Ilco Orion Ecodrill 2000 Code User manual

®
Operating manual
D425374XA
vers.
2.0
ECODRILL 2000 CODE

(c) 2003 SILCA - Vittorio Veneto
This manual has been drawn up by ILCO ORION.
All rights reserved. No part of this publication may be reproduced or used in any form or by any means (photocopying, microfilm
or other) without the permission of ILCO ORION.
Published: June 2003
Printed in Vittorio Veneto
by ILCo ORION
via Podgora, 20 (Z.I.)
31029 VITTORIO VENETO (TV) - Italy

INDEX
REFERENCE GUIDE .............................................................................................................5
GENERAL ..............................................................................................................................6
1TRANSPORT ..............................................................................................................7
1.1 Packing ................................................................................................................... 7
1.2 Transport ................................................................................................................ 7
1.3 Opening the packing ............................................................................................... 7
1.4 Handling the machine ............................................................................................. 7
2MACHINE DESCRIPTION ..........................................................................................8
3WORKING PARTS ...................................................................................................10
3.1 Technical data ...................................................................................................... 11
3.2 Graphics ............................................................................................................... 11
3.3 Electrical circuit ..................................................................................................... 12
4ACCESSORIES PROVIDED ....................................................................................13
5MACHINE INSTALLATION AND PREPARATION ..................................................14
5.1 Checking for damage ........................................................................................... 14
5.2 Environmental conditions ..................................................................................... 14
5.3 Positioning ............................................................................................................ 14
5.4 Description of work station ................................................................................... 14
6KEYPAD FUNCTIONS .............................................................................................15
7MACHINE REGULATION AND REGISTRATION ....................................................17
7.1 Fitting and regulating the tools ............................................................................. 17
7.2 Adjustment ............................................................................................................ 17
7.3 Temporary adjustment .......................................................................................... 18
7.4 Tracer springing .................................................................................................... 18
7.5 Spring system for LASER (Sidewinder) keys ....................................................... 19
7.6 Clamps ................................................................................................................. 21
8CUTTING OPERATIONS ..........................................................................................22
8.1 Fitting the keys ..................................................................................................... 22
8.2 Cutting dimple keys .............................................................................................. 22
8.3 Cutting the back .................................................................................................... 22
8.4 Cutting by code ..................................................................................................... 23
8.5 Choose key ........................................................................................................... 23
8.6 PC key .................................................................................................................. 23
8.7 Code cutting new keys ......................................................................................... 24
8.8 Cutting Laser (sidewinder) type keys ................................................................... 24
8.9 Cutting narrow-stemmed Laser (sidewinder) type keys ....................................... 25
8.10 Cutting keys for FICHET ....................................................................................... 26
9MAINTENANCE ........................................................................................................27
9.1 Replacing the belt and adjusting tension .............................................................. 27
9.2 Replacing the light bulb ........................................................................................ 28
9.3 Checking and replacing the fuses ........................................................................ 28
9.4 Replacing the electronic board - the keypad ........................................................ 29
9.4.1 Replacing the circuit board ...............................................................................29
9.4.2 Replacing the keypad unit ................................................................................30
9.5 Replacing the microswitch .................................................................................... 31
9.6 Replacing the motor ............................................................................................. 32
9.7 Replacing the clamp jaws ..................................................................................... 33
9.7.1 Replacing the left-hand jaw ..............................................................................33

9.7.2 Replacing the right-hand jaw ............................................................................34
9.7.3 Replacing the left-hand mobile jaw ...................................................................35
9.7.4 Replacing the right-hand mobile jaw ................................................................36
9.7.5 Replacing the central jaw .................................................................................37
10 WASTE DISPOSAL ..................................................................................................38
11 AFTER-SALES SERVICE ........................................................................................39
11.1 How to request service ......................................................................................... 39

