Moog G123-814 Supplement

1 Scope
These application notes are a guide to applying the G123-814
dual PWM Amplifier. They tell you how to install, connect and
adjust the PWM Amplifier. They do not tell you how to select
proportional valves or how to design a closed loop system.
2 Description
The G123-814 Dual PWM Amplifier is used to drive both coils
of a three position 24V solenoid operated proportional valve.
It is specifically intended for use in low end closed loop
applications. It allows a very low cost proportional valve to be
used where normally a much more expensive servovalve would
be needed. Coupling it with its companion servoamplifier, the
G122-824, and a proportional valve, produces an economical
closed loop solution.
For a more detailed description see data sheet G123-814
E01.01.
3 Applicability
The G123-814-001 has been structured to operate in a closed
loop and optimised with a Hydrolux WP series proportional
valve. The important specifications considered were the coils,
which are 24V @ 800mA, and the spool overlap, which is
12%. Output current is 25% higher than nominal to ensure
maximum flow is not overly compromised by valve production
tolerances and spool Benoulli forces. The deadband
compensation circuit, that cancels the spool overlap, has been
optimised on a flow stand and during field applications. The
dead band compensation is not user adjustable. Applying this
amplifier to other valves with the same specifications will
produce the same performance as achieved with the Hydrolux
valve.
The G12-814 is not suitable for traditional open loop
proportional valve applications. Because the deadband
compensation circuit cancels the spool overlap, it is highly
unlikely that a zero flow condition will result from zero
coil current.
4 Installation
4.1 Placement
A horizontal DIN rail, mounted on the vertical rear surface
of an industrial steel enclosure, is the intended method of
mounting. The rail release clip of the G123-814 should face
down, so the front panel and terminal identifications are
readable and so the internal electronics receive a cooling air
flow. An important consideration for the placement of the
module is electro magnetic interference (EMI) from other
equipment in the enclosure. For instance, VF and AC servo
drives can produce high levels of EMI. Always check the EMC
compliance of other equipment before placing the G123-814
close by.
Dual PWM Amplifier
G123-814
4.2 Cooling
Vents in the top and bottom sides of the G123-814 case
provide cooling for the electronics inside. These vents should
be left clear. It is important to ensure that equipment below
does not produce hot exhaust air that heats up the G123-814.
Application Notes
Bottom
vents
Cooling
airflow
release
Screw
terminals
Top vents
Screw
terminals
DIN rail
9 - 16
1 - 8
clip
Cover
release
tab ( )
DIN rial
1 3 4
910111
56 7 8
13 14 15 16
MOOG
cmd
zero
A
dither
B
dual PWM
Bottom
vents
Cooling
airflow
release
Screw
terminals
Top vents
Screw
terminals
DIN rail
9 - 16
1 - 8
clip
Cover
release
tab ( )
DIN rial
1 3 4
910111
56 7 8
13 14 15 16
MOOG
cmd
zero
A
dither
B
dual PWM
4.3 Wiring
The use of crimp “boot lace ferrules” is recommended for the
screw terminals. Allow sufficient cable length so the circuit
card can be withdrawn from its case with the wires still
connected. This enables the circuit to be checked while the
card is still connected and operating. An extra 100mm, for
cables going outside the enclosure, as well as wires connecting
to adjacent DIN rail units, is adequate.
Cables to the valve coils carry one Amp and so should be sized
accordingly. A conductor size of 0.2mm2is generally rated at
one Amp and is suitable for cable lengths up to five metres.
Longer cables should have 0.5mm2conductors.
4.4 EMC
The G123-814 emits radiation well below the level called for in
its CE mark test. However, the cables to the valve coils should
be screened to ensure no interfering radiation is emitted.
Connect the screens to chassis ground at each end. Use
terminals 10 and 14 on the G123-814.

Immunity from external interfering radiation is dependent on
careful wiring techniques. The accepted method is to use
screened cables for all connections and to radially terminate
the cable screens, in an appropriate grounded cable gland, at
the point of entry into the industrial steel enclosure. If this is
not possible, chassis ground screw terminals are provided on
the G123-814. Exposed wires should be kept to a minimum
length. Connect the screens at both ends of the cable to
chassis ground.
5 Power supply
24V nominal, 22 to 28V
45mA @ 24V without a load.
If an unregulated supply is used the bottom of the ripple
waveform is not to fall below 22V.
