HTL DS Series User manual

w
o
r
l
d
w
i
d
e
DEDICATED SQUARE
DRIVE TORQUE WRENCH
OPERATING
INSTRUCTIONS
HTL-Operating-Instructions-DS.indd 1 11/04/2017 10:15

contents...
HTL-Operating-Instructions-DS.indd 2 11/04/2017 10:15

FOR OUR LATEST PRODUCTS & OFFERS VISIT WWW.HTL-WORLDWIDE.COM
2
contents...
Introduction 03
Worldwide Warranty 03
Important Safety Instructions 04
Instructions Before Use 06
Setting the Torque 11
Setting the Pressure 12
Operating the Wrench 13
Loosening Procedure 14
Maintenance 15
Prior to use 17
Troubleshooting 18
Spare Parts List 21
Pressure/Torque Conversion Chart 22
HTL-Operating-Instructions-DS.indd 3 11/04/2017 10:15

OUTSIDE UK: +44 (0) 1670 700 018
3
Introduction
This manual is designed to provide you with the basic knowledge required to operate and maintain
your wrench. Please read this manual carefully and follow the instructions provided. If you have any
questions regarding your HTL Wrench, please call us on +44 (0) 1670 700 018 or alternatively
Your purchase of this wrench entitles you to the following FREE services:
• Free training in the application and operation of your HTL equipment.
• Free engineering assistance.
• Free loan wrenches in case of failure during the warranty period.
Worldwide Warranty
HTL equipment is engineered to the latest technological standards and is accompanied by a 12 month
warranty. Should your new equipment fail under normal use within 12 months, we will repair or replace
your damaged equipment.
HTL-Operating-Instructions-DS.indd 4 11/04/2017 10:15

FOR OUR LATEST PRODUCTS & OFFERS VISIT WWW.HTL-WORLDWIDE.COM
4
Important Safety Instructions
WARNING:Certain safety precautions should be observed to avoid accidents or personal injury. The
following tips will assist you.
• Read All Instructions.
• Keep Work Area Clean and Well Lit.
• Consider Work Area Environment.
Electrical pumps should never be used in any atmosphere which can be considered potentially
volatile. If there is any doubt, use an air pump.
NOTE: Metal to metal contact can cause sparks, precautions should be taken.
• Avoid Premature Tool Starting.
The Pump Remote Control is for the tool operator only. Avoid separate pump and tool operator.
• Stay Clear During Operation.
In most cases, the tool will allow hands free operation.
• Guard Against Electric Shock.
Ensure the pump is properly grounded and the proper voltage is being used.
• Store Idle Tools.
When not in use, tools and accessories should be properly stored to avoid deterioration.
• Use the Right Tool.
Don’t force small tools or attachments to do the job of a larger tool. Don’t use a tool for purposes
not intended. HTL can develop custom accessories for your job to ensure safe and simple
operation. Contact your local HTL representative for more information on our custom engineering
abilities.
• Correct Safety Attire.
When handling operating hydraulic equipment, use work gloves, hard hats, safety shoes, hearing
protection, and other applicable clothing.
• Use Safety Glasses.
• Moving Equipment.
Do not use hydraulic hoses, uni-swivels, pump power or remote cords as means to moving the
equipment.
HTL-Operating-Instructions-DS.indd 5 11/04/2017 10:15

OUTSIDE UK: +44 (0) 1670 700 018
5
• Hoses
Do not kink hoses. Inspect and replace if damaged.
• Shrouds and Cover Plates
All tools are equipped with shrouds and/or cover plates to cover up moving internal parts. If
shrouds are missing or damaged, please contact your local HTL representative for repair. A free
loaner tool will be made available to you during the time of repair.
• Maintain Tools With Care
For top performance, inspect tool powerpack, hoses, connectors, electric lines, and accessories
for visual damage frequently. Always follow instructions for proper tool and pump maintenance.
Refer to the operations maintenance section for further clarication.
• Stay Alert
Always take care. Do not use power equipment under the inuence of any mood altering
substances.
• Prior to Operation
Ensure that all hydraulic connections are securely connected. Verify that the hydraulic hoses are
not kinked. Ensure the square drive and its retainer are fully and securely engaged.
• Prior to Use
Cycle tool to ensure proper function. Locate a solid, secure reaction point. Be sure the reaction
arm retaining clamp is fully engaged. Be sure the hydraulic hoses are free and clear of the reaction
point. Pressurise the system momentarily; if the tool tends to ride up or to creep, stop and
readjust the reaction arm to a more solid and secure position.
• Always Use Quality Accessories
Always use high quality impact sockets in good condition which are the correct size and fully
engage the nut. Hidden aws, however, remain a possibility which could cause breakage, so stay
clear of sockets during operation.
• Do Not Use Force
Do not hammer on the socket or the tool to enhance performance. If the nut will not turn with the
wrench you are using, use a larger size HTL tool.
• Reaction Arm
Proper reaction is required. Adjust reaction arm or plate accordingly. Avoid excessive play. In case
of questions, consult with your HTL oce.
HTL-Operating-Instructions-DS.indd 6 11/04/2017 10:15

