KEBCO COMBIVERT G6 User manual

COMBIVERT
Original Manual
Mat.No. Rev.
00G6NEL-0C00 1E
GB Installation Manual Housing C
Power Unit Power 5.5…11 kW


GB - 3
Table of Contents
1. Preface..............................................................................................................5
1.1 General ................................................................................................................................. 5
1.2 Validity and liability ............................................................................................................. 5
1.3 Copyright.............................................................................................................................. 6
1.4 Speciedapplication........................................................................................................... 6
1.5 Product description............................................................................................................. 6
1.6 Part Code.............................................................................................................................. 7
1.7 Safety and operating instructions...................................................................................... 8
2. Technical Data .................................................................................................9
2.1 Operating conditions........................................................................................................... 9
2.2 Technical data G6 400V class........................................................................................... 10
2.3 Mechanical installation ..................................................................................................... 12
2.3.2 Dimensions and weights...................................................................................................... 12
2.3.3 Control cabinet installation................................................................................................... 13
3. Installation and Connection .........................................................................14
3.1 Overview of the COMBIVERT G6...................................................................................... 14
3.2 Connection of the power unit ........................................................................................... 15
3.2.1 Connection of the voltage supply......................................................................................... 15
3.2.1.1 Wiring instructions ............................................................................................................... 15
3.2.1.2 AC supply 400V / 3-phase ................................................................................................... 16
3.2.1.3 Line terminal strip X1A......................................................................................................... 16
3.2.1.4 Supply cable ........................................................................................................................ 16
3.2.1.5 Connection at DC voltage supply ........................................................................................ 17
3.2.1.6 Terminal strip X1B DC connection ....................................................................................... 17
3.2.2 Connection of the motor ...................................................................................................... 17
3.2.2.1 Selection of the motor cable ................................................................................................ 17
3.2.2.2 Motor line length at operation with DC voltage .................................................................... 17
3.2.2.3 Cable-fed disturbances depending on the motor line length at AC supply .......................... 18
3.2.2.4 Motor cable cross-section.................................................................................................... 18
3.2.2.5 Interconnection of the motor ................................................................................................ 18
3.2.2.6 Terminal strip X1B motor connection ................................................................................... 18
3.2.2.7 Wiring of the motor .............................................................................................................. 19
3.2.3 Connection of a braking resistor .......................................................................................... 19
3.2.3.1 Terminal strip X1B connection braking resistor.................................................................... 19
3.2.3.2 Wiring of an intrinsically safe braking resistor...................................................................... 19
3.2.3.3 Using a non-intrinsically safe braking resistor ..................................................................... 19
3.2.4 Connection of a Temperature Detection .............................................................................. 20
3.2.4.1 Temperature detection terminals T1, T2 .............................................................................. 20
3.2.4.2 Terminal strip X1C temperature detection ........................................................................... 20
3.2.4.3 Use of the temperature input in PTC mode ......................................................................... 21
3.2.5 Final test informations of the machines/systems which are provided with frequency
inverters according to EN 60204 Part 1 of 2007 .................................................................. 21
3.2.5.1 Voltage test (in accordance with EN60204-1 chapter 18.4)................................................. 21
3.2.5.2 Isolation resistance measurement (in accordance with EN60204-1 chapter 18.3).............. 21

GB - 4
Table of Contents
Annex A .....................................................................................................................22
A.1 Calculation of the motor voltage...................................................................................... 22
A.2 Maintenance ....................................................................................................................... 22
A.3 Shut down .......................................................................................................................... 23
A.3.1 Storage ................................................................................................................................ 23
Annex B.....................................................................................................................24
B.1 Certication........................................................................................................................ 24
B.1.1 CE-Marking.......................................................................................................................... 24
B.1.2 UL Marking........................................................................................................................... 24
B.2 Further informations and documentation ....................................................................... 26

