LabPlant SD-05 Quick reference guide

1
SD-05 SPRAY DRYER
ASSEMBLY & OPERATING INSTRUCTIONS
1)
Introduction
2)
Safety / COSHH
3)
General Safety Rules
4)
Components Included
5)
Packing List
6)
Connection to Electrical
Supply
7)
Assembly and Preparation
8)
Jet Spray Assembly
9)
Operation
10)
General Advice and Useful
Hints
11)
Optional Accessories
12)
Spare Parts List
13)
Notes
Last Revision: June 2002

2
1) INTRODUCTION
The Lab-Plant SD-05 Laboratory Scale Spray Dryer is based on more than 30 years of
continuous production and development.
The SD-05 has been designed primarily for simplicity and ease of use, rapid assembly
and disassembly for cleaning, minimal maintenance, efficiency of operation and
reproducibility of previous conditions.
2) SAFETY IN THE USE OF EQUIPMENT SUPPLIED BY LAB-PLANT LTD
Before proceeding to install, commission or operate the equipment supplied you should
be aware of potential hazards so that they may be avoided.
Although designed for safe operation, any equipment may involve processes or
procedures which are potentially hazardous. The major potential hazards associated
with this particular equipment are listed below.
•INJURY THROUGH MISUSE
•INJURY FROM ELECTRIC SHOCK
•RISK OF INFECTION THROUGH LACK OF CLEANLINESS
Accidents can be avoided provided that equipment is regularly maintained and
operators are aware of potential hazards. A list of general safety rules is included
in this manual, to assist in this regard. The list is not intended to be fully
comprehensive but for guidance only.
The COSHH Regulations (1988) - The Control of Substances Hazardous to Health
The COSHH regulations impose a duty on employers to protect employees and others from
substances used at work which may be hazardous to health. The regulations require
that you assess all operations which are liable to expose any person to hazardous
solids, liquids, dusts, vapours, gases or micro-organisms. You are also required to
introduce suitable procedures for handling these substances and to keep appropriate
records.
The equipment supplied by Lab-Plant Ltd may involve the use of substances which can
be hazardous (for example, cleaning fluids used for maintenance or chemicals used for
particular demonstrations) and it is essential that some person in authority is
responsible for implementing COSHH regulations.
Part of these regulations are to ensure that the relevant Health and Safety Data
Sheets are available for all hazardous substances used in the laboratory. Any person
using a hazardous substance must be informed of the following:
•Physical Data about the substances
•Any hazard from fire or explosion
•Any hazard to health
•Appropriate First Aid treatment
•Any hazard from reaction with other substances
•How to clean/dispose of spillage
•Appropriate protective measures
•Appropriate storage and handling
Although these regulations may not be applicable in your country, it is strongly
recommended that a similar approach is adopted for the protection of staff operating
the equipment. Local regulations must also be considered.

3
3) GENERAL SAFETY RULES
FOLLOW RELEVANT INSTRUCTIONS
a) Before attempting to install, commission or operate equipment the manufacturers
instructions should be understood and implemented.
b) It is dangerous to misuse equipment or ignore instructions, regulations or
warnings.
c) Do not exceed specified maximum operating conditions (e.g. temperature,
pressure, speed etc.).
INSTALLATION
a) Use lifting tackle where possible to install heavy equipment.
b) Care should be exercised to avoid damage to the equipment during handling and
unpacking. Damage may go unseen during commissioning creating a potential
hazard to subsequent operators.
c) Equipment involving inflammable or corrosive liquids should be sited in a
containment area or bund with a capacity 50% greater than the maximum equipment
contents.
d) Ensure that all services are compatible with the equipment and that independent
isolators are always provided and labelled. Use reliable connections in all
instances, do not improvise.
e) Ensure that all equipment is earthed and connected to an electrical supply at
the correct voltage. The electrical supply must incorporate an Earth Leakage
Circuit Breaker (ELCB) or Residual Current Circuit Breaker (RCCB) to protect the
operator from electric shock in the event of misuse or accident.
f) Potential hazards should always be the first consideration when deciding on a
suitable location for equipment. Leave sufficient space between equipment and
between walls and equipment
COMMISSIONING
1) Ensure that equipment is commissioned and checked by a competent member of
staff.
4) COMPONENTS INCLUDED
The SD-05 is supplied complete and ready for operation without any extra equipment
normally being required. Options are available such as alternative jet nozzle spray
assembly sizes, exhaust wet scrubber, bench type mobile trolley, protective screen,
large main chamber, inert gas inlet etc.
The unit comprises:
Main Cabinet Including control panel, inlet air filter, spares drawer, top
chamber, peristaltic pump, side support tray, outlets from
compressors to jet de-blocker and jet nozzle, doors to interior on
side and rear.
Spray Assembly Main chamber, cyclone, collection bottle and bottom collection
tube.
Other Items All necessary silicone pump tubing, exhaust tubing,
connectors, PTFE gaskets.

