PMA Digital 280-1 User manual

PMA Prozeß- und Maschinen-Automation GmbH
Digital 280-1
digital indicator
Digita
l
280-1
Di
g
ital 280-1
Operating manual
English
9499-040-67311
Valid from: 8415

© PMA Prozeß- und Maschinen-Automation GmbH •Printed in Germany
All rights reserved.
No part of this document may be reproduced or published in any form or by any means
without prior written permission from the copyright owner.
A publication of PMA Prozeß- und Maschinen Automation
P.O.Box 310229
D-34058 Kassel
Germany
ûBlueControl
More efficiency in engineering,
more overview in operating:
The projecting environment for the BluePortcontrollers
Description of symbols:
gGeneral information
aGeneral warning
lAttention: ESD sensitive devices
ATTENTION!
Mini Version and Updates on
or on PMA-CD
www.pma-online.de

Digital 280-1 3
Content
1Mounting ..............................5
2Electrical connections .......................7
2.1 Connecting diagram .........................7
2.2 Terminal connection.........................7
3Operation .............................11
3.1 Front view .............................11
3.2 Behaviour after power-on .....................11
3.3 Operating level ...........................12
3.3.1 Min/max function ............................12
3.3.2 Tare function ..............................13
3.3.3 Sample&hold amplifier .........................13
3.3.4 O2measurement .............................14
3.3.5 Extended operating level ........................15
3.3.6 Alarm handling .............................16
3.4 Maintenance manager / Error list .................17
4Controller .............................19
4.1 Operation..............................19
4.2 Control parameters .........................19
4.3 Self-tuning .............................20
4.3.1 Self-tuning start ( Ù+È)......................20
4.3.2 Self-tuning cancellation ........................20
4.3.3 Acknowledgement procedures in case of unsuccessful self-tuning . 21
4.3.4 Examples for self-tuning attempts ..................22
4.3.5 (controller inverse, heating or heating/cooling) ...........22
4.4 Manual tuning ...........................22
4.5 Operating structure.........................24
5Configuration level ........................25
5.1 Configuration survey........................25
5.2 Configuration ...........................26
5.3 Configuration examples ......................34
5.3.1 On-Off controller / Signaller (inverse) .................34

4 Digital 280-1
5.3.2 2-point controller (inverse) .......................35
5.3.3 Continuous controller (inverse) .....................36
5.3.4 Digital 280-1 with measured value output ...............37
6Parameter setting level ......................39
6.1 Parameter survey ..........................39
6.2 Parameter..............................40
6.3 Input scaling ............................41
6.3.1 Input Inp ...............................41
7Calibration level .........................43
7.1 Offset correction ..........................43
8BlueControl ............................47
9Versions ..............................49
10 Technical data ..........................51
11 Safety hints ............................57
11.1 Resetting to factory setting.....................58
12 Notes ................................59

1Mounting
Safety switch:
For access to the safety switches, the indicator must be withdrawn from the hou-
sing. Squeeze the top and bottom of the front bezel between thumb and forefinger
and pull the controller firmly from the housing..
10V i mA/Pt right 1 Current signal / Pt100 / thermocouple/mV at InP
left Voltage signal (V) at InP
Loc open Access to the levels is as adjusted by means of BlueControl
(engineering tool) 2
closed 1 all levels accessible wihout restriction
1Factory setting 2Default setting: display of all levels
suppressed, password PASS =OFF
aSafety switch 10V imA/Pt always in position left or right. Leaving the
safety switch open may lead to faulty functions!
lCaution! The unit contains ESD-sensitive components.
Mounting
Digital 280-1 5
or
*
Ü
*
Ü
%
max.
95% rel.
max. 60°C
0°Cmin.
Loc 10V imA/Pt
Loc 10V mA/Pt
security switch
1..10
(0.04..0.4")
48 (1.89")
96 (3.78")
10 (0.4")
118 (4.65")
92 +0,8
(3.62" )
+0.03
min.48
(1.89")
45
+0,6
(1.77" )
+0.02
F
FUNC
ADA
OUT1
OUT2
OUT3
ERR
min max
Digital 280-1

2Electrical connections
2.1 Connecting diagram
* Safety switch mA iV in position left
gThe indicator is provided with screw terminals from 0,5 to 2,5mm².
2.2 Terminal connection
Power supply connection 1
See chapter 10 "Technical data"
Connection of input INP1 2
Input for variable x1 (process value)
athermocouple
bresistance thermometer (Pt100/ Pt1000/ KTY/ ...)
cpotentiometer
dcurrent (0/4...20mA)
evoltage (-2,5...115/-25...1150/-25...90/ -500...500mV)
fvoltage (0/2...10V/ -5...5V)
Electrical connections
6 Connecting diagram Digital 280-1
U
Logic
di2
di3
UT
Option
RXD-B
GND
RXD-A
TXD-B
TXD-A
RS485 RS422
Modbus RTU
RGND
DATA B
DATA A
L
N
90...250V
24V AC/DC
di1
INP1
OUT3
OUT2
OUT1
1
7
5
8
6
9
10
11
12
13
14
15
4
3
2
1
7
5
8
6
9
10
11
12
13
14
15
4
3
(2)
17
16
7
8
9
di1
V*
-
+
mA
-
+
100%
0
+
mV
-
+
1
3
4
5
2
6
7
6
abcd e
f
8
ghi

