Johnson Controls R81EAA User manual

Installation Sheets Manual 121
Relays and Contactors Section R
Technical Bulletin R81EAA
© Johnson Controls, Inc. 1
Code No. LIT-121579
Part No. 34-492-0, Rev. --
R81EAA Type
Plug-In Electronic Circuit Board Kit
For Series M100 Motor Actuators
Application
R81 plug-in electronic board kits
are used in Series M100X base
motor actuators and as a
replacement or conversion board
kit in an existing Series M100
motor actuator. The R81EAA kit
consists of a vertical plug-in
board, a terminal board with
travel and set point adjustment,
top cover with a circuit board and
ribbon attachment, mounting
screws, and an identification
label.
The R81EAA economizer board
kit has a changeover relay,
refrigeration programming relay,
adjustable minimum position
potentiometer, mixed air set point
adjustment, proportional band
adjustment, and an actuator
travel adjustment.
When the R81EAA is installed in
the M100 Series, the motor
actuator controls outdoor air
dampers (O.A.), return air
dampers (R.A.), and exhaust air
(E.A.) dampers to maintain proper
mixed air. The motor actuator with
the R81EAA installed allows
economical use of outdoor air for
natural cooling and reduces
energy consumption by minimizing
the compressor run-time. The
internal changeover relay and
refrigeration programming relay
can be wired in various ways to
provide control sequences that
use available natural cooling.
These cooling options must be
wired with A19 temperature
controls (sensible changeover) or
W84 total heat controls (enthalpy
changeover). A91 thermistor
sensors are used for direct mixed
air control or T91 thermistor room
thermostats are used for
ventilation only systems.
All Series R81 electronic board
kits are designed for use only as
operating controls. An operating
control is not authorized for use
where its failure in any mode can
result in personal injury and/or
loss of property. It is the
responsibility of the user to add
those necessary devices that
protect against undesirable
system failure modes.
Operation
To accomplish greater energy
savings, the motor actuator will
be cycled by the room thermostat
on a call for cooling.
Fig. 1 -Drawing showing how to remove and/or
install the R81 Plug-In Electronic Board Kit

2 R81EAA Technical Bulletin
Relay “A” is energized by the
contacts of the changeover
control. (See Fig. 4.)
When relay “A” is energized, the
motor actuator will use outside air
for cooling. Should the O.A.
parameters rise too high for
natural cooling, the contacts of the
changeover control will open,
changeover relay “A” will de-
energize, and the motor actuator
will return to its minimum position.
Relay “B” is used as a refrigeration
programmer when two stages of
cooling are needed. The outside
air changeover control energizes
relay “B,” which switches the first
stage of cooling to outside air, and
the second stage of cooling
becomes the first stage
refrigeration when the outside
conditions are low enough for
natural cooling. See Fig. 5 for
wiring diagram.
Installation
To install the R81 board kit in a
Series M100X base motor
actuator, proceed as follows:
1. Remove the motor actuator’s
top cover by loosening the
two cover screws. (The old
cover will be replaced with the
new cover supplied in the R81
kit.)
2. Install terminal board “E” by
carefully placing the terminal
receptacles onto the pin
terminals. (See Fig. 1, 1-A.)
3. Fasten the board in place
using the screws “D” that are
supplied with the R81 kit.
4. Install vertical board “C” with
ribbon attached cover mounted
board by carefully placing the
terminal receptacles onto the
pin terminals. (See Fig. 1, 1-B.)
5. Place bracket “B”, supplied with
the motor actuator, over vertical
board “C” and fasten the bracket
in place with captive screw “A.”
(See Fig. 1, 1-C.)
6. Important: The adhesive
backed label supplied in the
R81 kit must be placed on the
label located on the insulation
barrier as shown in Figure 2.
The letter on the R81 label will
complete the number that
identifies the Series M100 with
the R81 installed.
7. Install the motor actuator.
8. Make wiring connections. Turn
on power supply. Adjust, and
check operation.
9. Fasten the motor actuator’s
cover that contains the
adjustment potentiometers to
the motor actuator. Make sure
the ribbon connector is
completely inside the cover.
To remove and replace the
electronic circuit boards in an
existing Series M100E motor
actuator, proceed as follows:
!
CAUTION: Disconnect the
electrical power supply before
attempting to remove the
wiring connections and the
boards to prevent possible
electrical shock or damage to
the equipment.
