LMI Gocator 200 Series User manual

USER MANUAL
Gocator Multi-Point Scanners
Gocator 205, 210, 230 &250
Firmware version:5.1.x.xx
Document revision:A

Gocator Multi-Point Scanners: User Manual 2
Copyright
Copyright © 2020 by LMI Technologies, Inc. All rights reserved.
Proprietary
This document, submitted in confidence, contains proprietary information which shall not be
reproduced or transferred to other documents or disclosed to others or used for manufacturing or any
other purpose without prior written permission of LMI Technologies Inc.
No part of this publication may be copied, photocopied, reproduced, transmitted, transcribed, or
reduced to any electronic medium or machine readable form without prior written consent of LMI
Technologies, Inc.
Trademarks and Restrictions
Gocator™ is a registered trademark of LMI Technologies, Inc. Any other company or product names
mentioned herein may be trademarks of their respective owners.
Information contained within this manual is subject to change.
This product is designated for use solely as a component and as such it does not comply with the
standards relating to laser products specified in U.S. FDA CFR Title 21 Part 1040.
Contact Information
LMI Technologies, Inc.
9200 Glenlyon Parkway
Burnaby BCV5J 5J8
Canada
Telephone: +1 604-636-1011
Fax: +1 604-516-8368
www.lmi3D.com

Gocator Multi-Point Scanners: User Manual 3
Table of Contents
Copyright 2
Table of Contents 3
Introduction 9
Gocator 200 Series Overview 10
True Differential Measurement 11
High Scan Rates 12
Temperature-Compensated Ranges 12
Tracheids 13
Migrating from chroma+scan 14
Safety and Maintenance 17
Laser Safety 17
Laser Classes 18
Precautions and Responsibilities 18
Class 3B Responsibilities 19
Systems Sold or Used in the USA 20
Electrical Safety 20
Handling, Cleaning, and Maintenance 21
Environment and Lighting 21
Getting Started 23
Hardware Overview 24
Gocator Cordsets 24
Gocator Sensor 25
Gocator Color Vision Module 26
Gocator Light Bar 26
Master 100 27
Master 810 / 2410 28
System Overview 29
Standalone System 29
Multi-Sensor System 30
Installation 32
Mounting 32
Scanners 32
Camera Module and Light Bars 33
Assembling a Sensor +Camera +Light Bar
System 33
Frame Design 34
Gocator 230/250 34
Gocator 210 35
Grounding 36
Gocator 36
Recommended Practices for Cordsets 36
Master Network Controllers 37
Grounding When Using a DIN Rail (Master
810/2410) 38
Additional Grounding Schemes 38
Installing DIN Rail Clips: Master 810 or 2410 38
Configuring Master 810 40
Setting the Divider 41
Encoder Quadrature Frequency 41
Setting the Debounce Period 42
Preparing the Alignment Bar 42
Network Setup 44
Client Setup 44
Gocator Setup 46
Running a Standalone Sensor System 46
Running a Multi-Sensor System 47
How Gocator Works 48
3D Acquisition 48
Clearance Distance, Field of Viewand
Measurement Range 48
Resolution and Accuracy 49
X Resolution 50
Z Resolution 50
Profile Output 51
Coordinate Systems 51
Sensor Coordinates 51
Gocator Web Interface 52
Browser Compatibility 52
Internet Explorer 11 Issues 52
Internet Explorer Switches to Software
Rendering 52
Internet Explorer Displays "Out of Memory" 52
User Interface Overview 54
Toolbar 55
Creating, Saving and Loading Jobs (Settings) 55
Recording, Playback, and Measurement
Simulation 57
Recording Filtering 59
Downloading, Uploading, and Exporting
Replay Data 60
Metrics Area 62
Data Viewer 63
Status Bar 63