GB - 5
Preface
1. Preface
1.1 General
First we would like to welcome you as a customer of KEB and congratulation to the purchase
of this product. You have decided for a product on highest technical niveau.
The described hard- and software are developments of the Karl E. Brinkmann GmbH. The
enclosed documents correspond to conditions valid at printing. Misprint, mistakes and tech-
nical changes reserved.
The instruction manual must be made available to the user. Prior to performing any work on
the unit the user must familiarize himself with the unit. This especially applies to the know-
ledge and observance of the following safety and warning indications. The used pictograms
have following signicance:
Danger Is used when the life or health of the user is in danger or con-
siderable damage to property can occur.
Warning
Caution
Attention Is used when a measure is necesary for safe and disturbance
free operation.
observe at
all costs
Information Is used, if a measure simplies the handling or operation of
the unit.
Aide
Tip
Non-observance of the safety instructions leads to the loss of any liability claims. This list is
not exhaustive.
1.2 Validity and liability
The use of our units in the target products is outside of our control and therefore lies
exclusively in the area of responsibility of the machine manufacturer.
The information contained in the technical documentation, as well as any user-specic advice
in spoken and written and through tests, are made to best of our knowledge and information
about the application. However, they are considered for information only without responsibili-
ty. This also applies to any violation of industrial property rights of a third-party.
Selection of our units in view of their suitability for the intended use must be done generally
by the user.
Tests can only be done within the application by the machine manufacturer. They must be
repeated, even if only parts of hardware, software or the unit adjustment are modied.
Unauthorised opening and tampering may lead to bodily injury and property damage and
may entail the loss of warranty rights. Original spare parts and authorized accessories by the
manufacturer serve as security. The use of other parts excludes liability for the consequences
arising out of.
The suspension of liability is especially valid also for operation interruption loss, loss of prot,
data loss or other damages. This is also valid, if we referred rst to the possibility of such
damages.

GB - 6
Preface
If single regulations should be or become void, invalid or impracticable, the effectivity of all
other regulations or agreements is not affected.
1.3 Copyright
The customer may use the instruction manual as well as further documents or parts from it for
internal purposes. Copyrights are with KEB and remain valid in its entirety.
1.4 Speciedapplication
The COMBIVERT G6 serves exclusively for the control and regulation of three-phase motors.
The operation of other electric consumers is prohibited and can lead to the destruction of the
unit. Frequency inverter are components which are intended for the installation in electric
systems or machines.
The used semiconductors and components of KEB are developed and dimensioned for the
use in industrial products. If the KEB COMBIVERT F5 is used in machines, which work under
exceptional conditions or if essential functions, life-supporting measures or an extraordinary
safety step must be fullled, the necessary reliability and security must be ensured by the ma-
chine builder. The operation of our products outside the indicated limit values of the technical
data leads to the loss of any liability claims.
1.5 Product description
The product family COMBIVERT G6 has been developed for the universal use at open-loop
three-phase drives. The units are equipped with an integrated EMC lter. This manual descri-
bes only the power circuits.
This accompanying instruction manual contains only information for the installa-
tion and connection of the power circuit KEB COMBIVERT G6.
Further parts of the installation manual are required depending on the ordered
type:
• Connection and adjustments of the control
• Safety function STO
• Safe digital output for f=0Hz
A manual with general safety requirements and EMC conform installation is
available under www.keb.de.

GB - 7
Preface
1.6 Part Code
xx G6 x x x - x x x x
Cooling (not valid at customer/special version)
0Air-cooling (housing C, D, E); air-cooling/at rear (housing A, B)
1 Flat rear
Control/keyboard/display (not valid at customer/special version)
0Open-loop without keyboard/display A like 0 on ASCL hardware
1 Open-loop with keyboard/display B like 1 on ASCL hardware
2 SCL without keyboard/display
3 SCL with keyboard/display
4 ASCL without keyboard/display
5 ASCL with keyboard/display
Switching frequency; short time current limit; overcurrent cut-off
(not valid at customer/special version)
02 kHz 125 % 150 % 14 kHz 125 % 150 %
28 kHz 125 % 150 % 316 kHz 125 % 150 %
42 kHz 150 % 180 % 54 kHz 150 % 180 %
68 kHz 150 % 180 % 716 kHz 150 % 180 %
82 kHz 180 % 216 % 94 kHz 180 % 216 %
A8 kHz 180 % 216 % B2 kHz 180 % 216 %
Voltage, connection
0 1-phase 230 V AC/DC 3 3-phase 400 V AC/DC
1 3-phase 230 V AC/DC 5 400 V DC
2 1/3-phase 230 V AC/DC 6 1-phase 230 V AC
A-Z Customer-/special version (rmware and download)
Housing type A, B, C, D, E
Variants
0
without lter, without braking transis-
tor,
without safety function STO
Alike 0 with
STO Hlike A with
f=0Hz
1without lter, with braking transistor,
without safety function STO Blike 1 with
STO ilike B with
f=0Hz
2internal lter; without braking tran-
sistor, without safety function STO Clike 2 with
STO Klike C with
f=0Hz
3internal lter, with braking transistor,
without safety function STO Dlike 3 with
STO Llike D with
f=0Hz
Control type
C Analog/digital (standard)
D CAN
E IO-link
F EtherCAT
GPronet
G6 unit type
Inverter size

