Lika SMA1 Series User manual

SMA1
MAN SMA1 E 2.3.doc 1www.lika.it
www.lika.biz
User manual
SMA1
Description
This manual describes the products of SMA1 series.
The purpose of these sensors is to measure linear
displacements on industrial machines and
automation systems. The measurement system
includes a magnetic tape and a magnetic sensor.
The tape is magnetized with magnetic north-south
poles. The poles are coded thus the magnetic tape is
absolute. As the sensor is moved along the magnetic
tape, it detects the displacement and produces an
absolute SSI output or BiSS output signal (B-mode
or C-mode) and an additional 1Vpp sin-cosine signal
for speed feedback.
The sensor has to be matched with MTA1 magnetic
tape.
Chapters
1Safety summary
2Identification
3Mounting instructions
4Position errors diagnostics
5Electrical connections
6SSI interface
7BiSS B-mode interface (SMA1-…/S682)
8BiSS C-mode interface
91Vpp outputs
10 Dimensional drawing
11 Maintenance
12 Troubleshooting
1 -Safety summary
Safety
•observe the professional safety and accident prevention
regulations applicable to your country during device
installation and operation;
•installation has to be carried out by qualified personnel
only, without power supply and stationary mechanics
parts;
•the device must be used only for the purpose appropriate
to its design;
•high current, voltage and rotating parts can cause serious
or fatal injury.
Electrical safety
•switch OFF the voltage before connecting the device;
•connect according to the chapter “Electrical connections”;
•according to the 89/336/CEE norm on
electromagnetic compatibility, following
precautions must be taken:
-before handling and installing, discharge electrical charge
from your body and tools which may come in touch with
the device;
-power supply must be stable without noise, install EMC
filters on device power supply if needed;
-always use shielded and twisted cables if possible;
-avoid cables runs longer than necessary;
-avoid running the signal cable near high voltage power
cables;
-mount the device as far as possible from any capacitive or
inductive noise source, shield the device from noise source
if needed;
-minimize noise by connecting shield or connector housing
to ground (GND). Make sure that ground (GND) is not
affected by noise. The shield connection point to ground
can be situated both on the device side and on user’s side.
The best solution to minimize the interference must be
carried out by the user.
Mechanical safety
•install according to the chapter “Mounting instructions”
with stationary mechanics parts;
•do not disassemble the device;
•do not tool the device;
•do not subject the device to knocks or shocks;
•protect the system against solvents and substances
damaging it;
•respect the environmental characteristics of the product;
•be sure that the system is mounted where hard or sharp
objects (e.g. metal chips) do not come into contact with
the magnetic tape and the bottom of the sensor head. If
these conditions cannot be avoided provide a wiper or
pressurized air.

SMA1
MAN SMA1 E 2.3.doc 2www.lika.it
www.lika.biz
2 -Identification
The device can be identified by the label's data
(ordering code, serial number). This information is
listed in the delivery document. For technical
features of the product, refer to the technical
catalogue.
3 -Mounting instructions
3.1 Magnetic tape
Install sensor and magnetic tape according to the
above figure.
The arrow shows standard counting direction.
The system doesn't work if mounted incorrectly.
3.2 Sensor mounting
fig.6
Sensor can be fixed by means of two M4 screws
over the buttonholes. Make sure that the gap
between sensor and tape is in respect with (fig. 6)
along the total measuring length. Avoid contact
between the parts. You can check planarity and
parallelism between sensor and magnetic tape using
a feeler gauge.
The allowed gap (D) is 0.1 mm ÷0.3 mm
(0.004” ÷0.012”).
Do not use the cover strip, it would cause excessive
gap between sensor and tape surface.
4 -Position errors diagnostics
In case of bad alignment between of the sensor on
the tape, the following errors may occur during
power-on or operation:
•during power-on: "LED on", invalid data could
be transmitted until the sensor is correctly
aligned (LED off);
•during operation: last valid position is freezed
until the next valid position on the tape is
detected.
4.1 Diagnostic LED
When lit, the LED indicates an incorrect alignment
of the sensor to the tape, like:
•gap between sensor and tape out of tolerance
(see fig. 6)
•incorrect installation of sensor
•sensor overlaps the tape
With BiSS interface, LED status is transmitted on nE
bit.
Note:
"LED off" confirms correct detection of absolute
position, but not correct detection of sine-cosine
signals.

