Igema EWLS User guide

Edition 03/2021
D-05-B-51500-EN-00
Installation and operating instruction
EWLSfor use with level probes: EL65 or EL60
Electronic Water Level Switch

2
Product philosophy
Thank you for placing your trust in IGEMA and deciding in favour of one of our
high-quality products.
For more than 100 years, measuring and control systems have been developed,
produced and sold worldwide under the IGEMA brand name.
“Steam is our passion” and we offer you the entire programme for the safe and
economic operation of your plants, especially in the steam and condensate sector.
Please read the installation and operating instructions carefully to ensure a safe and
reliable operation.
In addition to the information on installation and operation, you will also find important
information on maintenance, care, safety and value retention of your measuring and
control system.

3
Table of contents
1. Important safety instructions.............................................................................6
1.1 Symbols used in these instructions...................................................................6
1.2 Intended use of the device................................................................................7
1.3 Safety at work ...................................................................................................8
1.4 Safety instructions for this device......................................................................9
1.5 Exclusion of liability...........................................................................................9
2. Contents of the packaging...............................................................................10
3. Important information.......................................................................................10
3.1 Use in compliance with regulations.................................................................10
4. System description...........................................................................................10
4.1 Components....................................................................................................10
4.2 Function..........................................................................................................11
4.3 Setup...............................................................................................................12
4.4 Components of the control unit (CU-3)............................................................12
4.5 Operation........................................................................................................13
4.6 Error message ................................................................................................13
4.7 Overview of the system properties..................................................................13

4
Table of contents
5. Assembly and Installation................................................................................14
5.1 Water column..................................................................................................14
5.1.1 Installation dimensions and descriptions ....................................................15
5.1.2 Installation...................................................................................................15
5.2 Control unit CU-3 ............................................................................................16
5.2.1 Installation dimensions and descriptions ....................................................16
5.2.2 Power connection.......................................................................................17
5.3 Measuring unit MU-3.......................................................................................18
6. Configuration via Menu ....................................................................................19
7. Special features of system setup ....................................................................22
8. Commissioning .................................................................................................22
8.1 System setup..................................................................................................22
8.2 Factory settings...............................................................................................23
8.3 Commissioning when starting up the boiler.....................................................23
8.4 Commissioning during boiler operation...........................................................23
9. Technical data ...................................................................................................24
9.1 Device data.....................................................................................................24
9.2 Mains transformer...........................................................................................25
9.3 Rating plate.....................................................................................................26

5
Table of contents
10. System maintenance.........................................................................................27
10.1 Depressurising the water column................................................................27
10.2 Dismantling and fitting probes.....................................................................28
11. Fault analysis and rectification........................................................................29
12. Declaration of conformity.................................................................................31
13. Attachments ......................................................................................................32

6
1. Important safety instructions
KEEP THESE INSTALLATION AND OPERATING INSTRUCTIONS IN A SAFE PLACE!
Commissioning as well as maintenance and repair work may only be carried out by qualified
persons in compliance with the installation instructions given in this operating manual. The
correct installation, commissioning, maintenance and operation of the device presupposes that
the person in charge is familiar with measurement and control systems and complies with the
general installation and safety instructions. In addition, the correct and intended use of tools
and the handling of safety devices mustbe ensured. Unqualified persons must not be assigned
the above tasks!
IGEMA GmbH accepts no liability for damage to property or personal injury caused by
unqualified persons or by failure to observe these installation and operating instructions. If no
sufficiently qualified person can be found, IGEMA GmbH can be commissioned with the
installation/maintenance.
1.1 Symbols used in these instructions
In the following installation and operating instructions, safety instructions are marked with the
following symbols:
Danger
This symbol and signal word refer to a potentially
hazardous situation which could result in death or
injuries if ignored.
Caution electrical voltage
This symbol and signal word indicate live parts
with an immediate danger of death from electric
shock.
Caution hot
This symbol with a signal word indicates a
potentially hazardous situation that can result in
severe burns and scalds all over the body.