GB - 8
Safety Instructions
1. General
In operation, drive converters, depending on their degree
of protection, may have live, uninsulated, and possibly
also moving or rotating parts, as well as hot surfaces.
In case of inadmissible removal of the required covers,
of improper use, wrong installation or maloperation, there
is the danger of serious personal injury and damage to
property.
For further information, see documentation.
All operations serving transport, installation and commis-
sioning as well as maintenance are to be carried out by
skilled technical personnel (Observe IEC 364 or CENELEC
HD 384 or DIN VDE 0100 and IEC 664 or DIN/VDE 0110
and national accident prevention rules!).
For the purposes of these basic safety instructions, „skilled
technical personnel“ means persons who are familiar with
the installation, mounting, commissioning and operation
of the product and have the qualications needed for the
performance of their functions.
2. Intended use
Drive converters are components designed for inclusion in
electrical installations or machinery.
In case of installation in machinery, commissioning of the
drive converter (i.e. the starting of normal operation) is
prohibited until the machinery has been proved to conform
to the provisions of the directive 2006/42/EC (Machine-
ry Safety Directive - MSD). Account is to be taken of EN
60204.
The drive converters meet the requirements of the Low-
Voltage Directive 2006/95/EC. They are subject to the har-
monized standards of the series EN 61800-5-1.
The technical data as well as information concerning the
supply conditions shall be taken from the rating plate and
from the documentation and shall be strictly observed.
3. Transport, storage
The instructions for transport, storage and proper use shall
be complied with.
The climatic conditions shall be in conformity with EN
61800-5-1 .
4. Installation
The installation and cooling of the appliances shall be in
accordance with the specications in the pertinent docu-
mentation.
The drive converters shall be protected against excessive
strains. In particular, no components must be bent or iso-
lating distances altered in the course of transportation or
handling. No contact shall be made with electronic compo-
nents and contacts.
1.7 Safety and operating instructions
Safety and operating instructions for drive converters
(in conformity with the Low-Voltage Directive 2006/95/EC)
Drive converters contain electrostatic sensitive compo-
nents which are liable to damage through improper use.
Electric components must not be mechanically damaged
or destroyed (potential health risks).
5. Electrical connection
When working on live drive converters, the applicable nati-
onal accident prevention rules (e.g. VBG 4) must be com-
plied with.
The electrical installation shall be carried out in accordance
with the relevant requirements (e.g. cross-sectional areas
of conductors, fusing, PE connection). For further informa-
tion, see documentation.
Instructions for the installation in accordance with EMC
requirements, like screening, earthing, location of lters
and wiring, are contained in the drive converter documen-
tation. They must always be complied with, also for drive
converters bearing a CE marking. Observance of the limit
values required by EMC law is the responsibility of the ma-
nufacturer of the installation or machine.
6. Operation
Installations which include drive converters shall be equip-
ped with additional control and protective devices in ac-
cordance with the relevant applicable safety requirements,
e.g. act respecting technical equipment, accident preven-
tion rules etc.. Changes to the drive converters by means
of the operating software are admissible.
After disconnection of the drive converter from the voltage
supply, live appliance parts and power terminals must not
be touched immediately because of possibly energized
capacitors. In this respect, the corresponding signs and
markings on the drive converter must be respected.
During operation, all covers and doors shall be kept
closed.
7. Service and maintenance
The manufacturer’s documentation shall be followed.
KEEP SAFETY INSTRUCTIONS IN A SAFE PLACE!

GB - 9
Technical Data
2. Technical Data
2.1 Operating conditions
Standard Standard/
class
Instructions
Denition acc.
EN 61800-2 Inverter-product standard: Ratedspecications
EN 61800-5-1 Inverter-product standard: General safety
EN 61800-5-2 Inverter-product standard: Functional safety
Site altitude
max. 2000 m above sea level
With site altitudes over 1000 m a derating of 1% per
100 m must be taken into consideration.
Ambient conditions during operation
Climate Temperature EN 60721-3-3 3K3
extended to -10…45 °C
With temperature over 45°C to max. 55°C a derating of
5 % per 1 K must be taken into consideration.
Humidity 3K3 5…85 % (without condensation)
Mechanical Vibration
Track EN50155 max. amplitude of a vibration 1 mm (5…13Hz)
max. acceleration amplitude 7 m/s² (13…100Hz)
1 m/s² (100…200 Hz)
Germ. Lloyd Part 7-3
Contamination Gas EN 60721-3-3 3C2
Solids 3S2
Ambient conditions during transport
Climate Temperature
EN 60721-3-2
2K3
Humidity 2K3 (without condensation)
Mechanical Vibration 2M1 15 m/s² (200…500 Hz)
Surge 2M1 50 g/30 ms; drop from 0.25 m height
Contamination Gas 2C2
Solids 2S2
Ambient conditions for the storage
Climate Temperature
EN 60721-3-1
1K4
Humidity 1K3 (without condensation)
Contamination Gas 1C2
Solids 1S2
Type of protection EN 60529 IP20
Environment IEC 664-1 Pollution degree 2
Denition acc. EN 61800-3 Inverter-product standard: EMC
EMC emitted interference
Cable-based interferences – C1/C2 see chapter 3.2.2.3
Radiated interferences – C2
Interference immunity
Static discharges EN 61000-4-2 8 kV
4 kV
AD (air discharge)
CD (contact discharge)
Burst - Ports for process measu-
rement control lines and signal
interfaces
EN 61000-4-4 1 kV tested with 2 kV
Burst - Power ports EN 61000-4-4 2 kV tested with 4 kV
Surge - Power ports EN 61000-4-5 1 kV
2 kV
Phase-phase
Phase-ground
Immunity to conducted disturban-
ces, induced by radio-frequency
elds
EN 61000-4-6 10 V 0.15-80 MHz
Electromagnetic elds EN 61000-4-3 10 V/m
Voltage variation /
voltage drop EN 61000-2-1 +10 %, -15 %
90 %
Voltage unsymmetries /
Frequency changes EN 61000-2-4 3 %
2 %

