QRP Labs QCX 50W Amp User manual

QCX 50W Amp
50W HF QCX Power Amplifier kit assembly manual
A low-cost, 50W Power Amplifier for the QCX with Full-
break-in (Q K) solid state Tx/Rx switching
PCB Rev
Designed and produced by QRP Labs, 019
1

Contents
!"
!#$$%&&$'%(#$%$&"
)&&$'%(
)*+
)!*,-.*/-0*12
))/-/-/1202*/31**)
)"/-/-/%145*/-2,1*%+)
)/-/-/%145*/-2,1*%"/-%6"
)+/-/-/7**/31**!"
)6/-/-/*7**/31**6
)8/%145*,0,1*"/-89
)9/%145*,0,1*/-!!
)/%145*,0,1*9/-!!
)/%145*,0,1*9/-!!!
)!/,0,1*:!:):+:6:)/-+!!
))/,0,1*"/-!)
)"/,0,1*8/-!)
)/-1-!:":+:8:9/-!"
)+/-1-:):/-6!"
)6//-2,1*%:!:)::8:9/-!
)8/*1*6:::"/-6!
)9/*1*!+
)!/*1*+!+
)!/*1*8!6
)!!/*/1*)!6
)!)/*/1*"!8
)!"/*/1*/-+!8
)!/!9
)!+/*1*:+/-9!9
)!6/*1*!/-))
)!8/*1*))
)!9/*1*!/-")
))/***1*)
))/,0,1*/-6)!
))!/,1//,1*";14*/)!
)))/,1//,1*!;<=))
))"/,1//,1*/-);5//-2))
))/%$/-!)"
2

"$%&$;*/1*/>1/)
$%&$/>1/)6
+$%"!
+&,?>,"!
+!/02@/21*""
+)14*07*""
+"?*,1/-*>1/
+%145*!
++*/A, 4,?/.)
607*B20/-10*>1/+"
6*,2>1/+"
6!14*200+
6)1//,>1/1+
6"-C2/++
6&200 1. 2/-014*1202++
8'2*/+6
814*1202 &200 1.+6
8!%145*,?*,*>,+8
8)D/./ 10+8
9E*1/F1* +9
3

1. INTRODUCTION – PCB Rev
This 50W QCX Power Amplifier has the following features:
Up to 50W power output with 20V supply, falling to around 25W at 13.8V supply
tandard 50-ohm input and output
Fast clean solid-state Tx/Rx switching provides full break-in operation (Q K)
Can be built for one of 80, 40, 30m or 20m bands with the supplied components (or other
bands with suitable choice of Low Pass Filter components)
Uses two low-cost IRF510 transistors as the power amplifier in push-pull configuration
Recommended amplifier operation in Class C
On-board 7-element Low Pass Filter for harmonic attenuation
Two black anodized heatsinks sized 130 x 28mm with 25mm fins typically limit the
temperature rise to < 20C over ambient in normal CW operation
Through-hole plated PCB, all through-hole components (no urface Mount Devices)
All connectors board-mounted: two BNC, one 2.1mm barrel power connector, one 3.5mm
jack connector for keying
PCB size 130mm x 59.5mm (2.744 x 1.338 inches)
tandard inexpensive components throughout (easy to replace)
Optional black anodized aluminium enclosure
We hope you enjoy building and operating this kit! Please read this assembly manual carefully,
and follow the instructions step by step in the recommended order.
Note that this amplifier is NOT designed for Linear operation; linear operation would
require a higher bias current setting on the PA transistors and would result in higher heat
dissipation; it may be worthwhile experimenting with this but you will be in experimental
territory.
This amplifier is intended for single-band operation and may be built for 80, 40, 30 or 20m using
the supplied components. The band-specifying section of the circuit is the Low Pass Filter (LPF).
You may build it for other bands by suitable choice of low pass filter components; the LPF
component values should be the same as in the QCX kit http://qrp-labs.com/qcx, or the QRP Labs
LPF kit http://qrp-labs.com/lpfkit. T50 sized toroids must be used, and NP0/C0G type capacitors
with at least 100V rating, sufficient to handle the 50W output power.
A suitable power supply is required, for full power 50W operation it will need to be capable of
providing at 20V at a current of around 5A.
. GENERAL ASSEMBLY GUIDELINES
Assembly of this kit is quite straightforward. But there are quite a lot of components. o please
keep them methodically in trays or some convenient storage boxes. Be careful not to misplace
any. The usual kit-building recommendations apply: work in a well-lit area, with peace and quiet to
concentrate. Some of the semiconductors in the kit are sensitive to static discharge.
Therefore, observe Electrostatic discharge (ESD) precautions.
And FOLLOW THE INSTRUCTIONS!! Don’t try to be a hero and do it
without instructions!
A jeweler's loupe is really useful for inspecting small components and
soldered joints. You’ll need a fine-tipped soldering iron too. It is good
to get into the habit of inspecting every joint with the magnifying glass
or jeweler's loupe (like this one I use), right after soldering. This way
4