1. Remove the motor actuator’s
top cover by loosening the
two cover screws.
2. If the existing motor actuator
is installed and wired, be sure
the power supply is turned off
and then disconnect all wiring
connections to the terminal
board.
3. Loosen screw “A” and remove
board bracket “B.” (See Fig. 1.)
4. Pull vertical board “C” straight
up. Be careful not to bend or
damage the pin terminals.
5. Remove the two screws “D”
from terminal board “E.”
Remove the terminal board by
lifting straight up. Be careful
not to bend or damage the pin
terminals.
6. Install the replacement
terminal board “E” by carefully
placing the terminal
receptacles onto the pin
terminals. (See Fig. 1, 1-A.)
7. Fasten the board in place
using the screws “D.”
8. Install vertical board “C” by
carefully placing the terminal
receptacles onto the pin
terminals. (See Fig. 1, 1-B.)
9. Place bracket “B”, supplied
with the motor actuator, over
vertical board “C” and fasten
the bracket in place with
captive screw “A.” (See
Fig. 1, 1-C.)
10. Important: The adhesive
backed label supplied in the
R81 kit must be placed on
the label located on the
insulation barrier as shown
in Figure 2. The letter on
the R81 label will complete
the number that identifies
the Series M100 with the
R81 installed.
11. Make wiring connections.
Turn on power supply.
Adjust, and check operation.
12. Replace the motor
actuator’s cover. Be sure
the ribbon connector is
completely inside the wiring
compartment.
Wiring

R81EAA Technical Bulletin 3
Make wiring connections using
copper conductors only and in
accordance with the National
Electrical Code and local
regulations. Refer to the typical
wiring diagram for selected hookup.
All splices are to be made in
junction boxes using approved
solderless connectors, or by
soldering and then taping the
connections. All splicing and
excess wiring must be located
outside of the motor actuator wiring
compartment. If desired, a
standard electrical box can be
added to the wiring compartment of
the motor actuator. (See Fig. 3.)
When more than one Series M100
motor actuator, with the R81EAA
installed, is powered from the same
24 VAC power source, polarity
must be maintained; connect all T2
terminals to the same side of the 24
VAC supply.
To avoid potential miswiring,
separate transformers are
recommended. When slaving
motor actuators with the number
10 terminals connected together,
separate transformers must be
used. Never simultaneously
parallel terminals 10 and T1. If an
existing 24 VAC power supply is
available, Johnson Controls Y69
isolation transformer is
recommended. M100J motor
actuators may be slaved from the
R81EAA/M100 using the “X”
terminal and a common power
supply. (See Fig. 8.)
Adjustment
Set Point
The set point for the remote
sensor is located on the R81’s
terminal board and has a
calibrated dial that is adjustable
between 40 and 90°F (5 and
30°C). Should a remote set point
be desired, such as a room
ventilation control, turn the set
point knob counterclockwise to
its limit at the low temperature
end of the dial and set the
temperature at the T91BCA
thermostat or remote Y45BA-1
set point adjuster.
Proportional Band
The proportional band adjustment
is located on the cover mounted
circuit board. The proportional
band is adjustable between 2 and
20°F (1.1 and 11°C).
!
CAUTION: While narrowing
the proportional band is
usually desirable, too narrow
a proportional band may
result in poor control. The
proportional band must be
increased if the motor
actuator cannot maintain a
stable position when the
system is operating.
Instability causes the motor
actuator to oscillate (hunt).
Remote Minimum Position
Remote control of the outdoor
air dampers is desirable where
temporary additional ventilation
is required. For example, a
restaurant, conference room,
factory, or store may need to
have the air purged temporarily.
The “O.A. Minimum”
potentiometer is integral on the
cover mounted circuit board for
minimum position control. The
addition of a Y45AA-9 will allow
the building occupant to control
the minimum position from a
remote location. (See Fig. 6.)
Night Setback
During the “day” mode, the T26
night setback thermostat is locked
out of the heating circuit.
However, in the “night” position,
the T26 thermostat, with its lower
set point, will operate the heating.
Also, in the night position, cooling
will be entirely locked out and the
O.A. damper will be closed.
(Dampers close only with spring
return motor actuators.) When
supply power is cut to the
transformer, the spring return
motor actuator closes the damper.
(See Fig. 7.)

