Nagano Keiki ZT11 User manual

Doc. No: TY-ZT11-004A Ver. 3
User's Manual for ZT11 Pressure Sensor
for Semiconductor Industry
8.1

2 TY-ZT11-004A Ver. 3
FOR PROPER AND SAFE USE
Thank you for purchasing the ZT11 Pressure Sensor for the Semiconductor Industry. To use this
product properly and safely, read this User's Manual carefully. This pressure sensor is for a gas supply
system and equipment for semiconductor manufacturing. Incorrect use of the product may cause
malfunction, resulting in failures or accidents.
After reading this Manual, keep it in a safe place for future reference.
■Definition of Safety Terms
The safety precautions in this manual are classified according to the following definitions.
Indicates an imminently hazardous situation which, if not avoided,
may result in death or serious injury.
Indicates the risk that users may suffer from damage including death
or serious injury.
Indicates the risk that users may suffer from minor injury and the risk
that only property damage may be caused.
■Description of Graphic Symbols
Graphic
symbols
Meaning
●Generally prohibited activities
Indicates prohibited activities in handling the product.
●General instructions
Indicates activities based on instructions that users are forced to
conduct.
●Other information
Indicates precautions, special operating methods, and other important
information.
WARNING
DANGER
CAUTION

3 TY-ZT11-004A Ver. 3
■Precautions for Handling Product
●Do not apply excessive load, vibration or shock. Damage to the
product and release of measuring fluid may be caused, which
results in injury or damage to the surrounding environment.
●Repeated applied pressure shall be within the rated pressure
range and shall not exceed the maximum allowable pressure.
Damage to pressure elements may be caused, which results in
injury or damage to the surrounding environment.
●This gauge is NOT an explosion-proof structure. Do not use the
product in Hazardous Areas where flammable gases or liquids
may be present.
●Do not use the product for measuring fluid corrosive to materials
of wetted parts or gas contact areas.
●Do not use batteries or power supplies not specified.
They may cause failure, fire or electric shock.
●Do not use the product if its failure or malfunction poses a direct
threat to human life or may cause personal injury.
●Do not modify the product. Disassembly or modification of the
product, or modification by adding new functions may cause harm
to human bodies.
●For applications where serious damage or accidents may occur
due to malfunction or failure of this product, use several units to
configure various protection circuits according to the degree of
seriousness of such damage or accidents, such as "1 out of 2",
"2 x (1 out of 2)", "2 out of 3", etc.
●When measuring fluid is oxygen, use a degreased product.
Oil may be left in general products, reacting with oxygen, and
causing fire or explosion.
!
WARNING

4 TY-ZT11-004A Ver. 3
●Conduct wiring correctly according to the
wiring procedure
described in the User's Manual.
Incorrect wiring may cause failures or fires.
●Use the product within the operating temperature range.
Otherwise, the product fails or is damaged, which causes injury or
damage to the surrounding environment.
●Install the product in accordance with the installation instructions in
the User's Manual.
●For repair, please contact us.
Disassembly or modification of the product on your own may cause
failures.
* These precautions are selected from our common safety precautions for all products that correspond to this
product. ZT11-specific precautions are further described in detail in the following sections.
CAUTION

5 TY-ZT11-004A Ver. 3
TABLE OF CONTENTS
FOR PROPER AND SAFE USE............................................................. 2
■Definition of Safety Terms ................................................................................................... 2
■Description of Graphic Symbols ........................................................................................ 2
■Precautions for Handling Product...................................................................................... 3
TABLE OF CONTENTS.......................................................................... 5
1. INTRODUCTION ................................................................................ 7
2. PRODUCT OVERVIEW ...................................................................... 7
■2.1 Overview.......................................................................................................................... 7
■2.2 Features........................................................................................................................... 7
■2.3 Operating Principle ........................................................................................................ 7
3. SPECIFICATIONS .............................................................................. 8
■3.1 Common Specifications ................................................................................................ 8
■3.2 Specifications for Each Grade...................................................................................... 9
4. DIMENSIONS ................................................................................... 10
■4.1 Typical Dimensions...................................................................................................... 10
5. TRANSPORTATION AND UNPACKING .......................................... 11
■5.1 Precautions for Transportation................................................................................... 11
■5.2 Precautions for Unpacking.......................................................................................... 11
6. INSTALLATION AND REMOVAL ..................................................... 11
■6.1 Installation..................................................................................................................... 11
7. WIRING AND CONNECTION ........................................................... 12
■7.1 Example of Wiring and External Connection ............................................................ 12
■7.2 Load Resistance........................................................................................................... 14
■7.3 Specifications of M12-connector Cable (option) ...................................................... 15
8. OPERATION (ENERGIZATION) ....................................................... 16
9. MEASURES AGAINST NOISE......................................................... 17
■9.1 Effects of Noise ............................................................................................................ 17
10. STORAGE ...................................................................................... 17
11. MAINTENANCE.............................................................................. 18
■11.1 Maintenance................................................................................................................ 18
■11.2 Zero Adjustment ......................................................................................................... 19