you can easily identify any dry joints or solder bridges before they become a problem later on
when you are trying to test the project.
Triple check every component value and location BEFORE soldering the component! It is
easy to put component leads into the wrong holes, so check, check and check again! It is difficult
to de-solder and replace components, so it is much better to get them correctly installed the first
time. In the event of a mistake, it is always best to detect and correct any errors as early as
possible (immediately after soldering the incorrect component). Again, a reminder: removing a
component and re-installing it later is often very difficult!
Please refer to the layout diagrams and PCB tracks diagrams and follow the steps carefully.
The component colour coding of the layout diagram at every step of the assembly instructions is
as follows (kind of: components past, present and future):
Components shaded grey have already been installed
Components shaded red are the ones being installed in the current assembly step
Components shaded white are the ones which have not yet been installed
VERY IMPORTANT SOLDERING ADVICE: when soldering a component pin that goes to ground,
you need to allow extra time with the soldering iron. Ground pads are separated from the ground-
plane by what are called “thermals”, a gap between the pad and the ground-plane which is bridged
in 4 places at 0, 90, 180 and 270-degree around the circle. This is standard practice. However,
you may TILL find that it is harder to solder ground connections, because the soldering iron heat
is dissipated away more quickly. If a component ground connection is broken it can sometimes
have catastrophic consequences. o please check and recheck, particularly with ground
connections.
The following tools are required: good soldering iron, preferably 50-60W; wire-cutters; screw-
drivers; electrical insulation tape; Digital Volt Meter (DVM) or similar for continuity testing; marker
pen.
3. ASSEMBLY
Deburr the ferrite rings and tubes by gently but firmly scraping them with a pair of wire-cutters or
similar as shown. This should smooth any sharp edges and reduce the risk of cutting the insulation
of the enameled wire.
Refer to the parts list and accompanying photographs, carefully inventory the components and
familiarize yourself with the kit contents.
5

3.1 Parts list
This parts list shows the through-hole components to be inventoried and installed in the assembly.
Resistors
R1, 6, 9 1K 1W, brown-black-red-gold OR
brown-black-black-brown-brown (3pcs)
R2, 4 330-ohm, 2W, orange-orange-brown-gold OR
orange-orange-black-black-brown (2pcs)
R3 22-ohm, 2W, red-red-black-gold OR red-red-black-gold-brown
R5 4.7K trimmer potentiometer
R7, 10, 11, 14, 17 10K, ¼W, brown-black-black-red-brown (5pcs)
R8 470K, ¼W, yellow-purple-yellow-gold OR
yellow-purple-black-orange-brown
R12, 13 470-ohm, 2W, yellow-purple-brown-gold OR
yellow-purple-black-black-brown (2pcs)
R15 1.5K, ¼W, brown-green-red-gold or
brown-green-black-brown-brown
R16 470-ohm, ¼W, yellow-purple-black-black-brown
Capacitors
C1, 2, 3, 6, 7, 13, 16 1uF, 50V, code “105” (7pcs)
C4, 5 22nF, 50V, code “223” (2pcs)
C8, 10 47pF, 250V, code “470” (2pcs)
C9, 11, 12, 14, 18, 19, 20, 21 Band-dependent capacitors, see text
C15, 17 0.33uF, 250V, code “334” (2pcs)
180pF, 250V, code “181” (2pcs) – not used in 40m kit
270pF, 250V, code “271” (2pcs) – not used in 20m kit
390pF, 250V, code “391” (2pcs) – not used in 40m kit
680pF, 250V, code “681” (2pcs) – not used in 20m kit
Semiconductors
D1, 3, 5, 7 1N4007 (4pcs)
D2, 4, 6, 8, 9, 10 1N4148 (6pcs)
D11 3mm green LED
D12 3mm red LED
Q1, 2 IRF510, TO220, MO FET (2pcs)
Q3 FQPF2N60C, TO220, MO FET
IRFU9024 IRF9530, MO FET
Q5, 6 B 170, TO92, MO FET (2pcs)
IC1 78L05, 5V voltage regulator
Inductors
L1, 2, 3, 5, 8, 9, 10 47uH molded inductor, yellow-purple-black-silver (7pcs)
L4, 6, 7 T50-6 toroid, yellow, (3pcs)
T1, 2 Ferrite toroid, black (2pcs)
T3 Made from 2pcs ferrite tube (black)
Miscellaneous
PCB 130 x 59.5mm PCB, double-sided through-hole-plated FR4
1mm diameter wire Enameled wire (40cm)
6