FOR OUR LATEST PRODUCTS & OFFERS VISIT WWW.HTL-WORLDWIDE.COM
6
Instructions Before Use
READ CAREFULLY: Most malfunctions in new equipment are the result of improper operation and/or
set-up assembly.
PREPARATION: Remove torque wrench from shipping container.
INSPECTION: Visually inspect all components for shipping damage. If any damage is found, notify carrier
and HTL immediately.
Working Pressure
The tool’s maximum working pressure is 10,000 psi (700 Bar). Make sure that all hydraulic equipment
used with this wrench is rated for 10,000 psi maximum operating pressure.
Hydraulic Connections
When making connections with quick disconnect couplings, make sure the couplings are fully engaged.
Threaded connections such as ttings, gauges, etc., must be clean, securely tightened, and leak free.
If tool operates backwards, couplings are reversed. HTL hoses may only be joined together in odd
numbers only, 1, 3, 5 etc or please contact HTL for bespoke lengths to suit your requirements.
CAUTION: Loose or improper threaded ttings can be potentially dangerous if pressurised, yet, severe
over tightening can cause premature thread failure.
Fittings need only to be securely tightened and leak free. Never grab, touch or in any way come in
contact with a hydraulic pressure leak. Escaping oil could penetrate the skin and cause injury.
HTL-Operating-Instructions-DS.indd 7 11/04/2017 10:15

8OUTSIDE UK: +44 (0) 1670 700 018
Electrical Connections
Ensure correct power availability to prevent motor failure or dangerous electrical overloading. Observe
the motor nameplate for required amperage.
Do not use electric pump if ground is not connected on plug.
Minimise the length of extension cords and be sure they are of adequate wire size with ground
connections.
Extension cable should be 4mm² and maximum length 10 metres.
WARNING: Electric motors may spark. Do not operate in an explosive atmosphere or in the presence of
conductive liquids. If using in a hazardous or explosive atmosphere ensure pump is ATEX approved or
approved to the relevant zone.
Air Connections
Ensure that you have sucient air ow to operate your pneumatic pump. If in doubt, compare the pump
manufacturer’s recommended air ow rating prior to pressurising pump. Improper air ow may damage
the pump motor. For best results use air hoses larger than 3/4 I.D. diameter.
1. Adjust ow to one drop per 60 - 90 seconds
2. Fill half way with grade 46 hydraulic oil supplied
1. Adjust ow to one drop per 60 - 90 seconds
2. Fill half way with grade 46 hydraulic oil supplied
Use of a lter regulator lubricator (FRL) is highly recommended (pictured below).
7
AIR FLOW ON/OFF LEVER
CONDENSATION
BOWL
AUTO WATER
DRAIN PORT
OIL BOWL
OIL LUBRICATOR
ADJUSTMENT KNOB
OIL FILLER CAP
AIR ADJUSTMENT KNOB
l
l
l
l
l
l
l
l
l
l
l
l
l
l
l
l
l
l
l
l
l
l
l
l
l
l
l
l
l
l
l
l
2
46
8
100
HTL-Operating-Instructions-DS.indd 8 11/04/2017 10:15

OPERATION
All HTL torque wrenches are supplied
completely assembled and ready for use.
A HTL hydraulic power pack (for use with your
HTL wrench) is recommended to provide the
speed, pressure, and portability that makes
your HTL system ecient and accurate.
Using calibrated gauges enhances the
accuracy of your hydraulic system.
The accuracy of your 3-in-1Hydraulic
Torque Wrench is +/-3% based upon our
specications. This accuracy is certied
through our calibration laboratory, and we
recommend that the torque wrench be
recalibrated on a 12 month basis and should
be calibrated by a qualied calibration facility
who is traceable to the United Kingdom
Accreditation Standards (UKAS). Please
contact HTL or your local distributor for more
information.
8
FOR OUR LATEST PRODUCTS & OFFERS VISIT WWW.HTL-WORLDWIDE.COM
HTL-Operating-Instructions-DS.indd 9 11/04/2017 10:15

