Minnich A-2C User manual

A-2C DOWEL DRILL
OPERATOR/SERVICE MANUAL
Minnich Manufacturing
1444 ST RT 42
Manseld,OH 44903
Contact
Phone: (419)-903-0010
Email: [email protected]
Revision Date: 07/19/2023

Dowel Drill Manual 2
TABLE OF CONTENTS
See engine manual for information pertaining
to the engine.
If there are any questions regarding the ma-
chine or its application which are not covered
in this manual or in other literature accompa-
nying this unit, please contact your Minnich
Dealer or Minnich Manufacturing at 419-903-
It is Minnich’s policy to constantly strive to
improve our products. The information, spec-
ications, and illustrations in this publication
are based on the information in effect at the
same time as approval for printing and pub-
lishing. Minnich therefore reserves the right
to make changes in design and improve-
ments whenever it is believed the efciency
of the machine which has been shipped or
curring any obligation to incorporate such im-
provements in any machine which has been
shipped or is in service. It is recommended
that users contact Minnich or a Minnich Deal-
er for latest revisions.
Chapter 1-Introduction......................................................................................................................................1
General Warnings...................................................................................................................................3
General Safety.........................................................................................................................................4
Safety Decal Location..........................................................................................................................10
MachineSpecication...........................................................................................................................12
Pressure Regulator.................................................................................................................................13
Standard Setup.......................................................................................................................................14
Drilling Operations................................................................................................................................15
Troubleshooting Air Drill......................................................................................................................16
Drill Steel Information..........................................................................................................................19
Chapter 2-Parts Manual..................................................................................................................................22
Notes.....................................................................................................................................................39
Warranty.................................................................................................................................................40
Ordering Information...........................................................................................................................41

3
Dowel Drill Manual
GENERAL WARNINGS
CALIFORNIA PROPOSITION 65
Engine exhaust and some of its constituents,
and some dust created by power sanding,
sawing, grinding, drilling and other construction
activities contains chemicals known to the Sate
of California to cause cancer, birth defects and
other reproductive harm. Some examples of
these chemicals are:
Lead from lead-based paints.
Crystalline silica from bricks.
Arsenic and chromium from chemically treated
lumbar.
Your risk from these exposures caries, depend-
ing on how often you do this type of work. To
reduce your exposure to these chemicals:
ALWAYS work in a well ventilated area, and
work with improved safety equipment, such
as dust masks that are specically designed to
lter out microscopic particles.
SILICOSIS WARNING
Grinding/cutting/drilling of masonry, concrete,-
metal and other materials with silica in their
composition may give off dust or mist contain-
ing crystalline silica.
Silica is a basic components of sand, quarts,
brick clay, granite and numerous other minerals
and rocks. Repeated and/or substantial inha-
lation of airborne crystalline silica can cause
serious or fatal respirator disease, including sil-
icosis. In addition, California and some author-
ities have listed repairable crystalline silica as a
substance known to cause cancer. When cutting
such materials, always follow the respiratory
precautions mentioned above.
RESPIRATORY HAZARDS
Grinding/cutting/drilling of masonry, concrete,metal and fumes containing
chemicals known to cause serious or fatal injury or illness, such as respirato-
ry disease, cancer, birth defects or other reproduction harm, if you are
unfamiliar with the risks associated with the particular process and/or
material being cut or the composition of the tool being used, review the
material safety data sheey and/or consult your employer, the material
manufacturer/supplier, governmental agencies such as OSHA and NIOSH
and other sources on hazardous materials. California and some other
authorities, for instance, have published lists of substances known to cause
cancer, reproductive toxicity or other harmful effects.
Control dust, mist and fumes at the source where possible. In this regard use good work practices and
follow the recommendations of the manufactures of suppliers, OSHA/NIOSH, and occupational and
trade associations. Water should be used for dust suppression when wet cutting is feasible. When the
hazards from inhalation of dust, mist and fumes cannot be eliminated, the operator and any bystand-
ers should always wear a respirator approved by OSHA/NIOSH for the materials being used.

Dowel Drill Manual 4
GENERAL SAFETY
SYMBOL SAFETY HAZARD
Respiratory Hazard
Explosive fuel hazards
Burn hazard
Factory Settings
SAFETY SYMBOLS
Potential hazards associated with the operation
of this equipment will be referenced with hazards
symbols which may appear throughout this manu-
al in conjunction with safety messages.
Indicates a hazardous situation which, if not
avoided, COULD result in DEATH or SERI-
OUS INJURY
Indicates a hazardous situation which, if not
avoided, COULD result in MINOR or MOD-
ERATE INJURY
Indicates a hazardous situation which, if not
avoided, WILL result in DEATH or SERIOUS
INJURY
Addresses practices not related to personal
injury
SAFETY MESSAGES
The four safety messages shown below will
inform you about potential hazards that could
injure you or others. The safety messages specif-
ically address the level of exposure to the opera-
tor and are preceded by one of four words:
DANGER, WARNING, CAUTION or NOTICE.
Do not operate or service the equipment before
reading the entire manual. Safety precautions
should be followed at all times when operating this
equipment. Failure to read and understand the safe-
ty messages and operating instructions could result
in injury to yourself and others.
This operation manual has been developed to pro-
vide complete instruction for the safe and efcient
operation. Refer to the engine manufactures instruc-
tions for data relative to its safe operation. Before
using, ensure that the operating individual
has read and understood all instructions in the
manual. The surrounding environment and you,
could be damaged if you do not follow instructions.
∆ALWAYS be sure the operator is familiar
with the proper safety precautions and op-
erating techniques before using.
∆NEVER leave the machine unattended.
Turn off when unattended
DO NOT USE TOOL IF IT IS IN NEED OF SERVICE!

5
Dowel Drill Manual
GENERAL SAFETY
∆ NEVER operate this equipment without
proper protective clothing, shatter proof
glasses, respirator protection, hearing pro-
tection, steel-toes boots and other protec-
tive devises required by the job or city and
sate regulations.
∆ Never operate this equipment
when not feeling well due to
fatigue, illness or when under
medication.
∆ NEVER operate this equipment under the
inuence of drugs or alcohol.
∆ ALWAYS check the equipment for loosened
threads or bolts before starting.
∆ NEVER operate around corrosive chemicals
or water containing toxic substances. These
uids could create serious health and envi-
ronmental hazards. Contact local authorities
for assistance.
∆ DO NOT use the equipment for any purpose
other than its intended purpose or applica-
tions.
∆ This equipment should only be operated by
trained and qualied personnel 18 years of
age and older.
∆ This equipment is for industrial use only.
Whenever necessary, replace nameplate,
operation and safety decals when
they become difcult to read.
∆ Manufacturer does not assume responsibility
for any accident due to equipment modica-
tions. Unauthorized equipment modications
will void all warranties. Any modication
which it could lead to change in the original
characteristics of the machine should be
made only by the manufacturer who shall con-
rm that the machine is in comfortability with
appropriate safety regulations.
∆ Never use accessories or attachments that are
not recommended by Minnich for the equip-
ment. Damage to the equipment and/or injury
to user may result.
∆ Always know the location of the
nearest re extinguisher.
∆ ALWAYS know the location of the
nearest rst aid kit.
∆ ALWAYS know the location of the nearest
phone or keep a phone on the job site. Also,
know the phone numbers of the nearest
ambulance, doctor and re department. This
information will be invaluable in the case of an
emergency.
∆ NEVER operate the equipment in an
explosive atmosphere, near combus-
tible materials, or near ammable or
low ash point uids. An explosion or
re could result causing severe bodily
harm or even death.
∆ NEVER disconnect any emergency or safety
devices. These devises are intended for op-
erator safety. Disconnection of these devices
can cause severe injury, bodily harm or even
death. Disconnection of any of these will void
all warranties.
∆ NEVER operate equipment with the covers or
guards removed. Keep ngers, hands, hair and
clothing away from all moving parts to prevent
injury. Wear clothing that will not likely be-
come caught in the equipment or snag on any
moving parts.

Dowel Drill Manual 6
GENERAL SAFETY
∆ DO NOT expose vibrator to rain.
∆ DO NOT use vibrator motor in damp or wet
locations without proper electrical circuits.
∆ DO NOT immerse the motor part in con-
crete.
∆ ALWAYS keep clear of rotating or moving
parts while operating.
∆ NEVER leave the machine unattended while
running
∆ ALWAYS disconnect the motor from the
power source when not in use, before servic-
ing, and when changing exible shafting and
vibrator heads.
∆ Allow the machine to cool
before servicing. Contact with
hot components can cause
serious burns.
∆ Before Each use, ALWAYS check the motor
to make certain that there are no damaged
parts and that all parts function properly.
If any damage or malfunctioning parts are
found, have them repaired or replaced by an
authorized service facility.
∆ ALWAYS secure forms. Make sure the form
work is well made and braced to withstand
the stresses made by vibration.
∆ ALWAYS keep vibrator motor clean for bet-
ter and safer operation.
∆ ALWAYS store equipment properly when
it is not being used. Equipment should be
stored in a clean, dry location out of reach
of children and unauthorized personnel.
∆ Use only factory authorized replacement
parts.
∆ Store idle vibrator motor. When not in use,
motor should be stored in a dry, safe stor-
age area.
∆ DO NOT pour waste or oil directly into the
ground, down a drain or into any water
source.
ENVIRONMENTAL SAFETY/DECOMMISSIONING
∆ Contact you country department
of Public Works or recycling
agency in your area and arrange
for proper disposal of any elec-
trical components, waste or oil
associated with this equipment.
∆ When the life cycle of this equipment is over,
remove battery (if equip) and bring to appro-
priate facility for lead reclamation. Use safety
precautions when handling batteries that
contain sulfuric acid.
∆ When the life cycle of this equipment is over,
it is recommended that the unit frame and
all other metal parts be sent to a recycling
center.
Metal recycling involves the collection of
metal from discarded products and its trans
formation into raw materials to use in many
Manufacturing a new product.
Recyclers and manufactures alike promote the
process of recycling center promotes energy
cost savings.
Decommissioning is a controlled process used to
safely retire a piece of equipment that is no longer
serviceable. If the equipment poses an unaccept-
able and unrepairable safety risk due to wear or
damage or is no longer cost effective to maintain
(beyond life-cycle reliability) and is to be decommis-
sioned (demolition and dismantlement), be sure to
follow rules below.
∆ ALWAYS observe all applicable compulsory reg-
ulations relevant to environmental protection,
especially fuel storage, the handling of hazard-
ous substances, and the wearing of protective
clothing and equipment. Instruct the user as a
necessary, or, as the user, request this informa-
tion and training.

