MULTIPRESS M5P Series Troubleshooting guide

1
SERIES “M5P” 6 TO 20 TON
Pacic Press Technologies/MULTIPRESS
714 North Walnut Street
Mount Carmel, IL 62863
618-262-8666
sales@pacic-press.com January 25, 2022
HYDRAULIC EQUIPMENT
OPERATING INSTRUCTIONS
AND SERVICE MANUAL


3
CONTENTS
INTRODUCTION
MANUAL SCOPE 6
SERVICE POLICY 6
MULTIPRESS EQUIPMENT WARRANTY 6
SAFETY 6
WARNING AND CAUTION TAGS 7
SPECIFICATIONS 8
INSTALLATION
INSTALLATION INSTRUCTIONS 11
ELECTRIC 11
RECOMMENDED OIL SPECIFICATIONS 11
FILLING THE OIL RESERVOIR 12
SEQUENCE OF OPERATION
STARTING THE PUMP AND MOTOR 15
INCHING 16
SET-UP 17
CYCLING 18
AIR IN SYSTEM 18
MAINTENANCE
GENERAL 21
MAINTENANCE AND INSPECTION 21
INSPECTION
DAILY INSPECTION 25
SAMPLE ROUTINE LOG 25
PERIODIC INSPECTION 27
SAMPLE PERIODIC LOG 27
RELIEF VALVE SERVICE
RELIEF VALVE OPERATION 31
CYLINDER SERVICE 31
MANIFOLD ASSEMBLY 33
M5P HYDRAULIC CIRCUIT 34
M5P HYDRAULIC CIRCUIT COMPONENTS 35
POSITIVE STOP ASSEMBLY 36
SAFETY PROCEDURES
SAFETY PROCEDURES CHECKLIST 39
TROUBLESHOOTING
BASIC TROUBLESHOOTING 41

4

INTRODUCTION

6
MANUAL SCOPE
This manual is intended as a reference when installing and preparing MULTIPRESS
equipment for operation, and for normal maintenance and equipment repair.
SERVICE POLICY
The simplicity of MULTIPRESS equipment, the unitized construction of its major
components, and observance of the instructions in this manual assure ease of
servicing by the user.
All eld service requested by the user and rendered by our factory
representatives will be charged at the established rate per day plus expenses.
MULTIPRESS equipment may be sent to our factory for inspection and service
only upon receipt of a purchase order for such service.
Current user requirements to be specied at time of order.
MULTIPRESS EQUIPMENT WARRANTY
The Seller warrants to the Buyer that on the date of shipment, the Goods shall be
in substantial conformity with the specications therefore and free from material
defects in workmanship or material subject to the condition that Seller receive
notice of a claim hereunder of shipment of Goods within six (6) months on labor,
one (1) year for MULTIPRESS manufactured Parts, (Purchased Component Parts
have original manufacturer’s warranty).
This is the sole warranty of the Seller and all other warranties whether express or
implied or written or oral are superseded hereby.
SAFETY
It is suggested for the user to be familiar with the current revision of ANSI B11.2,
"American National Standard for Machine Tools - Hydraulic Power Presses -
Safety Requirements for Construction, Care, and Use", for personal safety of the
press operator.

7
WARNING AND CAUTION TAGS
Please observe the Caution, Warning, and Note tags on the press (reproduced
below) and in this manual.
When components have been removed, some
additional cycling may be required to ensure the
entrapped air is removed and smooth operation
occurs.
NOTE
Never operate the press if the oil level is low, or if
the oil temperature is greater than 150°F. The use
of a cooler is recommended when the fluid
temperatures are expected to exceed 130°F.
CAUTION
TO PREVENT SERIOUS BOLIDLY INJURY:
NEVER use this machine without guards or safety devices that are
intended to prevent hands from remaining in the die space.
NEVER operate, service, or adjust this machine, or install dies,
without proper instruction and without first reading and
understanding the instructions in the operator’s manual.
NEVER install dies or service this machine with the motor on, or the
ram in an unblocked position.
WARNING

