Prosensor N1500LC User manual

INDEX
1
SAFETY SUMMARY .............................................................................................. 1
2
TECHNICAL ASSISTANCE ................................................................................... 1
3
PRESENTATION.................................................................................................... 2
4
PROCESS VARIABLE INPUT - PV ....................................................................... 3
5
ALARMS ................................................................................................................. 3
5.1
ALARM FUNCTIONS .........................................................................................................3
5.2
ALARM TIMER....................................................................................................................4
5.3
ALARM INITIAL BLOCKING .............................................................................................4
6
SPECIAL FUNCTIONS .......................................................................................... 5
6.1
SPECIAL FUNCTION KEY AND DIGITAL INPUT .........................................................5
6.2
AND KEYS...................................................................................................5
6.3
PO ER SUPPLY FOR LOAD CELLS (10 VDC) ...........................................................5
6.4
PROCESS VARIABLE RETRANSMISSION...................................................................6
6.5
CUSTOMIZED LINEARIZATION......................................................................................6
7
INSTALLATION ...................................................................................................... 6
7.1
RECOMMENDATIONS FOR INSTALLATION................................................................6
7.2
ELECTRICAL CONNECTIONS ........................................................................................6
8
OPERATION........................................................................................................... 7
8.1
CONFIGURATION PROTECTION ...................................................................................8
9
PROGRAMMING THE INDICATOR ...................................................................... 8
9.1
ORK CYCLE ....................................................................................................................8
9.2
ALARM CYCLE ...................................................................................................................9
9.3
FUNCTION CYCLE ............................................................................................................9
9.4
CONFIGURATION CYCLE ............................................................................................ 10
9.5
CUSTOMIZED LINEARIZATION CYCLE..................................................................... 10
9.6
CALIBRATION CYCLE ................................................................................................... 11
9.7
AUTOMATIC CALIBRATION CYCLE ........................................................................... 11
10
SERIAL COMMUNICATION ................................................................................ 12
10.1
RS485 INTERFACE: ELECTRICAL CONNECTION................................................... 12
11
PROBLEMS ITH THE INDICATOR.................................................................. 13
12
SPECIFICATIONS................................................................................................ 13
12.1
ORDERING INFORMATION:......................................................................................... 14
13
ARRANTY ......................................................................................................... 14
1SAFETY SUMMARY
The symbols below are used on the equipment and throughout this document to draw the user’s
attention to important operational and safety information.
CAUTION or WARNING:
Read complete instructions prior to
installation and operation of the unit.
CAUTION or WARNING:
Electrical Shock Hazard
All safety related instructions that appear in the manual must be observed to ensure personal safety
and to prevent damage to either the instrument or the system. If the instrument is used in a manner
not specified by the manufacturer, the protection provided by the equipment may be impaired.
2TECHNICAL ASSISTANCE
If you encounter a problem with your controller, review the configuration with regard to inputs, outputs,
alarms, etc. If the problem persists, contact your supplier.
SPECIAL RECOMMENDATIONS
Should the indicator be repaired, some special handling care should be taken. The device must be
withdrawn from the case and immediately placed in an anti-static wrap; protected from heat and
humidity.

2
3PRESENTATION
N1500LC is a universal process indicator which accepts a large variety of input signals and sensors.
A six-digit LED display shows measured value and all programming parameters.
Instrument configuration is achieved from the keypad, without any hardware change. Thus, the
selection of input type and alarms modes, besides other special functions, are accessed and defined
from the frontal keypad.
The user should read this manual thoroughly before using the instrument. It must be handled with
care and should be used accordingly for best results.
Some of the features of the basic version are:
•Input:: 4 to 20 mA, 0 to 20 mA, 0 to 20 mV, -20 to +20 mV and 0 to 50 mV
•2 alarm relays
•10 Vdc (or 5 Vdc) power supply for load cells;
•Memory for maximum and minimum values.
•Ho d, peak ho d, tare, zero tare and automatic zero functions;
•Process Variable (PV) retransmission in 0-20 mA or 4-20 mA.
•RS485 MODBUS RTU serial communication.
•3rd and 4th alarm relays.
The front panel is shown below.
Figure 1 - Front panel identification
Status Disp ay: Shows the process variable (PV) and the programming prompts.
Indicators A1, A2, A3 and A4: show active alarms.
Indicators Rx and Tx: indicate RS485 communication line is active.
PROGRAM key - This key is used to access different displays with the programmable
parameters of the device.
BACK key - This key is used to go back to the previous parameter displayed in the menu
cycle.
INCREMENTS/ZERO key and
DECREMENTS/ZERO key – They make possible
the change the parameter values. They are also used to display maximum and minimum
values stored in memory.
FUNCTION key - This special function key is used for pre-programmed functions as
explained in the SPECIAL FUNCTION KEY section of this manual.