SMA1
MAN SMA1 E 2.3.doc 3www.lika.it
www.lika.biz
5 -Electrical connections
Connections
Colour Function
Violet Clock in +
Yellow Clock in -
Grey Data out +
Pink Data out -
Green A
Brown /A
Red B
Black /B
Brown/ Green +Vdc *
White/ Green 0Vdc GND
White not connected
Blue not connected
*:+10Vdc +30Vdc for standard SMA1
+5Vdc for SMA1-…/S188
+5Vdc for SMA1-…/S682
Specifications of the cable
T12 cable (TKD 4444)
Twisted pair 4 x 2 x 0,14mm2 + 4 x 0,25mm2
Screening : braided
Outside Ø : Ø 6.1 mm (Ø 0.24”)
Resistance : according to DIN VDE 0295 class 6
according to IEC
6 -SSI interface
SMA1-BA-5-…
SMA1-GA-5-…
6.1 LSB right aligned protocol
The type of transmission protocol is "right aligned"
with a length of 25 bits. The transmission starts with
MSB (most significant bit) and ends with LSB (less
significant bit).
The device uses 20 bits for the position, unused bits
are set to 0 (zero).
The output code of the sensor can be GRAY or
BINARY (see ordering code).
The measuring step is equal to the resolution (5µm).
Position structure:
bit 24…20 19 …0
value 00000 MSB …LSB
6.2 Recommended transmission rates
The SSI interface has a frequency of data
transmission from 100 kHz to 1 MHz.
The CLOCK signal and DATA signal follow the “EIA
standard RS-422”.
The transmission rate (baud rate) depends on the
length of cables.
Cable length Baud rate
< 50 m < 400 kHz
< 100 m < 300 kHz
< 200 m < 200 kHz
< 400 m < 100 kHz
The time interval between two Clock sequence
transmissions must be at least 16µs ( Tp > 16µs ).

SMA1
MAN SMA1 E 2.3.doc 4www.lika.it
www.lika.biz
7 -BiSS B-mode interface
SMA1-I7-…/S682
SMA1 is a slave device according to “BiSS B-mode
interface” and “Standard encoder profile”.
Refer to the official BiSS website for all information
not listed in this manual (www.biss-interface.org).
The sensor works in point-to-point configuration,
and has to be installed on a “single master, single
slave” network (not on a “single master, multi slave”
network).
CLOCK and DATA signals level are according to the
“EIA standard RS-422”.
7.1 Communication
The BiSS B-mode protocol uses two types of data
transmission protocols:
•Register Mode: used to read or write data into
the registers of the slave.
•Sensor mode: used to send process data from
the slave to the master.
7.2 Register Mode
See official BiSS documents for complete structure.
Main control data is described in this chapter.
Register address (7 bits)
Specifies the register to read or write.
DATA (8 bit)
Write register: value to write into the register
(transmitted from master to slave).
Read register: value read from the register
(transmission from slave to master).
Data bit structure:
bit 7……0
MSB ……LSB
CRC (4 bits)
Correct transmission control (inverted output).
Polynomial: X4+X1+1 (binary: 10011)
Logic circuit:
7.3 Sensor mode
Sensor mode (32 bits) is composed by position value,
1 error bit (nE), 1 warning bit (nW) and CRC
checking (6 bits).
Sensor data structure:
Start
DATA Stop
31…8 765…0
position
error warning
CRC
Attention: Multi-Cycle-Data bit (MCD) is not used,
the master mustn’t ask it!
Position (24 bits)
Process data transmitted from slave to master.
The transmission starts with MSB (most significant
bit) and ends with LSB (less significant bit).
bit 31…28 27 …8
value 0000 MSB …LSB
To see position value in mm, multiply the data value
received for the resolution (see 4Dhex register).
Error (1 bit)
Communicates an error of the slave.
nE = “1”: correct status (no error)
= “0”: error status: tape not read.
Check gap between sensor and tape,
planarity and parallelism of the system.
Warning (1 bit)
Not used (nW = “1”)
CRC (6 bits)
Correct transmission control (inverted output).
Polynomial: X6+X1+1 (binary: 1000011)
Logic circuit:
1st
stage
X1X2X3X5
Input Data (starts from MSB)
X0
2nd
stage
3rd
stage
4th
stage
5th
stage
6th
stage
X4
1st
stage
2nd
stage 3rd
stage 4th
stage
X0X1X2X3
Input Data (starts from MSB)

SMA1
MAN SMA1 E 2.3.doc 5www.lika.it
www.lika.biz
7.4 Used registers
Register (hex) Function
42…43 Profile ID
44…47 Serial number
48 Command
49 Configuration
4D Absolute resolution
51…53 Preset/ Offset
55 Device type
58 SIN/COS resolution
78…7D Device ID
7E…7F Manufacturer ID
All registers in this chapter are listed according to
the following outline:
Address Function name [access]
Description of the function and default value.
-Address: register address in hexadecimal values.
-Access: ro = read only
rw = read and write
wo = write only
-Default parameter values are written in bold.
42…43 Profile ID [ro]
These registers contain the identification code of
the used profile.
Register 42 43
Hex 28 14
See “Standard encoder profile”, “data format”,
“Variant 0-24”.
44…47 Serial number [ro]
These registers contain the serial number (hex value)
of the device.
reg.44: year of production
reg.45: week of production
reg.46, 47: progressive serial number
48 Command [wo]
Value
Function
00 Normal operation
01 Save parameters on EEPROM
02 Save and activate Preset/ Offset
04 Load and save default parameters
This register will set back to "00" automatically.
Wait min. 30ms (EPROM writing time) before using
the next function.
49 Configuration [rw]
Bit Function bit=0 bit=1
0SELSSI BiSS SSI
1Set preset/ offset Preset Offset
2Enable preset/ offset Enable Disable
3Not used
4Not used
5Output code Gray Binary
6Counting direction *
Standard
Inverted
7Not used
*: related to absolute position (not to sin/cos signal)
The new setting will be active immediately after
transmission. Use the function “Save parameters”
(set “01” register 48) to store the new value.
Default = 20h
4D Absolute resolution [rw]
Contains the resolution of absolute sensor.
64hex : Res.=0.1mm (max position = 00 FF FFh)
32hex : Res.=0.05mm (max position = 01 FF FFh)
0Ahex : Res.=0.01mm (max position = 07 FF FFh)
05hex : Res.=0.005mm (max position = 0F FF FFh)
The new setting will be active immediately after
transmission. Use the function “Save parameters”
(set “01” register 48) to store the new value.
After the modification of reg.4D Preset and Offset
values have to be updated according to the new
resolution!
Default = 05h.

