Quantech QCC2015CEE Installation and operating instructions

Products are produced at a
f a c i l i t y w h o s e q u a l i t y -
management systems are
ISO9001 certified.
R-410A
QCC2015CEE – QCC2070CEE
Air-Cooled Scroll Compressor Condensing Units
Style E (60 Hz)
15 ton to 80 ton
50 kW to 280 kW
Air-Cooled Scroll
Compressor Condensing Units
Installation, Operation, and
Maintenance Supersedes: QCC2-NM1 (1220) Form QCC2-NM1 (521)
Issue Date:
May 20, 2021
035-26916-000

QUANTECH
2
Form QCC2-NM1
Issue Date: 5/20/2021
This equipment is a relatively complicated apparatus.
During rigging, installation, operation, maintenance,
or service, individuals may be exposed to certain com-
ponents or conditions including, but not limited to:
heavy objects, refrigerants, materials under pressure,
rotating components, and both high and low voltage.
Each of these items has the potential, if misused or
handled improperly, to cause bodily injury or death. It
is the obligation and responsibility of rigging, instal-
lation, and operating/service personnel to identify and
recognize these inherent hazards, protect themselves,
and proceed safely in completing their tasks. Failure
to comply with any of these requirements could result
in serious damage to the equipment and the property in
Important!
Read before proceeding!
General safety guidelines
which it is situated, as well as severe personal injury or
death to themselves and people at the site.
This document is intended for use by owner-authorized
rigging, installation, and operating/service personnel. It
is expected that these individuals possess independent
training that will enable them to perform their assigned
tasks properly and safely. It is essential that, prior to
performing any task on this equipment, this individual
must have read and understood the on-product labels,
this document and any referenced materials. This in-
dividual must also be familiar with and comply with
all applicable industry and governmental standards and
regulations pertaining to the task in question.
Safety symbols
The following symbols are used in this document to alert the reader to specific situations:
Indicates a possible hazardous situation
which will result in death or serious injury
if proper care is not taken.
Indicates a potentially hazardous situa-
tion which will result in possible injuries
or damage to equipment if proper care is
not taken.
Identies a hazard which could lead to
damage to the machine, damage to other
equipment and/or environmental pollu-
tion if proper care is not taken or instruc-
tions and are not followed.
Highlights additional information useful
to the technician in completing the work
being performed properly.
External wiring, unless specied as an optional connection in the manufacturer’s product line, is
not to be connected inside the control cabinet. Devices such as relays, switches, transducers and
controls and any external wiring must not be installed inside the micro panel. All wiring must be in
accordance with Quantech published specications and must be performed only by a qualied electri-
cian. Quantech will NOT be responsible for damage/problems resulting from improper connections
to the controls or application of improper control signals. Failure to follow this warning will void
the manufacturer’s warranty and cause serious damage to property or personal injury.

QUANTECH 3
Form QCC2-NM1
Issue Date: 5/20/2021
AFFECTED PAGES DESCRIPTION
40 Physical data table units updatedl
Associated literature
MANUAL DESCRIPTION FORM NUMBER
Renewal Parts QCC2-RP1
Changeability of this document
In complying with Quantech policy for continuous
product improvement, the information contained in
this document is subject to change without notice.
Quantech makes no commitment to update or provide
current information automatically to the manual or
product owner. Updated manuals, if applicable, can be
obtained by contacting the nearest Quantech Service
office.
It is the responsibility of rigging, lifting, and operating/
service personnel to verify the applicability of these
documents to the equipment. If there is any question
regarding the applicability of these documents, rig-
ging, lifting, and operating/service personnel should
verify whether the equipment has been modified and
if current literature is available from the owner of the
equipment prior to performing any work on the chiller.
Revision notes

QUANTECH
4
Form QCC2-NM1
Issue Date: 5/20/2021
Nomenclature
Model
015C
020C
025C
030C
040C
045C
050C
060C
070C
QC C 2 015C E E 46 X E
Refrigerant
E = R-410a
High efficiency unit
Voltage code
-17 = 208-3-60
-28 = 230-3-60
-40 = 380-3-60
-46 = 460-3-60
-58 = 575-3-60
Scroll compressor
Unit
Quantech Air-Cooled
Scroll Condensing Units
Across-the-
line start
Design
level

QUANTECH 5
Form QCC2-NM1
Issue Date: 5/20/2021
Table of contents
SECTION 1 – GENERAL EQUIPMENT INFORMATION AND SAFETY ............................................................9
Introduction.......................................................................................................................................................9
Compressors ....................................................................................................................................................9
Condenser........................................................................................................................................................9
Refrigerant Circuit ............................................................................................................................................9
Warranty ...........................................................................................................................................................9
Safety and Quality ..........................................................................................................................................10
About this Manual...........................................................................................................................................10
Misuse of Equipment......................................................................................................................................10
SECTION 2 – PRODUCT DESCRIPTION...........................................................................................................13
Introduction.....................................................................................................................................................13
General System Description...........................................................................................................................13
Microcomputer Control Center .......................................................................................................................14
Building Automation System Interface............................................................................................................15
Communications.............................................................................................................................................15
Power Panel ...................................................................................................................................................15
Accessories and Options................................................................................................................................16
Discharge Pressure Transducers and Readout Capability.............................................................................16
Basic Unit .......................................................................................................................................................21
SECTION 3 – HANDLING AND STORAGE........................................................................................................27
Delivery and Storage......................................................................................................................................27
Inspection .......................................................................................................................................................27
Unit Rigging....................................................................................................................................................27
SECTION 4 – INSTALLATION .............................................................................................................................29
Installation Checklist.......................................................................................................................................29
Handling .........................................................................................................................................................29
Location And Clearances ...............................................................................................................................29
Spring Isolators (Optional)..............................................................................................................................30
Compressor Mounting ....................................................................................................................................30
Pipework Arrangement ...................................................................................................................................30
Ductwork Connection ....................................................................................................................................30
Recommendations Of The Building Services Research Association. ............................................................30
Wiring .............................................................................................................................................................30
High Pressure Cutout .....................................................................................................................................32
Compressor Heaters ......................................................................................................................................32
Refrigerant Piping...........................................................................................................................................32
Oil Traps .........................................................................................................................................................35
Refrigerant Charge.........................................................................................................................................35
Refrigerant Piping Reference .........................................................................................................................35
Filter Driers / Sight Glasses/ Txv’s .................................................................................................................35
SECTION 5 – TECHNICAL DATA........................................................................................................................39
SECTION 6 – COMMISSIONING .........................................................................................................................97
Preparation – Power Off.................................................................................................................................97
Preparation – Power On.................................................................................................................................98
Equipment Pre-Startup and Startup Checklist................................................................................................99

