Logos Electromechanical 1X3 Bridge Amplifier v2 User manual

8/29/2012
1X3 Bridge Amplifier v2
Resistive bridge amplifier with integrated excitation and power conditioning.
Logos Electromechanical

Logos Electromechanical
1
© 2010 Logos Electromechanical CC-BY-NC-ND 3.0
1X3 Bridge Amplifier v2
Resistive bridge amplifier with integrated excitation and power conditioning.
Introduction
A bridge circuit is a common arrangement in a variety of different measurement
applications, but particularly in force and pressure transducers. The output of these
sensor types is proportional to the excitation voltage applied, and is on the order of
millivolts in any case. Interfacing these sensors with a microcontroller or a data
acquisition system requires a precision voltage source and a precision high gain
amplifier stage. This board provides both in a convenient package.
In addition to force and pressure transducers, this bridge circuit can be used with strain
gauges, thermistors, RTDs, or hot wire anemometers. The versatility of this module is
further increased by onboard charge pump that allows it to develop ±5V bipolar output
from a 6V to 30V single-ended voltage supply. It can provide a jumper-programmable
excitation voltage of up to 10V at 40 mA.
Board Overview
This board is built around the Texas Instruments INA125, which combines a precision
voltage reference stage with a precision high-gain amplifier. This board provides the
support circuitry required to use it in your system with an absolute minimum of external
support.
It is supplied as a kit, with the gain resistor not installed in order to permit the end user
to install a gain resistor appropriate for their desired purpose. The board is provided

Logos Electromechanical
2
© 2010 Logos Electromechanical CC-BY-NC-ND 3.0
with precision resistors. The 182Ω resistor corresponds to a gain of 333 and the 121Ω
resistor corresponds to a gain of 500.
Board Layout
The board is roughly divided into three sections – the input power stage, the bipolar
power stage, and the amplifier stage. The input power stage contains a low dropout
regulator along with a resettable PTC fuse and a diode to prevent reverse connection of
the power from damaging the regulator. This produces a 5.75VDC output that feeds into
the bipolar power stage.
The bipolar power
stage uses a pair of
ICL7660 switched
capacitor voltage
converters. This
uses an array of
capacitors to
produce a +11.5V/-
5.75V bipolar supply for the amplifier stage. This allows the amplifier to read in both
directions for sensors such as push-pull load cells and RTDs. It also provides the voltage
and current required for driving the excitation. Also included are filter capacitors to
reduce switching and transient noise on the amplifier power inputs.
The amplifier stage consists of the INA125, a precision gain setting resistor, an output
protection resistor, input filter, pads for bridge completion resistors, and excitation
selection jumpers. The solder jumper block allows the user to use any of the four
Figure
1
: Board Layout

Logos Electromechanical
3
© 2010 Logos Electromechanical CC-BY-NC-ND 3.0
excitation voltages provided by the INA125 – 10V, 5V, 2.5V, or 1.24V. The input filter is
a capacitor pad provided for limiting the input bandwidth.
There are two different mounting options. The board can be screwed down to a
mounting plate with the provided mounting holes. This allows the user to use either the
provided 0.1” pin header connectors or the optional screw terminals. Alternately, the
board can be trimmed at the two lines of holes on each end. This will allow it to fit inside
a standard Ethernet cable joiner, such as the Bulgin Ethernet Buccaneer. With
appropriate cabling, this gives environmental protection up to IP68 as well as impact
protection.
Pinout
Table 1: Sensor connector pinout
Sensor Pin
Nam
e
Functions
1
Excitation
Selected excitation voltage, positive
2
Sense
-
Negative sense voltage
3
Sense +
Positive sense voltage
4
Excitation
Return/Ground
Excitation voltage return/ground (connected to pin 2 on output
side)
Table 2: Output connector pinout
Output Pin
Name
Functions
1
V
cc
Power supply, 6
–
30VDC
2
Ground
Circuit ground (connected to pin 4 on sensor side)
3
V
ref
Reference voltage
–
shorted to ground for most applications
4
V
out
Output
voltage