6 TY-ZT11-004A Ver. 3
12. PRODUCT WARRANTY/ EXPORT ADMINISTRATION REGULATIONS
........ 22
■12.1 Product Warranty ....................................................................................................... 22
■12.2 Export Administration Regulations.......................................................................... 22
13. OTHER ........................................................................................... 22

7 TY-ZT11-004A Ver. 3
1. INTRODUCTION
Check the specifications of the delivered model. Incorrect pressure range, power supply or output may
cause an accident. Make sure to use a model of the designated specifications in a location that meets
your use conditions and that it is properly wired and installed.
2. PRODUCT OVERVIEW
■2.1 Overview
This pressure sensor for the semiconductor industry converts pressure into an electrical signal for
transmission by means of a detector with an evaporated semiconductor strain gauge and a built-in
electronic circuit.
It has better temperature characteristics compared to those of the conventional one, and improves the
ease of use through a zeroing mechanism installed on the case side.
■2.2 Features
It is excellent in durability and stability due to use of a widely-proven vapor deposited (SS) sensor
element as well as an integrated structure design from the semiconductor strain gauge, pressure
sensor to pressure connection.
Design to greatly reduce the external leakage with a small dead zone where gas resides.
Absolute pressure range is available in addition to the gauge pressure range for a wide range of
applications.
■2.3 Operating Principle
The pressure receiving part of this instrument converts pressure into strain as a diaphragm and the
amount of strain is detected by the semiconductor strain gauge. The detection circuit is a full-bridge
type in which all four sides of the bridge consist of semiconductor strain gauges. The bridge circuit
gives an electric signal proportional to the strain, which is then amplified to a constant value in the
electric circuit and transmitted as direct current.
< Fig. 2-1 >
Detector
Amplifier
Circuit

8 TY-ZT11-004A Ver. 3
3. SPECIFICATIONS
■3.1 Common Specifications
Measuring fluid Various semiconductor process gases
Fitting type Single end and flow through integrated (forged)
Thread 1/4VCR®and 1/2 (3/8) VCR®compatible, 1/4UJR™
Dead volume Approx. 0.9 cm3
(will vary for single end and 1/4UJR™depending on the fitting type)
Pressure sensor sealing by welding
Pressure range
Gauge
pressure
0 to 0.3, 0.5, 1, 2, 3.5, 5, 10 and 20 MPa
- 0.1 to 0.3, 0.5, 1, 2, 3.5, 5, 10 and 20 MPa
Absolute
pressure 0 to 0.3, 0.5, 1, 2, 3.5, 5, 10, 20 MPa abs.
Supply voltage
10 to 30V DC
*See the following equation for the relationship bet. the supply voltage
and load resistance.
Load resistance R max. (Ω) = 50E − 500 (E: supply voltage)
Output 4 to 20 mA DC
Transmission system 2-wire system
Accuracy +/- 0.25%F.S. (at 23 deg. C)
(including linearity, hysteresis and repeatability)
Temperature Coefficient
(Zero/ Span)
+/- 0.02%F.S./ deg. C
Operating temp. range - 20 to 70 deg. C (no freezing or condensation)
Storage temp. range - 30 to 80 deg. C (no freezing or condensation)
Insulation resistance 100 MΩ or more (50V DC collectively for fitting to input-output terminal)
CE marking EMC Directive *1, RoHS Directive
UKCA marking EMC SI 2016 No.1091 *1, RoHS SI 2012 No.3032
Electrical connection M12 connector (4 pins)
Case material SUS305, PBT
Protection class IP67 (IEC 60529) *M12-connector cable in a mated state
Zeroing mechanism Side access (at case side surface)
Mass Approx. 70 g (will vary for single end depending on the fitting type)
< Table 3-1 >

9 TY-ZT11-004A Ver. 3
■3.2 Specifications for Each Grade
Grade EP GP
Surface roughness of
gas contact area
0.18 μm Ra Avg. 0.5 μm Ra Avg.
Gas
contact
material
Pressure
sensor
SUS316L
Fitting SUS316L
Max. allowable pressure
*2
150% of pressure range
Air-tightness (helium-
vacuum system) 5 × 10- 12Pa•m3/s or less
Particle Zero-count particles: 0.1 μm or more
(based on our inspection standards)
None
Cleaning Ultra-clean (cleaning) Degreasing cleaning
Recommended gas *3 High-purity gas, gas for
semiconductor materials, etc. Purge gas, exhaust gas, etc.
*1 Before use, connect the product to an indoor power distribution network that is not affected by lightning surge
voltages and power system switching transients.
*2 The maximum allowable pressure is the upper limit of pressure value which may safely be applied to the product
and remain in specification once pressure is returned to the rated range with a couple of times over-pressurization
for about 10 minutes. Effects of continuous over-pressure are not guaranteed.
*3 Make sure that the gas-contact material is suitable for the fluid to be measured.
●Using a device not specified in the User's Manual for electrical
connection requires confirmation with the manufacturer or expert of
such device to ensure its safety when used with other electrical devices.
< Table 3-2 >
WARNING