QUANTECH
6
Form QCC2-NM1
Issue Date: 5/20/2021
Table of contents (cont’d)
SECTION 7 – UNIT CONTROLS........................................................................................................................103
Introduction...................................................................................................................................................103
Microprocessor Board ..................................................................................................................................103
Unit Switch ...................................................................................................................................................104
Display..........................................................................................................................................................104
Keypad .........................................................................................................................................................104
Battery Back-Up ...........................................................................................................................................104
Transformer .................................................................................................................................................104
Single System Select and Programming # Of Compressors........................................................................104
SECTION 8 – UNIT OPERATION ......................................................................................................................133
Capacity Control...........................................................................................................................................133
Suction Pressure Limit Controls ...................................................................................................................133
Discharge Pressure Limit Controls...............................................................................................................133
Discharge Air Temperature Control ..............................................................................................................133
Suction Pressure Control .............................................................................................................................135
System Lead/Lag .........................................................................................................................................136
Compressor Lead/Lag..................................................................................................................................136
Anti-Recycle Timer .......................................................................................................................................136
Anti-Coincidence Timer ................................................................................................................................136
Evaporator Blower Control ...........................................................................................................................136
Evaporator Heater Control ...........................................................................................................................136
Pumpdown Control.......................................................................................................................................136
Load Limiting ................................................................................................................................................139
Compressor Run Status ...............................................................................................................................139
Alarm Status.................................................................................................................................................139
BAS/EMS Discharge Air Temperature Reset Using a Voltage or Current Signal ........................................ 140
SECTION 9 – SERVICE AND TROUBLESHOOTING ..................................................................................... 141
Clearing History Buffers................................................................................................................................141
Service Mode ...............................................................................................................................................141
Service Mode – Outputs...............................................................................................................................141
Service Mode – Condensing Unit Configuration ..........................................................................................142
Service Mode – Analog and Digital Inputs....................................................................................................142
Control Inputs/Outputs .................................................................................................................................143
Checking Inputs And Outputs.......................................................................................................................145
Optional Printer Installation ..........................................................................................................................149
SECTION 10 – MAINTENANCE.........................................................................................................................153
Important ......................................................................................................................................................153
Compressors ................................................................................................................................................153
Condenser Fan Motors.................................................................................................................................153
Condenser Coils...........................................................................................................................................153
Operating Parameters ..................................................................................................................................153
On-Board Battery Back-Up...........................................................................................................................153
Overall Unit Inspection .................................................................................................................................153
BACnet, Modbus and YorkTalk 2 Communications ......................................................................................154

QUANTECH 7
Form QCC2-NM1
Issue Date: 5/20/2021
List of gures
FIGURE 1 - Quantech Air-Cooled Scroll Compressor Condensing Unit ................................................................13
FIGURE 2 - Unit Components Front.......................................................................................................................18
FIGURE 3 - Power Panel Components ..................................................................................................................19
FIGURE 4 - Power Panel / Control Components....................................................................................................20
FIGURE 5 - Refrigerant Flow Diagram ...................................................................................................................25
FIGURE 6 - Process and Instrumentation Diagram................................................................................................26
FIGURE 7 - Unit Rigging ........................................................................................................................................27
FIGURE 8 - Single-Point Supply Connection – Terminal Block, Non-Fused Disconnect Switch
or Circuit Breaker ................................................................................................................................36
FIGURE 9 - Discharge Air Sensor Field Wiring ......................................................................................................36
FIGURE 10 - Control Wiring ...................................................................................................................................37
FIGURE 11 - Control Wiring Diagram, Single Circuit, IPU II...................................................................................50
FIGURE 12 - Control Wiring Diagram, Single Circuit, IPU II ..................................................................................52
FIGURE 13 - Control Wiring Diagram, Dual Circuit, IPU II.....................................................................................54
FIGURE 14 - Control Wiring Diagram, Dual Circuit, IPU II.....................................................................................56
FIGURE 15 - Control Wiring Diagram, Details, Single Circuit ................................................................................58
FIGURE 16 - Control Wiring Diagram, Details, Dual Circuit...................................................................................60
FIGURE 17 - Power Wiring, Single Circuit .............................................................................................................62
FIGURE 18 - Power Wiring, Single Circuit .............................................................................................................64
FIGURE 19 - Power Wiring, Single Circuit .............................................................................................................66
FIGURE 20 - Power Wiring, Single Circuit .............................................................................................................68
FIGURE 21 - Power Wiring, Dual Circuit................................................................................................................70
FIGURE 22 - Power Wiring, Dual Circuit................................................................................................................72
FIGURE 23 - Connection Wiring, Single Circuit .....................................................................................................74
FIGURE 24 - Connection Wiring, Single Circuit .....................................................................................................76
FIGURE 25 - Connection Wiring, Single Circuit .....................................................................................................78
FIGURE 26 - Connection Wiring, Single Circuit .....................................................................................................80
FIGURE 27 - Connection Wiring, Dual Circuit........................................................................................................82
FIGURE 28 - Connection Wiring, Dual Circuit........................................................................................................84
FIGURE 29 - Unit Clearances – All Models ............................................................................................................88
FIGURE 30 - Sample Isolator Location Drawing ....................................................................................................89
FIGURE 31 - Isolator Locations, 60 HZ..................................................................................................................90
FIGURE 32 - One Inch Deection Spring Isolator Cross-Reference......................................................................91
FIGURE 33 - One Inch Deection Spring Isolators Installation Instructions...........................................................92
FIGURE 34 - Two Inch Deection Seismic Isolator Cross-Reference .................................................................... 93
FIGURE 35 - Seismic Isolator Installation And Adjustment ....................................................................................94
FIGURE 36 - Durulene Isolator Cross-Reference ..................................................................................................95
FIGURE 37 - Installation of Durulene Vibration Isolators .......................................................................................96
FIGURE 38 - Discharge Air Temperature Control.................................................................................................134
FIGURE 39 - Suction Pressure Control................................................................................................................135
FIGURE 40 - QCC2040C – QCC2070C Fan Location (Typical) ..........................................................................137
FIGURE 41 - Microboard Layout ..........................................................................................................................144
FIGURE 42 - I/O Board Relay Contact Architecture ............................................................................................148
FIGURE 43 - Printer to Microboard Electrical Connections..................................................................................149
FIGURE 44 - Micro Panel Connections................................................................................................................155

QUANTECH
8
Form QCC2-NM1
Issue Date: 5/20/2021
List of tables
TABLE 1 - Fitting Equivalent Lengths.....................................................................................................................33
TABLE 2 - Refrigerant Piping Charges...................................................................................................................33
TABLE 3 - Miscellaneous Liquid Line Pressure Drops...........................................................................................34
TABLE 4 - Refrigerant Line Connections ...............................................................................................................34
TABLE 5 - Voltage Limitations................................................................................................................................39
TABLE 6 - Physical Data (English).........................................................................................................................40
TABLE 7 - Micro Panel Power Supply....................................................................................................................41
TABLE 8 - Voltage Range ......................................................................................................................................41
TABLE 9 - Lug Ranges...........................................................................................................................................45
TABLE 10 - Status Key Messages Quick Reference List..................................................................................... 110
TABLE 11 - Operation Data.................................................................................................................................. 114
TABLE 12 - Cooling Setpoints Programmable Limits and Defaults......................................................................125
TABLE 13 - Program Key Limits and Defaults .....................................................................................................125
TABLE 14 - Setpoints Quick Reference List.........................................................................................................126
TABLE 15 - Options Key Programming Quick Reference List .............................................................................132
TABLE 16 - Discharge Air Temperature Control for 5 and 6 Compressors (7 And 8 Steps) ................................134
TABLE 17 - Discharge Air Temperature Control for 4 Compressors (6 Steps).....................................................134
TABLE 18 - QCC2015C – QCC2070C Condenser Fan Control Using Outdoor Ambient Temperature and
Discharge Pressure ..........................................................................................................................137
TABLE 19 - QCC2040C – QCC2070C Condenser Fan Control Using Discharge Pressure Only ....................... 137
TABLE 20 - QCC2015C – QCC2070C Low Ambient Condenser Fan Control –
Discharge Pressure Control..............................................................................................................138
TABLE 21 - QCC2015C – QCC2030C Low Ambient Condenser Fan Control –
Discharge Pressure Control..............................................................................................................138
TABLE 22 - Compressor Operation – Load Limiting ............................................................................................139
TABLE 23 - I/O Digital Inputs ...............................................................................................................................143
TABLE 24 - I/O Digital Outputs.............................................................................................................................143
TABLE 25 - I/O Analog Inputs ..............................................................................................................................143
TABLE 26 - I/O Analog Outputs............................................................................................................................143
TABLE 27 - Outdoor Air Sensor Temperature/Voltage/ Correlation...................................................................... 145
TABLE 28 - Discharge Air Temp. Sensor Temperature/Voltage/Resistance Correlation......................................146
TABLE 29 - Pressure Transducers.......................................................................................................................147
TABLE 30 - Troubleshooting ................................................................................................................................150
TABLE 31 - Minimum, Maximum And Default Values ..........................................................................................155
TABLE 32 - Values Required For Bas Communication ........................................................................................156
TABLE 33 - Real Time Error Numbers .................................................................................................................156
TABLE 34 - BACnet and Modbus Communications Data Map ............................................................................158
TABLE 35 - YorkTalk 2 Communications Data Map .............................................................................................163