Operating manual - English ECODRILL 2000 CODE
5
REFERENCE GUIDE
This manual has been produced to serve as a guide for users of the ECODRILL 2000 CODE key-cutting
machine. Read it carefully; it is essential if you wish to operate your machine safely and efficiently.
Consultation
The contents of the manual are divided into sections relating to:
- Transport and handling
- Checking the safety of the machine
- Proper use of the machine
- Maintenance
Technical terms
Common technical terms are used in this manual.
To assist those with little experience of keys and key-cutting, below is an illustration of the terms most
frequently used (fig. 1).
Fig. 1
1) Head
2) Rim
3) Stop
4) Stem
5) Tip
6) Back
7) Cuts
2
1
5
7
3
4
6
1
5
7
3
DIMPLE KEY LASER (SIDEWINDER) TYPE KEY
keys with holes of different
dimensions, depths, positions and
shapes.
LASER is the name given to the
special sidewinder milled keys.

ECODRILL 2000 CODE Operating manual - English
6
GENERAL
ECODRILL 2000 CODE has been designed in compliance to the European Community normative (CE).
From the design stage, risks for the operator have been eliminated in all areas: transport, regulation,
cutting and maintenance.
Further risks have been eliminated by means of protective devices.
The protective devices used are designed not to provoke further risks and, above all, they cannot be
ignored unless deliberately cut out. They do not hinder visibility of the work area.
A special adhesive label is attached to the machine warning the operator to use goggles during the
cutting operations, and this is strongly recommended in this manual.
The materials used to manufacture this machine and all its components are not hazardous.
Use
The ECODRILL 2000 CODE must be installed and used in the way laid down by the manufacturer.
If the key-cutting machine is used differently or for purposes different from those described in this
manual, the customer will forego any rights he may have over Ilco Orion. Furthermore, unforeseen
danger to the operator or any third parties may arise from incorrect use of the machine.
Negligence in the use of the machine of failure on the part of the operator to observe the instructions
given in this manual are not covered by the guarantee and the manufacturer declines all responsibility in
such cases.
It is therefore indispensable to read the operating manual carefully in order to make the best use
of the ECODRILL 2000 CODE sand benefit from its potential.
Further risks
No further risks will arise when properly using the ECODRILL 2000 CODE.
Protection and safety precautions for the operator
The ECODRILL 2000 CODE key-cutting machine is entirely built in compliance to the Machine
Directives. The operations for which it has been designed are easily carried out with no risk to the
operator.
The adoption of general safety precautions (wearing protective goggles) and observation of the
instructions provided by the manufacturer in this manual eliminate all human error, unless deliberate.
ECODRILL 2000 CODE is designed with features which make it completely safe.
• Power supply
The machine is supplied with electricity by means of a grounded plug and differential switch.
•Electricpower
The machine is started up by means of the master switch.
• Start-up
The motor start switch activates the cutting tool.
• Illumination
The work area is illuminated by a lamp which operates when the machine is switched on with the master
switch.
• Maintenance
The operations to regulate, service, repair and clean the machine are structured in the simplest and
safest way possible. Parts that the operator can dismount cannot be incorrectly replaced therefore
avoiding any risks.
• Machine identification
The machine is provided with an identification label which includes the machine’s serial number (fig. 2).
Fig. 2
(*) see chap.10 WASTE DISPOSAL, page 38.

Operating manual - English ECODRILL 2000 CODE
7
1 TRANSPORT
The ECODRILL 2000 CODE key-cutting machine is easily transported and is not dangerous to handle.
The packed machine can be carried by one person.
1.1 Packing
The packing used for the ECODRILL 2000 CODE guarantees that the machine will travel safely without
danger of damage to it or its components.
The packing comprises four shells in expanded plastic in the machine is wrapped.
A strong outer cardboard box, the measurements of which can be seen in fig.3 and the plastic wrapping
protect the machine even over a long period of storage.
Fig. 3
1.2 Transport
The symbols on the outside of the packing box show the ideal conditions for transport.
Use of the packing box whenever the machine is transported will avoid knocks or bumps which could
cause damage.
1.3 Opening the packing
To remove the machine from the packing box:
1) cut the straps with scissors and remove.
2) open the box without damaging it as it may be used again (removals, despatch to the manufacturers
for repairs or servicing).
3) check the contents of the box, which should comprise:
- 1ECODRILL 2000 CODE key-cutting machine packed in protective shells.
- 1set of documents including: operating manual, spare parts list and guarantee.
- 1connecting wire.
- accessories provided
- CD WinTransfer Ecodrill 2000 Code
4)
remove the key-cutting machine from the protective shells
.
1.4 Handling the machine
When the ECODRILL 2000 CODE has been unpacked, place it directly on its workbench.
This operation can be carried out by one person,
firmly holding the base and no other part, to lift and
carry the machine
.
440 mm
555 mm
650 mm
Keep dry This side up
Handle with care