SMA1
MAN SMA1 E 2.3.doc 6www.lika.it
www.lika.biz
51…53 Preset/Offset [rw]
This function has to be enabled by setting reg.49 bit
2 = ”0”. Setting of Preset or Offset register can be
carried out only when the sensor is not moving.
Preset: any desired position value can be set (e.g.
"0", zero setting)
Offset: adds an offset to actual position.
Position = actual position + Offset.
Preset/Offset structure:
Reg.
51 52 53
MSB …LSB
223-2
16 215 -2827-2
0
Use the function “Save and activate Preset/ Offset”
(set “02” register 48) to store and activate the new
value.
The max. allowed Preset values are depending on
the resolution.
resolution = 0.1 àmax preset =00 FF FFh (16bit)
resolution = 0.05 àmax preset =01 FF FFh (17bit)
resolution = 0.01 àmax preset =07 FF FFh (19bit)
resolution = 0.005àmax preset =0F FF FFh (20bit)
Default = 00h.
55 Device type [ro]
Describes the type of device.
Default = 06h: linear encoder BiSS + SIN/COS
58 SIN/COS resolution [ro]
Describes the period of sin/cos signal
Default = 01h: resolution = 1mm
78…7D Device ID [ro]
These registers contain the Device ID.
Reg.
78 79 7A 7B 7C 7D
Hex 53 4D 41 31 xx xx
ASCII
SMA1--
xx: software version
7E…7F Manufacturer ID
These registers contain the Manufacturer ID.
Reg.
7E 7F
Hex 4C 69
ASCII
Li
Li = Lika Electronic.
7.5 Application note
Device communication characteristics:
Parameter Min Max
Clock Frequency Sensor Mode 350KHz
10MHz
Clock Frequency Register Mode
50KHz 250KHz
Timeout Sensor Mode 1.5µs 3.5µs
Timeout Register mode 15.5µs 17.5µs
7.6 Examples
All values are hexadecimal.
Set configuration register:
DATA Tx = 06h: set preset, Binary output code,
inverted counting direction.
Function ADR DATA Tx
write register 49 60
save parameters
48 01
Set Preset:
Preset = 01 86 A0h
Function ADR DATA Tx
51 01
52 86write register
53 A0
save and active
Preset 48 02

SMA1
MAN SMA1 E 2.3.doc 7www.lika.it
www.lika.biz
8 -BiSS C-mode interface
SMA1-I7-… standard
SMA1 is a slave device according to “BiSS C-mode
interface” and “Standard encoder profile”.
Refer to the official BiSS website for all information
not listed in this manual (www.biss-interface.org).
The sensor works in point-to-point configuration,
and has to be installed on a “single master, single
slave” network (not on a “single master, multi slave”
network).
CLOCK and DATA signals level are according to the
“EIA standard RS-422”.
8.1 XML file
The product is supplied with XML file
idbiss4C69.xml (see enclosed support or
www.lika.biz > PRODUCTS > LINECOD > SMA1).
Install XML file on BiSS master device.
8.2 Communication
The BiSS C-mode protocol uses two types of data
transmission protocols:
•Single Cycle Data (SCD): is the primary data
transmission protocol. It's used to send process
data from the slave to the master.
•Control Data (CD): transmission of a single bit
following the SCD data. It is used to read or
write data into the registers of the slave.
8.3 Single Cycle Data
SCD (32 bits) is composed by position value, 1 error
bit (nE), 1 warning bit (nW) and CRC checking (6
bits).
SCD structure:
bits 31…8 765…0
function
position error warning
CRC
Position (24 bits)
Process data transmitted from slave to master.
The transmission starts with MSB (most significant
bit) and ends with LSB (less significant bit).
bit 31…28 27 …8
value 0000 MSB …LSB
To see position value in mm, multiply the data value
received for the resolution (see 4Dhex register).
Error (1 bit)
Communicates an error of the slave.
nE = “1”: correct status (no error)
= “0”: error status: tape not read.
Check gap between sensor and tape,
planarity and parallelism of the system.
Warning (1 bit)
Not used (nW = “1”)
CRC (6 bits)
Correct transmission control (inverted output).
Polynomial: X6+X1+1 (binary: 1000011)
Logic circuit:
1st
stage
X1X2X3X5
Input Data (starts from MSB)
X0
2nd
stage
3rd
stage
4th
stage
5th
stage
6th
stage
X4