QUANTECH 9
Form QCC2-NM1
Issue Date: 5/20/2021
1
Section 1 – General equipment information and safety
Introduction
The 15 ton to 80 ton (50 kW to 280 kW) QCC2 models
are shipped complete from the factory ready for field
installation.
The unit is pressure-tested, evacuated and given a ni-
trogen holding charge and includes an initial oil charge
(R-410A refrigerant supplied by others). After assem-
bly, an operational test is performed to ensure that each
control device operates correctly.
The unit structure is heavy-gauge, galvanized steel.
This galvanized steel is coated with baked-on pow-
der paint which, when subjected to ASTM B117 1000
hour salt spray testing, yields a minimum ASTM 1654
rating of “6”. Units are designed in accordance with
NFPA 70 (National Electric Code), ASHRAE/ANSI 15
Safety code for mechanical refrigeration, and are cETL
listed. All units are produced at an ISO 9000-registered
facility.
Compressors
The condensing unit has suction-gas cooled, hermet-
ic, scroll compressors. The compressors incorporate
a compliant scroll design in both the axial and radial
direction. All rotating parts of the compressors are
statically and dynamically balanced. A large internal
volume and oil reservoir provides greater liquid toler-
ance. Compressor crankcase heaters are also included
for extra protection against liquid migration.
Condenser
Coils
Fin and tube condenser coils of seamless, internally-
enhanced, high-condensing-coefficient, corrosion re-
sistant copper tubes are arranged in staggered rows,
mechanically expanded into aluminum fins. Integral
subcooling is included. The design working pressure
of the coil is 650 psig (45 barg).
Low sound fans
The condenser fans are composed of corrosion resis-
tant aluminum hub and composite blades molded into
a low noise airfoil section. They are designed for maxi-
mum efficiency and are statically and dynamically bal-
anced for vibration-free operation. They are directly
driven, and positioned for vertical air discharge. The
fan guards are constructed of heavy-gauge, rust-resis-
tant, PVC (polyvinyl chloride)-coated steel wire.
Motors
The fan motors are Totally Enclosed Air-Over, squirrel-
cage type, current protected. They feature ball bearings
that are double-sealed and permanently lubricated.
Refrigerant circuit
All unit piping will be copper with brazed joints. The
liquid line will include a field connection shutoff valve
with charging port located on each condenser circuit.
Suction line connections are provided on each refrig-
eration circuit. A filter drier and sight glass are shipped
loose for field installation on each refrigerant circuit.
All expansion valves, liquid line solenoid valves,
refrigerant, and refrigerant field piping are supplied by
others.
Warranty
Quantech warrants all equipment and materials against
defects in workmanship and materials for a period of
eighteen months from date of shipment, unless labor
or extended warranty has been purchased as part of the
contract.
The warranty is limited to parts only replacement and
shipping of any faulty part, or sub-assembly, which has
failed due to poor quality or manufacturing errors. All
claims must be supported by evidence that the failure
has occurred within the warranty period, and that the
unit has been operated within the designed parameters
specified.
All warranty claims must specify the unit model, serial
number, order number and run hours/starts. Model and
serial number information is printed on the unit identi-
fication plate.
The unit warranty will be void if any modification to
the unit is carried out without written approval from
Quantech.
For warranty purposes, the following conditions must
be satisfied:
• The initial start of the unit must be carried out by
trained personnel from an Authorized Quantech
Service Representative (see SECTION 6 – COM-
MISSIONING).
• Only genuine QUANTECH approved spare parts,
oils, coolants, and refrigerants must be used.

QUANTECH
10
Form QCC2-NM1
Issue Date: 5/20/2021
SECTION 1 – GENERAL EQUIPMENT INFORMATION AND SAFETY
• All the scheduled maintenance operations detailed
in this manual must be performed at the specied
times by suitably trained and qualied personnel
(see SECTION 10 – MAINTENANCE).
• Failure to satisfy any of these conditions will au-
tomatically void the warranty (see Warranty Pol-
icy).
Safety and quality
Standards for safety and quality
QCC2 UNITS are designed and built within an ISO
9002 accredited design and manufacturing organiza-
tion. The condensing units comply with the applicable
sections of the following Standards and Codes:
• ANSI/ASHRAE Standard 15- Safety Code for
Mechanical Refrigeration.
• ANSI/NFPA Standard 70- National Electrical
Code (N.E.C.).
• ASME Boiler and Pressure Vessel Code- Section
VIII Division 1.
• ARI Standard 550/590 - Positive Displacement
Compressors and Air Cooled Rotary Screw Water
Chilling Packages.
• ASHRAE 90.1- Energy Eciency compliance.
• ARI 370- Sound Rating of Large Outdoor Refrig-
eration and Air Conditioning Equipment.
• Conform to Intertek Testing Services, formerly
ETL, for construction of condensing units and
provide E.T.L./c E.T.L. Listing label.
In addition, the condensing units conform to Under-
writers Laboratories (U.L.) for construction of chillers
and provide U.L./cU.L. Listing Label.
Responsibility for safety
Every care has been taken in the design and manufac-
ture of the unit to ensure compliance with the safety
requirements listed above. However, the individual
operating or working on any machinery is primarily
responsible for:
• Personal safety, safety of other personnel, and the
machinery.
• Correct utilization of the machinery in accordance
with the procedures detailed in the manuals.
About this manual
The following terms are used in this document to alert
the reader to areas of potential hazard.
A WARNING is given in this document
to identify a hazard, which could lead to
personal injury. Usually an instruction
will be given, together with a brief expla-
nation and the possible result of ignoring
the instruction.
A CAUTION identies a hazard which
could lead to damage to the machine,
damage to other equipment and/or envi-
ronmental pollution. Usually an instruc-
tion will be given, together with a brief
explanation and the possible result of
ignoring the instruction.
A NOTE is used to highlight additional
information, which may be helpful to
you but where there are no special safety
implications.
The contents of this manual include suggested best
working practices and procedures. These are issued for
guidance only, and they do not take precedence over
the above stated individual responsibility and/or local
safety regulations.
This manual and any other document supplied with
the unit are the property of Quantech which reserves
all rights. They may not be reproduced, in whole or in
part, without written authorization from an authorized
Quantech Sales Representative.
Misuse of equipment
Suitability for application
The unit is intended for DX cooling applications and is
not suitable for purposes other than those specified in
these instructions. Any use of the equipment other than
its intended use, or operation of the equipment contrary
to the relevant procedures may result in injury to the
operator, or damage to the equipment.
The unit must not be operated outside the design pa-
rameters specified in this manual.