Connection of input di1 4
Digital input, configurable as switch or push-button
Connection of outputs OUT1/2 5
Relay outputs 250V/2A normally open with common contact connection
Connection of output OUT3 6
glogic (0..20mA / 0..12V)
hvoltage (0/2...10V)
icurrent (0/4...20mA)
itransmitter power supply
Connection of inputs di2/3 7(option)
Digital inputs (24VDC external), galvanically isolated, configurable as switch or
push-button
Connection of output UT8(option)
Supply voltage connection for external energization
Connection of bus interface 9(option)
RS422/485 interface with Modbus RTU protocol
aIf UTand the universal output OUT3 is used there may be no external galvanic
connection between measuring and output circuits!
Electrical connections
Digital 280-1 Terminal connection 7
Option
+24VDC
5mA
5mA
0V
1
2
3
K
+
-
+
-
+
-
17,5V
22mA
OUT3
J
J
x
1
7
5
8
6
9
10
11
12
13
14
15
4
3
5
1
7
5
8
6
9
10
11
12
13
14
15
4
3
(2)
17
16
78 di2/3, UT2-wire transmitter supply
1
2
3
K
+
-
+
-
13V
22mA
7
8
9
10
11
12
13
14
15
6OUT3 transmitter supply

* Interface description Modbus RTU in seperate manual: see page .
Electrical connections
8 Terminal connection Digital 280-1
12
13
14
15
17
(16)
11
12
13
14
15
10
12
13
14
15
17
(16)
11
12
13
14
15
10
12
13
14
15
17
(16)
11
12
13
14
15
RGND RGND RGND
RT
interface
converter
RS485-RS232
PC
DATA A
DATA B
DATA A
DATA B
DATA A
DATA B
J
max. 1000m
twisted pair
10
RT
RGND optional connection
R = line resistanceT
12
13
14
15
17
16
10
11
12
13
14
15
10
11
12
13
14
15
10
11
12
13
14
15
12
13
14
15
17
16
12
13
14
15
17
16
9RS485 interface (with RS232-RS485 interface converter) *
3
4
7
5
8
6
9
10
+
_
SSR
+
_
SSR
+
_
SSR
serial installation
7
8
9
Logic
4V
4V
4V
12V
I=22mA
max
7
8
9
7
8
9
parallel installation
+
_
SSR
+
_
SSR
I=22mA
max
12V
7
5
8
6
9
10
4
3
7
8
9
6OUT 3 als Logikausgang mit Solid-State-Relais (Reihen- und Parallel-Schaltung)

Connecting exampleDigital 280-1:
aCAUTION:
Using a temperature limiter is recommendable in systems where
overtemperature implies a fire hazard or other risks.
Electrical connections
Digital 280-1 Terminal connection 9
1
2
3
4
7
5
8
6
9
10
11
12
13
14
15
Logic
+
_
L1
L2
N1
N2
fuse
1
2
3
4
7
5
6
fuse
TB 40-1
temperature limiter
1
Digital 280-1
fuse
SSR
reset-
switch
contactor
heating
1TB 40-1 temperature limiter
standard-version (3 relay)
TB40-100-0000D-000
further versions on demand
r
++
1
7
5
8
6
9
10
11
12
13
14
15
4
3
2
1
7
5
8
6
9
10
11
12
13
14
15
4
3
2

3Operation
3.1 Front view
1measured value display
2statuses of switching outputs OuT.1... 3(or alarm statuses)
3lit with self-tuning activated
4lit with tare or sample & hold function activated
5lit with entry in the error list
6function-key
7down-key
8up-key
9enter-key: calls up extended operating level/ errorlist
0pc connection for BlueControl (engineering-tool)
gThe measured value is displayed as standard. At parameter setting, configuration,
calibration level and at the extended operating level, the display changes
cyclically between parameter name and parameter value.
3.2 Behaviour after power-on
After supply voltage switch-on, the unit starts with the operating level.
The unit is in the condition which was active before power-off.
If KS4x-1 was in manual mode before power-off, the controller starts with cor-
recting value Y2 after switching on again.
Operation
10 Front view Digital 280-1
F
FUNC
ADA
OUT1
OUT2
OUT3
ERR
min max
Digital 280-1
2
3
4
5
6
1
0
987

3.3 Operating level
3.3.1 Min/max function
The minimum and maximum values are stored.
As long as the Ìkey is pressed, the minimum
value is displayed. As long as the Èkey is pressed, the maximum
value is displayed.
Deleting the minimum value
Keeping the Ìkey pressed whilst actuating key Èdeletes the minimum value.
Additionally, determination whether a digital input or key è should delete the mi-
nimum value is possible during configuration (rES.L).
Deleting the minimum and maximum values can be done also via interface.
Deleting the maximum value
Keeping the Èkey pressed whilst actuating key Ìdeletes the maximum value.
Additionally, determination whether a digital input or key è should delete the ma-
ximum value is possible during configuration (rES.H).
Deleting the minimum and maximum values can be done also via interface.
gWhen switching off Digital 280-1, minimum and maximum values are deleted.
Operation
Digital 280-1 Operating level 11
FUNC
ADA
OUT1
OUT2
OUT3
ERR
Digital 280-1
FUNC
ADA
OUT1
OUT2
OUT3
ERR
Digital 280-1
Ì
min
FUNC
ADA
OUT1
OUT2
OUT3
ERR
Digital 280-1
FUNC
ADA
OUT1
OUT2
OUT3
ERR
Digital 280-1
Ì
max

