Nelson SC40A Quick start guide

INSTALLATION, USE AND
MAINTENANCE MANUAL
GLASSES WASHERS
FRONT LOADING DISH WASHER

2
INDEX
1.INTRODUCTION ............................................................................................................................................ 3
2. WARNINGS................................................................................................................................................... 3
3. COMPLIANCE WITH “EEC” DIRECTIVES.................................................................................................. 3
4. IDENTIFICATION MARKING........................................................................................................................ 4
5. TECHNICAL CHARACTERISTICS .............................................................................................................. 4
6. INSTRUCTIONS FOR INSTALLERS ........................................................................................................... 7
6.1 PREPARING FOR INSTALLATION...................................................................................................................7
6.2 WARNINGS.......................................................................................................................................................7
6.3 LAWS, TECHNICAL REGULATIONS AND GENERAL RULES........................................................................7
6.4 INSTALLATION.................................................................................................................................................7
7. CONNECTING THE WATER SUPPLY......................................................................................................... 7
8. CONNECTING THE ELECTRICAL SUPPLY............................................................................................... 8
9. EQUIPOTENTIAL CONNECTION ................................................................................................................ 8
10. ADJUSTMENTS AND CHECKS................................................................................................................. 8
10.1 RINSE AID DISPENSER...................................................................................................................................8
10.2 LOADING THE DETERGENT ...........................................................................................................................9
11. DISPENSER FOR LIQUID DETERGENT (optional) ................................................................................. 9
11.1 START-UP.........................................................................................................................................................9
11.2 OPERATION....................................................................................................................................................10
11.3 HOW TO REGULATE THE DETERGENT DISPENSER.................................................................................10
11.4 EXAMPLE OF HOW TO SET THE AMOUNT OF DETERGENT REQUIRED.................................................10
12 FUNCTIONAL CHECKS......................................................................................................................... 11
13. USER INSTRUCTIONS............................................................................................................................. 12
14. CONTROL AND COMMAND PANELS .................................................................................................... 12
15. SETTING IN OPERATION:....................................................................................................................... 13
16. DECALCIFICATION AND REGENERATION OF RESINS ...................................................................... 13
17. DRAINAGE PUMP .................................................................................................................................... 14
18. ADVICE TO USERS.................................................................................................................................. 14
18.1 PERIODIC MAINTENANCE ............................................................................................................................14
19. SERVICE MANUAL AND ADVICE FOR TROUBLESHOOTING ............................................................ 15
21. INSTALLATION DIAGRAMS.................................................................................................................... 22
22. DECLARATION OF CONFORMITY ......................................................................................................... 25

3
1.INTRODUCTION
The manufacturing company declines all responsibility for any inaccuracies contained in this handbook due
to printing or spelling mistakes.
The manufacturers decline all responsibility if standard safety norms are complied with.
The manufacturers reserves the right to modify their products if necessary without compromising the basic
characteristics.
2. WARNINGS
The information contained in this manual aims at providing guidelines regarding:
•technical characteristics;
•installation and mounting instructions;
•information on how to train the personnel responsible for the use of the appliances;
•use of appliances;
•maintenance work.
The manual must be considered part of the appliances, and must therefore be kept in a safe place for future
reference.
Keep it safely with the machine for technicians and operators.
The manufacturer shall not be held liable for any of the following instances:
•improper use of the appliances;
•improper installation performed without complying with the procedures contained herein;
•faulty electrical power
3
upplì;
•serious inadequacies in the prescribed maintenance;
•unauthorised alterations or interventions;
•use of non-standard or non-specific parts;
•failure to comply with the instructions, either partially or fully.
Electrical appliances can be dangerous. Current standards and regulations must be adhered to during
installation and use of the appliances.
De-activate the appliance in case of damage or malfunctioning.
For repairs contact a reliable retailer only.
3. COMPLIANCE WITH “EEC” DIRECTIVES
NOTE: Our products are made in compliance with the essential requirements established by the EEC
directives in agreement with the “EEC 73/23 Low Voltage Directive, with the “EEC 89/336 EMC Directive,
and according to the EEC Directive no. 23 of 19/02/73, and amended directive no.791 of 18/10/87, our
appliances are manufactured according to current Italian and foreign technical standards.

4
4. IDENTIFICATION MARKING
The appliance is provided with a data plate. In order to identify the appliance, for an adequate after sales
service and proper use of this manual refer to “Electrical data –General characteristics”.
5. TECHNICAL CHARACTERISTICS
GLASSWASHER
TECHNICAL CHARACTERISTICS
MODELS
SC40A
SC40A WS
SC40A DP
SC40A WS DP
Standard
S
\
\
\
Water softener
\
S
\
S
Drain pump
\
\
S
S
Dimensions WxDxH ( mm)
480 x 520 x 695
Basket dimensions ( mm)
400 x 400
Useable clearance ( mm)
280
Total cycle time (sec)
120
Production baskets/hour
30
Tub capacity in lt.
8
Boiler capacity in lt.
4.5
Consumption of water per cycle (l)
2.2
Tub power (kW)
1.2
Boiler power (kW)
2.2
Wash pump power (kW)
0.2
Power rinse pump (kW)
0.33
Total power kW
2.4
Water supply temperature °C
15-55
Water hardness °F
Pressure (bar)
2-4
3-4
2-4
3-4
Power voltage
230 V 1N
Frequency
50 Hz
STANDARD EQUIPMENT
Supply fitting ¾ “G
Yes
Tub drain pipe
Yes
Boiler safety thermostat
Yes
Shining product dosing device
Yes
Detergent dosing device
Yes
Flat weave basket
2
Cutlery container (n°)
1
Saucer insert
1
ACCESSORIES ON REQUEST
Cutlery basket
Auxiliary rinse pump
Drain pump
Yes
Yes
Cold rinse
S= standard

5
DISHWASHERS
TECHNICAL CHARACTERISTICS
MODELS
SC45A
SC45A WS
SC45A DP
SC45A WS DP
Standard
S
\
S
\
Water softener
\
S
\
S
Drain pump
\
\
S
S
Dimensions WxDxH ( mm)
510 x 603 x 818
Basket dimensions ( mm)
450 x 450
Useable clearance ( mm)
310
Total cycle time (sec)
150
Production baskets/hour
24
Tub capacity in lt.
18
Boiler capacity in lt.
6.9
Consumption of water per cycle (l)
2.6
Tub power (kW)
1.2
Boiler power (kW)
3
Wash pump power (kW)
0.35
Power rinse pump (kW)
0.33
Total power kW
3.35
Water supply temperature °C
50
Water hardness °F
10-16
>16
10-16
>16
Pressure (bar)
2-4
4
2-4
4
Power voltage
230 V 1N
Frequency
50 Hz
STANDARD EQUIPMENT
Supply fitting ¾ “G
Yes
Tub drain pipe
Yes
Boiler safety thermostat
Yes
Shining product dosing device
Yes
Detergent dosing device
Yes
Plate basket 14 (n°)
1
Flat weave basket
1
Cutlery container (n°)
1
ACCESSORIES ON REQUEST
Saucer insert
Yes
Yes
Yes
Yes
Cutlery basket
Yes
Yes
Yes
Yes
Auxiliary rinse pump
Yes
No
Yes
No
Drain pump
Yes
Yes
No
No
Cold rinse
Yes
Yes
Yes
Yes
S= standard