10
OUTSIDE UK: +44 (0) 1670 700 018
Operation
Connecting the System
The wrench head and power pack are connected by a 10,000 psi operating pressure (40,000 psi burst)
twinline hose assembly. Each end of the hose will have one male and one female connector to ensure
proper interconnection between pump and wrench heads.
IMPORTANT: To avoid tool malfunction, do not reverse connectors.
Connect the twinline hose to the uniswivel as shown below:
Ensure the connectors are fully engaged and screwed closely and completely together.
9
R A
HTL-Operating-Instructions-DS.indd 10 11/04/2017 10:15

FOR OUR LATEST PRODUCTS & OFFERS VISIT WWW.HTL-WORLDWIDE.COM
10
Drive Direction Change
To remove the Square Drive, disengage the drive retainer assembly by depressing the round center
button and gently pulling on the square end of the Square Drive. The Square Drive will slide easily out.
To insert the drive in the tool, place the drive in the desired direction, engage drive and bushing splines,
then twist drive and bushing until ratchet spline can be engaged. Push drive through ratchet. Depress
drive retainer button, engage retainer with drive and release button to lock.
The above diagram illustrates the direction the Square Drive should face for loosening and tightening of
a standard right hand fastener.
Right is Tight.
Left is Loose.
Reaction Arm
All HTL torque wrenches are equipped with a universal reaction arm. These reaction arms are
employed to absorb and counteract forces created as the unit operates. The reaction arm should
extend in the same direction of the Square Drive; however, slight adjustments may be made to suit your
particular application.
In operation, the reaction arm must be fully engaged and secured.
To engage the reaction arm, depress the spring loaded button located on the rear of the end cap, push
into position and relase to lock. Ensure the retainer is locked in place prior to using the wrench.
To remove the reaction arm, depress the spring loaded button located on the rear of the end cap and
pull to release.
HTL-Operating-Instructions-DS.indd 11 11/04/2017 10:15

OUTSIDE UK: +44 (0) 1670 700 018
11
Setting Torque
Once the system is fully connected and proper power supply available, it is time to adjust the pump
pressure to the level needed on your job.
When tightening, use the manufacturer’s specications to determine the torque value which you will
ultimately require.
Torque sequence may vary from plant to plant and even within individual plants, depending upon the
gasket material, etc. Always abide by local procedures.
Next, use the pressure-torque conversion chart that is provided for the individual tool, similar to the one
below.
An example of nding the torque required is as follows:
Assume you are going to use a HTL-W2 tool to torque a 1 ¼ bolt to 835 ft.lbs.
1. First check the serial no. on the tool corresponds to the torque chart. On the left hand side of the
chart is the torque values. Find 835 ft.lbs on column
2. Then move across the chart until you come to a diagonal line.
3. At this point, move down to the bottom of the chart. The corresponding pressure value can be
found
4. For example the pressure is 5,300 psi on a tool to produce 835 ft.lbs.
5. Now set pressure on pump as follows in next section.
10,000 PSI = 1633 FT. LBS
1800
1700
1600
1500
1400
1300
1200
1100
1000
900
800
700
600
500
400
300
200
100
1000 PSI= 1171FT.LBS
0 1000 2000 3000 4000 5000 6000
7000 8000 9000 10000 11000
IN PUT (PSI)
Calibration Readout
Torque Values FT/Lbs
HTL-Operating-Instructions-DS.indd 12 11/04/2017 10:15