10 TY-ZT11-004A Ver. 3
4. DIMENSIONS
■4.1 Typical Dimensions
Single End Flow Through
* 2D matrix codes and alphabets laser-marked on the fitting or nut are used for the purpose of process control during
production at our factory and does not have an impact on product specifications.
* Type of pressure (gauge or absolute) can be easily identified by the color of the product label.
・Gauge pressure: Green
・Absolute pressure: Yellow-green
* QR code on the product label stores model and serial number information.
< Fig. 4-1 >
D=5
Air Inlet
(with filter)
One M12 In/out
connector
Zero Trimmer
HEX.
Zero Trimmer
Air Inlet
(with filter)
One M12 In/out
connector

11 TY-ZT11-004A Ver. 3
5. TRANSPORTATION AND UNPACKING
■5.1 Precautions for Transportation
This accurately-adjusted instrument may become inoperable when being dropped or given shocks.
Take extra care when transporting it.
■5.2 Precautions for Unpacking
(1) Check the appearance of a carton before unpacking it.
(2) Be careful not to roughly handle the package when unpacking.
(3) Unpack the product carefully to prevent accidental drop when removing it from the package.
(4) Open the sealed bag in a clean environment so that the gas contact area is not exposed to moisture,
dust, etc.
(5) After unpacking, make sure that the product is intact and that the model matches your order.
(6) If any abnormality is found, contact your purchasing agent or our sales office.
6. INSTALLATION AND REMOVAL
■6.1 Installation
(1) ZT11 pressure sensor, to be connected with union fittings such as a UJR™/VCR®integrated fitting,
needs to be connected in a specified manner using a designated gasket. When connecting the
sensor to the pressure line, do not tighten the main case body with a pipe wrench or similar tool.
During installation, always use the hexagon part of the thread or the square (hexagon) part of the
main unit.
(2) In addition to its IP67 equivalent protection grade (connector mating condition/IEC 60529), the life
of this product can be extended by selecting a place without direct sunlight and with little humidity
and dust, and a place not easily exposed to oil or water.
●Be careful not to block the air inlet on top of the case (see "4.
DIMENSIONS"). Otherwise, the specified performance cannot
be obtained.
●Do not apply excessive force to the case during installation.
●Never touch the gas contact area with your hands or blow on it.
Be careful not to damage the sealing surface.
●Do not apply excessive force on or severely bend the M12-
connector cable or the connector coupling to be connected to
this product. Also, during wiring, be careful not to subject the
product to the cable weight.
CAUTION

12 TY-ZT11-004A Ver. 3
●Use this product within the ambient temperature range of - 20 to
70 deg. C.
●The product with an absolute pressure range needs to be
installed in an environment with an atmospheric pressure of 70
kPa abs. or more (altitude: approx. 3,000 m or less). The
specified performance may not be obtained when the product is
used in an environment with extremely low atmospheric
pressure.
●This accurately-adjusted product may become inoperable when
being dropped or given shocks.
●Select an installation location with little vibration/dust, not
exposed to direct sunlight, and without external shock.
●Allow room for maintenance and adjustment around the product.
●Avoid snoop test for the sensor as it may cause insulation
resistance failure.
●It is recommended to fully purge the product with inert gas
before starting operation to remove atmospheric components,
particles and foreign matters within the pipe.
7. WIRING AND CONNECTION
■7.1 Example of Wiring and External Connection
Wiring and external connections should be made as follows. Insert the M12-connector cable into the
connector slot of this Instrument. Tighten the nut by hand until it does not move (tightening torque: 0.4
to 0.5 N·m).
< Table 7-1 >
Connector Terminal
Arrangement
Terminal No.
2-wire System
Cabling Color
Power (+)
Power (-)
Brown
White
Blue
Black

13 TY-ZT11-004A Ver. 3
< Output: 4 to 20 mA DC (current) >
* When using the same power supply to connect the equipment that causes surge or other phenomena,
a varistor or the like should be connected to protect the product.
Precautions for wiring are as follows.
●Do not pull the cable with excessive force or bend it severely.
●Do not perform wiring when the power is turned on.
●The M12 connector shall not be separated whilst energized.
●The degree of protection may be impaired if the nut of the M12-
connector cable is not tightened sufficiently. Also, be sure to
securely tighten the nut (thread) for potential loosening due to
vibrations (tightening torque: 0.4 to 0.5 N·m).
●Check the rated value specified for this product before
installation to determine the rated value of the power supply to
use. Ensure that the internal resistance of the connected
device is within the rated range of the load resistance applied
to the product.
●When soldering, be careful that the soldering iron does not
touch the case or the cable sheath.
●Use a stabilized power supply with a small ripple (noise)
fluctuation.
< Fig. 7-1 >
10 to 30V DC
Connector Terminal 1
Connector Terminal 3
Brown Cable
Blue Cable
Receiver
4 to 20 mA DC
Power (+)
Power (-)
CAUTION

