Omron F3SG-PG Series User manual

Standards
Safety Multi-Light Beam
Model
F3SG-□PG□Series
•
The F3SG-PG is designed and manufactured according to the following standards.
EN61496-1 (Type 4 and Type 2 ESPE), EN 61496-2 (Type 4 and Type 2 AOPD),
EN61508-1 through -4 (SIL 3 forType 4 and SIL 1 for Type 2),
EN ISO 13849-1:2015 (PL e, Category 4 forType 4 and PL c, Category 2 forType 2)
•
Dispose in accordance with
applicable regulations.
EU Declaration of Conformity
OMRON declares that the F3SG-PG is in conformity with the requirements of the
following EU Directives:
Machinery Directive 2006/42/EC, EMC Directive 2014/30/EU
©
OMRON Corporation 2020 All Rights Reserved.
Original instructions
Alert Statements
Users
Machines
Instruction Sheet
Thank you for purchasing the F3SG-PG Series Safety Multi-Light Beam (hereinafter
referred to as the "F3SG-PG").Be sure to have F3SG-PG be handled by a
"Responsible Person" who is well aware of and familiar with the machine to be
installed.The term "Responsible Person" used in this document means the person
qualified, authorized and responsible to secure "safety" in each process of the
design, installation, operation, maintenance services and disposition of the
machine.It is assumed that F3SG-PG will be used properly according to the
installation environment, performance and function of the machine.
Responsible Person should conduct risk assessment on the machine and
determine the suitability of this product before installation. Read this document and
reference manuals for F3SG-PG thoroughly to understand and make good use of
the descriptions before installing and operating the product.Keep this document at
the place where the operator can refer to whenever necessary.
Precautions for Correct Use
Reference Manuals
The F3SG-PG must be installed, configured, and incorporated into a
machine control system by a sufficiently trained and qualified person.An
unqualified person may not be able to perform these operations properly,
which may cause a person to go undetected, resulting in serious injury.
Do not use this sensor for machines that cannot be stopped quickly by electrical control.For
example, do not use it for a pressing machine that uses full-rotation clutch.Otherwise, the
machine may not stop before a person reaches the hazardous part, resulting in serious injury.
To use the F3SG-PG in PSDI mode (initiation of cyclic operation by a
presence sensing device), you must configure an appropriate circuit between
the F3SG-PG and the machine.For details about PSDI, refer to OSHA
1910.217, IEC 61496-1, and other relevant standards and regulations.
EN
Installation
Document Title
Safety Light Curtain F3SG-□SR□ Series
Safety Multi-Light Beam F3SG-□PG□Series
User’s Manual
Cat. No.
Z405-E1
5605730-1
Safety Multi-Light Beam F3SG-□PG□ Series
Quick Installation Manual
In the interest of product improvement, specifications are subject to change without notice.
Instructions in the official EU languages and a signed EU Declaration of Conformity in
English are available on our website at www.industrial.omron.eu/safety.
2865475-2A
Indications and Meanings for Safe Use
The precautions listed in this document indicated by alert symbols and statements must
be followed for the safe use of the F3SG-PG. Failure to follow all precautions and alerts
may result in an unsafe use or operation.Thoroughly read this document before using
the F3SG-PG.The following word and symbols are used in this document.
Meaning of SignalWord
Safety Precautions
Indicates an imminently hazardous situation which,
if not avoided, is likely to result in serious injury or
may result in death.Additionally there may be
severe property damage.
DANGER Indicates a potentially hazardous situation which, if
not avoided, will result in minor or moderate injury,
or may result in serious injury or death. Additionally
there may be significant property damage.
WARNING
WARNING
WARNING
Make sure Responsible Person tests the operation of the F3SG-PG and F39-SGIT-IL3
after installation to verify that the F3SG-PG and F39-SGIT-IL3 operate as intended.
Make sure to stop the machine until the test is complete.Unintended installation, wiring
or function settings may cause a person to go undetected, resulting in serious injury.
Install a protective structure so that the hazardous part of a machine can only be
reached by passing through the sensor's detection zone. If access to the hazardous
part by reaching over the detection zone of a vertically mounted F3SG-PG cannot be
excluded, the height of the detection zone and the safety distance shall be determined
in consideration of such a risk. Install the sensors so that part of the person is always
present in the detection zone when working in a machine's hazardous zones. If a
person is able to step into the hazardous zone of a machine and remain behind the
F3SG-PG's detection zone, configure the system with Restart Interlock function. Failure
to do so may result in serious injury due to unexpected startup.
Install the reset switch in a location that provides a clear view of the entire
hazardous zone and where it cannot be activated from within the hazardous zone.
Install the pre-reset switch always in the hazardous zone and
where it cannot be activated from outside the hazardous zone.
The F3SG-PG cannot protect a person from an object flying from
the hazardous zone.Install protective cover(s) or fence(s).
When muting error occurs with workpiece blocking the F3SG-PG, there are
two methods to forcibly remove the workpiece.
1) Manual operation (with additional safety measure); or
2) Override function (Override at Normal Operation / Override upon Startup)
Only one of the methods, either 1) or 2) must be used.
If they are used at the same time, the Override may be activated at an
unexpected timing.
The Muting and Override functions disable the safety functions of the device.