7
Caution
This symbol and signal word refer to a potentially
hazardous situation which could result in
personal injury, property and environmental
damage if ignored.
Caution
This symbol and signal word refer to a potentially
hazardous situation which could result in damage
to the equipment if ignored.
Info
This symbol indicates useful information and
recommendations as well as measures that will
prolong the value of your measuring and control
system.
1.2 Intended use of the device
Use these installation and operating instructions, the identification on the rating
plate (see 9.3) and the technical data sheet to check whether the device is
suitable for the intended use/application. The device complies with the
requirements of the European Pressure Equipment Directive 2014/68/EU.
The device may only be used to indicate fill levels on containers.
The maximum values of the pressure and temperature range of the device must be checked
before installation. If the maximum allowable operating values of the device are lower than
those of the system on which it is to be installed, protective instruments for the device, such
as pressure reducers or similar, must be provided to avoid limit situations. The device may
only be used in accordance with the information in these installation and operating instructions
or for the parameters and applications agreed in the supply contract. (see rating plate, 9.3)
The operator of the facility is obliged to familiarise himself on the compatibility of the medium
and the device. In case of doubt, contact the relevant installation manager or site manager.
The correct installation position, alignment and flow direction of the device must be observed!
Before installing the IGEMA product on boilers or containers, it is essential to remove all
protective covers and, if necessary, the protective film from rating plates.
Caution

8
1.3 Safety at work
Before installation or carrying out maintenance work on the device, safe access
must be ensured and a secure working area with sufficient lighting must be
defined and marked out. Always use lifting equipment for heavy loads!
Before starting any work, carefully check which liquids or gases are or have been in the
pipeline. (flammable substances, irritating substances, substances hazardous to health) When
opening or dismantling the device, residues of the medium can escape. Subsequent fumes
are also possible in unpressurized and cold systems. Use designated PPE such as safety
goggles and respiratory protection!
Special attention must be paid to the condition of the environment around the installation or
maintenance site. Be aware of e.g.: potentially explosive atmospheres, lack of oxygen in tanks
and pits, dangerous gases/liquids, extremetemperatures, hot surfaces, fire hazard (e.g. during
welding) and moving machine and system components. Protect yourself from excessive noise
by taking the required protective measures.
For all maintenance work or new installations, on new or existing boilers or vessels, it is
imperative to check that the boiler or vessel has been depressurised and that the pressure has
been safely reduced to atmospheric pressure. In principle, no system should be regarded as
unpressurized even if indicated by pressure measuring devices such as pressure gauges or
sensors. When releasing the pressure, make sure that no persons are in the release area.
Carefully check whether you and/or other persons in the vicinity need PPE to protect yourself
from external influences such as high and low temperatures, radiation, noise, danger to eyes,
loose objects that can fall down or chemicals.
There is always a risk of injury when handling large and/or heavy equipment. Observe the load
handling regulation as a minimum requirement for working with loads. Avoid handling the
device with your own physical force, e.g. by lifting, pulling, carrying, pushing or supporting it,
especially to prevent back injuries. Use lifting equipment to move heavy and bulky equipment
in accordance with Article 1, Section 2 of the German Load Handling Regulation
(LasthandhabV).
Under normal operating conditions the surface of the device can become very
hot! Under the maximum operating conditions, the surface temperature can
exceed 350°C. After shutting off or, if necessary, shutting down the boiler, wait
until the temperature has normalized to room level. To avoid the risk of burns
and scalds, always use PPE including safety goggles!
Danger
Caution
hot!

9
1.4 Safety instructions for this device
These installation and operating instructions are an integral part of the device
and must be forwarded to the responsible departments "Goods inward,
Transport, Installation, Commissioning and Maintenance". They must be kept in
such a way that the technical staff have access to these documents at all times.
If the device is passed on to a third party, these installation and operating
instructions must also be included in the national language of the third party.
Avoid shocks and hard contact during transport, as this can lead to damage. During
intermediate storage, the device must be kept dry and secured against damage.
When servicing the unit, check for damage. There is a risk of cutting hands and arms! Wear
work gloves!
For units with a dead weight of 30 kg or more, the customer must provide adequate support
(e.g. via a spring suspension device, etc.). This can be attached to the holding strap/eyelet on
the device.
When returning goods to IGEMA GmbH, the applicable safety and environmental laws
according to GGVSEB [German ordinance on the national and international carriage of
dangerous goods by road, rail, and inland waterways] must always be observed. If there are
any risks to health or the environment due to residues or the device has a mechanical defect
this must be indicated when returning the device and the necessary precautionary measures
must be taken. If the returned goods are devices that have come into contact with or contain
hazardous substances, a safety data sheet must be enclosed, and the goods must be clearly
marked. In addition, the hazardous substance must be reported to the logistics service
provider.
1.5 Exclusion of liability
IGEMA GmbH Mess- und Regelsysteme will assume no liability if the above regulations,
instructions and safety precautions are not observed and followed. If they are not expressly
listed in the installation and operating instructions, changes to an IGEMA device are carried
out at the risk of the user.
Caution