3.3.2 Tare function
When switching on the tare function, the instantaneous measured value is set to
zero. In this case, measurement is continued with this offset. By switching off the
tare function, the actual measured value is displayed again.
measured value
effective value
Tare can be activated during configuration (Func rFnc.1 = 1).
Dependent of configuration, tare can be made effective via one of the digital in-
puts di1, di2, di3, the èkey or interface (LOGI rtArA).
3.3.3 Sample&hold amplifier
With the sample & hold function activated, the measured value is held on the dis-
play. By switching off the sample & hold function, the actual measured value is
displayed again.
measured value
effective value
Sample & hold can be activated during configuration (Func rFnc.1 = 2).
Dependent of configuration, sample & hold can be made effective via one of the
digital inputs di1, di2, di3,the è-key or via interface (LOGI rHOLd).
Operation
Digital 280-1 Operating level 12
t
è
FUNC
ADA
ERR
è
FUNC
ADA
ERR
è
FUNC
ADA
ERR
è
FUNC
ADA
ERR
t
è
FUNC
ADA
ERR
è
FUNC
ADA
ERR
è
FUNC
ADA
ERR
è
FUNC
ADA
ERR
è
FUNC
ADA
ERR
è
FUNC
ADA
ERR

3.3.4 O2measurement
For measurement, lambda probes (λprobes) are used.
The electromotive force (in Volt) supplied by the λprobes is dependent of the
instantaneous oxygen content and of the temperature. Therefore, Digital 280-1
can display accurate measurement results only, provided that the probe tempera-
ture is known to the indicator.
Enter the temperature in °C in parameter tEmP. When using heated λprobes, the
probe temperature can be entered directly. When using non-heated λprobes, ho-
wever, the displayed values can be accurate only for a narrow temperature band.
gUnless the probe temperature is known, we recommend using our KS90-1
Oxygen (temperature measurement via a second input).
Configuration:
Adjust O2measurement in function 1:
Func rFnc.1 3 O2 measurement
Display: The displayed value is always a % value.
As it is mostly necessary to cover a wide measuring range, we recommend adju-
sting a high number of digits behind the decimal point during configuration, whe-
reby loss of high values is prevented due to floating decimal point display
(0,0001 (1 ppm) to 99999 is possible) .
Specify the number of digits behind the decimal point below othr :
othrrdP
0 0 digits behind the decimal point
1 1 digit behind the decimal point
2 2 digits behind the decimal point
3 3 digits behind the decimal point
4 4 digits behind the decimal point
Adjust the sensor type to one of the high-impedance voltage inputs in InP:
Specification in BlueControl Effective measuring range
Inp.1r
S.tYP
41 Special ( 0...100 mV) -2,5...115 mV
42 Special ( 0...1000 mV) -25...1150 mV
43 Special ( -25...90 mV)
44 Special ( -500...500 mV)
These high-impedance inputs are not provided with break monitoring. If necessa-
ry, measurement input protection is possible via limit value processing.
Operation
Digital 280-1 Operating level 13

3.3.5 Extended operating level
The content of the extended operating level is determined by means of BlueCon-
trol (engineering tool). Parameters which are important or which are used fre-
quently can be copied into the extended operating level.
Actuating key Ùswitches to the first value
of the extended operating level (may be
preceded by error list or set-point).
The selected parameters can be changed
by pressing keys Ìand È.
Press Ùto go to the next parameter.
Press Ùto return to the normal display
after the last parameter .
Operation
14 Operating level Digital 280-1
FUNC
ADA
OUT1
OUT2
OUT3
ERR
Digital 280-1
Ù
FUNC
ADA
OUT1
OUT2
OUT3
ERR
Digital 280-1
FUNC
ADA
OUT1
OUT2
OUT3
ERR
Digital 280-1
Ù
FUNC
ADA
OUT1
OUT2
OUT3
ERR
Digital 280-1
FUNC
ADA
OUT1
OUT2
OUT3
ERR
Digital 280-1
Ù

3.3.6 Alarm handling
Max. three alarms can be configured and assigned to the individual outputs. Ge-
nerally, outputs OuT.1... OuT.3 can be used each for alarm signalling. If more
than one signal is linked to one output the signals are OR linked. Each of the 3 li-
mit values Lim.1 …Lim.3 has 2 trigger points H.x (Max) and L.x (Min), which
can be switched off individually (parameter = “OFF”). Switching difference
HYS.x of each limit value is adjustable.
normally closed ( ConF /Out.x/O.Act =0)
normally open ( ConF /Out.x/O.Act =1)
Operation
Digital 280-1 Operating level 15
H.1
LED
HYS.1
InL.1 InH.1
Operaing principle absolut alarm
L.1 =OFF
LED
HYS.1
H.1
InL.1 InH.1
SP
Operating principle relative alarm
L.1 =OFFF
L.1
LED
HYS.1
InL.1 InH.1
H.1 =OFF
L.1
LED
HYS.1
InL.1 InH.1
SP
H.1 =OFF
L.1
LED LED
HYS.1 HYS.1
H.1
InL.1 InH.1
L.1
LED LED
HYS.1 HYS.1
H.1
InL.1 InH.1
SP