Especially setting the Muting Time Limit parameter to infinite may cause the safety
functions to be disabled for a long time. Install the F3SG-PG, muting sensor and
physical barrier and configure time settings for Muting and Override so that an
operator should not enter hazardous zone when the Muting and Override are active.
Install muting sensors so that they can distinguish between the object
that is being allowed to pass through the detection zone and a person.
If the Muting function is activated by the detection of a person, the
machine may not stop operating, resulting in serious injury.
Muting lamps that indicate the state of the Muting and Override functions must be
installed where they are clearly visible to workers from all the operating positions.
Use two independent input devices for muting inputs. Failure to do so
may cause the MUTING state due to a single muting sensor's failure.
Install the switch to activate the Override function in a location that
provides a clear view of the entire hazardous zone and where it cannot
be activated from within the hazardous zone.Make sure that nobody is
in the hazardous zone before activating the Override function.
Make sure to connect an override cancel switch to the RESET line when
using the Override function. Otherwise, the OVERRIDE state may not
be released by the override cancel switch, resulting in serious injury.
Install the F3SG-PG so that it is not affected by reflective surfaces.
Failure to do so may hinder detection, resulting in serious injury.
When using more than one set of F3SG-PG's in adjacent areas, the emitter of one F3SG-PG
may interfere with the receiver of the other, causing the safety functions to stop working
properly. Install, configure and maintain them so that mutual interference does not occur.
To change the response time, calculate the safety distance based on the setting.Otherwise, the
machine may not stop before a person reaches the hazardous part, resulting in serious injury.
Do not use the F3SG-PG with mirrors in a retro-reflective configuration. Doing so may hinder
detection.It is possible to use mirrors to alter the detection zone to a 90-degree angle.
Make sure to install the F3SG-PG at the safety distance from the hazardous part of the machine.Otherwise,
the machine may not stop before a person reaches the hazardous part, resulting in serious injury.
Position with detection zone bent at 90°
Mirror
Mirror
Position with retro-reflection
WARNING
Other
Settings
Do not use the output signal of the auxiliary output or IO-Link output for safety
applications.Failure to do so may result in serious injury when the F3SG-PG fails.
Double or reinforced insulation from hazardous voltage must be applied
to all input and output lines.Failure to do so may result in electric shock.
Extension of the cable must be within a specified length. If it isn't,
safety functions may not work properly, resulting in danger.
For the F3SG-PG to comply with IEC 61496-1 and UL 508, the DC power
supply unit must satisfy
all of the following conditions:
•
The DC power supply operates within the rated power voltage (24VDC ± 20%).
• The DC power supply has tolerance against the total rated current of
devices if it is connected to multiple devices.
• The DC power supply complies with EMC directives (industrial environment).
•
Double or reinforced insulation is applied between the primary and secondary circuits.
•
The DC power supply has an automatic recovery type of overcurrent protection characteristics.
• Output holding time is 20 ms or longer.
•
The DC power supply satisfies output characteristic requirements for class 2 circuit or
limited voltage current circuit defined by UL 508.
•
The DC power supply complies with laws and regulations, regarding EMC and electrical
equipment safety, of the country or region where the F3SG-PG is used. (For example, in
EU, the power supply must comply with the EMC Directive and the LowVoltage Directive.)
Make sure the Responsible Person test the operation of the F3SG-PG after setting with the
DIP Switch on the F39-SGIT-IL3, Teach-in, SD Manager 3 or End Cap to verify that the
F3SG-PG operates as intended. Make sure to stop the machine until the test is complete.
Unintended settings may cause a person to go undetected, resulting in serious injury.
Perform daily and 6-month inspections for all F3SG-PG as described
in the User's Manual or the Quick Installation Manual. Otherwise, the
system may fail to work properly, resulting in serious injury.
Do not try to disassemble, repair, or modify the product. Doing so
may cause the safety functions to stop working properly.
Do not use the product in environments where flammable or
explosive gases are present.Doing so may result in explosion.
Do not use the F3SG-PG in environments where strong electromagnetic field may
be produced.Doing so may cause the safety functions to stop working properly.
WARNING
WARNING
Precautions for Safe Use
Make sure to observe the following precautions that are necessary for ensuring safe use of the product.
■Storage conditions and installation environment
• Do not install, use, or store the product in the following types of environments:
- Areas exposed to intense interference light, such as direct sunlight
- Areas with high humidity where condensation is likely to occur
- Areas where corrosive gases are present
- Areas exposed to vibration or shock levels higher than in the specification provisions
- Areas where the pollution degree is harsher than 3, such as outdoor environment
- Areas where the product may get wet with liquid that can solve adhesive
• Do not drop the product.
■Wiring and installation
•The rated life of the LEDs used for this product is 6 years.
• Loads must satisfy both of the following conditions:
- Not short-circuited
- Not used with a current that is higher than the rating
• Make sure that the mounting brackets, fixing screws and connectors are properly
secured with the torque recommended in this document.
• Bending radii of cables must be equal to or higher than specified minimum values.
• When replacing the cables with those other than the dedicated cables, use cable
connectors that provide a protection grade of IP54 or higher, for the cables.
•
To extend a cable length with a cable other than the dedicated cable, use a cable with the same or superior specifications.
• Be sure to route the input/output lines for the F3SG-PG separate from high-potential
power lines or through an exclusive conduit.