8
PRESS MODEL NO. M5P-5P* M5P-6 M5P-8 M5P-8P* M5P-12 M5P-15 M5P-20
TONNAGE MAX. 5 6 8 8 12 15 20
RAM
SPEED
I.P.M
ADVANCED 600 430 440 585 420 420 216
PRESS 235 210 165 140 165 165 106
RETURN 390 415 270 190 270 270 208
CYLINDERS
DIAMETERS
BORE 2 1/2” 2 1/2” 3 1/4” 3 1/4” 4” 4” 5”
ROD 1 3/4” 1 3/4” 2” 2” 2 1/2” 2 1/2” 3 1/2”
OPERATING
PRESSURE
MAX. 2,425 2,445 1,929 2,349 1,910 2,387 2,038
MIN. 489 489 386 470 382 477 408
RAM
EFFORT lbs.
MAX. 10,000 12,000 16,000 16,000 24,000 30,000 40,000
MIN. 2,000 2000 4,000 4,000 6,000 8,000 8,000
RESERVOIR CAPACITY gal. 16 16 16 16 23 23 23
APPROX SHIPPING WT. lbs. 1,040 990 1,025 1,075 1,375 1,400 2,150
SPECIFICATIONS
Figure 1 - Specications

9
MODEL A B C D E F G H I J K L
M5P-6 18 12 7 14 11.5 18 5 6.5 30.5 16.75 50.75 15.5
M5P-8 18 12 7 14 11.5 18 5 6.5 30.5 16.75 50.75 15.5
M5P-12/15 18 12 8 17 13.5 24 6 7.5 37.0 20.00 51.13 18.5
M5P-20 18 12 10 20 15.5 26 6 9.0 40.0 21.00 53.62 19.5
SPECIFICATIONS (CONT.)
MODEL AA* BB CC DD EE FF GG HH JJ KK
M5P-6 1.75 9 8.13 7/16 1/4-20 7/8-9 8 4 3 6
M5P-8 2.00 9 8.13 7/16 1/4-20 7/8-9 8 4 3 6
M5P-12/15 2.50 11 8.63 7/16 1/4-20 7/8-9 10 5 3 6
M5P-20 3.50 12 9.12 3/8 3/8-16 1-14 12 6 4 8
2 & 4 POST GUIDED TOOL PLATE 4 POST
MODEL A B C D E F G H I J K
M5P-6/8 8 18 6 12 3 6 1.5 7.875 15.75 2.375 4.70
M5P-12/15 10 21 6 12 3 6 1.5 9.125 18.25 3.625 7.25
M5P-20 12 22 17 14 4 8 1.5 19.625 19.25 4.250 8.50
Figure 2 - Guided Tool Plate

10

INSTALLATION

12
INSTALLATION INSTRUCTIONS
After removing the press from the shipping crate, stand the press upright near
the area where it will be anchored. Care should be taken to avoid twisting
or dropping the press during unpacking and transportation to the area of
operation.
ELECTRIC
Your standard press is wired to be connected to current user requirements as
specied when ordered. Connection of press to the users’ power source should
be accomplished by qualied personnel.
RECOMMENDED OIL SPECIFICATIONS
The warranty for MULTIPRESS equipment applies only when the proper hydraulic
uid has been used, and the oil contamination level is equal to, or better than
NAS...1638...CLASS NO. 8 OR BETTER. NO PARTICLES OVER 200 MICRON. “New”
oil as received, is not clean. Oil must be ltered via a 10 micron (or better) lter
before lling the reservoir. A lter cart is recommended.
Certain basic physical and chemical properties are necessary for proper
operation of MULTIPRESS. The following basic properties should be presented
to the uid supplier for their recommendation of a product for use in this
MULTIPRESS.
VISCOSITY @ 100°F - 300 SUS ±20 SUS
VISCOSITY INDEX - 90 OR HIGHER
RUST & OXIDATION INHIBITORS - YES
ANTI-FOAM ADDITIVE - YES
SPECIFIC GRAVITY .882 - .887 @ 60F/ 60F (API Gravity 29-31)
It is suggested that the uid supplier provide the user with certication that their
product meets the above requirements.
Do not permit the electric motor to operate
before the press reservoir is filled with oil, or to
operate in the wrong direction of rotation. See
STARTING PUMP & MOTOR (Page 14) and the
direction of rotation arrow plate on the pump
motor assembly.

