Main MULTIPOINT FF User guide

MULTIPOINT FF
Room Sealed Fan-Assisted Water Heater
6 720 607 160 (04.02) JS
Please leave these instructions with the user
User Operating, Installation
and Servi ing Instru tions

26 720 607 160
Natural Gas
Main Multipoint FF
G. . No 52-467-02
User information
Your Main Multipoint FF is designed to meet all relevant
standards.
Main provide a 12 month guarantee on the appliance. The
guarantee operates from the date installation is completed
for the customer who is the original owner.
Any component or part which becomes defective during the
guarantee period as a result of faulty workmanship or
materials whilst in normal use will be repaired or replaced
free of charge.
This appliance conforms to European Standard EN 26.
Type test for purpose certified by Notified Body E-0087.
Product/Production certified by Notified Body E-0464.
For GB / IE only.
are must be taken when lifting and handling this appliance,
seek assistance where appropriate. Protective equipement
(e.g. gloves) should be warn as necessary.

36 720 607 160
1. User’s operating instructions ...................................... 4
2. General layout ............................................................... 5
3. Technical Data ...............................................................6
4. Dimensions and fixings................................................. 7
5. General inormation ....................................................... 8
6. Installation Regulations ................................................ 8
7. Siting the Appliance ..................................................... 9
8. Siting the Flue Terminal ............................................ 10
9. Air supply .......................................................................11
10. Gas supply ................................................................... 11
11. Electrical ...................................................................... 13
12. Installation .................................................................... 13
13. ommissioning ............................................................ 18
14. Performance optimization ......................................... 19
15. Inspection and Servicing .......................................... 20
16. Replacement of parts ................................................ 22
17. Fault Finding ................................................................ 24
18. Short Parts List ........................................................... 25
19. Notes ............................................................................. 26
page
Contents
Section

46 720 607 160
1. User’s Operating Instru tions
Swit hing on and off:
On
1. Turn the main switch to position I.
Water temperature ontrol:
1. Turn the control to the desired temperature.
Fault indi ation:
The appliance incorporates a fault indication system.
Fault indication is shown by a red light on the reset button.
If pressing the reset button does not restart the appliance,
consult your installer.
1. Turn the main switch to position 0.
Off
The hot water temperature is set by the control position.
Turn the control clockwise to increase the temperature and
anticlockwise to decrease.
When the control is set at the maximum position the highest
water temperature is achieved by controlling the flow at the
tap.
Note: if the appliance is to be left unused in an unheated
area during cold weather the electricity, gas and water
supplies should be isolated and the system drained.
Your installer will be able to advise you.

56 720 607 160
2. General Layout
Fig. 3
Applian e water flow diagram.
Fig. 4
Applian e omponents
4 Electronic control box
5 Heat sensor
6 Water flow sensor
10 Main switch
11 Temperature control
12 Reset button
13 Burner Indicator Button
17 Safety solenoid EV1
25 Water filter
28 Hot water pipe
29 old water pipe
35 Gas inlet pipe
42 Gas filter
49 Injector
50 Burner
55 Heat exchanger
92 Gas valve
117 Ignition electrode
118 Sensing electrode
119 Temperature limit stat
200 Minimum gas flow adjustment
screw
201 Maximum gas flow adjuster
210 Main valve
221 Flue support ring
222 Exhaust gas collector
224 Flow sensor
226 Fan
228 Pressure switch
229 Sealed box

66 720 607 160
3. Te hni al Data
TABLE1- GENERAL
TABLE3- PERFORMANCE
TABLE 2 - FLUE DETAILS
The appliance and flue components are packed in separate cartons.
The appliance is for use with Natural Gas only.
The Installation notes in these Instructions, particularly those regarding Maximum Flue Lengths and onfiguration
Options, take precedence over any universal instructions included in flue component packs.
Wall hole size 110 mm Diameter
Standard Horizontal Flue Kit
490mm wall thickness rear outlet Sales ode 430183
400mm wall thickness side outlet
Horizontal Flue Kit
680mm wall thickness rear outlet Sales ode 430184
590mm wall thickness side outlet
Flue Extension 1m Sales ode B4286
90° Bend Kit Sales ode 31/19034
135° Bend Kit Sales ode 31/19035
Telescopic Flue In Line Elbow Adaptor Sales ode 430174
Vertical Adaptor Sales ode 238014
oncentric Vertical Flue Kit Sales ode 238015
Flat roof flashing kit Sales Code 31/19040
Pitched roof flashing kit Sales Code 31/19041
Wall liner / internal flue fixing kit Sales Code 238012
Terminal guard Sales Code 205792
Maximum cold water supply inlet pressure 12 bar
Minimum cold water supply inlet pressure to operate the appliance 0.3 bar
Domestic hot water delivery with temperature control knob fully anticlockwise 4 to 14 litres/minute at
25° tem
p
erature rise
Domestic hot water delivery with temperature control knob fully clockwise 2.5 to 6 litres/minute at
55° tem
p
erature rise
Natural Gas
Gas category I2H
Appliance Type 12, 32
Minimum rated output 10 kW
Maximum rated output 23.8 kW
Rated input (Net) 27 kW
Gas rate ( V 34 MJ/m3)2.9 m
3/hr
Inlet pressure 20 mbar
Number of injectors 14
Injector diameter 1.20 mm
Injector marking 120
Burner pressure (max) 12.7 mbar
Burner pressure (min) 2.5 mbar
Height 700 mm
Width 388 mm
Depth 220 mm
Dry weight 20 kg
Gas connection 15mm opper
Hot/cold water connections 15mm opper
Electrical
p
rotection IPX4D