•
Make sure that foreign material such as water, oil, or dust does not enter the F3SG-PG, F39-SGIT-IL3 or the connector
while the end cap and root cables of the F3SG-PG or the cover of the DIP Switch on the F39-SGIT-IL3 is removed.
•
The F39-SGIT-IL3 is dedicated to the
F3SG-SR/PG
series. Do not use it for the equipment other than
F3SG-SR/PG.
•
In environments where foreign material such as spatter adheres to the F3SG-PG, attach a cover
to protect the F3SG-PG from the spatter.
■Oil resistance
• Some cutting oils may affect the product. Before using cutting oils, make sure that the oils
should not cause deterioration or degradation of the product.
•
Do not use the product with degraded protective structure such as swelling and crack in housing and/or sealing
components.Otherwise cutting oil or other substance may enter the product, resulting in a risk of corruption or burning.
•
Use the F39-JG□C-□Root-Straight Cables, F39-JGR3K-□Root-Plug Cables for Extended
or F39-JGR3K-□□-□Conversion Cables in environment where the product may be
exposed to oil.Using the other cables in such an environment may cause cutting oils or other
substances to enter the cables, resulting in a risk of damaging or burning the product.
•
Do not connect the Conversion Cable for the following purposes.Failure to do so may result in failure.
1.Connecting with the F39-SGIT-IL3, F39-GCNY2 or F39-GCNY3
2.Connecting between the F3SG-SR ,F3SG-PG
■Disposal
• Dispose of the product in accordance with the relevant rules and regulations of the
country or area where the product is used.
Observe the precautions described below to prevent operation failure, malfunctions,
or undesirable effects on product performance.
■Storage conditions and installation environment
• Do not install, use, or store the product in the following types of environments:
- Areas with a temperature or humidity out of the specified range
- Areas submerged in water or subject to rain water
•
This is a class A product (for industrial environments).In residential areas it may cause radio interference,
in which case the Responsible Person may be required to take adequate measures to reduce interference.
■Wiring and installation
• Properly perform the wiring after confirming the signal names of all the terminals.
•
Do not operate the control system until 3 s or more after turning ON the power of the F3SG-PG.
• When using a commercially available switching regulator power supply, make sure to
ground the PE terminal (protective earth terminal).
•
Install the emitter and receiver, emitter/receiver, and passive mirror to the same vertical direction.
•
Use brackets of specified quantities and locations according to the dimensions. If the
brackets described above are not used, ratings and performance cannot be met.
• Do not install the F3SG-PG close to a device that generates high-frequency noise.
Otherwise, take sufficient blocking measures.
• Sharing the power supply with other devices may cause the F3SG-PG to be affected
by noise or voltage drop. It is recommended that the F3SG-PG use a power supply
dedicated for safety components, not shared with other devices.
•
Do not change the scan code during normal operation.The F3SG-PG transitions to lockout.
•
Do not apply load to the connectors.
■Cleaning
• Do not use thinner, benzene, or acetone for cleaning.They affect the product's resin
parts and paint on the housing.
•
Use a soft cloth which is dry or wetted with clean water for cleaning.Do not use solvents.
■Object detection
• The F3SG-PG cannot detect transparent and/or translucent objects.
■Settings
• Do not operate the DIP Switch on the F39-SGIT-IL3 during normal operation of the
F3SG-PG. Otherwise, the F3SG-PG enters the LOCKOUT state.
• Do not operate the DIP Switch and Push Switch on the F39-SGIT-IL3 with tools that
may damage the product.
•
Be sure that the F3SG-PG is in the SETTING state when making a change to the setting.
Wiring
When using the PNP output, connect the load between the output and 0 V line.When using
the NPN output, connect the load between the output and +24 VDC line. Connecting the load
between the output and a different power supply line from the above line will result in a
dangerous condition because the operation mode of safety outputs are reversed to "Dark-ON".
WARNING
Make sure that the machine can be controlled correctly and as intended.Also make sure
that the machine can be stopped immediately at any time of the operation cycle without
danger to machine operators when the machine behavior does not meet safety-related
requirements.Otherwise, continued use of the machine may result in serious injury or death.
DANGER
When using the PNP output, do not ground +24 VDC line. When using the NPN output, do not ground 0 V
line.Otherwise, a ground fault may turn the safety outputs ON, resulting in a failure of stopping the machine.
Configure the system by using the optimal number of safety outputs
that satisfy the requirements of the necessary safety category.
Do not connect each line of the F3SG-PG to a DC power supply of higher than 24VDC+20%.
Also, do not connect it to an AC power supply.Failure to do so may result in electric shock.
Make sure to perform wiring while the power supply is OFF.
Suitability for Use
Omron Companies shall not be responsible for conformity with any standards,
codes or regulations which apply to the combination of the Product in the
Buyer’s application or use of the Product. At Buyer’s request, Omron will
provide applicable third party certification documents identifying ratings and
limitations of use which apply to the Product. This information by itself is not
sufficient for a complete determination of the suitability of the Product in
combination with the end product, machine, system, or other application or
use. Buyer shall be solely responsible for determining appropriateness of the
particular Product with respect to Buyer’s application, product or system.
Buyer shall take application responsibility in all cases.
NEVER USE THE PRODUCT FOR AN APPLICATION INVOLVING SERIOUS
RISK TO LIFE OR PROPERTY OR IN LARGE QUANTITIES WITHOUT
ENSURING THAT THE SYSTEM AS A WHOLE HAS BEEN DESIGNED TO
ADDRESS THE RISKS, AND THAT THE OMRON PRODUCT(S) IS PROPERLY
RATED AND INSTALLED FOR THE INTENDED USE WITHIN THE OVERALL
EQUIPMENT OR SYSTEM.