3
4PROCESS VARIABLE INPUT - PV
The process variable (PV) input type is configured through the frontal keypad according to the codes
shown in table 1 (refer to INPUT TYPE parameter "in.typ
in.typin.typ
in.typ"). All input types are factory calibrated
and no additional calibration is required.
Type Code Measurement Range
Non-linear 4-20 mA c.4-20
Non-linear 0-20 mA c.0-20
Linear 4-20 mA 4-20 a
Linear 0-20 mA 0-20 a
Linear 0 – 50 mV c. 50
Non-linear -20 a 20 mV c. -20
Non-linear 0 – 20 mV C. 20
Linear 0 – 50 mV 50
Linear -20 a 20 mV -20 . 20
Linear 0 –20 mV 20
Programmable indication range.
Three maximum range options:
-32000 to +32000
0 to 60000
0 to 120000 (only even values are shown)
Non linear signals will be linearized according to the
programmed custom linearization.
Table 1 - Input type codes
5ALARMS
The indicator has 2 alarm outputs in the basic version and up to 4 alarms outputs optionally.
Each alarm has a corresponding LED message in the front panel to show alarm status.
5.1 ALARM FUNCTIONS
The alarms can be set to operate in seven different modes. These modes are shown in table 2 and
described below. The alarm can also be set as ‘disabled’.
5.1.1 Sensor break - Ierr
IerrIerr
Ierr
The alarm is triggered whenever the sensor breaks or is badly connected.
5.1.2 Low alarm - Lo
LoLo
Lo
The alarm relay is triggered whenever the measured value is below the alarm set point.
5.1.3 High alarm - Ki
KiKi
Ki
The alarm relay is triggered whenever the measured value is above the alarm set point.
Differential low – Dif.lo
Dif.loDif.lo
Dif.lo
Deviation alarm. Alarm relay is triggered whenever the difference (deviation) between the Process
Variable and the reference value (AlrEF
AlrEFAlrEF
AlrEF) is lower than the values defined in SP.AL
SP.ALSP.AL
SP.AL. For this function,
the triggering point is defined as:
(ALrEF
ALrEFALrEF
ALrEF – SP.AL
SP.ALSP.AL
SP.AL)
Differential High – Dif.ki
Dif.kiDif.ki
Dif.ki
Deviation alarm. Alarm relay is triggered when the difference (deviation) between the Process
Variable value and the reference value (AlrEF
AlrEFAlrEF
AlrEF) is greater than the value defined in SPAL
SPALSPAL
SPAL. For this
function, the triggering point is defined as:
(ALrEF
ALrEFALrEF
ALrEF + SP.AL
SP.ALSP.AL
SP.AL)
4.1.6 Differential (or Band) out of range – Dif.ov
Dif.ovDif.ov
Dif.ov
Deviation alarm. Alarm relay is triggered when the difference (deviation) between the Process
Variable value and the reference value (AlrEF
AlrEFAlrEF
AlrEF) has its modulus greater than the value configured in
SPAL
SPALSPAL
SPAL. For this function, the triggering point is defined as:
(ALrEF
ALrEFALrEF
ALrEF – SP.AL
SP.ALSP.AL
SP.AL) and (ALrEF
ALrEFALrEF
ALrEF + SP.AL
SP.ALSP.AL
SP.AL)

4
4.1.7 Differential (or Band) within range – Dif.In
Dif.InDif.In
Dif.In
Deviation alarm. Alarm relay is triggered when the difference (deviation) between the Process
Variable value and the reference value (AlrEF
AlrEFAlrEF
AlrEF) has its modulus lower than the value defined in
SPAL
SPALSPAL
SPAL. For this function, the triggering points are defined as:
(ALrEF
ALrEFALrEF
ALrEF – SP.AL
SP.ALSP.AL
SP.AL) and (ALrEF
ALrEFALrEF
ALrEF + SP.AL
SP.ALSP.AL
SP.AL)
TYPE PROMPT ACTION
Disabled
ff
Alarm is inactive
Sensor Break (input Error)
Ierr
Alarm will go ON if sensor breaks
Low Alarm
(Low)
Lo
Alarm SP
PV
High Alarm
(High)
Ki
Alarm SP
PV
Differential Low
(differential Low)
Dif.lo
PV
AL SP +
Deviation
AL SP
Differential High
(differential High)
Dif.ki
PV
AL SP +
Deviation
AL SP
Differential out of range
(differential out)
Dif.ov
PV
AL SP +
Deviation
Positive
Deviation
AL SP
AL SP -
Deviation
Differential within range
(differential Within)
Dif.In
PV
AL SP +
Deviation
Negative
Deviation
AL SP
AL SP -
Deviat.
Table 2 - Alarm functions
5.2 ALARM TIMER
The alarms can be configured to perform timing functions. The configuration allows the alarm output
to be delayed, or to deliver a single pulse or a train of pulses. The delay, the pulse width and the
period are defined by the user.
Table 3 shows these advanced functions. Times T1 and T2 can be programmed from 0 to 6500
seconds. Programming 0 (zero) in the timer parameters T1 and T2 disables the timer function.
The display alarm indicators (A1, A2, A3 or A4) remain ON while their respective alarm conditions are
present, regardless of the current output status, which may be temporarily off due to the timer action.
Advanced
Function
T1 T2 ACTION
Normal
Operation
0 0
Alarm Event
Alarm
Output
Delayed 0 1 s to 6500
s
Alarm Event
Alarm
Output T2
Pulse 1 s to 6500
s
0
Alarm Event
Alarm
Output T1
Oscillator 1 s to 6500
s
1 s to 6500
s
Alarm Event
Alarm
Output T1 T2 T1
Table 3 - Timer Alarm Functions
5.3 ALARM INITIAL BLOCKING
The initial blocking option inhibits the alarm from being recognized if an alarm condition is present
when the controller is first energized. The alarm will be triggered only after the occurrence of a non
alarm condition followed by a new occurrence for the alarm.
The initial blocking is disabled for the sensor break alarm function.