FOR OUR LATEST PRODUCTS & OFFERS VISIT WWW.HTL-WORLDWIDE.COM
12
Setting the Pressure
To set the pressure on the pump, follow this procedure:
1. Loosen the knurled locking ring below the T handle on the pump’s external pressure regulator. Then
turn the T handle as shown below, CCW (counterclockwise) until it turns freely and easily.
2. Turn the pump on. Using the pump’s remote control pendant, push down the advance switch (or
button on air pumps) and hold it.
3. While holding the pump in the advance mode, slowly turn the T handle clockwise and observe the
pump pressure gauge rise.
4. When your gauge reaches 4,000 psi, stop turning the T handle and let the gauge settle out.
5. If the pressure continues to rise (above 4,000), release the advance button and back o your
pressure slighitly - by turning CCW on the T handle.
6. Then re-depress the advance switch on your remote and slowly bring pressure up to 4,000 psi
again.
7. When the pressure is correct, turn the pump o and tighten the knurled lock nut provided under the
T handle. This sets pump pressure, which determines torque wrench output.
8. Once your target pressure is set and locked, cycle the pump once more to ensure that your
pressure setting did not change as you turned down the knurled knob
NOTE: Always adjust the regulator pressure up, never down.
T Handle
Locking Ring
HTL-Operating-Instructions-DS.indd 13 11/04/2017 10:15

OUTSIDE UK: +44 (0) 1670 700 018
13
Operating the Wrench
The Tightening Process
1. Having set your target pressure, cycle the wrench three or four times to full pressure before putting
it on the application. Cycling the tool ensures that the system is operating properly and removes
trapped air, if any.
2. Place the proper size impact socket on the Square Drive and secure properly with a ring and pin.
3. Place the tool and the socket on the nut, making sure that the socket has fully engaged the nut.
Further ensure that the drive retainer is engaged.
4. Make sure the reaction arm is rmly abutted against a stationary object (e.g. an adjacent
nut, ange, equipment housing etc.) When positioning the wrench, make sure that the hose
connections are well clear of any obstructions, and that all body parts are safely out of harm’s way.
5. THEN, AND ONLY THEN, apply momentary pressure to the system to ensure proper tool
placement. If it doesn’t look or act right, stop and readjust the reaction arm.
In Use
1. By pushing down on the remote control button in the advance position, the rear of the tool will be
pushed back until the reaction arm makes contact with its reaction point.
2. Continue to hold down the button as the socket turns until you hear a click which will signify the
hydraulic cylinder inside the tool is fully extended and will not turn the socket further.
3. Continuing to hold down the remote control button will result in a rapid build up of pressure to the
point of where the gauge reads what was preset prior to applying the wrench.
IMPORTANT: The reading of full preset pressure after the cylinder is extended DOES NOT INDICATE that
this pressure (torque) is applied to the bolt. It only indicates that the cylinder is fully extended and cannot
turn the socket further until the wrench automatically resets itself.
Releasing the remote control button will retract the cylinder. The wrench will automatically reset itself and
the operator will hear a click indicating they can again push the remote control button and the socket will
turn. Each time the cylinder is extended and retracted, it is called a cycle. Successive cycles are made
until the wrench stalls at the preset torque.
HTL-Operating-Instructions-DS.indd 14 11/04/2017 10:15

FOR OUR LATEST PRODUCTS & OFFERS VISIT WWW.HTL-WORLDWIDE.COM
14
IMPORTANT: Always attempt one nal cycle to ensure the stall point has been reached.
Loosening Procedure
First, set the pump to 10,000 psi. Change the drive and the reaction arm to the loosening mode,
ensuring the reaction arm abuts squarely o a solid reaction point. Press and hold the remote control
button down. Pressure will decrease as the socket begins to turn. As the cylinder extends fully, you will
hear a click. Release the remote control button, and the cylinder automatically retracts, at which time you
again hear the click. Repeat this process until the fastener can be removed by hand.
NOTE: If the bolt does not loosen with the above procedure. it is an indication that you require the next
larger size tool to loosen the bolt.
HTL-Operating-Instructions-DS.indd 15 11/04/2017 10:15

MAINTENANCE
Tool failure, although
rare, does occur.
Such failure is
most often in the
hydraulic couplers
or hoses. These
items are repairable
or replaceable
immediately, since
they are available
universally. Failure of
structural members
of the tool are quite
rare, but replacement
parts are available
from stock. All repairs
to HTL tools may be
made by experienced
individuals according
to these instructions.
OUTSIDE UK: +44 (0) 1670 700018
15
HTL-Operating-Instructions-DS.indd 16 11/04/2017 10:15