7
Dowel Drill Manual
GENERAL SAFETY
∆ ALWAYS keep the machine in proper running
condition.
∆ ALWAYS become familiar with the compo-
nents of the machine before operation.
∆ Fix damage to machine and replace any bro-
ken parts immediately.
∆ ALWAYS store equipment properly when it is
not being used. Equipment should be stored
in a clean, dry location out of the reach of
children and unauthorized personnel.
∆ NEVER lubricate components or attempt ser-
vice on a running machine
∆ NEVER tamper with the factory
settings of the engine or en-
gine governor. Damage to the
engine or equipment can result
in operation in speed ranges
above the maximum allowabil-
ity.
∆ ALWAYS Dispose of hazardous waste proper-
ly. Examples of potentially hazardous waste
include used motor oil, fuel, and fuel lters.
∆ DO NOT use food or plastic containers to
dispose hazardous waste.
∆ DO NOT pour waste or oil directly onto the
ground, down or drain or into any waste
source.
BEFORE CONNECTING THE AIR COMPRESSOR:
∆ NEVER attempt to loosen any compressed air
hose that is pressurized.
∆ KEEP AWAY from all hot or spark generating
objects, do not smoke when handling fuel.
∆ So as to facilitate shipment, new or repaired
units are not lubricated before delivery to cus-
tomers.
∆ DO NOT use hydrocarbons and especially do
not use fuel oil for lubricating purposes.
∆ DO NOT OPERATE MACHINE WITHOUT
GUARDS AND COVERS IN PLACE
∆ ALWAYS disconnect the air supply before chang-
ing steel or dismantling the tool for service or
repair. For maximum safety we advise the in-
stallation of a shut-off valve at the end of the air
line.
∆ NEVER operate the engine with heat shields or
guards removed.
∆ DO NOT remove the engine oil drain plug while
the engine is hot. Hot oil will gush out of the
engine crankcase and severely scald any persons
in the general area of the machine.
∆ Install the drill steel and bits into the drill motors
and close the latch retainers and rod guides.
∆ Make sure that the air compressor is set at an
operating pressure of not more than 120 PSIG
(8Bar)
∆ Make sure air line is cleaned out and is of the
proper size and pressure rating for the drill unit.
∆ Make sure the lubricator is lled with proper
lubricant. See Minnich recommended lubricant
below.
∆ Make sure all controls are in the “off” position
and the lift lever (if so equipped) is in the “up”
position.
∆ Make sure all lock pins are in their locked posi-
tion.
NEVER REACH INTO
PINCH PIVOT POINTS
WARNING
NOISE MAY
DAMAGE HEARING
WEAR PROPER HEARING
PROTECTION
FLYING PARTICLES MAY CAUSE
EYE INJURIES
WEAR PROPER EYE
PROTECTION
HIGH PRESSURE
KEEP AWAY FROM LEAKS
BLEED DOWN BEFORE REMOVING
LINES TO SERVICE
DUST CAN CAUSE INJURY TO
YOUR HEALTH
IF VENTILATION IS INADEQUATE
USE AN APPROVED RESPIRATOR
12 28 7- 3
DRILLS WILL
AUTOMATICALLY START
WHEN AIR SUPPLY IS LOST
AND REAPPLIED
12287-64
WARNING
WARNING
BE SURE SUPPLY LINES ARE SECURE
DO NOT EXCEED 120 PSI (8.25 BARS)
OR DAMAGE TO MACHINE AND OR
BODILY HARM MAY RESULT
12287-1
INSTALL LOCK
PIN PRIOR TO
TRANSPORTING MACHINE
12287-7
INSTALL LOCK
PIN PRIOR TO
TRANSPORTING MACHINE
12287-7
INSTALL LOCK
PIN PRIOR TO
TRANSPORTING MACHINE
12287-7
WARNING
KEEP GUARDS IN PLACE
DISCONNECT POWER
BEFORE SERVICING
12287-12
WARNING
KEEP GUARDS IN PLACE
DISCONNECT POWER
BEFORE SERVICING
12287-12
12287-62 12287-62
12287-62 12287-62
XX
X
X
DRILLS
FEED
1 2
ON ON
OFF OFF
IN IN
OUT OUT
TM
WARNING
STAND CLEAR
WHEN RAISING OR LOWERING
12287-10
12287-43
READ & UNDERSTAND OWNERS MANUAL COMPLETELY.
TIGHTEN ALL LOOSE BOLTS INSPECT ALL LINES, PIPES, AND HOSES FOR DAMAGE.
REPAIR AS NECESSARY.
DRILL STEEL MUST NOT BE BINDING IN GUIDE BEARING. MAKE SURE DRILL STEEL
IS STRAIGHT, FREE OF OBSTRUCTIONS, AND NOT BINDING IN ANYWAY.
FILL THE OILER-PER MANUAL.
WARNING
STAND CLEAR
WHEN RAISING OR LOWERING
12287-10
Bio-Rock Drill
Oil 15W50
TM
Minnich Mfg. Recommended Rock Drill Oil
A-2-BW
A-2-BW

Dowel Drill Manual 8
GENERAL SAFETY
Connect/start
Storage
If the vibration intensity drops, check that the
lters are not clogged or that hoses are not
kinked.
To properly store unit after use, hang the
vibrator with the head up and set the handle
(variable control assembly) in the open position
to permit the discharge of possible impurities,
contaminants and water.
Placement and consolidation
The force exerted by an internal concrete vibra-
tor is controlled by the weight and the speed
at which the eccentric rotates. The centrifugal
force exerted can be arrived at by various com-
binations of weight (size of eccentric weight)
and the speed at which the weight rotates. For
years the most favorable working speed for a
vibrator was considered to be around 10,200
RPM (VPM) and consequently this gure is used
in many vibrator comparisons. More recently,
the optimum speed for compaction has been
accepted as being between 7500 and 9000
RPM.
To nd the latest revision of this publication,
visit our website at: www.minnich-mfg.com
THIS MANUAL MUST ACCOMPANY THE
EQUIPMENT AT ALL TIMES.
Specications and part numbers are subject
to change without notice.
∆ Stay alert, watch what you are doing, and use
common sense when operating the machine.
∆ DO NOT use the tool while tired or under the
inuence of drugs, alcohol, or medication. A
moment of inattention while operating power
tools may result in serious personal injury or
death.
∆ Dress properly. DO NOT wear loose clothing or
jewelry. Tie up long hair. Keep your hair, cloth-
ing and gloves away from moving parts. Loose
clothes, jewelery, or long hair can be caught in
moving parts.
∆ DO NOT overreach. Keep proper footing and
balance at all times. Proper footing and balance
enables better control in unexpected situations.
PERSONAL SAFETY
SERVICE
∆ Tool service must be preformed only by qual-
ied repair personnel. Service or maintained
preformed by unqualied personnel could
result in injury or death
∆ When servicing a tool, use only identical
replacement parts. Use of unauthorized parts
may create a risk of injury or death.
∆ CLEAR AIR SUPPLY LINE: Before connecting
vibrator, clear the compressed air supply line of
possible impurities, contaminants and water.
∆ LUBRICATE: Every day or every four hours
of continuous service, pour a ½ teaspoon of
non-detergent oil into the quick release cou-
pling. NOTE: An optional oiler/strainer is avail-
able.

9
Dowel Drill Manual
GENERAL SAFETY
TOOL USE AND CARE
1. Only qualied persons should operate the
machine. Make sure you operate and service your
machine according to the instructions listed in this
manual.
2. When positioning the machine for drilling,
always face the drill. DO NOT operate with your
back to the machine. Facing the machine during
positioning allows the operator to have better
control of the machine.
3. DO NOT force the machine. Use the correct
machine for your application. The correct machine
will do the job better and safer at the rate for
which it is designed.
4. DO NOT use the machine if the switch does
not turn it on or off. Any machine that cannot be
controlled with the switch is dangerous and must
be re-paired.
5. Disconnect the machine from the pow-er source
before making any adjustments, changing acces-
sories or storing the machine. Such preventative
safety measures reduce the risk of starting the
machine accidentally.
6. Store machines out of reach of children and
other untrained persons. Machines are dangerous
in the hands of untrained users.
7. Maintain machines with care and keep them
clean. Properly maintained ma-chines are less like-
ly to bind and are easier to control.
8. Check for misalignment or binding of moving
parts, breakage of parts and any other condition
that may affect the machines operation. If dam-
aged, have the machine serviced before using.
Many accidents are caused by poorly maintained
tools.
9. Use only accessories that are recommended by
the manufacturer for your model. Accessories that
may be suitable for one machine may become
hazardous when used on another.
SERVICE
1. DO NOT run the drill unit while you make
adjustments and repairs unless the procedure is
approved.
2. Escaping uid and air under pressure can
have sufcient force to penetrate skin causing
serious personal injury.
3. Before disconnecting lines, be sure to relieve
all pressure. Before applying pressure to the
system, be sure all connections are tight and
that lines, tubes and hoses are not damaged.
4. DO NOT use your hand to search for leaks.
Instead, use a piece of card-board or wood.
5. Tool service must be performed only by qual-
ied repair personnel. Service or maintenance
performed by unqualied personnel could
result in injury or death.
6. When servicing a tool, use only identical
replacement parts. Use of unauthorized parts
increase injury risk.

Dowel Drill Manual 10
SAFETY DECAL LOCATION
All safety labels on Minnich Manufacturing
units have been carefully placed so they can
be easily seen at all times. There are several
different types of labels on the units. Always
keep these warnings free of dirt, concrete,
or anything else that restricts visibility. Never
remove the labels for any reason. If the label
on your machine become worn or in any way
difcult to read, call our parts department for
replacements.
A
B
C
D
E
F
G
I
HIGH PRESSURE
BLEED AIR PRESSURE
BEFORE SERVICING
DRILLS WILL
AUTOMATICALLY START
WHEN AIR SUPPLY IS LOST
AND REAPPLIED 12287-64
WARNING
DRILLS WILL
AUTOMATICALLY START
WHEN AIR SUPPLY IS LOST
AND REAPPLIED 12287-64
WARNING
WARNING
NOISE MAY
DAMAGE HEARING
WEAR PROPER HEARING
PROTECTION
FLYING PARTICLES MAY CAUSE
EYE INJURIES
WEAR PROPER EYE
PROTECTION
HIGH PRESSURE
KEEP AWAY FROM LEAKS
BLEED DOWN BEFORE REMOVING
LINES TO SERVICE
DUST CAN CAUSE INJURY TO
YOUR HEALTH
IF VENTILATION IS INADEQUATE
USE AN APPROVED RESPIRATOR
12 28 7- 3
WARNING
BE SURE SUPPLY LINES ARE SECURE
DO NOT EXCEED 120 PSI (8.25 BARS)
OR DAMAGE TO MACHINE AND OR
BODILY HARM MAY RESULT
12287-1
12287-42
12287-38
1
12287-36
12287-36
12287-37
12287-43
READ & UNDERSTAND OWNERS MANUAL COMPLETELY.
TIGHTEN ALL LOOSE BOLTS INSPECT ALL LINES, PIPES, AND HOSES FOR DAMAGE.
REPAIR AS NECESSARY.
DRILL STEEL MUST NOT BE BINDING IN GUIDE BEARING. MAKE SURE DRILL STEEL
IS STRAIGHT, FREE OF OBSTRUCTIONS, AND NOT BINDING IN ANYWAY.
FILL THE OILER-PER MANUAL.
WARNING
KEEP GUARDS IN PLACE
DISCONNECT POWER
BEFORE SERVICING 12287-12
INSTALL LOCK
PIN PRIOR TO
TRANSPORTING MACHINE
12287-7
INSTALL LOCK
PIN PRIOR TO
TRANSPORTING MACHINE
12287-7
INSTALL LOCK
PIN PRIOR TO
TRANSPORTING MACHINE
12287-7
INSTALL LOCK
PIN PRIOR TO
TRANSPORTING MACHINE
12287-7
DRILL HAMMERS WILL NOT
FUNCTION WHEN INDICATOR IS RED
WHEN INDICATORS IS RED FILL OIL RESERVOIR
WITH PROPER ROCK DRILL LUBRICANT
GREEN INDICATES LUBRICATOR RESERVOIR IS FULL
Bio-Rock Drill
Oil 15W50
TM
Minnich Mfg. Recommended Rock Drill Oil
WARNING
STAND CLEAR
WHEN RAISING OR LOWERING
12287-10
WARNING
STAND CLEAR
WHEN RAISING OR LOWERING
12287-10
Pick Point
J
K
H
WARNING
NOISE MAY
DAMAGE HEARING
WEAR PROPER HEARING
PROTECTION
FLYING PARTICLES MAY CAUSE
EYE INJURIES
WEAR PROPER EYE
PROTECTION
HIGH PRESSURE
KEEP AWAY FROM LEAKS
BLEED DOWN BEFORE REMOVING
LINES TO SERVICE
DUST CAN CAUSE INJURY TO
YOUR HEALTH
IF VENTILATION IS INADEQUATE
USE AN APPROVED RESPIRATOR
12 28 7- 3
DRILLS WILL
AUTOMATICALLY START
WHEN AIR SUPPLY IS LOST
AND REAPPLIED
12287-64
WARNING
WARNING
BE SURE SUPPLY LINES ARE SECURE
DO NOT EXCEED 120 PSI (8.25 BARS)
OR DAMAGE TO MACHINE AND OR
BODILY HARM MAY RESULT
12287-1
INSTALL LOCK
PIN PRIOR TO
TRANSPORTING MACHINE
12287-7
INSTALL LOCK
PIN PRIOR TO
TRANSPORTING MACHINE
12287-7
INSTALL LOCK
PIN PRIOR TO
TRANSPORTING MACHINE
12287-7
WARNING
KEEP GUARDS IN PLACE
DISCONNECT POWER
BEFORE SERVICING
12287-12
WARNING
KEEP GUARDS IN PLACE
DISCONNECT POWER
BEFORE SERVICING
12287-12
12287-62 12287-62
12287-62 12287-62
XX
X
X
DRILLS
FEED
1 2
ON ON
OFF OFF
IN IN
OUT OUT
TM
WARNING
STAND CLEAR
WHEN RAISING OR LOWERING
12287-10
12287-43
READ & UNDERSTAND OWNERS MANUAL COMPLETELY.
TIGHTEN ALL LOOSE BOLTS INSPECT ALL LINES, PIPES, AND HOSES FOR DAMAGE.
REPAIR AS NECESSARY.
DRILL STEEL MUST NOT BE BINDING IN GUIDE BEARING. MAKE SURE DRILL STEEL
IS STRAIGHT, FREE OF OBSTRUCTIONS, AND NOT BINDING IN ANYWAY.
FILL THE OILER-PER MANUAL.
WARNING
STAND CLEAR
WHEN RAISING OR LOWERING
12287-10
Bio-Rock Drill
Oil 15W50
TM
Minnich Mfg. Recommended Rock Drill Oil
A-2-BW
A-2-BW
L
N
M