76 720 607 160
4. Dimensions and Fixings
Fig. 5

86 720 607 160
5. General Information
5.1 GENERAL INSTALLATION
If the appliance is to be fitted into a compartment, the
compartment must conform to the requiremens of BS 6798.
Do not place anything on top of the appliance.
The clearances specified for servicing must be maintained.
5.2 SHOWERS
If a shower control is supplied from the appliance it should
be of the thermostatic or pressure balanced type.
Thermostatic type shower valves provide the best comfort
and guard against water at too high a temperature. Existing
controls may not be suitable - refer to the shower valve
manufacturer.
6.1 Warning - heck the information on the data plate is
compatible with local conditions.
The installation must be carried out by a ORGI Registered
Installer or other registered competent person and be in
accordance with the relevant requirements of the current
Gas Safety (Installation and Use) Regulations, the building
regulations (Scotland) ( onsolidation), the local building
regulations, the current I.E.E Wiring Regulations and the
bye laws of the local water undertaking.
Where no specific instruction is given, reference should be
made to the relevant British Standard ode of Practice. For
Ireland, install in accordance with IS 813 “Installation of
Gas Appliances”.
6.2 B.S odes of Practice
Standard Scope
BS 6891 Gas Installation
BS 5546 Installation of water supplies for
domestic purposes
BS 6798 Installation of gas fired hot water boilers
BS 5440 Part1 Flues
BS 5440 Part2 Ventilation
WARNING - The addition of anything that may interfere
with the normal operation of the appliance without the
express written permission of Baxi Potterton could invalidate
the appliance warranty and infringe the Gas Safety
(Installation and Use) Regulations.
6. Installation Regulations

96 720 607 160
7. Siting the Applian e
7.1 The appliance is NOT suitable for external installation.
7.2 The appliance is NOT suitable for SEDU T
application.
7.3 The appliance does not require any special wall
protection.
7.4 The wall must be capable of supporting the weight of
the appliance. See Technical Data – Table 1.
7.5 If the appliance is to be fitted in a timber framed
building, refer to the Institute of Gas Engineers, ”Guide
for gas installations in timber framed housing” IGE/UP/7.
7.6 The following advisable clearances must be available
for installation and for servicing:
7.7 The minimum clearances required for Operation are:
7.8 The appliance can be installed in a cupboard used
for airing clothes provided that requirements of BS 6798
and BS 5440:2 are strictly followed. See section 9 for further
detail.
7.9 The airing space must be separated from the appliance
space by a perforated non-combustible partition. Expanded
metal or rigid wire mesh are acceptable provided that the
major dimension is less than 13 mm.
See BS 6798
Table 4
Above case 120 mm
In front 600 mm
Below 50 mm
Ri
g
ht hand side 10 mm
Left hand side 10 mm
Table 5
Above case 120 mm
In front 60 mm
Below 50 mm
Ri
g
ht hand side 10 mm
Left hand side 10 mm

10 6 720 607 160
8. Siting the Flue Terminal
See Fig. 7.
8.1 The flue must be installed as specified in BS
5440:Part 1.
8.2 The terminal must not cause an obstruction nor the
discharge cause a nuisance.
8.3 If the terminal is fitted within 1000 mm of a plastic or
painted gutter or within 500 mm of painted eaves then an
aluminium shield at least 1000 mm long should be fitted to
the underside of the gutter or painted surface.
8.4 If a terminal is fitted less than 2 metres above a
surface to which persons have access then a guard must
be fitted.
8.5 The terminal guard must be evenly spaced about the
flue terminal and fixed to the wall using plated screws.
8.6 In certain weather conditions a terminal may plume
when the appliance is operated. Siting where this could
cause a nuisance should be avoided.
8.7 Take care to ensure that combustion products do not
enter ventilated roof voids.
Fig. 7 - Siting of the flue terminal
Fig. 6
TERMINAL POSITION MIN. DIST.
A - directly below an openable window or
other opening e.g. air brick. 300 mm
B - Below gutters, soils pipes or drain pipes. 75 mm
C - Below eaves. 200 mm
D - Below balconies or car portroof. 200 mm
E - From vertical drain pipes and soil pipes. 150 mm
F - From internal or external corners. 300 mm
G - Above ground, roof or balcony level. 300 mm
H - From a surface facing a terminal. 600 mm
TERMINAL POSITION MIN. DIS.
I - From a terminal facing a terminal. 1200 mm
J - From an opening in a car port (e.g. door
window) into dwelling. 1200 mm
K - Vertically from a terminal on the same
wall. 1500 mm
L - Horizontally from a terminal on the same
wall. 300 mm
M - From door, window or air vent 300 mm