FOR OUR LATEST PRODUCTS & OFFERS VISIT WWW.HTL-WORLDWIDE.COM
16
• Lubrication
All moving parts should periodically be coated with HTL Pro-Moly grease. Under harsh
environmental conditions, cleaning and lubricating should be performed more frequently.
• Hydraulic Hoses
Hoses should be checked for cracks and leaks before, and after each job. Hydraulic ttings
can become plugged with dirt and should be ushed periodically.
• Quick Connects
Fittings should be kept clean and not allowed to be dragged along the ground or oor, as even
small particles of dirt can cause the internal valves to malfunction.
• Springs
Springs are used for the drive pawl assembly and for the accuracy assurance pawl. These
springs can be replaced if necessary.
• Cylinder Seals
If the cylinder requires disassembly, it is recommended that the cylinder seals be replaced at
the same time. Seal kits are readily available.
• Structural Members
All structural parts on the tool should be inspected once a year to determine if there are any
cracks, chips, or deformities. If so, immediate replacement is required.
Preventative Maintenance
HTL-Operating-Instructions-DS.indd 17 11/04/2017 10:15

OUTSIDE UK: +44 (0) 1670 700 018
Prior to Use
THIS TEST SHOULD BE RUN PRIOR TO EVERY USE OF A HTL TOOL.
Connect the tool, pump, and hoses together as normal. Cycle the pump several times. Cycle the
system once more and observe the sequence of operation. As you depress the advance button, the
tool drive should turn about 24 degrees and you should hear a click. On square drive tools, you will also
notice that the accuracy assurance levers will move to the rear of the tool and spring forward. At this
point, release the advance button. You should see no further movement and after a moment you will
hear another click. This is how the tools are designed to operate. If you observe any other sequence of
operation, the system is out of order and cannot deliver more than 10% of its designed capacity. Take
immediate corrective action. For reference, tools and pumps are designed from the factory plumbed as
follows. This ensures that the tool, pump and ONE hose cannot possible be connected up incorrectly.
• Tool Advance Side - Male
• Retract Side - Female
• Hose Advance Side - Female to Female
• Retract Side - Male to Male
• Pump Advance Side - Male
• Retract Side - Female
NOTE: Connecting two or any even number of hoses together creates one hose which is plumbed
backwards! Male to Female and Female to Male. This will cause the system to operate backwards. If
your hose isn’t long enough, connect 3 hoses together, move your pump or call HTL for a longer hose
assembly.
17
HTL-Operating-Instructions-DS.indd 18 11/04/2017 10:15

FOR OUR LATEST PRODUCTS & OFFERS VISIT WWW.HTL-WORLDWIDE.COM
18
Troubleshooting
Symptom Probable Cause Action Required
Gauge shows
pressure
build-up but
the tool will
not cycle.
1. Couplings loose or
inoperative.
2. Solenoid inoperative.
1. Tighten and/or replace couplings.
2. If solenoid is bad, replace.
Cylinder will
not retract.
1. Voltage to electric
pump is too low to line
drop or inadequate
amperage is available.
2. Linkage between
piston rod and drive
arms are broken.
1. Get shorter extension cord. If shop power is adequate, draw power
from welding machine or cal rod transformer.
2. Replace part as necessary
Wrench
pressure will
not build.
1. Oil blow by in wrench
(Piston seal leak,
blown O-ring, cracked
piston).
2. Pump problem.
1. Replace defective parts. Return to HTL.
2. Check to see if sub plate is worn. Remove screws from pump motor
to reservoir, slide pump motor to the side, turn pump on and while
holding down on the button, put your nger on the dump tube (round
tube under the directional control valve) if you feel pressure, then
replace the subplate and shear seals.
3. Check to see if you have leaks from the external relief valve and the 2
oil line connections (bottom of relief valve and connection into pump
body’s other end) of oil line. If leaking, retighten with 9/16” open end
wrench. Return to HTL.
4. If pump sounds like there is rattling in the air motor, take pump to
your local HTL oce or Distributor.
5. Air Pumps - Faulty air valve due to excessive moisture and/or dirt
in air supply. Disassemble air valve and wipe any residue from air
valve piston. Spray brake cleaner into air valve body, dry thoroughly.
Disassemble all small air lines and blow out with compressed air.
Lubricate both air valve piston and body with hydraulic oil (sparingly)
and reassemble. Return to HTL.
6. Air pumps - Faulty.
HTL-Operating-Instructions-DS.indd 19 11/04/2017 10:15