6
DISHWASHERS
TECHNICAL CHARACTERISTICS
MODELS
SC50A
SC50A WS
SC50A DP
SC50A WS
DP
Standard
S
\
S
\
Water softener
\
S
\
S
Drain pump
\
\
S
S
Dimensions WxDxH ( mm)
600 x 625 x 820
Basket dimensions ( mm)
500 x 500
Useable clearance ( mm)
330
Total cycle time (sec)
150
Production baskets/hour
24
Tub capacity in lt.
23
Boiler capacity in lt.
8.2
Consumption of water per cycle (l)
3
Tub power (kW)
2
Boiler power (kW)
4.5
Wash pump power (kW)
0.65
Power rinse pump (kW)
0.33
Total power kW
5.15
Water supply temperature °C
15-55
Water hardness °F
Pressure (bar)
2-4
3-4
2-4
3-4
Power voltage
230V ~1 _ 230V ~3 _ 400 V ~3+N
Frequency
50 Hz
STANDARD EQUIPMENT
Supply fitting ¾ “G
Yes
Tub drain pipe
Yes
Boiler safety thermostat
Yes
Shining product dosing device
Yes
Detergent dosing device
Yes
Plate basket 20 (n°)
1
Flat weave basket
Glass basket
1
Cutlery container (n°)
1
ACCESSORIES ON REQUEST
Saucer insert
Cutlery basket
Yes
Yes
Yes
Yes
Auxiliary rinse pump
Yes
Yes
Yes
Yes
Drain pump
Yes
Yes
Cold rinse
S= standard

7
6. INSTRUCTIONS FOR INSTALLERS
6.1 PREPARING FOR INSTALLATION
Carry out the following operations:
- place the appliance in the desired position on a solid, flat and stable floor;
- take care not to damage the appliance by banging it against nearby objects during loading and
offloading operations;
- Only qualified personnel, equipped with safety measures, can be present in the area during installation;
- Remove the appliance from its packaging, taking care not to damage any protruding parts (drains,
wiring, power cable);
- remove the protective film;
- Check that the appliance is in good condition. In the event of visible damage to the appliance contact
the retailer and the courier responsible for delivering the product immediately. If in doubt do not use the
appliance until it is checked by a specialised technician;
- transport and move the appliance using a fork-lift by inserting the forks under the appliance.
- carefully level the appliance by using the levelling feet;
- clean the appliance before using it with a cloth dampened in water and bicarbonate or other neutral
detergents and dry carefully.
6.2 WARNINGS
- Prior to connecting the machine to the power and water supply read the general instructions and the
information indicated on the data plate by the manufacturer.
- Do not leave the machine in rooms with a temperature lower than 0° C;
- The degree of protection of the machine is IP X4. Therefore it should not be washed with direct high-
pressure water jets;
- In the event of damage or breakdown switch off the appliance immediately.
- Only use original spare parts to replace damaged ones..
6.3 LAWS, TECHNICAL REGULATIONS AND GENERAL RULES
Comply with the following during installation:
a) safety norms;
b) laws in force in the country where the appliance is installed;
c) read all the indications given in this handbook carefully as they provide important information for safe
installation, use and maintenance;
d) keep this handbook in a safe place for future reference by those who use the appliance;
6.4 INSTALLATION
Installation, start-up and maintenance of the appliance should only be carried out by specialised personnel in
compliance with the instructions provided by the manufacturer.
The manufacturer declines all responsibility if the appliance malfunctions due to incorrect installation,
tampering, improper use, poor maintenance, failure to comply with the local laws and inexperience in using
the appliance.
7. CONNECTING THE WATER SUPPLY
Prior to connecting the appliance to the water supply make sure that a gate valve or tap has been placed
between the water supply system and the appliance that allow the power supply to be interrupted if needed
or if repairs are required.
The water supply minimum pressure, measured when water enters the machine during the final rinse (flux
pressure), should not be lower than 2 bar, even in the presence of other open taps on the same line.
We recommend that each machine is equipped with its own pipe having reduced length and a sufficiently
large cross section so as to avoid pressure or load losses.
An additional rinsing pump, available as an optional item, must be installed in cases where pressure is lower
than the minimum value required.
A pressure reducing valve must be installed upstream from the supply pipe in cases where static pressure is
greater than 5 bar. The supply pipe of the machine must have a capacity equal or greater than 20 lt/min.
A successful final rinse cycle is strictly dependent upon adherence to the values shown.
The drain hose must be connected directly to the drain duct after a siphon has been interposed.
Drainage occurs by gravity, therefore the joint to the drain hose must always be positioned below the bowl
level.

8
If the existing drain is located above the specified level an adequate drainage pump must be installed
(optional).
Do not install the outlet hose in tubs, sinks etc.
8. CONNECTING THE ELECTRICAL SUPPLY
1) The units are delivered ready for working with the voltage shown on the data plate.
2) Connect to the electricity line, interposing a suitably rated automatic circuit breaker, where the opening
distance between the contacts must be at least 3 mm. Furthermore, supply voltage must not deviate
from the voltage value by +5% to -10 %.
3) The characteristics of the flexible cable chosen for connection to the electricity line must not be inferior to
the type with rubber insulation H05RN-F and it must have a nominal cross section suitable to absorb
maximum current; hence, as indicated in the table, it must have the same minimum cross section
indicated relative to the model.
4) To access the power inlet terminal board and replace the power cord, check the positioning in the
attached installation diagrams.
N.B. It is essential that the appliance is connected to an efficient earth plug. For this purpose, near the
connection terminal board there is a terminal marked with a plate with the symbol on it and to
which the earth wire must be connected (yellow-green).
ATTENTION: The use of adaptors, multiple sockets or extension cables is strictly forbidden.
Check and tighten all the screws of the electric system which may have become loose during
storage or transport.
ATTENTION: Safety device installed; The appliances are equipped with a manual reset safety device
which, in the event of an increase in temperature beyond the predefined maximum limit, cuts in, thus
interrupting the power supply to the heating elements.
The event is signalled by the switching off of the light during normal operation.
9. EQUIPOTENTIAL CONNECTION
If several appliances are installed in a row, the appliance must be connected to an equipotential system
whose effectiveness must be verified in accordance with the relative current laws. The connection is at the
back of the appliances and marked with the “EQUIPOTENTIAL” plate.
NOTA: the manufacturers decline all responsibility if the accident prevention rules described above are not
complied with!
10. ADJUSTMENTS AND CHECKS
The temperature inside the bowl is set at 55/60°C.
This temperature favours the correct use of the chemical characteristics of all industrial detergents.
It is advisable not to change this parameter.
The temperature of the boiler is set at 87-90°C.
This value allows the rinse water temperature to be optimized throughout the cycle.
10.1 RINSE AID DISPENSER
The appliance is equipped with a fully automatic rinse aid dispenser.
Before starting the appliance make sure that the rinse aid suction tublet is inserted to its container.
During the manufacturing process the dispenser is calibrated for maximum opening and must be then
adjusted according to the water hardness.
Terminali cavetti di terra apparecchiatura