0.6mm diameter wire Enameled wire (320cm)
X1, 3 BNC Connector (2pcs)
X2 3.5mm stereo jack socket
X4 2.1mm DC barrel power connector
Pad TO220 insulating silicone pad (2pcs)
Insulating washer 2pcs white plastic insulating washer
9mm M3 screw Pan-head screw (2pcs)
6mm M3 screw Pan-head screw (4pcs)
Heatsink 130mm x 28mm x 25mm deep (2pcs)
Enclosure kit (OPTIONAL)
Enclosure 63w x 25h x 130d mm enclosure, drilled, cut and engraved
crew Enclosure front and rear panel mounting screws (8pcs)
Feet elf-adhesive rubber cabinet feet (4pcs)
The main 50W Amplifier kit bag contains the PCB, two smaller bags of components, and one small
plastic box. The plastic box contains the powdered iron toroidal and ferrite cores, in order to
prevent breakage during shipping.
7

8

9

3. Trace diagram and parts layout
Red = Top side; Blue = bottom side; Green = pads.
There are only two layers (nothing is hidden in the middle). Not shown in these diagrams are the
extensive ground-planes, on both sides of the board. Practically everything on both layers that isn’t
a RED or BLUE track, is ground-plane! The two ground-planes are connected at frequent intervals
(not more than 0.1-inches) by vias.
3.3 Wind and install output transformer T3
We start with the installation of the transformers and inductors, which are generally the most
difficult components; doing these first means we have space around them so it is easier to access
the wires etc.
First is the output transformer, T3. The windings are made from the thick, 1mm diameter
enameled copper wire. They are wound on the two ferrite tubes, which are placed side-by-side to
make a large binocular core.
10

I recommend taping the two tubes together using electrical tape; it just helps keep everything
nicely held together while winding the turns. An alternative would be to epoxy glue the two tubes
together (photo, right).
The turns ratio of the transformer (and the actual
number of turns) is 2:3. Note that “1 turn” means the
wire passes through the central hole of BOTH
tubes.
It is essential to have some way of identifying the
windings. If you install the kit with the transformer in
backwards, the power output will be much lower
than expected. Unfortunately it is very easy to mix
up the transformer, and it is very difficult to tell
which is the 2-turn winding and which is the 3-turn
winding, after the windings have been completed.
For this reason it is strongly recommended to mark the two sides of the
transformer in some way. In the photo (right), this has been done this
simply with a ball-point pen. Write 3 on the left side (the secondary
winding, having 3 turns) and 2 on the right side (the primary winding,
having 2 turns). If you write on the middle part of the tape then it is less
likely that the ink will be worn off during handling of the transformer
during the installation on the PCB.
Wind the 2-turn primary first (below left). The turns start and end on the RIGHT side of the core, as
shown. Take care not to scrape the enamel off the wire!
Wind the 3-turn secondary (below right). The turns start and end on the LEFT side of the core, as
shown. Take care not to scrape the enamel off the wire!
The enamel on the wire is a type which burns off easily with heat from the soldering iron.
Nevertheless the wire is 1mm thick and will quickly conduct heat away; the result is that it can be
difficult to heat up the wire to a sufficient temperature that the enamel insulation burns off.
The solution to this is to gently scrape the ends of the wires, such that the enamel is removed.
Then the wire can be easily tinned with solder. Hold the wire end in a large blob of solder for about
10 seconds to ensure remaining enamel is burned away. Ensure not much solder is left on the
wire after tinning, otherwise it will be hard to fit the wire into the holes on the PCB.
11