4 R81EAA Technical Bulletin
Parallel Damper Actuators
In certain applications, It may be
possible that outside air, return
air, and exhaust air dampers
cannot be modulated by a single
motor actuator. In this event, up
to two additional M100J motor
actuators can be slaved from the
first Series M100 motor actuator
with the R81EAA installed. This
is illustrated in Fig. 8.
Checkout Procedure
Relay “A”
Turn the O.A. minimum position
potentiometer full
counterclockwise (CCW), and
energize the changeover relay.
This simulates the availability of
outside air for natural cooling.
Adjust the set point to
approximately midrange, 65°F
(18°C). Next jumper sensor
terminals S1 and S2. Since a
negative temperature coefficient
sensor is used, this will simulate
a rise in mixed air temperature
and the O.A. dampers will
modulate open. Remove the
jumper and disconnect terminal
S2. This will now simulate a
drop in mixed air temperature
and the O.A. dampers should
modulate closed.
Minimum Position
De-energize the changeover
relay to simulate that outside air
is no longer available for natural
cooling. The motor actuator will
rotate to the minimum position.
By turning the minimum position
potentiometer clockwise (CW),
the minimum position should
increase. The motor actuator
will rotate CW.
Checkout Procedure
After the linkage and motor
actuator have been assembled
to the valve or damper, cycle the
motor actuator using the
controller. Observe at least
three complete operating cycles
to see that all components are
functioning correctly.