ECODRILL 2000 CODE Operating manual - English
8
2 MACHINE DESCRIPTION
The ECODRILL 2000 CODE is an excellent quality, high precision key-cutting machine. It features great
versatility in cutting keys of different types without the need to replace the clamp or apply fixed adapters.
ECODRILL 2000 CODE cuts the following types of keys:
• dimple keys
(with flat cuts)
• Laser (sidewinder) type keys
• keys for Fichet
dimple keys
keys for Fichet
(with adapter supplied)
Laser (sidewinder) type keys
Laser narrow-stemmed
(sidewinder) type keys

Operating manual - English ECODRILL 2000 CODE
9
High precision work is guarantee by the combination of the functional features on the ECODRILL 2000
CODE and all its components, such as:
• MOVEMENTS
The three axes move on ball guides which provide smooth running and easy sliding without play.
• SPRING SYSTEM FOR LASER (SIDERWIDER) KEYS
The machine is provided with a system which controls the run of the cross axis so that the operator can
easily trace the outline of the cuts along the key shaft.
• TRACER POINT SPRING SYSTEM
This system guides and facilitates self-centering of the cuts on dimple keys.
• ELECTROMECHANICAL SETTING
A precision electromechanical system ensures centesimal regulation of settings.
• PROTECTIVE SHIELD
A special transparent plastic shield prevents chippings from flying into the air.
•LAMP
Placed directly on the machine, it illuminates the work area.
• LEVERS AND KNOBS
Each lever and knob has been designed with dimensions, materials and positions which render grip and
movement extremely simple.
Materials and finish have been chosen according to the use of each part, especially:
- lever (I) for vertical carriage (Z axis)
ergonomic and provided with a locking mechanism which allows registration of the height of the cutter
assembly from the cutting surface, adapting this to the key (especially useful when cutting Laser
(sidewinder) keys) without a need for the operator.
- lever (C) X-Y axes
the lever which guides movement along the X-Y axes is ergonomic and makes precise, sensitive
movements due to a special joint with ball articulation and slide on ball guides.

ECODRILL 2000 CODE Operating manual - English
10
3 WORKING PARTS
Fig. 4
A - clamp carriage (X-Y axes)
B - left-hand jaw
B1- right-hand jaw
C - clamp carriage lever (X-Y axes)
E - left-hand jaw knob
E1- right-hand jaw knob
F - cutting tool
G - protective shield
H - clamp carriage locking knobs
I - vertical carriage lever (Z axis)
J-lamp
K - setting unit keypad
O - regulating knob for Laser (sidewinder) key spring system
P - master switch
Q - motor start switch
S - tool drawer
T - tracer point
U - tracer springing ring nut
I
K
G
E1
PB1
OS
H
B
E
C
J
T
F
Q
A
U

Operating manual - English ECODRILL 2000 CODE
11
3.1 Technical data
ELECTRICITY SUPPLY: 230V-50Hz (100V-50/60Hz)
MAXIMUM ABSORBED POWER: 230V: 1,1 Amp. 240 Watt - 100V: 1,3 Amp. 140 Watt
MOTOR: One-speed single phase
CUTTING TOOLS: Super rapid steel (HSS)
MOVEMENTS: on three axes
CLAMP: removable, with fixed and mobile interchangeable jaws
RUNS: X axis: 30 mm
Y axis: 50 mm
Z axis: 30 mm
DIMENSIONS: width: 350 mm depth: 420 mm height: 540 mm
MASS: Kg. 25
SOUND PRESSURE: Lp(A) = 78,2 dB(A)
3.2 Graphics
Fig. 5
THE USE OF PROTECTIVE GOGGLES
IS COMPULSORY