Cut the wires so that the binocular core body stands elevated 5mm from the workbench (below
left). Then scrape the enamel from 5mm of the wire ends, and tin (below right).
Install the transformer in the PCB as shown in red (below). Be VERY sure that the 2-turn primary
winding wire ends are on the right side, nearest to the transistors Q1 and Q2; whereas the 3-turn
secondary winding wire ends must be on the left, near inductor L4.
Now use a DVM, set to resistance mode (or continuity beeper if it has that facility) and hold the
black and red probes on the holes shown in the diagram below labeled “DVM” in blue. You should
measure continuity (zero resistance). If not, check that the wires are properly tinned and soldered.
12

3.4 Wind and install Low Pass Filter inductor L6
Measure and cut 34cm of the 0.6mm wire for winding inductor L6 which is wound on a T50-6
toroid (yellow). The number of turns and inductance of L6 is given in the table below:
Band Turns Inductance
80m 27 3.01uH
40m 20 1.70uH
30m 17 1.26uH
20m 14 0.904uH
tart the winding as shown (1). Remember that each time the wire passes through the hole of the
toroid counts as “1 turn”. Wind the wire as tightly as possible on the core. Wind the turns bunched
up next to each other (2). When the number of turns is correct, spread them out evenly around the
whole core (3). This method slightly tightens up the windings a bit more, as they are spread out.
Position the wires perpendicular to
the toroid and cut the wires at a
length of 5mm (4).
crape the last 5mm of the wires
using a knife or wire cutter and tin
them (5). Install and solder (below).
13

3.5 Wind and install Low Pass Filter inductors L4 and L7
Measure and cut two 30cm lengths of the 0.6mm wire for winding inductors L4 and L7. These two
inductors are wound on T50-6 toroids (yellow). The number of turns and inductance of L4 and L7
are given in the table below:
Band Turns Inductance
80m 24 2.42uH
40m 17 1.38uH
30m 15 1.09uH
20m 13 0.773uH
Wind and prepare the inductors as in the previous section.
Install L4 and L7 as shown below.
Now use a DVM in resistance or continuity-beeper mode (if available) to check for DC continuity.
Resistance should read zero if the DVM is in resistance mode. Poke the red and black probes in
the pads of C14 for this measurement. If you do NOT see DC continuity then it means that one or
more of the inductor wire ends is not properly stripped of enamel and trimmed; this is a common
error.
3.6 Wind and install bifilar transformer T
Measure the remaining length of 0.6mm wire and cut it into five equal lengths. For example, if the
remaining length is 230cm then cut it carefully into five equal lengths of 46cm each.
Two of these wires now need to be prepared as bifilar windings. To do this, hold two ends and
twist the wire repeatedly along its entire length. Try to avoid the situation where one wire remains
straight, and the other wire just wraps around it. Try to keep the twists even. It is difficult to do this
and end up with a beautiful result. Don’t worry! Regardless of how imperfect or messy it looks, it is
going to work just fine.
14

The bifilar wire should end up looking something like this (top scale in inches, bottom scale in cm):
Wind 10 turns around one of the ferrite toroids (remember,
each time the wire passes through the center counts as one
turn). Leave 4-5cm of wire at each end.
Try to wind the wire tightly on the toroid but be careful not to
scratch the enamel which could cause short circuits between
the wires.
In the end it should end up looking something like this (right).
Now comes the tricky business of determining which wire goes
in which hole on the PCB. It has to be done CORRECTLY or
the kit will not work. Step by step, slowly and carefully, will ensure success.
crape and tin the wire ends, just for the purposes of identification of windings using a DVM. Use
the DVM to identify continuity between a pair of wires. This is one of the windings. Use a felt-tip
pen to mark these two wires that have continuity between them. Check again, to make sure you
haven’t mixed up the wires!
Orientate the wires so that the wires with the black mark are at diagonals. These three photos all
show the same thing from different angles and hopefully make it clear.
15