5
6SPECIAL FUNCTIONS
6.1 SPECIAL FUNCTION KEY AND DIGITAL INPUT
The
key (special function key) in the frontal panel of the controller as well as the Digital Input
may be assigned different functions that will be chosen by the user during the setup: These functions
can be chosen independently, both for the
key and the Digital Input. The
key and Digital
Input functions are explained below.
6.1.1 kold – Freeze measured value
The ho d function freezes the measured value showed in the display. Each time the key or the
Digital Input is selected, there is a change from ho d to normal mode.
henever the indicator is in the ho d mode, the message “koLd
koLdkoLd
koLd” will be displayed so that the
operator will be aware that the value displayed is the frozen value and not the current reading.
6.1.2 Pkold – Maximum value
The indicator will automatically work in the Peak Ho d mode whenever the
key or the Digital
Input are programmed as “PkoLd
PkoLdPkoLd
PkoLd”.
hile in this operation mode the indicator always shows the maximum value measured, since the last
time the key or the Digital Input were pressed.
Each activation of the key or digital input triggers a new Peak Ho d cycle and the display resets
with a new peak value.
6.1.3 xi – Displays Maximum
Displays the maximum (High) value the indicator measured since the last reset.
6.1.4 Lo – Displays Minimum
Displays the minimum (Low) value the indicator measured since the last reset.
6.1.5 rESEt - Clears Maximum and Minimum
If this “rESEt” function is programmed, every touch of the key or Digital Input activation clears
the memory and a new cycle of maximum and minimum values memorization will start.
6.1.6 zero – Zero Function
Available only for the key. It resets the scale. This function is used to eliminate the influence of
interference or small deviations in the zero of a scale. Reset is only accomplished if the value shown
in the scale is within 2% of the end of scale. Zero is not lost if the scale is turned off.
6.1.7 tarE –Tare function
It is available only in the Digital Input configuration or through the
key. It changes indication to
zero (0000.0), regardless of the value applied to the input. It is used to eliminate indications of defined
values. In order to eliminate the tare, the user must press the key.
6.2 AND KEYS
The same Tare function available for the Digital Input can be quickly applied by using the key,
which does not need to be set up. The key is used to eliminate the tare applied.
The indicator accepts successive tares provided that the input signal (gross weight) does not exceed
the equipment end of scale.
6.3 POWER SUPPLY FOR LOAD CELLS (10 VDC)
N1500LC provides a 10 Vdc (or 5 Vdc) output to excite load cells. This power supply capacity is 50
mA.