OMRON Corporation (Manufacturer)
Contact: www.ia.omron.com
Regional Headquarters
Shiokoji Horikawa, Shimogyo-ku, Kyoto, 600-8530 JAPAN
OMRON EUROPE B.V. (Importer in EU)
Wegalaan 67-69, 2132 JD Hoofddorp
The Netherlands
Tel: (31)2356-81-300/Fax: (31)2356-81-388
OMRON ELECTRONICS LLC
2895 Greenspoint Parkway, Suite 200
Hoffman Estates, IL 60169 U.S.A.
Tel: (1) 847-843-7900/Fax: (1) 847-843-7787
OMRON ASIA PACIFIC PTE. LTD.
No. 438A Alexandra Road # 05-05/08 (Lobby 2),
Alexandra Technopark,
Singapore 119967
Tel: (65) 6835-3011/Fax: (65) 6835-2711
OMRON (CHINA) CO., LTD.
Room 2211, Bank of China Tower,
200 Yin Cheng Zhong Road,
PuDong New Area, Shanghai, 200120, China
Tel: (86) 21-5037-2222/Fax: (86) 21-5037-2200
tFeb, 2020F

Long
Short 20 to 70 m
0.5 to 20 m 0.5 to 5 m
Ratings and Specifications LED Indicators
*1.The indicator of the emitter is illuminated only in the case the Wired Synchronization
is enabled and is off in the case the Optical Synchronization is enabled.
*2. Configurable by SD Manager 3.
*3. This is the case for the Standard Muting mode. For other muting modes, refer to
the F3SG-SR/PG User's Manual.
*4.The Area Beam Indicator closer to the "TOP" mark on the F3SG-SR/PG blinks.
*5.The Area Beam Indicator closer to the "BTM" mark on the F3SG-SR/PG blinks.
*6. DIP switches is on the Intelligent Tap.
*7. Refer to the F3SG-SR/PG User's Manual for more information on blinking patterns.
*8. F3SG-PGA-A/C does not support the Operating Range Selection function.
Note: In the SETTING state to make settings with the SD Manager 3, the TEST, LONG and CODE
indicators on the emitter, and the CFG, PNP and CODE indicators on the emitter/receiver blink.
(TEST:Yellow, LONG/CODE:Green, CFG/PNP/CODE: Green)
■LED Indicators of the Receiver (F3SG-PGA-L/-A), Emitter/Receiver (F3SG-PGA-C)
CODE
or
C
ERR
or
E
OSSD
or
O
MAINT
or
M
PNP
or
P
CFG
or
F
SEQ
or
S
■LED Indicators of the Emitter (F3SG-PGA-L/-A)
1
2
3
4
5
Scancode
Lockout
Operatingrange
Test
AreaBeam
Indicator(ABI)
(*1)
Green
Orange
OFF
Red
Green
OFF
Yellow
Green
Orange
Red
OFF
Code A is selected
Code B is selected
Automatic interference prevention by wired synchronization being performed
LOCKOUT state.The indicator is illuminated in the emitter of another sensor
segment than that having a lockout error (when in cascade connection or
between the emitter and receiver in theWired Synchronization)
Long Mode (*8) is selected
Short Mode (*8) is selected
---
The target beams of the ABI are unblocked and the safety
outputs are turned ON
Incident light level of the target beams of the ABI is 170%
(factory default setting (*2)) or less of ON-threshold (for 5 to 10 s)
The target beams of the ABI are blocked
The target beams of the ABI are unblocked (The ABI then will be
illuminated in green when the safety outputs are turned ON.)
---
LOCKOUT state.The indicator is illuminated in the emitter of a sensor segment
having a lockout error
LOCKOUT state due to Operating range selection setting error
---
External Test is being performed
MUTING or OVERRIDE state.In the MUTING state, only the ABI indicators in the
muting zone are blinking.Or the target beams of the ABI are blocked instantaneously
Incident light level of the target beams of the ABI is 170% (factory default setting (*2)) or less of ON threshold
5 to 10 s after illuminated when incident light level of the target beams of the ABI is 170% (factory default
setting (*2)) or less of ON threshold.Or one muting input becomes the ON state and the MUTING state has
not been started yet, or one muting input becomes the OFF state and the other is not in the OFF state yet.(*3)
LOCKOUT state due to Cap error or Other sensor error (*4), or Lockout state due to DIP Switch settingS error (*5)
---
Location
Indicator Name Color Illuminated Blinking
Location
Indicator Name Color Illuminated Blinking
---
CODE
or
C
ERR
or
E
LONG
or
L
TEST
or
T
1
2
3
4
5
6
7
8
Scan code
Lockout
ON/OFF
Maintenance
PNP/NPN
mode
Configuration
Sequence
Area Beam
Indicator (ABI)
Green
Orange
OFF
Red
Green
Red
Red
Orange
Green
OFF
Green
Yellow
Green
Orange
Red
OFF
Code A is selected
Code B is selected
Automatic interference prevention by wired synchronization being performed
LOCKOUT state.The indicator is illuminated in the receiver of another sensor
segment than that having a lockout error (when in cascade connection or
between the emitter and receiver in theWired Synchronization)
Safety outputs are in ON state
Safety outputs are in OFF state
LOCKOUT state due to a recoverable error (When in cascade
connection, the indicator of only the sensor segment having the
error is illuminated)
Safety outputs are instantaneously turned OFF due to ambient light,
vibration or noise.Or sequence error in Muting or Pre-Reset
PNP is configured
NPN is configured
Slow mode of ResponseTime Adjustment is enabled.