Gocator Multi-Point Scanners: User Manual 4
Log 63
Frame Information 63
Quick Edit Mode 64
Interface Language 64
Management and Maintenance 66
Manage Page Overview 66
Sensor System 67
Sensor Autostart 67
Layout 67
Networking 68
Motion and Alignment 69
Alignment Reference 70
Encoder Resolution 70
Encoder Value and Frequency 71
Travel Speed 71
Jobs 71
Security 73
Maintenance 74
Sensor Backups and Factory Reset 75
Firmware Upgrade 76
Support 77
Support Files 77
Manual Access 78
Software Development Kit 78
Scan Setup and Alignment 80
Scan Page Overview 80
Scan Modes 81
Triggers 81
Trigger Examples 82
Trigger Settings 83
Maximum Encoder Rate 84
Sensor 84
Active Area 85
Transformations 86
Exposure 87
Single Exposure 88
Spacing 88
Sub-Sampling 89
Advanced 89
Material 90
Camera Gain 90
Tracheid 91
Data Viewer 92
Data Viewer Controls 92
Video Mode 93
Exposure Information 93
Overexposure and Underexposure 93
Profile Mode 95
Region Definition 96
Measurement and Processing 98
Measure Page Overview 98
Data Viewer 99
Tools Panel 99
Adding and Configuring a Measurement
Tool 99
Source 100
Regions 100
Feature Points 100
Fit Lines 103
Decisions 103
Filters 104
Measurement Anchoring 105
Enabling and Disabling Measurements 106
Editing Tool, Input, or Output Names 106
Changing a Measurement ID 107
Duplicating a Tool 107
Removing a Tool 108
Reordering Tools 108
Profile Measurement 108
Dimension 109
Position 112
Measurements and Settings 113
Script 115
Scripts 115
Built-in Script Functions 116
Output 120
Output Page Overview 120
Ethernet Output 121
Digital Output 125
Analog Output 127
Serial Output 128
Dashboard 130
Dashboard Page Overview 130
State and Health Information 130

Gocator Multi-Point Scanners: User Manual 5
Gocator Emulator 132
System Requirements 132
Limitations 132
Downloading a Support File from a Sensor 132
Running the Emulator 133
Adding a Scenario to the Emulator 134
Running a Scenario 135
Removing a Scenario from the Emulator 135
Using Replay Protection 135
Stopping and Restarting the Emulator 136
Running the Emulator in Default Browser 136
Working with Jobs and Data 137
Creating, Saving, and Loading Jobs 137
Playback and Measurement Simulation 138
Downloading, Uploading, and Exporting
Replay Data 139
Downloading and Uploading Jobs 141
Scan, Model, and Measurement Settings 143
Calculating Potential Maximum Frame Rate 143
Protocol Output 144
Remote Operation 144
Gocator Device Files 146
Live Files 146
Log File 147
Job File Structure 147
Job File Components 148
Accessing Files and Components 148
Configuration 148
Setup 149
Filters 150
XSmoothing 150
YSmoothing 150
XGapFilling 151
YGapFilling 151
XMedian 151
YMedian 151
XDecimation 152
YDecimation 152
XSlope 152
YSlope 152
Trigger 153
Layout 154
Alignment 155
Disk 156
Bar 156
Plate 157
Polygon 157
Polygon/Corner 157
Devices / Device 158
SurfaceGeneration 163
FixedLength 164
VariableLength 164
Rotational 164
SurfaceSections 165
ProfileGeneration 165
FixedLength 166
VariableLength 166
Rotational 166
PartDetection 166
EdgeFiltering 168
PartMatching 168
Edge 168
BoundingBox 168
Ellipse 169
Replay 170
RecordingFiltering 170
Conditions/AnyMeasurement 170
Conditions/AnyData 171
Conditions/Measurement 171
Streams/Stream (Read-only) 171
ToolOptions 172
MeasurementOptions 173
FeatureOptions 173
StreamOptions 174
Tools 174
Profile Types 174
ProfileFeature 174
ProfileLine 175
ProfileRegion2d 175
Geometric Feature Types 175
Parameter Types 175
ProfileArea 177
ProfileBoundingBox 179
ProfileCircle 181

Gocator Multi-Point Scanners: User Manual 6
ProfileDimension 182
ProfileGroove 184
ProfileIntersect 186
ProfileLine 188
ProfilePanel 190
ProfilePosition 192
ProfileRoundCorner 194
ProfileStrip 196
Script 198
Tool (type FeatureDimension) 199
Tool (type FeatureIntersect) 200
Custom 202
Output 203
Ethernet 203
Ascii 205
EIP 206
Modbus 206
Digital0 and Digital1 206
Analog 207
Serial 208
Selcom 208
Ascii 209
Transform 209
Device 210
Protocols 212
Gocator Protocol 212
Data Types 213
Commands 213
Discovery Commands 214
Get Address 214
Set Address 215
Get Info 216
Control Commands 217
Protocol Version 218
Get Address 218
Set Address 219
Get System Info V2 219
Get System Info 221
Get States 222
Log In/Out 223
Change Password 224
Set Buddy 224
List Files 225
Copy File 225
Read File 226
Write File 226
Delete File 227
User Storage Used 227
User Storage Free 228
Get Default Job 228
Set Default Job 228
Get Loaded Job 229
Get Alignment Reference 229
Set Alignment Reference 230
Clear Alignment 230
Get Timestamp 231
Get Encoder 231
Reset Encoder 231
Start 232
Scheduled Start 232
Stop 233
Get Auto Start Enabled 233
Set Auto Start Enabled 233
Start Alignment 234
Start Exposure Auto-set 234
Software Trigger 235
Schedule Digital Output 235
Schedule Analog Output 236
Ping 236
Reset 237
Backup 237
Restore 238
Restore Factory 238
Get Recording Enabled 239
Set Recording Enabled 239
Clear Replay Data 239
Get Playback Source 240
Set Playback Source 240
Simulate 241
Seek Playback 241
Step Playback 241
Playback Position 242
Clear Measurement Stats 242
Read Live Log 243