10
2. Contents of the packaging
1 EWLS consists of:
Water column with number of probes ordered (EL65 (<=32bar) or EL60 (>32bar))
Measuring unit (MU-3); completely pre-wired
Control unit (CU-3)
Switch box with green / red signal lamps and yellow warning lamps 24 VDC
1 set of installation and operating instructions
3. Important information
3.1 Use in compliance with regulations
The Electronic Water Level Switch (EWLS) is used for level monitoring of electrically
conductive liquids.
Typical applications:
- Steam lines (monitoring and discharge of condensate)
- Feedwater tanks (water tank, deaerator, condensate monitoring)
- Flash tanks, feedwater preheaters
- Turbine protection against water ingress (TWIP)
- Steam cooler
- High and low water (alarm and control)
The EWLS has been developed in compliance with the EU Directives 2014/35/EU,
2014/30/EU, 2014/68/EU and the standards:
EN 61000 -4 EN 61000 -6
EN 61010 -1 EN 13445
DIN EN 12952-7 DIN EN 12953-6
4. System description
4.1 Components
- Water column with number of probes ordered (EL65 (<=32bar) or EL60 (>32bar))
- Measuring unit (MU-3); completely pre-wired
- Control unit (CU-3) with separate power supply unit; for top-hat rail fitting within its switch
box
- Display unit (DU-3) –(optional) (4-20 mA)
- Various CAN-Bus connecting cables (optional)

11
H3
H6
H7
H4
H5
H2
H1
4.2 Function
The detection is done by a conductive measuring principle, which requires a minimum
conductivity of the liquid. The conductivity of the medium is measured in the unit µS/cm. The
conductive measuring method makes two statements: electrode immersed, or electrode
immersed.
The measuring unit (MU-3) can be equipped with up to 4 probes. Their spacing can be
determined by the customer.
Both the measuring unit and the control unit have 2 independent electronic circuits with their
own processors. All processors perform a regular self-check for internal errors ofthe electronic
circuits.
The control unit (CU-3) processes the acquired signals and controls the downstream functions.
It is installed in a steel housing (IP65/NEMA4X). In the switch housing there are two lamps per
electrode (water=green, steam=red), normal operation (green LED), water alarm (yellow) and
system error (yellow):
System Status
LED on
Status of
probes
Arrangement of the lights on the switch box door
Normal
Operation
H1, H5,
H7
All probes
in steam
System error /
Physical state
not possible
H1, H2,
H5, H6
Probe 1 in
Steam
Probe 2 in
Water
Water alarm
Visual Warning
H1, H4,
H7,
H3 blinkt
Probe 1 in
Water
Probe 2 in
Steam
Water Alarm
H1,
H4,H6,H
3
Probe 1 in
Water
Probe 2 in
Water
One contact (SPDT) is permanently connected as a signal contact for device errors. Signalling
(e.g. for PLC) for the 4 probes is done via a separate output contact each. Each processor
controls its own relay per contact, whereby the output contacts are only switched when both
processors signal the normal operating state in unison. In addition, a 4mA - 20mA interface is
available as an output. For each immersed probe, the output is increasedby the corresponding
proportion (16 mA / number of probes). In the event of an error, the output goes to 2 mA.
Programming is done via 4 buttons and a 2-row LCD display with 16 characters each. The
LCD display is also used for local error indication, such as failure of a supply, probe error,
display error (water over steam), electronic error as well as cable error (break or short
circuit). The local display, which is visible from a distance, informs the user of the system
status. If a fault occurs in the system, it is displayed immediately.