116 720 607 160
9. Air Supply
9.1 The appliance does not require a separate vent for
combustion air.
9.2 The appliance may be installed in an unvented
compartment.
9.3 There must be sufficient clearance around the
appliance to allow proper circulation of air. The clearances
required for operation will normally be adequate.
9.4 Refer to BS 6798 and BS5440:2 for additional
information.
10. Gas Supply
10.1 The gas installation should be in accordance with
BS 6891.
10.2 The connection to the appliance is 15mm
compression via the gas isolation valve supplied.
10.3 Ensure that the pipework from the meter to the
appliance is of adequate size. If the appliance gas rate
cannot be achieved, the specified hot water conditions will
not be reached.

12 6 720 607 160
Fig. 8
5 Temperature sensor
6 Water flow sensor
7 Fuse1,25A
8 Fuse 2A
92 Gas valve
117 Ignition electrode
118 Sensing electrode
119 Temperature limit stat
226 Fa n
228 Pressure switch

136 720 607 160
The installation must be carried out by a competent person.
12.1 INITIAL PREPARATION
12.1.1 Unpack the appliance and take care to remove the
fascia and the installation kit which are located on the
top and on the bottom of the polystyrene packing. Remove
the White painted Flue Elbow inclusive of sealing rings.
The installation kit (Fig. 9) consists of the following:
Gas inlet:
1x Flanged opper Pipe, ompression Nut, fibre washer
1x Isolation valve, 2 x ompression nuts and Olives
Water Inlet:
1x opper inlet elbow, ompression Nut, fibre washer
1x Isolation valve, 2 x ompression nuts and Olives
Water Outlet:
1x opper inlet elbow ompression nut, Fibre washer
12.1.2 Lay the appliance on its back, unfasten the two
retaining screws and lift the case clear (Fig. 10).
Place the paper mounting template in the required
location on the wall and mark the positions of the flue
and the three mounting holes (Fig. 11).
ut the flue hole and drill and plug the mounting holes.
Fix the wall mounting bracket, hang the appliance and
secure to the wall through the hole located in the valve
mounting bracket. To increase access to this area of the
appliance the control box may be temporarily re
positioned, depress the two curved finger tab latches on
top of the control box and withdraw forward. Use the
integral moulded hooks to hang the control from the
combustion box.
12. Installation
See Fig. 8.
11.1 MAINS SUPPLY.
230 V ~, 50 Hz, 65 watts.
11.2 It must be possible to completely isolate the
appliance.
11.3 The following connection alternatives must be used:
A 3 amp fused three-pin plug and unswitched shuttered
socket outlet (both complying with the requirements of BS
1363) or a double pole isolator with a contact separation of
3mm in all poles and supplying the appliance and controls
only.
11.4 The appliance must be earthed.
11.5 Mains able. 0.75mm2 (24 x 0.20mm) to BS 6500
Table 16.
11.6 The wiring between the appliance and the electrical
supply must comply with current IEE Wiring Regulations
and any local regulations which apply.
11.7 SAFET Y H E K .
After installation or in the event of an electrical fault the
electrical system shall be checked for short circuits, fuse
failure, incorrect polarity of connections, earth continuity
and resistance to earth.
11. Ele tri al
Fig. 9
Fig. 10
Fig. 11

14 6 720 607 160
Fig. 12
12.2 FLU E RESTR I TI ON
The Installation notes in these Instructions, particularly those
regarding Maximum Flue Lengths and onfiguration Options,
take precedence over any universal instructions included in
flue component packs.
To ensure the correct operation of the appliance, certain
flue lengths require one of two flue restrictor rings to be
fitted to the fan inlet. (Fig. 12).
Restrictor requirements for the horizontal and vertical flue
configurations shown in Figures13 and 17 are as per tables
9 and 10 respectively.
Fig. 13
Table 9
Flue length Restrictor
Diameter
Up to 2.0 m 58
2.0 m – 3.0 m 68
3.0 m – 4.0 m Max None
Up to 2.0 m 68
2.0 m – 3.5 m Max None
White Flue Elbow only –
no additional bends
Configuration
A
Horizontal configuration
Direct vertical rise from the
appliance: Vertical Adapter
+ 1 x 90 degree bend
Configuration
E
Flue length Restrictor
D
iameter
Configuration
ANo additional bends
Straight vertical Up to 4.0 m Max 58
Up to 3.5 m 58
3.5 m –4.0 m Max 68
Up to 2.5 m 58
2.5 m –4.0 m Max 68
Vertical configuration
Direct vertical rise from the
appliance: Vertical Adapter
+ 1 x 90 degree bend
Configuration
C
2 x 45 degree bends
Configuration
B
Table 10
12.2.1 Restrictor Ring Installation.
Remove the electrical connections to the fan.
Unfasten the fixing screws (Fig. 12, pos. 1) securing the fan
mounting plate to the appliance.
Remove the fan, unfasten the screws securing the mounting
plate to the fan (Fig. 12, pos 3).
Place the restrictor ring between the fan and the mounting
plate (Fig. 12, pos. 2), align the holes and re secure (Fig.
12, pos 3).
Re assemble the fan to the appliance and replace the
electrical connections.
12.3 FITTING A HORIZONTAL FLUE
Possible flue configurations are as per Fig 13.
The concentric horizontal flue system has an inner flue tube
diameter of 60 mm and an outer air duct diameter of 100
mm.
Standard horizontal flue terminal kits and flue extension
components are detailed in Section 3, Page 6, Table 2 -
Flue Details.
The Maximum and Minimum flue lengths available for
horizontal configurations are as per table 11.