9
Calibration: Turn the adjustment screw anticlockwise to increase the capacity and clockwise to decrease it.
A perfect dosage is obtained by turning the adjustment screw by approximately 90 degrees.
An excessive dose of surfactant leaves blue streaks on the crockery and leads to the formation of foam in
the bowl.
On the other hand, if crockery is covered with water droplets and drying is slow it means that the dose of
surfactant is insufficient.
Before setting the right amount of surfactant to be used, it is advisable to carry out a specific test to
determine the degree of water hardness.
If the hardness of the water is greater than 15°F. (French degrees), we advise to install a decalcifyer
upstream from the supply solenoid valve of the machine.
Considering that the amount of surfactant varies sensibly according to its concentration and type of
formulation, the values listed in this manual are totally indicative and must only serve as guidance.
The instructions supplied with the surfactant used will provide useful information on how to determine the
necessary dose.
In order to determine the exact amount of product, once the suction has been carried out, remove the
transparent tublet from the surfactant container and measure the shift in the internal column of liquid.
The doses shown have been calculated on the basis of the characteristics of a good product available on the
market (with a recommended concentration of 1.5g. per 10lt. of rinse water) and to a water hardness of 10-
12°F .
Given that 1g. of product (1cm³) is equal to 8 cm in the liquid column inside the transparent suction tublet,
the indicative amounts for the various models are as follows:
CONSUMPTION of H2O
RINSE (l)
AMOUNT OF PRODUCT
(cm)
SC40A
2.2
2.6
SC45A
SC45A WS
2.2
2.6
SC50A
3
3.6
10.2 LOADING THE DETERGENT
Pour the required amount of detergent into the dishwasher by following the instructions provided by the
manufacturer.
If powder detergent is used make sure that it is evenly distributed in the bowl and does not deposit on one
single area in order to avoid the formation of dark stains at the bottom; shake the water.
Considering that the dosage varies sensibly (0.8-2.5 grams/litre) according to the product concentration and
type of formulation, the amounts shown are purely indicative.
EXAMPLE OF DOSAGE WITH 2 g/litre
CAPACITY TUB (l.)
INITIAL DOSE
EVERY 5 WASH CYCLES
SC40A
8
16 g
7 g
SC45A
18
36 g
20 g
SC50A
23
46 g
23 g
Use only specific anti-foam detergents in the appropriate doses.
11. DISPENSER FOR LIQUID DETERGENT (optional)
11.1 START-UP
Before adjusting the detergent dispenser (optional), this and the corresponding small supply pipe must be
filled as follows:
Supply voltage to the machine.
The dispenser is connected in parallel with the load/rinse solenoid valve.
DO NOT insert the overflow in the drain hole and run the water until the small transparent plastic pipe and
the dispenser are filled.
Check the detergent concentration and the supply water hardness by referring to the product data sheet
before adjusting the dispenser.
Follow the manufacturer's instructions carefully.

10
The amount of detergent poured into the bowl depends on the amount of water consumed by the machine
during each rinse cycle.
The amount required may range between 0.8 and 2.5 grams/litre depending on the detergent type and
concentration.
11.2 OPERATION
Since the control is parallel to the load/rinse solenoid valve, when the machine is filled with water, the
dispenser adds the detergent according to the amount established by the manufacturer.
When the rinse cycle starts, the load/rinse solenoid valve allows the dispenser to replenish the detergent in
the bowl.
N.B. The setting of the operation of the dispenser must find a balance between the initial loading and
replenishing, by adjusting the operating time in relation to the intervals.
One second of dispenser operation corresponds to the input of one gram of product
11.3 HOW TO REGULATE THE DETERGENT DISPENSER
The regulator was designed to allow the dosage of detergent that normally flows through the dispensing
pumps.
Specifically this regulator carefully balances the two amounts of detergent (the initial and replenish ones)
which periodically are loaded into the machine.
By fully turning the timer anticlockwise the pump is always off, whereas by turning fully it clockwise the pump
is always on.
The intermediate settings of interval/operation are exemplified in the diagram below:
11.4 EXAMPLE OF HOW TO SET THE AMOUNT OF DETERGENT REQUIRED
Measure the water consumption of each rinse cycle by referring to the technical sheet of the appliance.
For example, let us assume that the consumption is equal to 2 litres:
2 lt of water x 1.5g (hypothetical amount of detergent recommended by the manufacturer for every litre of
wash water, taken from the product technical sheet) = 3 (gr. of detergent).
Given that 1 gr. = 1 cc. of detergent takes up 8 cm. of the transparent supply tublet of the dispenser, this
leads to: 3 (gr. of detergent) x 8 (cm. of tublet) = 24 (cm. of tublet corresponding to the volume of required
detergent).
The setting must be carried out so that the appliance produces an amount of detergent equal to 24 cm. in
length of the supply tublet, for every rinse cycle.
By following the same criteria, the consumption of every other dishwasher model can be calculated.
N.B. The data provided above refers to a standard supply tublet with a diameter of 5 mm
The amount of detergent is right when the crockery is free from any food residues at the end of the wash
cycle.
An excessive amount of detergent can give rise to the build-up of foam in the bowl and leave white streaks
on the crockery.
Insert the overflow in its housing and carry out some trial cycles.
Perfect wash results can be guaranteed by gradual setting.
N.B. Extra care must be taken in achieving a perfect balance between the amount of rinse aid and
the amount of detergent.
Do not immerse your hands in the wash lye. Should this happen rinse immediately with plenty of water.
Place the dishes with the cavity facing upwards and the cups and glasses upside down.
Place the saucers in the appropriate rack support and the knives and tea spoons in the cutlery basket with
the point facing downwards.
Do not place silver and stainless steel cutlery in the same container as this may cause silver to burnish and
stainless steel to corrode. If possible, wash glasses and glass dishes before the wash cycle.
Place the various types of crockery into the appropriate baskets (plates, glasses, mugs and cups, saucers,
cutlery etc.).

11
In order to save detergent and energy only start a wash cycle when the dishwasher is full without
overloading the racks and avoiding any overlapping of crockery.
In order to keep maintenance to a minimum, WE ADVISE TO CLEAN THE CROCKERY BEFORE LOADING
THE MACHINE; by removing food, lemon peel, toothpicks, olive pits etc. which could partially obstruct the
filter of the solenoid valve, thus compromising the washing performance, the quality of the final result will
improve considerably.
Remove all food residue from the crockery.
Leave the dishes and cutlery with dried-on food residue to soak in water before loading the rack.
Place the basket in the dishwasher, shut the door and start the wash cycle.
12 FUNCTIONAL CHECKS
Before operating the machine it is appropriate to follow the testing procedure below:
1) CHECKING THE WATER LEVEL:
▪During the filling of the bowl, the water must stop flowing into the bowl when its level is at least 1 cm
below the level of the overflow.
▪To protect the heating element while the bowl is being drained, the load solenoid valve must start
operating again when the water level is 2 cm above the heating element.
2) CHECKING THE RINSE CYCLE:
▪The rinse arms must rotate freely and all the sprayers must work correctly.
3) CHECKING THE WASH CYCLE:
▪The wash water must be distributed with high pressure by all the sprayers.
▪The wash arms must rotate freely under the water pressure.
4) CHECKING THE TEMPERATURE LEVELS:
▪The rinse and wash water temperature levels must correspond to the data highlighted in the
"Adjustments and checks" chapter
5) CHECKING THE DISPENSER/DISPENSERS:
▪During each cycle, the dispenser must intake the correct amount of surfactant and/or detergent. To
this end, it is useful to remember that 8 cm. of the transparent supply tublet with a cross-section of
5x8 mm. contain approximately 1 gram of product (1 cm³).
6) CHECKING THE WASH RESULTS:
▪The wash results must be visibly satisfactory and the wash cycle must ensure that every possible
food residue is removed from the surface of the crockery.
▪The rinse cycle must remove small residues of food and detergent from the crockery.
▪At the end of the cycle, the perfectly clean crockery must dry almost instantly by evaporation as soon
as the basket is extracted from the machine.