Logos Electromechanical
4
© 2010 Logos Electromechanical CC-BY-NC-ND 3.0
Electrical Characteristics
Table 3: Electrical characteristics
Symbol
Parameter
Max
Typ
Min
Units
V
in
Maximum Supply Voltage
(range)
60
-
20
V
G
Gain (range)
10,000
4
Safe sense voltage
±40
V
I
excitation
Excitation Current
4
0
mA
This table covers parameters required to successfully hook up this circuit without
damaging it or impairing its operation. For further performance information on the
performance of the INA125 amplifier and voltage reference stages, please see the
INA125 datasheet.
Board Usage
Selecting Gain
The gain of the INA125 is programmed with a gain resistor. This really wants to be a
precision resistor – 1% or 0.5% tolerance; anything more is not only absurdly expensive
but also pointless, because it is more precise than the amplifier stage. The resistors
supplied with the kit are 1%. Likewise, a temperature coefficient of greater than 25
ppm/°C is not generally useful as the tempco of the INA125 is typically ±25 ppm/°C
with a maximum of ±100 ppm/°C. The gain of the amplifier stage is equal to 4 +Ω
,
where Rgis the resistance of the gain resistor in kΩ.

Logos Electromechanical
5
© 2010 Logos Electromechanical CC-BY-NC-ND 3.0
The two resistors included with the kit are both 1% metal film resistors with a
temperature coefficient of 50 ppm/°C. The 182Ω resistor corresponds to a gain of 333
and the 121Ω resistor corresponds to a gain of 500. If the 10V excitation is selected,
these produce a 5V full scale output from a 3mV/V or 2 mV/V full-scale sensor,
respectively. These are common full range values for load cells and pressure
transducers. No gain resistor is installed by default; either select the appropriate one
from the two provided or acquire an appropriate one for your application.
Selecting Excitation
The INA125 provides four excitation modes. In addition, the default excitation modes
can be augmented with external circuitry. The default modes are 10V, 5V, 2.5V, or 1.24V
(BG). The appropriate voltage is selected by making one of the four provided solder
jumpers. These are on the output side of the board next to the end of the INA125, and
are labeled J-10, J-5, J-2.5, and J-BG. Never make more than one at a time. They are left
unmade by default in order to ease customization by the end user.
Selecting Reference
Since the INA125 is factory trimmed for extremely low offset and drift. Therefore, no
offset adjustment will be required for most applications. When no offset is desired, the
Vref pin should be shorted to ground. A solder jumper, J-REF, (unmade by default) is
provided for this purpose. When an offset is desired, it is set by providing a voltage to
this pin. The voltage on this pin is added to the output signal. It is imperative that the
value provided to this pin not be outside of the range of internal power supply rails (i.e.
greater than +11.5V or less than -5.75V). A low impedance voltage source is desirable in
order to provide good common-mode rejection.
Trimming the Board (optional)
If you wish to use the board in a compact space, like the aforementioned Bulgin
Ethernet Buccaneer, you will need to trim off the ends. This can readily be accomplished

Logos Electromechanical
6
© 2010 Logos Electromechanical CC-BY-NC-ND 3.0
with a pair of tin snips or a shear, cutting along the line of holes present at each end of
the board.
Mounting Connectors
There are three different connector options. If you are using the board as provided
(without trimming), you can mount the provided connectors in the inner rows of holes
on each end of the board, pointed outward. If you have trimmed, the board, you can
install the same connectors on the underside of the board, pointed inward. In both of
these cases, the pinout remains the same.
You can also install 3.5mm pitch screw-clamp connectors. These are installed in the
pads near the ends of the board. We sell a two-pack of connector blocks as an accessory
pack, or you can buy them from the usual distributors.
Load Cell/Pressure Transducer Interface
Typical millivolt output load
cells and pressure transducers
will have a 4-conductor
shielded cable. The wires in the
cable will be labeled with a
positive and negative excitation
and a positive and negative
sense. The shield should be
firmly bonded to either the
electronics enclosure or to the
system ground point. Figure 2
Figure
2
: Load cell/Pressure transducer wiring