Gocator Multi-Point Scanners: User Manual 7
Clear Log 243
Simulate Unaligned 243
Acquire 244
Acquire Unaligned 244
Create Model 245
Detect Edges 245
Add Tool 245
Add Measurement 246
Read File (Progressive) 246
Export CSV (Progressive) 247
Export Bitmap (Progressive) 248
Get Runtime Variable Count 249
Set Runtime Variables 249
GetRuntimeVariables 250
Upgrade Commands 250
Start Upgrade 250
Start Upgrade Extended 251
Get Upgrade Status 251
Get Upgrade Log 252
Results 252
Health Results 252
Data Results 257
Stamp 258
Video 259
Measurement 259
Alignment Result 260
Exposure Calibration Result 261
Event 261
Tracheid 261
Feature Point 262
Feature Line 262
Feature Plane 263
Modbus Protocol 264
Concepts 264
Messages 264
Registers 265
Control Registers 266
Output Registers 267
State 267
Stamp 268
Measurement Registers 269
EtherNet/IP Protocol 271
Explicit Messaging 271
Identity Object (Class 0x01) 272
TCP/IP Object (Class 0xF5) 272
Ethernet Link Object (Class 0xF6) 272
Assembly Object (Class 0x04) 273
Command Assembly 273
Runtime Variable Configuration
Assembly 274
Sensor State Assembly 274
Sample State Assembly 276
Implicit Messaging 277
Assembly Object (Class 0x04) 277
Implicit Messaging Command Assembly 278
Implicit Messaging Output Assembly 279
ASCIIProtocol 280
Connection Settings 281
Ethernet Communication 281
Serial Communication 281
Polling Operation Commands (Ethernet Only) 281
Command and Reply Format 282
Special Characters 282
Command Channel 283
Start 283
Stop 283
Trigger 284
LoadJob 284
Stamp 284
Stationary Alignment 285
Clear Alignment 285
Set Runtime Variables 285
Get Runtime Variables 286
Data Channel 286
Result 286
Value 287
Decision 288
Health Channel 288
Health 288
Standard Result Format 289
Custom Result Format 290
Selcom Protocol 291
Serial Communication 291
Connection Settings 291

Gocator Multi-Point Scanners: User Manual 8
Message Format 291
Development Kits 293
GoSDK and GoWebScanSDK 293
Setup and Locations 293
Class Reference 293
Examples 293
Header Files 293
Data Types 293
Value Types 294
Output Types 294
GoDataSet Type 295
MeasurementValues and Decisions 295
Limiting Flash Memory Write Operations 296
GoSDK 296
FunctionalHierarchy of Classes 297
GoSystem 298
GoSensor 298
GoSetup 298
GoLayout 298
GoTools 299
GoTransform 299
GoOutput 299
Operation Workflow 299
Initialize GoSdk APIObject 300
Discover Sensors 300
Connect Sensors 300
Configure Sensors 300
Enable Data Channels 301
Perform Operations 301
GoWebScanSDK 302
Main Classes 303
GoWebScanSettings 303
GoWebScanConfig 303
GoWebScanProcess 304
GoWebScanSystemMsg and the Message
Classes It Contains 304
Sample Application 304
Settings.xml File 304
Setup 305
Sampling 307
Detection 308
Calibration 309
Members / SensorGroup 309
Tools and Native Drivers 311
Sensor Discovery Tool 311
CSV Converter Tool 312
Troubleshooting 314
Specifications 315
Scanners 315
Gocator 200 Series 315
Gocator 205 (Color Vision Module) 316
Gocator 210 318
Gocator 230 / 250 322
Sensor Connectors 326
Gocator Power/LAN Connector 326
Grounding Shield 327
Power 327
Safety Input 327
Gocator I/O Connector 328
Grounding Shield 328
Digital Outputs 328
Inverting Outputs 329
Digital Input 329
Encoder Input 330
Serial Output 331
Analog Output 331
Light Bars 332
LB200 / LB210 332
Master Network Controllers 334
Master 100 334
Master 100 Dimensions 335
Master 810/2410 336
Electrical Specifications 338
Encoder 339
Input 341
Master 810 Dimensions 343
Master 2410 Dimensions 344
Accessories 345
Return Policy 347
Software Licenses 348
Support 353
Contact 354