INTERLOCK state
The target beams of the ABI are unblocked and the safety
outputs are turned ON
Incident light level of the target beams of the ABI is 170%
(factory default setting (*2)) or less of ON-threshold (for 5 to 10 s)
The target beams of the ABI are blocked
The target beams of the ABI are unblocked (The ABI then will be
illuminated in green when the safety outputs are turned ON.)
---
LOCKOUT state.The indicator is illuminated in the receiver of a sensor segment having
a lockout error
---
LOCKOUT state due to Safety Output error, or error due to abnormal power supply or noise
LOCKOUT state due to a replacement- recommended error (When in cascade
connection, the indicator of only the sensor segment having the error blinks)
IntelligentTap is in the LOCKOUT state
Polarity of PNP is changed to NPN, or vice versa, during operation, and internal circuit is defective
---
LOCKOUT state due to Configuration error or Parameter error
Sequence or sequence error (*7) in Muting or Pre-Reset
MUTING or OVERRIDE state.In the MUTING state, only the ABI indicators in the muting
zone are blinking.Or the target beams of the ABI are blocked instantaneously
Incident light level of the target beams of the ABI is 170% (factory default setting (*2)) or less of ON threshold 5
to 10 s after illuminated when incident light level of the target be ams of the ABI is 170% (factory default setting
(*2)) or less of ON threshold.Or one muting input becomes the ON state and the MUTING state has not been
started yet, or one muting input becomes the OFF state and the other is not in the OFF state yet.(*3)
LOCKOUT state due to Cap error or Other sensor error (*4), or LOCKOUT state due to
DIP Switch setting error (*5)
---
---
±2.5°or less at operating range of 3 m or greater for emitter, receiver, and emitter/receiver
Not applicable to passive mirror
Infrared LEDs,Wavelength:870 nm
SELV/PELV 24 VDC ±20% (ripple p-p 10% max.)
See F3SG-SR/PG User's Manual for more information.
Two PNP or NPN transistor outputs (PNP or NPN is selectable by wiring of power supply.), Load current: 300 mA max., Residual voltage: 2 V
max. (except for voltage drop due to cable extension), Capacitive load: 1 µF max., Inductive load: 2.2 H max. (*1)(*2)(*3), Leakage current: 1
mA max.(PNP), 2 mA max.(NPN)(*4)
*1.The load current is 150 mA max.when the operating ambient temperature is 45 to 55°C.
*2.The residual voltage is 3V max. when the IntelligentTap is connected to the sensor.
*3.The load inductance is the maximum value when the safety output frequently repeats ON and OFF.When you use the safety output at 4 Hz
or less, the usable load inductance becomes larger.
*4.These values must be taken into consideration when connecting elements including a capacitive load such as a capacitor.
One PNP or NPN transistor output (PNP or NPN is selectable by wiring of power supply.)
Load current:100 mA max., Residual voltage:2 V max.(*)
*The residual voltage is 3V max. when the IntelligentTap is connected to the sensor.
Light emission stops when connected to 24V DC
ON voltage:Vs-3 V toVs (short circuit current:approx.5.0 mA) *, OFF voltage:0 V to 1/2Vs, or open (short circuit current: approx.6.0 mA) *
Light emission stops when connected to 0V DC
ON voltage:0 to 3 V (short circuit current: approx.6.0 mA), OFF voltage:1/2Vs to Vs, or open (short circuit current:approx.5.0 mA) *
Long:12 V toVs (short circuit current: approx.4.2 mA) * or open
Short:0 to 3 V (short circuit current:approx.4.2 mA)
PNP ON voltage:Vs-3V to Vs (short circuit current: approx.9.5 mA) *
OFF voltage:0 V to 1/2Vs, or open (short circuit current: approx.13.0 mA) *
NPN ON voltage:0 to 3 V (short circuit current: approx.13.0 mA)
OFF voltage:1/2 Vs toVs, or open (short circuit current: approx.9.5 mA) *
PNP ON voltage:Vs-3V to Vs (short circuit current: approx.4.5 mA) *
OFF voltage:0 V to 1/2Vs, or open (short circuit current: approx.7.0 mA) *
NPN ON voltage:0 to 3 V (short circuit current: approx.7.0 mA)
OFF voltage:1/2 Vs toVs, or open (short circuit current: approx.4.5 mA) *
Output short-circuit protection
Optical synchronization by Scan Code: in up to 2 sets Wired synchronization: in up to 3 sets (See F3SG-SR/PG User's Manual for more
information.)
Self-test (at power-on, and during operation), External test (light emission stop function by test input)
Interlock, External Device Monitoring (EDM) Pre-Reset, PSDI, Fixed blanking/Floating Blanking Reduced Resolution Muting/Override, Mutual
Interference Prevention, PNP/NPN Selection, ResponseTime Adjustment (See F3SG-SR/PG User's Manual for more information.)