ECODRILL 2000 CODE Operating manual - English
12
3.3 Electrical circuit
The main parts of the electrical and electronic circuit on the ECODRILL 2000 CODE are listed below:
1) Plug with fuses
2) Main switch
3) Motor switch
4) Motor
5) Lamp
6) Electronic board
7) Transformer
8) Serial connection RS 232
9) Fuse 3,15A rapid
10)Step motor
11)Display
12)Keypad
13)Fan
14)Tracer contact
15)Cutter contact
16)Microswitch Z axis zeroing
Fig. 6
M
1
2
3
4
16
light blue
1
2
3
4
123
1
9
23
4
6
7
58
10
11
12
13
14
15
brown brown
light blue
light blue
brown
blue
brown
light blue
light blue
brown
white
white
black
black

Operating manual - English ECODRILL 2000 CODE
13
4 ACCESSORIES PROVIDED
A set of accessories is supplied for use with the machine or for servicing (tools, Allen keys and adapters).
The accessories include:
FUSE
code D312423ZZ
2 Amps delayed for 230V/100V
code D420785BA
ADAPTER for Opel keys
2 pcs.
code DMK260080
CUTTING TOOL
for dimple keys
code D300223ZZ
3 mm
ALLEN KEY
code DMS200080J
SETTING PLATES
2 pcs.
code DMK260340
TRACER POINT
for code cutting
FUSE
(2 pcs)
code D309226ZZ
3,15
Amps rapid for
230V/100V
code DMK260048
CUTTING TOOL
for Laser (sidewinder) keys
code DMK260047
TRACER POINT
for Laser (sidewinder) keys
1
2
3
4
5
9
10
11
code DMK260079
TRACER POINT
for dimple keys
12
614
715
13
code DMK260043
CUTTING TOOL
for dimple keys
code D300222ZZ
2,5 mm
ALLEN KEY
code DMK260044
TRACER POINT
for dimple keys
code D300225ZZ
5 mm
ALLEN KEY
8
code D426129RA
SETTING PINS
2 pcs.

ECODRILL 2000 CODE Operating manual - English
14
5 MACHINE INSTALLATION AND PREPARATION
The key-cutting machine can be installed by the purchaser and does not require any special skills.
The machine is supplied ready for use and does not need to be set up, except when changing to different
tools. However, some checks and preparation for use need to be carried out by the operator.
5.1 Checking for damage
The ECODRILL 2000 CODE key-cutting machine is solid and compact and will not normally damage if
transport, unpacking and installation have all been carried out according to instructions.
Notwithstanding, it is always advisable to check that the machine has not suffered any damage.
5.2 Environmental conditions
To ensure that the best use is made of the key-cutting machine, it is important to place it in a well-aired
area which is not too damp:
The ideal conditions for the machine are:
- temperature between 0 and 40°C
- relative humidity: approx 60%
5.3 Positioning
Place the machine on a horizontal surface, solid enough to support the weight of (30 Kg). The workbench
should be approx. 100-120 cm high to give easy access to the working parts of the machine.
Leave enough space around the machine (20-30 cm) to ensure good ventilation and room for
manoeuvre.
WARNING: ensure that the key-cutting machine voltage is suitable for the mains supply available, which
must be earthed and provided with a differential switch.
Fig. 7
5.4 Description of work station
The machine needs only one operator, who has the following controls at his/her disposal:
• master switch (P) placed on the back of the machine (fig.4, page 10).
• motor start switch (Q) (on the left-hand side of the machine).
• tool setting keypad (K).
• levers:
- lever (C) (fig.4, page 10) to move the clamp carriage.
- lever (I) to move the vertical carriage.
200mm
200mm
200mm