12
4.3 Setup
For ensuring high availability IGEMA recommends the use of 2 power supply units
(redundancy). In terms of hardware the CU-3 is designed for operation with 2 power supply
units.
Both the measuring unit (MU-3) and the control unit (CU-3) have 2 independent electronic
circuits with their own processors. All processors carry out regular self-tests for internal faults
in the electronic circuit. This provides self-monitoring of the device and thus a higher safety
standard.
Measuring unit
Both electronic circuits record the state of the probes and send it to the control unit.
Control unit:
Both electronic circuits evaluate the status messages of both electronic circuits of the
measuring unit. If both status messages are identical the required reaction (Chap. 4.2) is
carried out.
A plausibility check takes place.
Each electronic circuit switches its “own” relay (SPDT) for the corresponding output. Only
when both relays of both electronic circuits are driven (activated)equally (e.g. during normal
operating status) is the output active.
The output contacts do not have any latching. The switching behaviour is
exclusively in line with the desired specified (programmed) state. If
latching is required, this manual locking (latching) must be carried out on
site.
4.4 Components of the control unit (CU-3)
The control unit contains:
1 LCD display (2-line each 16 characters) for communication with the operator
(Programming and information display)
4 buttons for programming
3 LEDs as additional status indication
3 SPDT outputs to be freely assigned by customer (see assignment plan Chap.: 5.2.2)
when using two probes
1 4mA.. 20mA output for loads up to 500Ω, not galv. insulated (optional)
Danger

13
4.5 Operation
Operation of the EWLS is carried out by the 4 buttons on the front of the Control Unit CU-3.
This is described in Chap. 6 “Configuration via Menu”.
4.6 Error message
In the LCD display of the CU-3 errors from the evaluator and probes are displayed number-
coded and in plain text abbreviations.
For analysis and error correction see Chap. 11.
4.7 Overview of the system properties
- Up to 4 probes (minimum 2 probes) for level measuring / switching
- Can be used up to design pressures PS = 200 bar / 2901 PSI // Design temp. of TS =
554°C / 1030°F
- Double power supply (optional) for high availability (redundancy)
- Self-monitoring electronics for high system safety during monitoring functions
- Wire breakage monitoring
- Adjustable switching delay on all outputs for avoiding false signals
- 1 potentially free alarm output (SPDT) for the reaction in case of low water and/or
overfilling
- 1 potentially free error output (SPDT) for the display of (electronic) system errors
- 3 user specific and freely programmable outputs (SPDT): (when 2 probes are used in the
EWLS)
IGEMA
EWLI3 - CU

14
Enabling:
* Individual switch points e.g. horn when exceeding or falling below a fill level
* Double switch points e.g. for a pump control
In the case of identical programming of two outputs a “DPDT output” is possible.
- 1 4mA..20mA output for loads up to 500Ω, not galv. insulated (optional)
5. Assembly and Installation
5.1 Water column
Measuring unit MU
Process connections
Probes
Protective housing

15
5.1.1 Installation dimensions and descriptions
Process connection: on the side
Process connection: on the top/bottom
A: Boiler / Vessel connection dimensions
E: Visible length / switching range
D: Minimum water level
t: Probe distance
5.1.2 Installation
The water column with probes is supplied fully pre-wired.
It is attached via the process connections in accordance with the rules / regulations on the
boiler. Because of the temperature-dependent density of the medium, it must be
ensured that a flow through the add-on housing with the medium is
ensured, e.g. through a forced circulation (inclination).
Caution

16
5.2 Control unit CU-3
The control unit and also the associated power unit(s) are supplied in a plastic plug-in housing
for fitting into switch cabinets. The housing is designed for quick fitting with a spring catch for
the DIN EN 50022 standard 35 mm carrier rail.
Ensure protection class in accordance with current regulations
With quick fitting with a spring catch for standard DIN EN 50022 35 mm carrier rail
Fix device on standard carrier rail by means of the snap fastening (4).
5.2.1 Installation dimensions and descriptions
Front view:
Side view:
IGEMA
EWLI3 - CU
Danger