13
FILLING THE OIL RESERVOIR
CLEANLINESS is the most important requisite in proper maintenance of the
hydraulic equipment. Of the few maintenance difculties encountered in the
operation of oil hydraulic equipment, many of them are directly traceable to
dirt or foreign matter In the oil.
EXTREME CARE should be exercised in maintaining a clean supply of oil in the
reservoir and the hydraulic system of your MULTIPRESS equipment at all times.
Make certain that no lint, dirt, abrasive scale, or other foreign materials enter
the hydraulic system. Trouble-free operation over a long period of time may be
obtained from the press by taking these precautions with the oil in the press. See
MULTIPRESS EQUIPMENT WARRANTY on Page 6.
The oil reservoir is lled through the oil ller cap, which is located on top of the
reservoir. Lift the ller cap and ll the reservoir with any clean oil meeting our
recommended oil specications on Page 10. Fill the reservoir to within 1” of the
top of the reservoir, or to the high mark on the oil level gauge if provided.
CONTAMINANTS ARE FOUND IN NEW OIL SO A FILTER CART SHOULD BE EMPLOYED
TO TRANSFER OIL INTO RESERVOIR.
Never operate the press if oil level is low, or if the
oil temperature is greater than 150°F. The use of a
cooler is recommended when fluid temperatures
are expected to exceed 130°F.

14

SEQUENCE OF
OPERATION

16
STARTING THE PUMP AND MOTOR
IMPORTANT: Prior to start-up:
1. Start and stop the electric motor in order to check proper rotation. There are
arrows clearly marked on the motor indicating the correct rotation. If this is
incorrect, check the wiring to the motor leads.
2. Lower the setting of the RELIEF VALVE by loosening the LOCKNUT and
then turning KNOB counterclockwise until loose but not removed. See the
PRESSURE ADJUSTMENT plate on the front of press.
If the motor is permitted to operate in the wrong
direction of rotation, the pump will be damaged
after only a few seconds due to lack of oil to
lubricate its precision machined internal parts.
When the oil in the reservoir is at the proper level
and the pump is operating in the correct direction
of rotation, the pump will prime.
If the press has been shipped to you with the ram
extended, it is necessary to put the selector switch
in the JOG UP position and then actuate the
pushbuttons. The ram should go up if the motor
and pump are operating in correct direction of
rotation. The pump will prime itself and provide
adequate lubrication.

17
INCHING
Set the selector switch to JOG DOWN. Simultaneously actuate and maintain
actuation of both CYCLE START buttons to the desired position of the ram.
Release of either button allows the ram to stop. Set the selector switch to JOG
UP. Actuation of the dual push buttons allows the ram to move up.
Ram may not retract if the RELIEF VALVE has been
backed out too far.
NOTE
Upper proximity or limit switch (1PRS) must be
actuated at the top of the stroke before switching
to CYCLE mode. If this switch is not made, the unit
will not cycle.
NOTE

18
SET-UP
JOG the press to your desired lower stop position allowing ram to exert full
pressure against a set up block or workpiece.
Adjust the pressure by loosening the relief valve LOCKNUT and turning the
relief valve KNOB on front or side of press (clockwise increases pressure,
counterclockwise decreases pressure). Set the selector switch and JOG the
ram just off the work. If included, set the lower proximity or limit switch (2PRS)
to that point. This adjustment allows you to select where the PLC takes over to
approach the work, achieve tonnage, and time reverse. JOG the ram to your
upper stop position. Set the upper proximity switch (1PRS) at that position.
Set-up tooling before setting pressure on the ram.
NOTE
The ram must contact a set-up block or workpiece
to deliver force, so the pressure GAUGE can be
read.
NOTE

19
CYCLING
Simultaneously actuate and maintain actuation of both CYCLE START buttons.
The ram extends until it contacts the work, achieves tonnage and reverses
or until the lower proximity switch (2PRS), if included, no longer senses the
RAM GUIDE BAR, and reverses. Release of the CYCLE START buttons before
contacting work or making lower proximity switch (2PRS) retracts the ram to its
upper stop position.
AIR IN SYSTEM
It is not unusual for air to be entrapped in the cylinder, lines, or controls during
initial start up procedures. Operate with the main relief adjustment at low setting
until erratic action or noise disappears. It may also be necessary to “crack” a
pressure line slightly to allow the air to escape. Re-tighten, and then proceed
normally.