QUANTECH 11
SECTION 1 – GENERAL EQUIPMENT INFORMATION AND SAFETY
Form QCC2-NM1
Issue Date: 5/20/2021
1
Structural support
Structural support of the unit must be provided as in-
dicated in these instructions. Failure to provide correct
support may result in injury to the operator, or damage
to the equipment and/or building.
Mechanical strength
The unit is not designed to withstand loads or stresses
from adjacent equipment, pipework or structures. Ad-
ditional components must not be mounted on the unit.
Any such extraneous loads may cause structural failure
and may result in injury to the operator, or damage to
the equipment.
General access
There are a number of areas and features, which may
be a hazard and potentially cause injury when working
on the unit unless suitable safety precautions are taken.
It is important to ensure access to the unit is restricted
to suitably qualified persons who are familiar with the
potential hazards and precautions necessary for safe
operation and maintenance of equipment containing
high temperatures, pressures and voltages.
Pressure systems
The unit contains refrigerant vapor and liquid under
pressure, release of which can be a danger and cause
injury. The user should ensure that care is taken during
installation, operation and maintenance to avoid dam-
age to the pressure system. No attempt should be made
to gain access to the component parts of the pressure
system other than by suitably trained and qualified per-
sonnel.
Electrical
The unit must be grounded. No installation or main-
tenance work should be attempted on the electrical
equipment without first switching power OFF, isolat-
ing and locking-off the power supply. Servicing and
maintenance on live equipment must only be per-
formed by suitably trained and qualified personnel. No
attempt should be made to gain access to the control
panel or electrical enclosures during normal operation
of the unit.
Rotating parts
Fan guards must be fitted at all times and not removed
unless the power supply has been isolated. If ductwork
is to be fitted, requiring the wire fan guards to be re-
moved, alternative safety measures must be taken to
protect against the risk of injury from rotating fans.
Sharp edges
The fins on the air-cooled condenser coils have sharp
metal edges. Reasonable care should be taken when
working in contact with the coils to avoid the risk of
minor abrasions and lacerations. The use of gloves is
recommended.
Frame rails, brakes, and other components may also
have sharp edges. Reasonable care should be taken
when working in contact with any components to avoid
risk of minor abrasions and lacerations.
Refrigerants and oils
Refrigerants and oils used in the unit are generally non-
toxic, non-flammable and non-corrosive, and pose no
special safety hazards. Use of gloves and safety glasses
is, however, recommended when working on the unit.
The buildup of refrigerant vapor, from a leak for ex-
ample, does pose a risk of asphyxiation in confined or
enclosed spaces and attention should be given to good
ventilation.
High temperature and pressure cleaning
High temperature and pressure cleaning methods
(e.g. steam cleaning) should not be used on any part
of the pressure system as this may cause operation of
the pressure relief device(s). Detergents and solvents,
which may cause corrosion, should also be avoided.
Emergency shutdown
In case of emergency, the control panel is fitted with a
Unit Switch to stop the unit in an emergency. When op-
erated, it removes the low voltage 120 VAC electrical
supply from the inverter system, thus shutting down
the unit.

QUANTECH
12
Form QCC2-NM1
Issue Date: 5/20/2021
THIS PAGE IS INTENTIONALLY LEFT BLANK

QUANTECH 13
Form QCC2-NM1
Issue Date: 5/20/2021
2
Section 2 – Product description
Introduction
Quantech Series 40 Air-Cooled Scroll Condensing
Units provide chilled water for all air conditioning ap-
plications using central station air handling or terminal
units. They are completely self-contained and are de-
signed for outdoor (roof or ground level) installation.
Each unit includes hermetic scroll compressors, a liq-
uid cooler, air cooled condenser, and a weather resis-
tant microprocessor control center, all mounted on a
pressed steel base.
The units are completely assembled with all intercon-
necting refrigerant piping and internal wiring, ready
for field installation.
The unit is pressure-tested, evacuated and given a ni-
trogen holding charge and includes an initial oil charge
(R-410A refrigerant supplied by others). After assem-
bly, a operational test is performed to ensure that each
control device operates correctly.
The unit structure is heavy-gauge, galvanized steel.
This galvanized steel is coated with baked-on pow-
der paint which, when subjected to ASTM B117 1000
hour, salt spray testing, yields a minimum ASTM 1654
rating of “6”. Units are designed in accordance with
NFPA 70 (National Electric Code), ASHRAE/ANSI 15
Safety code for mechanical refrigeration, and are cETL
listed. All units are produced at an ISO 9000-registered
facility.
All exposed power wiring is routed through liquid-
tight, non-metallic conduit.
General system description
Compressors
The condensing unit has suction-gas cooled, hermetic,
scroll compressors. The QCC2 compressors incorpo-
rate a compliant scroll design in both the axial and
radial direction. All rotating parts are statically and
dynamically balanced. A large internal volume and oil
reservoir provides greater liquid tolerance. Compres-
sor crankcase heaters are also included for extra pro-
tection against liquid migration.
An annular discharge check valve and reverse vent as-
sembly provides low pressure drop, silent shutdown,
and reverse rotation protection.
Condenser
Coils – Fin and tube condenser coils of seamless, in-
ternally-enhanced, high-condensing-coefficient, corro-
sion resistant copper tubes are arranged in staggered
rows, mechanically expanded into aluminum fins. Inte-
gral subcooling is included. The design working pres-
sure of the coil is 650 psig (45 bar).
Figure 1 - Quantech Air-Cooled Scroll Compressor Condensing Unit

QUANTECH
14
Form QCC2-NM1
Issue Date: 5/20/2021
SECTION 2 – PRODUCT DESCRIPTION
Low sound fans
The condenser fans are composed of corrosion resis-
tant aluminum hub and composite blades molded into
a low noise airfoil section. They are designed for maxi-
mum efficiency and are statically and dynamically bal-
anced for vibration-free operation. They are directly
driven, and positioned for vertical air discharge. The
fan guards are constructed of heavy-gauge, rust-resis-
tant, PVC (polyvinyl chloride)-coated steel wire.
Motors
The fan motors are Totally Enclosed Air-Over, squirrel-
cage type, current protected. They feature ball bearings
that are double-sealed and permanently lubricated.
Microcomputer control center
All controls are contained in a NEMA 3R/12 cabinet
with hinged outer door and include Liquid Crystal Dis-
play (LCD) with Light Emitting Diode (LED) back-
lighting for outdoor viewing and includes:
• Two display lines
• Twenty characters per line
Display/Print
Color coded 12-button non-tactile keypad with sec-
tions for display and print of typical information:
• Suction temperatures (optional)
• Ambient temperature
• System pressures (each circuit)
• Operating hours and starts (each compressor)
• Print calls up to the liquid crystal display
• Operating data for the systems
• History of fault shutdown data for up to the last
six fault shutdown conditions.
• An RS-232 port, in conjunction with the press-to-
print button, is provided to allow hard copy print-
outs via a separate printer (by others).
Entry
This section is used to enter setpoints or modify system
values.
Setpoints
Updating can be performed to:
• Suction pressure setting
• Suction pressure control zone
• Remote reset temperature range
• Set daily schedule/holiday for start/stop
• Manual override for servicing
• Low and high ambient cutouts
• Number of compressors
• Low suction pressure cutout
• High discharge pressure cutout
• Anti-recycle timer (compressor start cycle time)
• Anti-coincident timer (delay compressor starts)
Unit
This section is used to:
• Set clock
• Set options
• Set unit option
Set unit control for Discharge Air Temperature Control
or for Suction Pressure Control (requires Suction Pres-
sure Transducers) is standard.
Unit On/Off switch
The microprocessor control center is capable of
displaying the following:
• Suction temperatures (optional)
• Low ambient temperature cutout setting
• English or Metric data
• Suction pressure cutout setting
• Each system suction pressure