6
6.4 PROCESS VARIABLE RETRANSMISSION
As an option, the indicator can be supplied with an isolated 0-20 mA or 4-20 mA analog output for
Process Variable (PV) retransmission.
The PV values that define the scale of the 0 mA / 4 mA to 20 mA retransmission can be programmed
by the user in the high and ow output imits (0v.lol
0v.lol0v.lol
0v.lol e 0v.kol
0v.kol0v.kol
0v.kol), at configuration level. High and
low limits can be freely programmed, even with a low limit higher than high limit, resulting in a
reversed retransmission signal (decreasing signal when PV increases).
hen this option is available, retransmission will be always active, so that the user will not be required
to turn it on or off.
For a voltage output signal an external shunt (calibrated resistor) should be installed at the analog
output terminals.
6.5 CUSTOMIZED LINEARIZATION
Three types of signals can be user-customized to fit particular linearization profiles. This means that
the operator can configure the instrument to read non-standard crescent non-linear signals with high
accuracy.
7INSTALLATION
The indicator is designed to be panel mounted. Remove the two plastic fixing clamps from the
instrument, insert the unit into the panel cut-out and slide firmly the fixing clamps from the rear against
the panel.
7.1 RECOMMENDATIONS FOR INSTALLATION
•
Input signal wires should be laid out away from power lines and preferably inside grounded
conduits.
•
Instrument mains (line) supply should be suitable for this purpose and should not be shared.
•
In controlling and monitoring applications, possible consequences of any system failure must be
considered in advance. The internal alarm relay does not warrant total protection.
•
Use of RC filters (47 R and 100 n, serial) are highly recommended when driving solenoids,
contactor coils or other inductive loads.
7.2 ELECTRICAL CONNECTIONS
The internal electronics can be removed from the front panel without any cable disassembly. The
input signals and power connections are shown in Figure 2.
Figure 2 – Back Panel Terminals

7
7.2.1 Power Connection
Figure 3 – Power Connection
7.2.2 Input signal connection
It is important that they are very well connected, the sensor wires must be well fixed in the terminals of
the rear panel.
Figure 3 – voltage connection Figure 4 – current connection
7.2.3 Digital Input (Dig In)
The digital input is activated by connecting a switch (or equivalent) to its terminals, as shown in Figure
5 above.
Figure 5 – Digital Input
6.2.2 Analog output
The N1500LC can deliver either 0-20 mA or 4-20 mA analog output, depending on how the instrument
is configured. The output is available at terminals 29 and 30.
8OPERATION
For best results, this indicator requires correct basic setting of parameters or a definition for
parameters displayed. It is necessary to define, for example: Type of input, triggering point, alarm
function, etc.
These parameters are divided in five levels (or groups) of parameters which we will refer to as
CYCLES.
Cyc e Access
1- ork free access
2- Alarms
3- Functions
4- Configuration
5- Customized Linearization
6- Calibration
reserved access
Table 4 - Parameters Cycles
The work cycle has free access. All other cycles require a certain combination of key strokes to be
accessed. The combination is:
and keys pressed simu taneous y
Once within a cycle, just press
to move to the subsequent parameters of this cycle. At the end
of each cycle the display will go back to the work cycle.
After reaching the intended prompt just press the or keys to change this parameter
accordingly. All changes are recorded in non-volatile memory as we move to next prompt. After 25
seconds with no key pressed the indicator will return to the measuring cycle (work cycle).

8
8.1 CONFIGURATION PROTECTION
As a safety measure, changes can be prevented by a combination of keys for each cycle Parameters
can be seen but not changed.
To protect a cycle just press the
and
keys simultaneously for 3 seconds at the beginning
of the referred cycle
To unlock this cycle (and allow for changes) just press the
and
keys for 3 seconds.
Disp ays wi f ash brief y to confirm ocking or un ocking operation.
ithin the controller, the PROT key completes the locking function. hen PROT is OFF the user is
allowed to lock and unlock the cycles. hen PROT is ON changes are not allowed. if cycles are
protected, protection cannot be removed, if there aren’t cycles protection, they cannot be made.
9PROGRAMMING THE INDICATOR
9.1 WORK CYCLE
This is the first cycle. At power up the indicator will display the Process Variable (PV). The alarm
triggering points are also displayed at this cycle (alarm Setpoints). To advance in this cycle simply
press .
TELA PROMPT PARAMETER DESCRIPTION
8.8.8.8.8.
Measure prompt - Shows the variable measured according to the limits
defined in the “in.LoL
in.LoLin.LoL
in.LoL” and “in.kiL
in.kiLin.kiL
in.kiL” prompts.
If the Hold function is programmed, the display shows the frozen variable
measure alternating it with the “koLd
koLdkoLd
koLd” message.
If the Peak Hold function is programmed, the display shows maximum
variable measured alternating it with the “P.koLd” message.
Should any failure occur, the indicator will display an error message, which is
described in item 11 of this manual.
Al.ref
Differentia A arm Reference Va ue - This prompt is shown only when there
is an alarm programmed with differential function. This value is used as a
reference for differential alarms triggering.
Sp.al1
Sp.al2
Sp.al3
Sp.al4
SP of A arms 1, 2, 3 and 4 – Value that defines the alarms triggering points
programmed with “Lo
LoLo
Lo” or “ki
kiki
ki” functions.
Note: For alarms programmed with differential functions, the alarm SP value
can not be changed, and the “diF” message is displayed. The value of
differential SP (deviation) is defined in the Alarms Cycle.
NOTE: The SP adjustment parameters are presented only if the corresponding
alarm function is configured.