Operating:-30 to 55°C (non-icing), Storage:-30 to 70°C
Operating:35% to 85% (non-condensing), Storage:35% to 95%
IEC 60529:IP65 and IP67, JIS C 0920 Annex 1:IP67G (IP67G is applicable to the F3SG-SRA only.)
In optical synchronization:100 m max* between power supply and emitter, between power supply and receiver, between power supply and emitter/receiver
In wired synchronization:100 m max* between power supply and emitter, between power supply and receiver, between emitter and receiver, between power
supply and emitter/receiver
* When the Intelligent Tap (F39-SGIT-IL3) is connected to the sensor, this applies in the case of the rated power supply of 24VDC to 24 VDC +20%.
Net:3.5 kg max., Gross: 4.2 kg max.
1.1×10-8 max.(IEC 61508)
Model F3SG-4PGA□□□□A F3SG-4PGA□□□□L F3SG-4PGA□□□□C
Object resolution (Detection capability)*
Beam gap
Number of beams
Operating
range
Response
time
Effective aperture angle
(EAA) (IEC 61496-2)
Light source
Power supply voltage (Vs)
Current consumption
Safety outputs (OSSD)
Auxiliary output
Input voltage
Protective circuit
Mutual interference prevention
Test function
Safety-related functions
Ambient temperature
Ambient humidity
Degree of protection (IEC 60529)
Cable
extension
PFHD
Performance
Electrical
Functional
Environmental
Connections
Weight
Conformity
Normal mode
×2 Slow mode
×4 Slow mode
×8 Slow mode
TEST
OPERATING RANGE
SELECT Input
RESET/EDM
MUTE A/B,
PRE-RESET
Rootcable
ON to OFF
OFF to ON
ON to OFF
OFF to ON
ON to OFF
OFF to ON
ON to OFF
OFF to ON
Optical synch.: 8 ms, Wired synch.: 10 ms
Optical synch.: 40 ms, Wired synch.: 50 ms
Optical synch.: 16 ms, Wired synch.: 20 ms
Optical synch.: 80 ms, Wired synch.: 100 ms
Optical synch.: 32 ms, Wired synch.: 40 ms
Optical synch.:160 ms, Wired synch.: 200 ms
Optical synch.: 64 ms, Wired synch.: 80 ms
Optical synch.: 320 ms, Wired synch.: 400 ms
*SelectablebySDManager3.
*The Vs indicates a supply voltage value in your environment.
See F3SG-SR/PG User's Manual for more information.
F3SG-4PGA0670-2□:500 mm
F3SG-4PGA1070-4□:300 mm
F3SG-4PGA1370-4□:400 mm
F3SG-4PGA0670-2□:2
F3SG-4PGA1070-4□:4
F3SG-4PGA1370-4□:4
--- ---
Self-test (at power-on, and during operation)
---