QUANTECH 15
SECTION 2 – PRODUCT DESCRIPTION
Form QCC2-NM1
Issue Date: 5/20/2021
2
• System discharge pressure
• Discharge Air Temperature Reset via a ISN DDC
or Building Automation System (by others) via:
• A pulse width modulated (PWM) input as
standard
• A 4 mA to 20 mA or 0 VDC to 10 VDC input,
or contact closure with the optional B.A.S.
interface option
• Anti-recycle timer status for each system
• Anti-coincident system start timer condition
• Compressor run status
• No cooling load condition
• Day, date and time
• Daily start/stop times
• Holiday status
• Automatic or manual system lead/lag control
(Discharge Air Temperature control only)
• Automatic lead/lag of compressors within a sys-
tem
• Compressor starts and operating hours (each com-
pressor)
• Status of hot gas valves, and fan operation
• Run permissive status
• Number of compressors running
• Liquid solenoid valve status
• Load and unload timer status
Provisions are included for pumpdown at shutdown,
optional remote discharge air temperature reset, and
two steps of demand load limiting from an external
building automation system. Unit alarm contacts are
standard.
The operating program is stored in non-volatile mem-
ory (EPROM) to eliminate condensing unit failure due
to AC powered failure/battery discharge. Programmed
setpoints are retained in lithium battery -backed RTC
memory for 5 years minimum.
Building automation system interface
The Microprocessor Board can accept a 4 mA to
20 mA, 0 VDC to 10 VDC or contact closure input
to reset the discharge air temperature from a Building
Automation System. Only one of the following remote
communications options can be offered on a unit at a
time: BAS Interface, Remote Control Panel or Multi-
unit Sequence Control (Factory Mounted).
• The standard unit capabilities include remote
start-stop, remote discharge air temperature re-
set through a PWM 4 mA to 20 mA or 0 VDC to
10 VDC input signal or up to two stages of de-
mand (load) limiting depending on model.
• The standard control panel can be directly con-
nected to a Quantech Building Automated Sys-
tem.
Communications
• Native communication capability for BACnet
(MS/TP) and Modbus
• Optional communication available for N2 and
LON via eLink option
Power panel
Each panel contains:
• Compressor power terminals
• Compressor motor starting contactors per Interna-
tional Electrotechnical Commission (I.E.C.).
• Control power terminals to accept incoming for
115-1-60 control power
• Fan contactors and overload current protection
The power wiring is routed through liquid-tight con-
duit to the compressors and fans.

QUANTECH
16
Form QCC2-NM1
Issue Date: 5/20/2021
SECTION 2 – PRODUCT DESCRIPTION
Accessories and options
Electrical options
Compressor Power Connections
Single-point terminal block connection(s) are provid-
ed as standard. The following power connections are
available as factory mounted options. (See Electrical
Data for specific voltage and options availability.)
Single-Point Supply Terminal Block (Standard
on QCC2 Models).
Includes enclosure, terminal-block and interconnecting
wiring to the compressors. Separate external protection
must be supplied, by others, in the incoming compres-
sor-power wiring. This option cannot be included if
either the Single Point Non-Fused Disconnect Switch
or Single-Point Circuit Breaker options have been in-
cluded.
Single-Point Non-Fused Disconnect Switch
Unit-mounted disconnect switch with external, lock-
able handle in compliance with Article 440-14 of
N.E.C., can be supplied to isolate the unit power volt-
age for servicing. Separate external fusing must be
supplied, by others in the power wiring, which must
comply with the National Electrical Code and/or local
codes.
Single-Point Circuit Breaker
A unit mounted circuit breaker with external, lockable
handle (in compliance with N.E.C. Article 440-14),
can be supplied to isolate the power voltage for ser-
vicing. (This option includes the Single-Point Power
connection.)
Control Transformer
This transformer converts unit power voltage to 115-
1-60 (0.5 KVA or 1.0 KVA capacity). Factory mount-
ing includes primary and secondary wiring between the
transformer and the control panel.
Power Factor Correction Capacitors
These factory mounted capacitors will correct unit
compressor to a power factor between 0.90 and 0.95.
Control options
Ambient Kit (Low)
Units will operate to 25°F (-4°C). This factory mounted
accessory includes all necessary components to permit
chiller operation to 0°F (-18°C). This option includes
the Discharge Pressure Transducer / Readout Capabil-
ity option. For correct head pressure control in applica-
tions below 25°F (-4°C), where wind gusts may exceed
five mph, it is recommended that factory mounted op-
tional Condenser Louvered Enclosure Panels also be
included.
Ambient Kit (High)
This factory mounted kit is required if units are to op-
erate when the ambient temperature is above 110°F
(43°C) and includes discharge pressure transducers.
This option includes the factory mounted Discharge
Pressure Transducer / Readout Capability option.
Building Automation System Interface
The factory addition of a Printed Circuit Board to ac-
cept a 4 mA to 20 mA, 0 VDC to 10 VDC or contact
closure input to reset the leaving chiller liquid tempera-
ture from a Building Automation System. Only one of
following options can be offered on a unit at a time:
BAS, Remote Control Panel or Multi-unit Sequence
Control. (Factory-Mounted) The standard unit capa-
bilities include remote start/stop, remote discharge air
temperature reset via a PWM input signal or up to two
steps of demand (load) limiting depending on model.
The standard control panel can be directly connected to
a Building Automated System via the standard onboard
RS485 communication port.
Language LCD and Keypad Display
Spanish, French, and German unit LCD controls and
keypad display are available; however the standard
language is English.
Discharge Pressure Transducers and
Readout Capability
The addition of factory mounted pressure transducers
allows models to sense and display discharge pressure.
This is recommended for brine chilling applications.
This option is included with either the low or high am-
bient kits.