SMA1
MAN SMA1 E 2.3.doc 8www.lika.it
www.lika.biz
8.4 Control Data CD
See official BiSS documents for complete CD
structure: “Protocol description C-mode”.
Main control data is described in this chapter.
Register address (7 bits)
Specifies the register to read or write.
RW (2 bits)
RW = “01” : write register
RW = “10” : read register
DATA (8 bit)
Write register: value to write into the register
(transmitted from master to slave).
Read register: value read from the register
(transmission from slave to master).
Data bit structure:
bit 7……0
MSB ……LSB
CRC (4 bits)
Correct transmission control (inverted output).
Polynomial: X4+X1+1 (binary: 10011)
Logic circuit:
8.5 Used registers
Register (hex) Function
42…43 Profile ID
44…47 Serial number
48 Command
49 Configuration
4D Absolute resolution
51…53 Preset/ Offset
55 Device type
58 SIN/COS resolution
78…7D Device ID
7E…7F Manufacturer ID
All registers in this chapter are listed according to
the following outline:
Address Function name [access]
Description of the function and default value.
-Address: register address in hexadecimal values.
-Access: ro = read only
rw = read and write
wo = write only
-Default parameter values are written in bold.
42…43 Profile ID [ro]
These registers contain the identification code of
the used profile.
Register 42 43
Hex 28 14
See “Standard encoder profile”, “data format”,
“Variant 0-24”.
44…47 Serial number [ro]
These registers contain the serial number (hex value)
of the device.
reg.44: year of production
reg.45: week of production
reg.46, 47: progressive serial number
1st
stage
2nd
stage 3rd
stage 4th
stage
X0X1X2X3
Input Data (starts from MSB)

SMA1
MAN SMA1 E 2.3.doc 9www.lika.it
www.lika.biz
48 Command [wo]
Value
Function
00 Normal operation
01 Save parameters on EEPROM
02 Save and activate Preset/ Offset
04 Load and save default parameters
This register will set back to "00" automatically.
Wait min. 30ms (EPROM writing time) before using
the next function.
49 Configuration [rw]
Bit Function bit=0 bit=1
0Not used
1Set preset/ offset Preset Offset
2Enable preset/ offset Enable Disable
3Not used
4Not used
5Output code Gray Binary
6Counting direction *
Standard
Inverted
7Not used
*: related to absolute position (not to sin/cos signal)
The new setting will be active immediately after
transmission. Use the function “Save parameters”
(set “01” register 48) to store the new value.
Default = 20h
4D Absolute resolution [rw]
Contains the resolution of absolute sensor.
64hex : Res.=0.1mm (max position = 00 FF FFh)
32hex : Res.=0.05mm (max position = 01 FF FFh)
0Ahex : Res.=0.01mm (max position = 07 FF FFh)
05hex : Res.=0.005mm (max position = 0F FF FFh)
The new setting will be active immediately after
transmission. Use the function “Save parameters”
(set “01” register 48) to store the new value.
After the modification of reg.4D Preset and Offset
values have to be updated according to the new
resolution!
Default = 05h.
51…53 Preset/Offset [rw]
This function has to be enabled by setting reg.49 bit
2 = ”0”. Setting of Preset or Offset register can be
carried out only when the sensor is not moving.
Preset: any desired position value can be set (e.g.
"0", zero setting)
Offset: adds an offset to actual position.
Position = actual position + Offset.
Preset/Offset structure:
Reg.
51 52 53
MSB …LSB
223-2
16 215 -2827-2
0
Use the function “Save and activate Preset/ Offset”
(set “02” register 48) to store and activate the new
value.
The max. allowed Preset values are depending on
the resolution.
resolution = 0.1 àmax preset =00 FF FFh (16bit)
resolution = 0.05 àmax preset =01 FF FFh (17bit)
resolution = 0.01 àmax preset =07 FF FFh (19bit)
resolution = 0.005àmax preset =0F FF FFh (20bit)
Default = 00h.
55 Device type [ro]
Describes the type of device.
Default = 06h: linear encoder BiSS + SIN/COS
58 SIN/COS resolution [ro]
Describes the period of sin/cos signal
Default = 01h: resolution = 1mm
78…7D Device ID [ro]
These registers contain the Device ID.
Reg.
78 79 7A 7B 7C 7D
Hex 53 4D 41 31 xx xx
ASCII
SMA1--
xx: software version
7E…7F Manufacturer ID
These registers contain the Manufacturer ID.
Reg.
7E 7F
Hex 4C 69
ASCII
Li
Li = Lika Electronic.

SMA1
MAN SMA1 E 2.3.doc 10 www.lika.it
www.lika.biz
8.6 Application note
Data transmission:
Parameter Value
Clock Frequency min 200KHz, max 10MHz
BiSS Timeout auto adaptation to clock,
max 16µs
Internal position update
frequency 6KHz
8.7 Examples
All values are hexadecimal.
Set configuration register:
DATA Tx = 06h: set preset, Binary output code,
inverted counting direction.
Function ADR DATA Tx
write register 49 60
save parameters
48 01
Set Preset:
Preset = 01 86 A0h
Function ADR DATA Tx
51 01
52 86
write register
53 A0
save and active
Preset 48 02

SMA1
MAN SMA1 E 2.3.doc 11 www.lika.it
www.lika.biz
9 -1Vpp sine/cosine output signals
The frequency of output signals is proportional to
the displacement speed of the sensor.
A and B signals (standard counting direction)
P is the electrical period length:
P = 1mm
9.1 Output signals voltage level
The voltage level refers to the difference between
normal and inverted signal (differential).
Recommended input circuit:
Sensor Input circuit
VREF = 2,5V ± 0,5V VA= 1Vpp · Av Av = R2/R1
10 -Dimensional drawing
Sensor and tape
11 -Maintenance
The magnetic measurement system doesn't need
any particular maintenance but as with all precision
devices it must be handled with care. From time to
time we recommend the following operations:
•check the gap between sensor and magnetic
tape along the measuring length. Wear of the
machine may increase the tolerances;
•the surface of the magnetic tape should
occasionally be cleaned using a soft cloth to
remove dust, chips, moisture etc.