6 Input signal
The input command is 0 to ±10V. Input resistance is 100k
Ohm. An input of 0 to +10V causes a proportional current of
0 to 1 Amp in coil A. 0 to –10V causes a proportional current
of 0 to 1 Amp in coil B. These outputs result from the input
connected to the positive terminal. Connecting the input to
the negative terminal reverses the outputs. Connect the
unused input to signal ground (terminal 7). Connect the input
signal ground to the signal ground of the device supplying the
input signal.
7 Outputs
Both sides of each valve coil must be wired back to the G123-
814. Do not place any diodes across the coil. See paragraph
3.3 for advice on cable size.
8 Enable input
The output current drivers will not deliver current to the valve
coils until the enable input has a voltage of between 10 and
24V connected to it.
11 Front panel indicators
The “cmd”(command) LED indicates the polarity and level of
the input signal. Red is positive and green is negative.
The IA and IB LEDs indicate the level of the corresponding coil
current.
12 Withdrawing the circuit card
from its case
If access to the circuit is required, the circuit card needs to be
withdrawn from its case. To do this, push one tab in with a
pen or screwdriver while gently pulling on the top cover on
that side. The cover will release approximately one mm. Repeat
on the other side and withdraw the cover and circuit card until
the required circuit points are exposed. The rigidity of the
connecting wires will hold the circuit card in position while
measurements are made.
MOOG
cmd
zero
A
dither
B
dual PWM
LED
LED
LED
POT
POT
9 Dither
The front panel dither pot allows up to 100mA of 100Hz
dither to be superimposed on both coil currents. Dither is used
to overcome resolution limitations of the proportional valve
and is normally used if performance is being compromised by
the resolution of the valve. Optimum dither is achieved by
firstly increasing the level until it can be detected in the load
(the controlled variable, such as position). When this condition
is reached, reduce the level until its influence is just
undetectable in the load.
10 Zero
The zero pot allows up to 150mA coil current offset. Clockwise
rotation increases the offset to coil A. With your desired zero
input signal adjust the zero pot for the desired valve output
flow.

14 Specifications
Input: Differential
0 to ±10V
100 kOhm input resistance
Enable: +10V to +24V
2mA @ 24V
Outputs: Dual PWM @ 24kHz
1.0A ±0.1A
Maximum coil resistance: 22 Ohm
Coil current test 0 to –10V for 0 to 1A current
terminals:
Deadband compensation: ±12% nominal, not user adjustable
Dither: 100 Hz
0 to 0.1A
Zero: 0 to ±0.15A
Front panel indicators: Command –positive = red
negative = green
I(A) = red
I(B) = green
Supply: 24V nominal, 22 to 28V
45mA @ 24V, no load
Mounting: DIN rail
IP 20
Temperature: 0 to +40ºC
Dimensions: 100W x 108H x 22.5D
Weight: 130g
CE mark: EN50081.1 emission
EN50082.2 immunity
C tick: AS4251.1 emission
13 Block-wiring diagram
LED
cmd
++
+
+
zero
dither
+ 4V
+ 4V
1
+ 4V
+15V
-15V
+
+
A
B
Power Supply
Integrator
Integrator
PWM
PWM
3
5
6
ENABLE
input Input Amp
Dead Band
Compensation
11
1
9
13
15
16
Coil A
Coil B
test
test
Output A
Output B
LED
LED
7
terminal
terminal
8
4
10
14
+ 4V
0V
Supply
see note 1
+
0Vref
+
+
Differential
10V
B
B
0 to -10V
0 to -10V
0 to 1Amp
0 to 1Amp
Note: 1. Connect cable screen to enclosure cable gland
or chassis ground terminal on G1 3-814.

C31886
Moog Australia Pty. Ltd. ABN 50 005 599 584, 14 Miles Street, Mulgrave, Vic 3170. Telephone: + 61 3 9561 6044. Fax: + 61 3 9562 0246.
Moog Australia Pty. Ltd. pursues a policy of continuous development and reserves the right to alter designs and specifications without prior notice. Information contained herein is for guidance only and does not form part of a contract.