11
Dowel Drill Manual
SAFETY DECAL LOCATION
WARNING
KEEPGUARDS IN PLACE
DISCONNECT POWER
BEFORE SERVICING
12287-12
WARNING
KEEPGUARDS IN PLACE
DISCONNECT POWER
BEFORE SERVICING
12287-12
WARNING
KEEPGUARDS IN PLACE
DISCONNECT POWER
BEFORE SERVICING
12287-12
WARNING
KEEPGUARDS IN PLACE
DISCONNECT POWER
BEFORE SERVICING
12287-12
WARNING
KEEPGUARDS IN PLACE
DISCONNECT POWER
BEFORE SERVICING
12287-12
WARNING
KEEPGUARDS IN PLACE
DISCONNECT POWER
BEFORE SERVICING
12287-12
WARNING
STANDCLEAR
WHENRAISING OR LOWERING
12287-10
WARNING
STANDCLEAR
WHENRAISING OR LOWERING
12287-10
INSTALLLOCK
PINPRIOR TO
TRANSPORTINGMACHINE
12287-7
INSTALLLOCK
PINPRIOR TO
TRANSPORTINGMACHINE
12287-7
INSTALLLOCK
PINPRIOR TO
TRANSPORTINGMACHINE
12287-7
INSTALLLOCK
PINPRIOR TO
TRANSPORTINGMACHINE
12287-7
12287-62 12287-62
12287-62 12287-62
12287-62
12287-62
DRILLSWILL
AUTOMATICALLYSTART
WHENAIR SUPPLYIS LOST
ANDREAPPLIED
12287-64
WARNING
DRILLSWILL
AUTOMATICALLYSTART
WHENAIR SUPPLYIS LOST
ANDREAPPLIED
12287-64
WARNING
WARNING
NOISEMAY
DAMAGEHEARING
WEARPROPERHEARING
PROTECTION
FLYINGPARTICLESMAYCAUSE
EYEINJURIES
WEARPROPEREYE
PROTECTION
HIGHPRESSURE
KEEPAWAYFROMLEAKS
BLEEDDOWNBEFOREREMOVING
LINESTOSERVICE
DUSTCANCAUSEINJURY TO
YOURHEALTH
IFVENTILATIONISINADEQUATE
USEANAPPROVEDRESPIRATOR
12287-3
12287-43
READ& UNDERSTAND OWNERS MANUAL COMPLETELY.
TIGHTENALL LOOSE BOLTSINSPECT ALL LINES, PIPES, AND HOSES FOR DAMAGE.
REPAIRAS NECESSARY.
DRILLSTEEL MUST NOT BE BINDING IN GUIDE BEARING. MAKESURE DRILL STEEL
ISSTRAIGHT,FREE OF OBSTRUCTIONS, AND NOT BINDING IN ANYWAY.
FILLTHE OILER-PER MANUAL.
HIGHPRESSURE
BLEEDAIRPRESSURE
BEFORESERVICING
WARNING
BESURESUPPLY LINES ARE SECURE
DONOT EXCEED 120 PSI (8.25 BARS)
ORDAMAGE TO MACHINE AND OR
BODILYHARMM AY RESULT
12287-1
INSTALLLOCK
PINPRIOR TO
TRANSPORTINGMACHINE
12287-7
12287-31
12287-62
12287-62
DRILL4DRILL3DRILL 2DRILL1
OFF
ON
OFF
ON
OFF
ON
OFF
ON
FEED4FEED3FEED 2FEED1
IN
OUT
IN
OUT
IN
OUT
IN
OUT
LIFT
UP
DOWN
A-4scSD
TRAVEL TRAVEL
PRESS FOOT PEDAL
TO TRAVEL
Bio-RockDrill
Oil 15W50
TM
MinnichMfg.Recommended Rock Drill Oil
HIGHPRESSURE
BLEEDAIRPRESSURE
BEFORESERVICING
DRILLSWILL
AUTOMATICALLYSTART
WHENAIRSUPPLYIS LOST
ANDREAPPLIED 12287-64
WARNING
DRILLSWILL
AUTOMATICALLYSTART
WHENAIRSUPPLYIS LOST
ANDREAPPLIED 12287-64
WARNING
WARNING
NOISEMAY
DAMAGEHEARING
WEARPROPERHEARING
PROTECTION
FLYINGPARTICLESMAYCAUSE
EYEINJURIES
WEARPROPEREYE
PROTECTION
HIGHPRESSURE
KEEPAWAYFROMLEAKS
BLEEDDOWNBEFOREREMOVING
LINESTOSERVICE
DUSTCANCAUSEINJURY TO
YOURHEALTH
IFVENTILATIONISINADEQUATE
USEANAPPROVEDRESPIRATOR
12287-3
WARNING
BESURESUPPLY LINES ARE SECURE
DONOTEXCEED 120 PS I (8.25 BARS)
ORDAMAGETO MACHINE AND OR
BODILYHARMMAY RESULT
12287-1
12287-42
12287-38
1
12287-36
12287-36
12287-37
12287-43
READ&UNDERSTAND OWNERS MANUAL COMPLETELY.
TIGHTENALLLOOSE BOLTS INSPECT ALL LINES, PIPES, AND HOSES FOR DAMAGE.
REPAIRASNECESSARY.
DRILLSTEELMUST NOT BE BINDING IN GUIDE BEARING. MAKE SURE DRILL STEEL
ISSTRAIGHT,FREE OF OBSTRUCTIONS, AND NOT BINDING IN ANYWAY.
FILLTHEOILER-PER MANUAL.
WARNING
KEEPGUARDS I N PLACE
DISCONNECT POWER
BEFORE SERVICING
12287-12
INSTALLLOCK
PINPRIOR TO
TRANSPORTINGMACHINE
12287-7
INSTALLLOCK
PINPRIOR TO
TRANSPORTINGMACHINE
12287-7
INSTALLLOCK
PINPRIOR TO
TRANSPORTINGMACHINE
12287-7
INSTALLLOCK
PINPRIOR TO
TRANSPORTINGMACHINE
12287-7
DRILLHAMMERSWILLNOT
FUNCTIONWHENINDICATORISRED
WHENINDICATORSISREDFILL OIL RESERVOIR
WITHPROPERROCKDRILLLUBRICANT
GREENINDICATESLUBRICATORRESERVOIRISFULL
Bio-RockDrill
Oil 15W50
TM
MinnichMfg.Recommended Rock Drill Oil
WARNING
STANDCLEAR
WHENRAISINGOR LOWERING
12287-10
WARNING
STANDCLEAR
WHENRAISINGOR LOWERING
12287-10
Pick Point
HIGHPRESSURE
BLEEDAIRPRESSURE
BEFORESERVICING
DRILLSWILL
AUTOMATICALLYSTART
WHENAIRSUPPLYIS LOST
ANDREAPPLIED 12287-64
WARNING
DRILLSWILL
AUTOMATICALLYSTART
WHENAIRSUPPLYIS LOST
ANDREAPPLIED 12287-64
WARNING
WARNING
NOISEMAY
DAMAGEHEARING
WEARPROPERHEARING
PROTECTION
FLYINGPARTICLESMAYCAUSE
EYEINJURIES
WEARPROPEREYE
PROTECTION
HIGHPRESSURE
KEEPAWAYFROMLEAKS
BLEEDDOWNBEFOREREMOVING
LINESTOSERVICE
DUSTCANCAUSEINJURY TO
YOURHEALTH
IFVENTILATIONISINADEQUATE
USEANAPPROVEDRESPIRATOR
12287-3
WARNING
BESURESUPPLY LINES ARE SECURE
DONOTEXCEED 120 PS I (8.25 BARS)
ORDAMAGETO MACHINE AND OR
BODILYHARMMAY RESULT
12287-1
12287-42
12287-38
1
12287-36
12287-36
12287-37
12287-43
READ&UNDERSTAND OWNERS MANUAL COMPLETELY.
TIGHTENALLLOOSE BOLTS INSPECT ALL LINES, PIPES, AND HOSES FOR DAMAGE.
REPAIRASNECESSARY.
DRILLSTEELMUST NOT BE BINDING IN GUIDE BEARING. MAKE SURE DRILL STEEL
ISSTRAIGHT,FREE OF OBSTRUCTIONS, AND NOT BINDING IN ANYWAY.
FILLTHEOILER-PER MANUAL.
WARNING
KEEPGUARDS I N PLACE
DISCONNECT POWER
BEFORE SERVICING
12287-12
INSTALLLOCK
PINPRIOR TO
TRANSPORTINGMACHINE
12287-7
INSTALLLOCK
PINPRIOR TO
TRANSPORTINGMACHINE
12287-7
INSTALLLOCK
PINPRIOR TO
TRANSPORTINGMACHINE
12287-7
INSTALLLOCK
PINPRIOR TO
TRANSPORTINGMACHINE
12287-7
DRILLHAMMERSWILLNOT
FUNCTIONWHENINDICATORISRED
WHENINDICATORSISREDFILL OIL RESERVOIR
WITHPROPERROCKDRILLLUBRICANT
GREENINDICATESLUBRICATORRESERVOIRISFULL
Bio-RockDrill
Oil 15W50
TM
MinnichMfg.Recommended Rock Drill Oil
WARNING
STANDCLEAR
WHENRAISINGOR LOWERING
12287-10
WARNING
STANDCLEAR
WHENRAISINGOR LOWERING
12287-10
Pick Point
HIGHPRESSURE
BLEEDAIRPRESSURE
BEFORESERVICING
DRILLSWILL
AUTOMATICALLYSTART
WHENAIRSUPPLYIS LOST
ANDREAPPLIED 12287-64
WARNING
DRILLSWILL
AUTOMATICALLYSTART
WHENAIRSUPPLYIS LOST
ANDREAPPLIED 12287-64
WARNING
WARNING
NOISEMAY
DAMAGEHEARING
WEARPROPERHEARING
PROTECTION
FLYINGPARTICLESMAYCAUSE
EYEINJURIES
WEARPROPEREYE
PROTECTION
HIGHPRESSURE
KEEPAWAYFROMLEAKS
BLEEDDOWNBEFOREREMOVING
LINESTOSERVICE
DUSTCANCAUSEINJURY TO
YOURHEALTH
IFVENTILATIONISINADEQUATE
USEANAPPROVEDRESPIRATOR
12287-3
WARNING
BESURESUPPLY LINES ARE SECURE
DONOTEXCEED 120 PS I (8.25 BARS)
ORDAMAGETO MACHINE AND OR
BODILYHARMMAY RESULT
12287-1
12287-42
12287-38
1
12287-36
12287-36
12287-37
12287-43
READ&UNDERSTAND OWNERS MANUAL COMPLETELY.
TIGHTENALLLOOSE BOLTS INSPECT ALL LINES, PIPES, AND HOSES FOR DAMAGE.
REPAIRASNECESSARY.
DRILLSTEELMUST NOT BE BINDING IN GUIDE BEARING. MAKE SURE DRILL STEEL
ISSTRAIGHT,FREE OF OBSTRUCTIONS, AND NOT BINDING IN ANYWAY.
FILLTHEOILER-PER MANUAL.
WARNING
KEEPGUARDS I N PLACE
DISCONNECT POWER
BEFORE SERVICING
12287-12
INSTALLLOCK
PINPRIOR TO
TRANSPORTINGMACHINE
12287-7
INSTALLLOCK
PINPRIOR TO
TRANSPORTINGMACHINE
12287-7
INSTALLLOCK
PINPRIOR TO
TRANSPORTINGMACHINE
12287-7
INSTALLLOCK
PINPRIOR TO
TRANSPORTINGMACHINE
12287-7
DRILLHAMMERSWILLNOT
FUNCTIONWHENINDICATORISRED
WHENINDICATORSISREDFILL OIL RESERVOIR
WITHPROPERROCKDRILLLUBRICANT
GREENINDICATESLUBRICATORRESERVOIRISFULL
Bio-RockDrill
Oil 15W50
TM
MinnichMfg.Recommended Rock Drill Oil
WARNING
STANDCLEAR
WHENRAISINGOR LOWERING
12287-10
WARNING
STANDCLEAR
WHENRAISINGOR LOWERING
12287-10
Pick Point
HIGHPRESSURE
BLEEDAIRPRESSURE
BEFORESERVICING
DRILLSWILL
AUTOMATICALLYSTART
WHENAIRSUPPLYIS LOST
ANDREAPPLIED 12287-64
WARNING
DRILLSWILL
AUTOMATICALLYSTART
WHENAIRSUPPLYIS LOST
ANDREAPPLIED 12287-64
WARNING
WARNING
NOISEMAY
DAMAGEHEARING
WEARPROPERHEARING
PROTECTION
FLYINGPARTICLESMAYCAUSE
EYEINJURIES
WEARPROPEREYE
PROTECTION
HIGHPRESSURE
KEEPAWAYFROMLEAKS
BLEEDDOWNBEFOREREMOVING
LINESTOSERVICE
DUSTCANCAUSEINJURY TO
YOURHEALTH
IFVENTILATIONISINADEQUATE
USEANAPPROVEDRESPIRATOR
12287-3
WARNING
BESURESUPPLY LINES ARE SECURE
DONOTEXCEED 120 PS I (8.25 BARS)
ORDAMAGETO MACHINE AND OR
BODILYHARMMAY RESULT
12287-1
12287-42
12287-38
1
12287-36
12287-36
12287-37
12287-43
READ&UNDERSTAND OWNERS MANUAL COMPLETELY.
TIGHTENALLLOOSE BOLTS INSPECT ALL LINES, PIPES, AND HOSES FOR DAMAGE.
REPAIRASNECESSARY.
DRILLSTEELMUST NOT BE BINDING IN GUIDE BEARING. MAKE SURE DRILL STEEL
ISSTRAIGHT,FREE OF OBSTRUCTIONS, AND NOT BINDING IN ANYWAY.
FILLTHEOILER-PER MANUAL.
WARNING
KEEPGUARDS I N PLACE
DISCONNECT POWER
BEFORE SERVICING
12287-12
INSTALLLOCK
PINPRIOR TO
TRANSPORTINGMACHINE
12287-7
INSTALLLOCK
PINPRIOR TO
TRANSPORTINGMACHINE
12287-7
INSTALLLOCK
PINPRIOR TO
TRANSPORTINGMACHINE
12287-7
INSTALLLOCK
PINPRIOR TO
TRANSPORTINGMACHINE
12287-7
DRILLHAMMERSWILLNOT
FUNCTIONWHENINDICATORISRED
WHENINDICATORSISREDFILL OIL RESERVOIR
WITHPROPERROCKDRILLLUBRICANT
GREENINDICATESLUBRICATORRESERVOIRISFULL
Bio-RockDrill
Oil 15W50
TM
MinnichMfg.Recommended Rock Drill Oil
WARNING
STANDCLEAR
WHENRAISINGOR LOWERING
12287-10
WARNING
STANDCLEAR
WHENRAISINGOR LOWERING
12287-10
Pick Point
HIGHPRESSURE
BLEEDAIRPRESSURE
BEFORESERVICING
DRILLSWILL
AUTOMATICALLYSTART
WHENAIRSUPPLYISLOST
ANDREAPPLIED
12287-64
WARNING
DRILLSWILL
AUTOMATICALLYSTART
WHENAIRSUPPLYISLOST
ANDREAPPLIED
12287-64
WARNING
WARNING
NOISEMAY
DAMAGEHEARING
WEARPROPERHEARING
PROTECTION
FLYINGPARTICLESMAYCAUSE
EYEINJURIES
WEARPROPEREYE
PROTECTION
HIGHPRESSURE
KEEPAWAYFROMLEAKS
BLEEDDOWNBEFOREREMOVING
LINESTOSERVICE
DUSTCANCAUSEINJURYTO
YOURHEALTH
IFVENTILATIONISINADEQUATE
USEANAPPROVEDRESPIRATOR
12287-3
WARNING
BESURESUPPLYLINESARESECURE
DONOTEXCEED120PSI(8.25 BARS)
ORDAMAGETOMACHINEAND OR
BODILYHARMMAYRESULT
12287-1
12287-42
12287-38
1
12287-36
12287-36
12287-37
12287-43
READ&UNDERSTANDOWNERSMANUAL COMPLETELY.
TIGHTENALLLOOSEBOLTSINSPECT ALL LINES, PIPES, AND HOSES FOR DAMAGE.
REPAIRASNECESSARY.
DRILLSTEELMUSTNOTBE BINDING IN GUIDE BEARING. MAKESUREDRILLSTEEL
ISSTRAIGHT,FREEOFOBSTRUCTIONS, AND NOT BINDING IN ANYWAY.
FILLTHEOILER-PERMANUAL.
WARNING
KEEPGUARDSIN PLACE
DISCONNECTPOWER
BEFORESERVICING
12287-12
INSTALLLOCK
PINPRIORTO
TRANSPORTINGMACHINE
12287-7
INSTALLLOCK
PINPRIORTO
TRANSPORTINGMACHINE
12287-7
INSTALLLOCK
PINPRIORTO
TRANSPORTINGMACHINE
12287-7
INSTALLLOCK
PINPRIORTO
TRANSPORTINGMACHINE
12287-7
DRILLHAMMERSWILLNOT
FUNCTIONWHENINDICATORISRED
WHENINDICATORSISREDFILLOILRESERVOIR
WITHPROPERROCKDRILLLUBRICANT
GREENINDICATESLUBRICATORRESERVOIRISFULL
Bio-RockDrill