SMA1
MAN SMA1 E 2.3.doc 12 www.lika.it
www.lika.biz
12 -Troubleshooting
The following list shows some typical errors that
occur during installation and operation of the
magnetic measurement system.
Problem:
The system doesn't work (no pulse output):
•The tape or sensor has been mounted incorrectly
(the active part of the tape doesn't face the
sensor's active side). See chapter 3 for correct
installation. LED is lighted.
•A magnetic piece or tape is in between the
sensor and the tape. Only non-magnetic
materials are allowed between sensor and tape.
LED is lighted.
•The sensor touches the tape because tolerance
gap between sensor and tape are not observed.
Check sensor's active side if damaged.
•The sensor has been damaged by short circuit or
wrong connection.
Problem:
The measured values are inaccurate or not present
at some positions:
•The gap between sensor and tape is not
observed along the total measurement length
(see chap. 4) or the sensor is not mounted
correctly to the tape (see chap. 3).
LED is lighted.
•The connection cable runs near to high voltage
cables or the shield is not connected correctly.
•The frequency of your clock is set too high or
too low and the sensor cannot synchronize
correctly (see chap. 6).
•A section of the magnetic tape has been
damage mechanically or magnetically along the
measuring length.
•The measuring error is caused by torsion of the
machine structure. Check parallelism and
symmetry of machine movement.
Rev. Man.Vers. Description
01.0 1^ issue
11.1 Add CRC calculations (chap.6.1.5)
“Operating parameters”: default=0
21.2 Chap.5 update
02.0 SW update
12.1 Add SSI interface
Electrical connections (chap.5) update
22.2 Note about MCD bit (chap.7.3)
32.3 Chap.6 update
Lika Electronic
Via S. Lorenzo, 25 -36010 Carrè (VI) -Italy
Tel. +39 0445 382814
Fax +39 0445 382797
Other manuals for SMA1 Series
2
Table of contents
Popular Security Sensor manuals by other brands
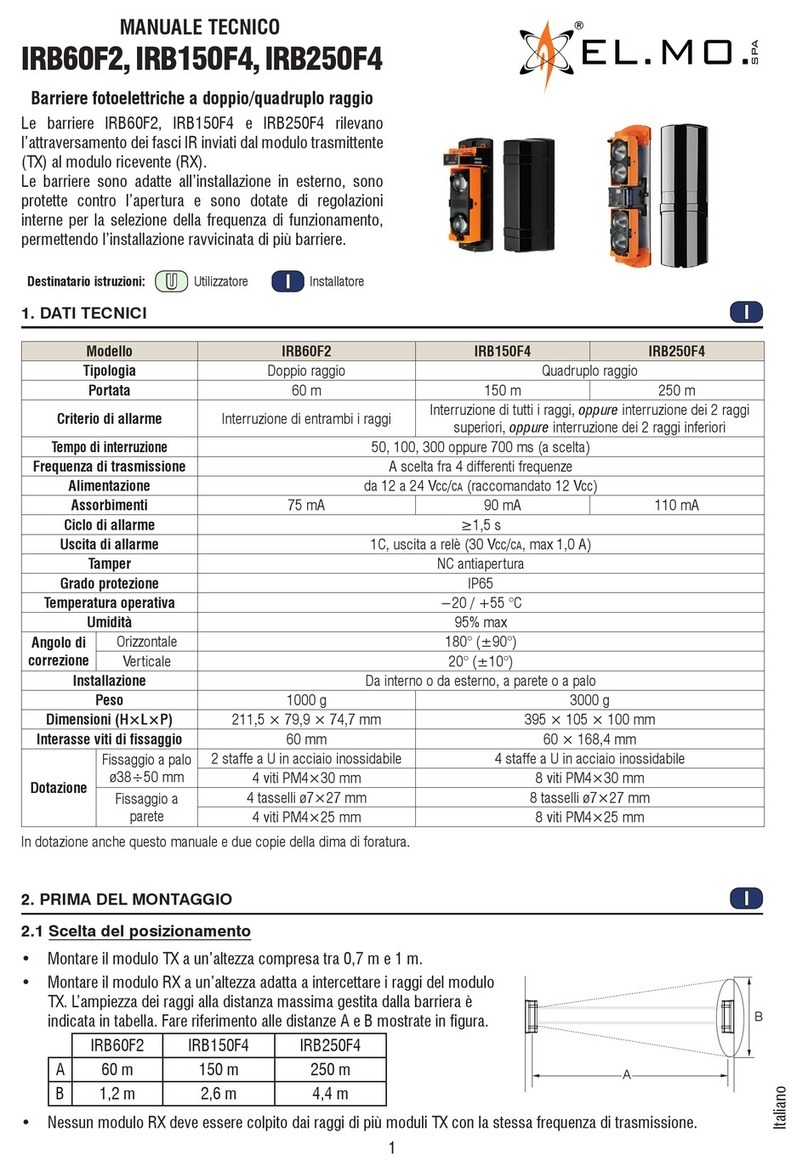
Elmo
Elmo IRB250F4 Technical manual
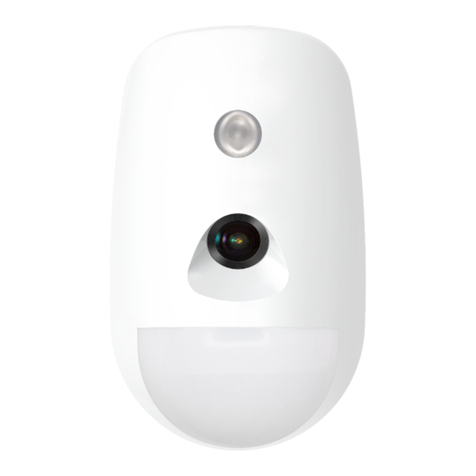
HIK VISION
HIK VISION DS-PDPC12P-EG2-WE quick start guide