gThe variable to be monitored can be selected seperately for each alarm via
configuration
The following variables can be monitored:
wprocess value
wcontrol deviation xw (process value - set-point)
wcontrol deviation xw + suppression after start-up or set-point change
As there is automatically a control deviation after starting up and after
set-point changes, however, the alarm is suppressed, until the signal was
within the limits once.
wSet-point
wCorrecting variable y (controller output signal)
gIf measured value monitoring + alarm status storage is chosen ( ConF /Lim /
Fnc.x=2), the alarm relay remains switched on until the alarm is resetted in the
error list ( Lim 1..3=1) or via interface.
3.4 Maintenance manager / Error list
In case of one or several errors, the extended operating
level always starts with the error list. A current entry
into the error list (alarm or error) is displayed by the
Err LED in the display.
For displaying the error list, pressing 1x Ùis necessary.
(with configuration as a controller, press 2x Ù).
Err LED status Signification Proceed as follows
blinks Alarm due to
existing error - Determine the error type in the error list via the error number
- Remove the error
lit Error removed,
Alarm not
acknowledged
-Acknowledge the alarm in the error list pressing key Èor Ì
-The alarm entry was deleted.
off No error, all alarm entries deleted
gSaved alarms (Err-LED is lit) can be acknowledged and deleted with the digital
input di1/2/3 or the Ò-key.
Configuration, see page 31: ConF /LOGI /Err.r
gIf an alarm is still valid that means the cause of the alarm is not removed so far
(Err-LED blinks), then other saved alarms can not be acknowledged and deleted.
Error status Signification
2Existing error Change to error status 1 after error removal
1Stored error Change to error status 0 after acknowledgement in error list
0No error/message not visible, except with acknowledgement
Operation
16 Maintenance manager / Error list Digital
280-1
FUNC
ADA
OUT1
OUT2
OUT3
ERR
Digital 280-1

4Controller
In addition to the simple indicator function, Digital 280-1 can be used also as a
signaller or an on/off controller, as a two point or a continuous controller.
Prerequisite: Digital 280-1 is fitted with option “with outputs” and is configured
for the controller function.
Configuration:
Function 2 provides selection between indicator and controller:
Func rFnc.2 Controller
4.1 Operation
Adjusting the set-point
Press key Ùto switch over to the
set-point. The set-point can be changed
by pressing keys Ìund È.
error list, if errors pending
extended operating level, if configured
4.2 Control parameters
The range of different processes to be controlled is very wide, from very fast
pressure control to very slow thermal processes such as control of a blast furnace.
As the controller behaviour has to be different with each of these processes, the
control parameters must be adjusted for the relevant process individually. Adjust-
ment can be done either manually or by the controller itself.
Controller
Digital 280-1 Operation 17
FUNC
ADA
OUT1
OUT2
OUT3
ERR
Digital 280-1
Ù
FUNC
ADA
OUT1
OUT2
OUT3
ERR
Digital 280-1
FUNC
ADA
OUT1
OUT2
OUT3
ERR
Digital 280-1
Ù
Ù
Ù

4.3 Self-tuning
After starting by the operator, the controller makes a self-tuning attempt. The
controller uses the process characteristics for quick line-out to the set-point wit-
hout overshoot.
gSelf-tuning start can be locked via BlueControl (engineering tool) ( P.Loc).
gti and td are taken into account only, if they were ≠OFF previously.
4.3.1 Self-tuning start ( Ù+È)
The operator can start self-tuning at any time. For
this, keys Ùand Èmust be pressed simultane-
ously. The AdA LED starts blinking.
The controller outputs 0% or Y.Lo, waits until the
process is at rest and starts self-tuning (AdA LED
lit permanently).
The self-tuning attempt is started when the following prerequisite is met:
wThe difference between process value iset-point must be ≥10% of the
set-point range ( SP.Hi -SP.LO) (with inverse action: process value smaller
than set-point, with direct action: process value higher than set-point).
After successful self-tuning, the AdA-LED is off and the controller continues
operating with the new control parameters.
4.3.2 Self-tuning cancellation
By the operator:
Self-tuning can always be cancelled by the operator. For this, press Ùand È
key simultaneously. With manual-automatic switch-over configured via Òkey,
self-tuning can also be canceled by actuating Òkey. The controller continues
operating with the old parameters in automatic mode in the first case and in ma-
nual mode in the second case.
By the controller:
If the Err LED starts blinking whilst self-tuning is running, successful self-tuning
is prevented due to the control conditions. In this case, self-tuning was cancelled
by the controller.
Dependent of control type, the output status is:
w3-pnt. stepping controller:
actuator is closed (0% output)
w2-pnt./ 3-pnt./ continuous controller:
If self-tuning was started from the automatic mode, the controller output is
0%. With self-tuning started from manual mode, the controller output is Y2.
Controller
18 Self-tuning Digital 280-1
FUNC
ADA
OUT1
OUT2
OUT3
ERR
Digital 280-1