Oil15W50
TM
MinnichMfg.RecommendedRockDrillOil
WARNING
STANDCLEAR
WHENRAISINGORLOWERING
12287-10
WARNING
STANDCLEAR
WHENRAISINGORLOWERING
12287-10
Pick Point
HIGHPRESSURE
BLEEDAIRPRESSURE
BEFORESERVICING
DRILLSWILL
AUTOMATICALLYSTART
WHENAIRSUPPLYIS LOST
ANDREAPPLIED 12287-64
WARNING
DRILLSWILL
AUTOMATICALLYSTART
WHENAIRSUPPLYIS LOST
ANDREAPPLIED 12287-64
WARNING
WARNING
NOISEMAY
DAMAGEHEARING
WEARPROPERHEARING
PROTECTION
FLYINGPARTICLESMAYCAUSE
EYEINJURIES
WEARPROPEREYE
PROTECTION
HIGHPRESSURE
KEEPAWAYFROMLEAKS
BLEEDDOWNBEFOREREMOVING
LINESTOSERVICE
DUSTCANCAUSEINJURY TO
YOURHEALTH
IFVENTILATIONISINADEQUATE
USEANAPPROVEDRESPIRATOR
12287-3
WARNING
BESURESUPPLY LINES ARE SECURE
DONOTEXCEED 120 PS I (8.25 BARS)
ORDAMAGETO MACHINE AND OR
BODILYHARMMAY RESULT
12287-1
12287-42
12287-38
1
12287-36
12287-36
12287-37
12287-43
READ&UNDERSTAND OWNERS MANUAL COMPLETELY.
TIGHTENALLLOOSE BOLTS INSPECT ALL LINES, PIPES, AND HOSES FOR DAMAGE.
REPAIRASNECESSARY.
DRILLSTEELMUST NOT BE BINDING IN GUIDE BEARING. MAKE SURE DRILL STEEL
ISSTRAIGHT,FREE OF OBSTRUCTIONS, AND NOT BINDING IN ANYWAY.
FILLTHEOILER-PER MANUAL.
WARNING
KEEPGUARDS I N PLACE
DISCONNECT POWER
BEFORE SERVICING
12287-12
INSTALLLOCK
PINPRIOR TO
TRANSPORTINGMACHINE
12287-7
INSTALLLOCK
PINPRIOR TO
TRANSPORTINGMACHINE
12287-7
INSTALLLOCK
PINPRIOR TO
TRANSPORTINGMACHINE
12287-7
INSTALLLOCK
PINPRIOR TO
TRANSPORTINGMACHINE
12287-7
DRILLHAMMERSWILLNOT
FUNCTIONWHENINDICATORISRED
WHENINDICATORSISREDFILL OIL RESERVOIR
WITHPROPERROCKDRILLLUBRICANT
GREENINDICATESLUBRICATORRESERVOIRISFULL
Bio-RockDrill
Oil 15W50
TM
MinnichMfg.Recommended Rock Drill Oil
WARNING
STANDCLEAR
WHENRAISINGOR LOWERING
12287-10
WARNING
STANDCLEAR
WHENRAISINGOR LOWERING
12287-10
Pick Point
HIGHPRESSURE
BLEEDAIRPRESSURE
BEFORESERVICING
DRILLSWILL
AUTOMATICALLYSTART
WHENAIRSUPPLY IS LOST
ANDREAPPLIED
12287-64
WARNING
DRILLSWILL
AUTOMATICALLYSTART
WHENAIRSUPPLY IS LOST
ANDREAPPLIED
12287-64
WARNING
WARNING
NOISEMAY
DAMAGEHEARING
WEARPROPERHEARING
PROTECTION
FLYINGPARTICLESMAYCAUSE
EYEINJURIES
WEARPROPEREYE
PROTECTION
HIGHPRESSURE
KEEPAWAYFROMLEAKS
BLEEDDOWNBEFOREREMOVING
LINESTOSERVICE
DUSTCANCAUSEINJURY TO
YOURHEALTH
IFVENTILATIONISINADEQUATE
USEANAPPROVEDRESPIRATOR
12287-3
WARNING
BESURESUPPLY LINES ARE SECURE
DONOTEXCEED 120 PSI(8.25BARS)
ORDAMAGETO MACH INEAND OR
BODILYHARMMAY RESULT
12287-1
12287-42
12287-38
1
12287-36
12287-36
12287-37
12287-43
READ& UNDERSTANDOWNERS MANUAL COMPLETELY.
TIGHTENALL LOOSE BOLTSINSPECT ALL LINES, PIPES, AND HOSES FOR DAMAGE.
REPAIRASNECESSARY.
DRILLSTEEL MUST NOT BE BINDING IN GUIDE BEARING. MAKESURE DRILL STEEL
ISSTRAIGHT,FREE OF OBSTRUCTIONS, AND NOT BINDING IN ANYWAY.
FILLTHE OILER-PER MANUAL.
WARNING
KEEPGUARDS IN PLACE
DISCONNECT POWER
BEFORE SERVICING
12287-12
INSTALLLOCK
PINPRIOR TO
TRANSPORTINGMACHINE
12287-7
INSTALLLOCK
PINPRIOR TO
TRANSPORTINGMACHINE
12287-7
INSTALLLOCK
PINPRIOR TO
TRANSPORTINGMACHINE
12287-7
INSTALLLOCK
PINPRIOR TO
TRANSPORTINGMACHINE
12287-7
DRILLHAMMERSWILLNOT
FUNCTIONWHENINDICATORISRED
WHENINDICATORSISREDFILL OIL RESERVOIR
WITHPROPERROCKDRILL LUBRICANT
GREENINDICATESLUBRICATORRESERVOIRIS FULL
Bio-RockDrill
Oil 15W50
TM
MinnichMfg.Recommended Rock Drill Oil
WARNING
STANDCLEAR
WHENRAISING OR LOWERING
12287-10
WARNING
STANDCLEAR
WHENRAISING OR LOWERING
12287-10
Pick Point
HIGHPRESSURE
BLEEDAIR PRESSURE
BEFORESERVICING
DRILLSWILL
AUTOMATICALLYSTART
WHENAIR SUPPLY IS LOST
ANDREAPPLIED
12287-64
WARNING
DRILLSWILL
AUTOMATICALLYSTART
WHENAIR SUPPLY IS LOST
ANDREAPPLIED
12287-64
WARNING
WARNING
NOISEMAY
DAMAGEHEARING
WEARPROPER HEARING
PROTECTION
FLYINGPARTICLESMAY CAUSE
EYEINJURIES
WEARPROPER EYE
PROTECTION
HIGHPRESSURE
KEEPAWAYFROM LEAKS
BLEEDDOWN BEFORE REMOVING
LINESTO SERVICE
DUSTCAN CAUSE INJURY TO
YOURHEALTH
IFVENTILATION IS INADEQUATE
USEAN APPROVED RESPIRATOR
12287-3
WARNING
BESURE SUPPLY LINES ARE SECURE
DO NOT EXCEED 120 PS I (8.25 BARS)
OR DAMAGE TO MACHINE ANDOR
BODILYHARM M AY RESULT
12287-1
12287-42
12287-38
1
12287-36
12287-36
12287-37
12287-43
READ & UNDERSTANDOWNERS MANUAL COMPLETELY.
TIGHTEN ALL LOOSE BOLTSINSPECT ALL LINES, PIPES, AND HOSES FOR DAMAGE.
REPAIRAS NECESSARY.
DRILL STEEL MUST NOT BE BINDING IN GUIDE BEARING. MAKE SURE DRILL STEEL
IS STRAIGHT,FREE OF OBSTRUCTIONS, AND NOT BINDING IN ANYWAY.
FILL THE OILER-PER MANUAL.
WARNING
KEEP GUARDS IN PLACE
DISCONNECT POWER
BEFORE SERV ICING
12287-12
INSTALL LOCK
PIN PRIOR TO
TRANSPORTING MACHINE
12287-7
INSTALL LOCK
PIN PRIOR TO
TRANSPORTING MACHINE
12287-7
INSTALL LOCK
PIN PRIOR TO
TRANSPORTING MACHINE
12287-7
INSTALL LOCK
PIN PRIOR TO
TRANSPORTING MACHINE
12287-7
DRILLHAMMERS WILL NOT
FUNCTIONWHEN INDICATORIS RED
WHENINDICATORSIS RED FILL OIL RESERVOIR
WITHPROPER ROCK DRILL LUBRICANT
GREENINDICATESLUBRICATOR RESERVOIR IS FULL
Bio-Rock Drill
Oil 15W50
TM
MinnichMfg. Recommended Rock Drill Oil
WARNING
STANDCLEAR
WHEN RAISING OR LOWERING
12287-10
WARNING
STANDCLEAR
WHEN RAISING OR LOWERING
12287-10
Pick Point
I
M
H
E
E
B
A
K
J
HIGHPRESSURE
BLEEDAIRPRESSURE
BEFORESERVICING
DRILLSWILL
AUTOMATICALLYSTART
WHENAIRSUPPLYIS LOST
ANDREAPPLIED 12287-64
WARNING
DRILLSWILL
AUTOMATICALLYSTART
WHENAIRSUPPLYIS LOST
ANDREAPPLIED 12287-64
WARNING
WARNING
NOISEMAY
DAMAGEHEARING
WEARPROPERHEARING
PROTECTION
FLYINGPARTICLESMAYCAUSE
EYEINJURIES
WEARPROPEREYE
PROTECTION
HIGHPRESSURE
KEEPAWAYFROMLEAKS
BLEEDDOWNBEFOREREMOVING
LINESTOSERVICE
DUSTCANCAUSEINJURY TO
YOURHEALTH
IFVENTILATIONISINADEQUATE
USEANAPPROVEDRESPIRATOR
12287-3
WARNING
BESURESUPPLY LINES ARE SECURE
DONOTEXCEED 120 PS I (8.25 BARS)
ORDAMAGETO MACHINE AND OR
BODILYHARMMAY RESULT
12287-1
12287-42
12287-38
1
12287-36
12287-36
12287-37
12287-43
READ&UNDERSTAND OWNERS MANUAL COMPLETELY.
TIGHTENALLLOOSE BOLTS INSPECT ALL LINES, PIPES, AND HOSES FOR DAMAGE.
REPAIRASNECESSARY.
DRILLSTEELMUST NOT BE BINDING IN GUIDE BEARING. MAKE SURE DRILL STEEL
ISSTRAIGHT,FREE OF OBSTRUCTIONS, AND NOT BINDING IN ANYWAY.
FILLTHEOILER-PER MANUAL.
WARNING
KEEPGUARDS I N PLACE
DISCONNECT POWER
BEFORE SERVICING
12287-12
INSTALLLOCK
PINPRIOR TO
TRANSPORTINGMACHINE
12287-7
INSTALLLOCK
PINPRIOR TO
TRANSPORTINGMACHINE
12287-7
INSTALLLOCK
PINPRIOR TO
TRANSPORTINGMACHINE
12287-7
INSTALLLOCK
PINPRIOR TO
TRANSPORTINGMACHINE
12287-7
DRILLHAMMERSWILLNOT
FUNCTIONWHENINDICATORISRED
WHENINDICATORSISREDFILL OIL RESERVOIR
WITHPROPERROCKDRILLLUBRICANT
GREENINDICATESLUBRICATORRESERVOIRISFULL
Bio-RockDrill
Oil 15W50
TM
MinnichMfg.Recommended Rock Drill Oil
WARNING
STANDCLEAR
WHENRAISINGOR LOWERING
12287-10
WARNING
STANDCLEAR
WHENRAISINGOR LOWERING
12287-10
Pick Point
HIGHPRESSURE
BLEEDAIRPRESSURE
BEFORESERVICING
DRILLSWILL
AUTOMATICALLYSTART
WHENAIRSUPPLY IS LOST
ANDREAPPLIED 12287-64
WARNING
DRILLSWILL
AUTOMATICALLYSTART
WHENAIRSUPPLY IS LOST
ANDREAPPLIED 12287-64
WARNING
WARNING
NOISEMAY
DAMAGEHEARING
WEARPROPERHEARING
PROTECTION
FLYINGPARTICLESMAYCAUSE
EYEINJURIES
WEARPROPEREYE
PROTECTION
HIGHPRESSURE
KEEPAWAYFROMLEAKS
BLEEDDOWNBEFOREREMOVING
LINESTOSERVICE
DUSTCANCAUSEINJURY TO
YOURHEALTH
IFVENTILATIONISINADEQUATE
USEANAPPROVEDRESPIRATOR
12287-3
WARNING
BESURESUPPLY LINES ARE SECURE
DONOT EXCEED 120 PSI (8.25 BARS)
ORDAMAGE TO MACHINE AND OR
BODILYHARMM AY RESULT
12287-1
12287-42
12287-38
1
12287-36
12287-36
12287-37
12287-43
READ& UNDERSTAND OWNERS MANUAL COMPLETELY.
TIGHTENALL LOOSE BOLTSINSPECT ALL LINES, PIPES, AND HOSES FOR DAMAGE.
REPAIRAS NECESSARY.
DRILLSTEEL MUST NOT BE BINDING IN GUIDE BEARING. MAKESURE DRILL STEEL
ISSTRAIGHT,FREE OF OBSTRUCTIONS, AND NOT BINDING IN ANYWAY.
FILLTHE OILER-PER MANUAL.
WARNING
KEEPGUARDS IN PLACE
DISCONNECT POWER
BEFORE SERVICING
12287-12
INSTALLLOCK
PINPRIOR TO
TRANSPORTINGMACHINE
12287-7
INSTALLLOCK
PINPRIOR TO
TRANSPORTINGMACHINE
12287-7
INSTALLLOCK
PINPRIOR TO
TRANSPORTINGMACHINE
12287-7
INSTALLLOCK
PINPRIOR TO
TRANSPORTINGMACHINE
12287-7
DRILLHAMMERSWILLNOT
FUNCTIONWHENINDICATORISRED
WHENINDICATORSISRED FILL OIL RESERVOIR
WITHPROPERROCKDRILL LUBRICANT
GREENINDICATESLUBRICATORRESERVOIRIS FULL
Bio-RockDrill
Oil 15W50
TM
MinnichMfg.Recommended Rock Drill Oil
WARNING
STANDCLEAR
WHENRAISING OR LOWERING
12287-10
WARNING
STANDCLEAR
WHENRAISING OR LOWERING
12287-10
Pick Point
HIGHPRESSURE
BLEEDAIRPRESSURE
BEFORESERVICING
DRILLSWILL
AUTOMATICALLYSTART
WHENAIRSUPPLY IS LOST
ANDREAPPLIED 12287-64
WARNING
DRILLSWILL
AUTOMATICALLYSTART
WHENAIRSUPPLY IS LOST
ANDREAPPLIED 12287-64
WARNING
WARNING
NOISEMAY
DAMAGEHEARING
WEARPROPERHEARING
PROTECTION
FLYINGPARTICLESMAYCAUSE
EYEINJURIES
WEARPROPEREYE
PROTECTION
HIGHPRESSURE
KEEPAWAYFROMLEAKS
BLEEDDOWNBEFOREREMOVING
LINESTOSERVICE
DUSTCANCAUSEINJURY TO
YOURHEALTH
IFVENTILATIONISINADEQUATE
USEANAPPROVEDRESPIRATOR
12287-3
WARNING
BESURESUPPLY LINES ARE SECURE
DONOT EXCEED 120 PSI (8.25 BARS)
ORDAMAGE TO MACHINE AND OR
BODILYHARMM AY RESULT
12287-1
12287-42
12287-38
1
12287-36
12287-36
12287-37
12287-43
READ& UNDERSTAND OWNERS MANUAL COMPLETELY.
TIGHTENALL LOOSE BOLTSINSPECT ALL LINES, PIPES, AND HOSES FOR DAMAGE.
REPAIRAS NECESSARY.
DRILLSTEEL MUST NOT BE BINDING IN GUIDE BEARING. MAKESURE DRILL STEEL
ISSTRAIGHT,FREE OF OBSTRUCTIONS, AND NOT BINDING IN ANYWAY.
FILLTHE OILER-PER MANUAL.
WARNING
KEEPGUARDS IN PLACE
DISCONNECT POWER
BEFORE SERVICING
12287-12
INSTALLLOCK
PINPRIOR TO
TRANSPORTINGMACHINE
12287-7
INSTALLLOCK
PINPRIOR TO
TRANSPORTINGMACHINE
12287-7
INSTALLLOCK
PINPRIOR TO
TRANSPORTINGMACHINE
12287-7
INSTALLLOCK
PINPRIOR TO
TRANSPORTINGMACHINE
12287-7
DRILLHAMMERSWILLNOT
FUNCTIONWHENINDICATORISRED
WHENINDICATORSISRED FILL OIL RESERVOIR
WITHPROPERROCKDRILL LUBRICANT
GREENINDICATESLUBRICATORRESERVOIRIS FULL
Bio-RockDrill
Oil 15W50
TM
MinnichMfg.Recommended Rock Drill Oil
WARNING
STANDCLEAR
WHENRAISING OR LOWERING
12287-10
WARNING
STANDCLEAR
WHENRAISING OR LOWERING
12287-10
Pick Point
A
D
II
F
G
C
N
L