14 TY-ZT11-004A Ver. 3
■7.2 Load Resistance
The following graph shows the relation between the load resistance and supply voltage.
R max (Ω) = 50 E − 500 (E: supply voltage)
0
100
200
300
400
500
600
700
800
900
1000
1100
10 11 12 13 14 15 16 17 18 19 20 21 22 23 24 25 26 27 28 29 30
Load Resistance (Ω)
Supply Voltage (V DC)
< Fig. 7-2 >
Operating Range

15 TY-ZT11-004A Ver. 3
■7.3 Specifications of M12-connector Cable (option)
The specifications of the M12-connector cable for wiring (option) are as follows.
Follow these specifications also for connectors to use if any.
PUR cable (oil-proof) PVC cable (stainless nut)
Straight
L-shaped
Material
①
Zinc die-cast
②TPU (green)
③
PUR (black)
①
Stainless-steel
②PP (white)
③
PVC (gray)
Cable
length (L)
3 m or 5 m 3 m or 5 m
Conductor
cross-
sectional
area
0.34 mm2 (22AWG) 0.34 mm2 (22AWG)
Insulator
outer dia.
1.27 mm 1.26 mm
Sheath
outer dia.
4.2 mm 4.7 mm
* Degree of protection of the M12 connector cable is ensured when it is in a mated state.
Please note that the white and black wires are not in use, which
are included in our optional 4-wire cable in addition to brown and
blue one. Also, the end of these unused wires needs to be
processed to avoid short-circuit.
< Table 7-2 >
CAUTION

16 TY-ZT11-004A Ver. 3
8. OPERATION (ENERGIZATION)
Before powering on, make sure once again that correct connections are established, and that the rated
voltage/current of the power supply as well as the internal resistance of externally connected
equipment are within the rated range of load resistance applied to the product.
When on, wait at least 15 minutes for warm-up (30 minutes recommended) to ensure system is
stabilized before performing zero adjustment as needed and starting a production run.
Zero adjustment can be performed by removing a resin cap on the case side. See the following section
"11.2 Zero Adjustment" carefully to make sure that the adjustment is correctly made.
Observe the following precautions during operation.
●Do not apply pressure exceeding the rated pressure indicated
on the ZT11 body label.
●Do not perform wiring or insert connectors while the power is
on. Otherwise damage to the product and electric shock may
result. Wire the cables according to the wiring diagram in "7.
WIRING AND CONNECTION".
●If corrosive gas is used, thoroughly purge the inside of the
instrument with nitrogen gas or other suitable gas when
removing this instrument for maintenance or other reasons.
Removing and leaving the instrument with the corrosive gas
residue inside may accelerate corrosion by strong acid or
alkaline substances that will be generated inside the instrument
due to atmospheric moisture or oxygen.
CAUTION

17 TY-ZT11-004A Ver. 3
9. MEASURES AGAINST NOISE
■9.1 Effects of Noise
If intermittent changes in measurement values or output are found, or if pressure values different from
actual ones are indicated, they may be affected by noise. Generally, sources of noise include power
supply, an output cable, peripheral equipment, and wiring. Values may be subject to effects of noise
depending on the installation place or position of the product. When you identify the source and take
the measures below, you can reduce effects of noise.
Radiation noise
• Keep the product away from the source
• Change the direction of the product toward the source to change an incidence angle to a board
• Install an electromagnetic shield to the source or the product
• Ground the instrument so that it is electrically connected to earth ground.
Induction noise
• Keep the product away from the wiring carrying high current
• Ground the instrument so that it is electrically connected to earth ground.
• Keep the product away from electrically charged machines or objects
Conductive noise
• Use the stable power supply that is difficult to generate noise
• Install power supply or output measurement equipment in an environment that is impervious to
being affected by noise
•Connect the shield to the earth with a highly noise-resistant cable such as a shielded cable.
10. STORAGE
Precautions in storing the instrument are as follows.
Do not store the product in the following locations.
They may cause failure, fire or electric shock.
●Locations subject to water
●Locations where adverse effects may occur due to atmospheric
pressure, temperature, humidity, ventilation, sunlight, dust, salt,
sulfur-containing air, etc.
●Locations subject to inclination, vibration or shock (including
those during transportation)
●Locations where chemicals are stored or gases are generated.
●Locations exposed to direct sunlight or in high-temperature cars
●Note that storing the product in a sealed bag under a high-
temperature or humid environment may deform or discolor the
resin parts of the product.
CAUTION