Error-Status Selfoptimization
4.3.3 Acknowledgement procedures in case of unsuccessful self-tuning
1. Press keys Ùand Èsimultaneously:
The controller continues controlling using the old parameters
The Err LED continues blinking, until the self-tuning error was
acknowledged in the error list.
2. Press key Ù:
Display of error list at extended operating level. After acknowledgement
of the error message, the controller continues control using the old
parameters.
Controller
Digital 280-1 Self-tuning 19
Error status Description Behaviour
0 No error
3 Faulty control action Re-configure controller (inverse idirect)
4 No response of process variable The control loop is perhaps not closed: check
sensor, connections and process
5 Low reversal point Increase ( ADA.H) max. output limiting Y.Hi or
decrease ( ADA.C) min. output limiting Y.Lo
6 Danger of exceeded set-point
(parameter determined) If necessary, increase (inverse) or reduce (direct)
set-point
7 Output step change too small
(dy > 5%) Increase ( ADA.H) max. output limiting Y.Hi or
reduce ( ADA.C) min. output limiting Y.Lo
8 Set-point reserve too small Increase set-point (inverse), reduce set-point
(direct) or increase set-point range(r PArA / SEtp
/ SP.LO and SP.Hi )

4.3.4 Examples for self-tuning attempts
4.3.5 (controller inverse, heating or heating/cooling)
Start: heating power switched on
Heating power Y is switched off (1).
When the change of process value X
was constant during one minute (2),
the power is switched on (3).
At the reversal point, the self-tuning at-
tempt is finished and the new parameter
are used for controlling to set-point W.