GB - 10
Technical Data
2.2 Technical data G6 400V class
Inverter size 13 14 15
Housing size C
Phases 3
Output rated power SA[kVA] 8.3 11 17
Max. rated motor power Pmot [kW] 5.5 7.5 11
Output rated current IN[A] 12 16.5 24
Max. short time current IHSR 1) [%] 180 180 150
Over current IOC 1) [%] 216 216 180
Maximum current 0Hz/corner frequency fd at fS=4 kHz If0/Ifd 1) [%] 100/180 100/180 100/180
Maximum current 0Hz/corner frequency fd at fS=8 kHz If0/Ifd 1) [%] 100/180 70/160 70/150
Maximum current 0Hz/corner frequency fd at fS=16 kHz If0/Ifd 1) [%] 60/150 – –
rated frequency fd [Hz] 6
Input rated current Iin [A] 17 23 31
Max. permissible main fuse type gG [A] 25 25 35
Rated switching frequency fSN 2) [kHz] 8 4 4
Max. switching frequency fSmax 2) [kHz] 16 8 8
Power loss at nominal operating PD3) [W] 210 220 285
Power loss at DC supply PDdc [W] 180 180 230
Power loss standby (nOP) PDnop [W] 10 10 11
Power loss control (separated supply) PDsep [W] 2
Max. heat sink temperature THS [°C] 82
Temperature for derating the switching frequency Tdr 4) [°C] 75
temperature for uprating the switching frequency Tur 4) [°C] 70
Min. braking resistor RBmin [Ω] 39
Max. braking current IBmax [A] 21.5
Input rated voltage UN5) [V] 400 (UL: 480)
Input voltage range Uin [V] 305…528 ±0
Input voltage range at DC supply Uindc [V] 420…746 ±0
Mains frequency FN[Hz] 50 / 60 ±2
Output voltage UA6) [V] 3 x 0…Umains
Output frequency FA2) [Hz] 0…400 (fs=4 kHz)
0…800 (fs=8 kHz)
minimum waiting period between two switch-on procedures [min] 5
1) The values refer percentage to the output rated current IN
2) The output frequency is to be limited in such way that 1/10 of the switching frequency is not exceeded.
3) Rated operation corresponds to UN=400 V; fSN; fA=50 Hz (typically value)
4) On reaching the temperature Tdr the switching frequency is step down. The switching frequency is increased again on cooling down to temperature
Tur.
5) At rated voltages > 460 V multiply the rated current with factor 0.86
6) The voltage at the motor is dependent on the series-connected units and on the control method (example see chapter A.1 in the annex)
The technical data are for 2/4-pole standard motors. With other pole numbers the inverter must be
dimensioned onto the motor rated current. Contact KEB for special or medium frequency motors.
The service life of the frequency inverter with intermediate voltage circuit depends on the current load
of the electrolytic capacitors in the intermediate circuit. The use of mains chokes can increase the
service life of the condensators to a considerable extent, especially when connecting to „hard“ power
systems or when under permanent drive load (continuous duty). For continuous duty (S1) drives with
a medium duty of >60%, KEB provided the use of mains chokes with a terminal voltage (Uk) of 4%.
The term "hard" power system means that the nodal point power (SNet) of the mains is very high (>>
200) compared to the output rated power of the inverter (SA).
k = SNet 2 MVA (supply transformer)
–––– >> 200 e.g. k = ––––––––––––––––––––– = 303 ––> Choke required
SA6.6 kVA (12.F5)