Gocator Multi-Point Scanners: User Manual 9
Introduction
This documentation describes how to connect, configure, and use a Gocator. It also contains reference
information on the device's protocols and job files, as well as an overview of the development kits you
can use with Gocator. Finally, the documentation describes the Gocator emulator.
The documentation applies to the following:
lGocator 200 series
Notational Conventions
This documentation uses the following notational conventions:
Follow these safety guidelines to avoid potential injury or property damage.
Consider this information in order to make best use of the product.

Gocator Multi-Point Scanners: User Manual 10
Gocator 200 Series Overview
The Gocator 200 series of scanners lets you build scanning systems using a modular design that allows
you to mix 3D profiles, tracheid detection, and color vision. Gocator 200 series systems can be used to
perform automatic wood-grading in machine centers found in saw and planer mills. The Gocator 200
series is designed for transverse board scanning.
Gocator 200 series system scanning board
Typically, you will use the two provided software development kits to implement system configuration
and data processing: GoSDKand GoWebScanSDK.
lGoSDK: Provides lower level device control and communication functions.
lGoWebScanSDK: Provides a library of common functions found in wood-scanning applications and
returns complete board data.
Measurements performed on the returned data are user-implemented, which gives you maximum
flexibility in system design. For more information on the development kits, see GoSDK and
GoWebScanSDK on page293.
Testing of settings on individual devices during initial setup, as well as troubleshooting and system
monitoring, can be performed using the built-in web interface (for more information, see Gocator Web
Interface on page52.)
The built-in measurement tools are not intended for wood applications.

Gocator Multi-Point Scanners: User Manual Gocator 200 Series Overview • 11
Gocator 210, 230, and 250
Gocator 210, 230, and 250 scanners are multi-point laser devices that return profiles of material passing
beneath them.
Gocator 250 scanners can also be used to measure the tracheid effect in boards. For more information,
see Tracheids on page13.
Gocator 205
Gocator 205 is a bolt-on color vision module that supports the detection and measurement of surface
defects such as knots, splits, and rot. Measurement of their size and location is key to grade-based
recovery optimization. It is used in conjunction with one or two strobed white light LED light bars that
provide efficient and effective illumination. This provides a simple and reliable method of capturing
features on material surfaces along the length of the system.
True Differential Measurement
Gocator 200 series scanners can be aligned co-planar top-to-bottom and side-to-side down the length of
the system to provide large-scale differential measurement. This prevents profile measurement errors
that could be introduced by hard-to-control mechanical issues such as chain vibration and material
bouncing as it is transported through the scanner system.

Gocator Multi-Point Scanners: User Manual Gocator 200 Series Overview • 12
Gocator 200 series system scanning board - Top and bottom system
High Scan Rates
Gocator 200 series multi-point scanners provide high profile scan rates yet at the same time maintain
excellent dark wood performance (equivalent to level 19 on the Kodak gray scale chart), insensitivity to
laser saturation, and immunity to ambient light.
For more information at model-dependent speeds and resolutions (for more information, see Scanners
on page315).
Temperature-Compensated Ranges
Gocator 200 series scanners are calibrated at several temperature points in their operational range to
ensure reliable and accurate range measurement throughout changes in ambient temperature.

Gocator Multi-Point Scanners: User Manual Gocator 200 Series Overview • 13
Tracheids
When a laser spot is projected onto healthy tracheid wood cells, laser light is scattered into the cells in the
direction of cell growth. If the wood fiber is dead (as in a knot), the laser light does not scatter. This effect
is measured via GoSDKby fitting an ellipse to the laser spot, which is nominally circular in the absence of
any tracheid effect. The following information based on the ellipse fit is available:
lAngle of the major axis of the ellipse
lArea of the ellipse
lLength of the major axis of the ellipse
lLength of the minor axis of the ellipse
lScatter, defined as the ratio of the major and minor axis