C.P. Electronics
C.P. Electronics MWS6-PRM-2CH-NC installation guide
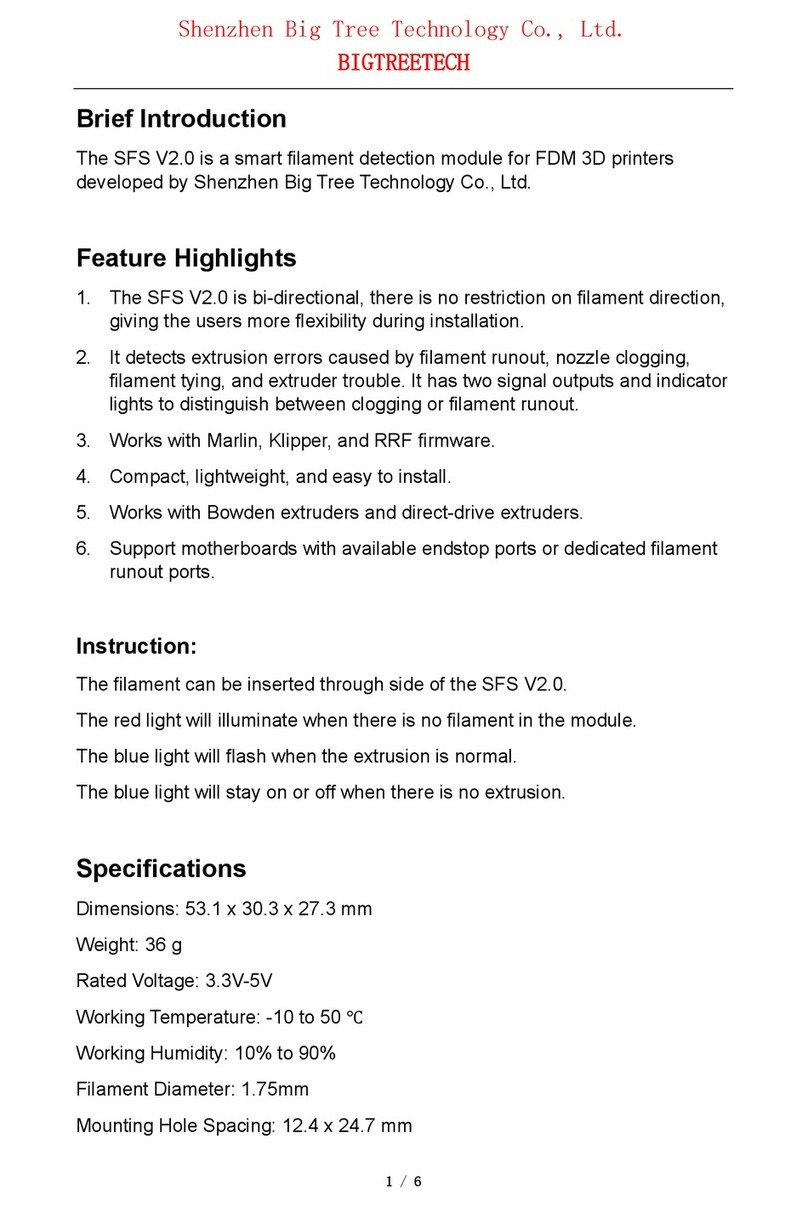
BIG TREE TECH
BIG TREE TECH SFS V2.0 manual