18 TY-ZT11-004A Ver. 3
11. MAINTENANCE
■11.1 Maintenance
A periodical maintenance once a half year will be needed due to possible aging under different
operating conditions. Also, perform calibration or zero adjustment as needed. Calibration should be
performed in a specified manner or at a designated calibration laboratory.
Refer to the following checklist for periodic inspections.
<Periodic Inspection Checklist>
•Appearance (scratches, cracks, deformation, corrosion, etc.)
•Corrosion condition of the pressure inlet
•Clogging at the air inlet
•Leakage check and thread re-tightening
•Double check and re-tighten the screws throughout the main body
•Insulation resistance between the case and all terminals tied (at 100 MΩ or more/50V DC or less)
•Output check with a reference pressure gauge and a measuring instrument
Avoid electrostatic charge.
When cleaning the exterior, use a soft, damp cloth.
Do not use thinner or benzene.
Otherwise, deterioration or malfunction may result.
CAUTION

19 TY-ZT11-004A Ver. 3
■11.2 Zero Adjustment
Remove the resin cap (with a simple fall-prevention function) from the case side as shown in Fig. 11-1.
●After powering on, wait at least 15 minutes for warm-up (30
minutes recommended) in an energizing state before performing
an adjustment.
●The factory-default movable area of the zero trimmer is
approximately 120 degrees to the left and right (approximately 240
degrees minimum to maximum). When turning the zero trimmer,
use the following cross slot driver without applying excessive
torque (within 5 m N·m).
Material: resin or ceramic
Size of cross slot driver (bit No. 0): shaft length of 10 mm or more,
shaft diameter of 2.8 mm or less
Recommended product: No. 9000 by Bessel
⊕
0 × 30
●For adjustment, use a traceable measuring instrument.
●Do not perform adjustments with moisture adhering to the product.
Moisture or other foreign matter entering the case may cause
malfunction.
●Never cause short-circuits with a driver (use a resin or ceramic
driver).
●Pulling the plastic cap hard will impair its simple fall-prevention
function. Be careful not to pull it too much (should be 1.1 N or less).
* Damage to the fall-prevention function will not affect the function of the
product itself as long as the plastic cap and gasket seal are intact. In this
case, cut the fall-prevention portion of the product before use.
Locked Opened
< Fig. 11-1 >
Fall Prevention
Zero Trimmer
Resin Cap Turn the resin cap
90° counterclockwise
to release the lock. Gasket Seal
CAUTION