QUANTECH 17
SECTION 2 – PRODUCT DESCRIPTION
Form QCC2-NM1
Issue Date: 5/20/2021
2
Suction Pressure Transducers
This transducer permits the unit to sense and display
suction pressure. This capability is standard on QCC2
models.
Multi-Unit Sequencing
A separate sequencing control center is provided to
handle sequencing control of up to eight chillers in
parallel based on mixed liquid temperature (intercon-
necting wiring by others). The only one of following
factory mounted options can be offered on a unit at a
time: BAS, Remote Control Panel or Multi-Unit Se-
quence Control.
Compressor and piping options
Chicago Code Relief Valves
Unit will be provided with relief valves to meet Chi-
cago code requirements. (Factory-Mounted)
Service Isolation Valve
Service isolation valves are standard to unit. This in-
cludes a system high pressure relief valve or inter-
nal compressor relief mechanism in compliance with
ASHRAE 15. (Factory-Mounted)
Hot Gas Bypass
Permits continuous, stable operation at capacities be-
low the minimum step of compressor unloading to as
low as 5% capacity (depending on both the unit and
operating conditions) by introducing an artificial load
on the cooler. Hot gas by-pass is installed on only re-
frigerant system #1 on two-circuited units. (Factory-
Mounted)
Condenser and Cabinet Options
Condenser coil protection against corrosive environ-
ments is available by choosing any of the following
options. For additional application recommendations,
refer to Form 150.12-ES1. (Factory-Mounted)
Pre-Coated Fin Condenser Coils
The unit’s coils are constructed with epoxy coated
aluminum fins. This can provide corrosion resistance
comparable to copper-fin coils in typical seashore loca-
tions. Either these or the post-coated coils (below) are
recommended for units being installed at the seashore
or where salt spray may hit the unit.
Post-Coated Dipped Condenser Coils
The unit’s coils are constructed with dipped-cured con-
denser coils. This is the choice for corrosive applica-
tions (with the exception of strong alkalis, oxidizers
and wet bromine, chlorine and fluorine in concentra-
tions greater than 100 ppm).
Copper Fin Condenser Coils
The unit’s coils are constructed with copper fins. This
is not recommended for units in areas where they may
be exposed to acid rain.
Enclosure Panels (Unit)
Tamperproof enclosure panels prevent unauthorized
access to units. Enclosure panels can provide an aes-
thetically pleasing alternative to expensive fencing.
Additionally, for correct head pressure control, Quan-
tech recommends the use of louvered panels.
Louvered Panels (Full Unit)
Louvered panels surround the front, back, and sides of
the unit. They prevent unauthorized access and visu-
ally screen unit components. Unrestricted air flow is
permitted through generously sized louvered openings.
This option is applicable for any outdoor design ambi-
ent temperature up to 115°F (46°C). (Factory-Mount-
ed.)
Sound Attenuation
One or both of the following factory mounted sound
attenuation options are recommended for residential or
other similar sound-sensitive locations. Louvered Pan-
els can be ordered for winter applications where wind
gusts may exceed five miles per hour. The following
types of enclosure options are available:
Compressor Acoustic Sound Blanket
Each factory mounted compressor is individually en-
closed by an acoustic sound blanket. The sound blan-
kets are made with one layer of acoustical absorbent
textile fiber of 5/8 in. (15 mm) thickness; one layer
of anti-vibrating heavy material thickness of 1/8 in.
(3 mm). Both are closed by two sheets of welded PVC,
reinforced for temperature and UV resistance.

QUANTECH
18
Form QCC2-NM1
Issue Date: 5/20/2021
SECTION 2 – PRODUCT DESCRIPTION
Ultra Quiet Fan
Lower RPM, 8-pole fan motors are used with steeper-
pitch fans on these factory mounted devices.
Vibration Isolators
Level adjusting, spring type 1 in. (25.4 mm) or seismic
deflection or neoprene pad isolators for mounting un-
der unit base rails. (Field-Mounted)
Unit components
Figure 2 - Unit Components Front
MICROPANEL FANS
COMPRESSORS
CONDENSER
COILS

QUANTECH 19
SECTION 2 – PRODUCT DESCRIPTION
Form QCC2-NM1
Issue Date: 5/20/2021
2
Power panel components
Figure 3 - Power Panel Components
LD13247
COMPRESSOR
CONTACTORS
XTBF1
FAN CONTACTORS
FAN CONTACTOR
COMPRESSOR
OVERLOADS
FAN FUSES
DISCONNECT
SWITCH

QUANTECH
20
Form QCC2-NM1
Issue Date: 5/20/2021
SECTION 2 – PRODUCT DESCRIPTION
Power panel/control components
Figure 4 - Power Panel / Control Components
COMPRESSOR
OVERLOADS
COMPRESSOR
CONTACTORS
FAN CONTACTORS
FAN FUSES
CONTROL
RELAY
MICROCOMPUTER
CONTROL
CENTER MICROPANEL
DISPLAY
KEYPAD
XTBC1
XTBC2
XTBF2
MICROBOARD
LD13248
This manual suits for next models
1
Table of contents
Popular Heat Pump manuals by other brands
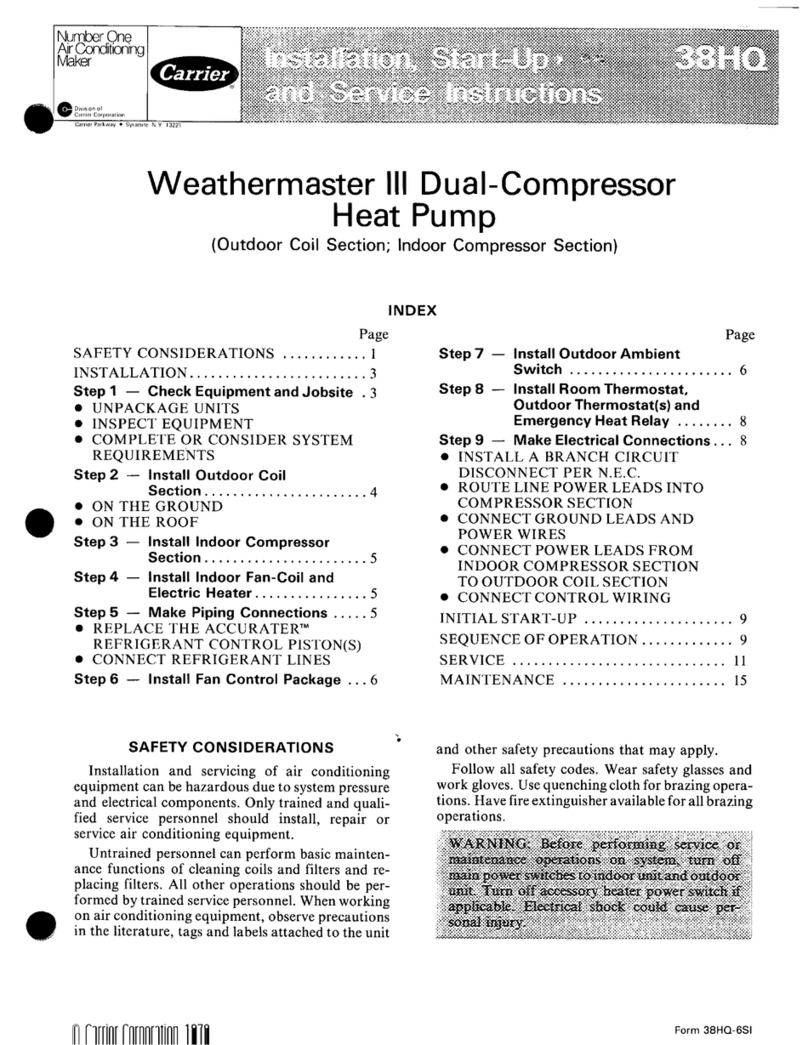
Carrier
Carrier Weathermaster III 38HQ Installation, Start-Up and Service Instructions
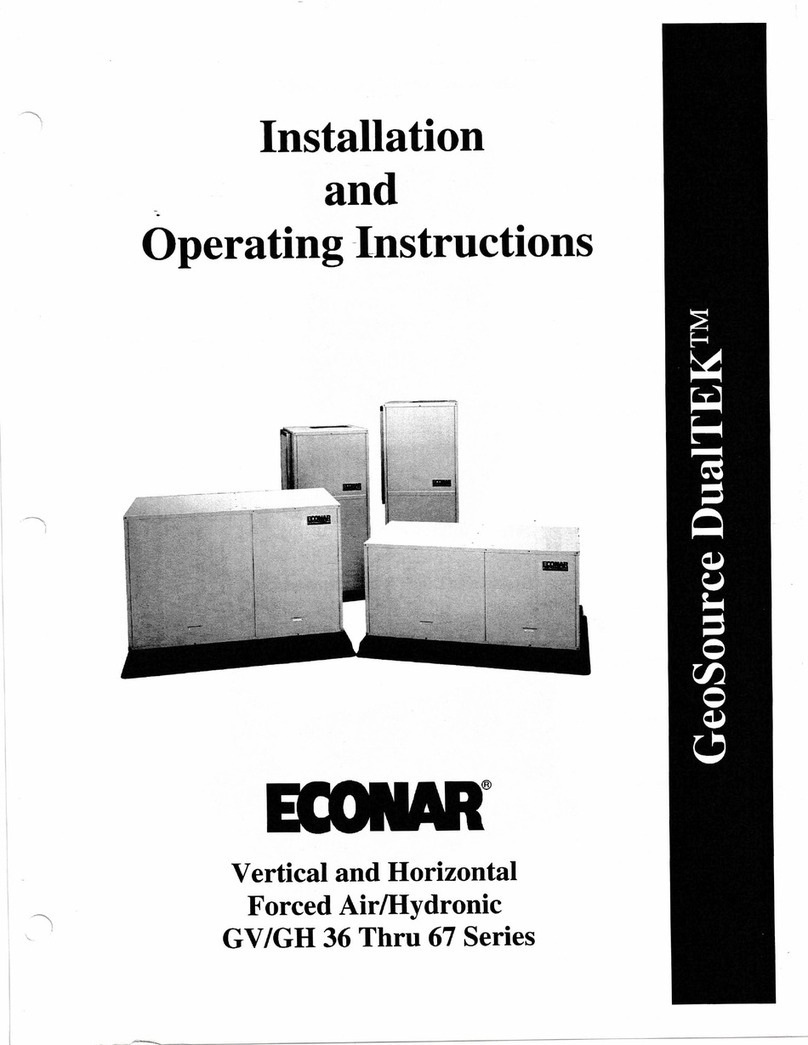
Econar
Econar GeoSource DualTEK GV Series Installation and operating instructions
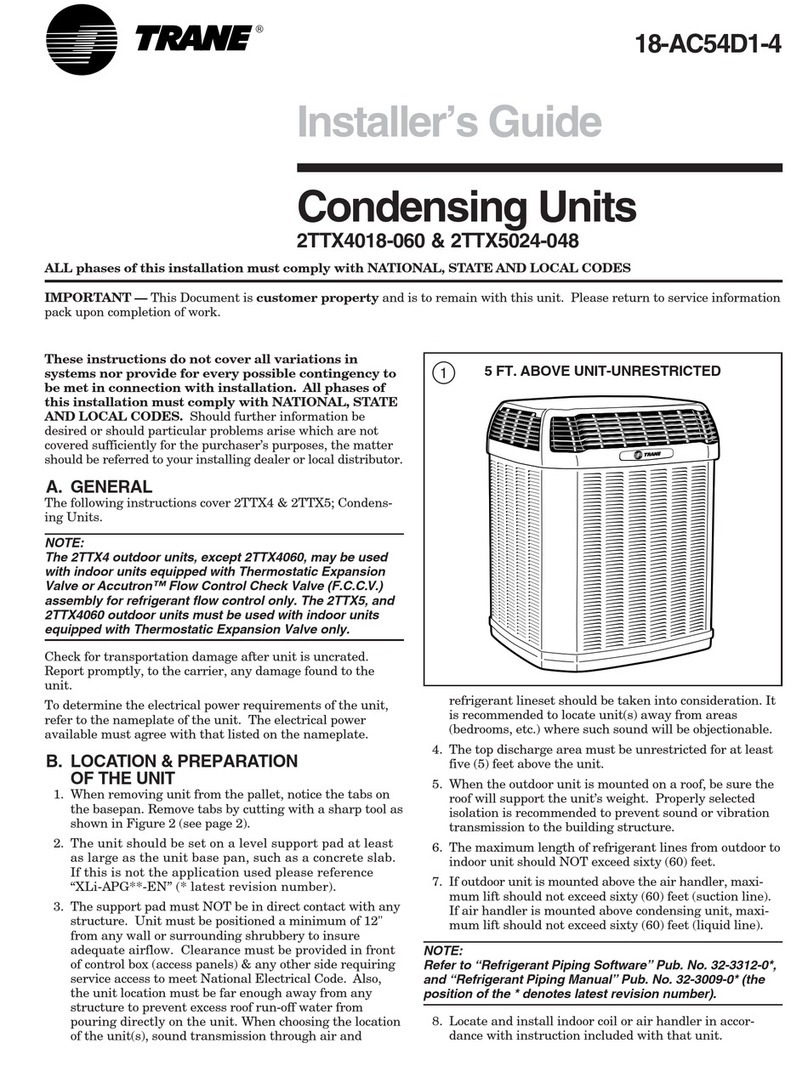
Trane
Trane 2TTX4018B Installer's guide