156 720 607 160
Measure
40mm
Top
View
Wall
Rear
Flue
Side
Flue
10mm
Wall
Thickness
Drip Ring
10mm
Fig. 14
12.3.1 Standard Telescopic Flue Installation:
Determine appropriate flue length (Fig. 14)
Rear Flue Application - Measure wall thickness, add 60mm.
Side flue application – Measure distance from outer face
of wall to centre line of appliance, deduct 55mm.
Set the Telescopic flue tubes to the length determined.
Drill through the pilot hole in the outer duct and secure with
the self tapping screw provided. Wrap tape around joint on
the outer duct to seal the flue, slide the drip ring in position
to coincide with the wall cavity.
Slide flue through the hole in wall until it stops against the
bayonet pin.
For side flue Applications – re orient flue support ring on
top of appliance: (Fig. 15) Unfasten Flue Support Ring (x 4
screws). Turn ring 90 degrees to left or right as appropriate.
Re secure.
Position the white painted Flue Elbow onto the Flue Support
Ring ensuring the Silicone Seal engages over the Fan Outlet,
secure the Elbow with 3 off screws provided.
Slide the Flue forward from the wall until it engages in the
white painted elbow’s bayonet connection, twist
anticlockwise to lock. ( Fig. 16)
Drill through the pilot hole in the white flue elbow and lock
the flue in position with self tapping screw provided.
Make good the opening around the flue.
12.3.2Extended Horizontal Flue Installation:
The flue may be extended to the maximum configuration
lengths shown in Table 11 with the application of 1m
extension kits, 45 and 90 degree Elbows and a Telescopic
Flue In Line Elbow Adapter. In all configurations the first
section of Standard Horizontal Flue is located in the white
painted Flue Elbow, the second section terminates the flue
after the extension components.
The 1m extensions can be cut to length as required.
Extended Horizontal flue with direct vertical rise:
The flue may be extended with a direct vertical rise from the
appliance with the application of a Vertical Flue Adapter,
1m extension kits, 90 degree elbow and a telescopic flue in
line elbow adapter. The maximum flue length for this
configuration is as per table 11.
Fig. 15
Flue
Elbow
Flue
Elbow
Connect
Flue
Lock Flue
into
position
Drill and screw
elbow and flue
The Flue Elbow
Arrow MUST align
to Flue Pin as shown
Fig. 16
Table 11
Flue length Restrictor
Configuration
AWhite flue elbow only –
no additional bends 4.0 m Max Table 9
Configuration
BWhite Flue Elbow +
1 x 90 degree bend 2.2 m Max None
required
Configuration
CWhite Flue Elbow +
2x 45 degree bends 2.5 m Max None
required
Configuration
DWhite Flue Elbow +
2x 90 degree bends 1.8 m Max None
required
Configuration
E
Direct vertical rise from the
appliance: Vertical Adapter
+ 1 x 90 degree bend 3.5 m Max Table 9
Horizontal configuration
Minimum flue length:
Rear flue, 230mm wall thickness. 0.29 m Min