12
13. USER INSTRUCTIONS
14. CONTROL AND COMMAND PANELS
MOD. Standard:
MOD. Water softener:
Table: 1. ALIVE MACHINE INDICATOR GREEN LIGHT
2. ON-OFF SWITCH
3. CYCLE START BUTTON(FOR EQUIPMENT WITH DRAINING PUMP)
4. OPERATING MACHINE INDICATOR YELLOW LIGHT
5. READY MACHINE INDICATOR YELLOW LIGHT
6. SHORT CYCLE(1)-LONG CYCLE(2)SWITCH
7. CYCLE START REGENERATION BUTTON(AND DRAINING FOR EQUIPMENT WITH
DRAINING PUMP)
8. REGENERATION CYCLE IDICATOR YELLOW LIGHT
2
6
5
4
2
4
5
6
8
1
1
7
3
3

13
15. SETTING IN OPERATION:
1. Supply voltage through the main switch upstream from the appliance.
2. Turn the water tap on.
3. Make sure that the filter and the overflow are placed in the correct position.
4. Shut the door and press switch (2); the machine starts filling up with water and detergent.
5. Once the machine has been loaded (from 1 to 4 minutes depending on the type of machine and the
supply pressure) the boiler heating elements automatically come into effect followed by the bowl
heating element once the boiler temperature (85°C) has been reached.
If it is necessary to open the door when the machine is running AVOID DOING IT TOO QUICKLY.
Although the appliance is equipped with a safety switch to prevent the door from opening suddenly, spurts of
water could still reach the user in the event of a hasty manoeuvre.
The machine is equipped with a programmer which switches on by briefly pressing thecycle(3) start up button
NORMAL OPERATING CYCLE:
Once the machine is ready to operate as per the “SETTING IN OPERATION” paragraph, follow the
instructions below to run the desired wash cycles :
❑Insert the rack with the soiled crockery and shut the door;
❑Select the long or quick cycle switch (6) press the cycle (3) start-up button. The indicator light (4) will
illuminate when the machine has started the selected wash cycle.
In case of accidental door opening the washing cycle will stop and the pilot light (4) will flash at intervals (1
sec.). Once the door will be closed again, the cycle will restart from where it has been interrupted.
Once the cycle has finished, the indicator light (4) will switch off.
Open the door, extract the rack with the clean crockery and insert another rack, which has been previously
loaded, into the dishwasher for the next wash cycle.
N.B. : If the instructions have been followed correctly the crockery will be perfectly clean, dry and
hygienically safe. In order to avoid wasting these efforts, make sure that crockery is stored in
areas having the same requisites.
16. DECALCIFICATION AND REGENERATION OF RESINS
Some dishwasher models are equipped with a system for water decalcification and the regeneration of ion
exchange resins in salt water.
DECALCIFICATION : the system is designed for decalcifying the inlet water that runs through the boiler
(without any external intervention).
REGENERATION OF RESINS: a regeneration of ion exchange resins in the water softener is required at
regular intervals depending on the hardness of the inlet water (see table) and must be carried out as follows:
The machine is set to do the regen program every 50 washing cycles; the warning light (4) will start to blink
when the regen program is requested. You can only stop the blinking by starting the regen program.
a) Switch off the machine by pressing switch (2)
b) Remove the overflow to drain the bowl (for equipment with drain pump press the button (7) the
draining and regeneration will start on sequence.
c) Once the bowl is empty, unscrew the threaded cap (located inside at the bottom of the bowl) and
pour in 1 kg of sodium chloride (large-grained kitchen salt). One load is generally sufficient for ¾
regeneration.
d) Shut the door and press button (7) until indicator light (8) remains on. In case of accidental door
opening the regenerating cycle will stop and the pilot light (8) will flash at intervals (1 sec.). Once the
door will be closed again, the cycle will restart from where it has been interrupted.
e) After approximately 20 minutes indicator light (8) switches off signalling that the regeneration cycle
has terminated.
f) Normal operation can be resumed by following the instructions at paragraph “SETTING IN
OPERATION”
N.B. : It is advisable to perform the regeneration process during periods in which the machine is not used.
Failure to carry out the regeneration process according to pre-defined intervals will cause
the decalcifyer to clog up and the amount of water supplied to the rinse jets to decrease.

14
THE AUTONOMY OF THE DECALCIFYER IS STRICTLY DEPENDENT ON THE CHARACTERISTICS OF
THE SUPPLY WATER, FOR EXAMPLE :
Inlet H2o hardness
No. of
cycles
Outlet H2o hardness
°F 15
°D 8.4
UK 10.5
85
°F 8
°D 4.5
UK 5.5
°F 25
°D 14
UK 17.5
60
°F 8
°D 4.5
UK 5.5
°F 35
°D 19.6
UK 24.5
40
°F 8
°D 4.5
UK 5.5
1° FRENCH = 0.56° German = 0.7° English = 10 p.p.m.
When the hardness of the water is more than 40°F it is advisable not to use a machine with built-in water
softener; it is suitable to install a separate water softener with a capacity not less 12 lt.
We also recommend the use of a machine with no integrated purifier and the installation of a separate
purifier with capacity equal or greater than 12 1.
17. DRAINAGE PUMP
The exceeding water which enters the bowl at the start of a rinse cycle is automatically drained.
Follow the instructions below to drain the bowl completely:
1. Remove the overflow (not the filter)
2. Switch off the machine by pressing the ON-OFF (1) switch
3. Press button 3 to start the draining cycle, the lamp (4) turns on, blinks for 3 seconds and the draining
cycle continue for 2 min. and 20 sec. At this point you can remove the filter tank for cleaning.
In models equipped with an inlet water decalcification system and drainage pump, the water is
automatically drained from the bowl during the regeneration cycle.
18. ADVICE TO USERS
18.1 PERIODIC MAINTENANCE
Disconnect the appliance from the power supply before carrying out any cleaning or maintenance
operations.
Remove the washing impellers every 2-3 days and make sure that there are no food deposits inside. Check
the slits and clean thoroughly if necessary.
Make sure that the rinse arm can rotate freely.
Remove any residues that may obstruct the holes of the nozzles by gently using a thin point.
The external surfaces of the machine may be cleaned using non-abrasive products which are specifically
designed for stainless steel maintenance.
Use a damp cloth avoiding spilling water on the control panel.
Do not clean the machine with pressure water jets.
Any marks on the appliance interior may be removed using a cloth dampened with water.
Do not use corrosive products such as sodium hypochlorite
(bleach) or hydrochloric acid (muriatic acid), steel wool or brushes.
Any disincrustation of the dishwasher must be carried out only by a specialised technician.
High quality products must be used, which are specifically designed by the best manufacturers of industrial
cleaning equipment.
In case of dirt particles check that:
➢The washing nozzles are clean;
➢The washing temperature is approximately 60°C;
➢The active chlorine detergent has been measured out correctly and is suitable for industrial cleaning.
➢The pump suction filter is clean;
➢The crockery has been placed in the appropriate rack;
➢The crockery has been arranged well.