9
9.2 ALARM CYCLE
fV.al1
fV.al2
fV.al3
fV.al4
A arm Function – Defines the alarm functions: 1, 2, 3 or 4, as defined in item
4.1.
oFF
oFFoFF
oFF : Alarm is inactive
iErr
iErriErr
iErr : Broken or shorted sensor.
Lo
LoLo
Lo : Minimum value
Ki
KiKi
Ki : Maximum value
DiFL
DiFLDiFL
DiFL : Minimum differential
DiFH
DiFHDiFH
DiFH : Maximum differential
DiF f
DiF fDiF f
DiF f : Differential out of range
DiF d
DiF dDiF d
DiF d : Differential within range
Ky.al1
Ky.al2
Ky.al3
ky.al4
A arm hysteresis
Defines the difference between the value at which the alarm is turned on and
the value at which it is turned off.
Bl.al1
Bl.al2
Bl.al3
bl.al4
Initia b ocking function
It makes possible to prevent alarms activation at the process start, when all
the system is powered. See item 4.3.
Al1t1
Al1t2
Al2t1
Al2t2
Al3t1
Al3t2
Al4t1
Al4t2
A arm Timer:
Prompts that define time T1 and T2, in seconds, shown in table 3. They allow
the user to delay the alarm triggering, to activate alarms momentarily or
sequentially.
To disable timer function, just set zero for T1 and T2.
9.3 FUNCTION CYCLE
f.fvnc
F Key function – Makes possible to define the F key function. Available
functions:
oFF
oFFoFF
oFF - Key not used;
kold
koldkold
kold - Hold PV
RESEt
RESEtRESEt
RESEt - Resets maximum and minimum values
PkoLd
PkoLdPkoLd
PkoLd - Peak Hold
XI
XI XI
XI - Displays maximum
L
LL
L - Displays minimum
ZER
ZER ZER
ZER - Automatic zero
These functions are described in item 5.2.
Dig.in
Digita input function – Makes possible to define the digital input function.
Functions available are the same as the ones available for the F key, except for
the Zero function, replaced by the Tare function.
oFF
oFF oFF
oFF - kold
kold kold
kold - rESEt
rESEt rESEt
rESEt - PkoLd
PkoLd PkoLd
PkoLd – XI
XI XI
XI -
--
- L
L L
L -
--
- tare
tare tare
tare
These functions are described in item 5.2.
filtr
Input digita fi ter - It is used to reduce instability of the measured value.
Adjustable between 0 and 60. 0 when the filter is off and 60 for the maximum
filtering. The higher the filter value, the lower is the measured value response.
ofset
Disp ayed offset – This is a value added to the measured value to shift PV
indication. The offset is shown in the programmed unit. For °F indications the
zero reference is at 32°F.
En A.z.
Enab es auto zero - Enables the auto-zero function of the indication. The
indication will turn to zero if the input value is within the programmed range in AZ
LEV for 3 seconds. Auto-zero occurs when the indication is relatively stable. It is
used to eliminate the influence of interference or small deviations in the zero of a
scale.
A.Z.rAn
Maximum eve for zero - Maximum level of the scale zero deviation, where
auto-zero is activated. This value can be programmed up to 2% of the end of
scale.