16 6 720 607 160
12.4 FITTING A VERTI AL FLUE
Possible configurations of flue are as per Fig. 17.
Vertical flue kits and flue extension components are detailed
in Section 3, Page 6, Table 2 - Flue Details.
For vertical application the white painted elbow is discarded.
The Maximum and Minimum flue lengths available for vertical
configurations are as per table 12.
Table 12
Fig. 17
Appliance
Adaptor
Terminal
Assembly
Flue Tube
Adaptor
Assembly
Contact Rim Lip
Appliance
Adaptor
Contact Rim
Pitched
Roof
Flashing
Flat Roof Flashing
Roof
Flue Tube
Adaptor
Assembly
Outer
Terminal
Tube
Inner
Terminal
Tube
Fig. 18
12.4.1 Standard Vertical installation:
Secure the flashing kit to the roof.
Refer to Fig. 18.
Measure the distance from the contact rim on the flashing
kit to the flue support ring on top of the boiler.
This is dimension ‘Y’.
Lay the Terminal Assembly flat and loosely connect the Flue
Tube Adaptor Assembly and the Appliance Adaptor.
Measure the overall length from the contact rim lip to the
base of the adaptor.
This is dimension ‘X’.
Subtract dimension ‘Y’ (actual) from ‘X’ (uncut), add 3mm,
this will give the cutting length ‘Z’.
Take the assembly apart and shorten the inner and outer
tubes by dimension ‘Z’. Remove any burrs.
Fit the Appliance Adaptor to the top of the appliance using
3 screws provided.
Slide the Flue Tube Assembly onto the Appliance Adaptor.
From the roof, slide the Terminal Assembly through the
flashing kit.
From the appliance side, position the terminal clamp bracket
and loosely secure to the roof. Fig. 19.
Locate the base of the Terminal Assembly into the Flue Tube
Adaptor Assembly From the roof, ensure the contact rim of
the flashing kit has slid up inside the outer tube of the Terminal
Assembly.
Secure the Terminal Assembly to the Flue Adaptor Assembly
and Flue Adaptor Assembly to the Appliance Adaptor. Drill
(2mm drill) through the pilot holes and secure using the
screws provided.
Fully secure the Terminal clamp bracket.
Tape around both joints to give an air tight seal.
Make good around the flashing kit.
Bracket can
pivot to angle
of roof
Roof or
ceiling
member
Bend bracket
to length
Extension
bracket
(100mm Dia.)
Terminal
support
bracket
(125mm Dia.)
Fig. 19
Flue length Restrictor
Configuration
ANo additional bends
Straight vertical 4.0 m Max Table 10
Configuration
B2 x 45 degree bends 4.0 m Max Table 10
Configuration
C2 x 90 degree bend 4.0 m Max Table 10
Vertical configuration
Minimum flue length: 1.4 m Min

176 720 607 160
12.4.2 Extended Vertical Installation
Vertical flue lengths may be extended to the limits as stated
in Table 12 using standard 1m extension kits and 45 and
90 degree elbows.
Secure the Flashing kit to the roof.
Refer to Fig. 20.
From the roof, slide the Terminal Assembly through the
flashing kit, ensure the contact rim of the flashing kit has
slid up inside the outer tube of the Terminal Assembly.
From the appliance side, position the Terminal clamp bracket
and loosely secure to the roof. Fig. 15.
Fit the Appliance Adaptor to the top of the appliance using
3 screws provided.
Assemble the Flue Extension(s), (elbows, seals, clamps where
used), centralising springs and fixing brackets until the
dimension between the end of the Flue Tube Adaptor
Assembly and the bottom of the last Extension Tube flange
is less than 1m, measure this dimension ‘W’.
Subtract 3mm from dimension ‘W’, mark this dimension onto
the final Extension Tube, both inner and outer and cut the
plane end (Not the flange end).
Remove all burrs.
Temporarily lift the Terminal Assembly and slide the extension
tube fixing bracket (if required) and the ceiling seal onto the
outer extension tube.
Position the final Inner Extension Tube.
Position the centralising spring.
Position the final Outer Extension Tube.
Lower and reconnect the Terminal Assembly, drill (2mm drill)
through the pilot holes in the Outer Extension Tube(s) and
Appliance Adaptor. Secure using the screws provided.
Fully tighten the fixing bracket(s) on the extension(s) and
the terminal clamp bracket in the roof.
Make good around the Flashing Kit.
12.5 MAKING THE GAS ONNE TION
Note: The whole of the gas installation should be inspected
and tested for soundness and purged in accordance with
the recommendations of BS 6891.
Make up the gas supply to the connection on the gas control
Valve using the Gas Inlet Kit.
Fit the gas Isolation Valve as close as possible to the
appliance (Fig. 21).
heck for soundness prior to making the water connections.
12.6 MAKING THE WATER ONNE TIONS
onnect the appliance to the incoming cold water supply
using the Water Inlet Kit.
Fit the Isolation Valve as close as possible to the Appliance
(Fig. 21).
onnect the appliance to the domestic hot water System
using the Water Outlet Kit. (Fig. 21).
Turn on the water supply to the appliance. Open the Isolation
Valve on the inlet to the appliance, open the hot water taps
and purge the system of air.
12.7 MAKING THE ELE TRI AL ONNE TIONS
The Appliance is supplied with an integral lead and fused
Plug.
The Appliance may be permanently wired to a double pole
Isolator.
Fig. 20
Flashing kit
Roof
Terminal
bracket
Flue tube
adaptor
assembly
Outer
extension
tube
Flue tube
adaptor
assembly
Terminal
assembly
Appliance
adaptor
Plain end
Measure 'W' - 3mm
and cut inner
extension
Measure 'W' - 3mm
and cut outer
extension
WW
25
Example
of flue
measurement
with one
flue
extension
Example
of flue
measurement
with two
flue
extensions
Fig. 21