4
5) PACKING LIST
The apparatus should be carefully unpacked and the components checked against the
Delivery Note.
Any omissions or breakages should be notified to Lab-Plant Ltd within three days of
receipt.
The check-list for unpacking is as follows:
DESCRIPTION
QTY
Main SD-05 unit
1
Main Chamber
1
Cyclone
1
Collection Bottle
1
Collection Tube
1
Screw Joint Connectors
2
PTFE Gaskets
2
Clamp for Chamber/Cyclone
1
Jet Assembly with 0.5 mm jet
1
Side Mounting Tray
1
Silicone Tube 4mm bore x 2mm wall 2.0 m
Exhaust Tube
1.7 m
Nylon Tube 4mm
∅
1.0 m
Nylon Tube 6mm
∅
1.0 m
The above comprises the unit SD-05.
Any accessories or spares ordered will be additional to the above.
6) CONNECTION TO ELECTRICAL SUPPLY
The Lab-Plant SD-05 Spray Dryer is supplied for 220/240V, 50/60Hz operation.
A 110/120V primary 240V secondary step down transformer is supplied for 110V
operation.
The power requirement for the 240 volt unit is 13 amp and for the 110 volt unit is 30
amps.
IMPORTANT
The mains cable is connected as follows:
Brown = Live
Black = Neutral
Green/Yellow = Earth
The SD-05 must always be connected to suitable earthing.

5
7) ASSEMBLY AND PREPARATION
Ensure the SD-05 is on a strong
level bench top and, if not being
used with an exhaust wet scrubber,
the unit must be positioned near an
outside window if exhausting to
atmosphere or to the main
laboratory fume cupboard. Do not
connect direct to any extraction
system as this
will affect the air
flow. If using with a wet scrubber
the SD-
05 may be positioned as
required but careful examination at
the exhaust outlet must be made to
determine if the product being
sprayed is being entirely cleaned
by the scrubber system.
Open the
main chamber clamp which
is fastened to the chamber head
and, carefully supporting the main
chamber, fit it into position and
tighten the clamp sufficiently to
hold the chamber whilst also
allowing it to be rotated to line
up with other components.
Loosen
the knurled screw ring at
the base of this assembly and slide
the top tube of the cyclone upwards
into the assembly. Rotate the
cyclone so that the flange of the
cyclone and the flange of the main
chamber are in line. Using the
small black anodised clamp connect
these flanges together and tighten
the clamp. Carefully tighten the
main chamber clamp, connecting
clamp and the knurled screw whilst
ensuring that all of the glass
components are lined up correctly
and are not under any strain.
The exhaust assembly has adjustments which are
factory set to match the glassware supplied and
should not require attention.
When all parts have been secured as described, the
stainless steel exhaust assembly can also be secured
in position using the grub screws provid
ed and, if
the glassware is correctly fitted, this part should
not require to be altered or moved in future
assembly/disassembly unless new glass parts are used.
When any new glass components (main chamber or
cyclone) are used some adjustments may be neces
sary.
The exhaust assembly slides in the direction shown
and this is sufficient to allow for adjustments.
Using the black plastic screw connectors and the PTFE gaskets, connect the tube to
the base of the main chamber and the collection bottle to the cyclone.
Tighten these parts so that they are firm against the gasket seals but not over-
tightened.
Connect the exhaust tube to the tapered stainless steel exhaust assembly by simply
sliding it over the top. For most applications this will be sufficient. However,
adhesive tape may be used as an added precaution.
Direct the other end of the exhaust tube to an outside vent or to a fume cupboard as
required.
(If using the wet scrubber see Note I).