10
Bavd
Communication Baud-Rate – Transmission rate used in the serial
communication of the device (RS-485), in bps. Available rates are: 1200,
2400, 4800, 9600,19200, 38400 and 57600 bps.
Adres
Communication address – Number that identifies the indicator in a network.
9.4 CONFIGURATION CYCLE
In.typ
Input Type - Selects the input signal or sensor type to be connected to the PV
terminals. Refer to table 1 for options.
Changing the input type causes all other parameters related to PV and alarms
to be changed as well, therefore, this parameter shall be the first to be set.
Dp.pos
Decima Point Position - Defines the decimal point position in the displayed
value.
Scale
Sca e - Defines the indication range.
0
00
0 Configurable indication from – 31000 to + 31000.
1
11
1 Configurable indication from 0 to + 60000.
2
22
2 Configurable indication from 0 to +120000. Only even values will be
displayed (resolution is not improved).
The selected scale affects values of PV, alarm setpoints and Offset.
In.lol
Input Low Limit – Determines the minimum limit for input signals. hen the
PV retransmission is used, this value defines the point that will correspond to
the 4 mA (or 0 mA) for any type of programmed input.
In.kil
Input High Limit – Determines the maximum limit for input signals. hen the
PV retransmission is used, this value defines the point that will correspond to
the 20mA for any type of programmed input.
vt.ty
Ana og Output Type - Selects the analog output type to either 0-20 mA or 4-
20 mA.
u.lol
Low Limit for Ana og Retransmission – Defines the PV value that results in
a 4 mA (or 0 mA) analog output current.
u.kil
High Limit for Ana og Retransmission – Defines the PV value that results in
a 20 mA analog output current.
vt.er
4-20 mA Output behavior in case of fai ures – Defines the output as 4-20
mA when there is an error in the indication.
Do
DoDo
Do – Applies a value < 4 mA; UP
UPUP
UP – Applies a value > 20 mA
9.5 CUSTOMIZED LINEARIZATION CYCLE
Inp.01
Inp.30
Defines the extreme points (lower and upper) of the customized linearization.
Values must be in the input signal unit.
vt.01
vt.30
Defines the proportional indications in respect to each segment of the
customized linearization. Values are in the intended indication unit (within the
Indication Lower and Upper Limits).
Figure 10 shows the sequence of cycles and parameters presented in the indicator display. There are
parameters that must be defined for each alarm available
Work Cyc e
A arm cyc e
Function
Cyc e
Configuration
Cyc e
Customized
inearization cyc e
Ca ibration
cyc e
Automatic
ca ibration cyc e
8.8.8.8.8. * Fv.al1 f.fvnc In.typ Inp.01 - inp.30 In.lo( a(all
Al.ref * Ky.al1 Dig.in Dp.pos Vt.01 - ovt.30 In.ki( a(alk
* Sp.al1 * Bl.al1 Filtr S(ale v.lo(
* Al.1t1 fset In.lol v.ki(
* Al.1t2 En AZ In.kil k.type
AZ ran VT.TY
Bavd 0v.lol
Adres 0v.kil
VT.er
Table 5

11
9.6 CALIBRATION CYCLE
A input and output types are factory ca ibrated. This cyc e shou d on y be accessed by
experienced personne . If this cyc e is accidenta y accessed do not touch the or
keys, just press the
key a few times to go back to the Work Cyc e.
In.lo(
Input Low Ca ibration - Sets the Process Variable low calibration (offset).
Several key strokes at or
might be necessary to increment one
digit.
In.ki(
Input Hi Ca ibration - Sets the Process Variable span calibration (gain).
v.lo(
Ana og Output Low Ca ibration - Sets the analog current output low
calibration (offset).
v.Ki(
Ana og Output Span Ca ibration - Sets the analog current output high
calibration (span) of the analog output (20 mA).
k.type
Hardware Type - This parameter adapts the firmware to the actual indicator
hardware (optional features) and should not be changed by the user.
2 Alarms ...................................................3
2 Alarms and 4-20 mA...........................19
2 Alarms and RS485 .............................35
2 Alarms, 4-20 mA and RS485 .............51
4 Alarms .................................................15
4 Alarmes and 4-20 mA.........................31
4 Alarmes and RS485 ...........................47
4 Alarmes, 4-20 mA and RS485........... 63
9.7 AUTOMATIC CALIBRATION CYCLE
This is an alternative calibration method where the user teaches the indicator the desired indication
values for two extreme input signals. First a low signal is applied to the indicator input (for example, 0
kg) and the desired value (0) is entered in A(ALL parameter. Then a high signal is applied to the
input (close to the upper measurement limit, for example 40000 kg) and the desired indication value
(40000) is entered in A(ALk parameter. After this 2 calibration steps, the internal calibration
parameters are automatically calculated to achieve the desired indication range.
A(all
Automatic ca ibration of input ow va ue – Low calibration value. Must only
be entered during a calibration procedure while applying a known input signal
to the indicator.
A(alk
Automatic ca ibration of input high va ue – High calibration value. Must
only be entered during a calibration procedure while applying a known input
signal to the indicator.
and 30 seconds.

12
10 SERIAL COMMUNICATION
The indicator can be supplied with an asynchronous RS-485 digital communication interface for
master-slave connection to a host computer (master).
The indicator works as a slave only and all commands are started by the computer which sends a
request to the slave address. The addressed unit processes the command and sends back the
answer.
Broadcast commands (addressed to all indicator units in a multidrop network) are accepted but no
response is generated.
CHARACTERISTICS
-RS-485 compatibility with two-wire bus from the host to up to 31 slaves in a multidrop network
topology.
-Up to 247 units can be addressed by the MODBUS RTU protocol.
-Maximum network distance: 1200 m.
-Time of indicator disconnection: Maximum of 2 ms after the delivery of the last byte.
-Communication signals electrically isolated from the rest of the instrument.
-Baud rate: 1200, 2400, 4800, 9600, 19200, 38400 or 57600 bps.
-Number of data bits: 8, without parity or even parity
-Number of stop bits: 1
-Time to start response transmission: 100 ms maximum delay after acknowledging the command.
-Protocol: MODBUS (RTU)
Dois parâmetros devem ser configurados para utilização da interface de comunicação serial: o Baud-
Rate de Comunicação (parâmetro bavd
bavdbavd
bavd) e o Endereço de Comunicação (parâmetro adres
adresadres
adres).
10.1 RS485 INTERFACE: ELECTRICAL CONNECTION
The RS-485 signals are: D1 = D: Bidirectional data line
D0 =
D:
Inverted bidirectional data line
C = GND: Optional connection. Improves communication performance for
long cable runs.