Dowel Drill Manual 12
MACHINE SPECIFICATIONS
A-2C Drill, On Slab with Steering
Model A-2C
Drill Steel Shank .875” x 4.25”
(2.22cm x 10.79cm)
Drill Steel Length (Under Collar) 24” (61.0cm)
Drill Bit Diameter .625” - 2.5”
(15.9mm - 63.5mm)
Maximum Drill Depth* 18” (45.7cm)
Drill Distance from Top of Slab 1.5” x 11.75”
(3.8cm x 29.8cm)
Minimum Cutout Width 48” (121.9cm)
SCFM Required 92.2 (2.61 m³/min)
PSIG Required 90 (6.2bar)
Weight 700lbs (317.5kg)
Specifications shown are standard. Variations to the standard are available.
*Based on 2 piece steel and bits. Whirly bits should be 1” (2.5cm) longer for maximum drilling depth.
Three position drilling: Horizontal, Vertical and 35° Stitch
Urethane filled tires
Larger oiler for easy maintenance
Adjustable drill height, depth and centers
Dust collection is available

13
Dowel Drill Manual
PRESSURE REGULATOR
OPERATION
ADJUSTMENT
MAINTENANCE
A regulator is used in a compressed air system to maintain nearly constant outlet pressure despite changes in the inlet air pressure and
changes in downstream ow requirements. Outlet pressure is controlled by the adjusting screw (1). clockwise rotation increases and
counter- clockwise rotation decreases outlet pressure setting. When the adjustment (1) is rotated fully counter- clockwise, no force is ap-
plied to the regulating spring (2), and the valve (6) is held closed by the valve spring (7). clockwise rotation of the adjustment (1) compresses
the regulating spring (2) which applies a downward force on top of the diaphragm (4). The diaphragm (4) and valve pin (5) move downward
forcing valve (6) off its seat (10) which allows air to ow through the regulator to the downstream system. Outlet pressure increases in the
downstream system and sensing chamber (9) and applies an upward force on bottom of the diaphragm (4). The diaphragm (4), valve pin (5);
and valve (6) move upward, compressing the regulator spring (2). Upward movement stops when the forces below the diaphragm balance the
forces above the diaphragm. When there is no downstream ow demand, the balance of forces occurs with the valve (6) closed. When there
is downstream ow demand, the balance of forces occurs when the valve opens sufciently to compensate for demand, thus maintaining the
desired outlet pressure. RELIEVING TYPE REGULATORS. With relieving regulators, outlet pressure can be reduced even though the system
is deadended. When the adjustment (1) is turned counterclockwise, the force on the regulating spring (2) is reduced, and air pressure in the
sensing chamber (9) moves the diaphragm (4) upward. This upward movement opens the relief passage (8) in the diaphragm and allows air to
escape from the outlet side of the regulator through the relief passage (8) and vent (3) to atmosphere. As the outlet air pressure decreases to
the reduced pressure setting, the diaphragm moves downward and closes the relief passage. The diaphragm will likewise move upward in a
response to an increase in outlet pressure above the regulator setting, allowing air to escape to the atmosphere as described above. Howev-
er, the ow capacity of the relief passage is limited, and depending upon the source of the overpressure condition, the outlet pressure might
increase to a point signicantly higher than the regulator setting. For this reason, the relief feature of a regulator must not be relied upon as an
overpressure safety device. See WARNING note below.
1. Before turning on system air pressure, turn regulator adjustment coun-
terclockwise until all load is removed from regulating spring.
2. Turn on system air pressure.
3. Turn regulator adjustment clockwise until the desired outlet pressure is
reached.
4.To avoid minor readjustment after making a change in pressure setting,
always approach the desired pressure from a lower pressure. When re-
ducing from a higher to a lower setting, rst reduce to some pressure less
than the desired, then bring up to the desired point.
5. Tighten jam out to lock pressure setting.
The regulator can be disassembled for servicing without removal from
pipe line. to disassemble, shut off the inlet air and reduce pressure in
inlet and outlet lines to zero. Turn adjusting screw (1) counterclockwise
until all load is removed from regulating spring (7 or 7a): Remove bonnet
screws (4), bonnet (3), upper springrest (5), spring (7), and diaphragm as-
sembly (8). The intermediate springrest (6) and compound spring (7a) are
used only on 3/4” (19mm) and 1” (25.4mm) models with 5 to 125 PSI (0.34
to 8.62 Bar) adjustment range. Unscrew and remove bottom plug (16),
O-ring (15) and valve spring (14). Pull valve assembly (11) together with
O-ring (12) out of body. Do not remove valve seat (10) unless replace-
ment is necessary. Remove O-ring (9) using a hook shaped tool, taking
care not to damage O-ring seating surfaces or valve seat. Clean parts
using warm water and soap. Dry thoroughly. Inspect each part carefully.
Replace any parts which are damaged. At reassembly, apply a wipe
coat of silicone base grease to O-rings (9, 12, 15), to stem and body of
valve assembly (11), and to center bore in bottom plug (16). Apply a light
even coat of light grease to full length of threads and tip of adjusting
screw (1). Tighten valve seat (10), if previously removed, to 80-100 inch-
pounds torque (9-11.3 N-m) (1/4”, 3/8” and 1/2” sizes) (6.35mm, 9.53mm,
and 12.77mm sizes) or 25-30 foot-pounds torque (33.9-40.7 N-m) (3/4”
and 1” sizes) (19mm and 25.4mm sizes). Tighten bottom plug (16) snugly
by hand. Tighten bonnet screws (4) to 20-30 inch-pounds torque (2.3-3.4
N-m) (1/4”, 3/8” and 1/2” sizes) (6.35mm, 9.53mm, and 12.77mm sizes) or
50-60 inch-pounds torque (5.6-6.8 N-m) (3/4” and 1” sizes) (19mm and
25.4mm sizes).
THESE REGULATORS ARE INTENDED FOR USE IN
INDUSTRIAL COMPRESSED AIR SYSTEMS ONLY.
DO NOT USE THESE REGULATORS WHERE PRES-
SURE OR TEMPERATURE CAN EXCEED RATED
OPERATING CONDITIONS. SEE SPECIFICATIONS.
IF OUTLET PRESSURES IN EXCESS OF THE
REGULATOR PRESSURE SETTING COULD CAUSE
DOWNSTREAM EQUIPMENT TO RUPTURE OR
MALFUNCTION, INSTALL A PRESSURE RELIEF DE-
VICE DOWNSTREAM OF THE REGULATOR. THE
RELIEF PRESSURE AND FLOW CAPACITY OF THE
RELIEF DEVICE MUST SATISFY SYSTEM REQUIRE-
MENTS.
BEFORE USING WITH FLUIDS OTHER THAN AIR,
FOR NON-INDUSTRIAL APPLICATIONS, OR FOR
LIFE SUPPORT SYSTEMS, CONSULT C.A. NOR-
GREN CO