15
If the machine is left unused for extended periods, drain the water from the boiler and the electric pump and
apply some Vaseline on the stainless steel surfaces.
N.B. : These operations must be carried out only after power has been removed from the appliance
by setting the main switch upstream from the machine into the “OFF” position.
19. SERVICE MANUAL AND ADVICE FOR TROUBLESHOOTING
Whenever the appliance fails to work, check for a solution from the following list so as to be able to give the
Technical Assistance Centre useful information for troubleshooting. The most recurring causes of
malfunction are:
A) BY SETTING THE SWITCHER INTO THE ON POSITION THE MACHINE DOES NOT START
B) THE WATER DOES NOT ENTER THE DISHWASHER
C) WATER KEEPS ENTERING THE DISHWASHER
D) THE WATER DOES NOT HEAT UP (MONO-PHASE MACHINE)
D1) THE WATER DOES NOT HEAT UP (TRI-PHASE MACHINE)
E) THE WATER OVERHEATS
F) THE WASH ELECTRIC PUMP IS FAULTY
G) THE MACHINE DOES NOT RINSE
H) THE MACHINE RINSES UNINTERRUPTEDLY
I) THE WASH RESULTS ARE UNSATISFACTORY
J) THE WATER DISPENSER OF THE SURFACTANT IS FAULTY
K) THE ELECTRIC DISPENSER OF THE DETERGENT IS FAULTY
L) THE REGENERATION CYCLE DOES NOT START
M) THE DRAINAGE PUMP IS FAULTY
Once the area where the anomaly has presumably occurred, has been identified, proceed as indicated in the
tables below.
A BY SETTING THE SWITCHER INTO THE ON POSITION THE MACHINE DOES NOT START
POSSIBLE CAUSE
SPECIFIC SOLUTION
•There is no voltage in the electrical system, or the main switch is
disconnected or the corresponding fuses are burned-out;
•The machine connecting cable may be interrupted;
•The conductors in the control panel terminal board may be
loosened;
•The machine line switch is inefficient;
•The conductor contacts are inefficient;
•Door micro may be faulty.
•Electronic board
•Check;
•Replace;
•Check and tighten;
•Replace;
•Check and replace
•Replace.
•Check connection and in case
replace the board
B THE WATER DOES NOT ENTER THE DISHWASHER
POSSIBLE CAUSE
SPECIFIC SOLUTION
•There is no water in the water system or the tap is closed;
•The supply pipe may be bent or compressed;
•The filter of the solenoid valve may be dirty;
•The coil of the solenoid valve may be broken;
•The small piston of the solenoid valve may be blocked.
•Connections on the circuit may be faulty;
•The pressure switch is faulty.
•Electronic board
•Check;
•Check;
•Remove and clean;
•Replace;
•Remove and check;
•Check all connections;
•Replace.
•Check connection and in
case replace the board

16
C WATER KEEPS ENTERING THE DISHWASHER
POSSIBLE CAUSE
SPECIFIC SOLUTION
•The solenoid valve is dirty;
•The membrane is torn;
•The small piston does not move into its housing.
•Loose connection between small tube and pressure
switch;
•The air trap or the small tube are pierced;
•There is water in the pressure switch or in the air
supply tube;
•Loss of pressure in the pressure switch;
•The pressure switch is faulty.
•Electronic board
•Remove the solenoid valve and clean the
membrane compensation cutout.
Replace, in the case of a sealed solenoid
valve;
•Replace;
•Check and replace the solenoid valve if
necessary.
•Slightly shorten the tube and re-insert it
by tightly fastening the strap;
•Replace;
•Remove the small tube and blow the
internal water away. Remove the
pressure switch and try to expel the
water from the inside. Replace if
necessary;
•Unload the dishwasher completely and
reload it;
•Replace;
•Check connection and in case replace
the board
D THE WATER IN THE BOILER AND/OR BOWL DOES NOT HEAT UP (MONO-PHASE MACHINE)
POSSIBLE CAUSE
SPECIFIC SOLUTION
•The boiler thermostat may be faulty;
•The bowl thermostat may be faulty;
•The safety thermostat may be faulty;
•The pressure switch contact may be faulty ;
•The safety thermostat has failed to cut in;
•The connections or conductors may be faulty;
•The boiler heating element may be damaged;
•The bowl heating element may be damaged.
•Replace;
•Replace;
•Replace;
•Replace;
•Reset and check the anomaly;
•Check;
•Replace;
•Replace;
D1 THE WATER IN THE BOILER AND/OR BOWL DOES NOT HEAT UP (TRI-PHASE MACHINE)
POSSIBLE CAUSE
SPECIFIC SOLUTION
•A phase is missing from the relay coil;
•The relay coil may be interrupted;
•The boiler thermostat may be faulty;
•The pressure switch contacts may be faulty;
•The relay contacts may be worn-out;
•The connections or conductors may be faulty;
•There is one phase missing;
•The boiler heating element may be damaged;
•The connection between the terminals and the
heating element is incorrect.
•Check;
•Check;
•Replace;
•Replace;
•Replace the contactor;
•Check;
•Check the appropriate circuit;
•Replace;
•Check;
•The bowl heating element may be damaged;
•The connections or conductors may be inefficient;
•The bowl thermostat is in the “O” position (OFF),or is
damaged;
•The contact on the boiler thermostat is incorrect.
•Replace;
•Check the bowl contactor and
thermostats;
•Adjust or replace;
•Replace;

17
E THE WATER IN THE BOILER AND/OR BOWL OVERHEATS
POSSIBLE CAUSE
SPECIFIC SOLUTION
•The contacts in the boiler and/or bowl thermostat
are locked in the “Closed” position.
•Replace;
•The relay has remained in the “Closed
position”,even though voltage is supplied to the coil.
•Check the closure contacts and replace if
necessary;
F THE WASH ELECTRIC PUMP IS FAULTY
POSSIBLE CAUSE
SPECIFIC SOLUTION
•The thermal protection is disconnected;
•The door micro is faulty;
•The condenser is faulty:
•The motor winding is faulty.
•Electronic board
•Replace;
•Replace;
•Replace;
•Replace;
•Check connection and in case replace
the board
•The rotor does not rotate properly and absorption
exceeds the nominal values;
•The motor rotor is blocked;
•There is insufficient water in the bowl;
•The pump suction filter is dirty;
•The pump and the washing impellers are dirty.
•Remove and clean the coil and replace
the seal and the bearings. Check that the
motor has been set at the system
voltage. Remove any residues. Check
that all phases are present;
•Make sure that there are no large food
deposits or cutlery in the body of the
pump. Make sure that the mechanical
seal and shaft bearings are not blocked;
•Make sure that the overflow is perfectly
tightened. Make sure that the pressure
switch prevents water from entering the
bowl at 1 cm from the overflow level;
•Make sure that the dishes are placed in
the dishwasher only after they have been
properly cleaned. Clean the filter
regularly according to its use;
•Make sure that the machine is not used
without a filter or that the filter is perfectly
inserted in its housing.
G THE MACHINE DOES NOT RINSE
POSSIBLE CAUSE
SPECIFIC SOLUTION
•There is no water in the system;
•The tap is partially closed;
•The supply pipe may be bent or squeezed;
•The filter of the solenoid valve may be dirty;
•The coil of the solenoid valve may be interrupted;
•The small piston of the solenoid valve may be
blocked;
•Pressure in the system is insufficient.
•Check;
•Check;
•Check;
•Remove and clean;
•Replace;
•Remove and check;
•Make sure that the system pressure is at
least 2 bar. If pressure is lower, install an
auxiliary rinse pump;