20
This manual suits for next models
7
Table of contents
Other MULTIPRESS Power Tools manuals
Popular Power Tools manuals by other brands
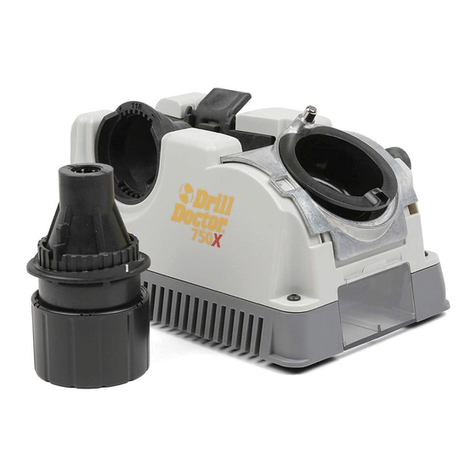
Drill Master
Drill Master Drill Doctor 750X user guide
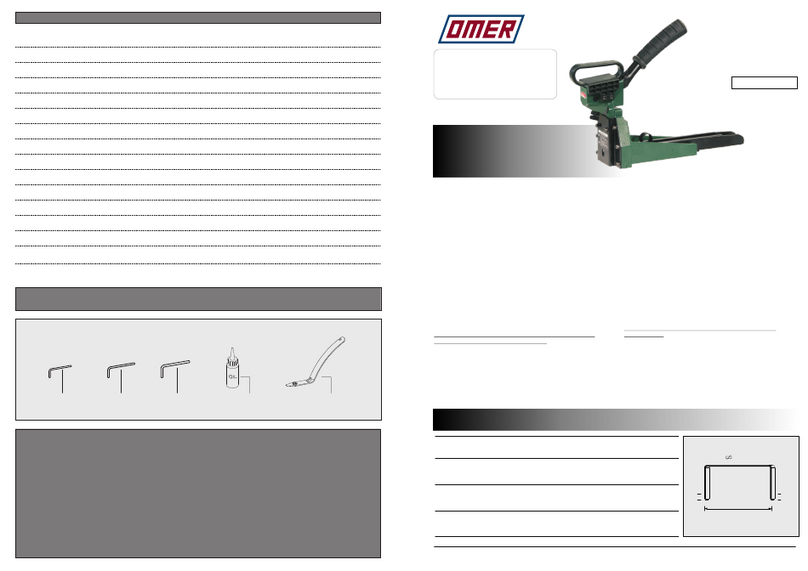
Omer
Omer 35.18 M Use, maintenance and spare parts manual