Dowel Drill Manual 14
STANDARD SETUP
UNLOADING THE UNIT
If you’re A-2C unit is on a truck bed or other
plat-form and needs to be lifted into position,
use the
FILLING LUBRICATOR
Prior to lling the lubricator, be sure there is no
air pressure in the unit. Failure to relieve air pres-
sure will result in the ll plug exploding from the
lubricator, which may result in injury.
Remove ll plug and ll with lubricant until sight
gauge is full. Replace ll plug. Lubricator should
be lled every two hours of use for an A-2C. See
Recommended Lubricants chart on page XX for
acceptable lubricants.
MACHINE INSPECTION
Prior to each use, it is imperative to inspect the
machine all over to ensure excellent condition
for the safety of the operator and to prevent
damage to the equipment.
• Check all drill bed bolts and tighten as neces-
sary on a daily basis. Tighten all other bolts at
least once weekly. Refer maintenance diagram
on page 5-1.
• Grease ttings around drill bed daily. Grease
all other ttings at least once a week. Refer
maintenance diagram on page 5-1.
• Verify that all lock pins are in their locked posi-
tion.
• Make sure all controls are in the “off” position
and the lift lever is in the “up” position.
• Check that the air line is cleaned out and is the
proper size and pressure rating.
• Ensure the air compressor is set at an operat-
ing pressure of not more than 120 PSI (8.27bar).
• Install drill steel and bits into the drill motors
and close the latch retainers and rod guides.
AIR COMPRESSOR CONNECTION
• Connect the air line to the drill in accordance
with hose connection instructions in the com-
pressor manual.
• Start the compressor according to manufactur-
er’s instructions.
POSITION MACHINE FOR DRILLING
• Position the drill unit where the rst set of
holes is to be drilled, keeping the drill unit back
from the edge of the slab slightly. Set the brake.
• With the lift lock still engaged, charge the lift
cylinder by toggling the lift lever up and down.
• With the lift valve in the “up” position and after
making sure that there are no obstructions in the
path of the drill bed, remove the lift lock pin.
• Using the lift lever, lower the drill bed into drill-
ing position.
HEIGHT ADJUSTMENT
To check the drilling height, measure from the
top of the slab to the center of the drill steel.
If necessary, loosen the locknuts and use the
ad-justing screws to raise or lower the drill bed
into the proper drilling height. After height is
properly adjusted, re-tighten the locknuts.
Verify the drill bed is parallel with the slab that
is to be drilled into. If necessary, loosen the
locknut on the lift cylinder and turn the adjust-
ing screw right to raise the bed or left to lower
the bed until the bed is parallel with the slab.
Re-tighten locknuts after complete.
DEPTH ADJUSTMENT
Physical motion is going to occur, stand clear of
the drill unit.
To set the drill depth, remove all of the rail lock-
ing pins and feed the drill bit into the face of the
slab without turning on the drills by turning on
Feed 1 and the feed switch. Repeat for Feed 2,
when applicable. Measure the distance between
the drill stop rod and the drill stop pad. Ad-
just the stop bolt so that the distance between
the stop pad and the stop bolt equals the drill
depth.
DRILL TEST HOLE
Refer to operating instructions to drill the rst
set of holes. After the rst set of holes, measure
the height and depth of the hole to ensure prop-
er alignment.