6
8) JET SPRAY ASSEMBLY
The stainless steel spray assembly
is a two fluid nozzle where the
inner nozzle develops the liquid
jet and the outer the compressed
air outlet. The compressed air
atomises the liquid as it emerges
from the jet to form the required
fine spray.
The jet and
outer nozzle can be
unscrewed from the main assembly
for cleaning if required.
Always be careful not to damage the
inner jet nozzle (which is only
0.5mm ∅
thin wall stainless steel
tubing) as any slight misalignment
will affect the efficiency of the
spray.
The jet assembly is easy to
disassemble by unscrewing the
knurled rings.
Instructions for testing the jet
spray assembly outside the main
chamber
Before fitting the jet into the top
chamber it is useful to operate it
outside, with water, to see the
actual spray formation and to
examine the changes caused by
reducing and increasing the
compressed air pressure.
The procedure is detailed below:
Connect to mains and the green ‘Mains’ indicator will illuminate. Switch on the main
switch next to the mains indicator lamp. Press the green ‘On’ position for the pump
and set the pump rotation speed so that it is very slow.
Open the hinged plastic cover of the pump and leaving sufficient tube to connect to
the jet when it is in the top chamber, insert the tube so that it is fed into the
peristaltic pump rollers.
Open the white plastic clips which retain the tube in position, insert the tube fully
and release the clips. The tube should now be regularly compressed by the pump
rotors. Fit one end of the tube to the riffled tubular on the jet tube body.
Using the larger 6mm diameter hard nylon tube push one end into the appropriate
connector at the top left side of the cabinet and the other end in the connector in
the jet. This is the main compressed air feed line to the jet nozzle.
Then connect the small diameter nylon tube into the appropriate connector at the
cabinet and the top of the jet. This is the compressed air supply for the jet de-
blocking system. There is no possibility of connecting these tubes incorrectly as
the connectors are of different sizes. To release these tubes simply push in the
black ring on the connector and pull the tube out.
When the three tubes are connected to the jet assembly place the open end of the
silicone pumping tube into a beaker of clean water and switch on the pump.
Increase the speed and watch the water travel through the tube.

7
8) JET SPRAY ASSEMBLY (continued….)
When the water reaches the jet assembly it will emerge from the jet nozzle in a fine
stream. Switch on the compressor touch switch on the main panel and the liquid
emerging from the jet should immediately form a fine spray mist. (Note: switching on
the compressor also activates the jet de-blocking system. This can be turned to low
or frequent, as required, using the de-blocker control knob).
Set the multi-indicator knob to ‘Pump Flow’ and then adjust the ‘Pump Speed’ knob at
the same time observing the digital indicator. The digital numerals will alter as
the pump speed is changed.
The information indicates pump speed on a nominal 10-50 scale. For appropriate flow
rates in ml/hr please see the chart on Note II.
Now set the multi-indicator to the ‘Compressor Air Pressure’ setting. The digital
indicator will now show the pressure to the jet in bar.
Whilst observing the digital indicator and the actual spray formation alter the air
pressure using the ‘Compressor Air Pressure’ knob at the top of the integral panel.
The maximum air pressure when using a 0.5mm jet is approximately 2.0 bar. This
setting produces a fine spray.
As pressure is reduced you will see the spray become progressively coarser. This is
producing larger liquid droplets and some products require reduced pressure settings
to spray dry successfully.
Note that the maximum air pressure available is considerably reduced when larger jet
diameters are used so that, for example, if using the 1mm jet the maximum compressor
pressure available may be as low 0.6 bar. This is normally sufficient for the
larger jets.
When you have become familiar with the operation of the jet system look closely at
the jet nozzle to see the fine jet de-blocking needle in operation. The frequency of
the de-blocking action is controlled by the ‘De-blocker’ knob. If de-blocking is not
required simply remove the small diameter (4mm) nylon tube from the top of the jet
assembly and from the outlet at the top left of the main unit. The internal de-
blocker controls will continue to operate but will not affect the jet
Now place the jet assembly in the top chamber and secure with the knurled screw.
The SD-05 unit is ready for operation.
9) OPERATION
Select the product you wish to spray dry but always start and end the process by
using clean or distilled water.
Place the pump tube in the water.
Switch on the mains switch on the SD-05 and then switch on the blower and the heater
using the appropriate green touch contacts.
Note: the heater will not operate unless the blower is running.
Using the σbutton on the air flow increase to maximum.
This is indicated by setting the multi-indicator switch to ‘Air-flow’.