Start: heating power switched off
The controller waits 1,5 minutes (1).
Heating power Y is switched on (2).
At the reversal point, the self-tuning at-
tempt is finished and control to the
set-point is using the new parameters.
Start: at set-point
Heating power Y is switched off (1).
If the change of process value X was
constant during one minute and the con-
trol deviation is > 10% of SP.Hi -
SP.LO (2), the power is switched on
(3). At the reversal point, the self-tu-
ning attempt is finished, and control to
set-point W is using the
new parameters.
4.4 Manual tuning
The optimization aid should be used with units on which the control parameters
shall be set without self-tuning.
For this, the response of process variable x after a step change of correcting varia-
ble y can be used. Frequently, plotting the complete response curve (0 to 100%)
is not possible, because the process must be kept within defined limits. Values Tg
and xmax (step change from 0 to 100 %) or ∆t and ∆x (partial step response) can
be used to determine the maximum rate of increase vmax.
Controller
Digital 280-1 Manual tuning 20
t
2
100%
Y
0%
X
W
start r13tturning point
blinks lit off
t
100%
Y
0%
X
W
start r12tturning point
blinks lit off
t
2
100%
Y
0%
X
W
start r13tturning point
blinks lit off
Table of contents
Other PMA Touch Panel manuals
Popular Touch Panel manuals by other brands
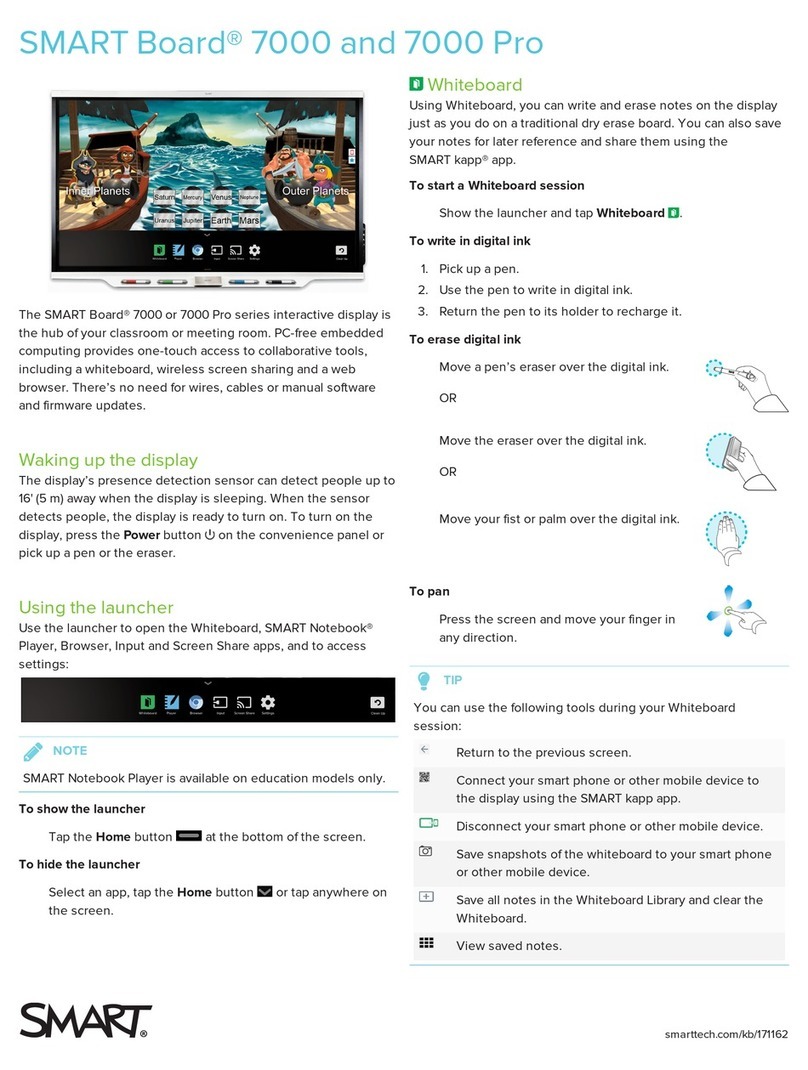
Smarttech
Smarttech SMART Board 7000 series manual
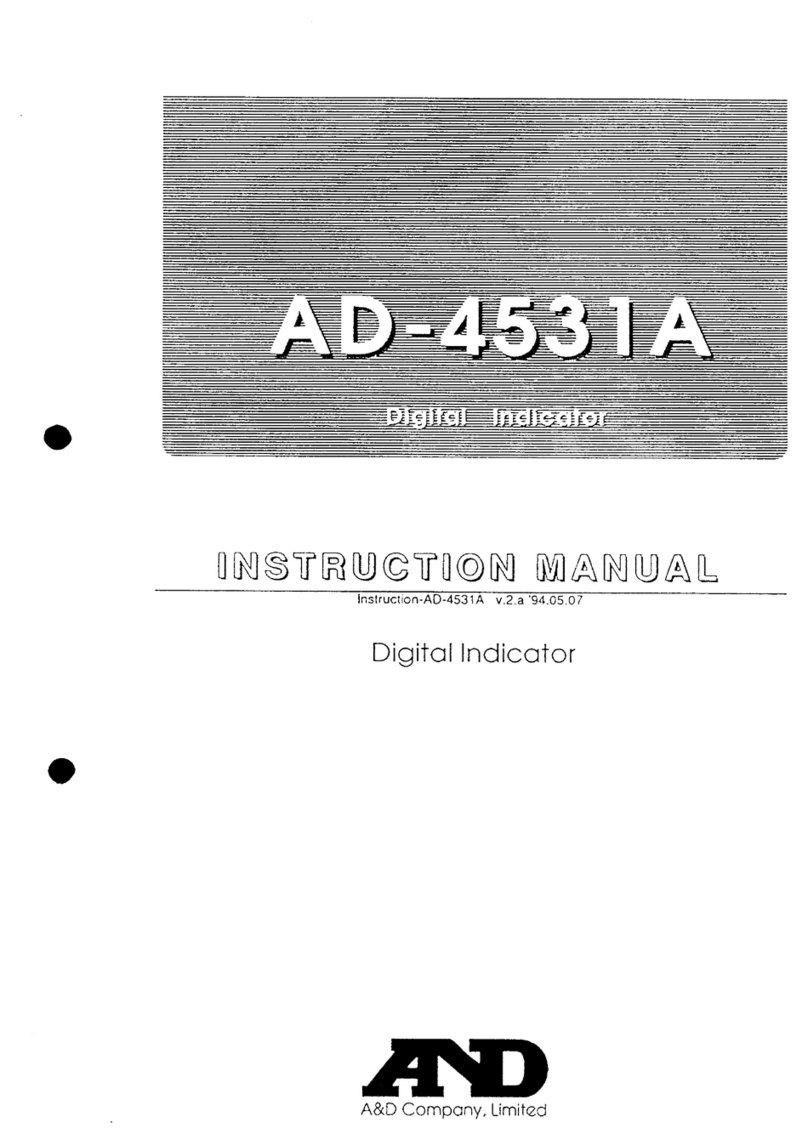
AND
AND Digital Indicator AD-4531A instruction manual
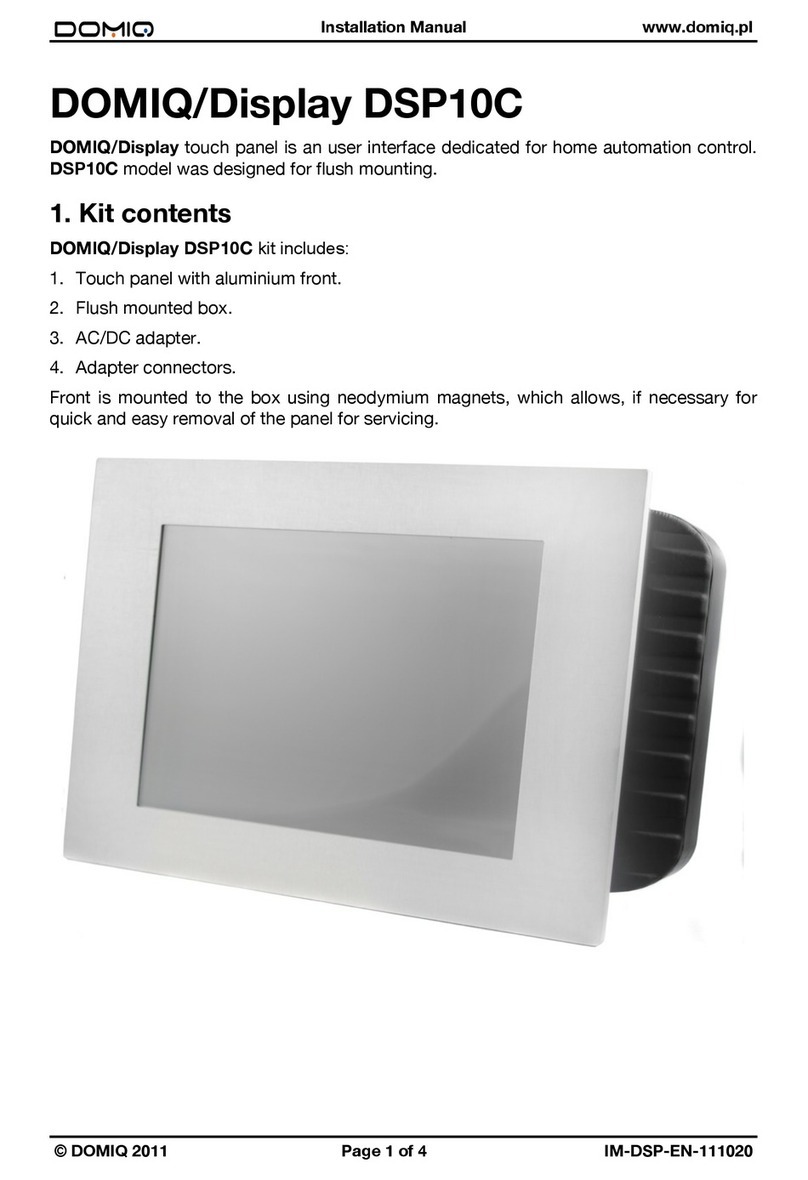
DOMIQ
DOMIQ Display DSP10C installation manual