Gocator Multi-Point Scanners: User Manual 14
Migrating from chroma+scan
Gocator 200 series multi-point sensors can be used to implement the same kinds of transverse wood-
processing systems possible with chroma+scan scanners. In general, specifications for the physical setup
(for example, mounting and frame design) of systems based on Gocator 200 series sensors are the
same. Furthermore, clearance distances and measurement ranges are equivalent to chroma+scan
scanners. Resolution and speed are the same if not better than the corresponding chroma+scan
scanners.
However, the hardware and software architecture has changed to give system developers full, low-level
control of system functionality. The following table gives a brief overview of the differences between
chroma+scan systems and systems based on Gocator 200 series sensors:
chroma+scan Gocator 200 series
Client PC with...
Client application written using Zen API and
FireSync Host Protocol (OR provided kClient
application)
User-written application developed
using GoSDK and GoWebScanSDK
Station PC with...
Proprietary, closed source Station services;
OS-dependent Ethernet drivers
Station PCnot required:Station
services provided by GoWebScanSDK
The main difference is that systems developed using Gocator 200 series sensors no longer require
Station PCs, which ran Station services. The functionality provided by the closed source Station services
is now accessed in GoWebScanSDK, which, along with the base GoSDK, is used to write a client
application to control and run a system based on Gocator 200 series scanners. Source code is provided
for both SDKs.
For initial system setup, you can use the Gocator web interface for troubleshooting and to quickly view
data from individual scanners. For more information on this interface, see Gocator Web Interface on
page52.
The following table lists the main tasks and processes that must be implemented using GoWebScanSDK
or GoSDK. Note that most tasks and process listed under the GoWebScanSDK column can be
implemented using the lower level GoSDK. GoWebScanSDK simply provides classes useful for typical
wood scanning applications, which greatly reduces development time.
Task GoSDK GoWebScanSDK Gocator Web
Interface
Misc

Gocator Multi-Point Scanners: User Manual Migrating from chroma+scan • 15
Task GoSDK GoWebScanSDK Gocator Web
Interface
Initial test setup of
individual sensors
X
Troubleshooting and
monitoring of live laser
profile data from a single
sensor
X
chroma+scan client Sensor enumeration and
assignment
X
Modes of operation X
Sensor upgrade logic X
Sensor and system health X
System, group, sensor
setup
X
Start/stop X
Station services
System architecture
mapping
X
Sensor synchronization
(time or encoder mode)
X
Top/bottom staggering X
Data storage structures X
System alignment (for
information on alignment
target specifications, see
Preparing the Alignment Bar
on page42)
X
Data acquisition and
transfer to data processor
(GoWebScan)
X
Profile Merging (between
sensors)
X
Tracheid processing and
merging (tracheid map )
X
Profile processing X
Vision processing X
Tracheid processing X

Gocator Multi-Point Scanners: User Manual Migrating from chroma+scan • 16
Task GoSDK GoWebScanSDK Gocator Web
Interface
Vision & Profile merging
(between Gocator 205 and
Gocator 210/230/250)
X
Board state machine X
Board / target detection
logic
X
Edge filtering X
White balance X
Bayer decoding X
X and Y resampling X
Resampling color pixel to
match height of board
X
Event channel X
Board post-processing
(spike filtering, gap filling
and blending)
X
Sensor multiplexing X
Retrieve digital model of
scanned object from
GoWebScanSDK.
X
For more information on GoWebScanSDK, see GoWebScanSDK on page302.

Gocator Multi-Point Scanners: User Manual 17
Safety and Maintenance
The following sections describe the safe use and maintenance of Gocator sensors.
Laser Safety
Gocator sensors contain semiconductor lasers that emit visible or invisible light and are designated as
Class 2, 2M, Class 3R, or Class 3B, depending on the chosen laser option. For more information on the
laser classes used in Gocator sensors, Laser Classes on the next page.
Gocator sensors are referred to as components, indicating that they are sold only to qualified customers
for incorporation into their own equipment. These sensors do not incorporate safety items that the
customer may be required to provide in their own equipment (e.g., remote interlocks, key control; refer
to the references below for detailed information). As such, these sensors do not fully comply with the
standards relating to laser products specified in IEC 60825-1 and FDA CFR Title 21 Part 1040.
Use of controls or adjustments or performance of procedures other than those specified herein
may result in hazardous radiation exposure.
References
1. International standard IEC 60825-1 (2001-08) consolidated edition, Safety of laser products – Part 1:
Equipment classification, requirements and user's guide.
2. Technical report 60825-10, Safety of laser products – Part 10. Application guidelines and explanatory
notes to IEC 60825-1.