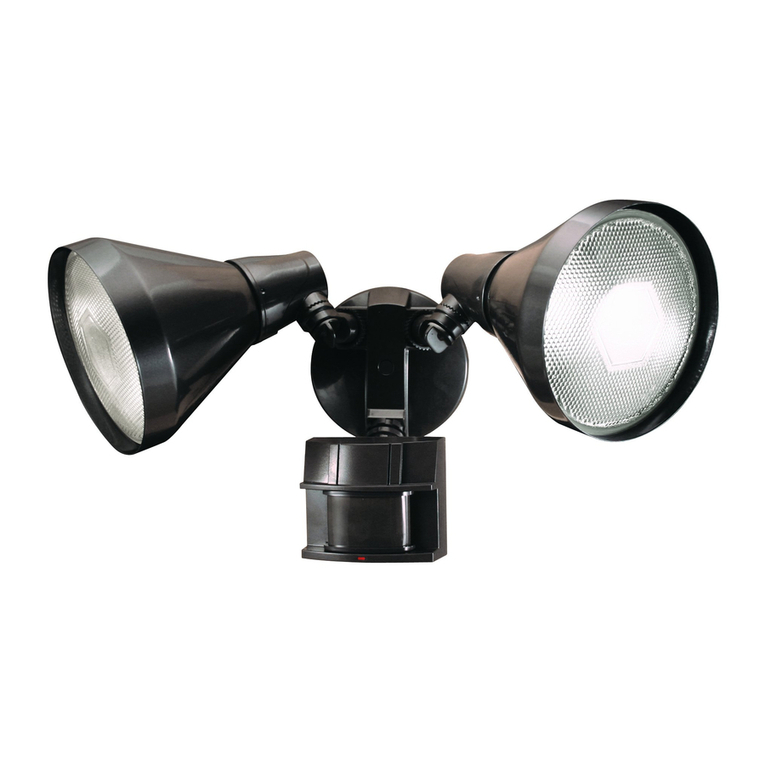
Heath Zenith
Heath Zenith 5412 user manual
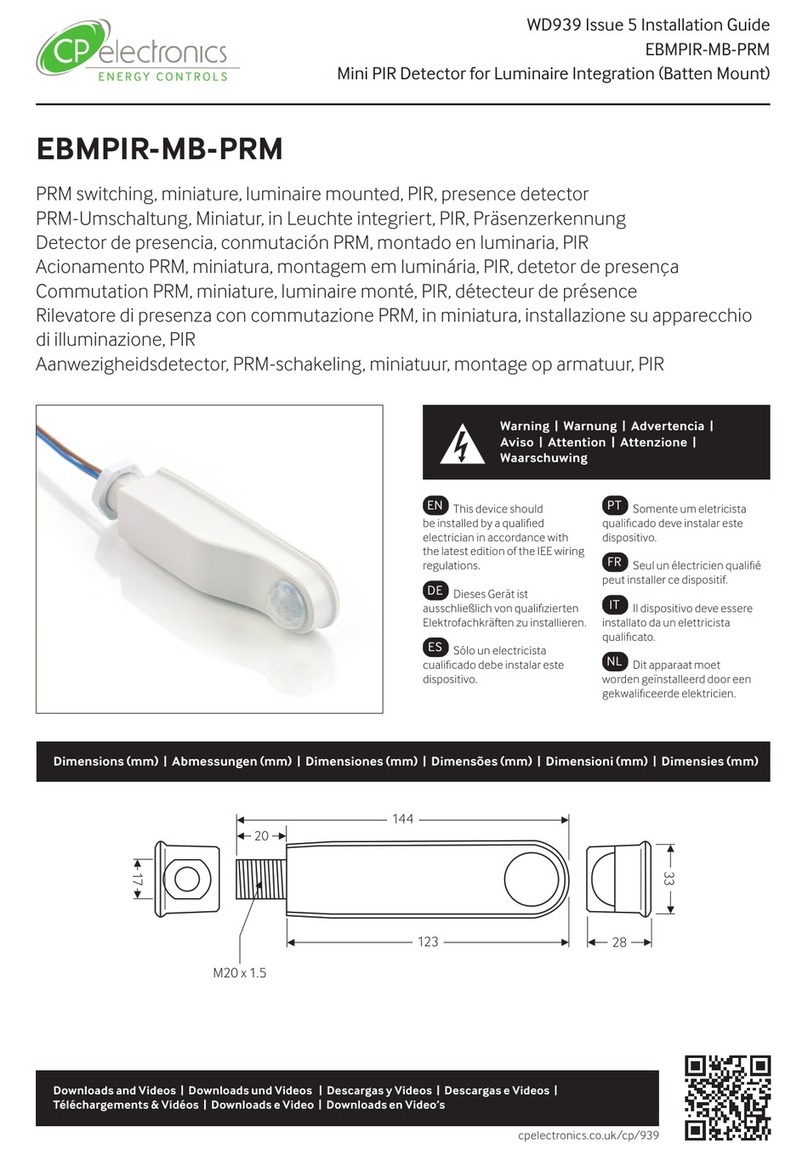
C.P. Electronics
C.P. Electronics EBMPIR-MB-PRM installation guide