17
5.2.2 Power connection
The device terminal strip is live during operation!!
Before working on the device disconnect it from the mains!!
If inductive equipment is connected, voltage peaks occur when switching
off. For this reason, connected inductive equipment (e.g. contactor) must
be provided additionally with an RC circuit: e.g. 0.1µF / 100 .
The output contacts are only switched when both electronic circuits
energise the corresponding relays (Chap. 4.3)
For free assignment are solely the outputs 5-7 and 2 potentially free
outputs. All of these 5 SPDT outputs are located on the terminal strip X3.
Assignment plan:
Danger
Danger
Caution

18
5.3 Measuring unit MU-3
The measuring unit is fixed to the water column and the probes are fully wired. The connection
to the control unit takes place via a 5-pin plug at the bottom of the switching cabinet of the
measuring unit.
If no assembled cable isordered, the assembling of theenclosed plug socket is done according
to the Device NetTM BUS System.
PIN
Lead colour
Signal
Device
NetTM
1
Drain
2
RD
V+
3
BK
V-
4
WH
CANH
5
BU
CANL
Screen fixed to housing
Pin assignment on the MU circuit board:
Connecting terminal
Signal
Device NetTM
2
o
⎯⎯
CAN L
3
o
⎯⎯
CAN H
4
o
⎯⎯
V -
5
o
⎯⎯
V +
Cable plug M12, 5-pin, A-coded
Cable socket M12, 5-pin, A-coded

19
6. Configuration via Menu
The menu of the EWLS is divided into two levels:
Level 1 | Level 2
The menu is accessed by pressing the “OK” key. A menu item of Level 1 will appear in the
LCD display. With the keys “▲” or “▼” you can choose between the menu items of the
respective level. The upper row is “active”.
By pressing the “OK” key you will get to the next level down or confirm the entry.
By pressing the “ESC” key you can get to the next level up or out of the menu without the
current entry being saved. (With “OK” confirmed data are already saved and remain so.)
The menu language is English
Automatic menu exit after 2 minutes if no key operation is carried out (without saving /
see “ESC).
The menu consists of 4 items. Items 1 to 3 are purely for information! Whereas item “1.1 Probe
state” and above all item “1.2 Relay state” are very useful for checking the correct programming
and the desired switching operations.