Australia: Melbourne Austria: Vienna Brazil: S~
ao Paulo Denmark: Birkerød England: Tewkesbury Finland: Espoo France: Rungis Germany: Böblingen, Dusseldorf Hong Kong: Shatin India: Bangalore
Ireland: Ringaskiddy Italy: Malnate (VA) Japan: Hiratsuka Korea: Kwangju-Kun Philippines: Baguio City Singapore: Singapore Sweden: Askim USA: East Aurora (NY)
This page left blank intentionally
Other Moog Amplifier manuals
Popular Amplifier manuals by other brands
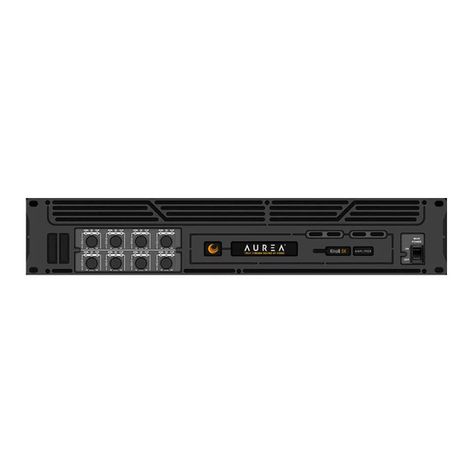