Green Brook
Green Brook Orion OD104 quick start guide
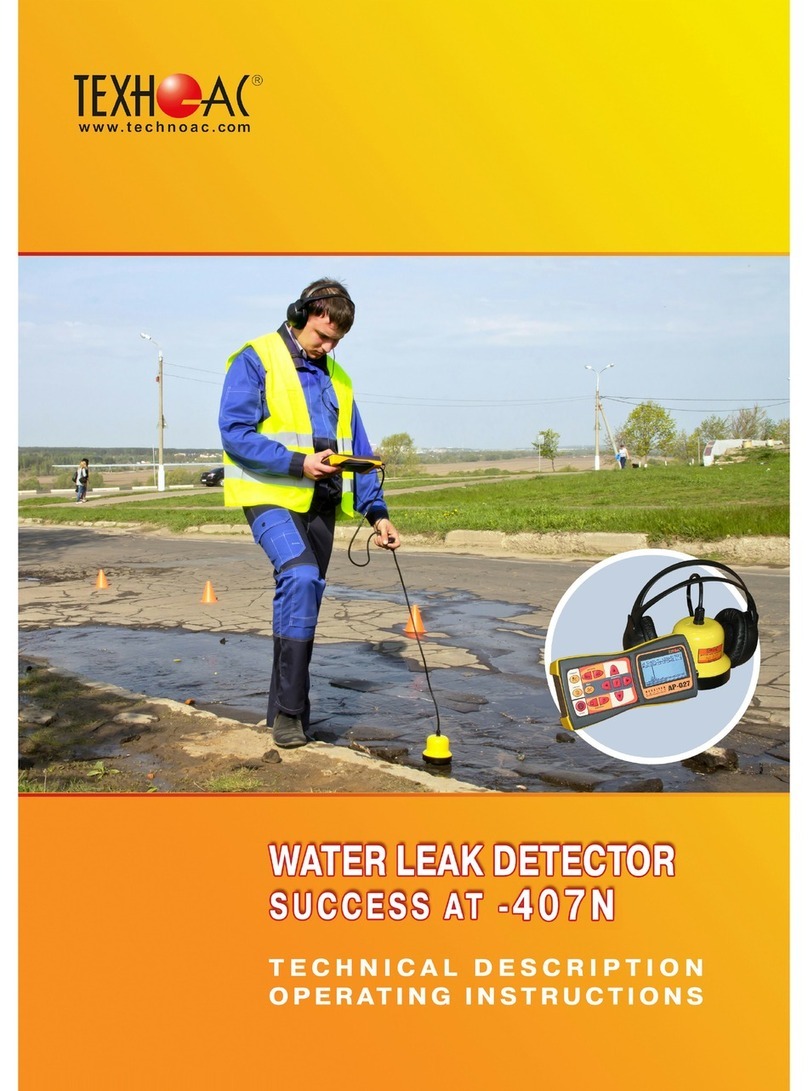
TECHNO-AC
TECHNO-AC Success AT-407N Technical description and operation instructions
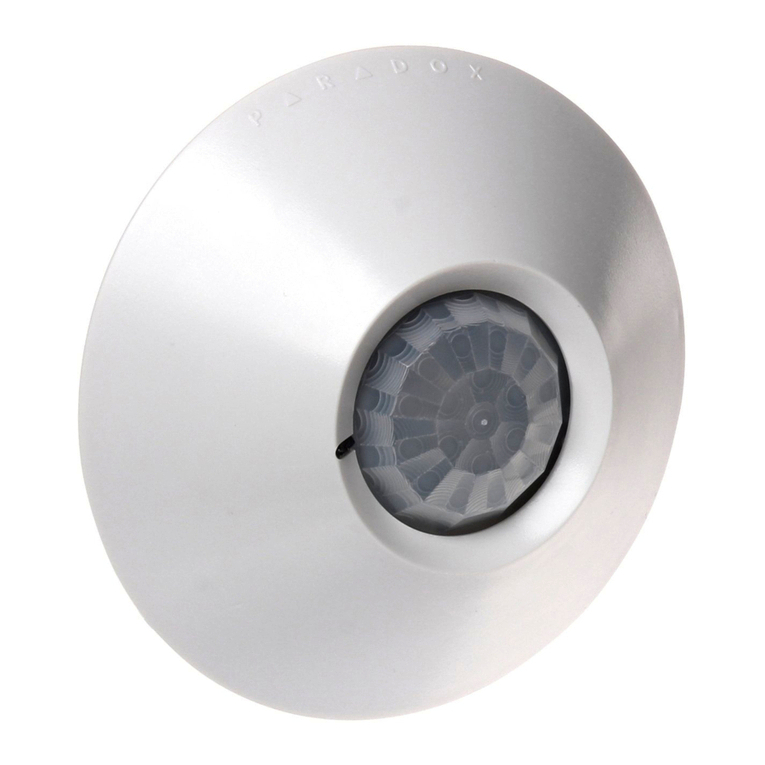
Paradox
Paradox Paradome DG467 user manual
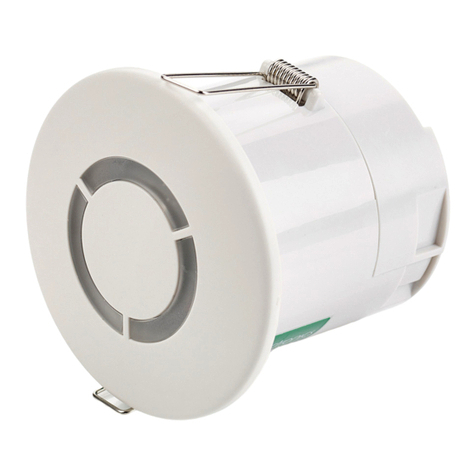
C.P. Electronics
C.P. Electronics MWS6-PRM-VFC-NC installation guide

TESTO
TESTO 316i instruction manual

hyfire
hyfire YAURUS TAU-OP-01-BL quick start guide