18 6 720 607 160
Fig. 22
Before commissioning the appliance, the gas installation
must be purged and tested for gas soundness in accordance
with BS 6891.
13.1) Ensure the gas isolation valve is turned off.
13.2) Remove the appliance outer case.
13.3) To increase access to the pressure test point, the
control box may be temporarily repositioned, depress the
two curved finger tab latches on top of the control box
and withdraw forward. Use the integral moulded hooks
to hang the control from the combustion box (Fig. 22).
13.4) Loosen screw (pos. 4) and connect a pressure gauge
to the test point. Replace the control box and outer case.
13.5) Turn on the gas isolation valve.
13.6) Move main switch to position I (On). Set the
temperature control knob to Maximum. Fully open any
hot water tap.
Note: On initial light up, or after prolonged shut down,
the establishment of a flame may take several attempts
due to the presence of air in the gas supply pipe.
13.7) heck the dynamic inlet gas pressure is 20.0 mbar.
If the pressure is not correct then check the gas supply
to the appliance.
If the pressure is correct, turn off the hot water tap and
move the main switch to the off position. Remove the
outer case and reposition the control box as in 13.3.
Turn off the gas isolation valve. Remove the pressure
gauge and tighten screw (pos. 4).
13.8) The burner pressure is factory set and should not
require adjustment.
To confirm the burner pressure stated in table 1, loosen
screw (pos 1) and connect a pressure gauge to the
pressure test point. Replace the control box and outer
case, turn on the gas isolation valve.
With the main switch in position O (off), on the control
box front turn the temperature control to position 60.
Press and hold the burner indicator button (Fig. 3, key
13). Move the main switch to position I (on), the green
burner indicator blinks. Fully open a hot tap, confirm the
burner pressure, turn the main switch to position O (off).
Turn off the hot water tap, close the gas isolation valve.
Remove the case and pressure gauge, tighten screw
(pos 1). Replace controls and outer case.
13.9) Should the burner pressure require adjustment, refer
to section 15.5, Service Adjustment.
13.10) Open gas Isolation Valve, fit the fascia and set the
Main Switch to I (on), the appliance is now ready for
operation.
13.11) On completion of the commissioning and testing of
the system, the installer should:
13.11.1) Give the Instructions to the user for safe
keeping.
13.11.2) Explain and demonstrate the lighting and
shutdown procedures.
13.11.3) Advise the user of the precautions necessary to
prevent damage to the system and to the building in the
event of the system remaining inoperative during frost
conditions.
13.11.4) Recommend that the appliance is serviced
annually for reasons of safety and economy and that the
servicing must be carried out by a competent person.
13. Commissioning
1Burner pressure measuring point
2Minimum gas flow ajustment screw
3Maximum gas flow adjuster
4Gas supply pressure measuring point

196 720 607 160
14. Performan e optimization
Performance optimization is a process that informs the
appliance about its installation/working conditions so that it
can adjust itself accordingly. The appliance is thus more
responsive.
14.1) Set the main switch to position O (off).
14.2) On the control unit front panel, place the rotary
temperature control knob at position ‘45’.
14.3) Press and hold the burner indicator button (Fig 3,
key13) and set the main switch to position I (on). The
green burner indicator button blinks.
The appliance is now in performance optimisation mode.
14.4) Fully open a hot water tap.
14.5) Operate the appliance for approximately 5 minutes.
14.6) Set the main switch to position O (off).
lose the hot water tap and set the main switch back to
position I (on).
The performance optimisation operation is complete.
Fig. 23