The diagram and explanation below
illustrates the correct wire placement.
It is CRITICALLY IMPORTANT to get
this right!
Now lay the toroid down flat on the
table as shown and identify the wires
which come from the center of the
core, over the top of the outside of the
core; and those which come out from
the underside of the toroid (see right).
All four wires go into holes that are on
the circumference of the outer circle of
the white silk-screen printing on the
PCB.
One black wire, that comes over the
outside of the top of toroid, must be inserted in the hole nearest the “Q2” text on the PCB (the top
left hole). The non-black wire that comes over the top of the outside of the toroid, which is twisted
together with this black wire, must be inserted in the hole nearest C6 (the top right hole).
One non-black wire coming from the underside of the toroid goes in the hole near the “Q1” text.
The corresponding black-marked wire goes in the hole near C7.
In this way, the lower pair of wires (Q1, C7) are from the twisted pair that comes from UNDER the
toroid; the top pair of wires (Q2, C6) are from the twisted pair that comes from the TOP side of the
toroid.
Pull the wires through the holes so that the toroid sits flat on the PCB, and is orientated accurately
with the white ink circle drawn on the PCB silkscreen. The toroid won’t sit perfectly flat of course,
because of the twisted bifilar windings. This is not a problem.
queeze the toroid gently to the PCB in the correct position, and cut the black-marked wire
nearest Q2, leaving a few spare mm. Now scrape some enamel from the last 5mm of this wire with
a knife or wire cutter; it does not have to be perfectly scraped but removing some enamel in this
way helps the remaining enamel to burn off easily. Tin it and solder it while it is in place in the hole
16

on the PCB. Hold the iron on the joint for at least 10 seconds and then feed in some more fresh
solder. This should ensure a good joint and all the enamel burned away.
Now similarly cut, prepare and solder the other “black marked” wire, which is the one in the hole
nearest to C7. Hold the toroid flat against the PCB in the correct position, while cutting the wire
with a few mm protruding; then scrape the wire and tin it and solder it to the pad, while in place;
hold the iron for 10+ seconds to ensure a good joint with all enamel burned away.
Use a DVM to measure continuity from the middle of the three pins of transistor Q2’s pads, and
the pad at right hand side of capacitor C7. The DVM in resistance mode should measure zero
ohms. If it does not, then you have either mixed up the wires or have a poor joint.
Now cut, prepare, and solder the wire in the bottom left hole, nearest to Q1. Check for continuity
with the DVM, from the middle pin of transistor Q1, to the right hand side of capacitor C7. You
should see continuity here.
Finally, cut, prepare and solder the wire at the top right hole, nearest to C6. Check for good DC
continuity with the DVM, from the middle pin of transistor Q1, to the right hand side of capacitor
C6.
3.7 Wind and install trifilar transformer T1
The three remaining wires are to be wound into trifilar transformer T1. They should be twisted
together in much the same way as the bifilar transformer T2 from the previous section. Again, it is
hard to twist three wires neatly and evenly. But again, it is not going to make much difference and
the amplifier will work regardless.
Now wind 10 turns carefully around the remaining ferrite toroid (remember one time through the
center, counts as 1 turn), again try to keep it compact but be careful not to pull hard, scraping the
wires against the toroid which could remove the enamel and cause short circuits later.
In the end you hopefully end up with
something looking like this (see right).
Identification of the wires is similar to the
earlier bifilar transformer T2. First scrape
the last 5mm of the wires, and tin them –
so that you can touch the DVM probes
there to determine continuity.
Find each pair for which continuity exists
and arrange the wires nicely so that the
windings are in order.
Label the wires again by drawing black
felt tip pen marks.
17

This photograph (right) illustrates the process.
Prefixes T (for Top) and B (for Bottom) are
used to indicate whether the wire comes out
from the top side or the bottom side of the
toroid when it is laying flat on the table.
Wires T-0 and B-0 have continuity.
Wires T-1 and B-1 have continuity and are
labeled with a single black marker stripe.
Wires T-2 and B-2 have continuity and are
labeled with two black marker stripes.
It is utterly critically important to insert these
wires into the correct PCB holes, as labeled in
the diagram below. There are two sets of 3-
holes. The top set of holes is to be connected
to the 3 twisted wires coming over the top of
the toroid. The bottom set of three holes is to be connected to the 3 twisted wires coming from
under the toroid core.
With all this in mind, we can start soldering.
Again, hold the T1 toroid flat against the PCB, orientated as precisely as possible over the white
circle drawn on the PCB silkscreen. Put the correct wires in the correct holes. Pull the wires
through reasonably tightly, still keeping the toroid in position flat on the PCB. Make sure the
labeled wires are in the correct holes, before soldering. It is hard to fix, later!
Now cut wire B-2 on the underside of the PCB, leaving a few mm spare. crape the insulation
from the last 5mm or so of the wire. Tin and solder it while it is in place in the hole. You will need
to hold the soldering iron to the joint for more than 10 seconds, firmly, and add more fresh solder
from time to time; the pad is grounded so the ground plane will dissipate heat and make achieving
a good joint more difficult.
imilarly cut wire T-2 with a few mm spare, scrape it, tin and solder it while it is in place in the
hole, holding the iron in position for 10 seconds to ensure all enamel is burned away and there is a
good joint. Now look for resistor R4 at the top of the PCB; hold the DVM probes to the pads of R4
18