13
11 PROBLEMS WITH THE INDICATOR
Connection errors or improper configuration will result in malfunctioning of the indicator. Carefully
revise all cable connections and programming parameters before operating the unit.
Some error messages will help the user identify possible problems.
Message Possib e Prob em
VVVVV
Measured value is above the value allowed for the selected sensor or above
the configured input signal limit.
nnnnn
Measured value is below the value allowed for the selected sensor or below
the configured input signal limit.
-----
Open input. No sensor is connected or the sensor is broken.
Err 1
Pt100 cable resistance is too high or the sensor is badly connected.
Different messages other than the ones above should be reported to the manufacturer. Please inform
the serial number if this should occur. The serial number can be viewed at the display by pressing the
key for about 3 seconds.
The software version of the instrument can be viewed at the time the unit is powered.
hen not properly configured, the instrument may show false error messages, particularly those
related to the type of input selected.
9.1 SPECIAL RECOMMENDATIONS
Should the indicator be repaired, some special handling care should be taken. The device must be
withdrawn from the case and immediately placed in an anti-static wrap; protected from heat and
humidity.
12 SPECIFICATIONS
DIMENSIONS: .............................48 x 96 x 92 mm (1/16 DIN). Approximate weight: 250 g
PANEL CUT-OUT:..................................................................... 45 x 93 mm (+0.5 -0.0 mm)
TERMINAL CONNECTION:.................................... 18 screws accepting 6.3 mm fork lugs.
POWER:....................................................................... 100 to 240 Vac/dc ±10 %, 50/60 Hz
Optional:............................................................................................ 24 Vdc/ac ±10 %
Max. Consumption:........................................................................................... 7.5 VA
ENVIRONMENTAL CONDITIONS:
Operating temperature:................................................................................ 5 to 50 ºC
Maximum RH:..............................................................................................80 % up to 30 ºC
......................................................For temperatures above 30 ºC, decrease 3 % per ºC
..............for indoor use; Installation category II, pollution degree 2; altitude < 2000 m
INPUT...................................................... Keyboard selection of input type (refer to table 1)
Interna reso ution:................................................................................128000 levels
Disp ay reso ution:.............................................................................................62000
Input samp e rate: ................................................................................ 15 per second
Accuracy: ........................................................................................... 0.15 % of span.
Input impedance: .................................................................................... mV >10 MΩ
........................................................................................................................mA: 15 Ω
ANALOG OUTPUT:..................... 0-20 mA or 4-20 mA, 550 Ω max.; 4000 levels, Isolated
RELAY OUTPUT: ................... ALM1 and ALM2: SPDT: 3 A / 240 Vac (3 A / 30 Vdc Res.)
........................................ALM3 and ALM4: SPST-NO: 1.5 A / 250 Vac (3 A / 30 Vdc Res.)
EMC:................................................................ EN 61326-1:1997 and EN 61326-1/A1:1998
SAFETY: ........................................................... EN61010-1:1993 and EN61010-1/A2:1995
START UP 3 SECONDS AFTER POWER UP;