IEI Technology
IEI Technology AFL3-W15C-ULT5-P-PC-4G user manual
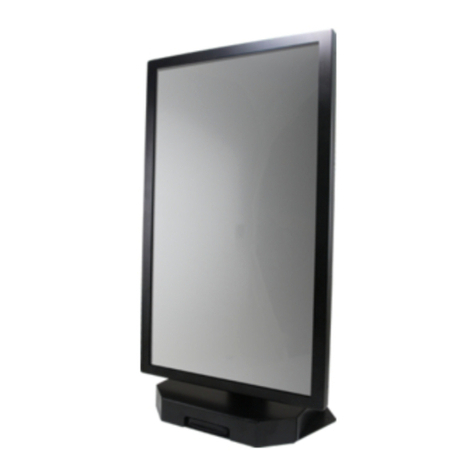
Avalue Technology
Avalue Technology SID-21V-Z37-A1R user manual
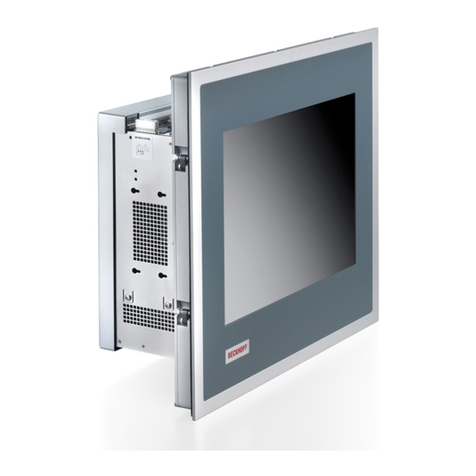
Beckhoff
Beckhoff CP65**-0060 Installation and operating instructions
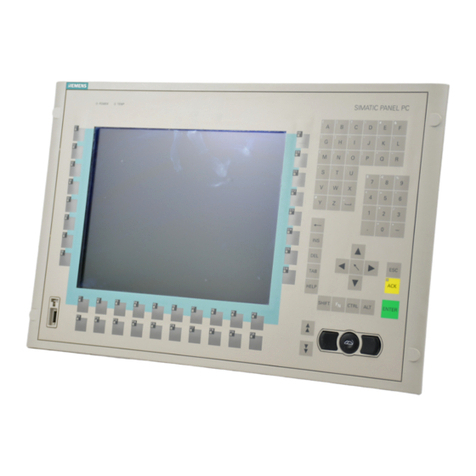
Siemens
Siemens SIMATIC PC 670 Equipment manual
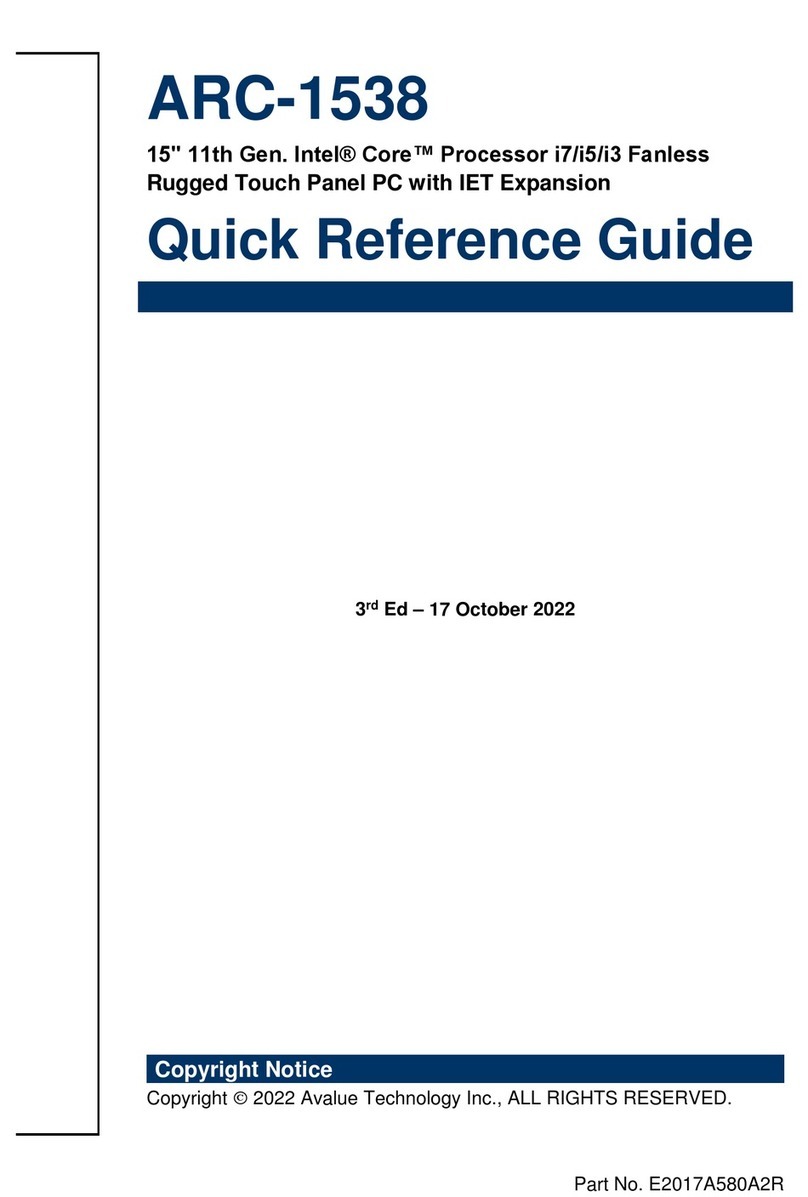