Becker
Becker VARIAIR SV 300 operating instructions
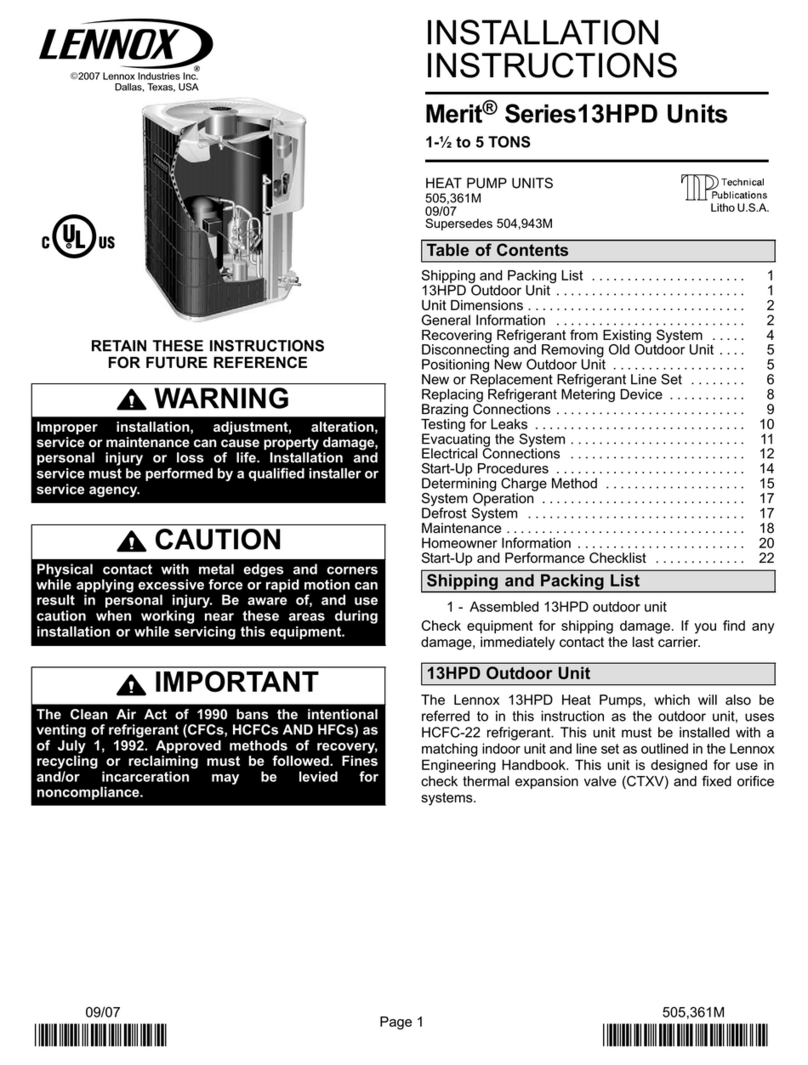
Lennox
Lennox Merit Series13HPD Units installation instructions