18
•Faulty connections or inefficient conductors on the
coil circuit;
•Electronic board
•The cold, manual (where present) rinse pushbutton
may be faulty;
•The door micro may be faulty.
•Check;
•Check connection and in case replace
the board
•Replace;
•Replace;
•There is lime in the rinse circuit;
•The sprayers may be obstructed or the rotating arms
blocked
•Check and clean. Install a decalcifyer if
necessary;
•Check and clean;
H THE MACHINE RINSES UNINTERRUPTEDLY
POSSIBLE CAUSE
SPECIFIC SOLUTION
•The solenoid valve is dirty;
•The membrane is torn;
•The small piston does not move properly in its
housing or it is blocked.
•Electronic board
•Remove the solenoid valve and clean the
membrane compensation cutout.
Replace, in the case of a sealed solenoid
valve;
•Replace;
•Check and replace the solenoid valve if
necessary.
•Check connection and in case replace
the board
I THE DISHES ARE NOT CLEAN
POSSIBLE CAUSE
SPECIFIC SOLUTION
•The electric pump may be faulty or damaged;
•The detergent is not suited to dishwashers;
•There is no detergent in the bowl;
•The impellers may be obstructed or damaged;
•The washing impeller may be blocked;
•Refer to various sections in paragraph F;
•Check the amount of detergent. Use only
EXCELLENT products, specifically
formulated for industrial washing by
leading companies of the sector.
•Always adhere to the doses stated on the
product technical sheets. Check the
corresponding dispenser where present;
•Clean and/or replace;
•Check and unblock;
•The water temperature is insufficient;
•The kitchenware has been loaded incorrectly;
•The baskets have been used incorrectly;
•The rinse cycle has not been carried out properly.
The crockery is lightly soiled;
•Adjust the thermostat by checking,
through a thermometer, that the wash
water temperature corresponds to the
pre-set temperature when the indicator
light illuminates;
•Make sure that the crockery is arranged
as per instructions and does not overlap;
•Use the supplied specific baskets for
each type of crockery and cutlery;
•Refer to specific sections in paragraph G;

19
•The washing slits are partially obstructed;
•The dishes or other crockery are overlapping;
•There is dried-on food residue on the crockery due
to late washing.
•The wash cycle may be inefficient;
•The rinse cycle may be inefficient;
•The rinse water may be too hard and contain
exceeding calcium and magnesium salts;
•There is excessive surfactant concentration in the
rinse water.
•The detergent or surfactant may not be suitable for
industrial dishwashers;
•The wash water temperature may be too low.
•Remove and clean;
•Check and separate correctly. Use the
appropriate rack;
•Soak the crockery in water and wash
again.
•Refer to various sections in paragraph F;
•Refer to various specific sections in
paragraph G;
•Install a decalcifyer upstream from the
machine with adequate capacity
according to the consumption of the
machine itself. If the machine is
equipped with a water softener make
sure that the regeneration of resins is
carried out regularly;
•Adjust the dispenser according to the
doses suggested by the product
manufacturer. Once the dispenser has
been adjusted, it is necessary to wait
until the product concentration has
stabilised on the new values, after a few
wash cycles, before being able to notice
any improvement in the quality of the
rinse cycle.
•Use a foam breaking detergent and an
anti-foam surcfactant;
•Check the calibration of the thermostat
that regulates the bowl temperature and
the status of the bowl heating element.
J THE WATER DISPENSER OF THE SURFACTANT IS FAULTY
POSSIBLE CAUSE
SPECIFIC SOLUTION
•The small transparent suction tube may be bent;
•The small suction tube may have a hole;
•The small suction tube is not properly tightened to
the rubber seal;
•The suction fitting of the dispenser is not tightened
properly.
•Pressure in the system is insufficient;
•Check;
•Check and replace if necessary;
•Check and replace if necessary;
•Check.
•Check;
K THE ELECTRIC DISPENSER OF THE DETERGENT IS FAULTY
POSSIBLE CAUSE
SPECIFIC SOLUTION
•The small tube inside the dispenser may be broken;
•The small suction tube may be bent or damaged.
•Replace the small tube;
•Check and replace if necessary.
•Faulty connection or inefficient conductors on the
motor coil circuit;
•Detergent doser fault
•Check and replace if necessary;
•Replace