Repairs and Replacement
Field repairs must not be made.
For a replacement electronic
board kit, contact the nearest
Johnson Controls Commercial
Systems wholesaler.

R81EAA Technical Bulletin 5

6 R81EAA Technical Bulletin
Notes

R81EAA Technical Bulletin 7
Notes

8 R81EAA Technical Bulletin
Notes
Controls Group
507 E. Michigan Street
P.O. Box 423
Milwaukee, WI 53201 Printed in U.S.A.
Table of contents
Other Johnson Controls Industrial Electrical manuals
Popular Industrial Electrical manuals by other brands

Murata
Murata GRT188R60J225ME13 Series Reference sheet
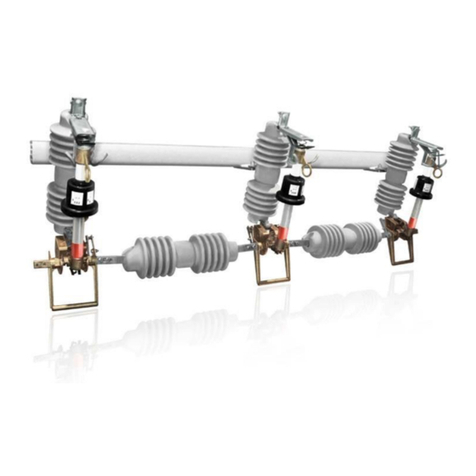
ABB
ABB Three Phase Mechanical AutoLink instruction manual
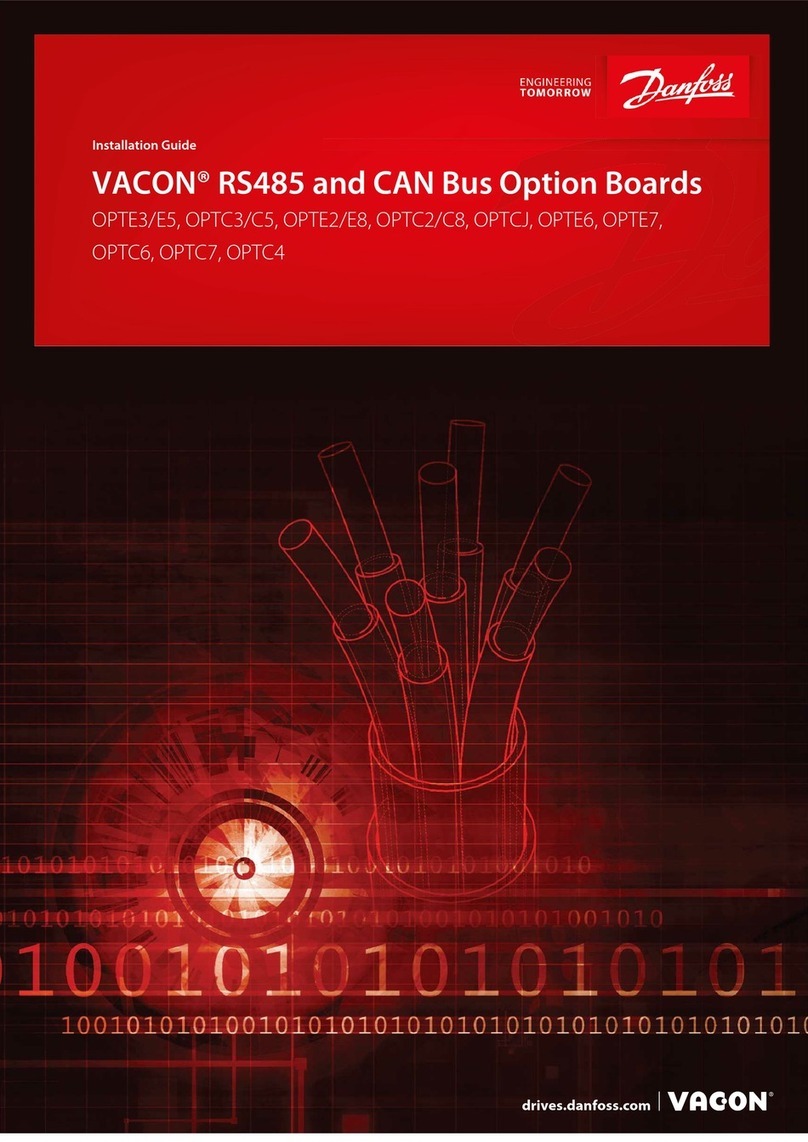
Danfoss
Danfoss VACON OPTE3 installation guide

Murata
Murata GRM1885C2A121GA01 Series Reference sheet
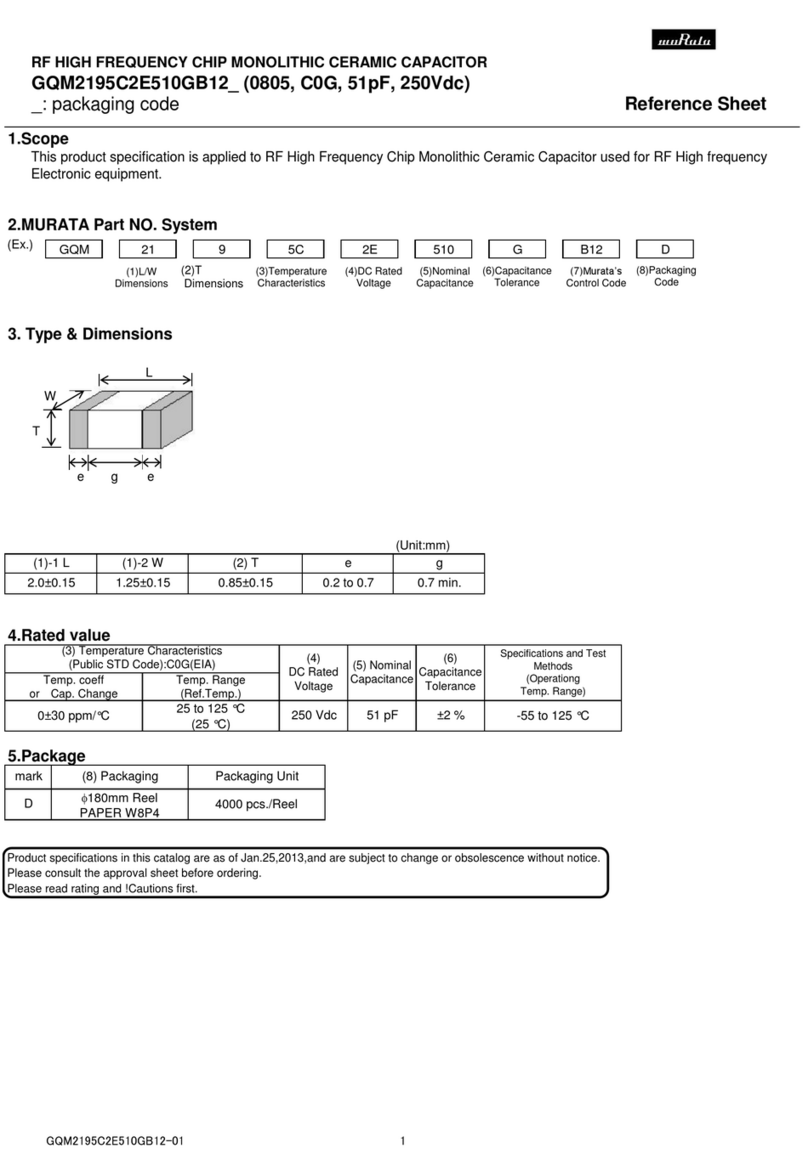
Murata
Murata GQM2195C2E510GB12 Series Reference sheet

Murata
Murata GRM0335C1E5R0CA01 Series Reference sheet
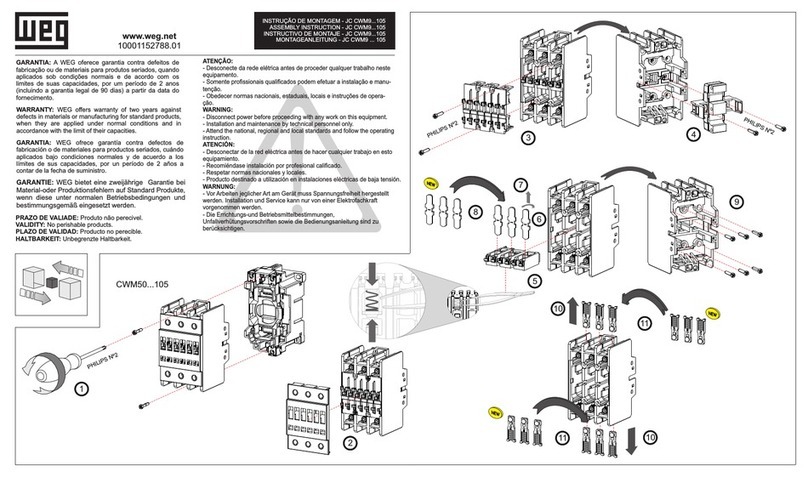
WEG