Aurea
Aurea Kino Series Operation manual
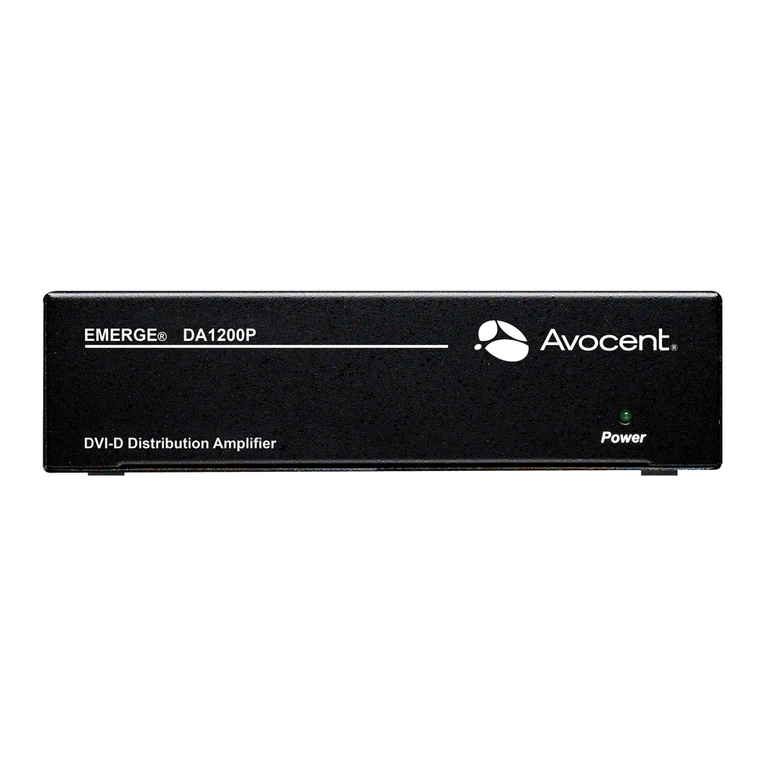
Avocent
Avocent Emerge DA1200P PC/VGA Technical specifications
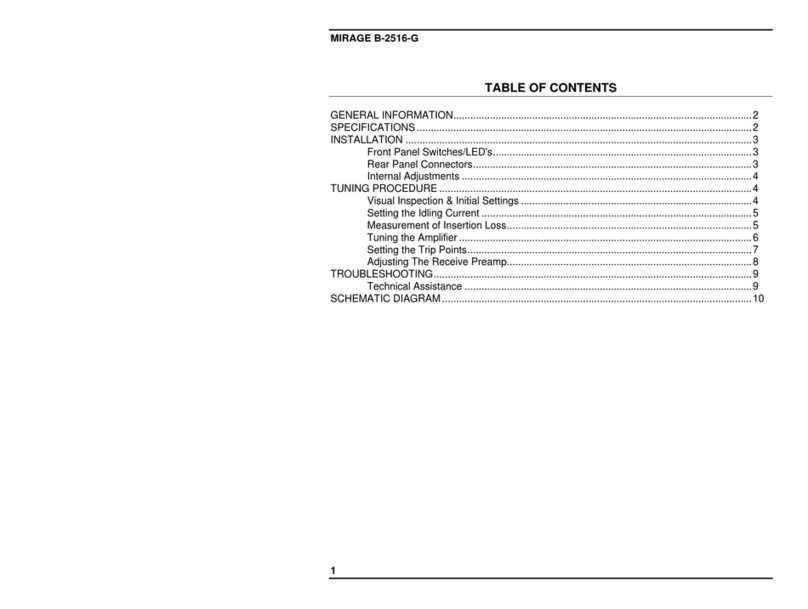
Mirage
Mirage B-2516-G quick guide
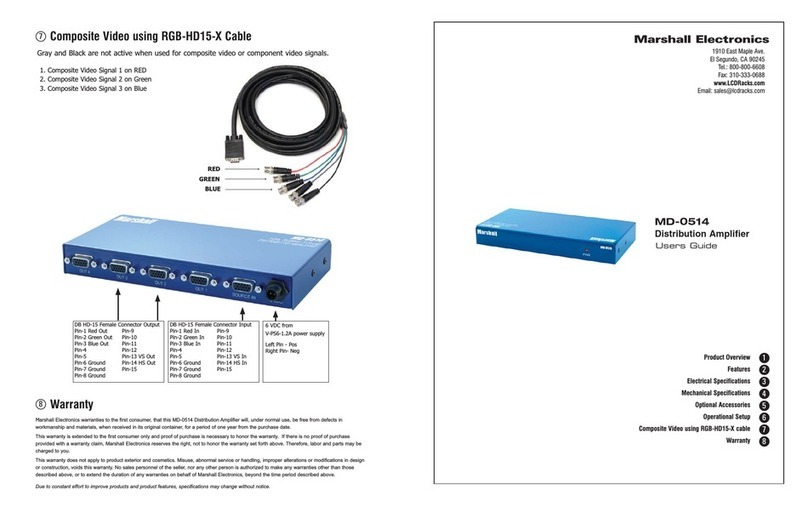
Marshall Electronics
Marshall Electronics MD-0514 user guide

ALLNIC AUDIO
ALLNIC AUDIO M-2500 owner's manual
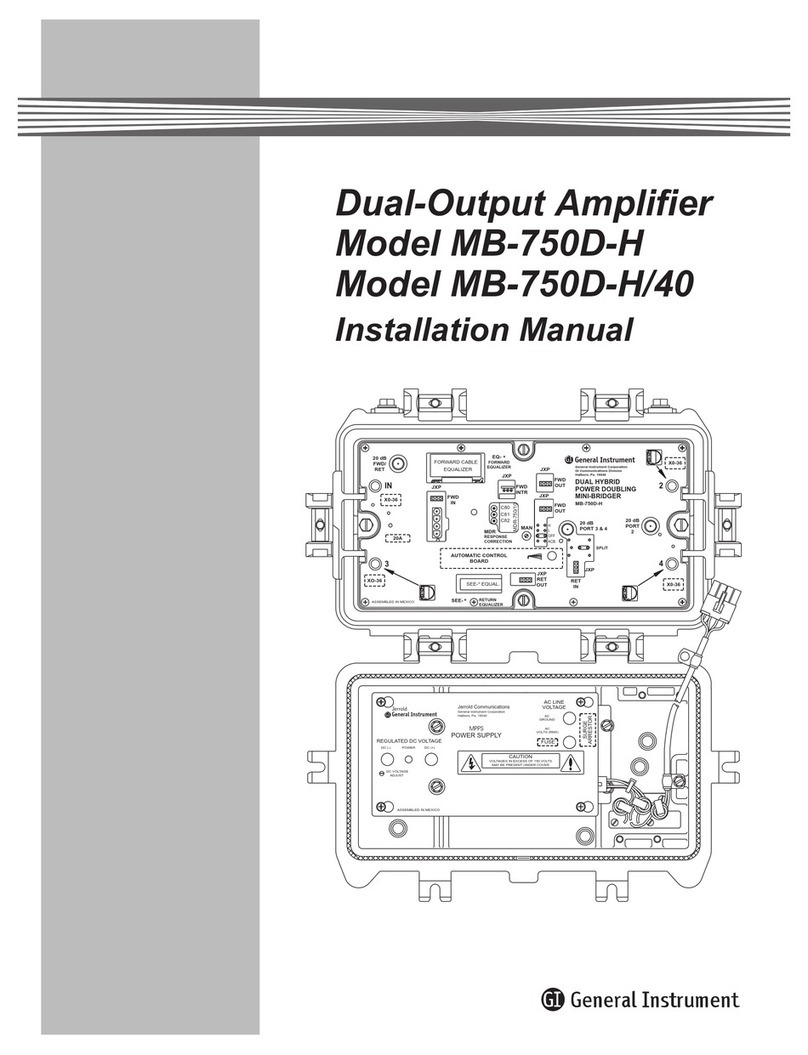
General Instrument
General Instrument STARLINE MB-750D-H installation manual