20
Diagram:
| --- 1. System Info ---
| | - 1.1. Probe state |
| | - 1.2. Relay state |
| | - 1.3. MU system A |
| | - 1.4. MU system B |
| --- 2. Supply ---
| |- 2.1. Input Pin 1 |
| |- 2.2. Input Pin 2 |
| |- 2.1. Output Pin 3 |
| --- 3. Version ---
| |- 3.1. Control |
| |- 3.2. Measurement |
| |- 3.3. Display |
| --- 4. Settings ---
| |- 4.1. Backlight |
| |- 4.2. Password |
| --- |-----After entering valid password------------------
| |- 4.3. Relay setup |
| |- 4.4. LLW Alarm |
| |- 4.5. HHW Alarm |
The password is: 123; it unlocks programming points 4.3, 4.4 and 4.5 and
is only used to prevent unintentional system programming.
Menu description:
1.1 Probe state: The state of the probes is displayed, “w” for water, “s”
for steam.
For illogical states, for example water over steam, the
submerged probe is displayed in capitals (e.g. “W”).
1.2 Probe state: The switch state of the 9 outputs is displayed “0” for rest
position (NO) and “1” for activated.
1.3/1.4 MU System A/B:Temperature of the respective electronics of the
measuring unit.
2.1 Input Pin 1: Supply voltage 1 (theoretical 24 V)
2.2 Input Pin 2: Supply voltage 2 (theoretical 24 V)
2.3 Output Pin 3: Can-Bus –voltage (theoretical 23.5 V)
3.1 Control: Version number CU
3.1 Measurement: Version number MU
3.1 Display: Version number DU
4.1 Backlight: Brightness setting of LCD display
4.2 Password: Password “123”
Caution
Table of contents
Popular Switch manuals by other brands
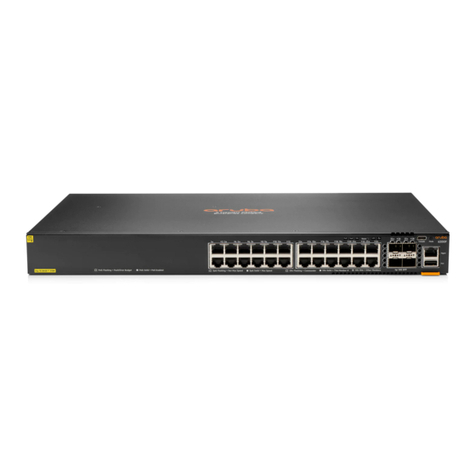
HPE
HPE Aruba 6200F Product End-of-Life Disassembly Instructions
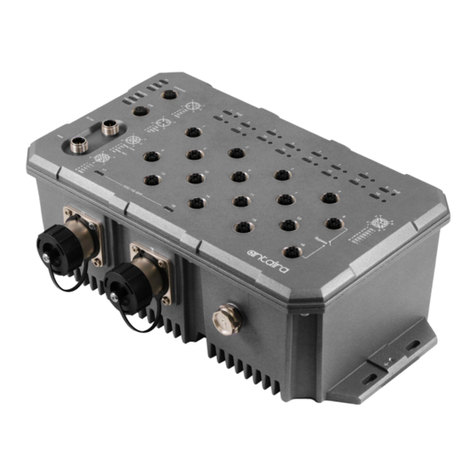
ANTAIRA
ANTAIRA LMP-1802G-M12-10G-SFP-67-24 Series Hardware manual
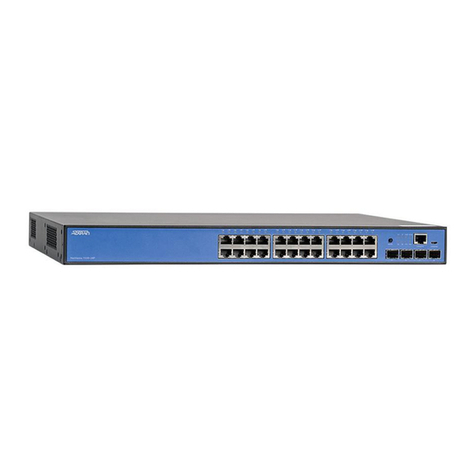
ADTRAN
ADTRAN NetVanta 1550 Series quick start
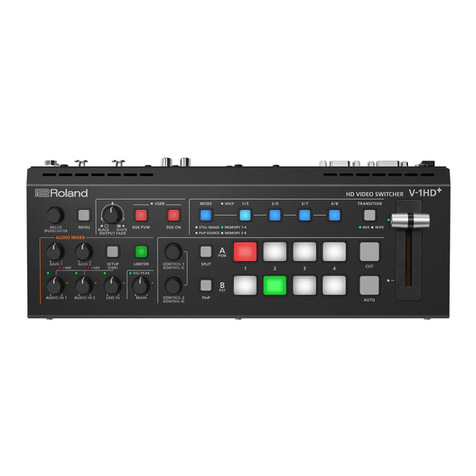
Roland
Roland V-1HD+ Reference manual

ICP DAS USA
ICP DAS USA ACS-20B-MRTU user manual
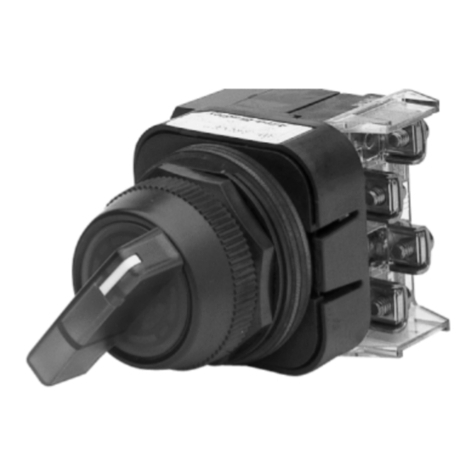
Rockwell Automation
Rockwell Automation Allen-Bradley 800F-ALR1 installation instructions