20 TY-ZT11-004A Ver. 3
To perform zero adjustment, turn the "zero trimmer" in Fig. 11-1 with a cross slot driver. For
products in the gauge pressure, compound and absolute pressure ranges, refer to the following
as they have different procedures.
< Gauge pressure range >
Release the pressure applied to the sensor completely to the atmosphere (no-pressure state) and
adjust the sensor output to 4 mA DC.
< Compound range >
Calculate the output in the no-pressure state based on the following equation.
•4 to 20 mA DC output (current)
(Output in no-pressure state (mA DC)) = (16 mA DC) / ({upper limit pressure range (MPa)} − {−0.1 MPa}) × 0.1 + (4 mA DC)
e.g. (compound range of 0.5 MPa: 6.67 mA DC) / (compound range of 1.0 MPa: 5.45 mA DC)
Release the pressure applied to the sensor completely to the atmosphere (no-pressure state) and
adjust the sensor output to the value calculated above.
< Absolute pressure range >
Vacuum with a vacuum pump or other means (check the vacuum level with a vacuum meter if
available). In the vacuum state, adjust the sensor output to the "output conversion value based
on the degree of vacuum" ≒4 mA DC.
●Do not perform zero adjustment for products with the absolute
pressure range when pressure is released to the atmosphere
(no-pressure state).
CAUTION