14
12.1 ORDERING INFORMATION:
N1500LC - 4R - RT - 485 - 24V
A B C D E
A: Series model: N1500LC
B: Relays outputs: b ank (2 relays); 4R (4 relays)
C: Analog output: RT – (Retransmission of the input signal) or B ank
D: Digital Communication: 485 – (RS485, ModBus protocol) or B ack
E: Voltage rating: b ank (100-240 Vac/dc); 24 V (24 Vdc/ac)
13 WARRANTY
This product is covered by a 12-month warranty provided the purchaser presents the sales receipt
and the following conditions are met:
♦
Products are covered for one year from the original date of purchase. Please retain the dated
sales receipt as evidence of the date of purchase. You will need it for any warranty service
♦
ithin this period, warranty against defects in material and workmanship under normal use is
free of charge.
♦
For repair, send the product and the sales receipt to our address. Expenses and transportation
risks are under the purchaser’s responsibility.
♦
This warranty does not cover any damage due to accident, misuse, abuse, or negligence.
V 2.3 a
Table of contents
Popular Measuring Instrument manuals by other brands
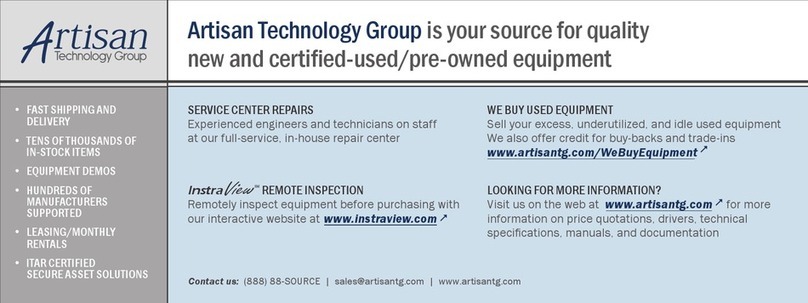
Brooks Instrument
Brooks Instrument Ar-Mite MT 3750 Installation and operation manual
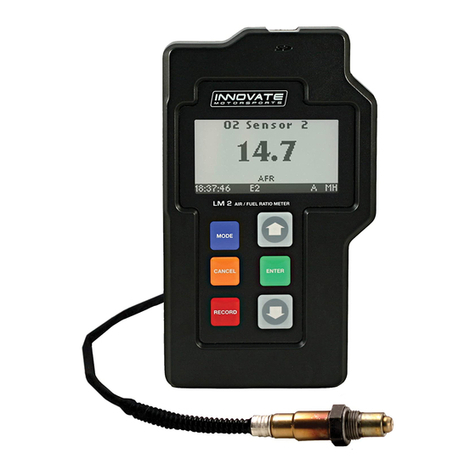
Innovate
Innovate LM-2 user manual

Omega Engineering
Omega Engineering DPG280 Series user guide

Horiba Scientific
Horiba Scientific LAQUAtwin Series instruction manual

Blaze
Blaze ALT-7 operating manual
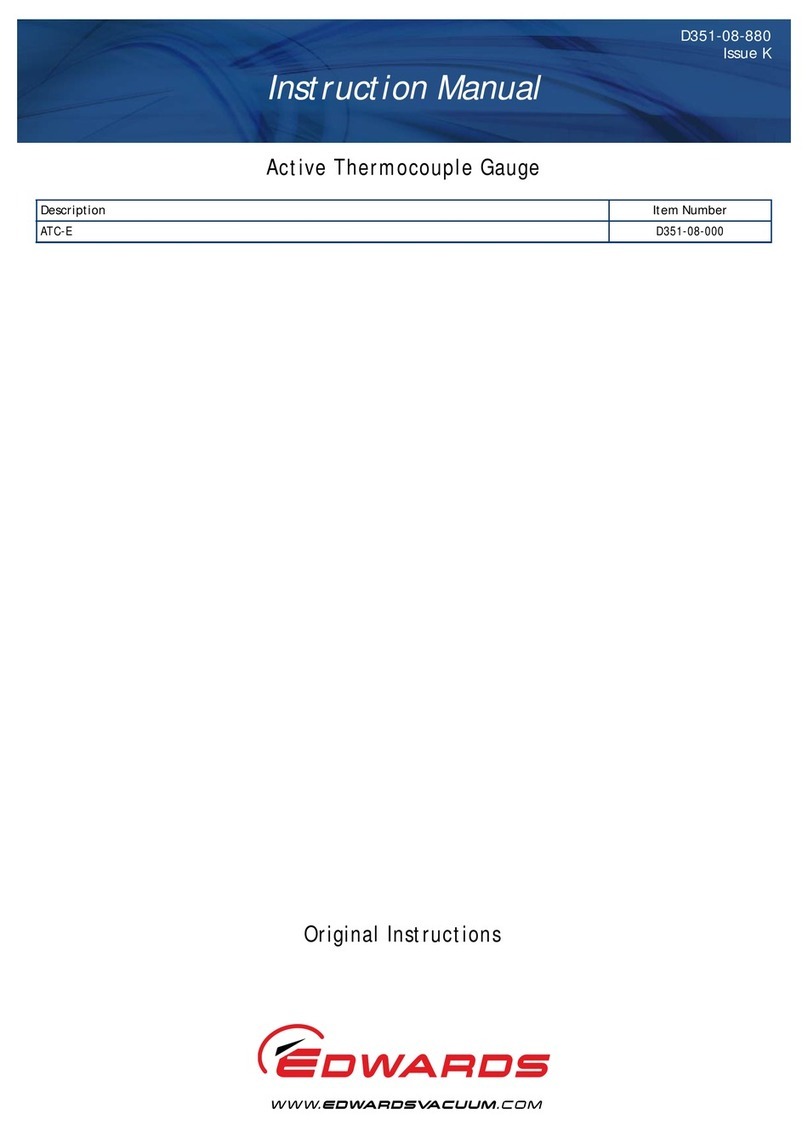
Edwards
Edwards ATC-E Original instructions