20
L THE REGENERATION CYCLE DOES NOT START
POSSIBLE CAUSE
SPECIFIC SOLUTION
•There is no water in the water system or the tap is
closed;
•The supply pipe may be bent or squeezed;
•The filter of the solenoid valve may be dirty;
•The coil of the solenoid valve may be interrupted;
•The small piston of the solenoid valve may be blocked;
•The connections on the coil electric circuit may be
faulty;
•Electronic board
•The relevant push-button is not giving power
•ON-OFF switch is defective.
•The coil may be interrupted.
•Check;
•Check;
•Remove and clean;
•Replace;
•Remove and check;
•Check all connections;
Check connection and in case replace
the board
•Check the connection and if necessary
replace the push-button or the switch.
•Check the connection and if necessary
replace the switch.
•Replace.
M THE DRAINAGE PUMP IS FAULTY
POSSIBLE CAUSE
SPECIFIC SOLUTION
•The coil may be interrupted;
•The pump may be clogged;
•The impeller of the drain pump may be damaged;
•The drain pipe may be obstructed.
•The drainage button may be faulty.
•ON-OFF switch defective
•The pressure switch has intervened
•Electronic board
•Replace the pump;
•Remove and clean;
•Replace the pump;
•Remove any food residue.
•Replace.
•Check the connection and if necessary
replace the switch
•Check the drain pump or replace the
pressure switch
•Check the connection and if necessary
replace the board
The manufacturer declines all responsibility for any incorrect information herein due to printing or spelling
mistakes. The manufacturers reserve the right to modify their products if necessary without compromising
their basic characteristics.
It is forbidden to reproduce or photocopy, even partially, any texts or images contained in this booklet without
previous insurance.