8
9) OPERATION (continued….)
The digital indicator will then show the flow on a scale of 10-50. When the unit is
cold approximately 46 may be the maximum indicated. This does not matter - simply
press the σbutton briefly until the digits do not increase any more. (Note: The 10-
50 scale is shown as m3/hr on the graph on Note III).
When the air flow is at maximum setting, using the ‘inlet temperature’ controller set
the temperature as required.
To see the set temperature press the Ξbutton. The set level is then indicated.
Keeping the Ξbutton pressed adjust the σor τbutton as required until the desired
setting indicates. Release the buttons and the temperature will rapidly increase
until the set level is achieved.
A variable overtemperature protection cut-out is included. Open the rear door and on
the panel facing is a dial control. Using a screwdriver set the max operating
temperature to any level required. In the event of the overtemperature cut-out
operating it will switch off the heater. The overtemperature control will require
re-setting. To do this press the red button through the hole below the setting dial.
Switch on the compressor and then the pump using the appropriate green touch
contacts.
Using the 0.5mm jet maximum back pressure is approximately 2.0 bar and this reduces
when larger diameter jets are used.
Using the ‘multi-indicator’ knob set the compressor flow to maximum.
Then set the pump to a fairly slow rate e.g. 15 or 20.
Allow a small amount of water to be pumped into the silicone tube to clean the tube
and the jet and then transfer the tube to the sample. When the sample reaches the
jet the Spray Drying Operation should commence and dried powder should be observed
spiralling down the cyclone into the collection bottle.
Once spray drying has commenced variations in temperature, air flow, pump speed,
compressed air pressure etc may be tried to improve the process.
10) GENERAL ADVICE AND USEFUL HINTS
1) Always start a trial with a low to medium inlet temperature (120-180°C), maximum
air-flow, maximum compressor air-pressure and a slow pump rate. Observe the
bottom of the main chamber for wetting and either reduce the pumping rate or
increase the temperature if the product is not completely drying. The optimum
pumping/temperature rates are achieved when no wet spotting of the product is
observed.
2) If the sample is a liquid with solids in suspension it may be necessary to keep
it continually agitated with a magnetic or overhead stirrer. Heavy suspensions
are best pumped from the sample container when it is positioned on the side
shelf as this shelf, the pump and the jet are all at a similar height. If the
sample is pumped from the bench top the product may separate as it is being
pumped upwards in the silicone tube.

9
10) GENERAL ADVICE AND USEFUL HINTS (continued….)
3) Most spray drying processes lose fines in the exhaust. The amount lost usually
depends on air flow and particle weight. The air flow can be reduced using the
panel controls and the particle size/weight can often be increased by using a
larger jet size and/or by reducing the compressed air pressure.
4) At the commencement of spray drying give the main chamber a few minutes to warm
up. The inlet temperature may show the required setting but the glassware and
main chamber will be quite cool for a few minutes.
5) If the sprayed sample is light coloured it may be more easily observed by
placing a dark card behind the cyclone.
6) The ideal flow path through the cyclone should be a continuous spiral. If
product accumulates on the cyclone wall try alterations to the air flow or the
compressor jet pressure or the jet size.
7) Only change one parameter at a time e.g. temperature, air flow etc.
8) Some samples may require pre-heating before spraying.
9) In rare instances the use of a suitably supported separating/dropping funnel
positioned as near as possible to the jet assembly has been found to be
effective rather than using the pump. This gravity feed method is effective
where e.g. abrasive ceramics may cause the pump tube to wear exceptionally
quickly.
10) Peristaltic pumping always creates a pulsing liquid flow. If this is a problem
the pulsing effect can be reduced by connecting a small glass expansion bulb in
the tube between the pump and the jet.
11) Generally the most efficient drying is achieved using the highest temperatures
compatible with the product but temperatures as low as ambient may be used with
e.g. non-flammable solvents.
12) If spraying with an inert gas is necessary a back plate with gas connectors may
be fitted to cover the air inlet position at the rear of the SD-05. However, if
using with inert gases we recommend that the SD-05 should be used in a fume
cupboard and that precautions are taken against the possibility of any gas
leaks. The SD-05 is not designed as an Ex. System. For inert gas supply please
consult the table in Note III.
13) The SD-05 successfully dries encapsulated products.
14) If agglomerated trials are required it is necessary to purchase an additional
full spray assembly (SDS 2046) and to use this with the counter current spraying
adapter and a separate peristaltic pump. Fit the counter current spraying
assembly to the bottom of the main chamber using the standard double screw
adapter and PTFE seal. Using a simple T or Y connector and the standard tubing
connect to the compressed air supply for the main jet but do not connect to the
de-blocking system. Using a separate peristaltic pump direct the agglomerating
spray onto the main sprayed product.