Avalue Technology
Avalue Technology ARC-1538-B Quick reference guide
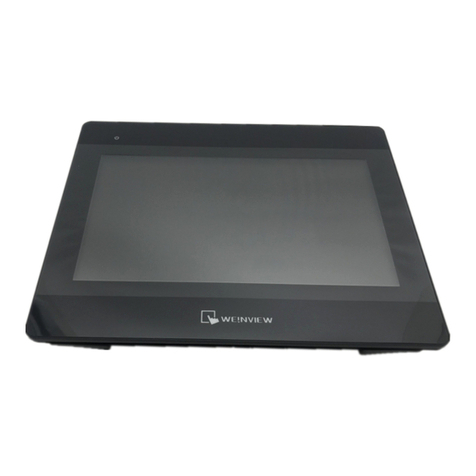
veinview
veinview MT6103iP series Installation instruction
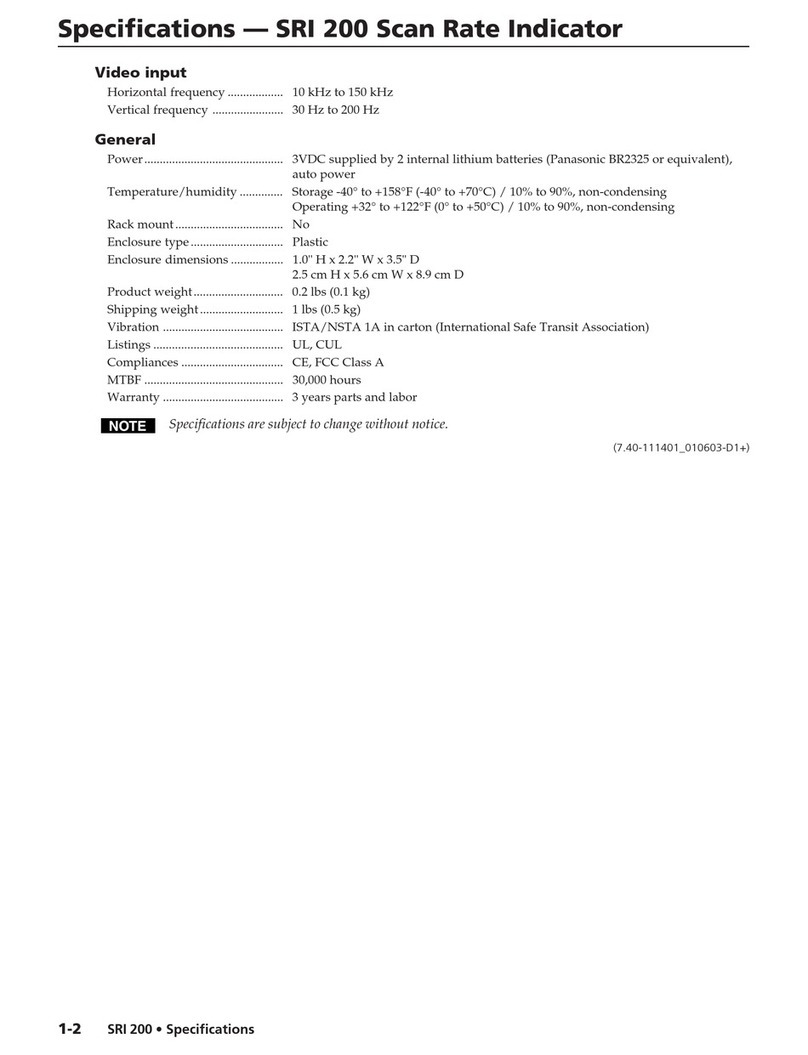
Extron electronics
Extron electronics Scan Rate Indicator SRI 200 Specifications

Sunricher
Sunricher SR-2300TR-G3-RGBW-US user manual

HDI
HDI mobi os Operation manual