GB - 11
Technical Data
Maximum load and derating depending on the switching frequency
80%
60%
100%
120%
140%
160%
180%
200%
220%
fd (6Hz)f0 (0Hz)
fA[Hz]
IN[%]
HSR (13/14.G6) OC (15.G6)
IN
OC (13/14.G6)
HSR (15.G6)
14.G6 (8 kHz)
15.G6 (8 kHz) 15.G6 (4 kHz)
13.G6 (16 kHz)
13.G6 (4/8kHz) & 14.G6 (4kHz)
Overload characteristic
30
60
90
120
150
180
210
240
270
300
0105 110 115 120 125 130 135 140 145 150 160 170 180 190 200 210 220
I
N
[%]
t [s]

GB - 12
Mechanical Installation
2.3 Mechanical installation
2.3.2 Dimensions and weights
242.5 ±2.5
100
117
260
für M5
230
8
230
Housing C Weight [kg]
4.6

GB - 13
Mechanical Installation
2.3.3 Control cabinet installation
The power loss for the control cabinet dimension is to be taken from the technical data.
Mounting distances Dimensi-
on
Distance in mm Distance in
inch
C
A
B
DD
A 150 6
B 100 4
C 30 1.2
D 0 0
X 1) 50 2
1) Distance to preceding elements in the cabinet door.
If construction-conditioned the control cabinet cannot be without indoor ventilation, appropri-
ate lters must avoid suction of foreign objects.
Direction of the
air ow
Front and side view of the coolant inlet
Coolant outlet
Coolant inlet

GB - 14
Unit Description
3. Installation and Connection
3.1 Overview of the COMBIVERT G6
Overview of the COMBIVERT G6
Size C No. Name Description
6
5
4
1
7
9
2
3
8
X4A X2B
X2A
1X1B
Terminal strip for three-phase
motor , braking resistor and DC
supply
2X4A
Diagnostic interface
RS232/485 interface with
DIN66019-II
3X2B Safety Function STO
(optional)
4X2A Control terminal strip 32-pole
5X1A Mains input 3-pole
6LED1 Inverter state (if without keyboard/
display)
7– Display/keyboard
8– Type plate
9X1C
Temperature monitoring;
Connection for external PTC or
temperature switch
10 PE,
Protective earth;
at connection to protective earth
each terminal may be assigned
only once.
The shielding e.g. from the motor
cable is laid on the mounting plate
in the control cabinet or on the
shield plate (optionally available
E0G6T88-0001).

GB - 15
Connection of the Power Unit
3.2 Connection of the power unit
Only Quali-
edElectro-
Personnel
All work from the transport, to installation and start-up as well as mainte-
nance may only be done by qualied personnel (IEC 364 and/or CENELEC
HD 384 and IEC-Report 664 and note national safety regulations). Accor-
ding to this manual qualied staff means those who are able to recognise
and judge the possible dangers based on their technical training and ex-
perience and those with knowledge of the relevant standards and who are
familiar with the eld of power transmission.
Electric
Shock
KEB COMBIVERT units contain dangerous voltages which can cause
death or serious injury.
The KEB COMBIVERT can be adjusted in such a way that energy regene-
ration into the supply net is possible at regenerative operation also during
mains power failure. Therefore a dangerous high tension can exist in the
unit after switching off the supply system.
Before working with the unit check the isolation from supply by mea-
surements in the unit. Motors are to be secured against automatic
starting.
Care should be taken to ensure correct and safe operation to minimise risk
to personnel and equipment.
The terminal strips meet the requirements on IEC 60947-7-1
3.2.1 Connection of the voltage supply
+
++
--
L1
L2
L3
The COMBIVERT G6-C corresponds to the inverter type
A1. This type can be supplied both by mains and via DC
terminals. The starting current limiting is arranged before
the DC link. When using as DC output parallel connected
frequency inverters must have their own starting current
limiting at the DC voltage input.
3.2.1.1 Wiring instructions
Never exchange the mains and motor cables.
Some countries demand that the PE-terminal is directly connected to the terminal box
(not over the mounting plate).