10
11) OPTIONAL ACCESSORIES
1) 0.5mm jet is supplied as standard. 1.0mm and 1.5mm jets are optional.
2) Amber stained low actinic glassware is available for products which are light
sensitive.
3) An exhaust air wet scrubber unit.
4) Magnetic stirrer hotplate MR 3001 for maintaining liquids in suspension and for
heating. The side tray is designed to accept this stirrer.
5) Magnetic hotplate MR 3000 when heating is not required.
6) Mobile bench - when standard bench space is not available or when the unit is
stored between projects or may be moved to different departments.
7) Large main chamber - 800 mm long. Gives added spray drying efficiency but must be
positioned to overhang the bench due to the extra length. Supplied with a
connection tube between the cyclone and the stainless steel exhaust assembly.
8) Inert gas connection plate. Designed to cover the air inlet filter and with a
riffled tubular for gas connection.
12) SPARE PARTS LIST
SDS 2018 Standard Main Spray Chamber - 500mm long x 215mm OD
SDS 2020 Large Main Spray Chamber - 800mm long x 215mm OD
SDS 2022 Cyclone
SDS 2001 Exhaust Tube - 3.5 metre length
SDS 2002 Exhaust Tube - 1.75 metre length
SDS 2031 Peristaltic Pump Silicone Tube 4mm ID x 1.6mm wall
SDS 2004 Peristaltic Pump Silicone Tube 2.5mm ID x 2.0mm wall
SDS 2056 Nylon Tube (for de-blocker)
SDS 2057 Nylon Tube (for atomiser)
SDS 2006 Sample Collection Bottle - 500 ml
SDS 2021 Sample Collection Bottle - 1000 ml
SDS 2046 Jet assembly complete with any specified standard jet size required
SDS 2010 Sample Collection Tube
SDS 2011 Double Plastic Screwcap Adapter
SDS 2012 PTFE Gasket Seal
SDS 2040 Plunger De-Blocking Needle Assembly
SDS 2042 Needle 0.5mm
SDS 2033 Pack of Assorted O Rings for Jet Assembly
SD 1004 0.5mm Stainless Steel Jet Nozzle Assembly (Inner Jet and Outer Nozzle)
SD 1006 1.0mm Stainless Steel Jet Nozzle Assembly (Inner Jet and Outer Nozzle)
SD 1007 1.5mm Stainless Steel Jet Nozzle Assembly (Inner Jet and Outer Nozzle)

11
13) NOTES
Note I Wet Scrubber
The SD 5002 Wet Scrubber effectively washes the exhaust and is particularly useful
when spray drying harmful substances e.g. fine ceramics etc or products which may
cause some nuisance e.g. colour pigments and products with strong flavours.
The scrubber unit is designed to be placed on top of the SD-05 and a small section of
the standard exhaust tube is used to connect the stainless steel exhaust outlet to
the bent tube inlet on the scrubber. The remaining exhaust tube is connected to the
top outlet and directed to a convenient window or to a nearby fume extraction
cupboard.
The scrubber requires a continuous supply of mains water at approximately 6-8 litres
per minute and minimum pressure of approximately 3 bar (44 psi). This is connected
to the top inlet and a separate tube from the bottom outlet should be directed to
drainage or, if required, to a settler tank and recycled by pump rather than using
mains supply.
The wet scrubber is constructed entirely in PVC and the double spray assembly in the
scrubber is 316 stainless steel.
Note II Pump Flow Rate
The digital information on the
multi-
indicator, when set at ‘Pump
Flow’, shows the pump speed on a
numerical scale of 0 to 50.
Note III Air Flow Rate
The multi-indicator shows the air
flow at the exhaust outlet on a 10-
50 digital scale. Approximate
values at the exhaust assembly
outlet are shown as follows:
Scale
ml/hr
Scale
M3/hr
0
0
10
38
10
350
15
44
20
600
20
47
30
1000
25
50
35
1500
30
54
40
1900
35
57
45
3200
40
62
50
4600
45
64
50
73
Air Flow Rate
The maximum ‘50’ indicator is set without any flexible exhaust tube attached e.g. for
when used in a fume cupboard. Long lengths or bends in the exhaust tube will reduce
the volume of drying air which is blown through the system.
Dependant on the length of exhaust tube used or the severity of bends in its length
the maximum reading may be reduced to as low as 40-45 on the digital indicator.
Please also note that when used in a fume cupboard the air suction may actually
increase the normal maximum air flow through the SD-05.