and check for DC continuity (zero resistance). If you do not get zero resistance, then either you
have installed the wires in the wrong holes, or you have failed to burn off all the enamel and
achieve good joints to the wire. Fix it before proceeding!
Next repeat the cut/tin/solder procedure for wires T-1 and B-1. Check with a DVM for DC
continuity between the right-hand pin of transistor Q1’s three pads, and the wiper pin of trimmer
potentiometer R5. R5 has three pins and the “wiper” pin is the one just to the left of the + symbol
on the PCB silkscreen. Again – do not proceed until DC continuity (zero resistance) is seen here.
Finally repeat the same procedure for wires T-0 and B-0. Check for DC continuity between the left
pin of Q2’s three pads, and the same wiper pin of the trimmer potentiometer R5.
If all is well, this is the most difficult parts of the assembly over, the rest is relatively easy; you
should now have an assembly that looks like the photograph below. Note that in the photo the blue
low pass filter capacitors have been installed, which yours will not have yet (this was for
measurement purposes of the LPF characteristics).
3.8 Install Low Pass Filter capacitors C14 and C18
These two capacitors are 250V NP0/C0G types. The capacitor value depends on the band the
50W PA kit is being built for, as follows:
Band Value Code
80m 270pF “271”
40m 270pF “271”
30m 270pF “271”
20m 180pF “181”
19

3.9 Install Low Pass Filter capacitors C11 and C1
These two capacitors are 250V NP0/C0G types. The capacitor value depends on the band the
50W PA kit is being built for, as follows:
Band Value Code
80m 680pF “681”
40m 680pF “681”
30m 390pF “391”
20m 390pF “391”
20
Table of contents
Other QRP Labs Amplifier manuals
Popular Amplifier manuals by other brands
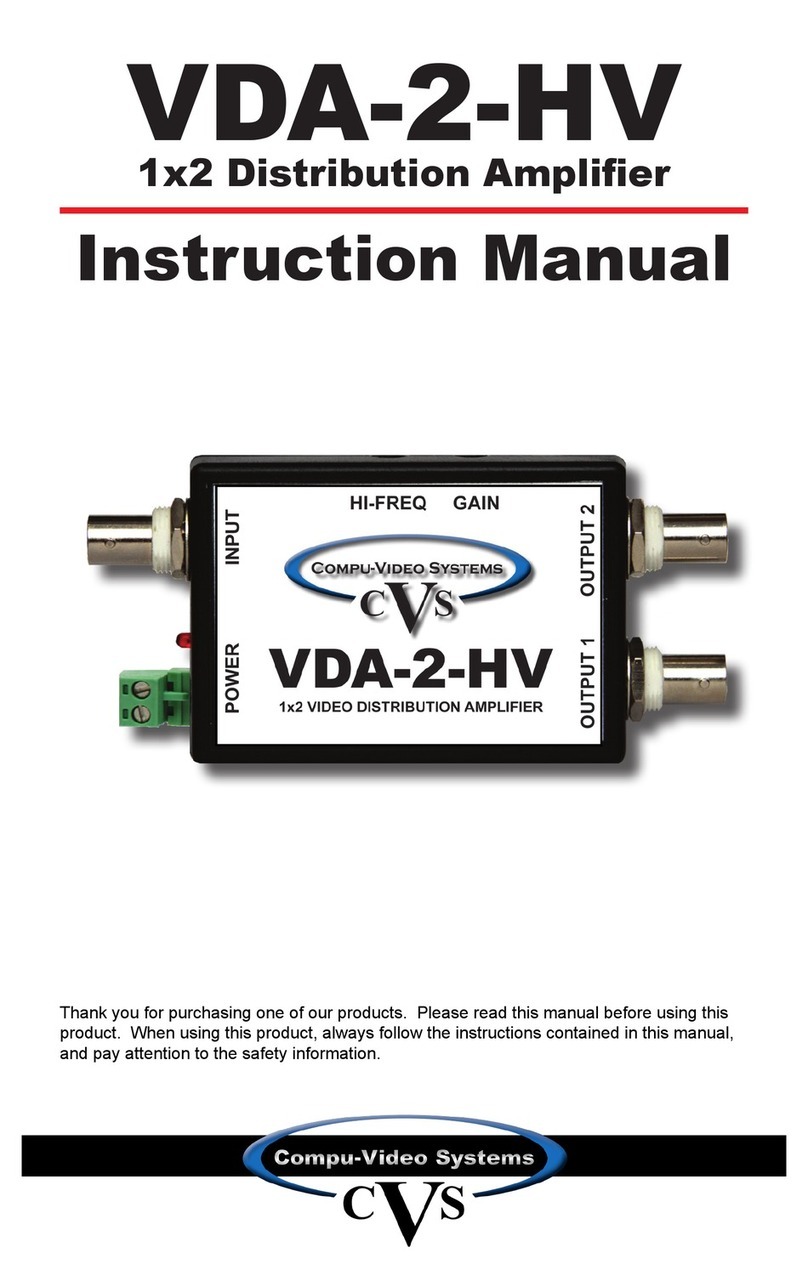
Compu-Video Systems
Compu-Video Systems VDA-2-HV instruction manual
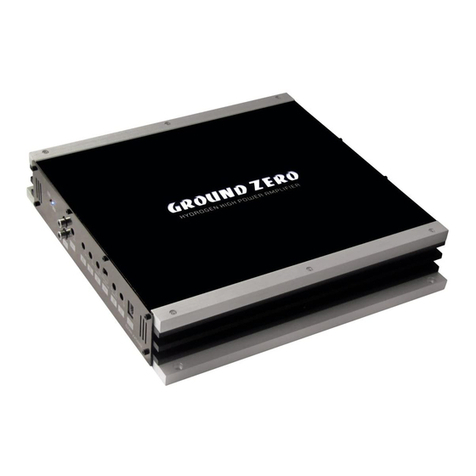
Ground Zero
Ground Zero HYDROGEN SERIES owner's manual