GB - 16
Connection of the Power Unit
3.2.1.2 AC supply 400V / 3-phase
Picture 3.2.1.3 Connection for power supply
L1
L2
L3
PE
L1
L2
L3
U
V
W
PE
PE
T1 T2
1 Mains voltage 3-phase 400 VAC
Mains form TN, TT IT
Personal protection RCMA with separator or
RCD type B
Earth leakage monitor
2 Main fuses Type gG or MCCB
3 Mains contactor
4 Mains choke (optional) 13, 14 or 15Z1B04-1000
5 KEB COMBIVERT G6-C
3.2.1.3 Line terminal strip X1A
X1A Name Function Cross-section Tightening
torque
L1, L2,
L3
Mains connection
3-phase
0.2-16 mm²
AWG 26-6
2.3 Nm
20.5 lb-inch
PE, Connection for pro-
tective earth
Screw M4 for
ring thimble
1.3 Nm
11 lb inch
3.2.1.4 Supply cable
The conductor cross-section of the supply cable is dependent on the input current, the cable
according to manufacturer's data, as well as the VDE regulations.

GB - 17
Connection of the Power Unit
3.2.1.5 Connection at DC voltage supply
Picture 3.2.1.5 Connection at DC voltage supply
- -
U
V
W
PEPEPE
T1 T2
++
+U
-U
1 Current DC - voltage 420…746 V DC
2 Fuses Type aR
Pay attention to the permissible voltage range !
3 KEB COMBIVERT G6-C
3.2.1.6 Terminal strip X1B DC connection
X1B Name Function Cross-section Tightening
torque
++, -- DC connection 0.2-16 mm²
AWG 26-6
2.3 Nm
20.5 lb-inch
PE, Connection for pro-
tective earth
Screw M4 for
ring thimble
1.3 Nm
11 lb inch
3.2.2 Connection of the motor
3.2.2.1 Selection of the motor cable
The correct cabling as well as the motor cable play an important part in case of low power
in connection with long motor line lengths. Ferrite cores and low-capacitance cable (phase/
phase<65 pF/m, phase/screen < 120 pF/m) at the output have the following effects:
•longer motor line lengths
•lower abrasion of the motor bearings by leakage currents
•improved EMC characteristics
3.2.2.2 Motor line length at operation with DC voltage
The maximum motor line length at DC operation is basically dependent on the capacity of
the motor cable. The internal lter is not active at DC operation. External measures must be
taken here, if necessary. The following data apply for operation under nominal rating condi-
tions.
Size Motor cable (standard) Motor cable (low capacitance)
13
100 m 200 m14
15

GB - 18
Connection of the Power Unit
3.2.2.3 Cable-fed disturbances depending on the motor line length at AC supply
The maximum motor line length is depending on the capacity of the motor cable as well as
on the EMC emitted interference. The following data apply for operation under nominal rating
conditions.
Size
Max. motor line length shielded
max. leakage
current
(at fN≤100 Hz)
in accordance with EN 61800-3
Category C1 Category C2
Motor cable
(standard)
Motor cable
(low capaci-
tance)
Motor cable
(standard)
Motor cable
(low capaci-
tance)
13
25 m 50 m 50 m 100 m < 5 mA14
15
The line length can be extend signicant by using motor chokes or lters. KEB recom-
mends the use of motor chokes or lters for a line length upto 50 m. Motor chokes or
lters are absolutely necessary upto 100 m.
3.2.2.4 Motor cable cross-section
The conductor cross-section of the motor cable is dependent on the output current, the cable
according to manufacturer's data, as well as the VDE regulations.
3.2.2.5 Interconnection of the motor
The connecting-up instructions of the motor manufacturer are generally valid !
Protect motor
against voltage
peaks !
Inverters switch at the output with du/dt ≤ 5kV/µs. Voltage peaks
that endanger the insulation system at the motor can occur espe-
cially in case of long motor cables (> 15 m).
A motor choke, a dv/dt-lter or sine-wave lter can be used for
protection of the motor.
3.2.2.6 Terminal strip X1B motor connection
X1B Name Function Cross-section Tightening
torque
U, V, W Motor connection 0.2-16 mm²
AWG 26-6
2.3 Nm
20.5 lb-inch
PE, Connection for pro-
tective earth
Screw M4 for
ring thimble
1.3 Nm
11 lb inch

GB - 19
Connection of the Power Unit
3.2.2.7 Wiring of the motor
L1
L2
L3
U
V
W
PE
U
V
WPE
PE
T1 T2
1 KEB COMBIVERT
2 Apply motor cable, shielding on both sides
over a large surface on the function earth
3 Three-phase motor
4 Temperature monitoring (optional)
see chapter „Temperature detection"
Do not lay PTC cable of the motor (also shielded) together with control cable !
PTC cable inside the motor cable only permissible with double shielding !
3.2.3 Connection of a braking resistor
3.2.3.1 Terminal strip X1B connection braking resistor
X1B Name Function Cross-section Tightening
torque
++, R
Connection for bra-
king resistor (alter-
native ++, PB)
0.2-16 mm²
AWG 26-6
2.3 Nm
20.5 lb-inch
PE, Connection for pro-
tective earth
Screw M4 for
ring thimble
1.3 Nm
11 lb inch
3.2.3.2 Wiring of an intrinsically safe braking resistor
X1B
R
--
++
U
V
W
R
PA
Only "intrinsically safe" braking resistors are per-
missible for this operation, since these resistors
interrupt themselves at fault such as safety fuse
without re risk. The delivered intrinsically safe
braking resistors by KEB are described in the inst-
ruction manual 00G6N1Z-0010.
3.2.3.3 Using a non-intrinsically safe braking resistor
see instruction of the brake resistors