12
13) NOTES (continued….)
Note IV Counter-Current Spraying
Often useful when a longer resonance time of the product in the main chamber may
assist in the drying process.
Also useful for agglomeration work when the standard jet may be used to spray the
product and an additional jet assembly together with the PTFE/stainless steel adapter
can be used to spray the agglomerator.
An additional peristaltic pump and compressed air supply is necessary if two jet
assemblies are used.
Sketch 1 Shows the unit set for counter-current spraying when the spray is
directed against the air flow.
Sketch 2 Shows the unit set for agglomeration work where the top jet sprays the
product and the bottom jet sprays the agglomerator.
Sketch 1
Sketch 2
Note V Maintenance
Regular maintenance of any equipment ensures maximum trouble-free life.
Customers are recommended to carry out simple maintenance at regular intervals - the
most basic of which is to keep the equipment clean! No matter how regularly your
equipment is in use always find time to thoroughly clean it.
Periodically remove the AIR FILTER in the rear door and wash.
Maintenance contracts are available for most products.

Thank you for reading this data sheet.
For pricing or for further information, please contact us at our UK Office, using the details
below.
UK Office
Keison Products,
P.O. Box 2124, Chelmsford, Essex, CM1 3UP, Engl nd.
Tel: +44 (0)330 088 0560
F x: +44 (0)1245 808399
Em il: s [email protected].uk
Please note - Product designs and specifications are sub ect to change without notice. The user is responsible for determining the
suitability of this product.
Table of contents
Other LabPlant Dryer manuals
Popular Dryer manuals by other brands

Bosch
Bosch WTY88898SN Installation and operating instructions
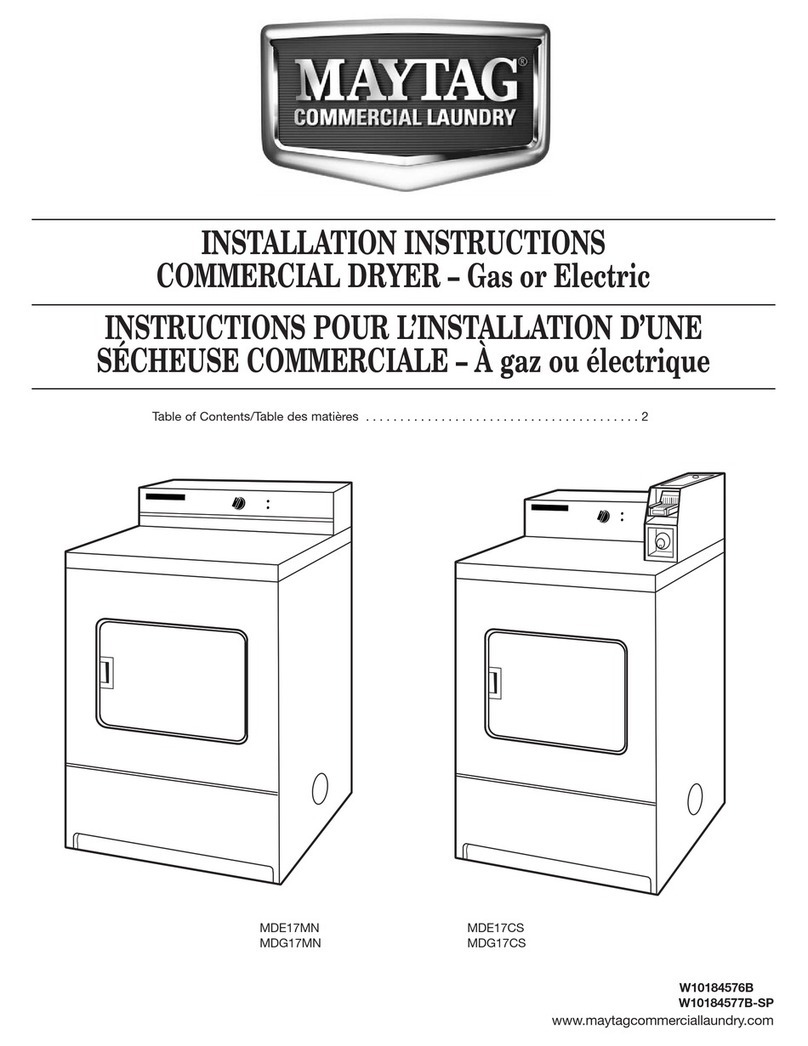
Maytag
Maytag MDE17MN installation instructions