Gocator Multi-Point Scanners: User Manual Safety and Maintenance • 18
3. Laser Notice No. 50, FDA and CDRH (https://www.fda.gov/Radiation-Emit-
tingProducts/ElectronicProductRadiationControlProgram/default.htm)
Laser Classes
Class 3B laser components
Class 3B components are unsafe for eye exposure.
lUsually only eye protection is required. Protective gloves may also be used.
lDiffuse reflections are safe if viewed for less than 10 seconds at a minimum distance of 13 cm.
lThere is a risk of fire if the beam encounters flammable materials.
lThe laser area must be clearly identified.
lUse a key switch or other mechanism to prevent unauthorized use.
lUse a clearly visible indicator to show that a laser is in use, such as “Laser in operation.”
lRestrict the laser beam to the working area.
lEnsure that there are no reflective surfaces in the working area.
Labels reprinted here are examples only. For accurate specifications, refer to the label on your
sensor.
For more information, see Precautions and Responsibilities below.
Precautions and Responsibilities
Precautions specified in IEC 60825-1 and FDA CFR Title 21 Part 1040 are as follows:
Requirement Class 3B
Remote interlock Required*
Key control Required – cannot remove
key when in use*
Power-on delays Required*
Beam attenuator Required*
Emission indicator Required*
Warning signs Required*
Beam path Terminate beam at useful
length
Specular reflection Prevent unintentional
reflections
Eye protection Required under special
conditions
Laser safety officer Required

Gocator Multi-Point Scanners: User Manual Safety and Maintenance • 19
Requirement Class 3B
Training Required for operator and
maintenance personnel
*LMI Class 3B laser components do not incorporate these laser safety items. These items must be added and completed by customers
in their system design. For more information, see Class 3B Responsibilities below.
Class 3B Responsibilities
LMI Technologies has filed reports with the FDA to assist customers in achieving certification of laser
products. These reports can be referenced by an accession number, provided upon request. Detailed
descriptions of the safety items that must be added to the system design are listed below.
Remote Interlock
A remote interlock connection must be present in Class 3B laser systems. This permits remote switches
to be attached in serial with the keylock switch on the controls. The deactivation of any remote switches
must prevent power from being supplied to any lasers.
Key Control
A key operated master control to the lasers is required that prevents any power from being supplied to
the lasers while in the OFF position. The key can be removed in the OFF position but the switch must not
allow the key to be removed from the lock while in the ON position.
Power-On Delays
A delay circuit is required that illuminates warning indicators for a short period of time before supplying
power to the lasers.
Beam Attenuators
A permanently attached method of preventing human access to laser radiation other than switches,
power connectors or key control must be employed.
Emission Indicator
It is required that the controls that operate the sensors incorporate a visible or audible indicator when
power is applied and the lasers are operating. If the distance between the sensor and controls is more
than 2 meters, or mounting of sensors intervenes with observation of these indicators, then a second
power-on indicator should be mounted at some readily-observable position. When mounting the
warning indicators, it is important not to mount them in a location that would require human exposure
to the laser emissions. User must ensure that the emission indicator, if supplied by OEM, is visible when
viewed through protective eyewear.
Warning Signs
Laser warning signs must be located in the vicinity of the sensor such that they will be readily observed.
Examples of laser warning signs are as follows:

Gocator Multi-Point Scanners: User Manual Safety and Maintenance • 20
FDA warning sign example IEC warning sign example
Systems Sold or Used in the USA
Systems that incorporate laser components or laser products manufactured by LMI Technologies
require certification by the FDA.
Customers are responsible for achieving and maintaining this certification.
Customers are advised to obtain the information booklet Regulations for the Administration and
Enforcement of the Radiation Control for Health and Safety Act of 1968: HHS Publication FDA 88-8035.
This publication, containing the full details of laser safety requirements, can be obtained directly from
the FDA, or downloaded from their web site at https://www.fda.gov/Radiation-
EmittingProducts/ElectronicProductRadiationControlProgram/default.htm.
Electrical Safety
Failure to follow the guidelines described in this section may result in electrical shock or
equipment damage.
Sensors should be connected to earth ground
All sensors should be connected to earth ground through their housing. All sensors should be mounted
on an earth grounded frame using electrically conductive hardware to ensure the housing of the sensor
is connected to earth ground. Use a multi-meter to check the continuity between the sensor connector
and earth ground to ensure a proper connection.
Minimize voltage potential between system ground and sensor ground
Care should be taken to minimize the voltage potential between system ground (ground reference for
I/O signals) and sensor ground. This voltage potential can be determined by measuring the voltage
between Analog_out- and system ground. The maximum permissible voltage potential is 12 V but should
be kept below 10 V to avoid damage to the serial and encoder connections.
Use a suitable power supply
The power supply used with sensors should be an isolated supply with inrush current protection or be
able to handle a high capacitive load. Verify the voltage input requirements for your sensor in the
sensor's specifications; for specifications, see Scanners on page315
This manual suits for next models
4
Table of contents
Other LMI Scanner manuals
Popular Scanner manuals by other brands