Operating manual - English ECODRILL 2000 CODE
15
6 KEYPAD FUNCTIONS
Fig. 8
The cutter-tracer button adjusts the cutting machine
.
The DEL button deletes (e.g. when you insert a code
)
The ESC button exits the operation and returns to the initial menu
.
The ENTER button confirms (in connection with the cursor position
)
The Arrow keys are used to move the cursor in the various menus: from r/h to l/h
(or vice versa), up and down (or vice versa).
The number keys insert codes or confirm a choice without pressing Enter.
Once you have connected the cutting machine to the line, press the main switch (P) (fig.4, page 10).
The display will show: Press a key will. Press any key to enter the main menu:
- Choose key
- Definit. key
- Key from PC
- Adjustment
- Relative setting
- Language
- Test
ABC
GHI JKL MNO
PQRS
TUV
WXYZ
DEF
123
456
789
DEL
ESC
0

ECODRILL 2000 CODE Operating manual - English
16
1 – Choose key
When the machine is new the “choose a key” menu contains a single system denominated Test, included
for machine testing during production. This menu is used to view the key system loaded with the PC
program Ecodrill Software (see instructions for Ecodrill Software in the chapter “Personalizing Ecodrill”).
2 – Definition key
Function for the creation of a new data card or code-cutting system.
3 – PC key
Cutting data can be received from the personal computer through a serial connection (ch. 8.4.2, page
23).
4 – Adjustment
Basic function for gauging (tool alignment) (see ch. 7.2, page 17).
5 – Temporary adjustment
Function used to edit the parameters of standard gauging (ch. 7.3, page 18).
6 – Language
Select the language required and press Enter.
7 – Test
There is an on board TEST menu that should be used to verify the cause of any breakdown that may
occur to the machine.
- State of microswitch
- Step motor
- Keypad
- Display
- Tracer point
-Cutter
-Serial
State of microswitch
Turn the ring nut (U) (fig.4, page 10) and check the passage from ON to OFF on the display.
Note: if the OFF/ON transition is not made, contact Technical Assistance Dept.
Step motor
Use the Arrow keys to check that the tracer point unit turns in both directions.
Note: if this is not so, contact Technical Assistance Dept.
Keypad
Press the various keys on the keypad to check that the display shows the corresponding numbers.
Note: if this is not so, contact Technical Assistance Dept.
Display
Check on the display that the cursor moves in all the writing spaces.
Note: if this is not so, contact Technical Assistance Dept.
Tracer point
Remove the cutter. Lower the lever (I) to take the tracer point into contact with the clamp and check the
passage from OFF to ON.
Note: if this is not so, contact Technical Assistance Dept.
Cutter
Remove the tracer point. Lower the lever (I) to take the cutter into contact with the clamp and check the
passage from OFF to ON.
Note: if this is not so, contact Technical Assistance Dept.
Serial
The display shows <Serial OK>.
Note: if this is not so, contact Technical Assistance Dept.

Operating manual - English ECODRILL 2000 CODE
17
7 MACHINE REGULATION AND REGISTRATION
Before carrying out cutting operations is necessary proceed with regulation about:
• fitting the tools and setting
• the cross spring for Laser (sidewinder) keys.
7.1 Fitting and regulating the tools
WARNING: make sure that the motor start switch
(Q)
(fig.4, page 10) is turned off.
Switch on the machine with the master switch.
Select the tools for the key to be cut and proceed as follows:
1) place the tracer point all the way into the left-hand sleeve and secure by tightening the grub screw (M)
(fig.9).
2) place the cutting tool all the way into the right-hand sleeve and secure by tightening the grub screw
(M1).
Releasing the tools
Unscrew the grub screw (M) and (M1) (fig.9) to remove the tracer point and cutting tool from the sleeves.
Fig. 9
7.2 Adjustment
Note: please note that before adjusting the machine you need to eliminate the tracer springing
(chap.7.4, page 18).
For carrying out adjustment, insert the cutter and tracer into their relative mandrils, block the bars (or 2
identical keyblanks) in the clamps and proceed as follows:
1) turn the machine on using the (P) main switch (fig.4, page 10).
2) press any key; then the top right-hand key (or choose “Adjustment” and press Enter). The message
appears <spring loaded tracer point>. Eliminate the spring and press Enter. The message appears
<put the cutter on the jaw>.
3) using the lever (I) (fig.4, page 10) lower the cutter against the bars (or keyblanks), correspondently the
two green leds will turn on and the message “Adjustment OK” will displayed.
4) the machine is ready to duplicate.
Fig. 10
MM1
ABC
GHI JKL MNO
PQRS
TUV
WXYZ
DEF
123
456
789
DEL
ESC
0