AEG Electrolux
AEG Electrolux LAVATHERM T35400 operating instructions

Bosch
Bosch WTG8640SSA Installation and operating instructions
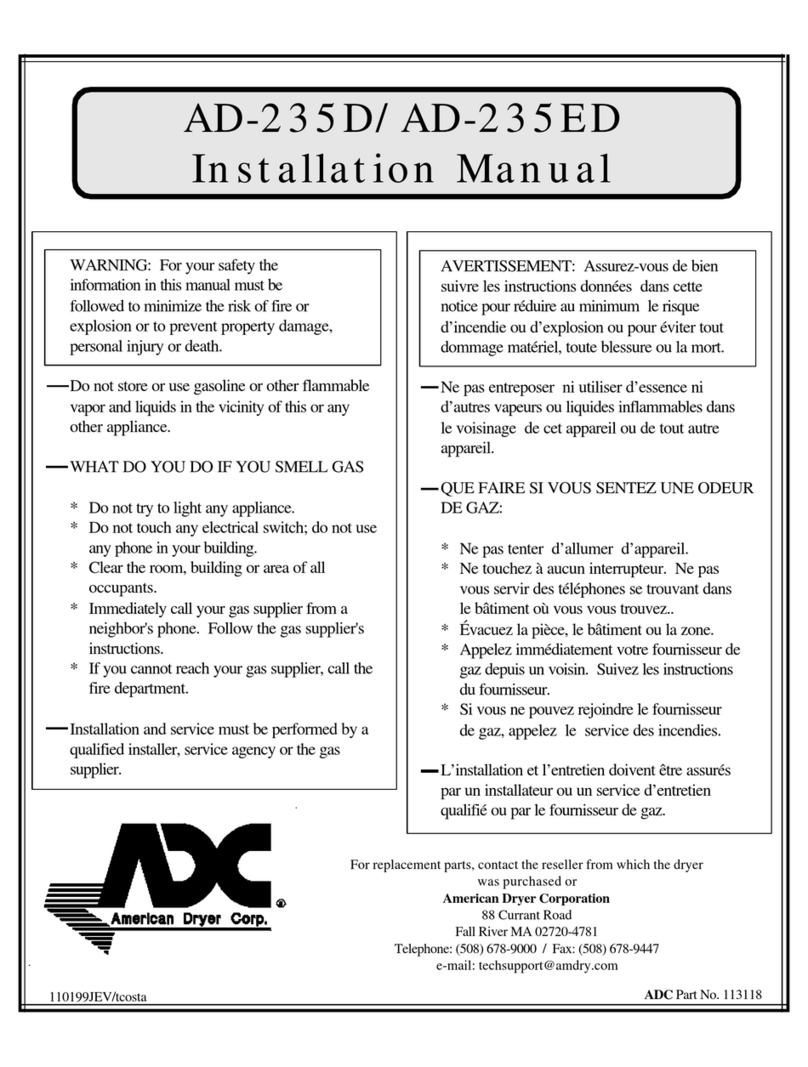
American Dryer Corp.
American Dryer Corp. AD-235D installation manual

White Knight
White Knight B96M8W Service manual