Canon
Canon imageFORMULA DR-G1100 Production Document... Service guide
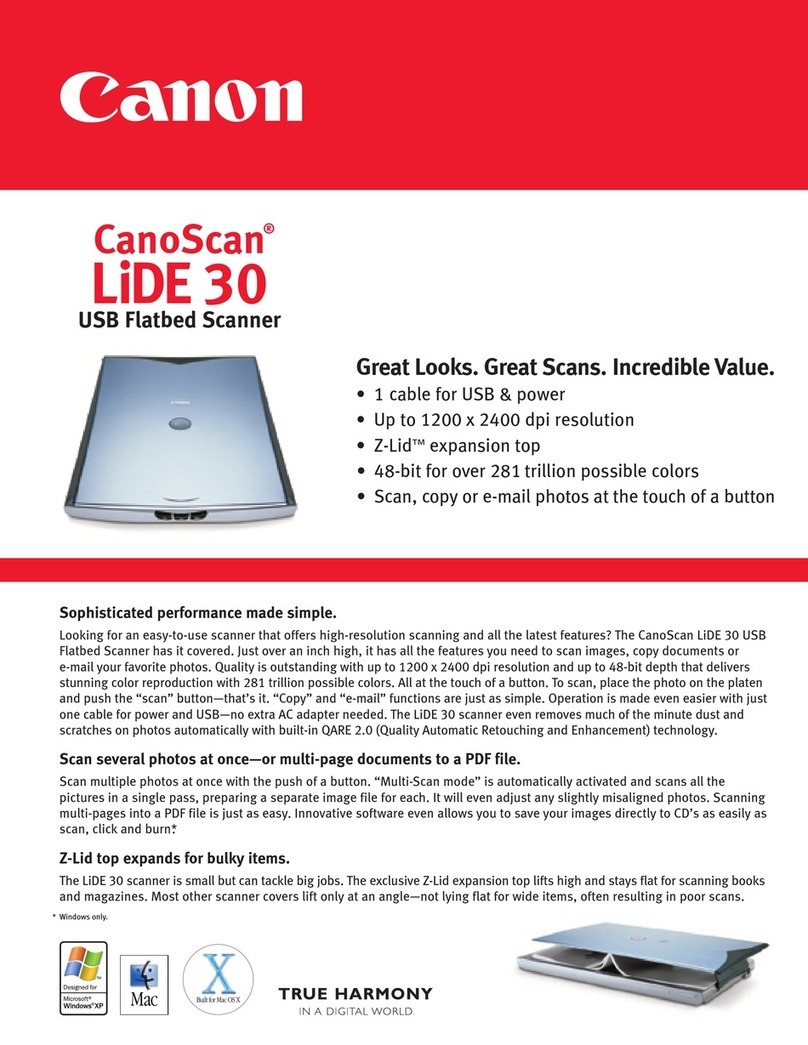
Canon
Canon CanoScan LiDE 30 Specification sheet
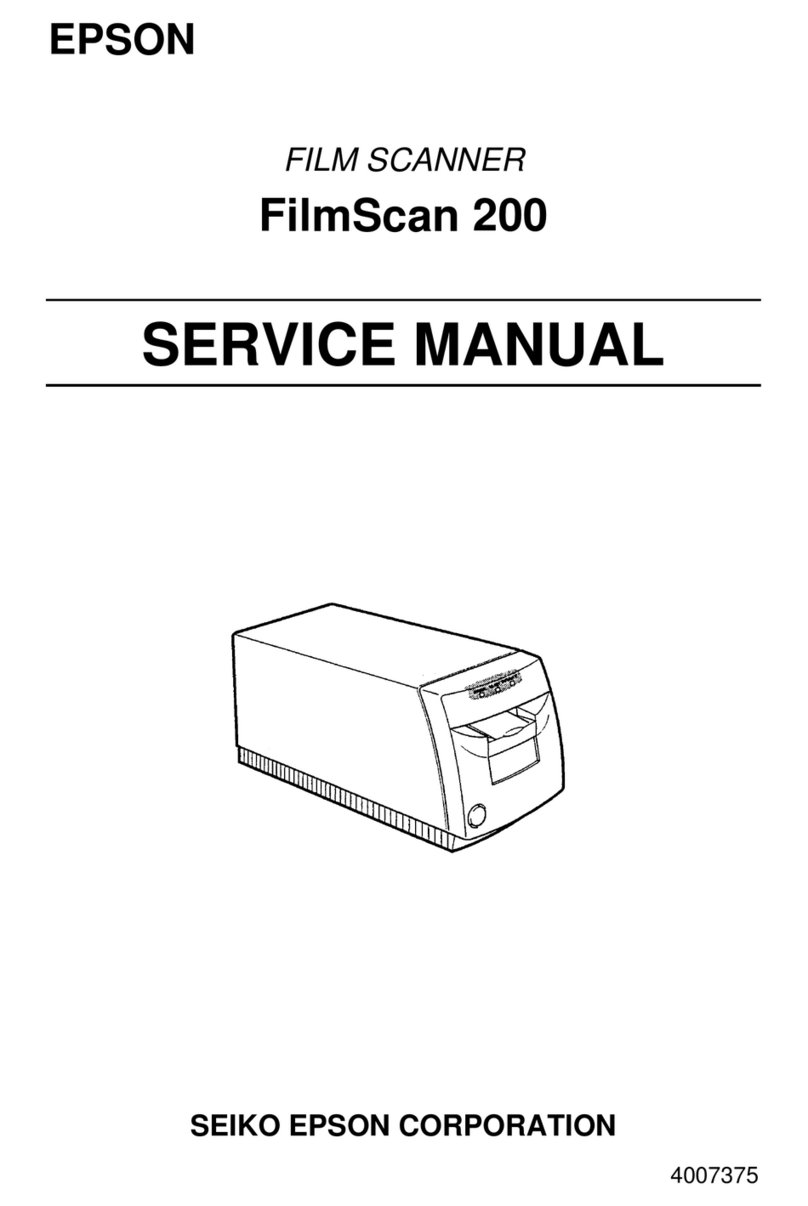
Epson