ECODRILL 2000 CODE Operating manual - English
18
7.3 Temporary adjustment
In order to cut a new key with a different depth from the original, it is necessary to act as follows:
1) after having carried outsetting (as inch. 7.2, page17) select option “Temp.adjustment” fromthe menu
and press Enter; the number zero will be appear.
2) when pressing the arrow keys next to the zero (on the control panel) some number values will be
displayed, in cents of millimetres, which express the depth difference, either positive or negative. By
pressing the left arrow key you willobtain a shallower cut. Confirm the desired valueby pressing Enter.
The setting you have thus obtained will remain until you perform a new one.
The setting you have thus obtained will remain until you perform a new one.
7.4 Tracer springing
You can obtain the tracer springing simply by turning the inferior ring nut (U) (fig.11) of the
holder tracer spindle, while doing so, keep the superior ring nut (N) fixed. So, you have:
- to turn left to obtain the springing
- to turn right to eliminate it
Fig. 11
N
U
without springing springing

Operating manual - English ECODRILL 2000 CODE
19
7.5 Spring system for LASER (Sidewinder) keys
The machine ECODRILL 2000 CODE is provided with a system which controls the run of the cross axis
so that the operator can easily trace the outline of the cuts along the key shaft.
The spring system for Laser (sidewinder) keys is activated by means of the knob (O) (fig.12). It
determines lateral pressure on the part of the tools throughout the cutting operation; this makes it
possible for the operator to follow the outline of the cuts manually without having to exert cross pressure
on lever (C).
Fig. 12, fig.13, fig.14 and fig.15 show three examples of the use of the spring system:
central cutting
right-hand cutting
left-hand cutting
Fig. 12
Fig. 13
central cutting
O
®
®
®
®
®
®
®
®

ECODRILL 2000 CODE Operating manual - English
20
REGULATING THE SPRING
Loosen knob (O) (fig.12, page 19).
Central cutting
:
take the cutter and tracer over the centre of the stems of the two keys (fig.12, page 19).
Right-hand cutting
:
take the cutter and tracer over the keys, positioning them to the left of the stems (fig.14).
Left-hand cutting
:
take the cutter and tracer over the keys, positioning them to the right of the stems (fig.15).
- Tighten knob (O) and carry out cutting operations.
Fig. 14
Fig. 15
right-hand cutting
adapter adapter
®
®®
®
left-hand cutting
®®
®®
Table of contents
Popular Drill manuals by other brands

Parkside
Parkside PEBH 780 ROTARY PERCUSSION DRILL Operating and safety instructions
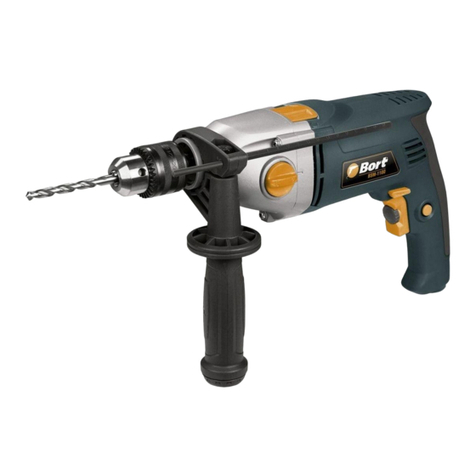
Bort
Bort 93726959 user manual
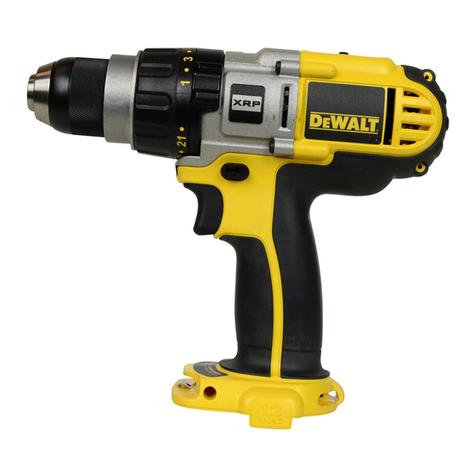
DeWalt
DeWalt DCD910 instruction manual