GB - 20
Connection of the Power Unit
3.2.4 Connection of a Temperature Detection
3.2.4.1 Temperature detection terminals T1, T2
The KEB COMBIVERT G6 is delivered with a PTC evaluation. The function corresponds to
DIN EN 60947-8 and works in accordance with the following table:
Function of T1, T2 Resistance Display ru.46 Error/warning
PTC or
temperature switch
< 750 Ω T1-T2 closed –
0.75…1.65 kΩ
(reset resistance) undefined
1.65…4 kΩ
(tripping resistance)
> 4 kΩ T1-T2 open x
The behaviour of the inverter in case of error/warning is dened with parameter
CP.37. As standard the PTC input is deactivated. An instruction for the activation
can be found in the annex.
3.2.4.2 Terminal strip X1C temperature detection
X1C No. Name Function Cross-section
1
2
4
3
5
1, 4 T1, T2 Connection for temperature sensor 0.2-1 mm²
AWG 24-16
2, 3 –
Insertion slots to release the cage
clamp terminal with screw driver
SD 0, 4x2.5 (DIN 5264)
–
5 – Unlocking the terminal strip –
Other manuals for COMBIVERT G6
12
Table of contents
Other KEBCO Portable Generator manuals
Popular Portable Generator manuals by other brands
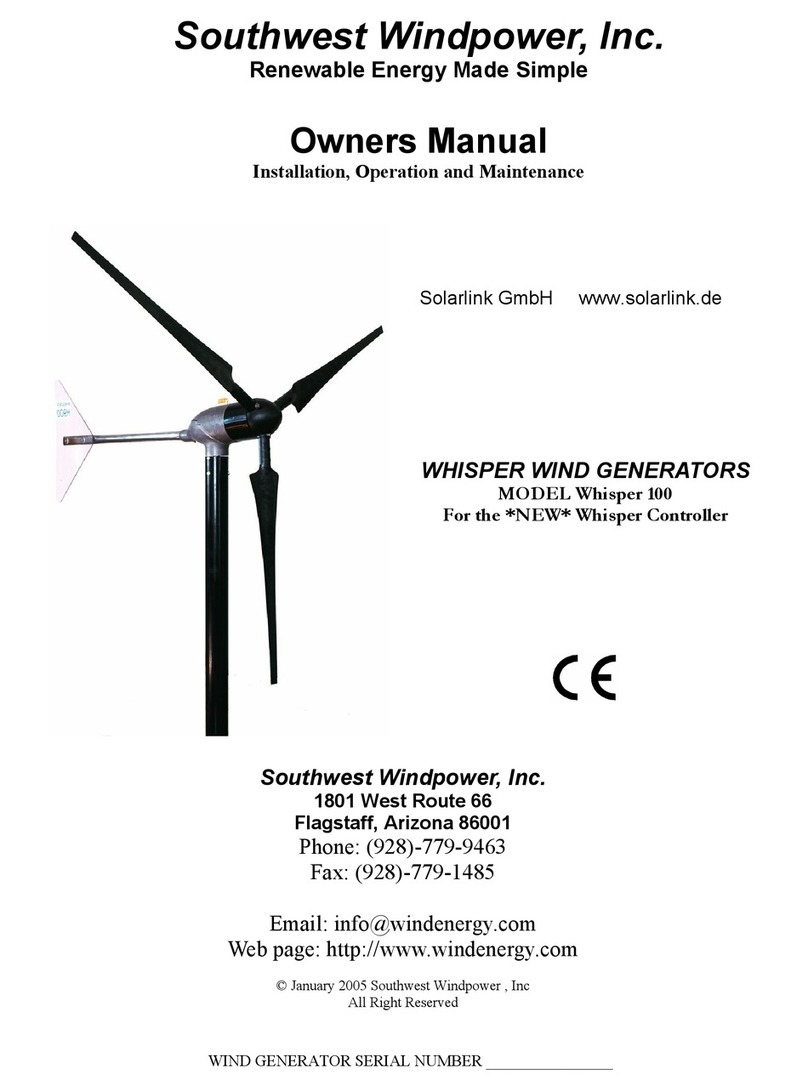
Southwest Windpower
Southwest Windpower Whisper 100 owner's manual

