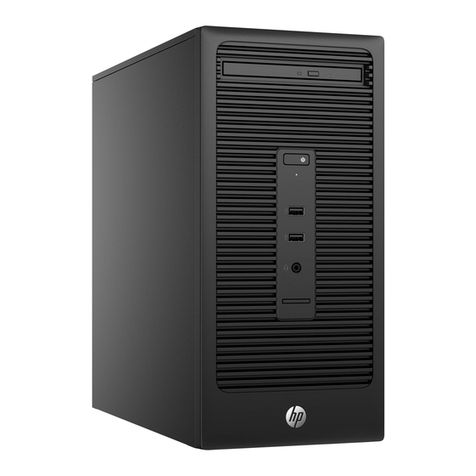
HP
HP 280 G2 MT Business Product End-of-Life Disassembly Instructions
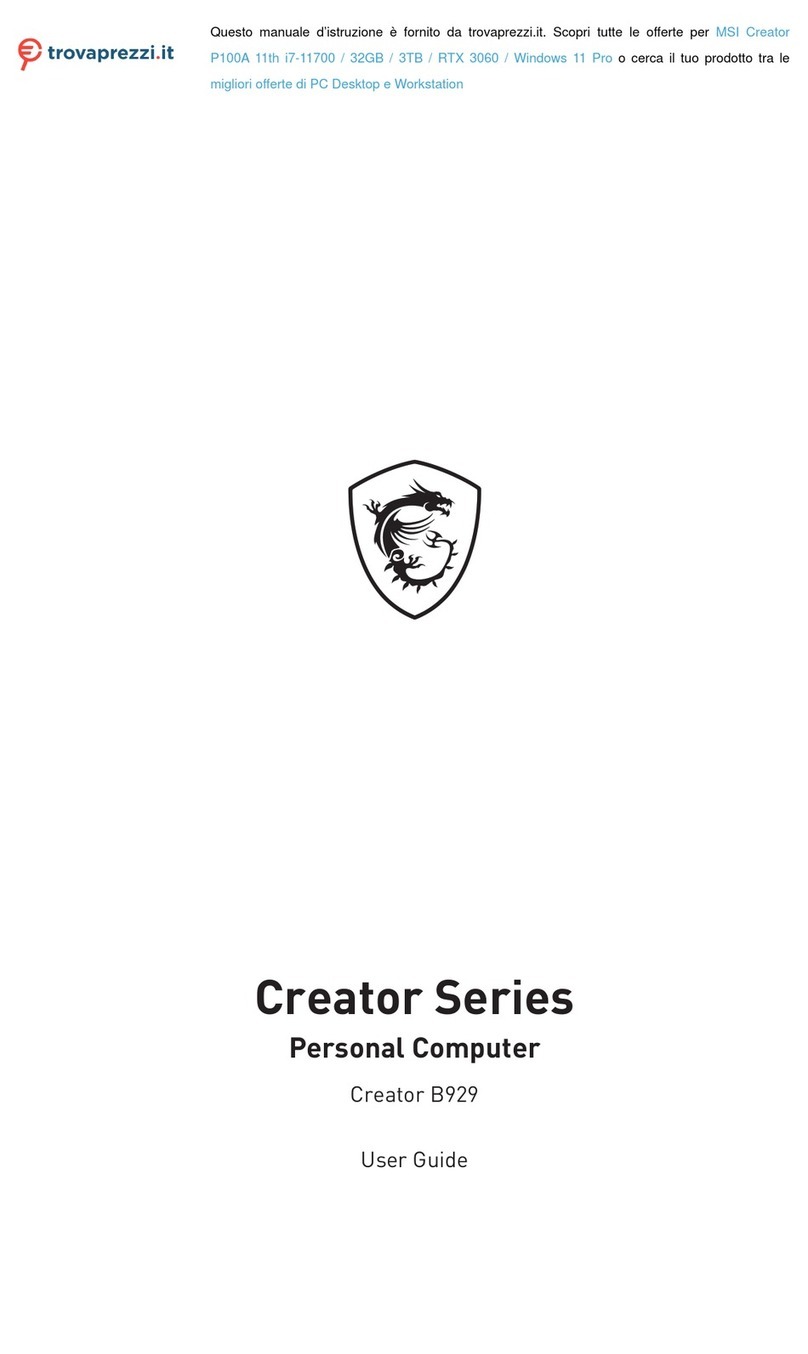
MSI