Narex
Narex EKK 26 E Original operating manual
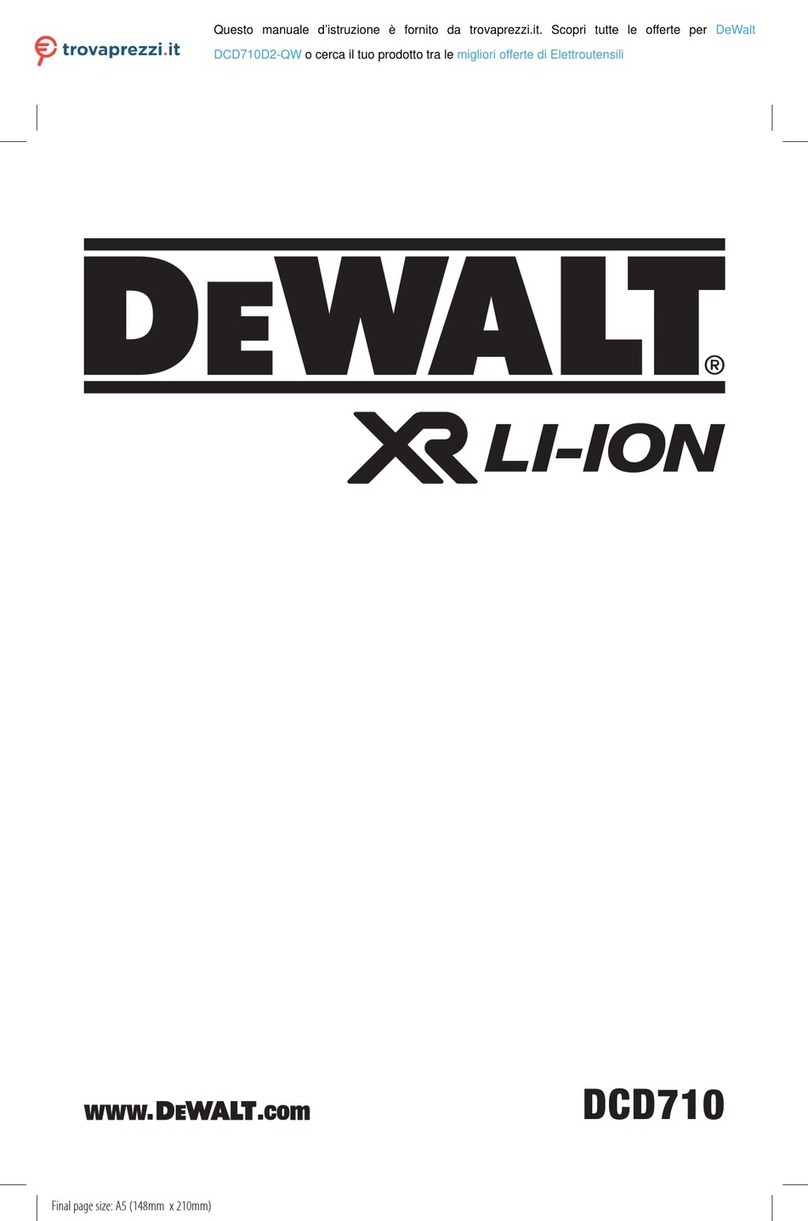
DeWalt
DeWalt XR LI-ION DCD710D2-QW user manual

Clarke
Clarke Contactor CON1200 Operating & maintenance instructions