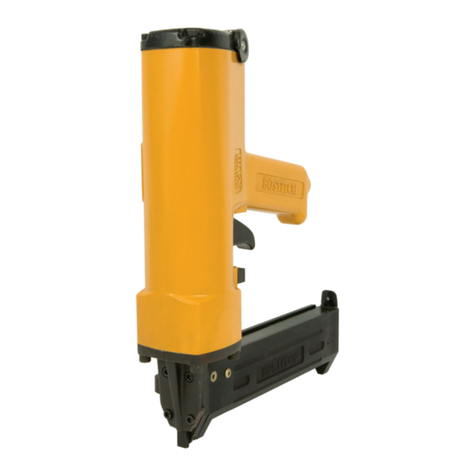
Bostitch
Bostitch MARK III Operation and maintenance manual
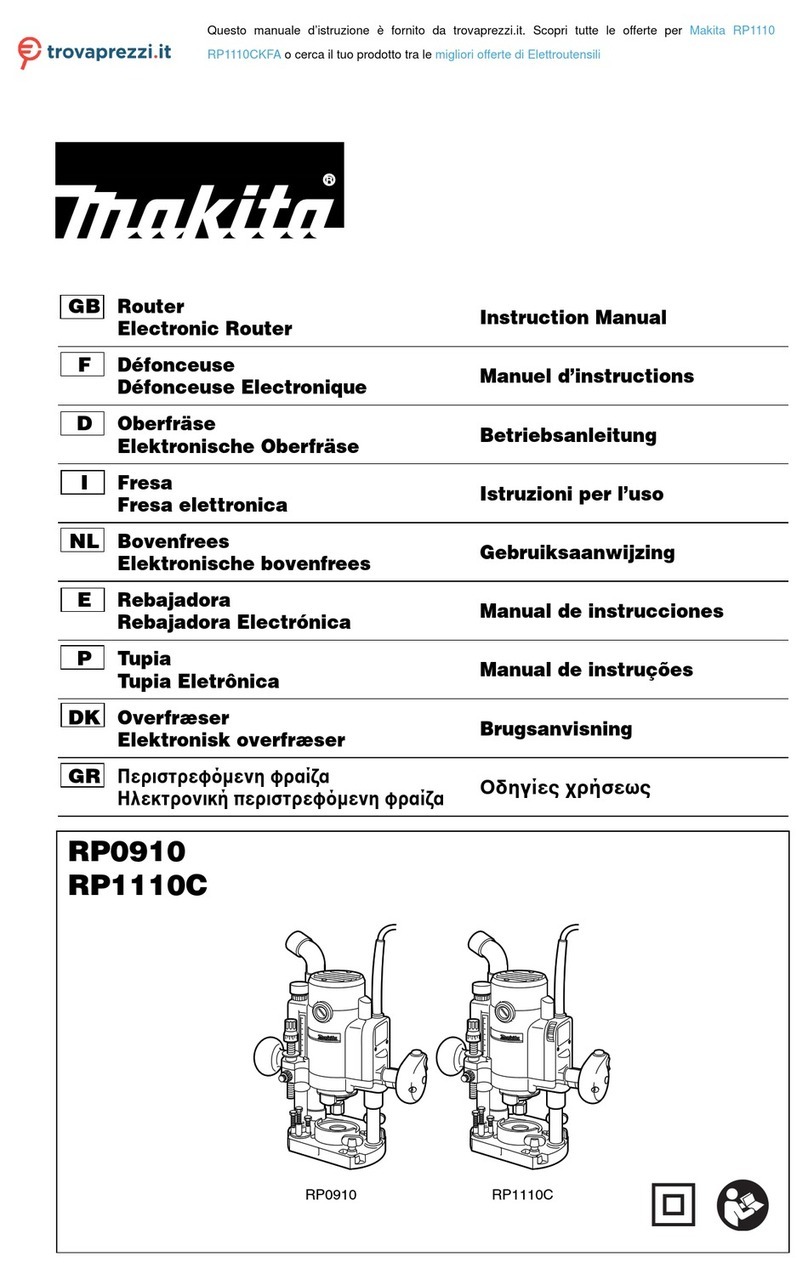
Makita
Makita RP1110 instruction manual

Orange Electronic
Orange Electronic M207 user manual
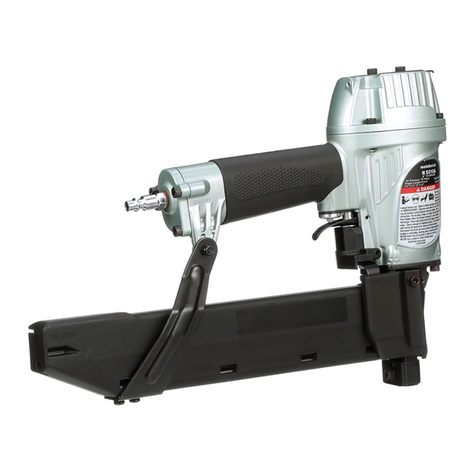
Hitachi
Hitachi N 5010A Instruction and safety manual