20
OUTSIDE UK: +44 (0) 1670 700 018
Symptom Probable Cause Action Required
Gauge
records no
pressure.
1. Gauge connection is
loose.
2. Bad gauge.
3. Pump will not build
pressure.
4. Tool seals are blown.
1. Tighten coupling.
2. Replace gauge
3. Return to HTL
4. Replace defective seals. Return to HTL.
Pump will
not build
pressure.
1. Air or electric supply
is low.
2. Defective relief or
regulator valve.
3. Low oil or clogged lter.
4. Internal leak in oil line
from external relief valve
to pump body.
5. Worn sub-plate.
1. Check air pressure or voltage.
2. Replace valve Return to HTL.
3. Fill reservoir and clean lter.
4. Open reservoir, inspect oil line while trying to build pressure if leaking
tighten ttings or replace.
5. See cylinder pressure will not build pressure above.
Motor
slow and
inecient
Sounds
laboured.
Slow
to build
pressure.
1. Air or electric supply
is low.
2. Clogged lter.
1. See #1 in preceding block
2. Clean or replace lter
Pump
heats
up.
1. Improper use.
2. Remote control is left in.
3. On position when pump
is not actively in use.
1. Have operator release advance stroke after accuracy assurance
levers spring forward.
2. Turn pump o whenever not actually being used. DO NOT leave pump
running when tool is not in use.
Hose or tool
tting is
damaged or
leaks.
1. Broken or melted plastic
outer covering.
2. Frayed Kevlar or steel
strands.
3. Oil leaks through bers.
4. Broken ttings.
1. If underlying Kevlar or steel is still intact continue operation. Inspect
frequently.
2. Cut hose in half and discard. Replace hose.
3. Remove old tting and replace with STEEL high pressure ttings only.
Electric
pump will
not run.
1. Loose electric
connections in control
box.
2. Bad brushes.
3. Motor burned up.
1. Replace motor components whichever is
necessary. Return to HTL.
2. Change defect fuse.
Tool locks
on to nut.
1. Drive segment is loaded
when the tool is maxed
out in torque.
2. Tool is operating
backwards.
3. Tool is wedged under a
xed object.
1. Press advance button on remote and build pressure - continue to
press down on remote while pulling back on one of the accuracy
assurance levers - release remote while continuing to hold back on
levers.
2. Push advance button down - tool should immediately fall free.
3. Remove shroud from around ratchet. Using any tool available, pry the
drive segment out of the ratchet and at the same time pull back on the
accuracy assurance levers. Tool should swing free or burnaway the
socket or obstruction.
19
Troubleshooting
HTL-Operating-Instructions-DS.indd 20 11/04/2017 10:15
This manual suits for next models
28
Table of contents
Other HTL Power Tools manuals
Popular Power Tools manuals by other brands
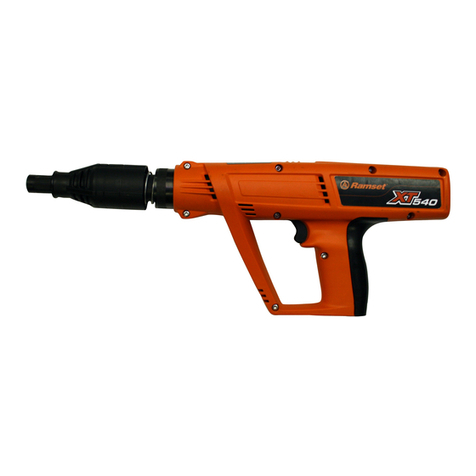
RAMSET
RAMSET XT540 Operator's safety & operating instruction manual
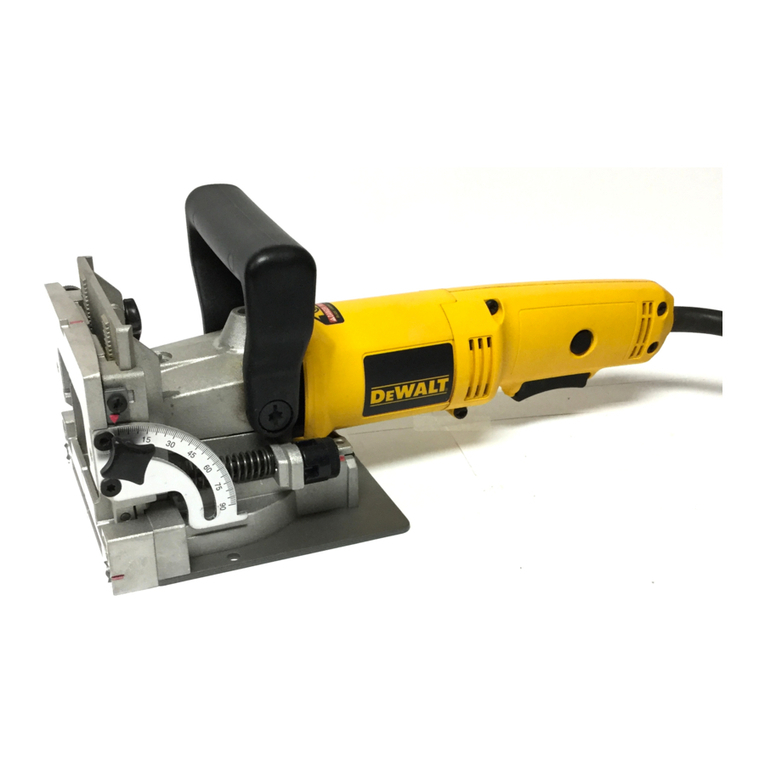
DeWalt
DeWalt DW682 Original instructions