15
Dowel Drill Manual
DRILLING OPERATIONS
1. Make sure the lubricator is full. See
recommended lubricants on page 3-1. A-1C
series units should be lled every two hours.
2. Use a 3/4” (19mm) hose to supply air to the
drill unit for A-1C series units.
3. Install the drill steel and bit into the drill.
4. Make sure the air compressor is on.
5. Position the drill where the rst hole is to be
drilled and set the brake.
6. Remove the rail locking pin.
7. Lower the rail to the horizontal drilling posi-
tion.
8. Make sure the rub strip is against the slab.
9. Using the feed control valve, feed the bit
against the slab.
10. Using the drill control valve, feed the bit
against the slab.
11. With the drill valve turned on and the feed
switch turned on, the slider and drill will move
and the drill will turn on. When the feed switch
is turned off, the slider is retracted from the
hole and the drill will turn off automatically. If it
does not, turn the drill switch off.
12. Once the hole is drilled, disengage the
brake and move the unit to the next hole loca-
tion, en-gage the brake, and repeat steps 8-11
as necessary.
13. There is a low-level oil indicator, this must
be “green” in order for the hammers to oper-
ate. If the indicator is “red”, please ll oil reser-
voir with proper rock drill oil.
PRIOR TO OPERATION
Wear proper safety equipment as the following
hazards may be present during operation:
• Flying Debris: During drilling, chips may be
ejected.
• Dust: Concrete dust will be emitted from the
hole.
• Loud Noise: The air compressor and drill unit
will create loud noise levels.
• Pinch Points: Keep clear of all moving parts.
This is not an all inclusive list. Be aware of your
surroundings and use any and all precautionary
measures available.
OPERATOR POSITION
Failure to follow the instructions below may re-
sult in serious injury.
The operator should always stand in a safe loca-
tion with good visibility where controls can be
easily reached. The operator should always stand
in a location so he/she is following the machine.
Never lead the machine with your back towards
it. Refer to the diagram below for proper operat-
ing positions.
DRILLING
• Place the feed levers in the “in” position to
move the bits against the face of the slab.
• Place the drill levers in the “on” position to
turn on the drill motors.
• When drill motors reach the required depth,
place the feed lever in the “out” position.
• When the drill steel is clear of the hole, place
the drill lever in the “off” position.
• Release the brake, position the drill for the
next set of holes, reset the brake, and repeat the
process until all holes are drilled.
MOVING THE UNIT
Move the unit by pushing or pulling to the de-
sired position. Be sure the operator is standing
in a safe location. See diagram below.
TURNING THE UNIT
Turn the unit by rotating the steering wheel
clock-wise or counterclockwise.

Dowel Drill Manual 16
Troubleshooting Air Drill
Cause Remedy
DRILL NOT GETTING AIR 1. On Multi Drill units, switch airline with drill
that is working properly. If drill now runs
check the air control valve. If the valve works,
check the drill.
2. Check clave on air compressor and drill unit
to be certain they are completely open
3. Check compressor. It should have 100SCFM
(47.20m^3/sec.) per drill and 110PSI (7.6 BAR)
at drill manifold when drilling with large drills.
4. Make certain all ttings are connected prop-
erly and not leaking.
COUPLING OR HOSE OBSTRUCTION Remove Obstruction
FAILURE IN THE ELECTRICAL CIRCUIT Check switches, connections, coils, ground &
voltage. If the power unit (backhoes, grader,
ETC.) is being jump started, check the AMPS &
voltage being jump supplied to coils from the
battery, it may be too low.
FAILURE OF DRILL SOLENOID VALUE
(MULTI DRILL UNITS WITH REMOTE
ELECTRICAL CONTROLS)
Check valve - you should be able to feel the so-
lenoid move when it is actuated. Make sure you
have current to the solenoid coil. Replace the
dolenoid if there is no movement.
MECHANICAL FAILURE OF DRILL Disassemble the drill & inspect for damaged
parts.
PROBLEM: DRILL DOES NOT RUN
Always disconnect the air supply before
changing steel or dismantling the tool for ser-
vice or repair. For maximum safety we advise
the installation of a shut-off valve at the end
of the air line.
DO NOT hit drill slider to retract the bit from
the hole. This will damage the drill slider.

17
Dowel Drill Manual
Troubleshooting Air Drill
Cause Remedy
NOT ENOUGH AIR REACHING
DRILL. IT SHOULD HAVE 100SCFM
(47. 2D M^3/sec.) PER DRILL AND 110
PSI (7.6 bar)
On Multi Drill units. Turn off one or two drills. If
the remaining drills pick up speed, check the air
compressor.
RESTRICTION IN AIR LINE A foreign object in the air line or possibly a
reduction in the air line caused by a reducer
tting.
TOO SMALL AIR LINE Following are supply line sizes for drilling:
A-1 Single Drill 3/4” (19mm)
A-2 Two Drills 1-1/4” (38.75mm)
A-3& A-4 Three & four drills 1-1/2” (38.1mm)
A-5 Five Drills 2” (50.8mm)
AIR PRESSURE TO CYLINDER “FEED-
ING” DRILL INTO CONCRETE NOT
ADJUSTED PROPERLY
Excessive pressure can cause drill to “bind up”
in the hole. Pressure that is too low will not
“feed” the drill into the concrete. The air pres-
sure required varies with the drill model.
Horizontal- all units with large drills use 22-26
PSI (1.5-1.8 bar). Drill units using the 15LB (6.8kg)
class drill will use 16-20 PSI (1.1-1.4 Bar).
Vertical - all drill units use 5-6 PSI (0.34-0.41
Bar). With the correct air pressure, the drill steel
should have a slight rattle.
INSUFFICIENT AIR FLOW TO KEEP
HOLE BLOWN CLEAN
Check for obstruction in the blow tube in the
drill.
LUBRICATOR PUTTING OUT TOO
MUCH OIL TO DRILL
If you notice more than a light lm of oil on the
air deector on the bottom of the drill adjust the
lubricator, make certain you are using the type of
oil called for in the operation and maintenance
manual.
MECHANICAL BLINDING OF DRILL
CARRIER
Make sure the eight bearing pads are adjusted
correctly. The square tube that the drill carrier
slides on must be free of rust so that the carrier
slides freely, drill steel must not be binding in
the guide bearing.
BENT DRILL STEEL, WORN DRILL BIT
OR DRILLING INTO REBAR
Replace the drill steel or bit. If drilling into rebar,
move the drill.
USING 3 1/4” (8.25cm) SHANK DRILL
STEEL IN 4 1/4” (10.8cm)SHANK
CHUCK DRILL
The drill steel will rotate but it will not allow the
drill piston to hammer properly, replace it with
the correct 4 1/4” (10.8cm) drill steel.
PROBLEM: DRILL RUNS SLOW OR DOES NOT DRILL EFFECTIVELY

Dowel Drill Manual 18
RECCOMENDED LUBRICANTS
Be sure lubricator is full. See recommended oils below.
Make sure slab wheels are square against face of slab.
Using feed control valve, feed bit against slab.
Using drill control valve, turn drill on and drill until the
drill slider is against the stop clamp, which should be
set for the required depth of hole.
Once drill slider is against the stop clamp, leave the
drill on and use the feed control valve to retract the
drill from the hole. Note: If bit will not retract from hole,
feed drill back into hole and retract drill again.
Step 1
Step 2
Step 3
Step 4
Step 5
Bio-Rock Drill™ Oil 15W50
Renewable
Lubricants

19
Dowel Drill Manual
DRILL STEEL
Warranty Policy
All drill steel and bits sold to customer are
intended for use in drilling concrete. It is not
capable of drilling through steel mesh, rebar
or dowel bars. Use in these applications will
void all warranties and dramatically shorten
bit life. Bit life is also affected by the sharp-
ness of the bit, type of aggregate and con-
dition of concrete. Minnich Manufacturing’s
drill steel and bit warranty is limited to the
warranty provided by the supplier. All war-
ranty claims must be submitted to Minnich
for evaluation and sent to the supplier for
authorization.
General Notes
1. 2” (50.8mm) diameter maximum bit for
hydraulic drills.
2. 2 1/2” (63.5mm) diameter maximum bit for
pneumatic drills.
3. 5/8” (16mm) diameter is the smallest hole
diameter.
4. Cutting speed varies from 15 to 30 sec-
onds for a 6” (152.4mm) deep hole, de
pending on bit diameter and aggregate.
5. On average you can get 180 holes, 9”
(228.6mm) deep per bit.
6. On average you can get 600 holes, 9”
(228.6mm) deep per drill steel.
7. Removable bits are carbide and cannot be
re-sharpened.
8. Whirly bit steel can be re-sharpened twice.

Dowel Drill Manual 20
DRILL STEEL
Part Number Hole Diameter Shank Size UC Length
005367-12.00 5/8” (15.9mm) 7/8” x 4 1/4” (22.2mm x 107.9mm) 12” (30.5cm)
005367-24.00 5/8” (15.9mm) 7/8” x 4 1/4” (22.2mm x 107.9mm) 24” (61.0cm)
004209-12.00 3/4” (19.1mm) 7/8” x 4 1/4” (22.2mm x 107.9mm) 12” (30.5cm)
004209-24.00 3/4” (19.1mm) 7/8” x 4 1/4” (22.2mm x 107.9mm) 24” (61.0cm)
004541-12.00 7/8” (22.2mm) 7/8” x 4 1/4” (22.2mm x 107.9mm) 12” (30.5cm)
004541-24.00 7/8” (22.2mm) 7/8” x 4 1/4” (22.2mm x 107.9mm) 24” (61.0cm)
004745-12.00 1” (25.4mm) 7/8” x 4 1/4” (22.2mm x 107.9mm) 12” (30.5cm)
004745-24.00 1” (25.4mm) 7/8” x 4 1/4” (22.2mm x 107.9mm) 24” (61.0cm)
All 4 1/4” (107.9mm) shanks can be cut to a 3 1/4” (82.55mm) Shanks
Part Number Shank Size UC Length
003749-12.00 7/8” x 4 1/4” (22.2mm x 107.9mm) 12” (30.5cm)
003749 -24.00 7/8” x 4 1/4” (22.2mm x 107.9mm) 24” (61.0cm)
004116-12.00 7/8” x 4 1/4” (22.2mm x 107.9mm) 12” (30.5cm)
004116 -24.00 7/8” x 4 1/4” (22.2mm x 107.9mm) 24” (61.0cm)
Tapered Steel
Notes
For 1” (2.54cm) Bits ONLY
003747-1.000
For 1 1/8” (2.86cm) & Larger
Bits ONLY
Tapered Bits
Part Number Shank Size UC Length
003747-1.000 1” (2.54cm) 003839-00000
003747-1.120 1 1/8” (2.86cm) 003901-00000
003747-1.180 1 3/16” (3.01cm) 003901-00000
003747-1.250 1 1/4” (3.18cm) 003901-00000
003747-1.310 1 5/16” (3.34cm) 003901-00000
003747-1.370 1 3/8” (3.49cm) 003901-00000
003747-1.430 1 7/16” (3.65cm) 003901-00000
003747-1.500 1 1/2” (3.81cm) 003901-00000
003747-1.560 1 9/16” (3.97cm) 003901-00000
003747-1.620 1 5/8” (4.13cm) 003901-00000
003747-1.750 1 3/4” (4.45cm) 003901-00000
003747-1.810 1 13/16” (4.60cm) 003901-00000
003747-1.880 1 7/8” (4.76cm) 003901-00000
003747-2.000 2” (5.08cm) 003901-00000
Notes
Use 003749-12.00 or 003749-24.00
Steel ONLY
Use 004116-12.00 or 004116-24.00
Steel ONLY
1 Piece Steel & Bit (Whirly Bit)
All 4 1/4” (107.9mm) shanks can be cut to a 3 1/4” (82.55mm) Shanks
Part Number Shank Size UC Length
005061-24.00 7/8” x 4 1/4” (22.2mm x 107.9mm) 24” (61.0cm)
05061B-24.00 1” x 4 1/4” (25.4mm x 107.9mm) 24” (61.0cm)
“H” Thread Steel
Part Number Hole Diameter
005140 -1.370 1 3/8” (3.49cm)
005140-1.500 1 1/2” (3.81cm)
005140-1.620 1 5/8” (4.13cm)
005140-1.750 1 3/4” (4.45cm)
005140-1.870 1 7/8” (4.76cm)
005140-2.000 2” (5.08cm)
005140-2.250 2 1/4” (5.72cm)
005140-2.500 2 1/2” (6.35cm)
“H” Thread Bits
Notes
Multiple use bit
All 4 1/4” (107.9mm) shanks can be cut to 3 1/4” (82.55mm) shanks
Table of contents
Other Minnich Drill manuals
Popular Drill manuals by other brands