Logos Electromechanical
7
© 2010 Logos Electromechanical CC-BY-NC-ND 3.0
shows the appropriate connections.
The sensitivity of the load cell or pressure transducer will typically be expressed in terms
of mV of full scale output per volt of excitation. The two most common values are 2
mV/V and 3 mV/V; resistors are provided in the kit for these two scale values that
provide 5V full scale output from 10V of excitation. Typically, these types of sensors are
calibrated at 10V of excitation. It's best to operate them at their calibration point, so you
should select the 10V excitation by making the J-10 solder jumper. Install the gain
resistor corresponding to your sensor's scale and the board is ready to use.
Strain Gauge
A strain gauge is a resistive
element that changes its
resistance when deformed.
You will have to provide the
other resistors to complete the
bridge circuit, as shown in
Figure 3. Care must be taken
with the sizing of the strain
gauge and bridge completion
resistors not to overtax the
excitation voltage reference.
There are four 0603 pads for
bridge completion resistor on
the board labeled R3, R4, R5, and R7. You can use these pads or install external
resistors.
All of the bridge completion resistors must be equal to each other and should have a
similar resistance to the nominal resistance of the sensor. Total resistive load on the
Figure
3
: Strain Gauge bri
dge completion

Logos Electromechanical
8
© 2010 Logos Electromechanical CC-BY-NC-ND 3.0
excitation will then be approximately equal to the nominal resistance of the sensor. Take
care to select sensor resistance values and excitation values that keep the total excitation
current below 40 mA.
RTD/Thermistor
RTD (resistance temperature detectors) and thermistors are wired in exactly the same
fashion as strain gauges, and all of the same caveats apply.
References
Datasheet for INA125 instrumentation amplifier http://focus.ti.com/lit/ds/symlink/ina125.pdf
Datasheet for ICL7660 charge pump
http://www.intersil.com/content/dam/Intersil/documents/fn30/fn3072.pdf
Datasheet for MIC2954 voltage regulator http://www.micrel.com/_PDF/mic2954.pdf
How load cells work http://www.sensorland.com/HowPage005.html
Table of contents
Popular Amplifier manuals by other brands
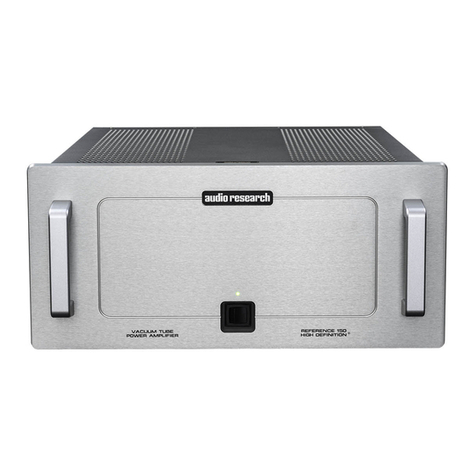
Audio Research
Audio Research Classic 150 owner's manual
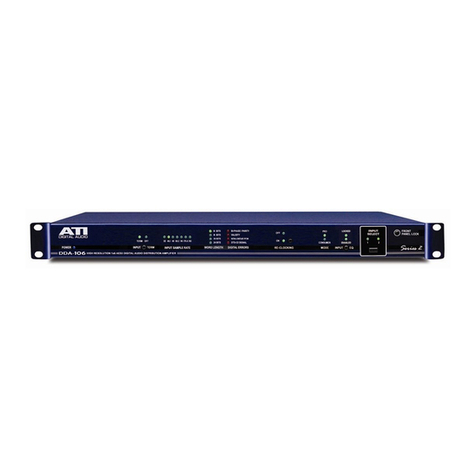
ATI Technologies
ATI Technologies DDA SERIES Operating and maintenance manual