MSI Creator Series user guide
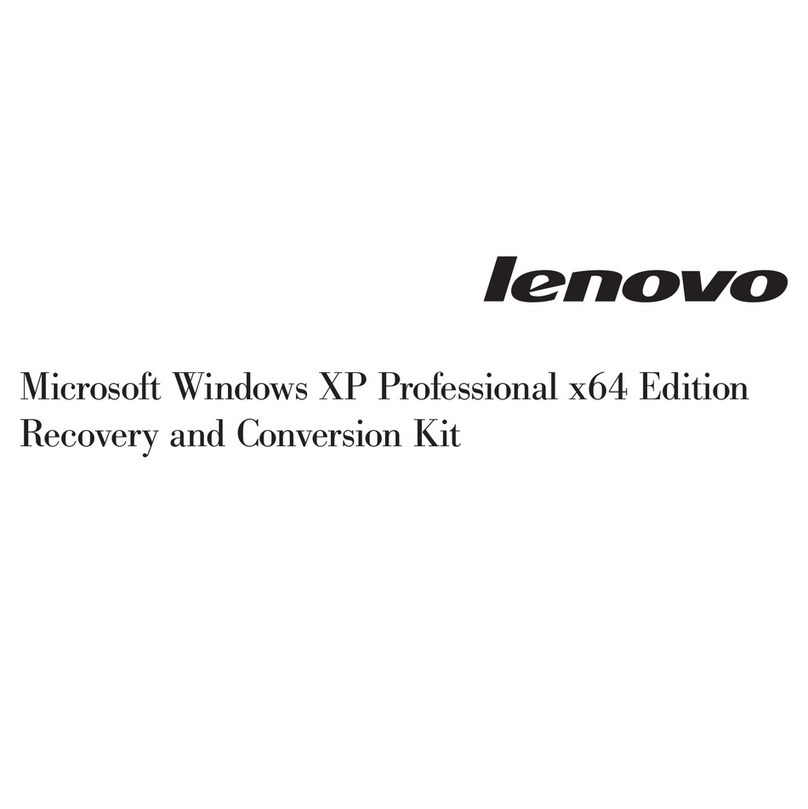
Lenovo
Lenovo ThinkStation D20 manual
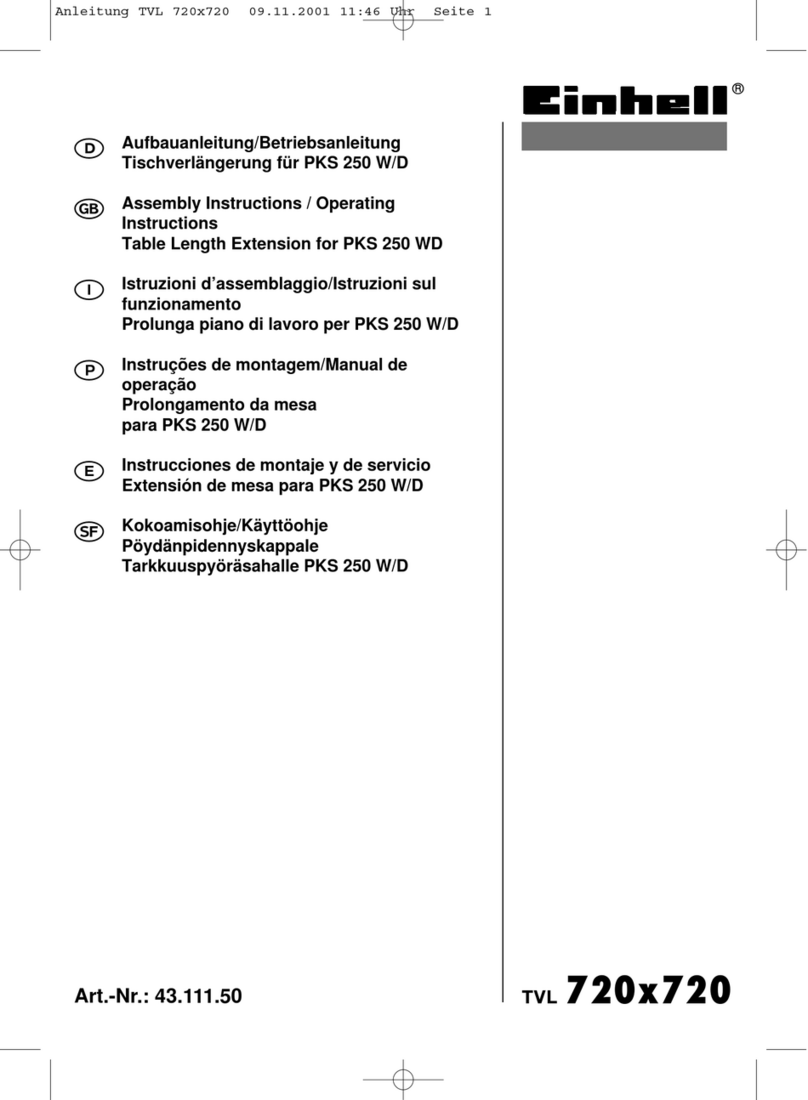
EINHELL
EINHELL TVL 720x720 Assembly