20 20. DISMANTLING - RECYCLING
Nessuna voce di sommario trovata. In conformity with art.13 of Legislative Decree No. 151 of 25 July 2005, ”Implementation of
directives2002/95/CE,2002/96/CE and 2003/108/CE,regarding the reduction in use of dangerous substances
in electrical and electronic equipment, as well as waste disposal”
Products bearing the barred dustbin symbol must be disposed of separately from other waste.
The recycling of old appliances is organised and managed by the manufacturer. Consumers should contact
the manufacturer for information concerning the correct disposal of their old appliance.
Separate waste collection allows used equipment to be recycled, treated and disposed of without negative
consequences for the environment and health, and it allows the materials in the equipment to be recycled.
Illegal dumping of the product by the user entails the administrative sanctions stated in the current
legislation.
Materials used in the manufacture of the equipment:
Stainless steel 18/10: Stainless steel: bodywork
PA (Nylon) Rubber: water system piping
This manual suits for next models
7
Table of contents
Popular Washer manuals by other brands
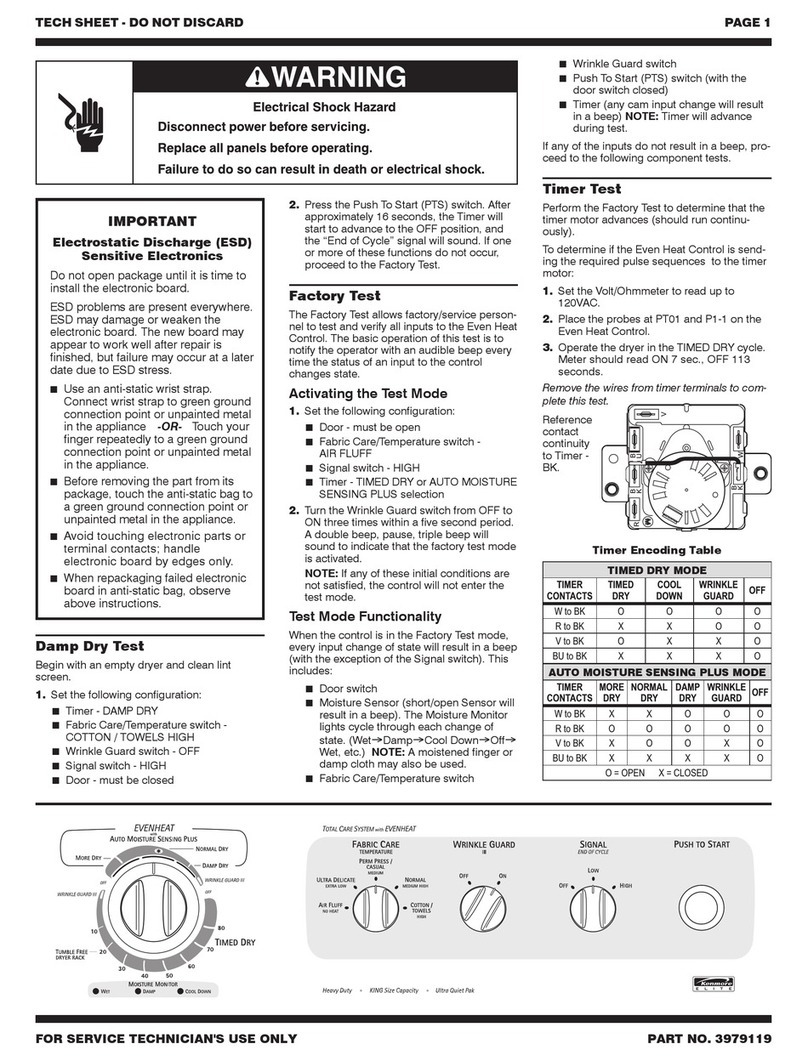
Whirlpool
Whirlpool 72972 Tech sheet
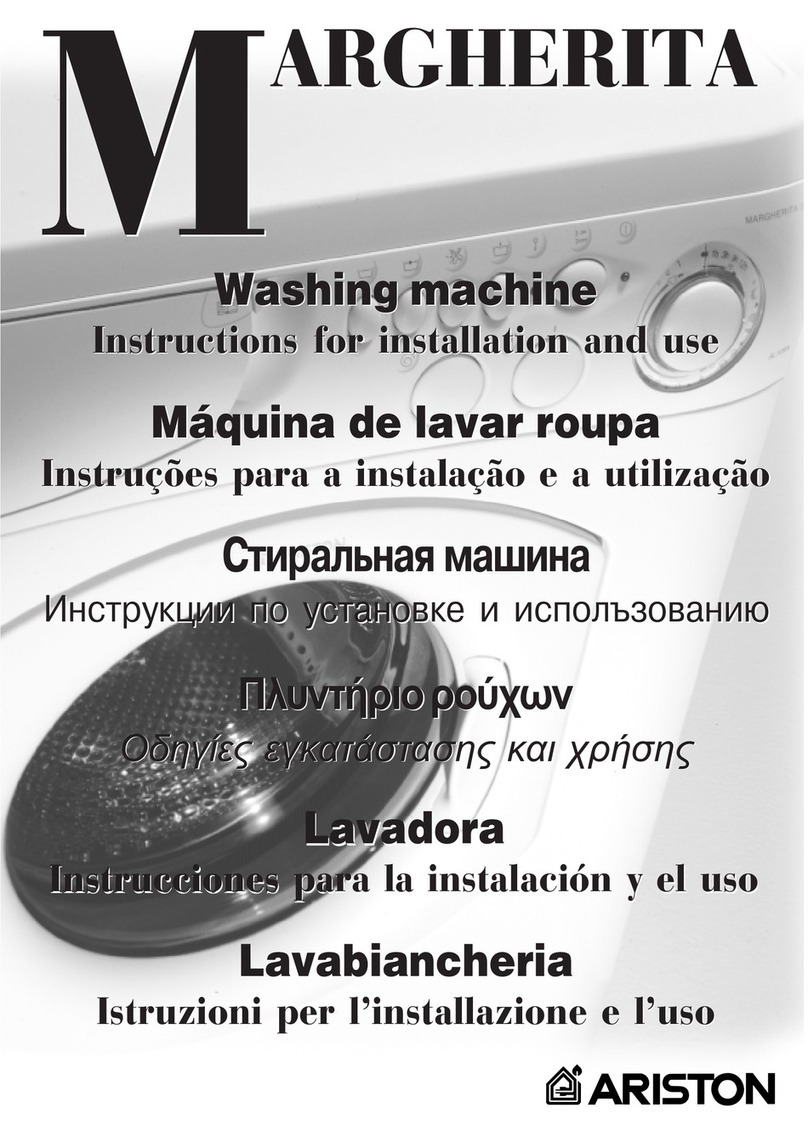
Ariston
Ariston AXD 100 Instructions for installation and use
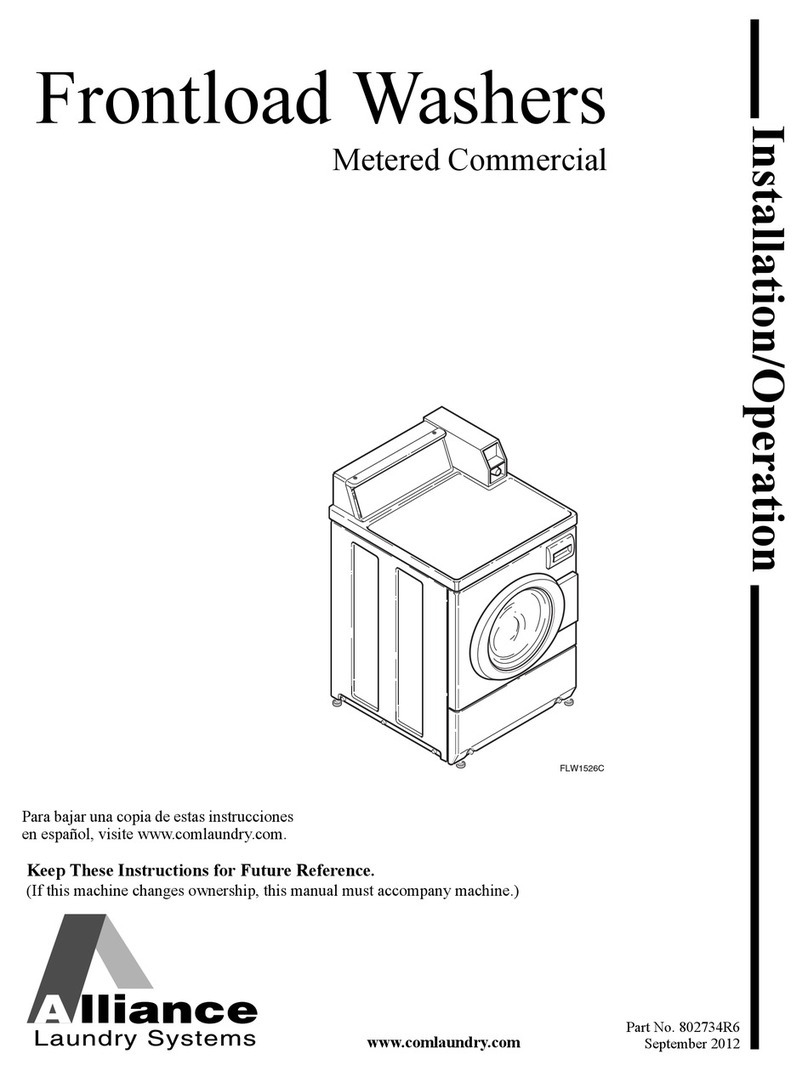
Alliance Laundry Systems
Alliance Laundry Systems 802734R6 Installation & operation
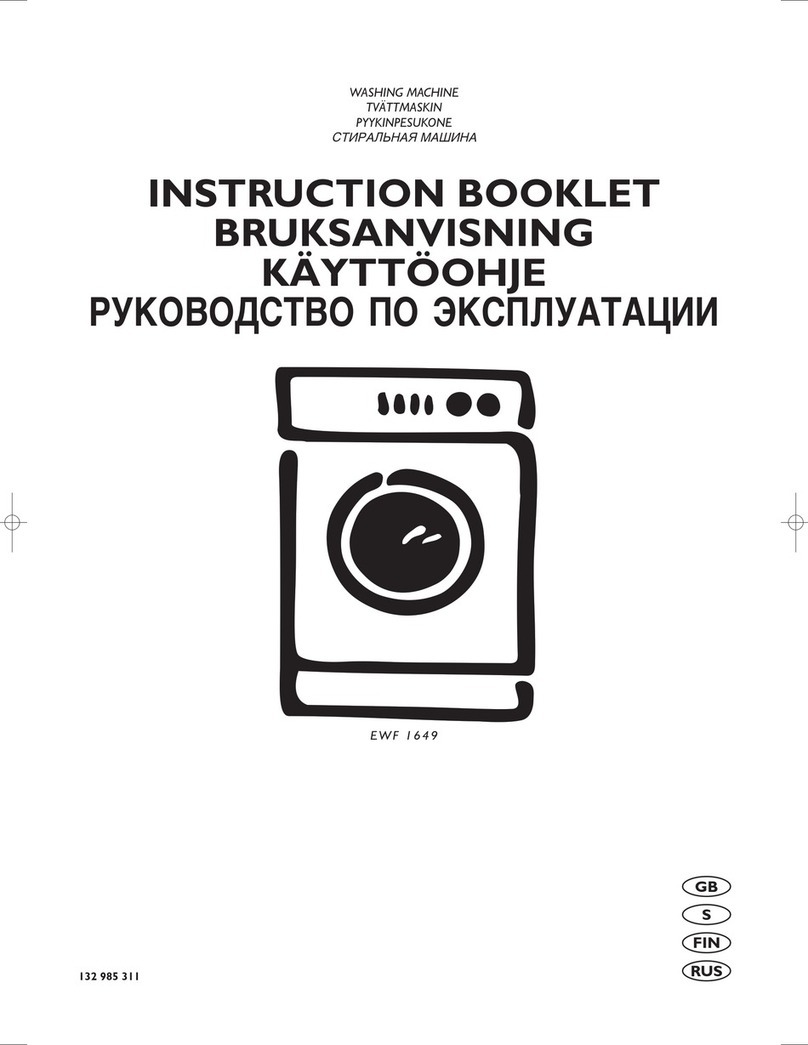
Electrolux
Electrolux EWF 1649 Instruction booklet
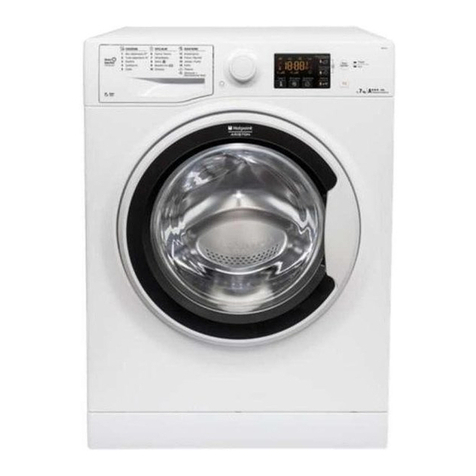
Hotpoint Ariston
Hotpoint Ariston RSG 724 J Instructions for use
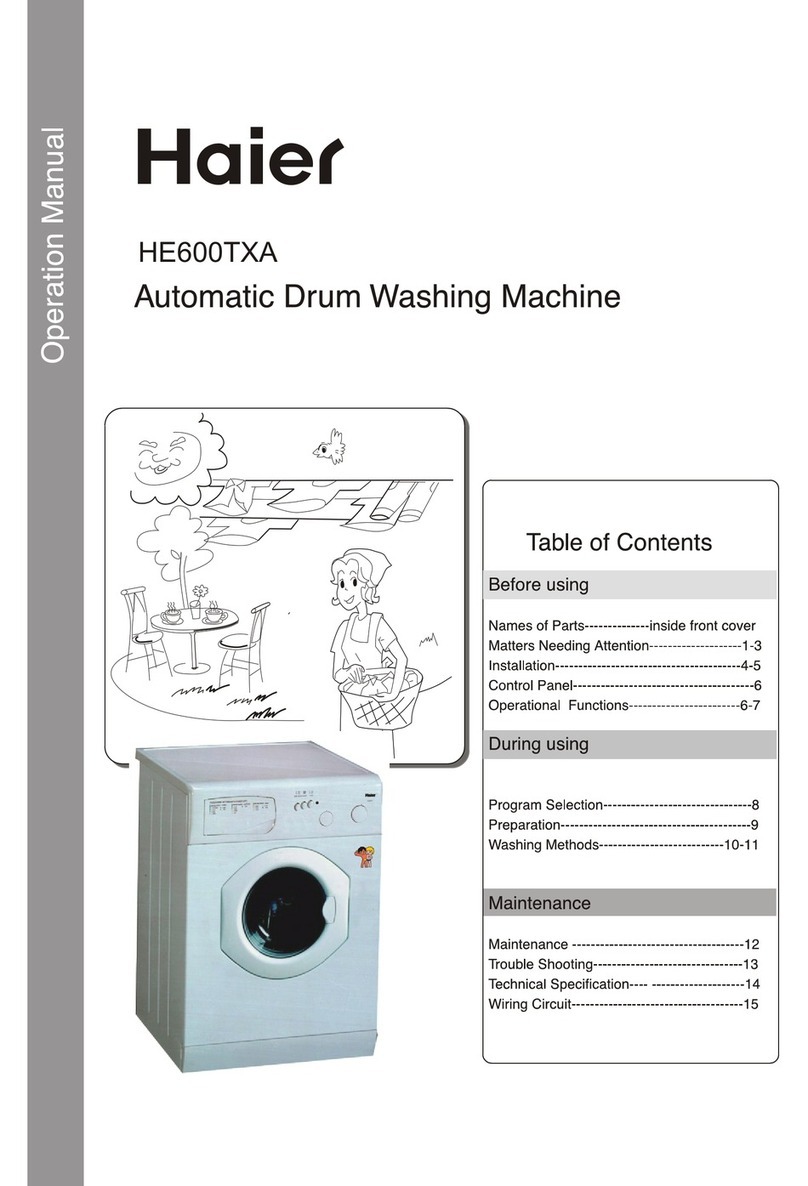
Haier
Haier HE805TX Operation manual