F3SG-4PGA0670-2□:500 mm
F3SG-4PGA0970-3□:400 mm
F3SG-4PGA1070-4□:300 mm
F3SG-4PGA1370-4□:400 mm
F3SG-4PGA0670-2□:2
F3SG-4PGA0970-3□:2
F3SG-4PGA1070-4□:4
F3SG-4PGA1370-4□:4
0.5 to 20 m
Opaque objects, 30-mm dia.
*It is the minimum diameter of an object that can be detected on the any optical axes, and the definition of the term is different from that for the F3SG-SR.The
minimum diameter that can be detected in any position of the product length is "detection capability (30 mm) + beam gap".
Other manuals for F3SG-PG Series
2
This manual suits for next models
3
Popular Floodlight manuals by other brands

Eurolux
Eurolux FS13 quick start guide
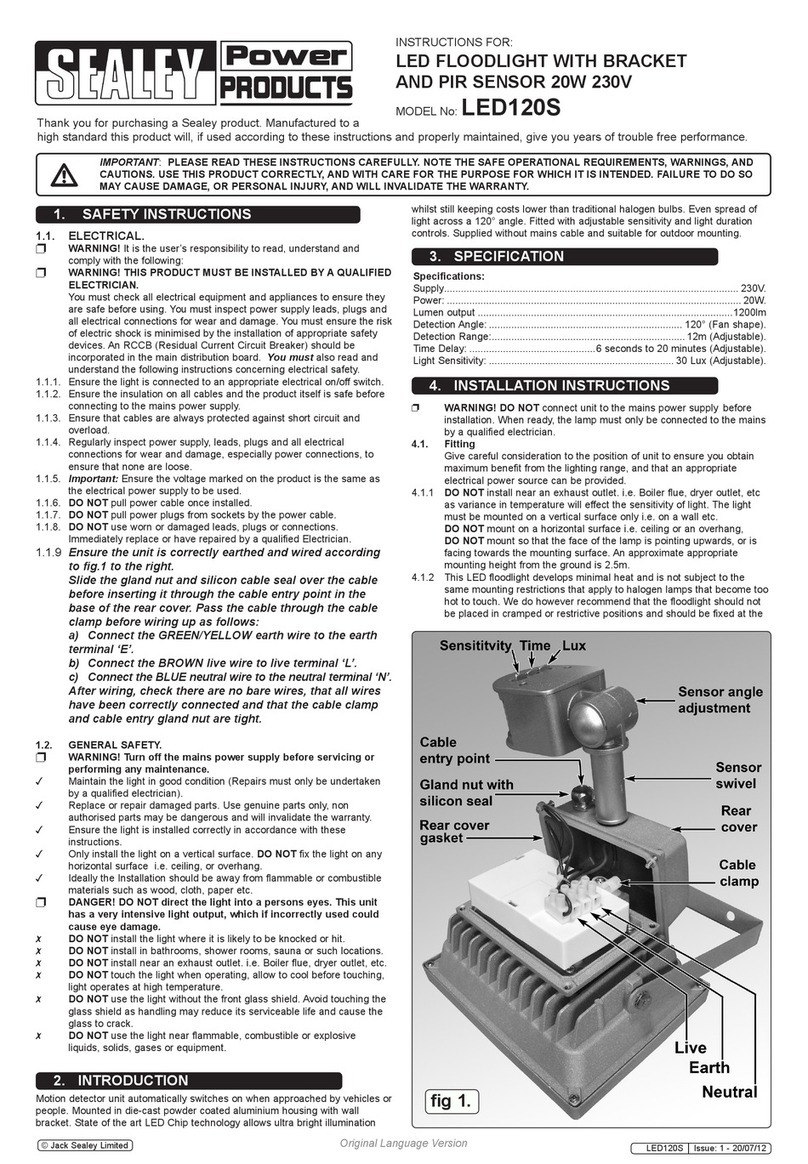
Sealey
Sealey LED120S instructions
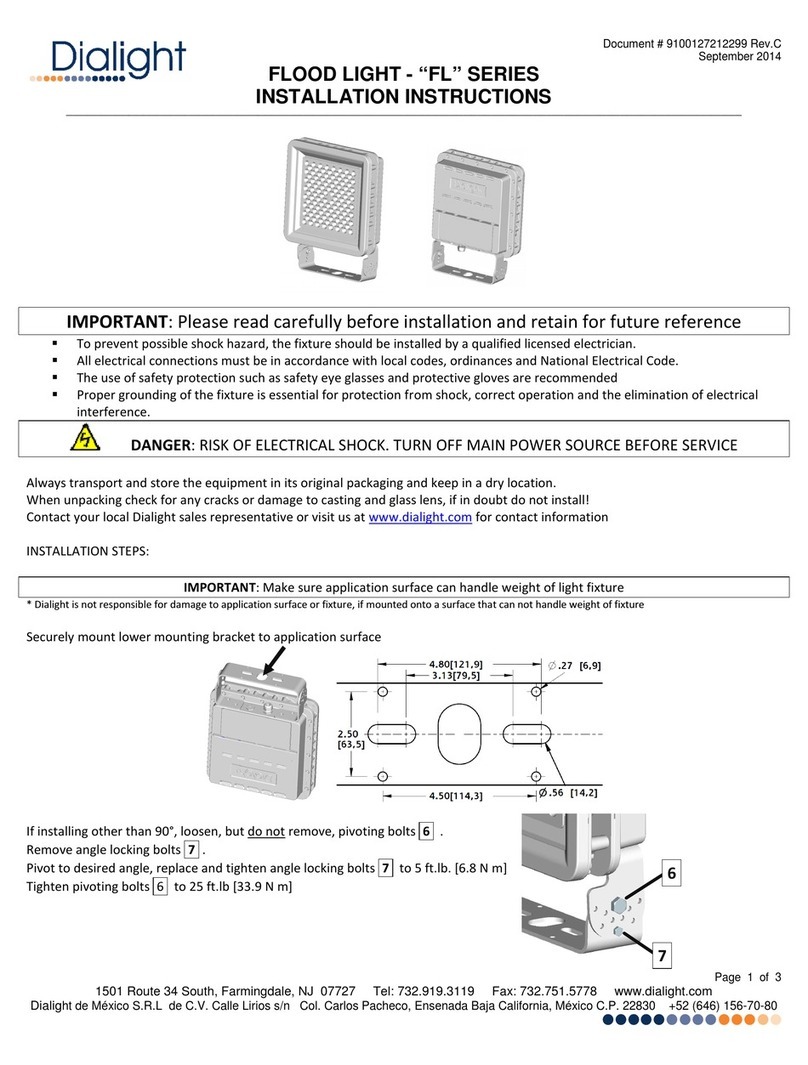
Dialight
Dialight FL SERIES installation instructions
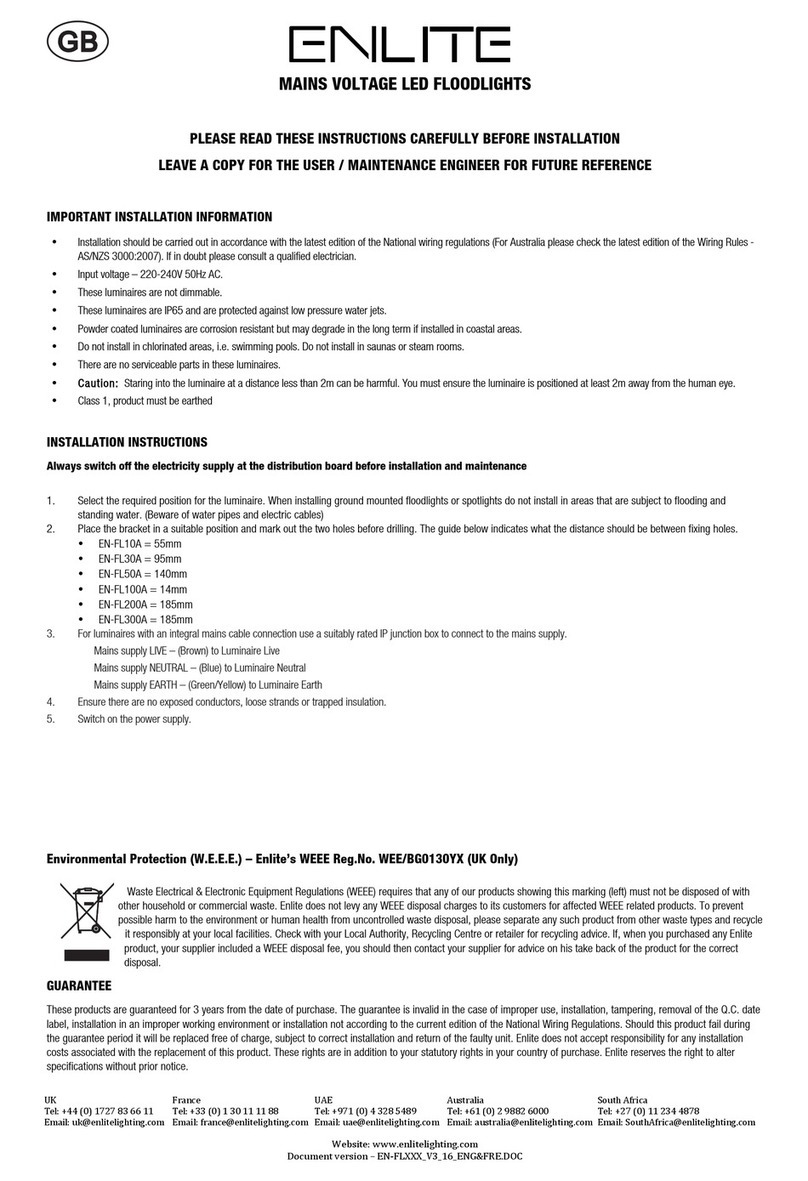
Enlite
Enlite EN-FL10A installation instructions

Good Earth Lighting
Good Earth Lighting Downfire SE1084-WH3-02LF0-G quick start guide
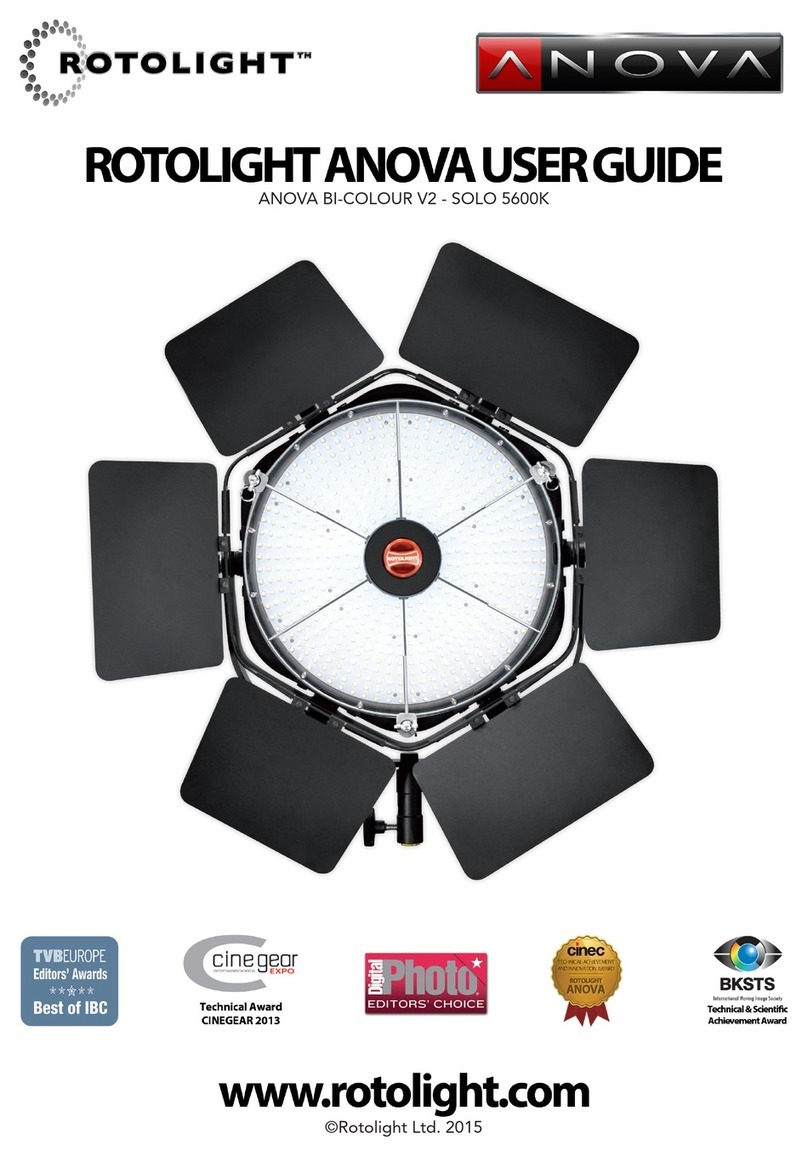
Rotorlight
Rotorlight ANOVA BI-COLOUR V2 - SOLO 5600K user guide