Chicago Electric
Chicago Electric 65414 Set up, operating, and servicing instructions
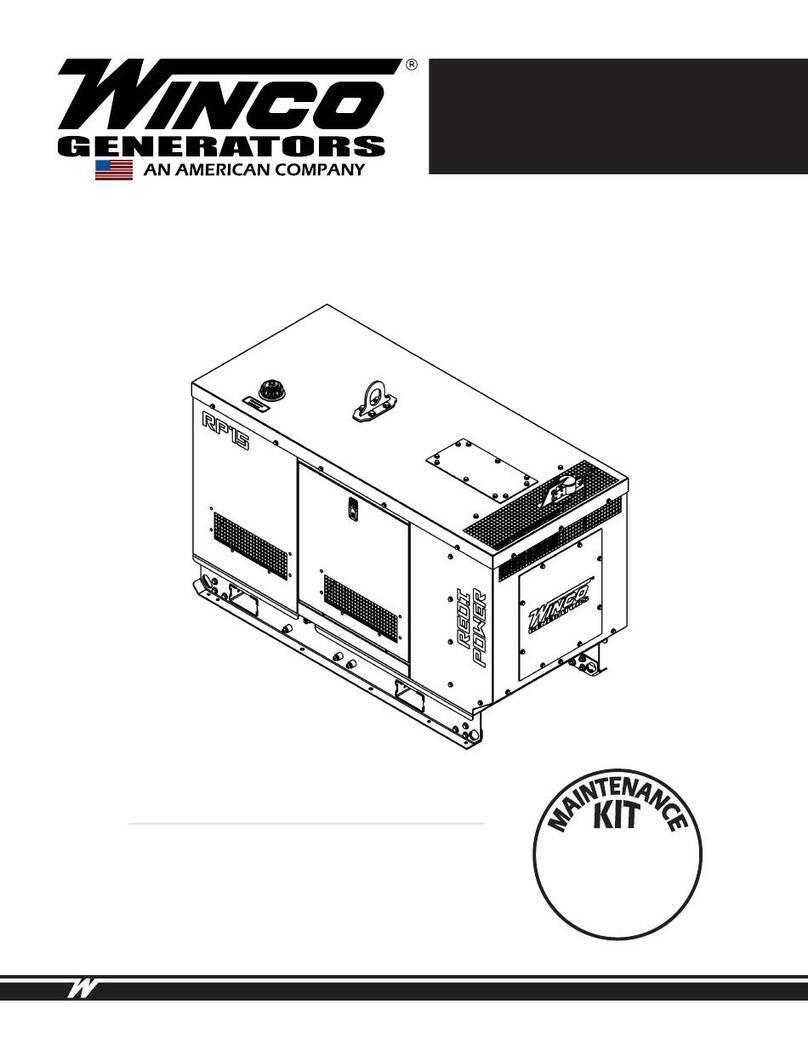
Winco
Winco RP15 Installation & operator's manual
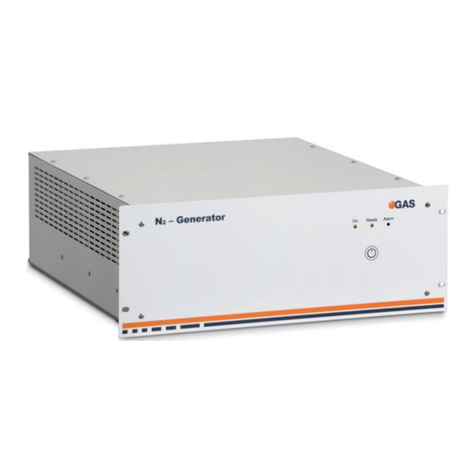
GAS
GAS N2-Generator user manual

Lincoln Electric
Lincoln Electric PRO-CUT 40 Operator's manual
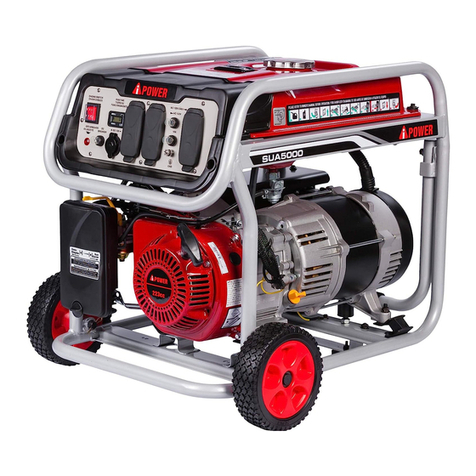
A-iPower
A-iPower POWER SUA5000 quick start guide