Cisco
Cisco Prisma II Installation and operation guide
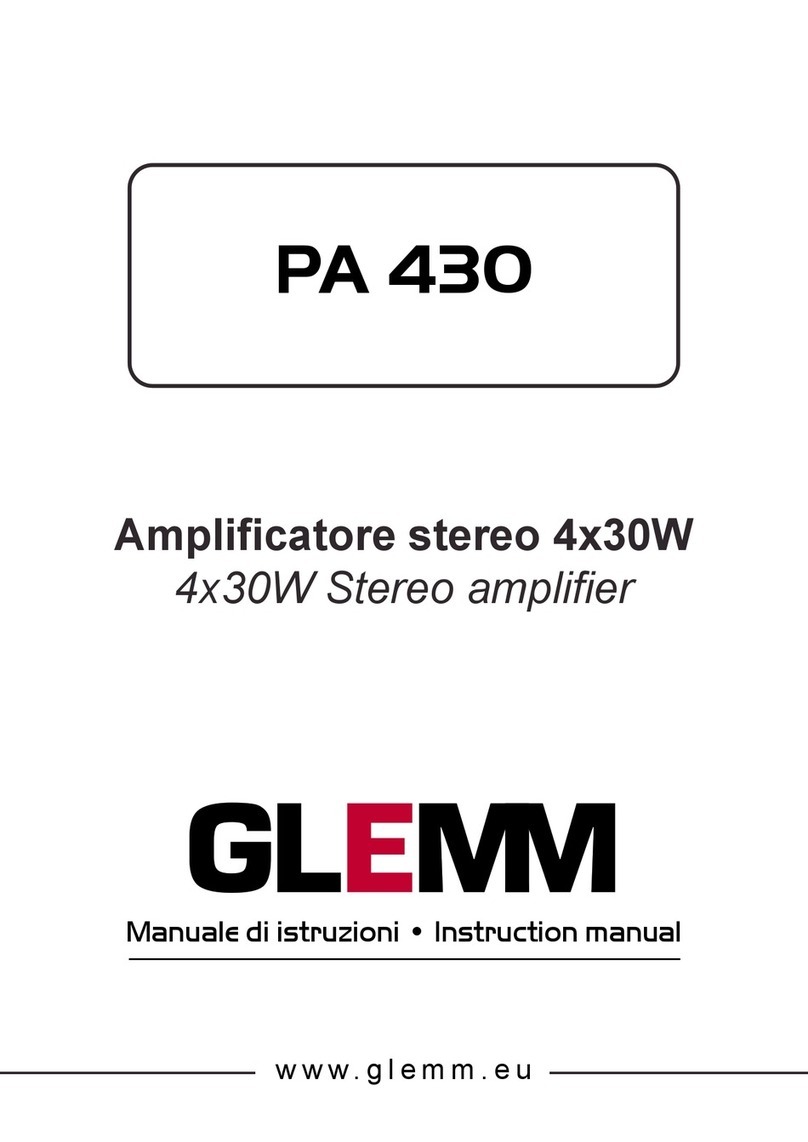
GLEMM
GLEMM PA 430 instruction manual
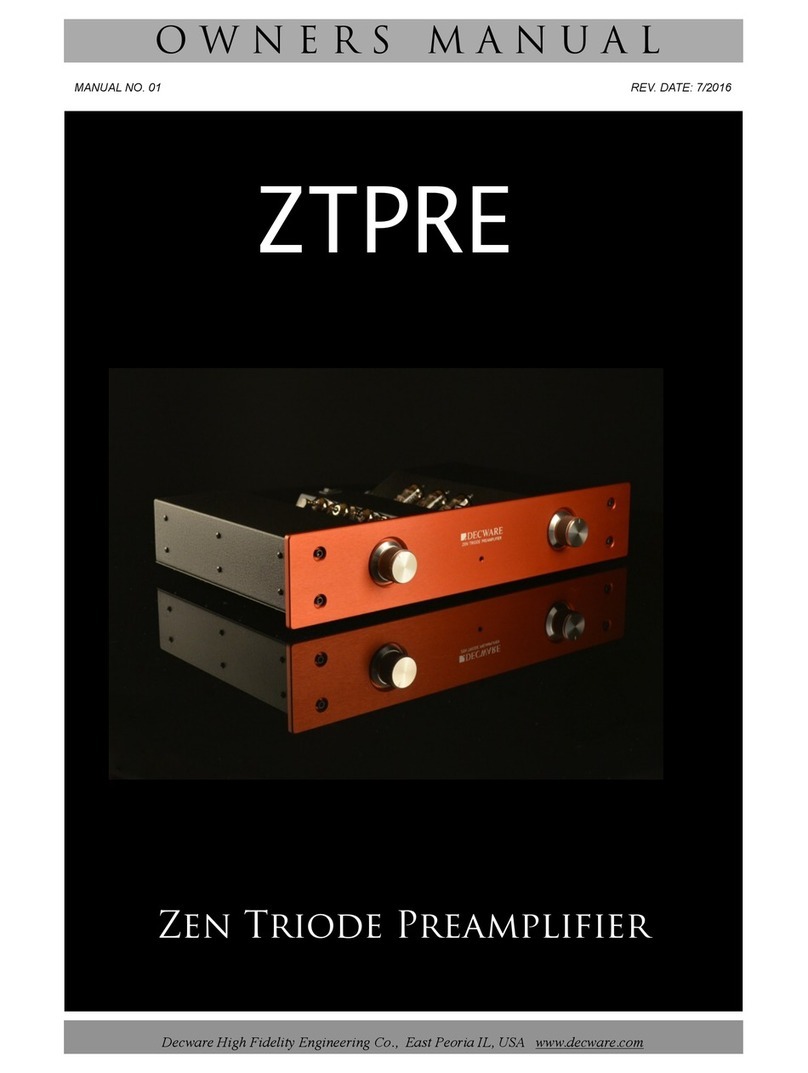
Decware
Decware Zen Triode Preamp owner's manual
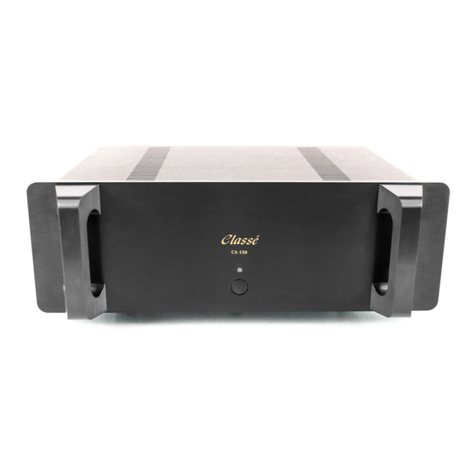
Classe Audio
Classe Audio CA-150 owner's manual