Skil
Skil 2497 operating instructions
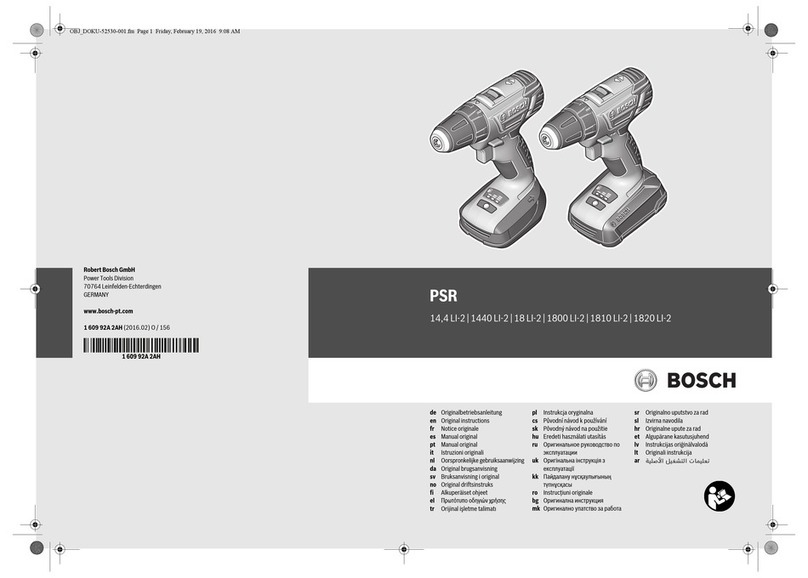
Bosch
Bosch PSR 1800 LI-2 Original instructions

ALFRA
ALFRA ROTABEST V32 Manual book
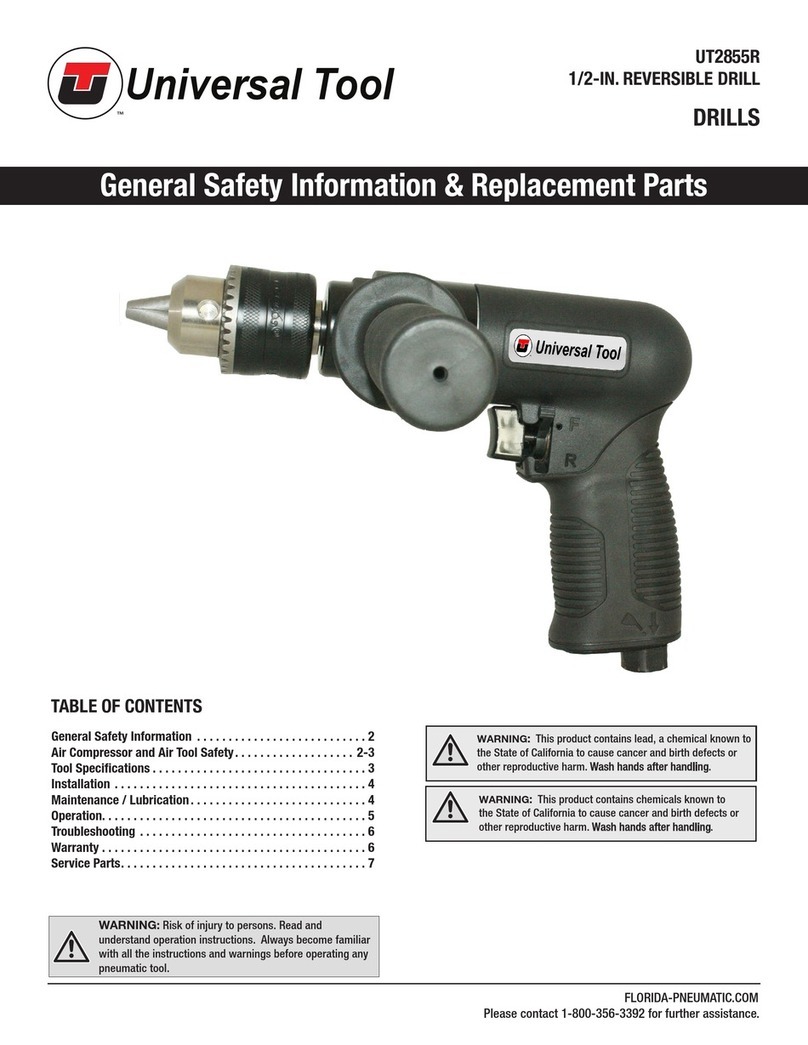
Universal Tool
Universal Tool UT2855R General Safety Information & Replacement Parts
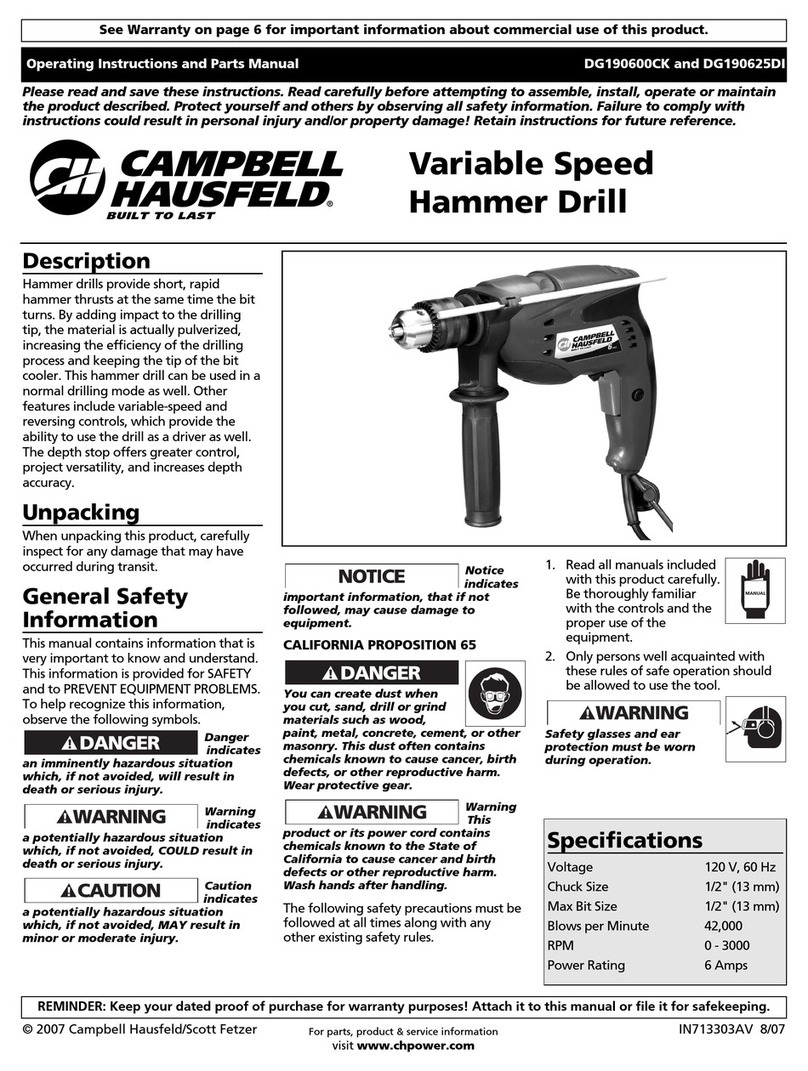
Campbell Hausfeld
Campbell Hausfeld DG190600CK S Operating instructions and parts manual

Makita
Makita BDF343 instruction manual
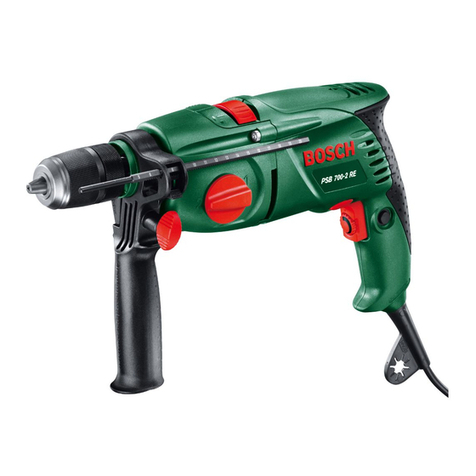
Bosch
Bosch PSB 700-2 RE operating instructions

Berner
Berner BACD-1 BL 12V Original instructions

Bosch
Bosch 060114E500 Original instructions

Narex
Narex EVP 13 G-2A Original operating manual

Howard Berger
Howard Berger Cordless Drill and Screwdriver brochure
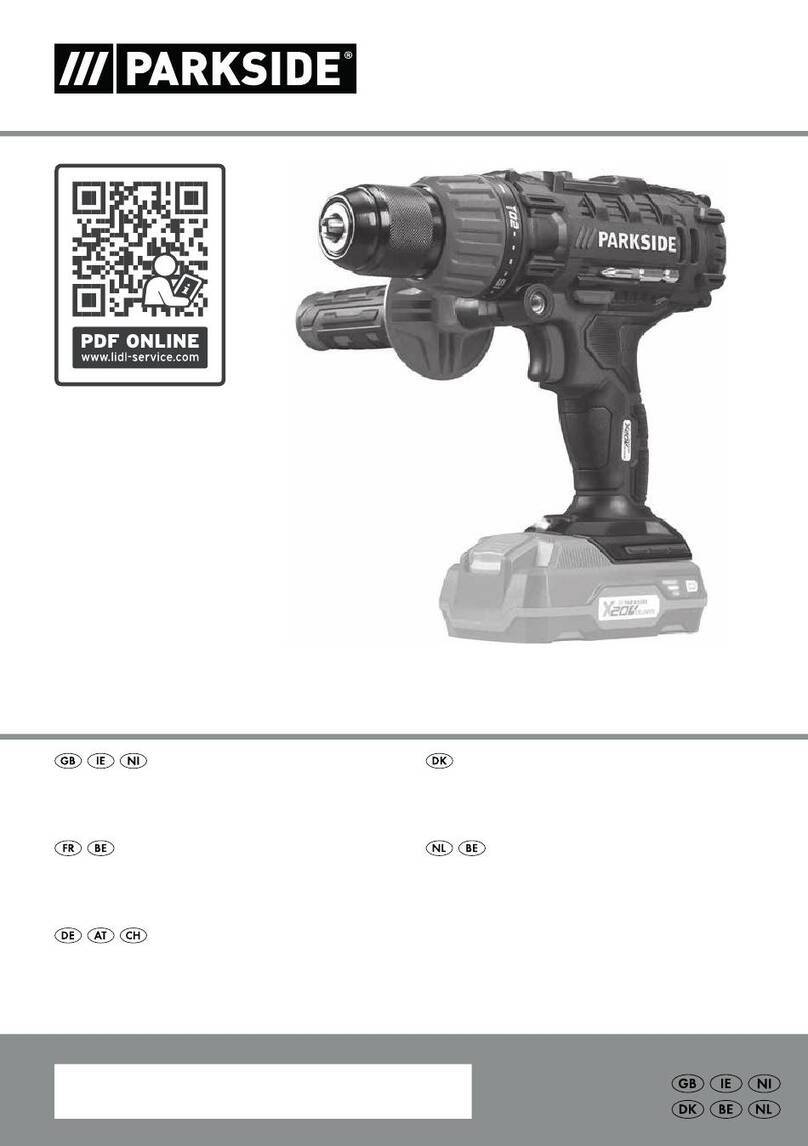
Parkside
Parkside PSBSA 20-LI B2 Translation of the original instructions