Payne
Payne PH1Z024 installation instructions
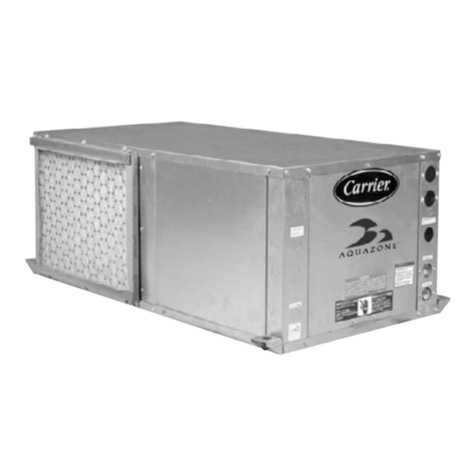
Carrier
Carrier Aquazone 50RHE 006 Installation, operation and maintenance instructions

Daikin
Daikin EWYT CZ Series operating manual
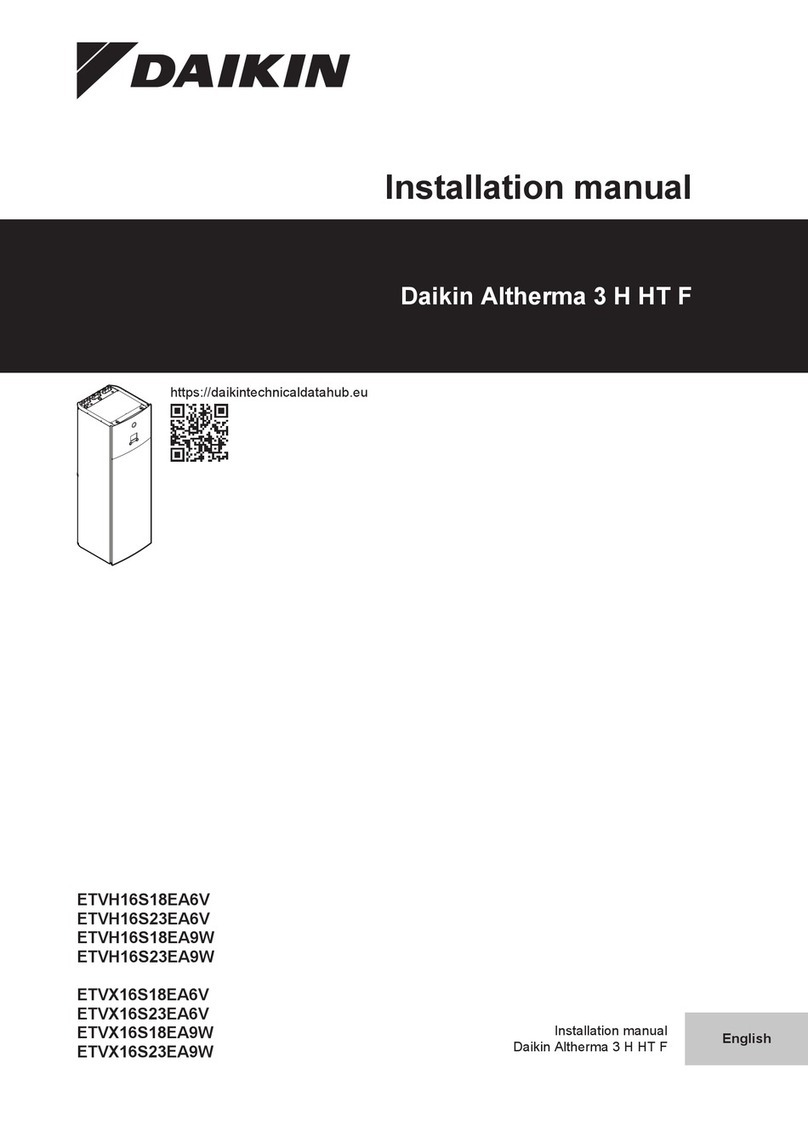
Daikin
Daikin 3 H HT F installation manual
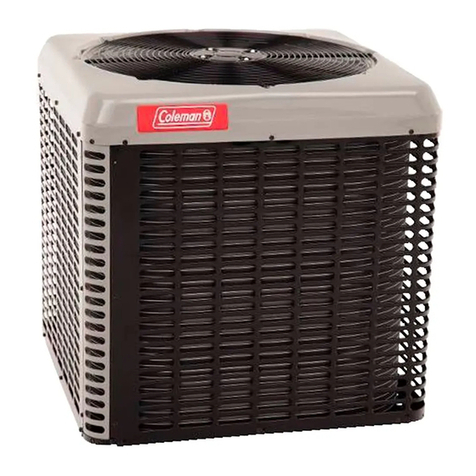
Coleman
Coleman LX SERIES Technical guide
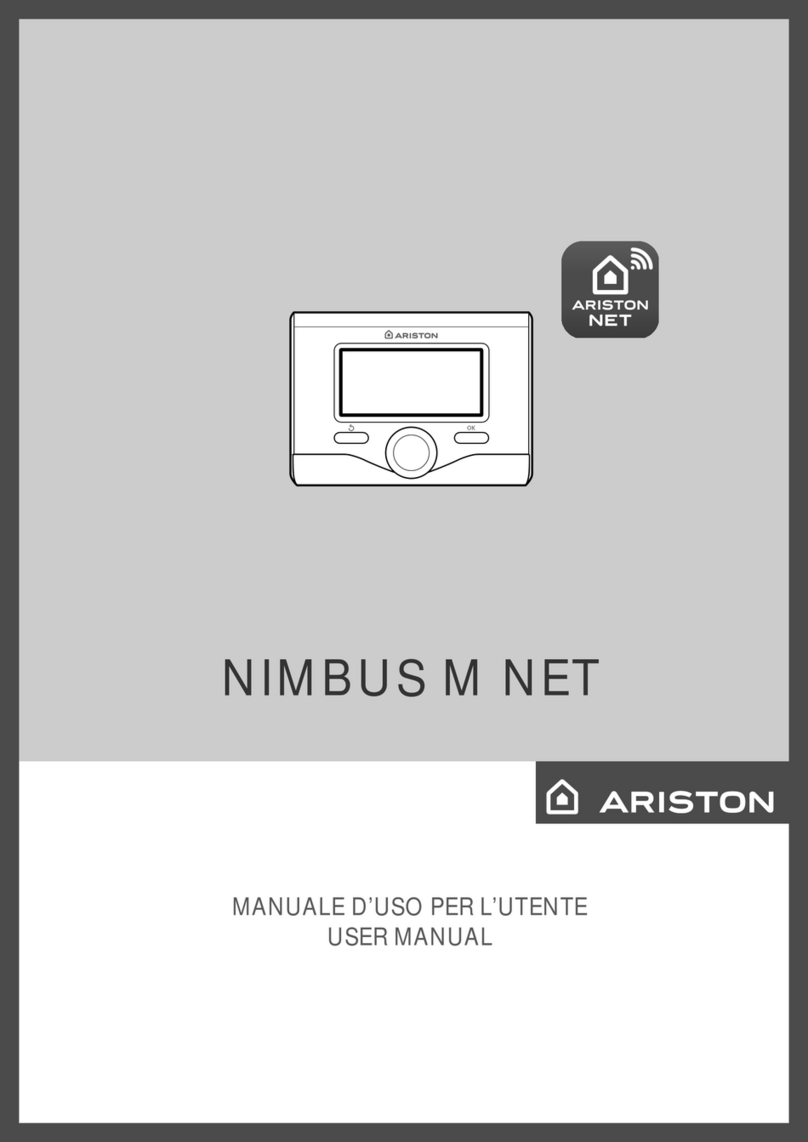
Ariston
Ariston NIMBUS M NET user manual

Viessmann
Viessmann VITOCAL 060-A Operating Instructions for the System User