Table of contents
Popular Security Sensor manuals by other brands
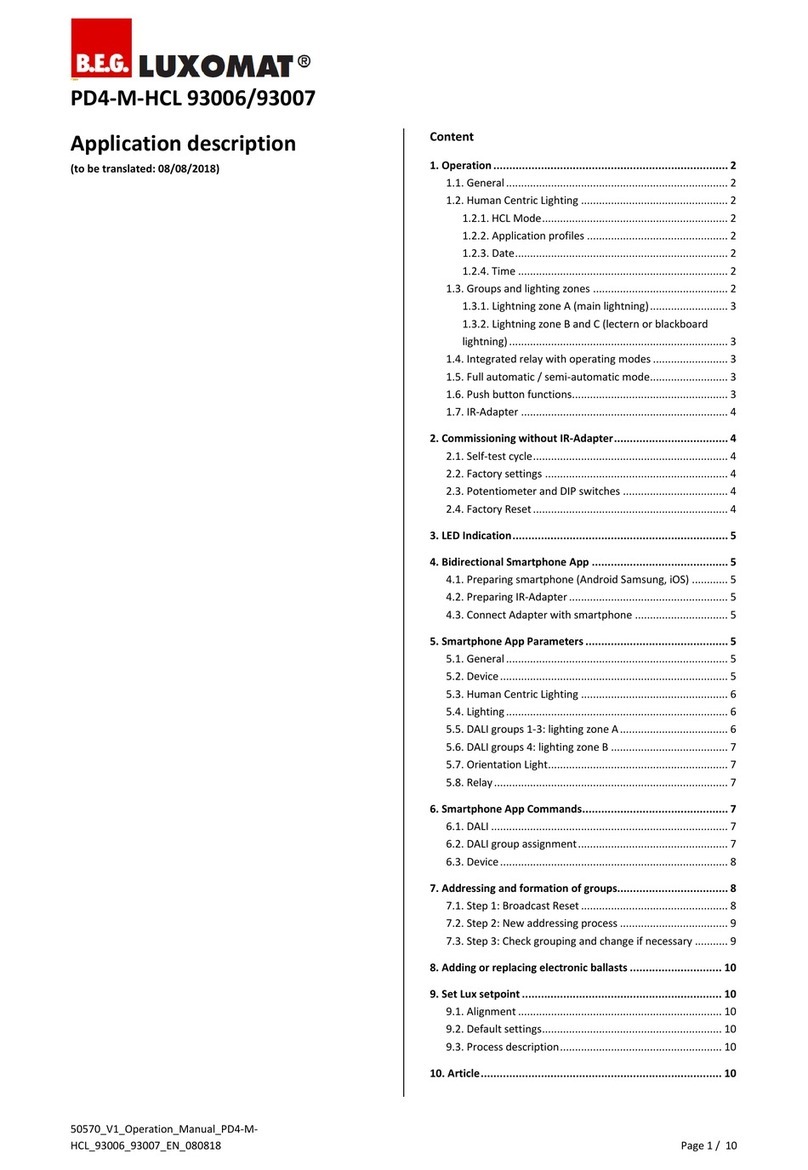
B.E.G. LUXOMAT
B.E.G. LUXOMAT PD4-M-HCL-FC Application description
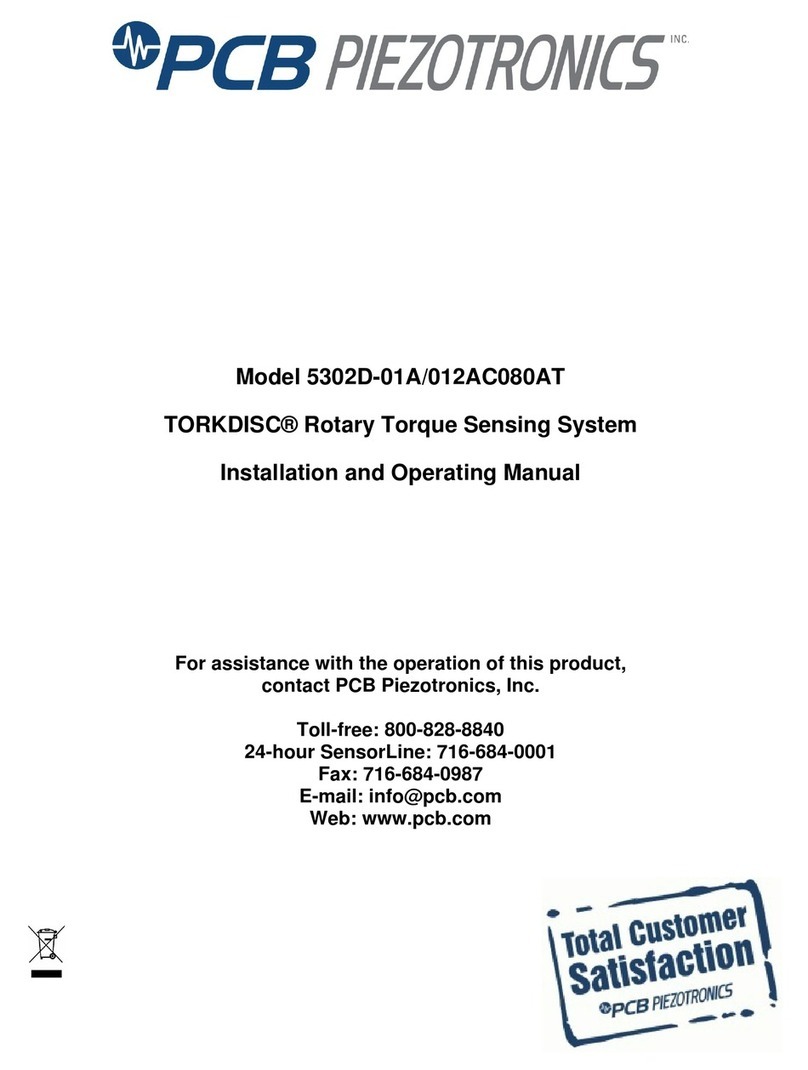
PCB Piezotronics
PCB Piezotronics TORKDISC 5302D-01A/012AC080AT Installation and operating manual
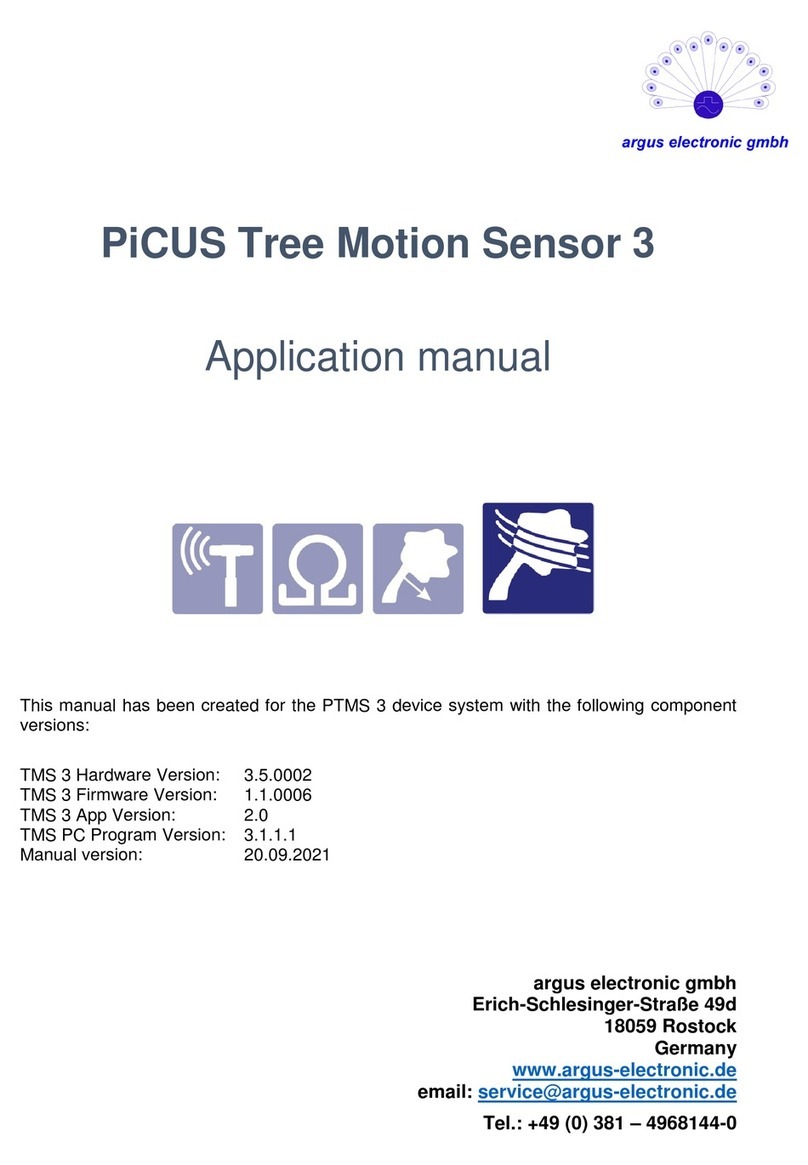
Argus
Argus PiCUS TMS 3 Applications manual
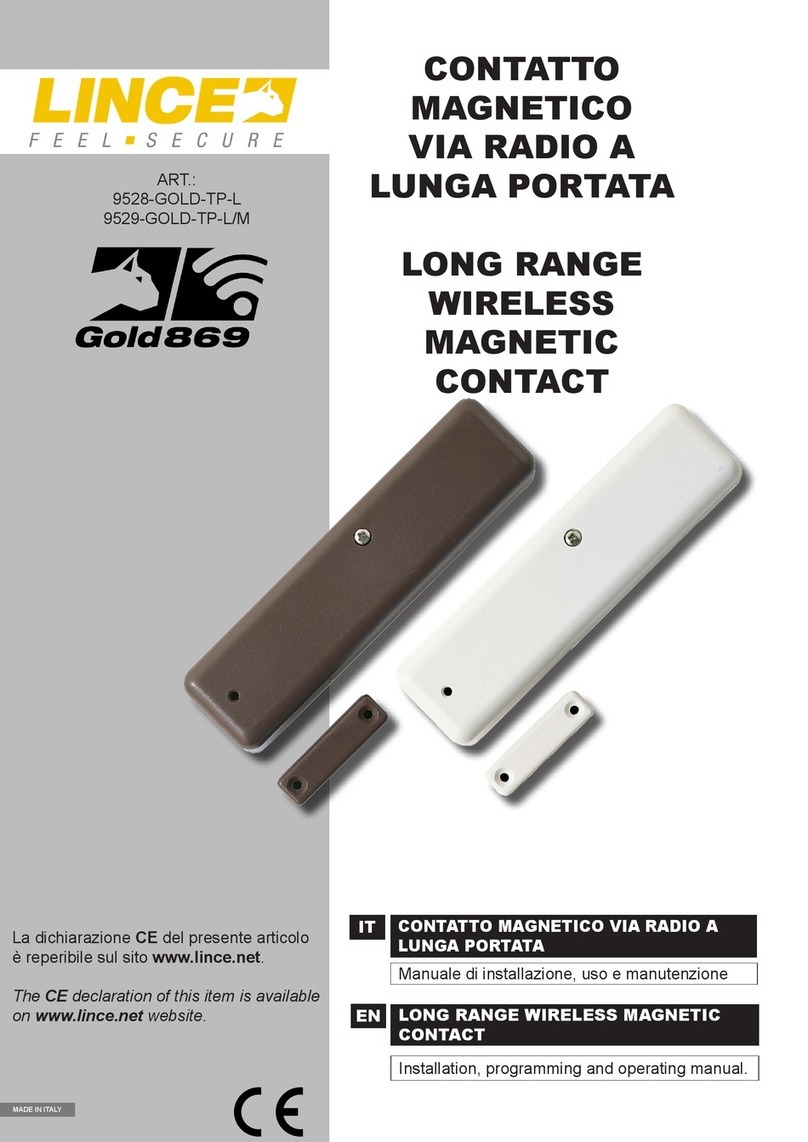
Lince
Lince 9528-GOLD-TP-L Programming and operating manual
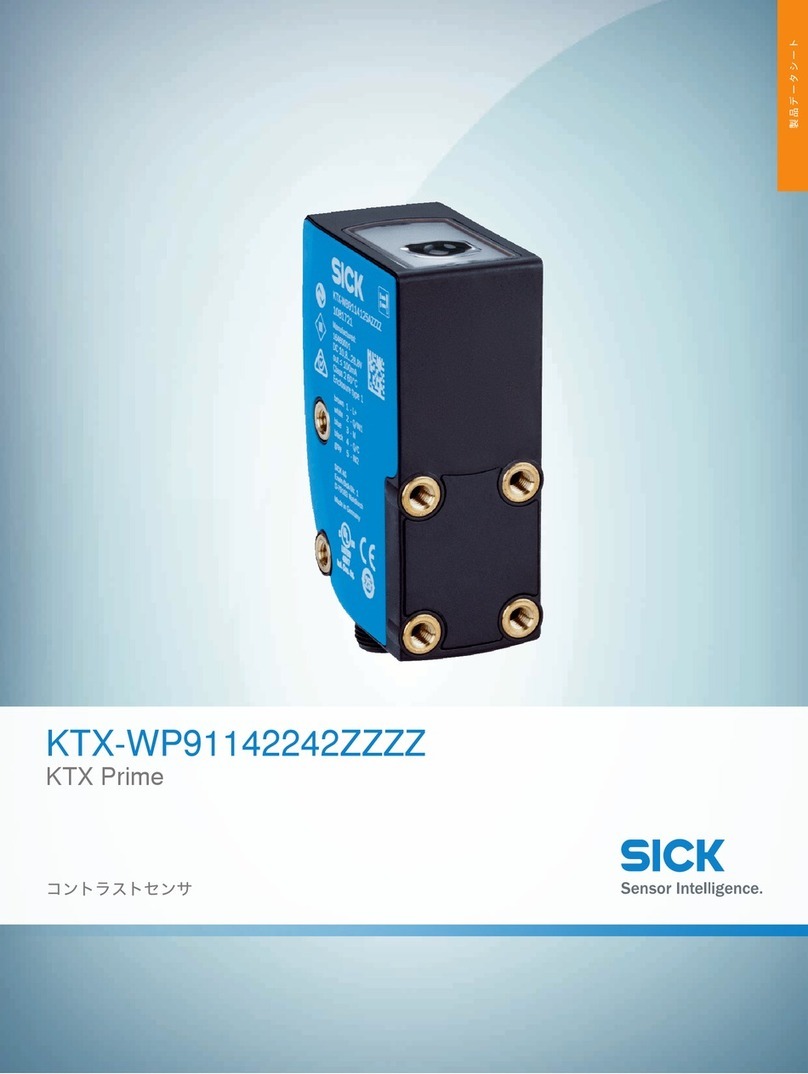
SICK
SICK Prime KTX-WP91142242 Series manual

Polon-Alfa
Polon-Alfa TUN-4046 Installation and maintenance manual