20 6 720 607 160
15. Inspe tion and Servi ing
Warning
Isolate electrical supply before servicing the appliance.
For reasons of safety and economy it is recommend that
the appliance is serviced annually. The servicing must be
carried out by a competent person.
Before commencing any service operation turn off the gas
supply at the main gas isolation valve. Ensure that the
appliance is cool.
ACCESS FOR SERVICING
Pull of the fascia and undo the two fixing screws.
Lift the outer case clear.
15.1 Heat Ex hanger
Undo the two retaining screws and remove the holding
bracket.
Inspect and if necessary clean the heat exchanger
flueways.
15.2 Main Burner
Disconnect the wire connections to the ignition and
sensing electrodes.
Undo the union connection below the burner.
Remove and retain the fibre washer.
Lift and rotate the front edge of the burner backward
through 180 degrees. With the burner oriented
horizontally and upside down, withdraw forward beneath
the combustion chamber skirt. (fig. 23).
Inspect and clean the injectors if necessary.
Inspect and clean the main burner bars if necessary.
15.3 Water filter
lose the water inlet isolation valve.
Open a hot water tap, open the drain screw and drain
the appliance.
Dismantle the cold water inlet pipe.
lean the water filter/regulator.
15.4 Re-assembling the Applian e
Re-assemble the appliance in reverse order ensuring the
following:
The washer in the main gas line union is correctly located.
The seals around the ignition leads and cable entries
are correctly seated in the combustion chamber base.
Turn on the gas supply at the main gas isolation valve
and check for gas soundness BS 6891 while the
appliance is running.
Re-commission the appliance as detailed in Section 13.
Fig. 25
Fig. 24
Table of contents
Other Main Water Heater manuals
Popular Water Heater manuals by other brands
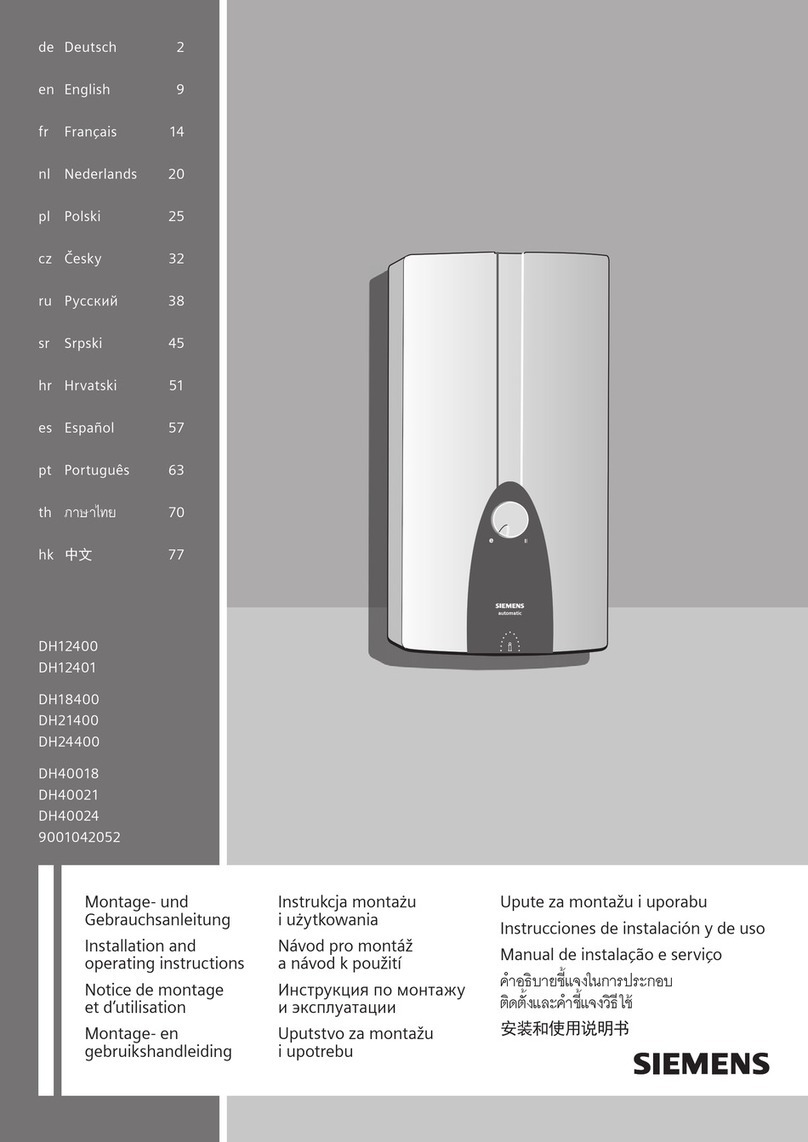
Siemens
Siemens 9001042052 Installation and operating instructions
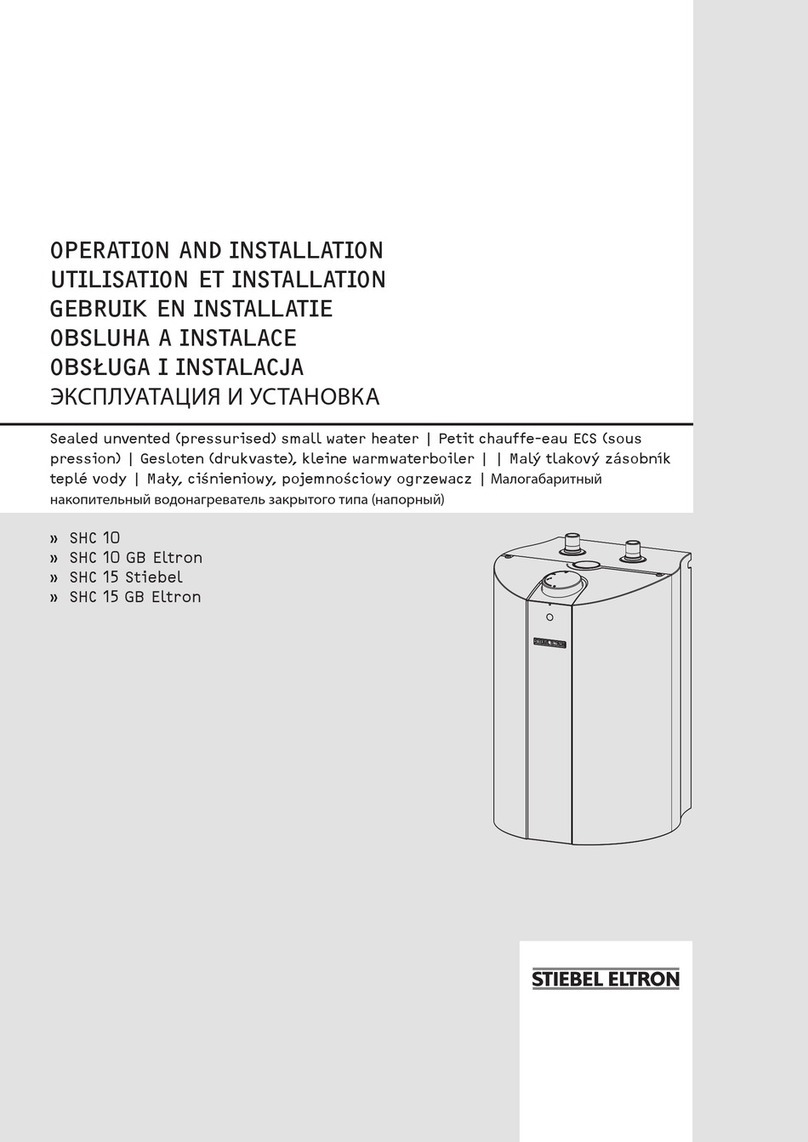
STIEBEL ELTRON
STIEBEL ELTRON SHC 10 Operation and installation
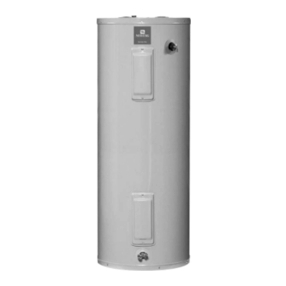
Maytag
Maytag Series Six user guide
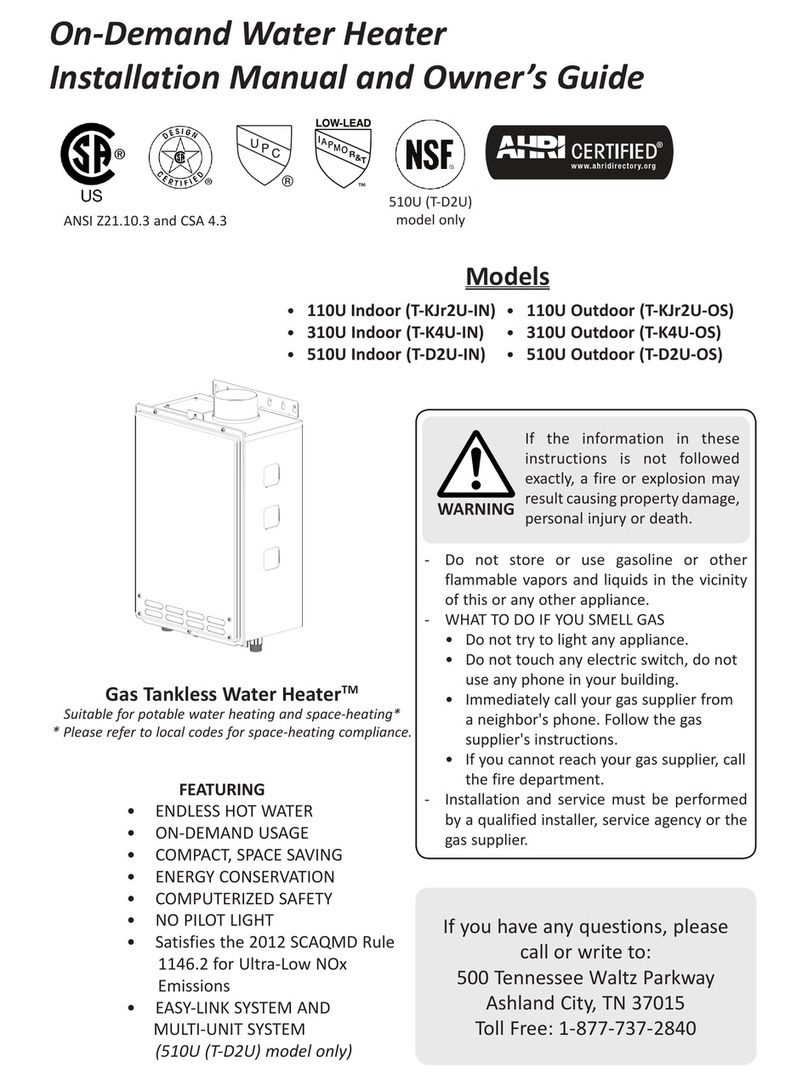
Takagi
Takagi T-K4U-IN Installation manual and owner's guide

Noritz
Noritz NC199-DVC-CA installation manual

Bosch
Bosch C1210ES Technical service bulletin