Epson FILMSCAN 200 Service manual
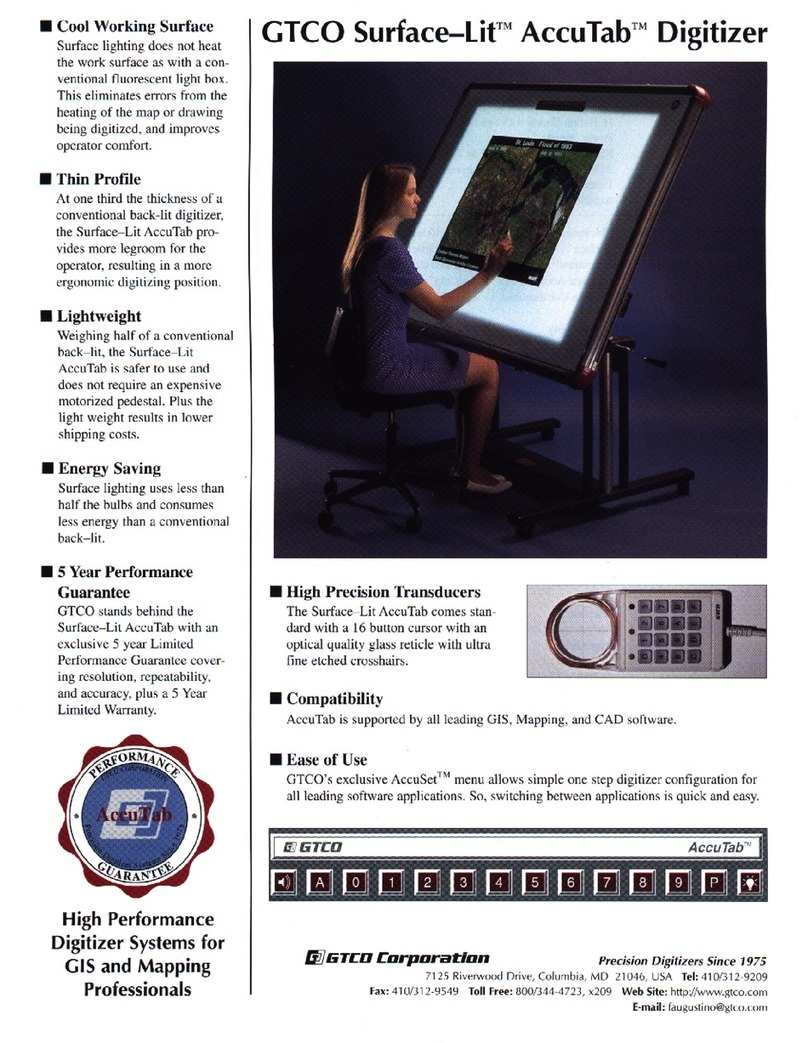
GTCO CalComp
GTCO CalComp 2024 Specifications

Canon
Canon imageFORMULA DR-M260 user manual

Canon
Canon DR-X10C - imageFORMULA - Document Scanner Service manual