Makita
Makita RF1100 instruction manual

Earlex
Earlex HG 2000K operating instructions

Sealey
Sealey STW805 quick start guide
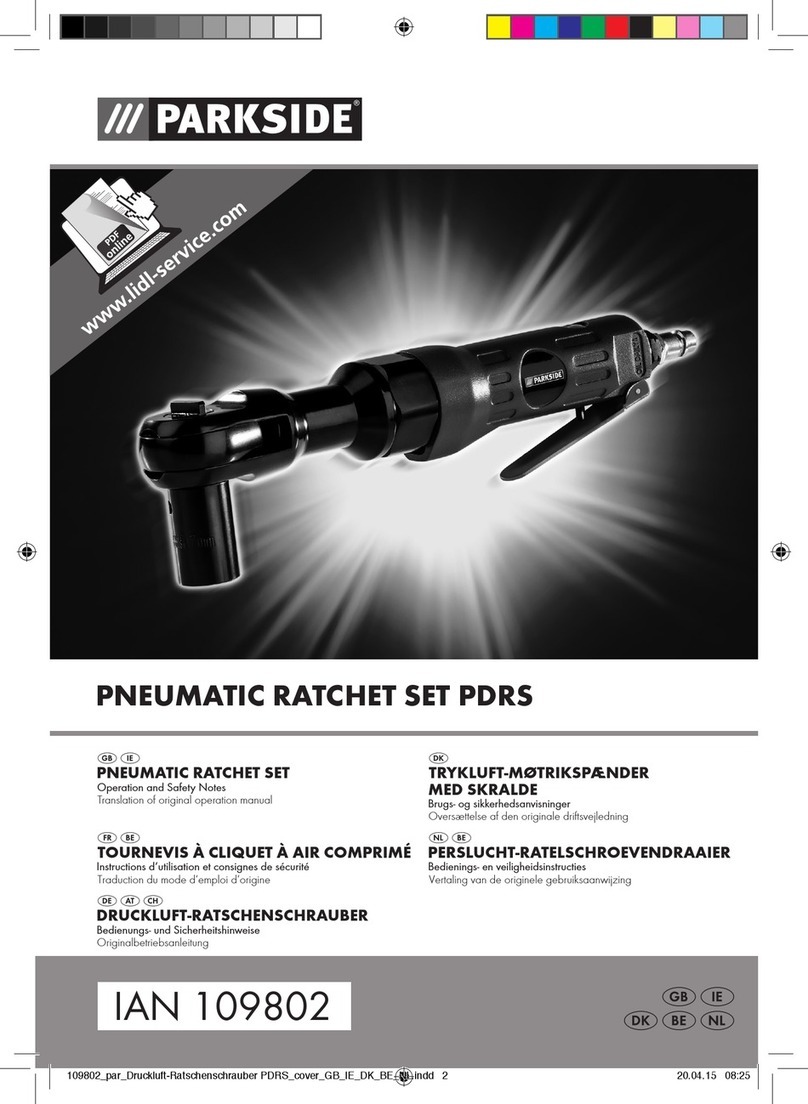
Parkside
Parkside 109802 Operation and safety notes translation of original operation manual