Channel Vision
Channel Vision Audio/Video Distribution Amplifier VDA-12 quick guide
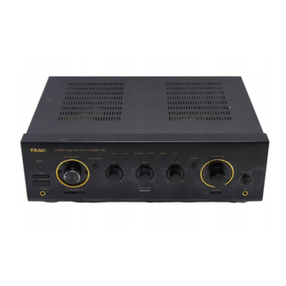
Teac
Teac A-R600 Service manual
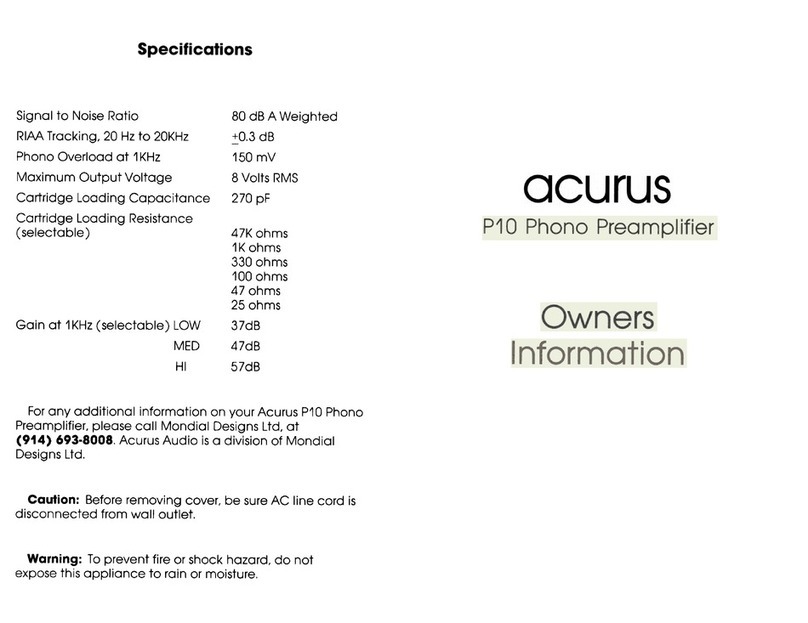
Mondial Designs Limited
Mondial Designs Limited Acurus P10 Owner's Information
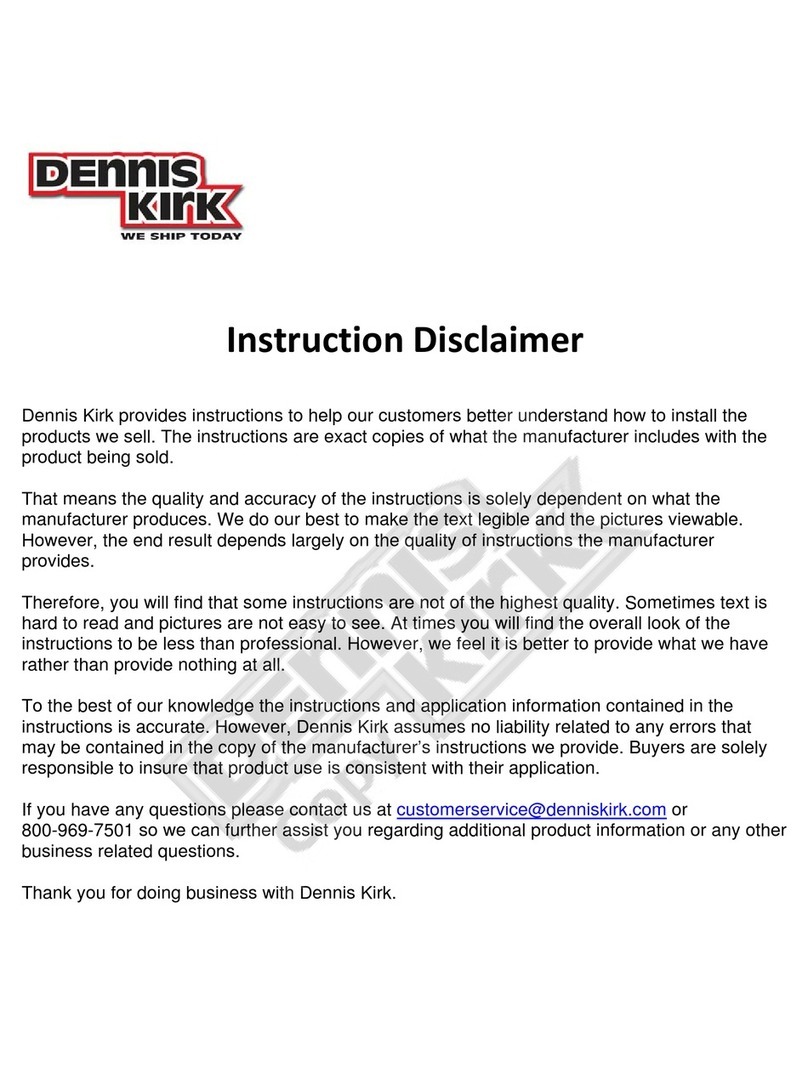
Hogtunes
Hogtunes REV 200-AA installation manual