instructions/Operating instructions
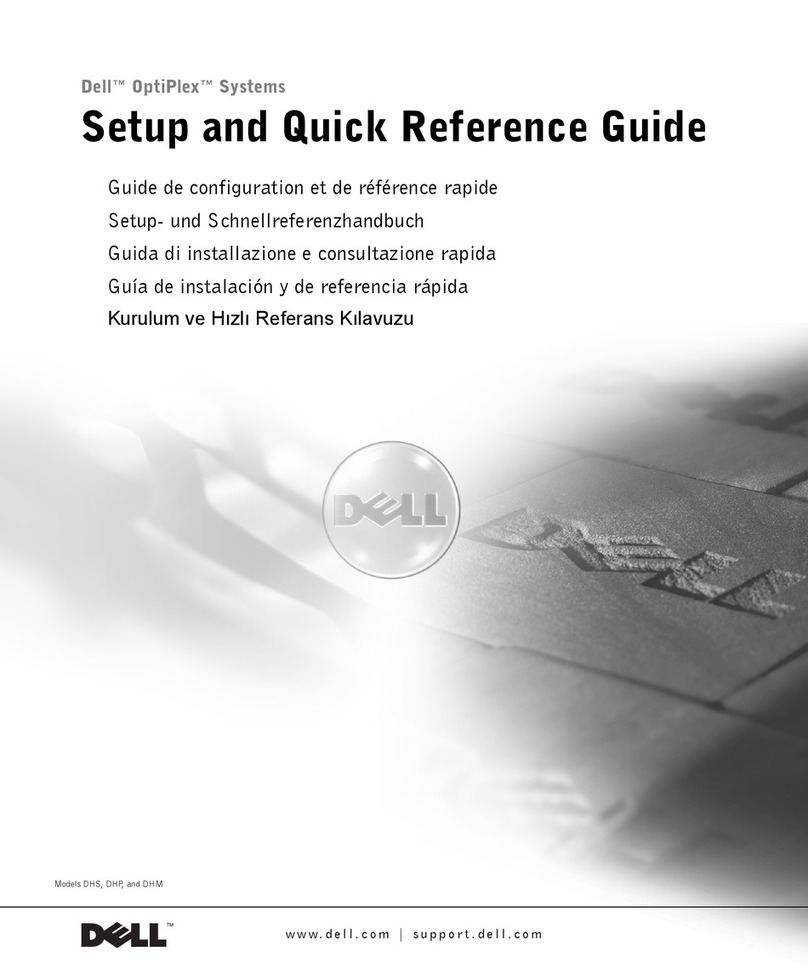
Dell
Dell GX240 - OptiPlex Pentium 4 1.8GHz 512MB 40GB CD... Setup and quick reference guide