WEG JC CWM9 105 Series Assembly instruction
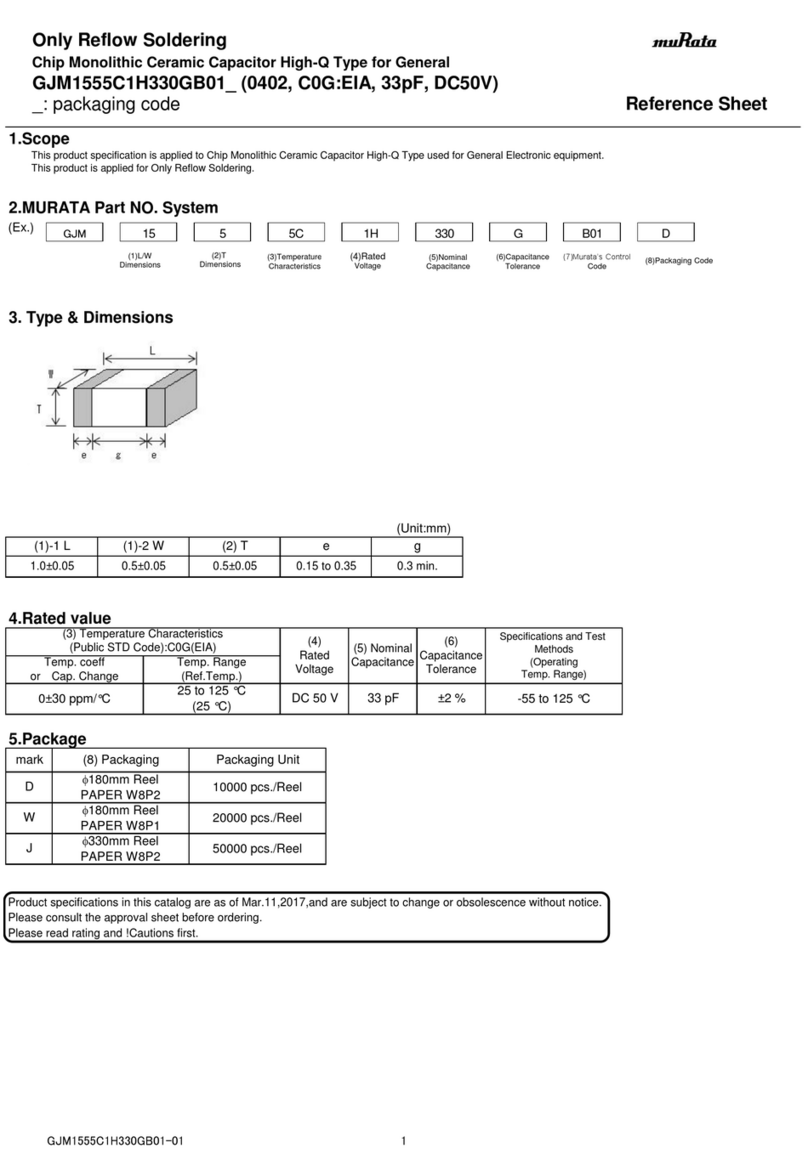
Murata
Murata GJM1555C1H330GB01 Series Reference sheet
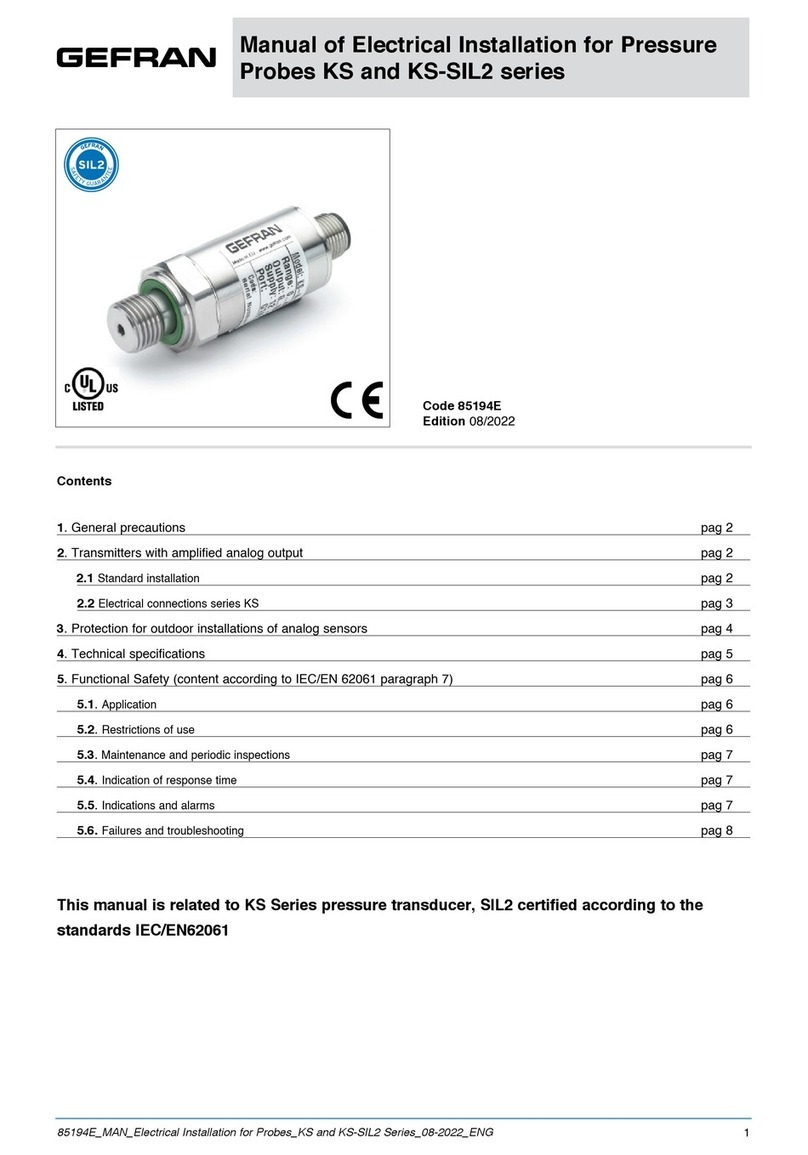
gefran
gefran KS Series Manual of Electrical Installation
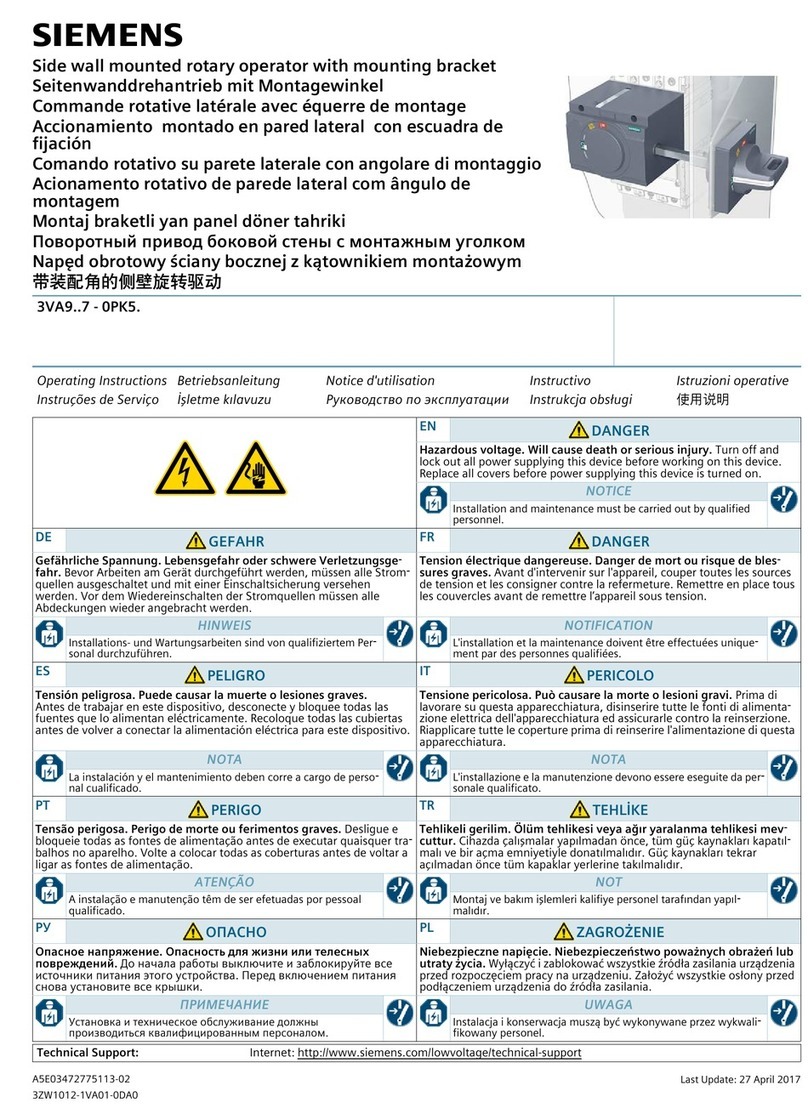
Siemens
Siemens 3VA9 7 0JA1 Series operating instructions
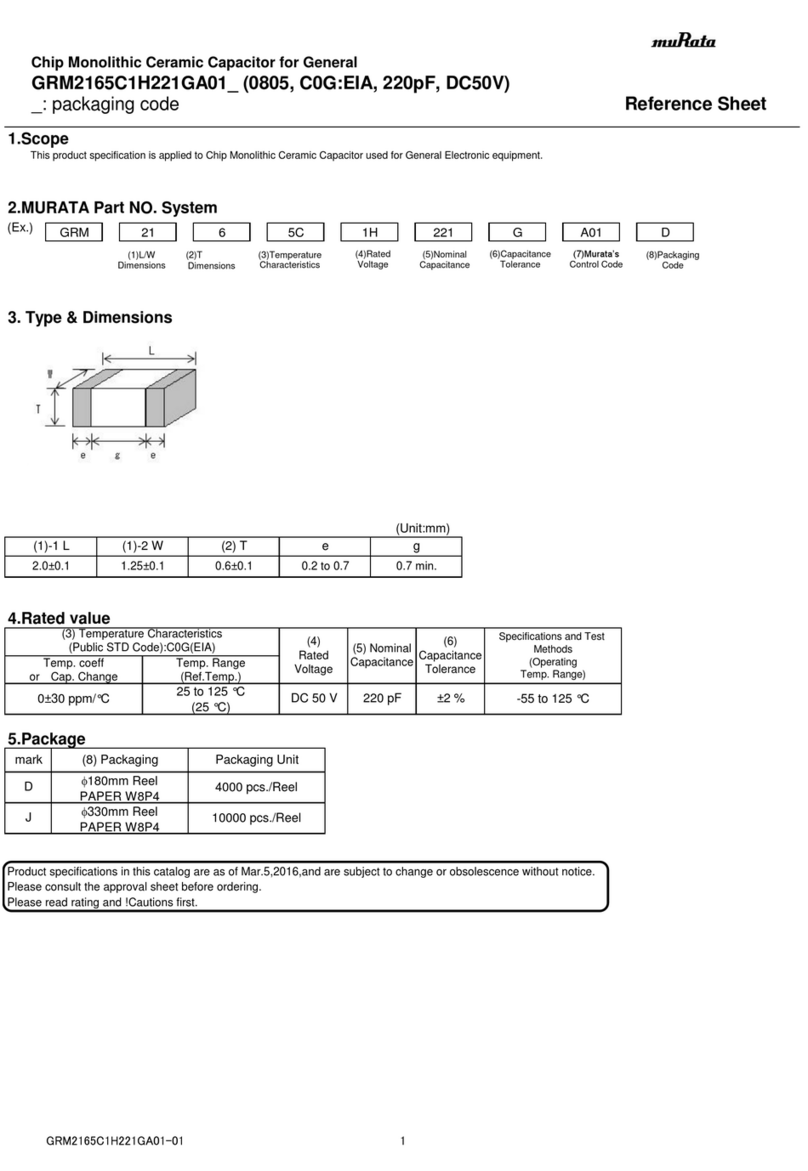
Murata
Murata GRM2165C1H221GA01D Reference sheet
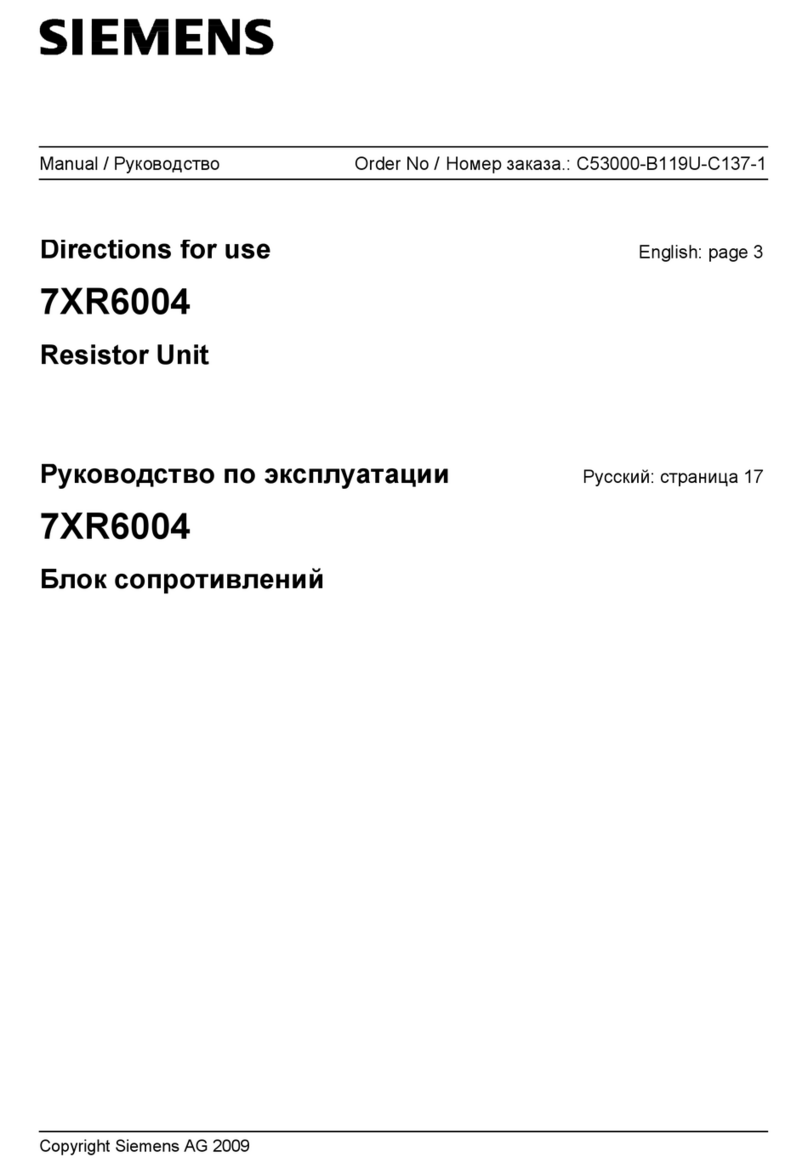
Siemens
Siemens 7XR6004 Series Directions for use